我国热轧宽带钢生产新技术及其特点
我国热轧带钢生产的新技术

我国热轧带钢生产的新技术作者:胡彬彬来源:《中国科技博览》2012年第32期[摘要]:近年来,我国热轧宽带钢产量迅猛增长,随着前期投产的生产线产量的陆续释放,以及即将投产产能的增加,后期国内热轧板卷产量增幅将继续保持在较高水平。
而近几年来我国集中建设了一大批宽带钢热轧机,数量之多,建设速度之快,不仅在我国,在全世界也是空前的。
[关键词]:热轧新技术连铸中图分类号:TG333.7+1 文献标识码:文章编号:1009-914X(2012)32- 0339-01近年来我国新建传统宽带钢热连轧机组除个别采用二手设备外有两种情况,一是引进国外技术装备的、具有当代世界最先进水平的轧机,二是由我国自主集式或国产的具有先进水平的轧机;热轧宽带钢连轧机组在工艺设备技术上的新发展,包括如下的新技术:板坯定宽压力机、带坯边部加热器、热卷箱及带钢无头轧制、精轧机组前设置立辊(FE)轧机、精轧机板型控制(凸度和平直度控制)、精轧机架数选择、全液压卷取机等。
1、连铸坯热送热装技术连铸坯热送热装是指连铸坯在600℃以上高温时直接装炉或先放入保温装置,以协调连铸与轧钢生产节奏,待机装入加热炉加热,然后再把经过加热1050℃以上的高温连铸坯直接送往轧机轧制。
该项技术具有节能、缩短生产周期、减少板坯存放仓库面积等效果,集成了几工序间的系统工程技术,需要多项技术的支撑,包括炼钢、连铸和热轧三者统一的生产计划管理,计算机进行实时控制;生产线设备具有较高的作业率;无缺陷高温连铸坯的生产;连铸和热轧均具有在线调宽的手段;热轧实施“自由轧制计划”;连铸和热轧厂布置紧凑或采取保温快速运输;加热炉采用多段快速步进梁,长行程装入机及热惰性小的陶瓷纤维耐火炉衬等,以适应热装的需要;在线补热和保温措施,如连铸和粗轧机间以及精轧机前设边部加热器,中间辊道设保温罩等。
2、直接轧制技术直接轧制是把1050℃以上的高温连铸坯,经边部加热后直接送往轧机轧制。
该技术要求炼钢、连铸能稳定生产无缺陷板坯,连铸机出料辊道和轧钢加热炉后装料辊道以辊道直接相连,输送辊道上加设保温罩等保温热坯设施,加热炉设有长行程装料机,以便于冷、热坯交叉装料时可将高温坯装入炉内深入。
我国热轧带钢生产发展趋势与对策
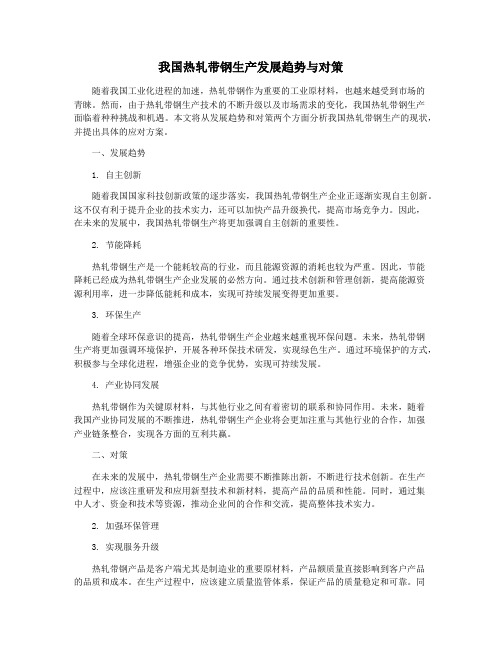
我国热轧带钢生产发展趋势与对策随着我国工业化进程的加速,热轧带钢作为重要的工业原材料,也越来越受到市场的青睐。
然而,由于热轧带钢生产技术的不断升级以及市场需求的变化,我国热轧带钢生产面临着种种挑战和机遇。
本文将从发展趋势和对策两个方面分析我国热轧带钢生产的现状,并提出具体的应对方案。
一、发展趋势1. 自主创新随着我国国家科技创新政策的逐步落实,我国热轧带钢生产企业正逐渐实现自主创新。
这不仅有利于提升企业的技术实力,还可以加快产品升级换代,提高市场竞争力。
因此,在未来的发展中,我国热轧带钢生产将更加强调自主创新的重要性。
2. 节能降耗热轧带钢生产是一个能耗较高的行业,而且能源资源的消耗也较为严重。
因此,节能降耗已经成为热轧带钢生产企业发展的必然方向。
通过技术创新和管理创新,提高能源资源利用率,进一步降低能耗和成本,实现可持续发展变得更加重要。
3. 环保生产随着全球环保意识的提高,热轧带钢生产企业越来越重视环保问题。
未来,热轧带钢生产将更加强调环境保护,开展各种环保技术研发,实现绿色生产。
通过环境保护的方式,积极参与全球化进程,增强企业的竞争优势,实现可持续发展。
4. 产业协同发展热轧带钢作为关键原材料,与其他行业之间有着密切的联系和协同作用。
未来,随着我国产业协同发展的不断推进,热轧带钢生产企业将会更加注重与其他行业的合作,加强产业链条整合,实现各方面的互利共赢。
二、对策在未来的发展中,热轧带钢生产企业需要不断推陈出新,不断进行技术创新。
在生产过程中,应该注重研发和应用新型技术和新材料,提高产品的品质和性能。
同时,通过集中人才、资金和技术等资源,推动企业间的合作和交流,提高整体技术实力。
