奔驰新 C级的钢铝混合车身结构
基于轻量化设计的新能源汽车车身设计
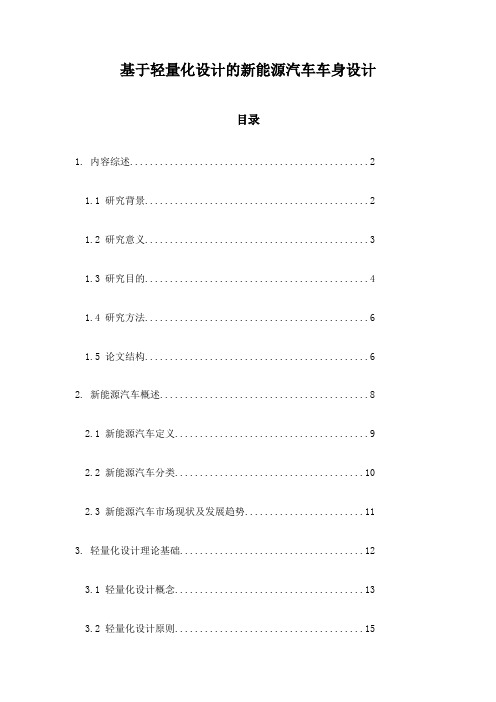
基于轻量化设计的新能源汽车车身设计目录1. 内容综述 (2)1.1 研究背景 (2)1.2 研究意义 (3)1.3 研究目的 (4)1.4 研究方法 (6)1.5 论文结构 (6)2. 新能源汽车概述 (8)2.1 新能源汽车定义 (9)2.2 新能源汽车分类 (10)2.3 新能源汽车市场现状及发展趋势 (11)3. 轻量化设计理论基础 (12)3.1 轻量化设计概念 (13)3.2 轻量化设计原则 (15)3.3 轻量化设计方案 (16)4. 新能源汽车车身轻量化设计方案 (17)4.1 车身结构优化设计 (18)4.2 材料选用与连接技术 (19)4.3 制造工艺优化 (20)5. 新能源汽车车身轻量化设计案例分析 (21)5.1 案例一 (22)5.2 案例二 (23)6. 新能源汽车车身轻量化设计评价与展望 (25)6.1 车身轻量化设计效果评价方法 (26)6.2 新能源汽车车身轻量化设计的发展趋势 (28)6.3 新能源汽车车身轻量化设计的挑战与对策 (29)7. 结论与建议 (30)7.1 主要研究成果总结 (31)7.2 建议与展望 (32)1. 内容综述随着全球环境问题日益严重,新能源汽车作为一种绿色、环保的交通工具,越来越受到各国政府和汽车制造商的重视。
在新能源汽车的发展过程中,车身设计作为影响车辆性能、安全性、舒适性和美观性的关键因素,其轻量化设计显得尤为重要。
本文旨在通过对新能源汽车车身设计的现状分析,探讨轻量化设计在新能源汽车车身设计中的应用,以期为新能源汽车车身设计提供有益的参考。
本文将对新能源汽车车身轻量化设计的概念进行阐述,明确轻量化设计的目标和意义。
本文将对新能源汽车车身轻量化设计的关键技术进行分析,包括材料选择、结构优化、制造工艺等方面。
结合实际案例,对新能源汽车车身轻量化设计的最新进展进行介绍。
本文将对新能源汽车车身轻量化设计的发展趋势进行展望,为未来新能源汽车车身设计提供指导。
新能源汽车车身结构研究
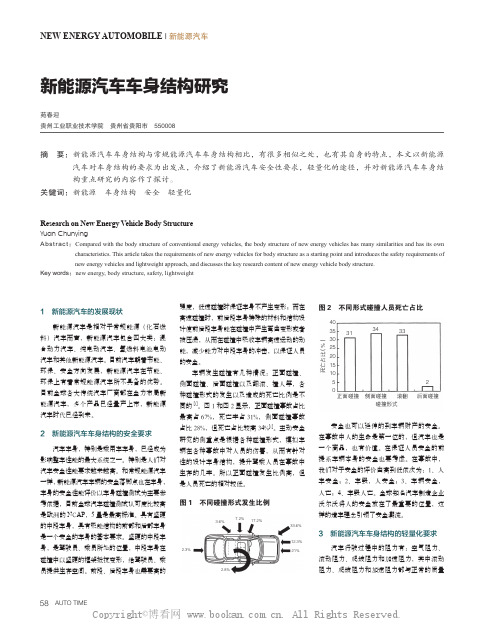
成正比,有资料研究表明:汽车自重每减少 10%,燃油消耗可降低 6% ~ 8%,排放可降 低 4% 左右 [1]。
汽车整车有四个部分组成,分别是:车身、 底盘、发动机和汽车电子。对于乘用车来说, 车身占整车质量的 40% ~ 60%,约 70% 的油 耗是用在车身质量上的,因此,汽车车身特 别是白车身的轻量化是车辆轻量化的重要部 分,国内外也大多以车身结构优化作为整车 轻量化的重点 [1]。
关键词:新能源 车身结构 安全 轻量化
Research on New Energy Vehicle Body Structure Yuan Chunying
