反应等离子喷涂的发展及其应用
反应等离子喷涂的发展及其应用

反应等离子喷涂的发展及其应用摘要:反应等离子喷涂试自蔓延高温合成(SHS)同等离子喷涂技术结合而发展起来的新技术。
本文综述了反应等离子喷涂的特点,涂层的种类以及涂层应用的领域。
并提出了需要研究的问题,展示了反应等离子喷涂的应用前景。
关键词:反应等离子喷涂;涂层种类;应用领域0 前言传统等离子喷涂具有焰流温度高,能量集中,粒子飞行速度快等特点[1]。
自蔓延合成(SHS)也称燃烧合成(CS),是利用化学反应自身放热制备材料的新技术,在常规制备方法中难以得到的陶瓷、金属间化合物等高熔点、高性能的材料方面显示出巨大的优越性[2]。
将等离子喷涂和自蔓延高温合成相结合,充分发挥两种工艺的特点,逐渐发展成为反应等离子喷涂[3]。
1 反应等离子喷涂的特点反应等离子喷涂是基于一定的燃烧合成反应实现的,将等离子喷涂和燃烧合成结合,充分发挥两种工艺的各自优点,利用等离子焰流来控制燃烧合成的反应程度。
反应等离子喷涂有两种,一种是S-S反应,这种反应所用粉末一般为高放热反应体系的复合粉末,另一种是S-G反应。
在喷涂过程中,喷涂材料在飞行过程中与反应气体发生反应,最终反应产物沉积到基体上形成涂层。
利用等离子焰流作为热源,引发所喷涂粉末发生燃烧合成反应,反应放出的热量使反应产物迅速升温,从而在焰流中合成所需产物,并以极高的速度喷出,沉积到基体上形成涂层。
由于产物的合成以及涂层的形成几乎同步完成,因此,反应等离子喷涂具有很高的生产效率。
反应等离子喷涂不仅可以用于制备氮化物和硼化物陶瓷涂层,还可制备原位合成的金属/陶瓷复合涂层,能够显著改善单一陶瓷涂层韧性差的缺点,提高涂层的机械性能。
反应等离子喷涂涂层呈波浪式堆叠在一起的典型的层状组织结构,硬质相和基体相变形粒子互相交错。
合成反应热与等离子弧热叠加,有利于高熔点硬质相的熔化,克服了传统等离子喷涂金属-硬质相粉末时硬质相分布不均匀、组织粗大、熔化不完全等缺点[2]。
2 反应等离子喷涂的研究2.1 粉末反应等离子喷涂以高放热反应组元为喷涂粉末,在喷涂过程中完成相的合成和涂层沉积。
等离子喷涂技术简介及其应用前景.
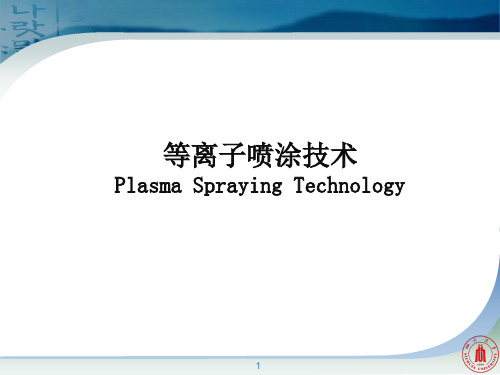
3
等离子喷涂技术介绍
热喷涂技术
热喷涂的工艺方法有很多种,根据加热源的不同可分为: 火焰喷涂、电弧喷涂、等离子喷涂( APS) 、爆炸喷涂
4
等离子喷涂技术介绍
等离子喷涂技术
等离子喷涂是利用等离子火焰来加热熔化喷涂粉末使之 形成涂层的热喷涂方法。
等离子体:自然界物质的第四态——等离子体。当气体 电离度大于0.1%时,正离子和电子数量增多且相等,其 空间电荷为零,呈中性状态,处于这种状态下的气体称 为等离子体 等离子喷涂工作气体常用Ar 或N2,再加入5% ~ 10% 的 H2,气体进入电极腔的弧状区后,被电弧加热离解形成等 离子体,其温度可达15000 ℃以上。
(2)合理选择喷涂工艺,优化工艺参数 (3)进一步研究涂层的形成机理、孔隙形成机理,寻求消除 或减少孔隙率的方法
(4)研究开发出能有效防止光辐射、高噪音、有害衍生 气体、粉尘及有害物质的新型等离子喷涂机
35
Thank You!
