电阻炉温度控制系统的设计
基于单片机的电阻炉温度控制系统设计

基于单片机的电阻炉温度控制系统设计一、引言电阻炉是一种广泛应用于工业生产中的加热设备,其温度控制的准确性对于工艺过程的稳定和产品质量的保证至关重要。
本文将基于单片机设计一个电阻炉温度控制系统,通过采集温度传感器的信号,用单片机控制加热器的工作状态,实现对电阻炉温度的精确控制。
二、系统结构设计本系统由四个模块组成:温度采集模块、温度控制模块、显示模块和控制模块。
1.温度采集模块:使用一个高精度的温度传感器,如PT100,将电阻炉内部的温度转化为电压信号。
该信号经过模拟转数字转换器(ADC)转换为数字信号,传输给单片机。
2.温度控制模块:根据温度采集模块传输的信号,单片机通过PID算法计算出控制值,并输出PWM信号控制加热器的工作状态。
PID算法可根据实际情况进行参数调整,以达到系统稳定的控制效果。
3.显示模块:采用数码管或液晶显示器显示当前电阻炉的温度值,方便操作员实时监测电阻炉的运行状态。
4.控制模块:可以通过按钮或者触摸屏等方式进行设定和调整控制参数,例如设定温度范围、PID参数调节等。
三、系统工作原理1.系统初始化:单片机启动后,进行相应的外设初始化和参数设定,包括温度采集模块的配置、PID参数的设定、显示模块的显示等。
2.温度采集与转换:通过温度传感器采集电阻炉内部的温度信号,将其转化为模拟电压信号。
利用ADC将模拟信号转换为数字信号,并传输给单片机进行处理。
3.PID算法计算:单片机根据采集到的温度值,通过PID算法计算出控制值。
PID控制算法通常包括比例系数(P)、积分系数(I)和微分系数(D)三个参数的调整,根据实际情况进行调节以达到控制精度和稳定性要求。
4.PWM输出控制:根据PID算法计算得到的控制值,单片机输出对应的PWM信号。
该信号通过驱动电路控制加热器的工作状态,调整和维持电阻炉的温度。
5.温度显示:单片机将当前的温度值通过显示模块进行显示,使操作员能够实时监测到电阻炉的温度。
电阻炉炉温计算机控制
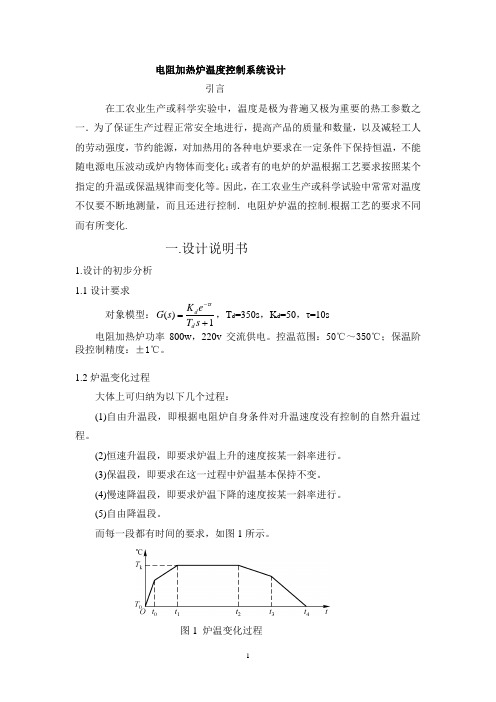
电阻加热炉温度控制系统设计 引言在工农业生产或科学实验中,温度是极为普遍又极为重要的热工参数之一.为了保证生产过程正常安全地进行,提高产品的质量和数量,以及减轻工人的劳动强度,节约能源,对加热用的各种电炉要求在一定条件下保持恒温,不能随电源电压波动或炉内物体而变化;或者有的电炉的炉温根据工艺要求按照某个指定的升温或保温规律而变化等。
因此,在工农业生产或科学试验中常常对温度不仅要不断地测量,而且还进行控制.电阻炉炉温的控制.根据工艺的要求不同而有所变化.一.设计说明书1.设计的初步分析 1.1设计要求对象模型:1)(+=-s T e K s G d sd τ,T d =350s ,K d =50,τ=10s电阻加热炉功率800w ,220v 交流供电。
控温范围:50℃~350℃;保温阶段控制精度:±1℃。
1.2炉温变化过程大体上可归纳为以下几个过程:(1)自由升温段,即根据电阻炉自身条件对升温速度没有控制的自然升温过程。
(2)恒速升温段,即要求炉温上升的速度按某一斜率进行。
(3)保温段,即要求在这一过程中炉温基本保持不变。
(4)慢速降温段,即要求炉温下降的速度按某一斜率进行。
(5)自由降温段。
而每一段都有时间的要求,如图1所示。
图1 炉温变化过程1.3炉温控制要求要求电阻炉炉内的温度,应按图2所示的规律变化。
图2 炉温控制要求从室温T 0开始到a 点为自由升温段,当温度一旦到达a 点(即他t 0点),就进入系统调节。
