化学镀镍
化学镀镍(共8张PPT)

层,甚至整个化学镀镍金工艺至关重要‘61。某个工序处理不当, 通常使用酸性镀液体系,其中包括镍盐(硫酸盐、氯化物),还原剂(次磷酸钠或硼氢化物)[8],配位剂(柠檬酸、乙酸、琥珀酸、丙酸或乙醇酸),稳定剂(重金属盐、硫脲、氟化物)[9]。
(pCu>800mg/L时开新缸)
工艺控制
• 前处理工艺是用以除去铜面氧化物、油脂等污染物,粗化铜表面, 化学镀镍由还原剂提供电子进行还原反应[7],镍首先围绕Pd的活性中心沉积出来,先沉积出来的镍具有自催化作用,随时间延长,镍厚度不断增加。
并在铜面沉钯,形成镍还原的活化中心。前处理对得到均匀的镀 不需要一般电镀所需的直流电机或控制设备。
b化e学ing镀d镍ep由os还ite原d剂”。提供电子进行还原反应[7],镍首G先F围酸绕除Pd的油活剂性中心沉积5出5来~,6先5沉积m出L来的镍具有自催化作用,随时间延长,镍厚度不断增加。 /L
(1)除油工艺
浓硫酸
90~110mL /L
化学镀镍
化学镀又称为无电解镀(Electroless plating),也可以称为自催化电镀 (Autocatalytic plating)[1]。具体过程是指:在一定条件下,水溶液中的金属离 子被还原剂还原,并且沉淀到固态基体表面上的过程。ASTM B374(ASTM,美
国材料与试验协会)中定义为Autocatalytic plating is “deposition of a metallic coating by a controlled chemical reduction that is catalyzed by the metal or alloy being deposited”。这一过程与一般电镀镍不同,其镀层是可以不断增厚的[2],
化学镀镍活化

化学镀镍活化化学镀镍活化是一种用于准备金属表面以便进行电化学镀镍的过程。
它的目的是清除金属表面上的杂质、氧化物和其他不良物质,以确保镀层能够与金属表面良好地结合,并且提供优异的耐腐蚀性和机械性能。
以下是化学镀镍活化的详细步骤:1.预处理:在进行活化之前,金属表面必须进行预处理,以去除表面的油脂、污垢和其他污染物。
这可以通过碱性清洗、酸性清洗、溶剂清洗或机械处理(如研磨或喷砂)来实现。
预处理的目标是确保金属表面干净、光滑,并且没有任何残留物。
2.酸性活化:一旦金属表面被清洁,接下来就是活化步骤。
酸性活化是最常用的方法之一,通常使用酸性活化剂,例如硫酸、盐酸或氢氟酸。
这些酸性活化剂能够溶解表面的氧化物,并暴露出金属表面,从而为镀镍做好准备。
活化的时间和温度通常根据金属类型、表面条件和活化剂的类型而有所不同。
3.中性化/清洗:在进行酸性活化后,金属表面通常需要中性化以去除残留的活化剂。
中性化通常使用碱性溶液(如碳酸氢钠溶液)来中和酸性残留物。
然后,表面可能需要再次进行清洗,以确保表面干净。
4.镀镍:完成活化和清洗后,金属件被浸入镀镍溶液中进行电化学镀镍。
在镀镍过程中,金属表面被涂上一层薄薄的镍层,这种镍层能够提供优异的耐腐蚀性和机械性能。
镀镍的时间、温度和电流密度通常根据所需的镀层厚度和金属类型进行调节。
5.后处理:完成镀镍后,通常需要进行后处理步骤,以增强镀层的特性。
后处理可以包括烘干、热处理、涂覆保护剂或其他表面涂层。
这些步骤有助于提高镀层的耐腐蚀性、硬度和表面光洁度。
化学镀镍活化是一种广泛应用的表面处理技术,常用于汽车工业、机械制造和电子行业等领域,以改善金属制品的性能和外观。
化学镀镍实验报告

化学镀镍实验报告化学镀镍实验报告一、实验目的本次实验的目的是通过化学方法对金属表面进行镀镍处理,探究镀镍的原理及影响因素,并观察不同条件下的镀镍效果。
二、实验原理化学镀镍是利用电解液中的镍离子在电流作用下还原到金属表面,形成一层均匀、致密的镍层的过程。
其原理主要包括以下几个方面:1. 镀液的组成:镀液一般由镍盐、酸性物质和添加剂组成。
镍盐提供镍离子,酸性物质调节溶液的酸碱度,添加剂则用于调节镀液的性能,如增加镀液的导电性、改善镀层的质量等。
2. 镀液的电解过程:在电解槽中,阳极是镍片,阴极是需要镀镍的金属。
当外加电源施加电流后,阳极上的镍片溶解成镍离子,并在电解槽中游离。
而金属阴极表面则发生还原反应,将镍离子还原成镍金属,并在金属表面生成一层镍层。
3. 镀液的条件:镀液的温度、pH值、镀液中的镍离子浓度以及电流密度等条件都会对镀层的质量和形貌产生影响。
合适的条件能够得到均匀、致密的镀层,而不合适的条件则可能导致镀层不均匀、孔洞较多。
三、实验步骤1. 实验前准备:清洗金属试样,去除表面的油污和氧化物,保证试样表面干净。
2. 镀液的配制:按照一定比例将镍盐、酸性物质和添加剂溶解在适量的水中,搅拌均匀。
注意控制镀液的pH值和浓度。
3. 实验操作:将金属试样作为阴极,与阳极(镍片)一起放入电解槽中,保证试样与阳极的距离适当。
调节电源,使电流通过试样,开始镀镍反应。
4. 观察实验现象:实验过程中,观察金属试样表面的变化情况。
注意观察镀层的均匀性、光泽度以及有无孔洞等。
5. 实验结束:实验一定时间后,关闭电源,取出试样,用水冲洗干净,再用酒精擦拭试样表面,使其干燥。