2. 加强环保管理3. 实现服务升级热轧带钢产品是客户端尤其是制造业的重要原材料,产品额质量直接影响到客户产品的品质和成本。
在生产过程中,应该建立质量监管体系,保证产品的质量稳定和可靠。
同时,对于客户提出的各种需求,应该积极地通过技术服务、物流配送等方式,实现服务升级,增强客户的满意度。
中国热轧及冷轧板带生产技术现状及发展趋势

中国热轧及冷轧板带生产技术现状及发展趋势十一五期间,中国钢材品种结构得到较大幅度的优化调整,钢材质量性能得到明显改善,彻底改变了过去扁平材品种和数量供应不足的局面,基本满足了经济发展和产业结构调整的需要。
在统计的2010年的22大类钢材品种中,17类品种自给率达到100%;有18类品种国内市场占有率≥95%,其他品种也达到85%以上。
其中热轧、冷轧板带生产发展迅速,在数量和质量上均有较大增长。
在热轧宽带钢生产线上,中国开发生产出系列高级别管线钢、高强耐候钢及高强工程机械用钢等,在大型油气管线工程建设、汽车、集装箱、火车车厢及工程机械轻量化制造及生产应用的减量化方面发挥了重要作用。
中国采用薄板坯连铸连轧线实现了大批量生产薄和超薄规格板带,并实现半无头轧制技术集成与创新。
中国通过引进、消化吸收、自主集成和开发,极大地提高了冷轧生产效率,大幅度提高了冷轧产品质量;运用自动化、智能化控制技术及高精度检测技术,显著提高了冷轧产品的尺寸精度和板形质量。
热轧:装备技术进步造就高精度、高性能产品到2010年底,中国已拥有热轧宽带钢轧机72套,设计能力2.13亿吨,其中,2050mm~2300mm超宽带钢线已达12条,薄(中薄)板坯连铸连轧生产线13条,产能3280万t/年。
2010年中国热轧卷板生产量为14050万t,其中,中厚宽带钢和薄宽带钢生产量分别为10289万t和3760万t。
热轧带钢装备技术跨越式发展。
热轧宽带钢的先进技术主要体现在:高精度的断面形状及板形控制、高表面质量控制、柔性轧制、减量化生产、节能降耗、高效生产、热轧超薄带钢生产,以及结合快速冷却和高效冷却路径控制的高性能带钢生产技术等。
基于新的热连轧宽带钢生产线,中国开发出了18.4mm厚X80管线钢、4mm~8mm厚屈服900MPa 高强结构用钢;实现了薄板坯连铸连轧线大批量生产高精度薄和超薄规格板带,有的薄板坯连铸连轧线产品中厚度≤2.0mm的比例达到80%以上,≤1.5mm的比例超过50%,体现了薄板坯连铸连轧产线的优势,半无头轧制2.0mm板带的纵向厚度偏差和板凸度均稳定控制在±30μm以下,楔形值波动在±10μm,Q235薄规格板带的屈服强度和抗拉强度波动在15MPa以内,伸长率波动不超过2%,超薄规格极限厚度达到0.77mm。
我国宽带钢热连轧机的最新发展和技术特点

近两年我国热带钢连轧机的产能和技术水平取 得了巨大的发展 。2002 年我国宽带钢热连轧机的生 产能力是 3 200 万 t ,2003 年则为 4 608 万 t 。产品产 量 、品种和规格有了极大的发展 ,以品质为特征的技 术水平也有了长足进步 。我国目前宽带钢热连轧机 的装机水平和生产能力可以说整体达到了国际平均 水平 ,有的则代表着当代国际最新水平 。国外轧钢界 专业人士说世界上最先进的热连轧机在中国 。据统 计 ,到 2006 年 末 我 国 将 拥 有 30 套 工 作 辊 宽 度 在 1 250 mm 以上的现代化的宽带钢热连轧机 (未含台湾 地区) ,设计产能将达到 8 700 多万 t 。截止到 2004 年 5 月末 ,其中已建成投产的是 17 套 ,已经签订合同在建 或启动建设的是 13 套 (不排除个别项目会停缓建设) 。 另外还有首钢 2 160 等工程正在积极筹建之中。
2916
200412
西马克 - 德 马格
本钢 1880
FTSC - CCM ×2 + E1R1 + R2 + F
280 ×5 + HS + DC ×2
1 366
18
(70~85) ×(850~ 1 750)
热轧带钢生产在我国的发展

热轧带钢生产在我国的发展我国钢铁工业自建国以后,技术以及行业发展速度令世界震惊,但无论从钢铁质量还是工艺技术、产品结构、设备应用以及经济指标技术管理等方面还同国际先进水平有一定的差距。
