精选影响加工精度的因素
机械加工精度的影响因素分析

机械加工精度的影响因素分析
一、概述
机械加工是现代工业中不可或缺的一环,其加工精度对产品质量和生产效率至关重要。
本文将对机械加工精度的影响因素进行详细分析。
二、加工机床的精度
加工机床是机械加工的关键设备,其精度是影响加工精度的首要因素。
加工机床的精度包括机床的基础平整度、导轨精度、直线度、角度等方面。
同时,加工机床的质量和结构也会影响加工精度。
三、切削刀具的精度
切削刀具是机械加工中使用较为广泛的切削工具,其使用寿命和切削效率直接影响加工精度。
切削刀具的精度包括直径误差、轴线偏差、齿面质量等。
四、工件材料和表面状态
工件材料和表面状态对机械加工精度也有重要影响。
不同材料的硬度、强度、切削性能等会直接影响加工难度和加工精度。
而表面状态也会导致加工后的精度差异,如表面粗糙度、表面硬度等。
五、加工工艺参数的选择
在机械加工过程中,加工工艺参数的选择也是影响加工精度的因素之一。
加工工艺参数包括切削速度、进给量、切削深度等。
不同的工艺参数会直接影响切削力和加工精度。
六、工作环境的影响
工作环境也会对机械加工精度产生影响,如温度、湿度等因素都会对加工精度造成一定的影响。
七、总结
综上所述,机械加工精度的影响因素是多方面的,包括加工机床的精度、切削刀具的精度、工件材料和表面状态、加工工艺参数的选择以及工作环境的影响等。
对于工业生产来说,保证机械加工精度是提高产品质量和生产效率的基础。
机械加工精度的影响因素及提高措施

机械加工精度的影响因素及提高措施机械加工精度是指在机械加工过程中所能达到的尺寸精度、形位精度和表面精度,它主要受到以下几个因素的影响:1. 加工设备的精度:加工设备的精度是机械加工精度的基础。
设备的精度主要包括切削力、回转精度、传动精度等方面。
高精度的加工设备能够减小加工误差,提高机械加工精度。
2. 材料的性质:材料的硬度、韧性和变形性等特性对机械加工精度有影响。
硬度高的材料会增加切削力,导致加工误差增大;韧性差的材料容易产生毛刺和划痕,影响表面精度;变形性差的材料会导致尺寸误差增大。
3. 刀具的选择和使用:刀具的质量和使用方式直接影响加工精度。
选择适合材料和工件的刀具,保持刀具的锋利度和稳定性,合理使用刀具,可以提高机械加工精度。
4. 加工参数的控制:加工参数的选择和控制直接影响加工精度。
切削速度、进给速度和切削深度等参数的选取要根据材料的性质和加工要求进行合理调整,过大或过小都会导致加工精度降低。
5. 加工过程的热变形:在机械加工过程中,切削热会引起工件和刀具的热变形,从而影响加工精度。
为了避免热变形,可以采取降低切削速度、加工液冷却、减小切削力等措施。
为了提高机械加工精度,可以采取以下措施:1. 选择优质的加工设备:优质的加工设备具有高精度、高刚度和高稳定性,能够保证加工精度。
2. 提高刀具的质量:选择高品质的刀具,保持刀具的锋利度和稳定性,及时更换磨损的刀具。
4. 采取适当的加工工艺:选择合适的工艺路线、夹具和刀具等加工工艺,减小加工过程中的变形和振动。
5. 加强员工培训:提高操作人员的技术水平和加工意识,提高人工操作的准确性和稳定性。
机械加工精度的影响因素很多,要提高机械加工精度,需要综合考虑各种因素并采取相应的措施,以保证加工精度的稳定性和可靠性。
12影响加工精度的因素解析

12影响加工精度的因素解析加工精度是指在加工过程中,所得到的工件尺寸与设计要求之间的偏差程度。
