杜邦工程塑料高性能齿轮技术手册
塑料工程技术手册
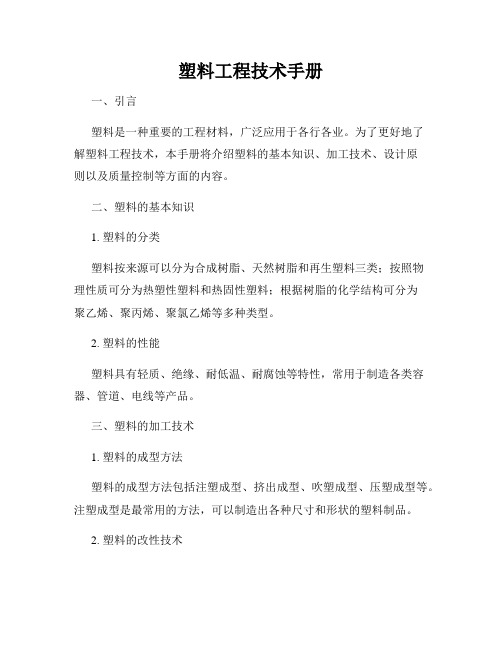
塑料工程技术手册一、引言塑料是一种重要的工程材料,广泛应用于各行各业。
为了更好地了解塑料工程技术,本手册将介绍塑料的基本知识、加工技术、设计原则以及质量控制等方面的内容。
二、塑料的基本知识1. 塑料的分类塑料按来源可以分为合成树脂、天然树脂和再生塑料三类;按照物理性质可分为热塑性塑料和热固性塑料;根据树脂的化学结构可分为聚乙烯、聚丙烯、聚氯乙烯等多种类型。
2. 塑料的性能塑料具有轻质、绝缘、耐低温、耐腐蚀等特性,常用于制造各类容器、管道、电线等产品。
三、塑料的加工技术1. 塑料的成型方法塑料的成型方法包括注塑成型、挤出成型、吹塑成型、压塑成型等。
注塑成型是最常用的方法,可以制造出各种尺寸和形状的塑料制品。
2. 塑料的改性技术塑料的改性技术可以改善塑料的物理性能,常用的改性技术包括填充剂增强、增韧剂掺入、改性剂添加等。
3. 塑料的表面处理技术塑料的表面处理技术可以提高塑料制品的外观质量和耐用性,常用的表面处理技术有喷涂、电镀、印刷等。
四、塑料制品的设计原则1. 强度设计原则塑料制品在设计时需要考虑到其受力情况,合理选择塑料材料和结构设计,确保制品的强度满足要求。
2. 尺寸设计原则塑料制品的尺寸设计需考虑到塑料材料的收缩率,以确保成型后的尺寸符合设计要求。
3. 壳体设计原则塑料制品的壳体设计需要满足结构强度、制造工艺和装配要求,合理选择壳体的厚度和型腔结构。
五、塑料制品的质量控制1. 塑料原料的质量控制塑料原料的质量对最终制品的性能有重要影响,应选用合格的原料并进行严格的质量检测。
2. 加工工艺的质量控制加工工艺的合理控制可以确保塑料制品的尺寸、外观等质量要求,需进行严格的加工工艺检验。
3. 成品质量的控制成品质量的控制包括外观检验、物理性能测试等,确保塑料制品能够满足使用要求。
六、未来发展趋势塑料工程技术在不断发展,未来的趋势包括绿色环保塑料的研发、智能制造技术的应用以及废弃塑料的回收利用等。
七、结论本手册从塑料的基本知识、加工技术、设计原则和质量控制等方面介绍了塑料工程技术的相关内容。
塑料齿轮设计(公司设计手册)

啮合率
虽说刘易斯公式是在假定所有的法向负荷都施加在一个齿尖上的基础上来加
速齿根强度的,但实际上啮合的轮齿不止一个。压力角为20°的标准齿正齿
轮的啮合率在1和2之间,如齿数为20和30的齿轮啮合率约为1.6。换言之,在1 对齿开始啮合的瞬间,另一对齿已在前1个法向节距处啮合,因此在随后的0.6 个法向节距内有2对齿啮合,而在此后的0.4个法向节距内只有1对齿啮合。因 此,考虑到把在齿尖承受所有法向负荷时所得出的值y用作齿形系数会大大超 过安全侧,于是本文采用节距附近承受负荷时的值y′。 啮合率越大则越有利于轮齿强度,因此对于传动齿轮来说,应重点考虑增大
3 计算示例
例题1
现将正齿轮的DuraconTM(等级M25)齿轮与金属齿轮组合起来,请求
出用于减速比为 的减速机时的DuraconTM齿轮的齿宽。
假定电动机的转速为1,800rpm,输出扭矩为T=0.6N·m,DuraconTM齿 轮的模数m=1mm,齿数Z=60,压力角α=20°。此外,假定金属齿轮 的齿数为10个。 假定使用条件为初期润滑脂润滑,使用温度为60℃,1天运转3小时,耐 用年数为2年。
2.1 齿隙、齿顶间隙 2.2.1 树脂层的厚度 2.3 齿轮形状
2.2.2 金属嵌件的缺口
2 齿轮形状设计方面的注意事项
2.1 齿隙、齿顶间隙
如果考虑到因热膨胀、水和润滑油而引起的尺寸变化以及成型时的尺寸公差,则塑
料齿轮的齿隙应比金属的更大。金属齿轮的齿隙是根据齿轮的制作精度、模数、节圆
直径、节点圆周速度以及润滑状态等来确定的。例如,根据日本齿轮工业会规格,轴
齿顶间隙也一样,金属取模数的12~25%,而DuraconTM则要取得更大。如果运转中 温度上升,则应估计到热膨胀,因此还要取得更大些。
杜邦膜技术手册
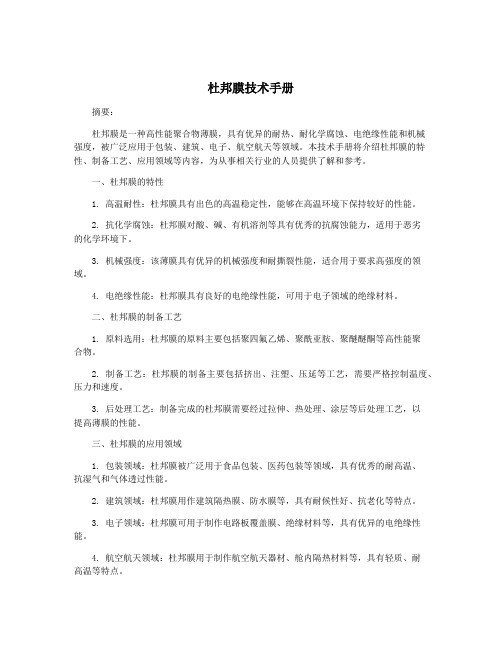
杜邦膜技术手册摘要:杜邦膜是一种高性能聚合物薄膜,具有优异的耐热、耐化学腐蚀、电绝缘性能和机械强度,被广泛应用于包装、建筑、电子、航空航天等领域。
本技术手册将介绍杜邦膜的特性、制备工艺、应用领域等内容,为从事相关行业的人员提供了解和参考。
一、杜邦膜的特性1. 高温耐性:杜邦膜具有出色的高温稳定性,能够在高温环境下保持较好的性能。
2. 抗化学腐蚀:杜邦膜对酸、碱、有机溶剂等具有优秀的抗腐蚀能力,适用于恶劣的化学环境下。
3. 机械强度:该薄膜具有优异的机械强度和耐撕裂性能,适合用于要求高强度的领域。
4. 电绝缘性能:杜邦膜具有良好的电绝缘性能,可用于电子领域的绝缘材料。
二、杜邦膜的制备工艺1. 原料选用:杜邦膜的原料主要包括聚四氟乙烯、聚酰亚胺、聚醚醚酮等高性能聚合物。
2. 制备工艺:杜邦膜的制备主要包括挤出、注塑、压延等工艺,需要严格控制温度、压力和速度。
3. 后处理工艺:制备完成的杜邦膜需要经过拉伸、热处理、涂层等后处理工艺,以提高薄膜的性能。
三、杜邦膜的应用领域1. 包装领域:杜邦膜被广泛用于食品包装、医药包装等领域,具有优秀的耐高温、抗湿气和气体透过性能。
2. 建筑领域:杜邦膜用作建筑隔热膜、防水膜等,具有耐候性好、抗老化等特点。
3. 电子领域:杜邦膜可用于制作电路板覆盖膜、绝缘材料等,具有优异的电绝缘性能。
4. 航空航天领域:杜邦膜用于制作航空航天器材、舱内隔热材料等,具有轻质、耐高温等特点。
结论:杜邦膜作为一种高性能聚合物薄膜,在包装、建筑、电子、航空航天等领域有着广泛的应用前景。
随着技术的不断进步,杜邦膜将会在更多领域展现出其优异的性能和应用价值。
NIDEC-SHIMPO 精密齿轮技术指南说明书

Precision Gear Technology GuideNidec-SHiMPO cORPORATiONOur companyNIDEC-SHIMPO has established itself as the leading supplier of precision gearing solutions to the industrial automation mar-ketplace. Since 1952, when we introduced the world’s first mechanical variable speed drive, NIDEC-SHIMPO has expanded into a diverse manufacturer of high precision power transmission systems for highly dynamic motion control applications. In 1994, SHIMPO was acquired by the NIDEC Corporation and became formally known as NIDEC-SHIMPO. NIDEC-SHIMPO began to focus on accelerating production volumes as the global market for motion control and mechatronics grew at an acceler-ated rate. We saw a unique opportunity to supply our customer base with the highest variety of transmission technologies, which brought forward strain wave, index table and worm gear products to complement our existing portfolio of planetary and cycloidal gearheads. The result for our customers was a single source drive solutions supplier.Today, our company is shipping over 100,000 gearheads per month out of our manufacturing plants in Kyoto and Shanghai. Our products are used in robotics, machine tools, food packaging, printing, paper converting, material handling, medical, semiconductor and aerospace related systems. Our diverse product portfolio, state-of-the-art equipment, engineering know-how and manufacturing scale allow our customers to compete and expand their businesses globally. NIDEC-SHIMPO has over 2,400 employees strong with a presence across five continents. Our engineering staff, customer support team and dis-tribution partners undergo rigorous product training to ensure the quickest response to our customers’ needs. Our aim is to continue to innovate and provide the highest quality, best-in-class products and services for our customer base.Our Local capabilitiesNIDEC-SHIMPO services the North American marketthrough our Headquarters and 50,000 sq. ft. assembly fa-cility in Glendale Heights, Illinois. This facility houses oursales, design and application engineering and customersupport teams. We assemble over 75% of our productsin North America, most of which can ship within 1 week.Motor adapters are readily available for easy mountingto any servomotor manufacturers’ models. With over$3MM in inventory, next day delivery is available for sev-eral common models and for emergency replacementsfor equipment in the field. We are highly flexible and canfulfill custom requirements such as