风力发电机叶片气动弹性响应分析
风电机组叶片气动弹性与颤振抑制

风电机组叶片气动弹性与颤振抑制风力发电是利用风能驱动发电机组产生电能的一种清洁能源。
风电机组叶片作为直接接触风的部件,其气动弹性和颤振抑制技术一直是风电行业的研究热点。
在风力发电系统中,叶片的气动弹性和颤振抑制技术对提高风电机组的性能和可靠性至关重要。
本文将从叶片气动弹性的基本原理、颤振的危害和抑制方法等方面展开探讨。
一、叶片气动弹性叶片气动弹性是指叶片在风力作用下发生的形变和振动现象。
风力是一种不稳定、非线性的力,而叶片作为受力部件,其振动响应受到风荷载的影响。
叶片在风力作用下会发生弯曲、扭转、挠曲等形变,这些形变会导致叶片的动态特性发生变化,从而影响叶片的运行性能和寿命。
1.1 叶片气动弹性的特点(1)风荷载的不确定性:叶片在运行过程中所受到的风荷载是不断变化的,同时风速、风向、气动系数等因素会对叶片的气动弹性产生影响。
(2)非线性:叶片在风力作用下会发生非线性的振动响应,包括颤振、共振等现象。
(3)多自由度:叶片是一个复杂的多自由度系统,其振动模态较多,受到外界扰动时会产生多种振动模式。
叶片气动弹性会对风电机组的性能和可靠性产生影响,具体表现在以下几个方面:(1)动态响应:叶片的气动弹性会导致叶片的动态特性发生变化,从而影响叶片的动态响应,包括振动幅值、频率、振型等。
(2)疲劳损伤:叶片在风力作用下会发生疲劳损伤,气动弹性会加剧叶片的疲劳破坏,降低叶片的使用寿命。
(3)颤振风险:叶片的气动弹性会增加叶片颤振的风险,一旦发生颤振现象会对风电机组造成严重的损坏。
二、颤振的危害颤振是指叶片在特定工况下受到外部扰动而产生的自激振动现象。
颤振会导致叶片产生剧烈的振动,加速叶片疲劳损伤,甚至导致叶片的破坏。
颤振还会引起风电机组的振动响应,对风电机组的安全性和稳定性产生威胁。
2.1 颤振的成因颤振的产生通常受到以下因素的影响:(1)固有频率:当外部扰动频率接近叶片的固有频率时,会导致颤振的产生。
(2)气动力失稳:当叶片的气动力失稳时,会导致气动弹性失控,引发颤振。
风电机组叶片气动弹性与颤振抑制
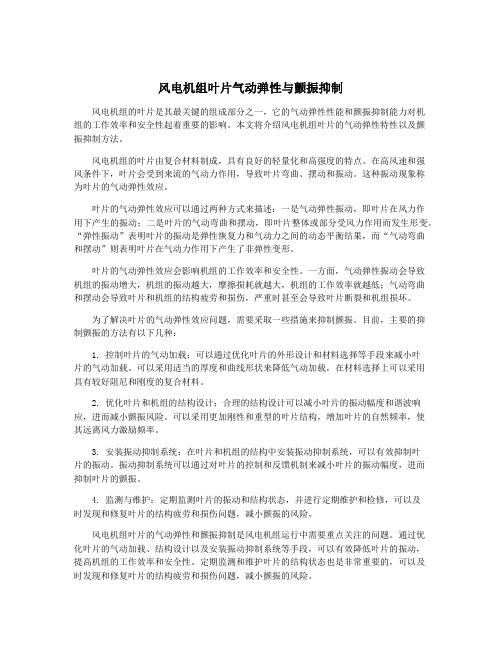
风电机组叶片气动弹性与颤振抑制风电机组的叶片是其最关键的组成部分之一,它的气动弹性性能和颤振抑制能力对机组的工作效率和安全性起着重要的影响。
本文将介绍风电机组叶片的气动弹性特性以及颤振抑制方法。
风电机组的叶片由复合材料制成,具有良好的轻量化和高强度的特点。
在高风速和强风条件下,叶片会受到来流的气动力作用,导致叶片弯曲、摆动和振动。
这种振动现象称为叶片的气动弹性效应。
叶片的气动弹性效应可以通过两种方式来描述:一是气动弹性振动,即叶片在风力作用下产生的振动;二是叶片的气动弯曲和摆动,即叶片整体或部分受风力作用而发生形变。
“弹性振动”表明叶片的振动是弹性恢复力和气动力之间的动态平衡结果,而“气动弯曲和摆动”则表明叶片在气动力作用下产生了非弹性变形。
叶片的气动弹性效应会影响机组的工作效率和安全性。
一方面,气动弹性振动会导致机组的振动增大,机组的振动越大,摩擦损耗就越大,机组的工作效率就越低;气动弯曲和摆动会导致叶片和机组的结构疲劳和损伤,严重时甚至会导致叶片断裂和机组损坏。
为了解决叶片的气动弹性效应问题,需要采取一些措施来抑制颤振。