影响加工精度的因素众多,主要包括机床精度、刀具质量、工件材料及加工方法等。
下面对这些因素进行详细分析。
第一、机床精度:机床精度是指机床本身的加工能力和稳定性。
包括机床的定位精度、运动精度、重复定位精度等方面。
定位精度:机床刀具在加工坐标轴上进行定位时的精度。
定位精度越高,机床的加工精度越高。
运动精度:机床刀具在进行运动时的精度。
运动精度包括刀具的速度、加速度保持平稳、方向精确等。
如果机床运动过程中存在震动或者晃动,会导致工件尺寸的变化,从而影响加工精度。
重复定位精度:机床进行多次定位时,每次定位的精度是否相同。
重复定位精度越高,加工精度越稳定。
第二、刀具质量:刀具是实现工件形状的关键工具。
刀具质量直接决定了加工精度。
刀具材料:刀具材料的硬度、耐磨性等性能会直接影响切削力的大小和稳定性。
如果刀具磨损严重,切削力难以控制,就会影响工件尺寸的精度。
刀具几何形状:刀具的几何形状包括刀尖半径、刀片角度、刀片刃口和刃后角等。
这些参数的选择会直接影响加工表面的光洁度和精度。
第三、工件材料:工件材料的硬度、韧性、热膨胀系数等参数都会对加工精度造成影响。
硬度:工件材料的硬度越大,加工难度越大,加工精度也会受到影响。
高硬度的材料容易导致刀具磨损,从而影响加工精度。
热膨胀系数:工件材料的热膨胀系数越大,加工过程中材料的膨胀和收缩也就越大,容易引起工件变形,从而导致尺寸精度降低。
第四、加工方法:加工方法对加工精度有直接的影响。
切削速度:过高或过低的切削速度都会影响切削力和刀具磨损,从而影响加工精度。
进给速度:过大的进给速度会导致切削力过大,造成加工表面的毛刺和震动。
过小的进给速度则会延长加工时间,增加刀具磨损。
冷却液使用:适当的冷却液可以降低加工过程中的温度,减小热变形的影响,保持加工精度的稳定性。
总结起来,加工精度受到多个因素的影响,包括机床精度、刀具质量、工件材料和加工方法等。
零件加工精度的影响因素及工艺优化设计

零件加工精度的影响因素及工艺优化设计随着工业技术不断向前发展,零件加工精度已经成为了衡量生产企业产品品质和竞争力的重要标准之一。
而影响零件加工精度的因素也越来越多,下面简要介绍零件加工精度的影响因素及工艺优化设计。
1.材料因素:零件加工精度直接受材料本身的性能、组织和温度等影响。
如材料的硬度、强度、韧性、断裂韧性都会影响零件加工精度,温度的高低也会影响零件的收缩率和热变形率,从而影响零件的加工精度。
2.机床因素:机床的精度和刚性也会直接关系到零件加工的精度。
比如机床的切削刚性和导向精度、主轴的转速和转动精度等等。
机床等设备的长期老化也会影响加工精度。
3.刀具因素:刀具的质量和耐用度也会影响零件加工的精度。
如切削刃的结构设计、刀具材料、工具的硬度、加工面积与刀具贴面等决定了刀具的切削性能和稳定性。
4.工艺因素:工艺参数的合理性也是影响零件加工精度的重要因素之一。
工艺参数包括进给速度、切削速度、冷却液的使用(注塑模具和淹没切削)、夹紧力(仅适用于加工旋转体零件),刀具尺寸和冷却液等等。
在以上因素的基础上,我们需要考虑以下几点来进行工艺优化设计:1.合理选择材料:各材料之间的性能差异会导致零件加工精度的差异,所以需要在设计零件时选择合适的材料。
在已有的材料中,需要考虑材料的硬度、强度、韧性、断裂韧性以及温度的影响等。
2.选择精度高、刚性好的机床:机床一定要保持精度高、刚性好,并保持机床的良好状态。
