机械产品英文说明书
机械液压设备产品说明书

Sleeve Bearing Lubrication Mike JohnsonPlain BearingsThere are two broad types of bearings used in machinery today: plain and rolling element bearings. This article targets the special lubrication requirements of plain bearings, also known as sleeve bearings and journal bearings.The plain bearing consists of a shaft, also called a journal, and a supporting component, which may be a shell around the shaft called a sleeve, a half shell that the shaft fits into, two half shells (top and bottom parts) or a multipart shell.See Figure1Plain bearings are used for high radial loads (perpendicular to the axis of the shaft) and low to high speeds. Typical applications include turbines, large milling systems, engine cranks, compressors, gearboxes, shaft bearing supports, etc.Every journal bearing has some common design characteristics as shown inFigure 2.The components that are separated by the oil film in a plain bearing are the bearing liner and the shaft. The shaft is composed of high-quality, wear-resistant, structurally strong steel. The bearing liner may be made of a single layer or multiple layers, depending on the design features of the equipmentLubrication RegimeUnder normal operating conditions, the lubrication regime will be a hydrodynamic full-fluid film. A hydrodynamic film occurs when there is sufficient lubricant between the lubricated surfaces at the point of loading to form a fluid wedge that separates the sliding surfaces. In this state, the lubricated components do not touch each another, reducing friction and wear.This condition is represented by the equation ZN/P, where Z = viscosity, N = speed (rpm) and P = load. This equation is represented by Figure 4.The curve on this graph is called the Stribeck Curve. It is the classical representation of the relationship between speed, load and friction.Mixed film conditions occur when a loss of the film resulting in momentary contact between the two surfaces is apparent. This can occur in response to momentary variations in loading, called shock-loading, that can collapse the film, resulting in physical contact of opposing asperities.Another condition that can occur is boundary film lubrication. This is when the film that separates the surfaces undergoes significant loss resulting in a high load of metal-to-metal contact. This happens any time the relative motion of component surfaces are slow and no oil film is formed.Lubrication Needs of a Plain BearingOperating under proper speed, surface area, viscosity and oil volume, a plain bearing can support very heavy loads. The balance between these conditions is important. If the load or the speed changes, the lubricant viscosity must be adjusted to compensate for the change. There is no simple formula that is used to calculate the viscosity requirements for oil lubricated plain bearings, but the ZN/P formula demonstrates the results of complex calculations used to arrive at the proper clearance.Criteria to consider once you have identified the proper viscosity grade include oxidation stability, corrosion inhibition, wear protection, water and air separation properties, etc. Because plain bearings can be used in a variety of applications, there is no single set of criteria that should be used. Selection depends on the equipment design and operating conditions.Plain bearings are normally oil lubricated, but may be lubricated with grease for slow-speed equipment, particularly if they are subject to frequent starts and stops or the bearings may be physically difficult to reach.The type and amount of grease depends on continuous replenishment of the body of grease that is held within the dynamic clearances (empty spaces while the bearing is turning) in order to maintain effective lubricant condition and hydrodynamic lift. Equipment with poor sealing characteristics may require a heavier body of lubricant and more frequent replenishment cycles.Under manual (intermittent) relubrication, the volume and the frequency are influenced by operating conditions, grease quality and available time for the task. Grease selection begins with consideration of the oil to be used. Heavy oils are used to formulate greases used to manually lubricate plain bearings in high-duty service.After the proper viscosity oil has been selected, then the soap thickener, oxidation and rust characteristics, worked consistency properties, pumpability (for automatic systems) and load-bearing (EP/AW) properties are considered. For long intervals and very heavy loading, solid additives such as molybdenum disulfide or graphite may be incorporated. The solid additives would serve to mechanically prevent metal contact in mixed film and boundary lubrication conditions.The grease should be pumped into the bearing in front of the load zone and at the location of the grease grooves used for lubricant distribution (Figures 5 and 6).Figure 6Wear and Failure Modes in Plain BearingsThere are several factors that can wipe or damage a plain bearing surface. Abrasive wear is one of the most common. If the wear is caused by a hard particle rubbing between the lubricated surfaces, it is called three-body wear. Wear caused by an asperity on one surface cutting the other surface is called two-body abrasion.Wear can also result from insufficient volume of lubricant (starvation leading to boundary conditions), overheated lubricant (viscosity at operating temperature cannot support the load causing frictional heat and additional oil thinning), rough surfaces (asperities on the journal cause rubbing), imbalance (improper loading of the support element causing shock loading), journal eccentricity (egg-shaped journal causing rubbing on the high spots), and metal fatigue from improper metallurgy. Journal bearing wear can be effectively monitored by oil and ferrographic analysis.See Figure7The telltale indicators that may point to high wear conditions include high metallic particle counts (two levels above norm), darkened metal surfaces, blued metal surfaces and wear metals formed into spirals or platelets. As oils age and become contaminated with moisture or acidic oxidation compounds, we can see evidence of corrosion and metallic oxidation on stationary surfaces in the reservoir.。
达克(Dake)机械工业有限公司产品说明书:达克(Dake)机械工业有限公司型号4M机械杠杆螺纹压机

Dake CorporationPhone: 800.937.3253DAKE RATCHET LEVER ARBOR PRESSModel 4MINSTRUCTIONAL MANUALWARNING!Read and understand all instructions and responsibilities before operating. Failure to follow safety instructions and labels could result in serious injury.TABLE OF CONTENTSDAKE STANDARD LIMITED WARRANTY (2)RETURN & REFUND POLICY (4)DAKE STANDARD TERMS & CONDITIONS OF SALE (5)SPECIFICATIONS (6)SAFETY (6)HANDLE POSITION (7)OPERATION (7)MAINTENANCE (7)LUBRICATION (7)EXPLODED VIEW & PARTS LIST (8)EXPLODED PARTS VIEW (8)PARTS LIST (9)ORDERING INFORMATION (9)DAKE STANDARD LIMITED WARRANTYFinished MachinesDake warrants to the original purchaser the finished machine manufactured or distributed by it to be free from defects in material and workmanship under normal use and service within 1 year (12 months) from the delivery date to the end user.PartsDake warrants to the original purchaser the component part manufactured or distributed by it to be free from defects in material and workmanship under normal use and service within 30 days from the delivery date to the end user. The standard limited warranty includes the replacement of the defective component part at no cost to the end user.Sale of Service (Repairs)Dake warrants to the original purchaser the component part repaired by Dake Corporation at the manufacturing facility to be free from defects in material and workmanship under normal use and service within 90 days from the return date to the end user, as it pertains to the repair work completed. The standard limited warranty includes repair of the defective component part, at no cost to the end user. Warranty ProcessSubject to the conditions hereinafter set forth, the manufacturer will repair or replace any portion of the product that proves defective in materials or workmanship. The manufacturer retains the sole right and option, after inspection, to determine whether to repair or replace defective equipment, parts or components. The manufacturer will assume ownership of any defective parts replaced under this warranty.All requested warranty claims must be communicated to the distributor or representative responsible for the sale. Once communication has been initiated, the Warranty Representative at Dake Customer Service must be contacted for approval:Phone: (800) 937-3253Email: ****************************When contacting Dake, please have the following information readily available: - Model # - Serial # - Sales Order #Purchasers who notify Dake within the warranty period will be issued a Case number and/or a Return Material Authorization (RMA) number. If the item is to be returned per Dake’s request, the RMA number must be clearly written on the exterior packaging. Any item shipped to Dake without an RMA will not be processed.Warranty Exceptions:The following conditions are not applicable to the standard limited warranty:a) Part installation or machine service was not completed by a certified professional, and is not inaccordance with applicable local codes, ordinances and good trade practices.b) Defects or malfunctions resulting from improper installation or failure to operate or maintain theunit in accordance with the printed instructions provided.c) Defects or malfunctions resulting from abuse, accident, neglect or damage outside of prepaidfreight terms.d) Normal maintenance service or preventative maintenance, and the parts used in connection withsuch service.e) Units and parts which have been altered or repaired, other than by the manufacturer specificallyauthorized by the manufacturer.f) Alterations made to the machine that were not previously approved by the manufacturer, or thatare used for purposes other than the original design of the machine.RETURN & REFUND POLICYThank you for purchasing from Dake! If you are not entirely satisfied with your purchase, we are here to help.ReturnsAll Dake manufactured / distributed machines and parts include a 30-day return option. These policies are valid from the date of final shipment to the end user.To be eligible for a return, the item must be unused and in the same condition as received.All requested warranty claims must be communicated to the distributor or representative responsible for the sale. Once communication has been initiated, Dake Customer Service must be contacted for approval by the distributor or representative: Phone: (800) 937-3253 Email:****************************Once the return request has been approved by Customer Service, a representative will supply a Return Material Authorization (RMA) number. The returned item must have the provided RMA number clearly marked on the outside packaging. Any item received without an RMA number clearly visible on the packaging will not be processed. An RMA number can only be provided by the Dake Customer Service team and must be obtained prior to the return shipment.The item must be shipped and received back to Dake within 30 days from being issued the RMA number, or the return will be void and nonreturnable.RefundsOnce the item has been received and inspected for damages, a representative will notify the requestor referencing the provided RMA number.If the return is approved, a refund will be issued to the original method of payment, less a 20% restocking fee. The restocking fee may be waived if an order is placed at the time of return with like-value merchandise.Transportation costs are the responsibility of the end user and will not be credited upon return approval. Any item that is returned after the initial 30 days or has excessive/obvious use will not be considered for a full refund.DAKE STANDARD TERMS & CONDITIONS OF SALE All proposals and quotations for the original sale of our products are subject to the following terms and conditions:ACCEPTANCE OF ORDER: All orders are subject to acceptance by Dake at its main office in Grand Haven, Michigan.APPLICABLE LAWS: This quotation or acceptance shall be governed in all respects by the laws of the State of Michigan.CANCELLATION: We reserve the right to cancel and/or refuse to complete your order if, in our opinion, you have not established credit to promptly meet the payment terms of your order. Any cancellation from the Purchaser may be subject to a 10% cancellation fee for any of our standard machinery and/or component parts upon the discretion of Dake. All non-standard or special quotes will not be eligible for cancellation, nor returns.DELIVERY: The proposed shipment date is an estimate and is contingent upon causes beyond Dake’s control. Under no circumstances shall Dake have any liability for loss of use or for any direct or consequential damages resulting from delay. All shipments from the Dake facilities are F.O.B.FREIGHT CLAIM: Lost or