金属材料热处理原理
热处理的原理

热处理的原理热处理是通过加热和冷却金属材料,以改变其物理和机械性能的工艺。
热处理的原理主要包括晶粒细化、组织调整和应力消除等方面。
下面将详细介绍热处理的原理及其作用。
首先,热处理的原理之一是晶粒细化。
在金属材料中,晶粒的大小直接影响着材料的力学性能。
通过热处理,可以使晶粒的尺寸变小,从而提高材料的强度和韧性。
晶粒细化的原理是在材料加热至一定温度时,晶界开始消失,晶粒开始长大,当温度继续升高时,晶界重新形成,此时晶粒的尺寸变小。
晶粒细化可以提高金属材料的塑性和韧性,使其更适合工程应用。
其次,热处理的原理还包括组织调整。
金属材料的组织结构对其性能有着重要影响。
通过热处理,可以改变材料的组织结构,从而改善其性能。
例如,通过淬火可以使钢材的组织转变为马氏体,从而提高其硬度和强度;而通过退火可以使马氏体转变为珠光体,从而提高其韧性。
组织调整的原理是通过控制加热和冷却过程中的温度和时间,使材料的组织结构发生相应的变化,从而达到改善材料性能的目的。
另外,热处理的原理还涉及应力消除。
在金属加工过程中,材料会产生内部应力,影响其使用性能。
通过热处理,可以消除材料中的内部应力,提高材料的稳定性和可靠性。
应力消除的原理是在加热过程中,材料的晶界和位错会发生移动和重排,从而减少内部应力。
应力消除可以有效减少材料的变形和开裂倾向,提高其使用寿命和安全性。
总的来说,热处理的原理主要包括晶粒细化、组织调整和应力消除。
通过热处理,可以改善金属材料的力学性能,提高其强度、硬度、韧性和稳定性,从而满足不同工程应用的需求。
因此,热处理是一项重要的金属加工工艺,对于提高材料的性能和使用寿命具有重要意义。
材料热处理原理第一章金属固态相变基础

1#楼203 周二 5-6节 周四 1-2节
热处理
热处理原理与工艺
• 热处理:将金属或工件放在一定的介质中,通 过加热、保温和冷却的方法,使金属或合金的 内部组织结构发生变化,从而获得所需性能的 技术。
• 金属材料生产和机械制造过程的重要组成部分 之一。
• 热处理的特点:
– 一般不改变材料或工件的形状和整体的化学成分 – 改变材料或工件的微观组织和结构,或表面的化学成
特点:
(1)存在由于均匀切变引起的宏观形状改变,可在预先制备的抛光试样 表面上出现浮突现象。
(2)相变不需要通过扩散,新相和母相的化学成分相同。 (3)新相和母相之间存在一定的晶体学位向关系。 (4)某些材料发生非扩散相变时,相界面移动速度极快,可接近声速。
4. 按相变方式分类
➢ 有核相变:通过形核-长大方式进行的。
• 其两个生成相的结构和 成分均与母相不同
• 加热时也可发生 α+→转变,称为逆 共析相变
平衡相变
④调幅分解
• 某些合金在高温下具有均匀单相固溶体,但冷却到 某一温度范围时可分解成为与原固溶体结构相同但 成分不同的两个微区,这种转变称为调幅分解。
特点:转变初期不存在明显的相界面和成分突变; 通过上坡扩散实现成分变化; 一个自发分解过程; 不经历形核阶段; 分解速度快
3. 按原子迁移特征分类
扩散型相变
相变时原子迁移特征
非扩散型相变
3. 按原子迁移特征分类
(1)扩散型相变
相变时,相界面的移动是通过原子近程或远程扩散而进行的相变。
如:脱溶型相变、共析型相变(珠光体型转变)、调幅分解和有序化 转变等。
特点:
(1)有原子扩散运动,相变速率受原子扩散速度所控制; (2)新相和母相的成分往往不同; (3)只有因新相和母相比容不同而引起的体积变化,没有宏观形状