2014年5月22日
36
27
等离子喷涂技术应用
(1)纳米涂层
等离子喷涂技术作为一个传统的涂层制备手段用于喷涂纳 米涂层具有独特的优势。如低成本、高效率,适于工业化 生产,所得涂层硬度高、耐磨性好、与基体结合强度高。
等离子喷涂原理与应用详解 共40页
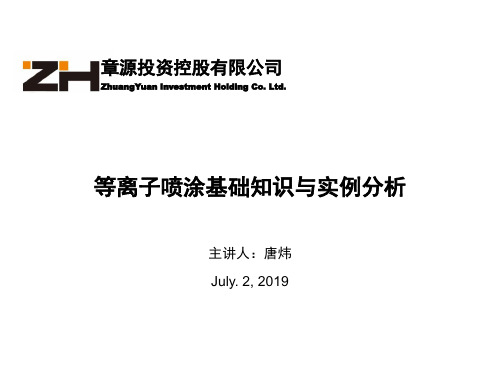
1946年朗道证明当朗缪尔波传播时,共振电子会吸收波的能量造成波衰减,这称为朗道阻 尼。朗道的这个理论,开创了等离子体中波和粒子相互作用和微观不稳定性这些新的研究 领域。
等离子喷涂的发发展史
19世纪30年代英国的M.法拉第以及其后的J.J.汤姆孙、J.S.E.汤森德等人相继研究气体放 电现象,这实际上是等离子体实验研究的起步时期。
1879年英国的W.克鲁克斯采用“物质第四态”这个名词来描述气体放电管中的电离气体。
美国的I.朗缪尔在1928年首先引入等离子体这个名词,等离子体物理学才正式问世。
2)条件不同 等离子喷涂可以直接在大气环境下 气相沉积必须在高真空下进行
等离子喷涂与其它表面改性技术的区别
3)涂层组织结构与厚度不同 等离子喷涂涂层的组织为层状堆积,涂层存在大量粒子间界面和气孔等
缺陷。 气相沉积涂层是致密的几微米厚的薄膜材料
4)性能上的不同 等离子喷涂在某种程度上提高了涂层的性能, 气相沉积大大提高了材料的性能
等离子喷涂时,喷涂后基体组织不发生变化,工件几乎不产生变形。 4)效率高
等离子喷涂时,生产效率高,采用高能等离子喷涂时,粉末的沉积速率 达8Kg/h。
等离子喷涂与其它表面改性技术的区别
1. 与火焰喷涂的区别 等粒子喷涂技术是继火焰喷涂之后大力发展起来的一种精密喷涂方法。
它具有:①超高温特性,便于进行高熔点材料的喷涂。②喷射粒子的速度高, 涂层致密,粘结强度高。③由于使用惰性气体作为工作气体,所以喷涂材料 不易氧化。
从20世纪30年代起,磁流体力学及等离子体动力论逐步形成。等离子体的速度分布函 数服从福克-普朗克方程。
等离子喷涂
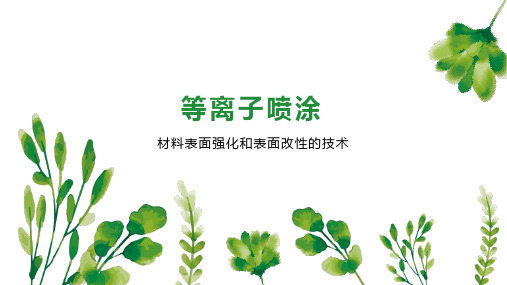
②转移弧:电弧离开喷枪转移到被加工零件上的等离子弧。这种情况喷嘴不接电源,工件接正极,电弧飞越 喷枪的阴极和阳极(工件)之间,工作气体围绕着电弧送入,然后从喷嘴喷出。
等离子切割,等离子弧焊接,等离子弧冶炼使用的是这类等离子弧。
③联合弧:非转移弧引燃转移弧并加热金属粉末,转移弧加热工件使其表面产生熔池。这种情况喷嘴,工件均 接在正极。
喷涂原理
等粒子喷涂是利用等离子弧进行的,离子弧是压缩电弧,与自由电弧相比较,其弧柱细,电流密度大,气体 电离度高,因此具有温度高,能量集中,弧稳定性好等特点。
按接电方法不同,等离子弧有三种形式:
①非转移弧:指在阴极和喷嘴之间所产生的等离子弧。这种情况正极接在喷嘴上,工件不带电,在阴极和喷 嘴的内壁之间产生电弧,工作气体通过阴极和喷嘴之间的电弧而被加热,造成全部或部分电离,然后由喷嘴喷出 形成等离子火焰(或叫等离子射流)。
特点
等离子喷涂技术是继火焰喷涂之后大力发展起来的一种新型多用途的精密喷涂方法,它具有:①超高温特性, 便于进行高熔点材料的喷涂。②喷射粒子的速度高,涂层致密,粘结强度高。③由于使用惰性气体作为工作气体, 所以喷涂材料不易氧化。
等离子的形成
(以N2为例): 0°k时,N2分子的两个原子呈哑铃形,仅在x,y,z方向上平动; 大于10°k时,开始旋转运动; 大于10000°k时,原子间产生振动,分子与分子间碰撞,则分子会发生离解变为单原子: N2+Ud——>N+N其中 Ud为离解能 温度再升高,原子会发生电离: N+Ui——>N++e其中 Ui为电离能 气体电离后,在空间不仅有原子,还有正离子和自由电子,这种状态就叫等离子体。 等离子体可分为三大类: ①高温高压等离子体,电离度100%,温度可达几亿度,用于核聚变的研究; ②低温低压等离子体,电离度不足1%,温度仅为50~250度; ③高温低压等离子体,约有1%以上的气体被电离,具有几万度的温度。
浅谈等离子喷涂

等离子喷涂技术的应用一、引言热喷涂技术是表面工程学的重要工艺方法之一,它是一种材料表面强化和表面改性的新技术,可以使基材表面具有耐磨、耐蚀、耐高温氧化、电绝缘、隔热等性能。
而等离子弧喷涂技术是热喷涂技术中应用最广的一种方法。
等离子弧喷涂射流速度高,气氛可控、火焰温度高,工艺简便,可喷涂金属、合金、陶瓷材料等。
所制备的耐磨、耐蚀、红外辐射、化学催化及多种功能涂层的应用,提高了材料整体性能和使用寿命,有效地解决了高性能材料性能价格比矛盾[1]。
因此近年来等离子弧喷涂技术进步和生产应用发展很快,现已广泛应用于核能、航空、航天、石化、机械等领域[2]。
等离子弧喷涂技术最早在航空、航天部门得到应用,迄今为止,高温等离子弧喷涂在此领域的应用仍超过其它领域。
航天、航空作为等离子弧喷涂最大最稳定的应用市场,今后将保持稳定并得到增长,在涂层技术及喷涂工艺方面也将不断得到改进和完善。
二、等离子喷涂的发展等离子喷涂(APS)是以电弧放电产生的等离子体为热源,以喷涂粉末材料为主的热喷涂方法。
等离子喷涂是热喷涂的一个重要分支,它是20世纪50年代随着现代航空航天和原子能工业技术的出现而发展起来的;当时对高熔点、高纯度、高强度的涂层提出需求,促使人们对高热源、高喷速、改善喷涂气氛等方面进行了研究,从而在50年代末,美国Plasma-dyne公司首先研制出等离子喷涂设备。