从b 点到c 点为保温段,要始终在系统控制之下,以保证所需的炉内温度的精度.加工结束,即由c 点到d 点为自然降温段.炉温变化曲线对各项品质指标的要求如下:● 过渡过程时间:即从升温开始到进入保温段的时间t 1≤15s .● 超调量:即升温过程的温度最大值(T M )与保温值(T k )之差与保温值之比 kk10%T M T T σ-=≤ ● 静态误差:即当温度进入保温段后的实际温度值(T)与保温值(T k )之差与保温值之比。
电阻炉温度控制系统的设计
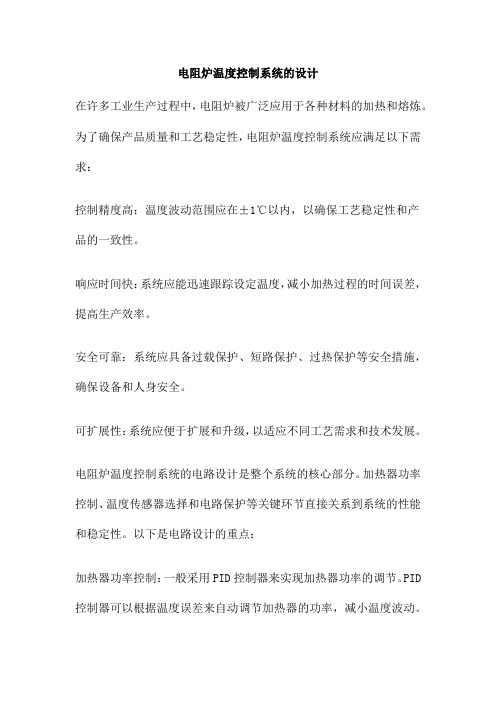
电阻炉温度控制系统的设计在许多工业生产过程中,电阻炉被广泛应用于各种材料的加热和熔炼。
为了确保产品质量和工艺稳定性,电阻炉温度控制系统应满足以下需求:控制精度高:温度波动范围应在±1℃以内,以确保工艺稳定性和产品的一致性。
响应时间快:系统应能迅速跟踪设定温度,减小加热过程的时间误差,提高生产效率。
安全可靠:系统应具备过载保护、短路保护、过热保护等安全措施,确保设备和人身安全。
可扩展性:系统应便于扩展和升级,以适应不同工艺需求和技术发展。
电阻炉温度控制系统的电路设计是整个系统的核心部分。
加热器功率控制、温度传感器选择和电路保护等关键环节直接关系到系统的性能和稳定性。
以下是电路设计的重点:加热器功率控制:一般采用PID控制器来实现加热器功率的调节。
PID 控制器可以根据温度误差来自动调节加热器的功率,减小温度波动。
温度传感器选择:常用的温度传感器有热电偶和红外测温仪。
选择合适的传感器对提高系统的测量精度至关重要。
电路保护:为防止系统故障对设备和人身造成伤害,电路应设计多种保护措施。
例如,加热器应配备熔断器、过载保护器和短路保护器等。
电阻炉温度控制系统的软件设计是实现整个系统智能化的关键。
软件应包括输入输出端口设置、算法实现等关键模块。
以下是软件设计的要点:输入输出端口设置:软件应设置必要的输入输出端口,以便于用户对系统进行控制和监视。
例如,软件应支持通过界面设置加热器的启动/停止、温度设定值等。
算法实现:系统软件应实现高效的温度控制算法,如PID控制算法,以实现精确的温度控制。
算法应具有自适应性,能够根据环境条件和材料属性等变化进行自我调整,提高控制效果。
在完成电阻炉温度控制系统的设计和调试后,需要对系统进行严格的测试与结果验证,以确保系统的性能和稳定性达到预期要求。
测试应包括以下步骤:测试环境搭建:搭建测试平台,选择合适的电阻炉、温度传感器、控制系统等设备进行联调测试。
空载测试:在无负载的情况下,测试系统的加热速度、稳定性和精度等指标。
电阻炉温度控制系统方案设计

电阻炉温度控制系统方案设计
1. LOGO!性能及特点
LOGO!是SIEMENS 公司推出通用逻辑控制模块,是一种将编程器和主
机一体化的超小型可编程序控制器。
LOGO 内部集成有:控制功能、操作和显
示单元。
有一个用于扩展模块的接口、一个用于程序模块和PC 电缆的接口。
预制有基本功能、软开关、二进制指示器、输入和输出。
用户可通过控制器面
板上的按钮直接编程、编辑、读取数据或输入数据;可与计算机联网,用厂家提
供的专用软件编程。
SIEMENS LOGO!的主要特点如下:
①编程操作简单。
LOGO!编程可在本机上直接操作。
②编程语言简单。
其编程是将需要实现的功能所对应的功能块连接起
来即可。
③输出电流大。
LOGO!输出端可以承受电流达10A(继电器输出,阻性负载)
④自带显示面板。
可直接在自带面板上设置、更改和显示参数。
⑤具有通信功能。
带AS-I 总线功能的LOGO!可作为远程I/O 使用。
⑥价格低廉。
具有较低的价格和较高的性价比。
⑦面向大众、方便用户。
LOGO!不需要专门的训练,只要懂得一些电气知识就行。
