模具表面处理种类及规格
模具表面处理种类与规格

抛光(Polish) 火花纹(Thin Fire Texture) 化学蚀纹(Texture)
蚀纹处理和模具斜度
电镀(Plating) 喷砂(Blasting)
抛光(Polish)
பைடு நூலகம்
SPI - Society of the Plastics Industry 塑料工业协会
Diamond Mold Polishing & Finishing Specifications
0.0508
0.0762 0.1143 0.0762 0.0762 0.0508 0.0889 0.1524 0.0635 0.0508 0.0635
MT-11140
MT-11150 MT-11160
0.0635
0.0698 0.1016
蚀纹处理和模具斜度的关系
Mold-Tech A Mold-Tech B
Ptn.# MT-11200 MT-11205 MT-11210 MT-11215 MT-11220 MT-11225 MT-11230 MT-11235 MT-11240 MT-11245 MT-11250 MT-11255 MT-11260 MT-11265 MT-11270 MT-11275 MT-11280
Plaque #7 Ptn.# Depth(mm) MT325 0.003 MT964 0.003 MT1038 0.002 MT1043 0.002 MT1170 0.0025 MT1192 0.0015 MT1239 0.003 MT1240 0.003 MT1241 0.002 MT1242 0.002 MT1243 0.002 MT1244 0.0025 MT1250 0.003 MT2019 0.0025 MT2020 0.002 MT2028 0.0025 23053 0.002 23064 0.0015
模具表面处理
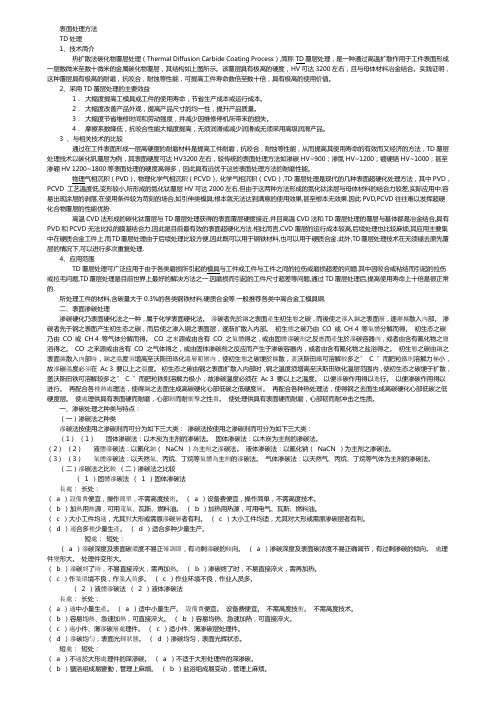
表面处理方法TD处理1、技术简介热扩散法碳化物覆层处理(Thermal Diffusion Carbide Coating Process),简称TD覆层处理,是一种通过高温扩散作用于工件表面形成一层数微米至数十微米的金属碳化物覆层,其结构如上图所示。
该覆层具有极高的硬度,HV可达3200左右,且与母体材料冶金结合。
实践证明,这种覆层具有极高的耐磨,抗咬合,耐蚀等性能,可提高工件寿命数倍至数十倍,具有极高的使用价值。
2、采用TD覆层处理的主要效益1.大幅度提高工模具或工件的使用寿命,节省生产成本或运行成本。
2.大幅度改善产品外观,提高产品尺寸的均一性,提升产品质量。
3.大幅度节省维修时间和劳动强度,并减少因维修停机所带来的损失。
4.摩擦系数降低,抗咬合性能大幅度提高,无须润滑或减少润滑或无须采用高级润滑产品。
3 、与相关技术的比较通过在工件表面形成一层高硬度的耐磨材料是提高工件耐磨,抗咬合,耐蚀等性能,从而提高其使用寿命的有效而又经济的方法,TD覆层处理技术以碳化钒覆层为例,其表面硬度可达HV3200左右,较传统的表面处理方法如渗碳HV~900;渗氮HV~1200;镀硬铬HV~1000;甚至渗硼HV 1200~1800等表面处理的硬度高得多,因此具有远优于这些表面处理方法的耐磨性能。
