新能源汽车特拉斯车身结构材料分析报告
特斯拉压铸铝的化学成分
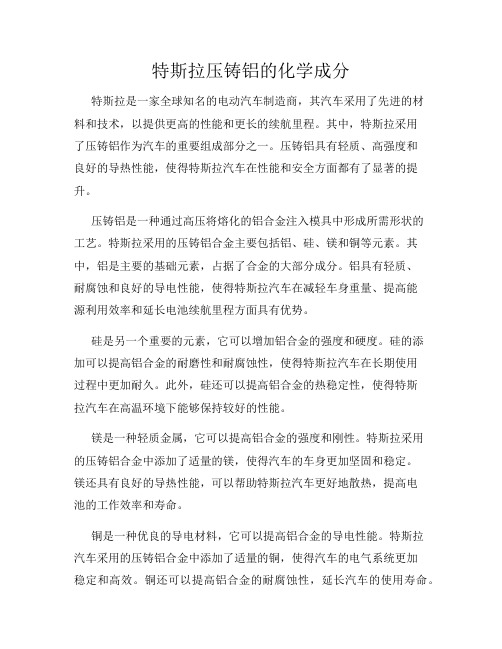
特斯拉压铸铝的化学成分特斯拉是一家全球知名的电动汽车制造商,其汽车采用了先进的材料和技术,以提供更高的性能和更长的续航里程。
其中,特斯拉采用了压铸铝作为汽车的重要组成部分之一。
压铸铝具有轻质、高强度和良好的导热性能,使得特斯拉汽车在性能和安全方面都有了显著的提升。
压铸铝是一种通过高压将熔化的铝合金注入模具中形成所需形状的工艺。
特斯拉采用的压铸铝合金主要包括铝、硅、镁和铜等元素。
其中,铝是主要的基础元素,占据了合金的大部分成分。
铝具有轻质、耐腐蚀和良好的导电性能,使得特斯拉汽车在减轻车身重量、提高能源利用效率和延长电池续航里程方面具有优势。
硅是另一个重要的元素,它可以增加铝合金的强度和硬度。
硅的添加可以提高铝合金的耐磨性和耐腐蚀性,使得特斯拉汽车在长期使用过程中更加耐久。
此外,硅还可以提高铝合金的热稳定性,使得特斯拉汽车在高温环境下能够保持较好的性能。
镁是一种轻质金属,它可以提高铝合金的强度和刚性。
特斯拉采用的压铸铝合金中添加了适量的镁,使得汽车的车身更加坚固和稳定。
镁还具有良好的导热性能,可以帮助特斯拉汽车更好地散热,提高电池的工作效率和寿命。
铜是一种优良的导电材料,它可以提高铝合金的导电性能。
特斯拉汽车采用的压铸铝合金中添加了适量的铜,使得汽车的电气系统更加稳定和高效。
铜还可以提高铝合金的耐腐蚀性,延长汽车的使用寿命。
除了上述主要元素外,特斯拉汽车的压铸铝合金中还可能添加其他微量元素,以进一步改善合金的性能。
这些微量元素可以根据特定的需求进行调整,以满足特斯拉汽车在不同方面的要求。
总之,特斯拉压铸铝的化学成分主要包括铝、硅、镁和铜等元素。
这些元素的添加可以提高铝合金的强度、硬度、导热性能和导电性能,使得特斯拉汽车在性能和安全方面都有了显著的提升。
特斯拉汽车的采用压铸铝作为重要组成部分,不仅体现了其对材料科学的深入研究和创新,也为电动汽车行业的发展做出了重要贡献。
电动汽车的车身材料与碰撞安全性

电动汽车的车身材料与碰撞安全性随着环保意识的增强和技术的进步,电动汽车逐渐成为人们选择的热门车型。
而与传统燃油汽车相比,电动汽车在车身材料和碰撞安全性方面的特点也备受关注。
本文将就电动汽车的车身材料以及其在碰撞安全性方面的表现进行探讨。
一、车身材料的选择车身材料对于电动汽车的重量、性能和安全性都起着至关重要的作用。
不同的车身材料具有不同的特点,下面将介绍几种常见的车身材料:1. 铝合金:铝合金是一种轻量化的材料,因其密度低、强度高、耐腐蚀性强等特点而广泛应用于电动汽车的车身制造中。
铝合金车身能够有效减轻整车重量,提高电池续航里程,并在提高驾驶稳定性方面具有突出表现。
2. 碳纤维复合材料:碳纤维复合材料是一种高强度、高刚性、轻质化的车身材料。
其具有优异的抗拉强度和抗弯强度,能够有效吸收碰撞能量并减小车身损伤。
然而,碳纤维复合材料的制造成本较高,仍面临着生产难度和成本控制等问题。
3. 钢材:与传统的燃油汽车相比,电动汽车的车身结构需要更加坚固和耐撞性。
因此,高强度钢材在电动汽车中得以广泛应用。
高强度钢材具有较高的屈服强度和抗冲击能力,能够有效提升车身的整体安全性能。
二、碰撞安全性的考量碰撞安全性是电动汽车设计中必须重视的一个方面。
以下是与电动汽车碰撞安全性相关的几个要素:1. 车身刚性:车身刚性是指车辆在受到外力冲击时不产生过大的形变和破坏,保障车内乘员的安全。
对于电动汽车来说,较高的车身刚性能够有效减少车身结构的变形,提供更好的碰撞保护。
