影响锅炉结渣的因素及其预防措施
锅炉结焦原因及预防

锅炉结焦原因及预防1 炉膛结渣的原因1)灰的熔融特性是判断燃烧过程中是否发生结渣的一个重要依据,不同煤质的灰具有不同的成分和熔融特性。
在实验室中对煤样进行灰化,测得其灰熔点比制定值低,因而灰粒很容易达到软化状态而发生结渣。
2) 炉膛燃烧器区域热负荷或容积热负荷偏高,在燃烧器区域燃料燃烧放出的大量热量没有足够的水冷壁受热面来汲取,因此导致燃烧器区域的局部温度过高,造成燃烧器区域的结渣;另外,燃料和烟气在炉内的停留时间过短,燃料未能完全燃烧,引起炉膛出口烟温偏高,造成炉膛出口过热器结渣。
3) 在实际运行中,由于炉内气流组织不佳,造成火焰中心偏移。
致使实际切圆变形,高温火焰偏离炉膛中心,因此后墙结渣严重。
4)经测试发现炉膛出口氧量偏小,因此不能充分实现炉内富氧燃烧,引起炉膛结渣。
5) 对煤粉进行分析发现煤粉细度变大,煤粉变粗,煤粉中的粗颗粒很容易从煤粉气流中分开出来与水冷壁发生冲撞;此外,粗颗粒的燃尽需要相当长的时间,因此经常贴壁造成还原性气氛而增加了结渣的机率。
6) 一次风速偏高。
由于一次风速度偏高,一次风射流本身的动量或者说一次风射流的刚性较强,致使煤粉气流冲击对面炉墙,造成炉墙结渣。
7〕煤种的变化对炉膛温度和烟温的影响非常大,燃用低位发热量在5400Kcal/Kg以上的煤时,炉内结焦显然加剧。
2 解决结渣问题的措施1) 适当降低一次风速度。
一次风速度调整必须依据煤质的变化来进行,在额定负荷下,当燃用优质烟煤时,将一次风速度降低到30 m/s;当燃用一般烟煤时,将一次风速度降低到26m/s。
降低一次风速度可降低一次风射流的刚性,防止煤粉气流冲击炉墙从而防止炉膛结渣。
2) 增大炉内的过量空气系数。
将炉膛出口氧量提升到不低于3.5%。
3) 调整四角燃烧器风粉动量分配使之达到均匀状态,坚持高温火焰中心位于炉膛断面的几何中心处。
4) 在高、低过热器,省煤器等处加装声波吹灰器,严格进行吹灰操作,使水冷壁和过热器、表面坚持基本干净,防止出现结焦、积灰影响传热。
锅炉防结渣解决方案

锅炉结渣原因及变化趋势燃煤电站锅炉结渣是影响锅炉安全经济运行的重要问题。
电站锅炉结渣主要指炉膛中的灼热灰渣与未燃尽的煤粉冲刷到水冷壁、屏式过热器等辐射受热面上呈液态或半液态粘附着,结成紧密的灰渣层。
受热面结渣后,传热效果降低,冷却能力下降,烟温会升高,又进一步加剧结渣的发展。
锅炉结渣特别是炉膛结渣对锅炉的安全经济运行及可靠性有很大的影响。
锅炉一旦出现结渣,轻则使受热面传热不良,排烟温度升高,降低锅炉效率;重则使燃烧工况恶化,迫使锅炉降负荷运行。
如果遇到大块炉渣落下时,可能会砸坏水冷壁管,并影响正常出渣。
有时出现炉膛正压,导致锅炉被迫停运。
通常,结渣的形成包括以下三个过程:(1)初始沉积层的形成炉管上灰沉积物迅速聚结的基本条件是存在一个粘性表面,粘性表面一般由硫酸钠、硫酸钙或钠、钙与硫酸盐的共晶体等基本物质组成。
粘性沉积物处于熔融或半熔融态,对金属或耐火材料具有润湿作用,并且灰成分一般也能相互润湿,这样由于粘附作用而形成初始沉积层。
(2)一次沉积层的形成随着初始沉积层的加厚,烟温升高,沉积速率加快,沉积物与沉积物之间以及沉积物与受热面之间粘接强度增加,沉积层表面温度升高,直至沉积到沉积层的熔融或半熔融颗粒基本不再发生凝固而形成粘性流体层,即捕捉表面。
(3)二次沉积层的形成捕捉表面形成后,无论灰粒的粘度、速度及碰撞角度如何,只要接触到沉积层的颗粒一般均会被捕捉,使沉积层快速增加,被捕捉的固体颗粒溶解在沉积面上,使熔点或粘度升高,从而发生凝固而又形成新的捕捉表面,直到沉积表面温度达到重力作用下的极限粘度值时的温度,使沉积层的形成不再加厚而使撞击上的灰粒沿管壁表面向下流动。
