热处理淬火开裂及预防
热处理常见缺陷分析与对策-学习总结
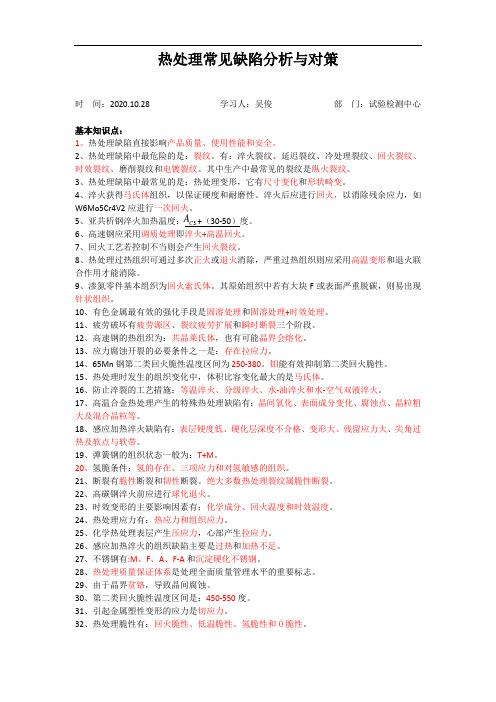
热处理常见缺陷分析与对策时 间:2020.10.28 学习人:吴俊 部 门:试验检测中心基本知识点:1、热处理缺陷直接影响产品质量、使用性能和安全。
2、热处理缺陷中最危险的是:裂纹。
有:淬火裂纹、延迟裂纹、冷处理裂纹、回火裂纹、时效裂纹、磨削裂纹和电镀裂纹。
其中生产中最常见的裂纹是纵火裂纹。
3、热处理缺陷中最常见的是:热处理变形,它有尺寸变化和形状畸变。
4、淬火获得马氏体组织,以保证硬度和耐磨性。
淬火后应进行回火,以消除残余应力,如W6Mo5Cr4V2应进行一次回火。
5、亚共析钢淬火加热温度: +(30-50)度。
6、高速钢应采用调质处理即淬火+高温回火。
7、回火工艺若控制不当则会产生回火裂纹。
8、热处理过热组织可通过多次正火或退火消除,严重过热组织则应采用高温变形和退火联合作用才能消除。
9、渗氮零件基本组织为回火索氏体。
其原始组织中若有大块F 或表面严重脱碳,则易出现针状组织。
10、有色金属最有效的强化手段是固溶处理和固溶处理+时效处理。
11、疲劳破坏有疲劳源区、裂纹疲劳扩展和瞬时断裂三个阶段。
12、高速钢的热组织为:共晶莱氏体,也有可能晶界会熔化。
13、应力腐蚀开裂的必要条件之一是:存在拉应力。
14、65Mn 钢第二类回火脆性温度区间为250-380。
钼能有效抑制第二类回火脆性。
15、热处理时发生的组织变化中,体积比容变化最大的是马氏体。
16、防止淬裂的工艺措施:等温淬火、分级淬火、水-油淬火和水-空气双液淬火。
17、高温合金热处理产生的特殊热处理缺陷有:晶间氧化、表面成分变化、腐蚀点、晶粒粗大及混合晶粒等。
18、感应加热淬火缺陷有:表层硬度低、硬化层深度不合格、变形大、残留应力大、尖角过热及软点与软带。
19、弹簧钢的组织状态一般为:T+M 。
20、氢脆条件:氢的存在、三项应力和对氢敏感的组织。
21、断裂有脆性断裂和韧性断裂。
绝大多数热处理裂纹属脆性断裂。
22、高碳钢淬火前应进行球化退火。
23、时效变形的主要影响因素有:化学成分、回火温度和时效温度。
42crmo淬火开裂危险尺寸

42crmo淬火开裂危险尺寸
摘要:
一、42CrMo 淬火开裂的定义和特点
二、42CrMo 淬火开裂的原因分析
1.原始材料原因
2.淬火原因
三、42CrMo 淬火开裂的预防措施
四、总结
正文:
一、42CrMo 淬火开裂的定义和特点
42CrMo 淬火开裂是指在42CrMo 钢经过淬火处理后产生的裂纹,这种裂纹往往在淬火过程中或淬火后的室温放置过程中产生,对钢材的性能和使用寿命有着重要的影响。
42CrMo 淬火开裂的特点是裂纹分布没有一定的规律,但一般容易在工件的尖角、截面突变处形成。
二、42CrMo 淬火开裂的原因分析
1.原始材料原因
42CrMo 钢在锻造过程中,可能会产生心部原始裂纹。
这些裂纹在淬火过程中会由于淬火应力而直接开裂。
另外,材料的元素偏析和原始组织粗大也可能导致开裂。
2.淬火原因
