脱硫增效剂使用方案
脱硫增效剂说明书

烟气脱硫增效剂(HP-525)湿法烟气脱硫工艺(FGD)是燃煤电厂控制SO2污染的主要技术,由于脱硫、除尘同时兼顾,适用性强,运行可靠,已成为我国燃煤电厂环保的主流配置。
但FGD投运以来,也暴露了一些问题:1、电煤资源紧张,煤种变化大,含硫量偏离设计值,直接影响脱硫率,甚至导致超环保限值排放。
2、因脱硫剂溶解物性差,维持浆液循环需用电量较高,在煤价上升和脱硫电价无法保本的情况下,运行成本居高不下。
3、特别因系统易结垢堵塞,被迫切换旁路,甚至发生增压风机喘振,造成运行可靠性下降。
HP-525 产品特性我公司研发的烟气脱硫增效剂(HP-525)可显著提高烟气石灰石-石膏湿法脱硫效率,实现高硫煤烟气达标排放,并较大幅度降低运行成本,延缓结垢,改善系统运行可靠性,为长周期运行提供技术支持。
该产品主要特点如下:特点运行意义脱硫效率高在不做设备升级的前提下,较大幅度提高脱硫率,并可实现中、高硫煤SO2达标。
经济性能好无须另行投资或增加设备,在各项措施选择中,有明显优势。
节能降耗相同脱硫率下:可以通过调整浆液循环泵投用配置,降低用电量,明显降低运行成本。
环保时效性水溶性好,低挥发,无害,化学稳定性好,无二次污染,不影响硫酸钙品质。
运行可靠,维护简便工艺流程精炼,简洁,无需停机检修,易掌握,易运行,运行和维护人员能快速操作。
产品组成本制剂是由复合多元酸、膦酸基高分子化合物、活性剂、助溶剂等组成的复杂混合物。
复合多元酸:在吸收塔浆液环境中提供缓冲,加快气、液膜之间的传质过程,提高反应速度;膦酸基高分子化合物:含有阻垢的活性基团,干扰晶体成长或形成疏松型多环螯合物;活化剂:降低液膜阻力,改变固、液相界面湿润性,提高界面传质效率;助溶剂:加速石灰石的溶解速度。
外观:白色结晶或粉末PH值(1%水溶液):≤6.0水不溶物含量(%):<0.1总Fe含量(mg/L):≤10产品使用方法1、将石灰配制成一定浓度的石灰石浆液,并加入一定量本制剂,机械搅拌均匀,经石灰石浆液泵打入脱硫反应塔内;或将本制剂加入地坑中,用滤液、循环液或工业水溶解,经地坑泵打入脱硫塔内。
脱硫增效剂的原理及使用 概述 石灰石 增效原理

使用脱硫增效剂,可在较低的液气比下保持所需的脱硫效率,从而减少浆液循环强度,合理调整浆液循环泵的运行,降低脱硫系统能耗,达到节能降耗的目的。
降低脱硫系统投资费用
在脱硫系统设计阶段,如考虑使用脱硫增效剂,在相同的脱硫效率条件下,可减少喷淋层的设置及可缩减吸收塔的高度,减少浆液池的体积和浆液循环泵的数量,最终降低投资费用,节省系统耗电量。
SO2+ H2O≒H++ HSO3-≒2H++ SO32-(1)
SO2溶解于水的反应为慢反应,是整个反应速度控制步骤之一。
在吸收塔浆液池中,HSO3-被通入的空气强制氧化为SO42-:
HSO3-+ 1/2 O2≒SO42-+ H+(2)
在水溶液中,石灰石溶解度是很低的(≈0.015kg/m3):
CaCO3≒Ca2++ CO32+(3)
脱硫增效剂的原理及使用
一、概述
改革开放以来,随着电力工业的快速发展,火电厂燃煤烟气排放造成的SO2污染日益严重,消减和控制火电厂燃煤SO2污染,就成为我国大气污染控制领域最急迫的任务。
