连接器工艺流程
连接器生产工艺

连接器生产工艺连接器是一种用于连接电子设备和电路的零部件,广泛应用于电子、通信、汽车等领域。
连接器的生产工艺决定了连接器的质量和性能,下面将介绍连接器的一般生产工艺。
连接器的生产工艺通常包括以下几个主要步骤:1.材料准备:连接器的主要材料包括金属、塑料和电子元件。
金属材料通常是铜合金,塑料材料通常是工程塑料。
在生产之前,需要根据产品设计要求选择合适的材料,并进行材料预处理,如切割、研磨和除锈等。
2.注塑成型:连接器的壳体和插针部分通常是通过注塑成型来生产的。
在注塑成型过程中,需要将预处理好的塑料颗粒放入注塑机中,加热熔化后注塑到模具中,经冷却后得到连接器的塑胶部分。
注塑成型的关键是保持模具的温度和压力的稳定,以确保产品的外观和尺寸精度。
3.金属加工:连接器的金属零件通常需要进行一系列的加工和处理,如冲压、切削、焊接和电镀等。
冲压是连接器生产中常用的金属加工方法,通过模具将金属板料按照要求的形状冲压成型。
切削是用于加工连接器的细小零件,如插针。
焊接是将连接器的金属零件进行连接的一种方法,主要用于连接壳体和插针。
电镀是对连接器的金属零件进行表面处理的一种方法,可以提高连接器的外观和耐腐蚀性能。
4.组装和测试:连接器的组装是将各种零件组装成完整的连接器的过程。
组装通常包括将塑胶部分和金属零件进行插接和固定,然后进行压合和焊接等操作。
组装完成后,还需要对连接器进行功能和性能测试,以确保连接器的质量和性能符合要求。
5.质量控制:连接器生产过程中还需要进行严格的质量控制,以确保连接器的质量和性能。
质量控制包括原材料的检验、过程控制、成品检验和不良品处理等。
其中,成品检验通常包括外观检查、尺寸测量和功能测试等。
以上是连接器的一般生产工艺,每个连接器的生产工艺可能会有细微的差异,具体的工艺流程还需要根据产品的不同要求进行调整。
连接器的生产工艺对连接器的质量和性能至关重要,良好的生产工艺能够保证连接器具有稳定的性能和可靠的品质。
连接器molding工艺流程及原理

连接器molding工艺流程及原理下载温馨提示:该文档是我店铺精心编制而成,希望大家下载以后,能够帮助大家解决实际的问题。
文档下载后可定制随意修改,请根据实际需要进行相应的调整和使用,谢谢!并且,本店铺为大家提供各种各样类型的实用资料,如教育随笔、日记赏析、句子摘抄、古诗大全、经典美文、话题作文、工作总结、词语解析、文案摘录、其他资料等等,如想了解不同资料格式和写法,敬请关注!Download tips: This document is carefully compiled by theeditor. I hope that after you download them,they can help yousolve practical problems. The document can be customized andmodified after downloading,please adjust and use it according toactual needs, thank you!In addition, our shop provides you with various types ofpractical materials,such as educational essays, diaryappreciation,sentence excerpts,ancient poems,classic articles,topic composition,work summary,word parsing,copy excerpts,other materials and so on,want to know different data formats andwriting methods,please pay attention!连接器molding工艺是一种将塑料等材料通过注塑成型的方式制成连接器的过程。