等离子喷涂技术自其问世以来,一直受到极大的关注,已成为现代工业和科学技术各个领域广泛采用的先进加工手段[3]。
由于等离子射流能够熔化几乎所有的固体材料,因此等离子喷涂技术可以形成涂层的种类及其应用极其广泛。
等离子喷涂技术的发展主要集中在喷枪功率的提高以及送进粉末方式的改良两大方面。
目前,特别是在轴向送粉方式等离子喷枪研制方面取得了巨大的进展。
20世纪80年代以前,等离子喷涂技术的发展主要体现在等离子电弧的功率的提高,即最大功率从50年代的20KW,到60年代的40KW,70年代的80KW级。
等离子体喷涂技术在航空领域的应用与发展
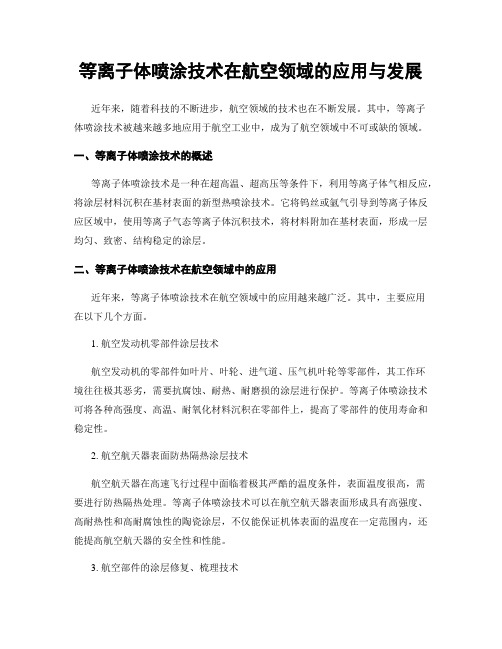
等离子体喷涂技术在航空领域的应用与发展近年来,随着科技的不断进步,航空领域的技术也在不断发展。
其中,等离子体喷涂技术被越来越多地应用于航空工业中,成为了航空领域中不可或缺的领域。
一、等离子体喷涂技术的概述等离子体喷涂技术是一种在超高温、超高压等条件下,利用等离子体气相反应,将涂层材料沉积在基材表面的新型热喷涂技术。
它将钨丝或氩气引导到等离子体反应区域中,使用等离子气态等离子体沉积技术,将材料附加在基材表面,形成一层均匀、致密、结构稳定的涂层。
二、等离子体喷涂技术在航空领域中的应用近年来,等离子体喷涂技术在航空领域中的应用越来越广泛。
其中,主要应用在以下几个方面。
1. 航空发动机零部件涂层技术航空发动机的零部件如叶片、叶轮、进气道、压气机叶轮等零部件,其工作环境往往极其恶劣,需要抗腐蚀、耐热、耐磨损的涂层进行保护。
等离子体喷涂技术可将各种高强度、高温、耐氧化材料沉积在零部件上,提高了零部件的使用寿命和稳定性。
2. 航空航天器表面防热隔热涂层技术航空航天器在高速飞行过程中面临着极其严酷的温度条件,表面温度很高,需要进行防热隔热处理。
等离子体喷涂技术可以在航空航天器表面形成具有高强度、高耐热性和高耐腐蚀性的陶瓷涂层,不仅能保证机体表面的温度在一定范围内,还能提高航空航天器的安全性和性能。
3. 航空部件的涂层修复、梳理技术随着航空工业的不断发展,有些飞机零部件在使用过程中造成损伤,如发动机涡轮叶片表面因为高温容易形成开裂、坑洼等缺陷而影响使用寿命。
等离子体喷涂技术可以通过涂层修复、梳理等技术手段来修复受损的零部件,延长使用寿命并节约维修成本。
三、等离子体喷涂技术在航空领域中的发展前景等离子体喷涂技术在航空领域中的应用前景十分广阔。
同时,也面临着技术难题、材料的选择和成本等问题。
其中,技术难题主要包括等离子体喷涂技术的喷涂质量控制和工艺精度控制的难度,以及喷涂过程中涂层厚度控制的不精确等问题。
另外,在等离子体喷涂技术中,材料的选择也是非常重要的。
热加工中的等离子喷涂技术
热加工中的等离子喷涂技术随着现代工业技术的不断发展,越来越多的先进制造技术应用于工业生产中,其中热加工技术在现代制造业中得到了广泛的应用。
在热加工过程中,等离子喷涂技术被认为是一种高效、环保、经济的材料表面改性、修复和再制造方法。
一、等离子喷涂技术介绍等离子喷涂技术是一种将被喷涂物质制成等离子体后再喷涂到被加工表面的方法。
等离子喷涂技术是通过将物质制成等离子体,然后将其通过高速气流喷涂到加工表面上,并在加工表面上形成一层高强度、耐磨、耐腐蚀的新材料。
等离子喷涂技术具有喷涂速度快、涂层硬度高、耐磨性好、防腐性强等优点,特别适用于加工表面的处理和表面的再制造。
二、等离子喷涂技术在热加工中的应用等离子喷涂技术适用于各种类型的金属、陶瓷、聚合物,也适用于复杂形状和不同大小的对像表面喷涂。
在热加工中,等离子喷涂技术的应用,大大提高了材料表面的质量和使用寿命。
以下是等离子喷涂技术在热加工中的几个应用:1.金属修复在工业加工过程中,金属材料很容易出现表面的缺陷、凸起、坑洼等问题,这时可以通过等离子喷涂技术对金属表面进行修复。
在等离子喷涂技术中,可以将喷涂材料制成等离子体,喷涂到金属表面上,形成一层高强度、耐腐蚀的涂层,在修复金属表面时,等离子喷涂技术具有成本低、操作简单等优点。
2.铝合金表面处理等离子喷涂技术在铝合金表面处理方面有着广泛的应用。
在制造飞机、汽车等汽车车身的过程中,经常需要对铝合金表面进行处理(如防锈、防腐、增加表面硬度等),这时可以采用等离子喷涂技术进行表面处理,大大提高了铝合金表面的质量和耐久性。
3.金属复合材料加工等离子喷涂技术在制作金属复合材料中也有着广泛的应用。
金属复合材料是由不同材料层状压合而成,所以在生产过程中,需要对表面进行处理,以保证复合材料之间的紧密连接。
而等离子喷涂技术可以提高复合材料之间的黏合力,保证复合材料的质量。
以上是等离子喷涂技术在热加工中的三个应用,通过以上的应用,可以看出等离子喷涂技术不仅可以提高材料表面的质量和使用寿命,还可以减少加工成本和提高生产效率。
2024年全球等离子喷涂材料市场前景分析
全球等离子喷涂材料市场前景分析引言等离子喷涂技术作为一种高效、环保、节能的涂装技术,已经在多个行业得到广泛应用。
等离子喷涂材料作为等离子喷涂技术的关键组成部分,对于等离子喷涂效果与性能起到决定性的影响。
本文将对全球等离子喷涂材料市场进行前景分析。
市场规模分析近年来,全球等离子喷涂材料市场规模呈现出快速增长的趋势。
这主要得益于等离子喷涂技术在汽车、航空航天、能源等领域的广泛应用。
据市场调研数据显示,全球等离子喷涂材料市场在过去五年中以每年10%的复合增长率增长,预计未来几年仍将保持较高增长。
