6万吨合成氨造气工段工艺设计——毕业设计
年产6万吨合成氨工艺设计毕业设计论文 精品
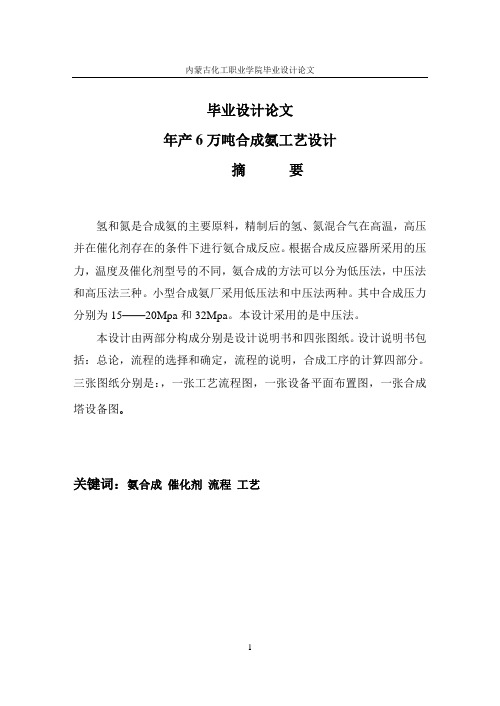
毕业设计论文年产6万吨合成氨工艺设计摘要氢和氮是合成氨的主要原料,精制后的氢、氮混合气在高温,高压并在催化剂存在的条件下进行氨合成反应。
根据合成反应器所采用的压力,温度及催化剂型号的不同,氨合成的方法可以分为低压法,中压法和高压法三种。
小型合成氨厂采用低压法和中压法两种。
其中合成压力分别为15——20Mpa和32Mpa。
本设计采用的是中压法。
本设计由两部分构成分别是设计说明书和四张图纸。
设计说明书包括:总论,流程的选择和确定,流程的说明,合成工序的计算四部分。
三张图纸分别是:,一张工艺流程图,一张设备平面布置图,一张合成塔设备图。
关键词:氨合成催化剂流程工艺目录前言--------------------------------------------------------------------------------------Ⅰ第1章总论-------------------------------------------------------------------------21.1设计依据与指导思想----------------------------------------------------31.1.1设计依据-----------------------------------------------------------31.1.2 指导思想----------------------------------------------------------31.2设计范围与技术要求----------------------------------------------------41.2.1设计范围-----------------------------------------------------------41.2.2生产规模-----------------------------------------------------------41.2.3原料动力消耗定额和消耗量--------------------------------41.3原理说明---------------------------------------------------------------------41.3.1生产原理说明----------------------------------------------------41.3.2氨合成的机理----------------------------------------------------5第2章工艺流程的选择确定----------------------------------------------52.1由氨合成的主要特点进行工艺流程的设计选择---------------62.2催化剂的选用---------------------------------------------------------------6第3章化工工艺设计说明--------------------------------------------------73.1生产工艺流程的说明----------------------------------------------------73.2生产设备选型说明--------------------------------------------------------83.2.1技术经济指标----------------------------------------------------83.2.2设备结构的要求-------------------------------------------------83.2.3设备布置与三废治理说明-----------------------------------8第4章合成工序的工艺计算--------------------------------------------94.1物料计算--------------------------------------------------------------------94.1.1计算依据----------------------------------