结渣速度取决于一次沉积层的形成过程,各沉积层的形成均以惯性沉积为主,是否结渣以及结渣的程度与煤种、炉温、空气动力场等有关。
针对某一种工况下,锅炉结渣稳定前后换热管半径对比图:经济效益粗略分析:。
锅炉结渣原因分析及预防措施
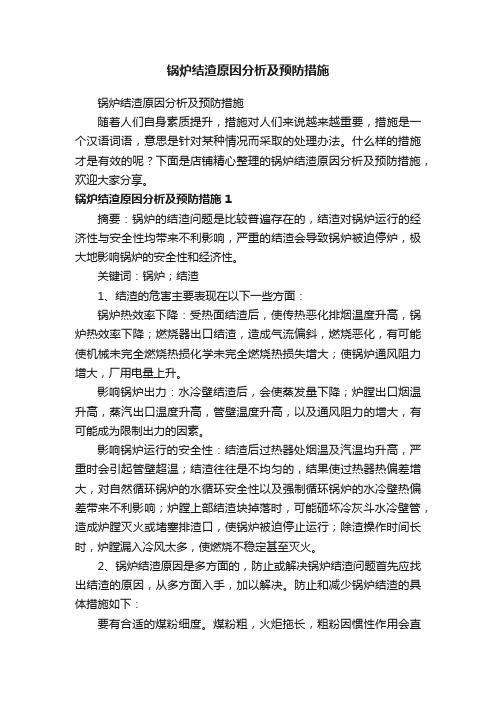
锅炉结渣原因分析及预防措施锅炉结渣原因分析及预防措施随着人们自身素质提升,措施对人们来说越来越重要,措施是一个汉语词语,意思是针对某种情况而采取的处理办法。
什么样的措施才是有效的呢?下面是店铺精心整理的锅炉结渣原因分析及预防措施,欢迎大家分享。
锅炉结渣原因分析及预防措施 1摘要:锅炉的结渣问题是比较普遍存在的,结渣对锅炉运行的经济性与安全性均带来不利影响,严重的结渣会导致锅炉被迫停炉,极大地影响锅炉的安全性和经济性。
关键词:锅炉;结渣1、结渣的危害主要表现在以下一些方面:锅炉热效率下降:受热面结渣后,使传热恶化排烟温度升高,锅炉热效率下降;燃烧器出口结渣,造成气流偏斜,燃烧恶化,有可能使机械未完全燃烧热损化学未完全燃烧热损失增大;使锅炉通风阻力增大,厂用电量上升。
影响锅炉出力:水冷壁结渣后,会使蒸发量下降;炉膛出口烟温升高,蒸汽出口温度升高,管壁温度升高,以及通风阻力的增大,有可能成为限制出力的因素。
影响锅炉运行的安全性:结渣后过热器处烟温及汽温均升高,严重时会引起管壁超温;结渣往往是不均匀的,结果使过热器热偏差增大,对自然循环锅炉的水循环安全性以及强制循环锅炉的水冷壁热偏差带来不利影响;炉膛上部结渣块掉落时,可能砸坏冷灰斗水冷壁管,造成炉膛灭火或堵塞排渣口,使锅炉被迫停止运行;除渣操作时间长时,炉膛漏入冷风太多,使燃烧不稳定甚至灭火。
2、锅炉结渣原因是多方面的,防止或解决锅炉结渣问题首先应找出结渣的原因,从多方面入手,加以解决。
防止和减少锅炉结渣的具体措施如下:要有合适的煤粉细度。
煤粉粗,火炬拖长,粗粉因惯性作用会直接冲刷受热面。
再则,粗煤粉燃烧温度比烟温高许多,熔化比例高,冲墙后容易引起结渣。
但是,煤粉太细也会带来问题,一是电耗高,制粉出力受到影响,二是炉膛出口烟温升高,易引起结渣。
适当提高一次风速可以减轻燃烧器附近的结渣。
提高一次风速可推迟煤粉的着火,可使着火点离燃烧器更远,火焰高温区也相应推移到炉膛中心,可以避免喷口附加结渣。
燃煤锅炉炉内结渣影响因素

燃煤锅炉炉内结渣影响因素分析燃煤电厂炉内结渣是很多电厂常常遇到的难题之一,也是确保火力电厂平安经济平稳运行必需解决的重大课题之一。
几十年来,国内燃煤电厂由于炉内结渣引起的各种设施、人身事故不计其数,轻则导致锅炉低负荷运行或停炉清渣,产生巨大经济损失,重则导致设施损坏,甚至引发人身事故。
结渣的本质就是熔化的固体杂质与锅炉内粘结的灰尘在高温条件下凝固在炉壁上而产生的一种现象,详细地说就是当炉内温度高于灰尘熔点并受到烟气的不断冲刷时就会使得灰渣凝聚在炉壁上而造成结渣,由上述描述可推知产生结渣有以下几方面的缘由:(1)炉内温度要高于灰尘熔点,使灰尘熔化;(2)气流要不断冲刷受热面,使熔灰有机会到达壁面并粘结在上面;(3)炉壁要有利于灰尘的凝固,即水冷壁对熔灰的冷却性差,煤灰未在炉膛出口处凝固而是粘黏在炉壁上形成炉渣。
下面将分别从这几个方面对炉内结渣的影响因素进行详细分析,指出炉内结渣的危害及防治措施。
一、影响因素1.煤灰特性和化学组成煤灰成分与组成是产生锅炉结渣的根源。
一般灰熔点低的煤简单结渣,与此同时,低熔点灰分通常粘性也强,因而增加了结渣的可能性。
1.1.灰的熔化温度灰熔温度同灰的成分有关,灰中的酸性氧化物,如SiO2,A12O3和Tio2等都是聚合物的构成者,因此会提高灰的熔化温度;碱性氧化物则相反,如CaO,MgO和Na20等都是聚合物的破坏者,会降低灰的熔化温度。