确保机床的润滑和清洗,机床上设置合理的液压装置,确保机床的摆动灵敏,提高机床的刚性等。
3.选择优质刀具且注意保养:优质的刀具能够提供更好的切削性能和稳定性,所以需要选择优质的刀具。
在刀具的使用过程中需要注意刀具的清洗和保养。
通过以上措施,能够更好的控制零件加工精度,并在实际生产中保证产品的质量和稳定性。
影响加工精度的因素及控制措施
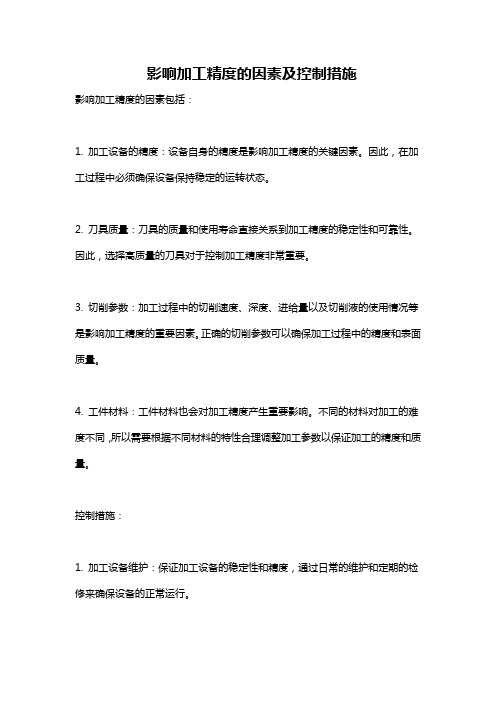
影响加工精度的因素及控制措施
影响加工精度的因素包括:
1. 加工设备的精度:设备自身的精度是影响加工精度的关键因素。
因此,在加工过程中必须确保设备保持稳定的运转状态。
2. 刀具质量:刀具的质量和使用寿命直接关系到加工精度的稳定性和可靠性。
因此,选择高质量的刀具对于控制加工精度非常重要。
3. 切削参数:加工过程中的切削速度、深度、进给量以及切削液的使用情况等是影响加工精度的重要因素。
正确的切削参数可以确保加工过程中的精度和表面质量。
4. 工件材料:工件材料也会对加工精度产生重要影响。
不同的材料对加工的难度不同,所以需要根据不同材料的特性合理调整加工参数以保证加工的精度和质量。
控制措施:
1. 加工设备维护:保证加工设备的稳定性和精度,通过日常的维护和定期的检修来确保设备的正常运行。
2. 刀具选择:选择质量稳定、寿命长、精度高的刀具,这不仅可以提高加工效率,也可以保证加工质量稳定。
3. 切削参数控制:合理设置切削速度、深度、进给量以及切削液的使用情况,确保加工质量和表面质量。
4. 工件材料选择:根据工件材料的特性确定加工参数,以确保加工的质量和精度。
数控机床加工精度的影响因素及提高方法

数控机床加工精度的影响因素及提高方法数控机床加工精度是指机床在进行加工过程中所能达到的准确度和稳定性。
影响机床加工精度的因素非常多,下面将对影响因素和提高方法进行一些阐述。
1. 机床自身的优劣:机床的设计、制造和装配技术对加工精度有直接影响。
优质的机床在设计和制造过程中会注重减小传动误差、提高定位精度和重复定位精度等。
2. 机床的刚性和稳定性:机床的刚性和稳定性对加工精度起着决定性的作用。
刚性不足会导致机床在加工过程中出现振动和变形,从而影响加工精度。
3. 传动装置的精度和可靠性:传动装置的传动误差、反向间隙等都会影响加工精度。
传动装置的精度和可靠性越高,加工精度也越高。
4. 控制系统的精度:数控机床的控制系统对加工精度有直接影响。
控制系统的精度主要包括伺服系统的控制精度、编码器的精度以及数控系统的实时性等。
5. 刀具和夹具的精度:刀具和夹具的精度直接影响加工质量。
刀具和夹具的选择和安装都需要考虑其精度和稳定性。
1. 选用优质的机床:选择优质的机床是提高加工精度的基础。
优质的机床具有高精度、高刚性和高稳定性,能够更好地满足加工要求。
2. 优化加工工艺:通过优化加工工艺,合理设置切削参数和进给速度等,可以减小加工误差,提高加工精度。
4. 优化编程和加工过程:合理优化数控程序和加工过程,减小加工误差。
尽量避免急停和急转等情况,保证加工过程的平稳性和稳定性。
5. 定期进行机床维护和保养:定期进行机床的维护和保养,保证机床的正常运行和精度稳定性。
包括清洁、润滑和紧固等工作。
数控机床加工精度的提高需要从机床自身的优劣、刚性和稳定性、传动装置的精度和可靠性、控制系统的精度以及刀具和夹具的精度等方面进行综合考虑。
