(整理)金属表面防护技术
TL 260-2004 金属表面涂漆 表面防护技术要求(中文)

2004年05月金属表面涂漆表面防护技术要求TL260 标准中心50 23 450 23 4共4页第1页首次采用日期专业负责批准更改负责采用翻译曹哲日期2004.09.01译校日期技校日期抄写萧明日期2004.11.02 主题词:表面防护,防腐蚀,油漆,金属表面修订同TL 260:1995-09比较,作了如下修改:—标准内容重新作了划分—相关参考文献有改动—禁止Cr (VI)和铅—薄弱环节技术要求有变更.以前版本1975-08,1980-06,1985-05,1986-12;1994-02;1995-09.1 适用范围本标准为在金属表面涂上防腐油漆而规定了技术要求.本标准不适用于给镀过锌的金属表面漆(见TL 227标准),也不适用于给装潢件涂防腐漆(见TL 218标准),或者,在一定情况下,给汽车行走部分中的空腔零件涂漆(见TL 262标准).2 标记见 VW 137 50, 2条3 技术要求3.1防护方式目前实行的防护方式列举在表中:表 1防护方式特性Ofl – x010 商业性的涂漆,只有与大众汽车股份公司中心实验室和/或奥迪股份公司实验室及其主管设计部门商妥之后方可进行.对防腐蚀没有技术要求Ofl –x100, Ofl –x300Ofl –x600预处理未作规定(但不能离开生产技术基础)单层 – 湿法涂漆方法不限,有选择地进行阴极浸渍涂漆(KTL) Ofl –x130Ofl –x330进行磷酸锌处理, 磷酸铁处理或磷酸锰处理单层 – 湿法涂漆方法不限,有选择地进行阴极浸渍涂漆(KTL) Ofl –x630 进行磷酸锌处理,阴极浸渍涂漆(KTL)Ofl –x631 进行磷酸锌处理,双层涂漆(浸涂+喷涂)Ofl –x634 进行磷酸锌处理,厚层的阴极浸渍涂漆或者KTL+浸涂(用于极强劲地施加负荷的零件,例如发动机室前端零件3.2基本技术要求首次供货和更改的批准按VW 011 55避免有害物质按VW 911 01一次圆满试验需用8个零件或零件的切断件所用的涂层不得含有Cr (VI)和铅的化合物3.3 母体材料见图纸3.4防护方法/外观见表1,如果图纸上没有另作规定,则颜色总是黑色的.3.5预处理如果风干的涂层投入使用,或者油漆组系没有在高温(>60℃)情况下烘烤过,则构件在试验之前应在60℃情况下预处理24 h,之后紧接着将试样按DIN 50014标准在室温(18 ~ 28)℃情况下冷却.3.6涂层厚度见表2,对于零件的接合面和接触面来说,严格规定涂层厚度的极限值是必要的,该极限值要在图纸上作出规定.表 2防护方式涂层厚度单位:μmOfl –x100, Ofl –x130, Ofl –x300, Ofl –x330,Ofl –x600 15 ~ 50 (用于湿法涂漆)>12 (用于阴极浸渍涂漆)Ofl –x630 15 ~ 35,在空腔内≥12Ofl –x631 40 ~ 60Ofl –x634 35 ~ 60, 在空腔内≥20 3.7附着性和脆性划格试验法按DIN EN ISO 2409,技术要求,特性值: 0 ~ 13.8耐碎石打击性能试验按DIN 55996-1的方法B进行,视觉判断.技术要求: ≤特性值2.3.9其他性能见表 3表 34 相关参考文献1210 车身,配件,腐蚀试验PVTL 766 制动液,材料技术要求TL 774 乙烯甘醇基冷却液添加剂,材料技术要求TL 521 07 初次用的发动机润滑油SAE 15W – 40,润滑剂技术要求TL 521 46 中央液压系统液压油,高耐热性,技术要求VW 011 55 汽车外构件概论;首次供货和更改的批准VW 137 50 金属表面防护;防护方法,缩写符号,技术要求VW 911 01 汽车环境标准,汽车零件,燃料,生产原料,避免有害物质VDA 621-412 涂漆技术试验,汽车施漆的化学稳定性DIN 50014 预处理和/或试验的标准气候,规定DIN 50017 气候及其在工业上的应用,冷凝水-试验气候DIN 50021 用不同量氯化钠溶液进行喷雾试验DIN 55996-1 涂覆材料;涂层耐碎石打击性试验;第1部分;多次打击试验DIN EN 228 汽车燃料,无铅汽油,技术要求和试验方法DIN EN 590 汽车燃料,柴油,技术要求和试验方法DIN EN ISO 2409 油漆和涂料;网格法试验DIN EN ISO 4628-1 涂料,涂层故障评估,损伤的数量与大小,以及外观上均匀变化强度的计值;第1部分:一般介绍和计值方法DIN EN ISO 4628-8 涂料,涂层故障评估,损伤的数量与大小,以及外观上均匀变化强度的计值;第8部分:在一些划痕上腐蚀的计值.DIN EN ISO 7253 涂料,抗中性盐雾稳定性的测定.。
金属的防护方法

金属的防护方法
金属在我们的生活中无处不在,从日常用品到工业设备,都离不开金属的身影。
然而,金属也会面临腐蚀等问题,这就需要我们采取有效的防护方法。
金属防护的方法有很多,其中比较常见的就是涂层防护啦。
就像给金属穿上一件保护衣一样。
具体步骤呢,首先要把金属表面清理干净,可不能有灰尘、油污啥的,这就好比要给人穿新衣服得先把身体洗干净呀!然后选择合适的涂层材料,小心翼翼地涂在金属表面,要涂得均匀、全面,不能有遗漏的地方哦!在这个过程中,可得注意操作规范呀,不然涂层效果可就大打折扣了。
还有啊,不同的金属适用的涂层也不一样,得选对才行呢!
