陶瓷材料的强韧化方法概述
陶瓷的强化与增韧

陶瓷材料的强化影响陶瓷材料强度的因素是多方面的,材料强度的本质是内部质点(原子、离子、分子)间的结合力,为了使材料实际强度提高到理论强度的数值,长期以来进行了大量研究。
从对材料的形变及断裂的分析可知,在晶体结构既定的情况下,控制强度的主要因素有三个,即弹性模量E,断裂功(断裂表面能)和裂纹尺寸。
其中E是非结构敏感的,与微观结构有关,但对单相材料,微观结构对的影响不大,唯一可以控制的是材料中的微裂纹,可以把微裂纹理解为各种缺陷的总和。
所以强化措施大多从消除缺陷和阻止其发展着手。
值得提出的有下列几个方面。
(1)微晶, 高密度与高纯度为了消除缺陷,提高晶体的完整性,细、密、匀、纯是当前陶瓷发展的一个重要方面。
近年来出现了许多微晶、高密度、高纯度陶瓷,例如用热压工艺制造的陶瓷密度接近理论值,几乎没有气孔,特别值得提出的是各种纤维材料及晶须。
(2)预加应力人为地预加应力,在材料表面造成一层压应力层,就可提高材料的抗张强度。
脆性断裂通常是在张应力作用下,自表面开始,如果在表面造成一层残余压应力层,则在材料使用过程中表面受到拉伸破坏之前首先要克服表面上的残余压应力。
(3)化学强化如果要求表面残余压应力更高,则热韧化的办法就难以做到,此时就要采用化学强化(离子交换)的办法。
这种技术是通过改变表面的化学组成,使表面的摩尔体积比内部的大。
由于表面体积胀大受到内部材料的限制,就产生一种两向状态的压应力。
4)陶瓷材料的增韧所谓增韧就是提高陶瓷材料强度及改善陶瓷的脆性,是陶瓷材料要解决的重要问题。
与金属材料相比,陶瓷材料有极高的强度,其弹性模量比金属大很多。
韧化的主要机理有应力诱导相变增韧,相变诱发微裂纹增韧,残余应力增韧等。
几种增韧机理并不互相排斥,但在不同条件下有一种或几种机理起主要作用。
相变增韧:利用多晶多相陶瓷中某些相成分在不同温度的相变,从而增韧的效果,统称为相变增韧。
例如,利用的马氏体相变来改善陶瓷材料的力学性能,是目前引人注目的研究领域。
陶瓷材料的强韧化方法概述
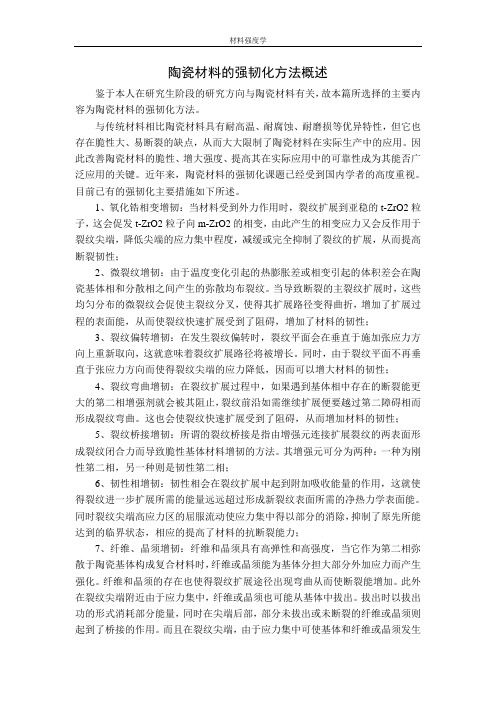
陶瓷材料的强韧化方法概述鉴于本人在研究生阶段的研究方向与陶瓷材料有关,故本篇所选择的主要内容为陶瓷材料的强韧化方法。
与传统材料相比陶瓷材料具有耐高温、耐腐蚀、耐磨损等优异特性,但它也存在脆性大、易断裂的缺点,从而大大限制了陶瓷材料在实际生产中的应用。
因此改善陶瓷材料的脆性、增大强度、提高其在实际应用中的可靠性成为其能否广泛应用的关键。
近年来,陶瓷材料的强韧化课题已经受到国内学者的高度重视。
目前已有的强韧化主要措施如下所述。
1、氧化锆相变增韧:当材料受到外力作用时,裂纹扩展到亚稳的t-ZrO2粒子,这会促发t-ZrO2粒子向m-ZrO2的相变,由此产生的相变应力又会反作用于裂纹尖端,降低尖端的应力集中程度,减缓或完全抑制了裂纹的扩展,从而提高断裂韧性;2、微裂纹增韧:由于温度变化引起的热膨胀差或相变引起的体积差会在陶瓷基体相和分散相之间产生的弥散均布裂纹。
