腐蚀案例介绍剖析
海洋管道腐蚀 案例

案例名称:北海深水油田海洋管道腐蚀案例分析1. 案例背景北海深水油田是中国海洋石油领域的重要开发区域之一,位于中国北部黄海海域。
该地区的海洋管道系统扮演着将海上采油平台产出的原油输送至陆上终端的重要角色。
然而,由于海洋环境的复杂性和海水中的各种腐蚀因素,海洋管道在长期使用过程中容易出现腐蚀问题,严重影响其安全运行和寿命。
2. 案例过程2.1 管道腐蚀背景分析北海深水油田的海洋管道主要由碳钢材料制成,碳钢在海水中容易发生电化学腐蚀。
海水中的氯离子、硫化物、氧、水分等物质与管道表面形成电化学腐蚀环境,导致管道表面发生腐蚀。
此外,海水中的微生物、水动力因素等也会加速管道的腐蚀。
2.2 腐蚀监测与评估为了及时发现管道的腐蚀情况并进行评估,油田公司采用了一系列的腐蚀监测手段。
其中包括使用超声波探伤仪对管道进行定期检测,以及安装在管道表面的腐蚀传感器,实时监测管道的腐蚀速率和程度。
2.3 腐蚀防护措施为了延长管道的使用寿命和确保安全运行,油田公司采取了一系列的腐蚀防护措施。
首先,对于新建的管道,采用了高性能防腐涂层,如环氧涂层、聚乙烯涂层等,以提供有效的物理隔离和防护。
其次,对于已经投入使用的管道,采取了阴极保护和定期防腐涂层修补等手段,以减缓腐蚀的发展速度。
2.4 腐蚀修复与维护在管道出现腐蚀问题时,油田公司及时采取了相应的修复和维护措施。
例如,对于局部腐蚀严重的区域,采用了局部修复方法,如补焊、切割更换等。
对于整体腐蚀较为严重的管道段,进行了全面的修复和更换。
3. 案例结果通过上述的腐蚀监测、防护和维护措施,北海深水油田的海洋管道腐蚀问题得到了有效的控制和处理。
管道的腐蚀速率得到了明显的降低,管道的使用寿命得到了延长,从而保障了油田的正常生产和运营。
同时,油田公司通过总结和分享这一案例,促进了海洋管道腐蚀防护技术的进一步发展和应用。
4. 启示与建议通过对北海深水油田海洋管道腐蚀案例的分析,可以得出以下启示和建议:•腐蚀监测和评估是及时发现和解决腐蚀问题的关键,油田公司应加强对管道腐蚀的监控和评估工作,以便及时采取相应的防护和修复措施。
金属腐蚀案例

金属腐蚀案例金属腐蚀是指金属在特定环境条件下受到化学或电化学作用而逐渐损坏的过程。
金属腐蚀不仅会降低金属材料的强度和耐久性,还会导致设备的故障甚至事故。
以下将介绍一些金属腐蚀的案例,以便更好地了解金属腐蚀的危害和防范措施。
案例一,海洋环境下的金属腐蚀。
在海洋环境中,金属材料容易受到盐雾、潮湿等因素的影响,导致腐蚀加剧。
一艘货轮在长时间的海上运输后,船体上的金属结构出现了严重的腐蚀,甚至出现了漏水的情况。
这不仅影响了货轮的使用寿命,还可能危及船员的生命安全。
为了解决这一问题,船舶制造商采用了防腐涂层和防腐处理技术,有效延长了船体的使用寿命。
案例二,化工设备中的金属腐蚀。
在化工生产过程中,许多设备和管道都是由金属材料制成的。
然而,由于化工生产中存在腐蚀性介质和高温高压等因素,金属材料容易受到腐蚀的影响。
某化工企业的反应釜在使用一段时间后出现了严重的腐蚀,导致了设备的泄漏和停产。
为了解决这一问题,企业采用了耐腐蚀合金材料和防腐涂层等技术,有效提高了设备的耐腐蚀性能。
案例三,建筑结构中的金属腐蚀。
在建筑领域,金属材料广泛应用于桥梁、钢结构等建筑中。
然而,由于大气中的雨水、酸雨等因素,金属结构容易受到腐蚀的影响。
某城市的大型钢桥在使用多年后出现了严重的腐蚀,影响了桥梁的安全性能。
为了解决这一问题,城市管理部门采用了防腐涂层和定期检测维护等措施,有效延长了桥梁的使用寿命。
结语。