市场驱动因素分析1.技术进步:随着科技的不断进步,等离子喷涂技术得到了持续改进和优化,使其在涂装效果、涂层质量和附着力等方面得到了不断提升,进一步推动了等离子喷涂技术的应用。
2.环保需求:全球环保意识的提高,对传统喷涂技术中存在的废水、废气和废涂料等环境问题日益关注,等离子喷涂技术因其低气体排放和低能耗等特点成为环保涂装的首选技术。
3.行业需求:汽车、航空航天、能源等行业对于表面保护和涂层修复的需求不断增加,推动了等离子喷涂技术及其材料的应用。
特别是航空航天行业对于涂层轻量化和抗腐蚀性能的要求,对等离子喷涂材料的市场需求提供了强劲动力。
市场挑战分析1.高成本:相较于传统喷涂技术,等离子喷涂技术的设备和材料成本较高,这对于一些中小型企业的推广和应用造成了一定的限制。
2.技术门槛:等离子喷涂技术相对于传统喷涂技术来说更为复杂,需要更高的技术门槛和操作技能。
这对于一些初创企业和技术水平较低的企业来说是一个挑战。
3.材料选择:等离子喷涂材料的选择对于喷涂效果和涂层性能至关重要,但当前市场上可供选择的等离子喷涂材料种类较少,品质也参差不齐,这限制了等离子喷涂技术的推广应用范围。
市场发展趋势展望1.创新材料的应用:未来全球等离子喷涂材料市场将出现更多创新材料的应用,例如纳米材料、复合材料等,以提升等离子喷涂技术的涂层性能和附着力。
2024年等离子喷涂系统市场前景分析
2024年等离子喷涂系统市场前景分析介绍等离子喷涂系统作为一种高效、高精度的涂装技术,正在被广泛应用于各个行业。
本文将对等离子喷涂系统市场前景进行分析,探讨其发展趋势和市场潜力。
市场规模据市场调研分析,全球等离子喷涂系统市场规模从2019年的XX亿美元增长到2025年的XX亿美元,年复合增长率为XX%。
行业应用航空航天等离子喷涂系统在航空航天行业的应用十分广泛。
它可以用于航空发动机涂装、航空器表面保护等方面。
随着航空客运需求的增加和航天科技的不断发展,等离子喷涂系统市场将持续增长。
汽车制造汽车制造业是等离子喷涂系统的主要应用领域之一。
这种技术可以应用于汽车车身涂装、发动机零部件涂装等方面。
随着汽车行业的快速发展和消费者对汽车外观质量的要求不断提高,等离子喷涂系统市场有望获得更大的增长空间。
电子设备等离子喷涂系统在电子设备制造过程中的应用也越来越重要。
它可以用于涂装电子器件外壳、电线电缆绝缘层等方面。
随着消费电子产品市场的蓬勃发展和5G技术的普及,等离子喷涂系统的市场前景十分广阔。
技术创新随着科技的进步,等离子喷涂系统的技术不断创新。
目前,一些新型的等离子喷涂系统已经开始应用于纳米材料涂装、多功能涂层等领域。
这些技术创新将进一步推动等离子喷涂系统市场的增长。
市场竞争等离子喷涂系统市场竞争激烈,存在着多家知名厂商。
主要竞争策略包括产品质量提升、服务优化、价格竞争等方面。
在市场竞争中,技术创新和研发能力是企业取得竞争优势的关键。
市场挑战尽管等离子喷涂技术有很多优势,但市场也面临一些挑战。
首先,高技术门槛和专业人才短缺对市场的发展造成了一定影响。
其次,环境保护、能源消耗等问题也需要加以解决。
只有克服这些挑战,才能更好地推动等离子喷涂系统市场的发展。
总结综上所述,等离子喷涂系统市场具有广阔的发展前景。
随着各个行业对高效、高精度涂装技术的需求增加,等离子喷涂系统将得到更广泛的应用。
技术创新和市场竞争将在市场发展中起到关键作用。
等离子在喷涂方面的应用与发展
等离子技术及应用论文学院:材料科学与工程班级:金属08-1姓名: xxx学号:0000000000000等离子技术及其在喷涂中的应用摘要:本文简要介绍了等离子技术以及等离子喷涂技术的原理、工艺、应用及其发展趋势关键词:等离子弧、喷涂、耐磨涂层对自由电弧的弧柱进行强迫“压缩”,从而使能量更加集中,弧柱中气体充分电离,这样的电弧称为等离子弧。
等离子弧又称压缩电弧。
它不同于一般的电孤,一般电弧焊所产生的电弧,因不受外界的约束,故也称它为自由电弧。
通常,提高弧柱的温度是通过增大电弧功率的方法来解决,但由于自由电弧的温度都不高,一般平均只有6000~8000oK左右。
等离子体可分为三大类:①高温高压等离子体,电离度100%,温度可达几亿度,用于核聚变的研究;②低温低压等离子体,电离度不足1%,温度仅为50~250度;③高温低压等离子体,约有1%以上的气体被电离,具有几万度的温度。
离子、自由电子、未电离的原子的动能接近于热平衡。
热喷涂所利用的正是这类等离子体。
等离子喷涂属于热喷涂技术,它是将粉末材料送入等离子体(射频放电)中或等离子射流(直流电弧)中,使粉末颗粒在其中加速、熔化或部分熔化后,在冲击力的作用下,在基底上铺展并凝固形成层片,进而通过层片叠层形成涂层的一类加工工艺。
它具有生产效率高,制备的涂层质量好,喷涂的材料范围广,成本低等优点。
因此,近几十年来,其技术进步和生产应用发展很快,己成为热喷涂技术的最重要组成部分。
表1列出了各种热喷涂方法的应用和发展情况。
等粒子喷涂原理如图1所示,等离子喷涂是以等离子弧为热源的热喷涂,指利用等离子弧将金属或非金属粉末加热到熔融或半熔融状态,并随高速气流喷射到工件表面形成覆盖层,以提高工件耐蚀、耐磨、耐热等性能的表面工程技术。
其中等离子弧是一种高能密速热源,当喷枪的钨电极(阴极)和喷嘴(阳极)分别接电源负极和正极(工件不带电)时,通过高频振荡器激发引燃电弧,使供给喷枪的工作气体在电弧的作用下电离成等离子体。
