3500mm炉卷轧机支承辊断裂原因分析
热轧轧辊剥落或断裂的原因及预防方法探究

热轧轧辊剥落或断裂的原因及预防方法探究热轧轧辊作为热轧设备中重要的组成部分,其质量直接影响到产品质量和生产效率。
在生产中,往往会出现轧辊剥落或断裂的情况,造成了生产效率低下和安全隐患,因此研究热轧轧辊剥落或断裂的原因及预防方法具有重要的实际意义。
1. 轧辊表面损伤导致轧辊剥落或断裂在轧辊使用过程中,出现轧辊表面损伤容易导致轧辊剥落或断裂。
这种损伤包括表面裂纹、划痕、磨损、腐蚀等,这些损伤会进一步扩大,最终导致轧辊剥落或断裂。
轧辊材质好坏直接影响到轧辊的使用寿命和质量。
如果轧辊的材质不够坚固耐用,那么在热轧过程中会出现轧辊变形、疲劳、裂纹等问题,将极大影响热轧产品质量。
热轧设备的操作不规范也容易导致轧辊剥落或断裂。
例如温度控制不当、轧辊调整不到位等等,都会在热轧过程中产生不同程度的影响,最终导致轧辊剥落或断裂。
热轧工艺参数是热轧过程中必须严格控制的参数,如果热轧工艺参数不合适将会直接影响到轧辊的寿命和使用效果。
例如,轧制过程中的拉伸率、轧制力、速度等参数不合适,都将导致轧辊剥落或断裂。
1. 轧辊材质的优化优化轧辊材质可以提高轧辊的抗拉、抗压、抗疲劳等性能。
特别是在硬度和韧性之间的平衡上,选择合适的轧辊材料可大大提高轧辊的使用寿命。
2. 加强对轧辊的检测热轧轧辊在使用过程中应每隔一些周期对轧辊进行检测,及时发现轧辊损伤和裂纹等问题并进行处理,避免因轧辊的损坏而影响到生产和产品质量。
3. 热轧设备的维护针对热轧设备操作不规范等问题,应加强设备维护,保持轧辊的良好状态。
定期做好轧辊的维护与更新,及时清理轧辊附着的物质,避免附着物进一步侵蚀轧辊表面。
4. 控制热轧工艺参数对于热轧工艺参数不合适问题,应严格控制热轧温度、轧制力、速度等参数。
调整工艺参数能够有效避免轧辊的剥落或断裂。
总之,对于热轧轧辊剥落或断裂问题,合理地选择轧辊材质,加强轧辊的检测和维护,规范热轧设备操作,严格控制热轧工艺参数,是预防轧辊剥落或断裂的有效方法。
热轧支承辊剥落问题根本原因分析及使用建议

热轧支承辊剥落问题根本原因分析及使用建议热轧支承辊剥落问题根本原因分析及使用建议■王维宁,赵学文我公司为客户热轧生产线提供的一只支承辊,辊身直径1461.02mm,客户反馈在某次轧钢时有异响,拉出后该辊的辊身发现有剥落。
通过现场勘察、支撑辊使用情况调查,对支承辊剥落问题进行根本原因分析,并根据分析结果为客户提供现场使用建议。
1. 现场勘察情况根据现场仔细勘察、测量,剥落处位于辊身中部至非字端(传动侧)辊身边部(见图1),范围约900mm(轴向)×800mm(周向),剥落断面中部有两个平滑的带状裂纹通道区域,均约100mm 宽。
①通道距辊身端部约500mm,②通道距辊身端部约300mm。
两条通道区域两侧有一个分界线,分界线及外侧较为粗糙,距辊面深度在25~30mm,条带上可以看到部分不太明显的疲劳扩展条纹,分布着比较经典的一圈一圈的“贝状纹(海滩样)”疲劳扩展条纹,这是每一阶段裂纹前沿轮廓留下的痕迹,贝状纹指示的两条裂纹通道的扩展方向均朝上,与支承辊在机旋转方向相反。