以上案例充分说明了金属腐蚀对设备、建筑等的危害,也表明了采取有效的防腐措施对延长金属材料的使用寿命具有重要意义。
因此,我们在生产和生活中应加强对金属腐蚀的认识,采取有效的防腐措施,保护好我们的设备和建筑结构,确保其安全可靠地运行。
案例▕史上分析最透彻的腐蚀破坏事故(7

案例▕史上分析最透彻的腐蚀破坏事故(7每期编制两篇真实腐蚀案例,希望大家喜欢。
点击页面底部“阅读原文”可查看腐蚀案例5-6事例7某厂生产氯化锌的方法是,将镀锌厂回收的锌和其它来源的锌用盐酸溶解,然后用化学药剂处理,再在浓缩槽中加热蒸发。
浓缩槽中使用的镍加热管发生孔蚀,寿命很短。
于是用锆制加热管在浓缩槽中进行了一个月试验,没有发现腐蚀问题,但锆制加热管仅使用了6个月就发生腐蚀破坏。
经过调查找出了原因:有的镀锌厂镀锌工艺配方中使用了氟化物,因此回收的锌中含氟化物。
评述锆是一种难熔金属,虽然锆的标准点位很负,化学性质活泼,但由于表面易生成致密的保护性氧化膜,所以具有优良的耐蚀性。
锆对碱和许多酸(包括氢碘酸和氢溴酸)耐蚀性很好,但锆不耐王水和氢氟酸的腐蚀,因为它们能使锆生成;络离子而溶解。
尽管锆对浓度低于35%、温度低于100℃的盐酸是耐蚀的,在本事例中耐蚀性应无问题,但由于回收锌中夹带氟化物,因而很快发生腐蚀破坏。
以上三个事例的共同点是:实际生产环境中含有某种杂质,对设备材料造成了严重的腐蚀问题。
而作为选材依据的腐蚀数据资料、使用经验、实验结果并没有包含这种环境细节。
相同的生产过程,相同的设备材质,往往腐蚀情况出现较大差异,一个重要原因就是杂质。
这方面的事例还有很多,如:1.有的硫酸生产厂为用户提供废酸处理设备,因为用户难以使用不影响环境的方法处理废酸。
处理工艺是:将被有机物污染的废酸焚烧,热气体通过废热锅炉回收热量。
有一个这样的厂一次发现废热锅炉钢管寿命突然很短。
检查结果表明,腐蚀是由于含磷酸盐和铅量很高的熔渣造成的,原来一个用户的废酸中含有这些组分。
2.某厂一台蒙乃尔合金制的石油化工装置萃取设备用于处理50%~65%硫酸和乙醇(温度29~38℃),热交换器管子预期寿命5年,但在5周就出乎预料发生破坏,更换的管子不到3周又发生破坏;腐蚀部位主要是焊缝。
溶液中所含的铜离子很高,难以用合金的简单溶解来解释。
海洋管道腐蚀 案例

海洋管道腐蚀案例一、引言随着我国海洋石油、天然气资源的开发,海洋管道在国民经济中的地位日益突出。
然而,海洋环境的复杂性使得管道腐蚀问题日益严重,不仅影响了管道的使用寿命,还可能引发安全隐患和经济损失。
本文将对海洋管道腐蚀的原因、影响及防腐措施进行探讨,并通过案例分析提出相应的建议。
二、海洋管道腐蚀的原因1.环境因素海洋环境中的水分、盐分、微生物等成分会对管道产生腐蚀。
其中,氯离子是导致腐蚀的主要原因,它能够加速金属的电化学腐蚀。
此外,海水中的溶解氧、硫酸盐等也对管道腐蚀有重要影响。
2.管道材料因素管道材料的化学成分、晶粒大小、热处理过程等都会影响管道的耐腐蚀性能。
一般来说,金属管道材料中的杂质、晶界、应力等因素容易导致腐蚀疲劳和应力腐蚀开裂。
3.施工因素管道施工过程中,焊接、防腐层破损、施工缺陷等可能导致管道局部腐蚀。
此外,施工时对管道的保护措施不足,如临时防腐措施不到位,也会加速管道的腐蚀。
三、海洋管道腐蚀的影响1.管道性能下降管道腐蚀会导致管道壁厚减薄、裂纹、凹坑等缺陷,从而降低管道的强度和密封性能。
2.安全隐患腐蚀管道在运行过程中容易出现泄漏、断裂等事故,不仅影响正常的生产运营,还可能引发火灾、爆炸等严重事故。
3.经济损失管道腐蚀导致的泄漏、停产等现象会给企业带来巨大的经济损失。
此外,腐蚀管道需要定期维修、更换,增加了运营成本。