2. 碰撞吸能结构:碰撞吸能结构是指车身的设计能够在碰撞事故中吸收和分散碰撞能量,减少对乘员的伤害。
电动汽车通常使用可压缩材料或者碰撞吸能区域来实现碰撞能量的吸收,以保护乘员的安全。
3. 安全气囊系统:安全气囊是车辆碰撞安全系统中的重要组成部分,能够在碰撞发生时迅速充气以减少乘员碰撞时所承受的冲击力。
电动汽车通常配备多个安全气囊,从多个方向提供乘员全方位的保护。
三、电动汽车的碰撞安全性表现与传统燃油汽车相比,由于电池组的布局和沉重的车重等因素,电动汽车在一些碰撞测试中可能表现出不同的特点。
特斯拉model3 PACK结构和电连接对标报告
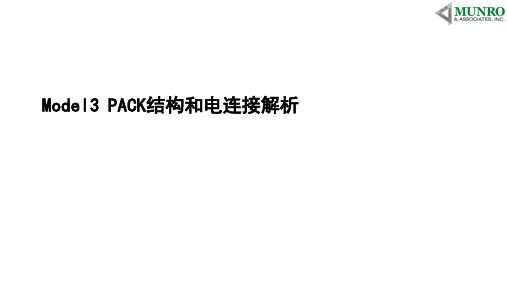
Model3 PACK结构和电连接解析目录页第1部分第2部分第3部分模组结构设计解析箱体结构设计解析高压箱结构解析模组结构设计解析模组信息尺寸重量冷却方式电连接输出方式排布方式46P25S1948*323*8193.5kg集成冷管螺栓错位46P23S1860*323*8186kg集成冷管螺栓错位电芯排布错位排布14排46P23S46P25S阵列75~76阵列82~83机械连接和固定负极盖板冷板胶水塑料侧板塑料侧板正极支架模组对外固定和连接螺栓固定孔一侧卡位+压板0.5mm 铝汇流片正负极铝丝健合在同一侧负极壳体正极盖帽绝缘垫2mm模组正负输出低压采样从控采集板铝丝健合低压对外连接模组间连接连接BMS接口接触防护及安全模组负极塑胶盖板模组侧边塑胶板模组正极支架+吸塑绝缘板电芯间填充胶水冷板表面绝缘处理绝缘盖板绝缘盖板亮点信息及对比Modle 3Bolt 大模组FPC 采样PCB 采样超声焊接超声健合焊接可以实现液冷差异Modle S Modle 3Bolt成本较高;新技术应用;排布规则、细节到位;整体感觉很高大上;成本较低;新技术应用;电连接排布杂乱、细节不是很到位;整体感觉有点“赶时间”;成本较低;新技术应用;排布规则、细节到位;整体感觉中规中矩中有特点;箱体结构设计解析PACK的信息尺寸重量冷却方式箱体材质模组固定方式密封方式PACK2148*1444*335/120mm469.5kg主动冷管钣金螺栓+压板胶粘密封整体排布低压采样低压通讯整体排布规则对称、高低压分开;有足够的安全距离;考虑热管理系统,整体很整洁;高压/控制盒高压连接模组固定螺栓固定压板固定模组固定梁模组固定梁机械强度模组固定纵梁模组固定纵梁模组固定纵梁模组固定纵梁模组固定纵梁模组固定纵梁无横梁增加机械强度-增加固定点数量模组间串联铝巴模组一极输出模组间串联铝巴模组间低压通讯模组间低压通讯模组间低压通讯从控到主控通讯从控到主控通讯接触防护橙色绝缘防护罩半透明绝缘护套蓝色绝缘防护套箱体底部防护安全防护机械强度靠增加固定点来弥补单层壁厚底部球击有些担忧电芯正极朝下安装在,并在正极端涂胶模组间做一定隔离IP防护使用粘接密封下箱体使用一体冲压成型,高低差过度圆滑,斜度较大;上盖使用一体冲压成型,高低差过度圆滑,斜度较大;密封界面子零件设计子零件设计对比一体冲压成型,IP 防护难度降低;通过增加挂点的方式增加结构强度,把一部分的结构强度转嫁给整车,增加了整车的安装难度;箱体加工工艺降低,成本降低,生产效率增加;整体趋近于大众化;冲压成型+型材焊接,IP 难度较高;箱体两侧有强度很高的贯穿型安装部位、内部有贯穿型纵横梁,箱体的强度较高可以增强整车的结构强度;箱体采用较新的工艺,工艺难度较高;生产效率较低,成本偏高;整体技术路线较新颖;高压箱结构解析高压箱+控制器+配电1.充电口连接器2.快充电流接触器总成3.通往 PCS 的冷却管4.