去除淬火油中水分方法的研究
黄铜钝化Word 文档

1 前言黄铜是一种铜锌合金材料,因其优异的性能被广泛地应用于仪器仪表、医疗设备、轻工制品、小五金及电子等领域。
由于外环境的影响,黄铜件极易变色,为此,黄铜制品必须经过表面防腐处理方可使用。
对黄铜件而言,比较有效的表面防腐处理方法是重铬酸盐钝化处理。
为了丰富钝化膜的外观色泽,获取抗变色性能更好的钝化膜,我们探讨了钝化工艺对外观色泽及抗变色性能的影响。
2 实验2.1 原料浓硫酸(CP)、浓硝酸(CP)、浓盐酸(CP)、碳酸钠(CP)、磷酸钠(CP)、硅酸钠(CP)、OP乳化剂(工业级)、重铬酸钾(CP)、氯化钠(CP)、黄铜(含Cu 60%)2.2 钝化工艺一步钝化工艺:化学除油→水洗→预酸洗液→水洗→混酸浸蚀→水洗→钝化(钝化液1号)→水洗→干燥二步钝化工艺:化学除油→水洗→预酸洗液→水洗→混酸浸蚀→水洗→钝化(钝化液1号)→钝化(钝化液2号)→水洗→干燥2.3 配方及工艺条件化学除油:碳酸钠10~20 g/L,磷酸钠10~20 g/L,硅酸钠10~20 g/L,OP乳化剂2~3 g/L,温度70~80℃。
预酸洗液:硫酸100~150 ml/L,盐酸30~50 ml/L,温度20~30℃,时间30~60 s。
混酸浸蚀液:硫酸25%~30%,硝酸12%~15%,盐酸0.5%~1.0%,食盐5%,余量为水,温度为20~30℃。
注意:如盐酸不足,浸蚀后的基体泛白,钝化膜色泽不均匀,有彩虹:如盐酸过量,浸蚀后的基体呈紫红色,钝化膜发黑。
加入食盐的目的是消除基体表面的纤维状条纹。
钝化液1号:硫酸(25%)1000 g,重铬酸钾65 g,温度20~30℃。
钝化液2号:硫酸(10%)1000 g,重铬酸钾65 g,温度20~30℃。
3 结果与分析3.1 黄铜件钝化前的酸蚀处理金属基体的表面性质对钝化效果产生极大的影响,只有在活性高的表面上才能得到性能优异的钝化膜。
混酸浸蚀的目的是均匀地溶掉一层金属,以使基体露出新鲜的、活性更高的表面,有利于后续的钝化处理。
黄铜钝化Word 文档

1 前言黄铜是一种铜锌合金材料,因其优异的性能被广泛地应用于仪器仪表、医疗设备、轻工制品、小五金及电子等领域。
由于外环境的影响,黄铜件极易变色,为此,黄铜制品必须经过表面防腐处理方可使用。
对黄铜件而言,比较有效的表面防腐处理方法是重铬酸盐钝化处理。
为了丰富钝化膜的外观色泽,获取抗变色性能更好的钝化膜,我们探讨了钝化工艺对外观色泽及抗变色性能的影响。
2 实验2.1 原料浓硫酸(CP)、浓硝酸(CP)、浓盐酸(CP)、碳酸钠(CP)、磷酸钠(CP)、硅酸钠(CP)、OP乳化剂(工业级)、重铬酸钾(CP)、氯化钠(CP)、黄铜(含Cu 60%)2.2 钝化工艺一步钝化工艺:化学除油→水洗→预酸洗液→水洗→混酸浸蚀→水洗→钝化(钝化液1号)→水洗→干燥二步钝化工艺:化学除油→水洗→预酸洗液→水洗→混酸浸蚀→水洗→钝化(钝化液1号)→钝化(钝化液2号)→水洗→干燥2.3 配方及工艺条件化学除油:碳酸钠10~20 g/L,磷酸钠10~20 g/L,硅酸钠10~20 g/L,OP乳化剂2~3 g/L,温度70~80℃。
预酸洗液:硫酸100~150 ml/L,盐酸30~50 ml/L,温度20~30℃,时间30~60 s。
混酸浸蚀液:硫酸25%~30%,硝酸12%~15%,盐酸0.5%~1.0%,食盐5%,余量为水,温度为20~30℃。
注意:如盐酸不足,浸蚀后的基体泛白,钝化膜色泽不均匀,有彩虹:如盐酸过量,浸蚀后的基体呈紫红色,钝化膜发黑。
加入食盐的目的是消除基体表面的纤维状条纹。