damage freight claims must be submitted to Dake within thirty (30) days of shipment from Dake’s facility. If shipment for order was set up by the Purchaser, Dake is not liable to handle the freight claims.PERMITS AND COMPLIANCE: Dake shall not be responsible for obtaining any permits, inspections, certifications, or licenses required for the installation or use of the equipment. Dake makes no promise or representation that the equipment or any services to be furnished by Dake will conform to any federal, state, or local laws, ordinances, regulations, codes or standards.PRICES: Unless otherwise agreed to in writing, all prices are F.O.B. from our plants in Grand Haven, Michigan, Grand Prairie, Texas, and Riverside, CA. In any event, the quoted prices for component parts become invalid ten (10) days after date of quotation, and machinery may become invalid sixty (60) days after date of quotation. Unless otherwise specified in Dake’s quotation, installation services and final on-site adjustments are not included in the quotation.TAXES: Prices do not include taxes. If any sales, use or similar tax is payable to Dake in connection with any transaction or part thereof between the Purchaser and Dake with respect to goods delivered, the Purchaser will, upon demand, pay to Dake the amount of any such tax. If you are tax exempt, please include your exemption document when submitting your order.TERMS OF PAYMENT: Terms of payment are as stated in Dake’s quotation subject to credit approval by our home office. Dake will invoice Purchaser when the equipment is completed and ready for shipment. Payment terms run from invoice date. Purchaser may be required to issue a down payment before production of order, at the discretion of Dake Accounting. For credit card purchases, a 2% processing fee may be applicable to the order. The following states are exempt from the 2% processing fee: CA, CO, KS, OK, TX, FL, NY, CT, MA, and ME.WARRANTY: If, within a period of one (1) year from date of shipment of the original order, any part of any equipment sold by Dake is defective in material or workmanship and is so found after inspection by Dake, it will be replaced or repaired at the option of Dake, providing the equipment has been given normal and proper usage and is still the property of the original Purchaser. Purchased components such as Micro Drop mist system or the like, installed as a part of Dake equipment are warranted only to the extent of the original Manufacturer’s warranty. Dake is not responsible for any service work performed unless authorized in advance.THE FOREGOING WARRANTY IS EXCLUSIVE AND IN LIEU OF ALL OTHER WARRANTIES WHETHER WRITTEN, ORAL, OR IMPLIED (INCLUDING ANY WARRANTY OF MERCHANTABILITY OR FITNESS FOR PARTICULAR PURPOSE). UNDER NO CIRCUMSTANCES SHALL DAKE BE LIABLE FOR ANY INCIDENTAL OR CONSEQUENTIAL DAMAGES.SPECIFICATIONSModel 4M Largest arbor 5-1/4” Number 902006 Capacity over table 26” Capacity 5 tons Capacity over table plate 24-1/2” Leverage ration 55:1 Base length21-1/2” Ram size2 x 2 x 23” Base width24” Max diameter work 20” Height 58” Throat 10” Weight1045 lbsSAFETYThis is the safety alert symbol. When you see this symbol on your press be alert to the potential for personal injury.Employer is responsible to perform a hazard/PPE assessment before work activity.Follow recommended precautions and safe operating practices. Carefully read all safetymessages in theseinstructions and on yourpress safety signs.Keepsafety labels in goodcondition. Replace missing ordamaged safety labels.This machine is intended tobe operated by one person.This person should beconscious of the press rammovement not only forthemselves but also forpersons in the immediatearea of the machine.Under no circumstancesincrease the leverage ratioof the press by using alonger handle or by placinga pipe over the handle.Never hammer on top of theram.HANDLE POSITIONCAUTION: NEVER PULL THE PRESS HANDLE PAST THE HORIZONTAL POSITION!To avoid personal injury and damaging the press only pull until the handle is horizontal, then return the handle back up as far as it allows before bringing the handle back down. This ensures that the pawl fully engages with the gear teeth to prevent tooth damage and gear slippage that can cause harm to the machine and worker. Examples above show the ideal minimum and maximum handle positions.OPERATIONHandwheel: The handwheel (item 15) can be turned to raise or lower the ram to and from the workpiece without exerting force on the workpiece.Handle: The handle (item 23) can be used to lower the ram to exert force onto the workpiece. See safety instructions for more information on handle position.MAINTENANCELUBRICATION•Keep all working parts of the press well-oiled for easier operation.•Keep a light film of oil over the entire surface of the ram to prevent rust.EXPLODED VIEW & PARTS LIST EXPLODED PARTS VIEWPARTS LISTItem Part Name Part Number Qty1 Frame 295 12 Mandrel Catcher 254 13 Table Pinion 271 14 Table Pinion Shaft 291 15 Table Crank 270 16 Table Pawl Handle 266 17 Table Pawl Shaft 287 18 Table Pawl 265 19 Spring (1/2” x 2”) 302436 110 Table Plate Assembly 701227 111 Hex Cap Screw (1/2”-13 x 1-3/4”) 43350 412 Label – Made in U.S.A. 76936 113 Ram Cap 296 114 Ram Cap Shim (.015”) 252 615 Handwheel 257 116 Ram Cap Shim (.008”) 251 217 Hex Cap Screw (3/8”-16 x 2”) 43333 118 Ram 253 119 Table 262 120 Hand Brake Stud 223A 121 Handbrake Clamp 215 122 Handbrake 214 223 Handle 283 124 Hex Jam Nut (1/2”-13) 43940 125 Flat Washer (1/2”) 43634 126 Compound Rest Pin 280 127 Headless Set Screw (1/2”-13 x 1-1/2”) 43608 128 Pawl 297 129 Spindle 256 130 Table Stud 282 231 Table Washer 279 232 Table Spring 281 233 Hex Cap Screw 53759 234 Table Clamp 267 135 Hex Nut (1-8) 43922 236 Headless Set Screw (3/8”-16 x 5/8”) 43589 437 Lever Weight 258 138 Pawl Pin 255 139 Retaining Ring 67955 140 Warning Label – Pinch Point 87130 141 Warning Label – Tipping 79979 142 Warning Label – Ganged 300168 1Please contact factory for current prices.ORDERING INFORMATIONParts are available for direct purchase from Dake or through a distributor. When placing a parts order, you will need to provide the part number, name of part, and model number. All parts shipped F.O.B. Factory in Grand Haven, MI.。
英文版焊线机说明书

EDP-No.
EDP-No.
Vertical grinding motor:
Nominal capacity: Connection voltage: Nominal current: Number of revolutions: Grinding wheel: 0,25 220 1,8 2880 0900-0105 kW V A min-1 EDP-No.
Dimensions (with carrier), abt.:
Weight (with carrier), abt.: Year of construction:
Illuminated magnifier:
Fluorescent tube:
230 V / 50 Hz 0550-0009 4W 0550-0011
8 8.1 8.2 9 9.1 9.1.1 ends
wire
9.2 9.3 9.4 9.5 9.6 9.7 9.8 10 10.1 10.2 10.2.4 10.2.5 10.2.6 10.2.7 11 12
../ 4
- 4 -
1.
Foreword
These operating instructions are designated to familiarize the user with the machine and its' designated use. The instruction manual contains important information on how to operate the machine safely, properly and most efficiently. Observing these instructions helps to avoid danger, to reduce repair costs and downtimes and to increase the reliability and life of the machine. The user has to supplement the instruction manual by the respective national rules and regulations for accident prevention and environmental protection. The operating instructions must always be available wherever the machine is in use. These operating instructions must be read and applied by any person in charge of carrying out work with or on the machine such as: transport, operation, including setting up, trouble-shooting in the course of work or upkeep, as well as maintenance such as servicing, inspection and repair. In addition to the operating instructions and to the mandatory rules and regulations for accident prevention in the country and place of use of the machine, the generally recognized technical rules for safe and proper working must also be observed.
LC型泵安装使用说明书-中英文

LC型泵Type LC Pump安装使用说明书Installation and Operation ManualC a u t i o n■请仔细阅读本说明书,理解各项内容,以便能正确安装、运行操作和保养维护等。
Please read this manual carefully and understand all the contents in it for correct installation, operation andmaintenance.■本说明书应保存在实际最终使用人的手中。
This manual should be kept in the hands of the actual end users.■本产品技术规范可能发生变化,恕不另行通知。
The technical specification of this product may change without notice.襄樊525泵业有限公司Xiangfan 525 Pump Industry Co., Ltd.目录Contents 1. 适用范围Scope of application2.泵的结构The Structure of the pump.3.开箱检查Unpacking and checking4.泵的安装Installation of the pump5.泵的运行Startup and operation of the pump 6.泵的维护Maintenance of the pump7.泵的拆卸Disassembling8.泵的装配Assembling9.故障原因及解决办法Possible troubleshooting and solutions 10.常用备件Spare parts1.适用范围Scope of applicationLC、LC——B系列泵是我公司引进的法国日蒙施乃德(JS)公司制造许可证技术,奥特桑伯尔(HS)公司耐腐蚀耐磨蚀泵用材料冶炼铸造技术。
车床 CZ系列C型说明书(机械部分)英文版

QualityLicensefor ExportProductsNo.: XJ 2007421Model CZ 6163C Model CZ 6263CModel CZ 6180C Model CZ6280CModel CZ 6185C Center Lathe Model CZ6285C Gap-bed latheModel CZ 6195C Model CZ6295CModel CZ 61100C Model CZ62100CModel CZ 61120C Model CZ62120CMechanical InstructionMax swing diameter over bed 630 800 850 9500 1000 1200mmMax. length of work piece between centers 750 1000 1500 2000 3000 4000mm 5000 6000 8000 10000 12000mmMax swing diameter in gapIdentification No.830 1000 1050 1150 1200 1400mmJiangsu Qihang CNC Machine Tools Co., Ltd.Add.: No. 1, Kuangji Road, Zhenjiang, Jiangsu, ChinaZip Code: 212003 Telex: 86-0511-********ContentI. Notice on use of the machine tool and safety measures thereof (2)II. Main purposes of the machine tool (8)III. Main technical parameters of the machine tool (8)IV. Transmission system of the machine tool and its structure (12)V. Lubrication and cooling of the machine tool (20)VI. Manipulation, adjustment and safety maintenance of the machine tool (21)VII. Conveying, installation and commissioning of the machine tool (37)VIII. Distribution diagram and list of rolling bearings of the machine tool (38)Ⅸ. Catalog and working diagram of wearing parts of the machine tool (48)X. Jointing techniques for bed, lead screw and feed rod (55)I. Notice on use of the machine tool and safety measures thereof1. Notice on operation1). The operator must accept skill trainings before operating on the machine.2). The operator shall refer to Instructions on Mechanical and Electrical Safety before using the machine tool for the first time, sufficiently lubricating each part as required and activating the machine tool only after having had a full understanding of positions and purposes of each handle and button.3). Before activating the machine during each shift, it is required to check the cleanness of various lubricating surfaces, sufficiency of lubricants as well as fastness of screw-nails on various places in addition to running each part idly for a short period.4). In case the machine tool is to be restarted after a long stop, it shall first idle for a certain period of time and shall be put into production only after all parts have been confirmed to be in a normal state.5). In case the spindle and gears in the feeding box are rotating, no change to rotational speed or feeds shall be made. Where any changes are required, it is imperative to stop the operation and place each gear-shift handle at specified positions in accordance with the label plate on the machine tool.6). When the tool post is moving at a fast pace, the direction of such a rapid move shall first be determined before pressing down the fast forward button.7). When utilizing the tailstock to support and hold the work-piece, the locking nuts between the bed and the tailstock as well as the locking handle of the tailstock sleeve shall be fastened.8). When adopting centers for processing, please pour oil onto centers and stop the machine immediately upon discovery of an over-heating center. It is not allowed to operate with damaged centers.9). Where steady rest and traveling rest are used for supporting the turning of work-piece, the contacting place between the support and the work-piece shall be lubricated.10). The voltage of the grid shall be kept in the range of AC380±15% so as to ensure normal operation.2. Maintenance and proper use1). It is not allowed to place any articles tend to damage the machine tool on the finishing surface or each guide-way surface of the machine tool.2). It is required to add oil, change oil and check the oil inlet/outlet within the spindlebox according to the lubrication diagram on a regular basis so as to prevent the oil inlet/outlet from clogging.3). The lubricant shall be replaced once within one month after the initial use of the machine tool and since then it shall be replaced every two months.4). When replacing the lubricant, strictly filter and clean the same so as to prevent bearings and gears from damaging.5). When the work is finished, clean the guide-way surface and apply an oil coating thereto.(6) The machine tool shall be kept working under good working conditions. Such situations as abnormal noises, smokes, heats or damages shall be reported to relevant personnel in time upon discovery and shall be inspected after the machine is off.