轴承套圈热处理技术
套圈热处理
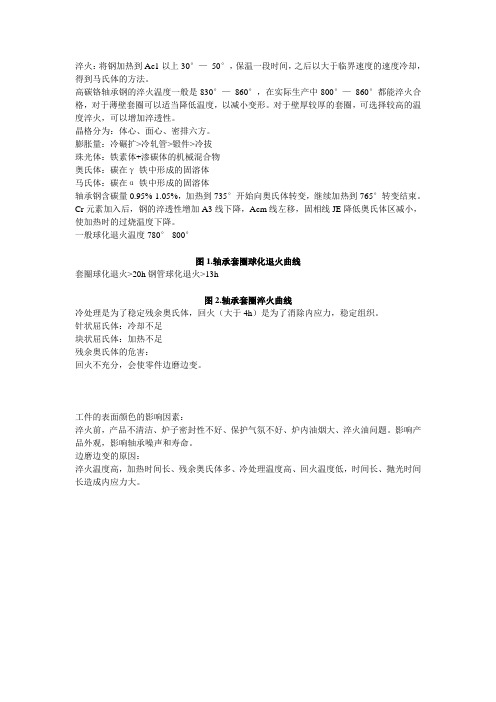
淬火:将钢加热到Ac1以上30°—50°,保温一段时间,之后以大于临界速度的速度冷却,得到马氏体的方法。
高碳铬轴承钢的淬火温度一般是830°—860°,在实际生产中800°—860°都能淬火合格,对于薄壁套圈可以适当降低温度,以减小变形。
对于壁厚较厚的套圈,可选择较高的温度淬火,可以增加淬透性。
晶格分为:体心、面心、密排六方。
膨胀量:冷碾扩>冷轧管>锻件>冷拔
珠光体:铁素体+渗碳体的机械混合物
奥氏体:碳在γ-铁中形成的固溶体
马氏体:碳在α-铁中形成的固溶体
轴承钢含碳量0.95%-1.05%,加热到735°开始向奥氏体转变,继续加热到765°转变结束。
Cr元素加入后,钢的淬透性增加A3线下降,Acm线左移,固相线JE降低奥氏体区减小,使加热时的过烧温度下降。
一般球化退火温度780°-800°
图1.轴承套圈球化退火曲线
套圈球化退火>20h钢管球化退火>13h
图2.轴承套圈淬火曲线
冷处理是为了稳定残余奥氏体,回火(大于4h)是为了消除内应力,稳定组织。
针状屈氏体:冷却不足
块状屈氏体:加热不足
残余奥氏体的危害:
回火不充分,会使零件边磨边变。
工件的表面颜色的影响因素:
淬火前,产品不清洁、炉子密封性不好、保护气氛不好、炉内油烟大、淬火油问题。
影响产品外观,影响轴承噪声和寿命。
边磨边变的原因:
淬火温度高,加热时间长、残余奥氏体多、冷处理温度高、回火温度低,时间长、抛光时间长造成内应力大。
轴承内外圈热处理
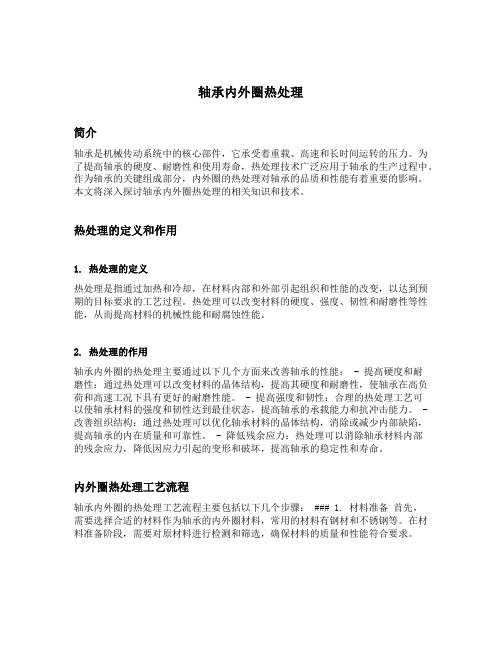
轴承内外圈热处理简介轴承是机械传动系统中的核心部件,它承受着重载、高速和长时间运转的压力。
为了提高轴承的硬度、耐磨性和使用寿命,热处理技术广泛应用于轴承的生产过程中。
作为轴承的关键组成部分,内外圈的热处理对轴承的品质和性能有着重要的影响。
本文将深入探讨轴承内外圈热处理的相关知识和技术。
热处理的定义和作用1. 热处理的定义热处理是指通过加热和冷却,在材料内部和外部引起组织和性能的改变,以达到预期的目标要求的工艺过程。
热处理可以改变材料的硬度、强度、韧性和耐磨性等性能,从而提高材料的机械性能和耐腐蚀性能。
2. 热处理的作用轴承内外圈的热处理主要通过以下几个方面来改善轴承的性能: - 提高硬度和耐磨性:通过热处理可以改变材料的晶体结构,提高其硬度和耐磨性,使轴承在高负荷和高速工况下具有更好的耐磨性能。
- 提高强度和韧性:合理的热处理工艺可以使轴承材料的强度和韧性达到最佳状态,提高轴承的承载能力和抗冲击能力。
- 改善组织结构:通过热处理可以优化轴承材料的晶体结构,消除或减少内部缺陷,提高轴承的内在质量和可靠性。
- 降低残余应力:热处理可以消除轴承材料内部的残余应力,降低因应力引起的变形和破坏,提高轴承的稳定性和寿命。
内外圈热处理工艺流程轴承内外圈的热处理工艺流程主要包括以下几个步骤: ### 1. 材料准备首先,需要选择合适的材料作为轴承的内外圈材料,常用的材料有钢材和不锈钢等。
