大型齿轮渗碳淬火变形原因及其控制
齿轮渗碳淬火热处理变形原因与改进技术

齿轮渗碳淬火热处理变形原因与改进技术摘要】齿轮是常见的机械零部件,其啮合传动力学在汽车、轮船等机械产品中广泛应用。
齿轮的重要作用不言而喻,但在齿轮的具体使用当中会存在齿轮失效的现象,此种现象的出现大部分是由于齿轮长期使用后磨损、折断所导致的。
齿轮的生产主要以渗碳淬火热处理的加工方式进行批量生产,但此种生产方式容易导致齿轮变形,不利于齿轮的批量成产与成本投入。
为保障齿轮的生产质量文章对齿轮渗碳淬火热处理技术进行分析,找寻齿轮变形原因并提出相关的改进措施,以供行业参考。
【关键词】渗碳淬火热处理齿轮渗碳淬火是当下齿轮生产中的重要工艺流程,渗碳淬火能够使齿轮的耐磨性能更加稳定。
渗碳淬火属于热处理技术,其具体工作开展分为多种形式,但渗碳淬火过程较为复杂,导致齿轮在淬火后容易发生变形。
齿轮变形属于齿轮制作过程中的常见问题,极大的影响了齿轮的使用质量,齿轮在机械中应用广泛,如何提高齿轮质量,改进工作技术成为当下技术研究的重点。
一、齿轮及渗碳淬火热处理工艺分析1.1齿轮结构从大部分的齿轮结构来讲,齿轮的整体结构呈现对称性,其制作材料主要包含调质钢、渗碳钢、合金钢等多种材料,制作完成的齿轮中间多为空心、内外径较大、齿轮壁较薄,渗碳淬火需要进行高温加热,以此齿轮容易发生变形现象。
1.2渗碳淬火热处理工艺齿轮的渗碳淬火热处理工艺较为复杂,包含直接淬火低温回火、预冷直接淬火低温回火、一次加热淬火低温回火、渗碳后感应加热淬火低温回火等多种工艺。
以20CrMnTi齿轮为例,首先要将齿轮要放置在炉温为920℃的渗碳淬火炉中进行长达3小时的渗碳处理,其次将渗碳炉的温度调至860℃,在保持50分钟的恒温状态后进行淬火出炉。
最后,使用淬火液处理,进行2小时的低温回火,在低温回火的过程中回火炉的温度应当保持在160℃。
在进行渗碳淬火热处理时,要注意四只齿轮在全过程当中要保持平放状态。
1.3齿轮渗碳淬火热处理后导致变形的因素在齿轮进行渗碳淬火热处理前后分别对齿轮的直径、公法线进行测量,发现在经过热工艺处理后,齿轮的内外直径与公法线均发生了变化。
风电齿轮渗碳淬火变形分析与改善

零件号 H1 H2 H3 H4
图10 H3零件左右齿面变形
图11 炉和热处理工艺对齿轮变形的影响
渗碳装炉 平装4块蜂窝板 平装8块蜂窝板
淬火装炉 挂放无阻尼工装 挂放有阻尼工装
挂放有阻尼工装
渗碳淬火工艺 原工艺 改进工艺
改进工艺
椭圆/mm 0.18 0.14 0.14 0.15
4)将左右齿面的磨齿对中数据进行平均,如图 6所示,发现零件节圆存在明显的椭圆,椭圆趋势呈 梨状分布,椭圆量约0.18mm。
根据对H1零件磨齿对中数据的分析,暂无法判 定零件齿向变形是由端面翘曲或齿部畸变造成的。 零件的椭圆趋势呈梨状分布,虽无法确定具体位置 是否与挂装有关,但根据单点挂装的情况推测,梨 柄位置(148号齿附近)应是与工装接触的位置, 此处凸起最大;左右齿面变形量最大位置无显著规 律,但在椭圆的梨状尾部附近(即挂装下部)变形 趋势最大。
要求 实测
2.9~3.9 3.39、3.46
58~64 60.26、59.62
≥30 38
ISO 6336:5 MQ级 细针状
弥散
细针状
≤30 15
无块状铁素体 ≤0.05 无块状铁素体 0.025
4.4 优化验证 在序列号为H3和H4的零件生产时,同时采用图
8的渗碳工艺、渗碳时底部蜂窝板满铺的平放装炉方 式(见图9),在挂装淬火装炉时,在底盘上增加网 孔阻尼工装,零件渗碳淬火后,变形得到大幅度改