四、海洋管道防腐措施1.选用耐腐蚀材料在选材时,应充分考虑管道所处环境的腐蚀性,选择具有良好耐腐蚀性能的材料。
例如,在氯离子浓度较高的海域,可以选用镍基合金、钛合金等材料。
2.涂层保护在管道表面涂覆一层防腐涂料,可以有效阻止腐蚀介质与管道金属的接触,从而降低腐蚀速率。
涂层材料可以选择聚乙烯、环氧煤沥青等。
3.阴极保护通过外加电流或牺牲阳极等方式,使管道表面产生负电位,从而抑制金属的电化学腐蚀。
阴极保护系统包括直流电源、电缆、阳极等部件。
4.定期检测与维护定期对管道进行检测,发现腐蚀缺陷及时进行修复。
失效分析典型案例分享--镍腐蚀
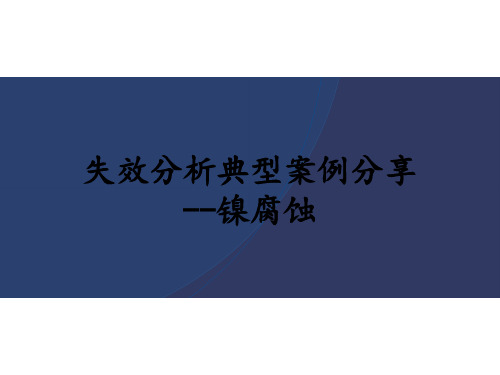
沉锡
沉银
无铅喷锡
(Immersion Tin) (Immersion silver) (Lead free HASL)
OSP
在电路板裸铜表面 在电路板裸铜表 在电路板裸铜表 在电路板裸铜表面 沉积形成一层平整 面经化学置换反 面经化学置换反 经热风整平形成一 而致密的有机覆盖 应形成一层洁白 应形成一层洁白 层较光亮而致密的 层,厚度约0.2而致密的锡镀层, 而致密的银镀层, 无铅覆盖锡合金层, 0.6um,既可保护 厚度约0.7-1.2um。 厚度约0.15-0.4um。 厚度约1-40um。 铜面,又可保证焊
表面易被污染而 影响焊接性能
表面易被污染,银 面容易变色,从而 影响焊接性能和外 观
表面处理温度高, 可能会影响板材和 阻焊油墨的性能
表面在保存环境差 的情况下易出现 OSP膜变色,焊接 不良等
电镍金后还经 过多道后工序, 表面处理后若 受到污染易产 生焊接不良
成本很高
完成沉锡表面处 理后如再受到高 温烘板或停放时 间较长,则可导 致沉锡层的减少
u
Pu
Pu
Pu
P uP
Pu P
uP
Pu P
u
u
Ni
Ni P
Ni
Ni
Ni
P
Ni
Ni
Ni P
Ni Ni
Ni P
Ni
Ni
Ni
P
Ni
富磷层
Ni
Ni P
Ni
Ni
Ni P
Ni
Ni
Ni
腐蚀品事故案例分系

第八类腐蚀品1、硝酸惹祸的两起事故[案情介绍] 案例一1973年11月3日,欧罗巴帕美国航空公司的一架喷气式货运飞机自纽约机场起飞。
数分钟后,机场的地面指挥系统就接到飞机机长的报告:机上发生异常状况,机舱内着火。
尽管采取了自救措施仍未见效果。
35分钟后,飞机坠毁于波士顿机场,三名机组人员全部死亡。
经有关部门对事故进行深入调查发现:在所装的货物中有一批硝酸。
其包装不符合运输要求,是桶装容器外套木板箱,中间用木屑作衬垫。
货物在装上飞机时,作业人员没有注意箱顶上“该面朝上”的指示标志,而是随意堆放。
由于箱内货物倒置,硝酸自桶中渗漏出来,与木屑相混,自燃而引起火灾。
案例二1989年2月6日下午4时20分,从西安开往济南的207次列车行至三门峡铁门路段时,8号车厢尽头的行李架上突然冒出一股呛人的烟雾,旅客纷纷夺路而逃。
车上秩序顿时大乱。
这时列车员与乘警不顾个人安危,冲上去抓起那只冒烟的手提包,打开车窗扔到窗外,接着又拉下紧急刹车的制动阀。
经现场展开的调查,查实了手提包的主人是河南省灵宝县程村乡的一个叫朱红军的农民。
他携带了一瓶硝酸,逃过车站的检查后自以为没事了,没想到手提包在行李架上倾倒,硝酸自瓶口渗出,险些酿成大祸。
就是这样,奋不顾身扔包的女列车员的手背已被多次灼伤,身上的衣服也被腐蚀后发脆、变色。
这个肇事者当即受到治安拘留的处理。
[事故原因分析] 硝酸,联合国编号为2031,属第八类·腐蚀品,是具有严重危险性的物品。
硝酸透明、无色,通常因溶有二氧化氮而呈红棕色。
有独特的窒息性气体。
硝酸的化学性能相当活泼,具有极强氧化性,几乎可以与一切金属、非金属起反应。
