连铸机的设计
1600mm不锈钢板坯连铸机结晶器设计

2 结构形 式及特 点
该 结 晶器 采 用 平 行 直 板 式 结 构 ,主要 生 产 厚
1 0mm 和 2 0m 规 格 的不 锈 钢 板 坯 。结 晶 器 铜 8 0 m
1 上弹簧 座 ;2 一 一活 塞杆 ;3 防尘环 ;4 ~ 一盖板 ;5 一上拉
杆 ;6 一锁紧螺母 ;7 一底垫 ;8 一球 面轴 承 ;9 一垫 圈;l一 O 上压盖 ;1一下拉杆 ;1一下 弹簧座 ;1一螺栓 ;1一下压 1 2 3 4
紧力夹紧窄边铜板 ,既保证有足够的夹紧力 ,又不
会 损 坏铜板 车 身 。夹紧装 置用 液压 装置 顶 开 ,顶 开 时活 动侧 水箱 沿着左 右 支承框 架 上 的左 右 滑动导 向
螺栓 向外 移 动 6 9m ~ m,在 宽 、窄边 铜 板 之 间形 成
必要 的调 宽和 维修 间隙 。
窄边部件 及足 辊 主要 由窄边本 体和 窄边 足辊 组 成 ,窄边本 体又 由支撑 板 、压板 和铜板 组成 。铜 板 的材 质与性 能 同宽边部 件 中的铜板 相 同 ,不 同 的
可采用 更换结 晶器 或在 线停机 调 宽 2 方法 。 种
是 为 防止调 锥度 时磨 损 窄边 ,在宽 向侧 面 上镀 N。 i 压板 为焊接 件结构 ,它与铜 板把合 在一起 ,当铜板 磨 损需 修磨 时 ,可 整 体 更换 ,当 与支 承 板 连接 上
盖 ,调节 螺母 和止挡 插 板等组 成 ( 图 2 。 见 )
固定侧 和 活动侧 冷却 水箱 用 4根拉 杆将 窄边 铜
板夹 紧 ( 图 3 。拉杆一端用螺母压在 内弧侧冷 见 ) 却水箱的外壁上 ,另一侧通过蝶形弹簧将外弧冷却 水箱压紧。由于蝶形弹簧力是预先设定的 , 以不 所 论在调宽或不调宽的浇注过程 中都能将窄边紧紧夹 住 。在调宽结束后 ,活塞杆后退 ,前后冷却水箱恢 复到蝶形弹簧所设定的夹紧力状态。 装 配 时首先 旋转 拉杆 使轴 与活 塞杆 相联 接 ,并 拉紧固定侧水箱和活动侧水箱 ,使 4 块铜板之间保 持 01 m间隙 ;先锁紧两连杆处的 4 .m 个锁紧螺母 和外侧 的 4 组锁紧螺母 ,然后用内侧 的 4 组螺母分 别 调节 4组 球 面轴承 的轴 向间隙并 锁紧 ( 保 持 必须
2300mm单流板坯连铸机设计特点及生产实践
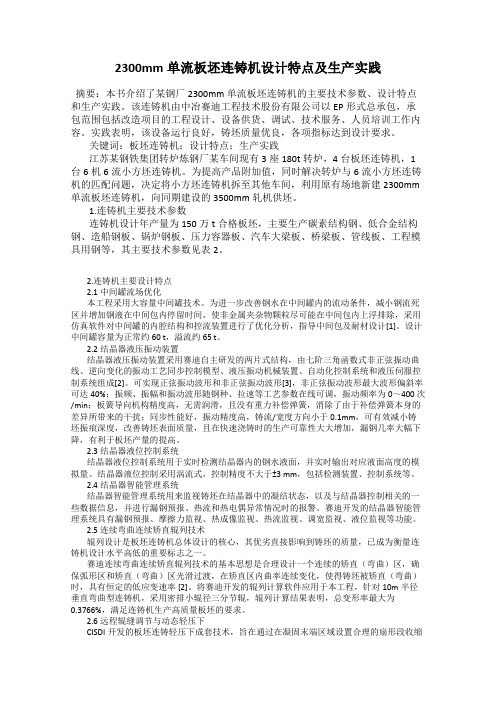
2300mm单流板坯连铸机设计特点及生产实践摘要:本书介绍了某钢厂2300mm单流板坯连铸机的主要技术参数、设计特点和生产实践。
该连铸机由中冶赛迪工程技术股份有限公司以EP形式总承包,承包范围包括改造项目的工程设计、设备供货、调试、技术服务、人员培训工作内容。
实践表明,该设备运行良好,铸坯质量优良,各项指标达到设计要求。
关键词:板坯连铸机;设计特点;生产实践江苏某钢铁集团转炉炼钢厂某车间现有3座180t转炉,4台板坯连铸机,1台6机6流小方坯连铸机。
为提高产品附加值,同时解决转炉与6流小方坯连铸机的匹配问题,决定将小方坯连铸机拆至其他车间,利用原有场地新建2300mm 单流板坯连铸机,向同期建设的3500mm轧机供坯。
