聚合反应实施方法1
3.聚合实施方法1
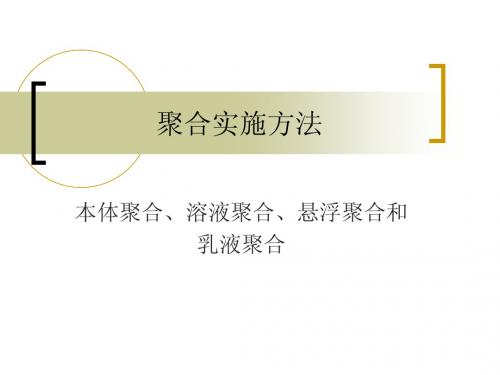
产品特性:分子量高达百万
高压聚乙烯—连续气相本体聚合
压力150~200MPa,温度180~200 ˚C,以 微量(10-6~10-4)氧为引发剂 一般在管式反应器中进行,停留时间只有几 分钟,单程转化率约15%~30% 产品特性:由于高温聚合因此有大量链转移 反应,造成主链上有大量的支链,密度 (0.91-0.93g/cm3)、结晶度(55-65%)、熔点 (105-110 ˚C)都较低。称作低密度聚乙烯 (LDPE),适合制造薄膜。
连续均相溶液聚合:以51-52%的硫氰化钠
(NaSCN)水溶液为溶剂,AIBN为引发剂,pH5±0.2, 温度75~85 ˚C,转化率70~75%。进料单体浓度 17%,出料聚合物浓度13%,脱除单体后直接用于纺 制腈纶纤维。
连续沉淀聚合:以水为溶剂,过硫酸盐类氧化
还原引发体系,温度40~50 ˚C,转化率80%。聚合 产物从反应体系中沉淀出来,经洗涤、分离、干燥后 重新配制成纺丝溶液用于腈纶纺丝。
聚合实施方法
本体聚合、溶液聚合、悬浮聚合和 乳液聚合
定义
本体聚合(Bulk Polymerization):在单体本身中加入少量引 发剂(甚至不加)进行的聚合反应。 溶液聚合(Solution Polymerization):将单体和引发剂溶解在 适当的溶剂中进行的聚合反应。 悬浮聚合(Suspension Polymerization):一般是将单体液滴 悬浮在水中进行的聚合,体系主要由水、单体、油溶性引发 剂、分散剂组成。也有将水性单体悬浮于油性溶剂中进行的 聚合,称反相悬浮聚合。 乳液聚合(Emulsion Polymerization):将单体在水中分散成 乳液状进行的聚合反应,体系由单体、水、水溶性引发剂、 水溶性乳化剂组成。
聚合实施方法

聚合实施方法第四章聚合实施方法4.1.本体聚合一.定义:不加其它介质,只有单体本身在印发剂、光、热辐射的作用下进行的聚合。
二.配方组成:单体+引发剂(或用光、热辐射引发)+(助剂,如少量颜料、增塑剂、润滑剂、分子量调节剂)三.分类:1.根据单体和聚合体的互溶情况分为均相和非均相两种。
均相本体聚合,是指聚合物溶于单体,在聚合过程中物料逐渐变稠,始终成为均一相态,最后变成硬块。
St、MMA的本体聚合就属均相本体聚合。
非均相本体聚合是单体聚合后新生成的聚合物不溶于单体中,从而沉淀下来成为异相,即非均相氯乙烯的本体聚合。
2.按参加反应的单体的相态分为气相和液相两种。
气相本体聚合最为成熟的是高压聚乙烯的生产。
典型的液相本体聚合有St、MMA 的本体聚合。
四.优缺点1.优点:生产流程短、设备少,易于连续化、生产能力大、产品纯度高、透明性好,此法适用于生产板材或其它型材。
2.缺点:①反应热大,不易排出,危险性大②由于反应体系粘度大,分子扩散困难,所以形成的聚合物分子量分布变宽。
五.聚合机理:遵循自由基聚合一般机理,提高反应速率时,往往分子量降低。
六.意义理论上:由于其组成简单、影响因素少,特别适用于实验室研究。
