盒形件冲压成形CAE分析
冲压CAE分析的有限元基础(教育知识)

教书育人
29
使用软件
Dynaform、autoform、pan-stamp
教书育人
30
谢谢!
教书育人
31
教书育人
3
❖ CAE各阶段所用的时间为:40%~45%用于模型的建立和数据输入,50%~55% 用于分析结果的判读和评定,而真正的分析计算时间只占5%左右。针对这种情 况,采用CAD技术来建立CAE的几何模型和物理模型,完成分析数据的输入, 通常称此过程为CAE的前处理。同样,CAE的结果也需要用CAD技术生成形象 的图形输出,如生成位移图、应力、温度、压力分布的等值线图,表示应力、温
制件旋转时以工艺基准点为中心旋转,转角大小及次序最好事先做好记录,制 件在X,Y,Z每个方向上仅限于旋转一次,因此制件最多允许旋转三次,90度或 180度的旋转不计算在内。
教书育人
14
3Hale Waihona Puke 压料面压料是拉延过程中非常重要的功能,坯料就是沿压料面逐渐流入模具型腔的。因 此压料面的设计要有利于材料的流动,保证制件在各个截面上变形均匀(拉延深 度一致)。
虚拟筋和实体筋的对应关系是个难点,要靠做大量的实验对比分析。
教书育人
17
教书育人
18
❖ 有限元方法的基本思想是将结构进行有限元 离散化,用有限个容易分析的单元来表示复 杂的工程结构,各单元之间通过有限元节点 相互连接,根据有限元基本理论建立有限元 总体平衡方程,然后求解。
教书育人
19
有限元分析理论
教书育人
5
冲压CAE分析的内容 产品工程设计阶段对工艺数模、铸造数模进行
可成型性分析。 分析产品的可成型性,是否有冲压缺陷如: ❖ 是否有冲压负角
板料成形性能及CAE分析

板料成形性能及CAE分析文献综述引言随着强度的提高,高强度钢板塑性变差、成形难度增加。
对典型高强度钢板,如DP 钢、TRIP 钢和BH 钢等在汽车上的应用情况进行介绍,介绍了目前处在实验测试阶段的TWIP钢,具有许多优良的性能,只是投入生产中还存在一些尚待解决的问题。
对高强度钢板冲压生产时成形性差、回弹严重,以及冲模受力恶劣等常见问题进行了分析,最后对高强度钢板冲压成形性能研究现状和回弹影响因素进行了总结。
结果表明,高强度钢板成形性随材料、模具和工艺参数变化而波动,所以须综合研究三者的影响规律,从而提高高强度钢板的成形性能。
1 高强度钢板在汽车上的应用情况高强度钢板的拉伸强度一般在350MPa 以上,它不但具有较高的拉伸强度,还有较高的屈服点,具有高的减重潜力、高的碰撞吸收能、高的成形性和低的平面各向异性等优点,在汽车上得到了广泛的应用[1]。
高强度钢板最初主要用于车身的前保险杠和车门抗侧撞梁。
近年来,随着高强度钢板的研制和开发,其成形性、焊接性、疲劳强度和外观质量都有所提高,现在高强度钢板已被广泛用来代替普通钢板制造车身的结构构件和板件[2]。
1. 1 双相钢( DP 钢)DP 钢是由低碳钢或低碳微合金钢经两相区热处理或控轧控冷而得到,其显微组织主要为铁素体和马氏体,马氏体以岛状弥散分布在铁素体机体上,DP 钢的显微组织示意如图1 所示[3]。
软的铁素体赋予DP钢较低的屈强比、较大的延伸率,具有优良的塑性; 而硬的马氏体则赋予其高的强度。
DP 钢的强度主要由硬的马氏体相的比例来决定,其变化范围为5% ~20%,随着马氏体的含量增加,强度线性增加,强度范围为500 ~ 1 200MPa。