1.连铸机主要技术参数连铸机设计年产量为150万t合格板坯,主要生产碳素结构钢、低合金结构钢、造船钢板、锅炉钢板、压力容器板、汽车大梁板、桥梁板、管线板、工程模具用钢等,其主要技术参数见表2。
2.连铸机主要设计特点2.1中间罐流场优化本工程采用大容量中间罐技术。
为进一步改善钢水在中间罐内的流动条件,减小钢流死区并增加钢液在中间包内停留时间,使非金属夹杂物颗粒尽可能在中间包内上浮排除,采用仿真软件对中间罐的内腔结构和控流装置进行了优化分析,指导中间包及耐材设计[1]。
设计中间罐容量为正常约60 t,溢流约65 t。
2.2结晶器液压振动装置结晶器液压振动装置采用赛迪自主研发的两片式结构,由七阶三角函数式非正弦振动曲线、逆向变化的振动工艺同步控制模型、液压振动机械装置、自动化控制系统和液压伺服控制系统组成[2]。
可实现正弦振动波形和非正弦振动波形[3],非正弦振动波形最大波形偏斜率可达40%;振频、振幅和振动波形随钢种、拉速等工艺参数在线可调,振动频率为0~400 次/min;板簧导向机构精度高,无需润滑,且没有重力补偿弹簧,消除了由于补偿弹簧本身的差异所带来的干扰;同步性能好,振动精度高,铸流/宽度方向小于0.1mm,可有效减小铸坯振痕深度,改善铸坯表面质量,且在快速浇铸时的生产可靠性大大增加,漏钢几率大幅下降,有利于板坯产量的提高。
224_板坯连铸机垛卸板机设计

1绪论1.1选题的背景和目的1.1.1选题的背景鞍钢第二炼钢厂现有职工 1855 人,下设 5 个生产车间和 4 个辅助车间。
厂区占地 面积17.8万平方米,建筑面积20.8万平方米。
设备总量3.6万吨,主要设备有:100公 称吨氧气顶吹转炉 3 座,R5.25 米弧型机六流高效连铸机两台,板坯连铸机 2 台,600 公称吨混铁炉2台,铁水预处理和炉外精练设备各1套。
钢年生产能力330万吨,方坯 年生产能力190万吨,板坯年生产能力180万吨。
正在建另一台板坯连铸机,预计2003 年5月投产,拟再建一座转炉,届时年钢产量将达450万吨。
主要产品规格:方坯120mm 2 、150mm 2 ;板坯 150mm×(850mm~1200mm);135mm×(900mm~1550mm);100mm×(900mm~1550mm);主要生产品种有:普通碳素结构钢、优质碳素结构钢、低合金钢、高合金钢、铝钢、军工钢等7个系列120多个品种。
1.1.2选题的目的本次设计的板坯连铸垛卸板机,为经连续铸钢后的板坯出坯后,用来堆垛钢板的一 台设备。
连铸垛卸板机为连铸机出坯系统中的一台专用设备。
它承载能力大,结构简单,占 地面积小,便于集中控制且检修周期长,在满足生产要求的同时,提高了成材率和劳动 生产率。
提高了连铸机的生产效率,缩短了劳动时间和工人的劳动强度。
1.2连铸在国内外的发展概况钢液经过连续铸钢机(简称连铸机)直接生产钢坯的方法叫连续铸钢,它生产出来 的钢坯叫连铸坯。
连续铸钢技术是在五十年代发展成功的。
从六十年代中期就在钢铁工业中迅速发 展。
七十年代以后,发展更为迅速,世界连铸比以3%的速度增长。
到1986年,世界钢 的连铸比已达 52%。
在几个主要产钢国家中,连铸比增长更快,日本连铸比 1979 年为 52%,1986年为92%;美国1979年为16.7%,1986年为53.6%,西欧一些国家连铸比已 达100%。
连铸机主要设计参数的确定