201热处理工艺

201热处理工艺201热处理工艺是一种常见的热处理方法,它通过对金属材料进行加热和冷却的过程,改变其组织和性能,以达到所需的性能要求。
本文将从热处理的基本原理、常见的热处理工艺以及热处理工艺的应用等几个方面来介绍201热处理工艺。
一、热处理的基本原理热处理是利用金属材料的固溶度、扩散性和相变等特性,在一定温度范围内进行加热和冷却处理,使材料的组织和性能发生变化。
其基本原理是通过加热将金属材料的晶体结构进行改变,然后通过冷却固定新的组织结构,从而达到改变材料性能的目的。
二、常见的热处理工艺1. 固溶处理:固溶处理是将合金材料加热至固溶温度,使固体溶解成固溶体,然后通过快速冷却固定固溶体的结构。
这种方法可以提高合金的强度和硬度,同时改善其塑性和韧性。
2. 时效处理:时效处理是在固溶处理后,将材料在较低温度下保持一段时间,使固溶体中的溶质元素析出,形成细小的析出相。
这种方法可以进一步提高材料的强度和硬度,同时保持较好的塑性和韧性。
3. 淬火处理:淬火是将材料加热至临界温度,然后迅速冷却至室温。
这种方法可以使材料产生强烈的变形和应力,从而改变其组织和性能。
淬火可以增加材料的硬度和强度,但会降低其塑性和韧性。
4. 回火处理:回火是将淬火处理后的材料加热至较低温度,然后保持一段时间后冷却。
这种方法可以缓解淬火产生的应力和变形,同时提高材料的韧性和塑性,降低其硬度和强度。
三、热处理工艺的应用热处理工艺广泛应用于各种金属材料的制造和加工过程中。
其中,201热处理工艺主要应用于不锈钢材料的加工中。
不锈钢具有较好的耐腐蚀性和机械性能,在许多领域得到广泛应用。
而201不锈钢是一种含有高锰奥氏体结构的不锈钢,通过适当的热处理工艺可以改善其机械性能和耐腐蚀性。
201热处理工艺的主要步骤包括固溶处理、时效处理和回火处理。
首先,将201不锈钢材料加热至固溶温度,使其固体溶解成固溶体。
然后,在适当的温度下保持一段时间,使溶质元素均匀分布,并形成细小的析出相。
热处理基本知识及工艺原理
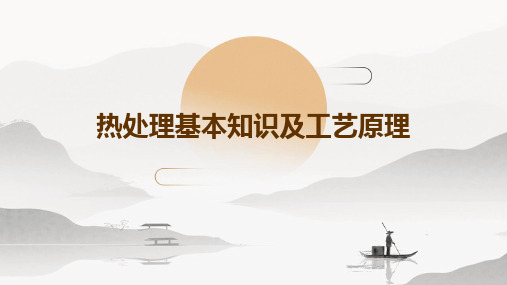
将淬火后的金属材料加热到适当温度,保温一定时间后冷 却至室温。回火可以消除淬火产生的内应力,提高金属材 料的韧性和塑性。
02
热处理工艺原理
加热与冷却
加热
热处理过程中,将金属材料加热至所 需温度,以实现所需的相变和组织转 变。加热方式包括电热、燃气热、微 波加热等。
冷却
热处理过程中,金属材料在加热后需 进行冷却,以控制相变和组织转变的 过程。根据冷却速度的不同,可分为 缓慢冷却和快速冷却。
感谢您的观看
THANKS
热处理的分类
1. 退火
将金属材料加热到适当温度,保温一定时间后缓慢冷却至 室温。退火可以提高金属材料的塑性和韧性,消除内应力 。
3. 淬火
将金属材料加热到适当温度,保温一定时间后快速冷却至 室温。淬火可以提高金属材料的硬度和耐磨性,但可能导 致内应力增大。
2. 正火
将金属材料加热到适当温度,保温一定时间后在空气中自 然冷却。正火可以提高金属材料的强度和韧性,细化组织 结构。
离子注入技术
将具有特定能量的离子注 入材料表面,改变其物理 和化学性质,提高耐磨、 耐腐蚀等性能。
提高热处理效率与节能减排
高效加热方式
采用电磁感应、微波加热 等高效加热方式,缩短加 热时间,提高热处理效率。
余热回收利用
对热处理过程中的余热进 行回收和再利用,减少能 源浪费,降低碳排放。
环保材料与工艺
