加工中心自动换刀
五轴加工中心的自动换刀故障
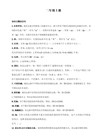
加工中心自动换刀功能及编程

加工中心自动换刀功能及编程加工中心自动换刀功能是通过机械手(自动换刀机构)和数控系统的有关控制指令来完成的。
换刀过程:装刀,选刀,换刀1.换刀过程(1)装刀:刀具装入刀库任选刀座装刀方式。
刀具安置在任意的刀座内,需将该刀具所在刀座号记下来。
固定刀座装刀方式。
刀具安置在设定的刀座内。
(2)选刀从刀库中选出指定刀具的操作。
1)顺序选刀:选刀方式要求按工艺过程的顺序(即刀具使用顺序)将刀具安置在刀座中,使用时按刀具的安置顺序逐一取用,用后放回原刀座中。
2)随意选刀:①刀座编码选刀:对刀库各刀座编码,把与刀座编码对应的刀具一一放入指定的刀座中,编程时用地址T 指出刀具所在刀座编码。
②计算机记忆选刀刀具号和存刀位置或刀座号对应地记忆在计算机的存储器或可编程控制器的存储器内,刀具存放地址改变,计算机记忆也随之改变。
在刀库装有位置检测装置,刀具可以任意取出,任意送回。
(3)换刀1)主轴上的刀具和刀库中的待换刀具都是任选刀座。
刀库一选刀一到换刀位一机械手取出刀具一装入主轴,同时将主轴取下的刀具装入待换刀具的刀座。
2)主轴上的刀具放在固定的刀座中,待换刀具是任选刀座或固定刀座。
选刀过程同上,换刀时从主轴取下刀具送回刀库时,刀库应事先转动到接收主轴刀具的位置。
3)主轴上的刀具是任选刀座,待换刀具是固定刀座。
选刀同上,从主轴取下的刀具送到最近的一个空刀位。
2.自动换刀程序的编制(1)换刀动作(指令):选刀(T XX);换刀(M06(2)选刀和换刀通常分开进行。
(3)为提高机床利用率,选刀动作与机床加工动作重合。
(4)换刀指令M06必须在用新刀具进行切削加工的程序段之前,而下一个选刀指令T常紧跟在这次换刀指令之后。
(5)换刀点:多数加工中心规定在机床Z轴零点(Z0),要求在换刀前用准备功能指令(G28使主轴自动返回Z0点。
(6)换刀过程:接到T XX指令后立即自动选刀,并使选中的刀具处于换刀位置,接到M06指令后机械手动作,一方面将主轴上的刀具取下送回刀库,另一方面又将换刀位置的刀具取出装到主轴上,实现换刀。
数控铣床自动换刀化改造(刀库式加工中心)

第一章绪论1.1 数控设备的发展历史>第一代数控系统:1952年至1959年,采川电子管元件。
>第二代数控系统:1959年开始,采刖晶体管元件。
>第三代数控系统:1965年开始,采川集成电路。
>第四代数控系统:1970年开始,采刖人规模集成电路及小型通用计算机。
>第五代数控系统:1974年开始,采用微处理机和微型计算机。
1.2 自动换刀系统的意义从换刀系统发展的历史米看,1956年日本富士通研究成功数控转塔式冲床,美国IBM公司同期也研制成功了“APT”(刀具程序控制装置)。
1958年美国K&T公司研制出带ATC(自动刀具交换装置)的加工中心。
1967年出现了FMS(柔性制造系统)。
1978年以后,加工中心迅速发展,带有ATC装置,可实现多种工序加工的机床,步入了机床发展的黄金时代。
1.1.1 加工中心加工中心机床的出现,加之CAD技术、信息技术、网络控制技术以及系统工程学的发展,为单机数控自动化向计算机控制的多机制造系统自动化方向发展,创造了必要的条件.计算机群控系统即直接数控(Direct NC-DNC)系统,就是这一发展趋向的具体体观。
DNC系统使用一台较大的计算机,控制与管理多台数控机床和数控加工中心,能进行多品种、多工序的加工。
