基于Dynaform软件的板料冲压成形仿真操作指引
应用Dynaform模拟冲压成形过程基础

– UG – Nastran文件 – LS-DYNA 输入文件 – LS-DYNA 模型文件 – LS-DYNA 输入文件 – LS-DYNA结果文件 – LS-DYNA重启动文件
*.df *.lin *.igs *.iges *.vda *.model&*.CATPart *.prt *.nas *.dat *.dyn *.mod *.blk dynain d3plotnn d3dumpnn runrsf
• 依赖于经验及“试错法”:设计→试模→修 模
• 这类经验的积累需要几年至十几年,以 时间、金钱为代价;并且不断重复
• 模具开发的周期长,成本高 • 模具及工艺只是“可行”的,而非“优化”的 • 市场需求的变化会使原来的经验失去作
用 • 市场经济使得传统的设计方法逐步丧失
竞争力
汽车覆盖件CAE技术在国外已日趋成熟
需要更多的设置时间
自动定义运动、载荷曲线等 手工定义运动、载荷曲线
接触等距方法
几何等距方法
模拟步骤(传统)
1. 读入凹模与板料的几何数模,可以读入iges、vda、lin、 dxf,stl,UG,CATIA及Pro/E等格式的数模文件
2. 将读入的几何模型划分网格,并检查网格质量 3. 利用凹模的网格生成凸模与压边圈 4. 定义板料材料属性及厚度 5. 定义冲压类型(单动or双动) 6. 模具自动定位 7. 定义模具运动和压边力 8. 提交求解器计算 9. 结果后处理
– CAD接口,IGES/VDA格式 – CAD模型整理 – 网格自动生成(模具/板料) – 网格修补 – 网格质量检查 – 工具定义 – 边界条件设置
• 求解 • 后处理
– 变形、云图 – 变形及云图的动画显示 – FLD – 接触力
基于Dynaform软件的板料冲压成形仿真操作指引

基于Dynaform 软件的板料冲压成形仿真操作指引1 常用仿真术语定义:冲压成形:用模具和冲压设备使板材产生塑性变形获得形状、尺寸、性能合乎要求的冲压件的加工方法。
多在室温下进行。
其效率高,精度高,材料利用率也高,可自动化加工。
冲压成形工序与工艺:剪切:将板材剪切成条料、块料或具有一定形状的毛坯的加工工序称为剪切。
分平剪、斜剪和震动剪。
冲裁:借助模具使板材分离的工艺。
分为落料和冲孔。
落料--从板料上冲下所需形状尺寸坯料或零件的工序;冲孔-- 在工件上冲出所需形状孔的工序。
弯曲:在弯曲力矩作用下,使平板毛坯、型材、管材等产生一定曲率和角度,形成一定形状冲压件的方法。
拉深:冲裁得到的平板毛坯成形成开口空心零件的冲压加工方法。
拉伸参数:• 拉深系数m :拉深零件的平均直径 d 与拉深前毛坯 D 之比值m, m = d/D ;• 拉深程度或拉深比:拉深系数 m 的倒数 1/m ;• 极限拉深系数:毛坯直径 D 确定下,能拉深的零件最小直径 d 与D 之比。
胀形:指将材料不向变形区转移,只在变形区内产生径向和切向拉深变形的冲压成形方法。
翻边:在毛坯的平面或曲面部分的边缘,沿一定曲线翻起竖立直边的成形方法。
板材冲压成形性能评价指标:硬化指数n 、厚度方向系数γ、成形极限图。
成形极限:是指冲压加工过程中所能达到的最大变形程度。
2 Dynaform 仿真分析目的及流程ETA/DYNAFORM 5.7是由美国工程技术联合公司(ENGINEERING TECHNOLOGY ASSOCIALTES, INC.)开发的一个基于LS-DYNA 的板料成形模拟软件包。
