丁辛醇装置的全流程模拟收敛策略及计算-天然气与石油
回收丁辛醇装置驰放气中丙烯和丙烷的工艺设计
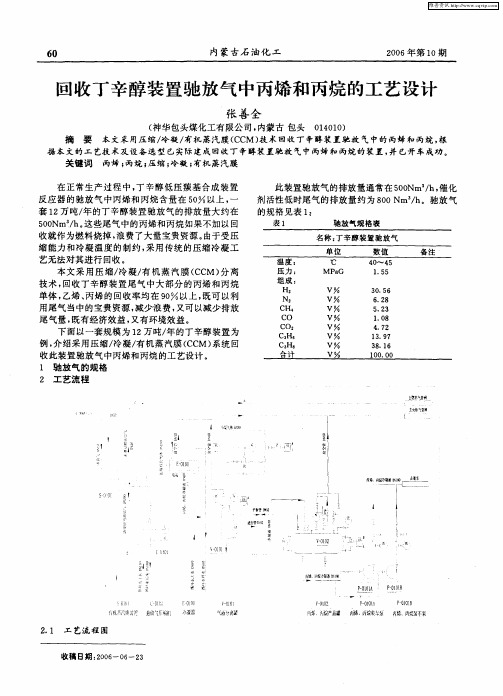
6 1
工 艺 流程 图见 带 控制 点工 艺流 程 图 。
2 2 工 艺 流 程 说 明 .
ห้องสมุดไป่ตู้
从 丁 辛醇 装置 反 应器 出来 的放空 驰放 气与 冷 凝 器 出来 的不 凝气 混合 后进 入 有机 蒸汽 膜膜 分离 装 置 S 1 1 经 膜 分离 后 富 含 丙 烯 、 烷 的膜 渗 透 气 进 一0 0 , 丙 入 驰 放 气 压缩 机 C一0 0 , 顶 部 分 离 出来 的 放 空 1 1膜 尾气 进入 燃 料气 管 网 。 富含 丙 烯 和 丙 烷 的渗 透 气 经 压缩 机 压缩 后 , 进 入 冷 凝 器 E一 0 0 , 部 分 的 丙 烯 、 烷 被 冷 凝 下 11 大 丙 来 , 凝 气 经 气液 分 离 罐 V一0 0 不 1 1罐 顶返 回有机 蒸 气 膜 装置 。 凝下 来 的丙烯 和 丙烷 冷 凝液 作为产 品 , 冷 注入 丙 烯 和 丙 烷产 品贮 罐 V一0 0 , 1 2 由丙烯 和丙 烷 装车 泵 P—O O A/ 1 1 B装车 。
维普资讯
6 0
内 蒙 古石 油化 工
20 年第 1 期 06 O
回收 丁辛醇装置驰放 气中丙烯 和丙烷 的工艺 设计
张 善 全
( 华包 头煤 化工 有 限公 司 , 神 内蒙 古 包头 0 4 1) 100 摘 要 本文 采 用压 缩/ 凝 / 冷 有机 蒸 汽膜 ( C 技 术 回 收丁 辛醇 装置 驰 放 气中的 丙 烯 和丙烷 , C M) 根 据 本文 的 工 艺技术 及设 备 选 型 已实际 建成 回 收丁 辛醇装 置驰 放 气 中丙烯 和 丙烷 的装 置 , 已开 车成功 。 并 关 键词 丙烯 ; 丙烷 ; 压缩 ; 凝 ; 冷 有机 蒸汽 膜 在 正 常 生产 过 程 中 , 辛 醇 低 压羰 基 合 成 装 置 丁 反应 器 的驰放 气 中丙 烯 和丙 烷 含 量 在 5 %以 上 , O 一 套1 2万 吨/ 的丁辛 醇 装置 驰 放气 的排放 量 大约 在 年 50 0Nm3h 这些 尾 气 中的丙 烯 和丙 烷如 果不 加 以 回 /。 收 就作 为燃 料烧 掉 , 费 了大量 宝 贵 资源 。 浪 由于 受压 缩 能力 和冷 凝 温 度 的制 约 , 采用 传 统 的 压缩 冷 凝 工 艺 无法 对其 进 行 回收 。
VMGSim流程模拟软件在天然气净化装置中的应用
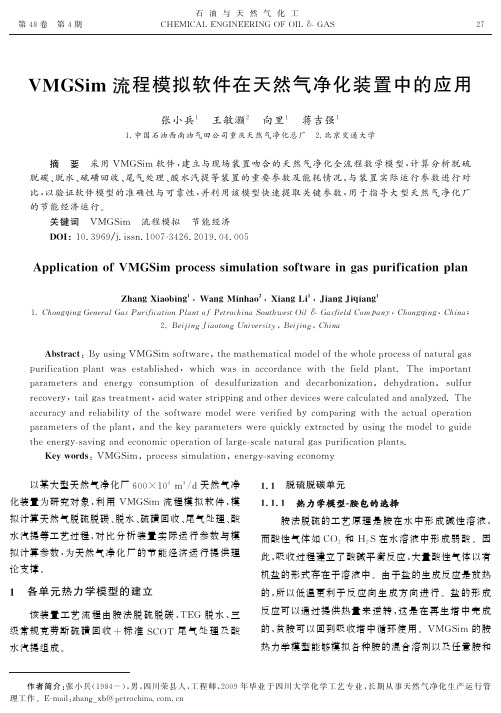
V M G S i m 流程模拟软件在天然气净化装置中的应用张小兵1王敏灏2向里1蒋吉强11.中国石油西南油气田公司重庆天然气净化总厂2.北京交通大学摘要采用VMG S i m软件,建立与现场装置吻合的天然气净化全流程数学模型,计算分析脱硫脱碳㊁脱水㊁硫磺回收㊁尾气处理㊁酸水汽提等装置的重要参数及能耗情况,与装置实际运行参数进行对比,以验证软件模型的准确性与可靠性,并利用该模型快速提取关键参数,用于指导大型天然气净化厂的节能经济运行㊂关键词 VMG S i m 流程模拟节能经济D O I:10.3969/j.i s s n.1007-3426.2019.04.005A p p l i c a t i o no fV M G S i m p r o c e s s s i m u l a t i o n s o f t w a r e i n g a s p u r i f i c a t i o n p l a nZ h a n g X i a o b i n g1,W a n g M i n h a o2,X i a n g L i1,J i a n g J i q i a n g11.C h o n g q i n g G e n e r a lG a sP u r i f i c a t i o nP l a n t o f P e t r o c h i n aS o u t h w e s tO i l&G a s f i e l dC o m p a n y,C h o n g q i n g,C h i n a;2.B e i j i n g J i a o t o n g U n i v e r s i t y,B e i j i n g,C h i n aA b s t r a c t:B y u s i n g VMG S i ms o f t w a r e,t h em a t h e m a t i c a lm o d e l o f t h ew h o l e p r o c e s s o f n a t u r a l g a s p u r i f i c a t i o n p l a n t w a se s t a b l i s h e d,w h i c h w a si na c c o r d a n c e w i t ht h ef i e l d p l a n t.T h ei m p o r t a n t p a r a m e t e r sa n d e n e r g y c o n s u m p t i o n o f d e s u l f u r i z a t i o n a n d d e c a r b o n i z a t i o n,d e h y d r a t i o n,s u l f u r r e c o v e r y,t a i l g a s t r e a t m e n t,a c