失蜡铸造(1)全解
失蜡铸造
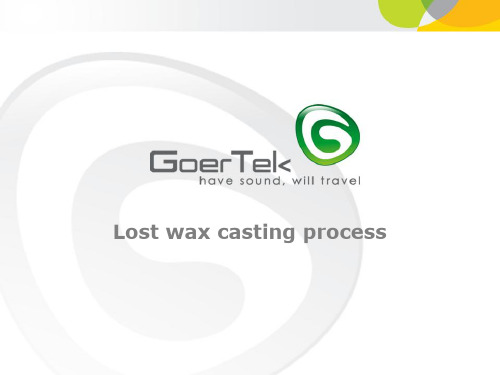
类型 机械加工压型
低熔点合金铸造 压型
特点
1.材料通常为钢,也有使用铜合金、铝合金 2.尺寸精度可以充分满足设计要求,型腔表面粗糙度
Ra=1.6~0.4цm 3.使用寿命可达10万次以上 4.制造成本高
1.材料:低熔点合金(通常熔点不超过300℃) 2.尺寸精度比机械加工压型低,型腔表面粗糙度
Ra=3.2~0.8цm 3.使用寿命可达几千次以上 4.制造成本较低
通孔
不通孔
5~10 >10~30 >30~60 >60~120 >120~200 >200~300 >25~50 >50~80 >80~100 >100~120
5.加工余量
熔模铸件单面加工余量(单位 mm)
铸件最大尺寸 单面加工余量 浇口面加工余量
≤50 >50~120 >120~250 >250~400
为便于脱模和模料回收,模料粘度不能太大,在90℃附近的粘度应为3×10-3~3×10-2Pa.S 。为得到清晰熔 模,模料应具有良好的流动性。 7.灰分
模料灼烧后的残留物称灰分,它将影响铸件的质量,也是模料最重要的指标之一。一般模料灰分的质量分 数应低于0.05%。
熔模铸件的铸造斜度
铸造斜度面高h/mm
取值
≤20 >20-50 >50-100
>100
外表面 0º20´
非加工面斜度
内表面 1º
0º15´
0º30´
0º10´
0º30´
0º10´
0º15´
4.最小铸出孔
孔的直径
3-5 >5~10 >10~20 >20~40 >40~60 >60~100 >100
最大孔深
1.3 压型种类及制造方法
特种铸造简介
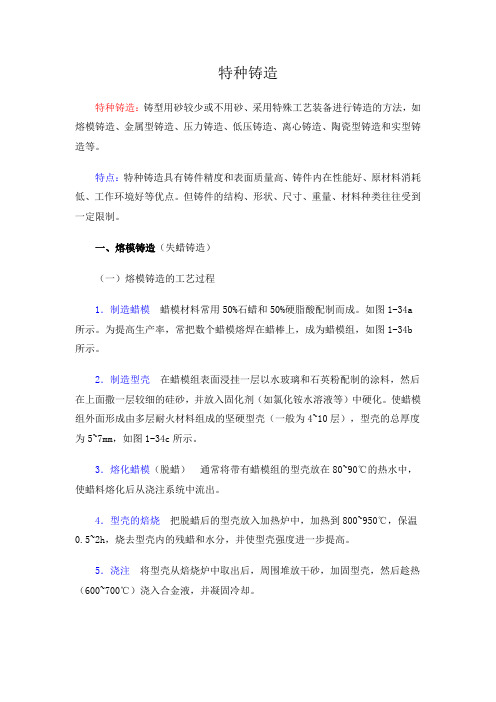
特种铸造特种铸造:铸型用砂较少或不用砂、采用特殊工艺装备进行铸造的方法,如熔模铸造、金属型铸造、压力铸造、低压铸造、离心铸造、陶瓷型铸造和实型铸造等。
特点:特种铸造具有铸件精度和表面质量高、铸件内在性能好、原材料消耗低、工作环境好等优点。
但铸件的结构、形状、尺寸、重量、材料种类往往受到一定限制。
一、熔模铸造(失蜡铸造)(一)熔模铸造的工艺过程1.制造蜡模蜡模材料常用50%石蜡和50%硬脂酸配制而成。
如图1-34a 所示。
为提高生产率,常把数个蜡模熔焊在蜡棒上,成为蜡模组,如图1-34b 所示。
2.制造型壳在蜡模组表面浸挂一层以水玻璃和石英粉配制的涂料,然后在上面撒一层较细的硅砂,并放入固化剂(如氯化铵水溶液等)中硬化。
使蜡模组外面形成由多层耐火材料组成的坚硬型壳(一般为4~10层),型壳的总厚度为5~7mm,如图1-34c所示。
3.熔化蜡模(脱蜡)通常将带有蜡模组的型壳放在80~90℃的热水中,使蜡料熔化后从浇注系统中流出。
4.型壳的焙烧把脱蜡后的型壳放入加热炉中,加热到800~950℃,保温0.5~2h,烧去型壳内的残蜡和水分,并使型壳强度进一步提高。
5.浇注将型壳从焙烧炉中取出后,周围堆放干砂,加固型壳,然后趁热(600~700℃)浇入合金液,并凝固冷却。
6.脱壳和清理用人工或机械方法去掉型壳、切除浇冒口,清理后即得铸件。