当导致断裂的主裂纹扩展时,这些均匀分布的微裂纹会促使主裂纹分叉,使得其扩展路径变得曲折,增加了扩展过程的表面能,从而使裂纹快速扩展受到了阻碍,增加了材料的韧性;3、裂纹偏转增韧:在发生裂纹偏转时,裂纹平面会在垂直于施加张应力方向上重新取向,这就意味着裂纹扩展路径将被增长。
同时,由于裂纹平面不再垂直于张应力方向而使得裂纹尖端的应力降低,因而可以增大材料的韧性;4、裂纹弯曲增韧:在裂纹扩展过程中,如果遇到基体相中存在的断裂能更大的第二相增强剂就会被其阻止,裂纹前沿如需继续扩展便要越过第二障碍相而形成裂纹弯曲。
这也会使裂纹快速扩展受到了阻碍,从而增加材料的韧性;5、裂纹桥接增韧:所谓的裂纹桥接是指由增强元连接扩展裂纹的两表面形成裂纹闭合力而导致脆性基体材料增韧的方法。
其增强元可分为两种:一种为刚性第二相,另一种则是韧性第二相;6、韧性相增韧:韧性相会在裂纹扩展中起到附加吸收能量的作用,这就使得裂纹进一步扩展所需的能量远远超过形成新裂纹表面所需的净热力学表面能。
陶瓷材料的增韧方法

陶瓷材料的增韧方法
陶瓷材料的增韧方法可以采用以下几种途径:
1. 添加增韧剂:向陶瓷材料中添加一定比例的增韧剂,如纤维、颗粒等微观颗粒,通过增加材料的断裂面积来阻止裂纹扩展,从而提高材料的韧性。
2. 控制晶粒尺寸:通过控制陶瓷材料的晶粒尺寸,可以增加材料的韧性。
通常,晶粒尺寸越小,材料的韧性越高,因为小晶粒可以提供更多的晶界来阻碍裂纹扩展。
3. 调节成分配比:通过调节陶瓷材料中的成分配比,可以改变材料的晶格结构和传输性能,从而影响材料的韧性。
例如,添加一些特定的元素,可以形成固溶体或次微晶结构,从而提高材料的韧性。
4. 控制材料微观结构:通过控制材料的微观结构,如孔隙度、烧结密度等,可以影响陶瓷材料的韧性。
通常,降低材料的孔隙度和提高烧结密度可以增加材料的韧性。
需要注意的是,以上方法并非适用于所有陶瓷材料,具体的增韧方法需要根据具体材料的性质和应用需求进行选择和优化。
2、3讲陶瓷基复合材料的强韧化机理

2) 韧化机理
• 均匀无限大基体中存在第二相颗粒时,颗粒将 受到一个压力 2TE m p 1 m 2 1 2 p • 式中,=p-m,、E为泊松比和弹性模量; 下标m、p分别表示基体和颗粒;T为基体的塑 性变形可忽略时的温度Tp冷却到室温TR时的温 度差,=Em/Ep。 • 这一内压力在基体中距球形颗粒中心为R处产生 径向正应力及切向正应力t(图) 3 r p R
陶瓷基复合材料的力 – 位移曲线
• 而纤维增强陶瓷基复合材料不仅使其弹性模量和强度大大提高,而且还改 变了力 – 位移曲线的形状(如图)。
陶瓷的强韧化
• 脆性是陶瓷材料的致命弱点,其来源于高键能引起的缺陷敏感 性,陶瓷材料的强韧化本质上就是降低其对缺陷的敏感性。 陶瓷材料缺陷敏感性存在着显著的尺寸效应,即块体材料的尺 寸越大,缺陷数量越多。根据统计学原理,缺陷数量越多,缺 陷的概率尺寸越大。 陶瓷材料的强度和韧性具有“最弱连接”特征,即取决于缺陷 的最大尺寸而不是数量,实际上,陶瓷基复合材料的强韧化就 是利用了缺陷的尺寸效应。(掺杂改性)
2 韧化机理
• 径向微开裂容易导致微裂纹连通,对材料强度不利;
• 切向微开裂使颗粒与基体脱开,相当于形成一个颗粒尺寸大小 的孔洞,同样对材料强度不利。
