铸铁件通用检验标准
铸件质量检查标准

一、目的:为了确保外协标准铸件、成品铸件质量符合工艺、技术要求,为了满足产品特性,结合相关文件特制定本标准。
二、适用范围:本办法适用于我公司产品外协、采购、装配过程中、全部铸件质量检查标准。
三、检查标准:3.1、铸件结构要符合设计要求或加工工艺要求。
无特殊要求时按铸件通用标准执行。
通用标准等级分为:交货验收技术条件标准;铸件质量分等通则(合格品、一等品、优等品)材质、检验方法;工艺和材料规格等一般性规则。
3.2、铸件成品检验。
铸件成品检验包括:相关技术条件的检验、表面质量检验、几何尺寸检验等项内容。
①相关技术条件的检验。
包括铸件化学成分、机械性能等检验内容。
机械性能检验和金相及化学成分检验等技术条件的检验,均必须按相关国家标准执行检验(此处略)。
②表面质量检验。
机械加工生产一线人员在工艺过程中对铸造毛坯的检查主要是对其外观铸造缺陷(如有无沙眼、沙孔、疏松、有无浇不足、铸造裂纹等)的检验;以及毛坯加工余量是否满足加工要求的检验。
表3-1铸件外观质量检验项目(GB6060.1—1985)表3-2 铸件表面粗糙度(R a 值μm)(GB6414—1986)③铸件成品几何尺寸检验。
主要一种是采用划线法检查毛坯的加工余量是否足够。
另一种方法是:用毛坯的参考基准面(也称工艺基准面)作为毛坯的检验基准面的相对测量法(需要测量相对基准面的尺寸及进行简单换算)。
表3-3 铸件尺寸公差数值(mm)(GB6414—1986)注:铸件基本尺寸≤10mm 时,其公差等级提高3 级;大于10mm 至等于15mm 时,其公差等级提高2级;大于16mm 至25mm 时,其公差等级提高1 级。
附表:铸件质量检验与缺陷处理实用技术。
铸件质量检验标准

铸件质量检验标准铸件是一种常见的生产工艺,广泛用于各个行业和领域。
铸件质量的好坏直接影响产品的性能和可靠性,因此进行铸件质量检验至关重要。
本文将介绍铸件质量检验的标准和方法。
一、铸件质量检验的重要性铸件质量检验的目的是确保铸件的尺寸精度、表面质量和机械性能达到设计要求。
一方面,铸件的尺寸精度和表面质量直接影响产品的装配和使用;另一方面,对于承受重载或高温等极端工况的铸件来说,其机械性能的好坏关系到产品的安全可靠性。
二、铸件质量检验的标准铸件质量检验的标准包括国家标准、行业标准和企业自身标准。
国家标准是根据相关法律法规制定的,具有强制性,是衡量铸件质量的重要依据。
行业标准是在国家标准的基础上,由行业协会或行业组织制定的,作为行业内铸件质量的参考指南。
企业自身标准是企业根据生产情况和需求制定的,用于规范和管理内部质量控制。
在铸件质量检验中,常用的国家标准有《铸造铁件技术条件》、《铸铝合金件技术条件》等,而行业标准包括《汽车铝合金压铸铸件技术规范》、《船用铸铁件技术条件》等。
企业自身标准则根据企业具体的生产工艺和要求制定,例如《XX公司铸件质量检验标准》。
三、铸件质量检验的方法铸件质量检验的方法主要包括外观检查、尺寸检测和性能测试。
1. 外观检查外观检查是铸件质量检验中最简单直观的方法。
通过肉眼观察铸件的外观,检查是否有裂纹、砂眼、气孔、夹渣等缺陷。
外观检查可以用目视检查或借助放大镜进行观察。
2. 尺寸检测尺寸检测是铸件质量检验中最常见的方法。
主要是测量铸件的外形尺寸、孔径尺寸和壁厚尺寸等。
常用的尺寸测量工具有游标卡尺、内径卡尺、外径卡尺、深度尺等。