物理气相沉积(PVD),物理化学气相沉积(PCVD),化学气相沉积(CVD),TD覆层处理是现代的几种表面超硬化处理方法,其中PVD,PCVD 工艺温度低,变形较小,所形成的氮化钛覆层HV可达2000左右,但由于这两种方法形成的氮化钛涂层与母体材料的结合力较差,实际应用中,容易出现涂层的剥落,在使用条件较为苛刻的场合,如引伸类模具;根本就无法达到满意的使用效果,甚至根本无效果.因此PVD,PCVD往往难以发挥超硬化合物覆层的性能优势.高温CVD法形成的碳化钛覆层与TD覆层处理获得的表面覆层硬度接近,并且高温CVD法和TD覆层处理的覆层与基体都是冶金结合,具有PVD 和PCVD无法比拟的膜基结合力,因此是目前最有效的表面超硬化方法.相比而言,CVD覆层的运行成本较高,后续处理也比较麻烦,其应用主要集中在硬质合金工件上.而TD覆层处理由于后续处理比较方便,因此既可以用于钢铁材料,也可以用于硬质合金.此外,TD覆层处理技术在无须褪去原先覆层的情况下,可以进行多次重复处理.4、应用范围TD覆层处理可广泛应用于由于各类磨损所引起的模具与工件或工件与工件之间的拉伤或磨损超差的问题.其中因咬合或粘结而引起的拉伤或拉毛问题,TD覆层处理是目前世界上最好的解决方法之一.因磨损而引起的工件尺寸超差等问题,通过TD覆层处理后,提高使用寿命上十倍是很正常的.所处理工件的材料,含碳量大于0.3%的各类钢铁材料,硬质合金等.一般推荐各类中高合金工模具钢.二、表面渗碳处理渗碳硬化乃表面硬化法之一种,属于化学表面硬化法。
模具表面处理
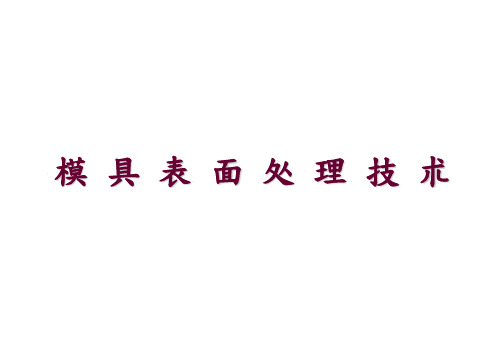
目
录
一﹑模具常規热处理 二﹑模具強韌化处理 三﹑模具化学热处理 四﹑其它表面強化技朮 五﹑真空镀硬质涂层 真空镀硬质涂层
前
言
模具是機械工業重要的基礎工藝裝備. 模具是機械工業重要的基礎工藝裝備. 模具成形具 有效率高﹑質量好﹑節約原材料﹑降低成本等優點. 有效率高﹑質量好﹑節約原材料﹑降低成本等優點. 模具的服役条件是选择模具材料及热处理的依据. 模具的服役条件是选择模具材料及热处理的依据. 影响模具失效的因素包括模具结构﹑模具材料﹑ 影响模具失效的因素包括模具结构﹑模具材料﹑热处理 及加工工艺等. 及加工工艺等. 主要用于金屬或非金屬冷態成形,承受拉伸﹑ 冷作模具主要用于金屬或非金屬冷態成形,承受拉伸﹑彎 壓縮﹑沖擊﹑疲勞等不同應力作用, 曲﹑壓縮﹑沖擊﹑疲勞等不同應力作用,而用于金屬冷 冷镦﹑冷拉伸的模具还要承受300℃ 300℃左右的交變溫 挤﹑冷镦﹑冷拉伸的模具还要承受300℃左右的交變溫 度作用. 度作用. 薄板冲压模主要失效形式是磨损,所以模具用钢要求 薄板冲压模主要失效形式是磨损, 主要失效形式是磨损 Cr4 MoV(120) CrNiSiMnMoV(GD) 具有高的耐磨性.Cr4W2MoV(120)﹑6CrNiSiMnMoV(GD)﹑
淬火后必须回火. 淬火后必须回火.