但这种解释对含有大量碱性物的灰来说不适用,所谓“褐煤型灰”就会有大量CaO和MgO,其量比Fe2O3多得多,这些灰中的SiC)2、Fe2O3、Na20和K20都会降低软化温度,而AI2O3、Cao和Mgo却提高软化温度。
灰中铁的作用,要视其氧化状态而定,三价铁是聚合物的构成者,提高灰熔温度;二价铁则是聚合物的破坏者,降低灰熔温度。
灰的熔化温度在氧化氛围与还原氛围中是不同的,两者的差异是随着灰中CaO和MgO成分的增加而变小。
1.2渣的粘度焦渣的粘度随温度而变化,温度提升,粘度变小,超过某一临界值时,焦渣便成液相,可在水冷壁表面形成一薄层而自由流淌,焦渣粘度温度曲线是预示煤粉炉结渣倾向的重要指标。
锅炉结焦原因及处理方法

锅炉结焦原因及处理方法影响锅炉结焦的主要因素有:煤质差(灰熔点低)、炉膛温度和空气动力场,火焰中心抬高,炉膛出口温度增高,低氧燃烧产生过多还原性气体,吹灰不及时、长期高负荷运行等。
解决措施:一、严格控制入厂煤和入炉煤:煤种变化将对结焦有很大影响,特别是燃用灰熔点低、挥发份相对较高的煤种。
因此要加强对入厂煤和入炉煤化验,严格把关,其在下部炉膛燃烧时着火点早,火焰相对密集,造成扩散性燃烧,下部炉膛容积热负荷较大,从而造成局部高温区壁面结渣。
因此燃用设计煤种是防止炉膛结焦最重要的因数。
二、运行方面防止锅炉结焦的技术措施:1.运行中加强配风工况调整,调节三次风,使火焰不贴壁;调节二次风使其提供充足的氧量保证煤粉的充分燃烧;调节一次风,使火焰长度合适;调节吸风机,保持炉膛负压在-70pa左右;既要保证煤粉在炉膛内充分燃烧所需要的时间,又要避免在下炉膛形成扩散燃烧。
控制氧量在4%-6%之间,严禁缺氧燃烧。
2.加强燃烧调整,避免大起大落,幅度太大。
严格控制升温升压速度,防止出现两侧烟气温度偏差。
3. 加强制粉系统检查,防止喷燃器结焦运行。
1) 正常巡回检查中,一定要注意检查燃烧器区及粉管闸板门前、后温度,发现异常,及时汇报,进行处理。
2) 磨煤机正常运行中,DCS CRT一定要注意监视各粉管风压,并注意其变化趋势。
发现异常,要立即就地检查并实测燃烧器温度。
若温度偏高,应立即停运并进行吹扫。
若燃烧器就地温度正常,其它参数也无异常变化,应联系热控检查粉管压力测点。
3) 磨煤机正常停运(包括正常减负荷停单侧)后,运行人员要就地检查分离器出口挡板、旋风子煤粉出口挡板、伐气出口挡板在关闭位置。
4) 磨煤机停运后,其相应的二次风控制挡板应保持5-10%的开度以保证对狭缝式喷燃器的冷却,防止喷燃器烧坏。
4.坚持锅炉定期吹灰工作,根据汽温变化、炉膛出口烟温及两侧烟温差变化可适当增加吹灰次数。
1)减温水量不正常地升高,应进行吹灰。
煤粉锅炉运行中炉内结渣原因及改善措施分析

煤粉锅炉运行中炉内结渣原因及改善措施分析由于煤粉锅炉燃料的特殊性,所以在锅炉运行过程中,极易出现炉内结渣现象。
炉内结渣会直接降低受热面的传热效率,锅炉整体热效率降低,在排烟中的含量增加,严重的情况下,会导致恶性事故的发生,对煤粉锅炉运行的安全性存在极大的威胁。
炉内结渣会对整个机组的运行产生影响,所以一定要减少炉内结渣现象的出现。
文章对煤粉锅炉运行中炉内结渣的原因进行分析,进而提出改善措施,为促进煤粉锅炉的高效稳定运行创造有利的条件。
标签:煤粉锅炉;炉内;结渣;原因;改善措施前言煤粉锅炉由于燃烧效率高,整体构造简单,节能环保,所以在电厂等工业领域得到了广泛的应用。
煤粉锅炉主要由炉膛、燃烧器和点火装置组成,其中的炉膛是锅炉中的重要组成部分,其要保证燃料能够得到充分燃烧,并且达到较高的热交换效率。
但是由于燃料为煤粉,如果设计运行参数不合理,烟气温度高于灰熔点时,就会导致炉内出现结渣现象。