special output shaftsdimensions, coatings, lubrication, materials of construc-tion and integrated product assemblies.Our products are 100% exit-tested to ensure allperformance specifications are met, giving our cus-tomers security and peace of mind. Each gearboxis inspected for noise, backlash, vibration, no-loadrunning torque, concentricity and input shaft slip-ping using the latest equipment and methods. Our 5Year Standard Warranty is our way of demonstratingNIDEC-SHIMPO’s commitment to quality and durabil-ity over the long term. Local, personal support is aphone call or email away. Each NIDEC-SHIMPO cus-tomer has a dedicated team of customer service andtechnical support professionals, on-standby to assistwith pricing, delivery, sizing, repairs, installation sup-port or other needs. We strive to deliver the highestquality, value and service in the industry.VR Series Inline Planetary GearheadsExceptional value for mid to high end motion controlapplications with demanding accuracy requirementsThe widest range of frame sizes (042-285) and ratios(3-100) available in the marketBest-In-class backlash (≤3 arc-min), with reducedbacklash option availableBroad range of mounting adapters offer a simple,precise attachment to any motorMaintenance-free solution that is lubricated for life.High performance grease allows for flexible mount-ing in any orientationIndustry standard mounting dimensionsAssembled in the USA, with immediate deliveryVR FeaturesCarburized helical gears with proprietary secondaryfinishing process for higher accuracy and smooth,quiet operation. 40% higher tooth surface area thanthe industry standardOne piece output shaft and planet carrier with twobearings straddling the planet gears. Higher stiffness,torque capacity and safety factor, with guaranteedalignment of gearingUncaged needle roller bearings provide excellenttorque density and torsional rigidity. 43% larger bear-ing surface area compared to the rest of the industry Unique labyrinth input seal design greatly reducesheat and increases system efficiency. IP65 protection is available for wash down applicationsOptimized mounting system with active centering on motor pilot diameter guarantees alignment of motor. Motor can be installed in any orientationTrue concentric motor shaft clamping connection,optimized for your specific motor. Reduced inertia for dynamic performance and balanced for highspeed operationRing gear machined directly into the housing, not welded or pressed in. Provides greater concentricityand elimination of speed fluctuation3 2VRSF VRL VRB VRS VRT Inline Inline Inline Inline Inline Helical Planetary Helical Planetary Helical Planetary Helical Planetary Helical Planetary042-220047-285EV Series Right-angle Planetary Gearheads5Compact right-angle design for application where space and clearance are a serious limitation Exceptional value for mid to high end mo-tion control applications with demanding accuracy requirementsThe widest range of frame sizes ( 060-255) and ratios (3-105) available in the marketBroad range of mounting adapters offer a simple, precise attachment to any motorMaintenance-free solution that is lubricated for life. High performance grease allows for mounting in any orientationHollow output shaft available for flexible mounting to machinery Assembled in the USAeV FeaturesRight angle bevel gear configuration allows motor to be mounted at a 90 degree position from the gearbox, saving spaceCarburized helical gears with proprietary secondary finishing process for higher accuracy and smooth, quiet operation. 40% higher tooth surface area than the industry standardOne piece output shaft and planet carrier with two bearings straddling the planet gears. Higher stiffness, torque capacity and safety factor, with guaranteed alignment of gearingUncaged needle roller bearings provide excellent torque density and torsional rigidity. 43% larger bear-ing surface area compared to the rest of the industry Optimized mounting system with active centering on motor pilot diameter guarantees alignment of motor. Motor can be installed in any orientationTrue concentric motor shaft clamping connection, optimized for your specific motor. Reduced inertia for dynamic performance and balanced for high speed operationRing gear machined directly into the housing, not welded or pressed in. Provides greater concentricity and elimination of speed fluctuationNeV eVL eVS eVT Right-angle Right-angle Right-angle Right-angle Spiral Bevel/Planetary Spiral Bevel/Planetary Spiral Bevel/Planetary Spiral Bevel/Planetary070-235060-240064-2553-1004-100EJ Series Servo Worm GearheadsExceptionally quiet, smooth running design. Zero backlash availableNo change in envelope with increase in ratio. Up to 90:1 available in a single stage 300% shock load capacity combined with high overhung load capacityHigh repeatability with exact ratios, beneficial for tuningExcellent fit for continuous duty applications with continuous running speeds as