煤矸石烧结砖的制作
煤矸石烧结砖工艺流程

煤矸石烧结砖工艺流程一、原料准备煤矸石是一种富含矿物质的废弃石煤,含有一定比例的硅酸盐、铝酸盐、铁酸盐等成分,因此是生产烧结砖的理想原料。
在生产前,需要对煤矸石进行原料分析,确定其化学成分和物理性能,以便后续的原料处理和成型等工艺操作。
二、原料处理在原料处理过程中,需要将煤矸石进行研磨和筛分,以去除其中的杂质,提高原料的纯度和均匀性。
首先将原料进行粗破碎,然后通过研磨机进行细碎和研磨,得到适当的颗粒度。
之后,将研磨后的原料进行筛选,挑选出颗粒大小适中、均匀的颗粒。
三、成型成型是煤矸石烧结砖生产的关键环节之一、成型有两种方法,一种是干法成型,即将原料进行水分调整后,直接进行成型;另一种是湿法成型,即在原料中添加适量的水分和粘结剂,之后进行成型。
无论是干法成型还是湿法成型,都需要使用模具进行成型。
在成型过程中,将原料填充到模具中,并通过振动或压力作用,使原料充分密实、成型。
四、干燥成型后的砖坯需要进行干燥,以去除其中的水分,提高砖坯的强度和稳定性。
干燥的方法有自然干燥和人工加热干燥两种。
自然干燥是将砖坯放置在通风良好的场地中,使其在自然条件下干燥。
人工加热干燥则是通过燃料或蒸汽等加热设备,对砖坯进行人工加热干燥。
无论采用哪种干燥方法,都需要确保砖坯的干燥均匀、彻底,以避免后续烧结过程中出现开裂、变形等问题。
五、烧结砖坯经过干燥后,需要进行烧结,使其在高温下发生结晶和化学反应,形成石英、长石、辉石等物质,并使各个颗粒之间产生结合。
烧结过程需要控制温度和时间的合理配合,以确保砖坯充分烧结、均匀硬化,并达到预期的物理性能和化学成分。
六、包装总结:综上所述,煤矸石烧结砖的生产工艺流程包含了原料准备、原料处理、成型、干燥、烧结和包装等多个环节。
在生产过程中,需要对原料进行处理和成型,并在干燥和烧结等环节,控制温度和时间的合理配合,以确保砖坯的质量和性能达到预期。
通过这些工艺流程,我们可以生产出优质、环保的煤矸石烧结砖,从而满足建筑工程的需求。
《煤矸石制备烧结透水砖及基本性能研究》范文

《煤矸石制备烧结透水砖及基本性能研究》篇一一、引言煤矸石作为一种煤炭生产过程中产生的废弃物,长期被视为一种环境污染源。
然而,随着环境科学技术的进步,煤矸石的价值逐渐被挖掘,其在建筑、材料等领域的应用日益广泛。
烧结透水砖是一种新型的环保建材,其具有良好的透水性能和环保效益。
本文旨在研究煤矸石制备烧结透水砖的工艺及其基本性能,为煤矸石资源化利用提供新的途径。
二、煤矸石制备烧结透水砖的工艺(一)材料选择与制备本实验选取的原料主要为煤矸石、粘结剂和其他辅助材料。
首先对煤矸石进行破碎、磨细处理,以提高其活性指数和均匀性。