如:a.单体聚合能力的初步鉴定b.动力学研究c.竞聚率测定d.少量聚合物的试制实际生产上:许多单体均可采用本体聚合方法,不论是气体、液体或固体。
七.生产工艺特征关键是反应热的排出,△H=55~95KJ∕mol20%以下,体系粘度小,散热无困难30%以上,粘度大,散热不易,加上凝胶效应,放热更高,如果散热不良,轻者,造成局部过热,分子量分布变宽,影响产品质量;重者,温度失调,引起短聚,为解决此问题,在工艺和设备的设计上采取了多种措施:〈1〉使反应进行到一定转化率就分离出聚合物。
〈2〉采用较低的反应温度、较低浓度的引发剂进行聚合。
〈3〉将聚合分布进行,控制转化率“自动加速效应”,使放热均匀。
〈4〉强化聚合设备的传热。
聚合反应实施方法
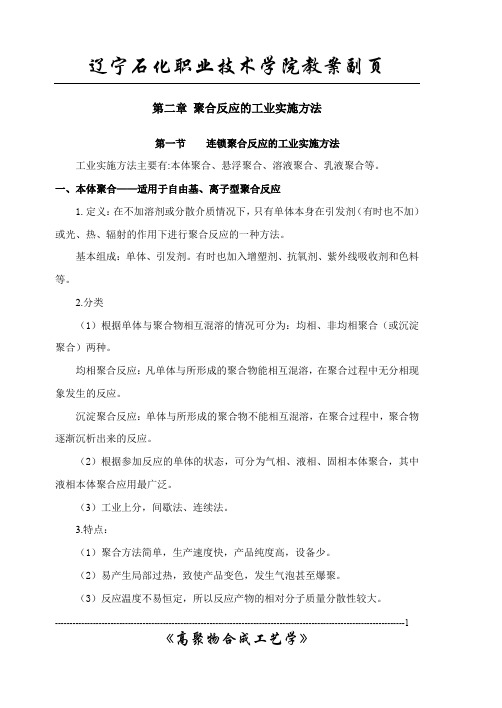
第二章聚合反应的工业实施方法第一节连锁聚合反应的工业实施方法工业实施方法主要有:本体聚合、悬浮聚合、溶液聚合、乳液聚合等。
一、本体聚合——适用于自由基、离子型聚合反应1.定义:在不加溶剂或分散介质情况下,只有单体本身在引发剂(有时也不加)或光、热、辐射的作用下进行聚合反应的一种方法。
基本组成:单体、引发剂。
有时也加入增塑剂、抗氧剂、紫外线吸收剂和色料等。
2.分类(1)根据单体与聚合物相互混溶的情况可分为:均相、非均相聚合(或沉淀聚合)两种。
均相聚合反应:凡单体与所形成的聚合物能相互混溶,在聚合过程中无分相现象发生的反应。
沉淀聚合反应:单体与所形成的聚合物不能相互混溶,在聚合过程中,聚合物逐渐沉析出来的反应。
(2)根据参加反应的单体的状态,可分为气相、液相、固相本体聚合,其中液相本体聚合应用最广泛。
(3)工业上分,间歇法、连续法。
3.特点:(1)聚合方法简单,生产速度快,产品纯度高,设备少。
(2)易产生局部过热,致使产品变色,发生气泡甚至爆聚。
(3)反应温度不易恒定,所以反应产物的相对分子质量分散性较大。
------------------------------------------------------------------------------------------------------------------------1《高聚物合成工艺学》(4)产品容易老化。
4.主要产品:PS树脂、PMMA树脂、PE树脂、PVC树脂等。
5.主要影响因素:(1)单体的聚合热会放出大量的热量,如何排除是生产中的第一个关键问题。
工业生产中:一般采用两段式聚合第一段在较大的聚合釜中进行,控制10%~40%以下转化率;第二段进行薄层(如板状)聚合或以较慢的速度进行。
(2)聚合产物的出料是本体聚合的第二个问题,控制不好不但会影响产品的质量,还会造成生产事故。
解决办法:根据产品特性,选出料方式浇铸脱模制板材或型材,熔融体挤出造粒,粉状出料。
二 聚合反应实施方法

3本体聚合的ຫໍສະໝຸດ 点:A 产品杂质少、纯度高、透明性好,尤其适于制板材、型材等透明制品。 B 自由基,离子聚合都可选用本体聚合。早期丁钠橡胶的合成属阴离子本 体聚合。在络合引发剂作用下,丙烯可进行液相本体聚合。 C 气态、液态及固态单体均可进行本体聚合,其中液态单体的本体聚合最 为重要。