在进行金属防护的过程中,安全性和稳定性那可是至关重要的呀!要是不小心出了问题,那可不得了。
比如说,在使用一些化学涂层材料时,得注意通风,不然对人体可不好呢。
而且操作过程中也要严格按照要求来,不能马虎大意,不然可能会导致涂层不均匀或者出现其他问题,那不是白忙活啦!
涂层防护的应用场景那可多了去了。
像汽车、船舶、建筑等领域都广泛应用呢。
它的优势也很明显呀,成本相对较低,防护效果又好,还能起到装饰的作用呢,多棒呀!
就拿汽车来说吧,大家都知道汽车经常暴露在外面,风吹日晒雨淋的,如果没有好的防护,那很快就会生锈腐蚀啦。
但是有了涂层防护,就能很好地保护汽车的金属部件,延长汽车的使用寿命。
我就见过一辆老车,因为主人爱护有加,做了很好的涂层防护,开了很多年还跟新的差不多呢!
总之,金属防护方法真的太重要啦!我们可得重视起来,选择合适的防护方法,让金属更好地为我们服务呀!。
GCM金属表面防腐防护方法

GCM金属表面防腐防护方法摘要:本文介绍一种使金属结构不被腐蚀,延长金属材料的使用寿命的金属表面防腐防护方法。
关键词:金属防腐GCM防护系统经济性一、前言桥梁工程钢管墩柱、吊桥主缆等关键部位,常年处于大气条件下,经受风霜雨雪和日光照射等外界介质的侵蚀,金属结构将发生不同程度的腐蚀,为了延长构件的使用寿命,必须对金属结构采取一定的防护措施。
二、GCM防腐防护系统GCM防腐防护方法,在金属表面形成三层结构:第一层为隔离层,第二层为加强层,第三层为耐候层。
防护原理:第一层:隔离层,也称密闭层,隔离层用高分子材料不饱和聚脂树脂加入引发剂喷射在金属表面,与金属表面咬和,引发剂分解产生自由基,引发不饱和聚脂树脂线型分子链中的不饱和双键与交联剂苯乙烯发生自由基连锁反应而形成网状体型大分子,在金属表面形成隔离模—由于液态树脂中作为溶剂的苯乙烯在固化成膜时作为交联剂参与反应,不存在溶剂挥发现象,形成隔离膜,该隔离膜可以认为是一个具有如下结构单元的巨型分子式:-CH2-CH-C-CH-CH2-O-OH-O-CH2-CH-O-C-CH-CH2-因而其具有其致密性、隔离性特征。
分子链中侧基-OH基是具有强极性官能团,与金属材料极性界面之间具有较强的亲和力。
加之金属表面较为粗糙,使亲和力界面面积大为增加,从而实现隔离层和被保护表面间的粘附效果,能有效地将空气中的氧、水及腐蚀性气体等介质与金属表面隔离开来,使金属表面免遭介质侵蚀。
第二层,强度层是一种高强度纤维—玻璃纤维增强的热固性高分子材料,其基体材料与第一层使用相同的在不饱和聚脂树脂中加入引发剂材料,强度层的比强度较优质钢材要高,拉伸强度可达180Mpa以上,弯曲强度可达200Mpa,强度层与隔离层和耐厚层间拉伸强度可达60Mpa以上;强度层的连续搭接被覆使整个被防护工作表面形成一个整体的具有高强度严密包裹隔离层的体系,切实有效地保护住对金属表面起防护作用的隔离层不受外力的直接损害。
金属表面防护技术.doc
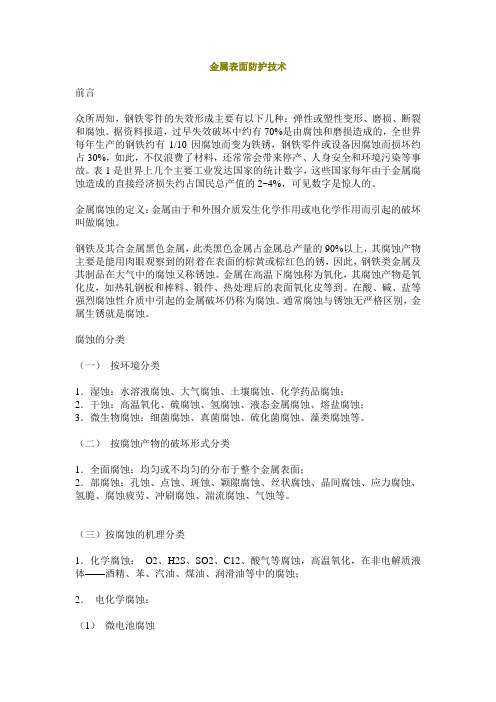
金属表面防护技术前言众所周知,钢铁零件的失效形成主要有以下几种:弹性或塑性变形、磨损、断裂和腐蚀。
据资料报道,过早失效破坏中约有70%是由腐蚀和磨损造成的,全世界每年生产的钢铁约有1/10因腐蚀而变为铁锈,钢铁零件或设备因腐蚀而损坏约占30%,如此,不仅浪费了材料,还常常会带来停产、人身安全和环境污染等事故。