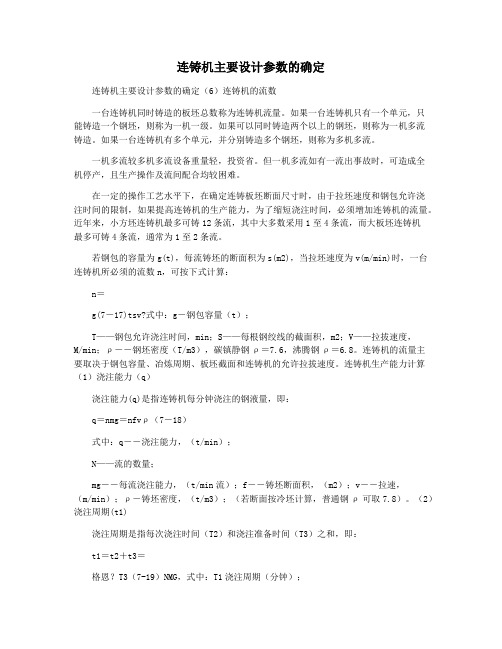
连铸机主要设计参数的确定连铸机主要设计参数的确定(6)连铸机的流数一台连铸机同时铸造的板坯总数称为连铸机流量。
如果一台连铸机只有一个单元,只能铸造一个钢坯,则称为一机一级。
如果可以同时铸造两个以上的钢坯,则称为一机多流铸造。
如果一台连铸机有多个单元,并分别铸造多个钢坯,则称为多机多流。
一机多流较多机多流设备重量轻,投资省。
但一机多流如有一流出事故时,可造成全机停产,且生产操作及流间配合均较困难。
在一定的操作工艺水平下,在确定连铸板坯断面尺寸时,由于拉坯速度和钢包允许浇注时间的限制,如果提高连铸机的生产能力,为了缩短浇注时间,必须增加连铸机的流量。
近年来,小方坯连铸机最多可铸12条流,其中大多数采用1至4条流,而大板坯连铸机最多可铸4条流,通常为1至2条流。
若钢包的容量为g(t),每流铸坯的断面积为s(m2),当拉坯速度为v(m/min)时,一台连铸机所必须的流数n,可按下式计算:n=g(7-17)tsv?式中:g―钢包容量(t);T——钢包允许浇注时间,min;S——每根钢绞线的截面积,m2;V——拉拔速度,M/min;ρ――钢坯密度(T/m3),碳镇静钢ρ=7.6,沸腾钢ρ=6.8。
连铸机的流量主要取决于钢包容量、冶炼周期、板坯截面和连铸机的允许拉拔速度。
连铸机生产能力计算(1)浇注能力(q)浇注能力(q)是指连铸机每分钟浇注的钢液量,即:q=nmg=nfvρ(7-18)式中:q――浇注能力,(t/min);N——流的数量;mg――每流浇注能力,(t/min流);f――铸坯断面积,(m2);v――拉速,(m/min);ρ―铸坯密度,(t/m3);(若断面按冷坯计算,普通钢ρ可取7.8)。
(2)浇注周期(t1)浇注周期是指每次浇注时间(T2)和浇注准备时间(T3)之和,即:t1=t2+t3=格恩?T3(7-19)NMG,式中:T1浇注周期(分钟);t2―浇注时间(从中间包开浇至中间包最后一流浇完为止的总时间,(min);T3——准备时间(从中间包浇注到下一个熔炉的假封头填充和浇注准备的总时间)间),(min);g――钢包钢液量,(t);N——每次连铸炉的平均数量。
永锋钢铁8流小方坯连铸机设计特点

永锋钢铁8流小方坯连铸机设计特点摘要:介绍永锋钢铁8流小方坯连铸机设计特点,该连铸机具有流数多、生产品种丰富、配置先进、自动化控制程度高的特点。
关键词:小方坯连铸机;设计特点;8流前言为了贯彻我国钢铁发展产业政策,淘汰落后产能,节能减排,优化生产结构,大力发展循环经济,山东莱钢永锋钢铁有限公司在不扩大产能的情况下进行技术升级改造,新建一台8机8流、铸坯断面为150mm×150mm(预留180mm×180mm)的小方坯连铸机,有利于进一步提高综合经济效益。
1生产规模及产品生产规模:年产合格方坯158万吨;铸坯断面:150mm×150mm,预留180mm×180mm;浇铸钢种:碳素结构钢、优质碳素结构钢、合金结构钢、冷镦钢、焊条钢、弹簧钢、轴承钢、非调质钢、标准件用钢等;代表钢种:Q235、82B、40Cr、ML45Mn、H08A、50CrVA、GCr15、F45MnV、BL2等。
2连铸机性能参数3连铸机工艺布置小方坯连铸机车间厂房由连铸跨、出坯跨组成,两跨平行布置。