热处理基本知识及工艺艺原理 • 常见热处理工艺 • 热处理的应用 • 热处理的发展趋势与挑战
01
热处理基本概念
热处理的定义
热处理:通过加热、保温和冷却等工 艺手段,改变金属材料的内部组织结 构,以达到改善其性能、满足使用要 求的一种工艺方法。
钢的热处理原理
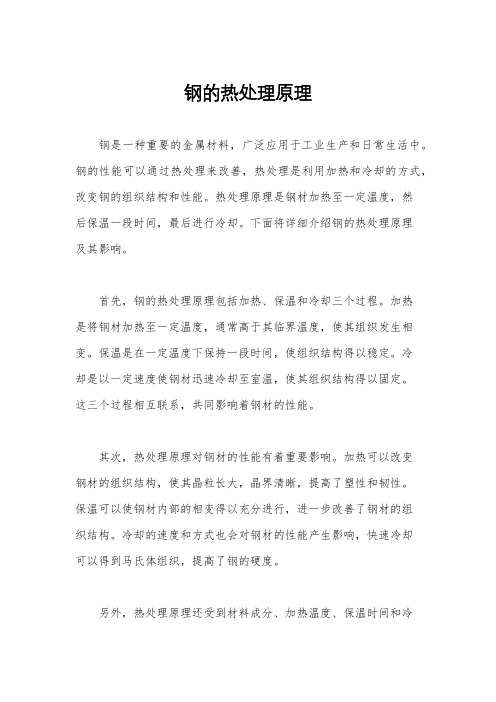
钢的热处理原理钢是一种重要的金属材料,广泛应用于工业生产和日常生活中。
钢的性能可以通过热处理来改善,热处理是利用加热和冷却的方式,改变钢的组织结构和性能。
热处理原理是钢材加热至一定温度,然后保温一段时间,最后进行冷却。
下面将详细介绍钢的热处理原理及其影响。
首先,钢的热处理原理包括加热、保温和冷却三个过程。
加热是将钢材加热至一定温度,通常高于其临界温度,使其组织发生相变。
保温是在一定温度下保持一段时间,使组织结构得以稳定。
冷却是以一定速度使钢材迅速冷却至室温,使其组织结构得以固定。
这三个过程相互联系,共同影响着钢材的性能。
其次,热处理原理对钢材的性能有着重要影响。
加热可以改变钢材的组织结构,使其晶粒长大,晶界清晰,提高了塑性和韧性。
保温可以使钢材内部的相变得以充分进行,进一步改善了钢材的组织结构。
冷却的速度和方式也会对钢材的性能产生影响,快速冷却可以得到马氏体组织,提高了钢的硬度。
另外,热处理原理还受到材料成分、加热温度、保温时间和冷却速度等因素的影响。
不同的钢材成分会影响相变温度和组织结构,加热温度和保温时间的选择也会直接影响到钢材的性能。
冷却速度的选择则会影响到钢材的硬度和韧性,不同的冷却方式也会得到不同的组织结构。
总之,钢的热处理原理是通过加热、保温和冷却三个过程,改变钢材的组织结构和性能。
热处理原理对钢材的性能有着重要影响,同时受到材料成分、加热温度、保温时间和冷却速度等因素的综合影响。
因此,在实际生产中,需要根据具体的要求和条件,合理选择热处理工艺参数,以达到最佳的效果。
通过对钢的热处理原理的了解,我们可以更好地掌握钢的性能调控方法,为工业生产提供更好的材料支持。
同时,也可以更好地利用钢材的性能,满足不同领域的需求。
希望本文能够对大家有所帮助,谢谢阅读!。
金属热处理技术手册
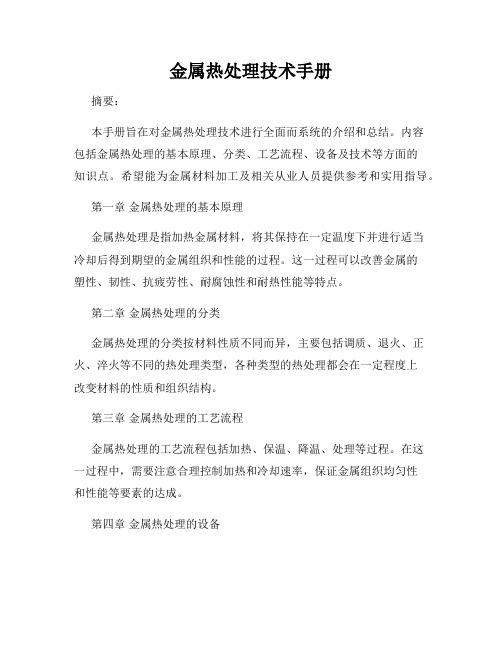
金属热处理技术手册
摘要:
本手册旨在对金属热处理技术进行全面而系统的介绍和总结。
内容
包括金属热处理的基本原理、分类、工艺流程、设备及技术等方面的
知识点。
希望能为金属材料加工及相关从业人员提供参考和实用指导。
第一章金属热处理的基本原理
金属热处理是指加热金属材料,将其保持在一定温度下并进行适当
冷却后得到期望的金属组织和性能的过程。
这一过程可以改善金属的
塑性、韧性、抗疲劳性、耐腐蚀性和耐热性能等特点。
第二章金属热处理的分类
金属热处理的分类按材料性质不同而异,主要包括调质、退火、正火、淬火等不同的热处理类型,各种类型的热处理都会在一定程度上
改变材料的性质和组织结构。
第三章金属热处理的工艺流程
金属热处理的工艺流程包括加热、保温、降温、处理等过程。
在这
一过程中,需要注意合理控制加热和冷却速率,保证金属组织均匀性
和性能等要素的达成。
第四章金属热处理的设备
金属热处理的设备通常包括热处理炉、热处理钢罐、加热炉、降温设备、炉具等。
其中,炉具的种类和质量直接决定着金属热处理成品的质量水平和工艺效率。
第五章金属热处理的技术