• 所以在采用第二相颗粒补强增韧时,一般要求颗粒的直径小于 导致自发微开裂的临界颗粒直径dc。
√ 应力诱导微开裂增韧(dmin<d<dc)
• 当p>m,d<dc时,宏观裂纹的尖端由于外加应力的作用会出现 一个微开裂过程区,如图所示。 • 可推导出产生应力诱导微开裂时第二相颗粒的最大直径dc和最 小直径dmin。当d>dc时材料在从烧结温度冷却到室温TR时将产生 自发开裂,当d<dmin时外加应力不能在裂纹尖端诱发微开裂。
晶须增韧陶瓷基复合材料强韧化机制的评述

晶须增韧陶瓷基复合材料强韧化机制的评述
1. 晶须增韧化技术是什么?
晶须增韧化技术是一种将晶须材料引入到基础材料中的技术,通过晶须的固定和增长,改善复合材料的机械性能和韧性。
2. 什么是陶瓷基复合材料?
陶瓷基复合材料是以陶瓷为基础材料,通过添加其他强化材料来提高其性能,具有高强度、高硬度、高温耐性、耐磨损等特点。
3. 强韧化机制是如何发生的?
晶须增韧陶瓷基复合材料的强韧化机制主要是由晶须与基础材料之间的相互作用所产生的。
晶须可以在材料中分散均匀,形成纤维状结构,避免裂纹扩展,增加其韧性。
同时,晶须具有很高的强度,它与基础材料之间的化学结合可以增强材料的力学性能。
4. 晶须增韧化技术的优点是什么?
晶须增韧化技术是一种有效提高材料性能的技术,具有以下优点:
(1)提高材料韧性,增强抗裂性;
(2)增加材料强度,提高其耐久性;
(3)降低材料疲劳度,延长材料的使用寿命。
5. 晶须增韧化技术的应用领域有哪些?
晶须增韧化技术可以应用于各种复合材料的制备中,主要应用领域包括:
(1)汽车工业——制备高硬度、高温度下可靠的发动机零件、制动系统;
(2)电子工业——制备高强度、高温度下可靠的电子陶瓷;
(3)航空航天工业——制备高强度、轻质、高温度下可靠的航空材料。
6. 晶须增韧陶瓷基复合材料的未来发展趋势是什么?
晶须增韧陶瓷基复合材料的未来发展趋势主要是往以下方面发展:
(1)研制更高性能的晶须材料;
(2)探索更加有效的晶须分散方式;
(3)进一步深入研究晶须与基础材料之间的相互作用机理;
(4)将晶须增韧化技术应用于更多领域,以满足工业和社会的需要。
强韧化
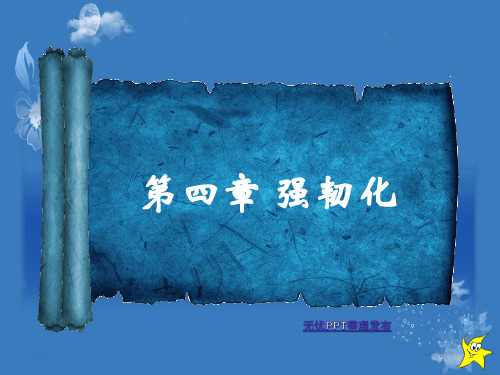
(1)偏转
现象:由于裂纹偏转,尖端应力强度因 子的变化引起表观断裂面积的增加。 起作用的条件:裂纹与强化相得作用 使内部产生不均匀应力场和裂纹尖端发生 微裂纹或界面剥离。 效果:△Kc增长1.1~3.5倍△Gc增长 1.1~4 .5倍,伴随裂纹分支时效果最大。
(2)弯曲
现象:由于强化相得存在,使基体中 的裂纹尖端弯曲且使裂纹进展的阻力增加 。 起作用的条件:需要裂纹通过之前的 强的界面结合和强化相间距与基体临界裂 纹长度的关系。 效果:△Kc增长1.1~3.5倍△Gc增长 1.1~4 .5倍,伴随裂纹分支时效果最大。在 多数场合与裂纹偏转完全分离困难。
(3)残余应力
现象:由残余压缩应力场产生的屏蔽。 起作用的条件:强化体材料与基体间热 膨胀系数最优化和强的界面粘结。 C 效果: K R 可增长(1+ △σm/σmu)倍。
