支架的机械加工工艺规程编制和专用夹具设计
支架加工工艺规程及工装夹具设计

⽀架加⼯⼯艺规程及⼯装夹具设计⽬录摘要 (1)引⾔ (1)第⼀章.零件的⼯艺分析及⽣产类型的确定 (5)1.1.零件的技术要求 (5)第⼆章确定⽑坯.绘制⽑坯简图 (6)2.1.选择⽑坯 (6)2.2.确定⽑坯的尺⼨公差和机械加⼯余量 (6)第三章拟订⼯艺路线 (7)3.1.定位基准的选择 (7)3.2.加⼯阶段的划分 (7)3.3.⼯序的集中与分散 (7)3.4.⼯序顺序的安排 (7)3.5.确定⼯艺路线 (8)第四章机床设备及⼯艺装备的选⽤ (8)4.1.机床设备的选⽤ (9)第五章加⼯余量.⼯序尺⼨和公差的确定 (9)5.1⽑坯余量及⼯序余量的确定 (9)5.2切削⽤量的选择 (11)第六章切削⽤量.时间定额的计算 (11)6.1 确定切削⽤量及基本⼯时 (12)第七章夹具设计 (16)7.1 问题的提出 (16)7.2 夹具的设计 (17)总结 (16)参考⽂献 (16)摘要能通过运⽤机械制造⼯艺学课程中的基本理论以及在⽣产实习中学到实践知识,正确的解决⼀个零件在加⼯过程中的定位.夹紧以及⼯艺路线安排.⼯艺尺⼨确定等问题,保证零件的加⼯质量学会使⽤图表资料以及⼿册,掌握与本本设计有关的各种资料的名称,出处,能够做到熟练运⽤。
因此,它在我们的⼤学⽣活中占有重要的地位。
就我个⼈⽽⾔,我希望能通过这次课程设计对⾃⼰未来从事的⼯作进⾏⼀次适应性训练,从中锻炼⾃⼰分析问题,解决问题的能⼒,为今后参加⼯作打下⼀个良好的基础。
由于能⼒有限,设计当中可能会有不⾜之处,恳请各位⽼师给予批评指正。
Abstract:Can through the utilization machine manufacture technology curriculum in elementary theory as well as in theof material with the notebook the name, the source, can achieve the skilled utilization. Therefore, it holds the important status in ours university life. To my own opinion, I hoped that can the work which will be engaged to own future carry on an adaptability training through this curriculum project, will exercise itself to analyze the question, will solve the question ability, will start the work for the present to build a good foundation. Because ability is limited, middle the design will possibly have the deficiency, will request earnestly fellow teachers to give the criticism to point out mistakes.引⾔机械⼯业是⼀种基本⼯业形式,对于我们国家来说,它关系到国计民⽣的⽅⽅⾯⾯。
毕业设计(论文)-支架零件加工工艺规程及夹具设计