在炉内的结渣越多,将会降低炉内受热面的传热效率,整体运行工况受到严重影响。
炉内结渣对煤粉锅炉运行的安全性、经济性、稳定性和可靠性都有一定的影响,所以应该通过对结渣的特征入手,分析炉内结渣的原因,进而在炉膛设计时优化各项参数,并且通过对运行的调整和控制来改善结渣现象。
1 煤粉锅炉炉内结渣的危害煤粉锅炉炉内结渣所产生的危害十分巨大,直接影响到锅炉运行的安全性和经济性。
当炉内受热面结渣较多时,由于灰污的热阻较大,所以水冷壁导热效率降低,在热量传导降低的情况下,就会提高排烟温度,造成排烟热损失。
为了保证锅炉的满负荷运行,还需要继续投入煤粉,炉内高温导致结渣愈加严重,从而引发恶性循环,在没有得到及时处理的情况下,就会导致过热器、省煤器管束堵灰、爆管、出渣系统堵死等现象。
同时,结渣还会对过热器、喷燃器产生损坏,增加引、送风机的运行负荷,不仅会产生极大的经济损失,而且对人身安全存在极大的威胁。
所以说煤粉锅炉炉内结渣所造成的危害较大,应该采取相应措施对此现象进行改善。
锅炉结焦的原因分析及预防措施
锅炉结焦的原因分析及预防措施一、结焦的概念在锅炉炉膛中心,火焰温度高达1400-1600℃左右,煤粉燃烧时,其灰分处于熔化状态,当熔化的灰粒在离开火焰碰到受热面或炉墙时受到冷却就会粘附在受热面的管子或炉墙上,而且越结越多,这种现象就叫结焦。
大家注意到上述概念牵扯到了这样的几个名词:煤粉燃烧,灰粉熔化状态,那么有必要对煤粉燃烧和灰粉熔化状态进行一简单的介绍:1、煤的成分为了了解煤的某些特性,将煤的成分分为:碳(C)、氢(H)、氧(O)、氮(N)、硫(S)、水分(H2O)、灰分(A);这里主要介绍灰分,灰分是煤粉燃烧完全燃烧后形成的固体残余物的统称,其主要成分有硅、铝、铁和钙以及少量的镁、钛、钠和钾等元素的组成的化合物。
依据炭化程度分,炭化程度越深,挥发分含量越少,碳的含量越多。
我国动力煤习惯上分为4类:无烟煤:挥发分6.5—10%,着火困难,燃尽不易;贫煤:挥发份低,约 10—19%,燃烧性质与无烟煤接近;烟煤:挥发分含量高,挥发分19—37%,碳化程度低于无烟煤;褐煤:挥发分含量较高,挥发分37%以上,有利于着火。
2、灰的性质灰的性质主要是指它的熔化性和烧结性,熔化性主要影响炉内的运行工况,烧结性主要影响对流受热面的结灰性能。
在火焰中心,灰分处于熔化状态或软化状态,具有粘性,如果遇到受热面管子,很容易粘接在上面,形成结渣。
关于灰分的熔化性能,目前都用实验的方法测得,把灰制成底为等边三角形的椎体,底边长为7mm,锥体高20mm,然后加热根据灰的状态变化确定三个温度指标来表示灰的熔化性质:(1)变形温度t1,指锥顶变圆或开始倾斜的温度;(2)软化温度t2,锥顶弯至锥底或萎缩呈球形的温度;(3)熔化温度t3,指椎体呈液体状态能沿平面流动的温度。
3、影响灰熔点的因素:(1)成分因素:灰的化学成分很复杂,通常用各种氧化物的百分含量来表示,包括SiO2、Fe0, Al2O3、Fe2O3,CaO, MgO,Na2O+K2O,TiO2,P2O5等,除氧化钠和氧化钾外,其它氧化物的熔点很高,为1600-2800℃,氧化钠和氧化钾的熔点800-1000℃。
锅炉结渣原因分析及预防措施(2)
锅炉结渣原因分析及预防措施(2)锅炉结渣原因分析及预防措施4、结渣原因分析.4.1炉内实际切圆太大切向燃烧在炉内形成强烈旋转上升的气流,气流最大切向速度的连线构成炉内实际切圆。
实际切圆是切向燃烧的一个重要参数,它对炉膛结渣、稳燃以及炉膛出的烟速、烟温偏差均有重要影响。
实际切圆偏大则易引起结渣,实际切圆偏小则影响燃烧的'稳定性,因此保证适中的实际切圆直径非常重要。
该炉假想切圆直径为∮864mm,冷态空气动力场试验表明实际切圆直径为8000—9000mm。