回火: 回火:
将淬火钢重新加热到A1点以下的预热温度, 将淬火钢重新加热到A1点以下的预热温度,保温预 A1点以下的预热温度 定时间,然后冷却下来.以消除含碳过饱和之马氏体、 定时间,然后冷却下来.以消除含碳过饱和之马氏体、 过冷残余奥氏体以及高密度位错、 过冷残余奥氏体以及高密度位错、大量相界面等晶体 缺陷、淬火应力等不稳定因素. 缺陷、淬火应力等不稳定因素. •低温回火: (150~200℃),得到回火马氏体组织,硬而耐 低温回火: (150~200℃),得到回火马氏体组织 得到回火马氏体组织, 低温回火 强度高,耐疲劳.多用于刃具, 冷冲模具等. 磨,强度高,耐疲劳.多用于刃具,量,冷冲模具等. •中温回火: (400~500℃),得到回火屈氏体组织,弹性好, 中温回火: (400~500℃),得到回火屈氏体组织 弹性好, 得到回火屈氏体组织, 中温回火 用于弹簧处理. 用于弹簧处理. •高温回火: (500~650℃),得到回火索氏体组织,强度和 高温回火: (500~650℃),得到回火索氏体组织 得到回火索氏体组织, 高温回火 韧性综合性能高. 用于轴类,连杆,连接件. 韧性综合性能高. 用于轴类,连杆,连接件.高温软化 回火,回火温度低于A1(20~24℃),得到回火珠光体组织, A1(20~24℃),得到回火珠光体组织 回火,回火温度低于A1(20~24℃),得到回火珠光体组织, 工艺性能好. 工艺性能好.
模具表面处理技术PPT课件
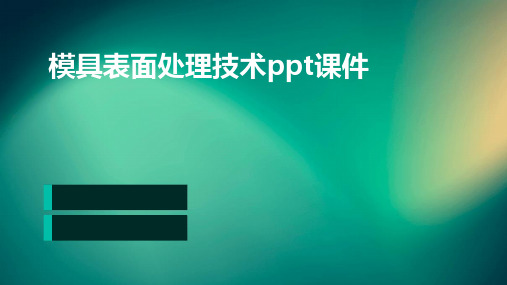
要点二
等离子喷涂技术
通过等离子喷涂将金属或非金属粉末熔融并喷射到模具表 面,形成均匀、致密的涂层,提高表面耐久性和抗腐蚀性 。
智能化和自动化技术的应用
智能监控系统
利用传感器和监测技术实时监测模具表面处理过程,实 现自动化控制和处理。
自动化处理设备
开发自动化表面处理设备,减少人工干预,提高处理效 率和一致性。
耐久性。
提高产品质量和生产效率
提高产品精度和一致性
通过表面处理技术,可以改善模具表 面的粗糙度和形貌,减小产品尺寸和 形状的误差,提高产品的精度和一致 性,从而提高生产效率。
降低生产成本
通过表面处理技术,可以提高模具的 耐磨性和耐久性,减少维修和更换模 具的频率和成本,降低生产成本。
降低生产成本
04 模具表面处理技术的优势 与挑战
提高模具使用寿命
增强模具表面硬度和耐磨 性
通过表面处理技术,可以在模具表面形成一 层高硬度的硬化层,从而提高模具的耐磨性 和抗疲劳性能,延长模具的使用寿命。
降低摩擦系数
通过表面处理技术,可以在模具表面形成一 层低摩擦系数的涂层,减小模具与材料之间 的摩擦力,降低磨损和摩擦热,提高模具的
优化生产流程
通过表面处理技术,可以优化模具的 设计和制造流程,减少加工时间和成 本,提高生产效率。
降低能耗和资源消耗
一些表面处理技术可以降低模具的能 耗和资源消耗,例如离子注入和激光 熔覆等,从而降低生产成本。
技术更新换代快
技术发展迅速
随着科学技术的不断发展,模具 表面处理技术也在不断更新换代 ,新的技术和工艺不断涌现。
常用的五金模具表面处理技术包括喷涂、电镀和化学热处理等。这些技术可以提 高模具表面的硬度和耐久性,降低生产成本和提高产品质量。
模具的表面处理情况
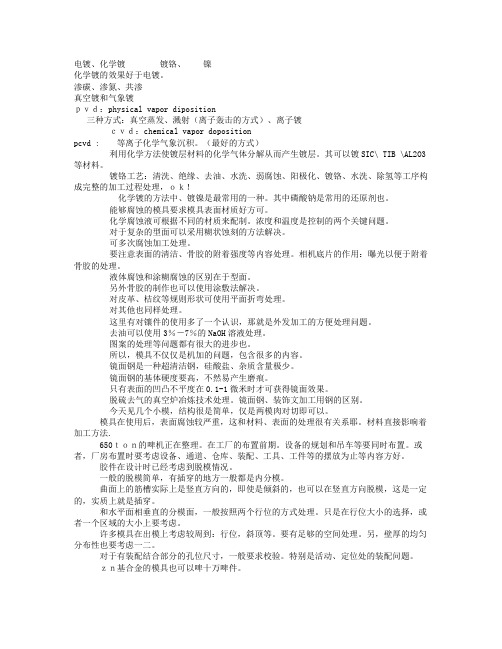
电镀、化学镀镀铬、镍化学镀的效果好于电镀。