功率转化器(PCS)5.高压控制器6.低压连接器7.PCS 的 12V 输出口8.正极高压电开关9.通往 PCS 的冷却管10.通往乘客舱取暖器、空调压缩机的高压电连接器11.乘客舱取暖器、空调压缩机和 PCS 直流输出保险12.后轴电机高压电连接器13.高压电热熔断器15.前轴电机高压电连接器16.负极高压电开关17.三相交流电连接器安装固定在车内空间增加压板固定在车内空间增加压板固定底部金属+塑胶底托缓冲支撑螺栓固定电气件及高压连接及差异高压箱配电箱接触器铝排连接接触防护塑料底托+大量嵌件塑料件绝缘塑料件之间卡扣固定铝排表面没有做绝缘处理亮点信息温度传感器?防护+散热固定+减震差异裸铜?没有表面处理压双线?不做绝缘?。
特斯拉新能源汽车调研报告
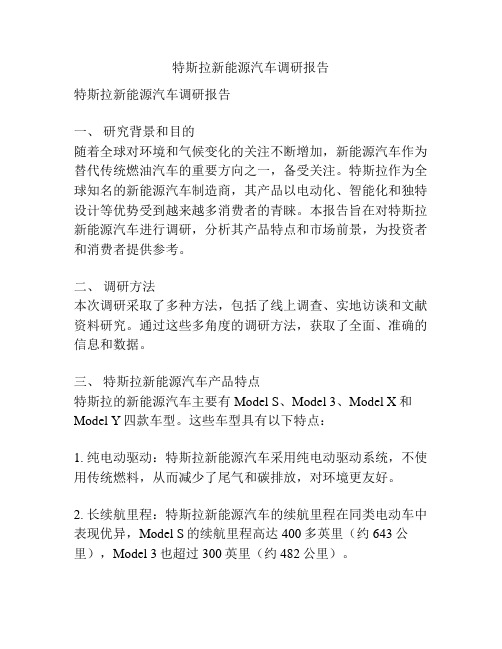
特斯拉新能源汽车调研报告特斯拉新能源汽车调研报告一、研究背景和目的随着全球对环境和气候变化的关注不断增加,新能源汽车作为替代传统燃油汽车的重要方向之一,备受关注。
特斯拉作为全球知名的新能源汽车制造商,其产品以电动化、智能化和独特设计等优势受到越来越多消费者的青睐。
本报告旨在对特斯拉新能源汽车进行调研,分析其产品特点和市场前景,为投资者和消费者提供参考。
二、调研方法本次调研采取了多种方法,包括了线上调查、实地访谈和文献资料研究。
通过这些多角度的调研方法,获取了全面、准确的信息和数据。
三、特斯拉新能源汽车产品特点特斯拉的新能源汽车主要有Model S、Model 3、Model X和Model Y四款车型。
这些车型具有以下特点:1. 纯电动驱动:特斯拉新能源汽车采用纯电动驱动系统,不使用传统燃料,从而减少了尾气和碳排放,对环境更友好。
2. 长续航里程:特斯拉新能源汽车的续航里程在同类电动车中表现优异,Model S的续航里程高达400多英里(约643公里),Model 3也超过300英里(约482公里)。
3. 快速充电:特斯拉新能源汽车支持Supercharger快速充电技术,可以在短时间内充满电,满足长途驾驶需求。
4. 智能化功能:特斯拉新能源汽车配备了智能驾驶功能,包括自动驾驶、自动泊车和自动紧急制动等,提升了驾驶的安全性和便捷性。
四、特斯拉新能源汽车市场前景特斯拉作为新能源汽车的领军企业,在全球市场具有强大的竞争力。
以下是特斯拉新能源汽车市场前景的几个重要因素:1. 政策支持:越来越多的国家和地区出台政策支持新能源汽车发展,如减免购置税、补贴和免费充电等,为特斯拉等企业提供了发展的机遇。
2. 市场需求:随着环保意识的增强和能源消耗的减少,消费者对新能源汽车的需求不断增加。
特斯拉作为高品质、高性能的新能源汽车品牌,能够受到更多消费者的青睐。
3. 科技创新:特斯拉在电池技术、自动驾驶技术和智能化功能方面的持续创新,使其产品具备了竞争优势,吸引了众多投资者和合作伙伴。
2017年特斯拉产业链上游车身与生产链分析报告

2017年特斯拉产业链上游车身与生产链分析报告2017年8月目录一、金属车身 (4)1、旭升股份:迅速成长的特斯拉供应商 (5)2、挪威海德鲁:车用铝材的先行者 (6)3、Shiloh Industries:全球领先的轻量化、噪声与振动解决方案供应商 (8)4、Arconic:航空与汽车铝材的专业制造商 (9)5、肯联铝业Constellium:国际领先航天铝板生产商 (11)6、AK钢铁: 特斯拉冷轧铝涂层不锈钢供应商 (12)二、轮胎 (13)1、韩泰轮胎(HANKOOK TIRE):韩国轮胎龙头 (14)2、横滨橡胶:高性能、低滚动阻力轮胎供应商 (16)3、Superior Industries公司:北美最大铝合金轮毂制造商 (16)三、车身装配件 (18)1、鸿海集团:富士康母公司 (19)2、Magna麦格纳:世界最大的后视镜供应商和四驱系统供应商 (19)3、宜安科技:全球唯一一家具备大块非晶成型能力企业 (21)4、美国镜泰公司:后视镜里的高科技 (23)5、旭硝子株式会社:全球第一大玻璃制造企业 (25)四、涂料 (27)1、BASF巴斯夫:全球最大化工企业 (27)2、Axalta艾仕得:全球汽车涂料领先企业 (28)五、生产链 (29)1、发那科:日本机器人制造业龙头 (30)2、Kuka:来自德国,世界领先机器人制造商 (31)3、ExOne: 3D打印材料新突破 (32)金属车身。
特斯拉的车身结合了高强度硼钢加强件与新型全铝挤压件、冲压件和铸件,实现需要的刚度和强度,旗舰车型Model S连续荣获美国高速公路安全管理局及欧洲新车安全协会的“双五星”安全评级。
特斯拉的车身铝合金部件是特斯拉购买北美最大的冲压线和定制模具在其弗里蒙特工厂自行冲压的。
特斯拉Model S 车型铝合金的比重达到了惊人的97%。
据特斯拉官网介绍,整车总长4979 mm、轴距2960mm、宽度2187 mm、高度1435mm。
【汽车工艺】特斯拉车身材料及工艺解析
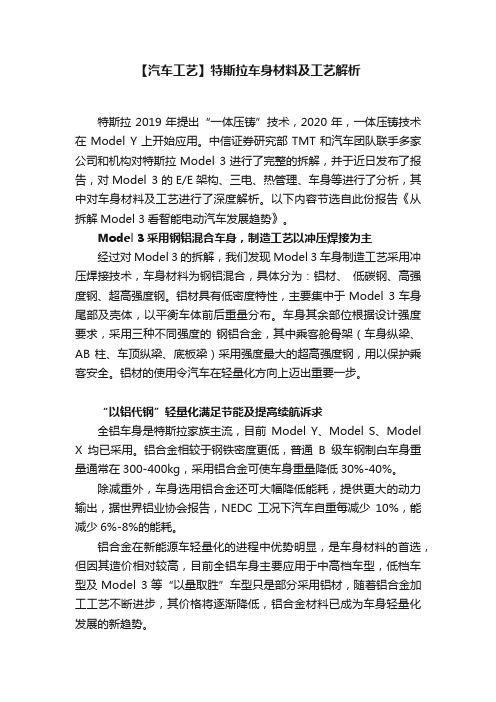
【汽车工艺】特斯拉车身材料及工艺解析特斯拉2019年提出“一体压铸”技术,2020年,一体压铸技术在Model Y上开始应用。
中信证券研究部TMT和汽车团队联手多家公司和机构对特斯拉Model 3进行了完整的拆解,并于近日发布了报告,对Model 3的E/E架构、三电、热管理、车身等进行了分析,其中对车身材料及工艺进行了深度解析。
以下内容节选自此份报告《从拆解Model 3看智能电动汽车发展趋势》。
Model 3采用钢铝混合车身,制造工艺以冲压焊接为主经过对Model 3的拆解,我们发现Model 3车身制造工艺采用冲压焊接技术,车身材料为钢铝混合,具体分为:铝材、低碳钢、高强度钢、超高强度钢。
铝材具有低密度特性,主要集中于Model 3车身尾部及壳体,以平衡车体前后重量分布。
车身其余部位根据设计强度要求,采用三种不同强度的钢铝合金,其中乘客舱骨架(车身纵梁、AB 柱、车顶纵梁、底板梁)采用强度最大的超高强度钢,用以保护乘客安全。
铝材的使用令汽车在轻量化方向上迈出重要一步。
“以铝代钢”轻量化满足节能及提高续航诉求全铝车身是特斯拉家族主流,目前Model Y、Model S、Model X均已采用。
铝合金相较于钢铁密度更低,普通B级车钢制白车身重量通常在300-400kg,采用铝合金可使车身重量降低30%-40%。
除减重外,车身选用铝合金还可大幅降低能耗,提供更大的动力输出,据世界铝业协会报告,NEDC工况下汽车自重每减少10%,能减少6%-8%的能耗。
铝合金在新能源车轻量化的进程中优势明显,是车身材料的首选,但因其造价相对较高,目前全铝车身主要应用于中高档车型,低档车型及Model 3等“以量取胜”车型只是部分采用铝材,随着铝合金加工工艺不断进步,其价格将逐渐降低,铝合金材料已成为车身轻量化发展的新趋势。
高压压铸是铝合金材料高效的成型方法,特斯拉率先提出一体压铸金属制品主要采用机床铣削、钣金成型焊接、铸造三种工艺生产。
新能源汽车车身材料特性及发展现状浅谈
新能源汽车车身材料特性及发展现状浅谈随着能源枯竭,环境污染日趋严重化,给国际汽车工业变更面提出了新的挑战。