表1是世界上几个主要工业发达国家的统计数字,这些国家每年由于金属腐蚀造成的直接经济损失约占国民总产值的2~4%,可见数字是惊人的。
金属腐蚀的定义:金属由于和外围介质发生化学作用或电化学作用而引起的破坏叫做腐蚀。
钢铁及其合金属黑色金属,此类黑色金属占金属总产量的90%以上,其腐蚀产物主要是能用肉眼观察到的附着在表面的棕黄或棕红色的锈,因此,钢铁类金属及其制品在大气中的腐蚀又称锈蚀。
金属在高温下腐蚀称为氧化,其腐蚀产物是氧化皮,如热轧钢板和棒料、锻件、热处理后的表面氧化皮等到。
在酸、碱、盐等强烈腐蚀性介质中引起的金属破坏仍称为腐蚀。
通常腐蚀与锈蚀无严格区别,金属生锈就是腐蚀。
腐蚀的分类(一)按环境分类1.湿蚀:水溶液腐蚀、大气腐蚀、土壤腐蚀、化学药品腐蚀;2.干蚀:高温氧化、硫腐蚀、氢腐蚀、液态金属腐蚀、熔盐腐蚀;3.微生物腐蚀:细菌腐蚀、真菌腐蚀、硫化菌腐蚀、藻类腐蚀等。
(二)按腐蚀产物的破坏形式分类1.全面腐蚀:均匀或不均匀的分布于整个金属表面;2.部腐蚀:孔蚀、点蚀、斑蚀、颖隙腐蚀、丝状腐蚀、晶间腐蚀、应力腐蚀、氢脆、腐蚀疲劳、冲刷腐蚀、湍流腐蚀、气蚀等。
(三)按腐蚀的机理分类1.化学腐蚀:O2、H2S、SO2、C12、酸气等腐蚀,高温氧化,在非电解质液体——酒精、苯、汽油、煤油、润滑油等中的腐蚀;2.电化学腐蚀:(1)微电池腐蚀(2)原电池腐蚀:电偶腐蚀、杂散电流腐蚀、浓差电池腐蚀。
如:潮湿空气中的大气腐蚀,酸、碱、盐溶液和海水中腐蚀,土壤腐蚀,不同金属接触处的腐蚀,其它电解质溶液中的腐蚀。
金属腐蚀的防护方法

金属腐蚀的防护方法金属腐蚀是一个全球性的问题,对材料、设备、设施和结构产生重大影响。
为了防止和减轻金属腐蚀的危害,以下是一些常用的金属腐蚀防护方法:1.涂层保护:涂层保护是一种常见的金属腐蚀防护方法。
通过在金属表面涂覆一层耐腐蚀的涂层,如油漆、涂料、塑料等,隔离金属与腐蚀介质,从而减缓或阻止金属腐蚀的进程。
2.改变金属结构:改变金属结构可以改变金属在腐蚀环境中的耐蚀性能。
例如,通过合金化添加耐腐蚀元素,提高金属表面的耐蚀性能。
此外,还可以采用耐腐蚀的合金材料,如不锈钢、钛合金等。
3.电化学保护:电化学保护是通过外部电流或牺牲阳极等方法改变金属表面的电化学状态,使金属表面形成一层保护膜,防止腐蚀介质与金属接触,从而达到防止腐蚀的目的。
4.表面处理:表面处理是通过物理或化学方法改变金属表面的形貌和结构,提高金属表面的耐蚀性能。
例如,表面抛光、喷砂处理、钝化处理等。
5.介质处理:介质处理是通过改变环境中的腐蚀介质来达到防止腐蚀的目的。
例如,去除环境中的腐蚀性气体或离子,控制湿度、温度等环境因素。
6.缓蚀剂:缓蚀剂是一种能够降低金属腐蚀速率的物质。
它们可以吸附在金属表面,形成一层保护膜,或改变金属表面的电化学状态,从而减缓或阻止金属腐蚀的进程。
7.温度控制:温度控制是通过控制环境中的温度来达到防止腐蚀的目的。
例如,通过加热、冷却、控制工作温度等方式,使金属表面保持干燥或维持适宜的温度范围。
8.维护保养:维护保养是通过定期检查、清洁、润滑、维修等方式来保持金属设备和设施的良好状态。
及时发现并修复腐蚀损伤,防止腐蚀进一步发展,是防止金属腐蚀的重要措施之一。
综上所述,以上这些方法可以单独或结合使用,以有效地防止和减轻金属腐蚀的危害。
在实际应用中,应根据具体的情况选择合适的方法。
列举金属的防护措施