连铸机回转台布置在连铸跨与钢水接收跨之间,浇铸设施、操作平台、结晶器及振动装置、导向段设备、引锭杆及存放设备、切割设备等布置在连铸跨,运输辊道设施、冷床设施布置在出坯跨。
中间包修砌、中间包干燥、中间包存放、结晶器维修、结晶器存放、振动装置维修等设备布置在连铸跨厂房内,铸坯堆存区域设在出坯跨。
4连铸机设计特点(1)连铸机机型选择大半径弧形连铸机,采用连续矫直技术,减小连铸坯的变形率,防止铸坯表面及内部裂纹。
(2)带升降、称量和钢包加盖的碟式大包回转台。
(3)按中间包冶金原理优化设计,采用大容量中间包,增加钢水在中间包内的平均停留时间,促进夹杂物充分上浮。
(4)中间罐钢水液面采用双渣保护:第一层采用合成渣,使钢液与空气隔绝并吸收上浮的夹杂物;第二层采用天然渣(炭化稻壳),覆盖于合成渣上面保温。
(5)中间罐采用碱性耐火材料,其氧化物易被钢液溶解且不易还原,具有较好的耐钢水热冲击和耐机械侵蚀性能,可以充分预热,降低第一包钢水的温降。
连铸机工艺设计有关问题

关于连铸机工艺设计有关问题的探讨摘要:随着经济的日益发展,人民的生活水平逐渐提高,连铸机的应用也越来越广泛,关于连铸机的工艺设计问题的探讨也越来越白日化,本文就连铸机在工艺设计方面有关问题如参数的确定、主要工艺设计思想等进行讨论,为完善连铸机的工艺设计提供参考。
关键词:连铸机,工艺设计,问题,讨论前言:把高温钢水连续不断地浇铸成具有一定断面形状和一定尺寸规格铸坯的生产工艺过程叫做连续铸钢。
而完成这一过程所需的设备叫连铸成套设备。
浇钢设备、连铸机本体设备、切割区域设备、引锭杆收集及输送设备的机电液一体化构成了连续铸钢核心部位设备,习惯上称为连铸机。
近年来,随着钢铁工业的迅速发展,连铸设计理念也得到完善,但是与国际水平相平,我国的整体实力仍有所差距。
因此,努力提高连铸工艺设计水平有着重大意义。
正文:1.连铸机工艺设计的意义随着现代工业对特殊钢、高质量钢的需求不断扩大,以及连续铸钢技术的迅速发展,对连铸工艺过程也有了更高的要求。
连续铸钢工艺从原料到成品的过程中起着关键性作用。
连铸工艺的优与劣直接影响钢产品的质量、性能和企业的经济效益。
且随着炼钢和轧钢技术的进展,钢铁工业结构的变化和对产品的规格、质量的新要求,这使得采用常规和铸锭—开坯工艺难以满足一些大型钢铁企业的生产和发展,为此,研究连铸的新工艺和新技术是必要的。
2.大、小方坯的特点通常,把边长220 mm(含圆坯、矩形坯)的方坯连铸机叫做大方坯连铸机。
大方坯连铸机浇注的主要钢种为中、高碳钢、合金钢等,用于轧制重轨、硬线、无缝钢管、大中型h型钢、棒材、锻材等。
大方坯连铸机钢种特殊且断面较大,在浇注过程中易出现表面纵、横裂纹、星状裂纹、角部凹陷、表面和皮下大型夹杂物和内部缩孔、白亮带、中心疏松、中心偏析和内部裂纹等缺陷,各大钢铁设计公司在大方坯连铸生产操作技术、生产组织、装备开发上作出了很多科研创新工作,使大方坯连铸技术得到了迅速发展。
而小方坯的铸坯断面小,热熔量比较小。
典型的小板坯连铸机设计

典型的小板坯连铸机设计
文 / 小光 李新 强 谷世群 侯
摘 要 :土耳其T S A I ̄ O Y L¥. I 流小板 坯连铸机 的工艺流程 ,设备 布置和装机 水平具有小板 坯连 铸机的典型性 。 本文介 绍 了该铸机 的基本 参数 ,关键技 术 以及 工艺保 证措施 。希 望通过本文 为同类连铸机 的设 计 与建设提 供参