在材料准备阶段,需要对原材料进行检测和筛选,确保材料的质量和性能符合要求。
加热处理是热处理的核心步骤,它通过加热和冷却来改变轴承材料的组织和性能。
加热处理可以分为多个阶段,包括预热、保温和冷却三个阶段。
预热阶段主要是将材料加热到合适的温度,以便于后续的变形和组织调整。
保温阶段是将材料保持在一定温度下一定时间,使材料的晶体结构发生变化。
冷却阶段是将材料迅速冷却到室温,以固定材料的新组织结构。
3. 表面处理表面处理是为了改善轴承的表面质量和耐磨性。
轴承零件的热处理
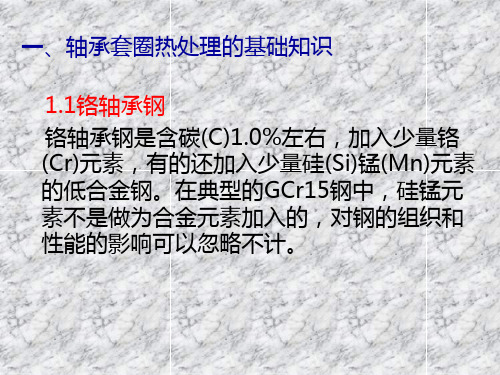
5.3 淬火工艺—工艺曲线图
温度/℃ Acm
升 A”c1 温
保温
冷却
时间/h
5.4淬火工艺过程
套圈
进炉
加热、保温
冷却
5.5 轴承钢套圈的常规淬火工艺温度
淬火加热温度的选择和许多因素有关,如套圈尺寸、淬火后 性能要求等,一般对于含碳量1.0%的轴承钢来说,淬火加 热温度见下表所示:
3)为了满足特殊要求的造成性能 有些轴承 产品要求抗回火性能好,即在淬火后经 200~250℃回火仍需保持较高的硬度。可以 对其施以正火,而后退火。这样可以获得极 细的珠光体组织,这种组织淬火后硬度高、 抗回火性能好。
3.3 正火的工艺
正火工艺的关键在于选择加热温度和冷却方法。由 于正火的目的、正火前显微组织中碳化物的形态以 及2.4 珠光体——铁素体与渗碳体组成的层片状
组织。
珠光体中铁素体与渗碳层片的粗细及形态,对 其性能影响很大,因此又将层片粗细不同的珠 光体分为普通片状珠光体、索氏体、屈氏体; 另外将片状珠光体中的碳化物熔断后形成球状, 得到球状珠光体。
球状珠光体是铁素体基体上分布着粒状渗碳体。
片状珠光体
2~5
2~4
时间/h
4.4.4 快速退火
温度/℃
900~910
30~50 min
正火
780±10
2~2.5 退火
冷却 60~90℃/h 至650℃
时间/h
五、套圈的淬火
5.1 淬火的含义 将钢加热到临界点A”c1~AcM之间某一温度,
保温一段时间,然后快速(大于临界速度)冷却 下来的热处理过程叫淬火。
5.2 淬火的目的
轴承钢淬火的目的是为了得到隐晶或细小的 马氏体、细小而分布均匀的碳化物及少量残 余奥氏体所组成的显微组织。
轴承套圈的材料和最终热处理方法

轴承套圈的材料和最终热处理方法
轴承套圈的材料通常选择高强度、高耐磨损和耐腐蚀的材料。
以下是常用的轴承套圈材料和一种常见的热处理方法:
1. 铬钼合金钢:铬钼合金钢具有较高的硬度和耐磨性,适用于高负荷和高速运转的应用。
对于这种材料,常用的热处理方法是淬火和回火。
淬火可提高材料的硬度,并增加其强度和韧性,而回火可以减轻淬火后的应力,提高材料的耐腐蚀性能。
2. 不锈钢:不锈钢具有良好的耐腐蚀性能,适用于一些特殊环境或要求无锈蚀的应用。
常见的不锈钢材料包括奥氏体不锈钢(如304和316)和马氏体不锈钢(如440C)。