在淬火过程中,可能会出现以下几种情况:
a.淬火时使组织粗大,过热过烧组织,不同组织间的应力;
b.淬火油底下有一点水,引起的硬度不均匀;
c.淬火温度过高或过低,淬火后残余奥氏体过多或过少。
三、42CrMo 淬火开裂的预防措施
针对42CrMo 淬火开裂的产生原因,可以从以下几个方面进行预防:
1.严格控制淬火温度,避免过高或过低;
2.确保淬火油的质量和数量,避免油中混入水分;
3.合理设计工件结构,避免尖角、截面突变等容易产生应力集中的部位;
4.对原材料进行充分的热处理,减少原始裂纹。
四、总结
42CrMo 淬火开裂是一个严重影响钢材性能和使用寿命的问题。
TP347厚壁不锈钢管道热处理及裂纹预防措施

TP347厚壁不锈钢管道热处理及裂纹预防措施TP347不锈钢管是一种具有耐高温性能的不锈钢管,常用于化工、石化、石油和电力等领域的管道系统。
在使用过程中,由于管道的厚壁特性和工作环境的复杂性,需要进行热处理和裂纹预防措施,以确保管道的安全可靠运行。
本文将介绍TP347厚壁不锈钢管道的热处理工艺和裂纹预防措施。
1. 固溶处理固溶处理是不锈钢管道热处理的第一步,其目的是溶解不锈钢中的铁素体相和碳化物,提高管材的塑性和加工性能。
TP347不锈钢在固溶处理时应控制温度在1050-1100℃范围内,保持一定时间后迅速冷却,以防止管道产生过度固溶和晶粒长大。
2. 淬火处理淬火处理是为了使固溶后的不锈钢管道获得更高的强度和硬度。
经过固溶处理的TP347不锈钢管道在850-900℃温度范围内进行快速加热,然后迅速冷却,从而形成奥氏体组织,提高管道的抗拉伸强度和硬度。
冷处理是通过冷却不锈钢管道的表面,以增强其表面硬度和耐磨性。
TP347不锈钢管道在冷处理过程中,可以采用液氮或空气冷却的方式,使表面形成马氏体组织,提高管道的耐磨性和抗腐蚀性能。
1. 控制热处理过程在TP347不锈钢管道的热处理过程中,需要严格控制加热温度、保温时间和冷却速度,以避免热处理过程中产生过度固溶或快速冷却而引起的热裂纹。
还需要对管道进行预热和后热处理,以缓解热应力和提高管道的抗裂性能。
2. 选择合适的焊接材料和工艺TP347不锈钢管道在焊接过程中容易产生焊接裂纹,因此需要选择合适的焊接材料和工艺。
可以采用低氢焊接材料、预热焊接和控制焊接层减氢处理等措施,避免焊接过程中产生裂纹。
3. 加强检测和监控在TP347不锈钢管道的制造和使用过程中,需要加强对管道的检测和监控,及时发现管道表面和内部的裂纹,采取相应的修复和防护措施。
可以采用无损检测、压力测试和振动检测等手段,确保管道的完整性和安全性。
4. 优化设计和选材在工程设计阶段,需要根据不同的工作条件和环境要求,优化TP347不锈钢管道的设计和选材,选择合适的管道壁厚、材质和连接方式,减少管道的应力集中和热应力,降低管道的裂纹风险。
淬火处理常见裂纹类型及预防措施
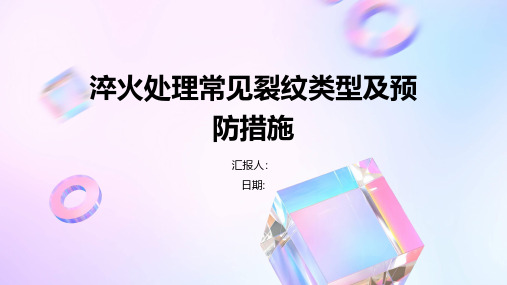