广东技术师范学院天河学院毕业设计题目:支架零件加工工艺规程及夹具设计系别:机电工程系专业:机械制造与自动化姓名:学号:指导教师:日期:2112年 4 月10 日广东技术师范学院天河学院毕业设计(论文)任务书————————————☆————————————设计(论文)题目:支架零件加工工艺规程及夹具设计姓名:系别:机电工程系专业:机械制造与自动化班级:机制091 学号:指导老师:教研室主任:一、基本任务及要求:设计任务是:按照支架零件的技术要求,设计一套工艺规程和一副专业机床夹具;其具体要求如:1)支架零件的生产批量为中批;2)要求在通用机床中采用专用夹具加工;3)保证支架的装配性,根据支架的技术要求,重要的是要保证其位置精度要求;4)设计夹具合理的工艺规程和专用机床夹具;二、进度安排及完成时间:1.宣布设计任务、收集阅读有关设计资料2012年3月1日~2012年3月15日2.调查研究、分析设计课题完成开题报告、实习2012年3月16日~2012年3 月25日3.总体方案设计:1)工艺线路方案的确定2012年3月25日~2012年3月27日2)绘制加工工序图2012年3月27日~2012年3月31日3)主要技术参数的确定2012年4月1日~2012年4月4日4)详细设计:1)工艺规程设计(工艺过程卡1张、工序卡2张)2012年4月4日~2012年4月10日2)草图设计2012年4月10日~2012年4月12日3)夹具总装配图设计2012年4月12日~2012年4月15日4)夹具零件工作图设计(全套) 2012年4月15日~2012年4月20日5)撰写设计、计算说明书2012年4月20日~2012年4月25日6)毕业答辩2012年4月26日~2010年5月1日摘要机械加工行业作为一个传统而富有活力的行业,近十几年取得了突飞猛进的发展,在新经济时代,行业呈现了新的发展趋势,由此对其质量、性能要求有了新的变化。
车床C6140A支架机械加工工艺及夹具设计

车床C6140A支架机械加工工艺及夹具设计车床是一种用途广泛的机床,用于加工各种工件的外形和内形。
在车床加工过程中,支架是一个关键的零件,它用于支撑工件,使其在车床上转动并进行加工。
本文将介绍车床C6140A支架的机械加工工艺以及一道工序的夹具设计。
首先,我们需要进行车床C6140A支架的机械加工工艺规划。
机械加工工艺规划是指在加工过程中,根据工件的形状、尺寸和要求,确定加工工艺流程和使用的刀具。
对于车床C6140A支架,通常的加工工艺流程包括车削、铣削、钻削和切割等。
在车削工艺中,我们可以采用外圆车削和内孔车削的工艺流程。
首先,通过车削外圆的工序,将工件的外圆加工成所需的直径和精度要求。
然后,再进行内孔的车削工序,将工件中心部位加工成所需的孔径和精度要求。
在铣削工艺中,我们可以采用平面铣削和凸台铣削的工艺流程。
首先,通过平面铣削将工件的平面面加工成需要的尺寸和形状。
然后,通过凸台铣削将工件上的凸台面加工成需要的形状。
在钻削工艺中,我们可以通过钻削工序将工件上需要的孔加工出来。
在加工孔的过程中,我们需要根据孔径和精度要求选择合适的钻具,并根据钻孔深度使用适当的进给量和转速。
最后,在切割工艺中,我们可以采用切削工序将工件上的不需要的部分切割掉。
在切割过程中,我们需要根据工件的尺寸、形状和材料,选择合适的刀具和切割速度,以及采取合适的切割方法。
在完成机械加工工艺规划后,我们需要进行一道工序的夹具设计。
夹具设计是指为了保证工件在加工过程中的安全、稳定和精度,设计合适的夹具来固定工件。
对于车床C6140A支架的夹具设计,我们可以采用三爪卡盘夹具来固定工件。
首先,我们需根据支架的形状、尺寸和加工要求,选择合适的三爪卡盘,并确定合适的夹爪位置。
然后,我们需要设计夹爪的夹持形状和夹持力。
根据支架的形状和材料,可以设计夹爪的夹持形状,以确保夹爪能够牢固地固定住支架。
同时,根据支架的尺寸和重量,可以计算夹爪需要的夹持力,以确保支架在加工过程中不会发生滑动或变形。