目前,主要的抑制颤振的方法有以下几种:1. 控制叶片的气动加载:可以通过优化叶片的外形设计和材料选择等手段来减小叶片的气动加载。
可以采用适当的厚度和曲线形状来降低气动加载,在材料选择上可以采用具有较好阻尼和刚度的复合材料。
2. 优化叶片和机组的结构设计:合理的结构设计可以减小叶片的振动幅度和谐波响应,进而减小颤振风险。
可以采用更加刚性和重型的叶片结构,增加叶片的自然频率,使其远离风力激励频率。
3. 安装振动抑制系统:在叶片和机组的结构中安装振动抑制系统,可以有效抑制叶片的振动。
振动抑制系统可以通过对叶片的控制和反馈机制来减小叶片的振动幅度,进而抑制叶片的颤振。
4. 监测与维护:定期监测叶片的振动和结构状态,并进行定期维护和检修,可以及时发现和修复叶片的结构疲劳和损伤问题,减小颤振的风险。
风力机叶片气动弹性稳定性分析

风力机叶片气动弹性稳定性分析随着能源问题的日益严重,利用可再生能源发电技术已越来越受到社会的重视。
风力发电是一种利用风能发电的技术,它能够以较小的环境影响,实现低成本的能源供应。
而风力发电系统的最关键部分就是风力发电机叶片,因此,风力发电机叶片的气动弹性稳定性也成为研究发电机叶片参数设计、挣度计算等的关键内容。
本文旨在对风力发电机叶片的气动弹性稳定模型进行分析,以深入了解叶片的气动弹性特性。
首先,文中将介绍风力发电机叶片的气动弹性特性,并介绍模型的基本原理。
其次,文中介绍了风力发电机叶片气动弹性稳定性模型计算的详细流程,包括:叶片模型的建立,其中主要涉及叶片模型的定义、叶片气动弹性特性参数的取值和截面参数的计算;叶片结构和气流环境的建立,主要涉及叶片装配状况、风速变化等;叶片气动弹性特性参数建立,其中包括叶片的弯曲系数、抗扭力系数和抗剪力系数等;叶片气动弹性状态分析,主要涉及叶片振动拟合和叶片气动弹性分析。
最后,文中介绍了采用计算流体动力学方法对模型的数值模拟,以验证模型的准确性。
总的来说,本文从理论分析的角度研究了风力发电机叶片的气动弹性特性,并从参数设置、模型分析和数值模拟三个方面阐述了分析过程,为风力发电机叶片性能设计提供了有效指导。
作为研究发电机叶片参数设计和挣度计算的关键内容,叶片气动弹性分析对风力发电机叶片的气动弹性参数建立和分析也具有重要意义。
风力发电机叶片的气动结构参数、叶片气动弹性特性参数以及叶片气动弹性分析等,都是需要综合考虑的因素。
本文从理论分析的角度研究了风力发电机叶片的气动弹性特性,并从参数设置、模型分析和数值模拟三个方面阐述了分析过程,为风力发电机叶片性能设计提供了有效指导。
未来风力发电机叶片气动弹性分析领域的研究将是在实验验证和计算机模拟的基础上,改进分析模型,提高分析的精度和准确性,以更好地支持叶片性能设计,为叶片的有效应用提供科学的依据。
总之,利用叶片气动弹性模型能够有效地分析风力发电机叶片的气动弹性特性,从而为风力发电设备的设计提供参考。
风电机组叶片气动弹性与颤振抑制

风电机组叶片气动弹性与颤振抑制随着风电行业的快速发展,风电机组叶片的气动弹性和颤振抑制成为了一个重要的研究方向。
叶片是风力发电机组的核心部件之一,其工作稳定性和性能直接关系到风电机组的发电效率和安全运行。
研究叶片的气动弹性与颤振抑制具有重要的意义。
叶片的气动弹性是指在风速变化时叶片的形变和振动情况。