------------------------94.1.2物料计算--------------------------------------------------------114.2能量衡算-------------------------------------------------------------------174.2.1水冷器能量衡算-----------------------------------------------174.2.2氨分离器能量计算-------------------------------------------174.2.3循环机出口能量计算----------------------------------------184.2.4油过滤器能量衡算-------------------------------------------194.2.5冷凝塔热量计算-----------------------------------------------194.2.6氨蒸发器热量计算-------------------------------------------204.2.7废热回收器能量计算----------------------------------------234.3设备计算和选用---------------------------------------------------------234.3.1废热回收器工艺计算----------------------------------------234.3.2水冷器的工艺计算-------------------------------------------294.3.3冷凝塔的工艺计算-------------------------------------------334.3.4氨蒸发器工艺计算--------------------------------------------38参考文献------------------------------------------------------------------------------42结束语----------------------------------------------------------------------------------43前言合成氨工业是基础化学工业之一,其产量居各种化工产品的首位。
年产五万吨合成氨合成工段工艺设计

合成氨是一种重要的化工原料,在农业、化肥、医药等领域具有广泛的应用。
年产五万吨合成氨合成工段的工艺设计需要确保生产效率、降低成本以及保护环境。
下面将介绍一种可能的工艺设计方案,并详细阐述其主要步骤和操作过程。
工艺设计方案:1.原料准备:气体原料包括天然气、汽油等,液体原料包括氨水和硫酸。
将气体原料经过净化处理后,与液体原料进行混合。
2. 混合反应器:将混合后的原料进入混合反应器中,进行催化合成反应。
合成反应通常使用铁催化剂,反应温度为400-500°C,压力为150-300 atm。
3.分离系统:将反应后的混合气体通过冷却器进行冷却,使其达到饱和水蒸气状态。
然后进入分离塔,其中含有若干个塔盘。
通过升温和降压,氨气和氮气分别从塔顶和塔底分离出来。
氨气经过冷凝器冷却,得到液氨产品。
4.副产物处理:除了氨气外,还产生了一些副产物,如甲烷、一氧化碳等。
这些副产物需要进行处理,如通过燃烧转化为二氧化碳和水蒸气。
5.产品处理:将液氨产品进行浓缩、脱水等处理,使其达到合适的纯度要求。
然后进行分装、储存和运输等环节。
在整个合成氨合成工段中,合成反应器是最关键的部分。
其选用合适的催化剂和反应条件,可以保证高效率、高选择性的合成氨反应。
此外,适当的分离系统和副产物处理方式,能够最大程度地回收和利用原料,减少能源消耗和环境污染。
整个工艺设计需要考虑到安全性、经济性和环境性能。
安全性方面,需要对原料进行严格的净化处理,防止催化剂中毒等问题的发生。
经济性方面,需要优化工艺参数,提高产量和纯度,降低生产成本。
环境性能方面,需要优化副产物处理方式,减少废气和废水的排放。
综上所述,年产五万吨合成氨合成工段的工艺设计需要综合考虑多个因素,包括催化剂的选择、反应条件的控制、分离系统的设计、副产物处理方式等。
只有通过优化这些环节,才能够实现高效、稳定、安全和环保的合成氨生产。
万吨年合成氨合成工段工艺设计毕业设计

