甲醇三塔精馏工艺技术
三塔精馏操作
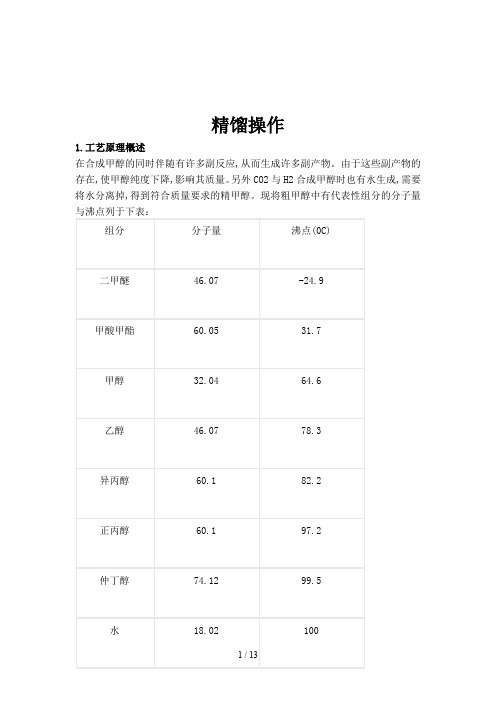
精馏操作1.工艺原理概述在合成甲醇的同时伴随有许多副反应,从而生成许多副产物。
由于这些副产物的存在,使甲醇纯度下降,影响其质量。
另外CO2与H2合成甲醇时也有水生成,需要将水分离掉,得到符合质量要求的精甲醇。
现将粗甲醇中有代表性组分的分子量由表可知,粗甲醇中的杂质可以分为两大类:一类包括二甲醚、甲酸甲酯等,它们的沸点低于甲醇;另一类包括乙醇、丙醇、水、丁醇等,它们的沸点高于甲醇沸点。
本工序正是利用这两类物质沸点的差异,采用三塔精馏工艺,在第一塔中除去沸点低于甲醇沸点的物质,在第二塔和第三塔中采出符合国家标准的精甲醇。
把液体混合物经过多次部分气化和部分冷凝,使液体分离成相当纯的组分的操作称为精馏。
连续精馏塔可以想象是由一个个简单蒸馏釜串联起来,由于原料液中组分的挥发度不同,每经过一个蒸馏釜蒸馏一次,蒸汽中轻组分的含量就提高一次,即yn+1>yn>X(y代表气相组成,X代表液相组分),增加蒸馏釜的个数就可得到足够纯的轻组分,而塔中残液中所含轻组分的量会越来越少,接近于零。
将这些蒸馏釜叠加起来,在结构上加以简化即成为精馏塔。
随着精馏操作压力的提高,液体混合物的沸点相应提高,加压精馏塔顶甲醇的冷凝温度相应提高,利用加压精馏塔顶较高温度成品甲醇的冷凝热来作为常压精馏塔再沸器的热源,这样可以降低甲醇精馏的蒸汽消耗。
本工序就是利用预蒸馏塔、加压精馏塔、常压精馏塔分离出粗甲醇中的轻组分物质和重组分物质而得到产品精甲醇。
三塔均用组合式导向浮阀塔,它比传统的浮阀塔板有更好的传质、传热性能。
2.工艺流程说明从合成工段送来的浓度为93%左右的粗甲醇到粗甲醇贮槽,经粗甲醇泵打到粗甲醇预热器,由蒸汽冷凝水提温至65℃左右进入预蒸馏塔,预蒸馏塔下部的预塔再沸器采用0.5MPa,170℃过热蒸汽间接加热液体粗甲醇,保持温度在75-80℃左右,塔顶温度用回流液控制在70℃左右,为了防止低沸点组分在塔顶冷凝,同时尽量减少甲醇损失,塔顶采用两级冷凝,一级冷凝器温度控制在65℃,二级冷凝器温度控制40℃。
甲醇三塔精馏工艺节能探讨
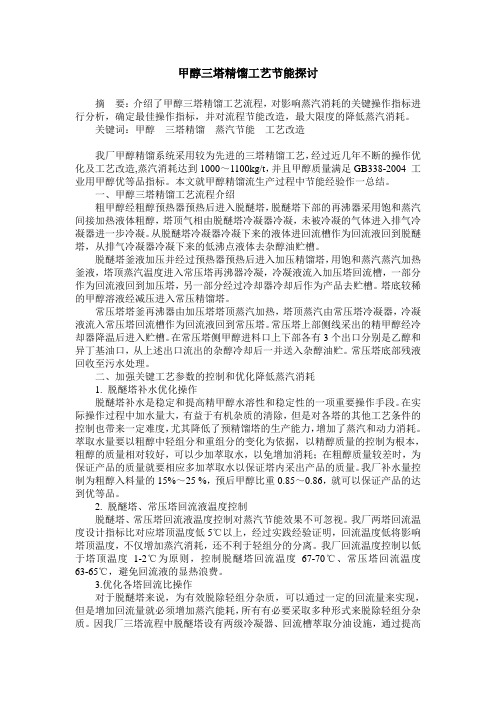
甲醇三塔精馏工艺节能探讨摘要:介绍了甲醇三塔精馏工艺流程,对影响蒸汽消耗的关键操作指标进行分析,确定最佳操作指标,并对流程节能改造,最大限度的降低蒸汽消耗。
关键词:甲醇三塔精馏蒸汽节能工艺改造我厂甲醇精馏系统采用较为先进的三塔精馏工艺,经过近几年不断的操作优化及工艺改造,蒸汽消耗达到1000~1100kg/t,并且甲醇质量满足GB338-2004 工业用甲醇优等品指标。
本文就甲醇精馏流生产过程中节能经验作一总结。
一、甲醇三塔精馏工艺流程介绍粗甲醇经粗醇预热器预热后进入脱醚塔,脱醚塔下部的再沸器采用饱和蒸汽间接加热液体粗醇,塔顶气相由脱醚塔冷凝器冷凝,未被冷凝的气体进入排气冷凝器进一步冷凝。
