基于有限元法的汽车构件疲劳寿命分析
有限元法进行疲劳分析

有限元法进行疲劳分析1一、有限元法疲劳分析的基本思路用有限元法进行疲劳分析,其基本思路是:首先进行静或动强度分析,然后进入到后处理器取出相关的应力应变结果,在后处理器中再定义载荷事件,循环材料特性,接着根据所需要的疲劳准则对每一个载荷事件进行寿命计算,最后根据累计损伤理论判断是否开始破坏。
由于结构受力状态往往是一复杂的应力状态,而在实验中测得的结构材料S-N曲线又常是在简单应力状态下获得的,因此常用最小能量屈服准则或其它等效准则,将所研究的疲劳点上的复杂应力用一个等效应力替代。
对有限元法而言,这一过程很容易实现。
等效替代以后,即可参照原始材料的S-N曲线进行疲劳寿命评估。
上述方法称之为应力-寿命法或S-N法,该方法不严格区分裂纹产生和裂纹扩展,而是给出结构发生突然失效前的全寿命估计。
当然,还可以采用更加现代化的局部应变法或初始裂纹法。
因篇幅所限,因此仅讨论S-N法,且针对车辆结构疲劳分析。
2二、疲劳分析由于车辆结构的零部件属于低应力、高循环疲劳,故常使用Stress life准则,并使用修正Goodman图,此时,S-N曲线的经验公式修正为:计算中需要的材料参数包括:弹性模量、疲劳强度系数、疲劳强度指数、强度极限。
其具体的分析过程是:1.建立物理模型(Physical Model)对于疲劳分析来说,物理模型即包含结点、单元、物理特性和材料特性的有限元模型。
2.建立数学模型(Mathematical Model)数学模型也就是使用物理模型计算应力或应变。
求解后,可从后处理器中获取相关的应力或应变。
3.载荷工况(Loading Conditions)对于静态疲劳分析来说,可以用建立载荷函数的方式施加载荷。
4.定义事件(Events)在进行疲劳评估之前,必须先定义事件。
它由物理模型、数学模型、载荷工况组成,如图1-1所示。
5.评估(Evaluation)一般来说,我们可进行下列估算:·事件损伤(Event Damage)·事件损伤方向(Event Damage Direction)·损伤累积(Accumulated Damage)·事件寿命估算(Event Life Estimate)6.后处理(Post Processing)疲劳分析的后处理与静力学的后处理完全一致,此处不再重复。
基于多体动力学和有限元法的车体结构疲劳寿命仿真

摘
要 : 出 一 种 多体 动力 学 仿 真 和 有 限 元 法 相 互 结 合 进 行 结 构 疲 劳 寿命 预 测 的方 法 , 以 机 车 车 体 结 构 为 例 提 并
பைடு நூலகம்
进 行 了疲 劳寿 命 计 算 。利 用 SMP K 的 多体 仿 真 技 术 获 得 车 体 结 构 的 动 载 荷 历 程 ; ANS I AC 在 YS中 利 用 准 静 态 应 力 / 变 分 析 法计 算 结 构 危 险节 点 应 力 影 响 因 子 ; 据 模 态 分 析技 术 确 定 车 体 结 构 固有 频 率 和 模态 振 型 以及 危 应 根 险 点 位 置 。最 后 , 于动 应 力 历 程 以及 P | ge- n r 基 a rnMie 损伤 理 论 , 用 F - A G mi 利 EF TI UE软 件 的 基 于 应 力 的 结构 安
o u tb d n m i s a d FEM n M li o y Dy a c n
MI AO ig r n ZHANG e— u , XI B n —o g, W i a h AO h u n , J N n —h n HE Ja — ig S o — e I Di g c a g, in qn
基于多体动力学和有限元法的机车车体结构疲劳仿真研究

基于多体动力学和有限元法的机车车体结构疲劳仿真研究一、概述本文主要研究机车车体结构在疲劳寿命方面的仿真,采用多体动力学和有限元法相结合的方法。
由于机车车体结构相对复杂且现场结构耐久性试验费用昂贵,目前国内外对机车车辆车体结构在动载作用下的结构疲劳强度和动应力分析方法涉及相对较少。