(7) The tightness degree of the triangular belt shall be inspected on a regular basis so as to maintain a good working status.(8) The maintenance of the machine tool shall be carried out on the prerequisite that the machine is off.(9) Please refer to drawings of relevant parts before carrying out maintenance or repair.(10) The repairman eligible to repair this machine tool shall have a clear understanding of its structure and obtain mechanical and electrical knowledge to a certain degree.3. Safety knowledge(1) Concentrate on works and always maintain safety consciousness. It is forbidden to smoke while working or operate the machine tool when drunk.(2) When operating the machine tool, no such accessories as tie, watch, ring and diamond is allowed to wear. People will get hurt if come in contact with rotating parts, so do not get close to the rotating head of the spindle in operation or hold the rotating part.(3) Various kinds of spanners, tools and parts shall be kept away from the spindle, work station or moving parts of the machine tool.(4) The ground around the machine tool shall always keep clean. No iron scraps shall accumulate on the ground or machine oil and liquid coolant spill over onto the ground, thus influencing the machine tool.(5) When the machine tool is running, do not put hands at somewhere close to the tool or moving devices.(6) Before running the machine tool, it is required to grip the work-piece and the clamp; otherwise, the machine tool shall not be started up.(7) The machine tool has to stop running when changing the tool.(8) The guard door of the change-gear device is not allowed to be open during work, soas to prevent abrupt power failure which might bring avoidable accidents.(9) The operator shall keep in mind positions of all emergency stop buttons, so as to be ready for any eventualities.(10) The tailstock is equipped with an unloading devise, so please be careful when pulling it.(11) The power supply must be cut off when examining and repairing the machine tool.(12) People getting an electrical shock of high voltage may die. Thus, person in charge of the implementation of maintenance and repair of electric appliances shall limit to those who have acquired knowledge on circuits of the machine tool and have accepted trainings on safety issues of electric appliances. The work shall be carried out only when the main power source has been cut off and an indication of “in operation” has been marked.(13) The cutting fluid, machine oil and cutting powders spilled over on the ground might hurt people by letting them fall over themselves or hit somewhere. Cut off the power of the machine and clean the interior of the machine and surrounding areas before operating the same. During installation and operation, it is required to wear safety helmet and protective shoes.(14) If any tools or work-pieces get stuck by the machine tool which activates abruptly, the broken and damaged ones might fly off and seriously hurt people. It is strongly required to cut off the power before carrying out maintenance and inspection.(15) In case the spindle is rotating, no change to rotational speed or feeds shall be made. When using three-jaw chuck and four-jaw chuck, their specification shall not exceed Ф630mm. Where four-jaw chuck of Ф4000mm is used, the rotational speed of the spindle shall not go beyond 380rpm. The Specification mainly aims at equipping the operator with a preliminary knowledge of the machine tool’s performance, proper operation, simple adjustment and maintenance. For profounder understanding and special requirement, please contact the After-sale Service Department of our company.Fig.1: Profile drawing of the machine toolFig.1: Profile drawing of the machine tool (5M 6M)Fig.1: Profile drawing of the machine tool (8M 10M 12M)II. Main purposes of the machine toolThis machine tool is capable of various coarse and fine turning of ferrous metal, nonferrous metal and non-metal work-pieces, such as turning of inner and outer cylindrical surfaces, conical surface and other surfaces of revolution. It is also capable of turning of end faces and various metric, inch, module and pitch threads in common use as well as multiple-threads. Moreover, it enables drilling, reaming, oil channeling and so on thereon. The dimensional accuracy of work-pieces processed on this machine tool can reach IT7 level, with its roundness error being no larger than 0.01 and its cylindricity on 300 mm length being no larger than 0.03. Its surface roughness can reach 1.6 (for standard sample piece).III. Main technical parameters of the machine tool310mm CZ6163C CZ6263C 400mm CZ6180C CZ6280C 425mm CZ6185C CZ6285C 475mm CZ6195C CZ6295C 500mm CZ61100C CZ62100C Central Height600mm CZ61120CCZ62120C 630mm CZ6163C CZ6263C 800mm CZ6180C CZ6280C 850mm CZ6185C CZ6285C 950mm CZ6195C CZ6295C 1000mm CZ61100C CZ62100C Max. Swing Diameter over Bed1200mm CZ61120CCZ62120C 345mm CZ6163C CZ6263C 485mm CZ6180C CZ6280C 535mm CZ6185C CZ6285C 635mm CZ6195C CZ6295C 685mm CZ61100C CZ62100C Max. Swing Diameter over Tool Post800mm CZ61120CCZ62120C830mm CZ6263C Max. Swing Diameter over Gap (Saddle Machine tool)l000mmCZ6280C1050mm CZ6285C1150mm CZ6295C1200mm CZ62100C1400mm CZ62120CMax. Turning Length 450/700/1200/1600/2600/3600/4600/560/7600/9600/11600mmWidth of Bed Guide-way 550mmSpindle Taper 1:16Taper of Spindle Center Sleeve No.6 (Morse)Spindle Bore 105mmRotational Speed Step/RangeClockwise 18 Steps 14-750 r/minof Spindle Counterclockwise9 Steps 21-857 r/min Kinds and Ranges of FeedsBasic FeedsLongitudinal 32 Kinds 0.10-1.42 mm/rCross 32 Kinds 0.03-0.45 mm/r Fine FeedsLongitudinal 8 Kinds 0.048-0.089 mm/rCross 8 Kinds 0.015-0.028 mm/r Increased FeedsLongitudinal 32 Kinds 1.52-22.8 mm/rCross 32 Kinds 0.48-7.2 mm/r Kinds and Ranges of ScrewingMetric Thread 54 Kinds 1-240Inch Thread 37 Kinds l-28 threads/inchModule Thread 45 Kinds 0.5~60mmPitch Thread 27 Kinds l-30 threads/inchMax. Travel of Top Slide 230mmMax. Travel of Cross Slide 400mmDistance from Spindle32mmCenterline to Tool BearingSurfaceCross-Section of Tool 30×30mmDiameter of Tailstock Spindle Ф100mm or Ф120mm Taper of Tailstock Spindle No.5 or 6 (Morse)Max. Travel of Tailstock Spindle200mm Y160M-4Power 11KW Model of Main MotorRotational Speed1460 r/minYS5634 Power0.12 KW or 0.18 KW Model of Rapidly-Traveling Motor of ApronRotational Speed1400 r/minLongitudinal 6 m/minRapid Traveling Speed of Apron Cross 2 m/min AB-25 or AB-100Power 0.09 KW or 0.12 KW Model of Cooling MotorFlow25 L/min or 100 L/min1000 kg CZ6163C CZ6263C Max. Weight between Two Centers1200 kgCZ6180CCZ6280C and aboveLength of BedExternal Dimensions of Machine Tool(L×W×H)Weight of Machine Tool (approximately, t)750 2702×1276×1260 3.8 1000 2952×1276×1260 4.0 1500 3452×1276×1260 4.5 2000 3952×1276×1260 5.0 3000 4952×1276×1260 5.5 4000 5952×1276×1260 6.5 5000 6952×1276×1260 9 6000 7952×1276×1260 10 8000 9952×1276×1260 11.5 10000 11952×1276×1260 13 12000 13952×1276×126014.5F i g .2: D i a g r a m o f t h e m a c h i n e t o o l t r a n s m i s s i o n s y s t e mn =1460 r /m i nIV. Transmission system of the machine tool and its structure(I) Machine tool transmission systemShown in Fig.2 is the machine tool transmission system.1. Main transmission systemThe work-piece shall be clamped on the chuck or between two centers. The motor drives the spindle via transmission of belts and gears so as to rotate the work-piece.There are two routes for its rotational transmission in clockwise direction, having been divided into 18 steps.Low-speed portion: (14-190 r/min)Main motor →Shaft I →Shaft II →Shaft III →Shaft IV →Shaft V →Shaft VI (Spindle) High-speed portion: (230-750 r/min)Main motor →Shaft I →Shaft II →Shaft III →Shaft V →Shaft VI (Spindle)There are also two routes for its rotational transmission in counterclockwise direction, having been divided into 9 steps.Main motor →Shaft I →Shaft VII →Shaft II →Shaft III→Shaft IV →Shaft V →Shaft VI Shaft V→ Shaft VI2. Feeding transmission systemThe feeding motion of the machine tool is enabled by the feeding box and apron. Its transmission route is: Headstock’s Shaft III or Shaft V →Shaft VIII →Shaft IX (or Shaft VIII →Shaft X →Shaft IX) →Change-Gear Bracket →Feeding box →Apron. The longitudinal, cross, clockwise and counterclockwise feeding motion of the machine tool can be realized via change of directions within the apron.3. Rapid movement of the tool carriage of the machine toolThe rapid movement of the tool carriage of the machine tool is realized by the rapidly-traveling motor installed on the apron.(II) Explanation on the structure of main subassemblies1. BedThe guide-ways of the bed include two planar ones and two rhombic ones. The front rhombic guide-way and the rear planar guide-way are used by the tool carriage, while the rest are for the tailstock and steady rest.2. Spindle boxThe rotational motion of the spindle is enabled by the main motor via the action of triangular belt and gear shift, having been divided into 18 steps. Its rotational speed ranges from 14 r/min to 750 r/min.A fiction clutch is installed on Shaft I of the spindle box so as to protect the transmission component of the machine tool as well as realize clockwise and counterclockwise rotation of the spindle in a convenient way without stopping the rotation of the main motor.The Shaft III and Shaft V of the spindle box lie in the same centerline and they can be joined together directly via internal gear 18 and gear 19 under the condition that gears 14, 15, 16 and 17 are disengaged in respect to each other (see Fig.2), thus realizing branch transmission of spindle rotation.The front bearings of the spindle are adjustable double-row short centripetal cylindrical roller bearings while the rear ones are single-row tapered roller bearings. In addition, single-direction thrust ball bearings are installed on the rear end of the spindle so as to bear axial load.The spindle box is an enclosed box which adopts splash lubrication.The maximum tolerable torque at gears of the spindle box is 1500N m.3. Feeding boxThe feeding box is a two-shaft sliding gear mechanism made up of three parts, namely, basic group, multiplication group and inch/mm conversion group.The feeding box is an enclosed box which adopts centralized lubrication by manual oil-pump.Operating relevant handles while shifting change-gears as per the upper pitch of the feeding box and the indication on the label plate of feeds may acquire different pitches of various screw threads and feeds.4. Apron (See Fig.3)It is mainly used to transfer the motion of the feed rod or lead screw to the tool post so as to provide the tool post with power-driven feeds in cross/longitudinal direction or screwing.In order to avoid interferences of power-driven feeds with the motion of screwing mechanism, an interlocking mechanism is installed in the apron for preventing these two motions from happening simultaneously. Also provided in the apron is an out-of-gear worm security device to avoid extremely heavy loads of the feed mechanism. In order to reduce the labor intensity of the operator, the apron is equipped with a rapidly-traveling motor and amechanical/electrical interlocking stopper to ensure that the motor won’t be activated during the process of power-driven feeds.5. Tool post (See Fig.4)The tool post can not only be driven in longitudinal direction along the bed and in cross direction along the cross slide but also be operated manually or traveling rapidly. But the compound rest can only be operated manually.The tool post swivel (1) can rotate 60° in left and right directions respectively in relation to the tool carriage (2) so as to facilitate the turning of conical parts.For machine tools of models above CZ6180C, the quadrate base of the cross slide can be properly adjusted in cross direction along the slide so as to broaden the processing scope of various parts.6. Tailstock (See Fig.5)The tailstock is tightly fixed onto the bed by the clamping plate (1) and this can be realized by rotating the locking handle (6) or nuts (7). For turning of long but less tapered work-pieces, the upper body of the tailstock (4) shall move crossly on the tailstock base (5) by bolts (2) and nuts (3) for the sake of center shift.The movement of the tailstock sleeve (8) is realized by the hand-wheel (9) while its locking and loosening are realized by the handle (10).The tailstock base (5) is equipped with an unloading device for facilitating the movement of the tailstock. It is made up of a disc spring (11), a rolling bearing (12) and subassemblies (13), (14) and (15). The screw-nail (16) is used as an axial limit.7. Steady rest (See Fig.6)The steady rest is used as a support when processing slender shaft components so as to prevent any bending caused by cutting force. The clamping scope is Ф20-145mm for CZ6163C or Ф20-185mm or Ф300mm for series above CZ6180C. It can also