目前大量使用的有DP590、DP780,热镀锌合金化DP980 的研发工作正在进行中[4]。
DP 钢具有低屈强比、高加工硬化指数、高烘烤硬化性能、无屈服延伸和室温时效等特点,一般用于需要高强度、高的抗碰撞吸收且也有一定成形要求的汽车零件,如车轮、保险杠、悬挂系统及其加强件等。
文具盒注射成型CAE分析

本 工 作 利 用 M I 件 对 文 具 盒 注 射 成 型 过 P 软
加 工 应 用 研 究 工 作 。 联 系 电 话 :0 0 8 3 2 7 ; — al ( 1 ) 14 3 8 E m i:
程数值模 拟 , 获得合 理 的工 艺参数 。
lej 1@yho1m、1 ed9 5 ao、 1 。 2 2 o 1
图 1 利用 Po 是 r E建 立 的文具 盒 零件 三维 模 / 型, 制件外 形 尺寸为 3 2mm ×2 2mm ×8 3 0 0mm,
由图 3可 以看 出 , 案 A和方 案 B的熔接 痕 方 比较 少 , 方案 C的熔 接 痕 比较 多 , 而 而且 集 中在 制 品的中 间部位 , 这样会 影响制 品 的外 观 , 以方 所 案 C不 合理 。 采用 不 同 的浇注 系统 进行 流 动填 充 分析 , 用 于优化制 品的浇注 系统 。 由图 4可 以看 出 , 案 B 方
维普资讯
第 5期
李 德 军 等 . 具 盒 注 射 成 型 C E分 析 文 A
4 9
一
方案 A
一
方案 B 图 2 浇 口设 计 方 案
F g 2 De i n s h me o h a e i. sg c e ft e g t
l 浇 注 系统 的 优 化
浇 口的位 置 和数 量不仅 影 响流动平 衡 ,还 影 响填充结 束时 的体 积收缩 。分析 浇 口位 置 目的在 于根据零 件结构 找到使流 动达到平 衡 的最佳 浇 口 位置 , 以尽可能减 少制 品缺 陷 , 而获得 质量好 的 从
产 品。
压力、 时间 以及模 具结构 和成型设 备等 ) 因此 , 。 长
参 数 为 : 射 时 间 为 l 4s 注 射 压 力 为 4 - 4 . MP , 压 时间 为 1 . s保 压 压力 为 3 . a 冷 却 水 温 度 2 c, 注 一 , 43 61 a保 — 91 , 32MP , 5q
机械毕业设计872基于CADCAE的桶形件变压边力冲压成形工艺研究

目录1 绪论 (1)1.1 选题背景 (1)1.2 桶形件变压边力冲压成形国内外研究现状 (2)1.2.1 变压边力的加载模式 (2)1.2.2 变压边力的技术的实验研究 (3)1.2.3 变压边力的有限元数值模拟研究 (3)1.3 主要研究目标及内容 (4)1.4 论文的组织结构 (4)2 桶形件冲压成形工艺理论分析 (5)2.1 桶形件冲压过程及特点 (5)2.2 桶形件拉深工艺 (7)2.3 常见桶形件拉深缺陷 (8)2.4 影响桶形件成形的主要因素 (8)3 基于CAD/CAE变压边力分析理论及方法 (10)3.1 基于CAD/CAE变压边力分析 (10)3.2 仿真实验流程图 (11)3.3 仿真模型的建立 (14)3.3.1 模具CAD建模 (14)3.3.2 前处理步骤具体设计 (15)3.3.3 变压边力的加载模式及影响因素 (17)4 变压边力桶形件冲压仿真与分析 (20)4.1 变压边力曲线选择 (20)4.2 后处理分析方法简介 (21)4.3 不同变压边力加载方式下桶形件冲压仿真 (22)4.4 不同变压边力加载方式的冲压性能对比和分析 (31)4.5 小结 (34)结束语 (36)致谢 (37)参考文献 (38)1 绪论1.1 选题背景板料冲压成形作为金属塑性加工的基本方法之一,主要用于加工板料,因此又称为板料冲压。