(二)熔摸铸造铸件的结构工艺性熔摸铸造铸件的结构,除应满足一般铸造工艺的要求外,还具有其特殊性:1.铸孔不能太小和太深否则涂料和砂粒很难进入腊模的空洞内,只有采用陶瓷芯或石英玻璃管芯,工艺复杂,清理困难。
一般铸孔应大于2mm.。
2.铸件壁厚不可太薄一般为2~8mm。
3.铸件的壁厚应尽量均匀熔摸铸造工艺一般不用冷铁,少用冒口,多用直浇口直接补缩,故不能有分散的热节。
(三)熔模铸造的特点和应用熔模铸造的特点是:(1)铸件精度高、表面质量好,是少、无切削加工工艺的重要方法之一,其尺寸精度可达IT11~IT14,表面粗糙度为Ra12.5~1.6μm。
失蜡法铸造

失蜡法铸造熔模铸造又称失腊法。
失腊法是用腊制作所要铸成器物的模子,然后在腊模上涂以泥浆,这就是泥模。
泥模晾干后,在焙烧成陶模。
一经焙烧,腊模全部熔化流失,只剩陶模。
一般制泥模时就留下了浇注口,再从浇注口灌入铜液,冷却后,所需的器物就制成了。
我国的失腊法至迟起源于春秋时期。
河南淅川下寺2号楚墓出土的春秋时代的铜禁是迄今所知的最早的失腊法铸件。
此铜禁四边及侧面均饰透雕云纹,四周有十二个立雕伏兽,体下共有十个立雕状的兽足。
透雕纹饰繁复多变,外形华丽而庄重,反映出春秋中期我国的失腊法已经比较成熟。
战国、秦汉以后,失腊法更为流行,尤其是隋唐至明、清期间,铸造青铜器采用的多是失腊法。
失腊法一般用于制作小型铸件。
用这种方法铸出的铜器既无范痕,又无垫片的痕迹,用它铸造镂空的器物更佳。
中国传统的熔模铸造技术对世界的冶金发展有很大的影响。
现代工业的熔模精密铸造,就是从传统的失腊法发展而来的。
虽然无论在所用腊料、制模、造型材料、工艺方法等方面,它们都有很大的不同,但是它们的工艺原理是一致的。
四十年代中期,美国工程师奥斯汀创立以他命名的现代熔模精密铸造技术时,曾从中国传统失蜡法得到启示。
1955年奥斯汀实验室提出首创失蜡法的呈请,日本学者鹿取一男根据中国和日本历史上使用失蜡法的事实表示异议,最后取得了胜诉。
【概述】熔模铸造又称"失蜡铸造",通常是在蜡模表面涂上数层耐火材料,待其硬化干燥后,将其中的蜡模熔去而制成型壳,再经过焙烧,然后进行浇注,而获得铸件的一种方法,由于获得的铸件具有较高的尺寸精度和表面光洁度,故又称"熔模精密铸造"。
可用熔模铸造法生产的合金种类有碳素钢、合金钢、耐热合金、不锈钢、精密合金、永磁合金、轴承合金、铜合金、铝合金、钛合金和球墨铸铁等。
熔模铸件的形状一般都比较复杂,铸件上可铸出孔的最小直径可达0.5mm,铸件的最小壁厚为0.3mm。
在生产中可将一些原来由几个零件组合而成的部件,通过改变零件的结构,设计成为整体零件而直接由熔模铸造铸出,以节省加工工时和金属材料的消耗,使零件结构更为合理。
失蜡铸造(1)报告

组装模组
型壳制造、 脱蜡、焙烧
填砂、浇注
观看 影片
熔模铸造的特点
1)、铸件尺寸精度高(CT4-CT7);表面 粗糙度低(Ra1.6-6.3μm)。减少了铸件的 切削加工余量,甚至可实现近净型铸造。
2)、能生产形状复杂的薄壁铸件。如前机 匣(由内、外环和14件叶片组成)。如发动 机叶片,叶型的最小壁厚可达0.7mm。