从脱醚塔冷凝器冷凝下来的液体进回流槽作为回流液回到脱醚塔,从排气冷凝器冷凝下来的低沸点液体去杂醇油贮槽。
脱醚塔釜液加压并经过预热器预热后进入加压精馏塔,用饱和蒸汽蒸汽加热釜液,塔顶蒸汽温度进入常压塔再沸器冷凝,冷凝液流入加压塔回流槽,一部分作为回流液回到加压塔,另一部分经过冷却器冷却后作为产品去贮槽。
塔底较稀的甲醇溶液经减压进入常压精馏塔。
常压塔塔釜再沸器由加压塔塔顶蒸汽加热,塔顶蒸汽由常压塔冷凝器,冷凝液流入常压塔回流槽作为回流液回到常压塔。
常压塔上部侧线采出的精甲醇经冷却器降温后进入贮槽。
在常压塔侧甲醇进料口上下部各有3个出口分别是乙醇和异丁基油口,从上述出口流出的杂醇冷却后一并送入杂醇油贮。
常压塔底部残液回收至污水处理。
二、加强关键工艺参数的控制和优化降低蒸汽消耗1. 脱醚塔补水优化操作脱醚塔补水是稳定和提高精甲醇水溶性和稳定性的一项重要操作手段。
在实际操作过程中加水量大,有益于有机杂质的清除,但是对各塔的其他工艺条件的控制也带来一定难度,尤其降低了预精馏塔的生产能力,增加了蒸汽和动力消耗。
萃取水量要以粗醇中轻组分和重组分的变化为依据,以精醇质量的控制为根本,粗醇的质量相对较好,可以少加萃取水,以免增加消耗;在粗醇质量较差时,为保证产品的质量就要相应多加萃取水以保证塔内采出产品的质量。
甲醇精馏工艺三塔双效向三塔三效升级的研究与应用

128 |常压塔回流槽。
在常压塔下部设有侧线采出口,所采次甲醇溶液经次甲醇冷却器冷却后,进入次甲醇贮槽,经次甲醇泵送入罐区。
常压塔回流槽内的甲醇液,经常压塔回流泵加压。
一部分送至常压塔顶作为回流,一部分经精甲醇冷却器作为采出送罐区。
回流槽中气相送至排放槽洗涤后放空,洗涤下来的甲醇水去地下槽。
常压塔塔底废水通过残液泵经残液冷却器送至生化处理。
甲醇精馏三塔双效工艺流程简图如图1所示。
图1 甲醇精馏三塔双效工艺流程简图1.2 三塔双效向三塔三效工艺转变的方法甲醇精馏的工艺流程的优化控制对节能降耗、提高经济效益有着至关重要的作用。
为了高效利用加压塔的塔顶甲醇蒸汽,在原三塔双效基础上将工艺流程升级为三塔三效工艺。
三塔三效是指加压塔与常压塔热量耦合称为二效精馏,加压塔与预精馏塔热量耦合称之为三效精馏,因而形成三塔三效的工艺。
甲醇精馏三塔三效工艺流程较三塔双塔工艺流程相比,其区别在于加压塔向常压塔供热的基础上同时向预塔供热,达到节约蒸汽又节约冷却水的目的。
通过三塔三效的热耦合工艺,充分利用加压塔塔顶甲醇气相焓值,分配给预精馏塔和常压精馏塔再沸器提供热量,达到进一步节能降耗目的。
将加压塔顶甲醇蒸汽的能量分成两部分,一部分给常压塔再沸器加热,满足常压塔精馏所需能量,剩0 引言甲醇[1]是一种重要的有机化工基础原料,应用广泛。
2016年甲醇世界需求量达到9500万吨,其中我国占比80%[2],国内需求量大,产品质量要求较高。
而在甲醇化工生产过程中,分离单元直接决定最终产品的质量和收率。
其中占据分离方法主导地位的就是精馏,精馏操作是一个高耗能过程[3-5]。
据不完全统计化工过程中40%~70%的能耗用于分离,而其中95%的为精馏能耗[6]。