一般认为,实际切圆相比炉膛断面的当量直径的范围在0.4~0,8之间,综合考虑煤质特性及稳燃、结渣问题,对于烟煤应取较小值。
本炉的实际切圆相对直径大于0.7,运行时易造成水冷壁结渣。
4.2炉膛结构设计不合理从炉膛结构方面来看,炉膛断面越大,炉膛越高,越不易结渣。
该炉炉膛断面为正方形炉膛,宽度和深度都是11600mm,炉膛高度是40000mm,上一次风喷口至屏式过热器下沿的高度为13000mm,燃烧器整体高度为6835mm,这些数值与同容量锅炉相比均较小,导致炉膛容积热负荷、燃烧器区域壁面热负荷较高,增大了结渣的可能性。
4.3炉膛底部漏风严重该炉排渣机液压关断门由于损坏密封不严,造成炉底漏风十分严重。
炉膛漏风使炉膛内的温度水平降低,炉内吸热减少,炉膛上部温度升高,特别是炉底漏风,会使火焰中心上移,引起炉膛顶部受热面结焦。
该炉炉顶大屏结焦多属此种情况。
4.4燃烧器调整不合理产生还原性氛围该炉自投运以来由于煤粉流动性、干燥度及输粉管的通畅性等原因造成四角给粉不均匀的情况比较常见。
四角风粉不均会造成炉内局部缺氧燃烧产生还原性氛围,在这种气氛中,灰中熔点较高的fe0会还原成熔点较低的fe0,能使灰熔点降低300~350℃,大大增加了结渣的可能性。
4.5射流两侧补气条件差异较大该炉燃烧器轴线与水冷壁夹角al为42。
和a248°,两侧区域不对称,由于a2 >al,因此a2侧的补气条件比a1侧充分,a2侧的静压高于ai侧的静压,在此压差作用下,射流向al侧倾斜,气流容易贴边而产生结渣。
造成锅炉结渣的原因及预防措施
锅炉结渣的原因及预防措施
(1)锅炉结渣,也叫结焦,指高温下粘附在受热面上的灰烬、炉墙、炉排之上并越积越多的现象。
燃煤锅炉结渣是一个常见问题,层燃炉,沸腾炉,煤粉炉都有可
能结渣,由于煤粉炉炉膛温度较高,煤粉燃烧后的细灰呈飞腾状态,
因而更易在受热面上结渣。
结渣使受热面吸热量减少,降低锅炉的出力和效率;局部水冷壁
管结渣会影响和破坏水循环,甚至造成水循环故障;结渣会造成过热
蒸汽温度的变化,使过热器金属超温;严重的结渣会妨碍燃烧设备的
正常运行,甚至造成被迫停炉。
(2)结渣的原因是:
①煤的灰渣熔点低;②燃烧设备设计不合理;③运行操作不当。
(3)发现锅炉结渣要及时清除,进行“打焦”,打焦应在负荷较低,燃烧稳定时进行。
炼焦人员应注意保护和安全。
(4)防止结渣的措施:
①在设计上,要控制炉膛燃烧热负荷,在炉膛中布置足够受热面,控制炉膛出口温度,使其不超过灰变形温度;合理设计炉膛形状,正
确设置燃烧器,在燃烧器结构性能设计中充分考虑结渣问题;控制水
冷壁间距不要太大,把炉膛出口处受热面管间距拉开,作成“垂彩管”;炉排两侧装设防焦联箱等。
②在运行中,要避免超负荷运行,控制火焰中心位置,避免火焰
偏斜和火焰冲墙,合理控制炉膛过剩空气系数,减少漏风。
③对沸腾炉和层燃炉,要控制送煤量,均匀送煤,及时调整料层
及煤层厚度。
火电厂锅炉结渣与积灰原因分析及防治措施研究
火电厂锅炉结渣与积灰原因分析及防治措施研究摘要:本文针对火电厂锅炉结渣与积灰问题进行了原因分析和防治措施研究。
通过对燃料质量、燃烧过程和操作的分析,确定了结渣与积灰的主要原因。
针对这些原因,提出了选用合适的燃料、加强锅炉清洗、优化燃烧工艺和加强操作培训等防治措施。
这些措施有助于减少结渣与积灰问题,提高火电厂锅炉的运行效率和安全性。
关键词:火电厂;锅炉;结渣;积灰;燃料质量引言:火电厂锅炉结渣与积灰是影响锅炉运行效率和安全性的重要问题。
结渣会导致热传递效率下降,增加能耗和运行成本;积灰则会影响燃烧稳定性和腐蚀锅炉设备。
目前,相关研究已经对结渣与积灰的原因进行了一定的探索,但仍需要深入研究和提出有效的防治措施。