支架的机械加工工艺规程及铣夹具设计课程设计

机械制造课程设计(论文)题目:支架的机械加工工艺规程及铣夹具设计所在学院专业班级姓名学号指导老师年月日目录1 引言 (2)2 课程设计的目的 (2)3 支架的工艺分析 (3)3.1支架的结构及其工艺性分析 (3)3.2支架的技术要求分析 (3)4 毛坯的选择 (3)5 支架机械加工工艺路线的制定 (4)5.1定位基准的选择 (4)5.1.1 精基准的选择 (4)5.1.2 粗基准的选择 (4)5.2拟定工艺路线 (4)5.2.1 加工方法的选择和加工阶段的划分 (4)5.2.2 工艺路线的拟定 (5)5.3加工余量和工序尺寸的拟定 (6)5.3切削用量的确定 (7)6 夹具设计设计 (15)6.1确定设计方案 (16)6.2选择定位方式及定位元件 (16)6.3确定导向装置 (16)6.4定位误差的分析与计算 (16)6.5设计夹紧机构 (16)7 致谢 (16)参考文献 (17)1 引言工艺综合课程设计是机械类专业的一门主干专业基础课,内容覆盖金属切削原理和刀具、机械加工方法及设备、互换性与测量技术、机械制造工艺学及工艺装备等,因而也是一门实践性和综合性很强的课程,必须通过实践性教学环节才能使我们对该课程的基础理论有更深刻的理解,也只有通过实践才能培养我们理论联系实际的能力和独立工作能力。
因此,工艺综合课程设计应运而生,也成为机械类专业的一门重要实践课程。
2 课程设计的目的工艺综合课程设计旨在继承前期先修基础课程的基础上,让我们完成一次机械零件的机械加工工艺规程和典型夹具设计的锻炼,其目的如下。
(1)在结束了机械制造基础等前期课程的学习后,通过本次设计使我们所学到的知识得到巩固和加深。
培养我们全面综合地应用所学知识去分析和解决机械制造中的问题的能力。
(2)通过设计提高我们的自学能力,使我们熟悉机械制造中的有关手册、图表和技术资料,特别是熟悉机械加工工艺规程设计和夹具设计方面的资料,并学会结合生产实际正确使用这些资料。
支架加工工艺规程及工装夹具设计

支架加工工艺规程及工装夹具设计一、引言支架是工业生产中常用的金属制品,其用途极为广泛。
支架的加工工艺和工装夹具设计对于支架生产的质量、效率和成本非常重要。
本文将详细介绍支架的加工工艺规程及其工装夹具设计。
二、支架加工工艺规程2.1 材料准备支架的材料通常为冷轧板、热轧板或铸铁件。
在材料准备阶段,应对原材料进行质量检查,包括检查材料的化学成分、物理性质和机械性能等指标,以确保加工后的支架具有所需的性能和质量。
2.2 加工工序2.2.1 图纸分析在进行支架加工之前,需要对支架的图纸进行分析,以确定加工方案和工序顺序,并完成生产计划表。
2.2.2 板料切割板料切割是支架加工的第一道工序,其目的是按照图纸要求将材料裁剪成所需的尺寸和形状。
2.2.3 冲孔冲孔是支架加工中比较常见的工序,其目的是为了安装时方便与加强支架的稳定性。
2.2.4 折弯折弯是将板材按照图纸要求形状进行折叠,通过调整对位板,达到强度和严格的尺寸控制要求。
2.2.5 焊接支架的连接部分通常通过焊接工艺进行,根据具体的情况,可以采用手工焊接、气焊或电弧焊等焊接方式。
2.2.6 支架整形经过上述工序处理后,支架最后需要进行整形,以保证其外观和精度符合要求。
2.3 检验经过支架加工之后,需要进行质量检验,检验项目包括外观、尺寸、材料性能、连接部位的强度等方面。
三、工装夹具设计在支架加工过程中,工装夹具是非常重要的辅助工具,能够大大提高加工效率和加工质量。
以下是工装夹具设计的主要要点。
3.1 工装夹具分类常见的工装夹具类型包括夹具、模具、卡具、检测治具等。