D 本体聚合适于实验室研究。例如单体聚合能力的鉴定,聚合物的试制、 动力学研究及共聚竞聚率的测定等。
8
3 悬浮聚合
溶解有引发剂的单体在强烈搅拌下,以小液滴状态悬浮分散于 水中进行聚合; 单体液滴在聚合过程中逐渐转化为聚合物固体粒子; 单体与聚合物共存时,聚合物一单体粒子有粘性,为了防止粒 子相互粘结,体系中常加有分散剂,使粒子表面形成保护膜; 悬浮聚合体系一般由单体、油溶性引发剂、水及分散剂四个基 本组分组成。
20
引发剂在水相中产生自由基,扩散进入单体液滴的几率比进入胶束的几率 要小得多。实验证实,单体液滴中形成的聚合物量极少 (~1%),说明单 体液滴不是主要聚合场所。 聚合发生在胶束内。 高得多的比表面积,有利于捕捉自由基, 胶束内单体浓度较高(相当于本体单体浓度), 是油溶性有机单体和水溶性引发剂相遇的场所,
此时体系中含有三种粒子:单体液滴、发生聚合的胶束----成聚合物乳胶粒, 及未发生聚合的胶束。
随聚合的进行,水相单体进入胶束,单体液滴中的单体又重复溶解到水中。
21
各种聚合方法的比较
23
24
2
1 本体聚合
无介质,只有单体本身
在引发剂或光、热、辐射能等作用下聚合。 有时可能加入少量颜料、增塑剂、润滑剂、分子量调节剂等助剂。
按聚合物能否溶解于单体
均相聚合,苯乙烯、甲基丙烯酸甲酯、乙酸乙烯酯等的聚合物能溶于 各自单体中;
聚合反应的实施方法

聚合反应的实施方法以下是 6 条关于聚合反应实施方法的内容:1. 嘿,你知道吗,温度可是聚合反应的关键一环啊!就好比烤蛋糕,温度不对,那蛋糕可就不松软好吃啦!比如说在自由基聚合反应里,控制好合适的温度能让反应顺顺利利进行。
要是温度太高,那不就跟火上浇油似的,反应可能失控哦!而温度太低,反应又会慢吞吞的,急死人啦!所以,可得好好把握这个温度呀!2. 自由基引发剂这玩意儿可重要啦!就像一场比赛中的发令枪响一样。
比如在某些聚合反应中,没有合适的引发剂,那反应就很难启动起来呀!这就好比汽车没有钥匙,怎么发动呀?有了好的引发剂,才能让聚合反应迅速起跑,一路向前冲呢!这可不是开玩笑的哟!3. 单体的纯度啊,那可太重要咯!你想想,如果单体里面有杂质,那不就像米饭里有沙子一样咯牙嘛!例如在做聚合反应时,单体不纯可能导致反应乱七八糟的,结果一塌糊涂呀!所以,在进行聚合反应之前,一定要确保单体纯净纯净再纯净呀,这可不能马虎哟!4. 反应时间也得拿捏好呀!你看哈,时间太短,反应可能还没完成,那多可惜呀!这不就跟跑步比赛还没到终点就停下一样嘛。
但要是时间太长呢,又浪费时间和精力啦!就像煮汤,时间太久汤都煮干咯!所以呀,要找到那个刚刚好的反应时间,才能收获完美的聚合反应结果哟!5. 搅拌也别小瞧呀!这就好像给反应来个大保健一样。
没有适当的搅拌,反应物们都不能好好混合呀,那不就跟一群人各玩各的没啥交流一样嘛。
比如在一些聚合反应中,好好搅拌能让反应更均匀,效果更好嘞!可别小看这一搅拌哦!6. 环境也很关键呐!这就好比鱼需要干净的水才能快活地游。
要是聚合反应的环境不合适,那反应也会受影响呀!比如湿度太大或者有杂质啥的,那可得小心咯!所以啊,给聚合反应创造一个舒适的环境真是太重要啦!我觉得啊,聚合反应的实施方法真的是每一个细节都不能马虎,都得认真对待,这样才能得到。