然后按照一定比例将煤矸石、粘结剂及其他辅助材料混合均匀,制成混合料。
(二)成型与烧结将混合料进行压制成型,制成所需形状的透水砖坯体。
然后进行烧结处理,烧结温度和时间根据实验条件进行控制。
在烧结过程中,煤矸石中的矿物质和粘结剂发生化学反应,使砖体逐渐形成具有特定性能的烧结体。
三、基本性能研究(一)物理性能本实验主要研究了烧结透水砖的抗压强度、抗折强度、密度等物理性能。
实验结果表明,经过合适的烧结工艺,制备的烧结透水砖具有较高的抗压强度和抗折强度,同时密度适中,满足建筑用砖的基本要求。
(二)透水性能透水性能是烧结透水砖的重要性能指标。
本实验通过测定砖体的透水系数和孔隙率来评价其透水性能。
实验结果表明,煤矸石制备的烧结透水砖具有较好的透水性能,其透水系数和孔隙率均达到相关标准要求。
(三)耐久性能耐久性能是评价建筑材料使用寿命的重要指标。
本实验通过模拟自然环境条件下的老化试验来评价烧结透水砖的耐久性能。
实验结果表明,煤矸石制备的烧结透水砖具有良好的耐久性能,能够满足长期使用的需求。
四、结论本文通过研究煤矸石制备烧结透水砖的工艺及其基本性能,发现煤矸石作为一种废弃物资源,在制备烧结透水砖方面具有很大的应用潜力。
制备的烧结透水砖具有较高的抗压强度、抗折强度和透水性能,同时具有良好的耐久性能。
这为煤矸石资源化利用提供了新的途径,同时也为环保建材的发展提供了新的选择。
煤矸石烧结砖生产技术及流程
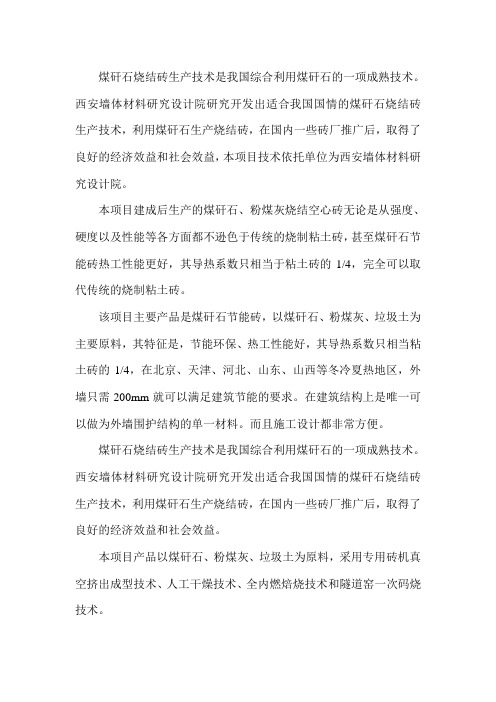
煤矸石烧结砖生产技术是我国综合利用煤矸石的一项成熟技术。
西安墙体材料研究设计院研究开发出适合我国国情的煤矸石烧结砖生产技术,利用煤矸石生产烧结砖,在国内一些砖厂推广后,取得了良好的经济效益和社会效益,本项目技术依托单位为西安墙体材料研究设计院。
本项目建成后生产的煤矸石、粉煤灰烧结空心砖无论是从强度、硬度以及性能等各方面都不逊色于传统的烧制粘土砖,甚至煤矸石节能砖热工性能更好,其导热系数只相当于粘土砖的1/4,完全可以取代传统的烧制粘土砖。
该项目主要产品是煤矸石节能砖,以煤矸石、粉煤灰、垃圾土为主要原料,其特征是,节能环保、热工性能好,其导热系数只相当粘土砖的1/4,在北京、天津、河北、山东、山西等冬冷夏热地区,外墙只需200mm就可以满足建筑节能的要求。
在建筑结构上是唯一可以做为外墙围护结构的单一材料。
而且施工设计都非常方便。
煤矸石烧结砖生产技术是我国综合利用煤矸石的一项成熟技术。
西安墙体材料研究设计院研究开发出适合我国国情的煤矸石烧结砖生产技术,利用煤矸石生产烧结砖,在国内一些砖厂推广后,取得了良好的经济效益和社会效益。