A b s t r a c t :Compared with the body structure of conventional energy vehicles, the body structure of new energy vehicles has many similarities and has its own characteristics. This article takes the requirements of new energy vehicles for body structure as a starting point and introduces the safety requirements of new energy vehicles and lightweight approach, and discusses the key research content of new energy vehicle body structure.
新能源汽车车身结构轻量化的途径: (1)新材料的应用 使用新材料是实现汽车轻量化的重要手 段。以铝合金材料、高强度钢材、碳纤维为 代表的新材料已经在大量使用。新材料的使 用不仅仅是对传统材料的替代,它还涉及多 种学科及技术的支持,比如物理、化学学科, 材料试验检查技术、零部件设计制造技术、 新材料回收技术等等。 车身轻量化在新材料使用中,高强度钢 材最为普遍,目前车身制造,已经普及使用 高强度的汽车专用钢材。铝合金车身的使用 在材料轻量化中效果是最好的一个,汽车品 牌中捷豹、奥迪、特斯拉都有铝合金车身的 产品问世。其减重效果优于高强度钢,但铝 合金车身价格是钢车身的 3 倍左右,所以只 有在高端品牌中铝合金车身才有市场。 轻量化就是在质量、性能和价格三者之 间找平衡。与高强度钢、铝合金相比,碳纤 维有密度优势,有比较高的比强度和比刚度, 还有比较好的耐腐蚀性,这是非金属材料比 较典型的特点。但价格是比较大的劣势,碳 纤维的综合成本是铝的综合成本的 2 ~ 2.5 倍 [3]。现阶段,在轻量化中碳纤维可以和铝合 金搭配,作为补充材料使用,也可以只在关
车身典型连接结构设计

2021.09 中国.合肥
目录
CONTNETS
01 车身连接形式简介 02 车身典型连接结构设计 03 总结
车身连接形式简介
01
PART ONE
01
车身连接形式简介
车身形式
4
01
电动车车身平台介绍
车身结构形式
多材料复合车身
全铝车身
钢铝混合车身
钢制车身
复合材料:CFRP 铝合金:挤压+冲压+铸造 钢:热成形+高强钢…
在进行点焊设计时需重点关注间距、结构及关键焊点。
8
02
车身典型连接结构设计
点焊设计:间距
焊点间距的设计,需要满足相应部位的性能要求。一般来说根据不同位置性能及结构特性要求,将间距分
为三个档次,即30±5mm、40±5mm、50±5mm;
碰撞部位关键零部件
座椅和安全带安装点关键零部件
其他区域零部件
9
铝合金:挤压+冲压+铸造
铝合金:挤压+冲压+铸造 钢:热成形+高强钢…
钢:热成形+高强钢+低碳钢
5
01
电动车车身平台介绍
车身连接形式
6
车身典型连接结构 设计
02
PART TWO
02
车身典型连接结构设计
点焊