由于受到风速、角速度等因素的影响,叶片在风力作用下会出现弹性变形和振动。
气动弹性对于叶片的结构和材料有一定的要求,需要具备一定的柔韧性和刚度。
叶片的气动弹性主要与叶片的长度、形状、材料等因素有关。
研究叶片的气动弹性可以提高叶片的工作效率,减少能量损失。
而叶片的颤振抑制是指通过控制和改善叶片的结构和设计,减少叶片因风力作用而产生的颤振。
颤振是由于风力的周期性变化而导致的叶片振动,严重的颤振会导致叶片的疲劳破坏和损坏。
颤振抑制是提高风电机组叶片耐久性和安全性的重要手段之一。
目前,针对风电机组叶片的气动弹性和颤振抑制的研究已经取得了一定的成果。
一方面,通过对叶片材料的改进和优化,提高叶片的韧性和刚度,减少叶片的振动幅度。
通过风力模型和数值模拟等手段,对叶片的气动弹性和颤振进行仿真分析,优化叶片的结构和设计,提高叶片的抗颤振能力。
除了材料和设计的改进外,风电机组叶片的气动弹性和颤振抑制还可以通过智能控制技术来实现。
通过引入传感器和控制器,监测叶片的振动情况,并进行动态调整,减少颤振的发生。
还可以采用压电效应和阻尼材料等技术,减少叶片振动的能量传递。
风电机组叶片的气动弹性和颤振抑制是一个复杂而重要的研究课题。
通过对叶片材料、结构和设计的改进,以及智能控制技术的引入,可以提高叶片的气动弹性,减少颤振的发生,提高风电机组的工作效率和安全性。
风电机组叶片气动弹性与颤振抑制
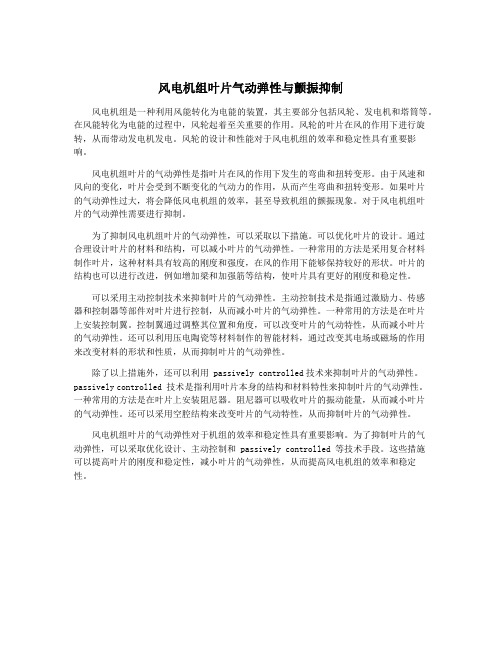
风电机组叶片气动弹性与颤振抑制风电机组是一种利用风能转化为电能的装置,其主要部分包括风轮、发电机和塔筒等。
在风能转化为电能的过程中,风轮起着至关重要的作用。
风轮的叶片在风的作用下进行旋转,从而带动发电机发电。
风轮的设计和性能对于风电机组的效率和稳定性具有重要影响。
风电机组叶片的气动弹性是指叶片在风的作用下发生的弯曲和扭转变形。
由于风速和风向的变化,叶片会受到不断变化的气动力的作用,从而产生弯曲和扭转变形。
如果叶片的气动弹性过大,将会降低风电机组的效率,甚至导致机组的颤振现象。
对于风电机组叶片的气动弹性需要进行抑制。
为了抑制风电机组叶片的气动弹性,可以采取以下措施。
可以优化叶片的设计。
通过合理设计叶片的材料和结构,可以减小叶片的气动弹性。
一种常用的方法是采用复合材料制作叶片,这种材料具有较高的刚度和强度,在风的作用下能够保持较好的形状。
叶片的结构也可以进行改进,例如增加梁和加强筋等结构,使叶片具有更好的刚度和稳定性。
可以采用主动控制技术来抑制叶片的气动弹性。
主动控制技术是指通过激励力、传感器和控制器等部件对叶片进行控制,从而减小叶片的气动弹性。
一种常用的方法是在叶片上安装控制翼。
控制翼通过调整其位置和角度,可以改变叶片的气动特性,从而减小叶片的气动弹性。
还可以利用压电陶瓷等材料制作的智能材料,通过改变其电场或磁场的作用来改变材料的形状和性质,从而抑制叶片的气动弹性。
除了以上措施外,还可以利用 passively controlled技术来抑制叶片的气动弹性。
passively controlled 技术是指利用叶片本身的结构和材料特性来抑制叶片的气动弹性。
一种常用的方法是在叶片上安装阻尼器。
阻尼器可以吸收叶片的振动能量,从而减小叶片的气动弹性。
还可以采用空腔结构来改变叶片的气动特性,从而抑制叶片的气动弹性。