2.5~4.0 1.5~3.0
2.0
2.0 0.8
3.0~5.0
3. 0~5.0 2.0~4.0
2.5
2.5 1.0
3.5~6.0
3.5~6.0 —
3.0
3.0 —
4.0~7.0
4.0~7.0 —
3.5
4.0 —
2.圆角
一般情况下铸件上各转角处都设计成圆角, 否则容易产生裂纹、缩松。铸件上内圆角和 外圆角按下式计算 r=(d+δ)/k R=r+ (d+δ)/2 r——转角内圆角mm;R——转角外圆角mm d, δ——连接壁的壁厚;k——转角的圆角 系数,根据角度大小接图选取。
1.2.2 熔模铸造浇注系统设计
一、浇注系统作用 1.把液体金属引入型腔 注意充型平稳,避免金属液氧化和卷入气体, 保证不产生冷隔和浇不足缺陷。 2.补充液体金属凝固时体积收缩 浇注系统应能保证补缩时通道畅通,并保证 能提供给铸件必要的补缩金属液,避免铸件 产生缩孔、疏松。
3.在组焊与制壳时起支撑易熔模和型壳作 用。要求有足够强度,防止制壳过程中易熔 模脱落。
1 熔模铸造
1.1
概述
定义:用熔模材料(通常为低熔点的 材料如蜡料)制成熔模样件并组成模 组,然后在模组表面上涂料(耐火材 料),待干燥固化后,将模组加热熔 出模料形成中空型壳,经高温烧结后 浇注金属液体,清理后得到铸件。由 于熔模材料通常为蜡基材料,因此又 称“失蜡铸造”。
失蜡铸造法

现代常用的失蜡铸造工艺是由古代铸造工艺发展而来的。
距今5000多年前的新石器时代晚期,我国古代工匠就在青铜器的制造中广泛采用了失蜡铸造工艺。
当时的工匠根据蜂蜡的可塑性和热挥发性的特点,首先将蜂蜡雕刻成需要形状的蜡模,再在蜡模外包裹黏土并预留一个小洞,晾干后焙烧,使蜡模气化挥发,同时黏土则成为陶瓷壳体,壳体内壁留下了蜡模的阴模。
这时再将熔化的金属沿小孔注入壳体,冷却后打破壳体,即获得所需的金属铸坯。
现代失蜡铸造技术的基本原理并无二致,只不过更加复杂精密。
这主要体现在对蜡模的型位精确的要求更加严格。
现代工艺中蜡模的获得不只是对蜡的直接雕刻,还可以通过对金属原模(版)的硅胶模压得到阴模,再由硅胶阴模注蜡后得到蜡模。
浇铸材料也不再是黏土,而代以铸造石膏。
这样的产品比古代的铸件精细得多。
夏、商、周三代创造了灿烂辉煌的青铜文化,大量造型复杂、纹饰繁缛、工艺高超的青铜铸件流传至今。
春秋时期创造出失蜡法、叠铸法等先进技术,铸成后的加工采用了镶嵌宝石、红铜以及错金技术。
到战国时又出现了鎏金工艺。
在春秋晚期,中国进入早期的铁器时代,及至战国,冶铁已非常盛行。
西汉时冶铁成为最大手工业部门,当时采用炒铁技术。
到了南北朝时又发明了灌钢法炼钢新技术,炼炉的鼓风设施亦有创造发明,汉代使用水力皮橐,宋代发明木风扇,明代改进为木风箱。
在商朝时,我们的祖先对于冶铸青铜器的技术已经非常纯熟,到了春秋时期则进入铁器时代,甚至到了战国中期以后,更发展出一整套的炼钢技术,包括了渗碳钢、百炼钢、炒钢、灌钢等等。
因为中国是世界上最早采用高炉炼铁的国家,所以在古时候炼铁技术是属于高水平的。
其次又在很早的时候就有了比较强的鼓风系统来加强炉子的温度,可以缩短冶炼的时间。