金属热处理的技术主要包括热处理工艺、工艺参数和环境因素等,其中前两者直接决定了金属组织和性能的变化方向和程度。
结论:
金属热处理作为一项重要的金属材料加工技术,一直以来受到广泛的关注和应用。
本手册对于金属热处理技术的全面系统介绍和总结,期望能为从事金属热处理的相关从业人员提供参考和实用指导,使其能更好地从事相关工作,提高工作效率和成果质量。
热处理工艺的原理和应用
热处理工艺的原理和应用热处理工艺的概述•热处理工艺是将金属材料经过加热、保温和冷却等过程,以改变其微观结构和性能的技术方法。
•热处理工艺主要包括退火、正火、淬火、回火等几种常用方法。
热处理工艺的原理1.退火–通过加热材料到一定温度,然后缓慢冷却,使材料达到均匀细小的晶粒结构,以提高材料的塑性和韧性。
–退火工艺可分为全退火、球化退火、回火退火等。
2.正火–通过加热材料到一定温度,然后迅速冷却,使材料形成马氏体组织,以提高材料的硬度和强度。
–正火工艺常用于钢材的处理。
3.淬火–通过加热材料到一定温度,然后迅速冷却,使材料快速形成马氏体组织,以提高材料的硬度和强度。
–淬火工艺常用于钢材的处理。
4.回火–在淬火后,通过加热材料到一定温度并保温一段时间,然后冷却至室温。
–回火工艺可减轻淬火产生的内应力,提高材料的韧性和硬度。
热处理工艺的应用•热处理工艺广泛应用于金属材料的制造领域,包括钢铁、铜、铝、镁等金属。
•在钢材的生产中,热处理工艺可改变钢材的组织结构和性能,增加钢材的硬度、韧性、耐磨性等特性。
•在铝合金的生产中,热处理工艺可改变铝合金的晶粒结构,提高其强度和抗腐蚀性能。
•在汽车、航空航天、造船等行业中,热处理工艺应用于零部件的制造,以提高零部件的硬度、耐磨性和强度,提高产品的质量和安全性能。
•在电子设备的制造中,热处理工艺应用于半导体材料的制备,以提供半导体材料的特殊电学和磁学性能。
热处理工艺的优点•可改善金属材料的物理性能,提高材料的硬度、韧性、强度等。
•可改变材料的晶粒结构和组织,提供特定的材料性能。
•可改善材料的表面质量,提高耐磨性和耐腐蚀性。
•可通过控制热处理工艺参数,实现材料性能的调控和优化。
热处理工艺的注意事项•热处理工艺的参数,包括加热温度、保温时间、冷却速度等,需要根据材料的类型和要求进行合理选择,以避免材料的过热或过冷现象。
•热处理工艺需要严格控制各个环节的温度和时间,以保证工艺的有效性和一致性。
表面热处理的原理及其应用
表面热处理的原理及其应用前言表面热处理是一种通过加热金属材料的表面以改变其性能的工艺。
它可以对金属材料的硬度、耐磨性、耐腐蚀性、抗疲劳性等进行改善,从而延长其使用寿命。
本文将介绍表面热处理的原理以及它在各个行业中的应用。
表面热处理的原理表面热处理的原理主要包括热软化、硬化、表面改性等几个方面。
热软化热软化是指将金属材料加热至其临界温度以下,使其晶粒长大并晶界迁移,从而降低其硬度和强度。
这种热处理方法常用于金属的冷加工工艺中,可以使材料变得更易于加工。
热软化方法有退火、回火等。
硬化硬化是通过加热金属材料并迅速冷却,使其发生组织和相变的改变,从而提高其硬度和强度。
这种热处理方法常用于提高金属材料的耐磨性和耐疲劳性。
硬化方法有淬火、淬火+回火、等离子氮化等。
表面改性表面改性是通过对金属材料表面进行处理,改变其表面形状、化学成分和微观结构,从而获得所需的表面性能。
这种热处理方法常用于提高金属材料的耐腐蚀性和耐磨性。
表面改性方法有氮化、碳化、镀层等。
表面热处理的应用表面热处理在各个行业中均有广泛的应用。