不锈钢的热处理方法包括退火和固溶处理。
3. 铜合金:铜合金具有优良的导热性和抗磨损性能,广泛应用于柔软轴承套圈中。
对于铜合金,常用的热处理方法是固溶处理和时效处理。
需要注意的是,选择轴承套圈的材料和热处理方法应根据具体的应用需求和工作环境来确定,以确保其性能和耐久性能得到最佳发挥。
轴承套圈热处理作业指导书
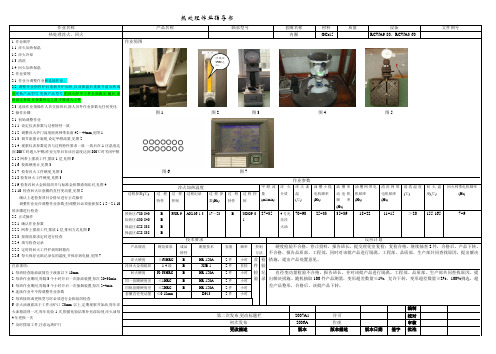
编制 第二次发布,更改标题栏 初次发布 更改描述 2007A1 2006A 版本 许可 作废 版本描述 版本日期 签字 . 校对 审核 批准
浮球在 27~35之
产品名称 作业简图
轴承型15
质量
设备 RCWA9-80,RCWA3-60
文件图号
间
图1
图2
图3
图4
图5
图6
图7 作业参数 淬火加热温度
过 程 控制 过程纪录 过 程 参 数(Hz) 过 程 特性 过程控 制 甲 醇 流 量 (ml/min) 4 号光 亮淬 火油 淬 火 介质 淬火油 温 (℃) 油槽小提 电机频率 (Hz) 油 槽 串 动 电 机 频 (Hz) 率 油槽网带电 机频率 (Hz) 清洗网带 电机频率 (Hz) 清洗温度 (℃) 回 火 温 度(℃) 回火网带电机频率 (Hz)
反应计划 硬度检验不合格,停止投料,报告班长,提交理化室复检;复检合格,继续抽查 2 件,合格后,产品下转。 方法 不合格,报告品质部、工程部,同时对该批产品进行隔离。工程部、品质部、生产部共同查找原因,提出解决 首 检 措施,提出产品处置意见。 件 验 检 纪 直径变动量检验不合格,报告班长,并对该批产品进行隔离。工程部、品质部、生产部共同查找原因,提 验 录 出解决措施。随机抽取 100 件产品测量,变形超差数量≤1%,允许下转,变形超差数量≥2%,100%挑选,超 差产品整形,合格后,该批产品下转。
热处理作业指导书
作业名称 热处理淬火、回火
1 作业顺序 1.1 淬火加热保温 1.2 淬火冷却 1.3 清洗 1.4 回火加热保温 2 作业要领 2.1 作业分调整作业和连续作业。 2.2 调整作业指停炉后重新开炉加热,以及保温后重新升温加热或 者更换产品型号.更换产品型号,把淬火炉中工件全部跑完.随后,重 新设定参数,在参数稳定之前,不准放入工件 2.3 连续作业指操作人员交接班后,除人员外作业参数无任何变化 2 操作步骤 2.1 初始调整作业 2.1.1 设定仪表参数与过程特性一致 2.1.2 调整淬火炉门高度距离网带表面 42~44mm,见图 1 2.1.3 调节流量计旋钮,设定甲醇流量,见图 2 2.1.4 观察仪表参数是否与过程特性要求一致.