一、背景介绍1.1火电厂锅炉结渣与积灰的问题火电厂锅炉结渣与积灰是火力发电过程中普遍存在的问题,对锅炉的正常运行和安全性产生不利影响。
结渣是指燃烧过程中燃料中的杂质在锅炉内壁上沉积形成的硬质物质,它会降低锅炉的热传递效率,增加能耗和运行成本。
积灰是指燃烧过程中产生的灰分在锅炉内部沉积的软质颗粒,它会堵塞燃烧器和烟道,影响燃烧稳定性,甚至引发锅炉事故。
因此,有效解决火电厂锅炉结渣与积灰问题对于提高锅炉的运行效率和保障安全非常重要。
1.2相关研究现状目前,针对火电厂锅炉结渣与积灰问题,已经进行了一系列的研究。
研究表明,燃料质量是导致结渣与积灰的重要因素之一。
燃料中的灰分含量高、灰分成分复杂会增加结渣和积灰的倾向。
此外,燃烧过程中的问题也是结渣与积灰的主要原因之一,如不完全燃烧、过量空气、燃烧温度不合适等都会导致结渣与积灰的形成。
此外,操作不当也会加剧结渣与积灰问题,如不合理的运行参数设置、清灰不及时等。
为了解决这些问题,相关研究已经提出了一些防治措施,如选用低灰分燃料、改善燃烧工艺、加强锅炉清洗和操作培训等。
然而,针对不同类型的锅炉和火电厂,仍需要进一步研究和优化具体的防治措施,以提高锅炉的运行效率、降低能耗和保障安全。
- 1、下载文档前请自行甄别文档内容的完整性,平台不提供额外的编辑、内容补充、找答案等附加服务。
- 2、"仅部分预览"的文档,不可在线预览部分如存在完整性等问题,可反馈申请退款(可完整预览的文档不适用该条件!)。
- 3、如文档侵犯您的权益,请联系客服反馈,我们会尽快为您处理(人工客服工作时间:9:00-18:30)。
影响锅炉结渣的因素及其预防措施华电山东十里泉发电厂(277103)谢孝东摘要:为了确保300MW机组安全经济运行,本文研究了引起炉膛结渣的主要原因,并制定了防止和减轻炉内结渣的技术措施。
关键词:炉内结渣防结渣技术 300MW机组0 引言近年,各个电厂锅炉结渣问题突出,不少300MW机组都发生过严重结渣。
锅炉结渣不仅影响机组的经济满发,而且严重威胁安全运行。
北仑港电厂1号机组特大事故的惨痛教训使人们不能不对锅炉结渣问题予以高度重视。
1 与锅炉结渣有关的因素结渣是复杂的物理和化学过程,国内外学者已做了大量研究,初步揭示了其形成的机理及与煤灰性质的关系,制定了若干用以判断煤灰结渣性的指数,同时揭示了锅炉设计和运行对结渣的影响。
1.1 灰与渣的特性煤灰的结渣性同灰的化学成分、灰渣的物理特性有关。
现选择其中一些主要的指标详述如下。
1.1.1 灰的熔化温度灰熔温度同灰的成分有关,灰中的酸性氧化物,如SiO2,Al2O3和TiO2等都是聚合物的构成者,因此会提高灰的熔化温度;碱性氧化物则相反,如CaO,MgO和Na2O等都是聚合物的破坏者,会降低灰的熔化温度。
但这种解释对含有大量碱性物的灰来说不适用,所谓“褐煤型灰”就会有大量CaO和MgO,其量比Fe2O3多得多,这些灰中的SiO2、Fe2O3、Na2O和K2O都会降低软化温度,而Al2O3、CaO和MgO却提高软化温度。
美国对国内一些特定煤种,依据大量统计数据已建立了精确的灰熔温度与灰化学成分之间的关系,这样,根据灰中的碱性组分就可以确定灰熔点。
至于灰中铁的作用,要视其氧化状态而定,三价铁是聚合物的构成者,提高灰熔温度;二价铁则是聚合物的破坏者,降低灰熔温度。
灰的熔化温度在氧化氛围与还原氛围中是不同的,两者的差异是随着灰中CaO和MgO成分的增加而变小。
1.1.2 渣的粘度焦渣的粘度随温度而变化,温度升高,粘度变小,超过某一临界值时,焦渣便成液相,可在水冷壁表面形成一薄层而自由流动,焦渣粘度温度曲线是预示煤粉炉结渣倾向的重要指标。
研究表明,焦渣粘度与煤灰化学成分有关,当烟煤焦渣温度超过其临界粘度相对应的温度Tcv 后,焦渣粘度就与灰分中的硅比SiO2/(SiO2+ Fe2O3+ CaO+ MgO)有一定的关系。
