影响加工精度的因素及其分析
机械加工精度的影响因素分析

机械加工精度的影响因素分析
一、概述
机械加工是现代工业中不可或缺的一环,其加工精度对产品质量和生产效率至关重要。
本文将对机械加工精度的影响因素进行详细分析。
二、加工机床的精度
加工机床是机械加工的关键设备,其精度是影响加工精度的首要因素。
加工机床的精度包括机床的基础平整度、导轨精度、直线度、角度等方面。
同时,加工机床的质量和结构也会影响加工精度。
三、切削刀具的精度
切削刀具是机械加工中使用较为广泛的切削工具,其使用寿命和切削效率直接影响加工精度。
切削刀具的精度包括直径误差、轴线偏差、齿面质量等。
四、工件材料和表面状态
工件材料和表面状态对机械加工精度也有重要影响。
不同材料的硬度、强度、切削性能等会直接影响加工难度和加工精度。
而表面状态也会导致加工后的精度差异,如表面粗糙度、表面硬度等。
五、加工工艺参数的选择
在机械加工过程中,加工工艺参数的选择也是影响加工精度的因素之一。
加工工艺参数包括切削速度、进给量、切削深度等。
不同的工艺参数会直接影响切削力和加工精度。
六、工作环境的影响
工作环境也会对机械加工精度产生影响,如温度、湿度等因素都会对加工精度造成一定的影响。
七、总结
综上所述,机械加工精度的影响因素是多方面的,包括加工机床的精度、切削刀具的精度、工件材料和表面状态、加工工艺参数的选择以及工作环境的影响等。
对于工业生产来说,保证机械加工精度是提高产品质量和生产效率的基础。
机械加工精度的影响因素及提高措施

机械加工精度的影响因素及提高措施机械加工精度是指在机械加工过程中所能达到的尺寸精度、形位精度和表面精度,它主要受到以下几个因素的影响:1. 加工设备的精度:加工设备的精度是机械加工精度的基础。
设备的精度主要包括切削力、回转精度、传动精度等方面。
高精度的加工设备能够减小加工误差,提高机械加工精度。
2. 材料的性质:材料的硬度、韧性和变形性等特性对机械加工精度有影响。
硬度高的材料会增加切削力,导致加工误差增大;韧性差的材料容易产生毛刺和划痕,影响表面精度;变形性差的材料会导致尺寸误差增大。
3. 刀具的选择和使用:刀具的质量和使用方式直接影响加工精度。
选择适合材料和工件的刀具,保持刀具的锋利度和稳定性,合理使用刀具,可以提高机械加工精度。
4. 加工参数的控制:加工参数的选择和控制直接影响加工精度。
切削速度、进给速度和切削深度等参数的选取要根据材料的性质和加工要求进行合理调整,过大或过小都会导致加工精度降低。
5. 加工过程的热变形:在机械加工过程中,切削热会引起工件和刀具的热变形,从而影响加工精度。
为了避免热变形,可以采取降低切削速度、加工液冷却、减小切削力等措施。
为了提高机械加工精度,可以采取以下措施:1. 选择优质的加工设备:优质的加工设备具有高精度、高刚度和高稳定性,能够保证加工精度。
2. 提高刀具的质量:选择高品质的刀具,保持刀具的锋利度和稳定性,及时更换磨损的刀具。
4. 采取适当的加工工艺:选择合适的工艺路线、夹具和刀具等加工工艺,减小加工过程中的变形和振动。
5. 加强员工培训:提高操作人员的技术水平和加工意识,提高人工操作的准确性和稳定性。
机械加工精度的影响因素很多,要提高机械加工精度,需要综合考虑各种因素并采取相应的措施,以保证加工精度的稳定性和可靠性。
数控车床加工精度的影响因素及对策探讨
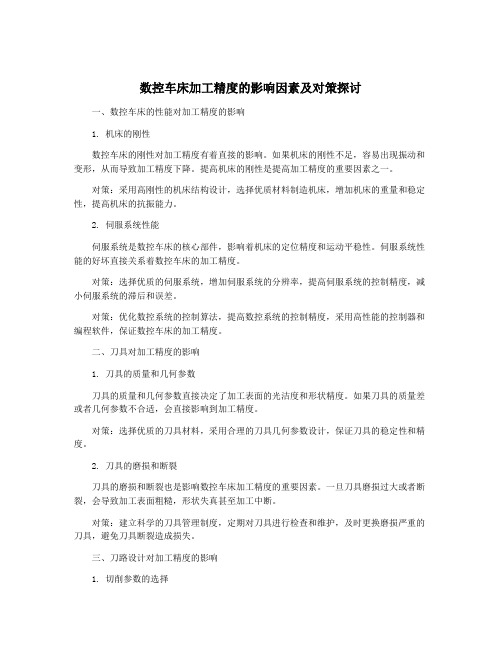