列举金属的防护措施金属是人类生产生活中不可或缺的材料,但同时也容易受到外界环境的侵蚀和损害。
为了延长金属的使用寿命,保护其表面,需要采取一系列防护措施。
一、防锈涂料防锈涂料是一种常见的金属防护措施。
它可以在金属表面形成一层保护膜,隔绝空气、水分等外界因素对金属的侵蚀和氧化。
常用的防锈涂料有底漆、面漆和清漆等。
其中底漆是最基础的一种,可以提高涂层附着力和耐腐蚀性;面漆则可以增加美观度和耐候性;清漆则可以保持金属表面光洁度。
二、电镀电镀是利用电解作用在金属表面镀上一层金属或合金覆盖物来达到防护目的。
这种方法不仅可以增加金属表面硬度、耐磨性和耐腐蚀性,还可以美化表面色泽。
常见的电镀方法有镍电镀、铬电镀、铜电镀、锌电镀等。
三、热浸镀热浸镀是将金属材料浸入熔化的金属液中,使其表面形成一层保护膜的方法。
这种方法可以提高金属表面硬度和耐腐蚀性,同时也可以美化表面。
常见的热浸镀方法有热浸锌、热浸铝、热浸锡等。
四、喷涂喷涂是将涂料通过喷枪均匀地喷射到金属表面上,形成一层保护膜来达到防护目的。
这种方法不仅简单方便,而且可以在大型工件上进行操作。
常见的喷涂方法有气动喷涂、电动喷涂和高压空气喷涂等。
五、钝化处理钝化是指通过一定的处理方式使金属表面形成一层致密的氧化物或盐类覆盖物,以隔绝外界因素对金属的侵蚀和氧化。
常见的钝化处理方法有酸洗钝化、碱洗钝化和电解钝化等。
六、阳极保护阳极保护是利用外加电源将金属作为阳极,使其表面形成一层氧化膜来保护金属的方法。
这种方法可以提高金属表面硬度和耐腐蚀性,同时也可以美化表面。
常见的阳极保护方法有铝阳极氧化、镀锌等。
七、涂覆保护剂涂覆保护剂是一种直接涂覆在金属表面上的防护措施。
它可以形成一层均匀的保护膜,隔绝外界因素对金属的侵蚀和氧化。
常见的涂覆保护剂有沥青、聚合物、橡胶等。
八、其他防护措施除了以上几种防护措施外,还有一些其他的防护措施。
例如,在海洋环境下,可以采用海水冷却系统来降低金属材料受到海水侵蚀和损害的风险;在高温环境下,可以采用隔热材料来降低金属材料受到高温侵蚀和损害的风险。
金属材料表面处理的腐蚀与防护技术

金属材料表面处理的腐蚀与防护技术随着工业化进程的加速发展,金属材料的使用范围越来越广泛,从机械、汽车、电气、电子、石油化工到航空航天等各行各业都离不开金属材料。
然而,金属材料的一大弊端就是易于腐蚀,导致减少使用寿命和安全问题,因此需要进行表面处理来延长使用寿命,提高耐久性和抗腐蚀性。
本文将阐述金属材料表面处理的腐蚀与防护技术。
一、腐蚀的影响1.1 金属腐蚀的定义金属在与制造它的环境接触时,通过电化学反应被腐蚀,称为金属腐蚀。
金属腐蚀主要是由于化学反应、电化学反应、气体腐蚀、水腐蚀、微生物腐蚀等因素的综合作用产生的。
1.2 腐蚀的影响腐蚀会影响金属的物理性质、机械性能、化学性质、外观质量等方面。
例如,金属材料的抗压、抗拉、抗弯等机械性能会因腐蚀而降低;金属表面的质量受到腐蚀的影响较大,例如生锈、变色、起泡等现象会降低产品的美观度;腐蚀还会造成管道、容器、设备等的漏水、泄漏、损坏等。
1.3 腐蚀分类根据腐蚀的不同成因,可以将其形式分为以下几种:1.3.1 化学腐蚀:由于材料表面的化学和物理性质产生变化而引起的腐蚀。
1.3.2 电化学腐蚀:由于金属和氧气、水和电解质等介质接触,而在金属表面形成各种电偶,导致电极反应,从而引起的腐蚀。
1.3.3 气体腐蚀:由于一些气体(例如酸瘤、硫化氢)与金属或合金表面相接触,而引起金属表面的化学变化,从而引起金属腐蚀。