聚合反应工业实施方法—乳液聚合过程及其机理
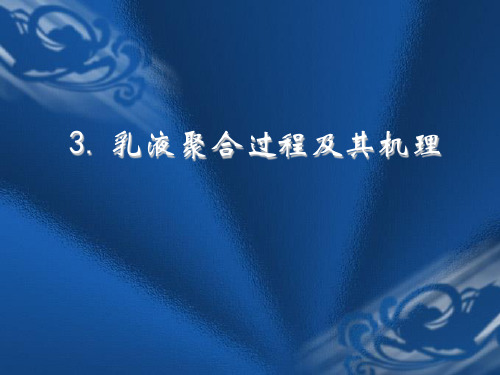
球状 ( 低浓度时 ) 直径 40 ~ 50Å
棒状 ( 高浓度时 )
直径约为乳化剂分子的两 倍,长度为 100 ~ 300 nm
胶束的大小和数目取决于乳化剂的用量,乳化剂 用量多,胶束的粒子小,数目多
(3)增溶胶束
当体系中存在油性组分时,油溶性分子由于热力学稳定的 趋向会进入胶束内部,从而使油性物质在水中的溶解度增加。 因此,胶束对于油溶性单体具有增溶作用。
当乳化剂分子分散到水中时,亲水基受到水的亲和力而亲油 基受到排斥力,以致乳化剂分子倾向于聚集在空气-水的界面 上,由于部分空气-水的界面变成了空气-油的界面,因此,原 有体系的界面张力就会因油的表面张力小而下降
CMC
界 面 张 力
乳化剂浓度 水 - 空 气 界 面 水面被乳化剂分子 上的乳化剂的 全部占据,达到饱 量越来越多 和
死
••••••
在整个乳液聚合过程中,死乳胶粒和活乳胶粒不断相互转化 。正是在这种连续不断的转化中,乳胶粒不断长大,单体转化 率不断提高
阶段I的特征
乳胶粒数目不断增加
阶段I结束的标志
胶束耗尽
影响阶段I长短的因素
乳化剂的特性和用量 引发剂的特性和用量 聚合温度
(3)阶段II(乳胶粒长大阶段)
在阶段I的终点,胶束全部消失,所以,阶段II中靠胶束成核机 理生成乳胶粒的过程已不存在,不再有新的乳胶粒生成
单体液滴
单体液滴
I
R•
I
R•
阶段II中,乳胶粒的数目将保持一个定值
自由基的扩散
一般而言乳胶粒的浓度可达1016cm-3,其数目要比单体液滴 的数目大得多(约一万倍),水相中继续分解出的自由基依然主 要向乳胶粒中扩散,并进而引发聚合使乳胶粒不断长大
高分子化学第五章_聚合方法

1
聚合物生产实施的方法,称为聚合方法。
气相聚合
在单体沸点以上聚合
单体形态
固相聚合
在单体熔点以下聚合
聚合物—单体不溶
沉淀聚合 均相聚合
聚合物—单体互溶
非均相聚合
溶解性
聚合物—单体部分互溶
2
本体聚合
悬浮聚合
物料起始状态
乳液聚合
溶液聚合
5.1 引言
自由基聚合有四种基本的实施方法。 • 本体聚合: 不加任何其它介质, 仅是单体在引发剂(甚至不 加)、热、光或辐射源作用下引发的聚合反应。 • 溶液聚合: 单体和引发剂溶于适当溶剂中进行的聚合反应。
溶剂对聚合度的溶解性能与凝胶效应有关 良溶剂,为均相聚合,[M]不高时,可消除凝胶效应 沉淀剂,凝胶效应显著,Rp 劣溶剂,介于两者之间
20
4、应用实例
多用于自由基聚合、离子聚合、配位聚合、逐步聚合等。
表4
单体
溶液聚合工业生产实例
溶剂 硫氰化钠 水溶液 水 甲醇 聚合机理 自由基聚合 自由基聚合 自由基聚合 产物特点与用途 纺丝液 配制纺丝液 制备聚乙烯醇、 维尼纶的原料
聚合物—单体—溶剂体系 均相聚合 乙烯高压聚合、苯乙烯、丙 烯酸酯 苯乙烯—苯、丙烯酸—水、 丙烯腈—二甲基甲酰胺 苯乙烯、甲基丙烯酸甲酯 苯乙烯、丁二烯、丙烯酸酯 沉淀聚合 氯乙烯、丙烯腈、丙 烯酰胺 氯乙烯—甲醇、丙烯 酸—己烷、丙烯腈— 水 氯乙烯 氯乙烯
均相体系
非均相体系
6
