外观缺陷不良分析
外观不良8D报告

1D:团队分析团队:团队长:总监成员:审核团队:团队长:成员:批准人员:供应商领导:2D:问题描述产品型号:发生时间:检验数:产品类型:PCM 异常类别:外观不良不良数:现象:1、2015年9月9日贵司试产HB366481的来料不良图片,其中脏污不良0.99%,定位孔不良104PCS,异物、压伤不良48PCS,不良率1.98%,2、此板为打样试产板,目前我司仓库已无该板库存,在线有小批量试产板6.5K在钻孔工序,将不良信息反馈给产线,重点管控以上不良3D:原因分析1、脏污产生原因:从不良图片分析,此不良为异物反粘板面造成脏污,查询产线生产工具,产线装板使用吸塑盒部分存在胶状物质,容易返粘板面造成脏污2、孔内毛刺、油墨入孔产生原因:此板为无卤素材料,材料脆性较大,钻孔后孔内位置毛刺无法避免,因毛刺未及时处理,阻焊之后孔内油墨不易显影完全,存在油墨残留现象3、黑油物产生原因:从不良图片分析,此不良为黑油印刷前,清洁不足导致,近期无尘车间改造,造成外来杂物增加,生产过程中清洁不到位容易导致杂物残留4、不良流出原因:此板为试产样品,检查人员检板过程中,为尽量满足多交货,针对部分外观缺陷问题板未做报废,导致不良流程4D:应急措施1、此板为试产板,贵司已无该板库存2、我司仓库已无该板库存3、在线6.5K二次打样板,在钻孔工序,项目组重点跟进以上异常5D:已进行的纠正行动验证:1、针对所有吸塑盘进行检查,有脏污、异物的统一挑出清洁,避免异物反粘板面2、目前产线施工改造已经完成,无尘室车间无尘含量达标,黑油每次印刷前,按要求清洁台面网版,防止杂物残留6D:永久纠正行动:1.钻孔后针对毛刺突出不良,安排刮毛刺处理(要求,孔径必须合格),钻孔后增加除胶渣流程,减少孔壁粗糙度2.入检验标准对员工进行培训;7D:防止问题再发生的措施1.针对所有新项目样品研发阶段必须严格执行合同评审制度,针对特殊工艺或软硬结合产品要求研发部门必须组织工程、生产、工艺、品质共同评估工艺及操作可行性,确定相关检验标准和验证方案并形成有效记录和控制计划来指导一线生产;2.所有新产品转批量之前必须出具样品品质记录、客诉记录及过程重要工艺问题点记录经品质经理和技术总监审核、副总批准后方能正式投料生产;8D:解决问题小组工作的认可。
塑胶产品外观常见不良分析

塑胶产品外观常见不良分析塑胶产品在生产过程中,由于种种原因可能会产生不良的外观缺陷,这些缺陷会对产品的质量和使用效果造成不利影响,下面就介绍几种常见的塑胶产品外观不良分析。
一、砂眼砂眼是指产品外表面上出现的类似小孔洞的缺陷,通常表现为圆形、椭圆形或不规则形状。
砂眼产生的原因是模具表面有斑点、气孔、异物等缺陷,导致塑料进模不畅或模内气体无法顺畅排出形成,最后留下小孔洞。
二、流痕流痕是指产品表面上出现的细长的纹路,一般与塑料的注射方向垂直,这样的缺陷往往会影响到产品的美观度。