1.3.4 水腐蚀:由于金属和水或水中的离子等介质接触,而引起的腐蚀。
1.3.5 微生物腐蚀:由于一些微生物在金属表面形成了一个微观环境,从而引起金属表面的腐蚀。
二、金属材料表面处理技术为了提高金属材料的使用寿命和抗腐蚀性,需要经过一系列的表面处理技术,主要有机械处理、化学处理、电化学处理、涂覆技术等。
2.1 机械处理机械处理是表面处理技术中最简单、经济的方法,主要有打磨、抛光、拉丝等,能有效去除材料表面的腐蚀产物和污染物,平整表面,使材料表面更易于涂覆。
金属材料表面处理与腐蚀防护
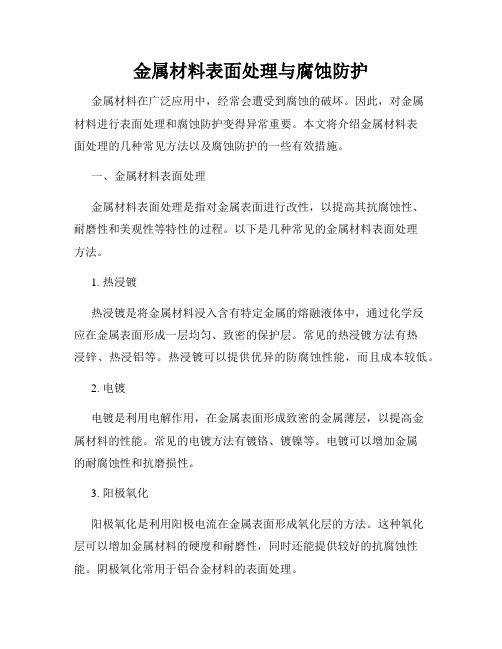
金属材料表面处理与腐蚀防护金属材料在广泛应用中,经常会遭受到腐蚀的破坏。
因此,对金属材料进行表面处理和腐蚀防护变得异常重要。
本文将介绍金属材料表面处理的几种常见方法以及腐蚀防护的一些有效措施。
一、金属材料表面处理金属材料表面处理是指对金属表面进行改性,以提高其抗腐蚀性、耐磨性和美观性等特性的过程。
以下是几种常见的金属材料表面处理方法。
1. 热浸镀热浸镀是将金属材料浸入含有特定金属的熔融液体中,通过化学反应在金属表面形成一层均匀、致密的保护层。
常见的热浸镀方法有热浸锌、热浸铝等。
热浸镀可以提供优异的防腐蚀性能,而且成本较低。
2. 电镀电镀是利用电解作用,在金属表面形成致密的金属薄层,以提高金属材料的性能。
常见的电镀方法有镀铬、镀镍等。
电镀可以增加金属的耐腐蚀性和抗磨损性。
3. 阳极氧化阳极氧化是利用阳极电流在金属表面形成氧化层的方法。
这种氧化层可以增加金属材料的硬度和耐磨性,同时还能提供较好的抗腐蚀性能。
阴极氧化常用于铝合金材料的表面处理。
4. 喷涂涂层喷涂涂层是将具有抗腐蚀性的聚合物、陶瓷等材料喷涂到金属表面的方法。
喷涂涂层可以提供良好的防腐蚀性能和绝缘性能,还可以改善金属表面的外观。
二、腐蚀防护金属材料腐蚀会导致材料性能的下降甚至失效,因此采取腐蚀防护措施变得至关重要。
下面是一些常用的腐蚀防护措施。
1. 防腐涂层防腐涂层是在金属表面涂覆一层具有防腐蚀性能的材料。
常见的防腐涂层有油漆涂层、涂覆聚合物涂层和涂层铝锌锡等。
涂层的选择应根据金属材料的使用环境、材料特性和预期寿命等因素进行。
2. 电化学保护电化学保护是通过外加电流将金属部件的电位移动到一个较不容易被腐蚀的区域,以减缓金属腐蚀的过程。
常见的电化学保护方法有阳极保护和阴极保护。
3. 金属合金化金属合金化是将金属材料与其他金属或非金属元素混合,在其组织结构中形成均匀分布的合金相,以提高材料的性能和耐腐蚀性。
4. 定期维护定期维护是指定期检查和修复金属材料的腐蚀损伤。
- 1、下载文档前请自行甄别文档内容的完整性,平台不提供额外的编辑、内容补充、找答案等附加服务。
- 2、"仅部分预览"的文档,不可在线预览部分如存在完整性等问题,可反馈申请退款(可完整预览的文档不适用该条件!)。
- 3、如文档侵犯您的权益,请联系客服反馈,我们会尽快为您处理(人工客服工作时间:9:00-18:30)。
金属表面防护技术前言众所周知,钢铁零件的失效形成主要有以下几种:弹性或塑性变形、磨损、断裂和腐蚀。
据资料报道,过早失效破坏中约有70%是由腐蚀和磨损造成的,全世界每年生产的钢铁约有1/10因腐蚀而变为铁锈,钢铁零件或设备因腐蚀而损坏约占30%,如此,不仅浪费了材料,还常常会带来停产、人身安全和环境污染等事故。