实际服役的机车车体结构承受的主要是随机的动载荷,因此直接将静强度分析结果应用于车体结构的疲劳强度评估会产生严重问题。
随着列车运营速度的不断提高,生产安全、可靠、轻量化的车体结构已成为现代机车车辆工业的主要发展趋势,因此机车车体结构疲劳寿命仿真研究成为一项迫切的任务。
本文基于相关领域结构疲劳研究成果,吸取文献中的最新算法,提出了一种利用多体动力学仿真和有限元分析相结合的方法对车体结构的疲劳寿命进行仿真,并进行了较为系统的研究。
研究范围主要集中在机车的多体动力学仿真、车体结构有限元分析和结构疲劳寿命预测上。
具体研究过程主要包括:使用时频复现技术获得多体动力学仿真的轨道随机时域激励利用SIMPACK对机车整车系统进行刚柔体混合建模与仿真(分别考虑车体为刚性和柔性)利用ANSYS计算车体结构的应力(包括模态分析、子结构分析等)结合材料SN曲线和疲劳损伤累积理论进行疲劳寿命预测。
通过这些研究,旨在深入了解机车车体结构的抗疲劳特性,为生产更安全、可靠的车体结构提供理论支持。
1. 研究背景和意义随着高速铁路和重载铁路的迅速发展,机车车体的安全性和可靠性要求日益提高。
疲劳破坏作为机车车体结构的主要失效形式之一,其预防和控制对于确保列车的安全运行至关重要。
传统的机车车体疲劳分析方法主要依赖于试验和经验,不仅周期长、成本高,而且难以覆盖所有可能的工况和边界条件。
开展基于多体动力学和有限元法的机车车体结构疲劳仿真研究具有重要的现实意义和工程价值。
多体动力学作为研究多体系统运动规律的有效工具,能够准确模拟机车在复杂工况下的动力学行为,为车体结构提供准确的动态载荷输入。
基于Hypermesh的汽车驱动桥壳有限元分析与疲劳寿命预测
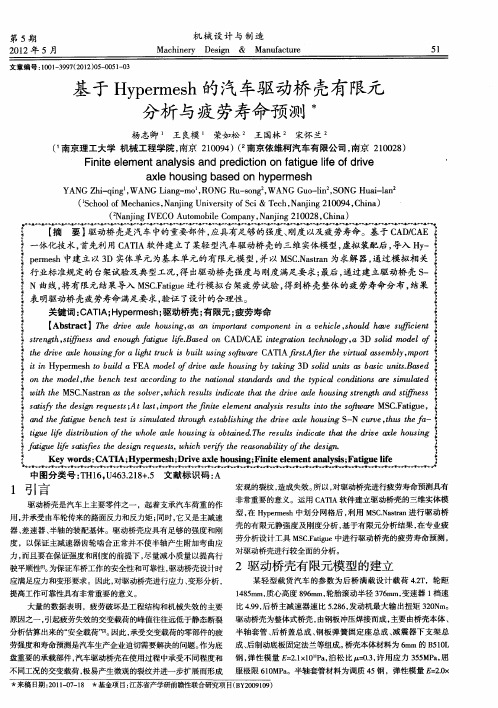
l
}w t eMS .at na esl rw ihrsh n ia a tedieal h uigs egha dsf s i t CN s a t ov , hc eu sidc ett h r e o n rn t in s{ hh r s h e t h v x s t n te
YANG i i g , ANG a -mo , Zh—q n 1W Ling 1RONG —s n 2W ANG o i , ONG a-ln Ru o g , Gu -l S n2 Hu i a
’
( c ol f c aisN nig nv r t o c &T c , aj g2 0 9 , hn ) h o o h nc , aj i s y f i e h N ni 10 4 C ia S Me n U e i S n ( aj gI E O A tm bl C m ay N nig2 0 2 , hn ) ni C uo o i o p n , aj 10 8 C ia N n V e n
}d —bhtiatgsig vno hr, :{ fte mxh h。h d i—ua tn n tio厂 ud e neu lu ylh一 ataentile。 6ehrah£ Nit。g ihd css u ts t sx s Sdeu gziu s eeo an i e n erh e l u g tQ l r bi e c e s ie 。 l r e u n舭 t b l e e g e es x
}tedi xeh u i o g trc s uluigs taeC TA fsA t evr a asm Z,p a { h r eal o n r l h uki b i n f r A I rt f r h i ul e by m o v s gf a i t t s ow i . et t s
汽车有限元法概述
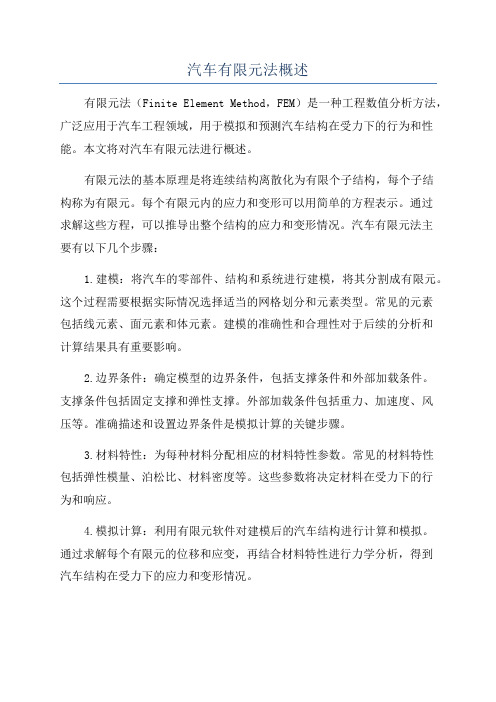
汽车有限元法概述有限元法(Finite Element Method,FEM)是一种工程数值分析方法,广泛应用于汽车工程领域,用于模拟和预测汽车结构在受力下的行为和性能。
本文将对汽车有限元法进行概述。
有限元法的基本原理是将连续结构离散化为有限个子结构,每个子结构称为有限元。
每个有限元内的应力和变形可以用简单的方程表示。
