螺旋齿轮传动设计计算
克林贝格螺旋锥齿轮设计及参数计算
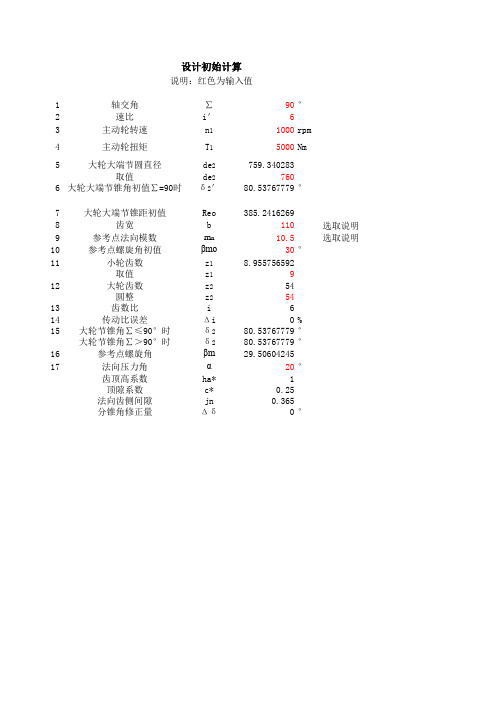
设计初始计算说明:红色为输入值1轴交角∑90°2速比i'63主动轮转速n11000rpm4主动轮扭矩T15000Nm5大轮大端节圆直径de2759.340283取值de27606大轮大端节锥角初值∑=90时δ2'80.53767779°7大轮大端节锥距初值Reo385.24162698齿宽b110选取说明9参考点法向模数m n10.5选取说明10参考点螺旋角初值βmo30°11小轮齿数z18.955756592取值z1912大轮齿数z254圆整z25413齿数比i614传动比误差Δi0%15大轮节锥角∑≤90°时δ280.53767779°大轮节锥角∑>90°时δ280.53767779°16参考点螺旋角βm29.5060424517法向压力角α20°齿顶高系数ha*1顶隙系数c*0.25法向齿侧间隙jn0.365分锥角修正量Δδ0°法冠刀(e (e取刮Au 刀小大无无小小齿小ch∑差至切刀克林贝格制螺旋锥齿轮参数及切齿干涉计算轴交角∑90°r o210压力角α20°z o5齿顶高系数ha*1m o10顶隙系数c*0.25x10.52236中点法向模数m n10.5小轮齿数z19大轮齿数z254中点螺旋角βm30°cosβm0.866025齿宽b110m et14.13368小轮高度变位系数x10.54实际m et14.13368大轮切向变位系数x t10.034小轮高度变位系数x2-0.54m et14.13368大轮切向变位系数x t2-0.034m n10.5小轮齿顶高ha116.17大轮齿顶高ha2 4.83全齿高h23.625外锥距R386.873分锥角修正量Δδ0°侧隙jn0.365大轮节锥角∑≤90°时δ280.5377°sinδ20.986394小轮节锥角δ19.46232°sinδ10.164399小轮大端节圆直径de1127.203大轮大端节圆直径de2763.219小轮齿顶圆直径da1159.103大轮齿顶圆直径da2764.807小轮参考点节圆直径d m1109.119大轮参考点节圆直径d m2654.715冠轮齿数Z p54.7449冠轮大端锥距Re386.873冠轮参考点锥距R m p331.873冠轮小端锥距Ri276.873刀齿方向角δo7.18076°刀位Ex316.516许用范围基圆半径Ey290.027Auxiliary angle at Re q e32.845°Auxiliary angle at Ri q i40.7686°大端螺旋角βe42.3153°小端螺旋角βi16.8113°大端法向模数m ne10.4512小端法向模数m ni9.68275大端模数检验m ne≥m n10.4512<10.5小端模数检验m ne>m ni10.4512>9.682746法截面内最大齿槽宽处的锥距Ry357.091冠轮齿顶高h ao13.125Hw9.91122e fny1 6.73227e fny27.44627e fne1 6.50543e fne27.21943e fni1 5.2984e fni2 6.0124刀顶宽s ao 3.44(e fn)min≥s ao>0.2m n 5.298403> 3.44> 2.1(e fn)max<3.0s