石灰石-石膏烟气湿法脱硫技术因其工艺成熟、对煤种的适应性好、脱硫效率高以及系统运行可靠性高而得以广泛的应用。近年来,由于煤炭市场的变化,很多火电厂进厂煤的含硫量已较设计值偏大许多,使脱硫系统超负荷运行,导致脱硫效率下降,严重影响烟气SO2达标排放。此外,脱硫系统运行厂用电率较高,节能降耗也是值得关注的问题。
本公司致力于环保技术的开发及应用,研发了----高效脱硫增效剂,用以改善石灰石浆液与SO2反应的边界条件,强化其脱硫过程,提升脱硫效率,拓展脱硫系统对燃煤含硫变化的适应能力,降低能耗,确保烟气SO2达标排放并大大降低脱硫电价考核和环保处罚的风险。
脱硫增效剂使用方案

脱硫增效剂应用技术方案1、目的使用增效剂后,在同等工况下提高脱硫效率,提高燃煤硫分的适应能力,停泵节能降耗。
2.脱硫系统运行情况分析说明2.1 项目情况脱硫系统主要设计参数为:燃煤设计含硫量2.1%,入口SO2浓度4810 mg/Nm3,出口SO2浓度小于197mg/Nm3。
目前实际平均硫份0.7-1.2%之间,出口SO2浓度要求控制50 mg/Nm3以内。
吸收塔内径15m,浆液溢流高度12.8m,塔底储浆池容积2260m3。
吸收塔浆液pH值5.0-5.5,配置4台浆液循环泵,浆液密度控制在1100kg/m3左右。
2.2 情况分析目前各项排放指标能满足排放要求,系统设计裕量较大,但新的环保排放标准要求SO2浓度从设计时200 mg/Nm3以内降至50 mg/Nm3以内,使得目前脱硫电耗大幅度提高。
使用脱硫增效剂后,不仅可以更好的满足环保要求,同时可以在节能方面挖掘潜力,降低脱硫厂用电。
经过对目前使用增效剂的用户充分了解,使用增效剂后对系统设备的安全没有影响,可以减小设备的腐蚀和结构。
3.使用脱硫增效剂预计达到的结果分析3.1脱硫增效剂可有效提高脱硫效率和系统处理能力,在保持相同效率的前提下可以提高系统燃煤适应范围(以一般经验来看可以在现有系统允许燃煤硫份的基础上提高20%—40%)。
当燃煤硫份提高或存在波动时,也可满足环保要求。
脱硫系统浆液循环泵运行情况:入口SO2浓度2000mg/Nm3左右时,负荷率80%左右,运行三台浆液循环泵;入口SO2浓度3000mg/Nm3时,负荷率80%以上时,运行4台。
目前脱硫装置入口SO2浓度基本稳定,大多数时间维持在2000mg/Nm3左右。
负荷率70%以上时,使用脱硫添加剂后,可减少1台浆液循环泵运行。
按照停运B循环泵,每套装置每年运行小时数为7900h,核算如下(以下数据是2套脱硫装置):节约电费:596×7900×0.299×2=281.56万元添加剂费用:(658×0.06+2×1.2)×45000=188.46万元预计直接节省费用93.1万元。
脱硫增效剂的使用说明及脱硫工艺流程图

一、增效剂的首次加入,加入点可选两种方案:1、增效剂的首次加入点选在吸收塔地坑(吸收塔排水坑或废水收集坑):加入方式:打开搅拌,加水,同时倒入计量的脱硫增效剂,搅拌5分钟,继续加水至高位时,开启地坑泵(提升泵)打入吸收塔;每次加入脱硫增效剂300~500KG,根据总加入量,分2~5次投加。
2、增效剂的首次加入点选在滤液池或滤液水箱(低位2m)加入:加入方式:检查滤液池或滤液水箱上的搅拌处于开启状态;在进入滤液池或滤液水箱的水沟中加入,此时应保证水沟中有较多的滤液正在流入滤液池或滤液水箱;边按一定速度加入增效剂,边搅拌,再通过滤液泵打入吸收塔。