工 博 21 ・ 2中旬刊 1 5 会 览・0 1 1 4
技 术交流
连铸金属收得率 :9% 7 年产合格铸坯 :10 / 台2 流CC 1万t 1 机2 M 三 ,连铸机工艺流程 该 铸机的主生 产流程是将 10 电炉 冶炼 的钢水经过 3t LF 炉处理后 ,使钢水的化学 成分 、温度等达到 浇注 要 求 ,处理合格的钢水经过双流板坯连铸机铸造 出一定厚 度和宽度的双流连铸坯 ,再经火焰切割机 切割成一定定 尺的合格铸坯 。 其 中一流铸坯经辊道直接输送 到轧钢车 间加 热炉前 的入炉辊道 ,另一 流铸坯经过横移台车的搬运 ,也同样 输送NS 钢车间加 热炉前的入炉辊道 ,最终两流铸坯均 L 成为中宽带轧机的坯料m 。 四 连铸机辊列 图 根据产 品大纲为保证铸坯质量 ,该辊列设计具有 以 下特点 : 2 、连铸机本体设备 ( )结 晶器 。平板组 合式直结 晶器 ,带柱 塞缸 与 1 蝶 形 弹 簧 组 合 实 现 软 夹 紧 功 能 的 夹 紧 机 构 ,调 宽 部 分 采用 高精度直 线传递 的变频伺 服驱动 装置 。铜 板长度 l0 mm,材质C —C _ r O0 u r Z 镀Ni Co _ — 合金 。宽边设 l 对辊 径为1O 0mm的足辊 ,窄边设3 对辊径为lO m足辊。 Om ()具有独立知识产权的结 晶器振动装置。该装置 2 采用板弹 簧导 向,液压缸为动 力源 ,可在线准确地调整 振动频率 、振幅 、速度 ,并可根据不 同钢种、不同拉速 变化而采用不 同的负滑动时 间的非正弦曲线,以控制铸 坯表面振痕深度 。通过调整液压缸控制参数实现振动参 数的优化选取 。 ( )弯 曲段 。 段 内采 用小 辊 径 密排 的 刚性 框 架 3 式结 构。其 中2 6 — #辊辊径 l0 3 mm,7 l #辊辊 径 一 8 10 7 mm。第2 8 — 对辊子对铸坯实施垂直导向。第9 l 一 8 对辊子构成 1 个长的弯 曲区 ,使铸坯 由垂直状态 连续 弯 曲至曲率半径R70mm。 00 ( )扇形段共1段 。扇形段l 为弧形段 ,扇形段 4 0 —4 5 Y 矫直段 ,扇形段7 1为水平段 。每 个扇形段均 、6 o — O 为带侧框架 ,液压夹紧可升 降式扇形段结构 ,实现浇注 不同厚度铸坯辊缝的设定与调节 。 ( )扇形段驱动装置。主要 由万 向联轴器,硬齿面 5 行星减速 器,鼓形齿联轴器 ,变频调速电机 ,电力液压 推杆制动 器,光电编码 器,中间轴 ,传动底座等组成 。 万向联轴器法兰一端与扇形段驱动辊相连,一端与减速 器相连 ,保证在浇铸不同厚度铸坯及设置不同辊缝时能 够有效地传递运动和驱动 力。
连铸机

第4章方坯连铸机总体设计及计算4.1 总体方案的确立钢水凝固成型有两种方法:传统的模铸法或连续铸钢法。
传统的模铸法分为脱模、整模、钢锭均热与开坯等工序。
基建投资大,能耗大,生产成本很高。
连续铸钢法的出现从根本上一个世纪以来占统治地位的钢锭初扎工艺,节省了工序,缩短了流程,提高了金属的收得率,降低的能耗。