high as 4,000 rpmFlexible mounting options include solidshaft, hollow shaft, dual shaft, ISO flange and shrink discSuperior environmental protection: stainless, black anodized or white epoxy coatings; IP65 orIP69K rated, with double input and output seals3Globoidal gear set – between 3-8 teeth in contact at once, allowing 300% shock load capacityAdapter–bushing connection al-lows simple mounting to virtually any servomotor manufacturerWide range of output mounting styles avail-able – hollow shaft, solid shaft, dual shaft, shrink disc, ISO flangeDouble oil seal and o-ring provide IP65 protectionTapered roller or ball bearings at input side Thermally efficient housings available in an-odized aluminum, cast iron or stainless steeleJ FeatureseJM eJL eJH EJP EJS Right-angle Right-angle Right-angle Right-angle Right-angle Globoidal Worm Globoidal Worm Globoidal Worm Globoidal Worm Globoidal Worm 02-0925-20015-3538-8939-76 5-605-905-605-605-60STH Series Rotary Index TablesSTH Features drive directions85mm pass through hole allows pass through of air lines, wiring or other peripheral components ≤2 arc-min backlash with +- 60 arc-sec indexing accuracyReduction ratios from 12:1 up to 400:15000N radial load capacity, ideal for mid-range index table applicationsBroad range of mounting adapters offer a simple, precise attachment to any motorMaintenance-free solution that is lubricated for life. High performance grease allows flexible mounting in any orientationAssembled in the USA with immediate deliverySTR Series Rotary Index TablesHighest level of positioning accuracy and runout accuracy, difficult to attain with other gearing technologiesZero Backlash Available – a unique preload mecha-nism to completely eliminate backlash and deliver motion that is true to input commandsImpressive dynamics – Exceptional with direction reversing applicationsReduction ratios up to 2000:1 are possible using a planetary primary stageLightweight, compact aluminum alloy housing for minimal footprintExcellent fit for rotary pick and place applications, large dial tables , positioners and transfer systems Maintenance free solution using grease lubrica-tion, can be mounted in any positionWedge-shape ribs on input shaft maintain contact with the roller followers under preload to com-pletely remove backlash.The steel alloy input shaft is made to meet extremely tight toler-ances. These shafts are balanced to suppress vibration under high speed rotation.Roller bearing construction trans-fers torque by the rolling action of the roller followers. Rolling con-tact maintains initial accuracy for extended periods of use.Preloadinput ShaftRoller FollowersSTR FeaturesThe output shaft has an oversized hollow bore that allows easy pas-sage of wiring and air lines, or the shaft of another device, for ex-tended design flexibility.Cross roller bearings are used in-side the output unit for increased rigidity and minimal runout.The motor or gearbox shaft is rig-idly clamped to the input shaft of the rotary unit for a direct transfer of power.Hollow Output Shaftcross Rollersinput clamping System< 1 arc-min backlash with 20-30 arc-sec repeatability High torsional stiffness with minimal hysteresis loss Large e-stop capacity of 5x rated torqueHigh reduction ratios and power density in a com-pact design4 frame sizes with acceleration torque ranging from 613-3185 NmHollow shaft for easy pass thru of wires, cabling or ball screwsFlexible integration into robotic joints, positioners,turntables or other automated machineryEccentricrollerbearings eRP FeaturesWheelseRH FeaturesMounting OptionsBase MountFlange MountRing MountHollow MountHigh efficiency cycloidal design 500% shock load capacity Backlash as low as 6arc-minVarious mounting options: Base, Flange, Ring, Hollow Reduction ratios up to 71:1 offered in a single stage Broad range of mounting adapters offer a simple, precise attachment to any motor Food grade options available Assembled in the USAWP Strain Wave GearsHarmonic gear reduction mechanism that achieves zero backlash, as well as exceptional positioning accuracy, repeatability and high torque densityHigh Reduction Ratios in a single stage. Lightweight, compact designVarious form factors, including component sets, simple contained assemblies and complete gear units. Cup, Silk Hat, solid and hol-low shaft configurations give engineers true design freedom Available in Ultra-Flat and High Torque variations for applications with demanding footprint and performance requirements Industry standard dimensions for simple implementation in legacy equipment designsSuperior choice for Robotics, Machine Tool, Medical, Semiconduc-tor, SatCom and Assembly Automation applicationsWave GeneratorCircular Spline Flexspline 123configure our planetary products with ease. download models.NIDEC-SHIMPO’s Online Product Configurator makes it eas-ier than ever for engineers to incorporate our products into their drive system design. Our configurator allows our