数控车床加工精度的影响因素及对策探讨一、数控车床的性能对加工精度的影响1. 机床的刚性数控车床的刚性对加工精度有着直接的影响。
如果机床的刚性不足,容易出现振动和变形,从而导致加工精度下降。
提高机床的刚性是提高加工精度的重要因素之一。
对策:采用高刚性的机床结构设计,选择优质材料制造机床,增加机床的重量和稳定性,提高机床的抗振能力。
2. 伺服系统性能伺服系统是数控车床的核心部件,影响着机床的定位精度和运动平稳性。
伺服系统性能的好坏直接关系着数控车床的加工精度。
对策:选择优质的伺服系统,增加伺服系统的分辨率,提高伺服系统的控制精度,减小伺服系统的滞后和误差。
对策:优化数控系统的控制算法,提高数控系统的控制精度,采用高性能的控制器和编程软件,保证数控车床的加工精度。
二、刀具对加工精度的影响1. 刀具的质量和几何参数刀具的质量和几何参数直接决定了加工表面的光洁度和形状精度。
如果刀具的质量差或者几何参数不合适,会直接影响到加工精度。
对策:选择优质的刀具材料,采用合理的刀具几何参数设计,保证刀具的稳定性和精度。
2. 刀具的磨损和断裂刀具的磨损和断裂也是影响数控车床加工精度的重要因素。
一旦刀具磨损过大或者断裂,会导致加工表面粗糙,形状失真甚至加工中断。
对策:建立科学的刀具管理制度,定期对刀具进行检查和维护,及时更换磨损严重的刀具,避免刀具断裂造成损失。
三、刀路设计对加工精度的影响1. 切削参数的选择切削参数的选择直接关系着加工表面的精度和光洁度。
如果切削参数选择不当,容易造成加工表面粗糙、振动和变形,从而影响加工精度。
对策:根据工件材料、加工情况和刀具性能选择合适的切削参数,保证切削过程的稳定性和加工精度。
2. 刀具路径设计刀具路径设计直接影响着加工表面的形状精度和轮廓精度。
如果刀具路径设计不合理,容易出现残余槽痕、振动和留痕等问题,影响加工精度。
对策:优化刀具路径设计,采用高效的刀具路径生成软件,减小刀具路径长度和交叉次数,减少振动和残余槽痕,保证加工精度。
12影响加工精度的因素解析

12影响加工精度的因素解析加工精度是指在加工过程中,所得到的工件尺寸与设计要求之间的偏差程度。
影响加工精度的因素众多,主要包括机床精度、刀具质量、工件材料及加工方法等。
下面对这些因素进行详细分析。
第一、机床精度:机床精度是指机床本身的加工能力和稳定性。
包括机床的定位精度、运动精度、重复定位精度等方面。
定位精度:机床刀具在加工坐标轴上进行定位时的精度。
定位精度越高,机床的加工精度越高。
运动精度:机床刀具在进行运动时的精度。
运动精度包括刀具的速度、加速度保持平稳、方向精确等。
如果机床运动过程中存在震动或者晃动,会导致工件尺寸的变化,从而影响加工精度。
重复定位精度:机床进行多次定位时,每次定位的精度是否相同。
重复定位精度越高,加工精度越稳定。
第二、刀具质量:刀具是实现工件形状的关键工具。
刀具质量直接决定了加工精度。
刀具材料:刀具材料的硬度、耐磨性等性能会直接影响切削力的大小和稳定性。
如果刀具磨损严重,切削力难以控制,就会影响工件尺寸的精度。
刀具几何形状:刀具的几何形状包括刀尖半径、刀片角度、刀片刃口和刃后角等。
这些参数的选择会直接影响加工表面的光洁度和精度。
第三、工件材料:工件材料的硬度、韧性、热膨胀系数等参数都会对加工精度造成影响。
硬度:工件材料的硬度越大,加工难度越大,加工精度也会受到影响。
高硬度的材料容易导致刀具磨损,从而影响加工精度。
热膨胀系数:工件材料的热膨胀系数越大,加工过程中材料的膨胀和收缩也就越大,容易引起工件变形,从而导致尺寸精度降低。
