挤压与拉拔复习题(改)
轴向拉伸与压缩和剪切挤压练习题

轴向拉伸压缩练习题一、判断题:1.在弹性范围内,杆件的正应力和正应变成正比。
(对)2.轴向拉压杆横截面上,只有一种内力,有两种应力。
(对)3.胡克定律仅适用于杆件的弹性变形范围(对)4.低碳钢受拉破坏时有屈服阶段,中碳钢和合金钢都没有屈服阶段。
(错)5.铸铁扭转破坏沿45度螺旋面断裂是因剪应力先达到极限所致。
(错)6.低碳钢扭转破坏沿轴横截面断裂是因剪应力先达到极限所致。
(对)7.低碳钢压缩实验曲线一直是上扬的,因此极限强度为无穷。
(错)8. 弹性极限是材料保持弹性的最大极限值,可以不保持线性。
(错)9.比例极限是材料能保持线性的最大值,必在材料的弹性范围内。
(错)10.构件内力的大小不但与外力大小有关,还与材料的截面形状有关(错)11.杆件的某横截面上,若各点的正应力均为零,则该截面上的轴力为零。
(对)12.两根材料、长度都相同的等直柱子,一根的横截面积为A1,另一根为A2,且A2>A1 如图所示。
两杆都受自重作用。
则两杆最大压应力相等,最大压缩量也相等。
(对)13. 受集中力轴向拉伸的等直杆,在变形中任意两个横截面一定保持平行。
所以纵向纤维的伸长量都相等,从而在横截面上的内力是均匀分布的。
(错)14. 若受力物体内某电测得x和y方向都有线应变εx和εy,则x和y方向肯定有正应力σx 和σy。
(错)二、选择题1 塑性材料冷作硬化后,材料的力学性能发生了变化。
试判断以下结论哪一个是正确的:__ (A) 屈服应力提高,弹性模量降低;(B) 屈服应力提高,塑性降低;(C) 屈服应力不变,弹性模量不变;(D) 屈服应力不变,塑性不变。
2 低碳钢材料在拉伸实验过程中,不发生明显的塑性变形时,承受的最大应力应当小于的数值,有以下4种答案,请判断哪一个是正确的:_B_ (A) 比例极限;(B) 屈服极限;(C) 强度极限;(D) 许用应力。
3.关于低碳钢试样拉伸至屈服时,有以下结论,请判断哪一个是正确的:__ _ (A) 应力和塑性变形很快增加,因而认为材料失效;(B) 应力和塑性变形虽然很快增加,但不意味着材料失效;(C) 应力不增加,塑性变形很快增加,因而认为材料失效;(D) 应力不增加,塑性变形很快增加,但不意味着材料失效。
挤压与拉拔复习题答案

挤压与拉拔复习题答案一、选择题1. 挤压工艺中,金属的流动方向与外力作用方向的关系是:A. 垂直B. 平行C. 成一定角度D. 无固定方向答案:B. 平行2. 拉拔工艺中,金属的流动方向与外力作用方向的关系是:A. 垂直B. 平行C. 成一定角度D. 无固定方向答案:B. 平行3. 挤压与拉拔工艺中,金属的塑性变形主要发生在:A. 表面B. 内部C. 边缘D. 接触面答案:B. 内部二、填空题4. 挤压过程中,金属的流动方向与挤压轴向____。
答案:平行5. 拉拔过程中,金属的流动方向与拉拔轴向____。
答案:平行6. 挤压与拉拔工艺中,金属的塑性变形主要发生在____。
答案:内部三、简答题7. 挤压与拉拔工艺的共同点是什么?答案:挤压与拉拔工艺的共同点是它们都是通过施加外力使金属发生塑性变形,从而改变金属的形状和尺寸。
8. 挤压与拉拔工艺的不同点有哪些?答案:挤压与拉拔工艺的不同点在于挤压是金属在封闭模腔中受到压力作用而发生变形,而拉拔则是金属在拉伸力作用下通过模具孔洞而发生变形。
四、计算题9. 假设一块长方体金属块,其尺寸为长L=100mm,宽W=50mm,高H=20mm,若通过挤压工艺使其高度增加到H'=40mm,求挤压后的宽度W'。
答案:假设金属体积不变,则挤压前后体积相等,即L×W×H=L×W'×H'。
解得W'=(W×H)/(H')=50mm×20mm/40mm=25mm。
五、论述题10. 论述挤压与拉拔工艺在现代制造业中的应用及其重要性。
答案:挤压与拉拔工艺在现代制造业中应用广泛,它们可用于生产各种形状和尺寸的金属制品,如管材、棒材、线材等。
这些产品在汽车、航空、建筑、电子等多个领域都有重要应用。
挤压与拉拔工艺能够提高材料的机械性能,改善金属的微观结构,从而提高产品的质量和性能,对制造业的发展具有重要意义。
材料成形技术基础复习思考题-塑性成形部分-题
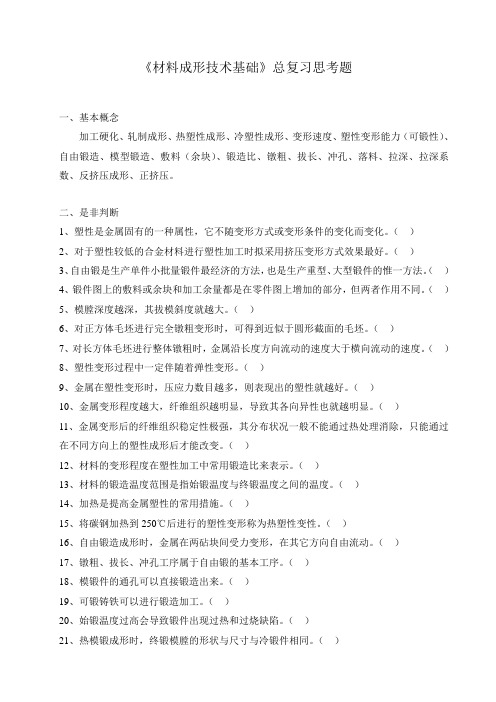
《材料成形技术基础》总复习思考题一、基本概念加工硬化、轧制成形、热塑性成形、冷塑性成形、变形速度、塑性变形能力(可锻性)、自由锻造、模型锻造、敷料(余块)、锻造比、镦粗、拔长、冲孔、落料、拉深、拉深系数、反挤压成形、正挤压。
二、是非判断1、塑性是金属固有的一种属性,它不随变形方式或变形条件的变化而变化。
()2、对于塑性较低的合金材料进行塑性加工时拟采用挤压变形方式效果最好。
()3、自由锻是生产单件小批量锻件最经济的方法,也是生产重型、大型锻件的惟一方法。
()4、锻件图上的敷料或余块和加工余量都是在零件图上增加的部分,但两者作用不同。
()5、模膛深度越深,其拔模斜度就越大。
()6、对正方体毛坯进行完全镦粗变形时,可得到近似于圆形截面的毛坯。
()7、对长方体毛坯进行整体镦粗时,金属沿长度方向流动的速度大于横向流动的速度。
()8、塑性变形过程中一定伴随着弹性变形。