一致后在 1 区温度达 到 800℃时通入甲醇;作业完毕后在该区温度达到 800℃时关闭甲醇 2.1.5 网带上摆放工件,摆放 1 层,见图 6 2.1.6 校准硬度计,见图 3 2.1.7 检查淬火工件硬度,见图 3 2.1.8 检查回火工件硬度,见图 3 2.1.9 检查淬回火金相组织并与标准金相图谱相比对,见图 4 2.1.10 检查回火后套圈的直径变动量,见图 5 确认上述检查项目合格后进行正式操作 调整作业允许调整作业参数,但调整后必须重新按 2.1.5~2.1.10 的步骤进行检查 2.2 正式操作 2.2.1 确认作业参数 2.2.2 网带上摆放工件,摆放 1 层,排列方式见图 6 2.2.3 按规范要求定时进行检查 2.2.4 填写检查记录 2.2.5 定时将回火工件铲到周转箱内 2.2.6 每天保存无纸记录仪的温度,并保存到电脑,见图 7 注意事项: 1 每班检查除油滚筒位于液面以下 10mm 2 每班作业期间,每隔 3 个小时开启一次除油装置,每次 20~30min 3 每班作业期间,每隔 3 个小时开启一次抽烟装置,每次 2~4min 4 连续作业中不得调整作业参数 5 每班接班或更换型号时必须进行金相组织检查 6 淬火油液面高于工件出炉口 50mm 以上,定期观察并加油,每年淬 火油箱清理一次,每年化验 1 次,根据化验结果补充添加剂,淬火油每 4 年更换一次 7 及时摆放工件,注意远离炉门 预热区:780-840 加热区:830-840 保温区:828-838 保温区:828-838 过程参数(℃) 过 程 特性
轴承零件热处理

快冷 炉冷至650℃后出炉
2~5
2~4 时间/h
4.4.4 快速退火
温度/℃
900~910 780±10
30~50 min 正火
2~2.5 退火
冷却 60~90℃/h 至650℃
时间/h
五、套圈的淬火
5.1
淬火的含义 将钢加热到临界点A”c1~AcM之间某一温度, 保温一段时间,然后快速(大于临界速度)冷却 下来的热处理过程叫淬火。
总之,通过热处理改变珠光体中碳化物的形状、粗细和分布,
可以控制钢的强度和硬度,在相同的抗拉强度下,球状的珠 光体比片状的疲劳强度有所提高。
2.5 马氏体——C在α -Fe中的过饱和固溶体,
体心正方晶体。 马氏体最主要的特征就是高硬度、高强度, 其硬度随着马氏体中碳含量的增加而升高, 当碳含量达到0.6%时,淬火钢的硬度接近最 大值,但塑性和韧性却明显下降。
825~ 830
830~ 835
835~ 840
840~ 845
保温时间 min
5~7
6~8
7~10
9~12
11~1 5
14~1 6
16~1 8
18~2 0
20~2 4
24~26
5.6淬火加热时间的计算
在淬火温度范围内,还要根据具体工艺条件来确定
具体的温度和时间,淬火加热时间的计算见下式:
t= a√ s
900~920 880~910
890~900 870~890
3.4 正火工艺的其它工艺要求
1) 正火的保温时间为30~50min;
2) 薄壁锻件,散开空冷或吹风冷却即可; 3) 壁厚较厚的锻件,需采用喷雾、浸油或浸
乳化液等手段快速冷却; 4) 不论何种冷却方法,冷速必须≥50℃/min。
轴承套圈盐浴淬火

轴承套圈盐浴淬火引言:轴承套圈是一种常见的机械零件,广泛应用于各种机械设备中。
为了提高轴承套圈的硬度和耐磨性,常采用盐浴淬火工艺。