尺寸检测可以帮助判断铸件是否满足设计要求。
3. 性能测试性能测试是铸件质量检验中最关键的方法,主要包括力学性能测试、化学成分分析和金相组织分析。
力学性能测试主要是测试铸件的拉伸、弯曲、冲击等力学性能。
化学成分分析可以确定铸件的材料成分是否符合要求。
金相组织分析可以观察铸件的金相组织结构,评估其机械性能。
压铸件外观通用检验标准(带图实例)
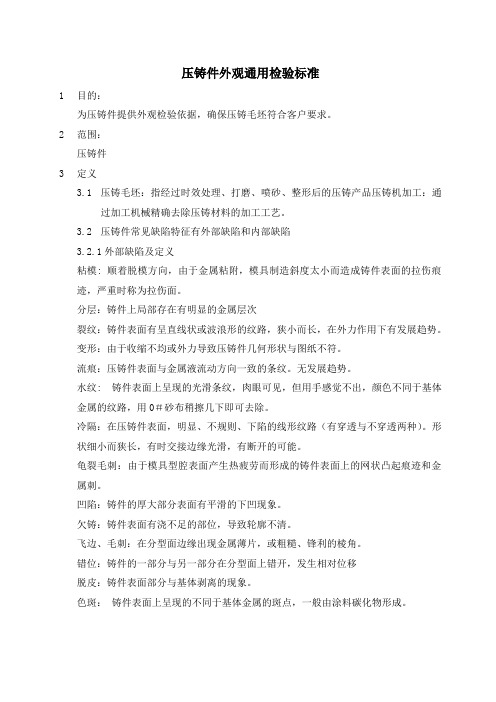
压铸件外观通用检验标准
1目的:
为压铸件提供外观检验依据,确保压铸毛坯符合客户要求。
2范围:
压铸件
3定义
3.1压铸毛坯:指经过时效处理、打磨、喷砂、整形后的压铸产品压铸机加工:通
过加工机械精确去除压铸材料的加工工艺。
3.2压铸件常见缺陷特征有外部缺陷和内部缺陷
3.2.1外部缺陷及定义
粘模: 顺着脱模方向,由于金属粘附,模具制造斜度太小而造成铸件表面的拉伤痕迹,严重时称为拉伤面。
分层:铸件上局部存在有明显的金属层次
裂纹:铸件表面有呈直线状或波浪形的纹路,狭小而长,在外力作用下有发展趋势。
变形:由于收缩不均或外力导致压铸件几何形状与图纸不符。
流痕:压铸件表面与金属液流动方向一致的条纹。
无发展趋势。
水纹: 铸件表面上呈现的光滑条纹,肉眼可见,但用手感觉不出,颜色不同于基体金属的纹路,用0#砂布稍擦几下即可去除。
冷隔:在压铸件表面,明显、不规则、下陷的线形纹路(有穿透与不穿透两种)。
形状细小而狭长,有时交接边缘光滑,有断开的可能。
龟裂毛刺:由于模具型腔表面产生热疲劳而形成的铸件表面上的网状凸起痕迹和金属刺。
凹陷:铸件的厚大部分表面有平滑的下凹现象。
欠铸:铸件表面有浇不足的部位,导致轮廓不清。
飞边、毛刺:在分型面边缘出现金属薄片,或粗糙、锋利的棱角。
错位:铸件的一部分与另一部分在分型面上错开,发生相对位移
脱皮:铸件表面部分与基体剥离的现象。
色斑:铸件表面上呈现的不同于基体金属的斑点,一般由涂料碳化物形成。
铸件的检验项目...
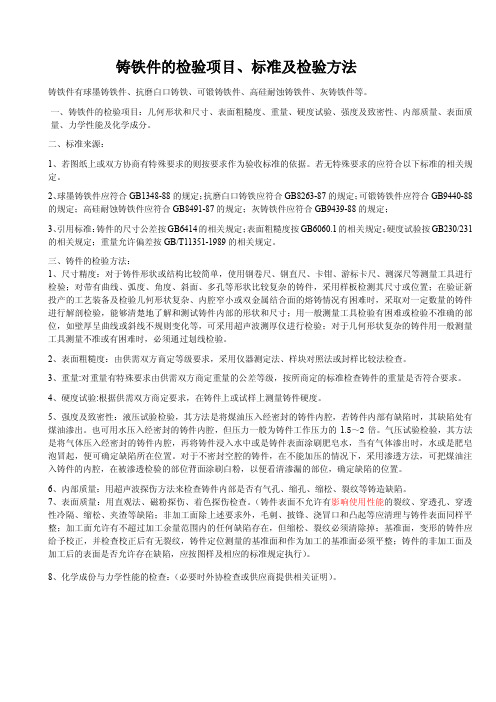
铸铁件的检验项目、标准及检验方法铸铁件有球墨铸铁件、抗磨白口铸铁、可锻铸铁件、高硅耐蚀铸铁件、灰铸铁件等。
一、铸铁件的检验项目:几何形状和尺寸、表面粗糙度、重量、硬度试验、强度及致密性、内部质量、表面质量、力学性能及化学成分。
二、标准来源:1、若图纸上或双方协商有特殊要求的则按要求作为验收标准的依据。
若无特殊要求的应符合以下标准的相关规定。
2、球墨铸铁件应符合GB1348-88的规定;抗磨白口铸铁应符合GB8263-87的规定;可锻铸铁件应符合GB9440-88的规定;高硅耐蚀铸铁件应符合GB8491-87的规定;灰铸铁件应符合GB9439-88的规定;3、引用标准:铸件的尺寸公差按GB6414的相关规定;表面粗糙度按GB6060.1的相关规定;硬度试验按GB230/231的相关规定;重量允许偏差按GB/T11351-1989的相关规定。
三、铸件的检验方法:1、尺寸精度:对于铸件形状或结构比较简单,使用钢卷尺、钢直尺、卡钳、游标卡尺、测深尺等测量工具进行检验;对带有曲线、弧度、角度、斜面、多孔等形状比较复杂的铸件,采用样板检测其尺寸或位置;在验证新投产的工艺装备及检验几何形状复杂、内腔窄小或双金属结合面的熔铸情况有困难时,采取对一定数量的铸件进行解剖检验,能够清楚地了解和测试铸件内部的形状和尺寸;用一般测量工具检验有困难或检验不准确的部位,如壁厚呈曲线或斜线不规则变化等,可采用超声波测厚仪进行检验;对于几何形状复杂的铸件用一般测量工具测量不准或有困难时,必须通过划线检验。