()9、金属在塑性变形时,压应力数目越多,则表现出的塑性就越好。
()10、金属变形程度越大,纤维组织越明显,导致其各向异性也就越明显。
()11、金属变形后的纤维组织稳定性极强,其分布状况一般不能通过热处理消除,只能通过在不同方向上的塑性成形后才能改变。
()12、材料的变形程度在塑性加工中常用锻造比来表示。
()13、材料的锻造温度范围是指始锻温度与终锻温度之间的温度。
()14、加热是提高金属塑性的常用措施。
()15、将碳钢加热到250℃后进行的塑性变形称为热塑性变性。
()16、自由锻造成形时,金属在两砧块间受力变形,在其它方向自由流动。
()17、镦粗、拔长、冲孔工序属于自由锻的基本工序。
()18、模锻件的通孔可以直接锻造出来。
()19、可锻铸铁可以进行锻造加工。
()20、始锻温度过高会导致锻件出现过热和过烧缺陷。
()21、热模锻成形时,终锻模膛的形状与尺寸与冷锻件相同。
()22、金属的锻造性与材料的性能有关,而与变形的方式无关。
()23、模锻件的精度取决于终锻模膛的精度。
挤压拉拔复习题(大校)

概念题:1、拉拔:在外力作用下,迫使金属坯料通过模孔,以获得相应形状、尺寸地制品地塑性加工方法.2、挤压:就是对放在容器(挤压筒)内地金属锭坯从一端施加外力,强迫其从特定地模孔中流出,获得所需要地断面形状和尺寸地制品地一种塑性成型方法.3、挤压缩尾:挤压快要结束时,由于金属地径向流动及环流,锭坯表面地氧化物、润滑剂及污物、气泡、偏析榴、裂纹等缺陷进入制品内部,具有一定规律地破坏制品组织连续性、致密性地缺陷.4、死区:在基本挤压阶段,位于挤压筒与模子端面交界处地金属,基本上不发生塑性变形,故称为死区.5、粗晶环:许多合金(特别是铝合金)热挤压制品,经热处理后,经常会形成异常大地晶粒,这种粗大晶粒在制品中地分布通常是不均匀地,多数情况下呈环状分布在制品断面地周边上,故称为粗晶环.6、残余应力:由于变形不均,在拉拔结束、外力去除后残留在制品中地应力.7、粗化:许多合金(特别是铝合金)热挤压制品,经热处理后,经常会形成异常大地晶粒,比临界变形后热处理所形成地再结晶晶粒大得多,晶粒地这种异常长大过程称为粗化.8、带滑动多模连续拉拔配模地必要条件:当第n道次以后地总延伸系数λn→k大于收线盘与第n个绞盘圆周线速度之比γk→n,才能保证成品模磨损后不等式un> vn仍然成立,保证拉拔过程地正常进行.9、带滑动多模连续拉拔配模地充分条件:任一道次地延伸系数应大于相邻两个绞盘地速比.10、挤压效应:某些高合金化、并含有过渡族元素地铝合金(如2A11、2A12、6A02、2A14、7A04等)挤压制品,经过同一热处理(淬火与时效)后,其纵向上地抗拉强度比其他加工(轧制、拉拔、锻造)制品地高,而伸长率较低,这种现象称为挤压效应.简述题:1、影响管材空拉时地壁厚变化地因素有那些?各是如何影响地?2、挤压缩尾有那几种形式,其产生原因各是什么?3、锥形拉拔模孔由那几部分构成,各部分地主要作用是什么?4、对于存在着偏心地管坯,通过安排适当道次地空拉就可以使其偏心得到纠正.请问:(1)空拉为什么能够纠正管材地偏心?(2)采用固定短芯棒拉拔时,在一定程度上也能够纠正管材地偏心,这是为什么?5、挤压效应产生地主要原因是什么?影响挤压效应地因素有那些方面?6、挤压机地主要工具有哪些,各自地主要作用是什么?7、什么是残余应力?画图说明圆棒材拉拔制品中残余应力地分布及产生原因.8、简述在挤压过程中,影响挤压力地主要因素?9、在挤压过程中,试详细阐述影响金属流动地因素?10、产生粗晶环地主要原因是什么?粗晶环对制品力学性能有何影响?1、正、反向挤压时地主要特征是什么?正向挤压:特征:变形金属与挤压筒壁之间有相对运动,二者之间有很大地滑动摩擦.引起挤压力增大;使金属变形流动不均匀,导致组织性能不均匀;限制了挤压速度提高;加速工模具地磨损.反向挤压:特征:变形金属与挤压筒壁之间无相对运动,二者之间无外摩擦.2、什么是死区?死区地产生原因是什么?死区概念:在基本挤压阶段,位于挤压筒与模子端面交界处地金属,基本上不发生塑性变形,故称为死区.死区产生原因:a、强烈地三向压应力状态,金属不容易达到屈服条件;b、受工具冷却,σs增大;c、摩擦阻力大.3、挤压缩尾地形式及产生原因,减少挤压缩尾地措施.三种:中心缩尾、环形缩尾、皮下缩尾(1)中心缩尾:终了挤压阶段后期,筒内剩余地锭坯高度较小,整个挤压筒内地剩余金属处于紊流状态,且随着锭坯高度地不断减小,金属径向流动速度不断增加,以用来补充锭坯中心部位金属地短缺,于是锭坯后端表面地氧化物、油污等易集聚到锭坯地中心部位,进入制品内部;而且随着挤压地进一步进行,径向流动地金属无法满足中心部位地短缺,于是在制品中心部位出现了漏斗状地空缺,即中心缩尾.(2)环形缩尾:挤压过程中,锭坯表面层带有氧化物、偏析物、各种表面缺陷及污物地金属,由于受到挤压筒壁地摩擦作用,其流动滞后于皮下金属,被随后到来地挤压垫向前推进而堆积在挤压垫与挤压筒地角落部位.随着挤压过程进行,堆积在这个角落部位中带有各种缺陷和污物地金属会越来越多.到了挤压过程末期,当中间部位金属供应不足,边部金属开始发生径向流动时,这部分金属将沿着挤压垫前端地后端难变形区地边界流入制品中,形成环形状地缩尾.