目前我国在板带钢的生产能力上还无法满足国民经济的发展要求,我国生产的带钢产品中质量能够达到先进水平的1/3。
所以板带材的发展,尤其是高技术、高价值的板带材,仍旧是我国今后轧钢工业的重要任务。
文章主要对国内外热轧带钢的需求进行分析,并对其技术发展进行了论述。
标签:热轧带钢;生产现状;发展1 概述1.1 生產现状目前国外的热轧带钢技术较为先进,主要表现在以下几方面:(1)无头轧制技术。
该技术在宽薄带钢的生产中稳定性较强,并且能够生产出超薄带钢,传统的热轧技术仅能生产出宽厚比为800:1的带钢,而无头轧制技术则能够将宽厚比提高至1000:1,另外通过强制冷却以及润滑轧制技术能够生产出性能更强的技术新品。
(2)连铸连轧波板坯技术。
其囊括了十余种生产工艺:热带钢紧凑式生产工艺、热带钢在线生产工艺、薄板坯灵活压制工艺以及连铸式直接扎制工艺等。
(3)变相控制轧制工艺。
该种工艺又被称作铁素轧制工艺。
其技术工艺目标为超薄规格的高质量深冲板的生产。
LTV公司某厂采用该工艺对超低碳钢产品的轧制生产,且生产量占总产量的40%以上。
而Arvedi公司采用该工艺进行生产的产品量占总产量的25%。
国内热轧带钢的生产起步较晚,虽然我国制钢产业发展较为迅速,但是在热轧带钢工艺上仍旧落后于国际发达工业国家。
国内生产概况如下:(1)传统热轧设备。
例如,宝钢在热轧带钢的生产中所使用的2050mm轧机,其主要产品生产目标为薄规格产品,采用卷取温度为最佳温度,分别对轧制速度以及负荷分配进行优化,合理分配精轧机架的凸度。
使得制得的产品厚度符合相关标准。
为集装箱用钢板提供了标准的耐腐蚀版,解决了长期需要进口集装箱板的局面,并且在2002年又生产出1.2mm厚的热轧薄带钢。
薄规格热轧带钢市场及生产新技术

薄规格热轧带钢市场及生产新技术90年代得到迅速发展的薄板坯连铸连轧和板坯定宽压力机在热连轧线上的应用,简化了生产工艺,降低了生产成本,并使热轧带钢的厚度降低到1.5mm以下,因此人们关心今后什么样的热轧产品能完全替代冷轧产品,并将对下游产品产生什么影响。
热轧带钢的市场规格在1995年前厚度小于1.5mm的热轧带钢只占生产份额的0.3%,厚度1.5~1.99mm之间的占10%(见图1),那时高碳钢(C70)的最小厚度约为2.0mm,低碳钢则约为1.5mm,而目前高碳钢和低合金高强度钢(HSLA)的最小厚度均可达1.5mm。
图11995年前热轧带钢厚度的典型分布代替冷轧带钢的市场分析图2给出冷轧带钢代表产品构成频率分布,从中可以看出,几乎60%的冷轧带钢在0.6~1.2mm厚度范围内,而大量的市场份额仍由冷轧带钢占有,因此提升热轧带钢代替冷轧带钢的潜力巨大。
按墨西哥希尔萨(Hylsa)公司的经验(CSP设备),可达到并能盈利的最小热轧带厚度为0.91mm(现可达0.80mm)。
图2薄规格热轧带钢和冷轧带钢厚度的重叠据研究有三个主要因素对薄规格热轧带钢(TGHR)的数量和最终消费极为重要:(1)用薄规格热轧带钢替代冷轧带钢。
(2)在市场开发中汽车和建筑业的应用增长起关键作用。
(3)在与铝、塑料代用品竞争中赢得的市场份额。
对市场应用的预测见图3。
引人注目的是市场年增长率美国为8.3%,欧盟为6.7%,日本为6.6%,这与不景气的钢总耗量明显相反。
图3薄规格热轧带钢未来市场潜力薄规格热轧带钢的生产成本。
图4显示“热轧工艺”(1.0mm厚经酸洗和平整的热轧带钢)与“常规生产工艺”的附加生产成本比较,在预算盈利中,附加成品是以2.0mm厚热轧带钢为基础,按两种工艺来计算的。
由图看出,目前两种工艺相比较,前者的每吨生产成本节省了20美元,还需指出成本分析中没有考虑相当大的“库存成本”另外还表明,轧制极薄的热带时,仍会产生每吨15美元的附加成本(工作辊磨损和产量损失)。
热连轧带钢生产现状及发展趋势资料

热连轧带钢生产现状及发展趋势摘要本文介绍了最近十几年热连轧带钢生产的最新发展、技术进步和目前的状况,全面分析了热连轧带钢的先进技术、新装备。