加工中心机床配备有装载多把刀具的刀具库,有自动更换刀具的功能,一次装夹中可以完成钻、镗、铣、铰等工序,特别适用于箱体类零件的多面、多工序加工。
它能完成车削加工的同时,兼有铣、镗、钻孔、攻丝等功能。
1.1.2 柔性制造单元柔性制造单元(FMC)是由中心控制计算机、加工中心与自动交换工件(AWC,APC)装置所组成。
工件一次装夹后可在柔性制造单元中的加工中心上加工,使得加工的柔性(可编程性)、加工精度和生产效率更高。
在柔性制造单元中,中心控制计算机负责作业调度、自动检测与工况自动监控等功能。
工件装在自动交换工件装置(工作台)上在中心控制计算机控制下传送到加工中心上加工;加工中心接收中心控制计算机传送来的数控程序进行加工,并将工况数据送中心控制计算机处理,如工件尺寸自动检测和补偿,刀具损坏和寿命躲控等。
自动换刀原理
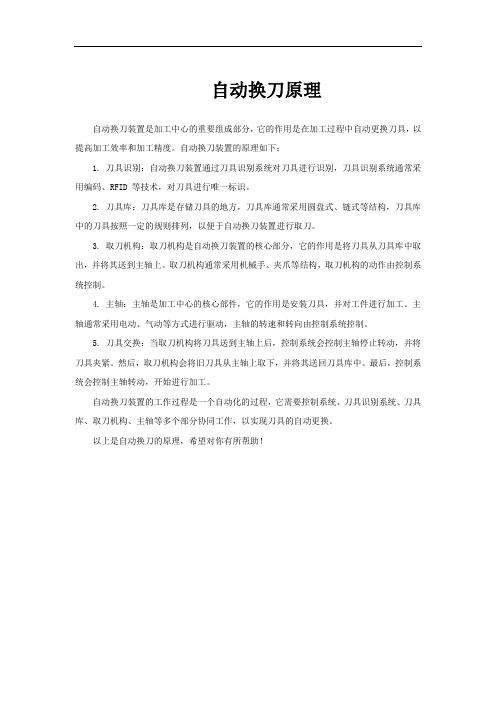
自动换刀原理
自动换刀装置是加工中心的重要组成部分,它的作用是在加工过程中自动更换刀具,以提高加工效率和加工精度。
自动换刀装置的原理如下:
1. 刀具识别:自动换刀装置通过刀具识别系统对刀具进行识别,刀具识别系统通常采用编码、RFID 等技术,对刀具进行唯一标识。
2. 刀具库:刀具库是存储刀具的地方,刀具库通常采用圆盘式、链式等结构,刀具库中的刀具按照一定的规则排列,以便于自动换刀装置进行取刀。
3. 取刀机构:取刀机构是自动换刀装置的核心部分,它的作用是将刀具从刀具库中取出,并将其送到主轴上。
取刀机构通常采用机械手、夹爪等结构,取刀机构的动作由控制系统控制。
4. 主轴:主轴是加工中心的核心部件,它的作用是安装刀具,并对工件进行加工。
主轴通常采用电动、气动等方式进行驱动,主轴的转速和转向由控制系统控制。
5. 刀具交换:当取刀机构将刀具送到主轴上后,控制系统会控制主轴停止转动,并将刀具夹紧。
然后,取刀机构会将旧刀具从主轴上取下,并将其送回刀具库中。
最后,控制系统会控制主轴转动,开始进行加工。
自动换刀装置的工作过程是一个自动化的过程,它需要控制系统、刀具识别系统、刀具库、取刀机构、主轴等多个部分协同工作,以实现刀具的自动更换。
以上是自动换刀的原理,希望对你有所帮助!。
加工中心的自动换刀系统

加工中心自动换刀装置
一、加工中心自动换刀装置的类型 1.转塔式 更换主轴换刀装置 (1)脱开主轴传动 (2)转塔头抬起 (3)转塔头转位 (4)转塔头定位 (5)主轴传动重新接通
加工中心自动换刀装置
加工中心自动换刀装置
加工中心自动换刀装置
一、加工中心自动换刀装置的类型 2.成套更换式 (1)更换转塔 (2)更换主轴箱 (3)更换刀库
六、几种典型换刀过程 1、无机械手换刀
加工中心自动换刀装置
加工中心自动换刀装置
六、几种典型换刀过程 2、机械手换刀
加工中心自动换刀装置
六、几种典型换刀过程 3、带刀套机械手换刀
加工中心自动换刀装置
加工中心自动换刀装置
二、加工中心刀库形式 2.链式刀库
加工中心自动换刀装置
二、加工中心刀库形式 3.格子式刀库
加工中心自动换刀装置
二、加工中心刀库形式 3.格子式刀库
加工中心自动换刀装置
三、加工中心刀库结构
加工中心自动换刀装置
三、加工中心刀库结构
加工中心自动换刀装置
四、JCS-018A加工中心机械手结构 2、机械手抓刀部分的结构
五、其他类型机械手 2、两手互相垂直的回 转式单臂机械手
加工中心自动换刀装置
五、其他类型机械手 3、两手平行的回转式单臂机械手
加工中心自动换刀装置
五、其他类型机械手 4、双手交叉式机械手 (1)机械手移动到机床主轴处-卸装刀具 (2)机械手移动到刀库处送回卸下的刀具