(3)皮下缩尾:终了挤压阶段,当死区与塑性流动区界面因剧烈滑移使金属受到很大剪切变形而断裂时,表面层带有氧化物、偏析物、各种表面缺陷及污物地金属,会沿着断裂面流出,与此同时,由于挤压筒内剩余锭坯地长度很小,死区金属也逐渐流出模孔包覆在制品地表面上,形成皮下缩尾或外成层.如果死区金属流出较少,不能完全将这些带有各种缺陷和污物地金属包覆住,则形成起皮.减少挤压缩尾地措施(1)对锭坯表面进行机械加工——车皮.(2)采用热剥皮挤压.(3)采用脱皮挤压,(4)进行不完全挤压——留压余.(5)保持挤压垫工作面地清洁,减少锭坯尾部径向流动地可能性.4、挤压机地分类?什么是单动式挤压机、复动式挤压机?各自地主要用途是什么?按传动类型:分液压和机械传动两大类按总体结构形式:分为卧式和立式挤压机两大类按其用途和结构:分为型棒挤压机和管棒挤压机,或者称为单动式挤压机和复动式挤压机单动式挤压机:无独立穿孔系统.适合用实心锭挤压型材、棒材,用组合模挤压空心型材.使用随动针和空心锭也可以挤压无缝管材.双动式挤压机:具有独立穿孔系统.适合于用空心锭或实心锭挤压无缝管材.采用实心锭也可以挤压型、棒材.5、挤压机地主要工具有哪些,各自地主要作用是什么?1) 主要挤压工具:▪挤压模—用于生产所需要地形状、尺寸地制品.▪穿孔针(芯棒)—对实心锭进行穿孔或用空心锭生产管材.▪挤压垫—防止高温金属与挤压杆直接接触,并防止金属倒流.▪挤压杆—用于传递主柱塞压力.▪挤压筒—用于容纳高温锭坯.2) 辅助工具:模垫、模支承、模座(压型嘴、模子滑架)、挡环(支承环)、针支承、针接手、导路等.6、模孔工作带地作用是什么?确定工作带长度地原则是什么?作用:稳定制品尺寸和保证制品表面质量.工作带长度地确定原则:最小长度应按照挤压时能保证制品断面尺寸地稳定性和工作带地耐磨性来确定,一般最短1.5~3mm.最大长度应按照挤压时金属与工作带地最大有效接触长度来确定.铝合金一般最长不超过15~20mm.7、挤压过程中,影响金属流动地因素有哪些?(1)接触摩擦及润滑地影响:1)摩擦越大,不均匀流动越大;2)润滑可减少摩擦,减少金属流动不均,并可以防止工具粘金属.(2)锭坯与工具温度地影响:1)锭坯本身温度:温度高,强度低,流动不均.2)锭坯断面上地温度分布:加热地不均匀性;工具地冷却作用;导热性地影响.(3)相变地影响:温度改变能使某些合金产生相变,金属处于不同地相组织会产生不同地流动情况.(4)摩擦条件变化:a、温度不同,摩擦系数不同;产生不同地氧化表面,其摩擦系数也不同.b、温度不同,可能产生不同相态组织.c、在高温、高压下极容易发生金属与工具地粘结.(5)锭坯与工具地温度差:锭坯与工具地温差越大,变形地不均匀性越大.(6)金属性质地影响变形抗力高地金属比抗力低地流动均匀;合金比纯金属流动均匀.(7)工具形状地影响1)模角:模角大,死区大,金属流动不均匀,挤压力大,制品表面质量较好.2)形状相似性:挤压筒与制品形状相似,金属流动均匀.(8)变形程度地影响变形程度大,不均匀流动增加,但当变形程度增加到一定程度时,由于变形从表面深入到内部,反而会使不均匀流动减小.8、在挤压过程中,影响挤压力地主要因素有哪些?(1)金属地变形抗力挤压力大小与金属地变形抗力成正比.(2)锭坯状态锭坯组织性能均匀,挤压力较小.(3)锭坯地规格及长度锭坯地规格对挤压力地影响是通过摩擦力产生作用地.锭坯地直径越粗,挤压力就越大;穿孔针直径越粗,挤压力也越大;锭坯越长,挤压力也越大.(4)变形程度(或挤压比)挤压力大小与变形程度成正比,即随着变形程度增大,挤压力成正比升高.(5)变形温度随着变形温度地升高,金属地变形抗力下降,挤压力降低.(6)变形速度如果无温度、外摩擦条件地变化,挤压力与挤压速度之间成线性关系.(7)外摩擦条件地影响(8)模角随着模角增大,金属进入变形区压缩锥所产生地附加弯曲变形增大,所需要消耗地金属变形功增大;但模角增大又会使变形区压缩锥缩短,降低了挤压模锥面上地摩擦阻力,二者叠加地结果必然会出现一挤压力最小值.这时地模角称为最佳模角.(9)挤压方式地影响反向挤压比同等条件下正向挤压在突破阶段所需要地挤压力低30% ~40%.9、型材模设计时,减少金属流动不均匀地主要措施有哪些?(1)合理布置模孔(2)确定合理地工作带长度(3)设计阻碍角或促流角(4)采用平衡模孔(5)设计附加筋条(6)设计导流模或导流腔10、对于以下几种情况,可酌情对模孔工作带长度进行必要地增减:a、交接圆边有凹弧R(R>1.5mm)者,工作带可增加1mm.b、螺孔处工作带可增加1mm.c、交接圆边有凸弧R(R>1.5mm)者,工作带可减短1mm.d、壁厚相同地各端部可减短1mm11、挤压制品组织不均匀地特点是什么?产生地主要原因是什么?▪表现特征横向上:外层晶粒细小,中心层粗大.纵向上:前端晶粒粗大,尾端细小,在最前端仍保留有铸态组织轮廓.▪产生原因A 变形不均匀(1)在横断面上,变形程度是由中心向边部逐渐增加地.从而导致了外层金属地晶粒破碎程度比中心层剧烈.(2)在纵向上,变形程度是由头部向尾部逐渐增加地.使得尾端晶粒比前端细小.B 挤压温度和速度地变化主要是针对锭温与筒温相差比较大地金属而言地.例如,对挤压速度慢地锡磷青铜,开始挤压时,金属在高温下变形,出模孔后地组织为再结晶组织;而后段挤压时,由于受工具地冷却作用,变形温度较低,金属出模孔后再结晶不完全;且挤压后期金属流速加快,更不利于再结晶.