ao≤7.446268<10.32<15.89521若小轮有刮伤时起始点的锥距计算取初始值βv=βi迭代求解βv16.8113°刮伤时起始点的锥距Rv249.542Auxiliary angle at Rv q v41.4768°βv处的螺旋角βv9.52966°刀盘干涉检查:小轮展成加工工艺分锥角δE19.46232°大轮展成加工工艺分锥角δE280.5377°Δh0λ8.35518°含义x0131.205y0288.04x e298.757y e245.123x i240.978y i135.123OE172.96OI188.239无干涉检查OE<r0+h a0tanαn172.9604<214.777不干涉<无干涉检查OE<r0+h a1tanαn188.2386<214.777不干涉小轮根切校核:小轮小端法面当量齿轮齿数Z ni110.2917齿顶高修正on inside diameter x i0.54小轮最小高变位系数x grenz0.5449check 初选x1数值x10.54check∑90°时等滑动率计算x1:K0.00527αtm22.7959°f(x1)0.00919f'(x1) 3.44935(x1)10.54(x1)20.53733将此值赋给x1差值:(X1)n+1 -(X1)n-0.00270.001至到(X1)n+1 -(X1)n≤0.001x1 =0.53733x1=(x1)2确定最终值在Ry处在Re处在Ri处切向变位系数计算刀尖圆角半径ρ'a00.28571βb28.0243°小轮大轮刀尖圆角圆心至刀具中心线距E0.096380.16438G-0.4243-1.5043zn13.5203486.732H刀盘半径选取说刀组数刀具模数按等滑动率计算初选参考值大轮大端端面模数小轮大端端面模数已知大端端面模数说明求得中点法向模数。
齿轮螺旋角计算公式

齿轮螺旋角计算公式
1关于齿轮螺旋角的计算公式
齿轮螺旋角是确定齿轮传动系统传递功率的重要参数,属于机械传动方面的基础知识。
齿轮螺旋角就是两个安装相邻轮毂的齿轮上,齿面在旋转过程中所形成螺旋形状所对应的夹角。
求取两个安装相邻轮毂的齿轮之间的齿轮螺旋角计算公式如下:
螺旋角α=(齿轮齿数z2-z1)π/z1z2
其中,z1为第一个齿轮的齿数,z2为第二个齿轮的齿数。
另外,根据齿轮传动的特点,轴上的轮毂应当以弹性关系相连,只有在定位和支承时才以传导热量和阻抗结构分开,因此在确定齿轮螺旋角时,要保证贴合度,轮毂的位置和可动性的定位应该具备一定的松偶合程度。
2如何求取一组齿轮传动系统的齿轮螺旋角
如果要确定一组齿轮传动系统的齿轮螺旋角,首先要获取每个齿轮的齿数参数,然后根据计算公式求取两个安装相邻轮毂的齿轮之间的齿轮螺旋角,依次递推至齿轮传动系统最后一个齿轮。
在求取螺旋角时,需要注意的是,一般在轮毂轴端会有限制位,确保轮毂可以正常旋转,而且要确定一定的阻尼用来减少非平衡情况下发生的转矩波动,以及限制在某个范围内的机械冲击情况。
以上就是关于齿轮螺旋角的计算公式以及如何求取一组齿轮传动系统的齿轮螺旋角的内容,了解这些基础知识可以使我们更熟悉机械传动的基本原理,避免在机械传动系统的设计和制造中出现不经预料的故障。
螺旋伞齿轮参数计算

螺旋伞齿轮参数计算螺旋伞齿轮是一种常见的传动元件,广泛应用于各种机械设备中。
在设计和制造螺旋伞齿轮时,需要考虑一系列参数,以确保其性能和可靠性。
本文将介绍螺旋伞齿轮的参数计算方法,帮助读者更好地理解和应用这一传动元件。
1. 齿轮模数(Module)齿轮模数是指齿轮齿廓曲线的参数,通常用来描述齿轮的尺寸大小。