- 1、下载文档前请自行甄别文档内容的完整性,平台不提供额外的编辑、内容补充、找答案等附加服务。
- 2、"仅部分预览"的文档,不可在线预览部分如存在完整性等问题,可反馈申请退款(可完整预览的文档不适用该条件!)。
- 3、如文档侵犯您的权益,请联系客服反馈,我们会尽快为您处理(人工客服工作时间:9:00-18:30)。
反应等离子喷涂的发展及其应用摘要:反应等离子喷涂试自蔓延高温合成(SHS)同等离子喷涂技术结合而发展起来的新技术。
本文综述了反应等离子喷涂的特点,涂层的种类以及涂层应用的领域。
并提出了需要研究的问题,展示了反应等离子喷涂的应用前景。
关键词:反应等离子喷涂;涂层种类;应用领域0 前言传统等离子喷涂具有焰流温度高,能量集中,粒子飞行速度快等特点[1]。
自蔓延合成(SHS)也称燃烧合成(CS),是利用化学反应自身放热制备材料的新技术,在常规制备方法中难以得到的陶瓷、金属间化合物等高熔点、高性能的材料方面显示出巨大的优越性[2]。
将等离子喷涂和自蔓延高温合成相结合,充分发挥两种工艺的特点,逐渐发展成为反应等离子喷涂[3]。
1 反应等离子喷涂的特点反应等离子喷涂是基于一定的燃烧合成反应实现的,将等离子喷涂和燃烧合成结合,充分发挥两种工艺的各自优点,利用等离子焰流来控制燃烧合成的反应程度。
反应等离子喷涂有两种,一种是S-S反应,这种反应所用粉末一般为高放热反应体系的复合粉末,另一种是S-G反应。
在喷涂过程中,喷涂材料在飞行过程中与反应气体发生反应,最终反应产物沉积到基体上形成涂层。
利用等离子焰流作为热源,引发所喷涂粉末发生燃烧合成反应,反应放出的热量使反应产物迅速升温,从而在焰流中合成所需产物,并以极高的速度喷出,沉积到基体上形成涂层。
由于产物的合成以及涂层的形成几乎同步完成,因此,反应等离子喷涂具有很高的生产效率。
反应等离子喷涂不仅可以用于制备氮化物和硼化物陶瓷涂层,还可制备原位合成的金属/陶瓷复合涂层,能够显著改善单一陶瓷涂层韧性差的缺点,提高涂层的机械性能。
反应等离子喷涂涂层呈波浪式堆叠在一起的典型的层状组织结构,硬质相和基体相变形粒子互相交错。
合成反应热与等离子弧热叠加,有利于高熔点硬质相的熔化,克服了传统等离子喷涂金属-硬质相粉末时硬质相分布不均匀、组织粗大、熔化不完全等缺点[2]。
2 反应等离子喷涂的研究2.1 粉末反应等离子喷涂以高放热反应组元为喷涂粉末,在喷涂过程中完成相的合成和涂层沉积。
其原理如图1所示。
利用粉末反应等离子喷涂技术可制备Ti-TiC、Ti-B4C、AlSi-SiO2[4]、Fe-TiB2、Fe-TiC、Cu-TiB2等涂层。
图1 粉末反应等离子喷涂示意图2.1.1 Fe-TiC涂层TiC 颗粒增强金属复合涂层是一种具有广泛工业应用前景的金属陶瓷复合耐磨涂层,因为其具有低摩擦因数、高硬度、低密度以及良好的高温稳定性等优点。
文献[5]中作者采用71.6%(wt)太铁粉和石墨粉为原料,若按化学计量比配制的反应物完全反应,则可得83%(V ol)TiC。
喷涂粒子在飞行过程中,钛铁和石墨发生如下反应:TiFe + Ti + 2C——2TiC + Fe + 154 kJ/mol喷涂粒子在飞行过程中发生上述SHS反应后,反应物熔滴在等离子弧的作用下,高速飞向基材,发生碰撞-变形-冷凝-收缩一系列过程而形成涂层。
制备得到的TiC-Fe涂层是多层结构,即富TiC层和贫TiC层得交错堆叠,其显微硬度分别为1000-1800N/mm2和3000-6000N/mm2,性能优于传统等离子喷涂Fe+TiC 团聚粉而制得的涂层。
调整原料的成分,可获得不同TiC含量的涂层。
涂层中TiC含量、极细小的硬质相颗粒在整个涂层中的均匀分布是影响其耐磨性的最重要因素。
文献[6,7,8,9,10]中黄继华等人则采用前驱体(蔗糖)碳化复合技术利用钛铁粉为原料制备Ti–Fe–Ni–C和Ti–Fe–C系粉末,并通过反应等离子喷涂技术(RPS)原位合成并沉积了TiC/Fe–Ni和TiC/Fe金属陶瓷复合涂层。
所制备的TiC/Fe复合涂层主要由不同含量TiC颗粒分布于金属Fe基体内部而形成的复合片层叠加而成;TiC颗粒大致呈球形,粒径呈纳米级;TiC理论质量分数53%的TiC/Fe金属陶瓷涂层的耐磨粒磨损性能较好,SHV磨损实验中涂层的磨损面积为基体(45钢)的1/25左右。
文献[11]中作者采用沥青作为前躯体,太铁粉为原料制备Ti-Fe-C复合粉末,并通过反应等离子熔覆原位合成并沉积了Fe-TiC涂层,涂层结构致密,涂层具有较高的硬度和良好的耐磨损性能。
2.1.2 Fe-Al2O3涂层文献[12]中牛二武等人根据铝热反应原理制备了Fe-Al2O3-FeAl2O4复合涂层。
Dong Zha[13]等人研究了Fe/FeAl2O4涂层的微波吸收特性和复介电常数。
Cagri Tekmen等人利用直流等离子喷涂制备了TiB2/Al2O3复合涂层[14],并研究了喷涂参数及飞行颗粒的特点[15]。
2.1.3 Al-Si合金涂层AlSi合金涂层具有良好的耐磨性能,耐冲蚀性能及高温强度,常用作汽车制动器,汽缸盖,连杆等零件。
文献[16,17,18]中作者先利用机械合金化制备Al-12Si/SiO2复合粉末,然后采用APS(atmospheric plasma spraying)制备得到Al-Si/Al2O3复相涂层。
反应机理为:4Al+ 3SiO2→2Al2O3+ 3Si , ΔH=−181.09kJ/mol。