流痕的原因是模具内部的热流动不均匀,某些部位的温度较低,导致塑料注入后无法均匀地流动分布,产生较深的沟痕。
三、气泡气泡是指产品表面或内部出现的像气泡一样的孔隙,它们不仅会让塑胶产品表面看起来不平整,还会降低产品的力学性能和密封性能。
气泡的产生可能是塑料攪拌不均匀或注射速度过快导致的空气混入塑料中,也可能是质量不佳的原料带有微小的空气颗粒。
四、色差色差是指产品颜色不均匀、不合一致标准要求的情况。
彩色塑胶制品通常是由数种颜色的颗粒混合而成,如果混合不均匀或是染料质量不稳定,这些问题就会显现在产品表面,造成色差。
此外,不适当的注塑温度和压力也会影响塑料颜色的均匀度。
五、毛刺毛刺是指产品表面上一些尖锐、突出的小物质,通常是模具零件分离不干净、模具中有棘手的地方,以及产品卡死在模具中发生磨损等造成的。
毛刺的出现不仅影响产品的整体美观度,还会损伤使用者的手部和其他部位。
六、变形变形是指产品在注塑后外观发生了形状和尺寸的变化,这种情况最常见的原因是模具温度不均匀,塑料被过快地冷却,导致变形。
另外,如果产品设计不合理、墙厚不足也会导致变形。
变形不仅会让产品表面看起来不平整,还会导致产品性能不稳定,从而进一步影响产品的生产和使用。
总之,塑胶产品外观缺陷的种类繁多,产生的原因也五花八门如果不及时有效地加以排查和处理,就会直接影响产品的质量和使用效果。
注塑品外观缺陷原因分析及方案

注塑品常見缺陷解決辦法
•注塑制品表面缺陷 1 .制品整体有塌瘪倾向的充填不足 成型材料的改进:选用流动性好的材料 成型条件的改进:提调幅浪射温度、压力、速度;
提高保压压力、加大从注射到保压的变换时间; 提高模具温度调整喷嘴逆流阀
注塑品常見缺陷解決辦法
•注塑制品表面缺陷 1 .制品整体有塌瘪倾向的充填不足 模具结构的改进:改变浇口的位置;浇口变短, 加大;流道变短、加宽;加大冷料穴;喷此和 模具口配合完好 制品设计的改进:调整树脂流动长度与厚度的比
偏小、合模精度不高、模具变形、融料过热等 造成
注塑品常見缺陷解決辦法
•有缺陷的制品通常由下面1个或几个原因 造成:
1.模塑前:原材料的处理和贮存; 2.模塑阶段:成型周期内的成型条件; 3.模塑之后:制品的处理和修饰
注塑品常見缺陷解決辦法
•在制品模塑前后出现的问题可能与污染、颜色、 静态粉尘收集器等相关的问题有关;在模塑阶 段,操作人员应能生产了质量好的熔体,在自测 的基础上保证熔体从喷嘴自由流出 每1套模具 和每种砂料都不同,因此无法概括好的熔体如何 可得到,操作人员的经验和加工需要成为最终点 决定因素
注塑品常見缺陷解決辦法
•在塑制品的质量出现问题,应从模具设计 和制造精度、成型条件、成型材料Байду номын сангаас成 型前后的环境4个方面来考虑 下面给出常 见的问题及改时办法
注塑品常見缺陷解決辦法
•注塑制品表面缺陷 1.充填不足原因在于:供料不足;压力不够;加
热不当;注塑时间不够;模具温度过低;夹入 空气造成反压;多模腔中,各模腔的流道不平衡
值.