经历了渗碳钢、百炼钢、炒钢等过程,『灌钢法』的发明,是重要的里程碑。
方法是选出素质较高的铁矿,冶炼生铁后,再将液态生铁浇注在熟铁上,经过融炼使得铁渗碳而成为钢。
这种方法不但加快了冶铁的时间,并减少锻打的次数,而且操作方法简便,同时对后来的炼钢的技术产生深远的影响。
失蜡铸造

失蜡铸造也叫精密铸造。
艺术品也常用此种方式浇注。
古代的艺术品大部分是此种方法。
材料:蜡、制壳耐火材料(如石英砂、铝矾土等)、粘结剂(如水玻璃、硅酸乙酯、硅溶胶等)第一步,设计工艺第二步,制作模具第三步,向模具里打蜡,再把蜡件取出。
蜡件的形状即浇注后铸件的样子第四步,修理蜡件第五步,将蜡件组到浇注系统上第六步,制壳。
首先将组好的蜡件放到浆料桶中,沾上浆料,然后取出,把蜡件放到砂子中,这样蜡件表面就会沾上一层砂子。
晾干。
待这一层干燥后,继续这样的程序,一般五至六层即可。
最后一层只沾浆料,不沾砂子第七步,脱蜡。
在制壳时,蜡件表面不是完全被砂子包住,而是在水口顶露出一部分,这时把蜡件放到设备中,加热,把蜡熔化,流出。
第八步,浇注。
浇注时需要把壳预热一下。
第九步,振壳/view/f19a40cf050876323112122b.html熔模铸造:/view/8b40812c7375a417866f8f72.html/content/10/0322/17/852653_19811005.shtml失蜡法是金属铸造的一种方法。
用蜡制成铸模,外敷造型材料,成为整体铸型。
加热铸模将蜡化去,形成空腔铸范,浇入液态金属,冷却后得到成型铸件。
古代多用于铸造具有复杂形状的铸件。
中国已知最早的失蜡铸件是河南淅川出土的春秋晚期铜盏部件和铜禁。
战国以后,失蜡法的应用范围逐渐扩大,除鼎、彝外,还用于铸造印玺、乐钟、佛像和少数民族地区的贮贝器、饰件等。
现代,失蜡法仍用于铸造金属铸件,称熔模铸造。
脱蜡法是一种铸造方法,中国古代在青铜铸造上已经使用这种方法,现代的精密铸造中称为熔模精密铸造。
脱蜡法是先用蜡制造模,应用到翻沙上,就是将蜡制的样品埋入铸造的沙型中,夯实,然后加热,使沙型变得结实,蜡融化倒出,再将熔化的青铜或铁水倒入。
一般翻砂是用木模或原型,得将砂型做成两半,再合在一起,模具必须可以从半个砂型中取出。
而脱蜡法不必取出模具,因此可以铸造形状非常复杂的物品。
教你了解“失蜡铸造法”

教你了解“失蜡铸造法”在距今5000多年前的新石器时代晚期,我国古代工匠就在青铜器的制造中广泛采用了失蜡铸造工艺。
当时的工匠根据蜂蜡的可塑性和热挥发性的特点,首先将蜂蜡雕刻成需要形状的蜡模,再在蜡模外包裹黏土并预留一个小洞,晾干后焙烧,使蜡模气化挥发,同时黏土则成为陶瓷壳体,壳体内壁留下了蜡模的阴模。
这时再将熔化的金属沿小孔注入壳体,冷却后打破壳体,即获得所需的金属铸坯。
现代失蜡铸造技术的基本原理并无二致,只不过更加复杂精密。
这主要体现在对蜡模的型位精确的要求更加严格。
现代工艺中蜡模的获得不只是对蜡的直接雕刻,还可以通过对金属原模(版)的硅胶模压得到阴模,再由硅胶阴模注蜡后得到蜡模。
浇铸材料也不再是黏土,而代以铸造石膏。
这样的产品比古代的铸件精细得多。