通过优化加工工艺、合理选择刀具和夹具、加强编程和加工过程的管理以及定期进行机床维护和保养等措施,可以有效提高数控机床的加工精度。
零件加工精度的影响因素及工艺优化设计

零件加工精度的影响因素及工艺优化设计零件加工精度是衡量零件制造质量的重要指标之一,精度的好坏直接影响着零件的使用性能和生产效率。
在零件加工过程中,有许多因素会对零件的加工精度产生影响。
了解这些影响因素并进行工艺优化设计是非常重要的。
本文将对零件加工精度的影响因素进行分析,同时提出相应的工艺优化设计方案,旨在提高零件加工精度,提高产品质量和生产效率。
一、影响零件加工精度的因素1.零件设计参数:零件的设计参数,如尺寸、形状、公差等都会直接影响零件的加工精度。
尺寸设计不合理、公差设置不合理都会导致零件加工精度降低,这就需要在设计阶段就进行精密度的控制。
2.材料选择:零件加工材料的选择也会对零件的加工精度产生较大的影响。
材料的硬度、密度、热膨胀系数等都会直接影响零件加工的精度,因此在选择材料时需要充分考虑到这些因素。
3.加工设备:加工设备的精度和稳定性,也是影响零件加工精度的重要因素。
加工设备的精度不能满足零件加工的要求,就会导致零件的精度降低。
需要选用精度高、稳定性好的加工设备,保证零件的加工精度。
4.加工工艺:加工过程中的工艺也是影响零件加工精度的重要因素。
包括切削刀具的选择、切削参数的设置、加工路径的规划等,都会对零件的加工精度产生影响。
需要合理规划加工工艺,提高零件加工的精度。
5.加工环境:加工环境的清洁度、湿度、温度等也会对零件的加工精度产生影响。
加工环境干净、温度恒定的情况下,能够降低加工振动和热变形,提高加工精度。
6.操作人员技术水平:操作人员的技术水平也会对零件的加工精度产生影响。
操作人员能否熟练掌握加工设备、合理使用切削工艺,都会直接影响零件的加工精度。
上述因素是影响零件加工精度的主要因素,了解这些因素并根据实际情况进行工艺优化设计是提高零件加工精度的关键。
二、工艺优化设计1.合理选择材料:在零件加工过程中,首先需要根据零件的使用要求和加工情况,选择合适的加工材料。
不同材料的物理性质和加工特性不同,选择合适的材料可以降低加工难度,提高加工精度。
影响机械加工精度的几个重要因素

(二)工艺系统刚度对加工精度的影响
1.加工过程中由于工艺系统刚度发生
变化引起的误差 图
x
y系 y刀架 yx y刀架 y主轴 y尾座 y主轴 l
lx
F主轴 Fp xl
F尾座 Fp
y系 y刀架 y 例
l
x
Fp
1 k刀 架
1 k主 轴
l
l
x
2
1 k尾
座
x l
2
2.由于切削力变化引起的误差 加工过程中,由于毛坯加工余量和工件 材质不均等因素,会引起切削力变化,使工 艺系统变形发生变化。从而产生加工误差。 误差复映现象: 图 车削一具有锥形误 差的毛坯,加工表面上必然有锥形误差;待 加工表面上有什么样的误差,加工表面上必 然也有同样性质的误差,这就是切削加工中 的误差复映现象。
例如:用三爪自定心卡盘装夹薄壁套简 镗孔时,夹紧前薄壁套筒的内外圆是圆的, 夹紧后工件呈三棱圆形;镗孔后,内孔呈圆 形;但松开三爪卡盘后,外圆弹性恢复为圆 形,所加工孔变成为三棱圆形,使镗孔孔径 产生加工误差。为减少由此引起的加工误差, 可在薄壁套筒外面套上一个开口薄壁过渡环, 使夹紧力沿工件圆周均匀分布。
通常都是通过机床完成的。工件的加工精度 在很大程度上取决于机床的精度。