能源的枯竭带动了新能源的迅速发展,但是新能源发展给整车的重量提出了一个新的挑战,一些新生材料的应用起到了关键性的作用。
研究表明,一般汽车每减轻1kg的重量,1L的汽油可使汽车多行驶约1m。
车身在整车中占约25%左右的重量,所以车身的材料对整车的重量减轻起着关键性的作用。
标签:车身;轻量化;高强纤维复合材料引言本文主要针对可应用于车身的主要材料进行性能、成型工艺、经济性等方面进行比对,寻找出适合现代汽车工业发展方向的高性能材料。
1 车身材料的种类车身材料既要满足车身设计、生产制造、装配、维修维护方面的要求;还要满足使用、安全、美观等方面的要求。
1.1 传统车身材料现在市面上的传统汽车大都还是钢结构车身,占整个汽车行业的80%,还有玻璃钢,传统塑料(材料为传统的PE、ABS、EMA等)。
1.2 新生车身材料随着科学技术的发展,各种新生材料被广泛的应用到车身当中,包括铝合金、碳纤维复合材料等为主。
2 各种材料的发展史钢结构车身已经有很悠久的历史了,1915年福特生产了第一辆钢结构车身。
50年代-70年代出现铝合金及塑料零件,但是仅是车身上的某个零部件,20世纪80年代,高强度钢板开始广泛应用到车身覆盖件上,从此一直延续到现在,而且在未来的10-20年,仍然被广泛应用。
1962年,中科院长春应用化学所成立“聚丙烯腈基碳纤维的研制”课题组,开展大量的基础研究,从此碳纤维材料这种新兴的材料被大众认知,进几年这种材料被广泛的应用到航天、方程式赛车及高端车身上。
随着科技的发展,材料的成本逐步下降,不久的将来将广泛地应用到民用车身。
3 材料的特性比较3.1 密度(重量)从表1可以看出,新兴的材料比传统的钢材密度要低三到七倍,这对整车车身重量来说是很大的优势,但是单纯地从密度来看是不够的,厚度也是起到决定性作用的,综合考量,铝镁合金和塑料、高强度复合纤维材料都是替代传统钢材的主要材料。
车身材料可行性分析
车身材料可行性分析车身材料选择主要是在保证一定强度的情况下力求做到材料最轻化。
车身的材料选择又取决于车身的结构,现在有三种可行性的结构方式:第一种是采用内置车架结构,外敷材料的方式;第二种车身结构是采用上下组合的形式,连接处用卡扣进行连接;第三种是带有车顶盖门的结构,类似于我们上一个节能车的样式。
三种结构各有自己的优缺点,下面分析一下各个结构和相适应的材料选择。
第一种方式对车身表面材料的强度要求不是很高,由于整个车的强度要求主要靠车架的力量支撑,所以我们可以在表面的材料上做到符合基本要求后的最轻化。
这样有涉及到一个车架的材料问题,车架的材料选择也要遵循以上原则,从目前市场上的材料来看铝合金材料和不锈钢管材是比较可行的方案。
一方面它们的质量相对于其他金属材料较轻,另一方面在可塑性和焊接性方面也比较优秀,我们目前的技术可以达到,在价格方面也比较能接受。
车身表面的材料首先是聚氯乙烯,它的成型温度:160-190℃,耐候性好、平整性好、易于和绝大多数的塑料油墨亲和,并且具有十分明显的经济性。
它的着色性较好,加入不同的着色剂很容易制得不同颜色的膜片,车身的喷漆过程可以简化。
另一特点是,PVC材料资源普遍,价格低廉,它仅为PC膜片价格的1|3~1|2。
PVC的不足之处是表面硬度较低,没有弹性,其耐温性能也有很大的局限,一般在70摄氏度时就会软化,当它长期暴露在空气中时,会有泛黄或变色的倾向。
车身表面材料还可以采用泡沫塑料,泡沫塑料的特点:1容重很低,可减轻包装重量,降低运输费用;2具有优良的冲击、振动能量的吸收性,用于缓冲防震包装能大大减少产品的破损;3对温、湿度的变化适应性强,能满足一般包装情况的要求;4吸水率低、吸湿性小,化学稳定性好,自身不会对内装物产生腐蚀,且对酸、碱等化学药品有较强的耐受性;5导热率低,可用于保温隔热包装,如冰淇淋杯、快餐容器及保温鱼箱等;6成型加工方便,可以采用模压、挤出、注射等成型方法制成各种泡沫衬垫、泡沫块、片材等。