2.2 非屏蔽机理
主要是利用裂纹与材料间的相互作用 而消耗的额外的能量,因此对应力强度因 子的贡献很小,主要是使断裂能量提高。 这种相互作用可以使裂纹发生两种情 况的转变,即弯曲和偏转。
(3)滑移
现象:裂纹面的摩擦使上下面的相对 位移受约束。 起作用的条件:大的摩擦系数。 C C 效果: K R , GR ,可增长1.0~2.0 倍。
2.1.2 区域屏蔽
区域屏蔽是通过强化相不直接承 受力,而是影响断裂过程中的相互作 用。
区域屏蔽也有三种形式,分别为:相变 、微裂纹、残余应力。 三种形式的特征分别为:
屏蔽机理和非屏蔽机理
2.1 屏蔽机理
定义: 在裂纹尖端施加应力,产生与原材 料不同特性的区域,从而使应力集中 缓和的机理。
主要特征:
可以使临界应力强度因子和断 裂能量同时增大。
陶瓷材料的强韧化
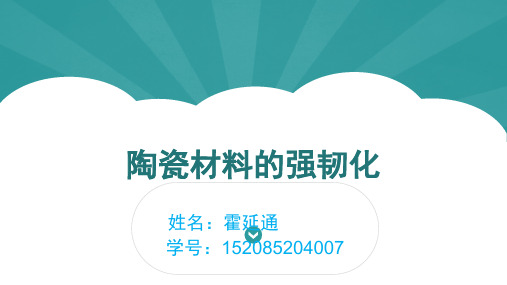
姓名:霍延通 学号:152085204007
陶瓷材料的强韧化
一、前言 二、陶瓷材料的断裂问题 三、陶瓷材料的晶须法增韧 四、陶瓷材料的相变增韧 五、陶瓷材料的纤维法增韧
陶瓷材料的强韧化
一、前言
现代陶瓷材料具有耐高温、硬度高、耐磨损、耐 腐蚀及相对密度轻等许多优良的性能。但它同时 也具有致命的弱点,即脆性,这一弱点正是目前 陶瓷材料的使用受到很大限制的主要原因。因此, 陶瓷材料的强韧化问题便成了研究的一个重点问 题。陶瓷不具备像金属那样的塑性变形能力,在 断裂过程中除了产生新的断裂表面需要吸收表面 能以外,几乎没有其它吸收能量的机制,这就是 陶瓷脆性的本质原因。
陶瓷材料的强韧化
变为单斜相,并产生体积膨胀,形成压缩表面层,从而 强化陶瓷。ZrO2增韧Al2O3陶瓷刀具是典型的相变增韧陶 瓷,美国和瑞典研制的ZrO2增韧陶瓷刀片具有相当高的 刀刃强度和耐磨性,用于加工合金钢时,粗车速度为 313m/s,精车速度为12m/s。它可以在高于硬质合金刀具 4~5倍的切削速度下加工高温合金。
陶瓷材料的强韧化
1、晶须的特性
陶瓷材料的强韧化
SiC晶须性质
陶瓷材料的强韧化
陶瓷材料的强韧化
2、SiC晶须的制备 (1)三氯硅烷法
(2)气液固法
陶瓷材料的强韧化
(3)加热SiC块 (4)稻壳 3、基质和晶须的选择考虑 (1)化学相容性 (2)弹性模量的匹配
(3)热膨胀系数的匹配
陶瓷材料的强韧化
五、陶瓷材料的纤维增韧
为了提高复合材料的韧性,必须尽可能提高材料断裂时 消耗的能量。任何固体材料在载荷作用下,吸收能量的 方式无非是两种:材料变形和形成新的表面。对于脆性 基体和纤维来说,允许的变形很小,因此变形吸收的断 裂能也很少。为了提高这类材料的吸收能,只能是增加 断裂表面,即增加裂纹的扩展路径。纤维的引入不仅提 高了陶瓷材料的韧性,更重要的是使陶瓷材料的断裂行 为发生了根本性变化,由原来的脆性断裂变成了非脆性 断裂。纤维增强陶瓷基复合材料的增韧机制包括纤维脱 粘、纤维拔出、纤维桥接、裂纹弯曲和偏转。
第二章 4陶瓷材料第二相颗粒强韧化

区的大小;m 表示微裂纹面积密度。微裂纹增韧对温度的敏感性