我国是能耗大国,随着能源的日益短缺,精馏过程如何能够更节能一直是挖潜降耗的热点。
本文就从精馏塔节能改造这一主题展开了简单的研究,以甲醇精馏三塔工艺作为研究对象,重点阐明介绍一种三塔双效工艺[7]向三塔三效工艺升级转变的方法。
浅述三塔精馏技术在甲醇生产中的运用

浅述三塔精馏技术在甲醇生产中的运用摘要三塔精馏技术具有产品质量高、操作容易、能耗低等优点,其在甲醇生产中的应用,能够有效提高甲醇生产效益,因此应结合甲醇生产要求,积极发挥三塔精馏技术优势,优化三塔精馏工艺,全面提高甲醇生产质量。
本文简要介绍了甲醇生产现状,分析了三塔精馏技术在甲醇生产中的运用。
关键词三塔精馏技术;甲醇生产;运用甲醇生产过程中不仅会发生很多副反应,而且产生很多杂质,三塔精馏技术是一种新型精馏技术,通过在甲醇生产中运用三塔精馏技术,可以有效减少甲醇损耗,提高甲醇生产质量。
1 甲醇生产现状1.1 甲醇酸度不达标由于预塔蒸汽用量较多,为了节约蒸汽,预塔回流量减小,并且由于不凝气管线中含有大量的甲醇积液不能及时回收,因此只能将原本的不凝汽温度下调,但是这样又造成甲醇酸度过高,如果采用加碱量方式,预塔底部pH值会明显提升,最终严重影响甲醇酸度。
1.2 甲醇浪费严重根据甲醇的生产流程,常压塔和加压塔在实际应用中相互制约、相互影响,为了控制两塔的气液平衡、物料平衡和热量平衡,必须做好常压塔和加压塔的控制处理。
甲醇生产操作时,通过控制加压塔回流量,降低蒸汽用量,甲醇生产负荷较高,甲醇采出量较大,这使得甲醇含水量较高,并且加压塔中蒸汽上升量相对较少,对于常压塔的供热量也较少,这时常压塔的运行负荷远远低于标准限值,然而由于物料在常压塔和加压塔分配存在较大差异,这使得常压塔供热量较少,无法保障常压塔运行负荷,上升蒸汽量较少,甲醇采出量不足,塔顶区域处于负压状态。
在某些甲醇生产工艺中,为了调整常压塔负压状态,往往选择提高回流温度或者增加回流量的方式,但是其實际应用效果较差,提高回流温度,会使得甲醇采出温度大幅度上升,由于甲醇容易挥发,因此在生产过程中会浪费大量的甲醇,还会污染周围环境。
虽然加大回流量在一定程度上能够保持塔顶处于正压状态,然而回流量过大,往往会降低灵敏板温度,由于常压塔底部几乎没有热负荷,这样更加加剧了热负荷上升的状态,甲醇轻组分不断向下移动,造成大量甲醇融入废水中被排出,造成生产原料的浪费[1]。
甲醇三塔精馏工艺技术
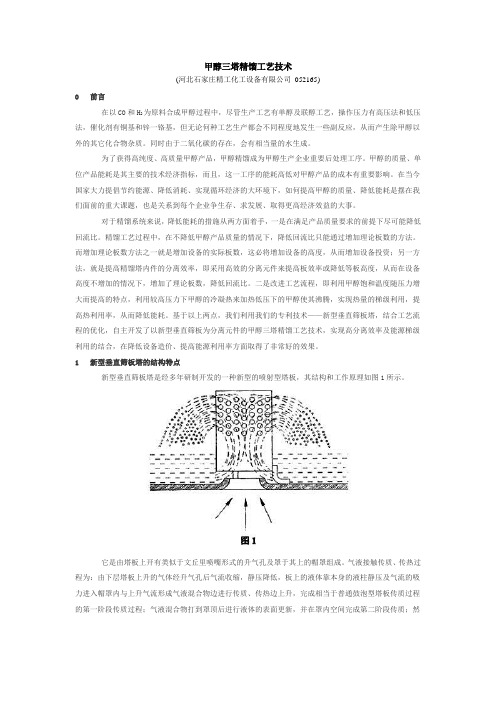
甲醇三塔精馏工艺技术(河北石家庄精工化工设备有限公司052165)0 前言在以CO和H2为原料合成甲醇过程中,尽管生产工艺有单醇及联醇工艺,操作压力有高压法和低压法,催化剂有铜基和锌一铬基,但无论何种工艺生产都会不同程度地发生一些副反应,从而产生除甲醇以外的其它化合物杂质。
同时由于二氧化碳的存在,会有相当量的水生成。
为了获得高纯度、高质量甲醇产品,甲醇精馏成为甲醇生产企业重要后处理工序。