并针对现状,展望对未来发展的趋势。
由于可控硅供电电气传动及计算机自动控制等新技术的发展,液压转动、升速轧制、层流冷却等新设备新工艺的利用,热连轧机的发展更为迅速。
热轧带钢是通用性钢材,目前是我国急需的短线产品,被广泛用于国民经济各部门。
热轧带钢按宽度尺寸分为宽带钢及窄带钢两类,宽度在700-2300mm者为宽带钢,由于宽度及卷重较大,所以在大型带钢厂连轧机上生产,其用途主要用于汽车、拖拉机、机械制造、船舶制造、桥梁、锅炉制造等。
一般宽度在50-250mm为窄带钢,多作为焊管、冷弯型钢、冷轧带钢的原料和用于建筑、轻工、机电等部门。
生产热轧带钢在我国目前有横列式、纵列式、连续式和行星式轧机等多种型式。
目前世界约有140套宽带热连轧机,其中60%为1960年所建在发展的国家中,由连轧机生产的板带钢已达板带钢总产量80%以上,占总钢材产量的50%以上,产品已达到优,高产和低成本的要求,因此热连轧带钢生产已成为轧钢生产的主流。
关键词:热连轧带钢轧机、现状及趋势Current situation and development trend of hot rolling stripproductionAbstractThis paper introduces the latest development in recent years, hot rolling strip production technology and the present situation, a comprehensive analysis of the advanced technology, the new equipment of hot rolling strip. And in view of the present situation, prospect of the future development trend. Due to the development of new technology of thyristor power supply electric drive and computer automatic control, with hydraulic rotation, increasing speed rolling, laminar cooling of new equipment and new technology of hot rolling mill, the more rapid development. Hot rolled strip steel is universal, is currently China's much-needed short-term products, widely used in various sectors of the national economy. Hot rolled strip in width size as broadband and narrowband steel steel two, width in 700-2300mm for broadband steel, because the width and volume weight is bigger, so the production in large belt steel rolling mill, its use is mainly used for automobile, tractor, machinery manufacturing, shipbuilding, bridge, boiler manufacturing etc.. General width of 50-250mm strip steel, much as welded tube, cold-formed steel, cold-rolled strip steel material and used for building, light industry, mechanical and electrical