钝化液1号:硫酸(25%)1000 g,重铬酸钾65 g,温度20~30℃。
钝化液2号:硫酸(10%)1000 g,重铬酸钾65 g,温度20~30℃。
3 结果与分析3.1 黄铜件钝化前的酸蚀处理金属基体的表面性质对钝化效果产生极大的影响,只有在活性高的表面上才能得到性能优异的钝化膜。
混酸浸蚀的目的是均匀地溶掉一层金属,以使基体露出新鲜的、活性更高的表面,有利于后续的钝化处理。
金属热处理选择题库+答案

金属热处理选择题库+答案一、单选题(共90题,每题1分,共90分)1、以下哪种铸铁的断口呈灰黑色()。
A、马口铁B、灰铸铁C、麻口铸铁D、白口铸铁正确答案:B2、不适宜进行锻造的铁碳合金有()。
A、共析钢B、亚共析钢C、亚共晶白口铁D、过共析钢正确答案:C3、DQ120-27中,Q代表的含义是()。
A、桥梁板B、抗拉强度C、屈服点D、取向硅钢正确答案:D4、轧件在轧制时,摩擦系数越大,轧件的宽展()。
A、不确定B、不变C、越大D、越小正确答案:C5、由于热处理工件的质量是加热温度和时间的(),因此,在编制热处理工艺时,加热时间是十分重要的。
A、正数B、函数C、分数D、倍数正确答案:B6、金属材料最适合切削加工的硬度应在()。
A、170-230HBWB、180-210HBWC、230-230HBWD、150-180HBW正确答案:A7、在切削加工前安排预先热处理,一般说来低碳钢采用()。
而高碳钢及合金钢正火硬度太高,必须采用退火。
A、回火B、淬火C、退火D、正火正确答案:D8、过冷奥氏体在低于Ms时,将发生()转变。
这种转变虽有孕育期,但转变速度极快,转变量随温度降低而增加,直到Mf点才停止转变。
A、奥氏体B、珠光体C、渗碳体D、马氏体正确答案:D9、疲劳试验时,试样承受的载荷为()。
A、应力载荷B、静载荷C、冲击载荷D、交变载荷正确答案:D10、()是延长工装夹具寿命的错误方法。
A、对底盘、料盘等工具经常进行正、反交替使用B、用多点悬挂支撑来代替单点悬挂支撑以平衡工件重量C、将圆筐改为方筐D、增加焊接加强肋以提高板或框架的牢固程度正确答案:C11、固体渗碳时,为了不使工件表面的碳浓度过高,防止出现网状或粗大的碳化物,一般将新、旧渗碳剂混合使用,它们的比例为()。
A、新渗碳剂 40%, 旧渗碳剂 60%B、新渗碳剂 50%, 旧渗碳剂 50%C、新渗碳剂 20%, 旧渗碳剂 80%D、新渗碳剂 30%,旧渗碳剂 70%正确答案:D12、高速钢的热硬性可达(),切削时能长期保持刃口锋利,故又称为锋钢。
淬火油检测标准

淬火油检测标准
淬火油检测标准主要包括以下几个方面:
1. 外观检查:检测淬火油的颜色、透明度、杂质等外观特征,应符合规定的要求。
2. 粘度检测:通过测量淬火油的粘度来确定其流动性,一般使用粘度计进行测定。
3. 水分含量检测:淬火油中的水分含量是影响其性能的重要指标,可以通过气相色谱法或湿度计进行测量。
4. 酸值检测:酸值是衡量淬火油酸性的指标,可以使用酸度计或滴定法进行检测。
5. 碱值检测:碱值是衡量淬火油碱性的指标,可以使用滴定法进行测定。
6. 抗氧化性能检测:通过模拟淬火工艺中的高温环境,评估淬火油的抗氧化性能,一般使用氧指数试验或模拟实验进行检测。
7. 总碱检测:总碱是淬火油中酸性组分与碱性组分的综合指标,可以通过滴定法进行测定。
8. 渗漏性能检测:检测淬火油在高温下的渗漏情况,常用方法有斜坡试验和滴油法。
以上仅为一般淬火油检测标准的基本内容,具体的标准和方法会根据不同国家和行业的要求而有所差异。
水作为淬火介质的缺点及克服方法