甲醇的质量、单位产品能耗是其主要的技术经济指标,而且,这一工序的能耗高低对甲醇产品的成本有重要影响。
在当今国家大力提倡节约能源、降低消耗、实现循环经济的大环境下,如何提高甲醇的质量、降低能耗是摆在我们面前的重大课题,也是关系到每个企业争生存、求发展、取得更高经济效益的大事。
对于精馏系统来说,降低能耗的措施从两方面着手,一是在满足产品质量要求的前提下尽可能降低回流比。
精馏工艺过程中,在不降低甲醇产品质量的情况下,降低回流比只能通过增加理论板数的方法。
而增加理论板数方法之一就是增加设备的实际板数,这必将增加设备的高度,从而增加设备投资;另一方法,就是提高精馏塔内件的分离效率,即采用高效的分离元件来提高板效率或降低等板高度,从而在设备高度不增加的情况下,增加了理论板数,降低回流比。
二是改进工艺流程,即利用甲醇饱和温度随压力增大而提高的特点,利用较高压力下甲醇的冷凝热来加热低压下的甲醇使其沸腾,实现热量的梯级利用,提高热利用率,从而降低能耗。
基于以上两点,我们利用我们的专利技术——新型垂直筛板塔,结合工艺流程的优化,自主开发了以新型垂直筛板为分离元件的甲醇三塔精馏工艺技术,实现高分离效率及能源梯级利用的结合,在降低设备造价、提高能源利用率方面取得了非常好的效果。
1 新型垂直筛板塔的结构特点新型垂直筛板塔是经多年研制开发的一种新型的喷射型塔板,其结构和工作原理如图1所示。
它是由塔板上开有类似于文丘里喷嘴形式的升气孔及罩于其上的帽罩组成。
甲醇三塔工艺流程

甲醇三塔工艺流程
《甲醇三塔工艺流程》
甲醇是一种重要的有机化工原料,广泛用于制造甲醛、甲醇酯、甲醇胺、甲醇醚等化工产品,也是制造合成氨、甲苯、二甲醚等产品的重要原料。
甲醇三塔工艺是一种常用的甲醇生产技术,下面将介绍其工艺流程。
甲醇三塔工艺包括原料气体净化系统、合成反应系统和产品分离系统。
首先,天然气或煤制气通过净化系统去除杂质,然后进入合成反应系统进行催化反应,生成含甲醇的合成气。
合成气中主要含有一氧化碳、二氧化碳、氢气和甲烷等成分。
通过反应塔内的催化剂,将一氧化碳和氢气在一定条件下进行合成反应,生成含甲醇的气体。
这一步通常是利用铜和锌为活性成分的ZnO/Cr2O3等催化剂,并在一定温度和压力下进行。
接下来,合成气进入产品分离系统,通过冷凝、吸附和蒸馏等过程,将其中的甲醇和其他组分进行分离。
通过适当的温度和压力控制,将甲醇从合成气中分离出来,得到纯净的甲醇产品。
同时,其他成分也会被分离出来,并可以进行相应的收集或处理。
甲醇三塔工艺流程具有较高的甲醇产率和纯度,且对原料气体的要求较低,适用于不同来源的合成气。
同时,通过合理设计和操作,可以使工艺流程稳定可靠,并且具有较好的自动化控制性能。
总之,甲醇三塔工艺流程是一种成熟的甲醇生产技术,具有较高的经济效益和环保性能,对于满足市场的需求和优化能源结构具有重要意义。
三塔精馏技术在甲醇生产中的应用
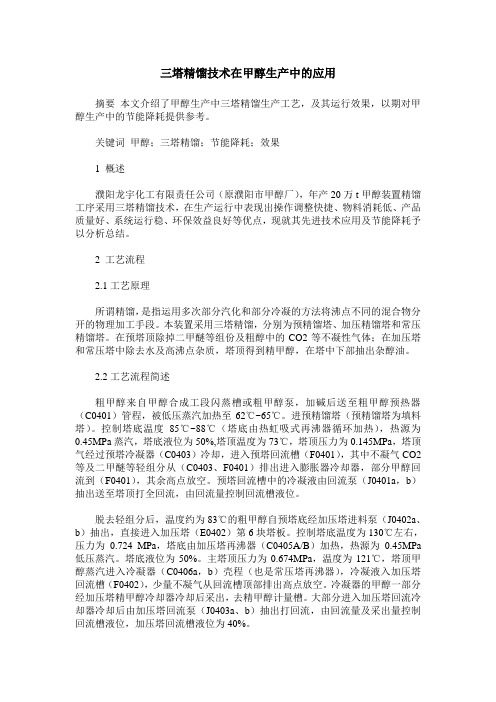