风电机组叶片的气动弹性对于机组的效率和稳定性具有重要影响。
为了抑制叶片的气动弹性,可以采取优化设计、主动控制和 passively controlled 等技术手段。
风电机组叶片气动弹性与颤振抑制

风电机组叶片气动弹性与颤振抑制风电机组的叶片是风能转化为机械能的关键部件,其气动弹性与颤振抑制是提高风电机组效率和可靠性的重要技术。
本文将从叶片气动弹性的影响因素、颤振机理以及抑制方法等方面进行探讨,以期为风电机组的设计和运行提供参考。
叶片气动弹性是指叶片在风力作用下发生变形或振动的能力,主要由叶片的材料、结构和风速等因素决定。
叶片材料的弹性模量和屈服强度直接影响叶片的刚度和强度,材料强度越高,叶片的刚度越大,相应的叶片形变和振动也会减小。
叶片结构的刚度和动力特性也会对叶片气动弹性产生影响,增加叶片厚度、加工精度和曲率等措施可以提高叶片的刚度和降低振幅。
颤振是指叶片在固有频率附近受到外界激励时发生的共振现象。
颤振对风电机组的安全和稳定运行造成了严重影响,可导致叶片断裂、机构破坏甚至整机倒塌。
叶片颤振的机理有多种,包括气动力激励、自激振动和失稳机制等。
气动力激励是指风场中的气流引起叶片受力激励,失稳机制是指叶片的动力特性与外界激励之间的相互作用导致共振现象。
对于叶片颤振的抑制,首先需要了解其共振频率和模态形状,然后采取相应的措施进行抑制。
常见的抑制方法包括增加叶片的阻尼、调整叶片的结构参数、改善叶片的气动性能等。
为了抑制风电机组叶片的气动弹性和颤振,需要综合考虑叶片的结构、材料、工艺和控制等因素。
在设计阶段,应根据叶片的工作条件和运行环境选择合适的叶片材料和结构,考虑叶片的刚度、强度和阻尼等要求,并采取相应的加工和组装工艺,以提高叶片的刚度和降低振幅。
在运行阶段,应通过叶片监测系统实时监测叶片的振动状态,并根据监测结果进行调整和控制,以保持叶片的稳定运行。
叶片气动弹性与颤振抑制是风电机组设计和运行中需要重点关注的问题。
通过选择合适的叶片材料和结构、优化叶片的气动性能以及采取合理的监测和控制措施,可以有效地提高风电机组的效率和可靠性,实现可持续发展的目标。
风电机组叶片气动弹性与颤振抑制
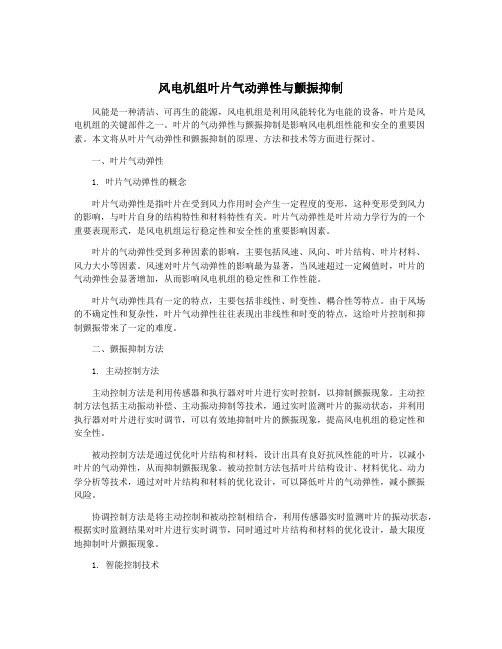
风电机组叶片气动弹性与颤振抑制风能是一种清洁、可再生的能源,风电机组是利用风能转化为电能的设备,叶片是风电机组的关键部件之一。
叶片的气动弹性与颤振抑制是影响风电机组性能和安全的重要因素。
本文将从叶片气动弹性和颤振抑制的原理、方法和技术等方面进行探讨。
一、叶片气动弹性1. 叶片气动弹性的概念叶片气动弹性是指叶片在受到风力作用时会产生一定程度的变形,这种变形受到风力的影响,与叶片自身的结构特性和材料特性有关。
叶片气动弹性是叶片动力学行为的一个重要表现形式,是风电机组运行稳定性和安全性的重要影响因素。
叶片的气动弹性受到多种因素的影响,主要包括风速、风向、叶片结构、叶片材料、风力大小等因素。
风速对叶片气动弹性的影响最为显著,当风速超过一定阈值时,叶片的气动弹性会显著增加,从而影响风电机组的稳定性和工作性能。
叶片气动弹性具有一定的特点,主要包括非线性、时变性、耦合性等特点。
由于风场的不确定性和复杂性,叶片气动弹性往往表现出非线性和时变的特点,这给叶片控制和抑制颤振带来了一定的难度。