连接器生产工艺流程

连接器生产工艺流程连接器是一种用于电子设备以及通信设备的重要组件,用于连接电路之间的信号传输。
连接器的生产工艺流程主要包括材料选择、模具设计、注塑成型、金属加工、电镀处理和组装等环节。
首先,连接器的生产过程始于材料选择。
连接器的材料选择非常重要,需具备良好的导电性能、耐高温性能、抗腐蚀性能以及机械强度。
常见的连接器材料有铜、铜合金、不锈钢等。
根据不同的要求和用途选择合适的材料。
接下来是模具设计。
模具设计是连接器生产过程中关键的一步。
根据产品的形状和规格要求,设计出合适的模具结构。
模具设计需要考虑到产品的尺寸精度、结构复杂度以及模具的可制造性等方面的要求。
随后是注塑成型。
注塑成型是连接器生产的关键环节之一。
通过将加热熔融的塑料材料注入到模具中,使其熔解、流动、冷却固化得到产品的成型。
注塑成型的过程需要控制好温度、压力以及注射速度等参数,以保证产品质量。
之后是金属加工。
对于某些连接器来说,金属加工是必不可少的一步。
金属加工包括冲压、弯曲、车削、铣削等工艺,用于制作连接器的金属部件。
金属加工过程中需要重点考虑尺寸精度、表面光洁度以及材料的变形等问题。
接下来是电镀处理。
电镀处理可提高连接器的导电性能、耐腐蚀性能以及外观质量。
常见的电镀处理方法有镀金、镀银、镀锡、镀镍等。
电镀处理需要控制好电镀液的成分、温度以及电流密度等参数,以保证电镀层的均匀度和质量。
最后是连接器的组装。
连接器的组装包括插座的安装、端子的焊接、密封圈的安装等步骤。
组装工艺需要控制好各个组件的相对位置和配合精度,以确保连接器的功效和可靠性。
总之,连接器的生产工艺流程包括材料选择、模具设计、注塑成型、金属加工、电镀处理和组装等环节。
每个环节都需要精细的操作和严格的控制,以确保连接器质量的稳定和可靠性。
只有通过优化和改进生产工艺流程,才能不断提升连接器的品质,并满足不同用户对电子设备和通信设备连接需求的日益增长。
连接器工艺流程范文

连接器工艺流程范文一、工艺准备阶段:1.确认连接器的规格型号、数量以及工艺要求;2.准备相应的连接器工艺文件和工艺工具;3.检查工艺工具的完好性和准确性,确保可以正常使用。
二、连接器组装阶段:1.将连接器的各个部件按照要求进行组装,包括端子、插座、插板等,确保正确、稳固地组装好;2.进行连接器的电气测试,确认连接器的电气性能符合要求。
三、连接器焊接阶段:1.选择适当的焊接方法,常用的有手工焊接、波峰焊接、回流焊接等;2.根据连接器的具体要求,在相应的位置焊接端子或插座,确保焊接牢固、稳定;3.进行焊接过程的质量控制,如焊接温度、时间的监控等。
四、连接器插装阶段:1.根据连接器的特点和应用要求,选择合适的插装方式,包括手工插装、机械插装等;2.将焊接好的连接器插装到相应的插孔或插座中,确保插座位置正确、连接紧密;3.进行插装后的连接器的电气测试,确认连接器的电气性能良好。
五、连接器包封阶段:1.选择合适的包封材料,常用的有热塑性材料、热固性材料等;2.将连接器进行包封,保护连接器的内部结构免受外部环境的侵蚀;3.进行包封后的连接器的外观检查,确保包封完好、外观整洁。