be used for processing parts with large length under circumstances where using the tailstock as the support is inappropriate.The traveling rest is a steady rest moving alongside with the tool post while fixed on the carriage. The clamping scope is Ф20-105mm for CZ6163C or Ф20-135mm or Ф180mm for series above CZ6180C.Fig.3: ApronV. Lubrication and cooling of the machine tool1. The spindle box of the machine tool adopts splash lubrication while the feeding box and apron adopt centralized lubrication by manual oil-pump. The rest utilize manual lubrication by oiling. For specific parts to be lubricated and the requirement thereof, please refer to the indications about machine tool lubrication on the label plate. Since part of the lubricant cannot return to the apron after having reached guide-ways of the bed, the apron shall be refilled with some lubricant according to specific situations so as to ensure that the surface of the lubricant is maintained at a certain level within the apron. The lubricant shall be filled to a depth of 80 mm in the spindle box where the oil scale for CZ6163C is placed. The lubricant shall be filled to a position reaching half of the orifice for series above CZ6180C. The feedbox needs 1.0L oil. The above-mentioned machines and components normally require HJ30 oil.2. The liquid coolant for the machine tool shall be replaced every three months in case of processing of casting and every six months in case of processing of steel parts. The coolant shall be replaced immediately upon deterioration and the water tank shall also be cleaned in time therewith, where the scrap iron shall be cleared by the magnet.3. The cooling system of the machine tool (See Fig.7).VI. Manipulation, adjustment and safety maintenance of themachine tool(I). Manipulation of the machine tool1. For information on positions of various manipulation handles of this machine tool, please refer to Fig.8, while for information on their names, please refer to Sheet2.2. Manipulating method of the main transmission systemThe rotational speed of the spindle is achieved by switching handles (1), (2) and (5), where the handle (5) has three positions marked as 1:1, 1:4 and 1:16, respectively. The handle (5) enables low-speed transmission at the position of 1:4 or 1:16 and can obtain a rotational speed of step 12 in clockwise direction and another of step 6 in counterclockwise direction when in cooperation with handles (1) and (2). In case a high-speed transmission is required, please turn the handle (5) to the position of 1:1 where a rotational speed of step 6 in clockwise direction and another of step 3 in counterclockwise direction can be attained in cooperation with handles (1) and (2).The manipulation handle (21) or (28) has three positions, where the spindle rotates in clockwise direction when the handle is lifted up and rotates in counterclockwise direction when the handle is pressed down. The spindle stops rotation when the handle is place at the middle position.The machine tool must be stopped when the gear shift handle is in operation; otherwise transmission gears might be damaged.3. Operating method of the feeding systemThe feeding motion is realized through proper switch of handles (3) and (4) of the headstock and handles (15), (16), (17) and (20) on the feeding box. The handles shall be placed at proper positions as indicated on the label plate above them.(1) The handle (3) is a handle for left/right threads. Aligning it with the mark□ can produce right-hand threads and feeds in clockwise direction; while aligning it with the mark□can produce left-hand threads and feeds in counterclockwise direction. No feeding motion will be generated when it is placed at the middle position.(2) The handle (4) is a standard handle for pitch enlargement. Aligning it with the mark□1/1 can attain basic pitch and basic feeds; while aligning it with the mark□ x/1 can attain enlarged pitch and increased feeds. No feeding motion will be generated when it is placed at the middle position.F i g .8: P o s i t i o n D i s t r i b u t i o n D i a g r a m o f M a n i p u l a t i o n H a n d l e s o f t h e M a c h i n e T o o lF i g .8: P o s i t i o n D i s t r i b u t i o n D i a g r a m o f M a n i p u l a t i o n H a n d l e s o f t h e M a c h i n e T o o l (5M 6M )F i g .8: P o s i t i o n D i s t r i b u t i o n D i a g r a m o f M a n i p u l a t i o n H a n d l e s o f t h e M a c h i n e T o o l (8M 10M 12M )Name Sheet of Various Manipulation Handles of the Machine Tool Sheet 2Numerals in DistributionDiagram of VariousManipulation Handles ofthe Machine ToolNames1 Gear Shift Handle for Changing the Rotational Speed of the Spindle of the Machine Tool2 Gear Shift Handle for Changing the Rotational Speed of the Spindle of the Machine Tool3 Handle for Left/Right Threads4 Standard Handle for Pitch Enlargement5 1:1, 1:4, 1:16 Gear Shift Handle for Changing the Rotational Speed of the Spindle6 Button for Starting/Stopping the Machine Tool7 Handle for Moving the Cross Slide8 Handle for Moving the Top Slide9 Handle for Clamping/Loosening the Quadrate Tool Post10 On/Off Button for the Coolant11 Button for Rapidly Moving the Slide12 Handle for Locking/Loosening the Spindle of the Tailstock13 Hand-wheel for Moving the Spindle of the Tailstock14 Handle for Locking/Loosening the Tailstock15 Handle for Inch/mm Conversion of Threads16 Hand-wheel for Speed Adjustment of the Basic Group17 Hand-wheel for Speed Adjustment of the Multiplication Group19 Handle for Lubricating the Feeding Box by Manual Oil-Pump20 Handle for Connecting the Lead Screw and the Feed Rod21 Handle for Manipulating the Spindle Rotation in Clockwise/Counterclockwise Direction22 Hand-wheel for Moving the Slide in Longitudinal Direction23 Hand-wheel for Switching Feeds in Clockwise/Counterclockwise Direction24 Handle for Lubricating the Apron by Manual Oil-Pump25 Handle for Feeds in Longitudinal/Cross Direction26 Handle for Manipulating Slit Nuts27 Handle for Manipulating the Out-of-Gear Worm28 Handle for Manipulating the Spindle Rotation in Clockwise/Counterclockwise Direction(3) The handle (15) on the feeding box is a handle for inch/mm conversion of threads.Placing the handle (15) at means cutting of metric and module threads in addition togaining feeds; while at means cutting of inch and pitch threads.The handle (16) is a manipulation hand-wheel for the basic group, and there are 1-8 positions indicated on its label. By aligning it with points indicated on the guard ring respectively, the pitches and feeds can be switched in sequence. In order to change the position of the hand-wheel (16), it is required to pull out the same and rotate it to the desired position before pushing it in. The hand-wheel can rotate in both clockwise and counterclockwise directions during manipulation.The handle (17) is a shift handle for the multiplication group, bearing I-IV positions. By aligning the Roman numerals with the L above them respectively, multiplied pitches and feeds can be attained. The handle (17) can rotate in both clockwise and counterclockwise directions during manipulation.The handle (20) is a handle for switching between the lead screw and the feed rod.Placing the handle (20) at will enable feed-rod transmission so as to realizepower-driven feeds of the tool post; while placing it at will enable lead screw transmission, thus processing various threads.The above-mentioned handles shall work in proper cooperation with other and with gears in Fig.9 as per locations indicated on the label plate of pitches and feeds so as to attain the desired feeding motion.(4) When processing threads with a dimension of 19 threads /inch, change the ratio of gears as required in Fig.12 and, at the same time, place the hand-wheel (16) at the position of numeral “7” and the hand-wheel (17) at “I”.4. Control of tool post motions(1) When cutting the threads, the movement of the tool post shall be controlled by thehandle for slit nuts (26). Press down the handle (26) to the position of , then the apron will be driven directly by the lead screw. The carriage will stop moving when the handle is lifted up.(2) Power-driven feeds of the tool post in longitudinal/cross direction shall be driven by the feed rod and controlled by handles (23), (25) and (27). The handle (23) is a handle for switching feeds in clockwise/counterclockwise direction. Feeds in clockwise direction can be achieved by aligning the mark indicated on the label of the handle (23) with the right T; while those in counterclockwise direction can be achieved by aligning the markwith the right T.The handle (25) is a handle for switching feeds in longitudinal/cross direction. Feeds orrapid movement in longitudinal direction can be achieved by aligning the mark indicated on its label with the upper T; while those in cross direction can be achieved byaligning the mark with the upper T.The handle (27) is a handle for controlling the out-of-gear worm. When lifting up the handle, the worm engages with the worm wheel, thus realizing power-driven feeds in the direction matching with the handle (25). When pressing down the handle, the worm disengages with the worm wheel so as to stop power-driven feeds. During the process of power-driven feeds, the handle (27) will fall off automatically when the resistance against feeds of the tool post in longitudinal direction reaches 5830N, thus serving as a security mechanism.(3) The manual control of the tool post can be realized via hand-wheel (22) and (7). Both hand-wheels are equippted with reading devices where an illuminating device is provided above the reading device of the hand-wheel (22). The hand-wheel (22) can control the manual longitudinal motion of the tool post in clockwise/counterclockwise direction; while the hand-wheel (7) can control the manual cross motion of the tool post in forward/backward direction.(4) In order to reduce the labor intensity of the operator, this machine tool is equipped with a rapidly-traveling device, which can be realized via cooperation by the button box (11)and the handle (25). When the handle (25) is placed at the position of , activating the button to connect with the left button will enable the carriage to move rapidly towards left; while activating the button to connect with the right button will enable the carriage to moverapidly towards right. When the handle (25) is placed at the position of , activating the button to connect with the left button will enable the tool post to move rapidly in forward direction; while activating the button to connect with the right button will enable the tool post to move rapidly in backward direction. The rapid motor can only be activated when the button is pressed down, and it will stop rapid movement as soon as the button is loosened. When the rapid motor is activated, the handle (27) must be put down. If the handle (27) is at “connected” position (namely, if the power-driven feeds are activated), then activating the button will not generate rapid movement (An interlocking device for power-driven feeds and rapid movement is provided in the apron).(5) In order to prevent lead screw and feed rod from interfering with each other and thus causing damages to various parts, an interlocking mechanism is provided in the apron. When the handle (25) stays at the middle position, the handle for slit nuts (26) can be connected in downward direction and if the handle (25) stays elsewhere, the handle for slit nuts (26) is unable to be connected. Also, when the handle for slit nuts (26) is connected in downward direction, then the handle (25) is unable to turn to other positions.(6) In order to prevent feeds and rapid motions from interfering with each other and thus causing damages to various parts, another interlocking security mechanism is also provided in。
数控加工中心机械说明书 中英文
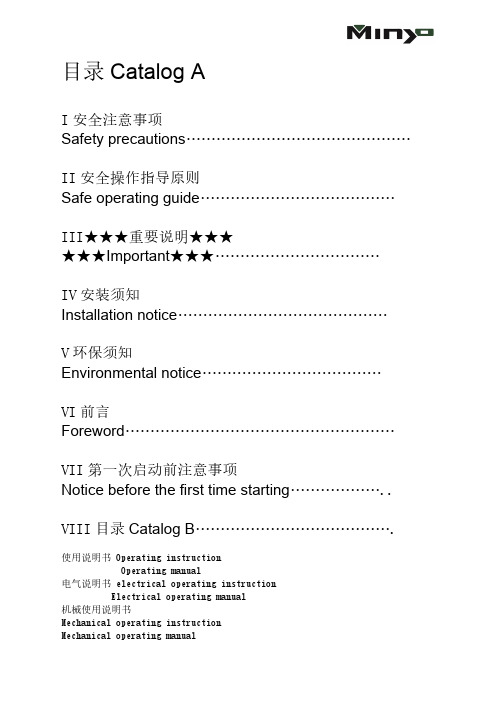
目录Catalog AI安全注意事项Safety precautions………………………………………II安全操作指导原则Safe operating guide…………………………………III★★★重要说明★★★★★★Important★★★……………………………IV安装须知Installation notice……………………………………V环保须知Environmental notice………………………………VI前言Foreword………………………………………………VII第一次启动前注意事项Notice before the first time starting………………..VIII目录Catalog B………………………………….使用说明书 Operating instructionOperating manual电气说明书 electrical operating instructionElectrical operating manual机械使用说明书Mechanical operating instructionMechanical operating manualI安全注意事项 Safety precautions在安装、运行、编程、维护、检修之前,请务必熟读机械制造商所刊行的规格书、本说明书、相关说明书、附属文件,然后正确使用。
请在熟悉了本装置相关知识、安全信息及注意事项之后再使用。
Before installing, operating, programming, maintaining, and overhauling, please be sure to read up on all related specification, instruction, manual book, and files.Before using this machine, please be familiar with all related knowledge, safety information, and precautions.在本说明书中,将安全注意事项的等级分为“危险”、“警告”、“注意”。
英特诺物流机械操作说明书 - DriveControl 20 DriveControl 54 Dri
INSPIRED BY EFFICIENCY操作说明书Interroll DriveControl DriveControl 20DriveControl 54DriveControl 2048制造商地址INTERROLL(Suzhou) Co. LTD.NO. 16 Huipu RoadSuzhou Industrial ParkJiangsu Province, P.R.ChinaZip code:215126英特诺物流机械(苏州)有限公司中国江苏苏州工业园区惠浦路16号;邮编215126内容我们力求信息的准确性,及时性和完整性,并精心准备了本文档中的内容。