i dw a t e r s t r i p p i n g a n d o t h e r d e v i c e sw e r e c a l c u l a t e d a n d a n a l y z e d.T h e a c c u r a c y a n dr e l i a b i l i t y o f t h es o f t w a r e m o d e lw e r ev e r i f i e db y c o m p a r i n g w i t ht h ea c t u a lo p e r a t i o n p a r a m e t e r s o f t h e p l a n t,a n d t h ek e yp a r a m e t e r sw e r e q u i c k l y e x t r a c t e db y u s i n g t h em o d e l t o g u i d e t h e e n e r g y-s a v i n g a n d e c o n o m i c o p e r a t i o no f l a r g e-s c a l en a t u r a l g a s p u r i f i c a t i o n p l a n t s.K e y w o r d s:VMG S i m,p r o c e s s s i m u l a t i o n,e n e r g y-s a v i n g e c o n o m y以某大型天然气净化厂600ˑ104m3/d天然气净化装置为研究对象,利用VMG S i m流程模拟软件,模拟计算天然气脱硫脱碳㊁脱水㊁硫磺回收㊁尾气处理㊁酸水汽提等工艺过程,对比分析装置实际运行参数与模拟计算参数,为天然气净化厂的节能经济运行提供理论支撑㊂1各单元热力学模型的建立该装置工艺流程由胺法脱硫脱碳㊁T E G脱水㊁三级常规克劳斯硫磺回收+标准S C O T尾气处理及酸水汽提组成㊂1.1脱硫脱碳单元1.1.1热力学模型-胺包的选择胺法脱硫的工艺原理是胺在水中形成碱性溶液,而酸性气体如C O2和H2S在水溶液中形成弱酸㊂因此,吸收过程建立了酸碱平衡反应,大量酸性气体以有机盐的形式存在于溶液中㊂由于盐的生成反应是放热的,所以低温更利于反应向生成方向进行㊂盐的形成反应可以通过提供热量来逆转,这是在再生塔中完成的,贫胺可以回到吸收塔中循环使用㊂VMG S i m的胺热力学模型能够模拟各种胺的混合溶剂以及任意胺和作者简介:张小兵(1984-),男,四川荣县人,工程师,2009年毕业于四川大学化学工艺专业,长期从事天然气净化生产运行管理工作㊂E-m a i l:z h a n g_x b@p e t r o c h i n a.c o m.c n碳酸钾的混合溶剂㊂胺热力学模型是基于在液相中吉布斯过剩自由能的概念,由3部分组成,如式(1)所示㊂G E=G E L R+G E M R+G E S R(1)式中:E为吉布斯过剩自由能;L R为极限值相关的长程静电力;M R和S R分别为溶剂/离子相互作用的中短程及局部作用项㊂VMG S i m提供了非常丰富的溶剂数据库,即:①链烷醇胺,包括:M D E A㊁T E A㊁D I P A㊁D E A㊁D G A㊁M E A,以及任意多种溶剂的混合物;②物理溶剂,包括:D MT E G㊁S e l e x o l㊁碳酸丙稀脂㊁N F M㊁M P G e n o s o r b;③物理-化学溶剂;如环丁枫与D I P A 及M D E A的混合溶剂;④无机盐,如碳酸钾㊂从工艺物流中脱除如C O2和H2S等酸性气是许多行业必须的工艺过程,这些行业包括气体加工㊁石油炼制㊁合成气净化㊁氨的合成和气化工艺等㊂尽管这些酸性气脱除工艺过程非常普通并且已经应用了许多年,但是精确模拟这些包含化学反应及选择性的工艺过程仍面临着挑战,而VMG S i m能够准确地模拟胺的混合溶液以及任意胺和碳酸钾的混合溶液在净化工艺过程中的详细功能㊂VMG S i m允许修改i=C O2和i=H2S的质量传递系数的值K o g,i=e i K p o g,i(2)式中:K o g,i为气相总体积传质系数;K i为气液平衡常数;e i为系数,可以让匹配的设备性能数据以及添加化学活化剂相关的效应增强[1]㊂1.1.2脱硫脱碳工艺流程的建立现给定装置原料气处理量为603ˑ104m3/d,压力为6.26M P a,温度为27.9ħ,原料气组成见表1㊂表1原料气组成T a b l e1F e e d g a s c o m p o n e n t%组分C H4C O2H2S C2H6C3H8H2O 摩尔分数96.751.900.700.450.040.16本单元采用化学法吸收工艺,利用C T8-5 (VMG S i m软件无法直接计算C T8-5脱硫溶剂,故而采用与之相近的M D E A溶剂进行模拟)水溶液在吸收塔内与含硫天然气逆流接触,吸收脱除含硫天然气中的酸性组分,脱硫后的湿净化气进入脱水单元㊂C T8-5水溶液通过蒸汽加热再生出酸性气体,进入硫磺回收单元㊂脱硫脱碳单元工艺流程如图1所示㊂1.2脱水单元1.2.1热力学模型-性能包的选择就像A P R(a d v a n c e dP e n g R o b i n s o n)属性包一样,A P R N G(a d v a n c e d P e n g R o b i n s o n f o r n a t u r a l g a s)即针对天然气的A P R方程修改了原始的彭罗宾逊(P R)状态方程㊂它比A P R属性包更为专业㊂A P R N