通过求解这些方程,可以推导出整个结构的应力和变形情况。
汽车有限元法主要有以下几个步骤:1.建模:将汽车的零部件、结构和系统进行建模,将其分割成有限元。
这个过程需要根据实际情况选择适当的网格划分和元素类型。
常见的元素包括线元素、面元素和体元素。
建模的准确性和合理性对于后续的分析和计算结果具有重要影响。
2.边界条件:确定模型的边界条件,包括支撑条件和外部加载条件。
支撑条件包括固定支撑和弹性支撑。
外部加载条件包括重力、加速度、风压等。
准确描述和设置边界条件是模拟计算的关键步骤。
3.材料特性:为每种材料分配相应的材料特性参数。
常见的材料特性包括弹性模量、泊松比、材料密度等。
这些参数将决定材料在受力下的行为和响应。
4.模拟计算:利用有限元软件对建模后的汽车结构进行计算和模拟。
通过求解每个有限元的位移和应变,再结合材料特性进行力学分析,得到汽车结构在受力下的应力和变形情况。
5.结果评估:根据计算得到的应力和变形结果,对汽车结构的强度、刚度、耐久性等性能进行评估和分析。
如果发现问题或不合理现象,可以进行模型修正和参数优化,以提高结构的性能。
在汽车工程领域,有限元法主要应用于以下几个方面:1.结构强度分析:通过有限元法,可以对汽车结构的强度进行评估和分析。
例如,分析车身在碰撞时的变形情况,以及主要部件在受力下的应力情况。
2.动态响应分析:有限元法可以模拟汽车在动力加载下的振动和动态响应情况。
例如,模拟车辆在行驶过程中的悬挂系统振动,以及发动机振动对车身的影响。
3.疲劳寿命评估:通过有限元法,可以分析汽车结构在复杂工况下的疲劳寿命。
FEMFAT疲劳分析教程

FEMFAT疲劳分析教程
FEMFAT(有限元疲劳分析工具)是一种用于预测部件疲劳寿命和性能的软件工具。
它基于有限元方法,可以对结构进行疲劳分析、寿命预测和结构优化。
本教程将介绍FEMFAT软件的基本使用方法和疲劳分析的基本原理。
第一部分:FEMFAT软件介绍
1.FEMFAT软件的基本功能和应用领域;
2.FEMFAT软件的主要特点和优势;
3.FEMFAT软件的安装和设置。
第二部分:建立有限元模型
1.导入CAD模型到FEMFAT软件;
2.确定模型的边界条件和加载条件;
3.定义材料性能参数。
第三部分:疲劳加载和分析
1.定义疲劳分析的加载条件;
2.进行疲劳分析,包括应力分析和应变分析;
3.疲劳寿命预测方法和理论。
第四部分:结果分析和优化设计
1.分析疲劳分析结果,包括寿命预测和疲劳热图;
2.根据结果进行优化设计,改进结构的疲劳性能;
3.结果验证和优化方案的效果评估。
第五部分:案例分析
1.疲劳分析实例,如汽车发动机支架的疲劳分析;
2.案例的建模、加载条件和分析过程;
3.案例结果分析和优化设计。
第六部分:注意事项和常见问题
1.使用FEMFAT软件时的注意事项和使用技巧;
2.常见问题解答。
总结:FEMFAT软件是一种强大的疲劳分析工具,可以用于预测结构部件的疲劳寿命和性能。
通过本教程,您将学会使用FEMFAT软件进行疲劳分析,并能够根据分析结果进行结构的优化设计,提高结构的疲劳寿命和性能。
希望本教程能够帮助您更好地理解和使用FEMFAT软件。
有限元法进行疲劳分析

展望
01
随着计算机技术和数值分析方法的不断发展,有限元法在疲劳分析中 的应用将更加广泛和深入。
02
未来疲劳分析的研究将更加注重实验验证和理论建模的结合,以提高 预测精度和可靠性。
03
针对复杂结构和材料的疲劳性能研究将进一步加强,以适应各种工程 应用的需求。
04
疲劳分析将与优化设计、可靠性分析和损伤容限设计等相结合,为产 品的全寿命周期管理提供支持。
有限元法进行疲劳分析
目录
• 引言 • 有限元法基础 • 疲劳分析基础 • 基于有限元法的疲劳分析 • 有限元法进行疲劳分析的案例 • 结论与展望
01 引言
疲劳分析的重要性
01
疲劳分析是产品寿命预测的关键 环节,有助于提前发现潜在的疲 劳断裂风险,避免产品在服役过 程中发生意外断裂。
02
通过疲劳分析,可以优化产品设 计,提高产品的可靠性和安全性 ,降低产品全寿命周期成本。