二、颤振抑制方法1. 主动控制方法主动控制方法是利用传感器和执行器对叶片进行实时控制,以抑制颤振现象。
主动控制方法包括主动振动补偿、主动振动抑制等技术,通过实时监测叶片的振动状态,并利用执行器对叶片进行实时调节,可以有效地抑制叶片的颤振现象,提高风电机组的稳定性和安全性。
被动控制方法是通过优化叶片结构和材料,设计出具有良好抗风性能的叶片,以减小叶片的气动弹性,从而抑制颤振现象。
被动控制方法包括叶片结构设计、材料优化、动力学分析等技术,通过对叶片结构和材料的优化设计,可以降低叶片的气动弹性,减小颤振风险。
协调控制方法是将主动控制和被动控制相结合,利用传感器实时监测叶片的振动状态,根据实时监测结果对叶片进行实时调节,同时通过叶片结构和材料的优化设计,最大限度地抑制叶片颤振现象。
1. 智能控制技术智能控制技术是利用人工智能、模糊控制、神经网络等技术,对叶片进行智能化控制,以实现对叶片颤振的精准抑制。
风力发电机的振动响应特性分析

风力发电机的振动响应特性分析随着全球清洁能源需求的增加,风力发电作为一种安全、低成本、环保、可再生的能源技术,已经广泛应用于工业和民用领域。
风力发电机的振动响应特性是优化其性能和提高其可靠性的关键因素之一。
本文将介绍风力发电机振动响应特性的分析方法和主要影响因素。
1. 风力发电机的振动响应特性振动是风力发电机中最常见的特性之一,其来源包括风、转子、传动系统、塔架和基础等。
振动响应是指风力发电机受到外部激励后产生的振动响应。
振动响应可分为正常振动和异常振动。
正常振动是风力发电机在正常运行时产生的振动,主要来源于风的作用,如气动振动和风载振动。
异常振动是指风力发电机受到异常外力作用,引起的异常振动,如风暴、地震等。
风力发电机的振动响应特性与其动力学性能和结构特征密切相关。
通常使用振动响应频率和振幅来描述振动响应特性。
风力发电机的振动响应频率主要由其主要结构元件的特性决定。
2. 风力发电机振动响应特性的分析方法风力发电机的振动响应特性分析方法主要包括计算方法和实验方法。
2.1 计算方法计算方法是通过数学模型对风力发电机进行分析和预测其振动响应特性。
计算方法主要包括有限元法、有限差分法、边值元法、模态分析法等。
有限元法是一种广泛使用的分析方法,该方法将结构离散化为一系列有限元,然后在每个有限元上解决运动方程。
该方法可以精确地预测风力发电机的振动响应特性。
2.2 实验方法实验方法是通过对实际风力发电机进行测试,获取其振动响应信号,并对其进行分析,以了解其振动响应特性。
实验方法包括模态分析、频率响应分析、时域分析等。
模态分析是一种通过激励和测量结构振动来确定其自由振动特性的方法。
模态分析可以确定风力发电机的结构振动模态和振动频率。
频率响应分析是一种测量结构响应随着激励频率变化的方法。
频率响应分析可以确定风力发电机的振动响应特性和共振频率。
3. 主要影响因素风力发电机振动响应特性的主要影响因素包括结构特征、环境影响和操作条件。
- 1、下载文档前请自行甄别文档内容的完整性,平台不提供额外的编辑、内容补充、找答案等附加服务。
- 2、"仅部分预览"的文档,不可在线预览部分如存在完整性等问题,可反馈申请退款(可完整预览的文档不适用该条件!)。
- 3、如文档侵犯您的权益,请联系客服反馈,我们会尽快为您处理(人工客服工作时间:9:00-18:30)。