六、连接器测试阶段:1.对连接器进行全面的功能测试,包括电气性能测试、机械性能测试等;2.根据连接器的要求,进行寿命测试、温度测试等特殊测试;3.将测试结果和连接器的要求进行对比,确保连接器的性能符合要求。
七、连接器维护阶段:1.定期对连接器进行维护,包括清洁、检查等,确保连接器的正常工作;2.对连接器的维护情况进行记录,及时处理连接器出现的故障或问题;3.定期对连接器的工艺流程进行评估和改进,提高连接器的生产效率和质量。
以上就是连接器工艺流程的详细介绍,通过严格按照工艺流程进行操作,可以确保连接器的质量稳定、生产效率高,并能提供可靠的连接和电气性能。
射频连接器工艺流程

射频连接器工艺流程
射频连接器的工艺流程包括以下几个步骤:
1. 冲压加工:这是制造射频连接器的第一步,涉及到使用大型高速冲压机将薄金属带冲压成插针。
大卷的金属带一端送入冲压机前端,另一端穿过冲压机液压工作台缠入卷带轮,由卷带轮拉出金属带并卷好冲压出成品。
2. 电镀:在射频插针冲压完成后,需要将其送至电镀工段。
在此阶段,连接器的电子接触表面将镀上各种金属涂层。
3. 注塑加工:射频连接器的塑料盒座在注塑阶段制成。
通常的工艺是将熔化的塑料注入金属胎膜中,然后快速冷却成形。
4. 组装:射频连接器制造的最后阶段是成品组装。
将电镀好的插针与注塑盒座接插的方式有两种:单独对插或组合对插。
单独对插是指每次接插一个插针;组合对插则一次将多个插针同时与盒座接插。
以上信息仅供参考,如有需要,建议咨询专业工程师。
连接器生产工艺流程
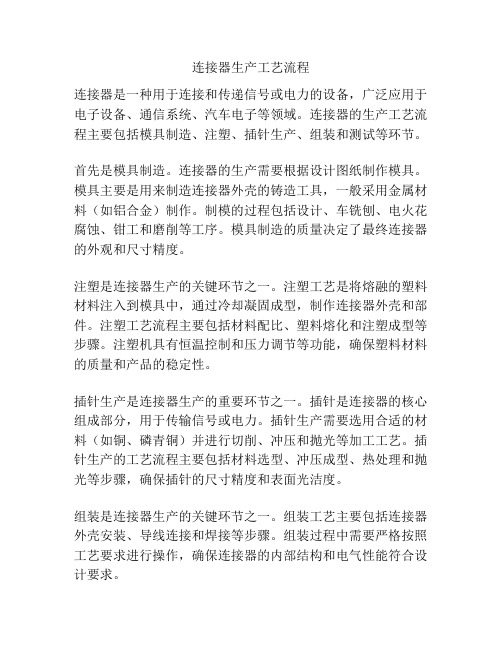
连接器生产工艺流程连接器是一种用于连接和传递信号或电力的设备,广泛应用于电子设备、通信系统、汽车电子等领域。
连接器的生产工艺流程主要包括模具制造、注塑、插针生产、组装和测试等环节。
首先是模具制造。
连接器的生产需要根据设计图纸制作模具。
模具主要是用来制造连接器外壳的铸造工具,一般采用金属材料(如铝合金)制作。
制模的过程包括设计、车铣刨、电火花腐蚀、钳工和磨削等工序。
模具制造的质量决定了最终连接器的外观和尺寸精度。
注塑是连接器生产的关键环节之一。
注塑工艺是将熔融的塑料材料注入到模具中,通过冷却凝固成型,制作连接器外壳和部件。
注塑工艺流程主要包括材料配比、塑料熔化和注塑成型等步骤。
注塑机具有恒温控制和压力调节等功能,确保塑料材料的质量和产品的稳定性。
插针生产是连接器生产的重要环节之一。
插针是连接器的核心组成部分,用于传输信号或电力。
插针生产需要选用合适的材料(如铜、磷青铜)并进行切削、冲压和抛光等加工工艺。
插针生产的工艺流程主要包括材料选型、冲压成型、热处理和抛光等步骤,确保插针的尺寸精度和表面光洁度。
组装是连接器生产的关键环节之一。
组装工艺主要包括连接器外壳安装、导线连接和焊接等步骤。
组装过程中需要严格按照工艺要求进行操作,确保连接器的内部结构和电气性能符合设计要求。
最后是测试。
测试是连接器生产的最后环节,用来检测连接器的质量和性能。
测试工艺主要包括外观检查、电阻测试、接触力测试、耐压测试和防水性能测试等。
测试的目的是确保连接器的可靠性和稳定性,提高连接器的质量和可信度。
总之,连接器的生产工艺流程涉及模具制造、注塑、插针生产、组装和测试等环节。
通过科学的工艺流程和严格的质量控制,可以生产出高质量和可靠性能的连接器产品。
连接器的工艺生产流程
连接器的工艺生产流程连接器是一种常用的电子元件,广泛应用于电子设备和通信领域。
连接器工艺生产流程是指连接器从原材料到最终产品的整个制造过程。