02 有限元法基础
有限元法简介
有限元法是一种数值分析方法, 用于解决各种复杂的工程问题, 如结构分析、热传导、流体动力
学等。
它通过将连续的物理系统离散化 为有限个小的单元,并对这些单 元进行分析,从而实现对整个系
统的近似求解。
有限元法广泛应用于工程设计、 产品开发和科学研究等领域。
有限元法的基本原理
结构应力分析
通过有限元法计算结构的应力分布。
疲劳裂纹扩展模拟
引入裂纹扩展模型,模拟裂纹在结构中的扩 展过程。
应力集中区域识别
找出结构中的应力集中区域,这些区域往往 是疲劳裂纹萌生的地方。
结构疲劳寿命评估
结合材料的疲劳性能参数和裂纹扩展规律, 评估结构的疲劳寿命。
05 有限元法进行疲劳分析的 案例
基于虚拟迭代及有限元理论的某中型货车驾驶室疲劳寿命研究

0引言机械零件大多数的破坏是由疲劳引起的,根据疲劳损伤机理进行零部件疲劳寿命的分析预测是工程师们面临的一项重要课题。
目前机械零件疲劳寿命分析预测方法主要有名义应力法、应力场强法、临界距离法等。
崔泗鹏等[1]在进行振动载荷下连接件疲劳寿命分析计算时使用了名义应力法,并综合考虑连接件孔边的应力均方根集中程度、孔表面状况和填充系数的影响。
该方法在疲劳寿命计算中用到的关键参数缺口系数为估算值,并且孔的填充系数为经验值,而孔的变化对填充系数影响较大。
李玉春等[2]针对缺口件运用应力场强法进行构件的多轴疲劳下的寿命预测,综合考虑了缺口效应、尺寸效应、不同加载方式及多轴效应的影响。
该方法考虑影响因素较多,在进行计算时所需参数较多,计算复杂。
辛朋朋等[3]针收稿日期:2017-06-19基于虚拟迭代及有限元理论的某中型货车驾驶室疲劳寿命研究刘俊1刘亚军1张少辉1杨建森2董强强21.合肥工业大学汽车与交通工程学院,合肥,2300092.中国汽车技术研究中心汽车工程研究院,天津,300300摘要:以某中型货车的驾驶室为研究对象,通过整车典型强化路面试验测量得到驾驶室悬置位置及车架上相应位置的加速度响应信号,并基于K&C 试验台和MTS 试验台分别测量得到驾驶室质心、转动惯量和衬套刚度阻尼等参数。
采用ADAMS 建立驾驶室和车架的刚柔耦合多体动力学模型;采用Fem⁃b 软件使用虚拟迭代的方法计算驾驶室悬置处和翻转机构处的载荷谱;最后运用Miner 线性疲劳累积损伤理论在疲劳仿真软件nCode 中进行疲劳分析。
通过台架试验验证了疲劳仿真的结果,并通过结构尺寸参数的重新设计使驾驶室前围板的疲劳寿命满足了设计要求。
关键词:惯性释放;刚柔耦合多体模型;虚拟迭代;疲劳分析;参数重设计中图分类号:U463.81DOI :10.3969/j.issn.1004⁃132X.2018.13.012开放科学(资源服务)标识码(OSID):Fatigue Analysis of a Medium Truck Cab Based on Virtual Iteration andFinite Element TheoryLIU Jun 1LIU Yajun 1ZHANG Shaohui 1YANG Jiansen 2DONG Qiangqiang 21.Institute of Automobile and Traffic Engineering ,Hefei University of Technology ,Hefei ,2300092.Automotive Engineering Research Institute ,China Automotive Technology and Research Center ,Tianjin ,300300Abstract :Taking the cab of a medium truck as the research object ,the acceleration response signals of the cab mounting positions and the corresponding positions on the frame were obtained through the typical reinforced road tests.The