在计算螺旋伞齿轮的参数时,首先需要确定齿轮的模数,这将直接影响到齿轮的齿数、齿顶高和齿根高等参数。
2. 齿数(Number of Teeth)齿数是螺旋伞齿轮的一个重要参数,它决定了齿轮的传动比和传动效率。
在进行齿数计算时,需要考虑齿轮的模数、齿顶高和齿根高等参数,以确保齿轮的传动性能符合要求。
3. 压力角(Pressure Angle)压力角是描述齿轮齿廓曲线的一个重要参数,它决定了齿轮齿面的形状和传动效率。
在计算螺旋伞齿轮的参数时,需要确定合适的压力角,以确保齿轮的传动性能和耐磨性。
4. 法向变位系数(Normal Base Pitch)法向变位系数是描述螺旋伞齿轮齿廓曲线的一个重要参数,它决定了齿轮齿面的形状和传动效率。
在计算螺旋伞齿轮的参数时,需要确定合适的法向变位系数,以确保齿轮的传动性能和耐磨性。
5. 齿宽(Face Width)齿宽是螺旋伞齿轮的一个重要参数,它决定了齿轮的承载能力和传动效率。
在计算齿宽时,需要考虑齿轮的模数、齿数和齿顶高等参数,以确保齿轮能够承受工作载荷和传递动力。
6. 中心距(Center Distance)中心距是指两个齿轮中心线之间的距离,它决定了螺旋伞齿轮的传动比和传动效率。
在计算中心距时,需要考虑齿轮的模数、齿数和齿顶高等参数,以确保齿轮传动系统的正常工作。
通过合理计算螺旋伞齿轮的参数,可以确保齿轮的传动性能和可靠性。
同时,也可以提高齿轮的使用寿命和传动效率,为机械设备的正常运行提供保障。
希望本文的介绍能够帮助读者更好地理解和应用螺旋伞齿轮的参数计算方法。
螺旋齿轮参数计算公式
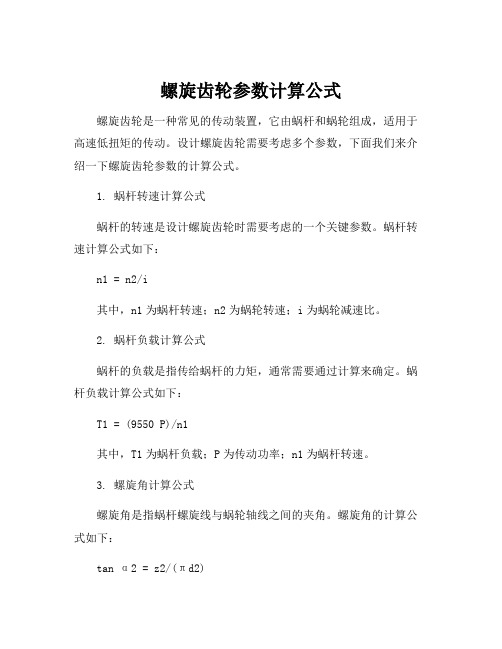
螺旋齿轮参数计算公式
螺旋齿轮是一种常见的传动装置,它由蜗杆和蜗轮组成,适用于高速低扭矩的传动。
设计螺旋齿轮需要考虑多个参数,下面我们来介绍一下螺旋齿轮参数的计算公式。
1. 蜗杆转速计算公式
蜗杆的转速是设计螺旋齿轮时需要考虑的一个关键参数。
蜗杆转速计算公式如下:
n1 = n2/i
其中,n1为蜗杆转速;n2为蜗轮转速;i为蜗轮减速比。
2. 蜗杆负载计算公式
蜗杆的负载是指传给蜗杆的力矩,通常需要通过计算来确定。
蜗杆负载计算公式如下:
T1 = (9550 P)/n1
其中,T1为蜗杆负载;P为传动功率;n1为蜗杆转速。
3. 螺旋角计算公式
螺旋角是指蜗杆螺旋线与蜗轮轴线之间的夹角。
螺旋角的计算公式如下:
tan α2 = z2/(πd2)
其中,α2为螺旋角;z2为蜗轮齿数;d2为蜗轮节圆直径。
4. 螺旋齿计算公式
螺旋齿计算公式是设计螺旋齿轮时必不可少的公式之一,它用来确定蜗轮的齿数。
螺旋齿计算公式如下:
z2 = (d1 tan α1)/π
其中,z2为蜗轮齿数;d1为蜗杆节圆直径;α1为蜗杆螺旋角。
5. 其他参数计算公式
除上述参数外,设计螺旋齿轮还需要考虑其他参数,如模数、齿距、齿顶高等。
这些参数的计算公式需要根据具体情况确定,并结合实际生产需要进行调整。
综上所述,螺旋齿轮的参数计算公式是设计螺旋齿轮必不可少的工具之一,不同的参数相互关联,需要综合考虑。
在实际应用中,设计人员需要根据具体用途和工作条件进行特别设计,以确保螺旋齿轮的可靠性和性能。
螺旋齿轮传动设计计算

螺旋齿轮传动设计计算
1.轴速比的计算
轴速比是指两个相邻轴上齿轮的转速比。
根据传动比的定义,轴速比可以通过齿轮的啮合齿数来计算。
假设小齿轮的齿数为N1,大齿轮的齿数为N2,则轴速比为:
轴速比=N2/N1
2.齿轮模数的选择
齿轮模数是指齿轮齿数与齿轮直径的比值。
在选择齿轮模数时,需要根据传动的功率和转速等参数来确定。
根据齿距计算公式,齿轮模数可以选择为:
模数=齿数/齿距
3.齿轮啮合角的计算
齿轮啮合角是指两个啮合齿轮的主动齿与被动齿之间的夹角。
根据传动比和齿轮啮合的齿数,齿轮啮合角可以通过以下公式进行计算:齿轮啮合角 = arccos(N1/N2)
4.齿轮中心距的计算
齿轮中心距是指两个相邻轴上齿轮的中心距离。
在设计计算中,齿轮中心距可以通过以下公式进行计算:
齿轮中心距=(齿数1+齿数2)/2*模数
其中,齿数1和齿数2分别为小齿轮和大齿轮的齿数。
5.齿轮弯曲强度的计算
齿轮的弯曲强度是指齿轮在传动过程中所承受的弯曲应力。
通常,齿轮的弯曲强度可以通过以下公式进行计算:
齿轮弯曲强度=270*Y*(Wt^2*Mt*Kv)/(b*m*Z)
其中,Y为齿轮弯曲系数,Wt为齿轮齿宽压力,Mt为传动扭矩,Kv 为动载荷系数,b为齿轮齿宽,m为齿轮模数,Z为齿轮齿数。
齿轮传动轴距公式

齿轮传动轴距公式
齿轮传动轴距公式是在机械传动领域中广泛应用的一种计算公式,它用于计算齿轮传动中两个齿轮之间的轴距。
轴距是指两个齿轮轴线之间的距离,它是齿轮传动设计中的重要参数之一。
在齿轮传动中,轴距的确定是十分关键的,它直接影响着齿轮传动的传动比、传动效率以及运转稳定性等方面。
因此,准确计算轴距对于齿轮传动的设计和运行十分重要。
齿轮传动轴距公式的推导是基于齿轮的齿数、模数以及齿轮的模数系数等参数。
根据齿轮传动的几何原理,可以得到如下的轴距公式:轴距 = (齿轮1的齿数 + 齿轮2的齿数) * 模数 * 模数系数
其中,齿轮1和齿轮2分别是齿轮传动中的两个齿轮,齿数是指齿轮上的齿的数量,模数是指齿轮齿数与直径的比值,模数系数是一个修正系数,用于考虑齿形误差、噪声等因素。
齿轮传动轴距公式的应用十分广泛,它可以用于计算各种类型的齿轮传动的轴距,如直齿轮传动、斜齿轮传动、螺旋齿轮传动等。
通过合理选择齿轮的齿数、模数和模数系数等参数,可以满足不同传动比要求的齿轮传动设计。
齿轮传动轴距公式的推导和应用需要一定的机械知识和计算能力。
在实际工程中,可以使用计算软件或者表格来进行轴距的计算,以
提高计算的准确性和效率。
同时,还需要考虑到实际生产制造的可行性和经济性,选择合适的齿轮材料和加工工艺,以确保齿轮传动的可靠性和耐久性。
齿轮传动轴距公式是齿轮传动设计中的重要工具,通过合理计算和选取参数,可以确保齿轮传动的传动性能和可靠性。
在实际应用中,需要综合考虑多种因素,进行全面的设计和分析,以满足实际需求。
齿轮传动设计计算实例(114)

解:
cos
mn 2a
z1
z2
4 30 60
2 190
0.9474
所以
1840
tan t
tan n cos
tan 20 cos1840
0.3640 0.9474
0.3842
d1
mn cos
z1
4 30 0.9474
mm 126.662mm
F2
2KT1 bm 2 z 2
YFa2YSa2
F1
YFa 2 YSa 2 YFa1YSa1
82.76 2.2881.734 MPa 2.52 1.625
80.18MPa< F 2
故轮齿齿根弯曲疲劳强度足够。
(4)计算齿根传动的中心距 a
a
m 2
z1
z2
2 2
db2 d 2 cos t 253.325 0.9335mm 236.479mm