文献[19]中作者采用APS制备了Al–12Si/TiB2/h-BN复相涂层。
两者均研究了喷涂参数对涂层性能的影响。
文献[20]中作者采用不同的反应热喷涂技术制备了Al-Si-Mg涂层,并对各种涂层的性能进行了比较。
2.2 气相反应等离子喷涂反应器中的气体被引入高温等离子射流中后,迅速发生分解,并使分解的离子处于激活状态,与喷涂粉末反应生成理想的产物,沉积到基材表面形成涂层。
由于产物在原始喷涂粉末中原位生成,因此涂层中产物与基体结合良好,分布均匀。
可制备的涂层有Ti+TiC、W+WC、Mo+Mo2C、NiCr/Ti+Ti+C+CrC、FeCrAlY+CrC、FeCrAlY+CrFe+FeC等。
以甲烷、丙烯等碳氢化合物作为反应气体,NiCr/Ti团聚粉末或钨粉作为喷涂粉末,形成含TiC、CrXCy或WC、W2C 的涂层,具有良好的耐磨性;将富氮的反应气氛引入高锰、高镍不锈钢粉末喷涂过程,可制备高氮不锈钢涂层,显著改善该类不锈钢涂层的耐蚀耐磨性[21]。
2.2.1 TiN涂层TiN本身具备高硬度(理论硬度可达21GPa)、高熔点(2955℃)、耐磨、耐腐蚀、导电性等特性被广泛用于刀具、减模、半导体等领域。
目前,TiN主要用作材料表面的耐磨、耐腐蚀涂层。
传统的TiN涂层制备方法如CVD,PVD制备得到的TiN涂层较薄,涂层组织一般为粗大的柱状晶粒,韧性差;而采用反应等离子喷涂技术可以避免这些缺点。
文献[22]中陈海龙等人采用的是Ti粉与等离子腔中的氮气氛围在等离子喷涂过程中发生原位反应生成TiN涂层,涂层是由多层典型的波浪形层状组织构成,涂层组织密度,层与层之间的结合情况良好,涂层与基体结合也很紧密。
文献[23]中冯文然等人采用自行设计的一种气体隧道等离子喷枪,使用该喷枪,以钛粉和氮气为反应物,通过反应等离子喷涂(RPS)技术,制备了致密的TiN涂层。
该TiN涂层具有厚度大(>500μm)的特点,且是由纳米晶粒(直径为:50-70nm)以及非晶态的TiN相所构成的。
文献[24,25]中作者采用低压反应等离子喷涂技术制备了Ti/TiN/Ti2N复合涂层,研究了喷涂参数(Ar/N2比,喷涂距离,等离子电流大小等)对涂层性能的影响。
试验结果表明,涂层的显微硬度跟N2成线性递增关系;当Ar/N2比为1时,涂层的孔隙率最低,与基体的结合也最好,从而提高了涂层的耐腐蚀性能和耐磨性能。
文献[26,27]中的两个作者分别对反应等离子喷涂制备的TiN涂层进行热处理,以提高涂层的致密性。
E. Galvanetto认为在氧气氛围下进行热处理,涂层与氧气发生如下反应:6TiN+7O2→2Ti3O+6NO2,由于Ti3O的密度小于TiN的密度,因此造成了体积膨胀,从而对对涂层中的孔隙起到了填充的作用,使涂层的致密度大大增高,从而提高了涂层的显微硬度;而陆晨光却认为是氧化生成的TiO2填充了孔隙。
2.2.2 TiC涂层文献[28]中作者采用钛铁矿作为原材料粉末,等离子喷涂过程中与反应室中的甲烷气体反应制得Fe-TiC涂层,反应式为:FeTiO3+4CH4=Fe+3CO+TiC+8H2;制备过程中得工艺参数是影响涂层性能的重要因素。
2.2.3 TiCN涂层由于TiN薄膜存在着高温抗氧化性不强等缺点。
为进一步改善TiN薄膜的综合性能,采用多远合金化一直是刀具应用领域的研究热点。
例如,在TiN薄膜中加入非金属元素C,通过C原子的固溶和析出形成的Ti(C,N)薄膜,是TiN 基多元薄膜中现行应用较多的一种改良型薄膜。
C原子的引入可提高涂层的硬度和降低涂层与被加工材料的摩擦系数。
但Ti(C,N)涂层的抗氧化能力还不及TiN,抗氧化温度只有400℃,因此大大限制了其应用。
文献[29]中作者采用RPS制备了TiN/TiC复合涂层,反应原料是Ti粉,反应气体是CH4、N2。
并对制得的涂层进行了性能测试,显微硬度,耐磨性能及耐腐蚀性能,结果表明RPS制备的涂层性能明显高于电沉积制备得到的涂层性能。
文献[30]中作者采用RPS制备了TiCN涂层,使用的反应气体为N2和乙炔。
2.3 其它反应等离子喷涂涂层文献[31]中M. Vijay等人采用TiH2粉末作为原材料,通过反应等离子喷涂过程中粉末被氧化从而制备纳米TiO2涂层,该涂层在可见光下具有优良的光催化性能。
Yaran Niu[32]等人采用等离子喷涂技术制备了SiC涂层。
Venkata Pasumarthi[33]等人采用反应等离子喷涂技术制备了Ti3SiC2涂层。
3 反应等离子喷涂的发展前景虽然反应等离子喷涂技术和理论研究取得了一些进展,但许多关键问题仍需深入研究。
在理论上,研究等离子喷涂条件下的SHS反应及陶瓷熔体形成的热力学条件和动力学过程;揭示非平衡条件下的陶瓷涂层的SHS原位合成规律;分析陶瓷涂层或金属间化合物涂层与基材间熔合连接过程及界面结合机制;探索涂层凝固规律,特别是对具有自增韧和复相增韧作用涂层的研究,为SHS反应喷涂这一新的陶瓷涂层技术的深入研究奠定理论基础。
在工艺上,优化反应配系,摸索可获得更高耐磨、耐蚀、耐高温性能的涂层体系;系统研究工艺参数对反应等离子喷涂的影响规律;设计、改进适宜反应等离子喷涂的喷涂装置以及相应的分析测试设备,特别是高温、高速条件下对粒子的观察与测量,为反应等离子喷涂技术的工程应用奠定技术基础。