②通道色泽相对发灰、发黑,表面有一薄层氧化腐蚀产物。
在剥落断面同侧的未剥落辊面上发现A、B两处表面裂纹区域,如图2、图3所示。
A区域位于剥落断面对面,距辊身端面385mm,范围100mm(轴向)×185mm(轴向),该区域内上方三处较小表面裂纹呈现“︿”形,“︿”形指向方向与裂纹通道扩展方向一致,下方有一条较长半弧形与轴向的竖直状组成的复合开口裂纹,根据裂纹交汇特点,竖直形裂纹为首先形成的主裂纹,该裂纹应为轧制事故造成的挤压裂纹。
B区域位于剥落断面上沿约400mm处,范围100mm (轴向)×185mm(轴向),距辊身端面100mm。
B区域有多处轴向小裂纹,裂纹密集处成带状,局部呈网状,此种裂纹为典型的热冲击裂纹。
根据着色显像,B区域下方较长的显像条带疑似为擦伤(硌痕),同时B区域下方有一小硌坑。
经超声波检测确定:外露①裂纹通道沿辊面下未剥离的裂纹通道与A区域相连,可确定A区域为①裂纹通道的起源,外露②裂纹通道沿辊面下未剥落暴露的裂纹通道与B区域相连,B区域为②裂纹通道的起源。
辊环裂的原因

辊环槽裂及破碎的原因分析及控制措施
辊环槽裂及破碎,会给生产及准备工作造成困扰,影响企业经济效益提高,需要分析,并采取相应措施.
1破碎及槽裂原因。
1)堆钢造成辊环突然停止转动,红钢和辊环产生面接触,辊环内部受到不同的热应力,产生热裂。
2)轧制中,导卫松动,导卫和辊环间存在摩擦,辊环沿周围方向过热,在辊环表面产生热裂纹。
3)冷却效果差,辊环过热受到大的热应力,导致辊环轧槽处产生热裂纹。
4)辊环安装过紧,张应力过大使辊环发生径向裂纹。
装配过松,锥套与辊环产生滑动,造成接触面磨损,会局部应力集中而损坏。
2控制措施
1)修磨时,微裂纹要车削干净,对辊环的检验强度提高,同时对破损大,损坏严重的辊环要直接报废处理。
2)导卫上面加装螺栓和螺母,将螺栓顶在辊环前的水分配器上,在轧制中,导卫底座螺母松动时,导卫不会和辊环发生滑动接触。
3)冷却水控制,水温控制在25℃以下。
冷却水喷水方向为径向,与辊环旋转方向成15-30度,谁不会散射或呈雾状,而是直接喷入轧槽。
4)辊环安装压力规范化。
多次测试,找出规范的压力值,防止安装过松或过紧,5)制定合理的轧槽吨位,根据钢种的不同,确定合理的轧机负荷。
6)辊环要有较高的耐磨性和抗热龟裂性,以保证棒、线材良好的尺寸公差和表面光洁度;此外确保辊环的匹配的型号一致性。
对热轧机轧辊断裂原因的分析

对热轧机轧辊断裂原因的分析【摘要】本文对产生热轧机轧辊断裂的原因、部位进行了分析,提出了减少或预防轧辊断裂的措施,供同行参考。
【关键词】轧辊断裂;原因;措施0 前言热轧机生产线,具有精度高、检测系统完善等特点。