四、实验结果与分析通过实验观察,我们可以得出以下结论:1. 镀液的浓度:镀液中镍离子的浓度越高,镀层的厚度也会增加,但过高的浓度可能会导致镀层不均匀。
因此,在实验中需要控制好镀液的浓度。
2. 镀液的pH值:镀液的pH值对镀层的质量和形貌有很大影响。
化学镀镍的基本原理
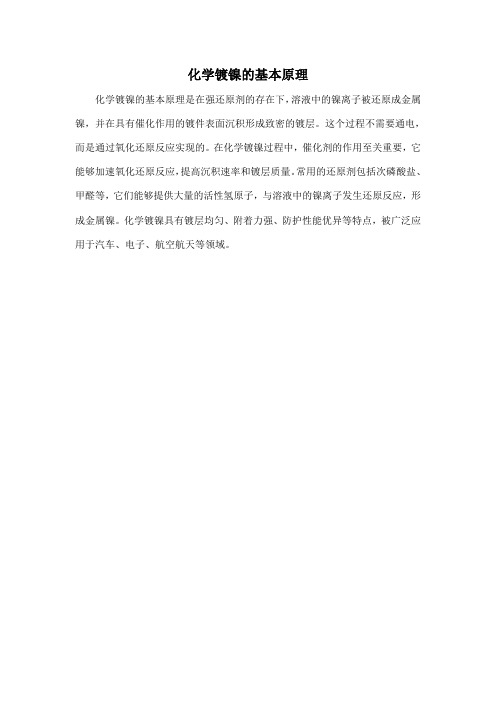
化学镀镍的基本原理
化学镀镍的基本原理是在强还原剂的存在下,溶液中的镍离子被还原成金属镍,并在具有催化作用的镀件表面沉积形成致密的镀层。
这个过程不需要通电,而是通过氧化还原反应实现的。
在化学镀镍过程中,催化剂的作用至关重要,它能够加速氧化还原反应,提高沉积速率和镀层质量。
常用的还原剂包括次磷酸盐、甲醛等,它们能够提供大量的活性氢原子,与溶液中的镍离子发生还原反应,形成金属镍。
化学镀镍具有镀层均匀、附着力强、防护性能优异等特点,被广泛应用于汽车、电子、航空航天等领域。
化学镀镍及其原理
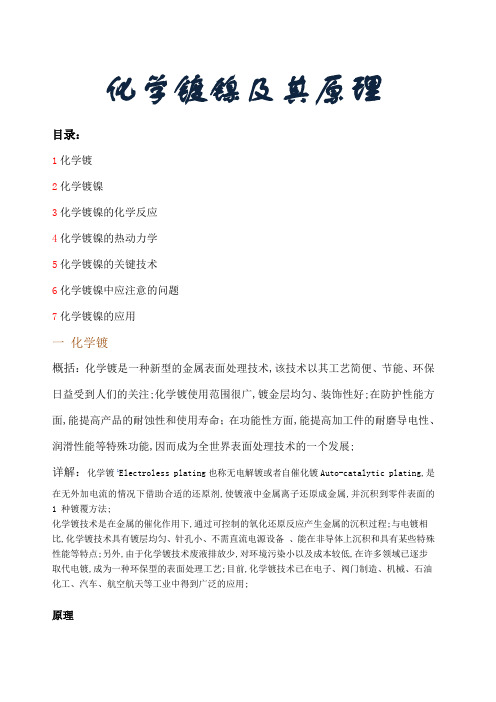
化学镀镍及其原理目录:1化学镀2化学镀镍3化学镀镍的化学反应4化学镀镍的热动力学5化学镀镍的关键技术6化学镀镍中应注意的问题7化学镀镍的应用一化学镀概括:化学镀是一种新型的金属表面处理技术,该技术以其工艺简便、节能、环保日益受到人们的关注;化学镀使用范围很广,镀金层均匀、装饰性好;在防护性能方面,能提高产品的耐蚀性和使用寿命;在功能性方面,能提高加工件的耐磨导电性、润滑性能等特殊功能,因而成为全世界表面处理技术的一个发展;详解:化学镀1Electroless plating也称无电解镀或者自催化镀Auto-catalytic plating,是在无外加电流的情况下借助合适的还原剂,使镀液中金属离子还原成金属,并沉积到零件表面的1 种镀覆方法;化学镀技术是在金属的催化作用下,通过可控制的氧化还原反应产生金属的沉积过程;与电镀相比,化学镀技术具有镀层均匀、针孔小、不需直流电源设备、能在非导体上沉积和具有某些特殊性能等特点;另外,由于化学镀技术废液排放少,对环境污染小以及成本较低,在许多领域已逐步取代电镀,成为一种环保型的表面处理工艺;目前,化学镀技术已在电子、阀门制造、机械、石油化工、汽车、航空航天等工业中得到广泛的应用;原理简称化学镀技术的原理是:化学镀是一种不需要通电,依据氧化还原反应原理,利用强还原剂在含有金属离子的溶液中,将金属离子还原成金属而沉积在各种材料表面形成致密镀层的方法;化学镀常用溶液:化学镀银、镀镍、镀铜、镀钴、镀镍磷液、镀镍磷硼液等;目前以次亚磷酸盐为还原剂的化学镀镍的自催化沉积反应,已经提出的理论有“原子氢态理论”、“氢化物理论”和“电化学理论”等;在这几种理论中,得到广泛承认的是“原子氢态理论”;二化学镀镍概念:通过电解或化学方法在金属或某些非金属上镀上一层镍的方法,称为镀镍;镀镍分电镀镍和化学镀镍;电镀镍是在由镍盐称主盐、导电盐、pH缓冲剂、润湿剂组成的电解液中,阳极用金属镍,阴极为镀件,通以直流电,在阴极镀件上沉积上一层均匀、致密的镍镀层;从加有光亮剂的镀液中获得的是亮镍,而在没有加入光亮剂的电解液中获得的是暗镍;化学镀镍是在加有金属盐和还原剂等的溶液中,通过自催化反应在材料表面上获得镀镍层的方法;化学镀镍经过多年的不断探索与研究,近几年已发展极成熟了;如Q/贻顺化学镀镍水几乎适用于所有金属表面镀镍;如:钢铁镀镍,不锈钢镀镍,铝镀镍,铜镀镍等等,它同样适用于非金属表面镀镍;比如:陶瓷镀镍,玻璃镀镍,金刚石镀镍,碳片镀镍,塑料镀镍,树脂镀镍等等;使用范围是非常广泛的;发展史的历史与相比,比较短暂,在国外其真正应用到工业仅仅是70年代末80年代初的事; 1844年,发现金属镍可以从金属镍盐的水溶液中被次盐还原而沉积出来;镍技术的真正发现并使它应用至今是在1944年,的和的发现,弄清楚了形成涂层的催化特性,发现了沉积非粉末状镍的方法,使化学技术工业应用有了可能性;但那时的化学镀镍溶液极不稳定,因此严格意义上讲没有实际价值;化学镀镍工艺的应用比实验室研究成果晚了近十年;以后,美国通用运输公司对这种工艺发生了兴趣,他们想在运输烧碱筒的内表面镀镍,而普通的方法无法实现,五年后他们研究了发展了化学镀镍磷合金的技术、公布了许多专利;1955年造成了他们的第一条试验生产线,并制成了商业性有用的化学镀镍溶液,这种化学镀镍溶液的商业名称为“Kanigen”;在国外,特别是美国、日本、化学镀镍已经成为十分成熟的高新技术,在各个工业部门得到了广泛的应用;中国的化学镀镍工业化生产起步较晚,但近几年的发展十分迅速,不仅有大量的论文发表,还举行了全国性的化学镀会议,据第五届化学镀年会发表文章的统计就已经有300多家厂家,但这一数字在当时应是极为保守的;据推测国内每年的化学镀镍市场总规模应在300亿元左右,并且以每年10%~15%的速度发展;三化学镀镍中的化学反应目前,化学镀镍镍磷合金有四种沉积机理,即原子氢理论、氢化物传输理论、电化学理论及羟基—镍离子配位理论;最为人接受的是原子氢理论: 1 化学镀镍溶液加温后,在催化作用下,次亚磷酸根脱氢形成亚磷酸根,同时析出初生态原子氢 2 初生态原子氢被吸附在催化金属表面上使其活化,使溶液中的镍阳离子还原,在催化金属表面上沉积金属镍: Ni2+ + 2H- → Ni + 2H↑ 3 催化金属表面上的初生态原子氢使次亚磷酸根还原成磷;同时,由于催化作用使次亚磷酸根分解,形成亚磷酸;原子态的氢还会合成氢气放出: H+ + H- → H2+ 其总反应为:Ni2+ + H2PO2- + H2O → HPO3 2- +3H+ + Ni 4 镍原子和磷原子共沉积,形成镍磷-合金层: Ni + P → NI-P合金固溶体或非晶态四.