3.2 工装夹具设计要点3.2.1 定位准确准确的定位是加工质量的基础,工装夹具的设计应当充分考虑定位问题,并采用合适的夹具或卡具来实现定位。
3.2.2 稳定可靠工装夹具的稳定性和可靠性对于加工质量和加工效率有很大的影响,设计时需要根据具体情况进行合理的优化。
3.2.3 便于调整在生产过程中,需要根据具体情况进行调整,工装夹具的设计应当考虑到这一点,并能够方便进行调整。
车床支架机械加工工艺及夹具设计
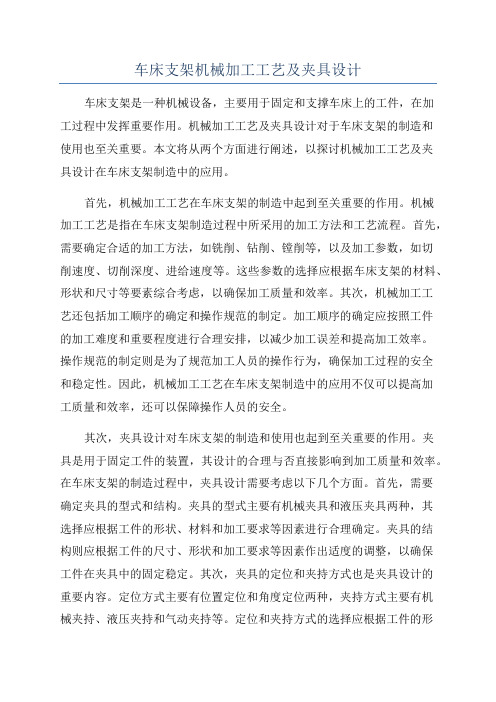
车床支架机械加工工艺及夹具设计车床支架是一种机械设备,主要用于固定和支撑车床上的工件,在加工过程中发挥重要作用。
机械加工工艺及夹具设计对于车床支架的制造和使用也至关重要。
本文将从两个方面进行阐述,以探讨机械加工工艺及夹具设计在车床支架制造中的应用。
首先,机械加工工艺在车床支架的制造中起到至关重要的作用。
机械加工工艺是指在车床支架制造过程中所采用的加工方法和工艺流程。
首先,需要确定合适的加工方法,如铣削、钻削、镗削等,以及加工参数,如切削速度、切削深度、进给速度等。
这些参数的选择应根据车床支架的材料、形状和尺寸等要素综合考虑,以确保加工质量和效率。
其次,机械加工工艺还包括加工顺序的确定和操作规范的制定。
加工顺序的确定应按照工件的加工难度和重要程度进行合理安排,以减少加工误差和提高加工效率。
操作规范的制定则是为了规范加工人员的操作行为,确保加工过程的安全和稳定性。
因此,机械加工工艺在车床支架制造中的应用不仅可以提高加工质量和效率,还可以保障操作人员的安全。
其次,夹具设计对车床支架的制造和使用也起到至关重要的作用。
夹具是用于固定工件的装置,其设计的合理与否直接影响到加工质量和效率。
在车床支架的制造过程中,夹具设计需要考虑以下几个方面。
首先,需要确定夹具的型式和结构。
夹具的型式主要有机械夹具和液压夹具两种,其选择应根据工件的形状、材料和加工要求等因素进行合理确定。
夹具的结构则应根据工件的尺寸、形状和加工要求等因素作出适度的调整,以确保工件在夹具中的固定稳定。
其次,夹具的定位和夹持方式也是夹具设计的重要内容。
定位方式主要有位置定位和角度定位两种,夹持方式主要有机械夹持、液压夹持和气动夹持等。
定位和夹持方式的选择应根据工件的形状、材料和加工要求等因素进行合理确定,以确保工件在夹具中的位置准确和固定稳定。
最后,夹具的刚性和稳定性也是夹具设计的重要指标。
夹具的刚性主要指夹具在夹持工件时的抗变形能力,而稳定性主要指夹具在加工过程中的抗振动和抗位移能力。
支架零件的机械加工工艺规程及工艺装备与夹具设计
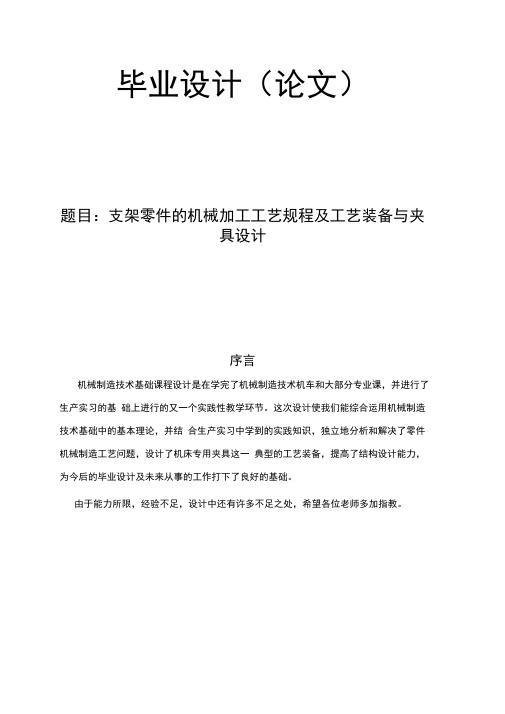
毕业设计(论文)题目:支架零件的机械加工工艺规程及工艺装备与夹具设计序言机械制造技术基础课程设计是在学完了机械制造技术机车和大部分专业课,并进行了生产实习的基础上进行的又一个实践性教学环节。
这次设计使我们能综合运用机械制造技术基础中的基本理论,并结合生产实习中学到的实践知识,独立地分析和解决了零件机械制造工艺问题,设计了机床专用夹具这一典型的工艺装备,提高了结构设计能力,为今后的毕业设计及未来从事的工作打下了良好的基础。
由于能力所限,经验不足,设计中还有许多不足之处,希望各位老师多加指教。