但热轧机组轧机较多,因此轧辊消耗较大,同时为了提高轧机的生产率,已进行了大量的尝试来改善设备性能和轧制工艺,特别对热轧机轧辊的断裂做了许多有益的研究,但是轧制条件变得愈加苛刻,并且随着产量的不断增加,轧辊断裂现象还时有发生,不但造成经济上的直接损失,还由于断辊停产,减少了产量,增加了热轧废品,增加了能源消耗,因而增加了总成本。
因此研究轧辊断裂的原因,并采取有效的预防措施,对降低成本,提高经济效益有非常重要的意义。
1 产生轧辊断裂的理论原因轧辊断裂是轧辊损坏的一种严重形式,而且处理时间长,影响生产。
轧辊断裂的原因有两种:一种内在原因,由于轧辊本身的内在缺陷造成,如夹杂等造成断裂;另一种是外在原因,由于轧制工艺条件和使用造成。
残余应力及热冲击断裂,轧制开始,轧辊与高温轧件接触,在轧制过程,轧辊表面温度高,而芯部温度低,在芯部产生合成拉应力,当超过极限时,芯部产生裂纹和断辊;疲劳裂纹扩展为断裂,轧辊上的裂纹受弯曲应力的作用,会沿着一条较深的裂纹扩展,继续轧制裂纹会迅速扩展,达到极限,会发生断辊。
使用原因,轧制钢类强度过高,或低温钢、黑头钢等易造成事故,轧制盲目加大压下量以减少道次,闭水轧制后,过快给冷却水,或冷轧薄板时,轧辊压靠力过大,扭矩大于轧制力矩,启动轧机可能扭断轴头。
2 轧辊断裂的具体部位及原因分析2.1在轧辊辊身处断裂。
从断裂现象看断裂部位绝大多数在辊环处,断裂截面为不规则的斜面或垂直截面。
断辊原因有以下几个方面:轧辊质量,工作辊与高温板坯直接接触,并承受各种载荷,因此要有良好的耐热性,如果轧辊辊身硬度随轧辊温度升高而降低的幅度较大时,说明轧辊的耐热性较差,将严重影响轧辊的整体性能;从轧制条件看要求轧辊还应具有良好的耐磨性和适当的硬度和强度。
轧制过程中断辊原因
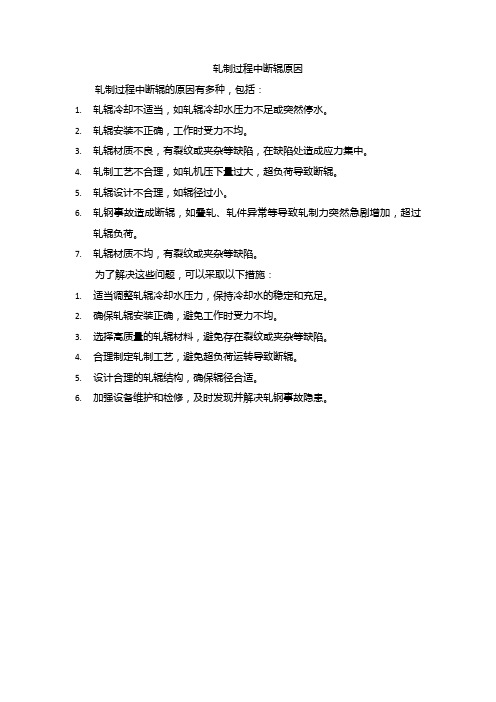
轧制过程中断辊原因
轧制过程中断辊的原因有多种,包括:
1.轧辊冷却不适当,如轧辊冷却水压力不足或突然停水。
2.轧辊安装不正确,工作时受力不均。
3.轧辊材质不良,有裂纹或夹杂等缺陷,在缺陷处造成应力集中。
4.轧制工艺不合理,如轧机压下量过大,超负荷导致断辊。
5.轧辊设计不合理,如辊径过小。
6.轧钢事故造成断辊,如叠轧、轧件异常等导致轧制力突然急剧增加,超过
轧辊负荷。
7.轧辊材质不均,有裂纹或夹杂等缺陷。
为了解决这些问题,可以采取以下措施:
1.适当调整轧辊冷却水压力,保持冷却水的稳定和充足。
2.确保轧辊安装正确,避免工作时受力不均。
3.选择高质量的轧辊材料,避免存在裂纹或夹杂等缺陷。
4.合理制定轧制工艺,避免超负荷运转导致断辊。
5.设计合理的轧辊结构,确保辊径合适。
6.加强设备维护和检修,及时发现并解决轧钢事故隐患。
轧机上断辊的原因分析
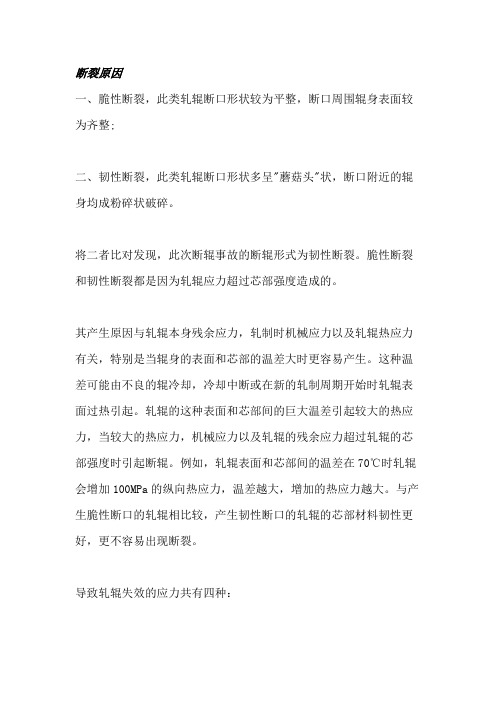
断裂原因一、脆性断裂,此类轧辊断口形状较为平整,断口周围辊身表面较为齐整;二、韧性断裂,此类轧辊断口形状多呈"蘑菇头"状,断口附近的辊身均成粉碎状破碎。
将二者比对发现,此次断辊事故的断辊形式为韧性断裂。