化学镀镍的热动力学化学镀起源于化学镀镍;化学镀镍已有 66年的历史, 但至今仍然作为一种高新技术而成为国内外的研究热点 ;化学镀镍镀液的基本成分由主盐镍盐、还原剂、络合剂、缓冲剂和稳定剂组成;化学镀反应进行的必要条件是镀液中还原剂的氧化电位必须低于氧化剂 N i2+的氧化电位, 满足这一条件的常用还原剂有次磷酸钠、肼、氨基硼烷和硼氢化钠等;络合剂是镀液中除了主盐与还原剂外的最重要的组分, 它的主要作用是在镀液中形成镍的络合物, 降低游离镍离子的浓度, 稳定镀液, 抑制氢氧化镍和亚磷酸镍沉淀的析出, 保持镀液有一定的沉积速率和较长的循环周期;络合反应能否自发地朝着目标方向进行, 对整个化学镀过程能否顺利进行起着关键性作用;因此进行络合反应的热力学研究对化学镀镍过程的理论和实践均有着重要的意义;有关化学镀镍中多元有机酸络合反应的热力学模型及其分析仅在文献 8 中报道过;但该文献存在不足的一是对不同酸根离子数 n = 1, 2, 3 的有机酸络合反应分别建立热力学模型, 而不是通式模型, 使得模型繁多和使用不便; 二是对模型进行计算时, 未考虑平衡时反应物和产物浓度对吉布斯自由能 G值和镀液pH 值当 G > 0时的影响, 使之计算误差较大; 三是未对模型中各有关参数对G 值的影响进行较为系统的理论计算和分析;针对以上不足, 本文采用热力学函数吉布斯自由能 G 为判据, 以次磷酸钠为还原剂, 取一元酸乳酸、二元酸琥珀酸、三元酸硼酸和四元酸焦磷酸 4种络合剂为例,建立了n 元酸与镍盐络合反应的热力学通式模型,并着重分析了pH 值、温度、络合率和络合剂种类对化学镀镍中络合反应热力学过程的影响;热学模型的建立在化学镀镍过程中, n 元酸性络合剂与镍盐的和H L 、热力学配位平衡中G 值不仅与化学镀镍的工艺条件如硫酸镍盐和络合剂的初始摩尔浓度 N i2+施镀温度T、n 元酸的络合率x 和镀液的pH 值有关, 而且还与络合剂的种类不同的络合剂具有不同的电离常数K 和酸根离子数 n 有关;但凡镀镍的化学反应,必定存在以下步骤:反应物向表面扩散;反就硪在催化表面上吸附;在催化表面上发生化学反应;产物从表面层脱附;产物扩散离开表面这些步骤中按化学动力学基本原理,最慢的步骤是整个沉积反应的控制步骤;五化学镀镍的关键技术1 化学镀镍液可实现再生循环利用,并可节省大量镍盐和其它成分;此外, 连续使用还可大大减少镀镍废水的排放量, 这对于提高经济效益、保护环境都有着重要的意义;2旧镀液施镀过程pH 值的降低与新镀液相比有所减少, 镀层中P 含量也有所下降;这可能是由于随着调整 pH使镀液的缓冲能力增加随着施镀次数的增加, 旧镀液镍盐的利用率在逐步提高, 镀速的增加也更快, 相应地劳动生产率也会提高, 所得镀层的外观比相同条件下新镀液的还要好一些;3镀液离子浓度;首先遇到的问题是, 镀件面积大,所需镀液容积太大;镀槽中不同位置镀液中的Ni离子浓度不均匀: 靠近镀件表面处, 因为Ni已经发生化学反应, 生成了镍磷合金镀层, 附着在设备的表面, 因而镀件周围的镀液离子浓度偏低; 而其它地方镀液离子浓度偏高,造成生产中的检测和控制困难;为此进行了一些试验;开始试验将镀件平放在镀槽底部, 换热器的管内镀液的流动是强制性的, 用封头把换热器的一头封住,与循环水泵连在一起,用循环水泵的抽吸力来带动管内镀液流动;但是结果因为镀件管内镀液流速太快, 导致形成的NiP 合金颗粒无法沉积到镀件日表面,最后镀件的两个端头没有镀好;后来发现,化学镀镍的反应过程中会产生大量的氢气, 这些气体自然会上浮到水面, 从而带动镀液发生循环流动;因此就将换热器的一端提高, 形成一定倾斜角度,反应过程中生成的气体在浮力的作一定倾斜角度,反应过程中生成的气体在浮力的作一定倾斜角度,反应过程中生成的气体在浮力的作件的面积较大,反应激烈, 因而产生的气体量巨大这样大量气泡的流动就带动了镀液的流动,使镀液换热器管内的这一端流动到了那一端,然后从换热器的管外再循环到这一端,形成了对流; 这样, 镀液的浓度就均匀了;六化学镀镍中应注意的问题化学镀镍与电镀相比,缺点是:所用的溶液稳定性较差,且溶液的维护、调整和再生都比较麻烦, 材料成本较高;但是化学镀镍得到的镀层是一种非晶态镍磷合金,结晶细致、孔隙率低、硬度高、镀层厚度均匀、可焊性好, 镀液深镀能力好, 化学稳定性高;1 镀镍液离子浓度应均匀;由于粒子浓度的差异,会导致最后被镀物两端没有镀好,因此应加强镀液的整体对流, 又采用循环水泵抽吸的办法,把镀液从镀槽的这一端抽起, 另一端流入, 方向与化学镀反应自动形成的对流循环方向一致, 加强了镀液在镀槽内的整体流动性,使镀液中的离子浓度分布更加均匀一致;2 镀镍面积问题由于镀件大, 液体多, 