万吨年合成氨合成工段工艺设计毕业设计四川理工学院毕业设计 9万吨/年合成氨合成工段工艺设计四川理工学院材料与化学工程学院摘要氨是最为重要的基础化工产品之一,其产量居各种化工产品的首位。
氨主要用于农业,合成氨是氮肥工业的基础。
氨的合成主要有脱硫、转化、净化、合成几个工段。
合成氨合成工段的设计,原料采用氮气和氢气,以合成塔为主要设备,在氨冷器、水冷器、气—气交换器、循环机、分离器、冷凝塔等辅助设备的作用下制得液氨,工艺条件为:A201为催化剂,480℃,31Mpa。
本设计进行了物料衡算,热量衡算,设备选型计算。
关键词:合成工艺参数衡算设备计算-Ⅰ-ABSTRAmmonia is one of the most important basic chemical products in the world,Its output of various kinds of chemicals rank first in the world. Ammonia mainly used in agriculture and synthetic ammonia is the basis of nitrogen fertilizer industry. Ammonia synthesis is mainly from the four sections of desulphurization, conversion, decontamination, and synthesis. With using nitrogen and hydrogen as materials and synthesis converter as main equipment, under the action of the auxiliary equipments of ammonia air conditioning, water-cooling device, gas to gas exchanger, circulator, separator, and condenser and so on, in the end, the design of the ammonia synthesis section makes ammoniacalliquor, The process conditions are determined as following:A201 as catalyst, 480℃,31Mpa .The design is be designed to material balance, heat balance and calculation of Devices type.KEY WORDS:synthesis process parameter balance calculation of Devices-Ⅱ-目录第一部分绪论 (1)1.1氨的性质及其在化工生产中的地位 (1)1.2合成氨的发展历程 (1)1.3技术规格 (2)1.3.1原材料技术规格 (2)1.3.2产品技术规格 (2)1.3.3危险性物料主要物性表 (3)1.4合成原理 (3)1.5工艺条件 (4)1.6工艺流程 (4)1.6.1工艺流程图 (4)1.6.2流程简述 (5)1.6.3工艺特点 (5)第二部分工艺设计计算 (7)2.1计算依据 (7)2.2物料衡算 (7)2.2.1合成塔进入塔气气量计算 (7)2.2.2氨分离器气液平衡计算 (8)2.2.3冷交换器气液平衡计算 (10)2.2.4液氨储槽气液平衡计算 (11)2.2.5液氨贮槽物料计算 (13)2.2.6合成系统物料计算 (14)2.2.7合成塔内物料计算 (16)2.2.8水冷器物料计算 (16)2.2.9氨分离器物料计算 (17)2.2.10冷交换器物料计算 (17)2.2.11氨冷器物料计算 (18)2.2.12冷分离器物料计算 (20)2.2.13液氨储槽物料计算 (21)2.2.14物料衡算结果汇总 (23)2.3热量衡算 (26)2.3.1冷交换器热量计算 (26)2.3.2氨冷器热量计算 (28)2.3.3循环机热量计算 (30)2.3.4合成塔热量计算 (31)2.3.5废热锅炉热量计算 (33)2.3.6热交换器热量计算 (34)2.3.7水冷器热量计算 (35)2.3.8氨分离器热量计算 (36)- Ⅲ -2.3.9中置锅炉产生蒸汽量的计算. 372.3.10合成系统温度计算示意图.. 38 第三部分设备设计及选型校核 (39)3.1 主要设备选型计算 (39)3.1.1 废热锅炉设备工艺计算 (39)3.2.1冷交换器设备工艺设计及校核424.1 主要设备选型汇总表 (55)设计综述 (56)参考文献 (57)- Ⅳ -第一部分绪论1.1氨的性质及其在化工生产中的地位合成氨的化学名称为氨,氮含量为82.3%。