center of mass ,moment of inertia of the cab and stiffness and damping of the bushing were measured based on the K&C test bench and the MTS test rig.The rigid⁃flexible cou⁃pling multi ⁃body dynamics model of the cab and frame was established in ADAMS software.The load spectrums of the cab suspension and flipping mechanisms were calculated by the method of virtual itera⁃tion in b software.Finally ,fatigue analysis was carried out in the fatigue simulation software nCode with the Miner linear ⁃cumulation fatigue damage theory.The results of fatigue simulation were validated by bench tests and the fatigue life of cab front panel was satisfied by redesign of the structural parameters.Key words :inertial release ;rigid ⁃flexible coupledmulti⁃body model ;virtual iteration ;fatigue anal⁃ysis ;parameter redesign··1588对TC4合金缺口试样运用临界距离法进行疲劳寿命的分析预测,指出临界距离法分析结果精度的提高需同时考虑临界距离与疲劳寿命、载荷比以及应力集中系数等因素的相关性。
- 1、下载文档前请自行甄别文档内容的完整性,平台不提供额外的编辑、内容补充、找答案等附加服务。
- 2、"仅部分预览"的文档,不可在线预览部分如存在完整性等问题,可反馈申请退款(可完整预览的文档不适用该条件!)。
- 3、如文档侵犯您的权益,请联系客服反馈,我们会尽快为您处理(人工客服工作时间:9:00-18:30)。
第21卷第2期 2008年4月
机械研究与应用 MECHANICAL RESEARCH&APPUCAlrl0N
Vol 2l No 2
2008硝
AMS计算输出路面载荷谱.DAC文件。
图5载荷时间历程 5.2建立有限元模型
在PATRAN中采用%a6和TetlO单元对其进行 划分,划分完后模型的单元数是9310个,节点数 4656个。划分后的有限元模型如图6所示。
机械研究与应用 MECHANICAL RESEARCH&APPLICATION
第2l卷第2期 2008年4月
在MSC.Fatigue软件中计算得到对应的安全因 子云图和疲劳寿命对数云图如图9、10所示。表1为 危险区疲劳损伤值最大节点的疲劳寿命、对数疲劳寿 命、疲劳损伤和安全系数值。
图10下控制臂对数疲劳寿命云图 表l下控制臂危险区节点的疲劳分析结果
由分析结果可看出,整体上下控制臂的疲劳强度 足够,疲劳寿命均超过了工程上循环lOE6次的要 求;存在疲劳强度薄弱处。但危险区最小安全因子 1.03,安全系数偏小,存在疲劳破坏的隐患。最低疲 劳寿命1.74E6次循环,载荷时间历程50s,则下控制 臂时间寿命I.74E6·50=8。70E7s,共计24167h。若 每天行驶8h,换算后得到寿命约8.3年。因此,该下 控制臂存在应力集中现象,在长期的变化载荷作用下 会产生破坏。由于条件的限制.。无法进行试验对比, 因此本文仿真结果有待试验验证。 7 结语
对于悬架系统,采用额定载荷作用下的单轮跳动 进行仿真。采用B级路面谱模拟路面状态如图4所 示,用C语言编辑路面谱,将.txt的程序文件读人
ADAMS。 .
