氨回收装置--精馏塔的设计与研究
氨吸收塔的设计

8-09单吸机号26.5传动类型:A 转速:1450 r/min
学生签名:
2014年8月1日
指导教师意见:
指导教师签名:
年月日
江苏联合职业技术学院
江苏省惠山中等专业学校(办学点)
毕业设计(论文)任务书
设计课题填 料 吸 收 塔 的 设 计
系 部电 信 工 程 系
专 业精细化学品生产技术
年 级班 级
姓 名
学 号
指导教师职 称
2014年4月23日
毕业设计(论文)任务书
(2)混合气的温度:30℃
(3)进塔混合气中氨的体积分数:0.02%;
(4)进塔吸收剂(清水)温度:20℃;
(5)操作压力:常压。
(6)操作温度:20℃。
(7)工作日:每年300天,每天24小时连续运转。
(8)厂址:江苏
第二章 设计方案的确定和流程说明
2.1
2.1.1
吸收过程是依靠气体溶质在吸收剂中的溶解来实现的,因此吸收剂性能的优劣,是决定吸收操作效果的关键之一,选择吸收剂时应着重考虑以下几个方面: 溶解度:吸收剂对溶质组分的溶解度要大。以提高吸收速率并减少吸收剂的需用量。
因为设计要求用水做吸收剂,故采用纯溶剂。
2.1.2设计方案的流程说明
该填料塔中,氨气和空气混合后,经由填料塔的下侧进入填料塔中,与从填料塔顶流下
的清水逆流接触,在填料的作用下进行吸收。经吸收后的混合气 体由塔顶排除,吸收了氨气的水 由填料塔的下端流出。(如下图所示)
第三章 吸收塔的物料衡算
3.1基础物性数据
2.1.1吸收剂的选择6
第六章对本设计的评价18
第一章 设计任务和条件
新型高效等压氨回收塔的设计及使用
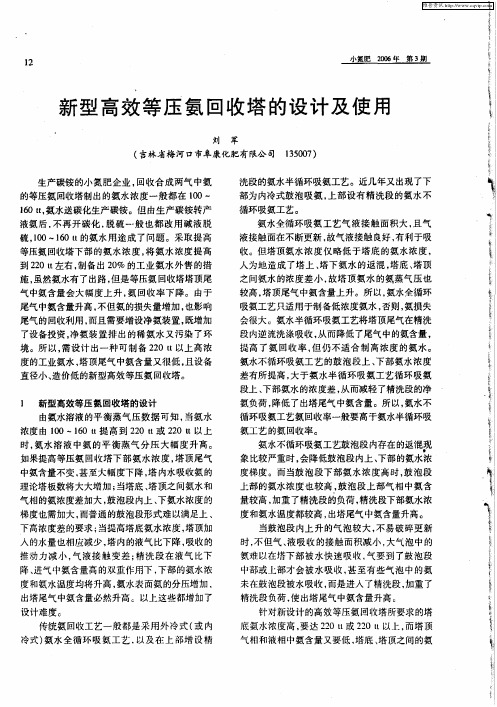
型高效等压氨 回收塔 , 用于制备 20t左右的浓 2 t
氨水外售 , 出塔尾气中氨含量最低可达 0 0 5 , .2% 出塔氨水最高浓 度为 32t 氨 回收率高达 9 % 6 , t 9
以 E。
2 新型高效等压氨回收塔的特点 该等压氨回收塔有以下特点: ()采用了雾化瞬时高效吸氨技术, 1 使大部分
循环 吸 氨工艺 。
硫, 0 6 的氨水用途成 了问题 。采取 提高 1 —1 t 0 0t
等压氨回收塔下部 的氨水浓度, 将氨水浓度提高 到 20t左右, 2 t 制备出 2 % 的工业氨水外售 的措 0 施, 虽然氨水有了出路 , 但是等压氨 回收塔塔顶尾 气中氨含量会大幅度上升 , 氨回收率 下降。由于 尾气中氨含量升高 , 不但氨的损失量增加 , 也影响 尾气的回收利用 , 而且需要增设净氨装置 , 既增加 了设备投资 , 净氨装置排出的稀 氨水又污染了环 境 。所以 , 需设计 出一种可制备 20t以 压 氨 回收 塔 的设 计 及 使 用
刘 军
( 吉林省梅 河口市阜康化肥有限公 司 150 ) 307 生产碳铵的小氮肥 企业 , 回收合 成两气 中氨 的等压氨回收塔制出的氨水浓度一般都在 10~ 0 10t氨水送碳化生产碳铵。但 由生产碳铵转产 6 , t 液氨后 。 不再开碳化 . 脱硫 一般也都改用碱液脱 洗段的氨水半循环吸氨工艺 。近几 年又出现 了下 部为 内冷式鼓泡吸氨 , 上部设有精洗段 的氨水不
氨水全循环吸氨工艺气液接触面积大 , 且气 液接触面在不断更新 , 故气液接触 良好 , 有利于吸 收。但塔顶氨水浓度仅略低于塔底 的氨水浓度, 人为地造成 了塔上 、 塔下氨水的返} 塔底 、 昆, 塔顶
氨回收分离工艺简介
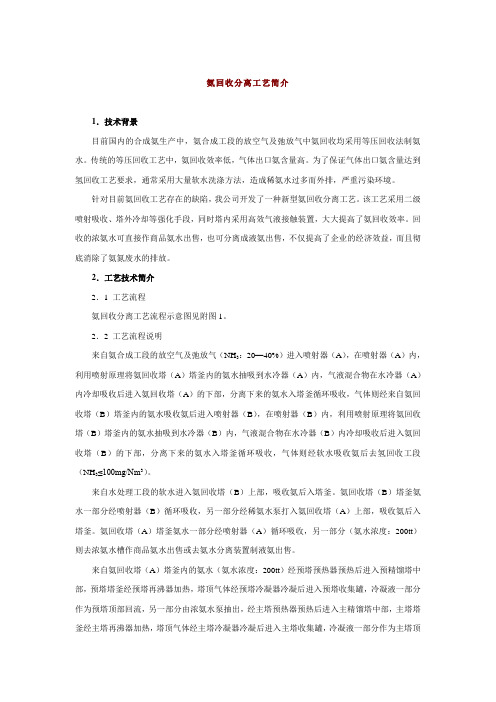
氨回收分离工艺简介1.技术背景目前国内的合成氨生产中,氨合成工段的放空气及弛放气中氨回收均采用等压回收法制氨水。
传统的等压回收工艺中,氨回收效率低,气体出口氨含量高。
为了保证气体出口氨含量达到氢回收工艺要求,通常采用大量软水洗涤方法,造成稀氨水过多而外排,严重污染环境。
针对目前氨回收工艺存在的缺陷,我公司开发了一种新型氨回收分离工艺。
该工艺采用二级喷射吸收、塔外冷却等强化手段,同时塔内采用高效气液接触装置,大大提高了氨回收效率。
回收的浓氨水可直接作商品氨水出售,也可分离成液氨出售,不仅提高了企业的经济效益,而且彻底消除了氨氮废水的排放。
2.工艺技术简介2.1 工艺流程氨回收分离工艺流程示意图见附图1。
2.2 工艺流程说明来自氨合成工段的放空气及弛放气(NH3:20—40%)进入喷射器(A),在喷射器(A)内,利用喷射原理将氨回收塔(A)塔釜内的氨水抽吸到水冷器(A)内,气液混合物在水冷器(A)内冷却吸收后进入氨回收塔(A)的下部,分离下来的氨水入塔釜循环吸收,气体则经来自氨回收塔(B)塔釜内的氨水吸收氨后进入喷射器(B),在喷射器(B)内,利用喷射原理将氨回收塔(B)塔釜内的氨水抽吸到水冷器(B)内,气液混合物在水冷器(B)内冷却吸收后进入氨回收塔(B)的下部,分离下来的氨水入塔釜循环吸收,气体则经软水吸收氨后去氢回收工段(NH3≤100mg/Nm3)。
来自水处理工段的软水进入氨回收塔(B)上部,吸收氨后入塔釜。
氨回收塔(B)塔釜氨水一部分经喷射器(B)循环吸收,另一部分经稀氨水泵打入氨回收塔(A)上部,吸收氨后入塔釜。