特斯拉Model3整车轻量化技术分析
轻量化是汽车领域的发展趋势,新能源汽车的轻量化不仅可以提升车辆动力性,降低行驶能耗,增加续航里程,还可以降低客户使用成本,轻量化的效果及意义可见一斑。
Model3是电动汽车的行业标杆,其在轻量化上有何建树?是否值得借鉴?国内轻量化水平与国外还有多大差距?这一期我们就来深入探讨一番。
1.Model3轻量化水平表1Model3车型基本信息车型尺寸(mm)4694×1850×1443轴距(mm)2875前轮距(mm)1580后轮距(mm)1580车身脚印面积(m²) 4.54注:脚印面积,(前轮距+后轮距)/2╳轴距,m2;图1 model 3车型示意图参照行业标准,从三个方面对Model3的轻量化水平进行分析。
(1)白车身轻量化系数(2)整车名义密度(3)整车轻量化指数(1)白车身轻量化系数白车身轻量化系数是业内用来评价白车身轻量化水平的系数,系数越小白车身轻量化水平越高。
它是综合了车身尺寸、重量和性能三方表现获得的数据。
对比ECB近7年的主流三厢轿车,可以发现主流车型白车身轻量化系数基本在3以下,而Model 3白车身轻量化系数远超其它车型,高达 4.5,处于不利位置,主要是白车身重量偏高而扭转刚度偏低的原因。
图 2 Model 3与竞品车白车身重量对比图图 3 Model 3与竞品车白车身轻量化系数对标散点图那整车轻量化指标又是什么样一个数据?(2)整车名义密度名义密度是整备质量与名义体积之比,名义密度小的车辆轻量化水平越高。
式中:D——名义密度;M——整备质量;V——名义体积;其中名义体积计算如下式:V=[(B×H)]+[(L-B) ×0.5×H] ×W 式中:H——车身高度;B——轴距;W——车身宽度;L——车身长度;Model 3对比Model S整备质量下降了约300kg,从名义密度上看Model 3的整车轻量化处于中等水平,虽然有所改善,但优势并不明显。
电动汽车的车身材质
电动汽车的车身材质随着环保意识的增强和对传统燃油车的限制,电动汽车作为一种清洁能源交通工具正逐渐成为人们的关注焦点。
而在电动汽车的设计和制造过程中,车身材质起着至关重要的作用。
本文将探讨电动汽车常见的车身材质,并分析其特点及优劣之处。
一、钢铁钢铁作为一种传统的车身材料,在汽车制造业中一直占据主导地位。
其具有高强度、稳定性好以及成本相对较低的特点,因此被广泛应用于电动汽车的车身结构。
此外,使用钢铁材质可以提供良好的车身刚性和耐撞性能,增加了车辆在碰撞事故中的安全性。
但是,钢铁车身也存在一些缺点,比如重量较大,容易增加车辆整体重量,从而影响电动汽车的续航里程。
二、铝合金铝合金作为一种轻质材料,逐渐成为电动汽车制造领域中的热门选择。
相比于传统的钢铁材料,铝合金具有较低的密度和良好的强度,因此可以显著降低电动汽车的整体重量,并提高续航里程。
此外,铝合金具有较好的耐腐蚀性和可塑性,适合进行各种复杂形状的车身设计。
然而,铝合金的生产成本相对较高,同时其强度可能不及钢铁,需要更多的工艺和技术来保证车身的牢固性。
三、碳纤维复合材料碳纤维复合材料作为一种先进的车身材料,近年来在电动汽车制造中引起了广泛的关注。
碳纤维具有极高的强度和轻质化特性,可以大幅度减轻车身重量,并提高电动汽车的能源利用效率。
此外,碳纤维具有优异的抗腐化性能和良好的刚性,提供了更高的安全性能。