图4 B级路面谱
图2多体有限元疲劳分析流程图
利用三维造型软件UG和机械系统动力学仿真 软件ADAMS/View,按照ADAMS建模的要求建立该 型轿车悬架的虚拟模型。如图3所示。
万·5方8·数据
悬架的仿真分析是为了对其中的转向节进一步 地有限元分析和疲劳寿命计算,得到的转向节在竖直 方向的受力随仿真时间的变化,经仿真动画计算,得 出转向节上端受力的载荷时间历程,如图5所示。
根据动力学仿真分析的结果,通过确定坐标标记 确定ADAMS输出的构件为刚性构件,即下控制臂。 载荷的作用点为下控制臂球头销连接处,在载荷的作 用点设置坐标标记以获得作用点的载荷值,同时可指 定载荷作用点的节点号(在有限元分析中,MSC系列 软件将自动的匹配运算确定节点号的对应关系),输 出仿真50s时刻下控制臂的载荷历程信息。由AD-
本参数和特性指标得出S—N曲线。如图8所示。
一16h
争_H Data PIot
SR¨:2835 bl:一0”b2:0 E:2ES UTB:64S
图6下控制臂有限元模型
针对水平路面的情况,仅模拟了垂直跳动的工 况。该模型采用下列约束条件:①在与车身连接的 孔和销约束3个方向的移动自由度;②在与悬架的 转向节的配合孔面上约束y方向的位移。 5.3强度计算及结果分析
合方程为:
lgN=口+blgr。
i
,
1
J
其中:6=∑£l眄L1l—叱一—寺—(二∑l—gc鼍rj.—)_(∑—l上啪L)
善(1眄)2一手(∑lgo))
,一1
J。1
.
1
l
1
口=÷∑(1叱)一手∑lg听
式中:盯,为第,级应力水平的应力值;lgJ ̄!『为口,下的 对数平均寿命;2为应力水平级数。
在MSC.Fatigue软件中,可以通过输入材料的基
用MSC系列有限元分析和疲劳软件对下控制臂进行分析,计算了其应力特性和疲劳寿命。
关键词:有限元;疲劳分析;S一Ⅳ疲劳分析
中图分类号:Tilll3.2+2
文献标识码:A
文章编号:1007—4414(2008)02一0057一04
Fatigue life analysis of automobile component based on FEM
本文给出了结构疲劳分析和寿命预测的一些基 本方法,并根据对某轿车下控制臂疲劳分析实例,对 其进行强度分析,确定了下控制臂的薄弱环节。并在 悬架的动力学仿真分析的基础上,进一步利用MSC. Fatigue软件对其作了疲劳寿命模拟计算。进行以上 分析可以得出结论:在对构件的设计中仅考虑静强度 或常规的方法不能满足零件的强度和寿命要求,进行 抗疲劳计算是必要的。‘
第2l卷第2期 2008年4月
机械研究与应用
MECHANICAL RESEARCH&APPLICATl0N
Vol 21 No 2
2008诅
基于有限元法的汽车构件疲劳寿命分析
黄民锋1,江迎春2
(1.合肥车桥有限公司,安徽合肥230009;2.合肥工业大学,安徽合肥230009)
摘要:对汽车构件结构疲劳分析和寿命预测方法即静态疲劳分析方法和总寿命s一Ⅳ预测方法进行了介绍。针对 某种型号轿车的悬架,应用多体动力学软件ADAMS构建了悬架的虚拟样机,进行了动力学仿真分析。并应
and fatigue life of the low control a珊arc calculated.