加工中心自动换刀装置
加工中心自动换刀装置
加工中心自动换刀装置
四、JCS-018A加工中心 机械手结构 2、机械手抓刀部分的 结构
பைடு நூலகம் 加工中心自动换刀装置
加工中心如何实现自动换刀

要实现自动换刀功能主要就是做长度补偿值,因为半径补偿值在软件编程时已经自动加入了。
本文以云南机床厂的加工中心为例,系统为西门子802C。
一、装刀
例如要装入T01、T02两把刀
1. 刀库先回零:按下回零键,再按启动按钮即可,此步骤也可不执行。
手动输入:
T01
TL
G40 G17 G71 G90 G54
......
TO2
TL
G40 G17 G71 G90 G54
......
TO3 Βιβλιοθήκη TL G40 G17 G71 G90 G54
......
M9
M30
%
TL(有的机床不需换行也能执行)
TL为此机床自带的换刀宏程序,,不同的机床此宏程序可能名称不同,用法也不同。
在主轴上装入要使用的一号刀,此时即为T01。
2.以T01来做基准刀具,直接对刀到工件坐标系(以G54为例)Z=0,输入到G54的Z值中,此刀的长度补偿值要为0。
二、程序
刀具号后面应加入零点偏移,如G54,
UG软件中,设置刀具参数时补偿寄存器一项填入数字1就输出D1,输入2就输出D2;
刀补D0必须取消,因为要使用刀补,默认D1不必显示,若刀补为D2时,必须应在程序中加入D2。
格式大致如下:
%_N_101_MPF
TO1
3.手动输入“T02 回车 TL”,此时T01入库,主轴上装入二号刀,即为T02;
对刀到Z=0,注意偏移值(即对刀时不能到达工件坐标系G54的Z向零点而做的偏移,如有对刀仪或偏置块时)。
4.在参数设置中找到2号刀,选择对刀(默认是D1),在偏移处输入偏移值(为正值),零点G处输入54,按计算即可算出T02的长度补偿值D1了。
fanuc加工中心换刀延时参数
fanuc加工中心换刀延时参数在fanuc加工中心的操作中,换刀延时参数是一个非常重要的设置。
换刀延时参数是指在进行自动换刀时,控制系统延迟执行换刀动作的时间。
这个参数的设置对于机床的稳定运行和加工效率都有着重要的影响。
我们需要了解fanuc加工中心自动换刀的工作原理。
当加工中心完成一道工序后,需要进行刀具的更换。
在自动换刀时,控制系统会发送指令,让换刀装置进行刀具的卸载和安装。
而换刀延时参数就是控制系统在发送换刀指令后,延迟执行实际换刀动作的时间。
这个时间的设置,可以影响到换刀的准确性和稳定性。
在实际操作中,换刀延时参数的设置需要根据具体的加工情况来进行调整。
如果设置的时间过短,可能会导致在换刀时,刀具未完全卸载或安装好,从而影响加工的精度和安全性。
而如果设置的时间过长,可能会影响整个加工流程的效率。
合理地设置换刀延时参数对于保证加工质量和提高加工效率至关重要。
在进行换刀延时参数的调整时,还需要考虑到不同加工物料的特性以及不同加工工序的要求。
对于硬度较高的工件,可能需要更长的换刀延时参数,以确保刀具的安全更换。
而在进行精密加工时,可能需要更短的换刀延时参数,以提高加工效率。
个人观点上,我认为在fanuc加工中心的操作中,合理地设置换刀延时参数是非常重要的。
只有通过综合考虑加工工艺、加工材料和加工精度的要求,才能够更好地调整换刀延时参数,从而实现稳定、高效的加工过程。
fanuc加工中心换刀延时参数的设置对于加工质量和加工效率都有着重要的影响。
需要我们根据具体情况综合考虑,合理地设置换刀延时参数,以确保加工过程的稳定性和高效性。
希望本文的解读可以帮助读者更好地理解和应用这一参数。