3计算结果及分析
以某型750KW风力发电机风轮叶片为例,计算了叶片 在正常安装 角时(2。), 14 m/s(额 定风速)、25
m/s、41.7 m/s、70 m/s
(停机风速) 四种情况, 以及安装角
达50。(安装-3.
错误)时70
。
时间/s
20
m/s风速下
▲图2扭转响应
70
机械设序计算流程如下:在每一个增量步,Marc 主程序将节点号及弯曲、摆振和扭转方向位移传给FORCDT 载荷子程序,子程序根据节点号得到截面翼型类型,以及该 点的初始展向位置,初始安装角及弦长,根据挥舞、摆振和扭 转方向位移修正展向位置及安装角,并计算攻角,由攻角插 值获得升力系数、阻力系数和力矩系数,根据动量叶素理论 计算微段的气动升力、气动阻力及气动力矩,并将其折算到 节点位置上,由于Mare主程序要求FORCDT载荷子程序返 回的是载荷增量,因此这里还需要取出上一增量步的载荷 值,从而获得增量值。Marc主程序根据返回的载荷增量,求 解结构的响应。如此实现反复迭带。
叶片为薄壁结构。可得扭转振动微分方程: .矛0 aM。
y。,孑2 i+鸭
截面E的剪应力与扭矩的关系为:
万方数据
JAlrlff'ldAl+JA2r2r2dA2+…=皿
可得:
夏dO、G。工,r2积。+G2上:蠢拟:+…)=丝
由此得到角位移和扭矩的关系
丝=(G。‘。+G2%+..·)=五dO 由此得振动方程
1 叶片气弹计算的基本思路
气弹计算方法可以分为三大类:第一类是将流体和固体 区域解耦,将流体对结构的作用折算到结构动力学方程中 去,或者反之。第二类方法将流体域和结构域的方程单独求 解,但是在每个时间步交换信息,这样一个域求解的结果就 被当作边界条件施加到另一个域中,即在每一步将计算得到 的流体压力施加到叶片上,得到叶片的新位置,而叶片的新 位置义被作为新的流同边界去计算下一步的流体压力。第 三类方法用一个统一的方程描述流体域和结构域,结构和流 体运动在每个时间步用同一个求解器同时求解。由于流体 与结构的刚度相差很大,因此该类方法实现起来比较困难, 还有待进一步的发展¨’。
2 气弹计算方法的实现
风力发电机属于涡轮机械,叶片主要承受旋转产生的离 心力、自身重力以及风对叶片表面的压力。由于其尺寸十分 巨大,导致风轮叶片的结构形式与机翼相似,并且风轮的转 速低,叶片的稠度低,可以用叶素理论而不需要用叶栅理论 来考虑。因此可以选用较为简单的气动力模型。 2.1气动力模型
参考国外风机设计软件气动力计算部分,我们选取修正 的动量叶素理论作为气动力计算方法,这样做的好处是.由 于动量叶素理论是一个二维的气动力计算方法,那么配合上 二维的梁单元模型作为风轮叶片结构模型,则气动弹性计算 的规模和时间都将成倍缩短,将计算时间南原来的以天计数 变为以小时计,而就计算精度来说,考虑到风轮的转速低,叶 片的稠度低,其精度已经足够。修正的动量叶素理论将叶片 沿展向分成许多微段,称这些微段为叶素,根据叶素的翼型 参数(升力系数、阻力系数、力矩系数、弦长)及位置参数(展 向位置,安装角)并引入叶尖修正因子、轮毂修正因子以及失
calculating example is siveu,the numerical results accord with real operational status of wind turbine blade. Key words:wind turbine blade;aeroelastie