目录序言,,,,,,,,,,,,,,,,,,,,,,,,,, 1一、零件的工艺分析及生产类型的确定,,,,,,,,,,,,,,, 31. 零件的工艺分析,,,,,,,,,,,,,,,,,,,,,,,, 32. 零件的生产类型,,,,,,,,,,,,,,,,,,,,,,, 3二、选择毛坯,确定毛坯尺寸,设计毛坯图,,,,,,,,,,,,, 31. 选择毛坯,,,,,,,,,,,,,,,,,,,,,,,,,, 32. 确定机械加工余量,,,,,,,,,,,,,,,,,,,,,, 33. 确定毛坯尺寸,,,,,,,,,,,,,,,,,,,,,,,, 34. 设计毛坯,,,,,,,,,,,,,,,,,,,,,,,,,, 3三、选择加工方法,制定工艺路线,,,,,,,,,,,,,,,,, 41. 定位基准的选择,,,,,,,,,,,,,,,,,,,,,,,, 42. 零件表面加工方法的选择,,,,,,,,,,,,,,,,,,,, 43. 制定工艺路线,,,,,,,,,,,,,,,,,,,,,,,,, 4四、工序设计,,,,,,,,,,,,,,,,,,,,,,,,,,, 51. 选择加工设备与工艺装备,,,,,,,,,,,,,,,,,,,, 52. 确定工序尺寸(工序Ⅸ),,,,,,,,,,,,,,,,,,,, 5五、确定切削用量及基本时间(工序Ⅸ),,,,,,,,,,,,,,, 51. 切削用量的计算,,,,,,,,,,,,,,,,,,,,,,,, 52.基本时间t m的计算,,,,,,,,,,,,,,,,,,,,,,, 63. 辅助时间t f 的计算,,,,,,,,,,,,,,,,,,,,,,, 64. 其他时间的计算,,,,,,,,,,,,,,,,,,,,,,,, 6六、夹具设计,,,,,,,,,,,,,,,,,,,,,,,,,,, 71. 定位方案,,,,,,,,,,,,,,,,,,,,,,,,,,, 72. 夹紧机构,,,,,,,,,,,,,,,,,,,,,,,,,,, 73. 导向装置,,,,,,,,,,,,,,,,,,,,,,,,,,, 74. 夹具与机床连接元件,,,,,,,,,,,,,,,,,,,,,, 75. 夹具体,,,,,,,,,,,,,,,,,,,,,,,,,,,, 7七、结束语,,,,,,,,,,,,,,,,,,,,,,,,,,,, 8参考文献,,,,,,,,,,,,,,,,,,,,,,,,,,,, 9附件第一章零件的工艺分析及生产类型的确定一、零件的工艺分析通过对该零件图的重新绘制,知原图样的视图正确、完整,尺寸、公差及技术要求齐全。
支架加工实用工艺规程和工装设计

支架加工实用工艺规程和工装设计支架加工的实用工艺规程和工装设计是确保支架加工过程能够达到预期要求的关键。
在本文中,将讨论支架加工的实用工艺规程和工装设计,以提供了解和指导。
一、实用工艺规程1.材料选择和准备:选择适合支架加工的材料,通常是钢材,确保材料的质量和性能符合要求。
在加工前,对材料进行清洗和去油处理,以确保表面光洁和无污染。
2.加工工艺和参数:根据支架的设计要求,确定加工工艺和参数。
包括切削速度、进给量、切削深度等,确保加工过程稳定和切削刀具寿命。
3.加工顺序和方法:根据支架的复杂程度和零件结构,确定加工顺序和方法。
可以采用分步加工、多道次加工等方式,确保加工过程顺利和效率高。
4.加工设备和工具的选择:选择适合支架加工的设备和工具。
例如,数控机床、切削刀具等,确保加工设备和工具的精度和性能符合要求。
5.质量控制和检测:在加工过程中进行质量控制和检测,确保支架的加工质量符合要求。
可以使用各种测量仪器和设备,如千分尺、显微镜等,进行尺寸、形状和表面质量的测量和检查。
二、工装设计工装设计是指设计和制作用于支架加工过程中的夹具和工装,以提高加工质量和效率。
以下是支架加工的工装设计的一些建议。
1.夹具设计:根据支架的零件结构和加工过程的需求,设计夹具。
夹具应具备固定工件、定位工件和实现加工所需切削力的功能,确保加工过程稳定和工件精度高。
2.定位和夹持:确保工件在加工过程中的准确定位和夹持。
可以使用定位销、定位块、夹紧螺栓等方式,确保工件的位置和角度的精确性。
3.导向和限位:为了确保加工过程的稳定性和工件的精度,需要设计导向和限位元件。