本项目产品以煤矸石、粉煤灰、垃圾土为原料,采用专用砖机真空挤出成型技术、人工干燥技术、全内燃焙烧技术和隧道窑一次码烧技术。
本项目生产线共分四道工序:①原料制备(备料、粉碎、搅拌);②原料陈化处理(陈化);③挤出成型;④干燥和焙烧。
1、原料配合:原料在进入生产工序前,须抽样化验分析,然后经筛选、破碎,计量进入高速强制对辊机,进行混合,经皮带机输送到陈化库,使混合料充分均化,提高物料的塑性,整个过程为常温常压。
2、成型陈化后的原料,经混式细碎机进一步均化,进入双轴搅拌挤出机而后入双级真空挤出机成泥条,再由自动切条切坯机切坯成型。
3、干燥及焙烧该生产线分别采用隧道式干燥室和节能型隧道窑进行干燥和焙烧,干燥和焙烧工艺采用一次码烧人工干燥技术,干燥热源取自隧道窑顶部的换热管道。
砖坯从干燥室出室后,由人工将干坯装至机动运坯车上,用机动运坯车将干坯送至隧道窑窑门,靠人工将干坯码入隧道窑窑室内。
烧结煤矸石实心砖和多孔砖(砌块)应用技术标准
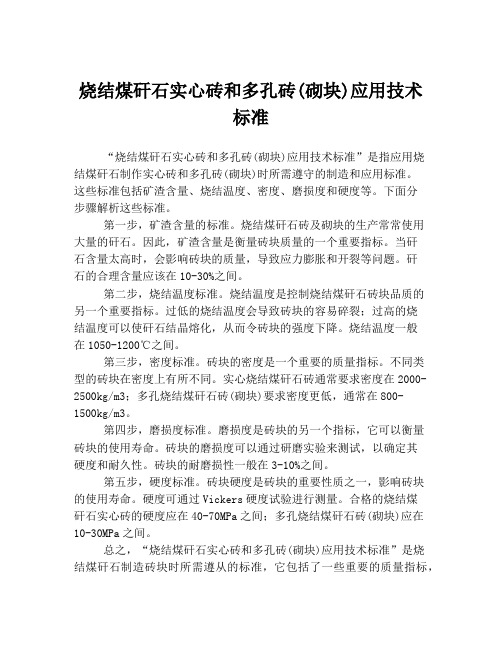
烧结煤矸石实心砖和多孔砖(砌块)应用技术标准“烧结煤矸石实心砖和多孔砖(砌块)应用技术标准”是指应用烧结煤矸石制作实心砖和多孔砖(砌块)时所需遵守的制造和应用标准。
这些标准包括矿渣含量、烧结温度、密度、磨损度和硬度等。
下面分步骤解析这些标准。
第一步,矿渣含量的标准。
烧结煤矸石砖及砌块的生产常常使用大量的矸石。
因此,矿渣含量是衡量砖块质量的一个重要指标。
当矸石含量太高时,会影响砖块的质量,导致应力膨胀和开裂等问题。
矸石的合理含量应该在10-30%之间。
第二步,烧结温度标准。
烧结温度是控制烧结煤矸石砖块品质的另一个重要指标。
过低的烧结温度会导致砖块的容易碎裂;过高的烧结温度可以使矸石结晶熔化,从而令砖块的强度下降。
烧结温度一般在1050-1200℃之间。
第三步,密度标准。
砖块的密度是一个重要的质量指标。
不同类型的砖块在密度上有所不同。
实心烧结煤矸石砖通常要求密度在2000-2500kg/m3;多孔烧结煤矸石砖(砌块)要求密度更低,通常在800-1500kg/m3。
第四步,磨损度标准。
磨损度是砖块的另一个指标,它可以衡量砖块的使用寿命。
砖块的磨损度可以通过研磨实验来测试,以确定其硬度和耐久性。
砖块的耐磨损性一般在3-10%之间。
第五步,硬度标准。
砖块硬度是砖块的重要性质之一,影响砖块的使用寿命。
硬度可通过Vickers硬度试验进行测量。
合格的烧结煤矸石实心砖的硬度应在40-70MPa之间;多孔烧结煤矸石砖(砌块)应在10-30MPa之间。