cus-tomers to select from wide range of servo motor manufac-turer models to ensure flawless fitment with our products. With over 75 motor manufacturers included, there is a good possibility we have a solution ready to go. The following are just a few examples of motor manufacturers we are fully compatible with:In addition to motor sizing, our configurator also allows our customers to select gearheads based on application. These applications include rotary tables, belt conveyors, rack and pinion drives, lifting and lowering devices, ball screws, drive gears, drive carriages and robot joints. After selecting the application template, customers can then input the application load parameters and motion profile. The proper frame size and reduction ratio are then deter-mined, with motor selection as the final last step.Once sizing is complete, our configurator will then display the full part number, along with gearbox and motor tech-nical specifications. This part number includes the motor mounting adapter, which can be sent directly to our sales support team for pricing & delivery.Drawings and models are also available in PDF, DXF, IG S and STEP formats, making it simple for machine designers to quickly drop them into machine schematics to check for proper fitment. We have seasoned application engineersstanding by to assist with any sizing or selection questions.http://www.nidec-shimpo.co.jp/selection/all/index.phpDrive GearsRack and PinionDrive CarriageRotary TableRobot JointsLifting & Lowering DeviceBall ScrewBelt ConveyorApplication Selection。
杜邦膜技术手册
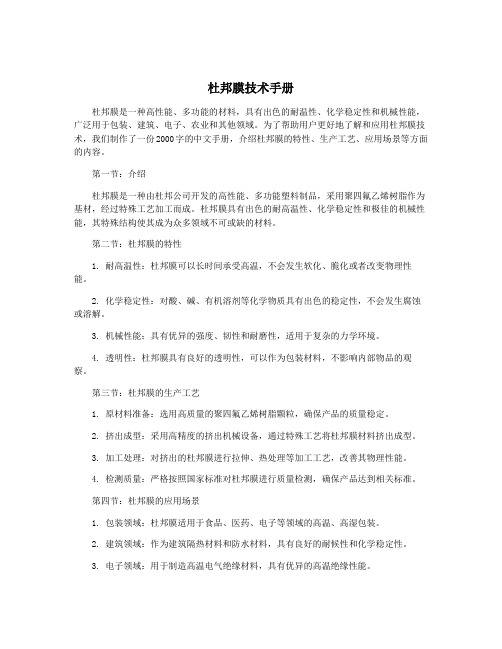
杜邦膜技术手册杜邦膜是一种高性能、多功能的材料,具有出色的耐温性、化学稳定性和机械性能,广泛用于包装、建筑、电子、农业和其他领域。
为了帮助用户更好地了解和应用杜邦膜技术,我们制作了一份2000字的中文手册,介绍杜邦膜的特性、生产工艺、应用场景等方面的内容。
第一节:介绍杜邦膜是一种由杜邦公司开发的高性能、多功能塑料制品,采用聚四氟乙烯树脂作为基材,经过特殊工艺加工而成。
杜邦膜具有出色的耐高温性、化学稳定性和极佳的机械性能,其特殊结构使其成为众多领域不可或缺的材料。
第二节:杜邦膜的特性1. 耐高温性:杜邦膜可以长时间承受高温,不会发生软化、脆化或者改变物理性能。
2. 化学稳定性:对酸、碱、有机溶剂等化学物质具有出色的稳定性,不会发生腐蚀或溶解。
3. 机械性能:具有优异的强度、韧性和耐磨性,适用于复杂的力学环境。
4. 透明性:杜邦膜具有良好的透明性,可以作为包装材料,不影响内部物品的观察。
第三节:杜邦膜的生产工艺1. 原材料准备:选用高质量的聚四氟乙烯树脂颗粒,确保产品的质量稳定。
2. 挤出成型:采用高精度的挤出机械设备,通过特殊工艺将杜邦膜材料挤出成型。
3. 加工处理:对挤出的杜邦膜进行拉伸、热处理等加工工艺,改善其物理性能。
4. 检测质量:严格按照国家标准对杜邦膜进行质量检测,确保产品达到相关标准。
第四节:杜邦膜的应用场景1. 包装领域:杜邦膜适用于食品、医药、电子等领域的高温、高湿包装。
2. 建筑领域:作为建筑隔热材料和防水材料,具有良好的耐候性和化学稳定性。
3. 电子领域:用于制造高温电气绝缘材料,具有优异的高温绝缘性能。
4. 农业领域:广泛用于温室大棚、土地覆盖等场合,提高农产品生产效率。
第五节:杜邦膜的未来发展趋势1. 绿色环保:杜邦膜将以更环保的生产工艺和可降解材料作为未来发展的趋势。
2. 多功能化:不仅作为包装材料,还将广泛应用于建筑、电子、医药等领域。
3. 智能化:通过添加智能感应材料,实现对温度、湿度等环境参数的感知和反馈。
duppont(杜邦)齿轮设计

8 – GearsIntroductionD ELRIN®acetal resins and Z YTEL®nylon resins are used in a wide variety of gear applications throughout the world. They offer the widest range of operating temperature and highest fatigue endurance of any thermoplastic gear mate-rial, accounting for their almost universal use in non-metallic gearing.The primary driving force in the use of plastic vs. metal gears is the large economic advantage afforded by the injection moulding process. In addition, cams, bearings, ratchets, springs, gear shafts and other gears can be designed as integral parts in a single moulding, thus elim-inating costly manufacturing and assembly operations. Tolerances for plastic gears are in some cases less critical than for metal gears because the inherent resiliency enables the teeth to conform to slight errors in pitch and profile. This same resilience offers the ability to dampen shock or impact loads. The use of Z YTEL®nylon resin as the tooth surface in engine timing chain sprockets is an outstanding example of this latter advantage. In this case, timing chain life is extended because nylon dampens somewhat the transmission of shock loads from fuel igni-tion. Z YTEL®nylon resin and D ELRIN®acetal resin have low coefficients of friction and good wear characteristics, offering the ability to operate with little or no lubrication. They can also operate in environments that would be adverse to metal gears. A summary of the advantages and limitations of plastic gears is given in Table 8.01. Knowledge of the material performance characteristics and use of the gear design information to follow is impor-tant to successful gear applications in D ELRIN®acetal resin and Z YTEL®nylon resin.Gear DesignThe key step in gear design is the determination of the allowable tooth bending stress. Prototyping of gears is expensive and time consuming, so an error in the initial choice of the tooth bending stress can be costly.For any given material, the allowable stress is dependent on a number of factors, including:–Total lifetime cycle.–Intermittent or continuous duty.–Environment – temperature, humidity, solvents, chemicals, etc.–Change in diameter and centre to centre distance with temperature and humidity.–Pitch line velocity.–Diametral pitch (size of teeth) and tooth form.–Accuracy of tooth form, helix angle, pitch diameter, etc.–Mating gear material including surface finish and hard-ness.