导向元件用于引导切削力和减小振动,限位元件用于限制切削深度和确保加工精度。
4.切削油和冷却液的输送:支架加工过程中需要切削油和冷却液的输送。
设计相应的管道、阀门和喷嘴,确保切削油和冷却液能够有效地达到切削区域并起到相应的作用。
5.工装的稳定性和可靠性:设计的工装应具备稳定性和可靠性,以确保在加工过程中不会发生变形、松动等情况。
- 1、下载文档前请自行甄别文档内容的完整性,平台不提供额外的编辑、内容补充、找答案等附加服务。
- 2、"仅部分预览"的文档,不可在线预览部分如存在完整性等问题,可反馈申请退款(可完整预览的文档不适用该条件!)。
- 3、如文档侵犯您的权益,请联系客服反馈,我们会尽快为您处理(人工客服工作时间:9:00-18:30)。
支架的机械加工工艺规程编制和专用夹具设计作者:陈野摘要:随着机械制造业的不断发展,社会对生产率的要求也越来越高,因此,大批量生产成为时代的需求,而组合机床就可以满足这一需求,我们有必要来研究他。
另外,支架是主要起支撑作用的构架,承受较大的力,也有定位作用,使零件之间保持正确的位置。
因此支架加工质量直接影响零件加工的精度性能,我们有必要对其进行研究。
机械制造毕业设计涉及的内容比较多,它是基础课、技术基础课以及专业课的综合,是学完机械制造技术基础(含机床夹具设计)和全部专业课,并进行了实训的基础上进行的,是我们对所有课程的一次深入的综合性的总复习,也是一次理论联系实际的训练,因此,它在我们三年大学生活中占有重要的地位。
本次毕业设计使我们能综合运用机械制造的基本理论,并结合生产实践中学到的技能知识,独立地分析和解决工艺问题,初步具备设计一个中等复杂程度零件(支架)的工艺规程的能力和运用夹具设计的基本原理和方法,拟定夹具设计方案,完成夹具结构设计的能力,也是熟悉和运用有关手册、图表等技术资料及编写技术文件等基本技能的一次实践机会。
关键字:机械制造;毕业设计;零件;一、 对零件进行工艺分析并画零件图1.1 支架的作用及结构特点支架是起支撑作用的构架,承受较大的力,也具有定位作用,使零件之间保持正确的位置。
在支架高20mm 处两个R12mm 宽12mm 的凸出部位之间相隔2mm ,其中一个上有螺纹孔,另一个上有通孔,则此处构造比较复杂,且在支架高36mm 处有2mm 宽的一个缺口,这两部分刚度比较低。
中间有Ф30mm 的孔,属于套类结构,伸出部分为一平台,上有螺纹盲孔,在端部有倾斜60°的凸出部分,起定位作用,此处应力教集中,强度要好。
在平台下面有增强其硬度的肋板。
两个R12mm 凸出,2mm 宽36mm 高处缺口及R10mm 凸出部分为复杂结构,其加工存在一定的难度,要求较高,防止其损坏,需要对其进行必要的热处理。
1.2 零件的工艺分析主要加工表面Ф30mm 中心孔及两端倒角,上、下端面,M6↓12螺纹盲孔,右端部倾斜60°凸出部分中间孔Ф8mm ,左端两个凸出部分外侧面及其中间M10螺纹孔和Ф11孔。
(1)选用灰铸铁HT150,硬度150~200HB ,负荷低,磨损无关重要,变形很小,经过正火处理。
灰铸铁件的牌号和应用范围如表1-1所示。
(2)未标注圆角半径为R3mm 。
(3)加工表面不应该有毛刺、裂缝、结疤、夹渣等缺陷,并应清理清洁。
(4)所有加工表面应光洁,不可有裂缝、压痕、毛刺、气孔、凹痕以及非金属夹杂物。
(5)上下表面应与中心孔轴线保持一定的垂直度0.06mm 和平面度0.05mm ,中心孔内表面表面粗糙度Ra ≤1.6μm ,左端两个凸出部分外表面Ra ≤6.3μm ,右端部倾斜60°凸出部分中间孔内表面Ra ≤1.6μm ,为较高精度,且Φ8015.00。