总之,“烧结煤矸石实心砖和多孔砖(砌块)应用技术标准”是烧结煤矸石制造砖块时所需遵从的标准,它包括了一些重要的质量指标,例如矿渣含量,烧结温度,密度,磨损度和硬度等。
这些标准对制造和使用烧结煤矸石砖块具有重要意义,是确保砖块质量的关键。
关于煤矸石、粉煤灰烧结砖

关于煤矸石、粉煤灰生产烧结砖我们把煤矸石、粉煤灰用来作为烧结砖的主要原料,实在不是因为它们是制砖的好东西,而是因为它们是数量最大的而且最没用的工业污染废弃物。
特别是“禁实”后,用它们做用粘土的替代品,有着环保节能、节土、节地等方面的综合积极意义。
但是都给我们的工艺生产技术,以及工装设备带来许多新的难题,尤其是高掺量制砖。
我们分别谈一下煤矸石和粉煤灰生产烧结砖的一些问题。
因为煤矸石与粉煤灰作为制砖原料性能上差别很大,有的方面甚至根本不一样。
所以它们的生产工艺及设备差别也很大。
先谈一下煤矸石做砖。
一、不是所有的煤矸石都可以直接用来制砖:1.从制砖原料的矿物成份来看:人类制造砖瓦的历史已经有几千年了。
但过去长久以来,无论是中国还是世界其他各国制砖的原料都是粘土,烧结后成为坚固的材料。
这是因粘土原料是以高岭石、伊利石(水云母)等粘土矿物为主,在高温焙烧后生成新的莫来石晶(3Al2O3•2SO2)。
而莫来石是一种硬质的、抗化学侵蚀的物相,其细长的晶体结构使制品的强度增高,是使烧结砖瓦制品最终获得较高机械强度的主要原因。
焙烧过程从950℃开始产生。
到1300℃可最终完成其晶体稳定成份。
同时粘土中含有长石和细粉状的石英。
粘土原料在塑性状态下,长石和石英起着成型后的产品中控制收缩和变形的填充料的作用。
在焙烧阶段,长石则是一种助熔剂,易玻化,补偿了耐火粘矿物和惰性石英不易溶融的不足。
而石英除了惰性填充料外,它还起着提供干燥和焙烧过程中坯体强度的作用。
根据这个道理,能够用来烧结的原料应该是具有的粘土特点,即含有高岭石、伊利石(水云母)等粘土矿物及长石、石英非粘土矿物这几种基本矿物的物质。
一般粘土矿物总量应占到50%左右。
那么,除粘土之外,自然界还具有和粘土矿物成份类似的物料,那就是页岩。
页岩在远古时代曾就是粘土,是疏松的粘土经过自然界长期的成岩作用而形成的,具有薄片状或薄页状原理构造的粘土岩,它的主要矿物成分有高岭石、伊利石、胶岭石、拜来石、并常含有石英、长石、云母等碎屑混入物。
烧结砖的工艺流程
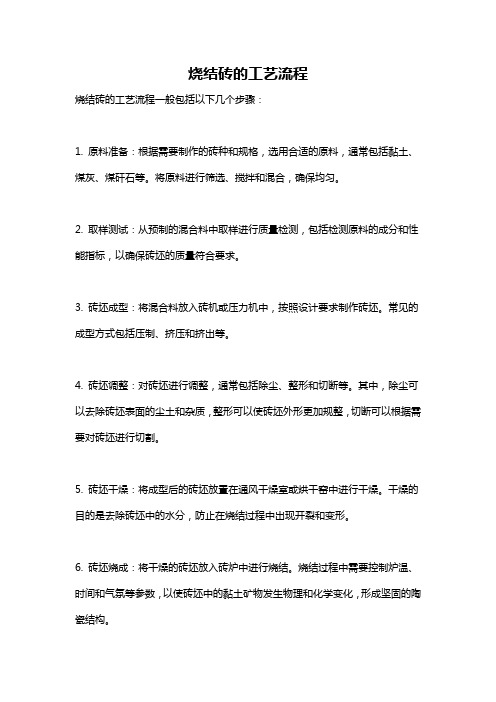
烧结砖的工艺流程
烧结砖的工艺流程一般包括以下几个步骤:
1. 原料准备:根据需要制作的砖种和规格,选用合适的原料,通常包括黏土、煤灰、煤矸石等。
将原料进行筛选、搅拌和混合,确保均匀。