冲压是在常温下,利用冲压模在冲压设备上对板料或型材施加压力,使其产生塑性变形或分离,从而获得所需形状,尺寸和性能零件的一种压力加工方法。
对于某些非金属材料,也可以采用冲压工艺制造零件。
冲压加工可以提高生产效率高、可以改善材料内部的结构和缺陷、提高零件的机械性能、减轻零件重量更可以提高材料利用率,由于其独特的优势广而被广泛应用于航空航天、汽车、摩托车、电器开关、家电、农用机械、医疗器械等行业,在工业生产中占有不可替代的地位。
近年来,随着板料成形理论的深入研究以及计算机信息技术、控制技术及自动化技术的快速发展,板料冲压技术也得到了前所未有的发展[1]。
盒形件冲压工艺分析及模具设计【毕业作品】

任务书设计题目:盒形件冲压工艺分析及模具设计1.设计的主要任务及目标(1)任务:1)模具装配图及零件图2)设计说明书一本3)电子资料一份(2)目标:以所学专业知识为基础,以实用为目的,通过对盒形件冲压工艺的分析及相关参数的计算,进一步进行模具的总装图及零件的设计,总结出并熟练掌握模具设计的规律和方法。
2.设计的基本要求和内容(1)基本要求1)认真学习相关书籍,查阅中外文资料,制定出合理的设计方案;2)认真做好各环节计算与分析,使零件的工艺分析正确,模具设计合理;3)勤于思考,应用所学的专业知识来解决设计中遇到的问题;4)翻译一篇与本课题相关的英文文献;(2)主要内容1)对盒形件的工艺性进行科学的分析;对相关参数进行准确的计算。
2)通过查阅相关的模具图册,设计出合理的模具装配图及主要零部件图(不少于5张)。
3)探索总结出一套相关的模具设计规律和方法。
3.主要参考文献[1]丁松聚. 冷冲模设计[M]. 北京.机械工业出版社. 2011.6.[2]王孝培. 冲压设计资料[M].北京. 机械工业出版社, 1983.12.[3]编写组. 冲模设计手册[M]. 北京.机械工业出版社, 1992.3[4]王芳.冷冲压模具设计指导书[M].北京.机械工业出版社,1988.104.进度安排1 资料查阅,完成开题报告2013.12.17—2014.03.172 制定工艺方案,制定模具大体结构2014.03.18—2014.03.253 绘制总体装配图2014.03.26—2014.04.304 绘制零件图2014.05.01—2014.06.015 撰写毕业设计2014.06.02—2014.06.126 制作答辩PPT,准备毕业设计答辩2014.06.13—2014.06.205.附图零件图如下:材料:1Cr18Ni9Ti厚度:0.8mm盒形件冲压工艺分析及模具设计摘要:模具技术生产的制品具有高精度、高复杂程度、高一致性、高生产效率和低消耗等特点。
盒形件冲压成形CAE分析报告
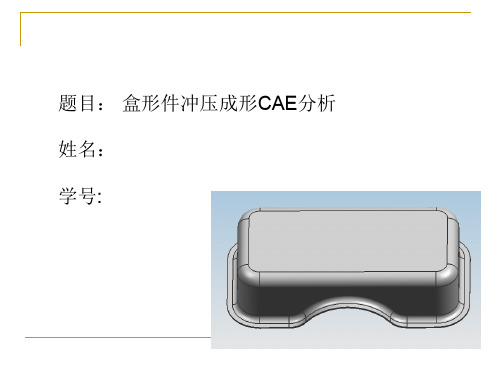
5.1工艺补充面的影响(优化前)
凹模圆角:R=65mm 压边面形状如图 各工艺补充面圆角大小如图
5.1工艺补充面的影响(优化前)
•板料:1400*1300,厚1.5mm •成形条件:
单动: 成形速度5000mm/s, 行程245.10mm 压边力10T
成形极限图
5.1工艺补充面的影响(优化) 优化的工艺补充面
5.3压边力的影响(优化前)
压边力20T
板料的拉深不足和起皱较为严重, 一些区域还存在金属流动较快快 要脱离压边圈。
5.3压边力的影响(优化)
成形极限图
压边力40T
增大压边力之后材料 的拉深不足有所改善, 起皱有所减轻,但是 在侧边孔部出现破裂 的趋势。
5.4坯料形状 的影响(优化前)
1/4板料为410*613
行程245.10mm
压边力10T
4、成形数值模拟(1次)
FLD变化(动画)
4、成形数值模拟(1次)
切面位置
切面变化(动画)
5、成形数值模拟讨论
FLD图
模拟结果中存在的问题: 1 拉深不足 2 起皱
解决上述问题的方法: 1. 改变工艺补充 2. 增加拉伸筋 1. 优化压边力 2. 增加坯料宽度尺寸
二次成形
6、结论
知识回顾 Knowledge Review
导入模型->网格划分->建立有限元模型->定义边 界条件->分析计算->得到模拟结果
有限元模型
4、成形数值模拟条件(1次)
第1次模拟坯料
模拟条件: 软件Dynamform5.6 板料:1226*820,厚度1.5mm 材料:B140H1 成形条件:
板料成形CAE技术与其应用完整

板料成形CAE技术与其应用完整(可以直接使用,可编辑优质资料,欢迎下载)板料成形CAE技术及应用长期以来,困扰广大模具设计人员的主要问题就是较长的模具开发设计周期,特别是对于某些特殊复杂的板料成形零件,甚至制约了整个产品的开发进度,而板料成形CAE技术及分析软件的出现,有效地缩短模具设计周期,大大减少试模时间,帮助企业改进产品质量,降低生产成本,从根本上提高了企业的市场竞争力。
一、前言计算机辅助设计技术以其强大的冲击力,影响和改变着工业的各个方面,甚至影响着社会的各个方面。
它使传统的产品技术、工程技术发生了深刻的变革,极大地提高了产品质量,缩短了从设计到生产的周期,实现了设计的自动化。
板料成形是利用模具对金属板料的冲压加工,获得质量轻、表面光滑、造型美观的冲压件,具有节省材料、效率高和低成本等优点,在汽车、航空、模具等行业中占据着重要地位。
由于板料成形是利用板材的变形得到所需的形状的,长期以来,困扰广大模具设计人员的主要问题就是较长的模具开发设计周期,特别是对于复杂的板料成形零件无法准确预测成形的结果,难以预防缺陷的产生,只能通过经验或类似零件的现有工艺资料,通过不断的试模、修模,才能成功。
某些特殊复杂的板料成形零件甚至制约了整个产品的开发进度。
板料成形CAE技术及分析软件,可以在产品原型设计阶段进行工件坯料形状预示、产品可成形性分析以及工艺方案优化,从而有效地缩短模具设计周期,大大减少试模时间,帮助企业改进产品质量,降低生产成本,从根本上提高企业的市场竞争力。
板料成形CAE技术对传统开发模式的改进作用可以通过图1 和图2进行对比。
图1 传统板料成形模具开发模式图2 CAE 技术模具开发方式通过比较,就可发现板料成形CAE技术的主要优点。
(1)通过对工件的可成形工艺性分析,做出工件是否可制造的早期判断;通过对模具方案和冲压方案的模拟分析,及时调整修改模具结构,减少实际试模次数,缩短开发周期。
(2)通过缺陷预测来制定缺陷预防措施,改进产品设计和模具设计,增强模具结构设计以及冲压方案的可靠性,从而减少生产成本。