fanuc加工中心换刀延时参数的设置有很多方面需要注意。
操作人员需要根据加工材料的特性,确定合适的换刀延时参数。
对于硬度较高的材料,换刀延时参数可能需要设置得更长,以确保刀具安全更换。
而对于一些易变形的材料,则可能需要更短的换刀延时参数,以避免对工件造成影响。
加工中心的刀库形式与自动换刀程序的调试
加工中心的刀库形式与自动换刀程序的调试————————————————————————————————作者:————————————————————————————————日期:ﻩ加工中心的刀库形式与自动换刀程序的调试一、实训目的( 1 )了解加工中心的各种刀库形式;( 2 )了解机械手换刀的基本动作组成;( 3 )掌握加工中心自动换刀程序的编写与调试运行;二、预习要求认真阅读加工中心组成、换刀装置、自动换刀程序的编写等章节内容。
三、实训理论基础1 .加工中心的刀库形式加工中心刀库的形式很多,结构各异。
常用的刀库有鼓轮式和链式刀库两种。
图 11-1鼓轮式刀库( a )径向取刀形式( b )轴向取刀形式 ( c )径向布置形式( d )角度布置形式鼓轮式刀库结构简单,紧凑,应用较多。
一般存放刀具不超过32 把。
见图 11-1。
径向取刀形式( a )多用于使用斗笠式刀库的立式加工中心和使用角度布置的机械手换刀装置的加工中心;形式( b )应用比较广泛,可用于立式和卧式加工中心,换刀可用机械手或直接主轴移动式换刀。
由于从布局设计方面的考虑,鼓轮式刀库一般都采用侧向安装的结构形式,若用于机械手平行布置的加工中心时,刀库中的刀袋(座)通常在换刀工作位可作90 o 翻转。
形式( c )多用于小型钻削中心;形式( d )一般用于专用加工中心。
链式刀库多为轴向取刀,适于要求刀库容量较大的加工中心。
见图11-2 。
图 11-2 链式刀库2 .自动换刀装置及其动作分解斗笠式刀库换刀装置我们已经在实训 4 中接触过,在此就不再赘述。
对于刀库侧向布置、机械手平行布置的加工中心,其换刀动作分解见图11-3。
换刀时,Txx指令的选刀动作和M6指令的换刀动作可分开使用。
图 11-3平行布置机械手的换刀过程图11-4 角度布置机械手的换刀过程对于刀库侧向布置、机械手角度布置的加工中心,其换刀动作分解见图 11-4 。
机械手换刀装置的自动换刀动作如下:(1)主轴端: 主轴箱回到最高处( Z 坐标零点),同时实现“主轴准停”。
自动换刀装置的形式---回转刀架换刀
8.4.1 自动换刀装置的形式自动换刀装置是加工中心的重要执行机构,它的形式多种多样,目前常见的有以下几种。
1.回转刀架换刀数控机床使用的回转刀架是最简单的自动换刀装置,有四方刀架、六角刀架,即在其上装有四把、六把或更多的刀具。
回转刀架必须具有良好的强度和刚度,以承受粗加工的切削力:同时要保证回转刀架在每次转位的重复定位精度。
图8-17为数控车床六角回转刀架,它适用于盘类零件的加工。
在加工轴类零件时,可以用四方回转刀架。
由于两者底部安装尺寸相同,更换刀架十分方便。
图8-17 数控车床六角回转刀架1-活塞2-刀架体3、7-齿轮4-齿圈5-空套齿轮6-活塞8-齿条9-固定插销10、11-推杆12-触头回转刀架的全部动作由液压系统通过电磁换向阀和顺序阀进行控制,它的动作分为4个步骤:(1)刀架抬起当数控装置发出换刀指令后,压力油由a孔进入压紧液压缸的下腔,活塞1上升,刀架体2抬起,使定位用的活动插销10与固定插销9脱开。
同时,活塞杆下端的端齿离合器与空套齿轮5结合。
(2)刀架转位当刀架抬起后,压力油从c孔进入转位液压缸左腔,活塞6向右移动,通过联接板带动齿条8移动,使空套齿轮5作逆时针方向转动。