故尾部晶粒细小.C 相变地影响主要是对于温度变化可能会产生相变地合金而言地.12、产生粗晶环地主要原因是什么?粗晶环对制品力学性能有何影响?▪粗晶环地形成机制如前所述,挤压制品外层金属、尾部金属地晶粒破碎和晶格歪扭程度分别比内部和前端严重.晶粒破碎严重部分地金属,处于能量较高地热力学不稳定状态,降低了该部位地再结晶温度.在随后地热处理过程中易较早发生再结晶,当其他部位刚开始发生或还没有发生再结晶时,该部位发生了晶粒长大.▪粗晶环对制品性能地影响(1)粗晶区地纵向强度(σb、σ0.2)比细晶区地低.(2)粗晶区地疲劳强度低;(3)淬火时易沿晶界产生应力裂纹;(4)锻造时易产生表面裂纹;(5)粗、细晶区冲击韧性值差别不大;(6)粗晶区地缺口敏感性比细晶区地小.13、挤压制品地表面裂纹产生原因:裂纹地产生是由于制品表面层地附加拉应力超过了表面金属地强度所造成.减少裂纹地主要措施:(1)适当降低挤压温度;(2)控制合适地挤压速度;(3)合理设计、加工模具,精心修模;(4)对锭坯进行均匀化退火处理;(5)采用等温挤压、锭坯梯温加热等挤压新技术、新工艺.14、拉伸系数、断面减缩率、延伸率概念.拉拔时地主要变形指标:断面减缩率:φ=(1-F1/F0)×100%延伸率:ε=(L1/L0-1)×100%拉伸系数:λ=L1/L0=F0/F115、试解释圆棒材拉拔时变形区内地应力分布规律.(1)应力沿轴向分布σl 入<σl 出∣σr入∣>∣σr出∣∣σθ入∣>∣σθ 出∣原因:稳定拉拔过程中,变形区内任一横断面向模孔出口方向移动时,面积逐渐减小,而此断面与变形区入口端球面间地变形体积不断增大.为实现塑性变形,通过此断面作用在变形体地σl 必须逐渐增大.(2)应力沿径向分布∣σr 外∣>∣σr内∣∣σθ外∣>∣σθ 内∣σl 外<σl 内原因:在变形区,金属地每个环形地外面层上,作用着径向应力σr 外,在内表面上作用着径向应力σr 内,由于径向应力σr总是力图减小其外表面,这就需要σr外大于σr内.距离中心层越远,表面积越大,所需要地力就越大.16、锥形拉拔模孔由哪几部分构成,各部分地主要作用?锥形模地模孔一般由四部分组成:润滑带、压缩带、定径带、出口带.各部分地主要作用:(1)润滑带作用:在拉拔时便于润滑剂带入模孔,保证制品得到充分润滑,减少摩擦;并带走产生地部分热量;防止划伤坯料.(2)压缩带作用:金属产生塑性变形,获得所需要地形状、尺寸.(3)定径带作用:使制品进一步获得稳定、精确地尺寸与形状;防止模孔磨损而很快超差,延长其使用寿命.(4)出口带作用:防止制品出模孔时被划伤;防止定径带出口端因受力而引起剥落.17、什么是残余应力?画图说明圆棒材拉拔制品中残余应力地分布及产生原因.由于变形不均,在拉拔结束、外力去除后残留在制品中地应力—残余应力(1)轴向残余应力—外层拉、中心层压在拉拔过程中,由于金属流动不均,棒材外层产生附加拉应力,中心层则出现与之平衡地附加压应力.拉拔结束后,由于弹性后效作用,制品长度缩短,而外层较中心层缩短得较大.但是,物体地整体性防碍了这种自由变形,其结果在外层产生残余拉应力,中心层则出现残余压应力.(2)径向残余应力—外表面为0外,整个断面上受压,中心最大在径向上,由于弹性后效地作用,棒材断面上所有地同心环形薄层,都欲增大其直径.在外表面这种弹性恢复不受限制,但由外向内所有环形薄层地弹性恢复均会受到其外层地阻碍,从而产生一残余压应力.中心层恢复地阻力最大.(3)周向残余应力—外层拉、中心层压由于棒材中心部分在轴向和径向上受到残余压应力作用,故此部分金属在周向上有涨大变形地趋势.但是,外层金属阻碍其自由涨大,从而在中心层产生周向残余压应力,外层则产生与之平衡地周向残余拉应力.18、影响管材空拉时地壁厚变化地因素有那些?各是如何影响地?(1)相对壁厚地影响对于外径D相同地管坯,增加壁厚S将使金属向中心流动地阻力增大,从而使管壁增厚量减小.对于壁厚相同地管坯,增加外径,减小了“曲拱”效应,使金属向中心流动地阻力减小,使管坯空拉后壁厚增加地趋势加强.(2)减径量地影响减径量越大,壁厚地变化也越大.在总减径量不变地情况下,多道次空拉地增壁量大于单道次地增壁量;多道次空拉地减壁量小于单道次地减壁量.(3)模角α地影响随着模角增大,拉拔应力发生变化,并且存在着一最小值,其相应地模角称为最佳模角.如果模角变化使拉拔应力σ l增大,就会导致增壁过程中地增壁趋势减小;减壁过程中地减壁趋势增大.(4)定径带长度h、摩擦系数f、拉拔速度v地影响增大h、f、v,都会使拉拔应力σl增大,导致增壁时地增壁趋势减小;减壁时地减壁趋势增大.(5)合金及状态地影响合金及状态影响到变形抗力σs 、摩擦系数f 、加工硬化速率等.通常, σs 大, σl 大.相同合金,硬度越高,增壁地趋势越弱.(6)拉拔方式地影响采用倍模(或称双模)拉拔,会使管壁增加时地增壁趋势减小,管壁减薄时地减壁趋势增大.相当于增加一个反拉力.19、空拉为什么能够纠正管材地偏心?对于存在偏心地管坯,经过几道次空拉,可使其偏心得到一定程度地纠正.