图8 H2零件渗碳后轴向圆跳动
图9 改善后的渗碳装炉 4.3 淬火装炉改善
综上所述,齿轮下部约1/4位置冷速较快是齿轮
热加工
63 2021年 第3期
热处理
Heat Treatment
变形的影响因素之一[6],故对淬火的装炉形式进行 调整。
机车从动齿轮渗碳淬火变形问题的分析与预防

机车从动齿轮渗碳淬火变形问题的分析与预防摘要齿圈类机车从动齿轮,因为尺寸较大的薄板形结构,渗碳淬火后不可避免地要发生变形。
这样既影响从动齿轮的精度,也严重影响齿轮的使用性能。
本文从材料、热处理等影响齿轮热处理变形的几个主要因素入手,分析其产生的原因,并通过适当的选材以及热处理工序等相应措施,减少齿轮热处理变形,从而提高齿轮加工精度。
关键词齿轮热处理变形因素变形控制1 前言目前,在铁路跨越式发展理念的引导下,各个主机厂都以“客运高速、货运重载”为目标,应用新材料、研究新工艺、开发新产品。
牵引从动齿轮是机车驱动装置上的关键零部件,它的好坏直接影响到机车是否能够高速重载。
由于大功率机车从动齿轮因为尺寸较大,渗碳淬火后易产生变形,已经成为制约产品质量和使用性能的瓶颈,所以对机车从动齿轮渗碳淬火的研究有重要的现实意义。
2 齿轮热处理变形的影响因素2.1齿轮材料对齿轮变形的影响由于同一牌号的钢材,其淬透性曲线会在一定范围内变化,导致了淬透性带宽的不同,渗碳淬火后的组织就会出现差异,变形也就不一样,如果淬透性带宽过宽,必然会导致齿轮热处理变形无规律。
实验表明,钢的淬透性越高,热处理后齿轮的变形就越大。
当心部硬度高于HRC40时,变形就会明显增大。
目前,使用与从动齿轮强度相匹配的窄淬透性带宽的渗碳钢已经成为齿轮行业选材的共识。
2.2 预备热处理对齿轮变形的影响齿轮预备热处理组织的均匀性和稳定性对齿轮最终热处理变形的影响很大,因为齿轮各部分的原始组织不同,其比热就不同,在热处理过程中产生的尺寸变化也就不同。
齿轮经高温锻造后,由于其组织粗大不利于随后的渗碳处理,所以一般高温锻造后的齿轮需要经过正火处理,以达到细化晶粒和改善显微组织的目的。
但是,往往正火硬度过高,出现大量索氏体或魏氏体组织,它们的存在都会使内孔变形增大,所以必须引起足够的重视。
2.3 渗碳工艺对齿轮的影响2.3.1 温度的均匀性对齿轮的影响温度的均匀性是造成热处理变形的因素之一。
浅析渗碳淬火齿轮的变形与控制

分 的均匀 性不是 很好 ,淬火后 应力 不 均 ,变 形无 规 艺 ,是 减小 与 防止 零 件热 处理变形 的有效 措施 。正 律 。现 国 内 一 般 要 求 将 淬 透 性 带 宽 控 制 在 ≤ 火 的质 量要 求 ,主要 是针 对硬度 与组 织 。普通 正火 l HR l C,国外 高标 准要 求 为 3 C 国 内钢材 质量 工艺 ,有些 难 以克服 的不 足 ,如带 状 组织 和混 晶组 HR 。 近年来 虽 提高很 快 ,但 在 “ 三性 ” 的控 制方 面与 国 织难 以消 除 ;受设 备炉 温 均匀性 和生 产方式 、装 护 外先进 水平 差距 还 较大 ,成 分 的波 动 范 围 也较 宽 , 方式 、能耗 等的 限制 ,工件 的硬度 也很 难均 匀 ;对 对渗 碳淬 火变形 的控制 难度 自然更 大 ,因此提 高齿 于某些 材料 ,由于冷却 速度 难以控 制 ,正火后 还会
脆性 断裂 。
可见 优化锻 造工艺 ,对改 善材料 的组织 、减小
4 正 火 工 艺 的 影 响 与 控 制 .