水作为淬火介质的缺点及克服方法Water as a quenching medium to overcome the shortcomings and methods摘要:水的冷却特性很不理想,很容易造成淬火工件的变形或开裂。
此外,水温对水的冷却特性影响很大,但是,水因其成本低等原因,仍然是广泛采用的淬火介质之一。
所以有必要讨论水作为淬火介质的缺点和解决方法。
关键词:自来水开裂变形克服方法1水作为淬火介质的缺点多数工件用自来水淬火会开裂,淬裂的原因是众所周知的:自来水的低温冷却速度太快。
这是自来水的一大缺点。
用水作冷却介质,还遇到另外的问题。
例如,多个工件采取比较密集的方式同时入水时,淬火后会有显著的硬度差异。
又如,工件上有较深的内孔、工件为大薄片状、以及形状复杂时,水淬后往往出现严重的硬度不均和较大的淬火畸变。
同样的情况,在油中淬火时,则不会发生这样严重的问题。
引起这些问题的原因是,水的冷却特性对水温变化太敏感。
图1a是温度对自来水冷却特性的影响曲线。
容易推知,当单个工件在自来水中淬火时,由于形状或所处位置的原因,工件不同部位的表面接触的水温是不同的:工件上的凹进部分接触的水温高,而突出部分接触的水温则相对要低些。
位于下面部分接触的水温较低,上面部位接触的水温较高。
当多个工件以比较密集装挂的方式同时入水时,位于外面的工件接触的水温较低,而内部的工件接触的水温则较高。
再加上同一工件朝外的面接触的水温较低,朝里的面接触水温则较高。
不同的水温对应不同的冷却特性,其结果就引起了上述种种问题。
图1b 为温度对油的冷却特性的影响曲线。
由图1的对比,可以看出水温对冷却特性的影响是很大的。
我们把冷却特性对液温变化太敏感列为自来水的第二大缺点。
有机聚合物水溶液,比如PAG淬火液、聚乙烯醇水溶液等也都有相同的缺点。
图1c为不同液温的10%硫酸钠水溶液的冷却特性曲线。
由图1c可见,10%的无机盐(或碱)溶入水中,可以大大减小冷却特性对水温的敏感性程度。
淬火油知识

淬火油的使用常识A、淬火油的冷却原理是什么?淬火油是将金属材料加热到相变温度以上,保温一段时间后迅速地投入到介质中冷却,得到马氏体组织,这种操作过程称为淬火。
钢在介质中冷却是以3种不同的方式进行热量传递的。
1、第一阶段即蒸气膜阶段,这个阶段的冷却速度很低。
随着冷却时间的延长,零件温度不断下降,蒸气膜稳定性也逐渐降低,最后因蒸气膜破裂而进入第2阶段。
2、第二阶段为沸腾阶段。
当蒸气膜破裂并消失以后,使淬火介质直接与零件表面接触,淬火介质就从零件上吸取大量的热量。
阻碍着淬火介质的流动,吸收了热量的介质不断逸出大量的气泡,而新的介质继续在零件周围激烈沸腾,形成沸腾阶段。
这时冷却速度最大。
随着零件温度不断下降,沸腾现象渐趋消失。
当零件温度低于淬火介质的沸点时,沸腾现象立即消失,便转入第3阶段。
3、第三阶段为对流传热阶段。
零件经过沸腾阶段,周围淬火介质的温度与零件温度接近,而远离零件处的介质温度较低。
由于零件周围的淬火介质与其他地方的介质温度不同,使淬火介质产生对流现象。
对流传热阶段的冷却速度较慢。
B、特性温度、特性时间、对流起始温度指的是什么?是怎样确定的?淬火油特性温度是指蒸气膜破裂即沸腾阶段开始的温度相对应的时间为特性时间,是根据冷却过程曲线描绘出来的,即根据冷却曲线上部出现的明显突区,沿突变区作两条切线,切线相交点A为特性点,A点所对应的纵坐标(温度坐标)为特性温度、A点所对应的横坐标(时间坐标)为特性时间。
对流起始温度是指沸腾阶段结束,对流起始阶段开始的温度,也是根据冷却过程曲线描绘出来的,即沿冷却曲线下部出现的突变区作两条切线,切线相交点B为另一特性点,B点所对应的纵坐标(温度坐标)即为对流阶段起始温度。