2. 取样测试:从预制的混合料中取样进行质量检测,包括检测原料的成分和性能指标,以确保砖坯的质量符合要求。
3. 砖坯成型:将混合料放入砖机或压力机中,按照设计要求制作砖坯。
常见的成型方式包括压制、挤压和挤出等。
4. 砖坯调整:对砖坯进行调整,通常包括除尘、整形和切断等。
其中,除尘可以去除砖坯表面的尘土和杂质,整形可以使砖坯外形更加规整,切断可以根据需要对砖坯进行切割。
5. 砖坯干燥:将成型后的砖坯放置在通风干燥室或烘干窑中进行干燥。
干燥的目的是去除砖坯中的水分,防止在烧结过程中出现开裂和变形。
6. 砖坯烧成:将干燥的砖坯放入砖炉中进行烧结。
烧结过程中需要控制炉温、时间和气氛等参数,以使砖坯中的黏土矿物发生物理和化学变化,形成坚固的陶瓷结构。
7. 砖砂处理:将烧制后的砖坯进行浸水、砂光和清洗等处理,以去除砖坯表面的灰尘和杂质,提高砖坯的质量和光洁度。
8. 成品包装:将烧结和处理完毕的砖坯进行包装和标识。
常见的包装方式包括将砖坯码垛、缠绕保护膜、贴上标识等。
以上是烧结砖的一般工艺流程,具体的步骤和要求可能因砖种和制作工艺的不同而有所差异。
煤矸石利用的流程和工艺条件
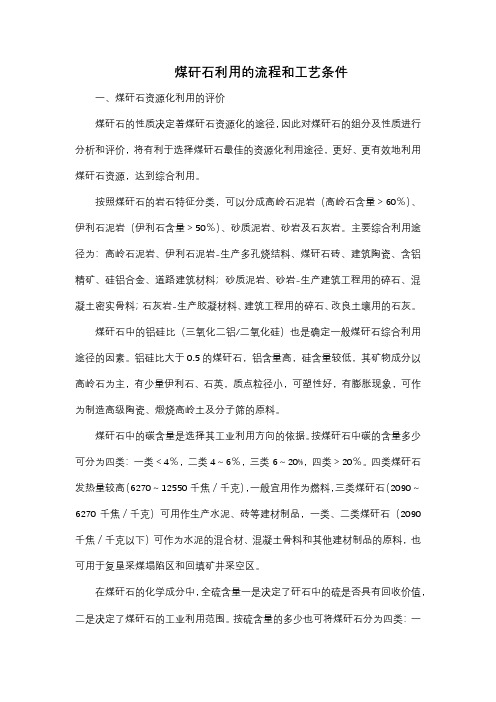
煤矸石利用的流程和工艺条件一、煤矸石资源化利用的评价煤矸石的性质决定着煤矸石资源化的途径,因此对煤矸石的组分及性质进行分析和评价,将有利于选择煤矸石最佳的资源化利用途径,更好、更有效地利用煤矸石资源,达到综合利用。
按照煤矸石的岩石特征分类,可以分成高岭石泥岩(高岭石含量>60%)、伊利石泥岩(伊利石含量>50%)、砂质泥岩、砂岩及石灰岩。
主要综合利用途径为:高岭石泥岩、伊利石泥岩-生产多孔烧结料、煤矸石砖、建筑陶瓷、含铝精矿、硅铝合金、道路建筑材料;砂质泥岩、砂岩-生产建筑工程用的碎石、混凝土密实骨料;石灰岩-生产胶凝材料、建筑工程用的碎石、改良土壤用的石灰。
煤矸石中的铝硅比(三氧化二铝/二氧化硅)也是确定一般煤矸石综合利用途径的因素。
铝硅比大于0.5的煤矸石,铝含量高,硅含量较低,其矿物成分以高岭石为主,有少量伊利石、石英,质点粒径小,可塑性好,有膨胀现象,可作为制造高级陶瓷、煅烧高岭土及分子筛的原料。
煤矸石中的碳含量是选择其工业利用方向的依据。
按煤矸石中碳的含量多少可分为四类:一类<4%,二类4~6%,三类6~20%,四类>20%。
四类煤矸石发热量较高(6270~12550千焦/千克),一般宜用作为燃料,三类煤矸石(2090~6270千焦/千克)可用作生产水泥、砖等建材制品,一类、二类煤矸石(2090千焦/千克以下)可作为水泥的混合材、混凝土骨料和其他建材制品的原料,也可用于复垦采煤塌陷区和回填矿井采空区。