脆性断裂和韧性断裂都是因为轧辊应力超过芯部强度造成的。
其产生原因与轧辊本身残余应力,轧制时机械应力以及轧辊热应力有关,特别是当辊身的表面和芯部的温差大时更容易产生。
这种温差可能由不良的辊冷却,冷却中断或在新的轧制周期开始时轧辊表面过热引起。
轧辊的这种表面和芯部间的巨大温差引起较大的热应力,当较大的热应力,机械应力以及轧辊的残余应力超过轧辊的芯部强度时引起断辊。
例如,轧辊表面和芯部间的温差在70℃时轧辊会增加100MPa的纵向热应力,温差越大,增加的热应力越大。
与产生脆性断口的轧辊相比较,产生韧性断口的轧辊的芯部材料韧性更好,更不容易出现断裂。
导致轧辊失效的应力共有四种:一、制造过程中的残余应力;二、轧制过程中的机械应力;三、轧制过程中轧辊的组织应力;四、轧辊内外温差造成的热应力。
如果是因为制造残余应力过大产生断裂,断辊通常发生在轧辊初始上机使用的前几次,且为开轧的前几块轧材。
此次断裂的轧辊已经上机轧制了四次,工作层消耗了14mm,因此不应是因制造残余应力形成的断裂。
如果是因为机械应力产生的断裂,需要很大的机械应力。
经粗略计算,如此大截面的高铬铸钢轧辊若被机械应力拉断,则需要100MN 以上的拉力,对于该轧辊工作的轧机来说这是不可能的。
轧辊受力最大的部位是传动端辊颈,如果材料的力学性能指标不足,正常轧制情况下首先损坏的是传动端辊颈。
从实际轧制和断辊情况来看,不是由于机械应力造成辊身断裂。
对组织应力影响最大的就是外层组织中残余奥氏体含量。
残余奥氏体在轧制温度,轧制压力和水冷的交变作用下,发生奥氏体向马氏体或贝氏体的转变,由于奥氏体的比容小,而马氏体的比容大,因而在组织转变的过程中伴随着体积的膨胀,会致使轧辊的工作层产生更大的压应力,芯部产生更大的拉应力,芯部应力一旦超过材料的强度,必然造成轧辊断裂。
轧辊失效方式及其原因分析

轧辊失效方式及其原因分析摘要:介绍了轧辊存在剥落、断裂、裂纹等几种失效方式,并重点分析了轧辊剥落和断裂产生的机理,为分析生产实践中轧辊失效原因和采取相应改进措施以提高轧辊使用寿命提供了依据。
关键词:轧辊;失效原因;剥落;断裂;裂纹1 前言轧机在轧制生产过程中,轧辊处于复杂的应力状态。
热轧机轧辊的工作环境更为恶劣:轧辊与轧件接触加热、轧辊水冷引起的周期性热应力,轧制负荷引起的接触应力、剪切应力以及残余应力等。
如轧辊的选材、设计、制作工艺等不合理,或轧制时卡钢等造成局部发热引起热冲击等,都易使轧辊失效。
轧辊失效主要有剥落、断裂、裂纹等形式。
任何一种失效形式都会直接导致轧辊使用寿命缩短。
因此有必要结合轧辊的失效形式,探究其产生的原因,找出延长轧辊使用寿命的有效途径。
2 轧辊的失效形式2.1 轧辊剥落轧辊剥落为首要的损坏形式,现场调查亦表明,剥落是轧辊损坏,甚至早期报废的主要原因。
轧制中局部过载和升温,使带钢焊合在轧辊表面,产生于次表层的裂纹沿径向扩展进入硬化层并多方向分枝扩展,该裂纹在逆向轧制条件下即造成剥落。
2.1.1支撑辊辊面剥落支撑辊剥落大多位于轧辊两端,沿圆周方向扩展,在宽度上呈块状或大块片状剥落,剥落坑表面较平整。