氨回收塔(A)塔釜氨水一部分经喷射器(A)循环吸收,另一部分(氨水浓度:200tt)则去浓氨水槽作商品氨水出售或去氨水分离装置制液氨出售。
来自氨回收塔(A)塔釜内的氨水(氨水浓度:200tt)经预塔预热器预热后进入预精馏塔中部,预塔塔釜经预塔再沸器加热,塔顶气体经预塔冷凝器冷凝后进入预塔收集罐,冷凝液一部分作为预塔顶部回流,另一部分由浓氨水泵抽出,经主塔预热器预热后进入主精馏塔中部,主塔塔釜经主塔再沸器加热,塔顶气体经主塔冷凝器冷凝后进入主塔收集罐,冷凝液一部分作为主塔顶部回流,另一部分则去液氨贮槽作商品液氨出售。
氨回收装置--精馏塔的设计与研究
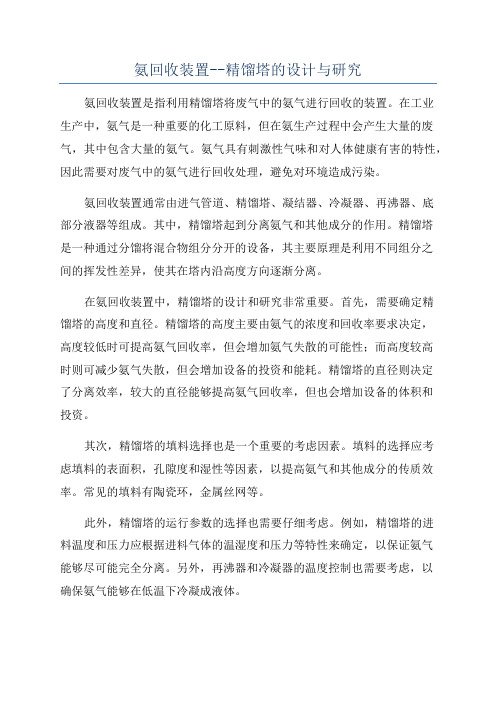
氨回收装置--精馏塔的设计与研究氨回收装置是指利用精馏塔将废气中的氨气进行回收的装置。
在工业生产中,氨气是一种重要的化工原料,但在氨生产过程中会产生大量的废气,其中包含大量的氨气。
氨气具有刺激性气味和对人体健康有害的特性,因此需要对废气中的氨气进行回收处理,避免对环境造成污染。
氨回收装置通常由进气管道、精馏塔、凝结器、冷凝器、再沸器、底部分液器等组成。
其中,精馏塔起到分离氨气和其他成分的作用。
精馏塔是一种通过分馏将混合物组分分开的设备,其主要原理是利用不同组分之间的挥发性差异,使其在塔内沿高度方向逐渐分离。
在氨回收装置中,精馏塔的设计和研究非常重要。
首先,需要确定精馏塔的高度和直径。
精馏塔的高度主要由氨气的浓度和回收率要求决定,高度较低时可提高氨气回收率,但会增加氨气失散的可能性;而高度较高时则可减少氨气失散,但会增加设备的投资和能耗。
精馏塔的直径则决定了分离效率,较大的直径能够提高氨气回收率,但也会增加设备的体积和投资。
其次,精馏塔的填料选择也是一个重要的考虑因素。
填料的选择应考虑填料的表面积,孔隙度和湿性等因素,以提高氨气和其他成分的传质效率。
常见的填料有陶瓷环,金属丝网等。
此外,精馏塔的运行参数的选择也需要仔细考虑。
例如,精馏塔的进料温度和压力应根据进料气体的温湿度和压力等特性来确定,以保证氨气能够尽可能完全分离。
另外,再沸器和冷凝器的温度控制也需要考虑,以确保氨气能够在低温下冷凝成液体。
总的来说,氨回收装置中精馏塔的设计和研究是非常重要的。
通过合理选择精馏塔的高度、直径和填料,以及科学确定运行参数,可以提高氨气的回收率,实现对废气的有效处理。
这对保护环境、减少对氨的资源消耗具有重大意义。
第八章----氨的蒸馏与回收
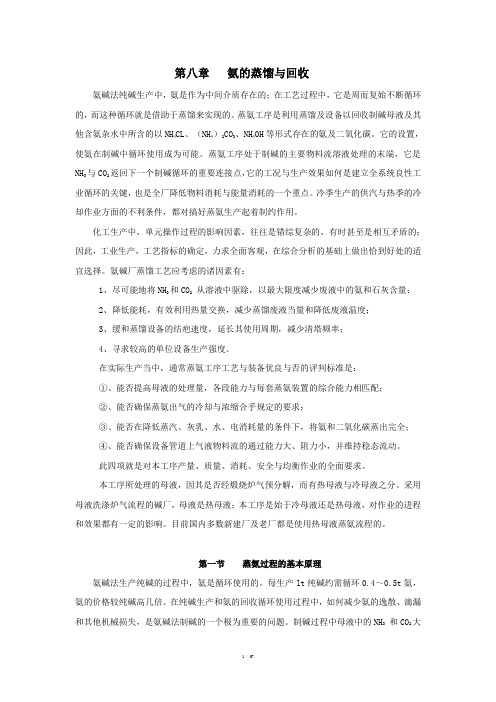
第八章氨的蒸馏与回收氨碱法纯碱生产中,氨是作为中间介质存在的;在工艺过程中,它是周而复始不断循环的,而这种循环就是借助于蒸馏来实现的。
蒸氨工序是利用蒸馏及设备以回收制碱母液及其他含氨杂水中所含的以NH4CL、(NH4)2CO3、NH4OH等形式存在的氨及二氧化碳。
它的设置,使氨在制碱中循环使用成为可能。
蒸氨工序处于制碱的主要物料流溶液处理的末端,它是NH3与CO2返回下一个制碱循环的重要连接点,它的工况与生产效果如何是建立全系统良性工业循环的关键,也是全厂降低物料消耗与能量消耗的一个重点。
冷季生产的供汽与热季的冷却作业方面的不利条件,都对搞好蒸氨生产起着制约作用。
化工生产中,单元操作过程的影响因素,往往是错综复杂的,有时甚至是相互矛盾的;因此,工业生产,工艺指标的确定,力求全面客观,在综合分析的基础上做出恰到好处的适宜选择。
氨碱厂蒸馏工艺应考虑的诸因素有:1、尽可能地将NH3和CO2从溶液中驱除,以最大限度减少废液中的氨和石灰含量;2、降低能耗,有效利用热量交换,减少蒸馏废液当量和降低废液温度;3、缓和蒸馏设备的结疤速度,延长其使用周期,减少清塔频率;4、寻求较高的单位设备生产强度。
在实际生产当中,通常蒸氨工序工艺与装备优良与否的评判标准是:①、能否提高母液的处理量,各段能力与每套蒸氨装置的综合能力相匹配;②、能否确保蒸氨出气的冷却与浓缩合乎规定的要求;③、能否在降低蒸汽、灰乳、水、电消耗量的条件下,将氨和二氧化碳蒸出完全;④、能否确保设备管道上气液物料流的通过能力大、阻力小,并维持稳态流动。
此四项就是对本工序产量、质量、消耗、安全与均衡作业的全面要求。
本工序所处理的母液,因其是否经煅烧炉气预分解,而有热母液与冷母液之分。
采用母液洗涤炉气流程的碱厂,母液是热母液;本工序是始于冷母液还是热母液,对作业的进程和效果都有一定的影响。
目前国内多数新建厂及老厂都是使用热母液蒸氨流程的。
第一节蒸氨过程的基本原理氨碱法生产纯碱的过程中,氨是循环使用的。
成套精馏塔设计,化工蒸馏塔装置工艺 ,精馏回收塔

精馏塔是进行精馏的一种塔式气液接触装置。
利用混合物中各组分具有不同的挥发度,即在同一温度下各组分的蒸气压不同这一性质,使液相中的轻组分(低沸物)转移到气相中,而气相中的重组分(高沸物)转移到液相中,从而实现分离的目的。
精馏塔也是石油化工生产中应用极为广泛的一种传质传热装置。
一、成套精馏塔设计,化工蒸馏塔装置工艺,精馏回收塔介绍:136干燥16-11-29-88无论是平衡蒸馏还是简单蒸馏,虽然可以起到一定的分离作用,但是并不能将一混合物分离为具有一定量的高纯度产品。