电阻点焊,是指利用电流通过焊件及接触处产生的电阻热作为热源将焊件局部加热到熔化或塑性状态,同 时加压进行焊接,使之形成金属结合的一种方法。焊接时,不需要填充金属,生产率高,焊件变形小,容易实 现自动化。
平行双排焊点
45mm
W型双排焊点
30-45mm
铝合金客车车身连接结构分析
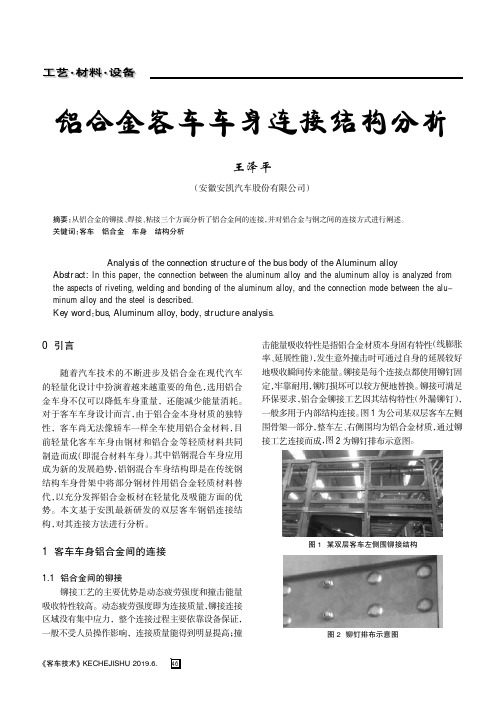
铝合金客车车身连接结构分析王泽平(安徽安凯汽车股份有限公司)摘要:从铝合金的铆接、焊接、粘接三个方面分析了铝合金间的连接,并对铝合金与钢之间的连接方式进行阐述。
关键词:客车铝合金车身结构分析Analysis of the connection structure of the bus body of the Aluminum alloy Abstract:In this paper,the connection between the aluminum alloy and the aluminum alloy is analyzed from the aspects of riveting,welding and bonding of the aluminum alloy,and the connection mode between the alu原minum alloy and the steel is described.Key word:bus,Aluminum alloy,body,structure analysis.0引言随着汽车技术的不断进步及铝合金在现代汽车的轻量化设计中扮演着越来越重要的角色,选用铝合金车身不仅可以降低车身重量,还能减少能量消耗。
对于客车车身设计而言,由于铝合金本身材质的独特性,客车尚无法像轿车一样全车使用铝合金材料,目前轻量化客车车身由钢材和铝合金等轻质材料共同制造而成(即混合材料车身)。
其中铝钢混合车身应用成为新的发展趋势,铝钢混合车身结构即是在传统钢结构车身骨架中将部分钢材件用铝合金轻质材料替代,以充分发挥铝合金板材在轻量化及吸能方面的优势。
本文基于安凯最新研发的双层客车钢铝连接结构,对其连接方法进行分析。
1客车车身铝合金间的连接1.1铝合金间的铆接铆接工艺的主要优势是动态疲劳强度和撞击能量吸收特性较高。
动态疲劳强度即为连接质量,铆接连接区域没有集中应力,整个连接过程主要依靠设备保证,一般不受人员操作影响,连接质量能得到明显提高;撞击能量吸收特性是指铝合金材质本身固有特性(线膨胀率、延展性能),发生意外撞击时可通过自身的延展较好地吸收瞬间传来能量。
试析车身零部件铝合金及钢铝混合连接工艺

试析车身零部件铝合金及钢铝混合连接工艺为解决汽车节能降耗的问题,所有汽车制造商都在通过车身整体减重来降低百公里油耗。
但减重同时又必须保证汽车整体结构刚度,并提高汽车安全性能,所以整车厂通过大量使用轻质、高强材料(比如各种高强钢、铝合金、镁合金、复合材料等)替代传统的普通钢材以实现车身轻量化,达到减重目的。
铝合金由于比重小、强度高,在顯著减重的同时仍能够大幅提高车身零部件的刚性,所以使用铝合金代替部分钢材是目前汽车制造的主要减重措施。