2、表面粗糙度:由供需双方商定等级要求,采用仪器测定法、样块对照法或封样比较法检查。
3、重量:对重量有特殊要求由供需双方商定重量的公差等级,按所商定的标准检查铸件的重量是否符合要求。
4、硬度试验:根据供需双方商定要求,在铸件上或试样上测量铸件硬度。
5、强度及致密性:液压试验检验,其方法是将煤油压入经密封的铸件内腔,若铸件内部有缺陷时,其缺陷处有煤油渗出。
铸件外观质量检验规范
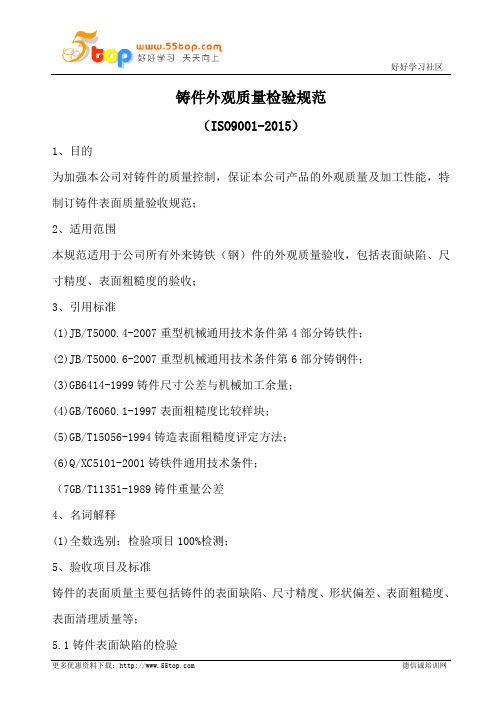
铸件外观质量检验规范(ISO9001-2015)1、目的为加强本公司对铸件的质量控制,保证本公司产品的外观质量及加工性能,特制订铸件表面质量验收规范;2、适用范围本规范适用于公司所有外来铸铁(钢)件的外观质量验收,包括表面缺陷、尺寸精度、表面粗糙度的验收;3、引用标准(1)JB/T5000.4-2007重型机械通用技术条件第4部分铸铁件;(2)JB/T5000.6-2007重型机械通用技术条件第6部分铸钢件;(3)GB6414-1999铸件尺寸公差与机械加工余量;(4)GB/T6060.1-1997表面粗糙度比较样块;(5)GB/T15056-1994铸造表面粗糙度评定方法;(6)Q/XC5101-2001铸铁件通用技术条件;(7GB/T11351-1989铸件重量公差4、名词解释(1)全数选别:检验项目100%检测;5、验收项目及标准铸件的表面质量主要包括铸件的表面缺陷、尺寸精度、形状偏差、表面粗糙度、表面清理质量等;5.1铸件表面缺陷的检验5.1.1表面缺陷检验的一般要求(1)铸件非加工表面上的浇冒口必须清理得与铸件表面同样平整,加工面上的浇冒口残留量应符合技术要求,若无要求,则按表8执行;(2)在铸件上不允许有裂纹、通孔、穿透性的冷隔和穿透性的缩松、夹渣等机械加工不能去除的缺陷;(3)铸件非加工表面的毛刺、披缝、型砂、砂芯等应清理干净;(4)铸件一般待加工表面,允许有不超过加工余量范围内的任何缺陷存在;重要加工面允许有不超过加工余量2/3的缺陷存在,但裂纹缺陷应予清除;加工后的表面允许存在直径*长度*深度小于等于2*2*2的非连片孔洞的铸造缺陷;(5)作为加工基准面(孔)和测量基准的铸件表面,平整度小于等于2.0毫米、粗糙度Ra50以内;(6)铸件表面气孔、砂眼、夹渣面积不大,但比较分散或者有连片麻点的表面不予接收;(7)除技术要求特别注明的铸件外,对于表面有气孔、缩孔、砂眼等缺陷的铸钢件允许补焊,但铸铁件未经允许不得焊补(铸铁件实行一案一判的原则)但补焊面积不允许超过铸件面积的10%,焊接质量应符合JB/T5000.7-2007标准要求,补焊后必须退火、机械性能达到图纸要求,且不得有渗漏及影响外观的缺陷;5.1.2铸件外观质量等级缺陷项目等级A B C飞边不允许飞边高度≤1.5毫米允许不易于伤手的飞边毛刺不允许允许不易于伤手的毛刺允许不易伤手的毛刺孔眼气孔 100cm 2面积内允许直径不大于φ2mm 深度不超过壁厚1/4的孔眼2个,两处距离>60mm ;整个铸件不超过4个100cm 2面积内允许直径不大于φ3mm 深度不超过壁厚1/3的孔眼2处,两处距离>60mm ;整个铸件不超过8个不致于影响强度,其余不做要求 针孔 渣眼 缩孔 不致于影响强度裂纹 不允许 不允许不允许 冷隔 沟槽 夹砂结疤 不允许 100cm 2面积内允许面积不超过8cm 2的缺陷2处;整个铸件不超过4处不致于影响强度 皱皮 不允许 不明显引人注意缩陷不允许不允许 不允许缺肉1、一般零部件采用B 级精度,在检查过程中,如有一个或多个项目超出B 级精度要求的零部件均判定为不合格;2、影响到零部件安全、性能的部位,外观质量采用A 级精度,如果有一个或多个项目超出规定级精度要求的零部件均判定为不合格;5.2铸件尺寸的检验 5.2.1铸件毛坯尺寸公差铸件尺寸公差应按毛坯图或技术条件规定的尺寸公差等级执行,当技术文件未规定尺寸公差时,则应以GB6414为依据,并按照下表选定公差值(粗线框内为推荐使用公差等级);毛坯铸件基本尺寸(mm )尺寸公差等级CT12CT13 CT14 CT15 CT16 ≤10~16 4.4 --- --- --- --- >16~25 4.6 6 8 10 12 >25~40 5.0 7 9 11 14 >40~63 5.6 8 10 12 16 >63~100 6 9 11 14 18 >100~160 7 10 12 16 20 >160~250 8 11 14 18 22 >250~400912162025>400~630 10 14 18 22 28 >630~1000 11 16 20 25 32 >1000~1600 13 18 23 29 37 >1600~2500 15 21 26 33 42 >25004000 17 24 30 38 49 >4000~6300 20 28 35 44 56 >6300~100002332405064注:1、毛坯铸件基本尺寸是指机械加工前毛坯铸件的尺寸,包括加工余量和起模斜度; 2、毛坯基本尺寸按铸件最大尺寸选取,该铸件较小尺寸公差等级与最大尺寸公差等级相同;3、壁厚采用低一级的公差等级;4、公差带应对称于毛坯铸件基本尺寸配置,例:基本尺寸30mm ,CT13公差值为±7mm ;如有特殊要求非对称式配置时,应在技术要求中单独列出公差范围;5.2.2铸件分型面处最大错型值应不得超过表2所示公差值,当需进一步限制错型量时,应从表中选取;公差等级CT 错型值(mm )11~13 1.5 14~162.55.2.3铸件加工余量应符合表的规定,有特殊要求的表面应在技术要求中单独标注加工余量;最大轮廓尺寸加工余量一个面顶面加量≤30 4 2>30~50 5 >50~180 6 >180~315 7 >315~500 8 >500~800 103>800~1250 12 >1250~1600 144>1600~250016>2500~3150 18>3150~4000 205>4000~6300 25>6300~10000 30 7注:1、属于该铸件的较小尺寸的加工余量与最大轮廓尺寸的加工余量相同;2、此表加工余量仅指一个面的加工余量,对于柱面和两面加工的铸件,铸件轮廓尺寸应为最终机械加工后成品尺寸与两倍加工余量之和;5.3表面粗糙度检测表面粗糙度总体检测原则依据图纸要求,当图纸无要求是执行国标GB/T15056;5.3.1一般情况下,表面粗糙度要求Ra50,铸件难以清理的部位,局部允许Ra100,待加工表面允许降低1级;5.3.2.