在石油化工生产中常常要求获得纯度很高的产品,通过精馏过程可以获得这种高纯度的产品。
精馏过程所用的设备称为精馏塔,大体上可以分为两大类:①板式塔,气液两相总体上作多次逆流接触,每层板上气液两相一般作交叉流。
②填料塔,气液两相作连续逆流接触。
一般的精馏装置由精馏塔塔身、冷凝器、回流罐,以及再沸器等设备组成。
进料从精馏塔中某段塔板上进入塔内,这块塔板称为进料板。
进料板将精馏塔分为上下两段,进料板以上部分称为精馏段,进料板以下部分称为提馏段。
二、成套精馏塔设计,化工蒸馏塔装置工艺,精馏回收塔分类:塔板的分类板式塔是一种应用极为广泛的气液传质设备,它由一个通常呈圆柱形的壳体及其中按一定间距水平设置的若干塔板所组成。
板式塔正常工作时,液体在重力作用下自上而下通过各层塔板后由塔底排出;气体在压差推动下,经均布在塔板上的开孔由下而上穿过各层塔板后由塔顶排出,在每块塔板上皆储有一定的液体,气体穿过板上液层时,两相接触进行传质。
板式塔种类繁多,通常可分类如下:①按塔板结构分,有泡罩板、筛板、浮阀板、网孔板、舌形板等等。
历史上应用最早的有泡罩塔及筛板塔,20世纪50年代前后,开发了浮阀塔板。
现应用最广的是筛板和浮阀塔板,其他不同型式的塔板也有应用。
一些新型塔板或传统塔板的改进型也在陆续开发和研究中。
②按气液两相的流动方式分,有错流式塔板和逆流式塔板,或称有降液管塔板和无降液管塔板。
氨回收装置精馏塔的设计与研究毕业论文

990t/a氨回收装置精馏塔的设计与研究The Design and Study of 990t/a Ammonia Recover Unit of The Rectifying Column目录摘要IAbstract II引言1第1章合成氨的生产与发展状况21.1 合成氨的概述21.2 合成氨的化学反应21.3 国合成氨的生产现状与发展21.3.1 水煤浆气化工艺路线21.3.2 常压气化路线31.4 国外合成氨的发展31.5 合成氨生产的发展前景3第2章合成氨尾气处理氨回收工艺42.1 产品与原料性能52.1.1氨52.1.2氢气62.1.3 氮气72.2氨回收工艺流程8第3章工艺计算103.1 精馏塔的物料衡算103.2相对挥发度α的计算103.3平衡线,q线,精馏段操作线,提馏段操作线方程的确定113.4 塔的工艺条件与相关物性数据计算123.4.1 物性数据123.4.2 精馏段工艺条件123.5 塔板数的计算133.5.1塔板设计选用数据133.5.2 理论板数的计算133.5.3 实际塔板数的计算143.6浮阀塔板工艺尺寸的确定与计算153.6.1塔高的计算153.6.2 塔径D153.6.3 降液管与溢流堰尺寸183.6.4 浮阀数与排列方式193.7 塔板流动性能的校核203.7.1 液沫夹带量校核203.7.2 塔板阻力h计算21f3.7.3 降液管液泛校核213.7.4 液体在降液管停留时间校核223.7.5 严重液漏校核223.8 塔板负荷性能图223.8.1 过量液沫夹带线223.8.2 液相下限线关系式233.8.3严重漏液关系式233.8.4液相上限线关系式233.8.5 降液管液泛线关系式233.9 热量衡算253.9 1塔顶冷凝器的热量衡算253.9.2塔底再沸器的热量衡算263.10浮阀塔工艺设计计算结果汇总26 结论28致错误!未定义书签。
参考文献30附件132附件233年产990吨氨回收装置精馏塔的设计与研究摘要:氨是基本化工产品之一,用途很广。
煤化工变换冷凝液氨回收装置流程模拟和优化

煤化工变换冷凝液氨回收装置流程模拟和优化摘要:科学技术的发展有利于煤炭、化工企业的发展。
煤燃烧装置的改造室。
原油在冷凝和洗涤过程中产生含有NH3、CO2和少量H2S的转化冷凝物。
目前,大多数公司使用氨蒸馏来处理这种库存。
蒸馏后,酸性气体被排出或送入火炬系统。
蒸煮后,立柱的立方溶液返回气化装置。
由于蒸气含水量高,多为白烟,通过火炬燃烧时对环境有一定危害;高浓度的氨氮,氨氮和氨的发明和气化系统的重用单元之后,石灰石和腐蚀的管道和设备的有关要求,除了引起高压氨氮污水处理灰水单元来说,影响污水处理系统的正常运行。
为解决这些问题,国内炼油厂硫磺成熟蒸馏废水、单纯引进技术压力侧线抽氨蒸馏浓缩处理,转换成氨、二氧化碳气化的硫化氢,就在当多个转换会使冷凝蒸发结晶系统转换和提取氨氨或氨水等,实现了零废水排放和氨回收综合利用的目标。
关键词:煤化工;变换冷凝液氨;回收装置;流程模拟引言煤气化变换工艺冷凝液中的氨氮含量较高,且含有氨、硫化氢、二氧化碳等,容易引起设备、管线腐蚀和结晶,使得工业装置难以长周期稳定运行。
处理煤气化变换工艺冷凝液中的氨氮、分离H2S、CO2,是煤气化行业要解决的一大难题,处理工艺常常会面临结晶、腐蚀、环境等诸多问题。
气化过程产生的高闪气采用循环水冷却,存在大量的热量浪费。
随着能源效率的提高和排放标准的严格,减少废水和废气排放,充分利用高闪气能量,降低工艺冷凝液汽提过程的蒸汽消耗,降低工艺冷凝液中氨氮含量,成为煤化工发展必须解决的问题。
1我国现代煤化工技术近年来,对石油和天然气的外部依赖不断增加,2021年达到72%,2021年达到44%。