例 3 试设计带式运输机减速器的高速级圆柱齿轮传动。已知输入功率 P 40kW ,小齿轮转速 n1 970r / min ,传动比 i 2.5 ,使用寿命为 10a(年)(设每年工作 300d(天)),单班制,电动机驱动,
(3)校核齿面接触疲劳强度
由式(8.45)
H 3.17Z E
KT u 1
bd 12 u
H
确定有关参数和系数:
1)分度圆直径
d1
mn z1 cos
3 24 cos1415
mm 74.29mm
螺旋齿轮设计须知
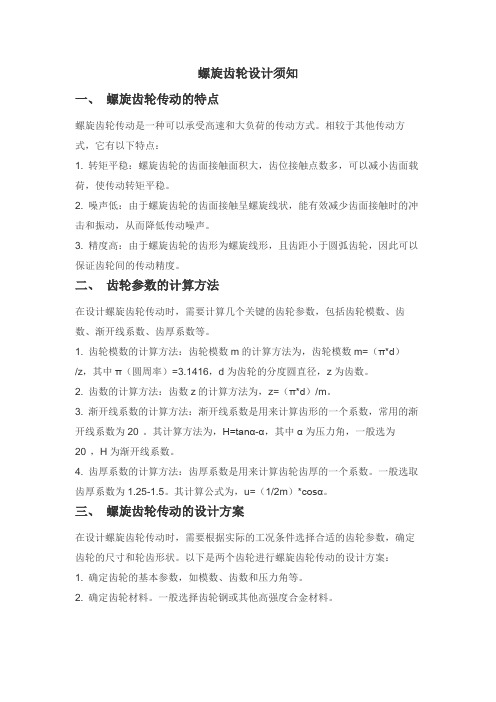
螺旋齿轮设计须知一、螺旋齿轮传动的特点螺旋齿轮传动是一种可以承受高速和大负荷的传动方式。
相较于其他传动方式,它有以下特点:1. 转矩平稳:螺旋齿轮的齿面接触面积大,齿位接触点数多,可以减小齿面载荷,使传动转矩平稳。
2. 噪声低:由于螺旋齿轮的齿面接触呈螺旋线状,能有效减少齿面接触时的冲击和振动,从而降低传动噪声。
3. 精度高:由于螺旋齿轮的齿形为螺旋线形,且齿距小于圆弧齿轮,因此可以保证齿轮间的传动精度。
二、齿轮参数的计算方法在设计螺旋齿轮传动时,需要计算几个关键的齿轮参数,包括齿轮模数、齿数、渐开线系数、齿厚系数等。
1. 齿轮模数的计算方法:齿轮模数m的计算方法为,齿轮模数m=(π*d)/z,其中π(圆周率)=3.1416,d为齿轮的分度圆直径,z为齿数。
2. 齿数的计算方法:齿数z的计算方法为,z=(π*d)/m。
3. 渐开线系数的计算方法:渐开线系数是用来计算齿形的一个系数,常用的渐开线系数为20°。
其计算方法为,H=tanα-α,其中α为压力角,一般选为20°,H为渐开线系数。
4. 齿厚系数的计算方法:齿厚系数是用来计算齿轮齿厚的一个系数。
一般选取齿厚系数为1.25-1.5。
其计算公式为,u=(1/2m)*cosα。
三、螺旋齿轮传动的设计方案在设计螺旋齿轮传动时,需要根据实际的工况条件选择合适的齿轮参数,确定齿轮的尺寸和轮齿形状。
以下是两个齿轮进行螺旋齿轮传动的设计方案:1. 确定齿轮的基本参数,如模数、齿数和压力角等。
2. 确定齿轮材料。
一般选择齿轮钢或其他高强度合金材料。
3. 确定齿轮的加工工艺和精度要求。
齿轮应采用先粗加工再精加工的工艺,以保证齿轮的精度。
4. 确定齿轮的润滑方式,选择合适的润滑油和润滑方式,保证传动的正常运转。
5. 进行螺旋齿轮的设计,包括计算轮齿形状、计算齿轮间隙、计算齿轮的径向力、计算齿轮的传动效率等。
6. 进行螺旋齿轮的校核与修正,通过计算校核其传动能力,用实验和模拟验证螺旋齿轮的传动效果。
- 1、下载文档前请自行甄别文档内容的完整性,平台不提供额外的编辑、内容补充、找答案等附加服务。
- 2、"仅部分预览"的文档,不可在线预览部分如存在完整性等问题,可反馈申请退款(可完整预览的文档不适用该条件!)。
- 3、如文档侵犯您的权益,请联系客服反馈,我们会尽快为您处理(人工客服工作时间:9:00-18:30)。
% 螺旋齿轮传动设计计算
% 已知条件:齿数、法面压力角、法面模数、齿顶高系数、顶隙系数、轴交角
z1=17;z2=50;alpha_n=20;m_n=2;ha=1;C=0.25;Sigma=60;hd=pi/180;
% 计算齿轮的分度圆柱压力角、基圆柱和节圆柱螺旋角、法面和端面节圆压力角
beta_1=0.5*(Sigma-1);beta_2=beta_1;