因此化学反应不易控制致使生产的镀件产品容易形成阴阳面, 这是指镀件和的上表面与下表面的镀层光亮程度、致密性和孔隙率不一致:上表面镀层粗糙、金属颗粒大、孔隙率高、易生锈; 下表面手感光滑, 孔隙率低、致密性良好;形成这一现象的原因有几个方面, 在后来的生产中采取多种措施进行了改进; 改进了配制镀液的用水用加热到90并经过沉淀以后的水取代自来水;由于所用的自来沉淀;如果这种颗粒在镀液中产生,伴随它的生成, 颗粒表面具有很大的表面活性和能量, 能起到高效催化作用, 使Ni 和H2PO2 在它的表面发生化学反应,生成NiP 合金小颗粒,产生沉积, 小颗粒在镀液中漂浮生长,再沉积到镀件的上表面;3 渡槽内衬材料要及时更换原来的镀槽是橡胶内衬, 在使用一段时间后会自然老化;考虑橡胶成本较高, 在试验室用镀液对847 涂料涂装件进行水煮试验, 经历36 h 的连续煮沸, 847 涂层无溶解变化;据此改用 847 涂料涂在镀槽内侧,代替橡胶内衬;但是用 847 涂料做内衬, 需要进行高温烘烤固化, 工艺复杂麻烦;于是再经过试验, 改用901 涂 .七化学镀镍的应用航空航天工业航空天工业为化学镀的使用大户之一比较突出的应用实是: 文献区价绍美国俄克荷马航空后中心 197 9, 西北空公司 1983 以来空前的发展平均净增镀厚 27 到75微米以防止燃气腐蚀,其疲劳强度的降低比电镀铬减少百分之二十五,经化学镀镍表面耐腐蚀耐磨切可焊;化学镀镍在航空航天中发挥着重要作用;汽车工业使用乙醇和汽油等混合燃料产生了燃油系统的腐蚀,应用化学镀镍技术保护锌压镀镍成为了汽化器的保护手段;汽车工业利用化学镀镍层非常均匀的特点,在形状复杂的零件上进行镀镍保护可以提供良好的抗燃油腐蚀和磨损性能;化学镀镍可有效的防止喷油器磨损,提高了可靠性和使用寿命;化学工业化学工业运用化学镀镍技术代替昂贵的耐腐蚀合金去解决问题,以便改善化学纯度以及环境提高操作安全性和生产运输可靠性,获得有利的技术经济竞争能力;石油和天然气油田采油和输油管道设备广泛的采用化学镀镍的技术,可以使抽油泵筒制成整体件,显着地提高抽油泵品质,降低了生产成本;食品加工业目前,食品包装机械中不直接与食品接触的零件为化学镀镍在食品加工中的重要应用;采矿工业某些露天采矿生产中要使用高压泵和喷射泵嘴,腐蚀和冲蚀相当严重耐蚀耐腐的化学镀镍可防止机械零件过早损坏;。
半导体化学镀镍
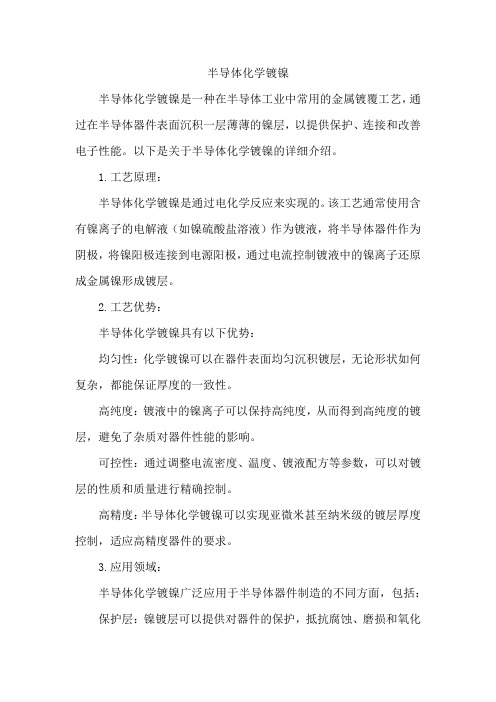
半导体化学镀镍半导体化学镀镍是一种在半导体工业中常用的金属镀覆工艺,通过在半导体器件表面沉积一层薄薄的镍层,以提供保护、连接和改善电子性能。
以下是关于半导体化学镀镍的详细介绍。
1.工艺原理:半导体化学镀镍是通过电化学反应来实现的。
该工艺通常使用含有镍离子的电解液(如镍硫酸盐溶液)作为镀液,将半导体器件作为阴极,将镍阳极连接到电源阳极,通过电流控制镀液中的镍离子还原成金属镍形成镀层。
2.工艺优势:半导体化学镀镍具有以下优势:均匀性:化学镀镍可以在器件表面均匀沉积镀层,无论形状如何复杂,都能保证厚度的一致性。
高纯度:镀液中的镍离子可以保持高纯度,从而得到高纯度的镀层,避免了杂质对器件性能的影响。
可控性:通过调整电流密度、温度、镀液配方等参数,可以对镀层的性质和质量进行精确控制。
高精度:半导体化学镀镍可以实现亚微米甚至纳米级的镀层厚度控制,适应高精度器件的要求。
3.应用领域:半导体化学镀镍广泛应用于半导体器件制造的不同方面,包括:保护层:镍镀层可以提供对器件的保护,抵抗腐蚀、磨损和氧化等因素的侵蚀,延长器件的寿命。
连接层:镍镀层可以用作电连接,提供良好的导电性和接触性能,使器件能够有效地连接到外部电路中。
金属化:半导体器件通常需要金属化来提供阻抗匹配和导电功能。
化学镀镍可以在半导体材料表面形成金属化层,提高器件的电性能。
抗反射:镍镀层具有一定的抗反射特性,可以在太阳能电池等器件中用于改善能量收集效率。
4.工艺步骤:半导体化学镀镍的主要工艺步骤包括:准备:清洁和预处理半导体器件表面,以确保良好的粘附性及镀层质量。
镀液配制:将镀液制备成适当的配方和浓度,以提供良好的镀层质量。
镀液控制:调整镀液的温度、PH值、电流密度等参数,以实现所需的镀层性质和厚度。
镀涂:将半导体器件浸入镀液中,通过电化学反应进行镀涂过程。
洗涤和处理:将镀液从器件表面洗净,并进行后续处理(如清洗、干燥等)。
检测和评估:对镀层的质量进行检测和评估,确认是否符合要求。
化学镍和电镀镍
化学镀和电镀的知识点电镀镍与化学镀镍的区别1. 化学镀镍层是极为均匀的,只要镀液能浸泡得到,溶质交换充分,镀层就会非常均匀,几乎可以达到仿形的效果。
2. 化学镀目前市场上只有纯镍磷合金的一种颜色,而电镀可以实现很多色彩。
3. 化学镀是依靠在金属表面所发生的自催化反应,化学镀与电镀从原理上的区别就是电镀需要外加的电流和阳极。
4. 化学镀过以对任何形状工件施镀,但电镀无法对一些形状复杂的工件进行全表面施镀。
5. 电镀因为有外加的电流,所以镀速要比化学镀快得我,同等厚度的镀层电镀要比化学镀提前完成。
6. 高磷的化学镀镍层为非晶态,镀层表面没有任何晶体间隙,而电镀层为典型的晶态镀层。
7. 化学镀层的结合力要普遍高于电镀层。