支撑辊和工作辊接触可看作两平行圆柱体的接触,在纯滚动情况下,接触处的接触应力为三向压应力,如图1所示。
在离接触表面深度(Z)为0.786b处(b为接触面宽度之半)剪切应力最大,随着表层摩擦力的增大而移向表层。
图1 滚动接触疲劳破坏应力状态疲劳裂纹并不是发生在剪应力最大处,而是更接近于表面,即在Z为0.5b的交变剪应力层处。
该处剪应力平行于轧辊表面,据剪应力互等定理,与表面垂直的方向同样存在大小相等的剪应力。
此力随轧辊的转动而发生大小和方向的改变,是造成接触疲劳的根源。
周期交变的剪切应力是轧辊损坏最常见的致因。
在交变剪切应力作用下,反复变形使材料局部弱化,达到疲劳极限时,出现裂纹。
另外,轧辊制造工艺造成的材质不均匀和微型缺陷的存在,亦有助于裂纹的产生。
引起轧辊发生垂直轧辊轴线断裂断面的主要原因_

引起轧辊发生垂直轧辊轴线断裂断面的主要原因1. 引言1.1 概述在轧钢过程中,轧辊是一种重要的工作部件,其质量和稳定性直接影响到整个轧制过程的效果和产品质量。
然而,在实际生产中,垂直轧辊轴线断裂断面问题时有发生,给生产运行带来了严重的影响和损失。
因此,了解引起这一问题的主要原因,并采取相应措施来预防和解决它们具有重要意义。
1.2 文章结构本文将从三个方面对垂直轧辊轴线断裂断面的主要原因进行探讨:轧辊质量问题、加工工艺问题以及动力系统问题。
每个方面将进一步细分为具体的子问题,并通过深入分析和研究来揭示这些子问题对垂直轧辊轴线断裂造成的影响。
1.3 目的本文旨在全面地研究并概述引起垂直轧辊轴线断裂断面的主要原因。
通过对这些原因进行深入剖析,我们可以更好地理解并找出有效的解决方案,从而提高生产过程中的效率和产品的质量。
给出相关的解决方案和改进建议有助于生产运行更加平稳和可靠地进行。
2. 垂直轧辊轴线断裂断面的主要原因垂直轧辊轴线断裂断面是钢铁工业中常见的问题之一,其主要原因可以归结为轧辊质量问题、加工工艺问题和动力系统问题。
2.1 轧辊质量问题轧辊质量问题是导致垂直轧辊轴线断裂断面的重要原因之一。
首先,材料的质量不合格会直接影响到轧辊的强度和韧性,在工作过程中容易出现疲劳破坏。
其次,热处理过程不当也可能使得轧辊内部存在残余应力或者晶粒生长异常,从而降低了其抗疲劳性能。
此外,加工精度不高也会导致负责分布不均匀以及表面误差增加,使得在工作过程中产生应力集中区域。
2.2 加工工艺问题加工工艺问题也是引起垂直轧辊轴线断裂断面的重要原因之一。
切割过程不正常会导致切口存在毛刺或者微裂纹等缺陷,这些缺陷在后续工作中会发展成裂纹,并最终导致轧辊断裂。
正火过程中温度和时间的控制不合理也会在轧辊内部形成大量的残余应力,使得轴线处于扭转应力状态,容易引发断裂。
此外,精加工磨削不足也可能使得表面存在凸起或者凹陷等缺陷,从而使得轧辊在工作过程中受到额外的摩擦和冲击。
- 1、下载文档前请自行甄别文档内容的完整性,平台不提供额外的编辑、内容补充、找答案等附加服务。