注塑品常見缺陷解決辦法
•注塑制品表面缺陷 2 .1模多腔时某些型腔不能充填 成型条件的改进:减小浇口充满前的注射速度,提
塑胶产品外观常见不良分析

塑胶产品外观常见不良分析塑胶产品在日常生活中被广泛使用,它们可以用于制作各种产品,如家庭用品、工业部件、玩具等。
由于制作工艺以及原材料的原因,塑胶产品的外观常常会出现一些不良,这不仅会影响产品的美观度,还有可能影响产品的性能和使用寿命。
对于塑胶产品的外观不良分析非常重要。
下面我们将对常见的塑胶产品外观不良进行分析。
一、表面缺陷1. 水波纹水波纹是指塑胶产品表面出现的波纹状不平整,通常是由于注塑时模具温度不均匀或注射压力不稳定造成的。
如果注射速度过快或者模具表面磨损,也会导致水波纹的出现。
水波纹不仅影响塑胶产品外观美观度,还可能降低其强度和耐磨性。
2. 毛刺毛刺是指塑胶产品表面出现的细小而锋利的突起,在注塑工艺中,毛刺通常是由于模具设计不当或者模具磨损严重造成的。
毛刺会影响产品的手感和安全性,同时也会影响产品的使用寿命。
3. 烧结烧结是指塑胶产品表面出现的凹凸不平的现象,通常是由于模具温度设置不当或者注塑过程中料温不均匀导致的。
烧结会影响产品的美观度和尺寸精度,严重时还会导致产品的性能下降。
二、色差1. 色泽不均匀在注塑过程中,如果原料的分散性不好或者混料不均匀,就会导致塑胶产品的表面色泽不均匀。
这不仅会影响产品的外观质量,还会影响产品的一致性和品质稳定性。
三、气泡气泡是指塑胶产品表面或内部出现的空洞状现象,通常是由于注塑过程中原料受潮或者含有挥发性成分,或者注射压力不足造成的。
气泡会影响产品的外观质量和性能稳定性,甚至会导致产品的强度和密封性下降。
四、变形针对上述常见的塑胶产品外观不良,我们可以采取一些措施来进行预防和解决。
对于表面缺陷,我们可以通过优化模具设计,提高模具制造精度和加工质量,以及优化注塑工艺参数来减少水波纹、毛刺和烧结的出现。
对于色差问题,我们可以选择优质的原料并保证混料均匀,严格控制注塑工艺参数,尽量避免色泽不均匀和色斑的出现。
对于气泡和变形问题,我们可以在原料筛选和混合过程中严格控制原料含水量和挥发性成分,保证原料质量。
电阻外观不良报告
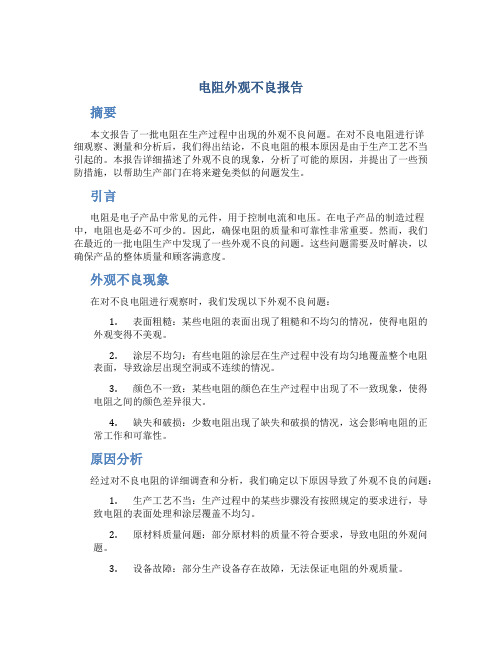
电阻外观不良报告摘要本文报告了一批电阻在生产过程中出现的外观不良问题。
在对不良电阻进行详细观察、测量和分析后,我们得出结论,不良电阻的根本原因是由于生产工艺不当引起的。
本报告详细描述了外观不良的现象,分析了可能的原因,并提出了一些预防措施,以帮助生产部门在将来避免类似的问题发生。
引言电阻是电子产品中常见的元件,用于控制电流和电压。
在电子产品的制造过程中,电阻也是必不可少的。
因此,确保电阻的质量和可靠性非常重要。
然而,我们在最近的一批电阻生产中发现了一些外观不良的问题。
这些问题需要及时解决,以确保产品的整体质量和顾客满意度。
外观不良现象在对不良电阻进行观察时,我们发现以下外观不良问题:1.表面粗糙:某些电阻的表面出现了粗糙和不均匀的情况,使得电阻的外观变得不美观。
2.涂层不均匀:有些电阻的涂层在生产过程中没有均匀地覆盖整个电阻表面,导致涂层出现空洞或不连续的情况。
3.颜色不一致:某些电阻的颜色在生产过程中出现了不一致现象,使得电阻之间的颜色差异很大。
4.缺失和破损:少数电阻出现了缺失和破损的情况,这会影响电阻的正常工作和可靠性。