以下是一些常见的应用领域:汽车制造业在汽车制造业中,表面热处理常用于发动机零部件、传动系统和悬挂系统等关键部件的制造中。
通过对这些部件进行硬化处理,可以提高它们的耐磨性和耐疲劳性,从而提高整车的可靠性和使用寿命。
机械制造业在机械制造业中,表面热处理常用于刀具、模具、轴承等零部件的制造。
通过对这些零部件进行硬化处理,可以提高它们的硬度和耐磨性,从而延长其使用寿命,并提高加工效率。
能源行业在能源行业中,表面热处理常用于燃气轮机、汽轮机、发电机等设备的制造。
通过对这些设备的叶片和叶栅进行表面改性处理,可以提高它们的耐腐蚀性和抗磨损性,从而提高能源设备的运行效率和可靠性。
航空航天业在航空航天业中,表面热处理常用于航空发动机、飞机结构和航天器零部件的制造。
通过对这些部件进行热软化和硬化处理,可以提高它们的强度和耐久性,从而确保航空航天器的安全性和可靠性。
钛合金的热处理基本原理(一)
钛合金的热处理基本原理(一)钛合金的热处理基本1. 什么是钛合金的热处理?钛合金是一种轻巧、高强度、耐腐蚀的金属材料。
然而,由于钛合金的制造过程中可能会导致材料内部存在一些不稳定晶相或缺陷,因此需要进行热处理。
热处理是通过加热和冷却的不同方式改变钛合金的晶体结构和性能,以达到所需的材料性能。
本文将介绍钛合金热处理的基本原理和常用方法。
2. 钛合金的热处理原理钛合金的热处理原理基于以下两个基本原则:固溶处理原理固溶处理是指将钛合金加热至其固溶温度以上,使合金中的溶质原子均匀地溶解在基体晶格中。
通过固溶处理,可以消除钛合金中的不稳定相,提高合金的强度和塑性。
相变处理原理相变处理是指在固溶处理的基础上,通过控制冷却速度使钛合金的晶体结构发生相变。
相变处理可以改变钛合金的晶体结构和晶界形貌,从而调整其力学性能和耐腐蚀性能。
钛合金的热处理方法主要包括固溶处理和时效处理两种。
下面将分别介绍这两种方法:固溶处理固溶处理是钛合金热处理的基础步骤,它可以消除钛合金中的不稳定相和缺陷,提高合金的强度和塑性。
固溶处理的具体步骤如下:•加热:将钛合金加热至其固溶温度以上,一般在摄氏度范围内。
•保温:保持合金在固溶温度下足够长的时间,使溶质原子充分溶解在基体中。
•冷却:迅速冷却合金至室温,固定溶质原子在基体中。
时效处理时效处理是在固溶处理的基础上进行的钛合金热处理方法,通过控制冷却速度,使合金的晶体结构发生相变,从而调整其力学性能和耐腐蚀性能。
时效处理的具体步骤如下:•固溶处理:按照固溶处理的方法对钛合金进行加热和冷却处理。
•时效处理:将处理过的钛合金再次加热至合金中存在的稳定相的温度,并保持一段时间。
•冷却:迅速冷却合金至室温,固定相变后的晶体结构。
钛合金的热处理广泛应用于航空航天、汽车、医疗器械等领域。
通过热处理,可以增加钛合金的强度和保持其良好的耐腐蚀性能,提高材料的使用寿命。
5. 结论钛合金热处理是一种重要的材料加工方法,通过固溶处理和时效处理可以调整钛合金的晶体结构和性能。
金属热处理原理与工艺
金属热处理原理与工艺金属热处理是指对金属材料进行加热处理来改变其组织结构和性质的一种方法。
这种方法可以通过控制加热温度和保温时间等参数来实现不同的处理效果。
金属热处理可以改善金属的硬度、强度、韧性、延展性、耐磨性、耐腐蚀性等性能,从而满足不同的工业应用需求。
金属热处理的原理金属热处理的原理基于金属的组织结构和性质随温度的变化而变化。
当金属材料受到热加工时,温度升高会导致金属晶粒的尺寸增加,晶粒之间的间距变大,这使得金属的塑性和韧性增加。