本文将对轴承套圈盐浴淬火进行介绍,包括其原理、工艺流程以及优点。
一、原理:盐浴淬火是一种通过将工件浸入熔盐中进行淬火的热处理方法。
在盐浴中,由于盐的导热性能较好,能够迅速吸热并传递给工件,从而使工件迅速冷却。
盐浴淬火不仅能够提高工件的硬度,还能够改善其组织结构,提高工件的耐磨性和使用寿命。
二、工艺流程:1. 准备工作:首先需要准备好盐浴淬火设备,包括加热炉、盐浴槽和升降装置等。
同时,还需要准备好合适的盐浴液和工件。
2. 加热:将盐浴液加热至适当的温度,通常在300℃到400℃之间。
加热过程中需要控制好温度,确保盐浴液达到预定的淬火温度。
3. 清洗:将待淬火的轴承套圈进行清洗,去除表面的油污和杂质,以保证淬火效果。
4. 浸入盐浴:将清洗后的轴承套圈缓慢地浸入预热好的盐浴液中,确保工件完全浸没在盐浴中,并且要注意不要产生剧烈的气泡。
5. 淬火保持时间:根据不同的工件材料和要求,设定合适的淬火保持时间,使工件充分吸收热量并达到所需的硬度。
6. 从盐浴中取出:淬火时间结束后,将轴承套圈从盐浴中取出,同时要注意避免盐浴液残留在工件表面。
7. 冷却:将取出的轴承套圈进行冷却处理,通常采用自然冷却或水冷却的方式。
8. 清洗与处理:淬火后的轴承套圈还需要进行清洗和处理,以去除盐浴残留和表面的氧化物,保证工件质量。
三、优点:1. 高硬度:盐浴淬火能够使轴承套圈获得较高的硬度,提高其抗磨性和使用寿命。
2. 均匀淬火:盐浴液具有良好的导热性能,可以使工件均匀受热,并且能够迅速吸热,保证工件在短时间内达到所需的淬火温度。
3. 组织结构改善:盐浴淬火可以改善轴承套圈的组织结构,细化晶粒,提高其耐磨性和强度。
4. 生产效率高:盐浴淬火工艺简单,操作方便,能够快速完成淬火过程,提高生产效率。
结论:轴承套圈盐浴淬火是一种常用的热处理方法,能够提高轴承套圈的硬度和耐磨性。
gcr15钢制圆锥滚子轴承套圈的热处理工艺
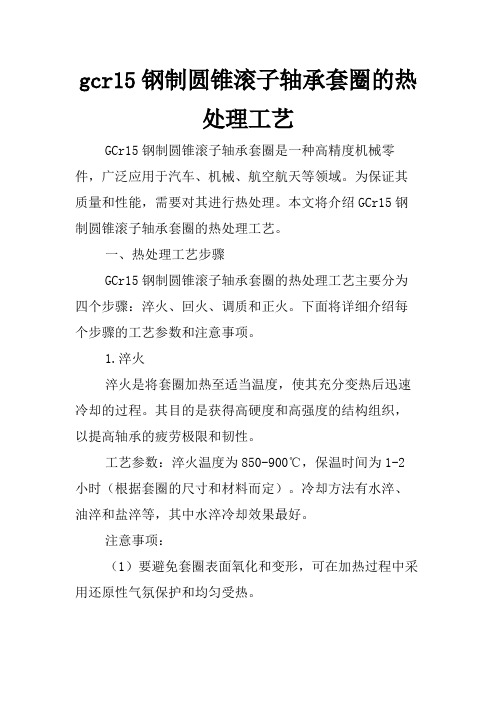
gcr15钢制圆锥滚子轴承套圈的热处理工艺GCr15钢制圆锥滚子轴承套圈是一种高精度机械零件,广泛应用于汽车、机械、航空航天等领域。
为保证其质量和性能,需要对其进行热处理。
本文将介绍GCr15钢制圆锥滚子轴承套圈的热处理工艺。
一、热处理工艺步骤GCr15钢制圆锥滚子轴承套圈的热处理工艺主要分为四个步骤:淬火、回火、调质和正火。
下面将详细介绍每个步骤的工艺参数和注意事项。
1.淬火淬火是将套圈加热至适当温度,使其充分变热后迅速冷却的过程。
其目的是获得高硬度和高强度的结构组织,以提高轴承的疲劳极限和韧性。
工艺参数:淬火温度为850-900℃,保温时间为1-2小时(根据套圈的尺寸和材料而定)。
冷却方法有水淬、油淬和盐淬等,其中水淬冷却效果最好。
注意事项:(1)要避免套圈表面氧化和变形,可在加热过程中采用还原性气氛保护和均匀受热。
(2)选用适当淬火介质,控制淬火速度和温度,以保证套圈的组织和硬度均匀。