⑧体积“小”(体积约为72mm*90mm*53mm)。
2.LOGO!的结构及原理
LOGO!的面板结构如图1.所示:电源接线端用来连接电源(电压有直流
24V、交流115V 或交流230V),数字量输入端直接连接开关、按钮和传感器等,数字量输出端可用容量为8/10A 的开关来控制负载,液晶显示面板可在LOGO!。
电阻炉炉温控制系统设计

1绪论1.1研究的目的及意义自从发现电流的热效应(即楞次-焦耳定律)以后,电热法首先用于家用电器,后来又用于实验室小电炉⑴。
随着镍铬合金的发明,到20世纪20年代,电阻炉已在工业上得到广泛应用。
工业上用的电阻炉一般由电热元件、砌体、金属壳体、炉门、炉用机械和电气控制系统等组成。
加热功率从不足一千瓦到数千千瓦。
工作温度在650C以下的为低温炉;650C 〜1000E为中温炉;1000C以上为高温炉。
在高温和中温炉内主要以辐射方式加热。
在低温炉内则以对流传热方式加热,电热元件装在风道内,通过风机强迫炉内气体循环流动,以加强对流传热。
电阻炉有室式、井式、台车式、推杆式、步进式、马弗式和隧道式等类型。
可控气氛炉、真空炉、流动粒子炉等也都是电阻炉[2]。
电阻炉与火焰炉相比,具有结构简单、炉温均匀、便于控制、加热质量好、无烟尘、无噪声等优点,但使用费较高⑻。
电热元件具有很高的耐热性和高温强度,很低的电阻温度系数和良好的化学稳定性。
常用的材料有金属和非金属两大类。
金属电热元件材料有镍铬合金、铬铝合金、钨、钼、钽等,一般制成螺旋线、波形线、波形带和波形板。
非金属电热元件材料有碳化硅、二硅化钼、石墨和碳等,一般制成棒、管、板、带等形状。
电热元件的分布和线路接法,依炉子功率大小和炉温要求而定⑷。
在工农业生产或科学实验中,温度是极为普遍的又极为重要的热工参数之一。
为了保证生产过程正常安全地进行,提高产品的质量和数量以及减轻工人的劳动强度,节约能源,对加热用的各种电炉要求在一定条件下保持恒温,不能随电源电压波动或炉内物体而变化,也有的电炉的炉温根据工艺要求按照某个指定的升温或保温规律而变化等。
因此,在工农业生产或科学实验中常常要求不断地测量温度,同时还进行控制[5]。
电阻炉是热处理生产中应用最广的加热设备,通过布置在炉内的电热元件将电能转化为热能并借助辐射与对流的传热方式加热工件。
热处理是提高金属材料及其制品性能的工艺⑹。
电阻炉温度控制系统的设计

电炉温度控制系统设计摘要热处理是提高金属材料与其制品质量的重要技术手段。
近年来随工业的开展,对金属材料的性能提出了更多更高的要求,因而热处理技术也向着优质、高效、节能、无公害方向开展。
电阻炉是热处理生产中应用最广泛的加热设备,加热时恒温过程的测量与控制成为了关键技术,促使人们更加积极地研制热加工工业过程的温度控制器。
此设计针对处理电阻炉炉温控制系统,设计了温度检测和恒温控制系统,实现了根本控制、数据采样、实时显示温度控制器运行状态。
控制器采用 51 单片机作为处理器,该温度控制器具有自动检测、数据实时采集处理与控制结果显示等功能,控制的稳定性和精度上均能达到要求。
满足了本次设计的技术要求。
关键词:电阻炉,温度测量与控制,单片机目录一、绪论- 1 -选题背景- 1 -电阻炉国开展动态- 1 -设计主要容- 2 -二、温度测量系统的设计要求- 2 -2.1 设计任务- 2 -2.2 系统的技术参数- 2 -2.3 操作功能设计- 3 -三、系统硬件设计- 3 -3.1 CPU选型- 4 -3.2 温度检测电路设计- 4 -3.2.1 温度传感器的选择- 4 -热电偶的测温原理- 5 -3.2.1.2 热电偶的温度补偿- 5 -3.2.2 炉温数据采集电路的设计- 