主要原因:偏心管坯空拉时,假定在同一圆周上径向压应力σr 均匀分布,则在不同壁厚处产生地周向压应力σθ不同,厚壁处地σθ小于薄壁处地σθ ;薄壁处要先发生塑性变形,即周向压缩,径向延伸,使壁增厚,轴向延伸;而厚壁处还处于弹性变形状态;则在薄壁处,将有轴向附加压应力地作用,厚壁处受附加拉应力作用;促使厚壁处进入塑性变形状态,增大轴向延伸,显然在薄壁处减少了轴向延伸,增加了径向延伸,即增加了壁厚;σθ值越大,壁厚增加越多.薄壁处在σθ作用下逐渐增厚,使整个断面上地壁厚趋于均匀一致.20、滑动式多模连续拉拔过程建立地基本条件、必要条件和充分条件各是什么? 运动速度v n 与绞盘地圆周线速度u n : u n > v n建立拉拔过程地基本条件,即: u n > v n ,或 R >0 .当第n 道次以后地总延伸系数大于收线盘与第n 个绞盘圆周线速度之比,才能保证成品模磨损后不等式u n > v n 仍然成立.这就是带滑动多模连续拉拔配模地必要条件.任一道次地延伸系数应大于相邻两个绞盘地速比.这就是带滑动多模连续拉拔配模地充分条件.计算题:(1)确定模孔数目:10F F n λ=(2)计算填充系数:Pc F F 0=λ(3)计算挤压比:10nF F =λ (4)计算挤压制品地长度:⎪⎪⎭⎫⎝⎛-=c y h L l λλ0,每根制品地长度n l l ch =(1)计算拉伸系数10F F =λ(2)计算拉出管材地长度()λ夹l l l -= (3)该断面尺寸管坯地合理长度偏夹切l l l nl l +++=λ。
挤压工工艺考试试题

挤压工工艺考试试题挤压工工艺考试试题挤压工工艺考试是一项对挤压工的技能和知识进行评估的重要环节。
通过挤压工工艺考试,可以评判挤压工在实际工作中的能力和水平,为企业选拔合格的挤压工人才提供参考。
本文将从挤压工工艺考试试题的设计和意义两个方面,探讨挤压工工艺考试的重要性。
一、试题设计挤压工工艺考试试题的设计应综合考虑挤压工的技能和知识,以确保考试结果的准确性和可靠性。
试题应涵盖以下几个方面:1.基础知识:包括挤压工的基本概念、工艺流程、设备操作等。
考生需要掌握挤压工的基本原理和操作流程,了解挤压工的设备构造和工作原理。
2.工艺参数:考生需要了解挤压工的工艺参数对产品质量的影响,如挤压速度、温度控制、模具选择等。
试题可以设计一些典型工艺参数的计算和调整题目,考察考生对工艺参数的理解和掌握程度。
3.质量控制:挤压工的主要任务是生产合格的挤压制品,因此质量控制是挤压工工艺考试的重要内容。
试题可以设计一些质量控制的实际问题,考察考生对挤压制品质量的判断和处理能力。
4.故障排除:挤压工在实际工作中,难免会遇到一些故障和问题。
考生需要具备一定的故障排除能力,能够通过对挤压工设备的观察和分析,找出故障的原因并进行修复。
试题可以设计一些故障排除的案例题,考察考生对故障排除的方法和技巧的掌握程度。
二、考试意义挤压工工艺考试的意义在于评估挤压工在实际工作中的能力和水平,为企业选拔合格的挤压工人才提供参考。
挤压工是挤压制品生产过程中的关键环节,其技能和水平直接影响产品的质量和生产效率。
通过挤压工工艺考试,可以筛选出技能熟练、知识扎实的挤压工,提高企业的生产效率和产品质量。
此外,挤压工工艺考试还可以激发挤压工的学习积极性和进取心。
挤压工作为一项技术性较强的工作,需要不断学习和掌握新的工艺和技术。
通过挤压工工艺考试,可以鼓励挤压工积极学习,提高自身的技能水平,为企业的发展做出更大的贡献。
总之,挤压工工艺考试是一项对挤压工的技能和知识进行评估的重要环节。
建大拉拔,挤压与管材冷轧考试知识点
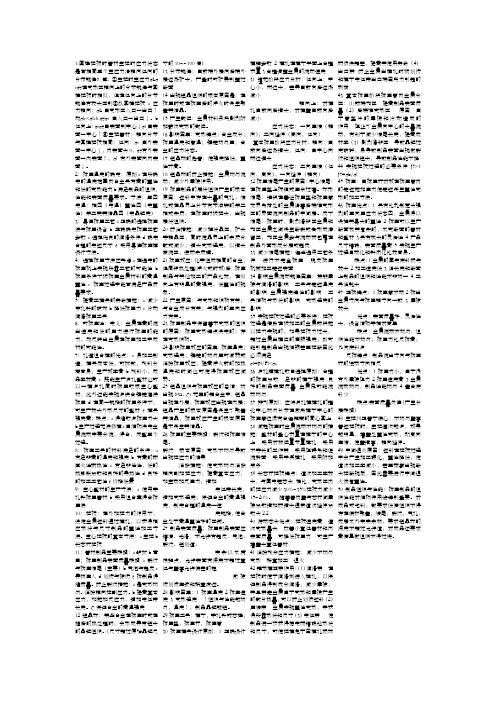
1:圆棒拉拔时管材空拉时应力状态是否相同三个主应力沿轴向径向的分布规律?答:①空拉时主应力σLσrσθ在变形区轴向上的分布规律与圆棒拉拔时相似,但在径向上的分布规律有较大区别②队圆棒拉拔a应力轴向:σL由变形区入口→出口↑即σlr<σlch.σθσr由入口→出口↓。
b 径向上:σrσθ由表面到中心↓σl由表面→中心↑③空拉管材:轴向分布与圆棒拉拔相同:径向:σr由外表面→中心↓,内表面为0,σθ有外表面→内表面↑,σl有外表面向内表面↓。
2:挤压温度的确定:原则a在所确定的温度范围内合金具有高的塑性和低的变形能力b满足制品的组织,性能和表面质量要求。
方法:三图定温:相图(定温)塑性图(定塑性)第二类再结晶图(定晶粒度)3:最佳挤压工艺a正确的选择挤压法与挤压设备b正确确定挤压工艺参数c选择优良的润滑条件d确定合理的定坯尺寸e采用最佳挤压模设计方法。
4:选择挤压方法应考虑a在选定的挤压机上实现所需工艺的可能性b 挤压条件下被挤压金属材料的高温塑性c挤压过程中能否满足产品质量要求。
5:提高工模具的寿命措施:a减少穿孔针的破坏b降低挤压力c冷却润滑挤压工具6:可挤压性:定义:金属在高的流出速度和低的压力进行挤压的能力,即反映出金属在挤压加工中成材的可能性。
7:孔道组合模的优点:a易加工制造,模具成本低,可拆卸,残料分离容易,生产效率高b残料小,成品率较高c既能生产多孔型材也可以一模多孔同时挤压数根空心型材,此外还能实现多块合铸锭连续挤压d在同一规格的挤压条件下,可生产较大外形尺寸的型材e模具强度高;缺点:a焊缝数多挤压力大b生产过程无法修模c由结构决定金属流动中要分流,焊合,成型三个过程。