第四、加工方法:加工方法对加工精度有直接的影响。
切削速度:过高或过低的切削速度都会影响切削力和刀具磨损,从而影响加工精度。
进给速度:过大的进给速度会导致切削力过大,造成加工表面的毛刺和震动。
过小的进给速度则会延长加工时间,增加刀具磨损。
冷却液使用:适当的冷却液可以降低加工过程中的温度,减小热变形的影响,保持加工精度的稳定性。
总结起来,加工精度受到多个因素的影响,包括机床精度、刀具质量、工件材料和加工方法等。
影响数控机床加工精度的相关因素及改善对策

影响数控机床加工精度的相关因素及改善对策
一、影响数控机床加工精度的相关因素
1.数控机床的性能和精度:数控机床的性能和精度是影响加工精度的重要因素。
数控
机床的刚性、动态特性、稳定性、热稳定性等性能直接影响其加工精度。
3.刀具和刀具系统:刀具和刀具系统的质量、刚性、精度和稳定性直接关系到数控机
床的加工精度。
刀具的选择、安装和使用对加工精度有着重要影响。
4.工件材料和切削参数:工件材料的硬度、韧性、热处理状态等特性将直接影响数控
机床的加工精度。
切削参数的选择和调整也对加工精度有着重要影响。
5.加工环境和工艺:加工环境的温度、湿度和工艺的合理性都会对数控机床的加工精
度产生影响。
加工环境的稳定和清洁度对数控机床的加工精度有着重要影响。
6.操作人员的技术水平:操作人员的技术水平和对数控机床的熟悉程度直接影响其加
工精度。
操作人员需要具备良好的操作技能和对数控机床的维护保养知识,从而保证数控
机床的加工精度。
2.提高数控系统的性能:使用高性能的数控系统,提高控制精度、反馈精度和稳定性,从而提高数控机床的加工精度。
5.改善加工环境和工艺:保证加工环境的稳定和清洁度,优化工艺流程,从而提高数
控机床的加工精度。
通过对数控机床加工精度的影响因素和改善对策的分析,可以更好地理解和把握数控
机床加工精度的提高方法,为实际生产中的加工提供更好的技术支持。
通过加强对数控机
床加工精度的改善对策的实施,可以提高数控机床的加工精度,从而提高产品质量,降低
加工成本,提高生产效率,为企业的发展提供更好的技术支持。
影响加工精度的因素及控制措施
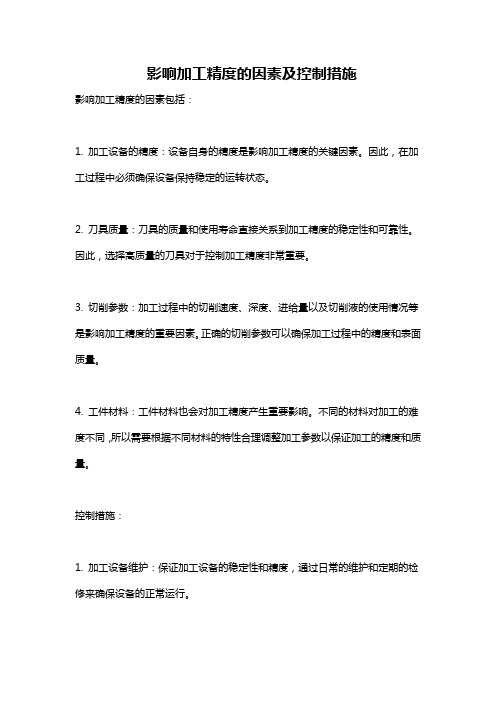
影响加工精度的因素及控制措施
影响加工精度的因素包括:
1. 加工设备的精度:设备自身的精度是影响加工精度的关键因素。
因此,在加工过程中必须确保设备保持稳定的运转状态。
2. 刀具质量:刀具的质量和使用寿命直接关系到加工精度的稳定性和可靠性。
因此,选择高质量的刀具对于控制加工精度非常重要。
3. 切削参数:加工过程中的切削速度、深度、进给量以及切削液的使用情况等是影响加工精度的重要因素。
正确的切削参数可以确保加工过程中的精度和表面质量。
4. 工件材料:工件材料也会对加工精度产生重要影响。
不同的材料对加工的难度不同,所以需要根据不同材料的特性合理调整加工参数以保证加工的精度和质量。
控制措施:
1. 加工设备维护:保证加工设备的稳定性和精度,通过日常的维护和定期的检修来确保设备的正常运行。
2. 刀具选择:选择质量稳定、寿命长、精度高的刀具,这不仅可以提高加工效率,也可以保证加工质量稳定。
3. 切削参数控制:合理设置切削速度、深度、进给量以及切削液的使用情况,确保加工质量和表面质量。
4. 工件材料选择:根据工件材料的特性确定加工参数,以确保加工的质量和精度。
数控机床加工精度的影响因素及提高方法