而当金属材料受到冷加工时(如锻造、轧制),由于冷加工过程中金属材料处于冷却状态,因此晶粒不会发生明显的变形,而是保持原来的晶粒组织。
这种组织结构会使金属变得更加硬而脆,但相应的韧性和延展性会降低。
金属热处理的工艺金属热处理的工艺包括加热、保温和冷却等步骤。
根据不同的处理效果,这些步骤的温度和时间可以做出相应的调整。
以下是几种常见的金属热处理方法:1. 灭火处理:灭火处理是指将金属加热至高温后迅速冷却至室温的处理过程。
这种处理可以改变金属的组织结构,从而提高其硬度和强度。
灭火处理通常适用于需要较高硬度和强度的金属制品。
2. 固溶处理:固溶处理是指将金属加热至一定温度后进行保温,使固态的金属中的固溶体中的扰动原子可以逸出到基体里。
这种处理可以改变金属的组织结构,从而提高其韧性和延展性。
固溶处理通常适用于需要具有良好机械性能和耐腐蚀性的金属制品。
3. 时效处理:时效处理是指将金属加热至一定温度进行保温,然后迅速冷却后再进行再加热保温的过程。
这种处理可以使金属的晶粒长大并沉淀出一些固相化合物,从而提高金属的强度和硬度。
时效处理通常适用于需要高强度和高韧性的金属制品。
4. 钝化处理:钝化处理是指将金属制品加热至一定温度后,在空气或氧化性环境中,使其表面形成一层韧性较强的氧化皮。
这种处理可以使金属制品具有较好的耐腐蚀性。
金属热处理是一种重要的金属加工工艺,可以通过控制加热温度、保温时间和冷却速率等参数来实现不同的处理效果,以满足不同的工业应用需求。
- 1、下载文档前请自行甄别文档内容的完整性,平台不提供额外的编辑、内容补充、找答案等附加服务。
- 2、"仅部分预览"的文档,不可在线预览部分如存在完整性等问题,可反馈申请退款(可完整预览的文档不适用该条件!)。
- 3、如文档侵犯您的权益,请联系客服反馈,我们会尽快为您处理(人工客服工作时间:9:00-18:30)。
(a)亚共析钢
(b)共析钢
(c)过共析钢
图4.9 亚共析碳钢、共析碳钢及过共析碳钢的C曲线比较
(3)影响 C 曲线的主要因素
②合金元素的影响
除 Co 外,凡溶入A的Me, 都能增加A’的稳定性,使C 曲 线右移。
除 Co 和 Al 外,凡溶入A的 Me均能使Ms 与Mf 点下降。
③ 奥氏体化条件的影响
(2)C曲线分析
转变开始线与纵坐标之间 的距离为孕育期。孕育期越 小,过冷奥氏体稳定性越小. 孕育期最小处称C 曲线的 “鼻尖”。碳钢鼻尖处的温 度为550℃。 在鼻尖以上, 温度较高,相 变驱动力小;在鼻尖以下,温 度较低,扩散困难。从而使 奥氏体稳定性增加。 C曲线明确表示了过冷奥 氏体在不同温度下的等温转 变产物。
③ M的组织形态与性能
影响M形态的因素
M形态→M转变温度→A化学成分(如左下图所示) 0.2%C 低碳M;1.0%C 高碳M。 0.2%~1.0%C:当小于0.6%C时,以低碳M为主;当大于0.6%C时,以高碳M为主。应
注意:A的碳含量≠钢的碳含量
随钢中奥氏体碳含量的增加,M的转变温度下降,残余奥氏体量增加, 如右下图所示。
(3)贝氏体(B)转变
4.过冷奥氏体连续冷却转变曲线(CCT曲线)
5.过冷奥氏体转变曲线的应用
请看:两张表
45钢经840加热,于不同冷却速度冷却后的性能(表4.1)
T8钢经不同速度冷却后的性能(10mm,800加热)
请思考? 1. 为什么钢(45,T8)加热A化后于不同冷却速度下的性能会有 如此的差别呢? 2. 为什么冷却速度越快,钢的硬度、强度越高,而塑性、韧性则 越低呢?