在煤矸石的化学成分中,全硫含量一是决定了矸石中的硫是否具有回收价值,二是决定了煤矸石的工业利用范围。
按硫含量的多少也可将煤矸石分为四类:一类(0.5%,二类0.5~3%,三类3~6%,四类>6%。
全硫量达6%的煤矸石即可回收其中的硫精矿,对于用煤矸石作燃料的要根据环保要求,采取相应的除尘、脱硫措施,减少烟尘和二氧化硫的污染。
二、煤矸石发电1、煤矸石发电的技术要求含碳量较高(发热量大于4180千焦/千克)的煤矸石,一般为煤巷掘进矸和洗矸,通过简易洗选,利用跳汰或旋流器等设备可回收低热值煤,供作锅炉燃料。
烧结砖的工艺流程
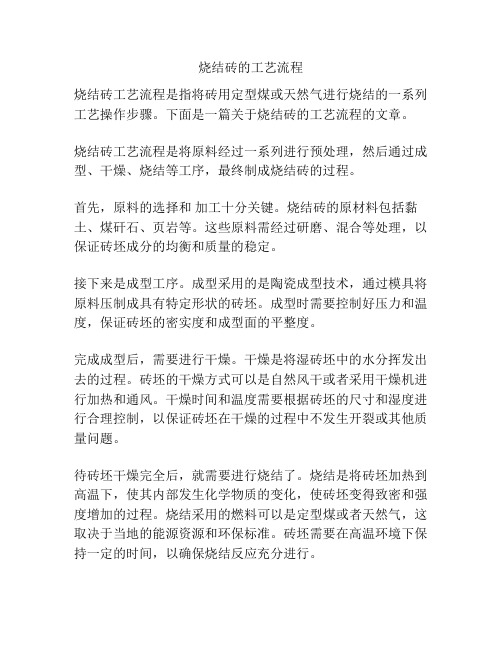
烧结砖的工艺流程烧结砖工艺流程是指将砖用定型煤或天然气进行烧结的一系列工艺操作步骤。
下面是一篇关于烧结砖的工艺流程的文章。
烧结砖工艺流程是将原料经过一系列进行预处理,然后通过成型、干燥、烧结等工序,最终制成烧结砖的过程。
首先,原料的选择和加工十分关键。
烧结砖的原材料包括黏土、煤矸石、页岩等。
这些原料需经过研磨、混合等处理,以保证砖坯成分的均衡和质量的稳定。
接下来是成型工序。
成型采用的是陶瓷成型技术,通过模具将原料压制成具有特定形状的砖坯。
成型时需要控制好压力和温度,保证砖坯的密实度和成型面的平整度。
完成成型后,需要进行干燥。
干燥是将湿砖坯中的水分挥发出去的过程。
砖坯的干燥方式可以是自然风干或者采用干燥机进行加热和通风。
干燥时间和温度需要根据砖坯的尺寸和湿度进行合理控制,以保证砖坯在干燥的过程中不发生开裂或其他质量问题。
待砖坯干燥完全后,就需要进行烧结了。
烧结是将砖坯加热到高温下,使其内部发生化学物质的变化,使砖坯变得致密和强度增加的过程。
烧结采用的燃料可以是定型煤或者天然气,这取决于当地的能源资源和环保标准。
砖坯需要在高温环境下保持一定的时间,以确保烧结反应充分进行。
烧结结束后,需要进行冷却和包装。
砖坯在高温环境下冷却后,可以进行质量检验和包装。
质量检验主要包括外观检查、尺寸测量、强度试验等,以确保砖坯符合相关标准。
包装可以采用编织袋、木箱等方式,确保砖坯运输和存放的安全和便利。
以上就是烧结砖的工艺流程。
每个环节都需要仔细控制和协调,以保证砖坯的质量和性能。
烧结砖作为建筑材料,具有韧性好、抗压强度高的特点,广泛应用于各类建筑工程中。
随着科技的进步和技术的革新,烧结砖的制造工艺也在不断更新与提升,以满足建筑行业对砖材的需求。
- 1、下载文档前请自行甄别文档内容的完整性,平台不提供额外的编辑、内容补充、找答案等附加服务。
- 2、"仅部分预览"的文档,不可在线预览部分如存在完整性等问题,可反馈申请退款(可完整预览的文档不适用该条件!)。