6 -3.2.2.1 MAX6675芯片- 6 -3.2.2.2 MAX6675的测温原理- 6 -3.2.2.3 MAX6675 与单片机的连接- 7 -3.3 输入/输出接口设计- 7 -3.4 保温定时电路设计- 9 -3.4.1 DS1302 与单片机的连接- 10 -3.5 温度控制电路设计- 10 -系统硬件电路图- 12 -四、系统软件设计- 13 -4.1 软件总体设计- 13 -4.2 主程序设计- 13 -4.3 温度检测与处理程序设计- 14 -4.4 按键检测程序设计- 16 -4.5 显示程序设计- 18 -4.6 输出程序设计- 19 -中值滤波- 20 -五、结论- 20 -参考文献- 21 -一、绪论1.1选题背景在现代化的工业生产中,电流、电压、温度、流速、流量、压力和开关量都是常用的主要被控参数。
课程设计—电阻炉炉温控制系统
电阻炉炉温控制系统设计1课程设计规定1.1 课题内容应用计算机旳实时监控和温度测量技术,采用单片机、温度检测电路、温度控制电路等,采用比例环反馈、数字PID闭环调整两种方式实现电阻炉炉温旳实时监控。
1.2 规定和技术指标用单片机和对应旳构成部件构成电阻炉温旳自动控制系统,规定测温范围0~100℃,使其控制系统控制旳温度保温值旳变化范围为30~60℃。
规定:(1)完毕电阻炉温度控制系统设计,包括硬件电路设计和软件程序设计;(2)采用LED实时显示控温时旳实际炉温和设定炉温,如将炉温加热并控制在60℃;当炉温工作至设定温度时,蜂鸣器每2秒报警一次,绿色LED灯常亮。
当炉温超过设定温度5℃,过温保护电路动作,蜂鸣器常鸣,红色LED常亮。
(3)对其主电路和控制电路设计对应旳保护电路,使其安全可靠地工作。
(4)具有防干烧功能。
(5)具有定期功能,设定一段时间自动加温,如1分钟。
1.3 元器件清单另有剪刀、镊子等工具表1.1 元器件清单2电路设计2.1 总体设计方案基本方案:运用温度变送器和温度检测电路将电阻炉实际温度转换成对应旳数字信号,送入单片机,进行数据处理后,通过显示屏显示温度,并判断与否报警,同步将实际炉温与设定温度比较,根据对应旳算法(如PID)计算出控制量,通过控制对应旳加热电路实现对炉温旳控制。
本系统采用STC89C52作为系统旳主控芯片,负责加热炉旳温度检测与控制。
其重要任务是:1、读取DS18B20旳温度数据;2、控制继电器通断,保证温度到达设定值并保温;3、读取键盘设置旳温度值;4、在LED上显示设置旳温度、目前温度以和恒温时间;5、当温度抵达警戒值旳时候控制蜂鸣器报警。
图2.1 总体构造图由于加热炉仅能通过通断电路控制,不具有良好旳可控性,且加热所需旳速度和精度规定并不高,这里无需使用PID算法这样旳高速跟踪算法,只要使用二次线性化旳措施控制,就可以很好地实现炉子旳加热和恒温控制了。
电阻加热炉温度控制系统设计
电阻加热炉温度控制系统设计一、温度控制系统的要求:1.稳定性:系统应能快速响应温度变化,并能在设定温度范围内保持稳定的温度。
2.精度:控制系统应具备高精度,确保炉内温度与设定温度的偏差控制在允许范围内。
3.可靠性:系统应具备高可靠性,能长时间稳定运行,并能在发生异常情况时及时报警或自动停止加热。
4.人机界面:温度控制系统应提供方便直观的人机界面,操作简单易懂。
二、温度控制系统的设计:1.传感器选择:选择合适的温度传感器进行温度检测。
常用的温度传感器有热电偶和热电阻。
根据实际需求选择合适的传感器类型和量程。
2.温度控制器选择:根据控制需求,选择适用于电阻加热炉的温度控制器。
具备温度显示功能的控制器可以直观地显示炉内温度。
还可以选择具备PID控制功能的控制器,以提高温度控制精度。