无论如何,错误和更改均明确保留。
版权/知识产权文本,图片,图形等及其排列受版权保护和其他保护法的保护。
禁止以任何形式复制,更改,传播或出版本文档的部分或全部内容。
本文档仅用于提供信息和预期用途,无权复制有问题的产品。
本文档中包含的所有标记(受保护的标记,例如徽标和商业名称)均为Interroll AG,CH或第三方的财产,未经事先书面许可,不得使用,复制或分发。
在线版本 - 仅适用于彩色打印!目录1 关于本文档 7 1.1 本文档中的警告提示 81.2 符号 92 与安全相关的信息 10 2.1 最新技术水平 10 2.2 按规定使用 10 2.3 违反规定使用 10 2.4 员工资质 11 2.5 危险 12人身伤害 12电力 12工作环境 12运行中的故障 12维护 12无意中启动 12 2.6 与其他设备之间的接口 13 2.7 功能安全 13根据DIN EN ISO 13849-1:2015的性能水平信息 13 2.8 运行模式/运行阶段 14正常模式 14特殊模式 142.9 其他适用文档 143 产品信息 15 3.1 产品描述 15能量回收/过压保护 15过载保护 15信号变化的封闭时间 16 3.2 结构 16DriveControl20/DriveControl2048 16DriveControl54 17 3.3 供货范围 17DriveControl20/DriveControl2048 17DriveControl54 17版本 2.0 (07/2022) 在线原版操作说明书译文第3页/共58页第4页/共58页版本 2.0 (07/2022) 在线原版操作说明书译文目录3.4 DriveControl 20/DriveControl 54技术参数 183.5 DriveControl 2048技术参数 183.6 DIP 开关/旋转编码开关19DriveControl 20 19DriveControl 54 20DriveControl 2048 203.7尺寸21DriveControl 20/DriveControl 2048 21DriveControl 54 214 运输和储存 224.1 运输 224.2 储存 225 装配和安装 235.1 关于装配的警告提示 235.2 DriveControl 的装配235.3 关于电气装配的警告提示 245.4电气安装25连接供电25DriveControl 20/DriveControl 2048 25DriveControl 54 265.5输入和输出端27DriveControl 20/DriveControl 2048 27DriveControl 54 295.6接线图31DriveControl 20、DriveControl 54原理图 31DriveControl 2048原理图31DriveControl 20、DriveControl 54 、DriveControl 2048 最小电路 33多个故障信号连接到一个PLC 上34目录6 调试和运行 35 6.1 调试 35首次调试前的检测 35 6.2 配置选项 35调整速度 35DriveControl20、DriveControl54通过DIP开关预选速度 36DriveControl20、DrivControl54通过数字输入端预选速度 38DriveControl20、DriveControl54将DIP开关RAMP用于加速和制动斜坡时的加速度 40DriveControl2048通过旋转编码开关预选速度 41DriveControl2048通过数字输入端预选速度 42DriveControl2048旋转编码开关DIR/RAMP 43 7 维护和清洁 44 7.1 维护 44检查DriveControl 44更换DriveControl 447.2 清洁 458 故障帮助信息 46 8.1 故障查找 468.2 LED指示灯的含义 479 停止运行和废弃处理 48 9.1 停止运行 489.2 废弃处理 4810 附录 49 10.1 DriveControl20、DriveControl54接口的电气数据 49输入/输出端接口 49RollerDrive接口 51 10.2 DriveControl2048接口的电气数据 53输入/输出端接口 53RollerDrive接口 55 10.3 欧盟一致性声明译文 57版本 2.0 (07/2022) 在线原版操作说明书译文第5页/共58页版本 2.0 (07/2022) 在线第6页/共58页原版操作说明书译文版本 2.0 (07/2022) 在线原版操作说明书译文第7页/共58页关于本文档1 关于本文档有关本操作说明书的信息该操作说明书描述Interroll DriveControl 系统• DriveControl 20• DriveControl 54• DriveControl 2048接下来将使用“控制系统”这个名称来代替。
Kaba 机械锁芯 产品说明书
Kaba 机械锁芯产品概述Kaba gemini SKaba quattro S系统特点•排列于3个不同的行列位置•合计32个弹子(tumbler pins)位置•合计16组弹子(tumbler pins)•特殊设计的弹子外形,有”防拍功能”,适用于小型至中型的主总匙系统•149万亿个独立钥匙•369万亿个钥匙组合•专利保护直到2009年•标准首盖颜色-蓝色•圆头版本Kaba gemini S keyKaba quattro S key•标准首盖颜色-蓝色•大头版本系统特点•排列于4个不同的行列位置•合计44个弹子(tumbler pins)位置•合计22组弹子(tumbler pins)•特殊设计的弹子外形,有”防拍功能”•超过2兆个独立钥匙•超过1千万亿个钥匙组合•专利保护直到2009年•适用于大型至复集的主总匙系统Kaba quattro pluS Kaba penta系统特点•排列于4个不同的行列位置•合计44个弹子(tumbler pins)位置•合计22组弹子(tumbler pins)•特殊设计的弹子外形,有”防拍功能”•超过2兆个独立钥匙•超过1千万亿个钥匙组合•专利保护直到2021年•标准首盖颜色-蓝色•大头跟首盖或没有首盖版本Kaba quattro pluS keyKaba penta key•标准首盖颜色-深红色•大头跟首盖或没有首盖版本系统特点•排列于5个不同的行列位置•合计85个弹子(tumbler pins)位置•合计22组弹子(tumbler pins)•特殊设计的弹子外形,有”防拍功能”•867兆个独立钥匙•31 septillion 个钥匙组合•专利保护直到2021年•适用于大型至复集的主总匙系统•适用于大型至复集的主总匙系统经销商产品概述Kaba gemini TKaba experT系统特点•排列于3个不同的行列位置•合计32个弹子(tumbler pins)位置•合计16组弹子(tumbler pins)•特殊设计的弹子外形,有”防拍功能”•专利保护直到2009年•标准首盖颜色-蓝色•圆头版本Kaba gemini T keyKaba experT key•标准首盖颜色-蓝色•大头版本系统特点•排列于4个不同的行列位置•合计44个弹子(tumbler pins)位置•合计22组弹子(tumbler pins)•特殊设计的弹子外形,有”防拍功能”•专利保护直到2021年•适用于大型至复集的主总匙系统供应香港及中国市场•适用于通匙锁芯系统过去的产品概述Kaba geminiKaba quattro系统特点•排列于3个不同的行列位置•合计32个弹子(tumbler pins)位置•合计16组弹子(tumbler pins)•不供应于新的系统,只供应锁芯更换或系统伸延•圆头版本Kaba gemini keyKaba quattro key•圆头版本系统特点•排列于4个不同的行列位置•合计44个弹子(tumbler pins)位置•合计22组弹子(tumbler pins)•不供应于新的系统,只供应锁芯更换或系统伸延机械锁芯系列技术参数系统特点双面互用式钥匙专利保护安全级别独立钥匙数量行列位置数量钥匙组合数量适用于中型至大型的主总匙系统于主总匙系统的独立钥匙数量适用于复集的主总匙系统根据EN1303防盗级别防盗级别第6级防攻击级别第2级根据DIN18252第82级于主总匙系统防盗级别根据VdS B 级防钻防钻及防拉主总匙系统安全功能大头钥匙可于其它家具锁配合主总匙系统主总匙系统可提供短形锁芯,可升级至电子主总匙系统钥匙复制只限于由制造商根据匙卡,顾客签名或密码才可复制基本长度为25/35mm Kaba gemini T是AT 396.502 1)是--3--------是是----------有是有是授权经销商系统代码= 92009Kaba experT是WO 01/177466 1)是907 billion 476.1 trillion 是最多12870--是是是M105323M105324M105325有是有是授权经销商系统代码= 52021Kaba quattro pluS 是WO 01/177466 1)是> 2 trillion 4> 1 quadrillion --> 30 million是是是是M105323M105324M105325有是有是是系统代码= 72021Kaba penta是WO 01/177466 1)是> 500 trillion 5> 30 septillion --> 50 million是是是是M105323M105324M105325有是有是是系统代码= 62021Kaba gemini S是AT 396.502 1)是149 billion 4369 billion --最多87,000--是是是--------有是有是是系统代码= 22009Kaba quattro S是AT 396.502 1)是> 2 trillion 4> 1 quadrillion --最多12,870是是是是M105323M105324M105325有是有是是系统代码= 42009机械锁芯一般资料5. Kaba security master key systems offer maximumcustomer protection. System keys are copy-protected by a technological and patented copy protection process.A specially designed key tip prevents unauthorized keys from being inserted into the keyway.Replacement keys are produced without exception at the factory after checking the security card and/or code.6. Kaba keys are manufactured from wear-resistant nickel silver and delivered with a colored clip bow (standard: Kaba blue, for penta dark red). An additional 11 colors are also available as an option.7. Systems have up to 32, 44 and/or 85 tumbler pin positions per cylinder side. Unlocking security is also increased through the use of special pin shapes. The block lengths of the pin pairs are always the same –this provides the highest security against lock picking.Each pin pair can be varied at several levels. The pin rows are arranged radially to the cylinder center and are not subjected to any reciprocal variation limitations.8. Kaba master key systems have a modular design . In combination with various lengths of cylinder housings(complete housings), cams and couplings, cylinders previously supplied can be quickly modified with regards to the length and/or function.The concept of modular inserts also allows the use of other cylinder types such as single cylinders, thumbturn cylinders, furniture cylinders in the modular system.9. All tumbler pins (in the stator and rotor) are made from hardened, chemically nickel plated steel to achieve increased drilling protection . In addition, the fixing area is secured with a 4 mm thick stud bolt made from hardened steel.10. Increased protection against pulling or ripping out the lock is provided as an option withVdSapproval . This protection can withstand a force of at least 15 kN for both the cylinder plugs and the cylinder body.11. As an option, Kaba cylinders in master key systems can also be equipped with a steel housing and additional special carbide fastening pins to provide increased protection against drilling, pulling and tearing.Kaba lock cylinders are ergonomically correct reversible key systems. The tumbler pin positions are arranged on each cylinder side in 3, 4 or 5 rows in a radial pattern around the keyway. The cylinder is hereby reliably resistant against picking -even with modern tools.The additional codes required for master key systems are not achieved by using additional subdivisions of the tnumbler pins, which would decrease securityconsiderably, but rather by using a different arrangement of the tumbler pins in the cylinder. Central locks are coded via a special groove on the key. In this way, they are as secure as individual locks.Kaba profile cylinders are serially equipped with increased drilling protection. All tumbler pins are made fromhardened, chemically nickel plated steel. In addition, a 4 mm thick stud bolt made from hardened steel is also integrated into the cylinder body for each cylinder side.The reversible key is protected against copying to a high degree. The code on factory made keys is not made by drilling but by using a special milling process which conceals the exact position of the code on the key. The key is made from nickel silver and offers high breakresistance, the best gliding properties and the lowest wear.Special labeling on the key and cylinder is possible ifdesired by the system user. A security card is required to receive duplicate keys (optional with signature and code).Features of Kaba Master Key Systems1. Kaba master key systems quattro S, quattro pluS and pentameet all the requirements of VdS approval for Grade B . In addition, they also fulfill DIN 18252and European Standard EN 1303 Key Related Security Grade 6requirements. With additional security elements, they can also meet European Standard EN 1303 Attack Resistance Grade 2 requirements.2. The systems Kaba quattro pluS and penta are suitable for large master key systems . For example, there aremore than 30 million individual locks possible for a system master key for Kaba quattro pluS and 50 million for Kaba penta.3. Kaba systems are ergonomically correct reversible key systems , i.e. the Kaba reversible key is inserted vertically into the cylinder keyway.4. Central lock functions for Kaba systems areimplemented without a loss of security, i.e. without additional pin subdivision.Mechatronic systems, consoles for access control and time attendance can also be integrated into the master key system. We also provide suitable software for access control and time attendance.19. We also offer an optional master key system management program.12. Double cylinders can be supplied optionally as short cylinders with full master key system functionality (basic length 25/35 mm).13. The system can be used with Euro profile double cylinders witha) Priority function(the cylinder can also be locked from the outside when a key is inserted in the inside)b) Emergency override key function(locking out one side is overcome by using an emergency override key) Note: Standard for double cylinders inEuroprofile, the emergency override key must be ordered separately.c) Cam with 360°freewheel function14. The following can also be integrated into the system:a) Cam locks with an installation diameter of 19 mm b) Switch/Elevator cylinders (round cylinders) with an installation diameter of 19 mmc) Furniture cylinders with an installation diameter of 22 mm d) Padlocks15. Euro profile cylinders are supplied standard with a 2x12 adjustable cam (in 15°increments).16. If required, mortise lock cylinders in "Swiss Profile“(22 mm) for special doors (main entrances, etc.) can beintegrated into master key systems with Euro profilecylinders while maintaining all lock functions.17. Kaba systems can optionally be equipped with a Duplo function (the regular key can only be turned so far so that only the lock latch can be activated).18. The mechanical master key system can also beupgraded with an electronic master key system. The Kaba reversible key can be upgraded with a Legic®transponder without having to change the existing mechanical master key system. Such keys may be used in mechanical, mechatronic and electronic master key systems.Kaba modular expands the application area of authorized dealers, especially in the service area. A quick conversion of an existing cylinder and an adjustment to changed customer desires and requirements increases versatility and flexibility.Specially trained and authorized modular dealers have an agreement with Kaba to carry out cylinder conversion. Kaba provides a dealer set to support these dealers (basic equipment of required cylinder parts for length changes and/or other conversions) as well as installation tools.Investment security and upward compatibility -in short, long term use and usability of products once purchased have always been an important issue for -and an substantial differentiating characteristic of Kaba. Kaba reversible key systems Kaba penta, Kaba quattro pluS, Kaba quattro S, Kaba gemini S, Kaba experT and Kaba gemini T have a module system design that makes it quick and easy to modify cylinder lengths and types.Existing cylinders can be modified quickly and easily regarding length and/or function in combination with different cylinder bodies (complete housings), couplings and cam hubs. The locking system itself cannot bemodified by the dealer. A general 2x12 conversion of the cam is possible.The module insert concept allows the inserts to be used trouble-free in other cylinder types (single cylinders, thumbturn cylinders, rim cylinders, furniture cylinders, padlocks and cam locks).Kaba模块式结构When determining the required cylinder length, the thickness of the door furniture and/or rosette being used must always be added to the door leaf thickness.The required cylinder length is determined after inserting the the mortise lock:1. Outside = distance from cylinder fastening screw to the outside (including door furniture)2. Inside = distance from cylinder fastening screw to the inside (including door furniture)3. Select the next larger dimension from the Kaba cylinder list.确定锁芯长度请注意下列事项信息是如何订购我们的产品。
IL-NT-MRS3.4-AMF8.9中英文说明书
InteliLite controller SW and HW versions compatibility
Be aware that IL-NT SW version 1.2.1 and older is not possible to use with IL-NT HW version 1.3 and newer!!! Software IL-NT 1.3 is compatible with IL-NT hardware version 1.3 and older.
unexpected automatic start of genset and GCB closing.
每次当您想要断开InteliLiteNT制MCB
切换InteliLite到手动或在关模式或者断开二进制输出启动和燃油以防止发动机自动起动动和GCB合闸。
接地端子总是连接的! 在任何情况下不要断开 InteliLiteNT电流端子!
!警告!