原因分析经过对不良电阻的详细调查和分析,我们确定以下原因导致了外观不良的问题:1.生产工艺不当:生产过程中的某些步骤没有按照规定的要求进行,导致电阻的表面处理和涂层覆盖不均匀。
2.原材料质量问题:部分原材料的质量不符合要求,导致电阻的外观问题。
3.设备故障:部分生产设备存在故障,无法保证电阻的外观质量。
预防措施为了解决电阻外观不良的问题,并确保今后不会再次发生类似的情况,我们采取了以下预防措施:1.改进生产工艺:优化生产过程中的关键步骤,确保电阻的表面处理和涂层覆盖均匀。
2.严格把控原材料质量:建立严格的原材料进货检验流程,确保所采购的原材料符合要求。
3.定期维护和检修设备:制定设备维护计划,定期检修生产设备,确保其正常运行并符合要求。
4.强化质量控制:加强对电阻外观的质量控制,设立专门的质量检验岗位,提升产品质量。
外观不良d报告

1D:团队
分析团队:
团队长:总监
成员:
审核团队:
团队长:
成员:
批准人员:供应商领导:
2D:问题描述
产品型号:
发生时间:
检验数:
产品类型:PCM
异常类别:外观不良
不良数:
现象:
1、2015年9月9日贵司试产HB366481的来料不良图片,其中脏污不良0.99%,定位孔不良104PCS,异物、压伤不良48PCS,不良率1.98%,
6D:永久纠正行动:
1.钻孔后针对毛刺突出不良,安排刮毛刺处理(要求,孔径必须合格),钻孔后增加除胶渣流程,减少孔壁粗糙度
2.入检验标准对员工进行培训;
7D:防止问题再发生的措施
1.针对所有新项目样品研发阶段必须严格执行合同评审制度,针对特殊工艺或软硬结合产品要求研发部门必须组织工程、生产、工艺、品质共同评估工艺及操作可行性,确定相关检验标准和验证方案并形成有效记录和控制计划来指导一线生产;
此板为无卤素材料,材料脆性较大,钻孔后孔内位置毛刺无法避免,因毛刺未及时处理,阻焊之后孔内油墨不易显影完全,存在油墨残留现象
3、黑油物产生原因:
从不良图片分析,此不良为黑油印刷前,清洁不足导致,近期无尘车间改造,造成外来杂物增加,生产过程中清洁不到位容易导致杂物残留
4、不良流出原因:
1.
2.
此板为试产样品,检查人员检板过程中,为尽量满足多交货,针对部Βιβλιοθήκη 外观缺陷问题板未做报废,导致不良流程
2、此板为打样试产板,目前我司仓库已无该板库存,在线有小批量试产板6.5K在钻孔工序,将不良信息反馈给产线,重点管控以上不良
3D:原因分析
1、脏污产生原因:
塑胶产品外观常见不良分析
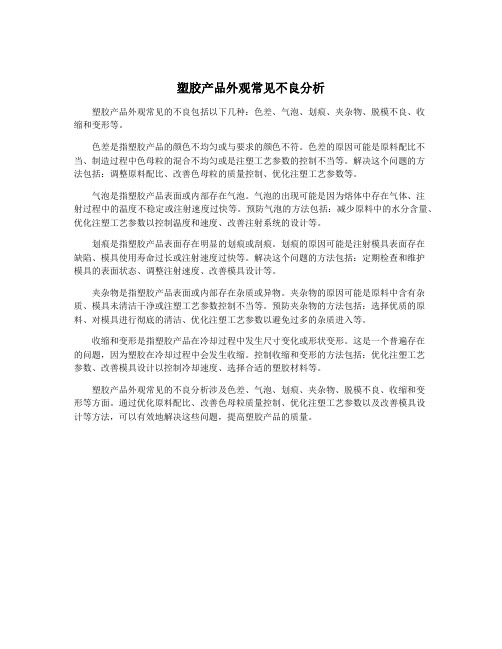
塑胶产品外观常见不良分析塑胶产品外观常见的不良包括以下几种:色差、气泡、划痕、夹杂物、脱模不良、收缩和变形等。
色差是指塑胶产品的颜色不均匀或与要求的颜色不符。
色差的原因可能是原料配比不当、制造过程中色母粒的混合不均匀或是注塑工艺参数的控制不当等。
解决这个问题的方法包括:调整原料配比、改善色母粒的质量控制、优化注塑工艺参数等。
气泡是指塑胶产品表面或内部存在气泡。
气泡的出现可能是因为熔体中存在气体、注射过程中的温度不稳定或注射速度过快等。
预防气泡的方法包括:减少原料中的水分含量、优化注塑工艺参数以控制温度和速度、改善注射系统的设计等。
划痕是指塑胶产品表面存在明显的划痕或刮痕。
划痕的原因可能是注射模具表面存在缺陷、模具使用寿命过长或注射速度过快等。
解决这个问题的方法包括:定期检查和维护模具的表面状态、调整注射速度、改善模具设计等。
夹杂物是指塑胶产品表面或内部存在杂质或异物。
夹杂物的原因可能是原料中含有杂质、模具未清洁干净或注塑工艺参数控制不当等。