–Type of lubrication (frictional heat).Selection of the proper stress level can best be made based on experience with successful gear applications of a simi-lar nature. Fig. 8.01 plots a number of successful gear applications of D ELRIN®acetal resin and Z YTEL®nylon resin in terms of peripheral speed and tooth bending stress. Note that all of these applications are in room temperature, indoor environments. For similar applications operating at higher temperatures, the allowable stress should be corrected, see factor C1in Table 8.02. Since fatigue endurance is reduced somewhat as temperature increases, this effect must also be considered. Where very high tem-peratures are encountered, thermal ageing may become a factor.Where suitable experience is not available, the allowable tooth stress must be based on careful consideration of all the factors previously outlined, and on available test data on the gear material of choice.Table 8.01Advantages and Limitations of Plastic GearsAdvantages LimitationsEconomy in injection moulding Load carrying capacityCombining of functions Environmental temperatureNo post-machining or burr removal Higher thermal expansion coefficientWeight reduction Less dimensional stabilityOperate with little or no lubrication Accuracy of manufactureShock and Vibration dampingLower noise levelCorrosion resistance5960A number of years ago, DuPont commissioned a series of extensive gear tests on gears of D ELRIN ®acetal resin and Z YTEL ®nylon resin, which resulted in the information summarised in Tables 8.02 and 8.03. This data can be combined with environmental operating conditions to arrive at an allowable tooth bending stress.Whether similar experience exists or not, it is essential that a prototype mould be built and the design carefully tested in the actual or simulated end-use conditions.®®Table 8.03Fatigue Strength (σ1) for DuPont gear materials for 106cycles (MPa)LubricationMaterial Mating Material Continuous InitialD ELRIN ®100Steel 4827D ELRIN ®500Steel 3618Z YTEL ®101Steel 4025Z YTEL ®101Z YTEL ®10118Once the admissible tooth bending stress has been deter-mined, the designer can proceed with the selection of theother variables, for which an understanding of the basic terminology used in gear work is helpfull. The terms most commonly used to describe gears are:–Pitch diameter (d) is the diameter measured at the pitch circle.–Diametral pitch (P d ) is the number of teeth per inch of pitch diameter, commonly used in USA.–Module (M) is pitch diameter divided by number of teeth (z). Thus: M = d/z.For standard gears:•external diameter = d + 2M;•tooth thickness = 0,5 πM;•tooth height = 2M + clearance.–Pinion is the smaller of a pair of meshing gears.–Gear is the larger of a pair of meshing gears.–Ratio is number of teeth gear/number of teeth pinion.Fig. 8.01Speed versus stress: Typical gear applications placed on curve61Gear with off-centre webin the rim or the web, then web thickness should equalhub thickness, as no section of a given thickness can befilled properly through a thinner one.The maximum wall thickness of the hub should usuallynot exceed 6 mm. For minimum out-of-roundness, useOn gears which are an integral part of a multifunctionalcomponent or which have to fulfill special requirementsas shown in Fig. 8.20-8.25, it could be impossible toapproach the ideal symmetrical shape as shown inFig. 8.03, in which case the assembly must be designedto accept somewhat less accuracy in the gear dimensions.The following additional examples illustrate a few moregear geometries which could lead to moulding and/orfunctional problems:Relatively wide gears which have the web on one sidewill be rather difficult to mould perfectly cylindrical,especially if the centre core is not properly temperaturecontrolled. If the end use temperature is elevated, thepitch diameter furthest from the web will tend to besmaller than the pitch diameter at the web (Fig. 8.04).Effect of radial ribs Ribbed worm take-off gear 6263Low shrinkageHigh shrinkageGate3 GatesWeld linesFig. 8.08Holes and ribs in moulded gearsFig. 8.09Centre gated gearFig. 8.10Web gated gear Measurement of tooth profile errorTotal profile errorBacklash and Centre DistancesAs shown in Fig. 8.11-e backlash is the tangential clear-ance between two meshing teeth. Fig. 8.12 providesa suggested range of backlash for a first approach.It is essential to measure and adjust the correct backlash at operating temperature and under real working condi-tions. Many gears, even though correctly designed and moulded fail as a result of incorrect backlash at operating conditions.64Center distance measuring instrumentFig. 8.11-c Center distance variation diagramFig. 