Adjust set points 调整设定点
All parameters are preadjusted to their typical values. But the set points in the “Basic settings” settings group !!must!! be adjusted before the first startup of the gen-set. 调整所有参数的标准值,但是在“基本设定”项目里面所有的设定点必须在第一次起动前设定好。
软件和硬件必须(例如AMF9硬件和AMF9 固件版本)相配,要不然功能将无效。如果下载软件有问题在控制器的屏 幕上会显示“HARDWARE INCOMPATIBLE”信息。在这种情况下使用跳线闭合跳线并按照LiteEdi操作指南指导“起动跳 线程序设计”,并下载正确的编程软件。
GEA 产品说明书 - 液压机械制冷系统
Compresores de tornillo de GEACompresores de tornillo para refrigeraciónindustrial y aire acondicionado2Máxima calidad basada en un desarrollo demostradoYa sea la industria alimentaria, la industria química, el transportenaval o en climatización de oficinas, todos ellos necesitanrefrigeración. GEA dispone de las soluciones de refrigeración y aireacondicionado adecuadas para sus necesidades. Otorgamos especial valor a la eficiencia energética, la fiabilidad, la optimización decostes y la sostenibilidad.Como líder tecnológico internacional, GEA se especializa en latecnología de soluciones y en componentes para sofisticadosprocesos de producción. GEA también está muy especializada enla tecnología de compresores. La excelente calidad de nuestroscompresores de tornillo es fruto de años de experiencia endicha tecnología. Nos esforzamos en ofrecer valor añadidoy funcionalidad desde el desarrollo en nuestros laboratoriosde investigación hasta el control de calidad, pasando por losprocesos de producción.Con una red global de ventas y servicio, podemos atenderle casien cualquier sitio lugar del mundo donde nos necesite. Nuestrasherramientas de software también le ayudan a seleccionar launidad compresora óptima, así como a encontrar los repuestosadecuados..Energéticamente eficiente• Capacidad y control de Vi (relación de volumen interno) lineal • Perfil de rotor 5/6 diseñado por GEAFiable y seguro• Sistema patentado de protección ante vibraciones, que evita pulsaciones en carga parcial a relaciones de presión alta.• Rodamientos de alto rendimiento y compensación de fuerza axial hidráulica para una larga vida útil de producto.• Indicador de posición de corredera estandarizado y sellado herméticamenteFácil mantenimiento• Cambio fácil de los cojinetes de empuje y el cierre mecánico, sin necesidad de desmontar el compresor o el motor • Diseño a prueba de explosiones bajo petición• Certificaciones según la API 619 o la ISO 10440, otras certificaciones bajo petición• Presiones de servicio: 28 bares y 52 bares, otros diseños bajo petición.• Diseño particular para compresores de alta presión: Material de carcasas (por ejemplo, hierro fundido nodular), geometría de rotor personalizada, cojinetes de empuje reforzados (diseño TRIAX), cierre mecánico de alto rendimiento, extremo del eje de transmisión reforzado, etc.ASPECTOS DESTACADOSVISTA GENERAL DEL PRODUCTOSerie Volumen desplazado (m3/h)01002003004005006007008009001000200040006000800010,00012,00014,000GEA Grasso M a 2940 rpm 231–870 m3/ha 4500 rpm 354–1332 m3/hGEA Grasso LT a 2940 rpm805–11467 m3/ha 3550 rpm972–13846 m3/hOPCIONES3GEA Grasso M – Aumentando la eficienciaLos compresores GEA Grasso M son los primeros compresores de tornillo con una válvula de retención integrada activada por presión que asegura baja caída de presión. La integración del filtro de aspiración y la campana de acoplamiento simplifica aún más el montaje de la unidad. La excelente eficiencia energética de estos compresores se basa en la capacidad ajustable linealmente combinada con una relación Vi variable ampliada. La velocidad variable desde 1000 hasta 4500 rpm (6000 rpm para los C, D, E y G) asegura un amplio rango de funcionamiento y una eficiencia máxima a carga total y parcial.GEA Grasso M viene en ocho tamaños de modelo y cubre un rango de volumen desplazado de 231 a 870 m 3/h a 2940 rpm (de 354 a 1332 m 3/h a 4500 rpm).En resumen• Excelente eficiencia energética • Fácil montaje de la unidadGEA Grasso M (C, D, E, G)GEA Grasso M (H, L, M, N)4CARACTERÍSTICAS Y VENTAJAS ÚNICAS1. Rotores de alta eficiencia • Perfil de rotor 5/6 diseñado por GEA • Diseño compacto y rígido2. Capacidad/control de Vi • Sistema compacto e integrado • Control de capacidad lineal (10-100 %)• El mejor coeficiente de rendimiento a carga total y parcial3. Indicador de posición de la corredera • Herméticamente sellado • Adecuado para zonas peligrosas4. Cierre mecánico• Diseño y materiales de alto rendimiento • De fácil acceso para el mantenimiento• Montado en el lado de aspiración para una mayor vida útil de servicio5. Rodamientos axiales• Acceso rápido y fácil desde el extremo de no accionamiento • Reemplazables in situ• Descargado mediante pistón de balance para una larga vida útil 6. Conexión de aceite centralizado• Conexión opcional el lado macho o hembra del rotor • La mayoría de casos no necesitan bomba de aceite • Inyección de aceite ajustable7. Filtro de aspiración integrado • Diseño compacto para un montaje fácil8. Válvula de retención en aspiración activada por presión• Mínima caída de presión• Sin ruidos de vibración de válvula o muelles• Diseño simétrico permite la instalación del recíproco en aspiración (solo para C, D, E, G)Protección por pulsación de gas• Vibraciones y pulsaciones de gas reducidas a bajas cargas parcialesCampana de acoplamiento embridada • Menores costes de montaje • No es necesario alinear la unidad• Acoplamiento que facilita el mantenimientoFiltro de aceite integrado• D isponible como opción (solo para C, D, E, G)GEA Grasso M (C, D, E, G)GEA Grasso M (H, L, M, N)12345678123456875GEA Grasso LT – Compacta y potenteLa serie GEA Grasso LT viene en 16 modelos y con un desplazamiento volumétrico que va desde los 805 hasta los 11467 m3/h a 2940 rpm. Gracias ala combinación de cojinetes lisos y rodamientos antifricción de los rotores, el compresor disfruta de un ciclo de vida extremadamente largo y de bajos niveles de vibración y ruido. Es posible conectar los sensores de presión, temperatura y vibración. Su diseño simple ofrece una integración inteligente de la gestión de aceite mediante electroválvulas directamente conectadas para la Vi (relación de volumen interno) y para los ajustes de capacidad. El acceso directo de las electroválvulas y otros componentes facilita el montaje y las tareas de mantenimiento de la unidad.En resumen• Vida útil del producto extremadamente larga • Excelente nivel de ruido y vibración en todas las condiciones de funcionamiento6CARACTERÍSTICAS Y VENTAJAS ÚNICAS1. Control de la vibración• Conexiones para sistemas de control de la vibración2. Cojinetes radiales• Cojinetes de deslizamiento para altas cargas• Funcionamiento sin contacto ni desgaste3. Rodamientos axiales• Acceso rápido y fácil desde el extremo de no accionamiento • Sustituibles in situ• Descargado mediante pistón de balance para una larga vida útil4. Protección por pulsación de gas• Vibraciones y pulsaciones de gas reducidas a bajas cargas parciales5. Corredera de capacidad/Vi• Sistema compacto e integrado• Control de capacidad lineal (10-100 %)• El mejor rendimiento a carga total y parcial 6. Cierre mecánico• Diseño y materiales de alto rendimiento• De fácil acceso para el mantenimiento• Montado en lado de aspiración para una mayor vida útil7. Rotores de alta eficiencia• Perfil de rotor 5/6 diseñado por GEA• Diseño compacto y rígidoPuerto economizador• Conexiones ECO para un aumento de capacidadmáximo y mayor eficienciaIndicador de posición de la corredera• Herméticamente sellado• Adecuado para zonas peligrosasServicio y mantenimiento sencillos• Diseño compacto y que facilita el mantenimiento• Fácil acceso a las piezas móviles12345677Datos técnicosSerieTipo de compresorVolumen desplazado(m 3/h)Presión máx. de diseño (bar)Dimensiones 1)(mm)DN1 2) (mm)DN2 3) (mm)Peso 1) (kg)2940 rpm3550 rpm 4500 rpm L A H GEA Grasso MC 231279354288526606608065/80392D 265320406288826606608065/80401E321388491288986606678080444G 372449569289276606678080451H 47156972128 / 5296480082012580581L 54465783328 / 52100080082012580605M 708855108428 / 521094800856150100772N8701051133228 / 5211458008201501008001)con campana de acoplamiento 2)conexión de aspiración 3)conexión de descargaGEA GRASSO M8M1746737432202N21582891424741) a 2940 rpm con recalentamiento de 5 K y subenfriamiento de 0 K, valores de temperatura indicados: evaporación/condensación2) con economizadorSerieTipo de compresorCompresor 28 bares 1)(kW)Compresor 52 bares 1)(kW)Capacidad frigorífica 2)R717 | -35/+35 °CCapacidad frigoríficaR717 | 0/+35 °CCapacidad frigorífica R744 | -50/-5 °CCapacidad de calefacción R717 | +35/+80 °CGEA Grasso LTP 2017728512679R 26099710993433S 328126114184318T 368141315994814V 443169018685780W 506193221356631Y614234425917990Z 714271*********XA 8443209359510853XB 107040704499–XC 126048075366–XD 149156896351–XE 18427030––XF 22008393––XG 25209615––XH294611244––1) a 2940 rpm con recalentamiento de 5 K y subenfriamiento de 0 K, valores de temperatura indicados: evaporación/condensación 2)con economizadorGEA GRASSO LT11R T -002-0301-E S -E U © G E A G E A R e f r i g e r a t i o n G e r m a n y G m b H . T o d o s l o s d e r e c h o s r e s e r v a d o s . S u j e t o a m o d i fic a c i ón .GEA GermanyGEA Refrigeration Germany GmbH Holzhauser Straße 16513509 Berlin, GermanyTel +49 30 43592-600Fax +49 30 43592-777************GEA Group es una empresa global de ingeniería mecánica con un volumen de ventas de miles de millones de euros, que realiza operaciones en más de 50 países. Fundada en 1881, la empresa es uno de los mayores proveedoresde equipamiento innovador y tecnología de procesos. GEA Group forma parte del índice STOXX® Europe 600.Vivimos nuestros valores.Excelencia • Pasión • Integridad • Responsabilidad • GEA-versidad。
- 1、下载文档前请自行甄别文档内容的完整性,平台不提供额外的编辑、内容补充、找答案等附加服务。
- 2、"仅部分预览"的文档,不可在线预览部分如存在完整性等问题,可反馈申请退款(可完整预览的文档不适用该条件!)。
- 3、如文档侵犯您的权益,请联系客服反馈,我们会尽快为您处理(人工客服工作时间:9:00-18:30)。
Manuale di istruzioni per l’uso e la manuten - Instructions and maintenance manual forZione delSOLLEVATORE ELETTROIDRAULICO ELECTROHYDRAULIC LIFTPER VEICOLI FOR VEHICLES Modello 204I/A Model 204I/AAnno di costruzioneYear of manufactureCOSTRUTTORE: MANUFACTURER:WERTHER INTERNATIONAL S.p.A WERTHER INTERNATIONAL S.p.A Via F. BRUNELLESCHI, 12 Via F. BRUNELLESCHI, 12 42124 CADE’(RE)-ITALY 42124 CADE’(RE)-ITALYTelefono ++/+522/9431 (r.a.) Telefono ++/+522/9431 (r.a.) Telefax ++/+522/941997 Telefax ++/+522/941997WEB WEB E-mail ******************** **************************Rev.1……………………………………29/12/2009CONTENTSPACKING, TRANSPORT AND STORAGE (5)PACKING (5)LIFTING AND HANDLING (5)STORAGE (5)CRATE STACKING (6)OPENING THE CRATES (6)DISPOSAL OF CRATES (6)INTRODUCTION WARNING (6)LIFT SATETY (6)THE SAFETY OF LIFTED VEHICLES (6)CONSERVING THE MANUAL (6)LAWS (7)CHAPTER 1 DESCRIPTION OF THE MACHINE (8)1.1 FIXED STRUCTURE (FIG.4) (9)1.2 MOVING UNITS (SEE FIG.4) (9)1.3 LIFT UNIT (SEE FIG.4) (9)1.4 HYDRAULIC POWER UNIT (FIG.5) (10)1.5 CONTROL BOX (FIG.6) (10)1.6 SAFETY DEVICE (10)CHAPTER 2 TECHNICAL SPECIFICATIONS (11)2.1 ELECTRIC MOTOR (12)2.2 HYDRAULIC UNIT PUMP (12)2.3 OIL (12)2.4 HYDRAULIC OIL DIAGRAM (12)2.5 VEHICLE WEIGHT AND SIZE (14)2.6 MAXIMUM DIMENSIONS OF VEHICLES TO BE LIFTED (15)CHAPTER 3 SAFETY (16)3.1 GENERAL PRECAUTIONS (17)3.2 RISKS OF ELECTRIC SHOCK: (17)3.3 RISKS AND PROTECTION DEVICES (17)3.4 LONGITUDINAL AND LATERAL MOVEMENT (17)3.5 RISKS WHILE THE VEHICLE IS BEING RAISED (18)3.6 RISKS OF PERSONS (19)3.6.1 RISK OF CRUSHING (OPEARATOR) (20)3.6.2 RISK OF CRUSHING (PERSONNEL) (20)3.6.3 RISK OF IMPACT (20)3.6.4 RISK DUE TO VEHICLE MOVEMENT (21)3.6.5 RISK OF VEHICLE FALLING FROM LIFT (21)3.6.6 SLIPPING (22)3.6.8 RISK OF COMPONENT FAILURE DURING OPERATION. (22)3.6.9 RISK RELATED TO IMPROPER USE (23)CHAPTER 4 INSTALLATION (23)4.1 INSTALLATION REQUISITE CHECKLIST (23)4.2 LIGHTENING (24)4.3 FLOOR (25)4.4 ASSEMBLING (26)PUT COLUMN (26)4.4.2 HYDRAULIC PLANT (27)4.4.3 ELECTRIC PLANT CONNECTION (28)4.4.4 ARM ASSEMBLING (29)TESTING AND CHECKS TO PERFORM BEFORE START-UP (30)4.5.1 MECHANIAL TESTS (30)4.5.2 ELECTRIC TESTS (30)4.5.3 OPERATING OF THE FOLLOWING DEVICES (30)4.5.4 HYDRAULIC OIL TEST (31)4.5.5 ROTATION DIRECTION TEST (31)4.6 SET UP (31)4.6.1 VACUUM TEST (without vehicles loaded) (31)4.6.2 LOAD TESTS (31)CHAPTER 5 OPERATIONS AND USE (32)CONMANDS (32)5.1.1 MAIN SWITCH (IG) (32)5.1.2 UP PUSH BUTTON (32)5.1.3 DOWN PUSH BUTTON (32)5.1.4 LOCK PUSH BUTTON (32)5.2 OPERATING SEQUENCE (32)5.2.1 LIFTING (32)5.2.2 PARKING (33)5.2.3 LOWERING (33)CHAPTER 6. MAINTENANCE (33)PRECAUTIONS (33)6.2 PERIODIC MAINTENANCE (34)6.2.1 OPERATION FREQUENCY (34)6.2.2 EVERY MONTH (35)6.2.3 EVERY 3-MONTH... (35)6.2.4 EVERY 6-MONTH... (35)6.2.5 EVERY 12-MONTH... . (36)6.3 PERIODIC LUBRIFICATION CHART (37)CHAPTER 7 TROUBLESHOOTING (38)7.1 TROUBLESHOOTING GUIDE (38)7.2 POSSIBLE PROBLEMS AND SOLUTIONS (38)APPENDIX A-SPECIAL NOTES (39)APPENDIX B SPARE PARTS (39)PACKING, TRANSPORT AND STORAGEALL PACKING, LIFTING, HANDLING, TRANSPORT AND UNPACKING ORERATIONS ARETO BE PERFORMED EXCLUSIVELY BY EXPERT PERSONNEL WITH KNOWLEDGE OF THE LIFT AND THE CONTENTS OF THIS MANULPACKINGThe lift is shipped disassembled into following parts: Weight (kg)Command post; complete with carriage, chain, hydraulic cylinder and control panel 320kg Service side post, complete with carriage, chain and hydraulic cylinder 310kgCrossbeam 30kgLong arms complete with extension and plate 35kgShort arms complete with extension and plate 30kgPower unit complete with motor and support 30kgAccessory package, nuts and bolts 27kgFoot guards 3kgBox containing 4 arm-blocking kitsThe lift is dispatched in an iron crate (Fig.1), weighing approx.850kg.LIFTING AND HANDLINGThe crates may be lifted and moved with a lift truck (Fig.1).If either of the latter two are used , crates must be harnessed with at least 2 slings.Fig.1 Fig.2The equipment chosen must be suitable for safe lifting and moving, bearing in mind the dimensions and weight.STORAGEPacked machinery nut always be kept in a covered, protected place, at a temperature between -10。