预防夹杂物的方法包括:选择优质的原料、对模具进行彻底的清洁、优化注塑工艺参数以避免过多的杂质进入等。
收缩和变形是指塑胶产品在冷却过程中发生尺寸变化或形状变形。
这是一个普遍存在的问题,因为塑胶在冷却过程中会发生收缩。
控制收缩和变形的方法包括:优化注塑工艺参数、改善模具设计以控制冷却速度、选择合适的塑胶材料等。
塑胶产品外观常见的不良分析涉及色差、气泡、划痕、夹杂物、脱模不良、收缩和变形等方面。
通过优化原料配比、改善色母粒质量控制、优化注塑工艺参数以及改善模具设计等方法,可以有效地解决这些问题,提高塑胶产品的质量。
质量控制部年度不良品分析

质量控制部年度不良品分析一、引言质量控制部是企业内部重要的部门之一,其主要职责是确保产品的质量符合标准和客户的要求。
然而,在生产过程中,不可避免地会出现一些不良品。
因此,对不良品进行年度分析,对于提高产品质量和生产效率具有重要意义。
本文将对质量控制部的年度不良品进行详细分析,并提出改善措施。
二、不良品分类1. 外观缺陷类不良品外观缺陷类不良品是指产品外观出现的瑕疵或损坏,例如划痕、凹痕、变色等。
在过去一年中,外观缺陷类不良品占据了总不良品数的30%。
主要原因是生产线上操作人员对产品外观的检查不够严谨,存在疏忽的情况。
2. 尺寸偏差类不良品尺寸偏差类不良品是指产品尺寸与设计要求存在偏差,无法达到预期的使用效果。
在年度不良品中,尺寸偏差类不良品占比为20%。
导致此类不良品的原因多数是由于设备的质量问题或者操作人员对设备的维护不善。
3. 功能故障类不良品功能故障类不良品是指产品在正常使用过程中出现的故障或无法正常运行。
在年度不良品中的占比为35%。
此类不良品主要是由于生产过程中零部件的不合格,导致产品功能无法得到有效保证。
4. 包装不良类不良品包装不良类不良品指产品在包装过程中出现的问题,例如包装破损、错标等。
该类不良品在年度不良品中占据了15%。
主要原因是在包装过程中操作人员的不细心或者包装材料的质量问题。
三、不良品分布分析对于质量控制部而言,了解不良品部门间的分布情况对于合理调配资源、提升整体质量有重要作用。
本年度不良品分布较为广泛,主要集中在生产车间A、B和D,分别占比45%、30%和25%。
四、不良品原因分析1. 人为因素人为因素,包括操作人员的技术熟练度、操作不规范以及生产线上的管理不到位等。
在年度不良品原因中,人为因素占比50%。
为了减少人为因素对不良品的影响,需要加强对操作人员的培训,并建立更严格的生产管理机制。
2. 设备问题设备问题包括设备的老化、维护不当以及质量不过关等。
在不良品原因中,设备问题占比30%。
- 1、下载文档前请自行甄别文档内容的完整性,平台不提供额外的编辑、内容补充、找答案等附加服务。
- 2、"仅部分预览"的文档,不可在线预览部分如存在完整性等问题,可反馈申请退款(可完整预览的文档不适用该条件!)。
- 3、如文档侵犯您的权益,请联系客服反馈,我们会尽快为您处理(人工客服工作时间:9:00-18:30)。
5).由进浇口到结合部的距离长的场合 由进浇口到结合部的距离长,則树脂温度大幅降低,此时必需追加 进浇口,变更位置. 6).排气不良的场合 汇集于融合部的空气.挥发分.水分.离模剂等影响树脂的融合,因 此需设置排气销.排气勾或利用顶出梢排气,设置樹脂的滞留区,並需 清除模具,干燥树脂. 7).进浇口的位置与数量不适当 可能的话尽量減少分流,进浇口位置需设于结合线不显眼位置与 不施加力量的地方.