Key words:finite element;fatigue life analysis;S—N fatigue analysis
1前言 车辆在行驶中零部件受到各种交变载荷,这种交
变载荷一般低于拉伸强度极限,在此载荷反复作用下 会发生裂纹萌生和扩展并导致突然断裂,这种现象称 为疲劳破坏。在技术改进和研究开发中,了解这种破 坏形式对车辆零部件的强度影响具有重要意义。因 此在汽车的研制过程中,需对零部件进行大量的台架 试验和整车耐久性试验,不仅试验费用高、周期长,且 问题大多出现在产品设计完成之后,对设计更改带来 一定难度。通过有限元疲劳分析,可以在产品设计初 期对整车的耐久性进行预测,找到结构的薄弱环节。 提出合理改进方案,还可大幅降低或最终取代部分疲 劳试验¨.2 J。笔者将结合工程实例。对各种疲劳分析 方法对汽车构件的分析及适用范围进行评述。 2有限元疲劳分析方法
采用有限元疲劳分析方法。很重要的步骤是获得 用于疲劳分析的路面载荷时间历程。该数据可用以 下任何一种方法获得¨J:
(1)试验法在路面耐久性试验时测量某固定 位置的载荷。
(2)直接来自路面载荷数据库或经验数据库
收稿日期:2007—12—14 作者简介:黄民锋(1976一),男,安徽安庆人.工程师,研究方向:轿车悬架设计开发。
图3悬架系统的动力学仿真模型
根据目标悬架中零部件间的相对运动关系,定义 零部件的拓扑结构,对零部件重新组合,将没有相对 运动关系的零部件组合为一体,确定重新组合后零件 间的连接关系和连接点的位置,计算或测量重新组合 后的零部件质心位置、质量和转动惯量,确定减振器 的阻尼特性和弹簧的刚度特性,定义主销轴线,输人 车轮的前束角和外倾角。不允许过约束的运动,橡胶 轴承和弹簧属于柔性连接,它们在发生运动干涉的部 件之间产生阻力,阻止迸一步的干涉发生。假定各 铰链处的橡胶轴承在各个方向上的刚度相等,则在相 应的位置施加轴套力。 5.1仿真结果
态疲劳分析方法…。3疲劳寿命S一Ⅳ预测方法
疲劳寿命的估算分为裂纹形成阶段寿命估算和 裂纹扩展阶段寿命估算两部分。常用的疲劳寿命计 算方法包括名义应力寿命法、局部应变寿命法和裂纹 扩展计算法。针对样例的分析,只介绍S—J『\『方法。
名义应力法又称S一Ⅳ方法,强调长疲劳寿命和 耐久性的限制,或假定疲劳失效不会发生时的安全应 力。它以材料或零部件的疲劳寿命曲线为基础,利用 名义应力或局部应力和寿命之间的关系,主要应用在 线性弹性应力的分析中H】。其设计思路是:从材料 的S一Ⅳ曲线出发,再考虑各种影响系数的影响,得 出零件的S—J\,曲线,并根据零构件的S一Ⅳ曲线进 行抗疲劳设计。当使用S一Ⅳ曲线的水平区段—— 疲劳极限进行设计时称为无限疲劳设计;当使用S一 Ⅳ曲线的倾斜部分进行抗疲劳设计时称为名义有限 寿命设计¨J。名义应力法的流程如图l所示。 4路面载荷时间历程的获取
(4)全理论分析方法无需试验,仅通过多体动 力学或虚拟实验场(VPG)仿真技术获取悬架和其它 位置的路面载荷时间历程。
本文实例是建立多体动力学仿真模型获取构件
圈 需要部位的载荷时间历程。
引渊嚣l l簖躺簇
亟匾H藉篙凄董籍
图1定义名义应力法流程
5工程分析实例 采用通过多体动力学仿真软件ADAMS,直接从
系统载荷谱求得结构的动力响应时间历程,采用有限 元法计算出关键结构部件上各关键危险部位的应力, 最后结合材料的基本疲劳性能数据进行结构寿命估 算【5】。系统载荷可以是实际的载荷、位移和加速度 等。多体动力学分析的结果是部件的载荷历程,可加 快结构的疲劳寿命分析,比如对于载荷历程中结构的 无损伤部分就可忽略。多体有限元疲劳分析流程如 图2所示。
万方数据
·57·
Vol 2l No 2
2008硝
机械研究与应用
MECHANICAL RESEARCH&APPLICATION
第2l卷第2期 2008年4月
以汽车企业长期积累的相关车型的路面载荷数据库 或典型零件的经验载荷数据库等作为参考载荷进行 疲劳分析。
(3)半理论分析方法根据部分位置的测量载 荷,通常为轮轴的载荷,利用多体动力学等方法可以 得到其它连接位置的载荷。
Huang Min—fen91.Jiang Ying—chun2
(1.盹似ade Co..删,Hefei Anlud 230(}09.China;2.Hefii universlty oftechnology。Hefei Anhui 230009.China)
the侧c iB∞ method眦intro- Abstract:The fatigue analysis d automobile component which is static state fatigue and S—N fatigue forecast