作为一款专业的CAE 软件,ETA/DYNAFORM 综合了LS-DYNA 强大的板料成形分析功能以及强大的流线型前后处理功能。
它主要应用于板料成形工业中模具的设计和开发,可以帮助模具设计人员显著减少模具开发设计时间和试模周期。
基于Dynaform 软件的仿真结果,可以预测板料冲压成形中出现的各种问题,如破裂、起皱、回弹、翘曲、板料流动不均匀等缺陷,分析如何及时发现问题,并提供解决方案。
dynaform操作流程文件
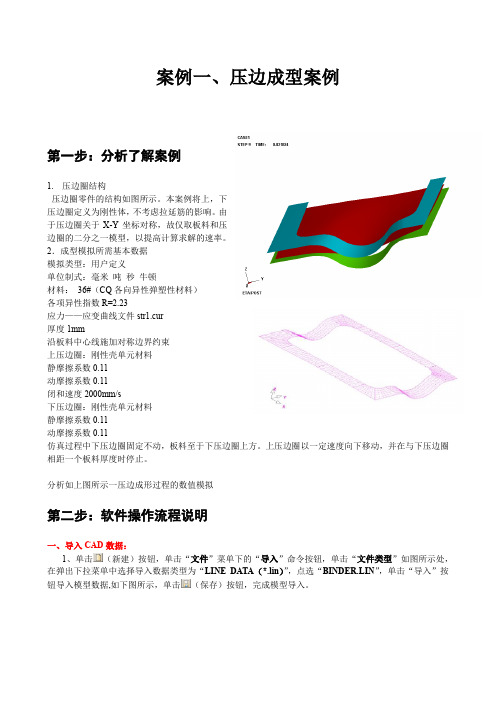
案例一、压边成型案例第一步:分析了解案例1.压边圈结构压边圈零件的结构如图所示。
本案例将上,下压边圈定义为刚性体,不考虑拉延筋的影响。
由于压边圈关于X-Y坐标对称,故仅取板料和压边圈的二分之一模型,以提高计算求解的速率。
2.成型模拟所需基本数据模拟类型:用户定义单位制式:毫米吨秒牛顿材料:36#(CQ各向异性弹塑性材料)各项异性指数R=2.23应力——应变曲线文件str1.cur厚度1mm沿板料中心线施加对称边界约束上压边圈:刚性壳单元材料静摩擦系数0.11动摩擦系数0.11闭和速度2000mm/s下压边圈:刚性壳单元材料静摩擦系数0.11动摩擦系数0.11仿真过程中下压边圈固定不动,板料至于下压边圈上方。
上压边圈以一定速度向下移动,并在与下压边圈相距一个板料厚度时停止。
分析如上图所示一压边成形过程的数值模拟第二步:软件操作流程说明一、导入CAD数据:1、单击(新建)按钮,单击“文件”菜单下的“导入”命令按钮,单击“文件类型”如图所示处,在弹出下拉菜单中选择导入数据类型为“LINE DATA(*.lin)”,点选“BINDER.LIN”,单击“导入”按钮导入模型数据,如下图所示,单击(保存)按钮,完成模型导入。
2、单击“工具”菜单下的“分析设置”命令按钮,在弹出的分析设置对话框中设置“接触间隙”为1mm,拉延类型为“Userdefine”,用户定义,如右图所示。
二、单元划分1、划分板料单元(1)、单击(关闭零件层)按钮,在弹出的对话框中仅留下曲线零件层,单击右下角的“当前零件层”按钮,在弹出对话框中点选“BLANK”零件层为当前零件层,如右图所示。
(2)、单击“工具”菜单下的“毛坯生成器”命令按钮,在在弹出的单元对话框中单击“边界线”按钮,点选曲线中的矩形坯料曲线,在弹出的单元划分对话框中输入尺寸6,单击“确定”按钮,结果如图所示。
(3)、保存文件2、划分下压边圈单元(1)、单击(关闭零件层)按钮,在弹出的对话框中仅留下压边曲线零件层,单击右下角的“当前零件层”按钮,在弹出对话框中点选“LWRING”零件层为当前零件层,如右图所示。
基于Dynaform软件的汽车内衬板冲压成形模拟

基于Dynaform软件的汽车内衬板冲压成形模拟
郑鹏;韩方方;姜彤
【期刊名称】《沈阳工业大学学报》
【年(卷),期】2009(031)005
【摘要】针对汽车覆盖件冲压成形后会出现起皱、拉裂等各种缺陷问题,以汽车覆盖件中最常用的内衬板为研究对象对其进行冲压仿真.详细阐述了用Dynaform 5.6软件实现板料成形有限元仿真的基本步骤及修正方法.模拟结果表明,所出现的起皱现象及增厚率都超出了允许范围,并提出在凹模入口处设置拉延筋以平衡材料流入量的修正方法,修正后的模拟结果基本理想.所阐述的板材冲压数值模拟方法,可显著降低模具加工成本和制作周期,为模具设计提供参考.