三塔精馏技术在甲醇生产中的应用摘要本文介绍了甲醇生产中三塔精馏生产工艺,及其运行效果,以期对甲醇生产中的节能降耗提供参考。
关键词甲醇;三塔精馏;节能降耗;效果1 概述濮阳龙宇化工有限责任公司(原濮阳市甲醇厂),年产20万t甲醇装置精馏工序采用三塔精馏技术,在生产运行中表现出操作调整快捷、物料消耗低、产品质量好、系统运行稳、环保效益良好等优点,现就其先进技术应用及节能降耗予以分析总结。
2 工艺流程2.1工艺原理所谓精馏,是指运用多次部分汽化和部分冷凝的方法将沸点不同的混合物分开的物理加工手段。
本装置采用三塔精馏,分别为预精馏塔、加压精馏塔和常压精馏塔。
在预塔顶除掉二甲醚等组份及粗醇中的CO2等不凝性气体;在加压塔和常压塔中除去水及高沸点杂质,塔顶得到精甲醇,在塔中下部抽出杂醇油。
2.2工艺流程简述粗甲醇来自甲醇合成工段闪蒸槽或粗甲醇泵,加碱后送至粗甲醇预热器(C0401)管程,被低压蒸汽加热至62℃~65℃。
进预精馏塔(预精馏塔为填料塔)。
控制塔底温度85℃~88℃(塔底由热虹吸式再沸器循环加热),热源为0.45MPa蒸汽,塔底液位为50%,塔顶温度为73℃,塔顶压力为0.145MPa,塔顶气经过预塔冷凝器(C0403)冷却,进入预塔回流槽(F0401),其中不凝气CO2等及二甲醚等轻组分从(C0403、F0401)排出进入膨胀器冷却器,部分甲醇回流到(F0401),其余高点放空。
预塔回流槽中的冷凝液由回流泵(J0401a,b)抽出送至塔顶打全回流,由回流量控制回流槽液位。
脱去轻组分后,温度约为83℃的粗甲醇自预塔底经加压塔进料泵(J0402a、b)抽出,直接进入加压塔(E0402)第6块塔板。
控制塔底温度为130℃左右,压力为0.724 MPa,塔底由加压塔再沸器(C0405A/B)加热,热源为0.45MPa 低压蒸汽。
塔底液位为50%。
主塔顶压力为0.674MPa,温度为121℃,塔顶甲醇蒸汽进入冷凝器(C0406a,b)壳程(也是常压塔再沸器),冷凝液入加压塔回流槽(F0402),少量不凝气从回流槽顶部排出高点放空。
甲醇三塔精馏工艺流程

甲醇三塔精馏工艺流程简述
嘿,咱今儿就来说说这甲醇三塔精馏工艺流程!你可别小瞧了它,就像咱过日子得一步一步来,这甲醇的精馏也是有它的门道和讲究呢!
咱先说说这第一个塔,就像是个大筛子,把那些乱七八糟的杂质先给过滤掉一大半。
你想啊,甲醇就像是一群小伙伴,里面有调皮捣蛋的杂质,这第一个塔就负责把那些捣蛋鬼给揪出来,让甲醇小伙伴们能更纯净地往前走。
然后呢,到了第二个塔,这可就更精细啦!就好像是给甲醇小伙伴们洗了个特别舒服的澡,把它们身上那些细微的脏东西都给洗掉了。
经过这一遭啊,甲醇变得更干净、更纯粹了。
最后到了第三个塔,哇哦,这可就是精华中的精华啦!就如同把一颗宝石精心打磨,让它绽放出最耀眼的光芒。
这个塔把甲醇提炼到了极致,让它成为了高质量的宝贝。
你说这过程神奇不神奇?就好像是一场奇妙的旅程,甲醇从一开始的混沌状态,一步步地变得纯净、完美。
这可不是随随便便就能做到的,得靠技术,靠经验,靠那些在工厂里辛勤工作的人们呐!