下面将为您详细介绍连接器的工艺生产流程。
第一步:材料准备连接器的制造需要使用多种材料,包括金属、塑料、绝缘材料等。
在工艺生产流程中,首先需要对各种材料进行准备和筛选,确保其质量和性能符合要求。
第二步:模具设计和制造连接器的制造需要使用模具,用于成型不同形状和尺寸的连接器零件。
模具的设计和制造非常关键,需要考虑到连接器的功能需求、尺寸精度和生产效率等因素。
第三步:金属加工连接器的金属零件通常采用冲压工艺进行加工。
首先,将金属板材放入冲压机中,通过冲压模具对其进行切割和成形。
然后,再进行折弯、冲孔和螺纹等工艺,最终得到需要的金属连接器零件。
第四步:塑料注塑连接器的塑料零件通常采用注塑工艺进行制造。
首先,将塑料颗粒加热熔融,然后将熔融的塑料注入到注塑机的模具中。
随后,通过压力和冷却过程,塑料凝固并形成连接器的塑料零件。
第五步:绝缘材料加工连接器中需要使用绝缘材料来隔离和保护电路,常见的绝缘材料有胶水、绝缘胶等。
绝缘材料的加工可以通过涂覆、注塑或胶合等方式完成。
第六步:组装和焊接连接器的组装通常包括将金属零件、塑料零件和绝缘材料组合在一起,并通过焊接或压接等方式进行固定。
组装过程中,需要严格控制连接器零件的位置和间距,确保其符合设计要求。
第七步:质量检测在连接器的工艺生产流程中,质量检测是非常重要的环节。
通过使用各种测试设备和仪器,对连接器的外观、尺寸、电气性能等进行全面检测,确保连接器达到质量标准要求。
第八步:包装和出货最后,连接器经过质量检测合格后,进行包装和出货。
连接器通常采用包装盒或塑料袋进行包装,并附上相关的产品标签和说明书等。
然后,将连接器出货给客户或分销商,以供他们使用或销售。
通过以上八个步骤,连接器的工艺生产流程就完成了。
这个流程是一个复杂而精细的过程,需要经过多道工序和环节的处理。
连接器生产工艺流程
连接器生产工艺流程
《连接器生产工艺流程》
连接器生产过程包括材料选购、模具设计、注塑成型、金属加工、装配和测试等多个环节。
下面是连接器生产的一般工艺流程:
1. 材料选购:首先需要确定连接器要使用的材料,一般包括塑料、金属、电镀材料等。
选择合适的材料对连接器的性能和可靠性具有至关重要的影响。
2. 模具设计:根据连接器的尺寸和形状,设计出适用的注塑模具和金属冲压模具。
模具的设计需要考虑连接器的结构和功能,以及生产效率和成本等因素。
3. 注塑成型:将塑料粒子加热到熔化状态后,通过注射成型机器将熔化的塑料注入到模具中,冷却后成型出连接器的外壳和插座。
注塑成型需要严格控制温度、压力和注射速度,以获得高质量的连接器外壳。
4. 金属加工:将金属材料经过冲床冲压成连接器的金属接触片和插脚等部件。
金属加工需要精准的模具和严格的工艺控制,以保证连接器的接触性能和耐久性。
5. 装配:将注塑成型的外壳和金属部件进行组装,包括焊接、粘接、插接等操作。
装配过程需要严格控制工艺参数,确保连接器的组装质量和性能。
6. 测试:对连接器进行功能测试、外观检查、接触电阻测试等检验,以确保连接器的可靠性和符合规定的标准。
连接器生产工艺流程需要各个环节之间紧密配合,严格控制每个细节,以确保连接器质量和性能达到客户要求。
同时,不断改进工艺技术和生产设备,提高生产效率和产品质量,是连接器生产过程中的关键。
玻璃烧结密封连接器工艺
玻璃烧结密封连接器工艺玻璃烧结密封连接器是一种常用于电子器件和光学器件中的连接器。
它具有优异的高温稳定性、密封性能和机械强度,因此被广泛应用于航空航天、汽车电子、通信设备等领域。
本文将详细介绍玻璃烧结密封连接器的工艺流程和关键技术。