数控机床加工精度的影响因素及提高方法数控机床加工精度是指机床在进行加工过程中所能达到的准确度和稳定性。
影响机床加工精度的因素非常多,下面将对影响因素和提高方法进行一些阐述。
1. 机床自身的优劣:机床的设计、制造和装配技术对加工精度有直接影响。
优质的机床在设计和制造过程中会注重减小传动误差、提高定位精度和重复定位精度等。
2. 机床的刚性和稳定性:机床的刚性和稳定性对加工精度起着决定性的作用。
刚性不足会导致机床在加工过程中出现振动和变形,从而影响加工精度。
3. 传动装置的精度和可靠性:传动装置的传动误差、反向间隙等都会影响加工精度。
传动装置的精度和可靠性越高,加工精度也越高。
4. 控制系统的精度:数控机床的控制系统对加工精度有直接影响。
控制系统的精度主要包括伺服系统的控制精度、编码器的精度以及数控系统的实时性等。
5. 刀具和夹具的精度:刀具和夹具的精度直接影响加工质量。
刀具和夹具的选择和安装都需要考虑其精度和稳定性。
1. 选用优质的机床:选择优质的机床是提高加工精度的基础。
优质的机床具有高精度、高刚性和高稳定性,能够更好地满足加工要求。
2. 优化加工工艺:通过优化加工工艺,合理设置切削参数和进给速度等,可以减小加工误差,提高加工精度。
4. 优化编程和加工过程:合理优化数控程序和加工过程,减小加工误差。
尽量避免急停和急转等情况,保证加工过程的平稳性和稳定性。
5. 定期进行机床维护和保养:定期进行机床的维护和保养,保证机床的正常运行和精度稳定性。
包括清洁、润滑和紧固等工作。
数控机床加工精度的提高需要从机床自身的优劣、刚性和稳定性、传动装置的精度和可靠性、控制系统的精度以及刀具和夹具的精度等方面进行综合考虑。
通过优化加工工艺、合理选择刀具和夹具、加强编程和加工过程的管理以及定期进行机床维护和保养等措施,可以有效提高数控机床的加工精度。
机械加工精度的影响因素及提高措施
机械加工精度的影响因素及提高措施
机械加工精度是指机械零件的尺寸、形状和位置精度的指标,它直接影响产品的质量
和性能,因此提高机械加工精度是制造业不断追求的目标。
机械加工精度的影响因素很多,主要有以下几点:
1.材料的影响:材料的硬度、韧性、强度、刚度等特性会影响机械加工过程中的切削力、振动、热变形等,直接影响零件加工精度。
2.机床的影响:机床的刚性、定位精度、稳定性等对加工精度产生重要影响。
机床刚
性好、精度高、稳定性好,可保证加工的精度。
3.加工刀具的影响:加工刀具的硬度、韧性、刃磨精度、刀尖圆弧半径等对加工过程
与加工质量产生直接影响,因此需要选用优质的刀具并保证刃磨质量。
4.加工条件的影响:包括切削速度、切削深度、进给速度等,这些加工条件的选择要
满足零件的加工需求,既要保证加工效率,又要保证加工质量。
那么如何提高机械加工精度呢?以下是一些方法:
1.提高机床的刚性和精度:使用优质的机床和检测设备,加强机床的维护保养,可提
高机床的刚性和精度,提高加工精度。
2.采用高精度的加工刀具:选用高精度的加工刀具,保证其质量和磨削精度,可提高
加工质量和精度。
4.精度检测和纠正:需要对零件进行精度检测和纠正,能够及时发现问题并解决,保
证零件加工精度。
综上所述,机械加工精度的影响因素很多,但采取合适的方法和措施,可以提高加工
精度,保证零件质量和性能。
影响机械加工精度的几个重要因素
(二)工艺系统刚度对加工精度的影响
1.加工过程中由于工艺系统刚度发生
变化引起的误差 图
x
y系 y刀架 yx y刀架 y主轴 y尾座 y主轴 l
lx