y,P筝=砉(G。‘。+G2如”·’面00饥
式中:Gi为截面各铺层材料的面内剪切模量;L为截面不同 材料的极惯性矩。且有
I,=∑I*
根据以上的推导,梁单元使用各向同性材料,E、G分别
由下式确定:
‘;∑w:毕;
‘:挲小船
在计算气动弹性响应之前,还应根据叶片的实际铺层结 构建立三维有限元模型,计算得到风轮叶片一阶挥舞动频为 1.66 Hz,一阶摆振动频为2.78 Hz,一阶扭转动频为18.37 Hz。而根据以上方法简化的梁单元模型,计算得到的固有频 率与此结果接近。 2.3耦合计算过程
参考文献:
[1]
J G MARSHALl。,M IMREGUN.A REVIEW OF AEROELASTIC— ITY METHODS WITH EMPHASIS ON TURBOMACHINERY AP—
PLICATlONS[J].Journal of Fluids and Structure;",1996,10(3):
叶片挥舞方向,摆振方向和扭转方向的气弹响应,并没有发 现振动发散的情况,图2一图4仅绘出安装角为50。时70 m/s 风速下叶尖节点三个方向的响应历程,另外几种情况下叶尖 节点三个方向的响应历程图形与此类似。
由前面提到的叶片的固有频率分布看,由于叶片一阶扭 转频率比一阶挥舞和摆振频率要高的多,因此叶片扭转振动 要衰减的比挥舞和摆振快,计算结果与此相符。另外,一般
paper a new method suitable for wind turbine blade is developed,this method adopts the Marc general finite element
program酗the fundamental platform.aerodynamic calculation is programmed into subroutine,based on the eharacteris— tic of subroutine calling.the boundary conditions exchange of fluid and structure in each incremental step is realized.A
风力机经常运行于随机变动的自然大气环境中,受力情 况非常复杂,风剪切、随机阵风、风力机起停机都会造成作用 在风力机上的荷载波动,引起结构振动。此外风能是一种低 廉的能源,为了从风中有效的吸取能源,风力机的大型化是 必然趋势。随着风力机尺寸的增加,一方面风轮叶片的叶尖 切向速度不断提高,另一方面考虑到重量问题,风轮叶片将 越来越细长,在这种趋势下,研究风力机气动弹性问题就变 得越来越重要。
第1期
傅程等:风力发电机叶片气动弹性响应分析
速修正因子即可计算l叶I该叶素上的气动力,然后沿展向积 分,即得到整个叶片的气动力。关于修正的动量叶素理论详 细推导过程见参考文献[2]。 2.2结构模型t4,5]