这几项指标是评价淬火油很重要的指标。
C、淬火油从800℃冷却到400℃时间的意义是什么?钢淬火的目的是为了获得马氏体或下贝氏体组织,从而使零件具有高硬度、高疲劳强度、高耐磨性等,要达到这个目的,就要求淬火介质的冷却速度必须大于临界冷却速度,即要求淬火油特性温度高,800℃冷却到400℃的时间短,以躲过“C”曲线鼻尖区,即奥氏体不稳定区,避免淬火零件向珠光体类型的组织转变,从而获得所需要的马氏体组织或下贝氏体组织。
淬火油曲线

淬火油曲线
淬火油曲线是指淬火油冷却过程中的温度变化曲线,通常用于评估淬火油的冷却性能。
淬火油冷却过程可以分为三个阶段:
1. 蒸汽膜阶段:在这个阶段,淬火油中的水分形成蒸汽膜,使得油膜和工件之间的传热速率下降,导致工件冷却速度下降。
2. 沸腾冷却阶段:在这个阶段,蒸汽膜被破坏,油膜和工件之间的传热速率增加,工件冷却速度加快。
3. 对流冷却阶段:在这个阶段,由于油的粘度增加,传热速率再次下降,导致工件冷却速度减缓。
淬火油曲线可以通过测量淬火油在不同温度下的冷却速率来得到。
通常使用的方法是在淬火油中放置一个温度传感器,并测量其温度变化。
随着淬火油的冷却,传感器的温度会下降,通过测量温度变化的速率,可以计算出淬火油的冷却速率。
通过绘制淬火油温度变化曲线,可以观察到上述三个阶段的冷却过程,并评估淬火油的冷却性能。
淬火油的常识
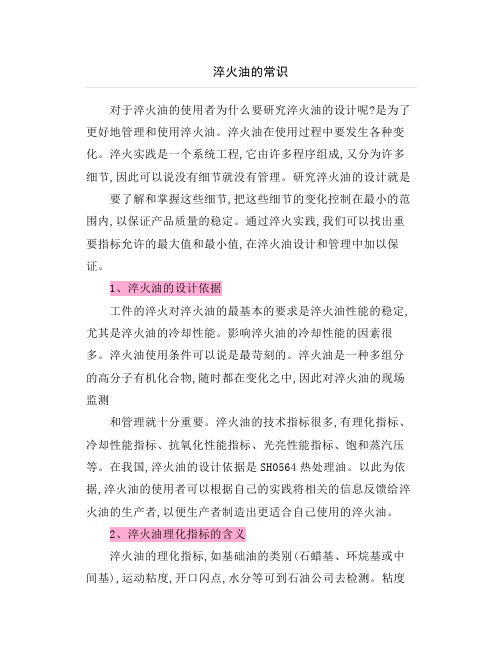
淬火油的常识对于淬火油的使用者为什么要研究淬火油的设计呢?是为了更好地管理和使用淬火油。
淬火油在使用过程中要发生各种变化。
淬火实践是一个系统工程,它由许多程序组成,又分为许多细节,因此可以说没有细节就没有管理。
研究淬火油的设计就是要了解和掌握这些细节,把这些细节的变化控制在最小的范围内,以保证产品质量的稳定。
通过淬火实践,我们可以找出重要指标允许的最大值和最小值,在淬火油设计和管理中加以保证。
1、淬火油的设计依据工件的淬火对淬火油的最基本的要求是淬火油性能的稳定,尤其是淬火油的冷却性能。
影响淬火油的冷却性能的因素很多。
淬火油使用条件可以说是最苛刻的。
淬火油是一种多组分的高分子有机化合物,随时都在变化之中,因此对淬火油的现场监测和管理就十分重要。
淬火油的技术指标很多,有理化指标、冷却性能指标、抗氧化性能指标、光亮性能指标、饱和蒸汽压等。
在我国,淬火油的设计依据是SH0564热处理油。
以此为依据,淬火油的使用者可以根据自己的实践将相关的信息反馈给淬火油的生产者,以便生产者制造出更适合自己使用的淬火油。
2、淬火油理化指标的含义淬火油的理化指标,如基础油的类别(石蜡基、环烷基或中间基),运动粘度,开口闪点,水分等可到石油公司去检测。
粘度指数:是基础油化学组成的函数。
粘度指数可以作为一种性能的标志,作为质量控制的尺度。
淬火油的粘度指数主要反映淬火油的基础油的类别。
基础油的挥发性与油耗、粘度稳定性、氧化安定性都有关系。
石蜡基油比环烷基油挥发性小,即粘度指数越高,挥发性越小。
粘度:淬火油的一个重要指标,流动物质的内摩擦力的量度叫粘度。
粘度值随温度的上升而降低,大多数的润滑油是根据粘度来划分油品牌号的。
淬火油常用的粘度是运动粘度和动力粘度。
动力粘度表示液体在一定的剪切应力下流动时内摩擦力的量度。
其值为加于流动液体的剪切应力和剪切速率之比。
在我国的法定计量单位制中,以帕/秒(Pa/s)表示,习惯上用的厘泊(cP)为非法定单位,1cP=10-3Pa/S。