改善对策:
1)增高聚合物温度及模具温度,充填中的聚合物保持高温,在 低粘度状态充填,即可防止. 2)聚合物的充填速度过慢时,充填中降溫,发生波纹.增大射 出柱塞的速度及压力,或施行外部润滑剂处理,防止压力损 失即可. 3) 模具的冷卻水沟位置在浇口部或其附近时,或在薄肉处时, 聚合物温度下降而充填成形空间,或聚合物温度的下降超出。 必要以上时,故易发生.此时须修正冷却水沟的位置. 4 )喷嘴过小的話,喷嘴部的聚合物温度易下降,在射出初期 压或粘度增高,引起压力降低.发生波纹. 5) cushion量(射出后残留的熔融聚合物)少的话,聚合物停滞, 加热筒內的时间短,实际的聚合物温度比指示温度低.因而 须增加cu-shion,加热筒內有充分的停滯时间升高聚合物 温度. 6)无熔渣积存部,或虽有而过小時,也会充填低温的聚合物, 造成冷流痕.
流 痕(FLOW MARKS)
定义:
(一)熔融材料流动的痕迹,以浇口为中心而呈现的条纹模样. 原因分析 1 流痕是最初流入成形空间內的材料冷却过快,而与其后流入的材 料间形成界限所致.为了防止流痕,可增高材料温度,改善材料流动性 ,调整射出速度. 2 殘留于射出成型机喷嘴前端的冷材料,若直接进入成形空间內,则 会造成流痕,因此在主道与流道的汇合处或流道与分流道的交接处 设充分的滯料部,可有效的防止流痕的发生.同时,亦可增大浇口的尺 寸来防止. 3在成形空間內,聚合物溫度下降,成高粘度狀態充填,接觸模面的聚 合物在半固化狀壓入,表面發生垂直流向的無數細紋,聚合物溫度再 下降時,不完全充填就固化,造成充填不足
毛边(BURR&FLUSH)
定义:
熔融塑料流入分模面或侧向蕊型的对合面间隙会发生 BURR;模具锁模力足夠,但在浇道与横流道汇合处长生薄 膜状多余树脂为F锁模力不足,塑料高压射入模具内时会在分模 面发生间隙,塑料由此缝流出. 对策:调整锁模力,提高锁模吨数.如已调至该机台最大 锁模力还无法改善,可更换较大型机台成型. (2)模具(固定侧)未充分接触喷嘴,模具发生间隙时. 对策:调整足射座顶力.
烧焦/包风(BURN MARKS)
定义:
一般所谓的烧焦(burn marks),包括成形品表面因材料过热 所致的变色及成型品的锐角部份或轂部.肋的前端等材料焦黑的 现象.烧焦是滯留成型空间內的空气,在熔融材料进入时未能迅 速排出,被压缩而显著升温,再将材料烧焦所致. 烧焦之有效防止对策是在易聚集空气部位设置排气孔或 利用顶出销,芯型销等的间隙,使残留空气急速排出.再者,可降 低材料温度.減低射出速度及射出压力或加大浇口尺寸.