department. The production of hot rolled strip in China have transverse, longitudinal, continuous and planetary mill and other types of current. At present, the world has about 140 sets of wide hot strip mill, of which 60% were built in 1960 in the developed countries, the strip rolling mill production has reached more than 80% of the total output of steel strip, accounted for more than 50% of steel production, the products have reached the quality, high yield and low cost requirements, so the hot strip rolling has become the mainstream in steel rolling production.Key words:current status and trend of hot strip mill目录摘要 (1)Abstract (2)1、前言 (2)2、热连轧生产工艺的发展 (4)3、带钢热连轧生产过程 (4)3.1、原料准备 (4)3.2、板坯加热及设备组成 (5)3.3、粗轧机组 (5)3.4、精轧机组 (6)3.5、调宽 (7)4宝钢1780热轧 (7)4.1、1780热轧的生产设备及工艺流程 (7)4.2、工艺流程图 (7)4.3、1780热轧的产品、规格及生产能力 (7)5热连轧钢的发展 (8)5.1热连轧钢的技术发展 (8)5.2热带钢装备技术进步 (9)5.3温度控制技术进步 (9)6现代热连轧机的发展趋势和特点 (10)结束语 (10)参考文献: (12)1、前言自1924年第一台带钢热连轧轧机投产以来,连扎带钢生产技术得到很大的发展。
TM热轧带钢工艺特点与生产应用
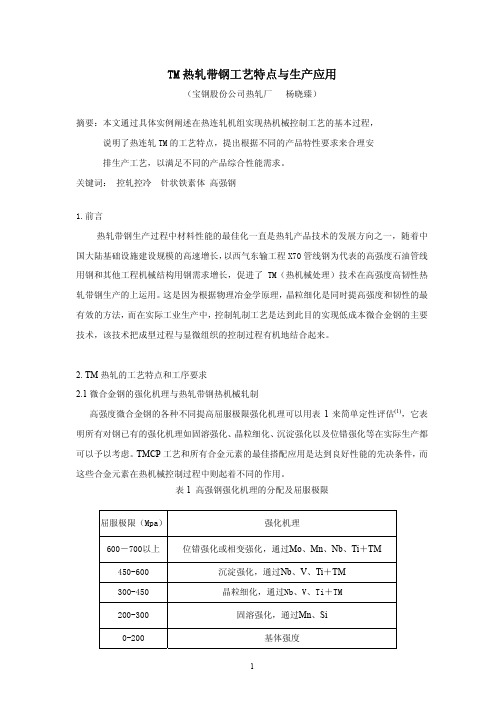
TM热轧带钢工艺特点与生产应用(宝钢股份公司热轧厂 杨晓臻)摘要:本文通过具体实例阐述在热连轧机组实现热机械控制工艺的基本过程,说明了热连轧TM的工艺特点,提出根据不同的产品特性要求来合理安排生产工艺,以满足不同的产品综合性能需求。
关键词: 控轧控冷 针状铁素体 高强钢1.前言热轧带钢生产过程中材料性能的最佳化一直是热轧产品技术的发展方向之一,随着中国大陆基础设施建设规模的高速增长,以西气东输工程X70管线钢为代表的高强度石油管线用钢和其他工程机械结构用钢需求增长,促进了TM(热机械处理)技术在高强度高韧性热轧带钢生产的上运用。
这是因为根据物理冶金学原理,晶粒细化是同时提高强度和韧性的最有效的方法,而在实际工业生产中,控制轧制工艺是达到此目的实现低成本微合金钢的主要技术,该技术把成型过程与显微组织的控制过程有机地结合起来。
2. TM热轧的工艺特点和工序要求2.1微合金钢的强化机理与热轧带钢热机械轧制高强度微合金钢的各种不同提高屈服极限强化机理可以用表1来简单定性评估(1),它表明所有对钢已有的强化机理如固溶强化、晶粒细化、沉淀强化以及位错强化等在实际生产都可以予以考虑。
TMCP工艺和所有合金元素的最佳搭配应用是达到良好性能的先决条件,而这些合金元素在热机械控制过程中则起着不同的作用。