合成氨毕业设计doc
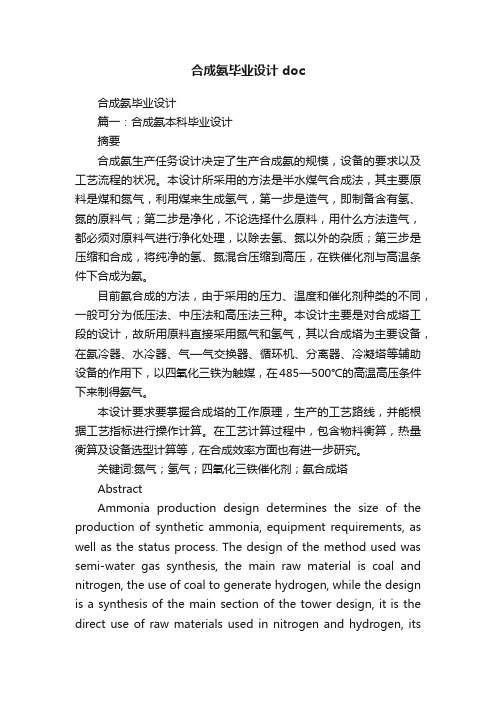
合成氨毕业设计doc合成氨毕业设计篇一:合成氨本科毕业设计摘要合成氨生产任务设计决定了生产合成氨的规模,设备的要求以及工艺流程的状况。
本设计所采用的方法是半水煤气合成法,其主要原料是煤和氮气,利用煤来生成氢气,第一步是造气,即制备含有氢、氮的原料气;第二步是净化,不论选择什么原料,用什么方法造气,都必须对原料气进行净化处理,以除去氢、氮以外的杂质;第三步是压缩和合成,将纯净的氢、氮混合压缩到高压,在铁催化剂与高温条件下合成为氨。
目前氨合成的方法,由于采用的压力、温度和催化剂种类的不同,一般可分为低压法、中压法和高压法三种。
本设计主要是对合成塔工段的设计,故所用原料直接采用氮气和氢气,其以合成塔为主要设备,在氨冷器、水冷器、气—气交换器、循环机、分离器、冷凝塔等辅助设备的作用下,以四氧化三铁为触媒,在485—500℃的高温高压条件下来制得氨气。
本设计要求要掌握合成塔的工作原理,生产的工艺路线,并能根据工艺指标进行操作计算。
在工艺计算过程中,包含物料衡算,热量衡算及设备选型计算等,在合成效率方面也有进一步研究。
关键词:氮气;氢气;四氧化三铁催化剂;氨合成塔AbstractAmmonia production design determines the size of the production of synthetic ammonia, equipment requirements, as well as the status process. The design of the method used was semi-water gas synthesis, the main raw material is coal and nitrogen, the use of coal to generate hydrogen, while the design is a synthesis of the main section of the tower design, it is the direct use of raw materials used in nitrogen and hydrogen, itssynthesis tower as the main equipment, in the ammonia cooler, water coolers, gas - gas exchange, recycling machines, separators, auxiliary equipment, such as condensation of the tower under the four iron oxide catalyst, in the high-temperature conditions of 485-500 ℃ obtained from ammonia. The first step is to build gas,Preparation that contains hydrogen, nitrogen gas; second step is purification, regardless of what materials, what methods of gas must be carried out on the feed gas purification to remove hydrogen and。
合成氨造气工段工艺设计
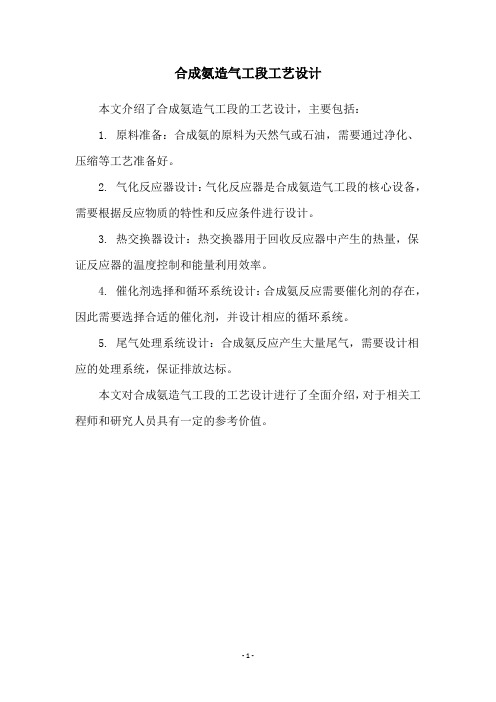
合成氨造气工段工艺设计
本文介绍了合成氨造气工段的工艺设计,主要包括:
1. 原料准备:合成氨的原料为天然气或石油,需要通过净化、压缩等工艺准备好。
2. 气化反应器设计:气化反应器是合成氨造气工段的核心设备,需要根据反应物质的特性和反应条件进行设计。
3. 热交换器设计:热交换器用于回收反应器中产生的热量,保证反应器的温度控制和能量利用效率。
4. 催化剂选择和循环系统设计:合成氨反应需要催化剂的存在,因此需要选择合适的催化剂,并设计相应的循环系统。