失蜡浇铸的工序流程是:压制胶模→开胶模→注蜡(模)→修整蜡模→种蜡树→灌石膏筒→石膏抽真空→石膏自然凝固→烘焙石膏→熔金、浇铸→炸石膏→冲洗、酸洗、清洗→剪毛坯。
下面分别讲述各个工序。
一、压制胶模制作胶模使用的胶是两面带沾胶的生橡胶片。
一般使用进口胶片,以Castaldo牌为多。
其中一种价格相对低一些,由于所含天然橡胶的成分较少,硫化后的硬度稍大,但压模时间较短,适合于经验比较丰富的开模师进行操作;另一种价格稍高,所含天然橡胶的充分较多,质地柔软,韧性十足,适合于花型较为复杂、轮廓尺寸细小、凸凹明显的银版压模,在取出蜡模时不易折断蜡模。
生胶片的保存必须注意控制其存放温度,在20℃以下一般可保存一年,在0~5℃保存时间可达到2~3年。
另外,也有一种预先制成一系列大小和厚度的橡胶模,其内壁有凸凹的连接脚,使用比较方便。
压制胶模的设备是(硫化)压模机,其主要部件由两块内带电阻丝和感温器件的加热板、定温器、定时器(有些型号没有此装置)等组成。
压模机上面还配有升降丝杠,用于压模及取出。
配套使用的还有压模框,根据其开孔的数量可以分为单板、双板、四板等型号,制造压模框的材料通常是铝合金。
失蜡法铸造古币流程

失蜡法铸造古币流程以下是更口语化的失蜡法铸造古币流程:1. 制作模种古代做法:用硬石头或金属雕出古币正反两面的模样,这就是母模,得雕刻得精细,因为后面造出来的古币就靠它了。
现代做法:可能会用电脑设计软件画出古币的样子,然后用3D打印机“打印”出超精确的母模。
2. 翻制蜡型古代做法:把母模加热,让它表面裹一层薄薄的蜡,蜡冷却变硬后剥下来,就得到了蜡做的正反面模具。
现代做法:如果用的是3D打印的母模,那就直接用3D打印机用蜡或者含蜡的材料打印出完整的古币蜡模。
3. 组装蜡模把正面和反面的蜡模对在一起,中间插根蜡棒当“浇铸通道”,再用蜡或者低熔点的合金把它们焊结实,就成了完整的古币蜡模。
4. 制作型壳古代做法:拿细腻的耐火泥浆(比如加了细沙的粘土)或草拌泥抹在蜡模外面,晾干后再抹几遍,每一层之间撒点细砂,这样型壳更结实、透气。
现代做法:用更精细的耐火材料,用机器把蜡模浸到含有水玻璃(硅酸钠)的水里,然后挂上5-9层耐火材料,做出超级结实、密实的型壳。
5. 脱蜡把包着型壳的蜡模放到热水或蒸汽里加热,让里面的蜡模全化成蜡水流出去,型壳里就空了。
6. 烘烤型壳把空的型壳放到火里烤一烤,让型壳变硬、去掉残余的蜡,还能抵抗高温铜水的冲击。
7. 倒铜水把熔化的铜合金(铜、铅、锌、锡这些金属混一起)倒进已经热乎乎的型腔里,等铜水凉下来,就形成了古币的金属坯。
8. 打磨与后期处理冷却后,敲掉或用药水洗掉外面的型壳,取出刚铸好的古币半成品。
磨一磨,把不平的地方磨平,把浇铸口多余的部分磨掉,让古币的图案、字都清楚饱满。
洗一洗,抛个光,让古币闪闪亮。
如果要做成老古董的样子,还可以做做旧处理,模仿古币那种氧化的颜色和磨损的痕迹。
9. 鉴定与入库检查新造的古币,看图案、字迹清不清楚,大小、重量对不对。
通过质检的古币,就分类、数一数,打包好,存到仓库里,等着卖或者展览。
总的来说,失蜡法造古币就是把古代的手艺和现代的技术结合起来,一步步精心制作,最后打造出既有历史感又精美无比的古币。