G方程最适用于碳氢化合物在水中的溶解度,专门用于计算酸气中的水含量㊁水合物抑制剂㊁乙二醇和烃类的溶解度㊂1.2.2脱水工艺流程的建立脱水单元主要实现湿净化气中的水分脱除㊂塔内湿净化天然气自下而上与T E G贫液逆流接触,脱除天然气中的饱和水㊂脱除水分后的天然气出塔后作为产品天然气输出,产品气要求水露点<-5ħ(在出厂压力条件下)㊂而T E G富液通过T E G再生器加热再生后成为T E G贫液,循环使用㊂脱水单元工艺流程如图2所示㊂1.3硫磺回收单元1.3.1基本克劳斯反应H2S+1/2S O2ң1/x S+H2O(Ⅰ)H2S+3/2O2ңS O2+H2O+热量(Ⅱ)2H2S+S O2ң3/x S x+2H2O+热量(Ⅲ)在改进的克劳斯工艺中,根据式(Ⅱ)的反应,进料气流中1/3的H2S经燃烧形成S O2㊂生成的S O2随后根据式(Ⅲ)与H2S平衡发生反应,生成气相的元素硫S x和H2O[2-4]㊂1.3.2热力学模型选择克劳斯过程的热力学模型较为简单,只要考虑到多种气相中的硫化物,同时考虑建立恰当的液硫物理性质的模型㊂由于所有在克劳斯反应炉和反应器中可能发生的反应使用平衡常数表示是不实际的㊂吉布斯自由能最小化的过程是必要的,因此,理想气体的吉布斯自由能在克劳斯过程中的反应需要1个较大的温度范围㊂从298.15K到3000K,VMG C l a u s性能包为以下物质提供了非常准确的理想气体的吉布斯自由能:S㊁S2㊁S3㊁S4㊁S5㊁S6㊁S7㊁S8㊁C O㊁C O2㊁S O2㊁S O3㊁H2O㊁H2S㊁N H3㊁C O S㊁C S2㊁C1㊁C2㊁C3㊁i-C4㊁n-C4㊁i-C5㊁n-C5㊁C6㊁C7㊁C8㊁C9㊁C10[5-6]㊂1.3.3常规克劳斯硫磺回收工艺流程建立该厂设有2套相同的常规克劳斯硫磺回收装置,与3套规模为600ˑ104m3/d的脱硫脱碳装置匹配,故可视为单套硫磺回收装置与900ˑ104m3/d的脱硫脱碳装置匹配㊂自脱硫单元来的酸气进入克劳斯反应炉,与自风机送出的空气按一定配比在炉内进行克劳斯反应,生成单质硫㊂而后,过程气进入三级常规克劳斯反应器中,在温度较低的情况下用特定的催化剂继续克劳斯平衡反应,将过程气中残留的H2S和S O2在催化剂作用下进一步转化生成硫㊂工艺流程见图3㊁图4㊂1.4S C O T尾气处理单元1.4.1热力学模型-胺包的选择S C O T尾气处理单元采用M D E A溶液为吸收溶剂,反应与脱硫脱碳单元类似,采用相同的胺包㊂1.4.2S C O T尾气处理工艺流程建立硫磺回收装置尾气在线燃烧炉混合室混合升温至最佳反应温度后,过程气进入加氢反应器,在钴/钼催化剂的作用下,硫磺回收装置尾气中的S O2㊁S6㊁S8几乎全部被还原转化为H2S㊂经过冷却后的过程气气流进入吸收塔,被M D E A溶液吸收,剩余尾气经焚烧炉焚烧后排放㊂完成吸收后的M D E A富液经蒸汽再生循环使用㊂尾气处理工艺流程见图5㊁图6和图7㊂1.5酸水汽提单元1.5.1热力学模型选择A P R模型具有P R模型的所有特征,该模型计算酸气中的水含量,以及各类物质在水中溶解度比P R方程更合适,且还具有大量与温度相关的相互作用参数,以及体积平移提升液体密度计算的能力㊂1.5.2酸水汽提单元工艺流程建立从尾气处理单元及其他单元来的酸水进入酸水汽提塔,与来自酸水汽提塔重沸器的蒸汽逆流接触㊂酸水汽提塔顶部出来的气体返回至尾气处理装置急冷塔进一步处理㊂酸水汽提塔底部出来的汽提水经换热冷却后,进入检修污水系统,见图8㊂2模拟参数与实际参数的对比2.1脱硫脱碳及脱水单元对现有装置负荷进行调整,将原料气处理量调整到604ˑ104m3,压力为6.124M P a,温度33.9ħ,模拟数据与实际原料气参数值保持一致,并调整脱硫脱碳㊁脱水单元循环量与之对应㊂原料气㊁产品气组成及其他主要工艺参数对比见表2~表4㊂表2原料气组成对比y/% T a b l e2C o m p a r i s o no f s o u r g a s c o m p o s i t i o n组分C H4C O2H2S C2H6模拟值96.751.90.70.13实际值96.751.90.70.13表3为产品气组成对比㊂由表3可知,模拟所得产品气气质与实际产品气气质较为接近,且完全达到G B17820-2012‘天然气“中二类天然气的技术指标要求㊂表3产品气组成对比y/% T a b l e3C o m p a r i s o no f p r o d u c t g a s c o m p o s i t i o n组分C H4C O2H2S C2H6H2O 模拟值98.4761.370.000680.1430.0050实际值98.3221.400.000460.1330.0051表4脱硫脱碳及脱水单元其他主要工艺参数对比T a b l e4C o m p a r i s o no f o t h e rm a i n p r o c e s s p a r a m e t e r s o f d e s u l f u r i z a t i o n,d e c a r b o n i z a t i o na n dd e h y d r a t i o n u n i t对象原料气处理量/(104m3㊃d-1)产品气流量/(104m3㊃d-1)产品气ρ(H2S)/(m g㊃m-3)产品气水含量/10-6脱硫溶液循环量/(k g㊃h-1)再生蒸汽用量/(k g㊃h-1)胺液质量分数/%脱水溶液循环量/(t㊃h-1)汽提气用量/(m3㊃h-1)模拟值6045987.89140.00117000.0012992.5845.004.92020实际值6045946.62449.68117515.8013380.4446.364.92018表5硫磺回收单元主要工艺参数对比T