CAE技术在汽车覆盖件冲压成形中的应用
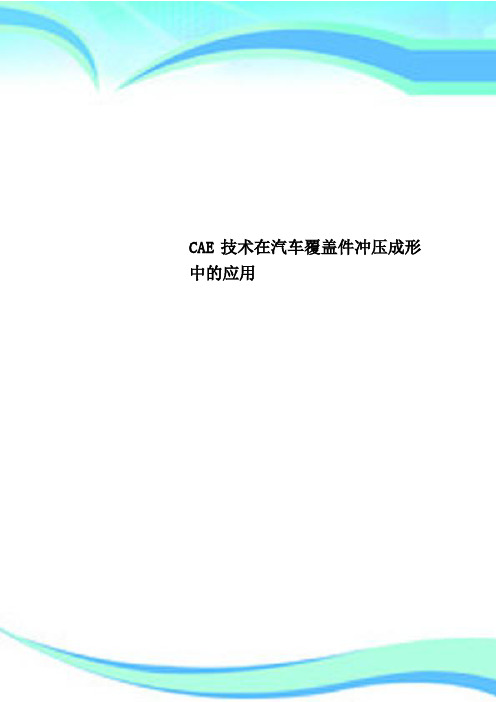
CAE技术在汽车覆盖件冲压成形中的应用————————————————————————————————作者:————————————————————————————————日期:CAE技术在汽车覆盖件冲压成形中的应用2007—1—17 14:13:00 进入论坛摘要:本文简述了CAE技术在汽车覆盖件冲压成形中的应用,通过对拉延工序进行冲压成形模拟分析,提前预知成形缺陷,并采取有效措施,进行工艺参数的调整与优化。
实践证明,分析计算缩短了模具制造周期,减少了模具调试次数,节约了生产成本.关键词:CAE技术;冲压成形;模具调试1 前言汽车覆盖件具有外形尺寸较大,材料比较薄,型面起伏复杂,尺寸精度与表面质量要求较高,在拉伸成形过程中容易出现拉裂、起皱现象。
模具调试过程中需要浪费大量的人力、物力和财力。
近年来随着计算机技术的不断发展,CAE(计算机辅助工程)技术目前已经在各大汽车模具厂广泛用于产品模拟分析、冲压板材成形过程分析。
通过提前对产品可能出现的成形缺陷进行研究,预示汽车覆盖件冲压成形的可行性。
根据理论上的模拟分析结果,提高产品工艺补充设计的合理性,减少模具实际调试次数,近而达到缩短模具制造周期、降低生产调试成本,提高企业生产效能,保证新车型及时投放市场。
本文利用Dynaform分析软件,以公司G项目中的顶盖产品分析为例,介绍CAE技术在汽车覆盖件冲压成形的应用。
2 产品介绍图1所示为我公司最近开发G项目标准短轴距顶盖产品,其材料为SPCC,料厚t=0.9mm,整体来看,具有材料较薄,外形尺寸较大,端部型面极不规则,成形困难,冲压工艺补充以及后续模具设计比较复杂等特点。
图1 顶盖产品数学模型3 CAE分析工作流程CAE分析技术在汽车覆盖件冲压成形应用中的工作流程,见下图2所示。
图2 CAE分析工作流程图4 汽车覆盖件工艺补充设计注意要点(1)选定合适的冲压方向,保证凸模将工件一次拉伸到位,凸模两侧包容角尽可能保持一致,周边进料均匀,尽可能降低拉伸深度,并尽量深度均匀。
- 1、下载文档前请自行甄别文档内容的完整性,平台不提供额外的编辑、内容补充、找答案等附加服务。
- 2、"仅部分预览"的文档,不可在线预览部分如存在完整性等问题,可反馈申请退款(可完整预览的文档不适用该条件!)。
- 3、如文档侵犯您的权益,请联系客服反馈,我们会尽快为您处理(人工客服工作时间:9:00-18:30)。
5.1工艺补充面的影响(优化前)
•板料:1400*1300,厚1.5mm •成形条件: 单动: 成形速度5000mm/s, 行程245.10mm
压边力10T
成形极限图
5.1工艺补充面的影响(优化)
优化的工艺补充面
5.1工艺补充面的影响(优化)
•板料:1400*1300,厚1.5mm •成形条件: 单动: 成形速度5000mm/s, 行程245.10mm 压边力10T
题目: 盒形件冲压成形CAE分析 姓名:
学号:
目录
1、产品介绍 2、工艺分析 3、工艺方案的确定 4、成形数值模拟 5、成形数值模拟讨论
5.1成形方向 5.2压边 5.3拉延筋 5.4坯料
6、结论
1、产品介绍
产品图
产品形状展示(动画)
材料信息
t=1.5
产品图
2、工艺分析