fprintf(' 两齿轮螺旋角 beta_1 = %3.4f °\n',beta_1);
alpha_t1=atan(tan(alpha_n*hd)/cos(beta_1*hd));alpha_t2=alpha_t1;
fprintf(' 两齿轮分度圆柱螺旋角 alpha_t1 = %3.4f °\n',alpha_t1/hd);
beta_b1=atan(tan(beta_1*hd)*cos(alpha_t1));beta_b2=beta_b1;
fprintf(' 两齿轮基圆柱螺旋角 beta_b1 = %3.4f °\n',beta_b1/hd);
k=sin(beta_b1)/sin(beta_b1);
beta_1p=atan(k*sin(Sigma*hd)/(1+k*cos(Sigma*hd)));beta_2p=beta_1p; fprintf(' 两齿轮节圆柱螺旋角 beta_1p = %3.4f °\n',beta_1p/hd);
alpha_np=acos(sin(beta_b1)/sin(beta_1p));
fprintf(' 两齿轮法面节圆压力角 alpha_np = %3.4f °\n',alpha_np/hd); alpha_t1p=acos(tan(beta_b1)/tan(beta_1p));alpha_t2p=alpha_t1p;
fprintf(' 两齿轮端面节圆压力角 alpha_t1p = %3.4f °\n',alpha_t1p/hd);
% 确定两齿轮的变位系数
inv_t1p=tan(alpha_t1p)-alpha_t1p;inv_t1=tan(alpha_t1)-alpha_t1;
inv_t2p=tan(alpha_t2p)-alpha_t2p;inv_t2=tan(alpha_t2)-alpha_t2;
xc=(z1*(inv_t1p-inv_t1)+z2*(inv_t2p-inv_t2))/(2*tan(alpha_n*hd))
x_n1=input(' 选择小齿轮法面变位系数 x_n1 = ');
x_n2=xc-x_n1;
fprintf(' 大齿轮法面变位系数 x_n2 = %3.4f \n',x_n2);
% 计算齿轮的几何尺寸
m_np=m_n*cos(alpha_n*hd)/cos(alpha_np);
fprintf(' 公共齿条的法面模数 m_np = %3.4f mm \n',m_np);
r_1p=m_np*z1/(2*cos(beta_1*hd));
r_2p=m_np*z2/(2*cos(beta_2*hd));
fprintf(' 小齿轮节圆柱半径 r_1p = %3.4f mm \n',r_1p);
fprintf(' 大齿轮节圆柱半径 r_2p = %3.4f mm \n',r_2p);
a=(r_1p+r_2p);
fprintf(' 两齿轮最小中心距 a = %3.4f mm \n',a);
r_1=m_n*z1/(2*cos(beta_1*hd));
r_2=m_n*z2/(2*cos(beta_2*hd));
fprintf(' 小齿轮分度圆半径 r_1 = %3.4f mm \n',r_1);
fprintf(' 大齿轮分度圆半径 r_2 = %3.4f mm \n',r_2);
r_b1=r_1*cos(alpha_t1);
r_b2=r_2*cos(alpha_t2);
fprintf(' 小齿轮基圆柱半径 r_b1 = %3.4f mm \n',r_b1);