8.11-d Moulding tolerances from center distance diagramTotal composite errorRunoutOne revolution of gearTooth-to-tooth errorT 1T65LubricationExperience has shown that initial lubrication is effective for a limited time. Units disassembled after completion of their service life showed that all the grease was thrown on the housing walls; hence the gears ran completely dry. Initial lubrication does not allow a high load, it should be considered as an additional safety factor. It should, however, always be provided as it helps greatly during the run-in period.On applications where lubricant cannot be tolerated, the combination of D ELRIN®acetal resin and Z YTEL®nylon resin offers great advantages. Even under dry conditions such gear trains run smoothly and with little noise. Where continuous lubrication of gears in D ELRIN®acetal resin and Z YTEL®nylon resin is practical, and where surface pressure on the meshing teeth is not excessive, wear is negligible and service life is determined exclu-sively by fatigue resistance.Testing Machined PrototypesThough it would appear that the easiest way to determine whether a proposed gear will show the expected perform-ance would be to test machined prototypes, results thus obtained must be interpreted with great care. A designer has no guarantee that a subsequently moulded gear will have the same performance characteristics. Therefore no final conclusion can be drawn from test results using machined gears. Making a trial mould is the only safe way to prototype a gear design. It allows not only mean-ingful tests but also the measurement of shrinkage, tooth profile, pitch diameter and overall accuracy.It is highly recommended to check tooth quality on a pro-file projector which enables detection of deviation from the theoretical curve.Prototype TestingThe importance of adequate testing of injection moulded prototype gears has been emphasized. Here are some guidelines:–Accelerated tests at speeds higher than requiredof a given application are of no value.–Increasing temperature above normal working tempera-ture may cause rapid failure whereas under normal working conditions the gear may perform well. Test conditions should always be chosen to come as close as possible to the real running conditions.The following examples further explain the need for meaningful end-use testing.–Gears under a high load (e.g., in appliances) which operate only intermittently should not be tested in a continuous run, but in cycles which allow the whole device to cool down to room temperature between running periods.–Infrequently operated, slow-running gears (such as window blinds) can be tested in a continuous run but at the same speed, providing temperature increase on the tooth surfaces remains negligible.–Other applications like windshield wiper gears reach their maximum working temperature quickly, and oper-ate most of their service life under these conditions. They should therefore be tested on a continuous-run base.Valuable conclusions can often be drawn from the static torque at which a moulded gear fails. If breaking torque proves to be 8-10 times the operating load, it can usually be taken as an indication that the gear will provide a long service life in use. However, plastic gears often operate very close to the endurance limit, and the above relation should not be considered as valid in all cases.In any event, backlash must be checked during all tests. Once a gear has failed, it is almost impossible to deter-mine whether incorrect backlash was partially or entirely responsible.Helical Gear DesignWhenever possible, helical gears should be used in pre-ference to spur gears. Among other advantages they run more smoothly and have less tendency to squeak. However, they require not only perfect tooth profiles but also exactly matching helix angles. This requirementis sometimes difficult to fulfill, especially if the plastic gear meshes with a metal gear.Helical gears generate axial thrust which must be con-sidered. It is advisable to use helix angles not greater than 15°. Compared to a spur gear having the same tooth size, a helical gear has slightly improved tooth strength. Since small helix angles are most commonly used, this fact can be neglected when determining the module and it should be considered as an additional safety factor only.66Fig. 8.13One piece worm gear9 side coresFig. 8.14Side-cored worm gearFig. 8.15Half throated worm gearFig. 8.16Split worm gear676869Worm gearof D ELRIN®dαWorm of Z YTEL® 101Fig. 8.18Can opener with worm drive70Fig. 8.21Impact resistant webFig. 8.20Ratchet and gear combinedFig. 8.22Backlash-free gear71Backlash-free gearFig. 8.24Torque limiting gearFig. 