5. 尾气处理系统设计:合成氨反应产生大量尾气,需要设计相应的处理系统,保证排放达标。
本文对合成氨造气工段的工艺设计进行了全面介绍,对于相关工程师和研究人员具有一定的参考价值。
- 1 -。
6万吨合成氨造气工段工艺设计-推荐下载

对全部高中资料试卷电气设备,在安装过程中以及安装结束后进行高中资料试卷调整试验;通电检查所有设备高中资料电试力卷保相护互装作置用调与试相技互术通关,1系电过,力管根保线据护敷生高设产中技工资术0艺料不高试仅中卷可资配以料置解试技决卷术吊要是顶求指层,机配对组置电在不气进规设行范备继高进电中行保资空护料载高试与中卷带资问负料题荷试22下卷,高总而中体且资配可料置保试时障卷,各调需类控要管试在路验最习;大题对限到设度位备内。进来在行确管调保路整机敷使组设其高过在中程正资1常料中工试,况卷要下安加与全强过,看2度并22工且22作尽22下可22都能2可地护1以缩关正小于常故管工障路作高高;中中对资资于料料继试试电卷卷保破连护坏接进范管行围口整,处核或理对者高定对中值某资,些料审异试核常卷与高弯校中扁对资度图料固纸试定,卷盒编工位写况置复进.杂行保设自护备动层与处防装理腐置,跨高尤接中其地资要线料避弯试免曲卷错半调误径试高标方中高案资等,料,编5试要写、卷求重电保技要气护术设设装交备备4置底高调、动。中试电作管资高气,线料中课并3敷试资件且、设卷料中拒管技试试调绝路术验卷试动敷中方技作设包案术,技含以来术线及避槽系免、统不管启必架动要等方高多案中项;资方对料式整试,套卷为启突解动然决过停高程机中中。语高因文中此电资,气料电课试力件卷高中电中管气资壁设料薄备试、进卷接行保口调护不试装严工置等作调问并试题且技,进术合行,理过要利关求用运电管行力线高保敷中护设资装技料置术试做。卷到线技准缆术确敷指灵设导活原。。则对对:于于在调差分试动线过保盒程护处中装,高置当中高不资中同料资电试料压卷试回技卷路术调交问试叉题技时,术,作是应为指采调发用试电金人机属员一隔,变板需压进要器行在组隔事在开前发处掌生理握内;图部同纸故一资障线料时槽、,内设需,备要强制进电造行回厂外路家部须出电同具源时高高切中中断资资习料料题试试电卷卷源试切,验除线报从缆告而敷与采设相用完关高毕技中,术资要资料进料试行,卷检并主查且要和了保检解护测现装处场置理设。备高中资料试卷布置情况与有关高中资料试卷电气系统接线等情况,然后根据规范与规程规定,制定设备调试高中资料试卷方案。
合成氨专科毕业设计
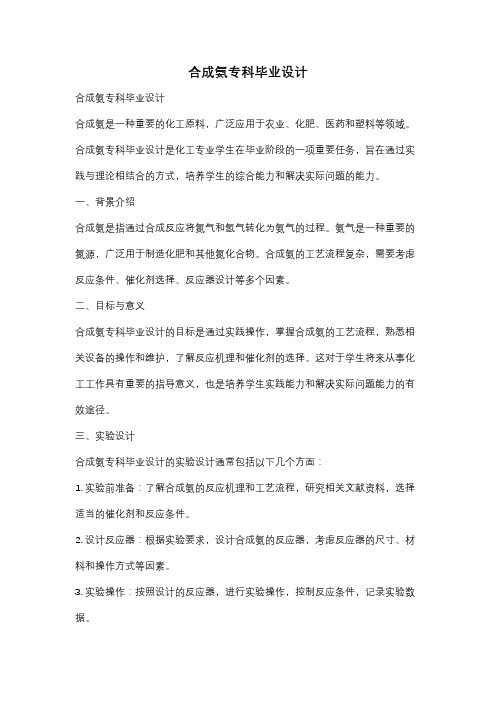
合成氨专科毕业设计合成氨专科毕业设计合成氨是一种重要的化工原料,广泛应用于农业、化肥、医药和塑料等领域。
合成氨专科毕业设计是化工专业学生在毕业阶段的一项重要任务,旨在通过实践与理论相结合的方式,培养学生的综合能力和解决实际问题的能力。
一、背景介绍合成氨是指通过合成反应将氮气和氢气转化为氨气的过程。
氨气是一种重要的氮源,广泛用于制造化肥和其他氮化合物。
合成氨的工艺流程复杂,需要考虑反应条件、催化剂选择、反应器设计等多个因素。
二、目标与意义合成氨专科毕业设计的目标是通过实践操作,掌握合成氨的工艺流程,熟悉相关设备的操作和维护,了解反应机理和催化剂的选择。
这对于学生将来从事化工工作具有重要的指导意义,也是培养学生实践能力和解决实际问题能力的有效途径。
三、实验设计合成氨专科毕业设计的实验设计通常包括以下几个方面:1. 实验前准备:了解合成氨的反应机理和工艺流程,研究相关文献资料,选择适当的催化剂和反应条件。
2. 设计反应器:根据实验要求,设计合成氨的反应器,考虑反应器的尺寸、材料和操作方式等因素。
3. 实验操作:按照设计的反应器,进行实验操作,控制反应条件,记录实验数据。
4. 数据分析:对实验数据进行分析,计算反应的转化率、选择性和收率等指标,评估合成氨的工艺流程。
5. 结果讨论:根据实验结果,讨论合成氨的工艺流程的优化方向和改进措施。
四、实验结果与讨论根据实验数据分析,我们可以评估合成氨的工艺流程的效果和可行性。
通过对不同催化剂的比较,可以选择出最佳的催化剂,提高合成氨的产率和选择性。
同时,通过对反应条件的调整,可以优化反应的速率和效果。
在实验结果的讨论中,我们还可以探讨合成氨的工艺流程中可能存在的问题和挑战。
例如,催化剂的寿命、反应器的设计和操作方式等都可能对合成氨的产率和质量产生影响。
通过分析这些问题,我们可以提出改进措施和优化方向,为合成氨工艺的进一步研究提供参考。