4.2 金属材料热处理原理
4.2.1 钢在加热时的转变 4.2.2 奥氏体在冷却时的转变 4.2.3 淬火钢在回火时的转变 4.2.4 金属材料的脱溶沉淀与时效
请思考 ?(见教材P83问题提示)
1.铁碳合金相图在钢铁材料热处理中的作用是什么呢? 钢铁材料冷却转变曲线(TTT、CCT曲线)的物理意义 是什么?您会使用它来分析不同热处理条件下所获得的 转变产物(组织)吗?您能在TTT或CCT曲线上示意地 标出退火、正火、单液淬火、双液淬火、等温淬火、分 级淬火与不完全淬火的冷却速度曲线吗? 2.“五大转变”指的是哪五种类型的转变,试从转变性 质、所处温度范围、转变特征、组织、性能的变化与应 用等方面说明?
以共析钢为例(如右图4.7所示→): i取一批小试样并进行奥氏体化. ii将试样分组淬入低于A1点的不同温度的盐浴中, 隔一定时间取一试样淬入水中。 iii测定每个试样的转变量,确定各温度下转变量 与转变时间的关系。 iv将各温度下转变开始时间及终了时间标在温 度—时间坐标中,并分别连线。
转变开始点的连线称转变开始线。转变 终了点的连线称转变终了线。
#P片层间距与硬度的关系图
#P片层间距与转变温度、性能关系
②珠光体的组织形态与性能
球化体(粒状珠光体)
球化体与片状P相比:
i 当碳含量相同时,球化
体的塑韧性好,可切削加
工性好,冷挤压成形性也
好,加热淬火时变形、开
裂倾向也小;
i i 当σb相同时,球化体 的σ-1高;
iii 当硬度相同时,球化
(a)
4.2.2 奥氏体在冷却时的转变
1.奥氏体冷却转变的理论依据是什麽?
2.过冷奥氏体的等温冷却转变曲线(C ,TTT曲线)
(1)C曲线是如何建立的?(2)C曲线分析
(3)影响C曲线的主要因素有哪些?
①化学成分(碳含量;合金元素的含量);②奥氏体化条件
3.过冷奥氏体转变产物的组织与性能
(1)珠光体(P)转变;(2)马氏体(M)转变;
线右端下降.
过共析钢CCT曲线
亚共析钢CCT曲线
5. 过冷奥氏体转变曲线的应用
(1)C曲线的应用
图4.23 在 C曲线上估 计连续冷却 时过冷奥氏 体转变产物 示意图
水油 冷冷
炉 空冷 冷
P
S
M+A’ T+M+A’
用C曲线定性说明共析钢连续冷却时
CCT曲线获得困难;
的组织转变
TTT曲线容易测得. 可用TTT曲线定性说明连续冷却时的组织转变情况。方
i 共析钢的CCT曲线没有贝体氏组体织转时变的区最,小在冷P转却变速区度之. 下多了一条转变中止线(K线)。
当连续冷却曲线碰到K线时,P转变中止,余下的过冷奥氏体一直保持到Ms以下
转变为M。
ii CCT曲线位于C曲线的右下方。
4.过冷奥氏体连续冷却转变曲线
它是通过测定不同冷速下过冷奥氏体的转变量获得的。
线
正方度越大,正方畸变越严重;当<0.25%C时,
c /a =1, 此时M为BCC晶格.