F主轴 Fp xl
F尾座 Fp
y系 y刀架 y 例
l
x
Fp
1 k刀 架
1 k主 轴
l
l
x
2
1 k尾
座
x l
2
2.由于切削力变化引起的误差 加工过程中,由于毛坯加工余量和工件 材质不均等因素,会引起切削力变化,使工 艺系统变形发生变化。从而产生加工误差。 误差复映现象: 图 车削一具有锥形误 差的毛坯,加工表面上必然有锥形误差;待 加工表面上有什么样的误差,加工表面上必 然也有同样性质的误差,这就是切削加工中 的误差复映现象。
例如:用三爪自定心卡盘装夹薄壁套简 镗孔时,夹紧前薄壁套筒的内外圆是圆的, 夹紧后工件呈三棱圆形;镗孔后,内孔呈圆 形;但松开三爪卡盘后,外圆弹性恢复为圆 形,所加工孔变成为三棱圆形,使镗孔孔径 产生加工误差。为减少由此引起的加工误差, 可在薄壁套筒外面套上一个开口薄壁过渡环, 使夹紧力沿工件圆周均匀分布。
通常都是通过机床完成的。工件的加工精度 在很大程度上取决于机床的精度。
机床制造误差中对工件加工精度影响较 大的误差有:主轴回转误差、导轨误差和传 动误差。
1.主轴回转误差
机床主轴是用来装夹工件或刀具,并将 运动和动力传给工件或刀具的重要零件,主 轴回转误差将直接影响被加工工件的形状精 度和位置精度。
3)第一次卸载后,刀架恢复不到第一 次加载的起点,这说明有残余变形存在,经 多次加载和卸载后,加载曲线起点才和卸载 曲线终点重合,残余变形才逐渐减小到零。
数控机床加工精度的影响因素及提高方法
数控机床加工精度的影响因素及提高方法数控机床在生产加工中,对于加工精度的要求非常高,因为加工精度直接关系到产品的质量和使用寿命。
因此,提高数控机床的加工精度是非常重要的。
1.机床结构和精度:数控机床的机床结构和精度是影响加工精度的关键因素。
机床结构的优劣直接决定了加工精度的上限,机床的精度则是决定加工精度的主要因素之一。
2.加工工件材料:不同材料对机床加工精度的影响程度不同。
硬度大,弹性模量小的工件会影响机床的振动和变形。
而硬度小、弹性模量大的工件对机床加工精度的影响就小。
3.切削工具:刀具的质量、刃口的状况、刀具的刃磨加工等,都会对数控机床的加工精度产生影响。
4.加工工艺:加工工艺的好坏也会直接影响加工精度。
包括加工速度、进给量、深度和切削液等各工艺参数的选取和控制情况。
1.加强机床结构的刚性和稳定性:提高机床自身的刚性和稳定性,能够有效地避免振动和变形现象,从而提高加工精度。
2.选用高精度的切削工具:刀具的质量对加工精度的影响很大。
选用质量好的高精度刀具能够更好地保证加工精度。
3.优化加工工艺:制定合理的加工工艺流程和工艺参数,可以有效降低加工误差。
4.强化加工质量控制:通过完善的检测手段和方法,改善和控制加工质量的各个环节,从根本上提高加工精度。
5.提高利用率和维护保养:维护机床的良好状态,保持设备稳定运行,能够避免由于机床运行不平稳等情况导致的加工精度下降,提高机床的利用率和寿命。
总之,在数控机床的加工过程中,加工精度是至关重要的。
应注意从机床结构、切削工具、加工工艺以及加工质量控制等各方面加强管理和提高水平,才能够更好地满足产业的需求。
- 1、下载文档前请自行甄别文档内容的完整性,平台不提供额外的编辑、内容补充、找答案等附加服务。
- 2、"仅部分预览"的文档,不可在线预览部分如存在完整性等问题,可反馈申请退款(可完整预览的文档不适用该条件!)。
- 3、如文档侵犯您的权益,请联系客服反馈,我们会尽快为您处理(人工客服工作时间:9:00-18:30)。