- 1、下载文档前请自行甄别文档内容的完整性,平台不提供额外的编辑、内容补充、找答案等附加服务。
- 2、"仅部分预览"的文档,不可在线预览部分如存在完整性等问题,可反馈申请退款(可完整预览的文档不适用该条件!)。
- 3、如文档侵犯您的权益,请联系客服反馈,我们会尽快为您处理(人工客服工作时间:9:00-18:30)。
粒度级别大约为(6~8)级。
以此种组织再进行调质处理,就会得到较为细小的回火索氏体组织。
图4 35CrNi3MoV 钢完全退火后的组织 ×1000Fig.4 Structure of 35CrNi3MoV steel afterfull annealing ×1000 工业试验表明,采用完全退火、不完全退火、A 1温度稍下的高温回火等工艺后,获得了平衡组织,破坏了组织遗传性。
大锻件经过调质处理后,原始奥氏体晶粒显著细化,晶粒度大约为9级,如图5所示,消除了混晶和晶粒粗大的现象。
性能检验表明,产品各项的性能指标合格。
经过完全退火+调质处理后,35CrNi3MoV 钢各项力学性能指标如表2所示。
4 结论 (1)35CrNi3MoV 钢大锻件去氢退火后组织粗大,正火+调质后出现混晶,质量不合格。
(2)混晶是组织遗传造成的,为杜绝混晶和晶粒异常长大,必须将非平衡组织转变为平衡组织,再图5 调质后的原奥氏体晶粒度(9级) ×500Fig.5 Grain size of primary austenite after quenching and tempering ×500表2 经完全退火和调质处理后35C r Ni3MoV 钢的力学性能T able 2 Mechanical properties of 35C r Ni3MoV steel after fullannealing and quenching and temperingHRC σ011/MPaσb /MPaδ(%)ψ(%)(-40℃)A K V /J4112501375124630进行最终热处理。
(3)将大锻件进行完全退火、不完全退火或A 1稍下保温的高温回火,完成再结晶,可以避免混晶现象。
参考文献:[1] 戚正风.金属热处理原理[M ].北京:机械工业出版社,1987:34236.[2] 刘宗昌,杨 慧,李文学,胡永平,崔玉军.去氢退火工艺设计及应用[J ].金属热处理,2003,28(3):51253.[3] 刘宗昌,张羊换,麻永林.冶金类热处理及计算机应用[M ].北京:冶金工业出版社,1999:66275.[4] 刘宗昌,任慧平,宋义全.金属固态相变教程[M ].北京:冶金工业出版社,2003:45260.去除淬火油中水分方法的研究关晓燕1,孔繁仲2,杨景芳1,张 维1(11大庆高等专科学校物理系,黑龙江大庆 163712;21大连海事局,辽宁大连 116002)摘要:研究了去除淬火油中所含微量水的方法,分别对采用底部加热和侧部加热以及对有、无搅拌情况下加热蒸发法去除油中微量水的效果进行了测试。
结果表明,采用底部加热或在有搅拌状态下加热管内置的侧部加热方式使除水效果得到提高,但是较难达到含水量低于011%的安全生产要求。
用真空加热的方法对油中微量水的去除进行了尝试,并取得了较理想的效果。