淬 火后 不仅变 形更 大 ,而且 在使 用过 程 中容易产 生 渗碳 淬火 后变形 十分重要 。 淬透 性带 的宽 度越 窄越好 。带宽太 大 ,说 明成 正 火是 渗 碳 之 前 的 一 种 常 规 的 预 先 热 处 理 工
控 制 在 ≤ 2 0级 。 , 2 零 件 设 计 的 影 响 与 控 { . 目 I
为 了减 少 变 形 ,零 件 设计 时 应尽 量避 免 尖 角 、 薄 壁 、台阶 等结 构 。对 零 件 中那 些 不 可 缺少 的孔 、
均匀性 包 括 成 分 、组 织 和 缺 陷分 布的 均 匀性 。 槽 、筋等要 素 ,则应 力求 分布 对称 与均匀 。在 截面
齿轮渗碳淬火变形原因及控制措施研究

齿轮渗碳淬火变形原因及控制措施研究摘要:齿轮零件在前期加工期间若是遭受到热处理变形作用,将会导致其获取的精度遭受到严重的影响,一旦出现变形即使是使用校直及磨齿等先进的修形技术也难以达到恢复的效果。
尤其是齿轮在遭受到渗碳淬火之后会出现变形情况,具有较大的变形量,该种变形无法通过控制来实现,并且变形过大,也会增加磨削成本及磨削量,对齿轮制造精度会造成极大的影响,承载能力显著降低,寿命也会随之而下降。
本文着重分析齿轮渗碳淬火变形原因,并提出合理化的变形控制措施。
关键词:齿轮渗碳淬火;变形原因;控制措施前言:在制造硬齿面汽车齿轮期间,目前所使用的主流工艺是渗碳淬火,但是在使用之后不得不面对的问题便是出现变形情况,会对齿轮的加工质量造成极大的影响。
有相关的研究报告显示,之所以会导致碳淬火齿轮出现变形,与锻造质量、原材料质量、齿轮的结构设计、毛坯预备热处理有直接关系,并且以上几种因素之间彼此也会出现相互影响的情况,进而增加了上述因素的控制难度。
现如今,在汽车齿轮制造中控制变形量已经成为一项需要解决的重难点问题。
一、齿轮渗碳淬火变形原因(一)渗碳件变形原因渗碳低碳钢,经过对原始相结构进行分析可知,由少量珠光体组织及铁素体共同来构成,经过对整个体积的占比情况进行了解可知,铁素体量的占比高达80%,当加温到AC1以上温度之后,珠光体会向奥氏体进行转变。
当温度为900℃时,铁素体会向奥氏体进行转变。
当渗碳的温度为920℃-940℃时,零件表面的奥氏体区碳浓度的升高度为0.6%-1.2%,碳浓度比较高的奥氏体区碳浓度会增加至0.6%-1.2%,当奥氏体的温度冷却到600-650℃时,会向索氏体及珠光体进行转变[1]。
当低碳奥氏体处于心部区时,若是在900℃的高温下会将其转变为铁素体,当冷却到550℃时,会全部转变完成。
比容增大的过程是心部奥氏体向铁素体进行转变的过程,而通过对表层奥氏体冷却情况进行探究可知,可将热缩量增加变化的整个过程呈现出来,在冷却期间,在生成心部铁素体时,会遭受到表层高碳奥氏体区的压力影响[2]。
影响齿轮热处理变形的几个重要因素

儿、J 续} f f 施
对 于 内 孔 磨 削 过 程 监 审 中 发
或y a n g k a i 1 9 8 0 @1 2 6 . c o m
皿口 2 ~ 0 i 7 0 3 2 4 :
5 0
造 参磊
…
F I 失 效 分 析
艺 , 产 品 采 州 串放 ,产 的 轴 向 跳 动较 好 ,渗碳 温 度 降 低 ,渗
业 。齿 轮 在 进 行 渗 碳 热 处 理 的过 程 中 ,常 遇 到 齿 轮 渗 碳淬 火 后平
产 品 结 构 示 意 , 图2 是 试 制 时 的 热 处 理 工 艺 , 图3 是 改 进 的 热 处
理 工 艺 。可 以 看 出 试 制 的 热 处 理
面扭 曲变形大 ,造成齿轮报废 ;
F : I 失 效 分 析
影响齿轮热处理变形的几个重要因素
一 陈正 国 。郝 丰林