英国根据(SiO2/ Al2O3)、Fe2O3、CaO、MgO来确定与临界粘度相对应的温度。
从临界粘度(约10~20Pa·s到约104Pa·s范围内的焦渣呈塑性状态液固两相混合),可根据其所对应的温度区域考虑吹灰器的型式和位置。
1.1.3 灰的烧结性B&W利用烧结试验来衡量烟煤的结渣倾向。
试验在一个专门的实验性燃烧室内进行,被试煤在其中悬浮燃烧以模拟煤粉炉工况,然后将烧出的灰压进一个直径17mm、高19mm的圆筒内,再将压出的灰块置于1.03MPa和704~1093℃下在空气中加热15个小时,然后慢慢冷却。
该烧结灰块的烧结温度、破碎强度与结渣倾向密切相关,B&W把这作为评价煤的主要指标之一。
易结渣的煤在927℃以下烧结强度高达27.58MPa,而不易结渣的煤在927~1093℃范围内的烧结强度低于6.9 MPa。
1.1.4 几个反映结渣倾向的导出因子美国CE和B&W等锅炉制造厂都各自研究和导出一些显示结渣和积灰特性的指标,现将有关结渣的指标列于附表中。
CE公司在评价结渣倾向时除了采用灰熔点外,还采用:(1)碱酸比如前所述,煤灰中碱性组分与灰熔点之间的关系呈抛物线形,碱酸比在0.4~0.7(大约30%~40%标准含量的碱性物)时最易结渣。
(2)硅铝比当以碱酸比作为判断结渣性指标时,还需注意硅铝比。
在碱酸比低的情况下,如硅铝比高,铝将发挥溶剂作用而降低T250。
T250是对应于粘度为250P(泊)时的灰渣温度,一般说,灰渣粘度低于250P时,流动性就很好。
硅铝比小于1.7不结渣,大于2.8将结渣。
(3)铁钙比此比值在0.3~3.0范围内会影响灰渣的共熔特性,使灰熔点降低,结渣倾向增加趋向1时会严重结渣;小于0.3或大于3.0都不结渣。
(4)2.0重液中的铁CE采用在比重为2.9重液中沉积下的煤灰铁含量作为衡量黄铁矿的多少。
黄铁矿在燃烧过程中不起反应而离析出来,形成焦渣结在靠近燃烧器的炉膛下部水冷壁上。
(5)单位发热量的煤灰量每百万英镑热单位的煤灰量被用来估量可能生成的渣和积灰的数量(当然还要依据灰的结渣和积灰特性)。
B&W用另一些指标来估计结渣倾向。
根据灰渣粘度导出的结渣指数R SVR SV=T250(氧化)-T1000(还原)/(97.5*FS)式中T250(氧化)——氧化氛围下灰渣粘度25Pa·s所对应的温度T1000(还原)——还原氛围下灰渣粘度1000Pa·s所对应的温度FS——一个相关系数,其数值范围为1~11,取决于灰渣粘度/温度曲线上对应于200Pa·s 的温度(氧化与还原氛围的中间值)R SV由0.5变化到3.0,相对应的结渣倾向由中等到严重。
(2)依据灰熔化温度导出的结渣指数R sfR sf=(MaxHT+4*MinID)/5式中MaxHT——氧化或还原氛围下较高的半球形温度MinID——氧化或还原氛围下较低的开始变形温度R sf是一个加权平均温度,以1份氧化或还原氛围下的最大半球形温度和4份氧化或还原氛围下的最小开始变形温度来平均。
R sf低于1149℃预示严重结渣;R sf在1232~1343℃范围内预示中等结渣倾向。
(3)由灰的化学成分导出的结渣指数RsbRsb=(CaO+MgO+Fe2O3+Na2O+K2O)*S%(干燥基)/(SiO2+ Al2O3+ TiO2)Rsb指数主要用于烟煤型灰,即灰中Fe2O3的含量大大高于CaO和MgO含量,Rsb植的范围从0.6以下(代表轻度结渣趋势)到2.6以上(代表严重结渣趋势)。
1.2 设计因素美国电力研究协会(EPRI)曾对燃用各种不同因素煤种的锅炉作了调查,结论是结渣和积灰不仅与煤灰性质有关,而且同锅炉设计密切相关,主要是炉膛热强度(包括炉膛容积热强度和断面热强度)、煤粉在炉膛内逗留的时间、燃烧器结构型式以及受热面的布置等。