渗碳、渗氮、共渗真空镀和气象镀pvd:physical vapor diposition三种方式:真空蒸发、溅射(离子轰击的方式)、离子镀cvd:chemical vapor dopositionpcvd : 等离子化学气象沉积。
(最好的方式)利用化学方法使镀层材料的化学气体分解从而产生镀层。
其可以镀SIC\ TIB \AL2O3等材料。
镀铬工艺:清洗、绝缘、去油、水洗、弱腐蚀、阳极化、镀铬、水洗、除氢等工序构成完整的加工过程处理,ok!化学镀的方法中、镀镍是最常用的一种。
其中磷酸钠是常用的还原剂也。
能够腐蚀的模具要求模具表面材质好方可。
化学腐蚀液可根据不同的材质来配制。
浓度和温度是控制的两个关键问题。
对于复杂的型面可以采用糊状蚀刻的方法解决。
可多次腐蚀加工处理。
要注意表面的清洁、骨胶的附着强度等内容处理。
相机底片的作用:曝光以便于附着骨胶的处理。
液体腐蚀和涂糊腐蚀的区别在于型面。
另外骨胶的制作也可以使用涂敷法解决。
对皮革、桔纹等规则形状可使用平面折弯处理。
对其他也同样处理。
这里有对镶件的使用多了一个认识,那就是外发加工的方便处理问题。
去油可以使用3%-7%的NaOH溶液处理。
图案的处理等问题都有很大的进步也。
所以,模具不仅仅是机加的问题,包含很多的内容。
镜面钢是一种超清洁钢,硅酸盐、杂质含量极少。
镜面钢的基体硬度要高,不然易产生磨痕。
只有表面的凹凸不平度在0.1-1微米时才可获得镜面效果。
脱硫去气的真空炉冶炼技术处理。
镜面钢、装饰文加工用钢的区别。
今天见几个小模,结构很是简单,仅是两模肉对切即可以。
模具在使用后,表面腐蚀较严重,这和材料、表面的处理很有关系耶。
材料直接影响着加工方法.650ton的啤机正在整理。
在工厂的布置前期。
设备的规划和吊车等要同时布置。
或者,厂房布置时要考虑设备、通道、仓库、装配、工具、工件等的摆放为止等内容方好。
胶件在设计时已经考虑到脱模情况。
第5章 模具钢料的热处理-模具表面处理技术

第二节模具表面处理工艺概述模具是现代工业之母。
随着社会经济的发展,特别是汽车、家电工业、航空航天、食品医疗等产业的迅猛发展,对模具工业提出了更高的要求。
如何提高模具的质量、使用寿命和降低生产成本,成为各模具厂及注塑厂当前迫切需要解决的问题。
模具在工作中除了要求基体具有足够高的强度和韧性的合理配合外,其表面性能对模具的工作性能和使用寿命至关重要。
这些表面性能指:耐磨损性能、耐腐蚀性能、摩擦系数、疲劳性能等。
这些性能的改善,单纯依赖基体材料的改进和提高是非常有限的,也是不经济的,而通过表面处理技术,往往可以收到事半功倍的效果;模具的表面处理技术,是通过表面涂覆、表面改性或复合处理技术,改变模具表面的形态、化学成分、组织结构和应力状态,以获得所需表面性能的系统工程。
从表面处理的方式上,又可分为:化学方法、物理方法、物理化学方法和机械方法。
在模具制造中应用较多的主要是渗氮、渗碳和硬化膜沉积。
◆提高模具的表面的硬度、耐磨性、摩擦性、脱模性、隔热性、耐腐蚀性;◆提高表面的高温抗氧化性;◆提高型腔表面抗擦伤能力、脱模能力、抗咬合等特殊性能;减少冷却液的使用;◆提高模具质量,数倍、几十倍地提高模具使用寿命。
减少停机时间;◆大幅度降低生产成本与采购成本,提高生产效率和充分发挥模具材料的潜能。
◆减少润滑剂的使用;◆涂层磨损后,还退掉涂层后,再抛光模具表面,可重新涂层。
在模具上使用的表面技术方法多达几十种,从表面处理的方式上,主要可以归纳为物理表面处理法、化学表面处理法和表面覆层处理法。