图4.15 M的晶体 结构示意图 →
因此,伴随M形成其比容增大,由此产生组织应力,易使工件产生变形开裂。
③ M的 组织形态与性能
钢中M的组织形态主要有板条状和片状两种基本类型。
板条状M,位错M或低碳M
片状M,孪晶M或高碳 M
片状珠光体的显微组织图
P(珠光体)→
(a)500× (b)8000×
(c)1000×
(d)19000×
← S(索氏体)
T(托氏体)→
(e)200× (f)19000×
3. 过冷奥氏体转变产物的组织与性能
(1) 珠光体(P)转变 (A1~550℃,高温转变或扩散型相变)
②珠光体的组织形态与性能
片状珠光体的性能
(b)
(c)
珠光体的硬度(a);(b)形态1000X;(c)原始组织1000X
体的综合力学性能好(不
易产生应力集中、裂纹)。
因此,高碳钢在机械加
工和最终热处理之前,常
要求材料先经球化退火处
理,以获得均匀的球化体
组织。
片状P与球化体力学性能对比
片状P与球化体切削性能比较
(2)马氏体(M)转变
① M的形成条件(T<MS,V>VkC)
图4.24 亚共析钢CCT曲线 图4.21 共析钢CCT曲 线
#过共析钢CCT曲线
4. 过冷奥氏体连续冷却转变曲线 (CCT曲线)
过共析钢CCT曲线也无贝氏体转变区, 但比共析钢CCT曲线多一条A→Fe3C转变开始线。
由于Fe3C的析出, 奥氏体中含碳量下降, 因而Ms 线右端升高.
亚共析钢CCT 曲线有贝氏体转变区,还多A→F开始线, F析出使A含碳量升高, 因而Ms
(2)注意区分三种奥氏体晶粒度
A起始晶粒度; A实际晶粒度; A本质晶粒度(如图4.5所示)。
(3)奥氏体晶粒度的控制
①合理选择加热条件; ②加热速度的选择(右下图示); ③化学成分的控制
图4.5 本质细晶粒和本质粗晶粒示意图
#珠光体向奥氏体的转变过程图
因此在热处理加热时,应严格控制加热温度、保温时间、加热速度及合理选择钢种。
图4.# M形态与碳含量关系
图4.# 奥氏体的碳含量对M转变温度(a)及AR量(b)的影 响
③ M的组织形态与性能
M的性能 M具有高强度、高硬度:固溶强化,相变强化,时效强化,细晶强化
等。 M是最经济、有效的综合强化效果。 M具有高的硬度和强度。M的硬度主要取决于碳含量(如右下图所示)。
表4.# 淬火钢的塑、韧性与碳含量间关系
请思考:回顾金工实习,各种热处理工艺的
共同点是什么?
(a)加热温度
(b)工艺规范
图4.35 各种退火与正火工艺规范
碳钢淬火加热温度范围
热处理工艺曲线示意图→
4.2.1 钢在加热时的转变
1.钢加热转变的理论依据是什麽?
加热和冷却对临界转变温度的影响 铁碳相图中PSK、GS、ES线分别用A1、A3、Acm表示。 实际加热或冷却时存在着过冷或过热现象,因此将钢加热时的实际转变温度分别 用Ac1、Ac3、Accm表示;冷却时的实际转变温度分别用Ar1、Ar3、Arcm表示。 因加热或冷却速度直接影响转变温度,因此一般热处理手册中的数据是以30~ 50℃/h的速度加热或冷却时测得的。
(a)Co
(b)Ni
(c)Cr
图4.10 Me对C曲线的影响
奥氏体化温度提高和保温时间延长,使奥氏体成分均匀、晶粒粗大、未溶 碳化物减少,增加了过冷奥氏体的稳定性,使C 曲线右移。
使用C 曲线时应注意奥氏体化条件及晶粒度的影响.
3. 过冷奥氏体转变产物的组织与性能
(1) 珠光体(P)转变 (A1~550℃,高温转变或扩散型相变)
金相显微组织500X 电子显微组织4000X
表4.2 贝氏体型转变的
形成温度、转变机制、
组织特征、形成特点、
硬度及性能特点,获得
工艺
→
A’等温转变的类型、产物、性能及特 征
注意区分与比较:
两种马氏体的性能比较(如下表所示)
贝氏体转变特征一览表(共析钢)
4. 过冷奥氏体连续冷却转变曲线 (CCT曲线)
C 曲线的物理意义
C曲线的 物理意 义——即
指C曲线中 各条特性线 的含义,以 及各个区域 的组织这双 层含义。
图4.8 共析碳钢的A’等温冷却转变曲线(C曲线)分析
2. 过冷A等温冷却转变曲线(C曲线)
C曲线的物理意义 (各条特性线含义;各区域组织)
各个区域对应何种类型组织?
①A1~Ms
间及转变开始线以左的区域为A’
温 度
(过冷奥氏体)区;
过
A1
A
②转变终了线以右及A1以下为转变产物区; ③两C线之间为A ’与转变产物共存区;
④MS~Mf之间为M转变区。
特性线A1 ,MS , C左 , C右线的含
冷 A’
P
A