本设计的主要工序流程是:钢水从钢水包中流出,先注入中间包,然后进入弧形结晶器,在结晶器中形成弧形铸坯沿着弧形辊道向下运动,运动中受喷水冷却,直至完成或部分凝固,然后铸坯到水平切点处进入拉矫机,然后用火焰切割车把铸坯切割成定尺,从水平方向出坯。
4.2 弧形连铸机总体设计计算与确定弧形连铸机总体参数包括:铸坯断面尺寸、冶金长度、拉坯速度、铸机半径以及连铸机的流数。
这些参数是确定铸即性能和规格的基本要素,也是设备选型和设计的主要依据。
4.2.1 铸坯断面连铸的坯型有:板坯、方坯、矩形坯、圆坯、六角或八角坯等。
以生产的铸坯断面尺寸和坯形如表4-1所示:确定铸坯断面尺寸时,应根据轧才的需要和轧制时的压缩比。
还应考虑炼钢炉的容量和铸机的生产能力。
对大型炼钢炉一般配置大断面和多流连铸机。
轧制的压缩比可取6~10。
对不锈钢和耐热钢最小取8,对高速钢和工具钢最小取10,对碳素钢和低合金钢可取6。
铸坯断面越大,对加杂物上浮越有利,同时铸机生产能力越大,但铸坯断面尺寸超过最大压缩比的要求时,就会相对得多消耗能量。
在选择铸坯断面形状和尺寸时,还应考虑与轧机能力的合理配合,可参照表4-2选用。
4.2.2 冶金长度从结晶器液面到铸坯全部凝固为止,铸坯中线距离称为液心长度或称冶金长度,因此液心长度与铸坯冷凝有关。
冷凝公式:铸坯凝壳厚度δ与冷凝强度和冷凝时间有关,冷凝强度用单位热流表示,即每单位时间单位面积上流出的热量,用0H 表示,单位为Kj/m 2·min,0H 越大表明冷凝强度越大,凝壳越厚。
由实验知,有如下关系:δ∝5.05.00τH (mm )或者 δ=ξ5.05.00τH(4.1)式中 τ——冷凝时间(min )ξ——系数(mm ·m/k 5.0J ),与铸坯形状和材质有关,由实验知ξ=0.0758式中(4.1)中( ξ5.00H )称冷凝系数,用K 表示,即K=ξ5.00H (mm ·5.0min -) (4.2)则冷凝皮可厚度δ为:δ=K 5.0τ(mm ) (4.3)式(4.3)称冷凝公式。
- 1、下载文档前请自行甄别文档内容的完整性,平台不提供额外的编辑、内容补充、找答案等附加服务。
- 2、"仅部分预览"的文档,不可在线预览部分如存在完整性等问题,可反馈申请退款(可完整预览的文档不适用该条件!)。
- 3、如文档侵犯您的权益,请联系客服反馈,我们会尽快为您处理(人工客服工作时间:9:00-18:30)。
13.引锭装置:本设计采用挠性上装引锭装置,短节距链式引锭杆的节距短 (小于辊间距),可制成直线型,加工方便,不宜变形,改变铸坯断面 时只需改变相应的断面的引锭头。
14.切割装置:本次设计采用火焰切割,火焰切割是利用预热氧和预热乙炔 混合燃烧的火焰把切缝处的金属熔化,然后以高压切割氧把熔化的金属 吹掉,从而把铸坯切断。
精选ppt
9
9.二次冷却装置:采用密排的夹棍,辊缝小,并要求对弧精度高
10.二次冷却二冷区总耗水量:337.3 t/h
11.比水量:又称冷却强度,即每单位质量的铸坯所消耗的二次冷却水量, 比水量δ值根据所浇铸的钢种决定,对低碳钢,低合金钢和裂纹不敏感 钢种取δ=1.0~1.2合金钢取0.6~0.8本设计δ取0.6。
9m
最大浇铸时间
68.5 min
实际浇铸时间
50 min
拉坯速度
1.7 m/min
理论拉坯速度
2.04 m/min
冶金长度
32.93 m
铸机长度
36.22 m
液相长度