2.回火回火是将淬火后的套圈加热至中温(通常在250-450℃之间)保温一段时间后冷却的过程。
其主要目的是调节淬火后套圈的硬度和韧性。
工艺参数:回火温度根据需求而定,通常在200-400℃。
保温时间可根据套圈的尺寸和厚度而定,一般为1-2小时。
冷却方式一般自然冷却即可。
注意事项:(1)回火时间和温度要适当,过长或过短都会影响套圈的性能。
(2)要避免回火过度导致套圈的硬度和强度下降。
3.调质调质是将回火后的套圈再次淬火并再次回火来达到优化微观组织的目的,同时使其保持高硬度的同时提高韧性。
工艺参数:调质温度根据需求而定,通常在500-650℃。
保温时间一般为1-2小时。
淬火介质通常选择油淬。
回火温度和时间要根据套圈的尺寸和厚度而定,一般在200-400℃下进行,保温时间为1-2小时。
注意事项:(1)保证套圈淬火均匀,避免质量差异。
(2)回火过程中要避免过度回火,导致硬度和强度下降,降低轴承寿命。
4.正火正火是将套圈加热至适当温度(一般在840-900℃之间),保温一段时间后进行自然冷却。
- 1、下载文档前请自行甄别文档内容的完整性,平台不提供额外的编辑、内容补充、找答案等附加服务。
- 2、"仅部分预览"的文档,不可在线预览部分如存在完整性等问题,可反馈申请退款(可完整预览的文档不适用该条件!)。
- 3、如文档侵犯您的权益,请联系客服反馈,我们会尽快为您处理(人工客服工作时间:9:00-18:30)。
规格
共4页第1页
轴承套圈热处理变形
技术条件
编号
代替
轴承外圈淬、回火椭圆度见表1
表1
设计外径
轻、中、重系列
特轻、超轻系列允许椭圆度
特轻、窄、超轻窄系列允许椭圆度
外径设计留量
淬、回火后磨量
允许椭圆度
>
≤
≥
≤
30
50
0.25+0.15
0.15
0.45
0.15
0.18
0.20
50
80
0.30+0.20
0.18
400
500
0.55
0.55
0.70
注:
1)挠曲度采用311仪器测量,以有沟面做没量面。
2)圆柱滚子轴承的平挡圈,其挠曲度按上表执行。
3)推力套圈端面凸凹度,是其挠曲度的1/2。
4)用塞尺测得的值,是本表的1/2。
0.35+0.13
0.30
0.40+0.13
0.35
0.50+0.13
0.45
120
180
0.40+0.15
0.35
0.50+0.15
0.45
0.60+0.15
0.50
180
250
0.45+0.17
0.40
0.55+0.17
0.48
0.65+0.17
0.55
250
315
0.50+0.20
0.45
0.60+0.20
共4页第4页
编号
4、推力轴承套圈和内隔圈热处理后变形量见表4
表4 mm
设计外径
椭圆度
D/B<12
17>D/B≥12
D/B≥17
内隔圈
>
≤
挠曲度
挠曲度
挠曲度
挠曲度
椭圆度
挠曲度
30
50
0.15
0.15
0.20
50
80
0.25
0.20
0.25
0.50
0.35
0.30
0.35
80
120
0.25
0.20
0.25