我 公 司 是 一 家 专 业 生 产 汽 车
及 热 处 理 项 目进 行 检 测 ;合 格 后 按照一炉 ( 或 者 一 盘 )热 处 理 , 检 测 变 形 ;合 格 后 连 续 生 产 几炉 ( 或 几盘 ) ,热 处 理 合 格 、变 形 合 格 ,这 样 热 处 理 工 艺 就 可 固定
碳时 I ' H 】 增加 ,减 少热 处理 变形 。 这样 改 进 后 的 热处 理 : [艺 生 产
了5 年 多 , 产 品 的 寿 命 周 期 就 要
于轴 向 圆跳 动 进 行 严 格 控 制 。后 来 有一 个 月 出现 的 量 较 大 ,检 查 从箱 体 拆 下 来 的 齿 轮 进 行 检 测 齿 形齿 向 ,发现 齿形 齿 向 不符 合 图
到 了 ,客 户 反 馈 变速 器有 噪 声 ,
大型齿轮齿轮轴渗碳淬火的变形及控制
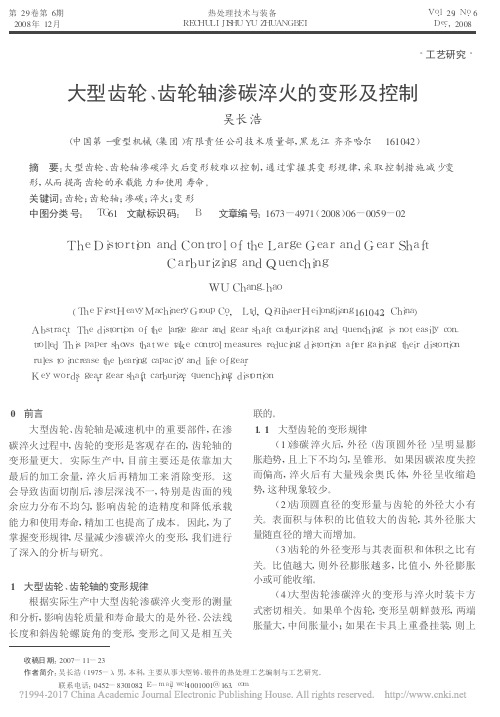
和分析 , 影响齿轮质量和寿命最大的是外径 、公法线 长度和斜齿轮螺旋角的变形 , 变形之间又是相互关
联的 。 1.1 大型齿轮的变形规律
(1)渗碳 淬火后 , 外径 (齿顶圆外径 )呈明显膨 胀趋势 , 且上下不均匀 , 呈锥形 。 如果因碳浓度失控 而偏高 , 淬火后有 大量残余奥氏 体 , 外径 呈收缩趋 势 , 这种现象较少 。
图 2 大型齿轮轴渗碳淬火后的变形 虚线为淬火后齿部外圆示意
Fig.2 Thedstortionofthelargegearshaftaftercarburizingandquenching Brokenlineisthesketchofexcircleofgearbodyafterquenching
Fig.3 Thedistortionandpredistortionofthehelical angleofthelargeherringbonegearshaft
Brokenlineisthedistortionsketchofexcircle ofgearandhelicalangleafterquenching
引起组织不均匀和应力不均匀 。 (2)选择合适的淬火剂 , 控制油温 (>100 ℃),
改善齿轮上中下部位冷却的均匀性 , 使组织转 变趋于同步 。可以在齿轮轴中段喷油加速冷却等措 施 , 也可在齿轮上下端面加热圈改善端面和中段的 冷速不均匀 , 可以收到明显的效果 。
4 结束语 经过近几年的生产实践与 理论分析 , 我们已初
步掌握了大型齿轮 、齿轮轴渗碳淬火的变形规律和 控制措施 , 并把这些控制措施应用于实际生产中 , 取 得了很好的效果 。 由于受到设备能力的限制 , 热处 理工艺的执行情况和实际操作等多方面的影响 , 以 及型齿轮和齿轮轴渗碳淬火后的变形比较复杂 , 仍 有待于进一步的探索与研究 。
玉力机大齿轮渗碳淬火裂纹成因及预防

金相分析可以根据工件表面 的组织确 定中频感应加热是否过热 , 是否有二次淬火烧伤 , 在适 当的位 置可以观察到裂纹
的形态 以及裂纹附近的夹杂物分布情况 , 根据裂纹附近的金相组织 、 夹杂物分布状况和裂纹形态来确定 裂纹 的性质。
磨削裂纹在显微镜下观察 , 主要表现为穿 晶而过 , 也有沿着晶界延 展的。如果由于磨 削过 于剧烈 引起表面裂纹 , 但 则可
感应淬火 ,5  ̄油淬 ,7  ̄回火。经过渗碳处理 的齿轮在磨削过程 中常产生裂纹 , 80C 10C 裂纹深 度O0 — . m, .3 05 尾部呈尖角状 , a r 延 伸方 向大致与磨削线速度方 向垂直 , 而且排列较规则。
2 裂纹产 生原 因
21 裂 纹类 型 判 断 .