【总页数】5页(P548-552)
【作者】郑鹏;韩方方;姜彤
【作者单位】沈阳工业大学,机械工程学院,沈阳,110870;沈阳工业大学,机械工程学院,沈阳,110870;沈阳工业大学,机械工程学院,沈阳,110870
【正文语种】中文
【中图分类】TH16
【相关文献】
1.基于Dynaform的汽车前门外板冲压成形模拟分析 [J], 江明天;彭成允;王书胜;潘燕
2.基于Dynaform的汽车覆盖件冲压数值模拟可成形性研究 [J], 陈思;阎开印;丁
国富
3.基于Dynaform的汽车零件冲压成形模拟的研究 [J], 母德强;陈思
4.基于Dynaform的汽车内盖板热冲压成形数值模拟 [J], 苏曦;陈泽中;茹林潺;魏雅新
5.基于DYNAFORM的汽车车身覆盖件冲压成形数值模拟 [J], 周小灵
因版权原因,仅展示原文概要,查看原文内容请购买。
冲压软件dynaform详细讲解

冲压软件dynaform详细讲解•引言•dynaform软件功能介绍•dynaform软件操作指南•dynaform在冲压工艺中的应用实例•dynaform软件高级功能探讨•dynaform软件使用技巧与经验分享•总结与展望01引言掌握冲压模拟技术介绍dynaform 软件在冲压模拟方面的功能和应用,使读者能够掌握该技术并应用于实际生产。
提高生产效率和产品质量通过讲解dynaform 软件在优化冲压工艺参数、预测产品缺陷等方面的作用,帮助读者提高生产效率和产品质量。
深入了解冲压工艺有更深入的了解,包括冲压过程、材料变形、模具设计等。
目的和背景软件概述软件功能应用领域技术特点02 dynaform软件功能介绍前处理功能灵活的网格划分工具强大的CAD数据接口便捷的工艺设置丰富的材料库内置多种常用材料参数,用户可直接调用或自定义材料属性,满足各种冲压工艺需求。
ABCD高效求解算法自动重启动功能实时监控与反馈多核并行计算求解器功能后处理功能全面的结果展示可展示多种物理量的计算结果,如应力、应变、位移、速度等,帮助用户全面了解冲压过程的力学行为。
强大的后处理工具提供丰富的后处理工具,如云图、矢量图、动画等,方便用户对计算结果进行可视化分析和处理。
自定义报告生成支持用户自定义报告模板和格式,可快速生成符合需求的计算报告和图表。
数据导出与共享可将计算结果导出为多种通用数据格式,方便与其他软件或平台进行数据交换和共享。
03 dynaform软件操作指南界面介绍及基本操作主界面视图操作文件管理建立模型提供丰富的建模工具,支持创建点、线、面等几何元素,构建完整的冲压模型。
导入模型支持导入多种格式的CAD模型,如IGES、STEP等,实现与其他CAD软件的协同工作。
模型修复提供模型修复功能,自动检测并修复模型中的错误,确保模型的正确性。
模型建立与导入内置丰富的材料库,支持用户自定义材料属性,如弹性模量、泊松比、密度等。
第 6 章 基于etaDYNAFORM 的冲压模有限元仿真.