通过端齿离合器使刀架转过60º。
活塞的行程应等于齿轮5分度圆周长的1/6,并由限位开关控制。
(3)刀架压紧刀架转位之后,压力油从b孔进入压紧液压缸上腔,活塞1带动刀架体2下降。
齿轮3的底盘上精确地安装有6个带斜楔的圆柱固定插销9,利用活动插销10消除定位销与孔之间的间隙,实现反靠定位。
刀架体2下降时,定位活动插销10与另一个固定插销9卡紧,同时齿轮3与齿圈4的锥面接触,刀架在新的位置定位并夹紧。
这时,端齿离合器与空套齿轮5脱开。
(4)转位液压缸复位刀架压紧之后,压力油从d孔进入转位液压缸的右腔,活塞6带动齿条复位,由于此时端齿离合器已脱开,齿条带动齿轮3在轴上空转。
如果定位和夹紧动作正常,推杆11与相应的触头12接触,发出信号表示换刀过程已经结束,可以继续进行切削加工。
加工中心的刀库形式与自动换刀程序的调试
加工中心的刀库形式与自动换刀程序的调试加工中心是一种用于在机械制造业中进行高精度、高效率切削加工的设备。
在加工中心中,刀具是起到关键作用的工具,因此刀具的选择和使用十分重要。
为了提高生产效率,减少人力成本,加工中心通常配备有刀库和自动换刀程序。
刀库是用于存放和组织各种刀具的设备,可以是一个简单的工具车,也可以是一个复杂的机械自动刀库。
刀库的形式直接影响到刀具的快速更换和选择的便捷性。
刀库的形式通常有以下几种:1.手动刀库:这是一种简单的刀具存放方式,操作人员需要手动将刀具放入和取出刀库。
这种方式比较容易实现,但是效率较低,不适合高产量的生产。
2.机械式刀库:这是一种半自动的刀具存放方式,刀具的放入和取出通过机械装置来实现。
操作人员只需按下相应的按钮或操作面板上的控制按钮,机械装置就会按照预定的程序进行刀具的换取。
这种方式相对于手动刀库来说效率更高,但仍然需要操作人员的参与。
3.自动式刀库:这是一种完全自动的刀具存放方式,刀具的放入和取出由机械装置自动完成。
机械装置按照预定程序自动和选择需要的刀具,并将其取出并装入主轴。
这种方式适用于高产量、高频率的生产,减少了人工干预的时间和机会。
刀库形式的选择取决于生产的具体要求和预算,需要根据实际情况进行选择。
自动换刀程序是用于控制刀具换取的程序,其目的是实现对刀具的快速且精确的换取。
自动换刀程序的调试主要包括以下几个步骤:1.刀具测量:在自动换刀程序调试之前,需要进行刀具的测量,包括刀具长度、半径等参数的测量,以确保程序的准确性。
刀具测量可以使用专门的刀具测量仪进行,也可以使用机床自带的刀具测量功能进行。
2.建立工件坐标系:在自动换刀程序中,需要指定刀具在切削时的位置,而刀具的位置是相对于工件坐标系来确定的。
因此,在调试自动换刀程序之前,需要先建立工件坐标系,并确定刀具换取位置的坐标。
3.轨迹规划:自动换刀程序需要通过规划刀具换取的轨迹来实现换取操作。
轨迹规划的目标是确保刀具在换取过程中的安全性和准确性。
- 1、下载文档前请自行甄别文档内容的完整性,平台不提供额外的编辑、内容补充、找答案等附加服务。
- 2、"仅部分预览"的文档,不可在线预览部分如存在完整性等问题,可反馈申请退款(可完整预览的文档不适用该条件!)。
- 3、如文档侵犯您的权益,请联系客服反馈,我们会尽快为您处理(人工客服工作时间:9:00-18:30)。
本文主要对数控加工中心自动换刀系统及控制系统进行设计。
本文主要对数控加工中心自动换刀系统及控制系统进行设计。
第一,了解数控加工中心的分类,其按换刀形式的分类以及加工中心刀库的形式;然后根据给定的参数进行刀库类型的选择以及电动机的确定;接着对刀库的转位定位机构进行了设计;最后是对于控制系统进行了简单设计。