使用面积法作为验收依据面积法常用的比较样块评定铸件表面粗糙度;方法如下:(1)铸造表面粗糙度比较样块应符合GB6060.1-1997标准;(2)按照国标BWZ001-88评定铸件表面粗糙度的等级;(3)铸件的浇道、冒口、修补的残余表面及铸造表面缺陷(如粘砂、结疤等)不列为被检表面;(4)以铸造表面粗糙度比较样块为对照标准,对被检铸件的铸造表面用视觉或触觉的方法进行对比;(5)用样块对比时,应选用适于铸造合金材料和工艺方法的样块进行对比;(6)被检的铸造表面必须清理干净,样块表面和被检表面均不得有锈蚀处;(7)用样块对比时,砂型铸造表面被检点数应符合表的规定;特种铸造表面被检点数应按表8的规定加倍;被检点应平均分布,每点的被检面积不得小于与之对比面的面积;被检铸造表面面积(cm2)<200 200~1000 100~10000 >10000被检点数(个) 不少于2 每200cm2不少于1 每1000cm2不少于1不少于40 (8)当被检铸造表面的粗糙度介于比较样块两级参数值之间者,所确定的被检铸造表面的粗糙度等级为粗的一级;(9)对被检铸造表面,以其80%的表面所达到的最粗表面粗糙度等级,为该铸造表面粗糙度等级;5.3.3铸件表面清理检测5.3.1铸件几何形状必须完整,非加工面上的清理损伤不应大于该处的尺寸偏差,加工面上的损伤不应大于该处加工余量的1/2;5.3.2允许铸件表面有少量的局部低凹或打磨痕迹,在直径不大于8mm,并能保证铸件规定的最小的壁厚;5.3.3为去除铸造缺陷而打磨后的铸件表面粗糙度应与一般铸件表面粗糙度基本一致;5.3.4除特殊情况外,铸件表面允许残留的浇冒口、毛刺,多肉残余量应按表8的要求进行;类别非加工面凸出高度(mm)加工面凸出高度(mm) 外表面非外表面浇冒口残余量-0.5~0.5 <2 <2~4毛刺残余量0 <2 <1~2多肉残余量<1 <2 <25.3.5铸件表面须经过防锈处理,保证在铸件进入面加工时不得有任何的锈蚀;5.3.6铸件表面如有油漆要求的,必须按有关涂装规定执行;5.4铸件重量检测5.4.1对于没有特殊要求的铸件,重量偏差可以不作为验收依据;如果技术条件有要求,供需双方协商后,铸件的重量偏差也应作为验收依据,一般应符合表的规定;公称重量(Kg) ≤200>200~500>500~1000>1000~5000>5000~10000>10000~30000>30000~50000>50000铸件重量上偏差(%)8 7.5 7 6.5 6 5.5 5 4.5。
铸铁件检验标准

铸铁件检验标准(总3页)--本页仅作为文档封面,使用时请直接删除即可----内页可以根据需求调整合适字体及大小--铸铁件检验标准一、检验项目、装配尺寸、性能、外观颜色包装。
二、检验方式:实配、测量。
三、抽样设计及允收水准3.1依照一般检查水平:Ⅰ级进行抽样。
3.2、每批从四点以上分散随机抽样。
3.3严重缺陷[CR]AQL=0,主要缺陷[MA] AQL=,次要缺陷[MI] AQL=四、检验内容:4.1 尺寸:4.4.1 烤板、烤网类一般检验长度与宽度尺寸,除特殊要求外,公差一般为±。
4.4.2 炉头类除了检验长度与宽度尺寸外,依照相应进料检验标准对其它重要装配尺寸进行检验。
4.4.3 其它不便检测之装配尺寸可利用检具或实配件进行检验。
4.2 外观、亮度及颜色:4.2.1铸铁烤漆件a. 刮边平直,无披锋、利边及尖角,无裂纹,无气孔起皮,浇铸不足、冷隔、沙粒、蚀料等铸造缺陷。