(6)在加工之前进行人工时效热处理,对毛坯预备性热处理,为降低零件硬度,在精加工阶段的磨削加工前进行淬火处理,淬火后工件硬度提高且易变形。
表1-1 灰铸铁件的牌号和应用范围1.3 支架的零件图,见图纸所示。
二、选择毛坯的制造方式并绘制毛坯简图2.1 选择毛坯的制造方式该零件加工要求高,加工面数量多,并且种类繁多,有车、磨端面,钻孔、扩孔、攻螺纹、车倒角、钻斜孔等,位置、形状、尺寸精度都各有要求。
支架材料为灰铸铁HT150,硬度为150~200HB,承受中等载荷的零件,摩擦面间的压力≤490KPa,用于一般机械制造,薄壁(重量不大)零件,工作压力不大的管子配件以及壁厚≤30mm的耐磨轴套等和圆周速度为6~12m/s的带轮以及其他符合表1-1中条件的零件。
毛坯种类的确定是与零件的结构形状、尺寸大小、材料的力学性能和零件的生产类型直接相关的,另外还和毛坯的具体生产条件相关。
铸件:包括铸钢、铸铁、有色金属及合金的铸件等。
铸件毛坯的形状可以相当复杂,尺寸可以相当大,且吸振性能好,但铸件的力学性能差。
生产纲领为大批量生产,采用精度和生产率高的毛坯制造方法,如金属型铸造,可以使毛坯的形状接近于零件的形状,因此可以减少切削加工用量,从而提高材料的利用率,降低了机械加工成本。
金属型铸造就是将熔融的金属浇注到金属模具中,依靠金属自重充满金属模具型腔而获得的铸件,这种铸件比砂型铸造铸件精度高,表面质量和力学性能好,生产效率也高,但需要专用的金属型腔模,适用于大批量生产中的尺寸不大的有色金属铸件,综合上述生产此支架零件选择金属型铸造铸件的方式。
2.2 确定毛坯的形状、大小(1)毛坯的特点,如表2-1所示:(2)铸件尺寸公差,如表2-2所示:(/μm)(5)机械加工余量,工序尺寸确定由于毛坯及以后各道工序或工步的加工都有误差,因此所规定的加工余量其实只是名义上的加工余量,实际上加工余量有最大加工余量和最小加工余量之分。
铸件的机械加工余量见毛坯的制造表2-3所示,尺寸公差等级为12,加工余量等级MA为G,则可选取毛坯的加工余量有4.5mm和3.0mm两种数值,及其他分析,确定毛坯的基本尺寸,画出毛坯简图,如图2-5所示:图2-5三、制订零件的机械加工工艺路线由于零件是大批量生产,它的主要工艺特征是广泛采用专用机床、专用夹具及专用刀具、量具,机床按工艺路线排列组织流水生产。
为减轻工人的劳动强度,留有进一步提高生产率的可能,该支架在工艺设计上采用了组合机床的流水线加工方式。
3.1 确定零件各孔、平面的加工方式(1)孔的加工方式,如表3-1所示:表3-1 孔的加工方案由表3-1可以确定支架零件各孔的加工方案如下: A 、加工孔Φ30032.00+,要求内表面粗糙度Ra ≤6.3μm ,则选择钻-扩-粗铰-精铰的加工方式;B 、加工Φ11,要求内表面Ra ≤6.3μm ,选择钻-铰的加工方式;C 、加工Φ8015.00+,要求内表面Ra ≤1.6μm ,选择钻-粗铰-精铰的加工方式。
(2)平面的加工方式,如表3-2所示:由表3-2可以确定支架零件各面的加工方案如下:分析零件的各部分技术要求,四处平面加工,精度要求都在表面粗糙度Ra ≤6.3~1.6μm 之间,结合零件形状尺寸,选择粗铣-精铣的加工方式。
(3)机械加工的安排原则 1. 对于形状复杂、尺寸较大的毛坯,或尺寸偏差较大的毛坯,应首先安 排划线工序,为精基准加工提供找正基准;2. 按“先基面后其他”的顺序,首先加工精基准面;3. 在重要表面加工前应对精基准进行修正;4. 按“先主后次、先粗后精”的顺序,对精度要求较高的各主要表面进行 精加工、半精加工和精加工;5. 对于主要表面有位置精度要求的次要表面,应安排在主要表面加工之后 加工;6. 一般情况,主要表面的精加工和光整加工应放在最后阶段进行,对于 易出现废品的工序,精加工和光整加工可适当提前。