表1 高强钢强化机理的分配及屈服极限屈服极限(Mpa) 强化机理600-700以上 位错强化或相变强化,通过Mo、Mn、Nb、Ti+TM 450-600 沉淀强化,通过Nb、V、Ti+TM300-450 晶粒细化,通过Nb、V、Ti+TM200-300 固溶强化,通过Mn、Si0-200 基体强度对于热连轧必须采取以下措施以更好地实现微合金的强化作用:z板坯在加热阶段,微合金元素应溶解在奥氏体中z在临界再结晶温度以下获得大的变形量,以产生未再结晶的奥氏体z通过应变诱导从过饱和的奥氏体中析出极其微小的微合金化元素的碳、氮化合物使再结晶过程推迟z使没有再结晶的变形程度很大的奥氏体转变为铁素体或其他转变产物z通过分段冷却控制和调整冷却速度,以谋求不同的沉淀强化效果2.2 TM工艺对热连轧机组各工序的要求为了通过TM工艺实现带钢性能的最佳化,必须通过以下措施来实现:因此,从材料的工艺要求可以得出热轧带钢机组配置和工序要求:z能够实现降低板坯加热温度和降低精轧入口温度的加工工艺z提高轧机功率以克服高的变形抗力并保证板材极限尺寸下所要求的板型(2)z提高精轧前飞剪功率以增加中间带坯的厚度,获得较大的精轧变形区压缩比z根据不同产品要求制订不同等级的冷却速度,同时在较低温度下能进行温度测量、计算机精确控制和厚规格带钢的顺利卷入,从而利用很低卷取温度改变组织性能的优点z采用诸如保温罩设备和加速轧制及计算机速度、温度控制,尽可能减少板材宽度和长度方向的温度差,以减小微合金钢性能上的波动和各向异性z制订针对微合金钢表面质量控制措施和加速冷却后板形控制措施采取这些措施后,就能够更好地执行热机械轧制工艺,同时获的更好的产品工艺质量,以利于进一步加工。
- 1、下载文档前请自行甄别文档内容的完整性,平台不提供额外的编辑、内容补充、找答案等附加服务。
- 2、"仅部分预览"的文档,不可在线预览部分如存在完整性等问题,可反馈申请退款(可完整预览的文档不适用该条件!)。
- 3、如文档侵犯您的权益,请联系客服反馈,我们会尽快为您处理(人工客服工作时间:9:00-18:30)。
我国热轧宽带钢生产新技术及其特点一、概述近年来,我国热轧宽带钢产量迅猛增长,2007年共生产热轧宽带钢万T,较2006年(万T)增长%;2008年继续快速增长,1~5月生产热轧宽带万T,比去年同期(万T)增加%,比钢材产量增幅高出个百分点,其中5月份产量万吨,同比增长%,创下热轧板卷月产量的历史新高,当月日均产量也首次突破30万吨,达到了万吨。
2008年是我国热轧板卷产能投产比较集中的一年,包括已经投产的北台1780机组、宁钢1780机组、武钢1580机组、唐钢1580机组和邯郸新金1250机组等,全年预计将有16条热轧生产线投产,新增产能超过4500万吨。
随着前期投产的生产线产量的陆续释放,以及即将投产产能的增加,后期国内热轧板卷产量增幅将继续保持在较高水平。
考虑到2008年下半年新投产机组的产能将逐渐释放,全年热轧宽带钢产量将有可能达到亿T。
而近几年来我国集中建设了一大批宽带钢热轧机,数量之多,建设速度之快,不仅在我国,在全世界也是空前的。
与此同时,我国宽带钢热连轧技术和装备能力水平也取得巨大发展, 其特点:一是投资规模前所未有,实现的投资延伸到从铁水预处理、钢水精炼到连铸,从钢铁冶金、压力加工到精整和配送的投入;二是技术和规模上水平,不仅引进了多套当代国际最先进的机组,而且建设了多条自主集成技术、自行设计和制造的轧制线;三是热轧宽带钢产品大纲普遍涵盖了建材、汽车、家电、机械、化工和管道输送等用途,包括低合金、高强度、薄规格、深冲板, 板形和厚度尺寸公差及表面质量俱佳的高端产品。
二、热轧宽带钢轧机工艺装备新技术近年来我国新建传统宽带钢热连轧机组除个别采用二手设备外有两种情况,一是引进国外技术装备的、具有当代世界最先进水平的轧机,二是由我国自主集式或国产的具有先进水平的轧机;热轧宽带钢连轧机组在工艺设备技术上的新发展,包括如下的新技术:板坯定宽压力机、带坯边部加热器、热卷箱及带钢无头轧制、精轧机组前设置立辊(FE)轧机、精轧机板型控制(凸度和平直度控制)、精轧机架数选择、全液压卷取机等。
现就其中关键设备技术做一下介绍:1、连铸坯热送热装技术连铸坯热送热装是指连铸坯在600℃以上高温时直接装炉或先放入保温装置,以协调连铸与轧钢生产节奏,待机装入加热炉加热,然后再把经过加热1050℃以上的高温连铸坯直接送往轧机轧制。