硝酸中溶有的二氧化氮越多,其氧化能力越强,腐蚀性就越大。
硝酸在发生腐蚀反应时一般总会生成有毒气体一氧化氮或二氧化氮,从而对人体生成危害。
硝酸的氧化能力能引起木材和其他纤维素物品燃烧。
一般常见的有机物如松节油、醋酸、丙酮、乙醇等与浓硝酸相混即发生爆炸。
史上分析最透彻的腐蚀破坏事故(5-6)

史上分析最透彻的腐蚀破坏事故(5-6)事例5一个碳钢容器装浓的乙二醇脚料,温度150℃。
脚料中含0.2%NaOH。
使用不久,碳钢容器发生严重的全面腐蚀,器壁减薄。
评述碳钢在NaOH溶液中的腐蚀与碱浓度和温度有很大关系。
在常温稀碱溶液中,碳钢腐蚀速度很小,属于耐蚀材料,这是因为表面生成了致密的保护膜。
因此碳钢是处理常温稀碱溶液的常用结构材料。
当NaOH浓度大于30%,表面膜的保护性能降低,腐蚀速度增大。
当NaOH 浓度大于50%,碳钢发生强烈腐蚀。
随温度升高,这一过程变得更显著。
碱浓缩罐中的腐蚀和锅炉碱腐蚀就是这类实例。
一般说来,碳钢材料可用于处理87℃以下、浓度小于50%的NaOH溶液。
当材料中存在应力,碳钢还会发生应力腐蚀破裂(关于应力腐蚀破裂,在以后的事例中还要介绍)。
本事例中虽然温度较高,但脚料中NaOH含量很低。
所以在使用中比较注意碳钢是否会发生应力腐蚀破裂,这当然是无可非议的。
但忽略了碳钢的全面腐蚀问题,结果造成了严重破坏,原因是没有考虑到设备的具体情况。
这里虽然相对于整个脚料NaOH浓度很低,但相对于混合物中的水,NaOH的浓度就大得多,即这种有机化合物脚料中的水时NaOH浓溶液;加之温度较高,故发生了很高的全面腐蚀速度。
我们反复强调,在为设备选择制造材料时,首先要把设备将服役的环境条件搞清楚,所谓环境条件,当然是最主要的是介质的种类、浓度和温度。
腐蚀数据手册和图标一般也是按照这三个条件来组织和表达数据的。
但是,对于介质的浓度,除了应注意主体浓度,还应注意介质浓度的不均匀,比如局部区域介质因浓缩而比主体浓度高很多。
本事例就是这种情况,因此这里的选材时错误的,考虑到NaOH 局部浓度,温度亦较高,应选用更耐蚀的材料,如304型不锈钢。
事例6某厂输送35%硫酸的泵,原来的材质为20号合金。
在20号合金泵损坏后,改用哈氏合金B。
这是因为人们都知道哈氏合金B对中等浓度硫酸的耐蚀性很好。
但哈氏合金B泵只用两周就发生腐蚀破坏。
金属腐蚀事故案例分析

金属腐蚀事故案例分析某石油化工厂常减压车间减粘事故线在109号阀后管道穿孔,引起火灾,使常压工段停工。
破口在管线底部距法兰盘50mm处,破口呈三角形,高85mm,宽72mm。
事故线介质为减压蒸馏塔底渣油,温度400℃,含硫量1.2%,流速0.3m/s。
事故线材质为20号钢,原厚度7mm,使用2年被蚀穿,最大腐蚀率达3.5mm/a。
评述与上一事例一样,渣油系统的腐蚀主要为高温硫腐蚀。
该厂渣油硫含量高(1.2%),温度达400℃,H2S和H2S分解生成的活性S反应生成无保护性的FeS,所以对碳钢腐蚀十分严重。
另外,流速和流动状态对高温硫腐蚀也有很大影响。
事故线渣油流速为0.3m/s,平常操作中109阀开度不足二分之一,在阀后一定距离流体界面最小,流速最大(约为0.8m/s),渣油直接冲击管线底部,故对该处管线产生严重磨损腐蚀,造成穿孔。
所以,应选择更耐腐蚀和磨损的材料。
比如管道可选低合金钢Cr5Mo,弯头和阀后管道可选1Cr18Ni8不锈钢。
介质流速也是一个很重要的环境因素。
但流速对材料腐蚀的影响又是很复杂的。
不过在很多情况下流速增大将使材料腐蚀率增加。
因为当流速增大时腐蚀剂的供应会更充足,使浓度极化降低;腐蚀产物会更容易流走,难以对被腐蚀金属表面提供保护。