所有孔洞<3mm x 1mm(深),且在100mmx200mm范围内不超过3处。
烤板烤网变形量:面≤ mm ,边≤2mm ,四脚(四角)≤2mm.b. 炉头类所有燃烧孔均匀及引火槽无堵塞,无明显扭曲,任何方向弯曲变形量<3mm.c. 烤板烤网类需无毒黑漆处理,炉头类普通黑漆处理。
颜色、亮度与确认的检验样板一致。
整体涂层均匀,油漆层完全烘干,无刮花、碰伤、气泡、漏喷、喷流、生锈等不良情形。
4.2.2 搪瓷铸件a. 瓷层均匀并完全覆盖基体,无烧焦、正面无明显焦点,无明显气泡,无毛刺。
表面瓷层无开裂,无裂纹,无污点,无杂色点等。
b. 无掉瓷爆瓷,正面无疤痕,侧面背面疤痕≤3mmx3mm且不超过3处,表面流痕≤3mm且不超过3处。
正面无搪瓷缺失,背面侧面搪瓷缺失≤3mmx3mm 且不超过3处。
c. 搪瓷铸件颜色、光泽与确认之样板一致.d. 铸件变形量:面≤3mm,边≤2mm , 四脚(四角)≤2mm。
4.3 性能4.3.1 铸铁件烤漆件a. 烧烤测试:取样在烤炉空烧1小时后油漆层可炭化,且油漆气味持续时间小于15分钟(每批次取样1~2pcs),此项为实验室测试,适用于新厂商开发、新工艺确认、新产品及不定期常规测试(2~4 次/月)。
铸件质量检验标准

—
—
—
—
—
—
—
—
0.64
0.72
0.80
0.9
1.0
1.1
1.2
1.4
1.6
1.8
2.0
2.2
2.6
2.8
3.2
3.6
4.0
4.6
5
6
7
7
8
9
10
11
13
1600
2500
4000
6300
2500
4000
6300
10000
—
—
—
—
—
—
—
—
—
—
—
—
—
—
—
0.24
0.26
0.28
0.32
0.36
0.40
0.46
0.50
0.56
0.64
0.70
0.78
0.9
1.0
1.1
1.3
1.4
1.6
1.8
2.0
2.2
2.6
2.8
CF3M
ASTM
A351
0.03 1.5 1.5 17~21 0.04 0.04 9~13 2~3
CF8M
ASTM
A351
0.08 1.5 1.5 18~21 0.04 0.04 9~12 2~3
CG3M
ASTM
A351
0.03 1.0 2.0 18~20 0.035 0.03 11~15 3~4
Q2024J04铸铁件、碳钢铸件检验规范
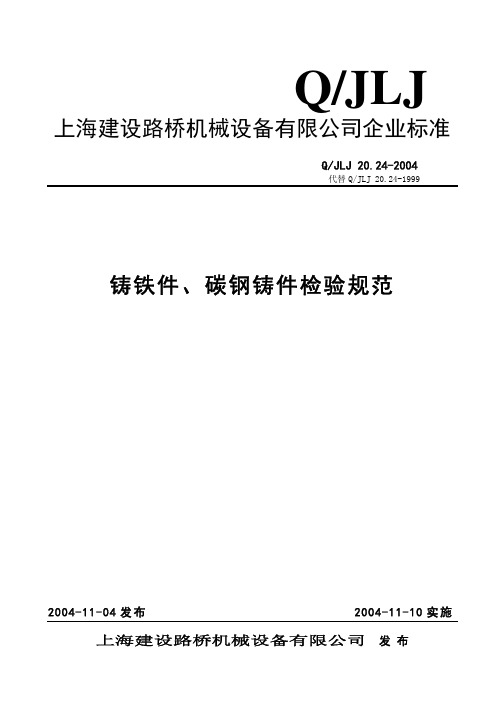
Q/JLJ 上海建设路桥机械设备有限公司企业标准Q/JLJ 20.24-2004代替Q/JLJ 20.24-1999铸铁件、碳钢铸件检验规范2004-11-04发布2004-11-10实施上海建设路桥机械设备有限公司发 布前 言本标准根据国家现有的铸件通用标准及本公司相关的技术文件而制定,指导检验人员用于铸件质量检验。
本标准对Q/JLJ 20.24-1993第3.1和3.3条款进行了修改,补充了相应的理化试验内容,作为进货检验和试验工作指导性文件。
本标准的格式按照GB/T 1.1-2000《标准化工作导则 第1部分:标准的结构和编写规则》进行编辑性修改,具体内容与Q/JLJ 20.24-1999完全一致。
本标准由公司标准化委员会提出;本标准由总工程师室归口;本标准主要起草人:张兰;本标准审核人:陈志兴;本标准标准化审查人:王定华;本标准由公司总工程师李本仁审定;本标准由公司总经理张庆伟批准。