达到同样的力学性能指标,铝比钢轻60%,但在承受同样冲击时,铝板比钢板多吸收冲击能50%。
车身是汽车中重量最大的部件,通过在全钢车身中引入铝合金材料,实现“钢铝混合材料车身结构”,已成为车身零部件减重的必然趋势。
在实现“钢铝混合材料车身结构”零部件制造中,铝合金连接及钢铝混合连接技术具有重要的作用。
目前车身零部件铝合金连接的工艺有铝弧焊、铝点焊、铝螺柱焊、摩擦焊、激光焊、压铆、拉铆、旋铆、热熔自攻螺丝连接(FDS)、自冲铆接(SPR)等。
而钢铝混合连接时为解决异金属接触面电化学腐蚀问题,须在连接钢铝零件之间涂上结构胶后再用FDS、SPR等工艺。
本文重点介绍铝弧焊、铝点焊、铝螺柱焊、FDS、SPR这五种使用频率较高的连接工艺和应用。
1 铝合金弧焊1.1 铝合金弧焊的特点由于铝合金焊接时极易氧化,生成氧化铝(Al2O3),易造成夹渣、未熔合、未焊透等缺欠。
铝表面氧化膜会吸附大量水分,易使焊缝产生气孔。
此外,铝及其合金的线胀系数大,导热性强,焊接时变形和应力较大,易产生裂纹。
因此,一般铝弧焊接前须进行表面清理,清除表面氧化膜,并在焊接过程采用高纯氩或氩氦混合气体保护,防止其氧化。
钨极氩弧焊时,选用交流电源,通过“阴极清理”作用,去除氧化膜。
采用大规范的熔化极气体保护焊时,在直流正接情况下,可不需要“阴极清理”。
为防止热裂纹的产生,可采用调整焊丝成分与焊接工艺的措施,对含镁量超过3%的Al-Mg合金板焊接时,可采用含Mg量超过3.5%或超过5%的铝镁合金焊丝,具有较好的力学性能和耐蚀性能。
6. 汽车轻量化的九大关键工艺
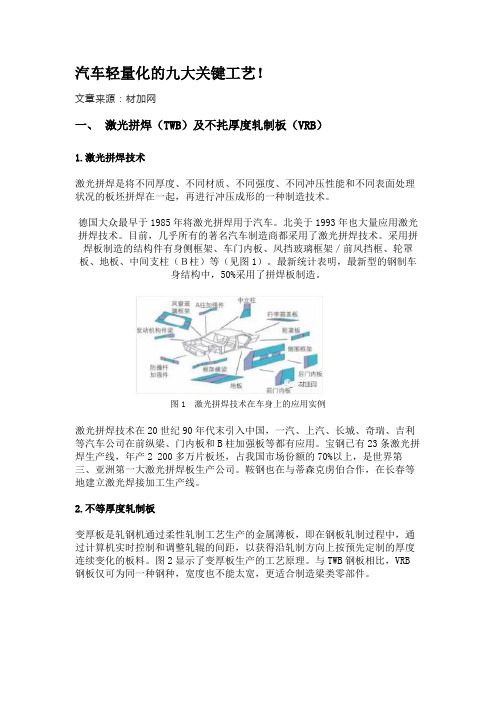
汽车轻量化的九大关键工艺!文章来源:材加网一、激光拼焊(TWB)及不扥厚度轧制板(VRB)1.激光拼焊技术激光拼焊是将不同厚度、不同材质、不同强度、不同冲压性能和不同表面处理状况的板坯拼焊在一起,再进行冲压成形的一种制造技术。
德国大众最早于1985年将激光拼焊用于汽车。
北美于1993年也大量应用激光拼焊技术。
目前,几乎所有的著名汽车制造商都采用了激光拼焊技术。
采用拼焊板制造的结构件有身侧框架、车门内板、风挡玻璃框架/前风挡框、轮罩板、地板、中间支柱(B柱)等(见图1)。
最新统计表明,最新型的钢制车身结构中,50%采用了拼焊板制造。
图1 激光拼焊技术在车身上的应用实例激光拼焊技术在20世纪90年代末引入中国,一汽、上汽、长城、奇瑞、吉利等汽车公司在前纵梁、门内板和B柱加强板等都有应用。
宝钢已有23条激光拼焊生产线,年产2 200多万片板坯,占我国市场份额的70%以上,是世界第三、亚洲第一大激光拼焊板生产公司。
鞍钢也在与蒂森克虏伯合作,在长春等地建立激光焊接加工生产线。
2.不等厚度轧制板变厚板是轧钢机通过柔性轧制工艺生产的金属薄板,即在钢板轧制过程中,通过计算机实时控制和调整轧辊的间距,以获得沿轧制方向上按预先定制的厚度连续变化的板料。
图2显示了变厚板生产的工艺原理。
与TWB钢板相比,VRB 钢板仅可为同一种钢种,宽度也不能太宽,更适合制造梁类零部件。