二、基础加药量及首次加药控制:首次使用时,浆液中增效剂的浓度按1000ppm左右控制:吸收塔浆液池体积=3.14×(吸收塔直径φ/2)2×浆液高度=V(m3)根据吸收塔浆液池体积计算增效剂使用量约为:吸收塔浆液池体积×1000PPM/1000=V (公斤)。
将增效剂分2~5次,每次加入量约300~500公斤,两次加药间隔2~4小时,每次加药前应将PH值调整至运行PH的上限后再加入。
三、增效剂的补加1、从滤液水箱加入:检查滤液池或滤液水箱上的搅拌处于开启状态;在进入滤液池或滤液水箱的水沟中加入,此时应保证水沟中有较多的滤液正在流入滤液池或滤液水箱;边按一定速度加入增效剂,边搅拌,再通过滤液泵打入吸收塔。
2、从吸收塔地坑加入:有浆液及其它水流入地坑时,边倒入脱硫增效剂边搅拌,继续加水至高位时,自动或手动开启地坑泵(提升泵)打入吸收塔。
当地坑容积较小、地坑液位上涨较快且脱硫增效剂加量较大时,可在30~120min内分2~4次加入。
3、后续加药规程:第一天投加基础量的脱硫增效剂后,根据机组及负荷的大小,以后每天投加一次,投加量约为80~240公斤,并根据脱硫效率的变化情况进行调整。
四、加药运行中的参数控制:PH值的控制范围(实测值):5。
燃煤电厂脱硫添加剂的使用与节能分析

燃煤电厂脱硫添加剂的使用与节能分析本文从燃煤电厂使用脱硫添加剂对达标排放以及节能的影响结合实际进行分析,总结脱硫添加剂在燃煤电厂的使用方法,以促进节能减排,为社会创造更多的能源价值。
标签:燃煤电厂脱硫添加剂节能1 脱硫添加剂与节能的关系1.1脱硫添加剂在燃煤电厂的使用据数据统计,截止到2013年11月,我国规模以上电厂火力发电量占社会总发电量80.41%,同比增加6.8%。
燃煤电厂SO2排放占全国排放量的近50%,并且有上升的趋势。
政府为了减小大气污染对人居环境的影响,已出台了严厉的脱硫电价考核激励措施。
作为基层燃煤电厂,在履行社会责任,积极创造经济效益的同时有责任运用先进的技术和有效的措施控制SO2排放。
石灰石—石膏湿法烟气脱硫技术成熟、脱硫效率高,被燃煤电厂广泛运用,但由于石灰石本身性质及工艺限制,该方法的脱硫工艺存在着能耗高、吸收塔脱硫能力适应性不强等方面的问题。
为此有必要在脱硫过程中通过增加添加剂提高石灰石浆液与含有SO2原烟气之间的化学反应活性,提高单位时间内的脱硫效率。
因为煤炭市场的不确定性以及环保标准的不断提高,致使脱硫装置在燃煤硫份低于设计值的工况运行时,脱硫系统运行能耗偏高;而在燃煤硫份超出设计值较多的工况运行时,又可能无法满足环保排放要求;另外由于设备磨损导致脱硫装置性能下降,脱硫装置的运行压力日益加大。
脱硫添加剂可以显著改善二氧化硫吸收的传质过程,从而提高脱硫装置对燃煤硫份的适应能力,增加脱硫装置的调节手段,并提高脱硫装置运行经济性。
脱硫添加剂是以复合多元酸为基础,辅以活性剂、助溶剂、反应催化剂、示踪剂辅助成分。
其主要作用是在吸收塔浆液环境中提供缓冲对,在吸收过程中吸收浆液中的氢离子,降低二氧化硫浓度,加快气膜和液膜之间的传质过程,有利于浆液对二氧化硫的吸收。
吸收氢离子后的添加剂在浆池中与石灰石发生反应,回复到原有的状态,如此循环往复。
添加剂参加了脱硫吸收的过程反应,但不因反应而消耗。
脱硫增效剂的原理及使用概述石灰石增效原理
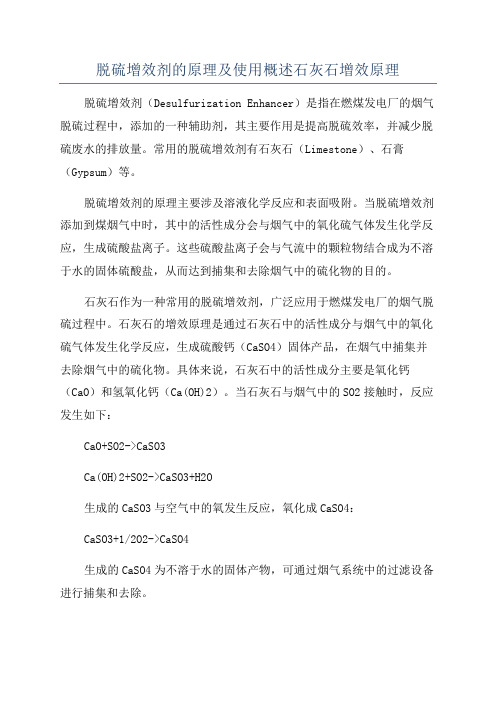