关键字:加工中心,换刀系统,刀库,PLC。
目录1 绪论 (3)2.................................................................................................... 刀库的总体设计方案 (5)2.1课程设计的任务及要求 (5)2.2刀库的类型选择 (5)3...................................................................................................... 电机的选择. (6)3.1电机的选型及相关参数 (6)3.2各部分转动惯量的计算 (6)3.3预选电机 (6)3.4电机的校核 (7)4.................................................................................................... 机械系统的设计 . (7)4.1刀库转动定位机构的设计 (7)4.2滚动轴承的选择计算 (9)4.2轴的校核计算 (10)4.3键的设计计算 (10)5.................................................................................................... 控制系统的设计 . (11)5.1 刀库的换刀动作如下: (11)5.2 利用PLC 实现随机换刀 (12)参考文献 (15)1 绪论在现代数控机床中,加工中心(MC-Machining Center) 能进行自动换刀、自动更换工件,实行平面、任意曲面、 孔、螺纹等加工,成为一种独特的多功能高精、高效、高 自动化的机床,并迅速向高速化、复合化、环保化、五轴 联动等方向发展,己成为当今国际机床展上最大的亮点。
加工中心特别适合于箱体、框架、叶片等特殊复杂零 件的柔性高效加工,能减省一些普通铣床、钻床、键床, 提高加工精度和效率,减少转换时间,降低生产成本。
在当今机械工业中,产品不断向个性化、精密化、小 批量发展,世界对 MC 的市场需求在不断增多。
特别是在要 求适量柔性、大批高效生产的汽车工业、单件、小批重切、 快速生产的航空、模具工业以至 IT 高精尖工业中,MC 已逐 渐成为重要的高效性机种。
1996 年国产加工中心与进口加工中心的台数比,仅为 百分之几,到 2005 年逐步增长到 39.4%。
2005 年与 2000 年相比,进口的加工中心数量增加 4.8 倍。
加工中心需求 猛增的主要原因,大致有三:(l)整个机械工业原有工艺装 备结构陈旧、性能落后,呈“三多三少”(手动的多、自动 的少;粗加工的多、精加工的少;低效的多、高效的少),函 需大量更新。
能源、交通、冶金、发电、工程机械、造船、 模具、IT 各业均需购置大、中、小各种 Mc ,量大面广;(2) 汽车工业迅速发展,2002-2004 年汽车产量分别为 325、444、 507 万辆,发动机缸体、缸盖、变速箱及各种汽车零部件加 工,均需增添高速、高精、环保、节能的各式 MC;(3)航空、 国防、军工产业,适应新形势发展,均在提高生产能力, 需要大、中型各种立式、卧式、龙门式、五轴控制的高性 能 MC ,而且要求品种多、质量好、供货快。
加工中心进口的快速增加,一方面反映了我国制造业 对这类数控机床的需求旺盛,另一方面也反映了我国机床 制造业在加工中心的生产能力和国产加工中心的竞争力上 还存在差距。