淬火处理常见裂纹类型及预防措施汇报人:日期:•淬火处理概述•淬火处理常见裂纹类型•淬火处理裂纹的预防措施目录•淬火处理的质量控制•淬火处理技术的发展趋势01淬火处理概述0102淬火处理的目的和原理淬火处理的原理是将金属材料加热到一定温度后迅速冷却,通过快速冷却使金属内部结构发生改变,从而实现性能的提升。
淬火处理的目的是提高金属材料的强度、硬度、耐磨性和韧性等性能。
将金属材料加热到一定温度。
保温一定时间,使金属内部结构调整均匀。
迅速冷却,使金属内部结构发生改变。
回火处理,进一步稳定金属内部结构,提高性能。
01020304淬火处理的基本步骤02淬火处理常见裂纹类型应力裂纹是在淬火过程中,由于工件内部温度不均匀,导致局部区域产生拉应力而产生的裂纹。
定义淬火过程中,工件内部温度变化大,导致内应力集中,尤其是在工件形状复杂或截面尺寸变化剧烈时,更容易产生应力裂纹。
原因采用缓慢淬火工艺,减小工件内外温差,降低淬火应力;合理设计工件结构,避免截面尺寸变化剧烈。
预防措施原因淬火后,工件内部仍存在一定的残余应力,当这些应力超过材料的屈服强度时,就会产生延迟裂纹。
定义延迟裂纹是淬火后,在工件冷却过程中,由于工件内部存在淬火应力,随着时间的推移,应力逐渐释放而产生的裂纹。
预防措施优化淬火工艺,降低淬火应力;淬火后进行回火处理,进一步释放内应力;采用喷丸、碾压等表面强化处理工艺,提高工件表面强度和抗疲劳性能。
淬火裂纹是由于淬火过程中,工件内部或表面局部区域温度过高或过低,导致相变不均匀,产生裂纹或开裂现象。
定义淬火过程中,工件内部或表面局部温度过高或过低,导致相变不均匀,产生淬火裂纹;淬火介质选择不当或冷却条件不良,也会引起淬火裂纹。
原因合理选择淬火介质和冷却条件;采用预冷、分级淬火等工艺措施,减小温度变化梯度;优化淬火工艺参数,避免出现过热、过冷现象。
预防措施淬火裂纹03淬火处理裂纹的预防措施预冷处理在淬火前进行预冷处理,可以减少工件在淬火过程中的温度变化,从而降低热应力。
钢的淬火裂缝产生原因及预防措施

工件淬火冷却时,如其瞬时内应力超过该时钢材的断裂强度,则将发生淬火裂缝。
因此产生淬火裂缝的主要原因是淬火过程中所产生的淬火应力过大。
若工件内存在着非金属夹杂物,碳化物偏析或其他割离金属的粗大第二相,以及由于各种原因存在于工件中的微小裂缝,则这些地方,钢材强度减弱。
当淬火应力过大时,也将由此而引起淬火裂缝。
在实际的生产中,往往会根据淬火裂缝特征来判断其产生的原因,从而采取措施预防其发生。
1、纵向裂缝沿着工件轴线方向由表面裂向心部的深度较大的裂缝,它往往在钢件完全淬透情况下发生。
从纵向裂纹方向看,恰好应力是在切向拉应力方向,而又常见于完全淬透情况下。
因此,纵向裂纹是因淬火时组织应力过大,使最大切向拉应力大于该时材料断裂抗力而发生。
纵向裂缝也可能是由于钢材沿轧制方向有严重带状夹杂物所致。
该带状夹杂物所在处,犹如既存裂缝,在淬火切向拉应力作用下,促进裂缝发展而成为宏观的纵向裂缝。
这时如果把钢材沿纵向截取试样,分析其夹杂物,常可发现有带状夹杂物存在。
纵向裂缝也可能由于淬火前既存裂缝在淬火时切向拉应力作用下扩展而成,这时如果垂直轴线方向截取金相试样观察附近情况,可以发现裂缝表面有氧化皮,裂缝两侧有脱碳现象。