脱硫增效剂的原理及使用概述石灰石增效原理脱硫增效剂(Desulfurization Enhancer)是指在燃煤发电厂的烟气脱硫过程中,添加的一种辅助剂,其主要作用是提高脱硫效率,并减少脱硫废水的排放量。
常用的脱硫增效剂有石灰石(Limestone)、石膏(Gypsum)等。
脱硫增效剂的原理主要涉及溶液化学反应和表面吸附。
当脱硫增效剂添加到煤烟气中时,其中的活性成分会与烟气中的氧化硫气体发生化学反应,生成硫酸盐离子。
这些硫酸盐离子会与气流中的颗粒物结合成为不溶于水的固体硫酸盐,从而达到捕集和去除烟气中的硫化物的目的。
石灰石作为一种常用的脱硫增效剂,广泛应用于燃煤发电厂的烟气脱硫过程中。
石灰石的增效原理是通过石灰石中的活性成分与烟气中的氧化硫气体发生化学反应,生成硫酸钙(CaSO4)固体产品,在烟气中捕集并去除烟气中的硫化物。
具体来说,石灰石中的活性成分主要是氧化钙(CaO)和氢氧化钙(Ca(OH)2)。
当石灰石与烟气中的SO2接触时,反应发生如下:CaO+SO2->CaSO3Ca(OH)2+SO2->CaSO3+H2O生成的CaSO3与空气中的氧发生反应,氧化成CaSO4:CaSO3+1/2O2->CaSO4生成的CaSO4为不溶于水的固体产物,可通过烟气系统中的过滤设备进行捕集和去除。
石灰石作为脱硫增效剂的使用方式主要有湿法喷雾吸收法和循环流化床吸收法。
湿法喷雾吸收法是将石灰石粉末和水混合制成浆料后喷雾到烟气中,烟气中的SO2与石灰石浆料中的活性成分发生反应,并通过脱硫装置进行去除。
循环流化床吸收法是将石灰石颗粒和烟气在流化床中进行接触和反应,通过循环流化床的循环体系将石灰石固定在吸收剂层中,并与烟气中的SO2发生反应并去除。
总而言之,脱硫增效剂主要通过化学反应和物理吸附作用,将烟气中的氧化硫气体捕集、去除,并生成固体硫酸盐产物。
石灰石作为常用的脱硫增效剂之一,通过与烟气中的SO2反应生成CaSO4,从而实现脱硫效果的提高。
巴克曼脱硫增效剂介绍

案例2:石膏湿式脱硫(600MW机组)
某电厂1#机组主要的经济效益 :
• 脱硫系统状况 • 日常采用3台浆液循环泵,运行电流55A,能耗较高 • 没有备用循环泵,当发生设备故障时,无法保证脱硫系统正常运行 • 遇到突发情况被迫提高高硫煤的使用比例时,脱硫率无法达标 试验结论:
• 脱硫效率在添加BLX13735时,可停一台浆液泵而安全运行
3.506 3.638 3.791 3.969 4.211 4.357 4.752 1.869 2.209 2.388 2.565 2.606 9 10 11 12 13 14 15 16 17 18 19
效果案例二:某电厂1#机组600MW
600MW机组湿法脱硫系统 1、脱硫塔浆液容量在 1100~1300 2、浆液循环泵:3台,每台的循环量在6000~7500,一般情况开3台,循 环泵的电流在55~85安培之间
4.催化剂强化石灰石-石膏湿式脱硫 效果案例一:某电厂1#和2#机组600MW*2
燃煤状况: 入炉煤含硫量0.51~2.0%,当燃煤含硫量大于0.63%时,脱硫 效率下降,并随燃煤含硫量增加而降低,脱硫塔出口烟气含硫量能够大于 100 mg/m3,超出环保要求。 其中含硫量低于0.63%的燃煤约占15%,含硫量在0.63~1.3%的燃煤约 占总煤量的80%,含硫量超出1.3%的燃煤不足5%。
7.加药方式及加药量