表1是世界上几个主要工业发达国家的统计数字,这些国家每年由于金属腐蚀造成的直接经济损失约占国民总产值的2~4%,可见数字是惊人的。
金属腐蚀的定义:金属由于和外围介质发生化学作用或电化学作用而引起的破坏叫做腐蚀。
钢铁及其合金属黑色金属,此类黑色金属占金属总产量的90%以上,其腐蚀产物主要是能用肉眼观察到的附着在表面的棕黄或棕红色的锈,因此,钢铁类金属及其制品在大气中的腐蚀又称锈蚀。
金属在高温下腐蚀称为氧化,其腐蚀产物是氧化皮,如热轧钢板和棒料、锻件、热处理后的表面氧化皮等到。
在酸、碱、盐等强烈腐蚀性介质中引起的金属破坏仍称为腐蚀。
通常腐蚀与锈蚀无严格区别,金属生锈就是腐蚀。
腐蚀的分类(一)按环境分类1.湿蚀:水溶液腐蚀、大气腐蚀、土壤腐蚀、化学药品腐蚀;2.干蚀:高温氧化、硫腐蚀、氢腐蚀、液态金属腐蚀、熔盐腐蚀;3.微生物腐蚀:细菌腐蚀、真菌腐蚀、硫化菌腐蚀、藻类腐蚀等。
(二)按腐蚀产物的破坏形式分类1.全面腐蚀:均匀或不均匀的分布于整个金属表面;2.部腐蚀:孔蚀、点蚀、斑蚀、颖隙腐蚀、丝状腐蚀、晶间腐蚀、应力腐蚀、氢脆、腐蚀疲劳、冲刷腐蚀、湍流腐蚀、气蚀等。
(三)按腐蚀的机理分类1.化学腐蚀:O2、H2S、SO2、C12、酸气等腐蚀,高温氧化,在非电解质液体——酒精、苯、汽油、煤油、润滑油等中的腐蚀;2.电化学腐蚀:(1)微电池腐蚀(2)原电池腐蚀:电偶腐蚀、杂散电流腐蚀、浓差电池腐蚀。
如:潮湿空气中的大气腐蚀,酸、碱、盐溶液和海水中腐蚀,土壤腐蚀,不同金属接触处的腐蚀,其它电解质溶液中的腐蚀。
影响金属锈蚀的主要因素(一)金属锈蚀的内部因素从热力学角度而言,金属和它的腐蚀产物相比,具有较高的能量,是不稳定的,有自发的向低能量的腐蚀产物转化的趋势,即金属发生锈蚀是自然现象。
工业中绝大多数的金属是多组分的合金,金相组织不同、含有杂质、机加工变形不均匀、应力分布不均匀等,这些物理的、化学的和电化学的不均匀性,当表面遇到腐蚀介质或表面形成水膜,不可避免地会发生化学或电化学腐蚀。
(二)金属腐蚀的外部因素1.相对温度的影空气中相对湿度越高,金属表面水膜越厚,空气中的氧透过水膜到金属表面作用。
相对湿度达到一定数值时,腐蚀速度大幅上升,这个数值称为临界相对湿度,钢的临界相对湿度约为70%。
2.温度的影响环境温度与相对湿度关联,干燥的环境(沙漠)下,气温再高金属也不容易锈蚀。
当相对湿度达到临界值时,温度的影响明显加剧,温度每增加10℃,锈蚀速度提高两倍。
因此,在湿热带或雨季,气温越高,锈蚀越严重。
3.氧气的影响用下列反应式表示生锈过程:Fe+H2O→Fe(OH)2Fe(OH)2+ H2O+O2→Fe(OH)3Fe+ H2O+O2→Fe(OH)3可见没有水和氧气,金属就不会生锈,空气中20%体积是氧气,它是无孔不入的。
4.大气其它物质的影响大气中含有盐雾、二氧化硫、硫化氢和灰尘时,会加速腐蚀,因此,不同环境下受腐蚀的大小差别是明显的,城市高于农村;工业区高于生活区;沿海高于内陆;高粉尘高于低粉尘。
(三)加工过程中的锈蚀因素原材料已锈蚀,加工后未能完成去除;加工中接触了切削液,润滑剂等工艺材料;酸洗后中和清洗不当;热处理氧化脱碳或残盐清洗不净;检查、搬运和装配时操作者留下的手汗;去应力或去氢退火不当;工序间和封存防锈不适宜等。
防止金属生锈的主要方法(一)选择耐蚀材料主要是采用有色金属合金和不锈钢。