与应力诱导相变增韧不同,前者主要靠残余应力产生的原因。如
果由于热膨胀失配而产生微裂纹,韧性会受到温度升高而降低。
但相变产生的微裂纹,如果发生在相变可逆的温度区,温度才会 影响到增韧效果。
对含有氧化锆材料的马氏体相变诱发微裂纹,一般有三种
途径; 1)单斜相的ZrO2在较高的烧结温度下为四方相,冷却过程 中发生t-ZrO2→ m-ZrO2的马氏体相变,在颗粒周围产生微裂纹; 2)四方相ZrO2晶粒由于烧结温度过高而造成晶粒尺寸r大 于临界相变尺寸rc,冷却过程自发相变为m-ZrO2,产生微裂纹; 3)t-ZrO2在外力载荷作用下,发生应力诱导相变m-ZrO2。
3 表面强化增韧
表面强化增韧陶瓷材料的断裂往往是从表面
拉应力超过断裂应力开始的。由于ZrO2陶瓷烧结体表面 存在基体的约束较少,t-ZrO2容易转变为m-ZrO2,而内 部t-ZrO2由于受基体各方向的压力保持亚稳定状态。因 此表面的m-ZrO2比内部的多,而转变产生的体积膨胀使 材料表面产生残余的压应力,可以抵消一部分外加的拉 应力,从而造成表面强化增韧。
Y2O3
ZrO2
2YZr ‘ +3 Oo + VO • •
根据稳定程度不同,氧化锆相变增韧陶瓷有 三种类型,分别为: 部分稳定氧化锆陶瓷(partially stabilized zirconia, PSZ) 四方氧化锆多晶体陶瓷(tetragonal zirconia polycrystal,TZP) 氧化锆增韧陶瓷(Zirconia Toughened Ceramics,ZTC)
单斜m-ZrO2
1170℃
950℃
- 1、下载文档前请自行甄别文档内容的完整性,平台不提供额外的编辑、内容补充、找答案等附加服务。
- 2、"仅部分预览"的文档,不可在线预览部分如存在完整性等问题,可反馈申请退款(可完整预览的文档不适用该条件!)。
- 3、如文档侵犯您的权益,请联系客服反馈,我们会尽快为您处理(人工客服工作时间:9:00-18:30)。
陶瓷材料的强韧化方法概述
鉴于本人在研究生阶段的研究方向与陶瓷材料有关,故本篇所选择的主要内容为陶瓷材料的强韧化方法。
与传统材料相比陶瓷材料具有耐高温、耐腐蚀、耐磨损等优异特性,但它也存在脆性大、易断裂的缺点,从而大大限制了陶瓷材料在实际生产中的应用。
因此改善陶瓷材料的脆性、增大强度、提高其在实际应用中的可靠性成为其能否广泛应用的关键。
近年来,陶瓷材料的强韧化课题已经受到国内学者的高度重视。
目前已有的强韧化主要措施如下所述。
1、氧化锆相变增韧:当材料受到外力作用时,裂纹扩展到亚稳的t-ZrO2粒子,这会促发t-ZrO2粒子向m-ZrO2的相变,由此产生的相变应力又会反作用于裂纹尖端,降低尖端的应力集中程度,减缓或完全抑制了裂纹的扩展,从而提高断裂韧性;
2、微裂纹增韧:由于温度变化引起的热膨胀差或相变引起的体积差会在陶瓷基体相和分散相之间产生的弥散均布裂纹。
当导致断裂的主裂纹扩展时,这些均匀分布的微裂纹会促使主裂纹分叉,使得其扩展路径变得曲折,增加了扩展过程的表面能,从而使裂纹快速扩展受到了阻碍,增加了材料的韧性;
3、裂纹偏转增韧:在发生裂纹偏转时,裂纹平面会在垂直于施加张应力方向上重新取向,这就意味着裂纹扩展路径将被增长。