图2 不等厚度轧制板生产原理德国Mubea公司有两条变厚板生产线,年产7万t。
板厚为0.7~3.5m m,原始板料的最高强度为800MP a级别。
目前,欧洲70余个车型使用变厚板或者变厚管产品。
奔驰C级车中通道加强板、前地板纵梁、后保险杠、后地板横梁等11个零件使用了VRB钢板。
我国宝钢和东北大学均开展了VRB钢板的研发和生产工作,目前具备了小批量供货的能力。
借助于强大的材料开发能力,宝钢形成了VRB零件的设计、材料开发、成形过程模拟、模具设计和产品质量评估的能力,并已试制成功前纵梁、仪表板支架、顶盖横梁等零件,同时也轧制成功了1 500MPa级别的非镀层和铝硅镀层的热冲压成形钢板,成功试制了热冲压成形VRB中通道零件。
钢铝混合车身先进连接工艺

钢铝混合车身先进连接工艺摘要:汽车车身的连接设计与制造是汽车生产中的重要环节,也是汽车生产新技术研究的主要内容。
文章主要阐述了汽车车身相关连接设计方法及新工艺的应用,希望对车身相关从业人员予以借鉴参考。
关键词:车身;连接设计;新技术前言低碳环保、安全节能、智能化、轻量化是汽车行业发展趋势,车身连接设计开发与制造是整车开发重要组成部分。
随着中国汽车保有量的不断增加,汽车增速逐渐放缓,更新换代周期越来越短,汽车市场的竞争也越来越激烈,如何提高车身的连接设计及制造水平,提升产品竞争力是当前研究的热点。
1汽车车身连接设计技术为保证整车结构刚度及安全性能要求,采用了以轻质铝合金材料为主,超高强度钢板为辅的钢铝混合车身结构。
整车铝合金比例达到88%。
在钢铝混合车身结构连接设计时,大量使用了钢铝混合车身连接工艺:自冲铆接(SPR)、自攻螺接(FDS)、螺栓连接、压铆、拉铆等冷连接工艺以及铝点焊、激光焊、铝弧焊、铝螺柱焊等热连接工艺。
汽车在使用钢铝混合车身先进连接工艺时,实现了两大创新:(1)热连接技术与冷连接技术的组合应用,优势互补;(2)几乎覆盖了所有车身连接工艺。
汽车车身钢铝混合连接技术目前已经大量应用,形成了一系列完整的数据与经验,将引领行业发展,指引方向。
1.1车身的连接设计开发流程当前主流汽车厂商通常将整车开发过程分为多个阀门进行管控,并对每个阀门制定了通过原则,以确保每个阶段开发活动满足要求,可以进入到下一个阶段。
全新整车连接设计开发一般分为预研立项阶段、概念连接设计阶段、详细连接设计阶段、连接设计验证阶段、生产认证与量产阶段。
每个阀门点都有相应的核心工作和通过原则,只有满足相应的要求,才能进入下一个阀点。
各个开发阶段相互交叉、同步进行,通过项目管理团队对整车开发质量、成本、进度进行协调管控。
车身连接设计开发是整车开发的一个重要组成部分,遵循整车开发流程并贯穿整车开发的全过程。
1.2车身平台化模块化随着汽车行业竞争加剧以及消费者对汽车品质要求的不断提高,各大汽车厂商推出新车型的速度不断加快。
全承载式纯电动城市客车钢铝混合骨架强度分析及改进

全承载式纯电动城市客车钢铝混合骨架强度分析及改进胡付超;林伟;方超【摘要】基于HyperMesh建立全承载式纯电动城市客车钢铝混合骨架的有限元模型,采用ANSYS软件对该钢铝混合骨架强度进行分析,并对产生集中应力的部位进行改进,为钢混合骨架在全承载式城市客车中的应用提供参考。