不需要增加任何硬件设备,可利用吸收塔区域浆池 (也称:地坑),将药倒入坑中,加入部分回收 水,启动搅拌器,使之完全溶解后,启动区域浆池 泵将溶解后的药剂打入浆中。首次加药量较大,一 次打入
投加量一般为500至800mg/l(相对石膏出量),初次 投加800~1000mg/l(相对脱硫塔浆液保有量积量)
脱硫增效剂

烟气湿法脱硫复合增效剂
简介:“烟气湿法脱硫专用复合增效剂”也可以称之为“湿式复合脱硫增效剂”,是专门针对电厂、钢厂、水泥厂等采用石灰石-石膏湿法脱除二氧化硫工艺而开发出来的一款产品。
详情:
一、产品简介
“烟气湿法脱硫专用复合增效剂”也可以称之为“湿式复合脱硫增效剂”,是专门针对电厂、钢厂、水泥厂等采用石灰石-石膏湿法脱除二氧化硫工艺而开发出来的产品。
二、技术指标
名称指标
外观白色或灰棕色粉末
PH(1%) 2.88
三、性能与用途
复合脱硫增效剂通过改变气液接触界面性质,降低传质阻力;氢离子传递,促进石灰石溶解,缓冲pH波动,维持系统稳定,提高脱硫效率;抑制吸收部位亚硫酸盐氧化,防止共混亚硫酸与硫酸钙混合垢形成;通过对硫酸钙结晶体表面的修辞,提高石膏脱水率。
四、使用方法
在吸收塔地坑口处一次或分批加入,可根据电厂实际情况提出具体方案;加药量可根据脱硫系统实际运转情况定,脱硫增效剂应用专工会推荐最佳加药量,一般加药量在200ppm-1500ppm之间;使用湿式复合脱硫增效剂脱硫塔循环浆液PH值控制在5.5~5.8脱硫效果较好,PH值以不超过6.0为宜。
五、包装与贮存
EXN-901采用塑料袋密封包装,每袋净重25Kg,可根据用户需求确定。
常温下,储存于避光阴凉干燥处,远离火种、热源,应与氧化剂、还原剂、碱性物质分开存放。
运输时包装要完整、装载要稳妥,途中要防雨淋、日晒、高温。
储存期为十二个月。
六、安全与防护
本品为粉末状易飞扬,操作时注意劳动保护,人工添加时需佩戴防护面罩,避免粉尘进入呼吸道对人体造成伤害;皮肤、眼睛等接触时用大量清水冲洗即可。
- 1、下载文档前请自行甄别文档内容的完整性,平台不提供额外的编辑、内容补充、找答案等附加服务。
- 2、"仅部分预览"的文档,不可在线预览部分如存在完整性等问题,可反馈申请退款(可完整预览的文档不适用该条件!)。
- 3、如文档侵犯您的权益,请联系客服反馈,我们会尽快为您处理(人工客服工作时间:9:00-18:30)。
脱硫增效剂应用技术方案
1、目的
使用增效剂后,在同等工况下提高脱硫效率,提高燃煤硫分的适应能力,停泵节能降耗。
2.脱硫系统运行情况分析说明
2.1 项目情况
脱硫系统主要设计参数为:燃煤设计含硫量2.1%,入口SO2浓度4810 mg/Nm3,出口SO2浓度小于197mg/Nm3。
目前实际平均硫份0.7-1.2%之间,出口SO2浓度要求控制
50 mg/Nm3以内。
吸收塔内径15m,浆液溢流高度12.8m,塔底储浆池容积2260m3。
吸收塔浆液pH值5.0-5.5,配置
4台浆液循环泵,浆液密度控制在1100kg/m3左右。
2.2 情况分析
目前各项排放指标能满足排放要求,系统设计裕量较大,但新的环保排放标准要求SO2浓度从设计时200 mg/Nm3以内降至50 mg/Nm3以内,使得目前脱硫电耗大幅度提高。
使用脱硫增效剂后,不仅可以更好的满足环保要求,同时可以在节能方面挖掘潜力,降低脱硫厂用电。