如何选择聚合方法: 根据产品性能的要求与经济效益,选用一种或几种方
PMMA为非晶体聚合物,Tg=105 ℃,机械性能、耐 光耐候性均十分优异,透光性达90%以上,俗称“有机 玻璃”。广泛用作航空玻璃、光导纤维、标牌、指示灯 罩、仪表牌、牙托粉等。
聚合反应工业实施方法—新的非均相体系聚合法

••••••
4.1 无皂乳液聚合
无皂乳液聚合是指在反应过程中完全不加乳化 剂或仅加入微量乳化剂(其浓度小于临界胶束浓度 CMC)的乳液聚合过程
乳化剂是乳液聚合成核和乳液体系稳定的关键
无乳化剂 乳液聚合何以成核? 乳液体系何以稳定?
聚合后:非均相体系
聚合物不溶 于该介质
分散剂
常用的稳定剂有聚乙 烯基吡咯烷酮、羟丙 基纤维素、聚丙烯 酸、聚乙二醇和糊精 等 合成和天然高分子
体系稳定
齐聚物沉淀机理
乳液聚合 隔离效应 体积效应 凝胶效应 富集效应
转化率(%)
反应速率较快
100
80
60
CB
A
40
20
0
50
100
反应时间(min)
A. 溶液聚合 B. 沉淀聚合 C. 分散聚合
无皂乳液聚合的成功事例是对经典乳液聚合理论中 胶束成核机理的挑战
均相成核和齐聚物胶束成核
single-chain 析出的成核
水中齐聚物的生成
multi-chain 析出的成核
临界链长时析出
饱和浓度时析出
分子链 的链长
因稳定而聚集
初步粒子
成长 继 稳续定成粒长子
齐聚物 链的数
最终粒子
与短链的溶解 性密切相关
4. 新的非均相体系聚合法
聚合物乳液
除水后或直接使用
涂料 油漆 粘合剂 油墨 橡胶
乳液聚合物以乳液的形式在传统的涂料、胶粘剂等 方面得到广泛的应用的同时,其聚合产物经处理而可制 得各种功能型复合高分子微粒子,并以其多样的粒子形 态和精细的复合结构在高科技新材料等众多领域具有广 阔的应用前景。
- 1、下载文档前请自行甄别文档内容的完整性,平台不提供额外的编辑、内容补充、找答案等附加服务。
- 2、"仅部分预览"的文档,不可在线预览部分如存在完整性等问题,可反馈申请退款(可完整预览的文档不适用该条件!)。
- 3、如文档侵犯您的权益,请联系客服反馈,我们会尽快为您处理(人工客服工作时间:9:00-18:30)。
第二章聚合反应的工业实施方法第一节连锁聚合反应的工业实施方法工业实施方法主要有:本体聚合、悬浮聚合、溶液聚合、乳液聚合等。
一、本体聚合——适用于自由基、离子型聚合反应1.定义:在不加溶剂或分散介质情况下,只有单体本身在引发剂(有时也不加)或光、热、辐射的作用下进行聚合反应的一种方法。
基本组成:单体、引发剂。
有时也加入增塑剂、抗氧剂、紫外线吸收剂和色料等。
2.分类(1)根据单体与聚合物相互混溶的情况可分为:均相、非均相聚合(或沉淀聚合)两种。
均相聚合反应:凡单体与所形成的聚合物能相互混溶,在聚合过程中无分相现象发生的反应。
沉淀聚合反应:单体与所形成的聚合物不能相互混溶,在聚合过程中,聚合物逐渐沉析出来的反应。
(2)根据参加反应的单体的状态,可分为气相、液相、固相本体聚合,其中液相本体聚合应用最广泛。
(3)工业上分,间歇法、连续法。
3.特点:(1)聚合方法简单,生产速度快,产品纯度高,设备少。
(2)易产生局部过热,致使产品变色,发生气泡甚至爆聚。