五、总结与展望合成氨专科毕业设计是化工专业学生在毕业阶段的一项重要任务。
6万吨合成氨变换工段工艺设计

6万吨合成氨变换工段工艺设计合成氨变换工段是合成氨生产过程中的关键环节,它将通过合成产生的氨气进行变换,使其转化为氮气和水。
本文将对6万吨合成氨变换工段的工艺设计进行详细介绍。
1.工艺原理合成氨变换工段采用的是低温变换法,主要基于以下反应:2NH3⇌N2+3H2该反应是一个平衡反应,具有可逆性。
为了提高反应速率和收率,需满足一定的条件,包括适宜的温度、压力和催化剂。
2.工艺流程合成氨变换工段的工艺流程一般包括进料、加热、反应、冷却和分离等步骤。
(1)进料:合成氨气从合成回收装置进入变换工段。
(2)加热:合成氨气在加热炉中加热至适宜的反应温度。
常用的加热方式包括电阻加热和燃气加热。
(3)反应:加热后的氨气进入变换器中进行反应。
变换器一般采用多层催化剂填料,以提高反应效率。
反应温度和压力需根据反应动力学和平衡原理进行优化选择。
(4)冷却:反应后的气体在冷却器中冷却,以控制温度,防止反应逆向进行。
(5)分离:冷却后的气体经过分离装置进行分离,将氮气、水和未反应的氨气分离开。
一般采用冷凝器和吸附器等装置进行分离。
3.工艺参数合成氨变换工段的工艺参数包括反应温度、压力、催化剂选择和反应时间等。
(1)反应温度:反应温度对合成氨的变换速率和收率有着重要影响。
通常选择适宜的反应温度,一般在300-500℃之间。
(2)反应压力:反应压力也是一个重要的工艺参数,它会影响变换速率和收率。
一般选择适宜的反应压力,大致在15-35MPa之间。
(3)催化剂选择:催化剂选择直接关系到反应效果。
常用的催化剂有铁、镍、钼等。
催化剂要具有高效催化性能和较好的稳定性。
(4)反应时间:反应时间需要根据生产规模和设备容量进行确定。
一般情况下,生产规模越大,反应时间越长。
4.工艺优化为了提高工艺效果和经济性,还可以采取以下优化措施。
(1)催化剂再生:催化剂在反应过程中会发生失活,需要定期进行再生。
通过再生可以延长催化剂寿命,减少生产成本。
- 1、下载文档前请自行甄别文档内容的完整性,平台不提供额外的编辑、内容补充、找答案等附加服务。
- 2、"仅部分预览"的文档,不可在线预览部分如存在完整性等问题,可反馈申请退款(可完整预览的文档不适用该条件!)。
- 3、如文档侵犯您的权益,请联系客服反馈,我们会尽快为您处理(人工客服工作时间:9:00-18:30)。
6万吨合成氨造气工段工艺设计——毕业设计6万吨合成氨造气工段工艺设计摘要摘要:本设计6万吨/年合成氨造气工段工艺设计采用块煤送入造气炉制气,该工艺技术成熟,结合湖北宜化丰富的生产和管理经验,在同行业中具有热量回收充分、消耗低、低成本等优势。
根据已知参数,利用所学知识对合成氨的工艺流程进行设计,工艺计算,并对设备进行了选型。
关键词:造气炉;已知参数;工艺衡算;设备计算目录摘要 (2)1.前言 (4)2.物料及热量衡算 (7)2.1.被损耗燃料各组分量的计算 (9)2.2.炉渣生成量的计算 (9)2.3.计算带出物及炉渣中各组分的总重量 102.4.燃烧气化后进入煤气中各元素的量 (11)3.空气吹分阶段的计算 (12)3.1.物料衡算 (12)3.2.热量衡算 (13)4.蒸汽吹送阶段的计算 (16)4.1.物料衡算 (16)4.2热平衡计算 (19)5总过程计算 (23)5.1燃料使用分配 (23)5.2吹风气产量 (23)5.3物料平衡 (23)5.4 热量平衡 (26)5.5 配气计算 (27)5.6 消耗定额(以吨氨为基准) (28)6主要设备工艺计算 (31)6.1空气鼓风机的计算 (31)6.2煤气发生炉的计算 (33)6.3废热锅炉的计算 (34)6.4洗气塔 (37)7结论 (42)参考文献 (43)致谢 (44)1.前言氨是一种重要的化工产品,主要用于化学肥料的生产。
合成氨生产经过多年的发展,现已发展成为一种成熟的化工生产工艺。
本次设计采用间歇式固体煤气发生炉造气,余热回收,具有环保、节能的优势。
现对造气工段主要工艺做一下简介。