机床制造误差中对工件加工精度影响较 大的误差有:主轴回转误差、导轨误差和传 动误差。
1.主轴回转误差
机床主轴是用来装夹工件或刀具,并将 运动和动力传给工件或刀具的重要零件,主 轴回转误差将直接影响被加工工件的形状精 度和位置精度。
3)第一次卸载后,刀架恢复不到第一 次加载的起点,这说明有残余变形存在,经 多次加载和卸载后,加载曲线起点才和卸载 曲线终点重合,残余变形才逐渐减小到零。
- 1、下载文档前请自行甄别文档内容的完整性,平台不提供额外的编辑、内容补充、找答案等附加服务。
- 2、"仅部分预览"的文档,不可在线预览部分如存在完整性等问题,可反馈申请退款(可完整预览的文档不适用该条件!)。
- 3、如文档侵犯您的权益,请联系客服反馈,我们会尽快为您处理(人工客服工作时间:9:00-18:30)。
1. 车、铣、钻、镗类机床
图 车床的热变形
主轴箱中的齿轮、 轴承摩擦发热、 润滑油发热。
4
2.龙门刨床、牛头刨床、立式车床类机床
导轨副的摩擦热
3.各 种 磨 床
砂轮主轴轴 承的发热和液压 系统的发热
1-床身 2-导轨 3-工件 4-砂轮 5-砂轮架 6-螺母
向位移时,工件会产生弯曲变形,严重影响加工精度。此 时宜采用弹性尾顶尖。
6
2. 工件不均匀受热 在刨削、铣削、磨削加工平面时,工件单面受热,上下平
面间产生温差,导致工件 向上凸起,凸起部分被工具切去,加 工完毕冷却后,加工表面就 产生了中凹,造成了几何形状误差。
薄板磨削时的弯曲变形
7
(四)刀具热变形对加工精度的影响
采用隔热罩减少热变形 10
2.均衡温度场
1)减小温差; 2)均衡关键 件的温升,避 免弯曲变形 (如图所示 )
用热空气均衡立柱前后壁的温度场
11
3.改进机床布 局和结构设计
1) 采用热对称 结构 2) 合理选择机 床零部件的安 装基准
车床上主轴箱两种结构的热位移
图中表示了车床主轴箱在床身上的两种不同定位方式。由于主轴部件是车床 主轴箱的主要热源,故在图b中,主轴轴心线相对于装配基准H而言,主要在 Z方向产生热位移,对加工精度影响较小。而在图a中,方向Y的受热变形直 接影响刀具与工件的法向相对位置,故造成的加工误差较大。
刀具热变形主要是由 切削热 引起的。切削加 工时虽然大部分切削热被切屑带走,传入刀具的 热量并不多,但由于刀具体积小,热容量小,导 致刀具切削部分的温升急剧升高,刀具热变形对 加工精度的影响比较显著。
8
图示为车削时车刀的热变 形与切削时间的关系曲线。 曲线A —— 车刀连续工作 时的热伸长曲线; 曲线B —— 切削停止后, 车刀温度下降曲线; 曲线C —— 传动作间断切 削的热变形切削。
第十六章 机械加工精度和表面质量
第二节 影响加工精度的因素
1
五、工艺系统热变形引起的加工误差
(一)概 述
工艺系统在各种热源作用下,会产生相应的热变形, 从而破坏工件与刀具间正确的相对位置,造成加工误差。
1. 工艺系统的热源
热源
内部热源 外部热源
切削热 摩擦热
?工件、刀具、切屑、切削液 ?电机、轴承、齿轮、油泵等
16
2、冷校直引起的残余应力
现象
冷校直工艺方法是在一些长棒 料或细长零件弯曲的反方向施加外 力F以达到校直目的,如图a所示。
ቤተ መጻሕፍቲ ባይዱ
原因
在外力F的作用下,工件内部的 应力重新分布,如图b所示,在轴
冷校直引起的内应力
心线以上的部分产生压应力(用负号表示),在轴心线以下的
部分产生拉应力(用正号表示)。在轴心线和两条虚线之间,