%Based on HyperMesh, the authors build the finite element model for steel and aluminum monocoque mixed framework of a pure electric city bus, then analyze the strength of the steel and aluminum mixed framework by ANSYS software, and improve the structure of stress concentration area, in order to provide a reference for applica-tion of the steel and aluminum mixed framework to the monocoque city bus.【期刊名称】《客车技术与研究》【年(卷),期】2016(038)004【总页数】3页(P23-25)【关键词】纯电动;城市客车;钢铝混合骨架;结构强度【作者】胡付超;林伟;方超【作者单位】山东沂星电动汽车有限公司,山东临沂 276017;山东沂星电动汽车有限公司,山东临沂 276017;山东沂星电动汽车有限公司,山东临沂 276017【正文语种】中文【中图分类】U463.83+1;U469.72目前,我国市场上已经有多个品牌的纯电动城市客车投入运营,但绝大多数都是将传统骨架进行简单改造而成。
虽然能够满足整车强度要求,但是车身整备质量较大,续驶里程被相对缩短[1],因此,对纯电动客车提出了采用铝合金轻型材骨架的要求。
- 1、下载文档前请自行甄别文档内容的完整性,平台不提供额外的编辑、内容补充、找答案等附加服务。
- 2、"仅部分预览"的文档,不可在线预览部分如存在完整性等问题,可反馈申请退款(可完整预览的文档不适用该条件!)。
- 3、如文档侵犯您的权益,请联系客服反馈,我们会尽快为您处理(人工客服工作时间:9:00-18:30)。
奔驰2014款C级车的新技术
钢铝混合车身结构
新C级的车身结构中,铝合金、热成型高强度钢以及超高强度钢材使用的比例相比前作大量提升,尤其是铝材的使用更是提升至整体车身的48%。
因此,奔驰将新C级的车身结构称为“钢铝混合架构”,不仅车身重辆大幅缩减了70kg,整车更是减去了100kg的“赘肉”。
另外,热成型高强度钢和超高强度钢材为驾驶者营造出了坚固的生存空间,而精确设计的钢铝混合结构以及车身板材又可以有效地吸收和分散传导撞击的能量,在奔驰内部的安全测试中,新C级达到了很高的水平。
旗舰规格的电子辅助安全系统
很多人应该对新S级的奔驰智能驾驶系统记忆犹新,大量的车辆辅助系统以及传感器、摄像机交联组成的一整套智能安全辅助系统可以为驾驶者提供最为全面的安全保护。
当在S级车型上首秀之后,这套系统也将出现在新C级之上,这使其在电子辅助安全系统方面力压同级对手。