关键词:淬火油;微量水;去除方法中图分类号:TG 15414 文献标识码:A 文章编号:025426051(2003)1220050204Method of R emoving T race W ater in Q uenching OilGUAN Xiao 2yan 1,KON G Fan 2zhong 2,YAN G Jing 2fang 1,ZHAN G Wei 1(11Daqing Advanced College ,Daqing Heilongjiang 163712,China ;21Dalian Maritime Bureau ,Dalian Liaoning 116002,China )Abstract :The method to remove the trace water in quenching oil was researched.Different heating evaporation methods such as the bottom heating ,the lateral heating as well as heating with and without stirring were adopted to measure the water contamination.The results show that although the bottom heating and heating on the stir condition are more efficient in removing the trace water in oil the water content in quenching oil is still higherthan 011%,but it is still difficultly to meet the safe production requirement.However ,a vacuum heating method was tested and a good result was achieved.K ey w ords :quenching oil ;trace water ;removing method作者简介:关晓燕(196317—),女,黑龙江哈尔滨人,吉林大学硕士生,副教授,主要从事磁学和热学在工程应用方面的研究,发表论文10余篇。
收稿日期:20032082141 引言 淬火油中含有微量水将严重影响油的冷却性能,造成淬火件光亮度下降、硬度不均、产生软点并加大工件畸变开裂倾向[1]。
研究表明,油淬产生的质量问题大多数是因油中含水造成的。
此外,油中含水还加速了油的乳化变质和促进油中添加剂的失效。
当油中含水量≥011%时,油受到加热时有可能使聚集在油槽底部的水达到沸点后,体积突然膨胀,易造成油溢出淬火油槽而引发火灾[1]。
R.T.von Bergen 通过冷却曲线测量含水量从0%~0120%的普通淬火油的冷却曲线变化情况表明,随着油中含水量的增加使对流冷却阶段的冷却速率增加(300℃的冷却速率从不含水时的8℃/s ,增加到含水0120%的40℃/s ),工件畸变和开裂倾向增大[1]。
文献[2]对快速淬火油中含水对冷却特性的影响的研究结果表明,由于微量水促使添加剂失效,导致快速淬火油的最高冷速明显下降,因此去除快速淬火油中的微量水显得更加重要。
去除淬火油中水分的传统方法是采用沉降法和加热蒸发法。
沉降法是利用水的密度大于油的密度的特性,采用抽除底部沉降的水的方法分离,该方法适合含水量较大和抗乳化能力强的淬火油,对于已乳化的油效果不佳,同时在去除过程中也将带出大量的油,并且也无法去除干净,会有大量的残留水。
加热蒸发法是将含水的油加热到100℃以上,利用水达到沸点以上将水去除,该方法具体效果如何尚未见报道。
笔者对采用底部加热和侧部加热以及有、无搅拌情况下的加热蒸发法去除油中微量水的效果分别进行了测试,并采用真空法对去除油中微量水进行了尝试,获得了较理想的结果。