定义:
黑条(Black Streaks)指成型品有黑色条纹的现象,其发生 的 主要原因是成形材料的热分解所致,常见于热安定性不良的材料. 有效防止黑条发生的对策是防止加热缸内的材料温度过高,減慢 射出速度.加热缸内壁或螺杆,若有伤痕或缺口,则附着于此部份 的材料会过热,引起热分解.逆流防止阀亦会因材料滯留而引起 熱分解,所以黏度高的材料或容易分解的材料要特別注意防止黑 条的发生
(3)模具导锁磨损,分模面偏移或模具安装板受损,导杆(大 柱)强度不足发生弯曲时. 对策: a更换模具销. b模具安装板整修. c模具重量超重 应更换较大机台成型. (4)异物附着模面时. 对策:清除模面异物.
(5) 成型品投影面过大或树脂(塑料)温度太高. 对策:(a)更换较大机台. (b)降低塑料温度.
银条(SLIVER STERAKS)
定义:银条(sliver streak)是在成型品表面或表面附近,沿材料流动方 向,呈现的银白色条纹.其发生大都是成形料中的水分或挥发物或附 着模具表面的水分等汽化所致,射出成型的螺杆卷入空气时也会发生 银条.防止其的对策是首先充分干燥成型材料,再者,增高模具温度.降 低材料温度.减慢射出速度.降低射出压力及升高螺杆背压等
噴流痕(JETTING MARKS)
定義:
噴流痕是熔融塑料由澆口往成型空間(模穴)內 射出時呈紐帶狀固化,而在成型品表面成蛇行狀態.使用側狀 澆口的成型品,在材料流路中無滯料部或不充足時,容易產生 噴流痕,原因是急速通過澆口的冷材料直接進入成型空間,然 后接觸成型空間表面而固化,接著被隨后進入的熱材料推流, 而殘留蛇行痕跡.
(5)流道中冷料井预留不足或不当,冷料头进入成型品而阻碍塑料 之正常流动充满模穴. 对策: 增加冷料井储存空间或打多段射出移开冷料头使塑料充 填顺畅. (6)模具温度太冷,塑料在某一特定压力下流动困难. 对策: 斟酌生产上实际需要,提高模具温度. (7)排气不良時,空气无法排除. 对策:防火級ABS成型时,挥发性气体殘渣,易造成模垢而发生排 气口阻塞现象,应定期清除之.
(4)螺杆有空气卷入的场合储料桶下的冷却充分,则储料桶侧的温度低,与加 热缸筒有温度差,则树脂经常擦伤螺杆,另外降低螺杆转数,增高背压,原料 受压缩则空气由储料桶侧排出. (5)树脂含水分.挥发物的场合有吸湿性的压克力树脂(ABS.AS.聚醯胺.聚 碳酯)等必需预先干燥 (6).模具温度低的场合 树脂迅速固化则引起排气不完全,因此需提高模温. (7).横浇道.进浇口过小的场合因流动阻力增大,填充速度慢,树脂迅速固化. 所以必需加大进浇口.横浇道. (8).模具的排气不良的场合模具排气不良的话,可以增设排气沟,或排气梢. (9).模具制品面有油或水分,或付着脱模剂场合模具制品面有油或水分或附 着脱模剂时,因树脂热蒸发而成气体状,随着树脂的冷却固化而液化.所以需 清除模具,并限制离模剂的使用.