由产品图可知: 需要的工序有 拉深,修边
2、工艺分析
A处: 由于设计已经压边圈的原 因容易起皱 B处:在成型过程中,由于圆 角变形区的影响会是B范围出 背拉破 C处:在成型过程的最后,由 于压边圈与材料接触部分减少 的影响容易起皱
3、工艺方案确定
冲压工艺流程 :
4、成形数值模拟 ————模型
导入模型->网格划分->建立有限元模型->定义边 界条件->分析计算->得到模拟结果
有限元模型
4、成形数值模拟条件(1次)
模拟条件: 软件Dynamform5.6 板料:1226*820,厚度1.5mm 材料:B140H1 成形条件:
单动 成形速度5000mm/s, 行程245.10mm 压边力10T
第1次模拟坯料
4、成形数值模拟(1次)
FLD变化(动画)
4、成形数值模拟(1次)
模拟结果中存在的问题: 1 拉深不足 2 起皱
解决上述问题的方法: 1. 改变工艺补充 2. 增加拉伸筋 1. 优化压边力
FLD图
2. 增加坯料宽度尺寸
5.1工艺补充面的影响(优化前)
凹模圆角:R=65mm 压边面形状如图 各工艺补充面圆角大小如图
成形极限图
5.2拉延筋的影响(优化前)
成形极限图
由于没有采用拉伸筋,零件出现拉深不足现象,由于模具轮廓 不同位置的形状差异,使得各处成形流动阻力也有较大的差异, 在侧边孔部圆角处以及工艺补充部分发生起皱 ,故需在工艺面 上对应位置设置分段拉延筋。
5.2拉延筋的影响(优化)
成形条件: 在离凹模口轮廓如图所 示处设置两条等效拉延 筋作用线,拉延筋力: 300N/mm
单动:
成形速度5000mm/s,
行程245.10mm 压边力10T
均布等效拉延筋设置
5.2拉延筋的影响(优化)
成形条件: 在离凹模口轮廓如图所示处设 置4条等效拉延筋作用线,拉延 筋力:300N/mm 单动: 成形速度5000mm/s, 行程245.10mm 压边力10T
优化的拉延筋:分段设置拉延筋
成形极限图
5.4坯料形状 的影响(优化)
厚度变化
6、结论
压边力:300000N
优化的模面主要尺寸:
二次成形
6、结论
由图可见, 成形过程出 现了拉深不 足和起皱的 情况
成形极限图
5.4坯料形状 的影响(优化)
成形条件:
1/4坯料575*593厚度 1.5mm 单动:
成形速度5000mm/s,
行程245.10mm 压边力10T
优化的坯料形状
5.4坯料形状 的影响(优化)
在明显的增大零件宽 度和缩小长度方向的 板料尺寸后,宽度方 向板料被压紧的效率 增加,从而明显改变 了侧边起皱现象,并 使盒形件底部中间出 现绿色拉伸现象。
5.2拉延筋的影响(优化)
拉伸筋1
拉伸筋2
5.2拉延筋的影响(优化)
通过设置分段的 拉延筋,并考虑 到等效的拉延筋 作用力对进料阻 力的平衡后,毛 坯边界的拉入量 趋于均匀,拉深 不足和起皱现象 有所减轻。
成形极限图
5.3压边力的影响(优化前)
压边力20T
板料的拉深不足和起皱较为严重, 一些区域还存在金属流动较快快 要脱离压边圈。
5.3压边力的影响(优化)
压边力40T
增大压边力之后材料 的拉深不足有所改善, 起皱有所减轻,但是 在侧边孔部出现破裂 的趋势。
成形极限图
5.4坯料形状 的影响(优化前)
1/4板料为410*613
成形条件: 单动 成形速度5000mm/s, 坯料形状 行程245.10mm 压边力10T
5.4坯料形状 的影响(优化前)