模具表面强化处理工艺主要有气体氮化法、离子氮化法、点火花表面强化法、渗硼、TD法、CVD化学气相淀积、PVD物理气相沉积、PACVD离子加强化学气相沉积、CVA铝化化学气相沉积、激光表面强化法、离子注入法、等离子喷涂法等等。
下面综述模具表面处理中常用的表面处理技术:一、物理表面处理法:表面淬火是表面热处理中最常用方法,是强化材料表面的重要手段,分高频加热表面淬火、火焰加热表面淬火、激光表面淬火。
模具表面处理工艺
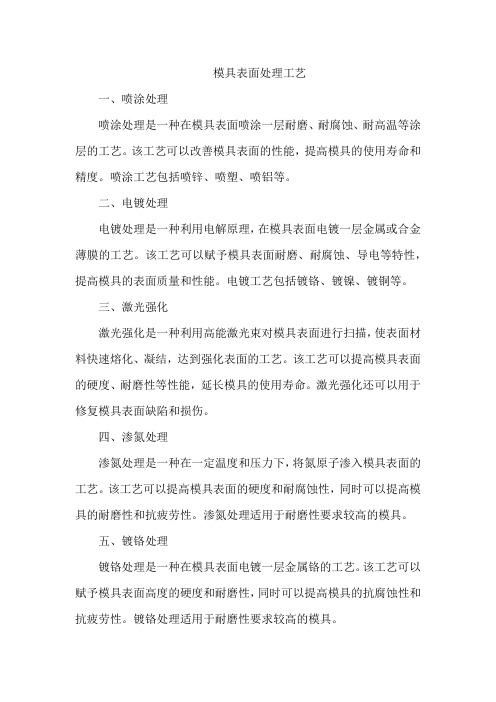
模具表面处理工艺一、喷涂处理喷涂处理是一种在模具表面喷涂一层耐磨、耐腐蚀、耐高温等涂层的工艺。
该工艺可以改善模具表面的性能,提高模具的使用寿命和精度。
喷涂工艺包括喷锌、喷塑、喷铝等。
二、电镀处理电镀处理是一种利用电解原理,在模具表面电镀一层金属或合金薄膜的工艺。
该工艺可以赋予模具表面耐磨、耐腐蚀、导电等特性,提高模具的表面质量和性能。
电镀工艺包括镀铬、镀镍、镀铜等。
三、激光强化激光强化是一种利用高能激光束对模具表面进行扫描,使表面材料快速熔化、凝结,达到强化表面的工艺。
该工艺可以提高模具表面的硬度、耐磨性等性能,延长模具的使用寿命。
激光强化还可以用于修复模具表面缺陷和损伤。
四、渗氮处理渗氮处理是一种在一定温度和压力下,将氮原子渗入模具表面的工艺。
该工艺可以提高模具表面的硬度和耐腐蚀性,同时可以提高模具的耐磨性和抗疲劳性。
渗氮处理适用于耐磨性要求较高的模具。
五、镀铬处理镀铬处理是一种在模具表面电镀一层金属铬的工艺。
该工艺可以赋予模具表面高度的硬度和耐磨性,同时可以提高模具的抗腐蚀性和抗疲劳性。
镀铬处理适用于耐磨性要求较高的模具。
六、喷丸处理喷丸处理是一种利用高速气流将弹丸喷射到模具表面,使表面材料发生塑性变形的工艺。
该工艺可以改善模具表面的粗糙度和形状精度,同时可以提高模具的抗疲劳性和耐磨性。
喷丸处理适用于各种类型的模具。
七、氧化处理氧化处理是一种将金属表面氧化成氧化膜的工艺。
该工艺可以提高模具表面的硬度和耐磨性,同时可以增强模具的抗腐蚀性和抗氧化性。
氧化处理适用于钢铁、铝合金等金属材质的模具。
八、抛光处理抛光处理是一种利用抛光机械对模具表面进行抛光加工的工艺。
该工艺可以改善模具表面的粗糙度和形状精度,同时可以提高模具的抗腐蚀性和抗疲劳性。
抛光处理适用于各种类型的模具。
九、渗碳处理渗碳处理是一种在高温下将碳原子渗入模具表面的工艺。
该工艺可以提高模具表面的硬度和耐磨性,同时可以增强模具的抗疲劳性和韧性。
模具表面处理技术

(2)氮碳共渗
第二节模具表面的化学热处理技术
四、渗硼
渗硼是将钢的表面渗入硼元素以获得铁的硼化物 的热处理工艺方法。
通过渗硼能显著提高钢件表面硬度(l400— 2000HV)和耐磨性,以及具有良好的红硬性及耐蚀性。 钢的表面渗入硼后,由于硼在α -Fe中的溶解 度很小,因此会形成硼化物Fe2B (硬度为l400— 1600HV) ,或FeB (硬度为l800—2000HV) 。Fe2B脆 性较小,一般呈梳齿状楔入基体;FeB脆性较大,易 剥落。
另一种是无氰液体渗碳,主要盐浴成分是氯化钠、 氯化钾和碳酸钠,加上经过加工制作的渗碳剂:碳粉、 碳化硅和尿素。
第二节模具表面的化学热处理技术
4、离子渗碳
采用甲烷或其它渗碳 气体和氢气的混合气作为 辉光放电的气体介质,在 渗碳温度(例如930℃) 下,利用辉光放电对工件 表面进行离子渗碳。 离子渗碳比气体渗碳 方法快得多。离子渗碳后, 应进行直接淬火,故在炉 内应有直接冷却装置。
第二节模具表面的化学热处理技术
5、真空渗碳