- 1、下载文档前请自行甄别文档内容的完整性,平台不提供额外的编辑、内容补充、找答案等附加服务。
- 2、"仅部分预览"的文档,不可在线预览部分如存在完整性等问题,可反馈申请退款(可完整预览的文档不适用该条件!)。
- 3、如文档侵犯您的权益,请联系客服反馈,我们会尽快为您处理(人工客服工作时间:9:00-18:30)。
由底座14,右半 型1,左半型3, 和盖板8四块组成 内腔由型芯2形成。
手工压蜡的压型结构图
1.4 易熔模制造
易熔模简称熔模,熔模的质量影响铸件的尺 寸精度及表面粗糙度,易熔模制造工艺流程 如图所示。
压型准备
原材料 定 量
热机械混 合均匀化
4.强度 为保证生产过程中不损坏,熔模需要有一定强 度,模料强度多以抗弯强度表示,一般模料抗 弯强度应不低于2.0MPa,最好为5.0~8.0MPa。 5.硬度 为保持熔模表面质量,模料应有足够的硬度, 以防表面损伤。模料硬度常以针入度表示,常 为4~6度(1度=10-1mm)
6.粘度和流动性 为便于脱模和模料回收,模料粘度不能太 大,在90℃附近的粘度应为3×10-3~3×102Pa.S 。为得到清晰的熔模,模料应具有良 好的流动性。
一、铸件结构的合理性 铸件结构是否合理,对于铸件质量、生产工 艺的可行性和简易性以及生产成本等影响很大, 根据生产实际,总结出铸件结构合理性的几条 基本原则。
1).易于从压型中取模
合理
不合理
合理
不合理
2).易于抽芯
合理
不合理
合理
不合理
3).壁厚均匀,减少热节
合理
不合理
4).避免大平面
合理
3.铸造斜度
为了便于取模,抽芯,在拔模面应设有铸造 斜度,铸造斜度的取值如下。 熔模铸件的铸造斜度
铸造斜度面高 h/mm 非加工面斜度 外表面 内表面
≤20 取值 >20-50 >50-100
>100
0º 20´ 0º 15´ 0º 10´
0º 10´
1º 0º 30´ 0º 30´
0º 15´
4.最小铸出孔
1.最小壁厚 由于熔模铸造的型壳内表面光洁,并且一般 为热型壳浇注,因此熔模铸件壁厚允许设计 得较薄,最小壁厚与合金种类及铸件轮廓尺 寸有关。
熔模铸件的最小壁厚(单位:mm)
铸 件 轮 廓 尺 寸 铸件 材料 >10~50 >50~100 >100~200 铸 件 最 小 壁 厚 推荐值 最 小 值 0.7 推荐值 最 小 值 1.0 推荐值 最 小 值 1.5 推荐值 最 小 值 2.0 推荐值 最 小 值 2.5 >200~500 >350
浇注成 料锭
料锭 破碎
重熔 模料
模料 压注
模组检 验标号
模组 组焊
蜡模及浇注 系统除油
蜡模 修补
蜡模 检验
蜡模 校型
1.4.1 模料 一、对模料的基本要求 概括为工作性能要求和工艺性能要求
1.熔化温度和凝固温度区间 兼顾模料耐热性要求并考虑到工艺操作方便, 熔化温度常选在50~80℃之间,凝固温度区间 以5~10℃为宜。
1.2.2 熔模铸造浇注系统设计
一、浇注系统作用 1.把液体金属引入型腔 注意充型平稳,避免金属液氧化和卷入气体, 保证不产生冷隔和浇不足缺陷。 2.补充液体金属凝固时体积收缩 浇注系统应能保证补缩时通道畅通,并保证 能提供给铸件必要的补缩金属液,避免铸件 产生缩孔、疏松。