然而,碳纤维复合材料的生产工艺复杂,制造成本较高,且可塑性较差,难以实现某些复杂形状的车身设计。
综上所述,电动汽车的车身材质对于车辆的性能和性价比具有重要影响。
传统的钢铁材质在车辆安全性方面表现出色,但会增加整体重量,影响电动汽车的续航里程。
铝合金车身重量轻,但成本较高,需要更多工艺和技术来保证车身的牢固性。
碳纤维复合材料具有高强度和轻质化特性,但生产成本较高且可塑性较差。
在未来的技术发展中,电动汽车的车身材质将更加多样化和先进化,以迎合市场对安全性、节能性和环保性的需求。
- 1、下载文档前请自行甄别文档内容的完整性,平台不提供额外的编辑、内容补充、找答案等附加服务。
- 2、"仅部分预览"的文档,不可在线预览部分如存在完整性等问题,可反馈申请退款(可完整预览的文档不适用该条件!)。
- 3、如文档侵犯您的权益,请联系客服反馈,我们会尽快为您处理(人工客服工作时间:9:00-18:30)。
新能源汽车特斯产车身结构材料分析报告
目录
1.车身结构的组成构件 (5)
1.1汽车结构件 (5)
1.2汽车加强件 (5)
1.3汽车覆盖件 (6)
1.3.1发动机盖 (6)
1.3.2翼子板 (7)
1.3.3保险杠 (7)
1.3.4车顶盖 (7)
1.3.5车门 (8)
1.3.6行李箱盖 (8)
2.97%全铝车身,实现极致轻量化 (8)
2.1全铝车身简介 (8)
2.2特斯拉Model S的铝合金结构件 (9)
2.2.1悬挂系统采用镂空锻造铝合金 (10)
2.2.2罕见的铸铝横梁 (11)
2.2.3汽车覆盖件 (11)
2.2.4铝合金制轮毂 (11)
2.3全铝车身“鼻祖”——奥迪ASF车身主要参数 (11)
3.关键区域的高强度钢应用提高乘员安全 (12)
3.1高强度硼钢加固 (12)
3.2汽车防撞梁 (13)
4.特斯拉其他材料使用情况 (13)
5.投资建议 (13)
6.风险提示 (13)
图目录
图1汽车结构件示意图 (5)
图2汽车加强件示意图 (6)
图3汽车覆盖件示意图 (6)
图4发动机盖结构示意图 (7)
图5发动机盖与前翼子板结构示意图 (7)
图6汽车前后保险杠示意图 (7)
图7汽车车门结构示意图 (8)
图8奥迪A8全铝车身 (9)
图9汽车“白车身”——结构件示意图 (9)
图10特斯拉全铝车身 (10)
图11特斯拉Model S悬挂系统 (11)
图12奥迪A8(D5)车身结构材料示意图 (12)
表目录
表1奥迪A8系列白车身重量 (12)
表2特斯拉MODEL S前后防撞梁强度表(MPa) (13)
表3特斯拉MODEL S其他关键构件所用材料 (13)
1. 车身结构的组成构件
车身结构是指包括纵、横梁和支柱等主要承力元件以及与它们相连接的钣件共同组成的刚性空间结构,是所有车身部件的安装基础。
车身结构的三大组成构件,按重要性由高到低排列为:汽车结构件、汽车加强件、汽车覆盖件。
1.1 汽车结构件
结构件是指具有一定形状,并能够承受载荷的构件,比如支架、框架内部骨架和支撑定位等。
汽车结构件指的是汽车承载重量的零部件,相当于车体的骨骼,是最重要的安全保障。
具体包括(如图所示):前纵梁、后纵梁、ABC三对立柱,前轮旋和后轮旋。
中间车身的立柱起着支撑风窗和车顶的作用,一般下部做得粗大,上部的截面尺寸需要考虑驾驶视野而缩小,立柱包括前柱(A柱)、中柱(B柱)与后柱(C柱)三种。
为了使驾车室空间尽量不变形,车身结构件一般使用超高强度钢。
前纵梁由两根位于两边的纵梁组合而成,多用低合金钢板冲压成,具有特定的截面设计(槽形或工字形),当车辆发生正面碰撞时,前纵梁属于吸能区,负担了碰撞能量的60%左右。