该项技术具有节能、缩短生产周期、减少板坯存放仓库面积等效果,集成了几工序间的系统工程技术,需要多项技术的支撑,包括炼钢、连铸和热轧三者统一的生产计划管理,计算机进行实时控制;生产线设备具有较高的作业率;无缺陷高温连铸坯的生产;连铸和热轧均具有在线调宽的手段;热轧实施“自由轧制计划”;连铸和热轧厂布置紧凑或采取保温快速运输;加热炉采用多段快速步进梁,长行程装入机及热惰性小的陶瓷纤维耐火炉衬等,以适应热装的需要;在线补热和保温措施,如连铸和粗轧机间以及精轧机前设边部加热器,中间辊道设保温罩等。
热装轧制工艺在热轧带钢轧机中已经普遍采用,日本、韩国的热轧带钢轧机热装比达到60%以上,最多可达80%,热装温度达到600℃以上,我国近年来建设的1580、1750、1780、2250机组在设计大纲中都对热装轧制比例作出了要求。
为加热直接热装板坯,国外热带钢轧机专门用一座加热炉进行加热。
例如日本JFE千叶厂3号加热炉、福山厂3号加热炉、鹿岛厂4号加热炉都专门用于直接热装炉加热。
2、直接轧制技术直接轧制是把1050℃以上的高温连铸坯,经边部加热后直接送往轧机轧制。
该技术要求炼钢、连铸能稳定生产无缺陷板坯,连铸机出料辊道和轧钢加热炉后装料辊道以辊道直接相连,输送辊道上加设保温罩等保温热坯设施,加热炉设有长行程装料机,以便于冷、热坯交叉装料时可将高温坯装入炉内深入。
为实现直接轧制工艺,无缺陷高温板坯、热送坯的保温设备,板坯边角加热炉,生产管理计算机以及区域管理计算机等硬件条件是必不可少的,且高水平的连铸和热轧操作、生产计划和各工序的协调是关键。
根据日本、韩国一些厂家的经验,如解决好这些问题可以不影响轧机小时生产能力。
至于直接轧制所受钢种的限制,根据日本生产厂的经验,除取向硅钢、高牌号非取向硅钢、不锈钢以及高牌号镀锡板之外,其余钢种都能直接轧制。
直接热装和直接轧制是当代热轧带钢轧机的发展方向。
热装的高水平即是直接热装。
正是因为直接轧制对软、硬件要求很高,投产后的一段时间难于实现直接轧制,国外新建热轧带钢轧机一般优先考虑热装炉工艺和直接热装炉工艺的实现,预留采用直接轧制工艺余地。
直接轧制作为热轧带钢轧机的发展方向是不容置疑的。
热装炉轧制工艺已有多年的生产经验,可以取得良好的节能效果;直接热装炉轧制工艺进一步提高节能效果,缩短生产周期,使连铸机和热轧机更紧密地联系在一起,同时,为实现直接轧制工艺,所采用的技术措施同样对实现直接轧制是必需的。
在新建热轧机时,直接轧制工艺要在平面布置上尽量考虑两车间紧凑布置,连铸机板坯输出辊道直接和热轧机加热炉出炉辊道相连,但设计上不应追求以高百分比直接轧制为目的,而是根据品种、规格及生产能力的要求考虑采用直接轧制的百分比,让生产厂根据今后实际操作水平来决定组织直接轧制,以期达到最佳的综合经济效益。
3、无头轧制和半无头轧制技术无头轧制和半无头轧制技术是近年来出现的新技术。
无头轧制主要应用在热轧带钢和棒线材生产中,采用传统分块轧制方式的轧机要频繁的咬钢、抛钢和变换轧制速度,造成钢材头、尾部的质量难以保证,轧机作业率较低,对产品尺寸精度的控制也较为困难。
对此,有关科技工作者通过在传统的热轧生产线上设置采用钢坯对焊机及精轧后连续轧制。
该方法与传统轧制方法相比,成材率可提高%至%;生产率可提高10%至15%;产品质量、精度也有较大的提高。
此外,用传统的轧制方法轧薄板时容易出现跑偏、甩尾、浪形等问题;而无头轧制则无此现象,可提高钢带行走的稳定性,可以生产0.8毫米至1.0毫米带材。
此技术由于避免了频繁的咬钢,设备的磨损和废品率也有所下降,可降低%至3%的生产成本。
半无头轧制主要用于薄板坯连铸连轧生产线,主要是为生产薄规格热轧带钢设计的,虽然其设备配置与传统的薄板坯连铸连轧大体相同,但是技术有很大变化。
比如,采用半无头轧制的CSP生产线,薄板坯出结晶器时的厚度为63毫米,经过液芯压下后离开连铸机时连铸坯厚度为48毫米。
此时,连铸坯不剪断进入隧道式加热炉(传统CSP生产线连铸坯剪断为40余米),加热炉可达300余米(传统CSP生产线为200米);连铸坯经均热以后进入7机架连轧机组轧制成材。