a b l e5C o m p a r i s o no fm a i n p r o c e s s p a r a m e t e r s o f s u l f u r r e c o v e r y u n i t对象酸气总量/(m3㊃h-1)空气流量/(m3㊃h-1)酸气组成,y/%H2S C O2烃类酸气温度/ħ主炉温度/ħ模拟值9089.59173.141.8257.660.5240.00924.7实际值8162.38592.244.8354.370.8041.381018.5表6各级再热炉参数对比T a b l e6P a r a m e t e r s c o m p a r i s o no f r e h e a t i n g f u r n a c ea t a l l l e v e l s对象一级再热炉出口温度/ħ二级再热炉出口温度/ħ三级再热炉出口温度/ħ一级空燃比二级空燃比三级空燃比模拟值260.00220.00200.009.389.389.38实际值260.12220.14200.069.249.199.172.2硫磺回收单元需要指出,本工程为3套600ˑ104m3天然气净化装置对应2套硫磺回收装置与2套尾气处理装置,3套脱硫脱碳单元再生酸气视为均匀进入2套硫磺回收装置㊂故单套回收装置酸气来源包含3部分,即:①本套装置脱硫脱碳单元产生的酸气;②另外一套装置脱硫脱碳单元产生酸气量的50%;③本套S C O T尾气处理装置再生酸气㊂硫磺回收单元酸气量模拟值与实际有一定差距,可能是由于模拟时选用M D E A溶液㊁溶液质量㊁塔板效率㊁计量误差等多方面原因导致(见表5)㊂在各级再热炉工况相近的(见表6)情况下进行生产,得到的尾气组分与实际差距较大(见表7),但是总硫比例相差不大,说明模拟计算的回收率与实际接近,只需在配风上加以调整即可㊂表7硫磺回收单元尾气数据对比T a b l e7C o m p a r i s o no f t a i l g a s d a t a i ns u l f u r r e c o v e r y u n i t y/%组分H2S S O2C O H2N2C O S C O2C S2模拟值0.0990.6420.7010.50447.0670.02531.4540.030实际值0.4250.2030.4550.48256.4290.00540.8380.000 2.3尾气处理及酸水汽提单元尾气处理装置重要参数见表8~表10㊂表8尾气处理装置反应器出口过程气组成T a b l e8P r o c e s s g a s c o m p o s i t i o no f r e a c t o r o u t l e t o ft a i l g a s t r e a t m e n t u n i t y/%组分H2S S O2C O H2N2C O S C O2模拟值0.82200.0361.27451.2720.00229.115实际值0.97100.0141.14063.3820.00033.558表9尾气处理装置其他工艺参数T a b l e9O t h e r p r o c e s s p a r a m e t e r s o f t a i l g a s t r e a t m e n t u n i t对象反应器入口温度/ħ急冷水循环量/(k g㊃h-1)富液循环量/(k g㊃h-1)贫液循环量/(k g㊃h-1)胺液质量分数/%重沸器蒸汽用量/(k g㊃h-1)外排酸水量/(k g㊃h-1)模拟值230.00102266.3286000.0084000.0040.008800.002859.2实际值227.81101508.4093788.3593038.8939.268063.882982.6表10尾气处理装置尾气组成y/% T a b l e10T a i l g a s c o m p o s i t i o no f t r a i l g a s t r e a t m e n t u n i t组分H2S S O2H2O N2O2模拟值00.01712.5563.230.09实际值00.0167.5076.283.89从表8~表10对比可知,过程模拟计算得到的诸如反应器出口氢含量㊁反应器出口有机硫含量㊁硫回收率等关键参数,与实际值接近㊂因为尾气组分中的C O2日常未进行人工分析,故而未在上述表中列出㊂根据表10尾气中硫含量,通过硫平衡计算可得硫回收率为99.9%,与实际硫回收率99.9%一致㊂3结论(1)利用VMG S i m软件,建立了与现场装置吻合的天然气净化全流程模型,并通过模拟计算得到脱硫脱碳单元㊁脱水单元㊁硫磺回收单元㊁尾气处理单元㊁酸水汽提单元的过程数据㊂通过对比,模拟数据与实际生产数据接近,外输产品气满足G B17820-2012‘天然气“二类气气质指标,外排尾气中S O2质量浓度和S O2排放速率均满足G B16297-1996‘大气污染物综合排放标准“㊂(2)硫磺回收单元流程模拟配风是微量过风,这是为了维持硫磺回收单元尾气中含有足够的S O2㊂然而在实际装置操作中,为防止S O2穿透,采取的配风方式是使硫磺回收尾气H2S与O2体积比大于2ʒ1,从而保证尾气处理单元的平稳运行[7]㊂(3)VMG S i m流程模拟软件虽然在产品气质量㊁尾气S O2排放等关键指标上显示出一定的预测性,但在硫磺回收单元过程气组成运算中与实际数据存在一定的误差,还需要持续对计算过程进行优化调整㊂(4)通过对天然气净化装置的多项关键数据进行对比验证,VMG S i m全流程的建立有利于模拟装置运行与参数调整,对大型天然气净化装置的节能㊁经济运行具有一定的指导意义㊂参考文献[1]廖小敏.