第6章 基于eta/DYNAFORM 的冲压模 有限元仿真(Typical Examples of FiniteElement Analysis Based oneta /Dynaform)教学目标在板料成形过程中,传统的设计方法很难预测其在冲压成形过程中板料的破裂、起皱、减薄、划痕、回弹等缺陷;然而利用有限分析软件恰恰解决了这个问题,它能够对整个模具开发过程进行模拟。
其中eta/DYNAFORM 具有易学易懂、操作简便、直观等特点,从而为板料成形及模具设计提供帮助。
希望通过本章的学习,使学生基本掌握eta/DYNAFORM 软件的使用方法。
本章应该具备的能力:具备冲模理论、理论力学、材料力学基础知识,初步学会利用有限元分析软件进行辅助模具分析和设计。
教学要求 能力目标 知识要点权重 自测分数 掌握eta/DYNAFORM 的基本命令功能前处理、坯料工程、零件展开40% 掌握快速设置/拉延功能 板料、工具定义30% 掌握后处理分析功能成形极限图、厚度变化、应力云图30% 引例如右图所示带凸缘盒形制件,利用eta/DYNAFORM完成如下分析:(1) 运用eta/DYNAFORM 软件一步法展开凸缘盒形制件的毛坯外形。
(2) 运用eta/DYNAFORM 软件分析此凸缘盒形件是否可以一次拉深成形。
(3) 如不能一次拉深成形,那么R 取多大值制件可以一次拉深成形?模具设计与制造·158· ·158·众所周知,对于圆筒形制件拉伸模具来说,早已具有完整的设计、计算方法及其数据资料。
但对于圆锥形制件或盒形制件拉伸模具,就没有像圆筒形制件拉伸模具那样的解析理论,设计、计算变得尤为复杂,而且是半理论、半经验的设计方式。
为此,板料成形CAE 技术应运而生,它为解决上述难题提供了有效手段,已经成为国际塑性加工领域的一个研究应用热点。
从20世纪70年代后期开始,经过二十多年的发展,板料成形数值模拟技术逐渐走向成熟,已形成了商品化的板料成形分析CAE 软件,得到了许多工业部门的重视和应用:国外的著名大型汽车制造公司,都已开始应用板料成形分析CAE 软件指导板料成形件的开发和生产,产生了很好的经济效益。
dynaform使用教程
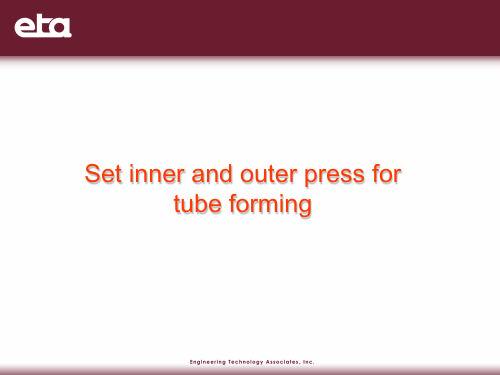
定义板料内外压力
点击Utilities->Load Curve,点击CREATE LOAD CURVE,定义载荷曲线定义1, Curve Number=1,Curve Name=inner press,曲线定义如下,OK完成定义
定义板料内外压力
同理定义载荷曲线2,Curve Number=1,Curve Name=inner press,曲线定义如下, OK完成定义
定义工具运动曲线
定义END1的运动曲线,点击Define Load Curve 点击Auto,在Motion Curve输入如下 曲线
定义工具运动曲线
同理定义END2的运动曲线
定义板料内外压力
点击Preprocess->Boundary Condition->LOADING OPTIONS 选择Pressure,点击Create新建,在LOAD SET NUMBER中点击OK 在ELEMENT PRESSURE中点击OK
定义板料
点击Tools->Define Blank,定义板料如下
定义工具
点击Tools->Define Tools,选择User Define Tools,点击New,新建工具,选择对应 的part。
定位工具
点击Tools->Position Tools->Auto Position,Apply进行定位。 如果导入的模型已经定 位好了,此步可以省略。
定义板料内外压力
在Select Elements对话框中勾选Select By,选择tube层,点击OK确认 在ELEMENT PRESSURE中点击Cancel退出,完成定义,需要注意的是,载荷方向 与单元法向相反,在定义载荷曲线时要注意载荷的正负值
DYNAFORM材料成型工艺仿真

Dynaform软件适用的设备有:单动压力机、双动压力 机、无压边压力机、螺旋压力机、锻锤、组合模具和特种 锻压设备等。
材料成型工艺仿真
Dynaform 举例
材料成型工艺仿真