特别当介质流速很高时,会造成一种破坏性很大的局部腐蚀形态:磨损腐蚀。
这是由于高速流动介质产生的机械冲刷和腐蚀的联合作用所造成的破坏。
流体的冲刷使材料表面保护膜被破坏,露出新鲜金属表面,遭受介质的腐蚀;腐蚀造成表面不平,流动紊乱,形成涡流和涡旋,进一步增大了流体的冲刷。
这种相互促进的联合作用导致设备壁厚严重减薄,最终穿孔。
流动系统中的设备,如管道、管件、阀门、搅拌器、泵、叶轮、汽轮机叶片等,磨损腐蚀是一种常见的腐蚀破坏原因。
前面两个事例都属于高速高温硫化物环境中的磨损腐蚀破坏。
对这种环境中工作的设备,在选材时不仅要考虑到介质的腐蚀性,还要考虑介质流速和流动状态与腐蚀的联合作用。
- 1、下载文档前请自行甄别文档内容的完整性,平台不提供额外的编辑、内容补充、找答案等附加服务。
- 2、"仅部分预览"的文档,不可在线预览部分如存在完整性等问题,可反馈申请退款(可完整预览的文档不适用该条件!)。
- 3、如文档侵犯您的权益,请联系客服反馈,我们会尽快为您处理(人工客服工作时间:9:00-18:30)。
加工高酸低硫原油腐蚀案例
(一)精蜡厂原油性质
(二)精蜡厂腐蚀现状及采取措施 (三)精蜡厂腐蚀案例
1
(一)原油性质
•我厂加工的原油为河南油田开采的魏岗原油、采油一厂稀油 和采油二厂稠油混合的南阳混合稀油和混合稠油。
•正常情况下,加工的稀油与稠油比例为68:32,极端情况为 61:39。
(三)腐蚀案例
初步结论:
1Cr5Mo中为Cr含量4-6,15CrMo中Cr含量≤1,抵抗高温硫腐蚀的作用随着 Cr含量的增高而增强。因此,用错材质为本次爆裂事故的主要原因。 工艺管道的走向:反应釜与换热器之间标高差距较大,导致流体在弯头处 流速较快,导致冲刷作用明显。
(三)腐蚀案例
(三)腐蚀案例
装置情况:2010年5月,改质装置搬迁,对相应管线进行了更换。查询图
纸S2010550-艺-1工管表,显示:该管段材质为1Cr5Mo,为∅159×7.1无缝 钢管,设计压力为0.88MPa,设计温度为543℃,介质:高温油气。破裂的
弯头为90E(L)150Ⅱ-Sch40长半径无缝弯头,材质1Cr5Mo。
混合原油 混合原油 60.9:39.1 68:32 11.85 8.57 8.18 <0.05 2.33 11.21 9.47 6.81 <0.05组分 密度20℃,㎏/m3 K值 温度范围 第二关键组分 密度20℃,㎏/m3 K值 原油类别
250~275℃ 250~275℃ 830 830.15 11.86 11.84 395~425℃ 395~425℃ 892.68 890.79 12.73 11.97 低硫中间 低硫中间 基 基
2008年精蜡厂原油评价报告
南阳稠油和稀油的酸度曲线
图6
410 390 370 350 330 310 290 270
酸
度
曲
线
稠油
酸度KOHmg/100ml
250 230 210 190 170 150 130 110 90 70 50 30 10 -10 60 90 120 150 180 210 240 270 300 330 360 390 420 450 480 510
混合60.9:39.1 混合68:32 IBP-180 IBP-180 4.7 5.2 742 739.68 0.8 65 0.77 59
0.81
0.73
分析:该处原料中含有腐蚀介质硫。
(三)腐蚀案例
测厚情况:
弯头处:原始壁厚8mm
3.9mm 1.8mm 2.0mm
(三)腐蚀案例
测厚情况:
直管段:整体减薄,厚度均≤3mm,原始壁厚7mm
分析:为整体的均匀减薄。
(三)腐蚀案例
管内:
管内存有大量片状焦炭状物 质,测量出该物质中铁含量 为37.5%。
打开保温时焦炭涌出, 占据管道内空间约1/3
(三)腐蚀案例
光谱分析:
检测部位 弯头1 弯头2 直管 Cr 0.91 0.85 0.97 Mn 0.74 0.85 0.55 Mo 0.57 0.6 0.54 Ti 0.99 0.78 Zn 1.43 1.23 Fe 95 95.43 97.94 11-4 Cr 显示材质
2008年精蜡厂原油评价报告
南阳稠油和稀油的含硫量曲线
图3 1970 1880 1790 1700 1610 1520 1430 1340 1250 硫含量曲线
稠油
硫含量μ g/g
1160 1070 980 890 800 710 620 530 440 350 260 170 80 -10 50 80 110 140 170 200 230 260 290 320 350 380 410 440 470 500 530
(一)原油性质
原油品种
Fe Ni V Na Cu
稀油
8.29 13.5 0.6 <0.05 0.3 250~275℃ 816.1 12.03 395~425℃ 882.5 12.08 低硫石蜡中间 基
稠油
17.4 0.9 20.0 <0.05 5.5 250~275℃ 860.0 11.43 395~425℃ 908.4 11.74 低硫环烷中 间基
(一)原油性质
原油品种 ㎏/m3 80℃ 运动粘度㎜2/s 100℃, 凝点 ℃ 残炭 m% 酸值 mgKOH/g 蜡含量 m% 胶质 m% 沥青质 m% 硫含量 m% 氮含量 m% 水含量 m% 盐含量 mgNaCl/L 密度 20℃ 稀油 882.2 10.89 7.845 31 4.06 0.159 26.91 8.57 0.10 0.129 0.37 0.04 23.14 稠油 混合原油 混合原油 60.9:39.1 68:32 897.99 26 29 5.01 0.92 23.75 10.28 0.116 0.16 0.46 0.16 24.70 933.5 901.57 957.4(40℃) 45.69 12.5 21 27 7.02 5.21 2.53 1.08 17.05 23.1 13.90 10.7 0.15 0.12 0.225 0.17 0.66 0.48 0.41 0.18 28.00 25.04
后随沸点的升高而逐渐增大; 南阳混合稀油的硫含量比稠油低,140℃前硫含量较低,140--380℃硫含量
随沸点逐渐增加,380--440℃逐渐降低,然后增加。硫含量在375℃以前随
沸 点 的 升 高而 增 加 , 在 375℃ 时 , 达一 峰 值 840μg/g , 随 后 呈 波 动 状 至 435℃时,出现谷底660μg/g,随后随沸点的升高而逐渐增大。
稀油
馏分中沸点温度
℃
2008年精蜡厂原油评价报告
酸度曲线说明
南阳稠油的酸度在 250℃前不到 10KOHmg/100ml, 250--370℃随沸点的增加
而增加较快,在370--410℃酸度逐渐降低,而后又逐渐升高。小于250℃时酸
度波动变化不大,在8 mgKOH/100ml左右,之后迅速增加,至370℃时出现 一 高 峰 为 348mgKOH/100ml , 后 下 降 , 在 415℃ 时 至 谷 底 250mgKOH/100ml,之后再次随沸点升高迅速上升。 南阳混合稀油的酸值比较低,均在 20 KOHmg/100ml以下。因此,环烷酸的 腐蚀主要从270℃以后逐渐加大,对应的是常减压装置E1019出口之后管线及 设备。小于 200℃的窄馏分酸度较低,都小于 1mgKOH/100ml ,之后逐渐增 加 , 至 350℃ 时 为 14.88mgKOH/100ml , 在 380℃ 时 达 到 一 峰 值 0.182mgKOH/g ,随后降低,于 430℃降至 0.12mgKOH/g ,之后逐渐增加, 到520℃时达到最高,为0.193mgKOH/g。