0.30
0.35
0.40
0.45
120
180
0.30
0.30
0.35
0.40
0.45
0.65
0.55
180
250
0.35
0.35
0.40
0.50
0.55
0.80
0.70
250
315
0.40
0.45
0.55
0.65
0.70
1.10
0.80
315
400
0.45
0.50
0.65
0.70
0.75
1.20
0.90
1.15
0.40
250
315
0.40
1.30
0.50
315
400
0.50
1.45
0.60
注:
1)无挡边的圆柱滚子轴承内圈、淬回火后滚道磨量较上表中数值增加0.05。
2)圆锥滚子轴承内圈椭圆度以大挡边为准。
3)带防尘盖的内圈其椭圆度是表的4/5。
轴承套圈热处理变形技术条件
共4页第3页
编号
3、一般轴承套圈淬回火后挠曲度见表3
轴承套圈热处理变形技术条件
共4页第2页
编号
2、轴承内圈淬、回火后椭圆度见表2
表2 mm
设计内径
淬回火后磨量
允许椭圆度
>
≤
≥
≤
30
0.15
0.45
0.45
30
50
0.18
0.60
0.16
50
80
0.20
0.70
0.20
80
120
0.25
0.85
0.25
120
180
0.30
0.95
0.30
180
250
0.35
表3 mm
设计内径
轻、中、重系列套圈
特轻、超轻系列套圈
特轻窄超轻窄系列套圈
>
≤
宽度设计留量
挠曲度
宽度设计留量
挠曲度
宽度设计留量
挠曲度
50
0.25+0.10
0.20
0.30+0.10
0.25
0.40
0.35
50
80
0.30+0.12
0.25
0.35+0.12
0.30
0.45+0.12
0.40
80
120
0.52
0.75+0.20
0.65
315
400
0.60+0.22
0.52
0.70+0.22
0.60
0.85
0.70
注:
1)外圈按同一型号的内圈内径确定。
2)挠曲度采用311仪器测量,以无字面做测量面。
3)带防尘盖及止动槽的套圈,其挠曲度按上表的2/3。
4)用塞尺测得的值,是本表的1/2。
轴承套圈热处理变形技术条件
0.60
0.18
0.20
0.25
80
120
0.35+0.20
0.20
0.70
0.20
0.25
0.30
120
150
0.40+0.25
0.25
0.85
0.25
0.30
0.35
150
180
0.45+0.25
0.30
0.90
0.30
0.35
0.40
180
250
0.55+0.30
0.35
1.10
0.35
0.40
0.45
250
315
0.65+0.35
0.40
1.25
0.45
0.55
0.65
315
400
0.80+0.40
0.50
1.50
0.50
0.60
0.90
400
500
0.95+0.40
0.65
1.65
0.70
0.80
0.85
注:
1)圆柱滚子轴承的中膈圈和平挡圈的椭圆度按上表执行。
2)带防尘盖及止动槽的外圈,其椭圆度是上表的4/5