(二)金属表面预制金属(合金)或非金属覆盖层1.转化膜:发黑(发蓝)、磷化、阳极氧化;2.表面合金化:渗氮、渗锌、渗硅、渗铝、渗铬等;3.金属覆盖层:电镀金属、喷涂金属、热浸镀、化学镀等;4.非金属覆盖层:搪瓷、陶瓷、油漆、塑料、橡胶等;5.涂覆防锈材料:防锈水、切削液、气相缓蚀剂、可剥塑料、防锈油、防锈脂等。
(三)阴极保护法以牺牲阳极而保护阴极的电化学法。
如在海水中,以镁块作阳极与钢板联在一起,通以电流使钢板变成阴极得以保护。
地下管道和化工设备,也是外另一个阳极并通电使钢件(阴极)得到保护。
(四)控制环境防蚀1.采用除湿机和加湿降低温度,相对湿度控制在低于60~70%,金属锈蚀减慢;相对湿度低于60%时,非金属不会发霉变质;2.充氮或真空包装封存可延缓锈蚀;3.包装内置缓蚀剂;4.钢铁制品在电炉加热(高温)时,炉内形成保护气氛或真家加热。
综上所述,防止金属锈蚀的方法很多,应考虑诸多因素后判断选择,如:零件的工作环境、零件的服役条件、生产的安全性、对环境的污染程度、制造成本等。
二、常用的几种表面防护技术(一)电镀采用电解的方法在基体(经过前处理)表面沉积所需要的覆盖层的过程称为电镀。
电镀是非常古老的传统技术,广泛应用于永久性的装饰和防护。
电镀可以分为单金属电镀,多层组合电镀,以及合金电镀等。
影响镀层质量的因素很多,如:镀前处理、镀液的净化方式和程度、予镀方式的合理性、镀液体系建立、组合及厚度的确定、工艺参数(PH值、温度、电流密度)、添加剂(光亮剂、整平剂、除应力剂、润湿剂、分散剂)、镀液分析及补充制度、操作制度、镀后处理(去氢、封闭)等。
由于电镀三废对环境污染和影响健康,各地环保部门管理日趋严格,很多企业自己不设电镀车间,而是去专业厂(车间)委托加工。
为确保电镀件的质量,应依据有关标准和规定对镀层的外观、结合力、厚度、孔隙率、耐蚀性等提出具体的要求。
一旦验收时或使用中出现质量问题,便于质量事故分析和改进。
(二)氧化氧化处理分为黑色金属氧化处理和有色金属氧化处理两类,这里仅涉及前者。
钢铁及合金的氧化处理,又称发蓝或发黑处理。
由于其成本低、效率高、收效快、工艺稳定、操作方便、设备简单,使用范围十分广泛。
1.碱性化学氧化法碱性氧化法是最常用的方法,它是在较高温度下,在含有一定氧化剂的氢氧化钠溶液中进行。
氧化剂和氢氧化钢与金属铁发生化学反应,最终形成氧化铁(Fe3O4)为主要成分的氧化膜。
膜的颜色取决于零件的表面状态、合金成分和氧化处理的工艺条件,一般为黑色或兰黑色。
膜厚0.6~0.8um.化学反应的顺序是无形成亚铁酸纳(Na2Fe02)和铁酸纳(Na2Fe204),然后由亚铁酸钠与铁酸钠反应形成Fe304氧化膜。
反应式如下:3Fe+Na02+5Na0H→3Na2Fe02+H20+NH3↑6Na2Fe02+NaN02+5H20→3Na2Fe204+7Na0H+NH3↑Na2Fe02+Na2Fe204+2H20→Fe304+4Na0H(1)碱性氧化法溶液配方及工艺规范(2)溶液的配制在氧化槽内加入2/3体积的水,将计算量的氢氧化钠加入槽内,使其溶解;在搅拌下加入亚硝酸钠或硝酸钠,待全部溶解后,加水至规定体积。
氧化液先在沸腾温度下浸入钢板,或加入部分旧溶液(约20%以下)进行处理,待溶液中积累了一定的铁离子,能使样片获得黑色氧化膜后,即可用于生产。
(3)溶液的维护1 氧化溶液在使用中消耗会使组分变化,可定期按分析结果补充,亦可按溶液的沸点和膜层质量来判定溶液需否调整。