由于消耗了1.4亿吨散装化学品,主要是烯烃、乙二醇和二甲苯,自给率仅为50%左右,能源安全形势严峻。
经过近20年的努力,中国现代煤炭技术和一般的国际领先的工业时代,国家的能源集团中石化集团中国煤炭和其他科研单位联合攻关,山西煤矿集团等大型国有企业、大型设施的科学发展示范项目的一组原创技术和知识产权,我们建造了一个大型示范综合体,并成功地在煤炭资源和石油天然气化工产品之间架起了一座桥梁。
- 1、下载文档前请自行甄别文档内容的完整性,平台不提供额外的编辑、内容补充、找答案等附加服务。
- 2、"仅部分预览"的文档,不可在线预览部分如存在完整性等问题,可反馈申请退款(可完整预览的文档不适用该条件!)。
- 3、如文档侵犯您的权益,请联系客服反馈,我们会尽快为您处理(人工客服工作时间:9:00-18:30)。
第 2 章 合成氨尾气处理氨回收工艺..............................................................................................5
2.1 产品及原料性能.................................................................................................................................5 2.1.1 氨......................................................................................................................................................... 5 2.1.2 氢气.....................................................................................................................................................6 2.1.3 氮气.................................................................................................................................................... 7 2.2 氨回收工艺流程................................................................................................................................. 8
ቤተ መጻሕፍቲ ባይዱ
第 3 章 工艺计算.......................................................................................................................................10
3.1 精馏塔的物料衡算.......................................................................................................................... 10 3.2 相对挥发度α的计算........................................................................................................................ 10 3.3 平衡线,q 线,精馏段操作线,提馏段操作线方程的确定............................................. 11 3.4 塔的工艺条件及相关物性数据计算..........................................................................................12 3.4.1 物性数据......................................................................................................................................... 12 3.4.2 精馏段工艺条件........................................................................................................................... 12