参考文献:[1] 李行志,胡树兵.等离子喷涂的发展及其应用[J].湖北汽车工业学院学报,2004,18(2):35-38.[2] 闫华,王爱华, 熊钊颋,等.自蔓延反应喷涂技术最新研究及进展[J].材料导报,2009,23(7):91-04.[3] 解永杰,阎殿然,何继宁,等.反应等离子喷涂陶瓷涂层的研究[J].新技术新工艺,2005,1:48-50.[4] O. Culha, C. Tekmen, M. Toparli, et al. Mechanical properties of in situ Al2O3 formed Al-Si composite coating via atmospheric plasma spraying [J]. Materials and Design, 2010, 31:533-544.[5] Cliché G, Dallaire S. Synthesis and deposition of TiC-Fe coatings by plasma spraying[J]. Surf Coat Technol, 1991, 46: 199-206.[6] 徐俊龙, 黄继华, 魏世忠等. TiC/Fe-Ni金属陶瓷复合涂层反应等离子喷涂研究[J].稀有金属材料与工程, 2007, 36(3): 687-691.[7] 朱警雷, 黄继华, 王海涛等. 反应等离子喷涂TiC/Fe-Ni 金属陶瓷复合涂层的显微组织[J].中国有色金属学报,2008,,18(1):36-41.[8] 张强,王海涛,黄继华等. 反应等离子喷涂TiC陶瓷增强金属复合涂层组织性能[J]. 中国表面工程, 2008, 21(6):32-36.[9] 张守全, 朱警雷, 黄继华等. 反应等离子喷涂TiC/Fe涂层的摩擦磨损性能研究[J]. 材料工程,2009,7:62-66.[10] 王海涛, 黄继华, 朱警雷等. 反应等离子喷涂TiC/Fe-Ni复合涂层及其耐冲蚀性能[J]. 复合材料导报, 2009, 26(1):74-79.[11] Junbo Liu. TiC/Fe cermet coating by plasma cladding using asphalt as a carbonaceous precursor [J]. Progress in Natural Science, 2008, 18: 447-454.[12] 牛二武, 阎殿然, 何继宁等. 反应等离子喷涂Fe-Al2O3-FeAl2O4复合涂层的反应机理研究[J].材料保护, 2005, 38(6): 21-23.[13] Dong Zhao, Fa Luo, Wancheng Zhou, et al. Microwave absorption properties and complex permittivity of Fe/FeAl2O4 coatings deposited by reactive plasma spraying Al/Fe2O3 powders [J]. Surface and Coatings Technology, 2011.[14] Cagri Tekmen, Yoshiki Tsunekawa, Masahiro Okumiya. In-situ TiB2 and Al2O3 formation by DC plasma spraying [J]. Surface and Coatings Technology, 2008, 202: 4170-4175.[15] Cagri Tekmen, Yoshiki Tsunekawa, Masahiro Okumiya. In-situ TiB2–Al2O3formed composite coatings by atmospheric plasma spraying: In fl uence of process parameters and in-fl ight particle characteristics [J]. Surface and Coatings Technology, 2009, 203: 1649-1655. [16] Cagri Tekmen, Masashi Yamazaki, Yoshiki Tsunekawa, et al. In-situ plasma spraying: Alumina formation and in-flight particle diagnostic [J]. Surface and Coatings Technology, 2008,202:4163-4169.[17] Cagri Tekmen, Yoshiki Tsunekawa, Masahiro Okumiya. Effect of plasma spray parameters on in-fl ight particle characteristics and in-situ alumina formation [J]. Surface and Coatings Technology, 2008, 203:223-228.[18] O. Culha, C. Tekmen, M. Toparli, et al. Mechanical properties of in situ Al2O3 formed Al–Si composite coating via atmospheric plasma spraying [J]. Materials and Design, 2010,31:533-544.