一、玻璃烧结密封连接器的工艺流程1. 材料准备:选择合适的玻璃粉末作为基材,并根据实际需求添加适量的助熔剂和稳定剂。
将材料粉末进行混合和研磨,以确保均匀性和细度。
2. 成型:将混合均匀的玻璃粉末通过注塑、压制等方法成型成所需的形状,如圆柱形、方形等。
成型后的零件需要经过烘干以去除水分。
3. 烧结:将成型的零件置于高温炉中进行烧结处理。
烧结温度和时间需要根据所使用的玻璃材料和连接器的要求进行调控。
烧结过程中,玻璃粉末会熔融并与助熔剂反应,形成致密的玻璃连接体。
4. 精加工:经过烧结后的零件需要进行精加工,包括切割、打磨、抛光等工艺,以满足连接器的尺寸和表面粗糙度要求。
5. 密封:将经过精加工的玻璃连接体与金属导体或其他器件进行密封连接。
可采用焊接、粘接等方式进行连接。
密封连接的质量和稳定性对于连接器的性能至关重要。
6. 检测:对密封连接器进行严格的质量检测,包括外观检查、尺寸测量、渗透测试等。
确保连接器的可靠性和完整性。
二、玻璃烧结密封连接器的关键技术1. 材料选择:选择合适的玻璃材料对于连接器的性能至关重要。
需要考虑玻璃的熔点、热膨胀系数、化学稳定性等因素,以及与金属导体的匹配性。
2. 烧结控制:烧结温度和时间的控制对于连接器的致密性和机械强度具有重要影响。
过高的温度可能导致玻璃熔化过度,而过低的温度则无法实现完全烧结。
3. 密封连接:选择适当的密封方式和材料,确保连接器具有良好的密封性能和电气性能。
焊接和粘接是常用的密封方式,需要考虑连接的可靠性和耐高温性。
4. 表面处理:连接器的表面粗糙度和平整度对于连接的稳定性和信号传输具有重要影响。
需要采用适当的加工工艺,如抛光、电镀等,以提高表面质量。
连接器工艺流程
连接器工艺流程连接器是一种用于连接电子设备的重要部件,广泛应用于电子通信、计算机、汽车、航空航天等领域。
连接器的工艺流程是连接器制造的重要环节,下面将详述连接器的工艺流程。
首先,连接器的工艺流程始于材料的准备。
连接器的主要材料包括金属、塑料、电子元件等。
首先需要对这些材料进行选择和采购,确保材料的质量符合要求。
然后根据连接器的要求,对材料进行切割、磨光、抛光等预处理工艺,以准备好待连接的零部件。
其次,连接器的工艺流程包括零部件的加工。
通过加工工艺,将感应极、插座等各种零部件加工成形,并确保其尺寸精确、形状规整。
加工工艺包括数控加工、冲压、注塑等,需要使用特定的设备和工具。
在加工过程中,需要对零部件进行质量检测,以保证其质量符合要求。
然后,连接器的工艺流程包括组装。
组装是连接器制造的重要环节,主要是将各种零部件按照设计要求进行组合。
组装工艺包括焊接、粘接、装配等。
在组装过程中,需要进行严格的质量控制,确保连接器的性能和可靠性。
同时,还需要进行功能测试和外观检查,以确保连接器能够正常工作和符合外观要求。
最后,连接器的工艺流程结束于包装和出厂。
连接器的包装主要是保护连接器免受损坏和污染,如使用泡沫塑料、纸箱等进行包装。
在包装过程中,还需要对连接器进行标识和记录,以便追溯和管理。
最后,连接器经过质量检验后,将被送往仓库,等待发货。
总之,连接器的工艺流程是一个复杂的制造过程,涉及材料准备、零部件加工、组装和包装等多个环节。
在整个流程中,需要严格控制质量,确保连接器的性能和可靠性。
连接器作为电子设备的重要组成部分,对产品的性能和稳定性起着重要的作用,连接器的工艺流程对产品的质量和可靠性有着直接的影响。
- 1、下载文档前请自行甄别文档内容的完整性,平台不提供额外的编辑、内容补充、找答案等附加服务。