3.在组焊与制壳时起支撑易熔模和型壳作 用。要求有足够强度,防止制壳过程中易熔 模脱落。
2.0
2.0 2.5 2.5
3.0~4.0
3.0~4.5 3.0~5.0 3.5~5.0
2.5
2.5 3.0 3.0
3.5~5.0
4.0~5.0 4.0~6.0 4.0~6.0
3.0
3.5 3.5 3.5
铝合金
碳钢 高温合金
2.0~2.5
2.0~2.5 0.9~2.0
1.5
1.5 0.6
2.5~4.0
不合理
5).减少不通孔
合理
不合理
6).简化压型加工
合理
不合理
7).设计必要的工艺筋
A).防止环形件、框型件变形设计的工艺筋
B).防止铸件开口部位变形而设计的工艺筋
C).减少大平面,防止壳形变形
8).设计必要的工艺孔
A).防止大平面型壳变形设计工艺孔
B).减少热节、防止缩孔设计工艺孔
二.铸件结构要素及工艺参数选定
此法依据铸件上热节圆直径或热节圆截面积,由下式确定 内浇道直径或内浇道截面积。 D内=(0.6~1.0)D节 S内=(0.4~0.9)S节 式中: D内—内浇道直径,mm D节—铸件上热节圆直径,mm S内—内浇道截面积,mm2 S节—铸件上热节圆截面积,mm2 这种方法简单,但精度差,因为比例系数取值范围较大。
常用压型类型
类型
机械加工压型
特 点
1.材料通常为钢,也有使用铜合金、铝合金 2.尺寸精度可以充分满足设计要求,型腔表面粗糙度 Ra=1.6~0.4цm 3.使用寿命可达10万次以上 4.制造成本高 1.材料:低熔点合金(通常熔点不超过300℃) 2.尺寸精度比机械加工压型低,型腔表面粗糙度 Ra=3.2~0.8цm 3.使用寿命可达几千次以上 4.制造成本较低 1.材料:石膏 2.尺寸精度低,型腔表面粗糙度Ra=6.3~1.6цm 3.母模可用木模,生产周期短,成本低
铅锡合金
1.0~1.5
1.5~2.0
2.0~3.0
2.5~3.5
3.0~4.0
锌合金
铸铁 铜合金 镁合金
1.5~2.0
1.5~2.0 2.0~2.5 2.0~2.5
1.0
1.0 1.5 1.5
2.0~3.0
2.0~3.5 2.5~4.0 2.5~4.0
1.5
1.5 2.0 2.0
2.5~3.5
2.5~4.0 3.0~4.0 3.0~4.0
2.耐热性 模料耐热性是指温度升高时其抗软化变形的能 力,它影响着熔模和铸件的精度。通常用热变 形量来表示,要求35℃温度时模量热变形量 △H35-2≤2mm。
3.收缩率 模料热胀冷缩小,才能提高熔模尺寸精度,也 才能减少脱腊时因模料膨胀引起的型壳胀裂现 象。因此模料的线收缩率是模料重要的性能指 标之一,一般应小于1%。优质模料线收缩率仅 为0.3%~0.5%。
4.在熔化易熔模时,起液体模料流出的通 道作用,浇注系统应能保证排除模料通畅。
二、浇注系统结构
按浇注系统组成分为: 1)直浇道一内浇道结构形式: 直浇道兼起冒口作用,操作方便,但排渣不利。
2)横浇道一内浇道结构形式: 常用于顶注,有利于顺序凝固。
3)直浇道一横浇道一内浇道结构形式