真空渗碳炉是将工件放 置在真空炉内通过不断的向 炉内充入渗碳气氛,使碳原 子渗入工件表面。 与气体渗碳相比真空渗 碳温度高(约1100℃), 渗碳速度快,质量好。
第二节模具表面的化学热处理技术
- 1、下载文档前请自行甄别文档内容的完整性,平台不提供额外的编辑、内容补充、找答案等附加服务。
- 2、"仅部分预览"的文档,不可在线预览部分如存在完整性等问题,可反馈申请退款(可完整预览的文档不适用该条件!)。
- 3、如文档侵犯您的权益,请联系客服反馈,我们会尽快为您处理(人工客服工作时间:9:00-18:30)。
30
0.01280
10
0.00128
31
0.01400
11
0.00140
32
0.01600
12
0.00160
33
0.01800
13
0.00180
34
0.02000
14
0.00200
35
0.02240
15
0.00224
36
0.02520
16
0.00252
37
0.02800
17
0.00280
38
0.03200
MT-11090
0.0889
MT-11100
0.1524
MT-11110
0.0635
MT-11120
0.0508
MT-11130
0.0635
MT-11140
0.0635
MT-11150
0.0698
MT-11160
0.1016
精品课件
Ptn.# MT-11000 MT-11010 MT-11020 MT-11030 MT-11040 MT-11050 MT-11060 MT-11070 MT-11080 MT-11090 MT-11100 MT-11110 MT-11120 MT-11130 MT-11140 MT-11150 MT-11160
600 Grit (600砂纸,光面)
400 Grit (400砂纸,光面)
320 Grit (320砂纸,光面)
600 Stone (600油石,光面)
400 Stone (400砂纸,光面)
320 Stone (320砂纸,哑面)
#11 Glass Bead (#11粗玻璃砂) #240 Aluminum Oxide Blast (#240氧化铝) #24 Aluminum Oxide Blast (#24氧化铝)
Description and Previous Finish Numbers
A0
A1
is comparable to
A2
is slightly finer than
A3
has more imperfections than
B1
is finer than
B2
is slightly finer than
Paper Stone Dry Blasted
Current SPI Finish Numbers
#1 Diamond Buff (#1钻石膏,光学要求)
#3 Diamond Buff (#3钻石膏,镜面)
#6 Diamond Buff (#6钻石膏,镜面)
#15 Diamond Buff (#15钻石膏,镜面)
ห้องสมุดไป่ตู้
蚀纹处理和模具斜度的关系
Mold-Tech A
Depth(mm) 0.0004 0.001 0.0015 0.002 0.003 0.0045 0.003 0.003 0.002 0.0035 0.006 0.0025 0.002 0.0025 0.0025 0.00275 0.004
Angle 1°
1.5° 2.5°
3° 4.5° 6.5° 4.5° 4.5°
3° 5.5°
9° 4° 3° 4° 4° 4° 6°