(3)反应温度不易恒定,所以反应产物的相对分子质量分散性较大。
(4)产品容易老化。
14.主要产品:PS树脂、PMMA树脂、PE树脂、PVC树脂等。
5.主要影响因素:(1)单体的聚合热会放出大量的热量,如何排除是生产中的第一个关键问题。
工业生产中:一般采用两段式聚合第一段在较大的聚合釜中进行,控制10%~40%以下转化率;第二段进行薄层(如板状)聚合或以较慢的速度进行。
(2)聚合产物的出料是本体聚合的第二个问题,控制不好不但会影响产品的质量,还会造成生产事故。
解决办法:根据产品特性,选出料方式浇铸脱模制板材或型材,熔融体挤出造粒,粉状出料。
6.优点;产物纯净,适于生产板材、型材等透明制品,也可生产电绝缘材料和医用材料。
7.应用:实验室研究(如单体聚合能力、动力学研究、竟聚率测定。
二、溶液聚合1.定义:将单体和引发剂溶解于适当溶剂中进行聚合反应的一种方法。
基本组成→单体、引发剂、溶剂2.类型:(1)根据溶剂与单体和聚合物相互混溶的情况分为:均相、非均相溶液聚合(或沉淀聚合)两种。
均相聚合反应:凡溶剂与单体和聚合物能相互混溶,得到的产物为高聚物溶液(此溶液可以直接用作油漆、涂料),将此溶液注入高聚物的非溶剂中,高聚物即可沉析出来,经过过滤、洗涤、干燥得到最终产品。
沉淀聚合:溶剂仅能溶解单体而不能溶解聚合物的,这时所生成的聚合物呈细小的悬浮体不断从溶液中析出,经过滤、洗涤、干燥可得最终产品。
(2)根据聚合机理可分为:自由基溶液聚合、离子型溶液聚合和配位溶液聚合。
3.溶液聚合的特点:(1)原料纯度要求严格。
(2)反应容易控制;(3)聚合物相对分子质量比较均匀;(4)易实现连续化生产。
(5)聚合后,分离、回收、后处理复杂。
4.溶剂对溶液聚合的影响(1)对自由基溶液聚合的影响:对引发剂有无诱导分解反应发生;溶剂对聚合物的溶解能力大小,对凝胶效应的影响常见溶剂:芳烃、烷烃、醇类、醚类、胺类等有机溶剂和水等。
(2)对离子型、配位型溶液聚合的影响:不能选择水、醇、酸等具有氢质子的溶剂,以防止破坏引发剂的活性;考虑对增长离子对紧密程度和活性的影响考虑向溶剂的链转移大小;考虑对引发剂及产物的溶解能力。
选择:烷烃、芳烃、二氧六环、四氢呋喃、二甲基甲酰胺等。
三、悬浮聚合31.定义:将不溶于水的,溶有引发剂的单体,利用强烈的机械搅拌以小液滴的形式,分散在溶有分散剂的水相介质中,完成聚合反应的一种方法。
2.基本组成:单体、水、分散剂(悬浮剂)、引发剂3.聚合场所:每个小液滴内,是一种微型化的本体聚合。
4.用途:聚氯乙烯、聚苯乙烯、离子交换树脂、聚(甲基)丙烯酸酯类、聚醋酸乙烯酯及它们的共聚物等。
5.特点:(1)工业生产技术路线成熟、方法简单、成本低;(2)产品质量稳定、纯度较高;(3)易移出反应热、操作安全、温度容易控制;(4)产物粒径可以控制;(5)只能间歇操作,而不宜连续操作。
6.悬浮聚合的组成基本组成为:单体、引发剂、分散剂和水。
单体(或油)相水相(1)单体相一般:油性单体、引发剂组成,有时也加入其他物质。
1)单体油性单体(非水溶性),必须处于液态。
气态→加压;结晶性→熔融。
2)引发剂一般:根据单体和工艺条件在油溶性的偶氮类和有机氧化物中选择单一型或复合型引发剂。