8. 化学镀由于大部分使用食品级的添加剂,不使用诸如氰化物等有害物质,所以化学镀比电镀要环保一些。
关于化学镀镍层的工艺特点:1. 厚度均匀性厚度均匀和均镀能力好是化学镀镍的一大特点,也是应用广泛的原因之一,化学镀镍避免了电镀层由于电流分布不均匀而带来的厚度不均匀,电镀层的厚度在整个零件,尤其是形状复杂的零件上差异很大,在零件的边角和离阳极近的部位,镀层较厚,而在内表面或离阳极远的地方镀层很薄,甚至镀不到,采用化学镀可避免电镀的这一不足。
化学镀时,只要零件表面和镀液接触,镀液中消耗的成份能及时得到补充,任何部位的镀层厚度都基本相同,即使凹槽、缝隙、盲孔也是如此。
2. 不存在氢脆的问题电镀是利用电源能将镍阳离子转换成金属镍沉积到阳极上,用化学还原的方法是使镍阳离子还原成金属镍并沉积在基体金属表面上,试验表明,镀层中氢的夹入与化学还原反应无关,而与电镀条件有很大关系,通常镀层中的含氢量随电流密度的增加而上升。
3. 很多材料和零部件的功能如耐蚀、抗高温氧化性等均是由材料和零部件的表面层体现出来,在一般情况下可以采用某些具有特殊功能的化学镀镍层取代用其他方法制备的整体实心材料,也可以用廉价的基体材料化学镀镍代替有贵重原材料制造的零部件,因此,化学镀镍的经济效益是非常大的。
化学镀镍
化学镀工艺化学镀,又称为无电解镀。
因为在工件施镀的过程中,虽说有电子转移,但无须外接电源,工件表面镀层完全是靠化学氧化还原反应实现的。
化学镀是指在无外加电流的状态下,利用一种合适的还原剂,使镀液中的金属离子还原并沉积在基体表面上的化学还原过程。
或者说,化学镀是将零件浸入到溶液中在催化剂的作用下在表面发生的金属的沉积,是一个在界面上发生的催化沉积的过程。
因此和电镀不同,化学镀过程不需要整流电源和阳极。
金属沉积仅在零件表面上进行,电子是通过溶解于溶液中的化学还原剂提供的。
完成化学镀的过程有三种方式:(1)置换沉积利用被镀金属的电位比沉积金属负,将沉积金属离子从溶液中置换在工件表面上。
其化学反应可表述为Me1+Me2n+→Me2+Me1m+溶液中金属离子被还原沉积的同时,伴随着基体金属的溶解,当基体金属表面被沉积金属完全覆盖时,反应即自动停止。
所以,采用这种方法得到的镀层非常薄。
(2)接触沉积利用电位比被镀金属高的第三金属与被镀金属接触,让被镀金属表面富积电子,从而将沉积金属还原在被镀金属表面。
其化学反应实际上与置换沉积相同,只是Me,不是基体金属,而是第三金属。
其缺点是第三金属离子会在溶液中积累。
(3)还原沉积利用还原剂被氧化时释放出的自由电子,把沉积金属还原在镀件表面;其反应过程可表述为:Me n++Re→Me+OX式中Me——沉积金属;Re——表示还原剂;0X——表示氧化剂。
一般意义上的化学镀是指这种还原沉积化学镀。
它只在具有催化作用的表面上发生。
如果沉积金属(如镍:铜等)本身就是反应的催化剂,该化学镀过程就称为自催化化学镀,它可以得到所需的镀层厚度。
如果在催化表面上沉积的金属本身不能作为反应的催化剂,一旦催化表面被沉积金属覆盖,沉积反应就会自动终止,所以只能获得有限厚度的镀层.化学镀可以在金属、半导体和非导体材料上直接进行,由于没有电流分布的问题,在复杂零件表面可以获得厚度均匀、孔隙率低、对深孔或形状复杂的零件具有很好覆盖能力的镀层。
化学镀镍概念
密度 镍的密度在 20℃时为 8.91g/cm3。含磷量 1%-4%时为 8.5 g/cm3;含磷量 7%-9%时为 8.1 g/cm3;含磷量 10%-12%时为 7.9 g/cm3。镀层密度变化的原因不完全是溶质原子质量的不同, 还与合金化时点阵参数发生变化有关。 热学性质 热膨胀系数是用来表示金属尺寸随温度的变化规律,一般是指线膨胀系数μm/m/℃。化学镀 Ni-P(8%-9%)的热膨胀系数在 0—100℃内为 13μm/m/℃。电镀镍相应值为 1算。化学镀镍的热导率比电镀镍低,在 4.396~5.652W/(m·K)
化学镀镍工艺的应用比实验室研究成果晚了近十年。第二次世界大战以后,美国通用运输 公司对这种工艺发生了兴趣,他们想在运输烧碱筒的内表面镀镍,而普通的电镀方法无法实 现,五年后他们研究了发展了化学镀镍磷合金的技术、公布了许多专利。1955 年造成了他们 的第一条试验生产线,并制成了商业性有用的化学镀镍溶液,这种化学镀镍溶液的商业名称为 “Kanigen”。
目前在国外,特别是美国、日本、德国化学镀镍已经成为十分成熟的高新技术,在各个工 业部门得到了广泛的应用。 我国的化学镀镍工业化生产起步较晚,但近几年的发展十分迅速,不仅有大量的论文发表,还 举行了全国性的化学镀会议,据第五届化学镀年会发表文章的统计就已经有 300 多家厂家,但 这一数字在当时应是极为保守的。据推测国内目前每年的化学镀镍市场总规模应在 300 亿元左 右,并且以每年 10%~15%的速度发展。