聚乙二醇二甲醚(N H D)脱硫系统模拟与优化改造[D].南昌:南昌大学,2010.[2]刘文君,余姣,马向伟,等.影响硫磺回收装置长周期运行因素分析[J].石油与天然气化工,2017,46(1):27-33.[3]陈赓良,肖学兰,杨仲熙,等.克劳斯法硫磺回收工艺技术[M].北京:石油工业出版社,2007.[4]曹文全,韩晓兰,周家伟,等.常规克劳斯非常规分流法硫磺回收工艺在天然气净化厂的应用[J].石油与天然气化工,2016,45 (5):11-16.[5]高艳楠,常宏岗.基于VMG S i m的M C R C工艺模拟计算与分析[J].化学工程与装备,2009(11):8-11.[6]熊俊杰,李涛,王小强,等.M C R C硫磺回收装置堵塞原因分析及预防措施[J].石油与天然气化工,2015,44(5):34-37. [7]马建明,刘文君.硫磺回收装置的流程模拟及操作优化研究[J].石化技术,2017,24(5):췍췍췍췍췍췍췍췍췍췍췍췍췍췍췍췍췍췍췍췍췍췍췍췍췍39-40.收稿日期:2019-04-08;编辑:温冬云。
丁辛醇装置工艺技术比选及技术可获得性分析
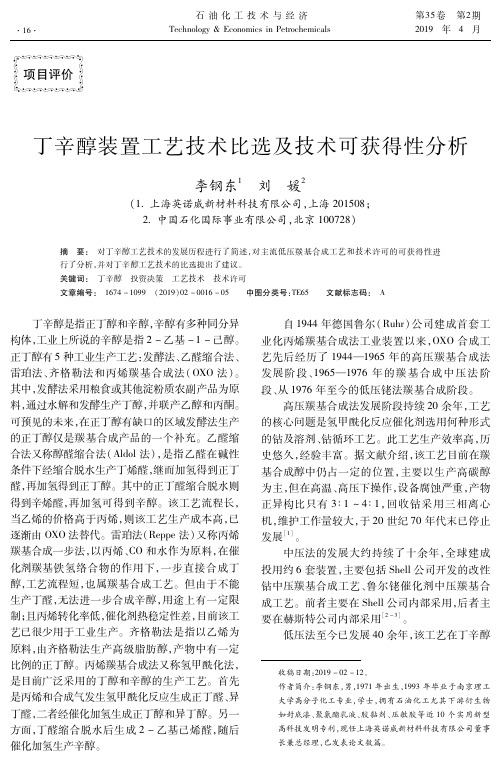
工艺技术及技术可获得性进行分析和比较,为投 资决策者提供决策依据。
1 Davy/Dow工艺技术及许可转让 11 工艺技术
按照羰基合成催化剂的循环方式不同,该技术 先后经历了气相循环工艺和液相循环工艺。前者 是指羰基合成催化剂保留在反应器内,催化剂不随 低碳醛类产物蒸发,从而不需设催化剂回收循环系 统,气相产物经冷凝可分离出醛类,未反应的丙烯、 氢气和一氧化碳等经增压后循环回到反应器;后者 是指羰基合成反应产物和催化剂共同离开反应器, 采用闪蒸和蒸发将催化剂溶液进行分离,从而循环 回到反应器,液相循环工艺于 1984年实现了工业 化[5]。与气相循环工艺相比,液相循环工艺主要是 将两台并联反应器变更为两台串联,提高了反应器 容积利用率,加快了反应速率,同样容积的反应器 能力则提高了 50% ~80%。最近 10年新建装置均 是采用液相循环工艺。
摘 要: 对丁辛醇工艺技术的发展历程进行了简述,对主流低压羰基合成工艺和技术许可的可获得性进 行了分析,并对丁辛醇工艺技术的比选提出了建议。 关键词: 丁辛醇 投资决策 工艺技术 技术许可 文章编号: 1674-1099 (2019)02-0016-05 中图分类号:TE65 文献标志码: A
丁辛醇是指正丁醇和辛醇,辛醇有多种同分异 构体,工业上所说的辛醇是指 2-乙基 -1-己醇。 正丁醇有 5种工业生产工艺:发酵法、乙醛缩合法、 雷珀 法、齐 格 勒 法 和 丙 烯 羰 基 合 成 法 (OXO法 )。 其中,发酵法采用粮食或其他淀粉质农副产品为原 料,通过水解和发酵生产丁醇,并联产乙醇和丙酮。 可预见的未来,在正丁醇有缺口的区域发酵法生产 的正丁醇仅是羰基合成产品的一个补充。乙醛缩 合法又称醇醛缩合法(Aldol法),是指乙醛在碱性 条件下经缩合脱水生产丁烯醛,继而加氢得到正丁 醛,再加氢得到正丁醇。其中的正丁醛缩合脱水则 得到辛烯醛,再加氢可得到辛醇。该工艺流程长, 当乙烯的价格高于丙烯,则该工艺生产成本高,已 逐渐由 OXO法替代。雷珀法(Reppe法)又称丙烯 羰基合成一步法,以丙烯、CO和水作为原料,在催 化剂羰基铁氢络合物的作用下,一步直接合成丁 醇,工艺流程短,也属羰基合成工艺。但由于不能 生产丁醛,无法进一步合成辛醇,用途上有一定限 制;且丙烯转化率低,催化剂热稳定性差,目前该工 艺已很少用于工业生产。齐格勒法是指以乙烯为 原料,由齐格勒法生产高级脂肪醇,产物中有一定 比例的正丁醇。丙烯羰基合成法又称氢甲酰化法, 是目前广泛采用的丁醇和辛醇的生产工艺。首先 是丙烯和合成气发生氢甲酰化反应生成正丁醛、异 丁醛,二者经催化加氢生成正丁醇和异丁醇。另一 方面,丁醛缩合脱水后生成 2-乙基己烯醛,随后 催化加氢生产辛醇。
丁辛醇装置合成气顺控程序的开发与应用

第2 5 卷
丁辛醇 装 置合成 气 顺控 程序 的开发 与应 用
李 春光 , 刘 新光 , 单 中强
( 大庆石化公 司信息技术 中心 , 黑龙江 大庆 1 6 3 7 1 4 )
摘要 : 丁辛醇装置合成气T段顺序控制系统的核心技术多年被外国垄断 。大庆石化公司在消化吸 收国外技术的基础 , 研发出具有 自主知识产权的控制系统技术 。开发出的程序创新性强 、 应用范
围广阔 , 对国内相关类似装置的顺序过程控制具有 良好的指导和借鉴作用。
关键词 : 丁辛醇 ; 安全仪表系统 ; 顺序控制 ; 合成气
实 时显 示 , 扫描周 期小 于 1 0 m s 。
( 8 ) 顺 序 控 制 程 序 的最 大特 点 能 迎 合 同一 工 段 不 同工 段 的 自动 调 整 功 能 , 工 艺 操 作 维 护 人 员 在 切换 另 一 物料 工 况 时 , 只需 要 输 入 简单 的参数 ,
使 工艺 生产 效益 最 大化 , 同 时 使 人 为 干 预 最 小 化 。所 有 控 制过 程 高 度 自动 化 、 模块 化 , 是 企 业 安
气高 温 氧化反 应 过程 中 , 炉 膛 内 部 压 力 控 制 在 3 . 4 8 MP a , 从投 料 到 原料 油 气化 时 间 不到 2 mi n , 所
单 独 的控 制 器 内完 成 , 2 个与 气化 炉 气化 过 程有 关
的 工段 连 续 送 料 和倒 料 时 , 全部 实 现 自动 化 。扫
照 T艺 生 产需 求 形 成 严谨 、 有 序 的顺 序 控 制 步骤 , 并 且伴 随成 熟 、 灵 活 的诊 断机 制 和 异 常处 理 机制 ,