8.25Gear with sliding coupling 72When to use D ELRIN®Acetal Resin or Z YTEL®Nylon ResinZ YTEL®nylon resin and D ELRIN®acetal resin are excellent gear materials, used extensively in a variety of applica-tions. The choice of one over the other may at first seem unclear, but as one examines the specific requirements of the application, it becomes relatively easy. Although the two materials are similar in many ways, they have distinct property differences, and it is these differences upon which the selection is made. Some guidelines are as follows:Z YTEL®Nylon Resin–Highest end-use temperature–Max. impact and shock absorption–Insert moulding–Max. abrasion resistance–Better resistance to weak acids and bases–Quieter runningD ELRIN®Acetal Resin–Best dimensional stability–Integrally moulded springs–Running against soft metals–Low moisture absorption–Best resistance to solvents–Good stain resistance–Stiffer and stronger in higher humidity environmentAs previously pointed out, running D ELRIN®acetal resin and Z YTEL®nylon resin against each other results in lower wear and friction than either material running against steel (not always true when high loads are encountered and heat dissipation is controlling). Some designers have used this combination in developing new, more efficient gear systems.When properties of D ELRIN®acetal resin are needed,D ELRIN®100 is the preferred gear material. As previously stated, D ELRIN®100 outperforms D ELRIN®500 by about 40%. D ELRIN®100 is the most viscous in the melt state, and cannot always be used in hard to fill moulds. D ELRIN®500 and 900 have been used successfully in many such cases.When Z YTEL®nylon resin is the chosen material,Z YTEL®101L is the most common material used.Z YTEL®103HSL, a heat stabilized version ofZ YTEL®101L, should be specified if the service life and end use temperature are high.Glass reinforced versions of either material should be avoided.The glass fibres are very abrasive and the wear rate of both the plastic gear and the mating gear will be high. Gears which operate for extremely short periods of time on an intermittent basis have been used with glass reinforcement to improve stiffness, strength or dimen-sional stability.Very careful testing is mandatory.The moulding conditions must be controlled carefully, not only for the usual purpose of maintaining gear accuracy, but also because glass reinforced resins will exhibit large differences in surface appearance with changes in mould-ing conditions, particularly mould temperature. It is pos-sible to vary mould temperature without changing dimen-sions, by compensating through adjustments in other process variables. Thus, establish surface smoothness specifications to be sure the type of gear surface tested is reproduced in mass production.73。
DURLON密封技术手册.Image.Marked
DURLON ®
杜拉巴尔密封技术手册
质量 | 性能 | 服务
DURLON® 耐久龙TMDURLON®耐久龙TM密封科技
加拿大杜拉巴尔创立于1911年,具有超过百年的密封专业技术经验。DURLON®全系列密封材料
科技及完善的密封技术服务一直处于世界领先地位。
耐久龙TM系列密封产品经过多年不断地研发和改良,适用于极其广泛的应用工况。耐久龙TM被广 泛应用于炼油,石油化学,化工,电力(火电及核电),造纸,食品,药品等终端用户及其相应 的设备制造,工程设计及施工等领域。耐久龙TM 适用工况的温度范围从低温零下268摄氏度到高 温1000摄氏度,压力从真空工况到美标2500磅级。耐久龙TM可以安全可靠地密封各种高危介质 如:液态氧气,光气,氢氟酸等等。在空分行业,耐久龙TM具有经广大行业用户应用验证的垫片 氧清洗脱油脱脂技术。对于大尺寸的PTFE垫片(直径大于1.5米以上),耐久龙TM具有先进成熟 的垫片焊接技术。耐久龙TM非金属板材垫片具有齐全的尺寸规格,厚度范围从0.4毫米到8.0毫 米,板幅最大可达3米X3米。因此,耐久龙TM的用户再也不需要选择和库存很多种类的密封材 料。这将在很大程度上改善用户生产过程的安全性。减少使用密封材料的种类意味着降低了在多 种工况下不当选用密封材料的潜在安全风险。
Page 4
颜色 结构系统 粘合 温度
Min Max
密度 g/cc (lbs/ft3)
压缩率, % ASTM F36J
回弹率, % ASTM F36J
蠕变松弛, % ASTM F38
拉伸强度 ASTM F152, MPa (psi)
热失重 @ 800oC DIN 52911
氮气气密性 cc/min ASTM F2378
Dupont杜邦工程塑料培训
®杜邦公司注册商标杜邦中国集团有限公司工程塑料部地址200021电话021 –6385 3155网址®杜邦公司注册商标特灵®聚甲醛特灵®聚甲醛是由聚甲醛是由杜邦公司于上世纪50年代末发明的均聚高分子材料共聚聚甲醛由Celanese公司在2年后发明Formaldehyde moleculeHydrogen atomHydrogen bondingOxygen atomCarbon atom®杜邦公司注册商标聚甲醛的改性品种n抗紫外线n耐摩擦和低磨损n增韧剂n挤出级别n玻璃纤维n抗静电处理相互摩擦时抗摩擦®杜邦公司注册商标n燃油系统n夹子n门把手n摇窗手柄n音响隔栅特灵®汽车工业的应用特灵®主要应用n运输带n齿轮n小型轮子n夹子n弹簧n轴承支架n空气阀门n录象带带座n滑雪板n点火机n泵体n拉链n照射系统n厨房家电n气枪n图章®DuPont’s registered trade name®杜邦公司注册商标特灵®标准牌号牌号类型特灵®100, 100P高韧级特灵®500, 500P, 511P中流动级特灵®900P, 911P低流动级特灵®127UV, 527UV耐侯级特灵®100ST, 100T, 500T冲击改性特灵®500AF, DE9156特氟龙®-改性特灵®500CL耐磨损如果您需要聚甲醛您需要聚酰胺是由杜邦公司于1920年发明的®杜邦公司注册商标PA 66, (120/180Zytel ®/ Minlon ®汽车工业的应用®杜邦公司注册商标n 连接器n 风扇n 风扇罩n后视镜n 阀门罩子n 进气歧管n 水箱n车轮盖Zytel ®/ Minlon ®电子/电器工业的应用®杜邦公司注册商标n 连接器n 扎带n 短路开关n线圈骨架n 插座n 封装马达n 电动工具n焊接工具Zytel ®/ Minlon ®主要应用®杜邦公司注册商标n 小型锯部件n 自行车轮子n 运动器械n 滑雪鞋n滑雪撬n 家具部件n 火车绝缘器n 焊接头盔n 热水泵n厨房器具Zytel®HTN 是杜邦开发的一种新型聚合物®杜邦公司注册商标优势:硬度(玻纤增强)低吸水性高的尺寸稳定性高的使用温度(150/200 ®杜邦公司注册商标如果您需要尼龙塑料,您需要®杜邦公司注册商标Crastin®Crastin®是杜邦公司热塑性PBT聚酯塑料的商品名杜邦公司在1993年收购了汽巴嘉技的PBT业务后在很大程度上扩展了自己的PBT销售规格®杜邦公司注册商标PBT改性l冲击改性l阻燃改性l ASA (丙烯晴-苯乙烯–丙稀酸) l PET –合金l增强类型:m玻纤增强m玻璃珠增强m矿物增强. (130 / 180如果您需要PBT聚酯塑料,您需要®杜邦公司注册商标Rynite®-PETRynite®是杜邦公司热塑性PET聚酯塑料的商品名Rynite®都是用玻纤或矿物增强的PET工程塑料. (155 / 200Rynite®主要应用®DuPont’s registered trade namen 烤炉手柄n 灯座n 封装马达n 线圈骨架n刮雨器n 变压器壳体n 连接器n 盖子n 熨斗裙角n烤饼机®杜邦公司注册商标Zenite®是杜邦公司液晶高分子聚合物的商品名这种材料是一种属于芳香族共聚物优势:同时具备较高的硬度, 强度和韧性.低吸水性尺寸稳定性高的使用温度(240®杜邦公司注册商标。
杜邦DuPont资料-工程塑料产品介绍
工程塑料
PPO
PC
PA POM
PBT TPE
PP-GF PP PE-LD
PET
通用塑料
ABS PS SAN
PMMA PVC
Crastin® & Rynite® Polyester
PE-UHMW PE-HD
无定型聚合物
®
结晶聚合物
Hytrel® Thermopla stic Polyester Elastomer
Registered trade name of DuPont
热塑性塑料的类别划分
Teflon® & Tefzel® Fluoropolymers
PI
Vespel® PI
Zenite® LCP
特种聚合物
Zytel® HTN
PSU PTFE LCP PES HPPA PPSU
Zytel® & Minlon® Polyamide Delrin® Polyacetal
“100” 高粘度, 高冲击 通用级 高性能等级 高成型 加工性 Enhanced ELEVEN 共聚物 挤出级 II 150 SA II 150 E II 550
Highlighted grades are new commercial offerings.
“300” 中-高 粘度
“500” 中 粘度 500
Glass Reinforced Mineral Reinf. Min, GR T, GR ST, GR DMX, GR FR, GR FR, Min ST, Min
FE6228
82G
FR51G
FR52G