[19] Cagri Tekmen, Ismail Ozdemir, Gudrun Fritsche, et al. Structural evolution of mechanically alloyed Al–12Si/TiB2/h-BN composite powder coating by atmospheric plasma spraying [J]. Surface and Coatings Technology, 2009, 203:2046-2051.[20] I. Ozdemir, I. Hamanaka, M. Hirose, et al. In situ formation of Al-Si-Mg based composite coating by different reactive thermal spray processes [J]. Surface and Coatings Technology, 2005,200:1155-1161.[21] 林鸿飞..基于混合模式的文本过滤模型[J].计算机研究和发展,2001,9.[22] 陈海龙,杨晖. 反应等离子喷涂TiN的反应过程及涂层形成机理研究[J].材料热处理技术,2009,38(20):104-106.[23] 冯文然,阎殿然,何继宁. 反应等离子喷涂纳米TiN涂层的显微硬度及微观结构研究[J].物理学报,2005,54(05):2399-2404.[24] T. Bacci, L. Bertamini, F. Ferrari, et al. Reactive plasma spraying of titanium in nitrogen containing plasma gas [J]. Materials Science and Engineering A, 2000,283: 189-195.[25] E. Galvanetto, F.P. Galliano, F. Borgioli, et al. XRD and XPS study on reactive plasma sprayed titanium-titanium nitride coatings [J]. Thin solid Films, 2001,384: 223-229.[26] E. Galvanetto, F. Borgioli,F.P. Galliano, et al. Improvement of wear and corrosion resistance of RPS Ti–TiN coatings by means of thermal oxidation[J]. Surface and coatings technology, 2006:3650-3655.[27] 陆晨光,阎殿然,董艳春,等. 反应等离子喷涂TiN涂层热处理后力学性能研究[J]. 稀有金属材料与工程,2009,38:129-132.[28] P.V. Ananthapadmanabhan,Patrick R. Taylor. Titanium carbide–iron composite coatings by reactive plasma spraying of ilmenite [J]. Alloys and Compounds, 1999, 287:121-125.[29] E. Lugscheider, II. Jungklaus, L. Zhao, et al. Reactive Plasma Spraying of Coatings Containing in situ Synthesized Titanium Hard phases [J]. Refractory Metals & Hard Materials, 1997,15: 311-315.[30] 朱琳, 何继宁, 阎殿然, 等. 利用反应等离子喷涂制备TiCN涂层的研究[J]. 材料导报, 2006, 20:468-470.[31] M. Vijay, V. Selvarajan, K.P. Sreekumar, et al. Characterization and visible lightphotocatalytic properties of nanocrystalline TiO2synthesized byreactiveplasmaprocessing [J]. Solar Energy Materials and Solar Cells, 2009, 93:1540-1549.[32] Yaran Niu, Xuebin Zheng, Chuanxian Ding, et al. Microstructure characteristics of silicon carbide coatings fabricated on C/C composites by plasma spraying technology [J]. Ceramics International, 2011.[33] Venkata Pasumarthi, Yao Chen, Srinivasa R. Bakshi, et al. Reaction synthesis of Ti3SiC2 phase in plasma sprayed coating [J].Journal of Alloys and Compounds, 2009,484:113-117.。