产生裂纹的原因有热处理不 当引起 的裂纹 和磨 削工艺不当引起 的磨 削裂纹 , 只有判 断出裂纹 产生的原 因, 才能采取 针
的马氏体集 中于表面 , 引起表面体积胀 , 成表面拉力 , 形 引起裂 纹。
22 磨 削 热 应 力 .2 .
磨 削过 程是切削 、 刻划 、 摩擦抛 光三个过程综合作用 的结果 。磨削加工 中 , 磨粒形状不 规则 , 多为负前角切削 , 挤压 和摩 擦严重 , 伴随砂轮高速转动摩擦 所产生的高热 , 工件表面温度在 80 0 ℃以上 , 磨削热 向内部传递 时受 到冷却液作用急剧冷却 , 外层趋于收缩 , 内层 因热传导而体积膨胀 , 导致外 层产生巨大拉力 。当表面应力大 于材料抗拉极 限时, 产生裂纹 。
2 1 年 0 月 00 3
内 蒙 古 民 族 大 学 学 报
J u n l f n e n oi iest r t n l is o r a n r oI Mo g l Unv ri f i ai e a y o Na o t
- 1、下载文档前请自行甄别文档内容的完整性,平台不提供额外的编辑、内容补充、找答案等附加服务。
- 2、"仅部分预览"的文档,不可在线预览部分如存在完整性等问题,可反馈申请退款(可完整预览的文档不适用该条件!)。
- 3、如文档侵犯您的权益,请联系客服反馈,我们会尽快为您处理(人工客服工作时间:9:00-18:30)。
大型齿轮渗碳淬火变形原因及其控制
2 大型齿轮渗碳淬火变形规律
对大型齿轮质量和寿命影响最大的变形来自齿轮外径、公法线长度和螺旋角等。
一般说来,变形趋势如下:
2.1 大型齿轮变形规律:大型齿轮渗碳淬火后齿顶圆外径呈明显胀大趋势,且上下不均匀呈锥形;径长比(齿轮外径/齿宽)越大,外径胀大量越大。
碳浓度失控偏高时,齿轮外径呈收缩趋势。
2.2 大型齿轮轴变形规律:齿顶圆外径呈明显收缩趋势,但一根齿轴的齿宽方向上,中间呈缩小,两端略有胀大
2.3 齿圈变形规律:大型齿圈经渗碳淬火后,其外径均胀大,齿宽大小不同时,齿宽方向呈锥形或腰鼓形。
3 渗碳淬火齿轮变形原因
3.1 渗碳件变形的实质
渗碳的低碳钢,原始相结构是由铁素体和少量珠光体组成,铁素体量约占整个体积的80%。
当加热至AC1以上温度时,珠光体转变为奥氏体,900℃铁素体全部转变为奥氏体。
920—940℃渗碳时,零件表面奥氏体区碳浓度增加至0.6—1.2%,这部分碳浓度高的奥氏体冷至600—650℃才开始向珠光体、索氏体转变,而心部区的低碳奥氏体在900℃即开始分解为铁素体,冷至550℃左右全部转变完成。
心部奥氏体向铁素体转变是比容增大的过程,表层奥氏体冷却时是热收缩量增加的变化过程。
在整个冷却过程中,心部铁素体生成时总是受着表层高碳奥氏体区的压应力。
此外,大型齿轮由于模数大、渗层深,渗碳时间较长,由于自重影响,也会增加变形。
3.2 大型齿轮渗碳淬火变形的原因
工件淬火时,淬火应力越大,相变越不均匀,比容差越大,则淬火变形越严重。
淬火变形还与钢的屈服强度有关,塑性变形抗力越大,其变形程度就越小。
从齿轮和齿轮轴渗碳淬火冷却各部位冷却速度、组织及硬度状态比较分析,可以发现上中下各部位冷却速度的差别,以及表面、过渡区、心部冷却速度差别,和其组织转变的不同时性是造成齿轮变形的主要原因。
减小大型齿轮渗碳淬火变形也要通过提高各环节的均匀性来实现。