- 2、"仅部分预览"的文档,不可在线预览部分如存在完整性等问题,可反馈申请退款(可完整预览的文档不适用该条件!)。
- 3、如文档侵犯您的权益,请联系客服反馈,我们会尽快为您处理(人工客服工作时间:9:00-18:30)。
电子连接器种类繁多,但制造过程基本可分为下面四个阶段:
·冲压(Stamping)
·电镀(Plating)
·注塑(Molding)
·组装(Assembly)
冲压
电子连接器的制造过程一般从冲压插针开始。
通过大型高速冲压机,电子连接器(插针)由薄金属带冲压而成。
大卷的金属带一端送入冲压机前端,另一端穿过冲压机液压工作台缠入卷带轮,由卷带轮拉出金属带并卷好冲压出成品。
电镀
连接器插针冲压完成後即应送去电镀工段。
在此阶段,连接器的电子接触表面将镀上各种金属涂层。
与冲压阶段相似的一类问题,如插针的扭曲、碎裂或变形,也同样会在冲压好的插针送入电镀设备的过程中出现。
通过本文所阐述的技术,这类品质缺陷是很容易被检测出来的。
然而对於多数机器视觉系统供应商而言,电镀过程中所出现的许多品质缺陷还属於检测系统的"禁区"。
电子连接器制造商希望检测系统能够检测到连接器插针电镀表面上各种不一致的缺陷如细小划痕和针孔。
尽管这些缺陷对於其他产品(如铝制罐头底盖或其他相对平坦的表面)是很容易被识别出来的;但由於大多数电子连接器不规则和含角度的表面设计,视觉检测系统很难得到足以识别出这些细微缺陷所需的图像。
由於某些类型的插针需镀上多层金属,制造商们还希望检测系统能够分辨各种金属涂层以便检验其是否到位和比例正确。
这对於使用黑白摄像头的视觉系统来说是非常困难的任务,因为不同金属涂层的图像灰度级实际上相差无几。
虽然彩色视觉系统的摄像头能够成功分辨这些不同的金属涂层,但由於涂层表面的不规则角度和反射影响,照明困难的问题依然存在。
注塑
电子连接器的塑胶盒座在注塑阶段制成。
通常的工艺是将熔化的塑胶注入金属胎膜中,然後快速冷却成形。
当熔化塑胶未能完全注满胎膜时出现所谓 "漏?quot; (Short Shots), 这是注塑阶段需要检测的一种典型缺陷。
另一些缺陷包括接插孔的填满或部分堵塞(这些接插孔必须保持清洁畅通以便在最後组装时与插针正确接插)。
由於使用背光能很方便地识别出盒座漏缺和接插孔堵塞,所以用於注塑完成後品质检测的机器视觉系统相对简单易行
组装
电子连接器制造的最後阶段是成品组装。
将电镀好的插针与注塑盒座接插的方式有两种:单独对插或组合对插。
单独对插是指每次接插一个插针;组合对插则一次将多个插针同时与盒座接插。
不论采取哪种接插方式,制造商都要求在组装阶段检测所有的插针是否有缺漏和定位正确;另外一类常规性的检测任务则与连接器配合面上间距的测量有关。
和冲压阶段一样,连接器的组装也对自动检测系统提出了在检测速度上的挑战。
尽管大多数组装线节拍为每秒一到两件,但对於每个通过摄像头的连接器,视觉系统通常都需完成多个不同的检测专案。
因而检测速度再次成为一个重要的系统性能指标。
组装完成後,连接器的外形尺寸在数量级上远大於单个插针所允许的尺寸公差。
这点也对视觉检测系统带来了另一个问题。
例如:某些连接器盒座的尺寸超过一英尺而拥有几百个插针,每个插针位置的检测精度都必须在几千分之一英寸的尺寸范围内。
显
然,在一幅图像上无法完成一个一英尺长连接器的检测,视觉检测系统只能每次在一较小视野内检测有限数目的插针品质。
为完成整个连接器的检测有两种方式:使用多个摄像头(使系统耗费增加);或当连接器在一个镜头前通过时连续触发相机,视觉系统将连续摄取的单祯图像"缝合"起来,以判断整个连接器品质是否合格。