后纵梁吸能压力虽然比前纵梁要小,但在追尾事故中承担了碰撞能量的大部分。
纵梁构件的设计思路是在发生碰撞事故时引导轴向压溃变形,同时控制弯曲变形量,从而实现理想的能量吸收效率。
图1汽车结构件示意图
1.2 汽车加强件
汽车加强件指的是结构件一系列强化保护结构,例如:前防撞梁、后防撞梁和翼子板内缘。
当车辆发生碰撞时,首先由加强件对碰撞力量进行缓冲吸能。
图2汽车加强件示意图
1.3 汽车覆盖件
汽车覆盖件指的是汽车表面的蒙皮,比如发动机盖、车门、翼子板、后备箱盖、前后保险杠等,相当于车体的表层皮肤。
图3汽车覆盖件示意图
1.3.1 发动机盖
发动机盖(又称发动机罩)一般由外板和内板组成,中间夹以隔热材料,内板是骨架形式,起到增强刚性的作用。
对发动机盖的选材要求是隔热隔音、刚性强、质量轻。
图4发动机盖结构示意图图5发动机盖与前翼子板结构示意图
1.3.2 翼子板
翼子板是遮盖车轮的车身外板,形似鸟翼而得名,分为前翼子板和后翼子板。
现在有的轿车翼子板与车壳设计成一个整体。
但因为前翼子板碰撞机会比较多,独立装配容
易整件更换,多数轿车的翼子板是独立的,尤其是前翼子板。
发动机盖和翼子板等车前
和尾部的材料,为了能够吸收撞击力,一般使用强度较低的材料。
有些车的前翼子板用
有一定弹性的塑性材料(例如塑料)做成。
塑性材料具有缓冲性,在遇到碰撞时能提升
安全性。
1.3.3 保险杠
汽车保险杠是缓冲吸收外界冲击力,保护车身前部和后部的安全构件。
随着汽车工业的发展,现代汽车的保险杠除了原有的保护功能外,还要追求与车体造型的协调,和
自身的轻量化。
目前汽车的前后保险杠普遍使用了塑料,称为塑料保险杠。
塑料保险杠可以分为由外板、缓冲材料和横梁等三部分。
其中外板和缓冲材料用塑料制成,横梁用厚度为1.5毫米的冷轧钢板冲压成U型槽。
图6汽车前后保险杠示意图
1.3.4 车顶盖
车顶盖是车厢顶部的盖板。
对于车壳的总体刚度而言,车顶盖不是很重要,这也是为什么车顶盖上能够开设天窗。
车顶盖可以分为固定式顶盖和敞篷式顶盖两种。
固定式
顶盖较为常见,主要由车顶板、车顶内衬、横梁组成,有的车型还备有车顶行李架和天
窗或者换气窗。
敞篷式顶盖一般用于高档轿车或跑车上,通过电动和机械传动实现部分
或全部顶盖的移动。
1.3.5 车门
车门是乘客上下的通道,其上还装有门锁、玻璃、玻璃升降器等附属设施,车门框架是车门的主要钢架,铰链、玻璃、把手等部件安装在门框架上。
车门主要包括车门外板和内板、门窗框、门玻璃导槽、门铰链、门锁及门窗附件等组成。
内板装有玻璃升降器、门锁等附件。
图7汽车车门结构示意图
1.3.6 行李箱盖
行李箱盖又称后备箱盖,结构与发动机盖类似分为内板和外板,内板有加强筋。
2. 97%全铝车身,实现极致轻量化
2.1 全铝车身简介
所谓的“全铝车身”中的“车身”指的是车体承重的框架主体结构,即汽车的结构件,也叫做“白车身”。
白车身内的一些影响碰撞安全的重要结构仍会使用高强度高或超高强度钢,也就是说“全铝车身”其实也属于钢铝混合车身。
所以,100%铝合金制造的“全铝车身”在量产车中是不存在的。
全铝车身框架结构,创造性地将钢与铝两种材质合为一体,可确保更具动态的驱动能力,在提高稳定性的同时亦令加速能力大大加强。
据汽车之家资料显示,世界上第一辆宣称采用“全铝车身”的量产车是1989年本田的初代NSX,而真正首次实现“全铝车身”大规模量产的是奥迪。
在1995年首次在A8上采用了“ASF空间框架”车身技术,该技术在白车身与车身覆盖件上大量使用铝合金,并且该技术继续沿用在了A2、TT、R8等车型上。