国产加工中心市场占有率低的主要原因是国 产加工中心在产品水平、交货期、质量和可靠性上与国外L h =86750 (h) 验算结果:合格。
同类产品相比存在不少差距。
因此研究加工中心及其控制系统具有现实和长远的意义,掌握其中的关键技术是充分发挥加工中心功能和性能的先决条件,必将对我国装备制造业的整体水平的提高起到积极的作用。
图 1-1 立式数控铣床2.刀库的总体设计方案2.1课程设计的任务及要求设计题目:数控加工中心自动换刀系统设计设计要求:设计一个立式数控加工中心自动换刀系统的刀库装置及其控制系统,主要性能指标参数如下:刀库载刀量:8 把;刀具形式:BT40 ;刀具直径:Φ 63mm ;刀盘最低转速:60r/min ;刀架水平运动行程240mm ;采用PLC控制。
2.2刀库的类型选择目前一般刀库按结构形式可以分为以下几种:1)刀具储存在圆型鼓轮上,这种刀库结构简单,但刀具环形排列,空间利用率低,为了不致于刀库外径过大导致转动惯量过大,一般刀库容量在32把以下。
使刀库中处于换刀位置的刀具轴线平行于主轴轴线,以简单的回转式机械手对刀库和主轴进行交换。
要求刀库容量较大的场合,可以采用空间利用率较高的多重型鼓轮式刀库,这种刀库的传动装置和控制装置较为复杂。
2)链式刀库。
刀具储存在链条环节上,再以链轮驱动,结构紧凑,刀库容量较大,链环的现状可以根据机床的布局配置成各种形状,也可以将换刀位置突出以利换刀。
当链式刀库需要增加刀库容量时,只需增加链条的长度,在一定的范围内,无需变更线速度及惯量,这种条件对系列刀库的设计与制造带来了很大的方便,可以满足不同的使用条件。
3)盒式刀库。
刀具储存在纵横排列的格子上,此种刀库空间利用率最高,刀库容量大。
4)转塔式刀库。
刀具储存在同一转塔上,其主要特征是刀库环绕是主轴,储刀位置即为主轴位置,因储存刀具数量有限,主要用于小型加工中心。
5)斗笠式刀库。
斗笠式刀库由于其形状像个大斗笠而得名,一般存储刀具数量不能太多,10~24把刀具为宜,具有体积小、安装方便等特点,在立式加工中心中应用较多。
加工中心的一个很大优势在于它有ATC装置,使加工变得更具有柔性化。
根据以上几种刀库的类型,立式加工中心的具体工作状态所需,所以选择斗笠式刀库。
3.电机的选择3.1 电机的选型及相关参数最大转矩(N*m) 2.2 7.8 16最高转速(r/min) 3000 2000 20002转子转动惯量(Kg m2) 7.310-5 3.610-4610-4(1)刀盘:J = 1m D 2= 1 3.560.252= 0.1113(2)轴:1mL2= 1 4.350.1352= 0.0264(3)刀具:J =m(R2+3r2)=83(0.1152+30.012) = 0.3192(4)槽轮:J =m (R2+r2)= 4.85(0.12+0.052)=0.0303(5)锁止盘:J =m (R2+r2)=1.634(0.12+0.042)=9.4810-3(6)套筒:J =mr2=0.0680.0252+0.1290.0252=1.2310-4 3.3 预选电机若选 200W,则J M= 3.610,最高转速为2000r/min 速比:预选电机200W n 2000 100n mc 60 3 可知:nJ =J ( nc)2 =(0.1113+0.0264+0.3192+0.0303+nmc1000.0095+0.0001)(100)2= 0.44710-33)电机的最大启动转矩:T =Tcam +T = 0.845 + 0.0807 =1.652 7.8 通过上述校核,得出电机符合要求。