- 3、如文档侵犯您的权益,请联系客服反馈,我们会尽快为您处理(人工客服工作时间:9:00-18:30)。
煤矸石粉煤灰页岩烧结砖的研制
摘要:以工业废渣煤矸石、粉煤灰及风化页岩为主要原料研制成烧结砖,具有较明显的社会效益和经济效益。
介绍了原料的性能、配方组成、工艺、产品性能;指出选用粘结剂,采用高压真空挤出成型工艺可提高半成品干燥强度;烧成审问速度在300℃以前以50~80℃/h,300℃以后以100℃/h左右为宜。
1.前言
煤矸石是我国排放量最大的工业废渣。
据统计,我国的煤矸石总堆积量已经超过30亿吨,现在还以每年1亿吨的增长速度增长,而我国煤矸石的总利用率仅25%左右。
我国粉煤灰每年排出量超出7000万吨,其中只有42%得到综合利用。
目前,这两者已成为公众关注的社会问题。
煤矸石与粉煤灰含量有一定量的可燃成分,及丰富的氧化铝、氧化硅、氧化钙等,是可供开发和利用的二次资源。
风化页岩在我国北方的一些地区储量很大,其基本的化学组成和物理性质与黏土相差不太大。
如何利用这一资源也是一个亟待解决的问题。
本研究利用煤矸石、粉煤灰和风化页岩研制实心烧结砖,粉煤灰的掺量可达40%,煤矸石的掺量也达20%。
2原料及试验过程
2.1原料的选择
粉煤灰为湘潭电厂的湿排灰,不需加工,可直接利用。
煤矸石取自萍乡安源煤矿矸石山,经破碎、粉磨至粒度小于0.15mm后再利用。
风化页岩选自河北石家庄,经破碎后使用。
三者的化学组成和物理性质见表1和表2。
表1 原料的化学组成%
表2 原料的物理性质
2.2配方及工艺过程
一般煤矸石砖很容易出现黑心现象,使砖的强度降低,为避免这一现象,煤矸石的掺量限定在20%~30%,试验过程中还对风化页岩和粘土进行了对比试验,其结果相差不大,有粘结剂十几本可以不用粘土,选取了6个配方进行试验,如表3所示。
表3 试验配方%
各种原料按配方计量,经2次挤切搅拌混练,将从ZK50/45-20A
双级真空挤砖机上挤出的泥条切成半成品砖坯,半成品经干燥后人窑烧结,得到烧结砖成品,产品性能见表4(F配方半成品干燥强度低,故其性能没测)。
表4 烧结砖性能
2.3中试
在工厂以日配方(实际粘结剂昂用量为1.5%)进行了中试,机械干燥,轮窑烧成。
干燥后半成品合格率96%,半成品烧成合格率92%,一级品率80%;产品外观规整,呈浅灰色至浅红色。
任取15块砖测试,平均抗压强度16.89MPa,最大21.35MPa,最小12.16MPa。
3讨论
3.1粘结剂的选择
提高粉煤灰的掺比,减少粘土用量,整个混合料的粘结能力下降,故必须引入粘结剂以提高半成品干燥强度。
当粉煤灰掺量超过50%时,粘结剂引入显得尤其重要。