按合金液注入铸件部位分为: 1)顶注式: 合金液从型腔的顶部注入,铸件自下而上凝固, 合金液易飞溅,排气不畅,适用于高度较低的 铸件。
最小铸出孔的孔径与深度(单位:mm)
孔的直径 3-5 >5~10 >10~20 >20~40 >40~60 >60~100 >100 最大孔深 通孔 5~10 >10~30 >30~60 >60~120 >120~200 >200~300 >300~350 不通孔 ≈5 >5~15 >15~25 >25~50 >50~80 >80~100 >100~120
应用范围
1.生产批量大的铸件 2.要求尺寸精度高、表面粗糙度 值低的铸件
低熔点合金铸造 压型
1.生产批量较大(几千件)的铸 件 2.机械加工困难的、型腔复杂的 压型 3.试生产铸件 1.单件小批生产 2.精度要求较低铸件 3.试生产铸件
石膏压型
硅橡胶压型
1.材料:硅橡胶 2.填充性好,复制性强、周期短 3.精度低,抗拉强度低、寿命短 4.质地较软,使用时外形需要硬质材料衬托
2)侧注式: 合金液从型腔侧面注入,铸件补缩好,应用 较广泛。
3)底注式: 合金液型腔底部平稳注入,不易产生夹渣。气 孔。不利于顺序凝固,需增设冒口。
三、浇注系统计算
步骤: 1)确定浇注系统形式:
封闭式或开放式。
2)计算内浇道尺寸。 3)根据浇注系统形式, 计算直浇道、横浇道 的尺寸。
1)浇注系统形式的确定 封闭式或开放式浇注系统是按照直浇道、 横浇道、内浇道的尺寸比例划分的。 封闭式浇注系统
3)、合金材料不受限制. 钢铁、铜、铝、钛、 镁等。熔点高的镍基高温合金;锌、锡等低熔 点金属。
4)、熔模铸造存在一定局限性。工艺流程 烦琐,生产周期长、铸件尺寸不宜太大。
熔模铸造典型产品应用实例
1.2 熔模铸件工艺设计
1.2.1 铸件结构设计
目的就是对于一些零件图做必要修改,得到适 合熔模铸造特点的最合理的铸件结构。
1.3
压型种类及制造方法
1.3.1 压型的种类
压型:用来制造易熔模的模具。
压型腔的尺寸精度、表面粗糙度和 压型结构,直接影响易熔模的生产 效率和压型制造成本。
按压型材料分为: 金属压型和非金属压型。 金属压型又分为: 钢模,铝合金模,易熔合金模压型; 非金属压型分为石膏压型,硅橡胶压型, 环氧树脂压型等。 各种压型的特点及应用范围如表所示。
组装模组
型壳制造、 脱蜡、焙烧
填砂、浇注
观看 影片
熔模铸造的特点
1)、铸件尺寸精度高(CT4-CT7);表面 粗糙度低(Ra1.6-6.3μm)。减少了铸件的 切削加工余量,甚至可实现近净型铸造。
2)、能生产形状复杂的薄壁铸件。如前机 匣(由内、外环和14件叶片组成)。如发动 机叶片,叶型的最小壁厚可达0.7mm。
5.加工余量
熔模铸件单面加工余量(单位 mm)
≤50 铸件最大尺寸 单面加工余量 浇口面加工余量 0.5 0.5~0.1 1.0~1.5 2.0~4.0 1.5~2.0 2.0~3.0 >50 ~120 >120 ~250 >250 ~400 >400 ~630
6.线收缩率
影响熔模铸件尺寸的收缩因素包括合金 的收缩;模料的收缩;型壳的膨胀等, 这几方面综合的影响称为熔模铸件的综 合线收缩率。