fprintf(' 大齿轮基圆柱半径 r_b2 = %3.4f mm \n',r_b2);
r_f1=r_1-m_n*(ha+C-x_n1);
r_f2=r_2-m_n*(ha+C-x_n2);
fprintf(' 小齿轮齿根圆柱半径 r_f1 = %3.4f mm \n',r_f1);
fprintf(' 大齿轮齿根圆柱半径 r_f2 = %3.4f mm \n',r_f2);
r_a1=a-r_f2-0.25*m_n; % 为保证合理顶隙0.25*mn,根据中心距计算齿轮齿顶圆柱半径
r_a2=a-r_f1-0.25*m_n;
fprintf(' 小齿轮齿顶圆柱半径 r_a1 = %3.4f mm \n',r_a1);
fprintf(' 大齿轮齿顶圆柱半径 r_a2 = %3.4f mm \n',r_a2);
% 校验齿轮传动的重合度
B1=sqrt(r_a1^2-r_b1^2)/cos(beta_b1)+sqrt(r_a2^2-r_b2^2)/cos(beta_b2);
B2=(a-r_b1*cos(alpha_t1p)-r_b2*cos(alpha_t2p))/sin(alpha_np);
B1B2=B1-B2;
fprintf(' 齿轮传动实际啮合线长度 B1B2 = %3.4f mm \n',B1B2);
b_a1=B1B2*sin(beta_b1);
b_a2=B1B2*sin(beta_b2);
fprintf(' 小齿轮有效宽度 b_a1 = %3.4f mm \n',b_a1);
fprintf(' 大齿轮有效宽度 b_a2 = %3.4f mm \n',b_a2);
epsilon=B1B2/(pi*m_n*cos(alpha_n*hd));
fprintf(' 齿轮传动重合度 epsilon = %3.4f \n',epsilon);
计算结果:
两齿轮螺旋角 beta_1 = 29.5000 °
两齿轮分度圆柱螺旋角 alpha_t1 = 22.6940 °
两齿轮基圆柱螺旋角 beta_b1 = 27.5632 °
两齿轮节圆柱螺旋角 beta_1p = 30.0000 °
两齿轮法面节圆压力角 alpha_np = 22.2632 °
两齿轮端面节圆压力角 alpha_t1p = 25.3006 °
xc = 0.8312
选择小齿轮法面变位系数 x_n1 = 0.40
大齿轮法面变位系数 x_n2 = 0.4312
公共齿条的法面模数 m_np = 2.0308 mm
小齿轮节圆柱半径 r_1p = 19.8328 mm
大齿轮节圆柱半径 r_2p = 58.3317 mm
两齿轮最小中心距 a = 78.1644 mm
小齿轮分度圆半径 r_1 = 19.5322 mm
大齿轮分度圆半径 r_2 = 57.4478 mm
小齿轮基圆柱半径 r_b1 = 18.0200 mm
大齿轮基圆柱半径 r_b2 = 53.0001 mm
小齿轮齿根圆柱半径 r_f1 = 17.8322 mm 大齿轮齿根圆柱半径 r_f2 = 55.8102 mm 小齿轮齿顶圆柱半径 r_a1 = 21.8543 mm 大齿轮齿顶圆柱半径 r_a2 = 59.8322 mm
齿轮传动实际啮合线长度 B1B2 = 8.4288 mm 小齿轮有效宽度 b_a1 = 3.9002 mm
大齿轮有效宽度 b_a2 = 3.9002 mm
齿轮传动重合度 epsilon = 1.4276。