And +40。
And must not be exposed to direct sunlight.CRATE STACKINGThe type of packing allows the possibility of stacking up to 3 crates.Up to 3 crates may be stacked one upon the other on lorries or in containers if property positioned and provided they are restrained to prevent falling.OPENING THE CRATESWhen the crates arrive, check that the machine has not been damaged during transport and that all parts listed are present. The crates must be opened using all possible precautionary measure to avoid damaging the machine or its parts. Make sure that parts do not fall from the crate during opening.DISPOSAL OF CRATESThe crates may be reused or recycled.INTRODUCTION WARNINGThis manual has been prepared for workshop personnel expert in the use of the lift (operator) and technicians responsible for routine maintenance (maintenance fitter): read the manual before carrying out any operation with the lift and /or the packing. This manual contains important information regarding:THE PERSONAL SAFETY OF operators and maintenance workers LIFT SATETYTHE SAFETY OF LIFTED VEHICLESExpress the rated load is 4000kg ,don’t allow the lift load weigh excess 4000kg. This symbol express attention should be taken for electrical hazardsCONSERVING THE MANUALThe manual is an integral part of the lift, which it should always accompany even if the unit is sold .The manual must be kept in the vicinity of the lift in an easily accessible place so that the operator and maintenance staff must be able to locate and consult the manual quickly at any time.ATTENTIVE AND REPEATED READING OF CHAPTER 3, WHICH CONTAINS IMPORTANT INFORMATION AND SAFETY WARNINGS, IS PARTICULARLY RECOMMENDED.Lift rack has been designed and built in compliance with the following:LAWSThe lifting, transport, unpacking, assembling, installation, starting up, initial adjustment and testing, EXTRAORDINARY maintenance, repair, overhauls, transport and dismantling of the lift must be performed by specialist personnel from the LICENSED DEALER or an SEVICE CENTRE authorized by the manufacturer (see authorized dealer on frontispiece).The manufacturer declines all responsibility for injury to persons or damage to vehicles or objects when any of the above mentioned operations have been performed by unauthorized personnel or when the rack has been subject to abuse.This manual indicates only the operative and safety aspects that may prove useful to the operator and maintenance works better understanding the structure and operation of the lift and for best use of the lift.In order to understand the terminology used in this manual, the operator must have specific experience in workshop, service, maintenance and repair activities, the ability to interpret correctly the drawings and descriptions contained in the manual and be acquainted with the general and specific safety rules relevant to the country in which the machine has been installed.The same applies to the maintenance fitter, who must also possess specific and specialized knowledge (mechanical, engineering) needed to perform the operations described in the manual in complete safety.The words “operator” and “maintenance fitter” used in this manual are construed as follows:OPERATOR: person authorized to use the lift.WORKING CONDITIONS:1、Regarding ambient temperature shall be 5-40℃.2、Regarding humidity shall be 30-95%.3、Regarding transportation and storage temperature shall bebetween25-55℃,and short period no exceeding 24 hours at up to70℃.4、Regarding installation altitude max 1000m.MAINTENANCE FITTER: person authorized for routine maintenance of the lift.The end user can only use the machine in correct way as defined in instruction.Loose clothes shall not be used protection cap shall also be used for long hair person, etc.The end user should provide the MSDS (Material Safety Data Sheet) at easy accessible place when providing lubrication.CHAPTER 1 DESCRIPTION OF THE MACHINEThe 2-post electro-hydraulic lift is a fixed installation. This means that it is anchored to the ground and built for lifting and positioning automobiles and vans at a certain height off the ground.The lift consists of the following main parts:1. Fixed structure (posts + upper beam);2. Mobile units (carriages + arms);3. Lift units (2 hydraulic cylinders + power unit);4. Control box;5. Safety devices;Figures 3 and 4 illustrate the various parts of the lift and the work areas reserved for use by operators around the lift.Command side: this side of the lift includes the area reserved for the operator to access the control box.Service side: this is the opposite side of the command side.Front side: the side with the short arms.Rear side: the side with the long arms.Fig.31.1 FIXED STRUCTURE (FIG.4)This structure consists of:1. 2 posts, (service 15 and command 3 side post) built with bent steel plate. The base is welded to adrilled plate to be anchored to the floor. The electric control box 4 and the hydraulic power unit 5 are attached to the command post. Inside each post are the moving parts to lift the vehicles. The control panel and the hydraulic unit are fixed to the command post.2. An upper beam 1,17 built with bent steel plate, connecting the upper posts with bolts.Fig.41.2 MOVING UNITS (SEE FIG.4)Each unit consists of:1. Both carriage (10 and 14) built with welded steel plate. It joints by chain 8 and the steel wire 7,and at the bottom to the lift arms by means of pins.The carriage moves along the post, guided by plastic sliding pads, located inside the post itself.2. Two telescopic arms, one long (13) and one short (12), built with tubular steel with a pad at eachend that can be height adjusted to hold the car and on the opposite side the carriage connection hole.1.3 LIFT UNIT (SEE FIG.4)It consists of:1 2 hydraulic cylinders (10), the carriages run by chains, and the cable keep both of them inparallel.1.4 HYDRAULIC POWER UNIT (FIG.5)The hydraulic power unit consists of:1. An electric motor2. A geared hydraulic pump3. Descent hand-valve equipped with a manual oil drain valve (see the use and maintenancechapter)4. A maximum pressure valve5. Oil tank6. An oil delivery and return flexible pipe to the cylinders feeding circuitNote: The oil delivery pipe may be under pressure1.5 CONTROL BOX (FIG.6)The panel that houses the electric control box contains the following:1 Main switch2 Rise push button3 Down push button4 Lock push buttonFig.5 Hydraulic power unit Fig.6 Control panel1.6 SAFETY DEVICEThe safety devices include:1 Mechanical safety device for carriage2 Arms locking system3 4 foot guards on the arms4 A synchronous device to control the carriages movement.5 2 post end limit switches6 General electric safety devices7 General hydraulic safety devicesThese safety devices will be described in further detail in the following chaptersCHAPTER 2 TECHNICAL SPECIFICATIONSCAPACITY……………………………………………4000kg(39200N)Car max lifting height…………………………………1820mmLift min stand height………………………………….100mmClearance between carriages………………………….2760mmTotal width……………………………………………3640mmLong arm maximum len gth………………………….1330mmLong arm minimum length…………………………..845mmShort arm maximum length………………………….1050mmShort arm minimum length…………………………..685mmRise time with three-phase motor……………………≤60secRise time with single-phase motor……………… ….≤75secDescent time…………………………………………18≤t≤40secTotal lift weight………………………………………about 850kgNoise………………………………………………….≤70db (A) 1mOperating temperature……………………………….5℃/40℃Work environment: …………………………… ……closed roomRelative humility……………………………………..90%Sea level height (3500)Fig.7 Dimensions and overall clearances2.1 ELECTRIC MOTORThe motor must be connected with reference to the attached wiring diagrams.The motor rotation wise must be the same as shown by the arrow on the pump: if not, modify the electrical connections (see ch.4.INSTALLATION-electric plant connection)2.2 HYDRAULIC UNIT PUMP2.3 OILThe oil reservoir contains hydraulic mineral oil in accordance with ISO/DIN 6743/4 with a level of contamination that does not exceed class 18/15 according to ISO 4406, for example IP HYDRUS OIL 32; SHELL TELLUS OIL T32 or equivalent.2.4 HYDRAULIC OIL DIAGRAMFig.8 Principle of Hydraulic PartKM SADOWNLOCKKTSBDSBLYA2YA1KTYVYA3YA4UP KTSQ1SBUKM+U124V 160VAT FU16A-FU22APEL3L1 1.5mm20223231I>I>QL2I>SQ2UWV 1112141516172122123456131078DOWNLOCKKTSBDSBLYA2YA1KTYVYA3YA4UP KTSQ1SBUKM+U124V 160VAT FU16A-FU22A20223231SQ2111214151617212213107KM SA UPE NL1.5mmI>Q12N2.5 VEHICLE WEIGHT AND SIZELift rack can be adapted to virtually all vehicles no heavier than 4000kg, the dimensions of which donot exceed the following.2.6 MAXIMUM DIMENSIONS OF VEHICLES TO BE LIFTEDMax width: 2400mmMax wheelbase: 3000mmThe underbody of cars with low ground clearance may interfere with the structure of the lift .Pay particular attention in the case of low body sports cars.Always keep the capacity of the lift in mind in the case of vehicles with particular characteristics. THE SAFETY area will be determined by the dimensions of the vehicle.CHECK OF LARGER VEHICLES. MAXIMUM WEIGHT OF THE VEHICLE TO BE LIFTFig.11 Weight distributionCHAPTER 3 SAFETYIt is vital to read this chapter of the manual carefully and from beginning to end as it contains important information regarding the risks that the operator and the maintenance fitter may be exposed to in the eventuality that the lift is used incorrectly.The following text contains clear explanations regarding certain situations of risk or danger that may arise during the operation or maintenance of the lift, the safety devices installed and the correct use of such systems, residual risks and operative procedures to use (general and specific precautions to eliminate potential hazards).Lift is designed and built to lift vehicles and hold them in the elevated position in a closed workshop. All other uses are unauthorized; in particular, the lift is not suitable for:-Washing and respire work;-Creating raised platforms or lifting personnel;-Use as a makeshift press for crushing purpose;-Use as goods lift-Use as a jack for lifting vehicles or changing wheels.THE MANUFACTURE DISCLAIMS ALL LIABILITY FOR INJURY TO PERSONS OR DAMAGE TO VEHICLES AND OTHER PCABLERTY CAUSED BY THE INCORRECT AND UNAUTHORISED USE OF THE LIFT.During lift and descent movements, the operator must remain in the command station as defined in figure 15. The presence of persons inside the danger zone indicated in the same figure is strictly prohibited. The presence of persons beneath the vehicle during operations is permitted only when the vehicle is parked in the