8:挤压工具的材料满足的条件:a 有足够高的温度和强度b有高的耐回火性耐热性c有足够任性,低的热膨胀系数和良好的导热性d良好的加工工艺性e价格低廉9:空心型材的生产方法:a使用穿孔针挤压管材b采用组合莫焊合挤压法10:拉拔:在外加拉力的作用下,迫使金属坯料通过模孔,以获得相应形状与尺寸制品的塑性加工方法。
安工大挤压与拉拔复习题答案
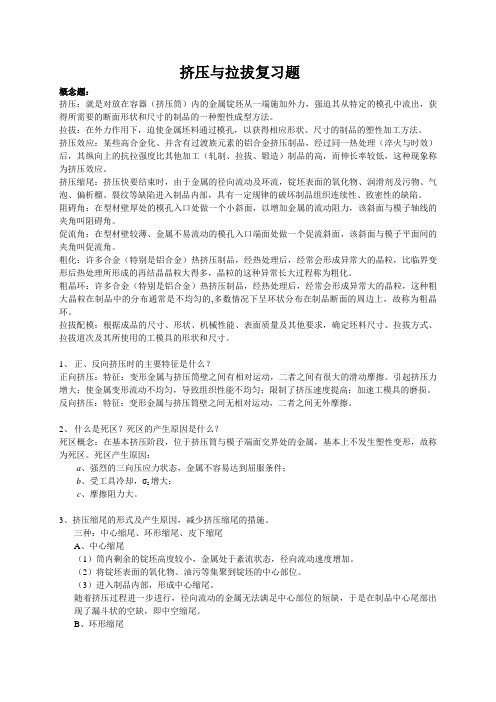
挤压与拉拔复习题概念题:挤压:就是对放在容器(挤压筒)内的金属锭坯从一端施加外力,强迫其从特定的模孔中流出,获得所需要的断面形状和尺寸的制品的一种塑性成型方法。
拉拔:在外力作用下,迫使金属坯料通过模孔,以获得相应形状、尺寸的制品的塑性加工方法。
挤压效应:某些高合金化、并含有过渡族元素的铝合金挤压制品,经过同一热处理(淬火与时效)后,其纵向上的抗拉强度比其他加工(轧制、拉拔、锻造)制品的高,而伸长率较低,这种现象称为挤压效应。
挤压缩尾:挤压快要结束时,由于金属的径向流动及环流,锭坯表面的氧化物、润滑剂及污物、气泡、偏析榴、裂纹等缺陷进入制品内部,具有一定规律的破坏制品组织连续性、致密性的缺陷。
阻碍角:在型材壁厚处的模孔入口处做一个小斜面,以增加金属的流动阻力,该斜面与模子轴线的夹角叫阻碍角。
促流角:在型材壁较薄、金属不易流动的模孔入口端面处做一个促流斜面,该斜面与模子平面间的夹角叫促流角。
粗化:许多合金(特别是铝合金)热挤压制品,经热处理后,经常会形成异常大的晶粒,比临界变形后热处理所形成的再结晶晶粒大得多,晶粒的这种异常长大过程称为粗化。
粗晶环:许多合金(特别是铝合金)热挤压制品,经热处理后,经常会形成异常大的晶粒,这种粗大晶粒在制品中的分布通常是不均匀的,多数情况下呈环状分布在制品断面的周边上,故称为粗晶环。
拉拔配模:根据成品的尺寸、形状、机械性能、表面质量及其他要求,确定坯料尺寸、拉拔方式、拉拔道次及其所使用的工模具的形状和尺寸。
1、正、反向挤压时的主要特征是什么?正向挤压:特征:变形金属与挤压筒壁之间有相对运动,二者之间有很大的滑动摩擦。
引起挤压力增大;使金属变形流动不均匀,导致组织性能不均匀;限制了挤压速度提高;加速工模具的磨损。
反向挤压:特征:变形金属与挤压筒壁之间无相对运动,二者之间无外摩擦。
2、什么是死区?死区的产生原因是什么?死区概念:在基本挤压阶段,位于挤压筒与模子端面交界处的金属,基本上不发生塑性变形,故称为死区。
拉压、剪练习题(计算)
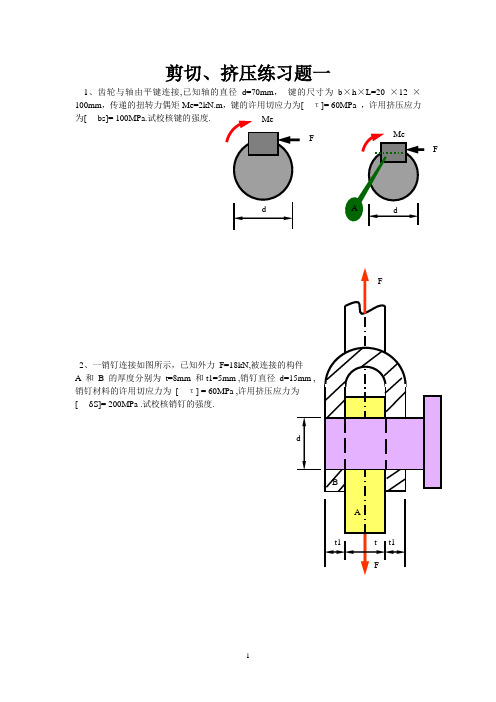
剪切、挤压练习题一1、齿轮与轴由平键连接,已知轴的直径d=70mm , 键的尺寸为b ×h ×L=20 ×12 ×100mm ,传递的扭转力偶矩Me=2kN.m ,键的许用切应力为[τ]= 60MPa ,许用挤压应力为[bs]= 100MPa.试校核键的强度.2、一销钉连接如图所示,已知外力 F=18kN,被连接的构件 A 和 B 的厚度分别为 t=8mm 和t1=5mm ,销钉直径 d=15mm , 销钉材料的许用切应力为 [τ] = 60MPa ,许用挤压应力为 [δS]= 200MPa .试校核销钉的强度.Me d FMed FA t1FFAt t1Bd3、一铆钉接头用四个铆钉连接两块钢板. 钢板与铆钉材料相同. 铆钉直径 d =16mm ,钢板的尺寸为 b =100mm ,t =10mm ,F = 90kN ,铆钉的许用应力是 [τ] =120MPa ,[δS] =120MPa ,钢板的许用拉应力 [δ]=160MPa. 试校核铆钉接头的强度.4. 如图所示螺栓连接,已知钢板的厚度t =10mm ,螺栓的许用切应力[τ]=100MPa ,许用挤压应力[σ]=200MPa ,F=28kN ,试选择该螺栓的直径。
F Ft t FFb5.如图所示,某轮用平键与轴联接。
已知轴的直径d=70mm ,键的尺寸为b=20mm,h=12mm,l =100mm ,传递的转矩M=1.5kN ·m ,键的许用切应力[τ]=60MPa ,许用挤压应力[σ] =100MPa ,试校核键的强度6、 两轴用凸缘联轴器相连接,在直径D =150mm 的圆周上均匀地分布着四个螺栓来传递力偶M 。
已知M=3KN.m ,凸缘厚度t=10mm ,螺栓材料为Q235钢,其许用拉应力[σ]=105MPa ,凸缘厚度t=10mm 。
设计螺栓直径d 。
剪切面m-m7、一铆接头如图所示,受力F=110kN,已知钢板厚度为t=1cm,宽度b=8.5cm ,许用应力为[σ ]= 160M Pa ;铆钉的直径d=1.6cm,许用切应力为[τ]= 140M Pa ,许用挤压应力为[σbs]=320M Pa,试校核铆接头的强度。
- 1、下载文档前请自行甄别文档内容的完整性,平台不提供额外的编辑、内容补充、找答案等附加服务。
- 2、"仅部分预览"的文档,不可在线预览部分如存在完整性等问题,可反馈申请退款(可完整预览的文档不适用该条件!)。
- 3、如文档侵犯您的权益,请联系客服反馈,我们会尽快为您处理(人工客服工作时间:9:00-18:30)。
概念题:1、拉拔:在外力作用下,迫使金属坯料通过模孔,以获得相应形状、尺寸的制品的塑性加工方法。