混合稀油 IBP-130 IBP-180 3.40 7.47 718.0 739.0 1b 1a 1.0 0.7 25 42 0.00047 0.00043 1 0.40 0.51 —— 36 43.96 27.54 55.51 57.67
稠油 IBP-180 0.39 791.6 —— 3.8 750 —— 9.92 ——
2008年精蜡厂原油评价报告
原油评价结论(腐蚀性角度): 精蜡厂现阶段加工原油为中质原油,硫含量较低(平均 为0.17%),酸值较高(平均为1.58mgKOH/g,极端值 达到2.53mgKOH/g),N含量、金属离子中Ni、V含量 较高。为典型的低硫高酸原油。
精蜡厂原料油酸值变化趋势
南阳原油性质变化曲线
(三)腐蚀案例
2014年8月10日,我厂汽油芳构化装置反应釜高温油气至E102原料汽化器 BIU600-2.64/2.97-85-6/25-4管线在二层平台上方弯头处(DN150)处发
生爆裂,高温油气大量喷出,噪音强烈,导致装置立即停工。现场查看保
温处冲开,看到弯头处有一孔洞,直径约80mm,边缘不规则,可见明显减 薄。
稀油
馏分中沸点温度 ℃
2008年精蜡厂原油评价报告
含硫曲线说明
南阳稠油的硫含量在190℃前随着沸点的升高而降低,190--240℃硫含量基
本不变, 240--390℃硫含量增加较快,腐蚀逐渐增大, 390--470℃硫含量 逐渐降低,随后逐渐增加。硫含量在 395℃以前随沸点的升高而增加,在
395℃时达一峰值为 1790μg/g ,随后下降至 460℃出现谷底 1570μg/g ,随
1.8 1.6 1.4 1.2 1 0.8 0.6 0.4 0.2 0 2002年 2003年 2004年 2005年 2006年 2007年 2008年
酸值 硫含量(%)
随着河南油田的深度开采,原油劣质化情况严重,我厂原料油酸值逐渐升高, 预计未来酸值将继续上升。
(二)精蜡厂腐蚀现状及应对措施
原料油性质变化:现阶段加工原料油酸值比装置原设计防护值上升了3.16 倍,含硫量、金属离子含量、含盐量均有所增加 ;
分析:该装置自建成后运行至今,工艺及设备均未经过改动,装置负荷比 符合设计要求。在此温度下,管内存在气液两相。且现场弯头及管道走向
是向下,存在冲刷可能;
(三)腐蚀案例
重整料及直馏汽油馏分的性质(即进改质装置原料性质)
原油品种 温度范围℃ 收率 m% 密度 (20℃) kg/m3 铜片腐蚀(50℃,3h) 氮含量 μg/g 硫含量 μg/g 硫醇硫 m% 实际胶质 mg/100ml 酸度 mgKOH/100ml 辛烷值 芳烃(三苯)潜含量 芳烃收率指数N+2A
(三)腐蚀案例
光谱分析:
分析:由此可见,现场管道实际材质为15CrMo ,而不是原图纸要求的1Cr5Mo,存在使用材质错误问题。
(三)腐蚀案例
初步结论: 属于高温硫腐蚀,在API581中温度很高的情况下,即使硫的含量不高,腐 蚀速率也较大。使用时间四年,年腐蚀速率超过1.5mm/a。(通常认知高 温硫腐蚀发生在240℃-500℃之间,那在530℃情况下,活性硫是否存在? 或者在腐蚀行为中起到多大的作用?或者是在高温情况下非活性硫发挥了 较大的作用?) 采取措施:在本次大修中整体更换为1Cr5Mo材质,且初步商定三年一换。 (两者材质存在不同,但在此种环境下1Cr5Mo能否坚持一个周期?)