同时,由于裂纹平面不再垂直于张应力方向而使得裂纹尖端的应力降低,因而可以增大材料的韧性;
4、裂纹弯曲增韧:在裂纹扩展过程中,如果遇到基体相中存在的断裂能更大的第二相增强剂就会被其阻止,裂纹前沿如需继续扩展便要越过第二障碍相而形成裂纹弯曲。
这也会使裂纹快速扩展受到了阻碍,从而增加材料的韧性;
5、裂纹桥接增韧:所谓的裂纹桥接是指由增强元连接扩展裂纹的两表面形成裂纹闭合力而导致脆性基体材料增韧的方法。
其增强元可分为两种:一种为刚性第二相,另一种则是韧性第二相;
6、韧性相增韧:韧性相会在裂纹扩展中起到附加吸收能量的作用,这就使得裂纹进一步扩展所需的能量远远超过形成新裂纹表面所需的净热力学表面能。
同时裂纹尖端高应力区的屈服流动使应力集中得以部分的消除,抑制了原先所能达到的临界状态,相应的提高了材料的抗断裂能力;
7、纤维、晶须增韧:纤维和晶须具有高弹性和高强度,当它作为第二相弥散于陶瓷基体构成复合材料时,纤维或晶须能为基体分担大部分外加应力而产生强化。
纤维和晶须的存在也使得裂纹扩展途径出现弯曲从而使断裂能增加。
此外在裂纹尖端附近由于应力集中,纤维或晶须也可能从基体中拔出。
拔出时以拔出功的形式消耗部分能量,同时在尖端后部,部分未拔出或未断裂的纤维或晶须则起到了桥接的作用。
而且在裂纹尖端,由于应力集中可使基体和纤维或晶须发生
脱粘。
以上种种现象都能够使材料的韧性得到提高;
8、表面参与压应力增韧:由于陶瓷断裂往往始于表面裂纹,而表面残余压应力则能有效的阻止表面裂纹的扩展,因此该种方法也能起到增韧的作用。
在实际应用中,河南理工大学的张明等人从纤维(晶须)增韧的机理出发,对以SiCw为晶须增韧后的ZrO2陶瓷复合材料增韧进行了研究。
在文中作者指出SiCw/ ZrO2陶瓷复合材料的晶须增韧机理有两种,即晶须的裂纹转向机制和拔出桥连机制。
在实验观察中发现SiCw/ ZrO2陶瓷复合材料(Y2O3摩尔分数为8%)的断裂韧性随晶须含量的增加而提高,如下表所示。
表中ΔKd为裂纹偏转对于断裂韧性贡献量,而ΔKb则为晶须桥联对于断裂韧性贡献量,ΔK*和ΔK则分别为复合材料断裂韧性的理论计算值和实际测量值。
SiCw/ ZrO2陶瓷复合材料的断裂韧性表
SiCw体积分数(%)
预测值测量值ΔKdΔKbΔK*ΔK
0 3.43
10 0.795 0.62 4.64 4.26~4.58
20 1.047 1.02 5.25 4.51~5.25
30 1.192 1.38 5.77 5.64~5.92
由于材料中不可避免的会出现一定的缺陷,因此其实际测量值必然会比预测值低。
从上表中可以看出,在添加晶须后,材料断裂韧性的理论值逐步提高,而实际测量值也有显著的上升。
作者指出,虽然该实验中材料的断裂韧性受到晶须的裂纹转向和拔出桥连两种不同机制的影响,但是以上两种机制对增韧的贡献均随晶须含量而增加。
由此可见,纤维、晶须增韧是一种理想的陶瓷材料增韧方法。
附:本文参考文献:
张明,赵波,刘传绍等. SiCw/ ZrO2陶瓷复合材料晶须增韧机理与效果预测研究[J].新技术新工艺,2006,12:64-66。