2、横向裂缝和弧形裂缝横向裂缝常发生于大型轴类零件上,如轧辊、汽轮机转子或其他轴类零件。
其特征是垂直于轴向方向,由内往外断裂,往往在未淬透情况下形成,属于热应力所引起。
大锻件往往存在着气孔、夹杂物、锻造裂缝和白点等冶金缺陷,这些缺陷作为断裂的起点,在轴向拉应力作用下断裂。
3、表面裂缝这是一种分布在工件表面的深度较小的裂纹,裂纹分布方向与工件形状无关,但与裂纹深度有关。
当工件表面由于某种原因呈现拉应力状态,且表面材料的塑性又很小,在拉应力作用下不能发生塑性变形时就出现这种裂纹。
例如表面脱碳工件,淬火时表层的马氏体因含碳量低,其比体积比与其相邻的内层马氏体的小,因而脱碳的表面层呈现拉应力。
当拉应力值达到或超过钢的破断抗力时,则在脱碳层形成表面裂纹。
42crmo淬火开裂危险尺寸

42crmo淬火开裂危险尺寸
摘要:
1.42CrMo 钢材概述
2.42CrMo 淬火开裂的原因
3.42CrMo 淬火开裂的预防措施
4.结论
正文:
一、42CrMo 钢材概述
42CrMo 是一种合金结构钢,具有较高的强度、韧性和耐磨性,广泛应用于各种机械零件的制造。
在42CrMo 的加工过程中,淬火是提高其硬度和耐磨性的重要环节。
然而,42CrMo 在淬火过程中可能会出现开裂现象,给生产带来安全隐患。
二、42CrMo 淬火开裂的原因
1.原始材料原因:原材料中可能存在裂纹、夹杂物等缺陷,在淬火过程中这些缺陷会扩展,导致开裂。
2.淬火温度和冷却速度原因:如果淬火温度过高或冷却速度过快,会导致钢材内部应力增大,超过钢材的抗拉强度,从而产生开裂。
3.淬火介质原因:淬火介质的性能和温度对钢材的淬火效果有重要影响。
如果淬火介质的性能不佳或温度不稳定,可能导致淬火效果不理想,进而引发开裂。
4.组织结构原因:在淬火过程中,钢材的组织结构会发生变化。
如果组织
结构过于粗大或不均匀,可能导致开裂。
三、42CrMo 淬火开裂的预防措施
1.选用高质量的原材料,避免使用有缺陷的钢材。
2.合理控制淬火温度和冷却速度,避免过高的温度和过快的冷却速度。
3.选择合适的淬火介质,并确保其性能和温度稳定。
4.通过调整热处理工艺,优化钢材的组织结构,降低开裂风险。
5.对淬火后的零件进行回火处理,以消除内部应力,提高韧性。
减少淬火变形和防止淬火开裂的措施
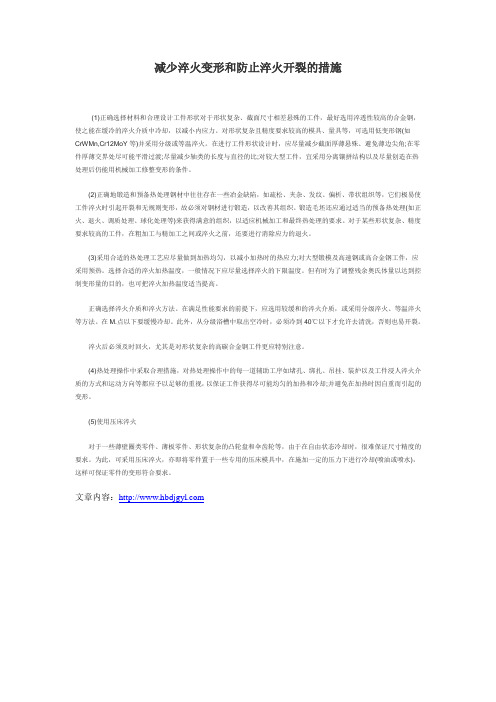
减少淬火变形和防止淬火开裂的措施(1)正确选择材料和合理设计工件形状对于形状复杂、截面尺寸相差悬殊的工件,最好选用淬透性较高的合金钢,使之能在缓冷的淬火介质中冷却,以减小内应力。
对形状复杂且精度要求较高的模具、量具等,可选用低变形钢(如CrWMn,Cr12MoY等)并采用分级或等温淬火。
在进行工件形状设计时,应尽量减少截面厚薄悬殊、避免薄边尖角;在零件厚薄交界处尽可能平滑过渡;尽量减少轴类的长度与直径的比;对较大型工件,宜采用分离镶拼结构以及尽量创造在热处理后仍能用机械加工修整变形的条件。
(2)正确地锻造和预备热处理钢材中往往存在一些冶金缺陷,如疏松、夹杂、发纹、偏析、带状组织等,它们极易使工件淬火时引起开裂和无规则变形,故必须对钢材进行锻造,以改善其组织。