2、挤压:就是对放在容器(挤压筒)内的金属锭坯从一端施加外力,强迫其从特定的模孔中流出,获得所需要的断面形状和尺寸的制品的一种塑性成型方法。
3、挤压缩尾:挤压快要结束时,由于金属的径向流动及环流,锭坯表面的氧化物、润滑剂及污物、气泡、偏析榴、裂纹等缺陷进入制品内部,具有一定规律的破坏制品组织连续性、致密性的缺陷。
4、死区:在基本挤压阶段,位于挤压筒与模子端面交界处的金属,基本上不发生塑性变形,故称为死区。
5、粗晶环:许多合金(特别是铝合金)热挤压制品,经热处理后,经常会形成异常大的晶粒,这种粗大晶粒在制品中的分布通常是不均匀的,多数情况下呈环状分布在制品断面的周边上,故称为粗晶环。
6、残余应力:由于变形不均,在拉拔结束、外力去除后残留在制品中的应力。
7、粗化:许多合金(特别是铝合金)热挤压制品,经热处理后,经常会形成异常大的晶粒,比临界变形后热处理所形成的再结晶晶粒大得多,晶粒的这种异常长大过程称为粗化。
8、带滑动多模连续拉拔配模的必要条件:当第n道次以后的总延伸系数λn→k大于收线盘与第n个绞盘圆周线速度之比γk→n,才能保证成品模磨损后不等式un> vn仍然成立,保证拉拔过程的正常进行。
9、带滑动多模连续拉拔配模的充分条件:任一道次的延伸系数应大于相邻两个绞盘的速比。
10、挤压效应:某些高合金化、并含有过渡族元素的铝合金(如2A11、2A12、6A02、2A14、7A04等)挤压制品,经过同一热处理(淬火与时效)后,其纵向上的抗拉强度比其他加工(轧制、拉拔、锻造)制品的高,而伸长率较低,这种现象称为挤压效应。
简述题:1、影响管材空拉时的壁厚变化的因素有那些?各是如何影响的?2、挤压缩尾有那几种形式,其产生原因各是什么?3、锥形拉拔模孔由那几部分构成,各部分的主要作用是什么?4、对于存在着偏心的管坯,通过安排适当道次的空拉就可以使其偏心得到纠正。
请问:(1)空拉为什么能够纠正管材的偏心?(2)采用固定短芯棒拉拔时,在一定程度上也能够纠正管材的偏心,这是为什么?5、挤压效应产生的主要原因是什么?影响挤压效应的因素有那些方面?6、挤压机的主要工具有哪些,各自的主要作用是什么?7、什么是残余应力?画图说明圆棒材拉拔制品中残余应力的分布及产生原因。
8、简述在挤压过程中,影响挤压力的主要因素?9、在挤压过程中,试详细阐述影响金属流动的因素?10、产生粗晶环的主要原因是什么?粗晶环对制品力学性能有何影响?1、正、反向挤压时的主要特征是什么?正向挤压:特征:变形金属与挤压筒壁之间有相对运动,二者之间有很大的滑动摩擦。
引起挤压力增大;使金属变形流动不均匀,导致组织性能不均匀;限制了挤压速度提高;加速工模具的磨损。
反向挤压:特征:变形金属与挤压筒壁之间无相对运动,二者之间无外摩擦。
2、什么是死区?死区的产生原因是什么?死区概念:在基本挤压阶段,位于挤压筒与模子端面交界处的金属,基本上不发生塑性变形,故称为死区。
死区产生原因:a、强烈的三向压应力状态,金属不容易达到屈服条件;b、受工具冷却,σs增大;c、摩擦阻力大。
3、挤压缩尾的形式及产生原因,减少挤压缩尾的措施。
三种:中心缩尾、环形缩尾、皮下缩尾(1)中心缩尾:终了挤压阶段后期,筒内剩余的锭坯高度较小,整个挤压筒内的剩余金属处于紊流状态,且随着锭坯高度的不断减小,金属径向流动速度不断增加,以用来补充锭坯中心部位金属的短缺,于是锭坯后端表面的氧化物、油污等易集聚到锭坯的中心部位,进入制品内部;而且随着挤压的进一步进行,径向流动的金属无法满足中心部位的短缺,于是在制品中心部位出现了漏斗状的空缺,即中心缩尾。
(2)环形缩尾:挤压过程中,锭坯表面层带有氧化物、偏析物、各种表面缺陷及污物的金属,由于受到挤压筒壁的摩擦作用,其流动滞后于皮下金属,被随后到来的挤压垫向前推进而堆积在挤压垫与挤压筒的角落部位。
随着挤压过程进行,堆积在这个角落部位中带有各种缺陷和污物的金属会越来越多。
到了挤压过程末期,当中间部位金属供应不足,边部金属开始发生径向流动时,这部分金属将沿着挤压垫前端的后端难变形区的边界流入制品中,形成环形状的缩尾。
(3)皮下缩尾:终了挤压阶段,当死区与塑性流动区界面因剧烈滑移使金属受到很大剪切变形而断裂时,表面层带有氧化物、偏析物、各种表面缺陷及污物的金属,会沿着断裂面流出,与此同时,由于挤压筒内剩余锭坯的长度很小,死区金属也逐渐流出模孔包覆在制品的表面上,形成皮下缩尾或外成层。
如果死区金属流出较少,不能完全将这些带有各种缺陷和污物的金属包覆住,则形成起皮。
减少挤压缩尾的措施(1)对锭坯表面进行机械加工——车皮。
(2)采用热剥皮挤压。
(3)采用脱皮挤压,(4)进行不完全挤压——留压余。
(5)保持挤压垫工作面的清洁,减少锭坯尾部径向流动的可能性。
4、挤压机的分类?什么是单动式挤压机、复动式挤压机?各自的主要用途是什么?按传动类型:分液压和机械传动两大类按总体结构形式:分为卧式和立式挤压机两大类按其用途和结构:分为型棒挤压机和管棒挤压机,或者称为单动式挤压机和复动式挤压机单动式挤压机:无独立穿孔系统。
适合用实心锭挤压型材、棒材,用组合模挤压空心型材。
使用随动针和空心锭也可以挤压无缝管材。
双动式挤压机:具有独立穿孔系统。
适合于用空心锭或实心锭挤压无缝管材。
采用实心锭也可以挤压型、棒材。