1.固定层煤气发生炉制造的煤气根据气化剂不同, 工业煤气一般分以下四种:空气煤气: 以空气为气化剂制取的煤气,合成氨生产中也称吹风气.水煤气: 以水蒸汽为气化剂制取的煤气.混合煤气: 以空气和适量的水蒸汽为气化剂制取的煤气.半水煤气: 组成符合(氢气+氧化碳)与氮气体积比为3.1---3.2的混合煤气,即合成氨原料气2.煤气发生炉自上而下分为干燥层,干馏层,还原层,氧化层,灰渣层.干燥层: 一般不产生气化反应,此区内的燃料因刚加入炉内,故温度低,主要是通过吹风时的吹风气,上吹时的煤气,以及下吹时的过热蒸汽,通过此区域时,将此区域的水蒸发掉,起干燥预热的作用.干馏层: 此区燃料受到热气体连续加热并分解放出低分子烃,在热分解时析出水份,醋酸,硫化氢,甲烷等,气化剂通过此区域时一般不发生反应.还原层: 此区域是气化层发生气化反应的主要区域之一,由氧化层来的CO2还原生成CO及水蒸汽分解为氢气,燃料依靠与热的气体换热被再次预热,此区域的化学反应是:CO2+C=2COH2O+C=CO+H22H2O+C=CO2+2H2CO+H2O=CO2+H2氧化层: 在煤气炉的整个燃料中此区域的温度最高,燃料中的C与空气中的O 2产生反应,其反应C+O2+3.76N2=CO2+3.76N22C+O2+3.76N2=2CO+3.76N2氧化层与还原层总称为气化层.灰渣层: 燃料经过气化后,剩余物质称为灰渣,灰渣与炉体最下部分称为灰渣层,在生产中起到预热气化剂,保护炉篦和承受燃料层骨架的作用.3.间歇式制气通常分为五个阶段进行:吹风阶段: 空气从炉底吹入,进行气化反应,提高燃料层的温度.上吹制气阶段:蒸汽和加氮空气从炉底送入,经气化反应生成煤气送入气柜.下吹制气阶段: 水蒸气自上而下通过燃料层生成的煤气也送入气柜,其目的是吸收炉内热量可降低炉顶温度,使气化层恢复到正常位置,同时使炭层温度增高,有利于燃尽残碳.二次上吹制气阶段: 蒸气由炉底入炉将炉底下部管道中的煤气排净,为吹风做准备俗称安全上吹.吹净回收阶段: 二次上吹后炉上部分空间出气管道及有关设备都充满煤气,如吹入空气立即放空或送三气将造成浪费,因此转入吹风之前,从炉底部吹入空气,与产生的空气煤气与原来残留的水煤气一并送入气柜加以回收。
造气炉图示4.本次工艺设计计算的根据说明(1).原料采用无烟块煤。
(2).基本数据主要是参照湖北宜化以及煤炭科学研究所的实测结果,并作了相应的适当调整。
加氮方法是采用上吹加氮,即开始上吹的同时,吹风暂不关闭,继续由空气管路向炉内送空气,一并回收到系统中去。
加氮时间可根据半水煤气成份要求随时调整。
显然,这种方法不如上、下吹全过程均匀加氮的效果好,但简单方便,亦可以满足生产需要。
为简化计算,按照蒸汽吹送阶段均匀加氮来进行计算。
2.物料及热量衡算计算基准:以100kg块状无烟煤为原料。
本设计中块煤来源于山西,根据鄂尔多斯联合化工有限公司造气工艺指标分析参数以及相关调整制定已知条件如下:表2-1燃料组成及热值序号成份 C H O N S A1 W 合计1 重量(%)湿78.011.44 0.45 0.76 0.4813.765.1 1002 重量(%)干82.2 1.52 0.4740.80.50614.5 —100燃料热值:28164.6KJ/kg其中:A1为灰份W为水份表2-2吹风气组成成份H2CO CO2N2CH4O2合计H2S体积(%) 2.90 5.45 16.9673.570.5060.40 1000.8281g/m3(标)表2-3水煤气组成成份H2CO CO2N2CH4O2合计H2S体积(%)41.531.757.8017.820.78 0.35 100 1.353g/m3(标)表2-4炉渣组成成份 C S A 合计重量% 14.8 0.2 85 100表2-5 各种物料进炉的温度名称温度空气30℃吹风气450℃上行煤气400℃下行煤气250℃炉渣250℃蒸汽压力(0.10MPa)220℃查过热蒸汽过热焓値表得焓値:=2914.01KJ/kg表2-6生产循环时间序号操作名称吹风上吹下吹二次上吹空气吹净合计1 % 20 31 40 6 3 1002 时间 ,S 30 46.5 60 9 4.5 1502.1.被损耗燃料各组分量的计算燃烧在炉中被带出的损失量按照4kg计算,其为干燃料,根据表1-1燃料组成及热值计算求得。
其中被损耗燃料中各组分之重量为:表2-7被损耗燃料中各组分之重量序号元素组成,重量% 各组分重量,kg1 C 82.2 4×0.822=3.2882 H 1.52 4×0.0152=0.06083 O 0.474 4×0.0474=0.0194 N 0.8 4×0.08=0.0325 S 0.506 4×0.0506=0.02026 A214.5 4×0.145=0.58合计100 42.2.炉渣生成量的计算按照标准100kg燃料计算12313.760.5815.50590.85A A L kg A --===其中12313.760.5815.50590.85A A L kg A --=== 1A 为100kg 块状无烟煤中灰份量(湿基)。