Dynaform 举例
材料成型工艺仿真
例1 单动拉延成形
材料成型工艺仿真
对 话 框 显 示 区
图形显示窗口
消息提示窗口
材料成型工艺仿真
Dynaform
Dynaform软件可应用于不同的领域,汽车、航空航 天、家电、厨房卫生等行业。可以预测成形过程中板料的 裂纹、起皱、减薄、划痕、回弹、成形刚度、表面质量, 评估板料的成形性能,从而为板成形工艺及模具设计提供 帮助。
材料成型工艺仿真
Dynaform
Dynaform软件设置过程与实际生产过程一致,操作上 手容易。来设计可以对冲压生产的全过程进行模拟:坯料 在重力作用下的变形、压边圈闭合过程、拉延过程、切边 回弹、回弹补偿、翻边、胀形、液压成形、弯管成形。
2、设定单位 Tools→Analysis Setup
单位
材料成型工艺仿真
拉延类型
工具、毛坯的接触类型: 用于成形的单面接触 冲压方向 接触间隙
setup→Auto setup
材料成型工艺仿真
3、自动设置
材料成型工艺仿真
模拟类型:
板料成形
管材的液压成形 工艺类型:单动成形模拟
板料厚度:
模具的参考零件表面
Dynaform 显示选项区
重新设置(Reset):恢复所有的选项至默认值。 线(Lines):开/关线显示。 曲面(Surface):开/关曲面显示。 单元(Elements):开/关单元显示。 收缩(Shrink):创建一单元图可减少20%尺寸。 法线(Normal):用箭头显示单元法线方向。 节点(Nodes):开/关节点显示。 隐藏(Hidden) 填充色(Fill Color) 渲染(Shade)
- 1、下载文档前请自行甄别文档内容的完整性,平台不提供额外的编辑、内容补充、找答案等附加服务。
- 2、"仅部分预览"的文档,不可在线预览部分如存在完整性等问题,可反馈申请退款(可完整预览的文档不适用该条件!)。
- 3、如文档侵犯您的权益,请联系客服反馈,我们会尽快为您处理(人工客服工作时间:9:00-18:30)。
基于Dynaform 软件的板料冲压成形仿真操作指引1 常用仿真术语定义:冲压成形:用模具和冲压设备使板材产生塑性变形获得形状、尺寸、性能合乎要求的冲压件的加工方法。
多在室温下进行。
其效率高,精度高,材料利用率也高,可自动化加工。
冲压成形工序与工艺:剪切:将板材剪切成条料、块料或具有一定形状的毛坯的加工工序称为剪切。
分平剪、斜剪和震动剪。
冲裁:借助模具使板材分离的工艺。
分为落料和冲孔。
落料--从板料上冲下所需形状尺寸坯料或零件的工序;冲孔-- 在工件上冲出所需形状孔的工序。
弯曲:在弯曲力矩作用下,使平板毛坯、型材、管材等产生一定曲率和角度,形成一定形状冲压件的方法。
拉深:冲裁得到的平板毛坯成形成开口空心零件的冲压加工方法。
拉伸参数:• 拉深系数m :拉深零件的平均直径 d 与拉深前毛坯 D 之比值m, m = d/D ;• 拉深程度或拉深比:拉深系数 m 的倒数 1/m ;• 极限拉深系数:毛坯直径 D 确定下,能拉深的零件最小直径 d 与D 之比。
胀形:指将材料不向变形区转移,只在变形区内产生径向和切向拉深变形的冲压成形方法。
翻边:在毛坯的平面或曲面部分的边缘,沿一定曲线翻起竖立直边的成形方法。
板材冲压成形性能评价指标:硬化指数n 、厚度方向系数γ、成形极限图。
成形极限:是指冲压加工过程中所能达到的最大变形程度。
2 Dynaform 仿真分析目的及流程ETA/DYNAFORM 5.7是由美国工程技术联合公司(ENGINEERING TECHNOLOGY ASSOCIALTES, INC.)开发的一个基于LS-DYNA 的板料成形模拟软件包。
作为一款专业的CAE 软件,ETA/DYNAFORM 综合了LS-DYNA 强大的板料成形分析功能以及强大的流线型前后处理功能。
它主要应用于板料成形工业中模具的设计和开发,可以帮助模具设计人员显著减少模具开发设计时间和试模周期。
基于Dynaform 软件的仿真结果,可以预测板料冲压成形中出现的各种问题,如破裂、起皱、回弹、翘曲、板料流动不均匀等缺陷,分析如何及时发现问题,并提供解决方案。