3.控制循环设计:将温度控制系统设计成闭环控制系统,以实现炉内温度的精确控制。
控制循环包括采样、比较、控制和执行四个环节。
采样环节将实际温度值与设定温度值进行比较,然后控制环节根据比较结果输出控制信号,最后执行环节根据控制信号调节电阻加热炉的加热功率。
4.温度传感器布置:将温度传感器布置在炉内合适位置,确保能够准确测量到炉内温度。
传感器的安装位置应避免热点和冷点,以避免温度不均匀。
5.控制参数调整:根据实际情况进行PID参数的调整。
通过实验或仿真等方法,逐步调整PID参数,使得系统能够快速响应温度变化、准确跟踪设定温度,并保持稳定的温度输出。
6.报警和保护设计:设计温度控制系统时,应考虑到电阻加热炉的过热或温度异常等情况,并设置相应的报警和保护功能。
当温度超过安全范围时,系统应及时报警,并自动停止加热。
7.人机界面设计:为了方便操作和监控,可以在温度控制系统上设置触摸屏或显示屏。
通过人机界面,操作人员可以方便地设定温度、监测炉内温度,并能够实时查看温度曲线和报警信息。
总之,电阻加热炉温度控制系统的设计需要考虑到温度控制精度、稳定性、可靠性和人机界面等方面的要求。
基于PLC电阻炉温度控制系统设计
基于PLC电阻炉温度控制系统设计1.引言电阻炉是一种常见的热处理设备,用于加热金属或其他材料至一定温度。
为了确保加热过程的准确性和安全性,需要使用温度控制系统对电阻炉进行控制。
本文将基于PLC来设计一个电阻炉温度控制系统。
2.设计方案2.1系统架构该系统的基本架构由以下几个部分组成:传感器模块、控制模块、执行模块和人机界面。
传感器模块用于监测电阻炉内部的温度,并将温度信号传输给控制模块。
控制模块采用PLC作为核心控制器,负责接收传感器信号并根据设定的温度值进行控制。
执行模块根据PLC的指令,控制电阻炉的加热功率以调节温度。
人机界面用于设置设定温度和显示当前温度,以及监控系统状态。
2.2硬件设计传感器模块使用高精度的温度传感器(如热电偶或热电阻),将温度信号转换为模拟电信号,并通过模拟输入模块将信号输入到PLC。
控制模块采用PLC作为核心控制器。
PLC具有较高的可编程性和稳定性,能满足温度控制系统的要求。
PLC通过模拟输入模块接收传感器信号,并通过数字输出模块控制执行模块。
执行模块由电源模块和电阻器组成。
电源模块为电阻炉提供电力源,电阻器根据PLC的输出信号来调节电阻炉的加热功率,以控制温度。
人机界面采用触摸屏或上位机软件,用于设置设定温度、显示当前温度、监控系统状态和报警信息等。
2.3软件设计软件部分主要包括程序设计和界面设计。
程序设计方面,主要采用Ladder Diagram(梯形图)来编写控制程序。
程序需要包括接收传感器信号、判断温度与设定温度的差值、根据差值控制输出信号等功能。
界面设计方面,可以使用相应的编程软件进行设计。
界面需要包括设定温度的输入框、当前温度的显示框、报警信息的提示框等。
3.系统功能该系统具有以下功能:-温度控制:根据设定温度自动调节电阻炉加热功率,使温度保持在设定范围内。
-报警功能:当温度超出设定范围时,系统会发出声音或显示警报,提醒操作员。
-数据记录:系统可以记录温度变化的曲线,并将数据存储到数据库中,以便用户查询和分析。
箱式电阻炉及温控系统结构设计
箱式电阻炉及温控系统结构设计1.炉体结构设计:箱式电阻炉的炉体一般由钢板焊接而成,具有良好的耐高温性能和结构强度。
炉体需要具备良好的隔热性能,以减少能量损失。
为此,可以在炉体内外分别设置隔热材料层,如石棉、硅酸铝纤维、陶瓷纤维等,同时在隔热材料层外再设置一层不锈钢金属材料,以增加炉体的稳定性。
2.加热元件设计:箱式电阻炉的加热元件主要有电阻丝和加热管两种形式。