丁辛醇生产工艺

丁辛醇生产工艺丁辛醇的生产工艺有两种路线〜一种是以乙醛为原料〜巴豆醛缩合加氢法,另一种是以丙烯、合成气为原料的低压羰基合成法〜该法是当今国际上最为先进的技术之一〜目前世界丁辛醇70%是由丙烯羰基化法生产的。
它以丙烯、合成气为原料〜经低压羰基合成生产粗丁醛〜再经丁醛处理、缩合、加氢反应制得丁辛醇。
低压羰基合成法生产丁辛醇典型的流程包括: 原料净化、羰基合成、丁醛精制、缩合、加氢、粗醇精馏等工序。
丁醛精制是指粗丁醛除去轻组分后在异构塔内精馏分离得正丁醛和异丁醛。
缩合是指正丁醛脱去重组分后进入缩合系统〜在NaOH存在、120?和0.4MPa条件下〜进行醛醛缩合生成辛烯醛(EPA)。
加氢一般是指正、异丁醛或混合丁醛或辛烯醛加氢生产相应的醇。
但是不论采用那一种方法〜都必须经过丁烯醛/ 丁醛、辛烯醛加氢来制取丁醇和辛醇。
醛加氢是丁辛醇生产过程的重要组成部分〜对丁辛醇的产品质量和生产过程的经济性都有很大的影响。
1丁辛醇加氢工艺路线丁醛加氢制备丁醇和辛烯醛加氢制备辛醇的工业化工艺路线主要有气相法和液相法两种。
液相加氢反应采用多段绝热固定床反应器〜由于液相热容量较大〜反应器内不用设置换热器。
根据反应条件〜段间设置换热器移走反应热〜防止醛的缩合反应。
BASF公司曾经采用过高压液相加氢〜加氢的压力为25.33MPa高压加氢的唯一优点是氢气耗量较少〜所用的液相加氢催化剂为70%N、i 25%Cu、5%M〜n 该催化剂要求氢气分压不低于3.5MPa~所以总高压时〜尾气的氢气浓度可降低〜氢耗少。
但采用该高压工艺〜原料氢气必须高压压缩〜电耗大、设备费用大〜目前已经被淘汰。
BASF公司和三菱化成工艺中醛的加氢采用中压液相加氢工艺〜加氢压力为 4.0-5.0MPa〜加氢反应器形式采用填充床〜反应温度为60-190?。
气相加氢法由于操作压力相对较低〜工艺设备简单而被广泛应用。
目前〜工业上丁辛醇装置上大多采用铜系催化剂气相加氢工艺。
丁辛醇装置回收尾气中氢气的措施及实践

CHEMICAL INDUSTRY AND ENGINEERING PROGRESS 2009年第28卷增刊·264·化工进展丁辛醇装置回收尾气中氢气的措施及实践黄绍海(北京东方石化化工四厂,北京 102400)变压吸附(pressure swing adsorbtion,简称PSA)是吸附分离技术中的一项用于分离气体混合物的新型技术。
在20世纪60年代世界能源危机情况下,美国联合碳化物公司(UCC)首先采用变压吸附技术从含氢工业废气中回收高纯度氢。
1966年第一套PSA回收氢工业装置投产之后至2000年止,仅美国UCC公司已出售300套PSA装置,大部分用在炼油厂、焦炉气、变换气中回收H2,PSA装置也由4床流程发展到现在的16床流程,产品纯度、回收率、生产的连续性都有大幅提高。
装置能力为200~100 000 m3/h 不等。
变压吸附技术在气体分离与纯化领域中应用范围日益扩大。
例如从变换气、焦炉煤气、石油裂解气、甲醇尾气、炼厂气、甲醛尾气、城市煤气中回收氢;从煤矿瓦斯气中回收甲烷;从天然气或油田伴生气中除去乙烷以上杂质;从变换气中脱除二氧化碳;从富二氧化碳或富一氧化碳气源中提取纯二氧化碳或纯一氧化碳;此外,还广泛应用于空气净化和空气分离抽取富氧或纯氮等领域。
我厂丁辛醇造气装置制氢单元也是应用PSA技术把CO变换气中大部分氢提纯成高纯度氢气,但是在制氢单元产生的3000 m3/h尾气中含有大约25%的氢气,尾气中还含有H2O、NH3、CO2、CO、N2、Ar、CH4等杂质,原来一直直接排入火炬进行燃烧,不仅浪费了大约750 m3/h的氢气,而且也污染了环境,经过充分的认证并结合二氧化碳回收项目最终进行了技术改造,新建一套小型PSA回收氢气装置,实现节能与环保效益。
1 PSA制氢的原理PSA制H2是在等温条件下,通过压力的变化来提纯H2的。
在高压时,杂质分子被吸附在吸附剂的表面,是气体分子与吸附剂相互之间的物理作用,类似于气体在液体中的凝结或溶解,其吸附力决定于进料气体的温度、压力、分子半径、分子极性、分子形状以及吸附剂的材料表面特性和孔径率、孔径分布。
丁辛醇装置降膜蒸发器蒸发效率分析

丁辛醇装置降膜蒸发器蒸发效率分析摘要:降膜蒸发器是一种高效的蒸发设备,具有温差小、滞留时间短、工作寿命长、结构紧凑、效数不受限制等优点。
提高蒸发器的传热性能和蒸发效率,对于工程投资和节能降耗都具有重要意义。
中国石油天然气股份公司大庆石化分公司化工二厂丁辛醇装置(简称丁辛醇装置)降膜蒸发器在羰基合成系统中起着重要的作用,它通过蒸发的方法使闪蒸溶液分离出产品醛,并影响着铑催化剂的回收量、活性、寿命、进料和尾流比、反应器的液位及三苯基膦(TPP)在溶液中的含量。
该设备在设计压力为0.15MPa和95-135℃下操作,为热水加热的降膜式换热器。
关键词:丁辛醇;装置;降膜蒸发器;蒸发效率;分析引言:丁辛醇是随着石油化工、聚乙烯塑料工业的发展和羰基合成工业技术的发展迅速发展起来的。
羰基合成反应技术是1938年在德国最先开发成功的,随着在英、美、法、意等国家获得发展。
目前丁辛醇的合成方法有四种:乙醛缩合法,发酵法,齐格勒法和羰基合成法,前几种方法被羰基合成法所取代。
羰基合成法又分为高、中、低压合成法,同样高压和中压合成法又被低压合成法所取代。
1.丁辛醇装置工艺简介大庆石化化工二厂丁辛醇装置采用气相循环羰基合成技术,装置于1986年10月正式建成并投入使用。
装置以纯度在95%以上的丙烯及合成气(一氧化碳、氢气)作为主要原料,催化剂为铑、三苯基磷,经羰基合成反应生成正丁醛和异丁醛,再经过分离处理后,混合丁醛加氢反应后可以生成粗丁醇产品,通过提纯可产出正丁醇、异丁醇产品;混合丁醛通过正异分离后,正丁醛也可以进行缩合反应后再进行加氢反应生成粗辛醇产品,通过精馏产生辛醇产品。