同一煤种,在某台锅炉上燃烧会严重结渣,而在另一台设计不同的锅炉上可能根本不结渣。
同时,锅炉设计在改善灰沉积物方面也起着重要的作用。
1.3 运行因素锅炉结渣积灰与锅炉负荷、烟气温度、煤粉细度、过剩空气量等有关。
结渣、积灰随锅炉负荷及烟气温度的增加而增加。
煤粉细度对炉膛结渣的影响说法不一,其一,提高煤粉细度将使燃烧区域温度升高,从而加剧结渣,我国125MW机组的运行实践也表明,煤粉过细着火快,燃烧器区域易结渣。
而在一台600MW机组上进行的试验结构却相反,其结论是粗煤粉将加重结渣。
笔者认为煤粉细度应视煤种与具体的锅炉结构而定,过细不仅增加制粉电耗,而且会提高燃烧器区域热负荷而可能引起结渣;过粗不仅不利于着火和煤粒的燃尽,而且易造成炉膛上部和过热器部位结渣。
所以应通过试验确定合理的煤粉细度。
较大的燃烧过剩空气能减少结渣与积灰,这是由于炉膛内还原区范围缩小以及炉膛出口温度降低。
在600MW机组上的试验显示,增加过剩空气,同时将燃烧器正向倾斜,水冷壁和大屏上的沉积物明显减少。
2 防止结渣与积灰的措施2.1 运行措施2.1.1 吹灰对水冷壁结渣和积灰最通常的方法就是吹灰,吹灰可以防止焦渣累积,保持受热面清洁,从而使烟气分布和蒸汽温度维持在设计水平。
吹灰介质一般采用蒸汽,但对于硬焦,用蒸汽往往吹不掉,而采用水力吹灰就很有效。
水力吹灰必须设计好喷嘴的尺寸、角度、水压力、水流量、喷枪移动速度以及吹灰频率,以免对水冷壁和过热器造成热冲击。
据称,如能正确使用水力吹灰器,那么它对炉管寿命的影响决不会超过蒸汽吹灰(水力吹灰国内用的很少)。
据有些电厂经验,联合使用水、汽吹灰效果更佳,即水吹灰后接着再用蒸汽吹。
如美国Big Stone电厂的一台400MW旋风炉,燃用北达科他褐煤,结渣严重,后来在炉膛内装了32只水力喷枪和24只附加的蒸汽吹灰器,有效地控制了积灰;在过热器部位也加装了8只水力吹灰器,同时将原来二级过热器第一、二排的14只蒸汽吹灰器也改为水力吹灰器,使过热器积灰情况大为改善。
吹灰必须做到定期定时,运行人员还需加强检查。
此外,很重要的一点是维修要跟上,以确保其使用可靠。
2.1.2 其他运行措施a. 防止炉温过高。
堵塞炉底漏风,降低炉膛负压,不使空气量过大,直流喷燃器尽量利用上排喷燃器,防止火焰中心上移,以免炉膛出口结渣。
另外,保持各磨出力均匀,使直流喷燃器四角气流的动量相等,切圆合适。
防止喷燃器变形,都能防止火焰偏斜,以免水冷壁结渣。
b. 防止炉内过多还原性气体生成保持合适的空气动力场,不使空气量过小,喷燃器损坏及时修理,都能使炉内减少还原性气体,防止结焦。
c. 提高煤质,保持合适的煤粉细度。
避免燃料多变,清除煤中杂质,可减少结焦的可能性,保持合适的煤粉细度,不使煤粉过粗,以免火焰中心过高,导致炉膛出口结渣,或因煤粉落入冷灰斗又燃烧而形成结焦。
d.控制燃烧过剩空气量。
e.通过调整过剩空气量﹑燃烧器倾斜角度﹑烟气挡板﹑烟气再循环﹑燃烧器选型或其他可行手段来限制炉膛出口烟气温度在许可的限度内。
f.对于四角燃烧锅炉,国内一些厂的经验是调整一二次风,减小切圆,以避免火焰C冲刷而引起水冷壁结渣。
2.2 改变煤质2.2.1 配煤在原来的燃煤中掺入另一种煤可改变煤的性质,达到不结渣的目的。
采用此法须注意两点:a.两种煤按一定比例混合,配出来的煤的特性并不是这两种煤数学上的平均值,每一个配煤必须看成是一种新的煤种,其主要特性往往并不是所期望的。
b. 配煤必须均匀。
配煤可在煤矿﹑输煤皮带上或在炉膛内进行。
2.2.2 精选煤通过对原煤精选处理来降低其灰分及杂质。
3 总结本文讨论了与炉膛结渣的有关因素和引起炉膛结渣的原因,并制定了防止炉膛结渣的技术措施。
由于个人水平有限以上观点仅供参考。