该生产线的输出冷却辊道分为两段,第一段较短,为30米左右,其中快速冷却水集管为10米左右,冷却段后是超薄带卷取机(旋转卷取机);第二段为传统的层流冷却和传统的卷取机,主要生产一般规格的热带。
为对生产的成品带钢进行分卷,在每个卷取机前均设有高速飞剪。
该生产线的产品以超薄规格热带为主,其中0.8毫米至3毫米的带钢占60%以上;高强度钢的最小厚度为1.2毫米,低碳钢的最小厚度可以达到0.8毫米。
宽度为900毫米至1600毫米的产品如果采用半无头轧制技术,双流连铸的最大产量可达240万吨。
企业采用半无头轧制技术可利用连铸坯可以较长的特点,减少穿带过程产生的带钢温度降低、厚度不易控制和生产不稳定等问题,非常有利于薄规格产品的轧制。
4、板坯定宽压力机(SSP):板坯宽度大侧压经历大立辊(VSB)侧压、大立辊与R1二辊轧机构成组合式轧机K1R1侧压,发展到了全新概念的板坯定宽压力机(FLYING S1ZING PRESS)。
我国新建武钢、马钢、首钢、邯钢2250MM轧机、宝钢1880MM轧机、鞍钢1780MM 轧机等都设有连续/ 间断式定宽压力机SSP。
板坯定宽侧压机(SP)的轧制原理是靠模块步进式动作,在板坯侧面施加压力,以达到板坯的减宽目的。
为实现上述要求、模块有动作和传动系统,即模块的开口调整、模块的开闭动作、模块与板坯的同步动作。
定宽压力机的主要技术特点是:宽度调整能力大。
一道次最大侧压量可达350毫米,平均侧压量为200毫米,减少了连铸板坯的宽度规格,连铸板坯宽度规格与没有采用定宽压力机前相比可以减少50%以上,对于2250MM 轧机仅需6 种宽度的板坯,因而可提高连铸机产量25%,结晶器宽度变化少,铸速恒定,连铸坯表面质量良好,可提高热装比率,节省加热炉能源达29%。
板坯侧压速度快。
由于连续、快速侧压(40-50行程/分,400毫米/行程),一块10米长板坯只需约30秒可完成侧压提高了生产力,而且能控制板坯表面温度下降。
侧压后的板坯形状非常规整,切损少,比采用大立辊切损约减少一半,侧压板坯边部凸起量较立辊轧制小得多, 有效减少了水平轧制后的鱼尾切损, 成材率提高。
定宽压力机结构复杂,但维修时间并未比过去增加。
定宽压力机设有两对上、下布置压下模块,可交换使用,更换时间每对只需30分钟。
对大批量热装和直接轧制生产十分有利,可缩短热坯的在库时间。
直接热装比因此可提高1倍。
5、中间坯短行程控制和宽度自动控制立辊轧机的辊缝在轧制过程中不断变化,使头尾部失宽量减少,短行程法可减少切头损失率,并显着提高头尾部的宽度精度。
西马克- 德马格公司新开发的无镰刀弯轧制CFR(CAMBER FREE ROLLING) 技术, 通过粗轧机前的强力侧导机构, 增强的粗轧能力和液压压下以及自动化控制系统有效地防止了中间坯强力轧制后镰刀弯的产生;全液压的立辊机架具有良好的自动调宽AWC 和短行程控制SSC 功能, 提高了中间坯宽度控制精度, 改善了板坯的头尾形状, 减少了头尾切损。
加大轧机主马达功率和机架刚度,减少粗轧机架数,粗轧机1~2架即可与精轧机能力相适应,过去武钢1700MM轧机、宝钢2050MM轧机均设有4架粗轧机;新建武钢、马钢、邯钢2250MM轧机均仅设有2架粗轧机,R1 和R2 均为四辊轧机, 采用电动机械压下和液压压下,R1的轧制力由30000~40000KN 提高到45000KN , R2的轧制力达到50000KN , 有利于增大压下量, 轧制较薄、厚度均匀的中间坯,且利于增加轧制工艺与精轧机组能力匹配的灵活性;首钢、太钢2250MM轧机、宝钢集团一钢公司1780MM轧机等仅设有1架粗轧机;粗轧机架数的减少可节约投资,减少设备维修量及劳动定员,效益明显。
?6、中间坯保温技术和边部感应加热技术粗轧机出口处带坯较长,为减少头尾温差,在延伸辊道增加保温罩, 改善了中间坯温度的均匀性, 减少了头尾温差,宝钢2050MM、1580MM和鞍钢1780MM轧机、邯钢2250MM等均采用了保温罩。
而采用电感应加热器提高带坯边部温度,是近十年来发展的新工艺,主要目的是改善钢坯断面温度分布和金相组织,防止薄带钢和硅钢、不锈钢、高碳钢等特殊品种的边部裂纹,减少轧辊发生不均匀磨损的几率。