由于气相循环技术存在副产物较多、污染物排放量大、能耗高等缺陷,国外对其进行了更新换代,改为液相循环技术,其特点是操作安全、前期投资少、工艺简单、对反应条件的要求相对较低等等。
通过可行性调研,2012年针对装置现存的问题和不足,利用大乙烯扩建的机会进行再次技术改造,将羰基合成反应成功更换为液相循环反应,新增一台反应器、高压、低压降膜蒸发系统。
丁辛醇装置全流程模拟计算

[ 4 ]阎芳 , 刘军. 物联 网环境下我国物流信息化发展策略研究[ J ] . 商业
时代 , 2 0 1 1 ( 4 ) : 3 0 — 3 1 .
配送 线 路 自动 优 化 。结 合 先 进 的 物 联 网 理念 , 运 用G P S 、 G I S 、 智 能数据 采集 、 电子锁 等先 进技 术 , 实 现基 于 物联 网 的成 品油 二次 配 送监 控 调度 。该 系
收 稿 日期 : 2 0 1 3 — 0 l 一 0 6
算法[ J ] . 系统工程与电子技术 , 2 0 1 0 , 3 2 ( 8 ) : 1 7 6 0 — 1 7 6 5 .
[ 2 ]张铃 , 张钹. 模糊商空间理论[ J ] . 软件学报 ,
2 0 0 3.1 4( 4) : 7 7 0 — 7 7 6 .
作者简介 : 戴俊源 , 男, 工程师 , 2 0 0 3 年毕业于齐齐哈尔大学 , 现从事 成品油配送调度管理工作。
2 0 1 3 年第1 期
4 1 的结果 见表 2 。
1 . 3加 氢反 应器
丁辛醇装置的辛醇生产流程 由原料精制 、 羰 基 合 成 反 应 回路 、 E P A缩 合 反应 回路 和 加氢 反 应
回路 、 粗辛 醇 精制 组成 …。 1 . 1羰 基 合成反 应 回路
装置 加氢 反应 器 的流程 见 图 3 。
丁辛 醇装 置 的原 料 合 成气 和丙 烯 经 过脱 除 杂 质 净 化 后 进 入 羰 基 反 应 系统 , 在 铑 和 三 苯 基 膦催
原料 精制 、 羰基 合成 反应 回路 的流 程见 图 1 。 在图 1 中, 有 多个物 流 可 以作为 撕裂 流对 回路 进 行 收 敛计 算 乜 。现 选 择 物 流 9 8 作为撕裂流 , 需 要 计 算 的收 敛 变 量 最 少 , 计 算 时 间最 短 。 以物 流 9 8 为撕 裂 流 , 应用 A S P E N P L U S 软 件 ’ 计 算 出该
- 1、下载文档前请自行甄别文档内容的完整性,平台不提供额外的编辑、内容补充、找答案等附加服务。
- 2、"仅部分预览"的文档,不可在线预览部分如存在完整性等问题,可反馈申请退款(可完整预览的文档不适用该条件!)。
- 3、如文档侵犯您的权益,请联系客服反馈,我们会尽快为您处理(人工客服工作时间:9:00-18:30)。
丁辛醇装置的全流程模拟计算
陈丽
(大庆石化公司信息技术中心,黑龙江大庆163316)摘要:应用ASPEN PLUS软件对某化工厂丁辛醇装置进行了全流程模拟,探讨了该装置在
全流程模拟中的羰基合成反应回路、EPA缩合反应回路和加氢反应回路撕裂流的选择及收
敛方法,并进行了合成气在汽提塔3种不同工况下的计算,结果表明整个装置的收敛性很好。
关键词:丁辛醇装置;全流程;模拟计算;收敛性
丁辛醇装置的原料合成气和丙烯经过脱除杂质净化后进入羰基反应系统,在铑和三苯基膦催化作用下生成混合丁醛,混合丁醛以气相离开反应器,冷却后经过汽提脱出轻组分,轻组分返回合成反应系统。
脱出轻组分后的稳定丁醛去异构物塔,将正丁醛和异丁醛分离,异丁醛去储罐,正丁醛进入缩合反应系统在NAOH作用下缩合生成辛烯醛,辛烯醛蒸发后进入加氢反应器同氢气反应生成粗辛醇。
粗辛醇再经过预分馏塔和精馏塔脱出轻组分和重组分最后得到终产品丁醇。
1模拟计算
丁辛醇装置的辛醇生产流程中由原料精制、羰基合成反应回路、EPA缩合反应回路和加氢反应回路、粗辛醇精制组成[1]。
1.1 羰基合成反应回路
原料精制、羰基合成反应回路的流程示意见图1。
图1 原料精制、羰基合成反应回路的流程
在图1中,有多个物流可以作为撕裂流对回路进行收敛计算[2]。
如物流8、18、92、93、98等。
如果选择物流8作为撕裂流则同时必须选择物流18作为撕裂流,这样才能进行计算,同样若选择物流92则同时必须选择物流93才能进行计算。
而只有当选择物流98作为撕裂流时,则不需再选其它物流。
选择物流98作为撕裂流,需要计算的收敛变量最少,计算时间最短。
以物流98为撕裂流,应用ASPEN PLUS软件[3,4]计算出该回路出口物流26的结果见表1。
表1 羰基合成回路模拟计算结果
组分
组分的摩尔分率
撕裂流S98初值撕裂流S98收敛终值出口物流S26
CO 0.105 3 0.119 067 5 4.877 7×10-28 H20.262 7 0.264 749 5 7.380 2×10-31 C3H60.261 8 0.279 097 4 2.187 0×10-11 C3H80.234 6 0.204 024 4 5.800 4×10-5 CO 0.231 9 0.027 667 7 2.055 2×10-18 CH40.049 4 0.042 239 6 1.077 2×10-8
N20.024 6 0.020 943 9 2.172 0×10-30
AR 0.012 3 0.010 595 2 1.261 7×10-27
H2O 0.000 8 0.013 526 6 4.808 7×10-5 SULFU-01 0 1.297 30×10-25 6.942 7×10-8