主轴的回转运动误差表现为端面圆跳动、径向圆跳动、角度摆动三种基本形式。 1)端面圆跳动。主轴实际回转轴线沿平均回转轴线的方向作纯轴向蹿动,它对内、 外圆柱面车削影响不大。主要是在车端面时它使工件端面产生垂直度、平面度误差 和轴向尺寸精度误差,在车螺纹时它使螺距产生误差。 2)径向圆跳动。主轴实际回转轴线 相对于平均回转轴线在径向的变动 量,车削外圆时它影响被加工工件 圆柱面的圆度和圆柱度误差。
之间的位置,从而引起了工件的种种误差,称为工艺系统的动误差。还包括内应力
引起的变形。
(4)测量——测量方法和量具本身的误差,测量误差; (5)原理误差——某些表面的加工中,从加工面的形成原理中就存在着误差,称
之为原理误差。
.
综上所述,加工过程中可能出现的种种原始误差如下图所示:
与工艺系统原始状 态有关的原始误差 (几何误差)
(2)成形车刀、成形铣刀也采用了近似的刀具轮廓。
(3)采用近似的成形运动和刀具刃形,不但可以简化机床或刀具的结 构,而且能提高生产效率和加工的经济效益。
.
(二)机床误差 来源:机床制造,磨损和安装。 机床在出厂以前都要通过机床精度检验,检验内容是机床主要零部件本身
的形状和位置误差,要求它们不超过规定的数值。 以车床为例,主要项目有: ➢ 床身导轨在垂直面和水平面内的直线度和平行度 ➢ 主轴轴线对床身导轨的平行度 ➢ 主轴的回转精度 ➢ 传动链精度 ➢ 刀架各溜板移动时,对主轴轴线的平行度和垂直度 以上各项检验是在没有切削载荷的情况下进行的,所反映的各项误差称之
下面着重分析机床静误差中对加工精度占举足轻重地位的导轨误差、主轴 误差和传动链误差。 (1)导轨误差
机床导轨副是机床中确定各主要部件位置关系的基准,是实现直线运动的 主要部件,其制造和装配精度是影响直线运动的主要因素,直接影响工件的加 工精度。
如,车床床身导轨在水平面内有了弯曲之后,在纵向切削过程中就可能产 生鞍形或鼓形加工误差。
(一)原理误差 指由于采用了近似的加工方法,即近似的成形运动或近似的刀具轮
廓而产生的误差。 (1)例如滚齿用的齿轮滚刀,就有两种误差,一是为了制造方便,采 用阿基米德蜗杆代替渐开线基本蜗杆而产生的刀刃齿廓近似造形误差; 二是由于滚刀切削刃数有限,切削是不连续的,因而滚切出的齿轮齿形 不是光滑的渐开线,而是折线。
机床导轨的几何精度,不但取决于它的制造精度和使用的磨损情况,而且还和机 床的安装情况有很大关系,安装这项工. 作被称为“安装水平的调整”。
(2)主轴误差 机床主轴使工件或刀具的位置基准和运动基准,它的误差直接影响着工件的加
工精度。 对主轴的要求就是在运转的情况下,它能保持轴心线的位置稳定不变,也就是
研究原始误差的目的——研究零件的机械加工精度,就是研究工艺系统原 始误差的物理、力学本质,掌握其基本规律,分析原始误差和加工误差之间的 定性与定量关系,这是保证和提高零件加工精度的必要理论基础。
以某工厂活塞精镗销孔工序为例,在加工时以止口定位,顶部夹紧,通过 分析可能影响工件和刀具间相互位置的种种因素,对工艺系统的原始误差做一 个全面的了解。
原始 误差
与工艺过程有关的 原始误差(动误差)
原理误差
调整误差 装夹误差
工件相对于刀具静止状态下 的误差
刀具误差
夹具误差 机床误差
主轴回转误差 工件相对于
导轨导向误差 刀具运动状
传动误差
态下的误差
工艺系统受力变形(包括夹紧变形)
工艺系统受热变形
刀具磨损
测量误差
工件残余应力引起的变形
Байду номын сангаас
.