经过对目前使用增效剂的用户充分了解,使用增效剂后对系统设备的安全没有影响,可以减小设备的腐蚀和结构。
3.使用脱硫增效剂预计达到的结果分析
3.1脱硫增效剂可有效提高脱硫效率和系统处理能力,在保持相同效率的前提下可以提高系统燃煤适应范围(以一般经验来看可以在现有系统允许燃煤硫份的基础上提高20%—40%)。
当燃煤硫份提高或存在波动时,也可满足环保要求。
脱硫系统浆液循环泵运行情况:入口SO2浓度
2000mg/Nm3左右时,负荷率80%左右,运行三台浆液循环泵;入口SO2浓度3000mg/Nm3时,负荷率80%以上时,运行4台。
目前脱硫装置入口SO2浓度基本稳定,大多数时间维持在2000mg/Nm3左右。
负荷率70%以上时,使用脱硫添加剂后,可减少1台浆液循环泵运行。
按照停运B循环泵,每套装置每年运行小时数为7900h,核算如下(以下数据是2套脱硫装置):节约电费:596×7900×0.299×2=281.56万元
添加剂费用:(658×0.06+2×1.2)×45000=188.46万元
预计直接节省费用93.1万元。
注释:
596:每小时节省的电量,即1.732×6×66×0.87=596 KW/h。
(B循环泵运行电流66A,)
7900:脱硫系统运行时间,单位:h。
0.299:含税电费单价,单位:元/度。
658:两套装置累计运行的天数,单位:天。
0.06:每天需加的添加剂量,单位:吨/天。
45000:脱硫剂单价,单位元/吨。
3.2其他效益
①脱硫增效剂POLYTE®4080A具有减少系统腐蚀结垢的作用,系统在添加脱硫增效剂后,可以减少结垢风险。
在一定程度上能够改善或缓解系统结垢的问题。
②因添加脱硫增效剂后提高了效率,可停用一台浆液循环泵,可以提高设备备用系数。
并减少循环泵系统的检修、维护工作量。
③脱硫增效剂POLYTE®4080A具有提高石灰石活性,加速石灰石溶解的作用,可有效降低浆液及石膏中CaCO3含量,节约石灰石用量。
4.方案
4.1使用前应满足的条件
1)保证石灰石质量合格;石灰石浆液浓度符合脱硫系统设计要求。
2)试验期间电除尘器高/低压设备运行正常,电场全部投入,运行参数调整至最佳状态,达到设计除尘效率;
3)各吸收塔浆液严禁向事故浆液箱排放;同时也严禁事故浆液箱向各吸收塔排放浆液;各吸收塔地坑浆液均需回流至各吸收塔;脱硫公用区域地坑浆液通过滤液箱到各吸收塔(至各炉流
量要均匀);
4)脱硫系统主要设备应稳定运行,如烟风系统、吸收塔系统、石灰石浆液制备系统、石膏脱水系统、废水系统等。
5)FGD主要参数应达到稳定,如吸收塔浆液pH值(5.0—5.5)等;
6)浆液密度控制在15%-18%。
4.2 加药说明
4.2.1 加药前数据采集
1)加药前10-15天的运行数据记录表,最好包括各个负荷段工况;
2)进行燃烧高硫煤试验,确定加药前燃烧高硫煤脱硫系统所能承受的极限工况。
3)进行停泵时(脱硫效率较高时),即先将系统控制在稳定状态,然后停止一台循环泵,记录24内运行数据,若在24小时内系统脱硫效率急剧降低,即恢复启泵。
4.2.2 初次投加
1)使各参数保持稳定(煤种、负荷、pH值等);
2)加药前略微降低吸收塔液位0.5m,预留一定加药容积。
试验过程保持吸收塔液位在一定范围内,如果出现液位不稳定的状态建议投加消泡剂;
3)初次加药过程中建议停止脱水和排石膏,为减少药剂损