elevated position.DO NOT USE THE LIFT WITHOUT PROTECTION DEVICES OR WITH THE PROTECTION DEVICES INHIBITED. FAILURE TO COMPLY WITH THESE REGULATIONS CAN CAUSE SERIOUS INJURY TO PERSONS, AND IRREPERABLE DAMAGE TO THE LIFT AND THE VEHICLE BEING LIFTED.Fig.12 Working Area3.1 GENERAL PRECAUTIONSThe operator and the maintenance fitter are required to observe the prescriptions of accident prevention legislation in force in the country of installation of the lift.Furthermore, the operator and the maintenance fitter must:1. Always work in the scheduled working area as shown in the manual.2. Never remove deactivate the guards and mechanical, electrical, or other types of safetydevices.3. Read the safety notices affixed to the machine and the safety information in this manual.In the manual all safety notices are shown as follows:DANGER: indicates imminent danger that can result in serious injury or death.WARNING: indicates situations and /or types of maneuvers that are unsafe and can cause injuries of various degrees or death.CAUTION: indicates situations and /or types of maneuvers that are unsafe and can cause minor injury to persons and /or damage the lift, the vehicle or other psaltery.3.2 RISKS OF ELECTRIC SHOCK:Specific safety notice affixed to the lift in areas where the risk of electric shock is particularly high.3.3 RISKS AND PROTECTION DEVICESWe shall now examine the risks to which the operator and the maintenance fitters may be exposed when the vehicle is immobilized in the raised position, together with the protection devices and adopted by the manufacture to reduce all such hazards to the minimum.3.4 LONGITUDINAL AND LATERAL MOVEMENTLongitudinal movement is considered the backward and forward shifting of the load.Lateral movement implies the shifting to the left or right of the vehicle, especially during the lifting phase on the rack.These movements can be avoided by positioning the vehicle correctly on the arm disk support plates, which must be previously adjusted to the same height (by loosening or tightening) as the vehicle.Do not move the vehicle in relation to the arms or adjust arms and disk support plates until the arms have been totally lowered, i.e. the disk support plates must be free from all contact with the vehicle.Fig.13 Risk of vehicle fallWARNINGDO NOT ATTEMPT TO MOVE THE VEHICLE WHEN IT IS RESTING ON THE DISK SUPPORT PLATES.It is important to position the vehicle on the lift so that the weight is correctly distributed on the arms (Fig.14) for person and equipment safety, it is important that:1. People rest inside the safety area while the vehicle raising (Fig.12)2. The engine is off, the clutch engaged and the parking brake pulled.3. The vehicle is correctly positioned. (Fig.14).4. Only authorized vehicle (Fig.10-11) are raised without exceeding the rate capacity and overalldimensions.Fig.14 correctly loaded vehicle3.5 RISKS WHILE THE VEHICLE IS BEING RAISEDThe following safety devices have been installed to protect against overweight conditions and equipment failure:1. The thermal relay in the electric box will trip if the motor is overloaded.2. The maximum pressure valve (fig.15), located on the hydraulic oil power unit, will trip if the liftis overloaded.3. In case of a sudden, great leakage in the hydraulic circuit (a broken pipe), the blocking valves,at the bottom of each cylinder, will trip (fig.16).4. If the lift reaches to the maximum height, push the button to stop it(Fig.17).5. Keep both cables in balance during raising or lowering (Fig.18).6. If the hydraulic cylinder breaks, the safety wedges will trip (fig.19), located inside the posts.The wedges are pushed by the spring and immediately stop the carriage preventing their descent.Fig.15 Fig.16Fig.17 Fig.18Fig.197. If the moving part exceed its travel distance, on the upper part of the command post there istwo limit switches connected in series and are usually set working by the “actuator”(fig.17) on the command side carriage. If the first limit switch did not work, the second one would trip after 3sec of carriage run.8. In case of total breakdown of the limit swatches, the carriage will stop a few mm higher,because the hydraulic cylinders come to end stroke, will cause the maximum pressure valve (on hydraulic unit) to trip.3.6 RISKS OF PERSONSThis paragraph illustrates risks to which the operator, maintenance worker, or any person near the operating area of the lift may be exposed in the case of impeccable use of equipment.3.6.1 RISK OF CRUSHING (OPEARATOR)Possible if the operator controlling the lift is not in thespecified position at the command panel. When theplatform and the vehicle are descending, theoperator must never be partly or completelyunderneath the moving structure. During this phasethe operator must remain in the command zone(Fig.20).Fig.203.6.2 RISK OF CRUSHING (PERSONNEL)When the platform and the vehicle are descendingpersonnel are prohibited from entering the areabeneath the moving parts of the lift. (Fig.21) .the liftoperator must not start the maneuver until it hasbeen clearly established that there are no persons inpotentially dangerous positions.Fig.213.6.3 RISK OF IMPACTCaused by the parts of the lift or the vehicle thoseare positioned at head height. When, due tooperational reasons, the lift is immobilized atrelatively low elevations (less than 1.75m from theground) personnel must be careful to avoid impactwith parts of the machine not marked with specialhazard coloring (Fig.22).Fig.223.6.4 RISK DUE TO VEHICLE MOVEMENTMovement may be caused during operations, whichinvolve force sufficient to move the vehicle (fig.23). Ifthe vehicle is of considerable dimensions or weight.Movement may lead to overload or unbalancing; allmeasures must be taking to avoid such anoccurrence.3.6.5 RISK OF VEHICLE FALLING FROM LIFTThis risk could be caused by the incorrectpositioning on the arm disk support plates (Fig.24) orin incorrect position of the arm disk support plates inrelation to the lift.Fig.24NEVER BOARD THE VEHICLE AND/OR TURNTHE ENGINE ON WHEN LIFT IS RAISED (FIG.25) Fig.25NEVER LEAN OBJECTS AGAINST THE POSTSOR LEAVE THEM IN THE AREA WHERE MOVINGPARTS ARE LOWERED.This could hamper lowering or cause the vehicle tofall from the rack (Fig.26)3.6.6 SLIPPINGThis risk may arise due to spillage of lubricants inthe surrounding area (fig.27).ALWAYS KEEP THE AREA SURROUNDING THELIFT CLEAN BY REMOVING ALL OIL SPILLS.To avoid the risk of slipping, make use of therecommended personal protection (anti-slipfootwear).Fig.273.6.7 RISK OF ELECTRIC SHOCKRisk of electric shock in areas of the lift housingelectric wiring. Do not use jets of water, steam (highpressure wash units), and solvents Or paint in theimmediate vicinity of the lift, and take special care tokeep such substances clear off the electricalcommand panel (fig.28).Fig.283.6.8 RISK OF COMPONENT FAILURE DURINGOPERATION.The manufacturer has used appropriate materialsand construction techniques in relation to thespecified use of the machine in order to manufacturea reliable and safe lift. Note however, that the liftmust be used in conformity with the manufacturersprescriptions and the frequency of inspections andmaintenance work recommended in chapter 6“MAINTENANCE” must be observed.Fig.293.6.9 RISK RELATED TO IMPROPER USEPersons are not permitted to stand or sit on theplatforms during the lift maneuver or when thevehicle is already lifted(fig.29). All uses of the liftother than the uses for which it was designed areliable to give rise to serious accidents involving thepersons working in the immediate vicinity of the unit.It is therefore essential to adhere scrupulously to allregulations regarding use, maintenance and safetycontained in this manual.3.7 SAFETY INSTRUCTINS FOR SERVICING1. Maintenance or repair work by authorized service personnel only.2. Turn off and padlock the main switch before doing any maintenance,or repair work.3. Work on pulse generators or proximity switches by authorized service personnel only.4. Work on the electrical equipment by certified electricians only.5. Do not replace or override the safety devices.6. Ensure that ecologically harmful substances are disposed of only in accordance with theappropriate regulations.CHAPTER 4 INSTALLATIONTHE FOLLOWING OPERATIONS MUST BE PERFORMED EXCLUSIVELY BY SPECIALISED TECHNICAL STAFF WITH AUTHORISATION FROM THE MANUFACTURER OR LICENSED DEALER. IF THESE OPREATIONS ARE PERFORMED BY OTHER PERSONS, SERIOUS PERSONAL INJURY AND/OR IRREPERABL DAMAGE TO THE LIFT UNIT MAY RESULT.4.1 INSTALLATION REQUISITE CHECKLISTThe lift is designed for installation in enclosed areas suitably protected from the weather. The place of installation must be well clear of areas destined to washing or painting, and away from solvent or paint storage areas or areas where there is a risk of potentially explosive atmosphere.SUITABILITY OF THE DIMENSIONS OF THE PLACE OF INSTALLATION AND SAFTY CLEARANCE.The lift must be installed in observance of the clearances between walls, pillars, other machines, etc. indicated in figure 30 and incompliance with any legislative requirements in the county of installation.Check in particular:1. Minimum height: 5000mm inclusive of height of vehicle, maximum height of arms,( i.e. 1900mm),and upper post height (i.e.2828mm)2. minimum distance from walls: 600mm3. Minimum working area: 700mm4. Area for command station5. Area for maintenance, access and emergency escape routes.6. Position in relation to other machines7. Proximity to power supply for trouble-free hook-upFig. 304.2 LIGHTENINGAll parts of the machine must be uniformly lit with sufficient light to assure that the adjustment and maintenance operations specified in the manual can be performed, and without areas of shadow reflected light, glare and avoiding all situations that could give rise to eye fatigue.The lighting must be installed in accordance with the laws in force in the place of installation (responsibility lies with the lighting equipment fitter)4.3 FLOORThe lift must be installed on a horizontal concrete bed with a minimum thickness of 200mm built and a resistance ≥30N/mm2.The floor must also be flat and level (10mm of tolerance for leveling). Consult the manufacturer with regard to special applications.Fig.324.4 ASSEMBLINGWARNINGDURING INSTALLATION ONLY AUTHORISED PERSONNEL IS ALLOWEDTo assemble the lift, the weight of the various parts is to be considered, in order to provide a lifting machine with the minimum capacity 500kgMax. Lifting height 2900mmBefore starting to assemble the lift, check the crate contains all the needed material.PUT COLUMN1. Position the base plate of both column of which the open side should be inner side oriented.Make sure the distance from up to bottom should be 2760mm. The thickness of the spacer is over 300mm to ensure the operation of installing safety devices, cables, oil pipe and wire.2. Install safety devices, which including solenoid, self-locking board and hook according to fig.33.Fig.333. Connect crossbeams to both columns to both columns to fig.34.(Notice that the limited switchedFig.344. Install the safety bar according to fig.35 and fig.36.Fig.35 Fig.36Fig.37 Fig.386. Connect the long hose inside both columns according to fig.40, tighten (upside connect to maincolumn and the down side connect with sub-column), and then fix the oil pipe by using clip. 7. Install the electrical box on the main column and then cross all the wires through holes andconnect with limited switch and solenoid.8. Put up the main column (Notice that the carriage engages in the ratchet and keep in the sameheight). Adjust the uprightness of the column and install the expansion bolt according to fig.32.9. Adjust two balance cables.4.4.2 HYDRAULIC PLANT1. Connect the pump on the connecting board according to fig.41 and then fix on the main column.2. Connect the hydraulic unit to the circuit crossing with a flexible pipe(Fig.40).3. Tight all the fittings very well, even the one already mounted by the manufacturer.4. Full the hydraulic unit tank with 8 liters of hydraulic oil ISO 32 as IP HYDRUS OIL 32, SHELLTELLUS OIL T32 or similar (See Ch.2, Technical specifications).5. Remove the oil filling cap and substitute it with the given drain cap.Fig.39。