- 2、"仅部分预览"的文档,不可在线预览部分如存在完整性等问题,可反馈申请退款(可完整预览的文档不适用该条件!)。
- 3、如文档侵犯您的权益,请联系客服反馈,我们会尽快为您处理(人工客服工作时间:9:00-18:30)。
通过对不同断 口的观察 与分析 , 几乎所有断 口都起源于碳化物与夹杂的聚集区。即起源于低 倍 下 肉眼可 见 的 白色 斑点状 及 网状偏 析 。 由于 白
色 斑点 状及 网状 偏 析 是 由颗粒 状 碳 化 物 及 炉渣 、
( 1 ) 碳化物分布不均匀。主要 体现在低倍下 的 白色斑点 状偏 析及 网状偏 析 。这是 原始 铸锭 在
打 碎形成 弥 散分 布 , 严 重 割 裂 了金 属 基 体 的连 续 性, 降 低 了合 金 强度 与塑 韧性 , 并 产 生 应 力集 中 , 从 而导致 事 故辊萌 生 断裂源 。 无论 是 裂纹 源区 , 还是裂 纹 扩展 区 , 断 口形貌 均 以解理 脆性 断 裂 为 主 , 表 明该 事 故 辊 系 典 型脆
凝 固过 程 中受钢 的冶 炼 质 量 、 浇 注条 件 及 冷 却 结 晶特 点共 同影 响 的结 果 。原始 铸锭组 织 中存在 严 重 的碳 化物 分 布不 均 匀 , 锻 造 及 锻后 退 火 又 不 充
低熔点夹杂 、 氧化物等组成的集合体 , 造成合金塑 韧性极度降低 , 并产生应力集中, 促成裂纹萌生。 尤 其是 处
锭 在浇 注时 形成 翻皮 , 内部 夹 杂及 碳 化 物 聚集 非
分, 使碳化物不均匀现象未能得到有效改善。正
是 由于碳化 物不 均 匀 , 也 造 成 了基 体 组 织 品粒 大 小 分布 不均 匀 , 尤 其是 贫碳 区容 易产生 过热 , 形 成
粗 大组 织 。
常严重。翻皮在锻造过程 中没有被压合 , 夹杂物 及 碳化 物聚集 也 未在 锻造及 锻后 热处理 过程 中被
《 大型铸 锻件》
HEAVY CAS TI NG AND FORGI NG
No. 1
J a n u a r y 2 01 4
综合 以上分析得知 , 事故辊断 口裂纹起源于 各种非金属夹杂。由于基体组织粗大、 碳化物分 布不均匀降低 了合金 的塑韧性 , 在应力作用下 , 促 使裂纹扩展 , 并最终断裂。
一
塑韧性 , 促 使裂 纹扩 展 , 并 以解 理脆性 方式 断裂 。
5 结 论
状偏析; 富含 C 、 N a 、 c l 、 s i 、 c r 的颗粒夹杂只在断 口中发现 , 而且是 以尺寸更小 的聚集体存在。以
Z r 、 Mn等 的氧 化 物 多数 是 附着 在 炉 渣 表 面 , 伴 随 炉渣 而存 在 。有 的是 以独 立 的小颗粒 氧 化物伴 随 碳化 物 的聚集 而 聚集 , 形 成 白色 斑 点状 偏 析 及 网
组织粗大 、 夹杂物及碳化物聚集 、 基体晶粒大小不 以及 脆性 组织 存 在 , 都 会 严 重 降 低合 金 强 度 及