稳定。
机床在开始工作的一段时间内,其温度场处于 不稳定状 态,其精度也是很不稳定的,工作一定时间后,温度才逐渐 趋于稳定,其精度也比较稳定。
因此,精密加工应在热平衡状态下进行。
3
(二)机床热变形对加工精度的影响
机床热变形会使机床的静态几何精度发生变化而影 响加工精度,其中主轴部件、床身、导轨、立柱、工作台 等部件的热变形,对加工精度影响最大。
车外圆时,车刀热变 形会使工件产生圆柱度误 差(喇叭口)。
车刀热变形曲线
τ 1 — 刀具加热至热平衡时间 τ 2 —刀具冷却至热平衡时间 τ 0 —刀具间断切削至热平衡时间
9
(五)减少工艺系统热变形的主要途径
1.减少发热和隔离热源 分离热源、采用隔热
措施,改善摩擦条件,减 少热量产生,如图所示。 有时可采用强制冷却法, 吸收热源热量,控制机床 温升和热变形。合理安排 工艺、粗精分开。
14
残余应力对零件的影响影响
?存在残余应力的零件,始终处于一种不稳定状态, 其内部组织有要恢复到一种新的稳定的没有内应 力状态的倾向。
?在内应力变化的过程中,零件产生相应的变形, 原有的加工精度受到破坏。
?用这些零件装配成机器,在机器使用中也会逐渐 产生变形,从而影响整台机器的质量。
15
1、毛坯制造中产生的残余应力
是弹性变形区域,在虚线以外是塑性变形区域。
?在铸造、锻造、焊接及热处理过程中,由于工件各部分
冷却收缩不均匀以及金相组织转变时的体积变化,在毛坯 内部就会产生残余应力。
?毛坯的结构越复杂,各部分壁厚越不均匀以及散热条件
相差越大,毛坯内部产生的残余应力就越大。
?具有残余应力的毛坯,其内部应力暂时处于相对平衡状
态,虽在短期内看不出有什么变化,但当加工时切去某些 表面部分后,这种平衡就被打破,内应力重新分布,并建 立一种新的平衡状态,工件明显地出现变形。
13
六、 工件残余应力引起的加工误差
什么是残 余 应 力
?残余应力是指在没有外部
载荷的情况下,存在于工件 内部的应力,又称内应力。
(一)内应力的产生及其对加工精度的影响
产生原 因
残余应力是由金属内部的相 邻宏观或微观组织发生了不 均匀的体积变化而产生的, 促使这种变化的因素主要来 自热加工或冷加工。
12
4.保持工艺系统的热平衡 加工前使机床高速空转,达到热平衡时再切削加工。
5.控制环境温度 恒温车间、使用门帘、取暖装置均匀布置;恒温精度一 般控制在±1℃以内,精密级较高的机床为±0.5℃。恒 温室平均温度一般为20℃,在夏季取23℃,在冬季可取 17℃。
6. 热位移补偿 寻求各部件热变形的规律建立热变形位移数字模型并 存入计算机中进行实时补偿。
牛头刨床滑枕热变形
外园磨床的热变形示意图
5
(三)工件热变形对加工精度的影响
1. 工件均匀受热
对于一些形状简单、对称的零件,如轴、套筒等,加 工时(如车削、磨削)切削热能较均匀地传入工件。 ? 在精密丝杆加工中,工件的热伸长会产生螺距的累积误差。
? 在较长的轴类零件加工中,将出现锥度误差。 如工件在两顶尖间车削,工件受热伸长而顶尖不能轴
环境温度 热辐射
?气温、室温变化、热、冷风等 ?日光、照明、暖气、体温等
2
2. 工艺系统的热平衡
工艺系统受各种热源的影响,其温度会逐渐升高。同时,它们 也通过各种传热方式向周围散发热量。
热平衡
必须注意 :
? 当单位时间内传入和散发的热量相等时,
工艺系统达到了热平衡状态。
? 而工艺系统的热变形也就达到某种程度的