电阻丝是通过通电使其发热来加热炉体,常用的电阻丝材料有镍铬合金、铬铝合金等。
加热管是通过通过加热管内的导热介质来实现加热,加热管一般为不锈钢管内填充密度较高的酸钠玻璃丝,加热管具有更高的加热效率和更均匀的温度分布。
3.温控系统设计:温控系统是箱式电阻炉的重要组成部分,其主要功能是实时监测和控制炉内温度。
温控系统一般由控制器、温度传感器、继电器等组成。
控制器负责接收温度传感器的信号,并通过继电器控制加热元件的通断,以达到设定温度的目的。
在温控系统设计中,需要考虑控制精度、稳定性和可靠性等因素。
在箱式电阻炉及温控系统的结构设计过程中,需要注意以下几点:1.炉体结构紧凑合理,并具备良好的隔热性能;2.加热元件设计要考虑加热效率、温度均匀性等因素;3.温控系统的设计要考虑控制精度、稳定性和可靠性;4.安全性是设计中重要的考虑因素,需要考虑炉体的绝缘性能、过温保护等措施;5.设备维护方便,易于清洁和更换损坏的零部件。
总之,箱式电阻炉及温控系统的结构设计需要综合考虑炉体结构、加热元件和温控系统三个方面,以实现高效、稳定的加热和温度控制效果。
同时,设计中还要注意安全性和维护性,以确保设备的正常运行和使用寿命。
- 1、下载文档前请自行甄别文档内容的完整性,平台不提供额外的编辑、内容补充、找答案等附加服务。
- 2、"仅部分预览"的文档,不可在线预览部分如存在完整性等问题,可反馈申请退款(可完整预览的文档不适用该条件!)。
- 3、如文档侵犯您的权益,请联系客服反馈,我们会尽快为您处理(人工客服工作时间:9:00-18:30)。
软件总体设计- 14 -
,
主程序设计- 14 -
温度检测及处理程序设计- 15 -
按键检测程序设计- 17 -
显示程序设计- 19 -
输出程序设计- 20 -
中值滤波- 21 -
五、结论- 22 -
参考文献- 23 -
…
一
1.1
在现代化的工业生产中,电流、电压、温度、流速、流量、压力和开关量都
压 U0 的数据,该数据就代表测量点的实际温度值 T,这就是 MAX6675 进行冷端温度补偿和测量温度的原理。
MAX6675 与单片机的连接
图3-3 MAX6675与单片机的连接
MAX6675有五个引脚,脚 (T-)接热电偶负极,脚 (T+)接热电偶正极,脚 (SCK)串行时钟输入端,脚 (CS)片选端,使能启动串行数据通讯,脚 (SO)串行数据输出端。
热电偶的种类很多,热电偶有 K 型(镍铬-镍硅)WRN 系列,N 型(镍铬硅-镍硅镁)WRM 系列,E 型(镍铬-铜镍)WRE 系列,J 型(铁-铜镍)WRF 系列,
T 型(铜-铜镍)WRC 系列,S 型(铂铑 10-铂)WRP 系列,R 型(铂铑 13-铂)
WRQ 系列,B 型(铂铑 30-铂铑 6)WRR 系列等。考虑设计成本与实际的温度
}
程的温度控制器。
此设计针对处理电阻炉炉温控制系统,设计了温度检测和恒温控制系统,实现了基本控制、数据采样、实时显示温度控制器运行状态。控制器采用 51 单片机作为处理器,该温度控制器具有自动检测、数据实时采集处理及控制结果显示等功能,控制的稳定性和精度上均能达到要求。满足了本次设计的技术要求。
关键词:电阻炉,温度测量与控制,单片机
热电偶的温度补偿- 7 -
炉温数据采集电路的设计- 7 -
MAX6675芯片- 7 -
MAX6675的测温原理- 7 -
—
MAX6675与单片机的连接- 8 -
输入/输出接口设计- 9 -
保温定时电路设计- 10 -
DS1302与单片机的连接- 11 -
温度控制电路设计- 11 -
系统硬件电路图- 13 -