性的硼氢化钠浴及 90℃温度下,有些稳定剂往往会分解、沉淀而失效。有报道说用铊盐效果 不错。另外,硝酸铊还能增加较低温度下镀浴的沉积速度。铊盐能在 Ni—B 镀层中共沉积,有 时高达 6%的含量。 加速剂 为了增加化学镀的沉积速度,在化学镀镍溶液中还加入一些化学药品,它们有提高镀速的作用 而被称为加速剂。加速剂的作用机理被认为是还原剂次磷酸根中氧原子可以被一种外来的酸根 取代形成配位化合物,或者说加速剂的阴离子的催化作用是由于形成了杂多酸所致。在空间位 阻作用下使 H-P 键能减弱,有利于次磷酸根离子脱氢,或者说增加了次磷酸的活性。实验表 明,短链饱和脂肪酸的阴离子及至少一种无机阴离子,有取代氧促进次磷酸根脱氢而加速沉积 速度的作用。化学镀镍中许多络合剂即兼有加速剂的作用。 缓冲剂 化学镀镍过程中由于有氢离子产生,使溶液 pH 值随施镀进程而逐渐降低,为了稳定镀速及保 证镀层质量,化学镀镍体系必须具备 PH 值缓冲能力,也就是说使之在施镀过程中 pH 值不至于 变化太大,能维持在一定 pH 值范围内的正常值。某些弱酸(或碱)与其盐组成的混合物就能 抵消外来少许酸或碱以及稀释对溶液 pH 值变化的影响,使之在一个较小范围内波动,这种物 质称为缓冲剂。缓冲剂缓冲性能好坏可用 pH 值与酸浓度变化图来表示,酸浓度在一定范围内 波动而 pH 值却基本不变的体系缓冲性能好。 化学镀镍溶液中常用的一元或二元有机酸及其盐类不仅具备络合镍离子的能力,而且具有缓冲 性能。在酸性镀浴中常用的 HAC-NaAC 体系就有良好的缓冲性能,但醋酸根的络合能力却很 小,它一般不做络合剂用。 其它组份 与电镀镍一样,在化学镀镍溶液中加入少许的表面活性剂,它有助于气体的逸出、降低镀层的 孔隙率。另外,由于使用的表面活性剂兼有发泡剂作用,施镀过程中在逸出大量气体搅拌情况 下,镀液表面形成一层白色泡沫,它不仅可以保温、降低镀液的蒸发损失、减少酸味,还使许 多县浮的脏物夹在泡沫中而易于清除,以保持镀件和镀液的清洁。 表面活性剂是这样一类物质,在加入很少量时就能大幅度地降低溶剂的表面张力、界面张力, 从而改变体系状态。在固—液界面上由于固体表面上原子或分子的价键力是未饱和的,与内部 原子或分子比较能量相对较高,尤其金属表面是属于高能表面之列,它与液体接触时表面能总 是减小的。换句话说,金属的固—气界面很容易被固—液界面代替(润湿定义就是固体表面吸 附的气体为液体取代)。 化学镀镍是一种功能性镀层,一般不做装饰用,故不要求光亮。但有人将电镀镍用的光亮剂如 苯基二磺酸钠用于酸性化学镀浴中收到一定效果。蛋白质、萘磺酸、脂肪醇磺酸盐以及糖精等 据报道在醋酸缓冲镀浴中也能起到光亮作用。 某些金属离子的稳定剂还兼有光亮剂的作用,如铬离子、铊离子、铜离子,认为是与 Ni-P 形 成共沉积的原因。加入痕量铜离子因改变镀层结构而呈现镜面光亮的外观。但目前很多厂家在 化学镀的要求上都明确表示要无铬镀层,所以在光亮剂的选择上必须慎重。
化学镀镍
化学镀镍化学镀镍已成为国际上表面处理领域中发展最快的工业技术之一,以其优良的性能,在几乎所有的工业部门都得到了广泛应用,每年总产值达10亿美元,而且每年还以5%~7%的速度递增。
化学镀镍是以次磷酸盐为还原剂,经自催化电化学反应而沉积出镍磷合金镀层的新技术。
镀履过程由于是无电流通过的条件下进行的,又称无电解镀镍(Elctroless Nickelplating)简称EN技术。
它具有深镀能力强、均镀能力好、镀层致密、孔隙率低等技术特点,应用范围已扩展到工业生产的各个领域,目前是全球最优秀的表面处理之一。
一、性质和用途用次磷酸钠作还原剂获得的镀层实际上是镍磷合金。
依含磷量不同可分为低磷(1%~4%)、中磷(4%~10%)和高磷(10%~12%)。
从不同pH值的镀液中可获得不同含磷量的镀层,在弱酸性液(pH=4~5)中可获得中磷和高磷合金;从弱碱性液(pH=8~10)中可获得低磷和中磷合金。
含磷为8%以上的Ni-P合金是一种非晶态镀层。
因无晶界所以抗腐性能特别优良。
经过热处理(300~400℃)变成非晶态与晶态的混合物时硬度可高达HV=1155;化学复合镀层硬度更高,如Ni-P-SiC,镀态HV=700,350℃热处理后可达到HV=1300。
非晶态合金是开发新材料的方向,现已成为工程学科的一大热门。
近年低磷化学镀镍是研究开发的又一热点,含磷1%~4%的Ni-P合金,镀态的HV=700,热处理后接近硬铬的硬度,是替代硬铬层的理想镀层,又是可在铝上施镀的好镀种。
化学镀层的种类、性质和主要用途,列于表3-1-2。
化学镀镍层与电镀镍层的性能比较,列于表3-1-3。
表3-1-2 化学镀镍种类性质和主要用途表3-1-3 化学镀镍与电镀镍的性能比较化学镀镍的脆性较大,在钢上仅能经受2.2%的塑性变形而不出现裂纹。
在620℃下退火后,塑性变形能力可提高到6%;当热处理温度达840℃时,其塑性还可进一步改善。
化学镀镍层同钢铁、铜及其合金、镍和钴等基体金属有良好的结合力。
- 1、下载文档前请自行甄别文档内容的完整性,平台不提供额外的编辑、内容补充、找答案等附加服务。
- 2、"仅部分预览"的文档,不可在线预览部分如存在完整性等问题,可反馈申请退款(可完整预览的文档不适用该条件!)。
- 3、如文档侵犯您的权益,请联系客服反馈,我们会尽快为您处理(人工客服工作时间:9:00-18:30)。
化学镀镍張正東发表于: 2010-8-18 16:10 来源: 半导体技术天地化学镀化学镀是在无电流通过(无外界动力)时借助还原剂在同一溶液中发生氧化还原作用,从而使金属离子还原沉积在自催化表面表面上的一种镀覆方法。