加速装置采用XB1型通用谐波减速器,减速比 100:3,输 出轴径 20mm 。
4.1 刀库转动定位机构的设计自动换刀装置为了实现快速可靠,应该满足三点要求:①运动平稳、无冲击,即最大加速度和最大速度要小。
② 各相邻动作可重叠者,要按其规律尽量多重叠。
③各个动 作要可靠。
为了实现自动换刀装置的功能,可以通过电、 液、气、机联合实现需要的动作。
常用的间歇运动机构有:1)弧面分度凸轮机构和圆柱分度凸轮机构; 2)平行凸轮机构; 3)槽轮机构; 4)改良型槽轮机构; 5)余摆线机构根据实际工作情况与目前以上几种间歇机构的特点,选择机械部分结构采用槽轮机构,槽轮机构是20世纪初就 开始使用的间歇运动机构,也是成本最低的结构。
槽轮机 选用槽轮机构折算到电机上的 负载惯量J = 0.44710-3kg •m 2JL= 0.44710-3 =1.24惯量比: J M0.3610-3,满足 20 倍以下的要求。
由此可知刀库系统的转动惯量为:J =J +J = 0.44710-3+ 0.3610-3 = 0.80710-33.4 电机的校核(1)由摩擦引起的摩擦力矩:T G R = 0.1538.590.0678= 0.392 1.0 (2)最大加速转矩:惯量比在20倍以 内,满足要求 刀库系统的转动 惯量J = 0.80710-3kg •m 22nC max60t Ca= 0.80710-3 2• 2000 600.2= 0.845 T FC T额定T Cam T最大所以电机符合要 求 选用XB1 型谐波 齿轮,减速比 100:34.机械系统的设计构(又称马尔他机构)能把主动轴的匀速连续运动转换为从 动轴的周期性间歇运动,常用于各种分度转位机构中。
槽 轮机构有三种基本类型:外啮合槽轮机构、内啮合槽轮机 构和球面槽轮机构。
立式加工中心斗笠式刀库采用外啮合 槽轮机构。
该刀库可容纳8 把刀具,即槽轮的齿数为 8。
刀库的回 转选刀由刀库电机通过减速器带动曲柄回转,曲柄每回转 一周,槽轮转过 45°,刀库刀盘转过一个刀位,并由锁止盘 定位。
刀库上的刀位信号由两只开关联合发出,在刀库的 一号刀位上安装一只挡铁,在支架上安装一只检测开关, 机床开机后,刀库自动回转寻找一号刀位(基准刀位),当 一号刀位上的挡铁触发支架上检测开关后刀库停止回转, 刀库的当前刀位为一号刀位,刀库处于初始状态。
其余刀 位信号由安装在曲柄上的挡铁触发刀位检测开关进行累计 计数,曲柄每回转一周即刀库转过一个刀位触发一次。
通 过控制刀库电机的旋转方向,实现刀库的双向选刀。
综上所述:故刀库转动定位机构选择平面单销外槽轮 机构。
具体计算参数如下:锁止弧半径:R x = R 1 - r - e = 61.6 -8.6 2 = 44.4考虑具体装配要求,取20.1 由于槽轮的角加速度变化较大,且在转位过程的前半360槽间角:22 =8= 45槽轮每次转位时曲柄的转角:21=180-22=135槽数:z=8; 槽轮与锁止盘间的中心距:L=100.54mm ; 主动曲柄长度:R 1 = L sin2=100.54sin 22.5 = 38.47 根据装配要求,取61.6槽轮半径:R 2 = L cos2=100.54cos22.5 = 93 ,取100圆销半径: 槽底高:= 61.6 6 =10.27,取8.6b = L -(R +r )-(3~5)=100.54-(61.6+8.6)-4=26.34槽间角45槽数 8中心距 100.54 曲柄长 61.6槽轮半径 100圆销半径 8.6锁止弧半径 20.1阶段与后半阶段的角加速度方向不同,因此当槽与滚子之间存在间隙时,会产生冲击。