本标准所代替标准的历次发布情况为:——Q/JLJ 20.24-1993、Q/JLJ 20.24-1999。
I铸铁件、碳钢铸件检验规范1 范围本规范规定了质量检查项目和检验频次等事项。
本规范适用于本公司外协铸铁件、碳钢铸件的检验。
不适用高锰钢件及高铬铸铁件。
2 规范性引用文件下列文件中的条款通过本标准的引用而成为本标准的条款。
凡是注日期的引用文件,其随后所有的修改单(不包括勘误的内容)或修订版均不适用于本标准,然而,鼓励根据本标准达成协议的各方研究是否可使用这些文件的最新版本。
凡是不注日期的引用文件,其最新版本适用于本标准。
GB/T 1348 球墨铸铁件GB/T 6414 铸件尺寸公差GB/T 9439 灰铸铁件GB/T 9441 球墨铸铁金相GB/T 11352 一般工程用铸造碳钢件3 质量检查项目3.1 铸件进厂应含有下列内容的质量证明书a ) 铸造厂名;b ) 炉批号;c ) 材质牌号;d ) 机械性能;e ) 化学成分(铸钢件);f ) 浇注随炉试样(重要铸件);3.2 几何形状和尺寸检查按图纸规定的尺寸检查,毛坯中未注公差的尺寸按 GB/T 6414 检验。
- 1、下载文档前请自行甄别文档内容的完整性,平台不提供额外的编辑、内容补充、找答案等附加服务。
- 2、"仅部分预览"的文档,不可在线预览部分如存在完整性等问题,可反馈申请退款(可完整预览的文档不适用该条件!)。
- 3、如文档侵犯您的权益,请联系客服反馈,我们会尽快为您处理(人工客服工作时间:9:00-18:30)。
1目的:
规范公司对铸铁件的检查验收。
2适用范围: 适用于铸铁件。
※本标准是铸件的通用标准,铸件有特殊要求时,参见相关铸件分类验收标准。
3 验收标准:
3.1铸铁件材质检验标准:
3.1.1球墨铸铁件材质检验标准:
球墨铸件材质验收标准应符合GB1348或EN1563:1997球墨铸铁的标准,以机械性能(抗拉强度、延伸率)、球化率和渗碳体含量为验收依据,硬度、其它金相组织及化学成份做为参考。
3.1.1.1球墨铸铁牌号及机械性能(单铸试块)见下表:
3.1.1.2 球墨铸铁常规金相组织
3.1.1.3球墨铸铁化学成份
3.1.2灰铸铁件材质检验标准:
灰铸件材质验收标准应符合GB9439或EN 1561:1997灰铸铁件的标准,以机
械性能(抗拉强度)和硬度为验收依据,金相组织及化学成份做为参考。
3.1.2.1灰铸铁牌号及机械性能(单铸试块)见下表:
HT250250-350190-240
3. 1.2.2 灰铸铁常规金相组织
3.1.2.3灰铸铁化学成份
3.1.3 材质检验取样规范
3.1.3.1机械性能检查:机械性能测试的试棒,每班次每种牌号至少浇一组,有新产品时增加一组,每组浇三根,若铸件进行退火处理,必须连同试棒(试块)一同进行热处理(若是渗碳体超标需热处理的件,按热处理后铸件本体的金相组织来验收)。
机械性能试验:二根用于生产厂测试性能(第一根合格则该批次合格,余下试棒留存(留有生产日期、包次标识),在工厂存放,存放期三年;若第一根试棒不合格,测试剩余二根,若第二根不合格则该批次产品全部报废;若第二根合格,应加试第三根,合格则判定该炉产品合格,若第三根不合格则该批次产品全部报废)。
材质检测报告存根(原始记录)保留11年。
常规灰铸铁试棒见下图:
常规球墨铸铁试棒见下图:
其余
其余