5.2.2 各种误差因素分析
为机床的静误差,包括了机床的几何误差和传动链误差。
.
评价一台机床精度的高低不能只看它在静态下的情况,还应应注意要看它 在切削载荷下的动态情况。机床静态精度是其动态精度的基础。
此外,合格的机床经过一段较长时期的使用后,由于不可避免的磨损、地 基变动和其他原因,原有精度会有不同程度的降低,并可能产生相关精度问题, 此时就需对机床进行某些项目的测量和分析。
所谓的回转精度。主轴的回转精度与制造精度(包括加工和装配精度)、受力后的 变形、随速度增加相关的散热问题等因素有关。
主轴的回转运动误差,是指主轴的实际回转轴线对其理想回转轴线的变动量。 变动量越大,回转精度越低;变动量越小,回转精度越高。
实际上,主轴的理想回转轴线虽然客观存在,但很难确定其位置,所以通常用 平均回转轴线(即主轴各瞬时回转轴线的平均位置)来代替它。
O
a)
Y
X ΔR
O
X
b)
Y
ΔR =ΔX
普通车床车削外圆
ΔY
分析导轨导向误差对加工精度的影响时,主要考虑刀具与工件在误差敏 感方向上的相对位移。 车床和磨床的床身导轨误差(根据部颁检验标准)共有三个项目:: 1)导轨在水平面内的直线度误差1。 2)导轨在垂直面内的直线度误差 2。 3)前后导轨的平行度误差(扭曲度) 3。
.
导轨在水平面与垂直面内的弯曲 (误差)
对加工精度的影响的比较:
RY
Y 2 2 R0
RX X
显然:
RX RY
说明:在垂直面内导轨的弯曲对加工精 度的影响很小,可以忽略不计;而在水平面 内同样大小的导轨弯曲就不能忽略。
总结:工艺系统原始误差方向不同,对 加工精度的影响程度也不同。对加工精度影 响最大的方向,称为误差敏感方向,一般为 已加工表面过切削点的法线方向。 .
§5.2 影响加工精度的因素及其分析
本节内容: ➢ 工艺系统及原始误差的组成 ➢ 各种误差因素分析 ➢ 保证和提高加工精度的途径
.
5.2.1 工艺系统及原始误差的组成
(1)工艺系统 机床、夹具、刀具和工件构成的完整系统。 (2)原始误差 工艺系统中的种种误差,在不同的具体条件下,以不同的程度 复映到工件上,形成了工件的加工误差。工艺系统的误差是“因”,是根源; 加工误差是“果”,是表现,因此把工艺系统的误差称为原始误差。
.
(1)装夹——产生工件装夹误 差(设计基准与定位基准不重合 引起的定位误差和夹紧误差);
(2)调整——调整误差和工艺 系统的静误差(机床、刀具、夹 具的制造误差);
(3)加工——由于在加工过程中产生了切削力、切削热、摩擦等因素,工艺系系统
就产生了受力变形、热变形、刀具磨损等原始误差,影响了已调整好的工件、刀具