锻造毛坯还应通过适当的预备热处理(如正火、退火、调质处理、球化处理等)来获得满意的组织,以适应机械加工和最终热处理的要求。
对于某些形状复杂、精度要求较高的工件,在粗加工与精加工之间或淬火之前,还要进行消除应力的退火。
(3)采用合适的热处理工艺应尽量做到加热均匀,以减小加热时的热应力;对大型锻模及高速钢或高合金钢工件,应采用预热。
选择合适的淬火加热温度,一般情况下应尽量选择淬火的下限温度。
但有时为了调整残余奥氏体量以达到控制变形量的目的,也可把淬火加热温度适当提高。
正确选择淬火介质和淬火方法。
在满足性能要求的前提下,应选用较缓和的淬火介质,或采用分级淬火、等温淬火等方法。
在M.点以下要缓慢冷却。
此外,从分级浴槽中取出空冷时,必须冷到40℃以下才允许去清洗,否则也易开裂。
淬火后必须及时回火,尤其是对形状复杂的高碳合金钢工件更应特别注意。
(4)热处理操作中采取合理措施,对热处理操作中的每一道辅助工序如堵孔、绑扎、吊挂、装炉以及工件浸人淬火介质的方式和运动方向等都应予以足够的重视,以保证工件获得尽可能均匀的加热和冷却;并避免在加热时因自重而引起的变形。
淬火时出现裂纹的原因及解决方法
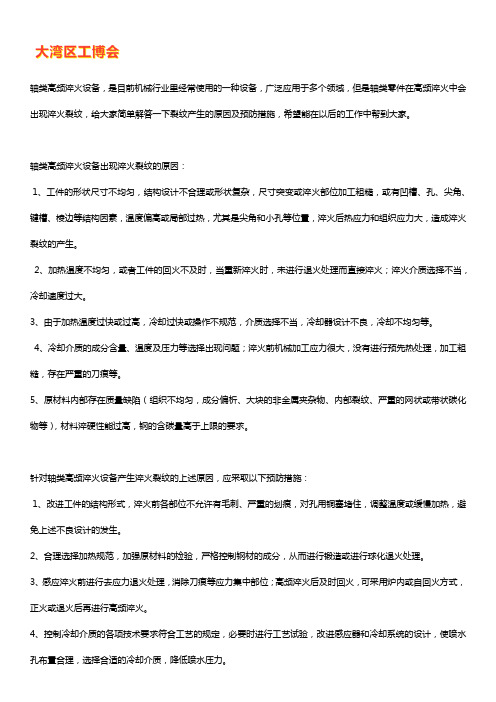
轴类高频淬火设备,是目前机械行业里经常使用的一种设备,广泛应用于多个领域,但是轴类零件在高频淬火中会出现淬火裂纹,给大家简单解答一下裂纹产生的原因及预防措施,希望能在以后的工作中帮到大家。
轴类高频淬火设备出现淬火裂纹的原因:1、工件的形状尺寸不均匀,结构设计不合理或形状复杂,尺寸突变或淬火部位加工粗糙,或有凹槽、孔、尖角、键槽、棱边等结构因素,温度偏高或局部过热,尤其是尖角和小孔等位置,淬火后热应力和组织应力大,造成淬火裂纹的产生。
2、加热温度不均匀,或者工件的回火不及时,当重新淬火时,未进行退火处理而直接淬火;淬火介质选择不当,冷却速度过大。
3、由于加热温度过快或过高,冷却过快或操作不规范,介质选择不当,冷却器设计不良,冷却不均匀等。
4、冷却介质的成分含量、温度及压力等选择出现问题;淬火前机械加工应力很大,没有进行预先热处理,加工粗糙,存在严重的刀痕等。
5、原材料内部存在质量缺陷(组织不均匀,成分偏析、大块的非金属夹杂物、内部裂纹、严重的网状或带状碳化物等),材料淬硬性能过高,钢的含碳量高于上限的要求。
针对轴类高频淬火设备产生淬火裂纹的上述原因,应采取以下预防措施:1、改进工件的结构形式,淬火前各部位不允许有毛刺、严重的划痕,对孔用铜塞堵住,调整温度或缓慢加热,避免上述不良设计的发生。
2、合理选择加热规范,加强原材料的检验,严格控制钢材的成分,从而进行锻造或进行球化退火处理。
3、感应淬火前进行去应力退火处理,消除刀痕等应力集中部位;高频淬火后及时回火,可采用炉内或自回火方式,正火或退火后再进行高频淬火。
4、控制冷却介质的各项技术要求符合工艺的规定,必要时进行工艺试验,改进感应器和冷却系统的设计,使喷水孔布置合理,选择合适的冷却介质,降低喷水压力。