Delrin 聚甲醛树脂
®
Delrin® acetal 由杜邦在 50年代末 期发明.
PA66 46 6T 9T 10T的性能及应用
PA66/46/6T/9T/10T的性能及应用电子、电气等设备的小型化、高性能化对材料的要求越来越高.特别是表面贴装技术(SMT)的出现和发展,促进了电子元件小型化、密集化并降低了成本。
但采用SMT技术对材料的耐回流焊性和尺寸稳定性提出了更高的要求,如承受短期约260℃的回流焊的峰值温度。
汽车的轻量化、高性能化促进和深化了金属部件的塑料化,也同时对塑料提出了更高的要求,如发动机周边部件的耐热、耐久性等.PA6、PA66等通用工程塑料,性能优异,价格适中,用途广泛,在工程塑料中占有重要的地位,但也存在不足,如容易吸湿、耐高温性能有待提高等。
为进一步提高耐热性,满足汽车、电子电气等行业越来越高的要求,耐高温PA应运而生,与PA66相比,它是一类熔点和使用温度更高的均聚或共聚树脂及其增强改性材料。
常见的耐高温PA主要有PA46、PA6T、PA9T、PA10T、聚对苯二甲酰对苯二胺(PPTA)等,其中,PA6T、PA9T、PA10T等半芳香族聚酰胺因其耐热高、力学性能优异、不易吸湿、加工灵活方便等特点,在电子、电气+汽车等领域具有广阔的应用前景,成为争相研究的热点。
1耐高温聚酰胺的结构与性能聚合物的耐热性与其熔点(Tm)、玻璃化温度(Tg)密切相关。
表1列出了PA66及主要耐高温PA的化学结构、熔点及玻璃化温度。
1。
1耐热性耐高温PA的主要特点之一就是熔点比通用PA如PA66高,但熔点太高,难以加工,所以一般多在320℃以下。
PA46玻璃化转变温度低,模量开始下降的温度低,但由于其结晶度高,因此在高温下物性下降小。
PA6T、PA9T、PA10T等半芳香族聚酰胺,玻璃化温度高,模量降低起始温度高。
PPTA玻璃化温度太高,难以用通用塑料加工方法加工。
1.2加工性注射成型要求材料具有较高的流动性及较宽的加工窗口。
一般情况下,PA的熔融成型加工温度在320℃左右,分解温度在350℃附近。
PA6T均聚物熔点在370℃左右,熔融温度超过了分解温度,难以加工成型,因此需要改性,使成型温度降到320℃以下。
- 1、下载文档前请自行甄别文档内容的完整性,平台不提供额外的编辑、内容补充、找答案等附加服务。
- 2、"仅部分预览"的文档,不可在线预览部分如存在完整性等问题,可反馈申请退款(可完整预览的文档不适用该条件!)。
- 3、如文档侵犯您的权益,请联系客服反馈,我们会尽快为您处理(人工客服工作时间:9:00-18:30)。
低翘曲
高结晶度
尺寸稳定
高强度
2010-8-15
15
保压时间对品质的影响
保压时间可以影响: 成型产品的
机械性能 (产品内部空洞) 外观 (缩痕) 收缩 (尺寸稳定性) 翘曲
产品内部空洞 良好的结构 不良的结构 (压力线)
பைடு நூலகம்
2010-8-15
16
模具温度
主要影响冷卻速度及结晶 (1)高模温 慢冷卻高结晶度高模收縮低后收縮制品尺寸稳定 (2)低模温 快冷卻低结晶度低模收縮高后收縮(在高温下)制品尺寸 不稳定
2010-8-15
22
Applications for Plastic Gears – 塑料齿轮的应用 General Types 一般分类
• Power Transmission 动力传送
- high loads/low speed - high torque - motor used to develop work or carry a load - part life extends until gear breaks - external lubrication - steel countersurface
DuPont Technical Seminar
杜邦技术研讨会 采用工程塑料是高性能齿轮的明智选择
DuPont Engineering Polymers Jul 2007
2
杜邦人员介绍
• 杜邦日本齿轮专家剑持纲雄先生 • 杜邦技术经理-Justin Wu 吴经理 • 杜邦市场开发经理-陈铓
2010-8-15
2010-8-15
17
模温 - 结晶
过低的模温导致: • • • 微晶 (弱) 表层 不良表面外观 内应力
好的结构 (高模温) 糟糕的结构 (低模温)
2010-8-15
18
Delrin POM成型参数
熔胶温度 °C 种类
模具温度 °C
保压 压力 MPa 85 - 100 70 - 80
保压 时间 秒/mm 8 8
2010-8-15
5
2010-8-15
6
The plastic industry
Performance High performance engineering polymers
PEI PES PAR PSU PC MPPO ABS SMA PMMA
热塑性塑料分类
PEK
高性能工程塑料
PPS
LCP PI HTN PET PA66 PBT TPE PA6 POM
2010-8-15
Plastic Gears Applications塑料齿轮应用
Stress on Teeth Surface (N) 50
100
Steering Drive驾驶方向
齿轮牙表面应力
Window Lift,窗门提起 Wind Shield Wiper雨刷 Office Automation办公室设备, Audio, Video影音器材
3
Agenda 研讨会安排
• 2:15-2:55 DuPont Introduction (杜邦简介) Homo vs Copolymer (均聚与共聚的区别) Key points in processing(注塑成形要点)
• 3:00-4:30 Gear Technics & Material selection 齿轮技术探讨及材料选择 Q & A (问题讨论)
DuPont Engineering Polymers Jul 2007
20
Content
内容
•Why use plastics for gears?为何选用塑料于齿轮上? •Applications for plastic gears 塑料齿轮的应用
power 动力vs. motion transmission运转传送 •Top engineering polymers for gears齿轮首选工程塑料 • New Low Wear / Low Friction Resins and Applications 最新的低摩擦、低磨耗系列塑料及其应用
5
10
15
20
°C
建议熔融温度
2010-8-15
13
熔胶品质
均匀的熔化
良好的结构
一致的结晶
最佳性能 最小内应力
较差的结构 – 未熔
2010-8-15
14
保压
PVT - DIAGRAM P = 1 bar
保压越大
1,4 1,2 1 P = 1000 bar 0,8 0,6 0,4 0,2 0 0 20 40 60 80 100 120 140 160 180 200 220 240 260 280 300 Temperature °C Crystalline Plastic
聚甲醛--均聚与共聚在分子结构上的不同
HOMOPOLYMER 均聚(Delrin)
CH3 – O – H | C – O –– | H n H | C – O ….… | H H | C –O– | H O || C – CH3
COPOLYMER 共聚
CH3 – O – OH H | C – O ––– | H n H | C – | H H | C – O –– | H H | C – O ––– | H n
杜邦 Delrin POM 注塑成型要点
DuPont Engineering Polymers Jul 2007
11
滞留时间 / 含水量 螺杆及料筒设计 熔融温度
熔胶品质
背压 温度曲线
螺杆转速
2010-8-15
12
熔胶品质
机械强度 100%
80% 60% 40% 20% 0%
-20
-15
-10
-5
570 510GR, 525GR
500 AF 500TL, 520MP 500MP 500 CL 500SC 500 AL
100 AL
911 AL
Highlighted grades are new commercial offerings.
2010-8-15
DuPont Technical Seminar
最高滞留 时间 分钟 30 15 - 25
所有无增韧级别 215 / 210 - 220 90 / 80 - 100 增韧级别 205 / 200 - 210 50 / 40 - 60
2010-8-15
DuPont Technical Seminar
Gear Technics & Material selection 齿轮技术探讨及材料选择
2010-8-15
21
Why Use Plastics for Gears?为何选用塑料于齿轮上
Lubricity 自润性
internally lubricated grades available low wear/low friction
Noise Reduction
减低噪音
low impact noise reduce high pitch squeak
0
0
50
100
Frequency of Gear Engaging (rpm)
齿轮转速
24
Plastic Gears Applications塑料齿轮应用
100
High loads involved Motor used to develop a work or to carry a load Part life is until gear breaks
Flow Series
Impact modified Super Tough Medium Tough Toughened UV Stabilized Improved UV
“100”
“300/400”
“500”
“900”
冲击增强
100 ST 100T 500 T
耐候级
127 UV 327UV 527 UV
Comonomer group 共聚集团
Formaldehyde molecule
H | C – | H
H | C – O – ……. – | H
H | C – | H
H | C – | H
甲醛单体
Formaldehyde molecules
甲醛单体
The repeating unit for all acetals is CH20 The backbone is C - O Copolymer has C - C bonds randomly interspersed every 70 to 100 units.
High stiffness (glass or mineral) Filled 玻纤增强 Reinforced Low wear / low friction 耐磨损/低摩擦 Teflon® PTFE Fibers Teflon® PTFE Micropowder 100TL Kevlar® Aramid Resin Internal Chemical Silicone Concentrate Advanced Lubricant 100 KM
抗张强度
2010-8-15
72 62
80
均聚高粘度型号 Delrin® 100P 共聚高粘度型号
35 25 23 6.5
Elongation at Elongation at Break Yield
断裂点伸长率 屈服点伸长率
Impact Strength
冲击强度
9
Delrin® acetal resin – Modified for Special Applications