Dynaform 仿真分析分析的步骤和流程如下图:冲压成形分离工序剪切冲裁修边成形工序 弯曲拉深胀形翻边数值模拟分析流程总的来说分为前处理、求解计算和后处理三个主要部分。
其中,前处理可细分为读入零件几何模型、有限元网格划分、定义成形工具、生成及定义毛坯、定义拉延筋和设置成形参数等几个部分。
前处理的好坏直接影响到求解计算,关系到数值模拟结果的精确性。
一、前处理1.读入零件模型。
Dynaform软件可以直接读入由UG、CATIA和Pro/E等软件产生的数学模型。
以某公司的典型钣金件为例进行冲压成形数值模拟分析。
首先将零件的数学模型的IGES、VGA等格式文件导入DYNAFORM中,如图2所示。
图2 零件的数学模型Fig.2 The part’s mathematic model根据零件的数学模型和实际生产经验,编制的工艺路线为拉深-2.确定冲压方向Dynaform默认的冲压方向为-Z方向。
3.创建零件的单元模型选择菜单“Preprocess/Surface”命令,点击”Generate Middle Surface”按钮,进行零件中性层的抽取。
可删除原导入的零件模型,并编辑抽取中性层后的零件,重新命名为零件“Part”,将其ID序号数值设置为1,保存*.df文件。
4.创建零件1)分析此零件的几何模型,由于该零件的翻边工序在最后,故在模拟中不考虑翻边这道工序,将其拉平。
选择菜单栏“BSE/Preparation”,点击“Unfold Flange”命令,选择零件的翻边部位,此时翻边部分轮廓呈白色高亮显示,如图3所示。
图3 选择零件翻边部位2)点击“Accept”按钮,输入弯曲角“Bent Angle=180”,如图4。
点击“Delete Original Flanges”按钮,删除零件原有的翻边工艺修正,如图5,点击“DONE”完成。
删除翻边后的零件如图6。
此时系统会自动创建一个新零件“Unfolded”,选择菜单栏“Part/Add…To Part”命令,点击“Surface(s)”,点击“Part”按钮,选择系统新创建的零件“UNFOLDED”,返回“Add…To Part”,点击“Apply”。
至此零件“Part”创建成功,如图7。
图4 输入零件的翻边角度图5 删除原翻边图6 删除翻边后的零件图图7 创建的零件图3)创建零件网格将右下角的当前零件改为“Part”,选择菜单“Preprocess/Element”命令,选择“Surface Mesh/Part Mesh”按钮,最大网格尺寸设置为8,其它尺寸为缺省值。
点击“Select Surfaces”按钮,选择“Displayed Surf.”,此时零件“Part”呈白色高亮显示,点击“OK”和“Apply”按钮,并点击“Yes”加以确认,退出对话框。
零件网格如图8所示。
注意:在网格划分时一定要将右下角当前的零件设为和网格划分的零件一致,否则划分的网格不是当前的零件。
右下角的“Surfaces”可不选,此时零件的几何模型会隐藏,只显示网格。
图8 零件的网格模型5.创建Blank1)创建毛坯轮廓打开零件Part,用工具栏的“Surface Mesh/Part Mesh”对零件进行网格划分。
选择菜单栏“BSE/Preparation”命令,选择“Blank Size Estimate”按钮,设置“Material”选项下的“NULL”按钮,点击“Material Library”,选择材料“Europe/DX54D”,输入板料厚度“Thickness=1.2”,点击“Apply”按钮,进行毛坯展开计算,如图9。
(a) (b) (c)图9 毛坯的展开计算生成的毛坯轮廓如图10。
系统会自动创建OUTLINE零件。
在“Parts/Edit Part”下修改零件名称“OUTLINE”为“Blank”,点击“Modify”按钮,点击“OK”,如图11所示。
(注意右下角当前零件不能为“OUTLINE”,应改为其它零件名,不能对当前零件名进行修改和编辑)。
图10 展开后的毛坯轮廓图11 编辑毛坯零件名2)考虑毛坯余量,扩展毛坯轮廓选择菜单“Preprocess/Line/Point”,点击“Offset”进行偏移,选择边界轮廓,输入偏移距离为90mm,扩展后的边界线及其网格模型如图12所示。