Ptn.# MT-11200 MT-11205 MT-11210 MT-11215 MT-11220 MT-11225 MT-11230 MT-11235 MT-11240 MT-11245 MT-11250 MT-11255 MT-11260 MT-11265 MT-11270 MT-11275 MT-11280
模具表面处理种类及规格
精品课件
精品课件
抛光(Polish)
精品课件
SPI - Society of the Plastics Industry 塑料工业协会
精品课件
Diamond Mold Polishing & Finishing Specifications
Types of Finishes Diamond
MT Specification
单位:mm
号码
咬花深度
MT-11000
0.0102
MT-11010
0.0254
MT-11020
0.0381
MT-11030
0.0508
MT-11040
0.0762
MT-11050
0.1143
MT-11060
0.0762
MT-11070
0.0762
MT-11080
0.0508
粗糙度 Ra 0.40 Ra 0.50 Ra 0.80 Ra 1.12 Ra 1.60 Ra 2.24 Ra 3.15 Ra 4.50 Ra 6.30 Ra 9.00 Ra 12.5 Ra 18.0
Ra -在取样长度内,轮廓偏距绝对值的算术平均值,单位: μ 。
精品课件
化学蚀纹(Texture)
精品课件
#1
0-1
1-2 #2
2-3
2-3
#3
4-5
9-10
10-12
#4
25-28
38-42
10-12
#5
26-32
190-230
精品课件
火花纹(Thin Fire Texture)
精品课件
CHARMILL VDI Specification
号码
电火花深度(mm)
号码
电火花深度(mm)
0
0.00040
B3
is comparable to
C1
is finer than
C2
is slightly finer than
C3
is comparable to
D1
is finer than
D2
is comparable to
D3
is a little more coarse than
精品课件
Roughness Comparison R.A.
粗糙度 Ra 0.2 Ra 0.315 Ra 0.5 Ra 0.8 Ra 1.25 Ra 2.00 Ra 3.15 Ra 5.0 Ra 8.0 Ra 12.5
Fine Fine Medel Grov
符号 VDI12 VDI15 VDI18 VDI21 VDI24 VDI27 VDI30 VDI33 VDI36 VDI39 VDI42 VDI45
21
0.00448
1
0.00044
22
0.00504
2
0.00048
23
0.00560
3
0.00056
24
0.00648
4
0.00064
25
0.00720
5
0.00072
26
0.00800
6
0.00080
27
0.00880
7
0.00088
28
0.01000
8
0.00100
29
0.01120
9
0.00112
18
0.00320
39
0.03600
19
0.00360
40
0.04000
20
0.00400
41
0.04480
精品课件
火花纹规格和图纸表面粗糙度要求对照表
符号 AGIE 1 AGIE 2 AGIE 3 AGIE 4 AGIE 5 AGIE 6 AGIE 7 AGIE 8 AGIE 9 AGIE 10