失,在今后使用中可适当减少废水排放量,但要保持浆液的氯离子浓度在20000ppm 以内(最好在12000ppm以内);
4)建议吸收塔浆液的pH 值处于5.3-5.5,电除尘的效率在控制范围内;
5)本系统所需药剂浓度为550ppm,经计算所需初次投加量为每台吸收塔1200Kg。
将1200Kg POLYTE®4080A分两次加入脱硫集水坑内,每次分别投加600KG,间隔1-3小时为宜。
加时通过提升泵打入脱硫塔内,收集坑的搅拌器保持开启,确保药剂的溶解和扩散均匀。
6)初次加药后2小时,根据情况可进行停泵试验,即先将系统控制在稳定状态(最好为满负荷情况下),然后停止一台浆液循环泵,记录24内运行数据。
若在24小时内系统脱硫效率急剧降低,即恢复启泵。
4.2.3 二次投加及日常维护投加
根据初次投加反应情况,及现场条件,继续试验。
可考虑停泵或煤质变化(参烧部分高硫煤)试验。
二次的投加时间和加入量根据系统参数结合现场一次投加后运行情况而定,建议投加量为每台吸收塔60-80kg/天(硫份1.0%以下60kg/天,硫份1.0%以上80kg/天)。
具体的投加量由技术工程师确认。
加药时,考虑系统中浆液、滤液水若流失会造成试验药剂流
失,从而使药剂浓度降低,此时所需补充量会有所增加,所以日常巡检人员需要引起注意。
4.2.4注意事项
1)向吸收塔地坑加药时应缓慢加入,确保药品充分搅拌均匀。
每次地坑泵运行时吸收塔最好打至最低液位、确保药液全部进入吸收塔。
加药前2小时应安排运行人员尽量降低吸收塔液位,以便接收吸收塔排水坑中药品的浆液。
2)每小时抄表一次,但是浆液循环泵启停要单独做好记录,以便运行分析。
3)FGD加入增效剂后脱硫效率可能明显上升,易发生吸收塔石膏浆液pH值降低的情况,要求运行人员在增效剂加入前维持运行pH值(5.2—5.5)。
4)注意控制脱硫废水排放量,建议保持相对稳定,如100吨/天。
4.2.5用量
使用药量按每塔初次1.2吨,后续每天补充60kg。
4.3 脱硫系统设备的要求
因为脱硫增效剂加入后,快速提高吸收塔内反应速度,石灰石浆液及石膏生成量增快,要求相应系统设备能力够用,保证较低的吸收塔浆液密度。
系统设备能力不足可能会出现以下情况:
1)供浆系统设备能力不足时,会出现吸收塔内pH值下降,石灰石利用率降低,脱硫效率下降。
2)氧化系统设备能力不足时,会出现石膏氧化不足,大量生成亚硫酸钙。
亚硫酸钙影响石灰石溶解及脱水系统正常运行。
3)脱水系统设备能力不足时,石膏脱水效率达不到要求,处理能力不足,影响设备正常运行。
4)石膏浆液排放系统能力不足时,吸收塔内浆液密度升高,影响脱硫系统正常运行。
4.4脱硫系统出力不足时处理方法
1)机组脱硫系统目前可能存在氧化系统出力不足,使用时如果开启备用氧化风机,则必须准备消泡剂,防止因两台氧化风机启用造成吸收塔内泡沫大量增加产生溢流事故。
2)增效剂能提高吸收塔内反应速度,加入后要求石灰石浆液供给量、石膏浆液排出量相应增加。
若出现浆液供给系统、石膏排出系统出力不足的情况,会影响吸收塔内反应的正常运行。
出现问题时进行以下操作
①停运最大浆液循环泵,降低脱硫效率。
②若停运循环泵后仍反应速度过快,减少石灰石浆液供给量,降低脱硫效率维持吸收塔内物料平衡。
③增加废水排放量,降低吸收塔内增效剂浓度,降低反应速度。
④停止增效剂补充量。