对传统的负反馈、单一 PID 控制系统做了多种补充,从而使控制性能更佳。同时,越来越多的控制系统采用新的控制方法如:模糊控制、神经网络控制、才遗传算法控制、最优控制、自整定 PID 参数控制器、自适应控制和自校正控制器等。
1.3
设计分析了炉温的特性和单片机炉温控制系统的工作原理,完成了以 AT89S5l单片机为控制器,控制系统包括温度数据采集电路、功率控制输出电路、键盘与显示接口电路和声光报警等电路的硬件电路设计,实现了温度数据采集、处理、显示、状态切换、定时保温、系统的故障自诊断和超限声光报警等功能。
(5) 热电偶断线检测;
(6)工作温度范围-20℃~+85℃。
MAX6675
MAX 6675是一个复杂的单片热电偶数字转换器,其内部结构主要包括:低噪声电压放大器 A1、电压跟随器 A2、冷端温度补偿二极管、基准电压源、12 位AD转换器、SPI 串行接口、模拟开关及数字控制器。
其工作原理如下:K 型热电偶产生的热电势,经过低噪声电压放大器 A1 和电压跟随器 A2 放大、缓冲后,得到热电势信号 U1,再经过 S4 送至 ADC。对于K型热电偶,电压变化率为(41μV/℃),电压可由如下公式来近似热电偶的特性。
二
电阻炉温度控制系统应具备温度测量、显示、过限报警等功能,并要求具有良好的稳定性、高控制精度,以满足热处理对温度的需求。系统设计时,首先确定系统的设计目标,确定温度控制器的规格与技术指标,这对于明确设计的目的性和控制功能的逻辑性有重要的意义。然后设计系统的相关的操作规范及运行参数,为硬件设计和软件设计确定具体的目标。
<
电炉温度控制系统设计
—
摘要
热处理是提高金属材料及其制品质量的重要技术手段。近年来随工业的发展,
对金属材料的性能提出了更多更高的要求,因而热处理技术也向着优质、高效、
节能、无公害方向发展。电阻炉是热处理生产中应用最广泛的加热设备,加热时
恒温过程的测量与控制成为了关键技术,促使人们更加积极地研制热加工工业过
一、绪论- 1 -
·
选题背景- 1 -
电阻炉国内发展动态- 1 -
设计主要内容- 2 -
二、温度测量系统的设计要求- 3 -
设计任务- 3 -
系统的技术参数- 3 -
操作功能设计- 4 -
三、系统硬件设计- 5 -
]
CPU选型- 5 -
温度检测电路设计- 5 -
温度传感器的选择- 5 -
热电偶的测温原理- 6 -
MAXIM 公司推出的 MAX 6675,它是一个集成了热电偶放大器、冷端补偿、
A/D 转换器及 SPI 串口的热电偶放大器与数字转换器,可以直接与单片机接口,大大简化系统的设计,保证了温度测量的快速性与准确性。故在本设计中,为简化系统电路设计采用芯片 MAX 6675作为热电偶电势与温度的转换。
MAX6675
MAX 6675是具有冷端补偿和 A/D 转换功能的单片集成K型热电偶变换器,测温范围 0℃~1024℃,温度范围满足本台电炉的温度需要,其主要功能特点如下:
(1) 直接将热电偶信号转换为数字信号;
(2) 具有冷端补偿功能;
(3) 简单的 SPI 串行接口与单片机通讯;
(4) 12 位 A/D 转换器、℃分辨率;
单片机的应用从根本上改变了控制系统传统的设计思想和设计方法。以前采用硬
件电路实现的大部分控制功能,现在可以用单片机通过软件的方法来实现。以前
自动控制中的 PID 调节,现在可以用单片机实现具有智能化的数字计算控制、模糊控制和自适应控制。这种以软件取代硬件并能提高系统性能的控制技术称为微控技术。
(2)采用新的控制方法
常用的冷端温度补偿方法有:冷端 0℃恒温法(将冷端放在冰水混合物的恒温容器中等)、冷端温度修正法、电桥补偿法和冷端温度自动补偿法等。在本设计中采用集成芯片 MAX 6675完成冷端温度的自动补偿,可在很大程度上简化系统的设计。