原因与对策:
1).塑料润滑剂不足时,严重发生摩擦热,且因排气不良而引起燃烧. 对策: 添加适当润滑剂,但如超过0.2%的剂量时,润滑剂的可燃、 性挥发物,反令燃烧容易发生而产生黑条. 2).成型品小,料管尺寸太大,塑料滯留太久而分解. 对策: 更换机台或更换较小螺杆. 3).螺杆局部受损或逆流环间隙大. 对策: 更换螺杆或逆流环. 4).塑料异常升温,引起塑料局部分解. 对策: 检修料管温度 5).螺杆塑粒咬入不良卷入过多空气. 对策: 适当加大背压
(二)以进浇口为中心在表面上出现指纹状的格子模样, 在树脂温度低的高粘度动性不佳的树脂与模穴接触,是成半固化 状态被压入,所以在与流动方向垂直的方向产生很多细的皱纹的 现象. 1 树脂温度低的场合:树脂温度低则粘度增高而发生流痕, 如此需增高树脂温度。 2 模具温度低的场合:低温則夺走大量的树脂热,使树脂 温度下降,粘度增高而发生流痕. 3 射出速度慢的場合:速度慢,树脂温的降低增大,粘度增 高而发生流痕则需提高射出速度. 4 进浇口部与薄肉部在必要冷却温度以上的场合进浇口部 与薄肉部在必要冷却温度以上时,树脂温度显著地降低,粘度增 高,则需調整冷却水温与肉厚. 5 无冷料滞留区或太小的场合以冷的高粘度树脂压入模穴 部时,必需设置适当的冷料滞留区
原因:
烧焦現象是成型品最远离浇口的末端或接合部的融熔塑料 排气不良引起压缩燃烧之残痕. 1).降低射出压力,但应注意压力下降后射速随之減慢容易造 成流痕及熔合线之产生. 2).采用多段射出,在成型过程末端分多段減速以利多余气体 排出. 3).采用真空泵抽取模穴內之空气,使模穴成真空状态而成型.
黑条(BLACK STREAKS)
外观件不良现象及解决方法
缩水/凹陷(SINK MARKS)
定义:成型品表面产生凹陷的现象.这是体积收缩所致,通常见于肉 厚部分、肋或凸出的背面、肉厚不均的部份.
1)射出压低的场合:射出压低则树脂的压缩不完全而产生收缩下陷,最好提高射出 压. 2)射出压保持时间短的场合:射出压保持时间短,则无法弥补树脂的热收缩量,另外 也容易造成回流(back flow),而发生压缩不完全,因此延长射出保持时间 3)射出速度过慢、过快的场合:太慢的话,固化即刻开始,压力传达不足,因此需加 快射出速度.太快的话,仅能填充少量,所以要减缓射出速度,增加计量. 4)射出量少的场合:射出量少则树脂的压缩比少,因此需加射出 5)树脂温度高,模温高的场合,因为冷却速度慢,收缩不完全而产生收缩下陷,因此 最好降低树脂温度及模温. 6)横浇道、进浇道狭小场合:横浇道、进浇道狭小的话,压力损失增大,树脂压降低, 则压缩不完全.如果加大进浇口而横浇道维持原状的话,会使长的横浇道压力损 失是进浇口的数倍,因此不仅考虑进浇口,对横浇道也不能忘.太大的横浇道将会 浪费材料,因此不可随便加大. 7)有厚肉部与宽的补强肋的场合:普通补强肋厚度需控制在壁厚的0.5~0.8倍以内, 距离进浇口远的位置或容易造成收缩下陷问题的位置,尽量减小补强肋的肉厚.另 外,为了缩小与周围的热收缩差,由周边部补强肋.由根部渐渐增加肉厚. 8)模具冷却不适当的场合:模具冷却不适当将使热收缩不均一,因此厚肉部与补强
原因: 1).塑料中含有水份或挥发性成份.2).塑料在料管中滞留过久.3).塑料在料 管中异常升温,部份塑料分解.4).模具排气沟堵塞或排气不良.5).润滑剂或水份附着 模具表面.6).粉碎料中含有细微颗粒多.7).异种塑料混入.8).螺杆卷入过多的空气 沒有排出.9).针点或潜入式浇口因射速太快,引起塑料升过剧部份塑料分解.10).模 穴表面温度太低. 对策: (1)射出容量.可塑化能力不足的场合初期射出的树脂迅速固化,因而气体的排出不 完全发生阴线.此时, 需采压力大的机械. (2)树脂滞留或过热的场合由树脂所发生的气体量多,这些排出不完全而固化时会 产生银线,因此需清除加热缸,并下降树脂温度. (3)射出压过高.射出速度过快的场合有急速的肉厚变化的话,流动中的压缩树脂急 速地减压而膨胀,挥发分解气体与模穴接触后液化,因此需降低射出压.射出速度, 并减小肉厚变化情况.