27.4 m
连铸机流数
2
浇铸周期时间
281 min
连铸机的作业率
80%
连铸机铸坯收得率
98%
连铸机平均日产量
7231.8 t/d
连铸机的平均年产量
精选ppt
8
8 中间包车
本设计采用门型中间包车2台承重120吨,升降距离为 400mm,还采用新技术电子秤量系统、保护渣自动下 料装置,同时中间包小车上安装摆动溜槽。中间包车 的运行速度为10~20m/min,最高可达30 m/min,升降 速度为2m/min,中间包更换时间最快也为2~3min。
精选ppt
10
14 连铸机结构简图
精选ppt
11
14 连铸车间平面布置图构简图
精选ppt
12
L=R+L1+L2+L3+L4+L5=55.34m
L1—拉矫机长度,取1.5~1.8m。本设计取1.8m L2— 拉矫机后至切割区前距离,m。此段距离的加长利
于提高拉速,设计取6m。 L3— 切割区长度,m。机械切割时为设备尺寸,火焰切
割时至少等于或大于铸坯最小长度,本设计取6.6m。 L4— 输出辊道或铸坯等待区长度 m,一般至少大于最
大定尺长度的1.5倍,设计为20 m。 L5— 冷床或出坯区长度 m。最大定尺长度再增加1米。
本设计取13 m。
精选ppt
13
连铸机的高度 H=R+H1+H2+H3+H4=16.05 m
H1— 拉矫机底座基础面至铸坯底面距离,取决于出坯 的标高和设备尺寸,一般取0.5~1.0 m;本设计取1.0 m。
211.15万吨/年
连铸机台数的确定
精选ppt 2台
4
4金属平衡图
精选ppt
5
5 钢包回转台
钢包回转台时是连铸机浇钢设备的重要组成部 分,它的作用是将位于受包位置的满载钢包 回转至浇钢位置,准备进行浇注。同时将浇 注完钢水的空包回转至受包位置,准备运走 。其转速为0.7~1.0转/min,换包时间为 0.5~2.0min。本设计采用的是蝶型钢包回转台 ,回转半径2.55m,升降行程0.56m。
精选ppt
14
敬请各位老师指正
精选ppt
15
针对180t转炉的连铸机的设计
精选ppt
1
一 连铸工艺流程图
精选ppt
2
2 连铸机型的选择
连铸机的分类: 立式﹑直弧形、弧形、多点矫直 弧形﹑超低头和水平式等连铸机, 几种机型都有采用,但是弧形连 铸机应用最多
精选ppt
3
3 主要工艺参数
项目
参数
铸坯断面范围
225 mm×1475 mm
连铸机弧形半径
精选ppt
6
6结晶器的尺寸参数
项目 结晶器长度 结晶器的倒锥度 结晶器的水缝面积 结晶器拉坯阻力 水直径
参数 619 mm 0.95% 13414mm2 34490 N 3.05cm
精选ppt
7
7 中间包主要工艺参数
项目 中间包容量 中间包高度 中间包长度 中间包的倾角 水口直径
参数 20.54 t 1200 mm 7100 mm 12° 3.05cm
H2 — 铸机弧形中心至结晶器顶面的距离,常取结晶器 高度的一半,如取:0.35~0.45 m;设计取0.45 m, 由于设计选用的是垂直弯曲型连铸机垂直段取4 m, 则 =4.45 m。
H3— 结晶器顶面至中间包水口升至最高位置时的距离 ,一般取:0.1~0.2,设计取:0.2 m。
H4 — 中间包全高,一般为:1.0~1.5 m,较大的中间 包可达2 m,设计取:1.4 m