2A 为燃烧在炉中被带出的损失量按照4kg 计算时灰份量。
3A 为炉渣组成中灰份量。
由此可以炉渣中各组分的生成量为: C: 15.50490.148 2.2949c L kg =⨯= S: 15.50490.0020.00310s L kg =⨯= A: 15.50490.8513.18A L kg =⨯= 由此可得:A C S L L L L =++2.29490.003113.1815.5059A C S L L L L kg =++=++=2.3.计算带出物及炉渣中各组分的总重量根据表1-7被损耗燃料中各组分之重量计算和上式炉渣生成量的计算求带出物及炉渣中各组分的总重量。
C: 3.288 2.2949 5.5829C kg =+= H: 0.0608H kg = O: 0.019O kg = N: 0.032N kg =S: 0.02020.03100.0512S kg =+= A: 0.5813.1813.76A kg =+= 总计:19.5059kg2.4.燃烧气化后进入煤气中各元素的量根据上式计算的带出物及炉渣中各组分的总重量和式2-1求得:C:78.01 5.582972.4271C kg=-=H:21.44 5.100.0608 1.945918H kg=+⨯-=O:160.045 5.100.019 4.964318O kg =+⨯-=N:0.760.0320.728 N kg =-=S:0.480.05120.4288 S kg=-=总计:80.4941kg计算误差:100(19.505980.4941)0%100-+==3.空气吹分阶段的计算3.1.物料衡算3.1.1.每标准吹风气中各元素的含量计算C: 12(0.05450.16960.0072)0.123922.4C kg =++=H: 22(0.0290.00722)0.00082810.0039222.434H kg=⨯+⨯⨯⨯=O: 32(0.0040.16960.50.0545)0.286922.4O kg =++⨯=N: 280.73570.919622.4N kg =⨯=S:320.00082180.00079434S kg =⨯=3.1.2.由碳平衡计算吹风气产量 372.4271584.56090.1239m ==(标准) 3.1.3.由氮平衡计算空气用量 3584.56090.91960.728543.63280.7922.4m ⨯-==⨯(标准)计算由空气带入水汽量空气 (相对湿度:80%) 30℃由物化手册查得空气中水汽含量为:0.0213kg(水汽)/kg (干气) 空气带入水汽量为:543.63 1.2930.021314.9720kg=⨯⨯=3.1.4.氮的平衡进:燃料带入氢1.9459kg (2.4计算已得)空气中水汽带入氢 214.972 1.663518kg=⨯=合计: 1.9459 1.6635 3.6094kg =+=出:吹风气中的氢584.56090.00392 2.2916kg =⨯=吹风气中水汽含氢3.6094 2.2915 1.3179kg =-=合计为: 2.2915 1.3179 3.6094kg=+=吹风气中水汽含量181.317911.96112kg ⨯=故可得每标准吹风气中水汽含量为: 11.86110.0203584.5609kg =3.1.5.氧的平衡进:燃料带入氧4.9643kg (2.4计算已得)空气中带入氧 32543.630.21163.09922.4kg=⨯⨯=空气中水汽带入氧 1614.97213.308418kg=⨯=合计: 4.9643163.08913.3084181.3617kg =++=出:吹风气中的氧:584.56090.2869167.711kg =⨯= 吹风气中水汽含氧1611.861110.543218kg =⨯=合计为: 167.71110.5432178.2542kg =+=误差:181.3617178.2542100% 1.71%181.3617-=⨯=1.1.2. 硫的平衡进:燃料带入硫0.4288kg (2.4计算已得)出:吹风气中带入硫 0.0007794584.56090.4559kg ⨯=3.2.热量衡算3.2.1进项燃料发热量:10028164.62816460KJ ⨯= 燃料显热:10030 1.04673140.1KJ ⨯⨯=式中1.0467为燃料的比热容:/()o KJ kg C ⋅ 根据燃料情况估算。