当沸点过高时,表示浓度过高,此时易形成红色挂灰,可加水稀释。
沸点过低时,表示浓度不足,此时膜的颜色不深或不能发黑,应补加药品或蒸发多余水分。
氢氧化钠的添加量,可按溶液沸点每高1℃,每升溶液添加10~15g计算。
亚硝酸钠的加入量可参照如下比例:一次氧化:Na0H:NaN02=(2~3):1;二次氧化:Na0H:NaN02=(2.5~3.5):1(一槽);Na0H:NaN02=(3.4):1(二槽)。
2 停产期间溶液表面硬结,加热之前应先用铁器打碎硬皮,加水至工作液面,搅拌均匀后升温至工作温度。
3 清理漏入槽中零件应及时打捞,避免溶液中铁离子增加。
定期除渣保持溶液清洁,工作温度下投入零件前,液面浮起的大量红褐色铁氧化物应用网捞出。
亦可在100℃以下搅拌情况下,按每升溶液加入甘油5~10ml的比例加入。
4 操作氧化膜中杂质的红色挂灰,多为氧化初期形成。
进行一次氧化时,最好在零件入槽10分钟后,取出用热水冲洗,观察有无红色挂灰。
如有可用毛刷擦除,或将零件放入含150~200g/L铬酐和10~15g/L的硫酸的溶液中,浸1~1.5分后清洗,重新入槽氧化。
氧化过程中定期抖动零件也是必要的。
5 槽液的使用期限处理量和溶液的维护程度直接影响槽液使用期限,更换时,可先澄清1~2天,清除表层和沉淀的残渣后,澄清的部分用来配制新溶液。
6氧化温度和时间同钢的含碳量有密切关系,选择这些参数时,可参考下表2所列数据。
表2 氧化温度、时间与含碳量的关系(4)氧化后的处理后处理的目的在于提高氧化膜的防锈能力,一般进行皂化或填充处理,其配方规范如表3表示。
表3钢铁氧化后处理工艺规范经填充或皂化后,还进行封闭处理,可在100~110℃下的机油、锭子油、变压器油中浸5~10分钟。
如不进行填充或皂化处理,氧化后经清洗,可直接进入脱水防锈油。
2.酸性化学氧化法(常温发黑)同碱性化学氧化相比,常温发黑具有节能优点,仍需进行除油、漂洗、酸蚀、漂洗以及后处理。
市场上常温发黑剂品种较多,可直接先购应用,但膜与基体的附着力还有待提高。
三、磷化金属表面在含有磷酸、磷酸盐和其他化学药品的稀溶液中发生化学反应,转变成完整的,具有中等防蚀作用的不溶性磷酸盐膜层的工艺,叫磷化处理。
这类转化膜的形成是人工诱导及控制的腐蚀过程。
磷化膜的用途很广,主要是由磷化膜的种类和厚度所决定。
厚膜磷化常常用作单独防护(浸油、油脂、蜡等)、电绝缘(如硅钢片)、耐磨、冷成型(拉、拔、冷挤压、冲压等)、薄膜磷化则主要用于工序间的防护及油漆和粉末等有机涂层的基底。
1.磷化的分类(1)按磷化膜的转化形式分类1转化型磷化:溶液对金属基体腐蚀,由金属基体提供阳离子与溶液中P043-的结合成膜的磷化(如铁系膜)。
2伪转化型磷化:膜中主要阳离子(锌、猛、铬)由溶液提供的磷化。
(2)按磷化液及磷化膜的成分分类有锌系、锰系、锌钙系、锌猛系、铁系、钙系、锌猛镍系、锌猛镍钙系等。
(3)按磷化膜结晶形状分类1结晶型:如磷酸锌膜、磷酸锌锰膜、磷酸锌钙膜、磷酸铁(Ⅱ)膜、磷酸锰铁膜等。
2无定型:主要是铁(Ⅲ)系磷化膜。
(4)按膜重和用途分类1膜重:膜重指单位面积膜层重量,通常以g/m2表示。
可分为重量级、中量级和轻量级。
如表4所示:表4 磷化膜类型及重量等级2用途:A.涂装前底层磷化:用于涂漆、浸漆、喷塑。
B.促进冷成型磷化:手于拔比、拔管、冷冲压、冷挤压、冷拉伸。