化学镀与电镀的区别在于不需要外加直流电源,无外电流通过,故又称为无电解镀(Electroless Plating)或“自催化镀”(Autocatalytic Plating)。
所以化学镀可以叙述为一种用以沉积金属的、可控制的、自催化的化学还原过程,其反应通式为:上述简单反应式指出,还原剂Rn+经氧化反应失去电子,提供给金属离子还原所需的电子,还原作用仅发生在一个催化表面上。
因为化学镀的阴极反应常包括脱氢步骤,所需反应活化能高,但在具有催化活性的表面上,脱氢步骤所需活化能显著降低。
化学镀的溶液组成及其相应的工作条件也必须是使反应只限制在具有催化作用的零件表面上进行,而在溶液本体内,反应却不应自发地产生,以免溶液自然分解。
对于某一特定的化学镀过程来说,例如化学镀铜和化学镀镍时,如果沉积金属(铜或镍)本身就是反应的催化剂,那么,这个化学镀的过程是自动催化的,基本上是与时间成线性关系,相当于在恒电流密度下电镀,可以获得很厚的沉积层。
如果在催化表面上沉积的金属本身不能作为反应的催化剂,那么一旦催化表面被该金属完全覆盖后,沉积反应便终止了,因而只能取得有限的厚度。
例如化学镀银时的情形,这样的过程是属于非自动催化的。
化学镀不能与电化学的置换沉积相混淆。
后者伴随着基体金属的溶解;同时,也不能与均相的化学还原过程(如浸银)相混淆,此时沉积过程会毫无区别地发生在与溶液接触的所有物体上。
随着工业的发展和科技进步,化学镀已成为一种具有很大发展前途的工艺技术,同其他镀覆方法比较,化学镀具有如下特点:(1)可以在由金属、半导体和非导体等各种材料制成的零件上镀覆金属;(2)无论零件的几何形状如何复杂,凡能接触到溶液的地方都能获得厚度均匀的镀层,化学镀溶液的分散能力优异,不受零件外形复杂程度的限制,无明显的边缘效应,因此特别适合于复杂零件、管件内壁、盲孔件的镀覆;(3)对于自催化的化学镀来说,可以获得较大厚度的镀层,甚至可以电铸;(4)工艺设备简单,无需电源、输电系统及辅助电极,操作简便;(5)镀层致密,孔隙少;(6)化学镀必须在自催化活性的表面施镀,其结合力优于电镀层;(7)镀层往往具有特殊的化学、力学或磁性能。
某些化学镀溶液的稳定性较差,溶液维护、调整和再生等比较严格。
有实用价值的化学镀溶液的基本构成列于表7—0—1。
现在能用化学镀获得纯金属、合金及复合镀层,按其组成可分为以下各种:(1)纯金属镀层,有Cu、Sn、Ag、Au、Ru、Pd。
(2)二元合金化学镀层,主要集中于Ni和c0分别与P和B形成的二元合金,如Ni—P、Ni—B;C0—P、C0—B。
(3)三元及多元合金化学镀层,如三元合金有Ni—M—P(M=Cr、M0、W、Ru、Fe、C0、Nb、Cu、Sn、Zn、Re),Ni—M—B(M=C0、M0、W、Sn),C0—M—P(M=Ni、W、Mn);四元合金有Ni—w—Sn—P、Ni—W—Sn—B、C0—Ni—Re—P、C0—M n—Re—P。
(4)化学复合镀层,是将金属、金属化合物或非金属化合物微粒加入到化学镀液中,使之均匀地沉积到化学镀层中去的一种技术。
按加入的微粒性质可分为三大类:①金属化合物如Al2O3、Ti02、Zr02、Cr203、Ce02、TiC、WC、Cr3C2、MoS2、WS2、CaF2、BaF2;②非金属化合物如sc、B4C、BC、BN、(CF)。
、金刚石、石墨、聚四氟乙烯、碳纳米管;③金属微粒如Cr、Ni、Cu、Zr、Nb。
将这种复合镀层进行热处理时,可形成新的介稳或非晶态合金相。
化学镀溶液的基本构成化学复合镀所用微粒有微米级、亚微米级和纳米级,微米和亚微米颗粒直径在0.1μm~101μm之间,纳米颗粒直径为10nm~100n m。
微粒的化学稳定性要好,不溶于化学镀液中,而且不具备催化活性,否则镀液很快自分解。
亚微米和纳米颗粒要防止在镀液中团聚,比较有效的方法是超声波分散。
化学复合镀主要集中于Ni—P镀液,以提高其硬度、耐磨润滑等性能。
本章主要介绍化学镀镍、铜、钴、银等金属的化学镀方法。
第一章化学镀镍早在1844年A.Wurtz就发现金属镍可以从它的盐类水溶液中被次磷酸盐还原而沉积出来。
作为应用至今的化学镀镍技术,是l946年A.Brenrer和G.Riddell发现并发展了化学镀镍的实用体系。
1955年美国通用运输公司(GATC)建成了第一条化学镀镍生产线和第一个商品化镀镍溶液,商标名为“Kanigen”(Catalytic Nickel Generation)。
它是由GATC的Gutzeit博士研发的。
20世纪70年代他又研发了以硼氢化钠为还原剂的“Nibodur”工艺。
目前化学镀镍已成为表面处理领域中发展最快的新技术之一,以其优异的功能性镀层,在几乎所有的工业部门都得到了广泛应用,特别是计算机的高密度硬盘的化学镀镍等。
第一节化学镀镍的分类化学镀镍工艺到20世纪80年代有了巨大发展,其研究和应用达到了一个新的水平,工艺类型较多。
化学镀镍均形成镍的合金镀层,按合金成分分类,可分为Ni—P合金和Ni—B合金两大类工艺。
化学镀Ni—P 合金工艺,采用次磷酸及其盐类作为还原剂,除了镍离子被还原以外,次磷酸根本身也会被吸附氢原子还原为磷,因而形成Ni—P合金镀层。