3.1.3.2金相组织检查:球铁铸件从每包铁水的最后一型附铸金相试块或铸件本体进行检验,依次往前直到合格(或本包铁水所浇铸件检验完)为止。
附铸试块应能代表本体。
试块不好,破件进行检验。
对于灰铸铁件每炉铁水至少分析一件附铸试块或本体废件。
若金相有问题,加倍抽查。
金相本体试块应按天分类以月为单位保存,保持期6个月。
检验报告保留11年。
3.1.3.3化学成份检查:每天必须分析每炉铁水(炉前)及至少两炉铸件(炉后)的化学成分。
炉前主要化验碳、硅和硫;炉后碳、硅、锰、硫、磷、稀土、镁(灰铸铁件无稀土、镁两元素)全部化验。
每天第一炉熔清后必须检测C、Si、Mn、S,之后C、Si每炉化验检测。
化学成分记录要求齐全,归档存放保留11年。
3.2 铸件尺寸精度
3.2.1 铸件尺寸符合图纸要求,未注尺寸公差采用CT9公差,具体数值见下表:
3.3 铸件外观质量
3.3.1 铸字、标识:铸件上所要求的铸字、标识必须完整、清晰、正确,符合图纸要求。
3.3.2 错箱值:铸件最大错箱值不超过0.8mm。
3.3.3 浇冒口、飞边残留高度:铸件上浇冒口、披缝等要清理干净,最大残留高度不超过0.5mm。
3.3.4 表面粗糙度:铸件表面应光滑、平整,表面有粘砂、氧化皮、锈蚀等应清理干净,表面粗糙度应小于Ra25。
3.3.5 铸件表面缺陷
3.3.5.1生产交货的铸件表面质量应进行100%目测检验。
铸件上不允许存在影响性能的缺陷(裂纹、冷隔、浇不足、缩孔等)存在。
3.3.5.2铸件非加工面允许不大于2×2mm深1.5mm的单个孔洞存在,并且每12.5×12.5mm面积范围内的孔数,不多于3处存在,相邻缺陷间隔在10mm 以上。
但不允许在铸件壁厚的对应面出现,不允许成片的孔眼类缺陷。
3.3.5.3 铸件加工面允许存在加工时可以去除的缺陷,一般控制在加工量的2/3。
3.3.5.4 铸件非加工表面每棱边上的磕碰砸伤不得多于2处,并且每处面积不得大于2×2mm。
3.3.5.5 铸件非加工面上缺陷如果超出3.3.5.2的规定(但缺陷深度不允许超过铸件壁厚的二分之一),且不在铸件的关键部位(密封面、受力部位、应力点等)周围直径30毫米范围内时,经过允许可以通过焊补或胶补的方法进行修补。
4. 铸件表面防护处理
4.1 铸件表面的锈蚀、粘砂、氧化皮等应通过抛丸处理干净。
4.2 对有防腐处理要求的铸件,按指定的要求(喷涂、防锈油或防锈漆)进行表面处理,表面处理后颜色应一致且符合要求。
涂层均匀表面光滑,没有磕碰、划伤、流挂、堆集和气泡等明显缺陷。
表面洁净,无污物粘连。
待确认铸件表面涂层完全干透之后,方可进行装箱工序操作,防止涂层粘连的质量问题发生。
5. 铸件包装及装箱
5.1 铸件包装时表面应干净、整洁。
5.2 铸件装箱时,应在包装箱内放防潮塑料袋,铸件摆放整齐、放置牢靠、数量准确,装箱后及时将防潮塑料袋扎口密封以防生锈。
5.3 装箱后的铸件,箱内必须附带产品合格证、并填写产品库存卡:必须标明装箱产品的名称、产品图号、模型号、箱编号XXXXX-YYYY-ZZ(年月日(年一位数)-日期码-当日装箱序号)、数量等所需标签贴在包装箱外测,并准确无误。
5.4 铸件包装箱采用多层胶合板,外测必须用至少三道钢制打包带固定牢靠。
6. 引用标准
GB1348 球墨铸铁件牌号GB9439 灰铸铁件牌号
GB6414 铸件尺寸公差GB9441 球墨铸铁金相检验GB7216 灰铸铁金相检验EN1563:1997
EN1561:1997。