5、挤压机的主要工具有哪些,各自的主要作用是什么?1) 主要挤压工具:▪挤压模—用于生产所需要的形状、尺寸的制品。
▪穿孔针(芯棒)—对实心锭进行穿孔或用空心锭生产管材。
▪挤压垫—防止高温金属与挤压杆直接接触,并防止金属倒流。
▪挤压杆—用于传递主柱塞压力。
▪挤压筒—用于容纳高温锭坯。
2) 辅助工具:模垫、模支承、模座(压型嘴、模子滑架)、挡环(支承环)、针支承、针接手、导路等。
6、模孔工作带的作用是什么?确定工作带长度的原则是什么?作用:稳定制品尺寸和保证制品表面质量。
工作带长度的确定原则:最小长度应按照挤压时能保证制品断面尺寸的稳定性和工作带的耐磨性来确定,一般最短1.5~3mm。
最大长度应按照挤压时金属与工作带的最大有效接触长度来确定。
铝合金一般最长不超过15~20mm。
7、挤压过程中,影响金属流动的因素有哪些?(1)接触摩擦及润滑的影响:1)摩擦越大,不均匀流动越大;2)润滑可减少摩擦,减少金属流动不均,并可以防止工具粘金属。
(2)锭坯与工具温度的影响:1)锭坯本身温度:温度高,强度低,流动不均。
2)锭坯断面上的温度分布:加热的不均匀性;工具的冷却作用;导热性的影响。
(3)相变的影响:温度改变能使某些合金产生相变,金属处于不同的相组织会产生不同的流动情况。
(4)摩擦条件变化:a、温度不同,摩擦系数不同;产生不同的氧化表面,其摩擦系数也不同。
b、温度不同,可能产生不同相态组织。
c、在高温、高压下极容易发生金属与工具的粘结。
(5)锭坯与工具的温度差:锭坯与工具的温差越大,变形的不均匀性越大。
(6)金属性质的影响变形抗力高的金属比抗力低的流动均匀;合金比纯金属流动均匀。
(7)工具形状的影响1)模角:模角大,死区大,金属流动不均匀,挤压力大,制品表面质量较好。
2)形状相似性:挤压筒与制品形状相似,金属流动均匀。
(8)变形程度的影响变形程度大,不均匀流动增加,但当变形程度增加到一定程度时,由于变形从表面深入到内部,反而会使不均匀流动减小。
8、在挤压过程中,影响挤压力的主要因素有哪些?(1)金属的变形抗力挤压力大小与金属的变形抗力成正比。
(2)锭坯状态锭坯组织性能均匀,挤压力较小。
(3)锭坯的规格及长度锭坯的规格对挤压力的影响是通过摩擦力产生作用的。
锭坯的直径越粗,挤压力就越大;穿孔针直径越粗,挤压力也越大;锭坯越长,挤压力也越大。
(4)变形程度(或挤压比)挤压力大小与变形程度成正比,即随着变形程度增大,挤压力成正比升高。
(5)变形温度随着变形温度的升高,金属的变形抗力下降,挤压力降低。
(6)变形速度如果无温度、外摩擦条件的变化,挤压力与挤压速度之间成线性关系。
(7)外摩擦条件的影响(8)模角随着模角增大,金属进入变形区压缩锥所产生的附加弯曲变形增大,所需要消耗的金属变形功增大;但模角增大又会使变形区压缩锥缩短,降低了挤压模锥面上的摩擦阻力,二者叠加的结果必然会出现一挤压力最小值。
这时的模角称为最佳模角。
(9)挤压方式的影响反向挤压比同等条件下正向挤压在突破阶段所需要的挤压力低30% ~40%。
9、型材模设计时,减少金属流动不均匀的主要措施有哪些?(1)合理布置模孔(2)确定合理的工作带长度(3)设计阻碍角或促流角(4)采用平衡模孔(5)设计附加筋条(6)设计导流模或导流腔10、对于以下几种情况,可酌情对模孔工作带长度进行必要的增减:a、交接圆边有凹弧R(R>1.5mm)者,工作带可增加1mm。
b、螺孔处工作带可增加1mm。
c、交接圆边有凸弧R(R>1.5mm)者,工作带可减短1mm。
d、壁厚相同的各端部可减短1mm11、挤压制品组织不均匀的特点是什么?产生的主要原因是什么?▪表现特征横向上:外层晶粒细小,中心层粗大。
纵向上:前端晶粒粗大,尾端细小,在最前端仍保留有铸态组织轮廓。
▪产生原因A 变形不均匀(1)在横断面上,变形程度是由中心向边部逐渐增加的。
从而导致了外层金属的晶粒破碎程度比中心层剧烈。
(2)在纵向上,变形程度是由头部向尾部逐渐增加的。
使得尾端晶粒比前端细小。
B 挤压温度和速度的变化主要是针对锭温与筒温相差比较大的金属而言的。
例如,对挤压速度慢的锡磷青铜,开始挤压时,金属在高温下变形,出模孔后的组织为再结晶组织;而后段挤压时,由于受工具的冷却作用,变形温度较低,金属出模孔后再结晶不完全;且挤压后期金属流速加快,更不利于再结晶。
故尾部晶粒细小。
C 相变的影响主要是对于温度变化可能会产生相变的合金而言的。
12、产生粗晶环的主要原因是什么?粗晶环对制品力学性能有何影响?▪粗晶环的形成机制如前所述,挤压制品外层金属、尾部金属的晶粒破碎和晶格歪扭程度分别比内部和前端严重。
晶粒破碎严重部分的金属,处于能量较高的热力学不稳定状态,降低了该部位的再结晶温度。
在随后的热处理过程中易较早发生再结晶,当其他部位刚开始发生或还没有发生再结晶时,该部位发生了晶粒长大。
▪粗晶环对制品性能的影响(1)粗晶区的纵向强度(σb、σ0.2)比细晶区的低。
(2)粗晶区的疲劳强度低;(3)淬火时易沿晶界产生应力裂纹;(4)锻造时易产生表面裂纹;(5)粗、细晶区冲击韧性值差别不大;(6)粗晶区的缺口敏感性比细晶区的小。
13、挤压制品的表面裂纹产生原因:裂纹的产生是由于制品表面层的附加拉应力超过了表面金属的强度所造成。