咱再打个比方,这甲醇三塔精馏工艺流程就像是做一道超级美味的菜肴。
第一个塔是准备食材,把不好的部分去掉;第二个塔是初步加工,让食材更有型;第三个塔那就是最后的烹饪,让这道菜达到色香味俱佳的境界。
你想想,如果没有这一步步精细的操作,那甲醇能有那么高的质量吗?那肯定不行啊!所以说,这甲醇三塔精馏工艺流程可真是太重要啦!它就像是一个神奇的魔法,把普通的甲醇变得了不起。
这就是甲醇三塔精馏工艺流程,它虽然看起来复杂,但其实就像是我们生活中的很多事情一样,只要一步一步认真去做,就能收获美好的结果。
咱得尊重和珍惜这个过程,因为它带来的是高质量的产品,是推动我们生活前进的力量啊!可不是随便说说的哟!。
- 1、下载文档前请自行甄别文档内容的完整性,平台不提供额外的编辑、内容补充、找答案等附加服务。
- 2、"仅部分预览"的文档,不可在线预览部分如存在完整性等问题,可反馈申请退款(可完整预览的文档不适用该条件!)。
- 3、如文档侵犯您的权益,请联系客服反馈,我们会尽快为您处理(人工客服工作时间:9:00-18:30)。
浅析甲醇三塔精馏工艺技术( 新疆新业能源化工有限责任公司郑军 )摘要:甲醇是重要的工业有机原料之一,也是煤基产业链合成新型能源的优质基础产品,它的主要下游产品有芳烃、烯烃、二甲醚、1,4丁二醇、甲醇叔丁基醚等。
随着科技的发展及工业技术的提高,甲醇的应用也愈加广泛,国内甲醇产能持续快速增长,工业生产技术更是精益求精。
精馏在甲醇生产中极为重要,本文以精馏塔为例论述了甲醇精馏技术中双塔和三塔精馏工艺, 介绍了精馏塔中导向型浮阀塔板的优点。
对双塔和三塔精馏技术的经济性进行了比较。
关键词:甲醇; 导向型浮阀塔板; 双塔精馏; 三塔精馏前言在以CO和H2为原料合成甲醇过程中,尽管生产工艺有单醇及联醇工艺,操作压力有高压法和低压法,催化剂有铜基和锌一铬基,但无论何种工艺生产都会不同程度地发生一些副反应,从而产生除甲醇以外的其它化合物杂质。
同时由于二氧化碳的存在,会有相当量的水生成。
为了获得高纯度、高质量甲醇产品,甲醇精馏成为甲醇生产企业重要后处理工序。
甲醇的质量、单位产品能耗是其主要的技术经济指标,而且,这一工序的能耗高低对甲醇产品的成本有重要影响。
在国家大力提倡节约能源、降低消耗、实现循环经济的大背景下,如何提高甲醇的质量、降低能耗已是每个企业争生存、求发展、取得更高经济效益的大事。
对于精馏系统来说,降低能耗的措施从两方面着手,一是提高精馏塔内件的分离效率,即采用高效的分离元件来提高板效率或降低等板间距,从而在设备高度不增加的情况下,增加了理论板数,降低回流比。
二是改进工艺流程,即利用甲醇饱和温度随压力增大而提高的特点,利用较高压力下甲醇的冷凝热来加热低压下的甲醇使其沸腾,实现热量的梯级利用,提高热利用率,从而降低能耗。
综上两点,我公司结合当前工艺流程的优化,引进了以导向型浮阀塔板为分离元件的甲醇三塔精馏工艺技术,实现高分离效率及能源梯级利用的结合,在提高能源利用率方面取得了非常好的效果。
一、导向型浮阀塔板的结构原理及特点我公司甲醇精馏塔采用的是导向型浮阀塔板,利用气体的动量推动液体向前流动的导向推液作用,从而减小直至消除液面落差,减小局部漏液,改善气体流动的均匀性,进而提高塔板效率。
导向浮阀塔板保留F1型浮阀塔板上优点,克服了浮阀塔板存在的缺点。
具有良好的流体力学和传质性能,为目前国内外最佳塔板之一。
导向浮阀塔板与F1型浮阀塔板相比,处理能力可提高20-30%,塔板效率提高10-20%,塔板压降减小20%左右。
用导向浮阀塔板代替F1型浮阀塔板,可获得显著的经济效益。
(一)导向型浮阀塔的结构:导向型浮阀塔板的塔板是由A型导向浮阀和B型导向浮阀按适当的配比组合而成。
如图所示:其特点:结构简单,通量大,压降低,效率高,负荷弹性大。
1.组合导向型浮阀塔板上A型导向浮阀与B型导向浮阀的浮阀总数之比,称为组合配比,简称配比(K)。