1.1 合成氨的概述..................................................................................................................................... 2 1.2 合成氨的化学反应............................................................................................................................ 2 1.3 国内合成氨的生产现状及发展..................................................................................................... 2 1.3.1 水煤浆气化工艺路线.................................................................................................................... 2 1.3.2 常压气化路线..................................................................................................................................3 1.4 国外合成氨的发展............................................................................................................................ 3 1.5 合成氨生产的发展前景...................................................................................................................3
3.4.3 提溜段工艺条件........................................................................................................................... 12 3.5 塔板数的计算................................................................................................................................... 13 3.5.1 塔板设计选用数据.......................................................................................................................13 3.5.2 理论板数的计算........................................................................................................................... 13 3.5.3 实际塔板数的计算.......................................................................................................................14 3.6 浮阀塔板工艺尺寸的确定与计算...............................................................................................15 3.6.1 塔高的计算.....................................................................................................................................15 3.6.2 塔径 D..............................................................................................................................................15 3.6.3 降液管及溢流堰尺寸.................................................................................................................. 17 3.6.4 浮阀数及排列方式.......................................................................................................................18 3.7 塔板流动性能的校核..................................................................................................................... 20 3.7.1 液沫夹带量校核........................................................................................................................... 20 3.7.2 塔板阻力 h f 计算......................................................................................................... 20 3.7.3 降液管液泛校核........................................................................................................................... 21 3.7.4 液体在降液管内停留时间校核................................................................................................22 3.7.5 严重液漏校核................................................................................................................................22 3.8 塔板负荷性能图...............................................................................................................................22 3.8.1 过量液沫夹带线........................................................................................................................... 22 3.8.2 液相下限线关系式.......................................................................................................................22 3.8.3 严重漏液关系式............................................................................................................................23 3.8.4 液相上限线关系式.......................................................................................................................23 3.8.5 降液管液泛线关系式.................................................................................................................. 23 3.9 热量衡算.............................................................................................................................................25 3.9 1 塔顶冷凝器的热量衡算..............................................................................................................25 3.9.2 塔底再沸器的热量衡算..............................................................................................................25 3.10 浮阀塔工艺设计计算结果汇总................................................................................................. 26