Ni—B合金工艺,采用硼氢化钠NaBH4或二甲基胺基硼烷(CH3)2NH·BH3(简称DM AB)作为还原剂,因而形成Ni—B合金镀层。
化学镀镍的还原剂列于表7—1—1。
甲醛(HCHO)广泛用于化学镀铜的还原剂,但对化学镀镍的还原反应没有用。
目前,由于胺硼烷还原剂价格昂贵,因此,化学镀Ni—B合金尚未大规模工业化应用,而以次磷酸盐为还原剂的化学镀Ni—P合金为主,工艺稳定成熟。
化学镀Ni—P合金镀层中磷的含量范围约0.5%~l4%(质量),化学镀Ni按溶液的pH值可分酸性和碱性两大类。
碱性化学镀镍,镀层中磷含量很低,稳定性较差,主要用于非金属材料电镀前的预金属化镀层以及铝及其合金,镁及其合金电镀前的底镀层,以提高电镀层与铝、镁基体的结合力。
在铝轮毂的电镀中有较成功的应用。
化学镀镍的还原剂酸性化学镀Ni—P工艺是应用最广泛的化学镀镍工艺,按镀层中磷含量又可分为高磷、中磷和低磷三大类。
高磷工艺(HP):含磷10%(质量)以上,镀层为非磁性,随着磷含量的增加,镀层的抗蚀性能也增加。
利用镀层的非磁性,主要应用于计算机磁记录装置的硬盘,还应用于耐蚀性要求高的零部件。
中磷工艺(M P):含磷量6%~9%(质量),在工业中应用最广泛。
如汽车、电子、办公设备、精密机械等工业。
中磷含量的化学镀镍层经热处理,部分晶化,形成Ni3P弥散强化相,镀层硬度大大提高。
低磷工艺(LP):含磷量2%~5%(质量),低磷镀层有特殊的力学性能。
如镀态硬度可达Hv700,耐磨性好,韧性高,内应力低,是目前研究开发的热门。
美国的T.Bleeks,G.Shawhan发表了代替硬铬的新技术,即采用低磷含量的化学镀镍(LPEN)。
低磷的Ni—P镀层经350℃~440℃.1h热处理.其砸摩和耐磨件明显优千硬.已录第二节化学镀镍的机理(一)化学镀镍的热力学选择化学镀镍的还原剂时首先要从热力学上判断它还原Ni2+的反应能否进行。
化学镀镍是在催化活性表面上的自发氧化还原反应.该反应能否自发讲行的热力学半Jl断县反府的白由能蛮秒△F298还原反应:氧化反应:总反应:总反应的自由能变化:总反应的自由能变化△F298为负值,远小于零,所以该反应可以自发进行。
我们也可以从电池反应电势来判断该化学反应能否自发进行E为可逆电池电动势;F阴极反应(还原反应):阳极反应(总反应:总反应的电动势:△Eo为正值,表示自由能变化△F298为负值,该反应能自发进行。
这样就可以简单的判断,只要还原剂的电势Ea0比镍的电势Ec0负,化学镀镍的氧(二)化学镀镍的动力学从化学镀镍被发现以来,一直在研究其动力学过程,提出了几种沉积反应机理,如原子氢理论,电化学理论,氢化物传输理论(又称氢负离子理论)和氢氧(1)化学镀镍总是伴随氢气的析出;(2)镀层中除镍外,还有来自还原剂的P、B或(3)沉积反应只发生在有催化活性的表面:(4)随着施镀过程的进行,槽液pH(5)还原剂的利用率小于100%。
可以解释)”。
1.原子氢理论镍的沉积是由于在催化剂活性的表面上H2P02-与H2O反应释放加能量也就是在较高的温度(60℃2.氢化物理论(氢负离子理论) 这种理论认为,次亚磷酸盐的分解是由于溶液中氢离子同次亚磷酸根作用生成还原能力以次磷酸盐作还原剂的化学镀镍磷合金工艺已广泛应用,国内外已有商品镀液(如长沙军工民用产品研究所的HHll8G化学镀镍液。
美坚化工原料有限公司的无电沉积镍系列商品等),工艺稳定,价格的耐磨性能。
主要成分及作用列于表7—1—2。
组成与工艺参数(见表7—1—3)成与工艺参数(见表7—1—4)三、化学镀镍液的配制方法化学镀镍配方多,使用成分多,且有弱酸性和弱碱性两种,特别要根据选用的配方采用正确的配制方法,防止因配制不当产生镍的氢氧化物沉淀。
这里介绍配制应遵循的顺序:(1)用不锈钢、搪瓷、塑料作镀槽。
(2)用配槽总体积的1/3水量加热溶解镍盐。
(3)用另外1/3的水量溶解配位体、缓冲剂及其他化合物,然后将镍盐溶液在搅拌下倒入其中,澄清过滤。
(4)用余下1/3水量溶解次磷酸钠,过滤,在将要使用前在搅拌下倒人上述混和液中,稀释至总体积,用l:10的H2S04或1:4的氨水调pH值。
加入槽中的次磷酸盐最终约90%转化为亚磷酸盐,亚磷酸镍溶解度低,当有配位体存在,游离镍离子少时,不产生沉淀物。
当有亚磷酸镍固体沉淀物存在时,将触发溶液的自分解。
在化学镀中不可避免地会有微量的镍在槽壁和镀液中析出,容易导致自催化反应在均相中发生,需要用稳定剂加以控制。
反应中生成的氢离子将降低镀液pH值,从而降低沉积速度,所以需加pH值缓冲剂和及时调pH值。
四、镀液成分和工艺参数的影响1.镍盐为镀液的主成分一般随镍盐浓度升高沉积速度加快(见表7—1—5)。
但镍盐过高时,速度过快易失控,发生镀液自分解,同时镍盐含量还受配位体、还原剂比例的制约,通常在20g/L~35g/L范围。
表7—1—5 镍盐浓度对沉积速度的影响2.次磷酸钠(俗称次亚磷酸钠)为还原剂在化学镀镍磷合金中,几乎只使用次磷酸钠,这是因为价格便宜,容易买到。
次磷酸钠的最佳用量主要取决于镍离子的浓度。
化学镀镍在pH=4以上,次磷酸盐都能将镍离子还原,通常沉积lg镍需消耗5.4g次磷酸钠,含量高沉积速度快,但镀液稳定性差。