当液流强度较大或液体流路较长时,K值适当增大,反之,K值适当减小,以适应消除塔板上的液面梯度的需要。
在塔板两侧的弓形区与塔板上的中央区相比,弓形区内梯形导向浮阀所占比率较大,以满足消除塔板上的液体滞止区的需要。
当塔内部分塔板的液流强度较大,部分塔板的液流强度较小时,可采用不同的组合配比,以适应不同的需要。
2.组合导向型浮阀塔板的阀孔临界气速与相应条件下的导向浮阀塔板的相同。
导向浮阀塔板吸取了圆形浮阀塔板和条形浮阀塔板的优点,导向浮阀塔板的桥形阀孔和阀片前后为条形,中间为弧形或圆形,圆形部分可以有效增加浮阀的周长,以期浮阀在较小的长宽比下达到较大长宽比条形浮阀的要求,增大浮阀侧面汽体通道,同时由于浮阀长宽比较小,使浮阀在塔内的排布均匀,操作中使塔内汽体分布均匀,能够有效地减小雾沫夹带。
3.组合导向浮阀阀片边缘开有三角形、波浪形或齿形凹槽,有利于细化汽体通道,同时减小浮阀与阀孔板的接触点,使浮阀与阀孔板的接触型式由线接触变为点接触,有利于浮阀的开启,对于塔板上鼓泡区的形成具有明显优势。
阀孔结构为中间宽,前后窄,可以有效地减小浮阀列间距,增大塔板最大开孔率,这对提高塔的处理能力大有好处。
浮阀前后为条形结构,设有条形阀腿,浮阀在操作中不转动,只会上下浮动,结构可靠。
(二)浮阀塔F-型(国外通称V-型)的结构:浮阀塔F-型是用钢板冲压而成的圆形阀片,下面有三条阀腿,把三条阀腿装入塔板的阀孔之后,用工具将腿下的阀脚扭转90°,则浮阀就被限制在浮孔内只能上下运动而不能脱离塔板。
当气速较大时,浮阀塔F-型浮阀被吹起,达到最大开度;当气速较小时,气体的动压头小于浮阀自重,于是浮阀塔F-型浮阀下落,浮阀周边上三个朝下倾斜的定距片与塔板接触,此时开度最小。
定距片的作用是保证最小气速时还有一定的开度,使气体与浮阀塔F-型塔板上液体能均匀地鼓泡,避免浮阀与塔板粘住。
浮阀塔F-型浮阀的开度随塔内气相负荷大小自动调节,可以增大传质的效果,减少雾沫夹带。
结构原理如下图:(三)导向型浮阀塔板在结构上与F1型浮阀塔板的不同点:1.塔板上配有导向浮阀,浮阀上有一个或二个导向孔,导向孔的开口方向与塔板上的液流方向一致。
找操作中,从导向孔喷出的少量汽体推动塔板上的液体流动,从而可明显减少甚至完全消除塔板上的液面梯度。
2.导向浮阀两端设有阀腿,在操作中汽体从浮阀的两侧流出,体流出的反向垂直于踏板上的液体流动向。
因此,导向浮阀塔板上的液体返混是很小的。
3.踏板上导向浮阀,有的具有一个导向孔,有的具有两个导向孔。
具有两个导向孔的导向浮阀,适当排布在塔板两侧的弓形区内,以加速该区域的液体流动,从而可消除踏板上的液体滞止区。
4.由于导向浮阀在操作中不转动,浮阀无磨损,不脱落。
二、甲醇三塔精馏工艺(一)传统的双塔常压精馏工艺双塔常压精馏分离工艺是以前最为普遍的流程。
该流程主要有2个精馏塔构成,即预塔和主塔。
粗甲醇首先进入预塔,它实际上是1个萃取精馏塔,在塔顶或回流槽中加入相当于粗甲醇进料20%~30%左右的水,以水作为萃取剂将粗甲醇进料中所含的非水溶性组分与甲醇分离。
经预塔脱除了低沸点的甲醇进入主塔,在该塔内实现甲醇与杂醇、水的分离。
其操作、控制较为简单,精甲醇质量也较容易保证,但是蒸汽及冷却水消耗较高,吨甲醇蒸汽消耗达1.7~2.5t。
其流程如图:(二) 我公司的三塔精馏工艺甲醇三塔精馏工艺由预精馏塔、加压精馏塔和常压精馏塔组成。
该工艺消化吸收了国外先进的甲醇三塔精馏技术优点,结合新疆中建导向型浮阀塔板技术,由中国化学赛鼎工程有限公司设计完成,工艺流程如图:现场实景如下:该流程中,预精馏塔的作用和控制指标与双塔常压流程无异,其生产方法采用三塔流程,将粗甲醇中的杂质分别脱除,不凝气经回收甲醇后送至火炬系统。
在预精馏塔充分脱除低沸点组分后,采用加压精馏的方法,提高甲醇的气相分压与沸点,并减少甲醇的气相挥发。
加压塔底流出的较低浓度的甲醇水等经减压后流入常压精馏塔。