後一种方式是PPT视觉检测系统在连接器组装完成後通常所采用的检测方法。
"实际位置"(True Position)的检测是连接器组装对检测系统的另一要求。
这个"实际位置"是指每个插针顶端到一条规定的设计基准线之间的距离。
视觉检测系统必须在检测图像上作出这条假想的基准线以测量每个插针顶点的"实际位置"并判断其是否达到品质标准。
然而用以划定此基准线的基准点在实际的连接器上经常是不可见的,或者有时出现在另外一个平面上而无法在同一镜头的同一时刻内看到。
甚至在某些情况下不得不磨去连接器盒体上的塑胶以确定这条基准线的位置。
这里的确出现了一个与之相关的论题-可检测性设计。
可检测性设计(Inspectablity)
由於制造厂商对提高生产效率和产品品质并减少生产成本的不断要求,新的机器视觉系统得到越来越广泛的应用。
当各种视觉系统日益普遍时,人们越来越熟悉这类检测系统的特性,并学会了在设计新产品时考虑产品品质的可检测性。
例如,如果希望有一条基准线用以检测"实际位置",则应在连接器设计上考虑到这条基准线的可见性。
连接器的常用注塑材料:
,,,,NYLON66
聚酯树脂(PET、PBT )
聚苯硫醚(PPS)
聚氯乙烯(PVC)
液晶聚合物(LCP)
聚己二酰己二胺之商品名﹐一般通称尼龙六六(Nylon 66)
台湾连接器产业状况
国内连接器市场除鸿海一家独大外,其余所有厂商全年营业额均不及其营业额的一半,由於鸿海在连接器的制造部份已建立完整的专利权架构,因此目前台湾其他厂商在产品的研发上皆必须规避鸿海的专利权,因此主攻利基市场;少量多样的产品线,是国内大多数连接器厂商的现况。
以2000年产值计算,台湾整体连接器产业的产值超过500亿元,但因生产基地大多移往大陆,因此有60%的产品由大陆生产,依台湾连接器协会预估,今年台湾连接器的产值预计较2000年衰退5%,但大陆地区有近%的高成长,因此彼长我消的情况在连接器产业中相当明显。
台商在大陆连接器的布局
连接器的市场,从材料到组装成品,在大陆均已经建立完整的供应体系,国内业者从研发、行销及有效整合管理两地所发挥的优势来创造利基。
若从上游原材料供应部分来看,原材料如青铜、黄铜、钛铜等,电镀材料如镀金、镀银、镀镍等,塑胶材料有LCP、PPS、PCT、PBT、PC等。
目前大陆在材料方面的供应已经日趋成熟,尤其在环保的要求下,电镀部份均全数移往大陆地区,因此目前以台商为主体的连接器产业体系已经相当完整。
目前连接器厂商至大陆设厂多以来料加工厂为主,因此无法经营当地的内销市场,但当地一般消费电子产品的需求亦高,因此部分厂商亦有经营内销市场的计划,然其中大部分的厂商仍以组装为主,虽然当地劳工成本极低,经营成本亦不高,造成台商竞争力成长缓慢,并遭遇大陆当地业者急起直追的状况;因此长期而言,以大陆为制造
中心,并加强内部管理及并加重台湾地区的研发及接单能力的厂商,较能维持长期的竞争优势。
连接器制造流程
在制造的流程上,车床加工、冲模制作、冲压加工、塑模制作、射出成形、压铸模具制作、压铸射出成形及电镀加工,业者为掌握商机通常会自组或以可靠的方式成立模具厂,再做後段的装配组立、测试及做成电子连接器成品,供应相关产业。
目前下游组装业者纷纷采向上垂直整合,因此许多中小型的业者势必遭遇相当之竞争压力,因此多数连接器厂商采公开市场筹资的方式,扩大竞争规模,或以策略联盟合作模式,增加整体竞争力;不过在业者皆扩大规模的同时,亦容易产生过度竞争及供过於求的情况,因此如何将竞争规模及利基,有效导入非专以PC连接器之产品,是未来增加产品附加价值及成长的关键。