与动量叶素理论相配套,叶片结构采用梁单元模拟。叶 片由玻璃纤维增强复合材料制成,其铺层层数多且形式复 杂,图1示出了部分铺层,可见无论沿弦向还是沿展向材料 都不存在均匀性,将叶片简化成梁后,每个实际截面变成了 一个点,梁单元的材料属性如何给出,才能保证梁单元模型 的动力学特性与真实叶片的动力学特性一致,是需要考虑的 问题。在分析叶片的振动时,根据受力情况,叶片主要有三 个方向的运动,即挥舞振动(z向.坐标参考图1),摆振振动 (y向)和扭转振动(绕X轴)。l,向弯曲振动微分方程为:
下面采用第二类方法,用Marc有限元软件实现风轮叶 片气动弹性计算。选用FORCDT载荷子程序,该子程序给出
收稿日期:2008—08—22
万方数据
的是节点载荷增量,根据Marc子程序的调用特点,在计算的 每一个增量步中,对于每一个将节点力定义成FORCDT子程 序的节点,该子程序都要被调用一次。在静力分析中,位移 向量被传递到子程序中;在动态分析中,速度和加速度量也 被传递过来。由此可见,如果将计算风轮叶片气动载荷的方 法编成FORCDT子程序,将可实现在计算中每个增鼍步互相 交换边界条件的目的。
4结 论
一般来说,兆瓦级以下的风轮叶片在不变矩的情况下, 发生失稳的可能性不大,当叶片达到50 In左右时,一阶挥舞 频率值低于1 Hz,一阶扭转频率约为5至8 Hz,这时就容易 出现耦合失稳的现象H J。由于目前国内的风电行业正处于 发展之中,各商家都视叶片参数为商业机密,因此很难取得 多个型号的叶片参数用于计算。而50 In以上的叶片,国内 目前还没有产品,因此以上仅从理论上去说明方法的实用 性,实例的检验还有待国内风电行业的进一步发展,数据的 进一步丰富。
[4] M O L Hansen,J N S rensen,S Voutsinas,et a1.Madsen.State of the art in wind turbine aerodynamics and aeroelasticity【J].Pro- gress in Aerospace Sciences,2006,42(4):285—330.
关键词:风轮叶片;气动弹性
中图分类号:TK83
文献标识码:A
Aeroelastic Response Analysis of Wind Turbine Blade
FU Cheng,WANG Yah-tong (School of Jet Propulsion,Beihang University,Beijing 100083,China) Abstract:With increasing of wind turbine unit capacity,more attention is paid to aeroelastie problems.In this
▲图1铺层示意图L6J
等可+鲁+=iPy一2一 弘盎”O一 t2
截面上的应力与弯矩的关系为:
Jalyl盯ldAl+JA2),1盯2dA2+…=恤
可得:
等工。衍烈.+鲁正:尤以:+…=鸩
由此得挠度与弯矩的关系:
幔=(目‘-+易如”’)孑
代人振动方程得:
毒暇 (吼+易如+...)+"窘优 -p,’ 一警研
237—267.
[2] R.Lanzafame,M Messina.Fluid dynamics wind turbine design: Critical analysis,optimization and application of BEM theory[J]. Renewable Energy,2007,32(14):2291~2305.