- 1、下载文档前请自行甄别文档内容的完整性,平台不提供额外的编辑、内容补充、找答案等附加服务。
- 2、"仅部分预览"的文档,不可在线预览部分如存在完整性等问题,可反馈申请退款(可完整预览的文档不适用该条件!)。
- 3、如文档侵犯您的权益,请联系客服反馈,我们会尽快为您处理(人工客服工作时间:9:00-18:30)。
热处理淬火开裂及预防
在工件热处理过程中,淬火开裂是一种常见的现象,它对工件的机械性能、使用寿命等有重大影响,加强对热处理淬火开裂问题的讨论和预防,对公司企业产品质量的提高及经济效益等有重大意义。
一、淬火裂纹
(1)淬火裂纹是热处理应力超过材料的锻裂强度时引起的开裂现象。
(2)裂纹现象 裂纹呈断续的串联分布,断口有淬火油或盐水的痕迹,无氧化色,裂纹两侧也无脱碳现象。
二、淬火开裂的原因
1、由人为因素、淬火工艺不当等因素造成的。
(1)材料管理混乱 误把高碳钢或高碳高合金钢当做低、中碳钢使用,采用水淬,或者淬火液选择不当;有的淬火油中混入水,使冷却速度
不均匀等。
(2)淬火加热温度过高,或者在高温下保温时间过长,引起晶粒粗化,组织粗大,晶界弱化,如过热组织,就大大降低了钢的力学性能,使钢
的脆断强度降低,很容易产生淬火开裂。
(3)冷却不当 在Ms温度以下快冷,因组织应力大引起开裂。
如水-油双介质淬火。
在水中停留时间长,淬火油中含有过多水份。
(4)未淬透工件心部硬度为36~45HRC时,在淬硬层中和非淬硬层交界处易形成淬火裂纹。
(5)重复淬火前未经中间退火,过热倾向大,前项淬火的应力未能完全消
除,以及多次加热引起表面脱碳,都会促使淬火开裂。
(6)大截面高合金钢工件,淬火加热时未经预热或加热速度过快,加热时热应力和组织应力增大,引起开裂。
(7)高速钢、高铬钢分级淬火,工件工件未冷至室温,急于清洗(Ms以下快冷)引起开裂。
(8)深冷处理因急冷急热形成的热应力和组织应力都比较大,且低温时材料的脆断强度低,易产生淬火开裂。
(9)淬火后未及时回火工件内部的显微裂纹在淬火应力作用下扩展形成宏观裂纹。
(10)淬火后产生应力不平衡,未使工件开裂,但在后来机加工中或者在搬运过程中,受外力过大,造成开裂。
2、内部组织不良原因造成的
(1)严重表面脱碳易形成网状裂纹。
严重脱碳的高碳工具钢工件,脱碳层
马氏体比未脱碳层马氏体体积小,收到拉应力作用易形成网状裂纹。
(2)原始组织不良,如高碳钢球化质量欠佳,其组织是细片状珠光体或点状珠光体,过热倾向大;晶粒粗化,马氏体碳含量高,淬火开裂倾向
大。
(3)原材料显微裂纹,非金属夹杂物,严重碳化物偏析淬开裂倾向大,如非金属夹杂物或严重碳化物沿轧制方向形成带状分布,由于力学性能
的各向异性,其横向性能比纵向性能低30%~50%,在表面最大拉应力作
用下。
常沿非金属夹杂物或碳化物分布方向呈纵向裂纹。
(4)淬透性低的钢,用钳子夹持淬火时,被夹持部位冷却速度慢在非马
氏体组织,钳口位于淬硬层与非淬硬层交界处,其拉应力大,容易开裂。
3、设计工艺不合理等原因造成开裂。