3)其他组分根据需要,在单体中加入链转移剂、发泡剂、溶胀剂或致孔剂、热稳定剂、紫外光吸收剂等。
(2)水相是影响悬浮聚合成粒机理和颗粒特性的主要因素。
组成→水、分散剂和其他成分。
1)水去离子的软化水。
作用:保持单体呈液滴状,起分散作用;作为传热介质。
2)分散剂作用:降低表面张力,帮助单体分散成液滴;在液滴表面形成保护膜,防止液滴(或粒子)粘并;防止出现结块危险。
类型:非水溶性无机粉末、水溶性高分子①水溶性高分子:一般用量约为单体的0.05%~0.2%分散机理→吸附在单位液滴表面,形成一层保护膜,起保护胶体的作用;同时,使液滴变小。
②非水溶性无机粉未一般用量约为单体的0.1%~0.5%分散机理→起机械隔离的作用。
3)其他组分无机盐、pH值调节剂和防粘釜剂等。
7.单体液滴与聚合物粒子的形成过程(1)单体液滴的形成过程(2)聚合物粒子的形成过程在悬浮聚合过程中搅拌的作用是使单体分散为液滴的必要条件,而分散剂的5作用是防止粘稠液滴之间发生粘合的必要条件,进而确保聚合渡过结块危险期。
1)均相粒子的形成过程分为三个阶段:聚合初期、聚合中期、聚合后期生成的聚合物能溶于自身单体中而使反应液滴保持均相,最终形成均匀、坚硬、透明的固体球粒。
单体液滴聚合初期聚合中期聚合后期透明粒子2)非均相粒子的形成过程一般认为有五个阶段,聚合物不溶解于自己的单体中,有聚合物产生就沉淀出来。
形成由均相变为单体和聚合物组成的非均相体系,产物不透明,外形极为不规则的小粒子。
3)悬浮聚合聚合物粒子形成过程的特点①非均粒子的形成有相变化:液相→液、固两相→固相。
②均相粒子的形成无相变化:聚合过程始终保持为一相。
③由单体转化为聚合物的过程是体积缩小的过程④均相聚合体系危险性比非均相聚合体系危险性大⑤分散剂外膜8.粒径的大小与形态取决于搅拌强度、分散剂性质和浓度、水-单体、聚合温度、引发剂种类和用量、聚合速率、单体种类、其他添加剂等。
四、乳液聚合1.定义:在用水或其他液体作介质的乳液中,按胶束机理或低聚物机理生成彼此孤立乳胶粒,在其中进行自由基聚合或离子聚合来生产高聚物的一种方法。
体系组成:单体、水、乳化剂、水溶性引发剂。
2.乳液聚合的特点(1)反应速度快,聚合物相对分子质量高(独到的)。
(2)易移出反应热(水作导热介质)。
(3)乳化液稳定,利于连续生产。
(4)产物是乳胶,可以直接用作水乳漆、粘合剂。
(5)若最终产品为固体聚合物时,后处理复杂(凝聚、洗涤、脱水、干燥),生产成本高。
6.主要高聚物:丁苯橡胶、丁腈橡胶、糊状聚氯乙烯;聚甲基丙烯酸甲酯、聚醋酸乙烯酯(乳白胶)、聚四氟乙烯等。
(二)乳液聚合体系的组成1.单体→乙烯基单体具备条件:①可以增溶溶解但不是全部溶解于乳化剂水溶液;②可以在发生增溶溶解作用的温度下进行聚合;③与水或乳化剂无任何活化作用,即不水解。
2.水相组成:水、乳化剂、稳定剂、pH调节剂、引发剂等。
(1)水纯净的非离子水。
主要作用:分散介质,用量占乳液聚合体系总质量的60%~80%。
(2)乳化剂→表面活性剂能使油水变成相当稳定难以分层乳状液物质。
①乳化剂的作用:降低表面张力降低界面张力乳化作用→形成稳定乳状液7分散作用→使每个颗粒稳定地分散并悬浮于水中而不凝聚。