( 2 ) 非 金 属 夹 杂 物 。事 故 辊从 表 到 里 , 都 有
较 多不 同类 型 的非 金 属 夹 杂存 在 , 夹 杂 物 类 型 不 同, 存在 方式 也不 一样 。综合 不 同试样 能谱 分析 , 事 故辊 内部 主要 夹 杂 物类 型 有 : 大块状 T i N、 T i C 和 长条 状 Mn S ; 富含 C 、 O、 A 1 、 Mg 、 Mn 、 Z r 、 T i 、 C a 、
4 事 故辊 断 裂原 因分析 综合 上述试 验 分 析 , 事 故 辊 断裂 主要 与 以下
几方 面有关 :
分布集中。这主要是合金浇注过程 中由于浇注不 当造成翻皮 , 将合金表面的氧化物 、 低熔点夹杂及 易偏析溶质元素、 炉渣 、 保护渣等类夹杂卷入钢液 而未 能上浮 。 由此 可 知 , 事 故 辊 的 断裂 起 源 于 翻
表到里都有存在。除了 M n S具有一定塑性 以长 条形 式存 在 外 , T i N、 T i C都 以棱 角分 明 的 大 块 状
形式 存在 ; 低熔 点 炉 渣 主要 以颗 粒 大 小 不一 的 聚
集体存在 。由于所处事故辊部位不同 , 其存在形 式也 有所 不 同 。在事 故 辊 外 层 , 主 要 与低 熔 点 夹 杂相伴 , 以大小不一 的颗粒状聚集存在 , 低倍下表 现为边缘黑色斑点状偏析 。在事故辊内部中间层
寸 更小 的 白 色 小 颗 粒 聚 集 夹 杂 。 其 中 , 大 块 状 T i N、 T i C和长条 状 Mn S在 事 故 辊 不 同部 位 , 即从
消除, 作为残余应力保存 于事故辊中。又由于事 故辊从表层到心部 不 同区域基体组织 有较大差
异, 不 同类 型 、 不 同大小 、 不 同形态 的夹 杂及 碳 化 物 聚集 分 布 , 基 体组 织 晶粒粗 大且不 均匀 , 必然 产 生应 力集 中 , 尤 其 是 夹 杂 物及 碳 化 物 严重 聚集 区 域应 力集 中最 大 。事 故辊 的残 余热 应力 与复 杂组
性断裂。这与其基体组织粗大 、 存在较多夹杂及 碳化物分布不均匀的组织特点相印证。 ( 3 ) 残余应力 。由于事故辊尺寸大 , 表面和
心部 在热 处理 加 热 和 冷 却过 程 中温 度 分布 不 均 ,
而产 生热 应力 。热 处理 后热应 力 又没有 得 到完全
P 、 S 等的颗粒状低熔点炉渣 ; 富含 M g 、 A 1 、 N a 、 Z r 、 Mn等 的小 颗粒 氧化 物 ; 富含 C、 N a 、 c l 、 s i 、 C r 的 尺
及心 部是 伴 随着 颗 粒 状 碳 化 物 的 聚集 而 聚 集 , 与
织应力的叠加 , 致使其超过了材料的断裂抗力 , 于 是 在该 处 萌生裂 纹而 成 为断裂 源 。
裂 纹一 旦 萌生 , 就 由 内 向外 扩 展 。 由于 基 体
颗粒状碳化物 、 氧化物等夹杂形成聚集体 , 低倍下 表现 为 白色 斑 点状 偏 析 及 网状 偏 析 ; Mg 、 A I 、 N a 、