(1)内径较小的深孔工件(如机筒),由于内表面冷却速度较外表面小的多,残余热应力小,所受的残余拉应力较外表面大,外壁较内壁收缩的
快,因此如果加上材料偏析,内壁就容易开裂。
(2)工件的尖角、孔、截面突变及粗加工刀痕等因冷却速度不均,应力集中引起开裂。
(3)具有最危险淬火尺寸的工件易形成淬火裂纹。
工件的全部淬透时有一最危险的的淬火尺寸,其直径(或厚度)是:水淬时约8~15㎜;油
淬时约25~40㎜。
尺寸小于最危险的尺寸时,心部与表面温差小,淬
火应力小,不易开裂。
工件尺寸大于最危险尺寸时,淬火应力虽然大,
但拉应力峰值远离表面,淬火倾向反而减小。
只有中间某一尺寸(最危
险尺寸)的工件,拉应力峰靠近表面,且数值也较大对淬裂最敏感。
4、典型裂纹现象
(1)锻造裂纹在淬火时扩大,在普通炉内淬火加热时,开裂的破断面有
黑色的氧化皮,裂纹两侧有脱碳层。
(2)过烧裂纹。
裂纹多呈网状,晶界有氧化或熔化现象。
三、淬火开裂的防止措施:
(1)原材料应避免显微裂纹,及严重的非金属夹杂物和材料组织偏析。
(2)合理选择钢材,形状复杂容易开裂的工件,应选择淬透性高的合金钢制造,以便采用冷却速度缓慢的的淬火介质,减少淬火应力。
(3)改进工件结构,截面力求均匀,不同截面处有圆角过渡,尽量减
少不通孔、尖角、避免应力集中引起开裂。
(4)正确预先热处理,避免正火、退火组织缺陷(魏氏组织等)。
(5)正确选择加热参数。
减少因加热温度过高、加热速度过快等原因
引起的开裂。
(6)正确的选择淬火介质和淬火工艺(方法)。
(7)合理的安排热处理工艺,尽量减少截面突变等容易引起冷却速度不 均匀,应力增大的开裂现象。
(8)对工件容易开裂的部位,如尖角、薄壁、孔等进行局部包扎。
1、(9)易开裂的工件淬火后应及时回火或带温回火纵向裂纹亦称轴向裂纹,
是典型的组织应力(切向应力)引发的裂纹,由表面向内开裂,裂纹深而长。
常发生与脆透的工件。
钢中有严重的带状碳化物偏析或沿纵向排列的非金属夹杂物等缺陷会增大形成纵向裂纹的敏感性。
2、横向裂纹或弧状裂纹,裂纹经常发生于工件尖角处。
未淬透的高碳钢件或渗碳
件的过渡区易产生拉应力峰值,此类裂纹常萌生于一定深度的表层或工件内部。
淬火件上有软点时,也易形成细小的弧性形裂纹。
3、内孔纵向裂纹钢的淬透足够大时内孔表面的内应力以组织应力为主,切向应
力较大,易在内孔壁上形成纵向分布的裂纹,从端面看呈放射状。
4、截面薄厚悬殊引起的淬火裂纹冷却时在薄厚相差悬殊的部位马氏体相变的
时间差很大,形成很大的组织应力,以至产生裂纹。
例如小件头部毛坯裂纹。
5、应力集中引起裂纹钢件上有尖角、缺口等存在的情况下,易在淬火时造成
应力集中而产生裂纹,尤其在应力集中和截面急剧变化的共同作用下淬裂危险更大。
6、网状裂纹这种裂纹具有任意方向性而与工件形状无关,网状裂纹的深度一
般在0.01~0.15范围内,是一种表现裂纹,高碳工具钢和合金工具钢表面脱碳后淬火医形成网状裂纹。
7、原材料缺陷引起的淬火裂纹原材料中的夹杂、网状碳化物、塑性成型过程
中的表面折叠、加热时过热组织都可能成为裂纹源,在淬火时会暴露出来或进一步扩展。
解决此类裂纹,应从控制淬火前的原材料质量着手。