增溶作用发泡作用→对生产有不良影响,要加以控制。
②乳化剂的类型阴离子型乳化剂阳离子型乳化剂按照亲水基团的性质可分:非离子型乳化剂两性乳化剂阴离子型乳化剂→使用最多的主要乳化剂,多在碱性介质中使用。
最常见:皂类、十二烷基硫酸钠C12H25SO4Na、烷基磺酸钠、十二烷基苯磺酸盐C12H25C6H4SO3Na等。
阳离子型乳化剂→多在酸性介质中使用,乳液聚合一般较少使用。
常见:胺盐、仲胺盐、叔胺盐和季胺盐类。
非离子型乳化剂→对介质酸碱性不敏感,一般作辅助乳化剂使用常见:聚环氧乙烷类物质。
两性乳化剂→本身带有碱性基团和酸性基团。
常见:羧酸型、硫酸酯型、磷酸酯型、磺酸型等。
③临界胶束浓度,简称CMC临界胶束浓度:能够形成胶束的最低乳化剂浓度,是乳化剂性质的一个特征参数。
CMC的大小主要取决于乳化剂的分子结构及水电解质浓度。
④乳化剂的特点a.分子结构中具有亲水和亲油基团两部分。
b.能降低表面张力,使液滴稳定。
c.具有乳化作用⑤乳化剂的选择a.乳状液的类型:水包油乳液→标志为O/W;油包水乳液→标志为W/O。
b.乳化剂的亲油亲水平衡值(HLB值)c.乳化剂的选择方法根据HLB值进行选择经验法选择一般:先用选择HLB合适的乳化剂,再借鉴实践经验进行确定。
(3)引发剂用量为单体质量的0.1%~1.0%。
(4)稳定剂保护胶体,用以防止乳液的析出和沉淀。
常用:明胶、酪素等,用量: 2%~5%。
(5)表面张力调节剂作用:控制单体粒度大小和保持乳液的稳定性。
用量: 0.1%~0.5%。
(6)缓冲剂(pH值调节剂)pH值大小直接影响乳液体系的稳定性和引发剂分解速度。
常用:磷酸盐、碳酸盐、醋酸盐等,用量: 2%~4%。
(7)相对分子质量调节剂目的:调节产物的相对分子质量,避免支化和交联,提高产品质量和加工性能。
常用:脂肪族硫醇9(三)乳液聚合反应原理分四个阶段:分散阶段、乳胶粒生成阶段、乳胶粒长大阶段和聚合完成阶段。
1.单体分散阶段没加引发剂时的乳液聚合系统。
2.乳胶粒生成阶段该阶段从开始引发聚合,直至胶束消失,聚合速率递增。
3.乳胶粒长大阶段自胶束消失开始,乳胶粒继续增大,直至单体液滴消失,是聚合恒速阶段。
4.聚合完成阶段5.乳液聚合速率与相对分子质量(四)乳液聚合技术的发展1.乳液定向聚合2.辐射乳液聚合3.非水介质中的乳液聚合第二节缩聚反应的工业实施方法工业实施方法主要有:熔融缩聚、固相缩聚、溶液缩聚、界面缩聚、乳液缩聚等。
一、熔融缩聚1.定义:指反应中不加溶剂,反应温度在单体和缩聚物熔融温度以上进行的缩聚反应。
2.特点:(1)反应温度高(一般在200℃以上);(2)利于提高反应速率和排出低分子副产物;(3)符合可逆平衡规律;(4)单体易发生成环反应,缩聚物易发生裂解反应。
3.工艺特点:(1)不用溶剂、工艺过程简单、成本低(聚酯、聚酰胺、聚氨酯)熔融→缩聚→造粒→干燥→成品(2)反应需要在高温(200~300℃)下进行;(3)反应时间较长(4——6小时);(4)常需在惰性气体的保护下进行;(5)反应后期需要在高真空度下进行;(6)反应物的浓度大,生产能力大。
4.关键问题:充分除出低分子副产物。