图12 扩展后的毛坯轮廓3)划分毛坯网格将右下角的当前零件设为“Blank”,对毛坯进行网格划分。
在工具栏选择“Blank generator”命令,选择“Boundary line”,此时鼠标变成“+”符号,点击毛坯轮廓线选择,此时轮廓线会呈白色高亮显示,点击“OK”。
输入毛坯网格尺寸“Mesh Size/Element Size=8”,点击“OK”完成,如图13。
点击“Yes”确认网格大小。
毛坯划分网格后的模型如图14所示。
图13 毛坯网格尺寸图14 毛坯的网格模型6.创建Punch1)选择菜单“Parts/Create”,输入“Name=Punch”,编辑颜色,点击“OK”。
如图15所示。
在屏幕右下方会自动出现“Current Part=PUNCH”。
图15 创建Punch零件2)创建零件网格将“Part”零件的单元网格显示,选择“Parts/Add…To Part”,点击“Elements”按钮,选择“Displayed”,此时当前的零件网格会呈白色高亮状态,点击“OK”确认。
将所选网格加入到“To Part:PUNCH”,点击“…”选择刚创建的“PUNCh”,确认后关闭对话框,如图16所示。
此时“Part”零件的单元网格被添加到“Punch”零件中。
如图2-16所示。
此时“Part”零件只剩下Surfaces。
图16 Punch的网格模型3)PUNCH网格模型的法线方向检查点击菜单栏“Preprocess/Model Check/Repair”命令,点击“Auto Plate Normal”按钮进行法线方向检查。
选择其中任一单元,观察法线方向,点击“YES”或“NO”按钮。
注意,法线方向的设置总是由工具指向与坯料的接触面,如图17。
图17 Punch的法线方向检查4)网格边界检查点击菜单栏“Preprocess/Model Check/Repair”命令,点击“Boundary Display”按钮进行边界检查。
通常只允许除边缘轮廓边界呈白色高亮显示外,其余部位均保持不变。
如图18。
如果其余部分的网格有白色高亮显示,则说明在白色高亮处的单元网格有缺陷,须进行修补或重新网格划分。
修补可点击“Gap Repair”按钮。
完成边界检查后,若网格边界无缺陷,可点击工具栏中的“Clear Highlight”,清除边缘轮廓高亮显示部位。
图18 网格模型的边界检查7. 创建凹模DIE1)偏置得到DIE的单元网格选择菜单“Parts/Create”,输入零件名称“Name”为凹模“DIE”,则右下角的当前零件自动变为“DIE”。
打开零件“Punch”,选择菜单“Preprocess/Element”下的“Offset”命令,关闭“In OriginalPart”复选框,使得新生成单元放置在当前零件中,关闭“Delete Original Element”复选框,保留原始零件中的单元。
“Copy Number”为1,板料厚度“Thickness”的设定值为1.32(即为1.1t,其中t为板料厚度)。
显示“Select Element”对话框,点击“Displayed”,则所有被选单元呈白色高亮显示,点击“OK”返回,则复制后的单元自动生成到“DIE”中。
关闭零件“Punch”显示。
新建的DIE的网格模型如图19所示。
图19 偏置得到的DIE的网格模型8. 创建BINDER1) 设置Die为工具选择菜单栏“DFE/Preparation”的“Define”命令下,将“Tool/Tool Name”下添加“DIE”为工具。
选择“DFE/Binder”,在“Create”命令下选择“Binder Type”为“Flat Binder”,并输入“Binder Size”的尺寸,点击“Apply”,如图20所示。
此时右下角自动创建新零件“C_BINDER”,关闭零件“DIE”的显示,生成的压边圈轮廓表面如图21所示。
图20 创建BINDER过程图图21 压边圈的轮廓表面2) 划分网格在工具栏“Surface Mesh”下选择“Tool Mesh”,输入最大网格尺寸为20mm,选择压边圈的轮廓表面,点击“Apply”和“YES”,关闭右下角的Surfaces显示,则得到如图22的压边圈网格模型。