在塔内完成甲醇、水及高级醇的分离,最终的残液经冷却后送生化处理。
预塔和常压塔塔顶冷凝采用空冷,大大降低了冷却水的消耗。
常压塔可以完全利用加压塔的余热提供加热源,降低了蒸汽的消耗,又减少了冷却水的用量。
在此工艺流程中,操作的关键是适当确定加压塔操作压力、加压塔取出量。
首先,因加压塔冷凝器即为常压塔再沸器,而常压塔塔釜温度在110~115℃,要使加压塔塔顶气可以作为常压塔的加热源,其温度需高于常压塔釜温10℃以上,即加压塔塔顶温度约125℃,其对应压力应在0.6MPa(g)。
另外,加压塔的取出量大小,也直接影响三塔精馏操作的稳定性及能耗。
取出量小,为保证常压塔的热负荷,需加大加压塔回流比;若取出量大,需人为地加大常压塔回流比,都将造成能耗的增大,这可以由两个极限情况说明,其一为加压塔取出为零,这时加压塔仅相当于常压塔再沸器;其二为常压塔取出为零,常压塔为加压塔的冷凝器。
经过操作经验优化,认为当两塔取出量相近时,系统能耗最低,投资最小,这与双塔精馏工艺的控制条件有很大区别。
三、甲醇三塔精馏工艺应用成果我国甲醇产能持续快速增长,甲醇三塔精馏技术已为煤化工企业所瞩目。
自2015年以来,宁夏宝丰能源集团年产150万吨等数个合计产能720万吨的甲醇项目建成投产,使国内甲醇有效年产能增至7200余万吨;2016年,数套煤制烯烃配套甲醇项目投产后,国内甲醇有效年产能将攀高至7800万至8000万吨。
我公司甲醇三塔精馏工艺生产能力为年产50万吨,其精甲醇设计产量72.3t/h,实际产量26.97t/h,单耗为1.08,循环水设计耗水量6.50m3/h实际耗水量4.85m3/h,脱盐水设计用量8m3/h,实际用量6.2m3/h,主要物料累计如下:生产实践表明三塔精馏工艺具有以下特点:(1)设备处理能力大。
不同流程及塔型的设备规格及处理能力见表1。
(2)蒸汽消耗低,节能效果显著。
通过合理选择操作参数,使加压和常压精馏塔的生产能力合理匹配,均衡采出产品,并适当降低回流比,进一步降低了系统的蒸汽消耗,吨醇汽耗已降低到1 t以下。
不同流程的蒸汽消耗的相对数值见表2。
(3)甲醇产品纯度高,残液中的含醇量低。
通过优化设计,确定最佳的进料及取出位置,使甲醇纯度达到99.9%以上,残液中的甲醇含量得到了最大限度地降低,一般在0.1%以下(传统浮阀精馏塔残液中的甲醇含量为0.5%~1.0%),有的用户残液甲醇含量接近“0”。
这不仅保证了甲醇的高收率,而且使残液的处理及污染得到了有效控制。
(4)在运行中有效解决了精甲醇酸值易偏高的问题。
在生产中,通常需要加入烧碱来降低精醇的酸值。
在加压操作下,烧碱中的CO2溶入加压精馏塔的精醇中,会使精醇的酸值增高,这就会形成越加碱酸值越高的问题。
通过操作优化,得到了最佳配碱量,将pH值调整到7.5~9,不仅节省烧碱,更重要的是产品质量得到了提高,产品优级品率达到100%。
(5)适合于对二塔流程进行三塔扩产节能的改造。
现有双塔精馏用户进行扩产改造时一般采用新上1套同类装置的方法,而进行三塔改造,仅需增加1台加压精馏塔、1台加压回流槽及回流1套年生产能力25万t精馏装置为例,改三塔后能力增加到50万t/a,比新建1套25万t精馏装置可节省一次性投资800万元左右,每年节约蒸汽约40万t,循环水3500万t,价值3150万元左右,相当于每吨甲醇降低成本430元。
结语以下是新疆化工研究院有限责任公司对导向型浮阀塔板三塔精馏技术的鉴定意见,将作为本文的结语:该技术与三塔精馏流程有机结合实现了国产化甲醇三塔精馏装置的各项技术经济新疆化工设计研究院有限责任公司2016年11月1日指标可与国内大型企业从国外引进的三塔精馏技术相媲美,有的指标还超过了引进装置,整体技术水平达到了国内领先。
(1)导向型浮阀塔板技术与三塔精馏流程有机结合,设备处理能力大,形成了一个高效、节能、安全、产品质量好的甲醇精馏体系。