3.2 定位基准的选择工件在机床上用夹具进行夹紧加工时,用来决定工件相对于刀具的位置的工件上的这些表面称为定位基准,定位基准分为粗基准和精基准。
1、粗基准的选择粗基准的选择要重点考虑如何保证各个加工表面都能分配到合理的加工余量,保证加工面与非加工面的位置、尺寸精度,还同时要为后续工序提供可靠的精基准。
按照有关粗基准的选取原则(即当零件有非加工表面时,应以这些非加工表面作粗基准;若零件有若干个非加工表面时,则应以与加工表面要求相对位置精度较高的不加工表面作粗基准):①加工D 面时,选取Φ60外表面外圆为粗基准,利用V 型块和一紧固螺钉以Φ60外圆定位夹紧,以限制四个自由度,再以C 面为次要粗基准,限制一个自由度,共限制五个自由度,可以满足加工要求;②加工M10和Φ11以R12非加工表面外圆为粗基准;③加工Φ8015.00+以R10非加工表面外圆为粗基准。
2、精基准的选择 选择精基准时,重点考虑的是减少工件的定位误差,保证零件的加工精度和加工表面之间的位置精度,同时也要考虑零件的装夹方便、可靠、准确。
结合零件形状尺寸大小、装夹定位,取D 面为精基准,较好定位,且定位基准与设计基准重合。
3.3 制订工艺路线拟定工艺路线的出发点是使零件的几何形状、尺寸精度以及位置精度等技术要求能得到保证。
工艺路线的拟定一般需要做两个方面的工作:一是根据生产纲领确定加工工序和工艺内容,依据工序的集中和分散程度来划分工艺;二是选择工艺基准,即主要选择定位基准和检验基准。
在生产纲领已确定为批量生产的条件下,可以考虑采用万能机床,组合机床和专用夹具,并尽量采用工序集中的原则,通过减少工件安装的数量来提高生产率。
除此之外,还应尽量考虑经济精度以便使生产成本尽量下降。
根据以上原则及前文分析,拟定如下工艺路线: 工序1 铸坯(铸造)工序2 热处理(人工时效,降低硬度) 工序3 以所选基准,划C 、D 、E 面加工线 工序4 粗铣-精铣D 面 工序5 粗铣-精铣C 、E 面 工序6 钻M6↓12螺纹底孔 工序7 攻螺纹M6↓12 工序8 粗铣-精铣F 面 工序9 钻M10螺纹底孔 工序10 攻螺纹M10 工序11 粗铣-精铣G 面 工序12 钻-铰Ф11工序13 钻-扩-粗铰-精铰Φ30032.00+工序16 钻-粗铰-精铰Φ8015.00+工序17 热处理淬火,提高硬度,150~200HB 工序18 去毛刺 工序19 终检 工序20 入库分析:为了提高效率,尽量减少零件的装夹定位,如同一平面上孔加工在一次装夹就完成加工要求,使工序集中,节约时间,提高了生产率,按机械加工安排原则,合理的拟定工艺路线。
3.4 选择各工序机床及工、夹具,刀具,加工余量及工序间尺寸与公差的确定(1)工序3,工件固定在平台上,用划线尺划线找正;(2)工序4,选择X6130A 万能升降台铣床,专用夹具,采用高速钢镶齿三面刃铣刀Ф225mm ,量具卡板。
D 面有3mm 加工余量,粗铣2mm 留1mm 余量,精铣,保证平面度0.05mm ;(3)工序5,选择X6130A 万能升降台铣床,专用夹具,采用高速钢镶齿三面刃铣刀Ф225mm ,量具卡板。
C 、E 面有4.5mm 加工余量,粗铣3.5mm 留1mm 余量,精铣,相对A 基准,保证其垂直度度0.06mm ;(4)工序6,选择X6130A 万能升降台铣床,专用夹具。
①Ф5麻花钻,螺旋角β=28°,顶角2K γ=118°,后角α。
=16°,横刃斜角ψ=40~60°,钻孔深度12mm Ф5盲孔,M10螺纹底孔,量具卡尺;②攻螺纹,丝锥M6×1,螺纹量规,攻螺纹机S4012A ;(5)工序8,选择X6130A 万能升降台铣床,专用夹具,采用高速钢镶齿三面刃铣刀Ф225mm ,量具卡板。