本试验先后选用了5种有机和无机系列的粘结剂,通过对比试验,最后选择有机的WG作粘结剂,使用时,根据配方及成型水分要求将WG溶于水中,再加入到粉煤灰、煤矸石、风化页岩或粘土的混合物中。
粘结剂WG掺比的确定与保证半成品强度、半成品成本及成型方式有关,这里主要讨论与前二者的关系。
图1与图2以配方E为试验
基准,描述了粘结剂掺比与半成品干燥强度及半成品成本之间的关系。
从图1、图2见,随W G掺比的增大,半成品成本和干燥强度均呈增加状态。
图1 粘结剂的掺比与干燥强度的关系
图2 粘结剂按比与半成品成本的关系
3.2成型方法
为了保证半成品干燥后的强度,采用了高压真空挤出成型工艺,挤出机为ZK50/45-20A双级真空挤砖机,配用ZKS-6型二级水环真空泵。
该工艺有以下特点:
(1)原材料不需作过细的加工处理,粉煤灰不用于干燥,粘土不必粉碎(只要引入一台细碎对辊机碾细即可)。
(2)当粉煤灰掺比不超过40%时,不必引入粘结剂,依靠煤矸石与风化页岩或粘土的粘结作用可使砖坯半成品获得足够的强度。
粉煤灰掺比过高使用粘结剂时,粘结剂用量也比同掺比采用其他成型法少得多,故成本较低。
(3)生产效率高,易实现工业化生产,也便于利用目前砖厂的生产设备开发新产品,具有较大的推广应用市场。
(4)由于挤出成型的砖坯水分含量高,故干燥能耗较高,干燥时间也较长。
3.3烧成
低温阶段,考虑到热冲击性和残余水分的影响,升温速率可适当慢些,一般以50~80℃/h为宜。
温度达到300℃以上时,砖体内的燃料已开始燃烧,升温速率可以提高到约100℃/h,以这样升温速率一直到最高烧结温度。
该阶段,过快的升温速率也不可取。
因为升温速率过快,一方面试样中的一些反应不完全,将导致最终试样强度较差:另一方面砖体内的可燃物燃烧过于剧烈,可能导致砖体开裂。
表5列出了日组配方试样在不同温度下烧成的性能及外观状况。
显然,随着烧成温度的升高,砖的表观密度随之增大,体积收缩率也相应增加;砖的耐压强度在1090℃左右有一个最大值,温度继续升高,砖体内可能局部瓷化,而使材料性质不均匀,降低强度。
从表5的数据看,B组配方试样最高烧成温度确定在1060~1120℃比较合适。
表5 B组试样经不同温度烧成后的性能
注:保温时间均为2h
4结论
(1)以煤矸石、粉煤灰和风化页岩为原料研制烧结砖,减少了粘土的应用,并有效地利用煤矸石和粉煤灰中的可燃成分,降低生产能耗,经济效益和社会效益十分显著。
(2)选用WG为粘结剂和对传统成型工艺的改进,可以获得理想的成型效果。
(3)烧成时的升温速度,300℃前以50~80℃/h,300℃后约100℃/h为宜;烧成温度以1060~1120℃为宜。