HCl 0 1.956 98×10-79.852 0×10-22
HCN 0 2.778 78×10-7 1.363 4×10-9 AMMON-01 0 1.242 80×10-6 4.146 2×10-17
O20 2.030 77×10-6 4.761 1×10-31 ACETY-01 0 2.351 19×10-5 2.433 0×10-20
N-BUT-01 0 0.015 3374 0.912 793 2 ISOBU-01 0 2.723 22×10-30.086 943 2 RESIDUE 0 0 1.574 4×10-4
总流率/( kg·h-1) 76 660 88 984.99 14 089.99
温度/℃69.0 55.838 09 80.100 41
压力/MPa 2.0 2.0 2.0
1.2 缩合反应回路
丁辛醇装置缩合反应回路的流程示意见图2。
图2 装置缩合反应回路的流程
在图2中,有多个物流可以作为撕裂流给回路进行收敛计算,如物流34、36、37、99、39、40,选择任何物流作为撕裂流均可[5]。
现以物流40作为撕裂流,应用ASPEN PLUS软件计算出该回路出口物流41的结果见表2。
表2 缩合反应回路模拟计算结果
组分
组分的摩尔分率
撕裂流S40初值撕裂流S40收敛终值出口物流S41
H2O 0.989 8 0.991 727 0.040 835
N-BUT-01 0.001 0 0.063 767
EPA 0.000 1 1.002 65×10-40.888 626 SODIU-01 0 8.171 97×10-30
总流率/( kg·h-1) 8 574.000 8 542.627 11 048.66
温度/℃62.000 68.027 40.000
压力/MPa 4.6 4.6 9.0
1.3 加氢反应器
装置加氢反应器的流程示意见图3。
图3 装置加氢反应器回路的流程
在图3中,有多个物流可以作为撕裂流进行回路收敛计算,现以物流55作为撕裂流,应用ASPEN PLUS软件计算出该回路出口物流57的结果见表3。
表3 加氢反应回路计算结果
组分
组分的摩尔分率
撕裂流S55初值撕裂流S55收敛终值出口物流S57
H20.766 4 0.809 808 1.211 17×10-3
CH20.233 9 0 0
H2O 0.00 16 7.299 0×10-30.031 876 7
N-BUT-02 0 3.871 6×10-40.052 592 1
EPA 0 2.461 2×10-50.144 738 2 EMPEL 0 0 5.131 2×10-10
EHA 0 0 7.903 74×10-4
2-EH 0.000 1 0 0.760 694 8 EMPOH 0 0 5.151 62×10-3 SODIU-01 0 0 9.5094×10-14 RESIDUE 0 0 4.949×10-13
总流率/( kg·h-1) 14 410 14 808.31 13 825.9
温度/℃141.0 141.0 31.928 37
压力/MPa 6.5 6.5 3.0
23种不同工况辛醇产品的组成和含量
在实际生产中,根据进料负荷和工艺情况经常调整净化后的合成气进入羰基合成反应器的分流分率。
为了验证流程是否具有较好的收敛性,选择3种不同工况,即净化后的合成气50%、80%、100%进汽提塔T1180(即50%、20%、0%合成气进入羰基合成反应器),选择物流98、40、55作为循环撕裂流,计算终产品辛醇(即2-乙基己醇)的产量和组成,应用ASPEN PLUS软件计算结果见表4。
表4 3种不同工况下辛醇产品的计算结果
组分
组分的摩尔分率
50%去汽提塔80%去汽提塔100%去汽提塔
EPA 1.406 86×10-4 1.407 40×10-4 1.405 80×10-4 EMPEL 6.108 3×10-10 6.108 0×10-10 6.1035 ×10-10 EHA 9.697 89×10-99.698 62×10-99.695 81×10-9 2-EH 0.993 819 6 0.993 820 7 0.993 821 3 EMPOH 6.039 71×10-3 6.038 57×10-3 6.038 11×10-3 RESIDUE 4.457 0×10-31 2.154 9×10-32 4.650 4×10-29总流率/( kg·h-1) 11 333.87 11 334.17 11 334.31 温度/℃42.0 42.0 42.0
压力/MPa 3.3 3.3 3.3 由表4可见,3种不同工况下全流程的收敛性均很好。
3 结论
应用ASPEN PLUS软件对丁辛醇装置进行模拟计算时,选择适当的撕裂流不仅可以节省设计时间,而且是保证流程模拟准确的条件。
同时装置的工程技术人员必须熟知工艺原理、流程模拟模型的适用条件和范围,才能保证对装置在各种工况条件下的模拟计算结果真实和准确。
参考文献
[1] 王松汉,何细藕.乙烯工艺与技术[M].北京:中国石化出版社,2000:18-21.
[2] 陈滨.乙烯工学[M].北京:化学工业出版社,1997:42-45.
[3] 张洪原.化工原理[M].成都:成都科技大学出版社,2003:52-55.
[4] 缪晖.浅析ASPEN PLUS软件在三甘醇脱水工艺设计中的应用[J].天然气工业,1995(5):12-14.
[5] 张伏生.低压羰基合成生产丁辛醇装置的模拟[D].北京:北京化工大学,2005.
收稿日期:2013-01-06
作者简介:陈丽,女,工程师,1994毕业于辽阳石油化工高等专科学校,现从事化工装置的先进控制与优化工作。