2 试验方法 试验采用大连仪器厂制造的水分测定仪测量油的含水量,仪器的分辨率为0101%。
检测过程:将被测的油样搅拌均匀,取出100g倒入预先烘干的圆底烧瓶中,投入一些无釉瓷片、浮石、毛细管。
将洗净并烘干的接收器支管紧密安装在圆底烧瓶上,然后将接收器连接冷凝管,冷凝管下端的接收器有体积刻度线。
用热源在圆底烧瓶的底部进行加热蒸馏,蒸馏后的水蒸气经过冷凝管进入接收器中,当接收器中水的体积不再增加而且溶剂的上层完全透明时,停止加热。
圆底烧瓶冷却后将仪器拆卸,读出接收器中收集到的水的体积。
油样中所含的水分质量分数x 可由下式计算:x =ρV /M ×100%式中:V —在接收器中收集到的水的体积,cm 3;M —油样的质量,g ;ρ—水的密度,g/cm 3。
3 试验过程及结果 试验1:将500g 的N32机械油加热到140℃,然后倒入装有115g 水的烧杯中(相当于0130%的水),保温1h 。
结果水全部沉在烧杯底部,水在油中无沸腾发生,油中含水量无变化。
试验2:将500g 的N32机械油倒入装有115g 水的烧杯中(相当于0130%的水)搅拌均匀后,在容器的底部进行加热,分别加热到100℃、120℃和140℃保温1h ,加热过程中不进行搅拌。
测量结果为:加热到100℃,保温1h ,含水量为0122%;加热到120℃,保温1h ,含水量为0121%;加热到140℃,保温1h ,含水量为0118%。
试验中观察到的现象如下:加热过程中容器底部的水有一定的沸腾现象,随着加热温度的升高,沸腾现象变得剧烈,并在油的表面出现大量白沫。
试验3:将500g 的N32机械油倒入装有115g 水的烧杯中(相当于0130%的水)搅拌均匀后,在容器的底部进行加热,分别加热到100℃、120℃和140℃,保温1h ,与试验2不同之处是在整个试验过程中对介质进行搅拌。
测量结果为:加热到100℃,保温1h ,含水量为0115%;加热到120℃,保温1h ,含水量为0113%;加热到140℃,保温1h ,含水量为0112%。
试验中观察的现象如下:在加热过程中容器底部的水在搅拌的作用下沸腾加剧,加热温度越高,沸腾现象越剧烈,并在油面出现大量白沫。
试验4:将500g 的N32机械油倒入装有115g 水的烧杯中(相当于0130%的水)搅拌均匀后,将加热管插入烧杯中对油进行加热(模拟实际淬火槽的加热方式),分别加热到100℃、120℃和140℃,保温1h ,在此过程中不对介质进行搅拌,测量含水量的结果均在0128%~0129%之间。
试验中观察不到沸腾现象的发生。
试验5:将500g 的N32机械油倒入装有115g 水的烧杯中(相当于0130%的水)搅拌均匀后,将加热管插入烧杯中对油进行加热(模拟实际淬火槽的加热方式),分别加热到100℃、120℃和140℃,保温1h ,在此过程中对介质进行搅拌,测量含水量的结果分别为0128%、0126%、0125%。
试验中观察到沸腾现象随搅拌强度的增强而加剧。
试验6:将含有0130%水的N32机械油搅拌均匀后,采用按图1所示流程图制成的设备进行去除油中水的试验。
因液体具有其沸点随表面压力的下降而降低的特性,当压力为8×103Pa 时,水的沸点仅为40℃,淬火油沸点降为180℃。
因此,在真空条件下去除油中水的方法可获得很好的效果。
试验过程是采用图1所示原理的设备将含水的油加热到60℃~80℃后抽到具有8×103Pa 压力的真空容器内,被处理的油进入真空容器后流过特制发散装置,单位体积的油液产生巨大的表面面积,使油液曝露于相对湿度很低的气氛中,从而清除油中的水使其蒸发,蒸发的水蒸汽通过真空管路排出,处理后油中含水为0103%。