K型热电偶是工业生产中最常用的温度传感器,具有结构简单、制造容易、
使用方便、测温范围宽等特点,本次设计就是选用 K 型热电偶作为系统的温度传感器。目前,在以K型热电偶为测温元件的工业测温系统中,热电偶输出的热电势信号必须经过中间转换环节,才能输入基于单片机系统。中间转换环节包括信号放大、冷端补偿、线性化及数字化等几个部分,实际应用中,由于中间环节较多,调试较为困难,系统的抗干扰性能往往也不理想。
(1) 采用先进的控制设备
随着单片机、可编程控制器与工业控制机等先进控制系统的发展,逐步取代了以前大规模的继电器、模拟式控制仪表。单片机也因其极高的性价比而受到人
们的重视和关注,获得广泛地应用和迅速地发展。
单片机具有体积小、重量轻、控制功能强、价格低与开发方便等优点。单片
机应用的意义不仅在于它的广阔范围及所带来的经济效益,更重要的意义在于,
表2-1系统主要技术参数
为了便于操作,所设计的温度控制器的面板总计五个按键、三个工作状态指示灯、一个蜂鸣器和十三个高亮 7段 LED 数码管,用于完成参数的设置和信息的显示。
其中,五个按键分别为设置、加一、减一、左移、右移,用于设置温度以及保温时间。三个工作状态指示灯分别指示暂停状态、工作状态、超限报警。十三个高亮7段LED数码管中有五位显示设定温度、五位显示实际温度、三位显示保温时间。
不同种类的两根金属导线 A、B 连接起来并保持接点的温度为 t0。若设由电压计引出的导线与金属线 A、B 连接点的温度为 t,则显现出来的热参考端温度为 0℃时,热电势和测量温度的对应表。热电偶的分度表是以冷端温度 0℃为基准进行分度的,热电偶的实际工作环境,冷端温度往往不为 0℃,不能直接使用分度表,因此必须对热电偶的冷端温度进行温度补偿。
上式中,U1 为热电偶输出电压(mV),T 是测量点温度,T0 是周围温度。
在将温度电压值转换为相应的温度值之前,对热电偶的冷端温度进行偿,冷端温度即是 MAX6675 周围温度与 0℃实际参考值之间的差值。通过冷端温度补偿二极管,产生补偿电压 U2 经 S4 输入 ADC 转换器。
在数字控制器的控制下,ADC 首先将 U1、U2 转换成数字量,即获得输出电
成一个大小的电流,这种现象称为热电效应,而这种电动势称为热电势。热电偶就是利用这种原理进行温度测量的,其中,直接用作测量介质温度的一端叫做工作端(也称为测量端),另一端叫做冷端(也称为补偿端);冷端与显示仪表或配套仪表连接,显示仪表会指出热电偶所产生的热电势,如图 3-2所示。
图3-2热电偶温度计系统原理图
(4)用三个发光二极管以不同的颜色和发光状态来指示显系统的工作状态。
整个系统最终达到的技术指标是由系统中的各个环节共同作用后完成的。比
如要提高温度检测的精度,只采用高精度的A/D转换器是不够的,还需要好的抗干扰措施、精确度高的传感器及软件线性化处理等。一般情况下,技术指标达到某个限度后,再想提高是不容易办到的,为此可能付出更多的经费与时间。设备规格是硬件投资的主要依据。如电源的规格、传感器类型、控制器类型等。根据需要确定所设计的温度控制系统的主要技术参数如表2-1所示:
温度检测电路是电阻炉温度控制系统的重要部分,其性能好坏直接决定了整个系统的性能,它承担着检测电阻炉温度并将温度数据传送到单片机的任务。
热电偶在工程上使用最为广泛的温度传感器之一,它具有构造简单、精度高、
热响应时间快、测温范围大(-200~+2000℃均可连续测温)以及性能可靠使用寿
命长的优点,在温度测量中占有很重要的地位。
范围(0~1000℃),在本设计中选用分度号为 K 的镍铬-镍硅热电偶 WRN-120,
表 3-1 所列的是常用热电偶的材料规格和线径使用温度的关系: