成型工艺流程及条件介绍DOC
注塑成型工艺流程及工艺参数
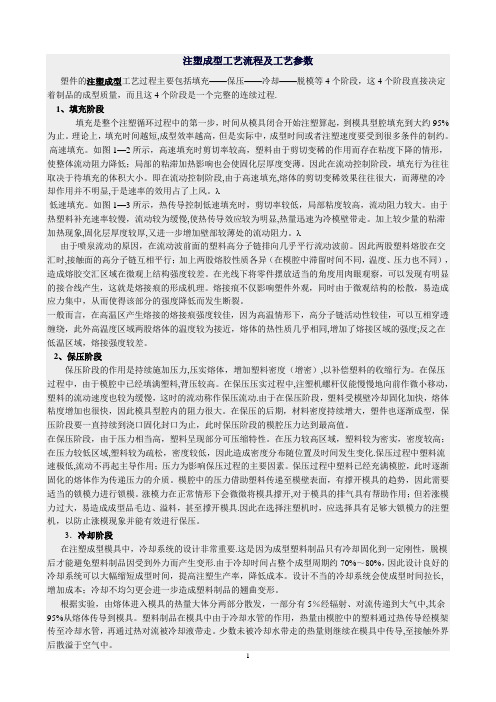
注塑成型工艺流程及工艺参数塑件的注塑成型工艺过程主要包括填充——保压——冷却——脱模等4个阶段,这4个阶段直接决定着制品的成型质量,而且这4个阶段是一个完整的连续过程.1、填充阶段填充是整个注塑循环过程中的第一步,时间从模具闭合开始注塑算起,到模具型腔填充到大约95%为止。
理论上,填充时间越短,成型效率越高,但是实际中,成型时间或者注塑速度要受到很多条件的制约。
高速填充。
如图1—2所示,高速填充时剪切率较高,塑料由于剪切变稀的作用而存在粘度下降的情形,使整体流动阻力降低;局部的粘滞加热影响也会使固化层厚度变薄。
因此在流动控制阶段,填充行为往往取决于待填充的体积大小。
即在流动控制阶段,由于高速填充,熔体的剪切变稀效果往往很大,而薄壁的冷却作用并不明显,于是速率的效用占了上风。
λ低速填充。
如图1—3所示,热传导控制低速填充时,剪切率较低,局部粘度较高,流动阻力较大。
由于热塑料补充速率较慢,流动较为缓慢,使热传导效应较为明显,热量迅速为冷模壁带走。
加上较少量的粘滞加热现象,固化层厚度较厚,又进一步增加壁部较薄处的流动阻力。
λ由于喷泉流动的原因,在流动波前面的塑料高分子链排向几乎平行流动波前。
因此两股塑料熔胶在交汇时,接触面的高分子链互相平行;加上两股熔胶性质各异(在模腔中滞留时间不同,温度、压力也不同),造成熔胶交汇区域在微观上结构强度较差。
在光线下将零件摆放适当的角度用肉眼观察,可以发现有明显的接合线产生,这就是熔接痕的形成机理。
熔接痕不仅影响塑件外观,同时由于微观结构的松散,易造成应力集中,从而使得该部分的强度降低而发生断裂。
一般而言,在高温区产生熔接的熔接痕强度较佳,因为高温情形下,高分子链活动性较佳,可以互相穿透缠绕,此外高温度区域两股熔体的温度较为接近,熔体的热性质几乎相同,增加了熔接区域的强度;反之在低温区域,熔接强度较差。
2、保压阶段保压阶段的作用是持续施加压力,压实熔体,增加塑料密度(增密),以补偿塑料的收缩行为。
材料成型工艺基础金属塑性成形

材料成型工艺基础:金属塑性成形1. 引言金属塑性成形是制造业中常见的一种材料成型工艺。
通过对金属材料施加力量,使其在一定的温度和应变条件下发生塑性变形,从而得到所需形状和尺寸的制品。
这种成形工艺广泛应用于汽车、航空航天、机械制造等领域。
本文将介绍金属塑性成形的基本概念、工艺流程以及常见的金属塑性成形方法。
2. 基本概念2.1 金属塑性成形的定义金属塑性成形是指将金属材料通过施加力量,在一定的温度和应变条件下,使其发生塑性变形,从而得到所需形状和尺寸的工艺过程。
2.2 塑性变形的基本概念塑性变形是指材料在一定的应力作用下,在超过其屈服点之后发生的可逆性变形。
在这种变形中,金属材料的原子结构会发生改变,从而改变了材料的形状和尺寸。
3. 工艺流程金属塑性成形的工艺流程主要包括以下几个步骤:3.1 原材料准备在金属塑性成形工艺中,首先需要准备好所需的金属原材料。
原材料的选择需要满足产品的要求,包括材料的强度、韧性、耐蚀性等。
3.2 材料加热在金属塑性成形之前,通常需要将金属材料进行加热。
加热可以使金属材料达到一定的塑性状态,更容易发生塑性变形。
加热的温度和时间需要根据不同的金属材料和成形要求进行调整。
3.3 成型工艺金属塑性成形的成型工艺包括以下几种常见方法:3.3.1 锻造锻造是一种利用压力将金属材料塑性变形成形的方法。
在锻造过程中,金属材料会经过压缩、拉伸、冷却等多个步骤,最终得到所需的形状。
3.3.2 拉伸拉伸是将金属材料放在拉伸机上,通过施加力量使其发生塑性变形的方法。
通过拉伸可以改变金属材料的形状和尺寸。
3.3.3 深冲深冲是将金属材料放在冲压机上,通过模具对材料进行冲压,使其发生塑性变形的方法。
通过调整模具的形状和尺寸,可以得到不同形状和尺寸的制品。
3.4 后处理在金属塑性成形完成之后,通常需要进行一些后处理工艺。
包括去除表面的氧化物、清洗、退火等。
后处理的目的是提高产品的表面质量和性能。
4. 常见的金属塑性成形方法4.1 冷镦成形冷镦成形是一种将金属材料通过冷镦机进行挤压、拉伸、弯曲等操作,使其发生塑性变形的方法。
注塑工艺

注塑成型工艺优质的塑料产品来自上好的原料、精密的模具和先进的成形设备,注塑模具又处于核心的地位一、注塑成型(injection molding)二、注塑成型机1、合模装置——开闭模具以执行脱模作业2、注塑装置将树脂预加热融化后,再射入模具内,此时要旋转螺杆并如图所示,染投入到料斗的树脂停留在螺杆前端(计量),经过相当于所需树脂的行程储藏后再进行射出。
当树脂在模具内流动时,则控制螺杆的移动速度(射出速度),并在填充树脂用压力(射出压力)进行控制,当达到一定的螺杆位置或射出压力时则从速度控制切换成压力控制。
三、注塑模具1.模具的分类(1)按塑料材料类别分a:热塑性注塑模b:热固性注塑模(2)按模具型腔分a:单型腔注塑模b:多型腔注塑模(3)按注塑机类型分a:卧式注塑机用注塑模b:立式注塑机用注塑模(4)按模具浇注系统分a:冷流道模b:绝热流道模c:热流道模d:温流道模2.注塑模具的组成部分(1)成型零部件赋予成型材料形状及尺寸的零件。
通常由型芯、凹模或型腔、以及螺纹型芯或型环、镶块等组成(2)浇注系统将熔融塑料由注射机喷嘴引向闭合的模腔。
通常由主流道、分流道、浇口和冷料井组成。
(3)导向部分为了保证动模与定模闭合时能准确对准而设置的导向部件。
通常导向部件由导柱和導套组成。
有的模具还在推板上设置导向部件上设置导向部件,保证脱模机构的运动灵活平稳。
(4)脱模机构实现塑件脱模的装置。
其结构形式常用的有推杆(顶针)、推管、推板、侧抽芯和斜顶等脱模机构。
(5)调温系统为了满足注塑成型工艺对模具温度的要求,需要有调温系统对模具温度进行调节的设施。
(6)排气系统为了将模具型腔内的气体顺利排出,常在模具分型面处开设排气槽。
排气槽的形式有:利用顶针进行排气、利用分型面、开设专用的排气槽、模具结构做成镶件形式进行排气。
(7)其它零部件支撑、固定零件、定位、限位等2. 浇注系统定义:模具中从注塑机喷嘴起到型腔入口为止的塑料融体的流道通道,或在此通道内冷凝的固体塑料。
塑料模具的设计与成型工艺

塑料模具的设计与成型工艺摘要:塑料成形是一种以人工合成金属树脂材料为基本合成原材料,加入其他一定量化学添加剂,在一定的工作压力、温度下,制成一定形状,并在室温下长久保持形状不变的材料。
塑料是20世纪末期发展壮大起来的一类工业新型材料,包装材料工业、日常用品制造工业,机械工业,医疗器械等工业领域。
医疗器械等领域。
塑料模具产品设计的基本技术要求之一是企业能不断生产研制出能在尺寸,精度,外观及热物理及流体力学性能等各方面条件均能充分满足实际使用性能要求的优质材料塑件。
在进行模具生产使用时,应该要力求模具生产过程效率高,自动化管理程度高,操作方便,寿命长;在应用模具结构制造工艺方面,要求模具结构设计合理,制造容易,成本低。
引言:20世纪70年代以来,石油危机持续爆发虽然使得目前我国大型塑料制品加工制造产业的主要产品原料价格上涨,其宏观经济发展趋势仍然受到很多较大一定程度的宏观经济因素抑制和被经济抑制。
所以,改善塑料的性能、推广和使用先进的模具设计制造技术,研究塑料快速成型技术显得尤为重要。
塑料模具是使塑件成型的主要工具,它可使塑件获得一定的结构形状及所需性能。
其发展受到很大程度的抑制抑制。
所以,改善塑料的性能、推广和使用先进的模具设计制造技术,研究塑料快速成型技术显得尤为重要。
塑料模具是使塑件成型的主要工具,它可使塑件获得一定的结构形状及所需性能。
用特殊模具工艺生产制造出来的的新型塑件产品具有高工艺复杂程度,高质量一致性,高操作精度、高生产率以及低材料消耗率等几大特点。
一、塑料模具简介塑料产品是用各种零件作为材料后再进行加工再成型而得以获得的一种产品。
而腔体模具就是一种利用其本身特定的腔体密闭性和腔体部件去加工成型,从而可以做成一种具有一定整体形状和大小尺寸的大型塑料金属制件的一种工具。
1、用新型机械塑料模具自动加工塑料生产工艺制造加工出来的的新型柔性塑件塑料制品。
它具有高度易操作和低精度、高性能和低一致性、高生产率和低使用材料资源消耗率等几个新的显著特点。
注塑成型工艺流程及工艺参数详解
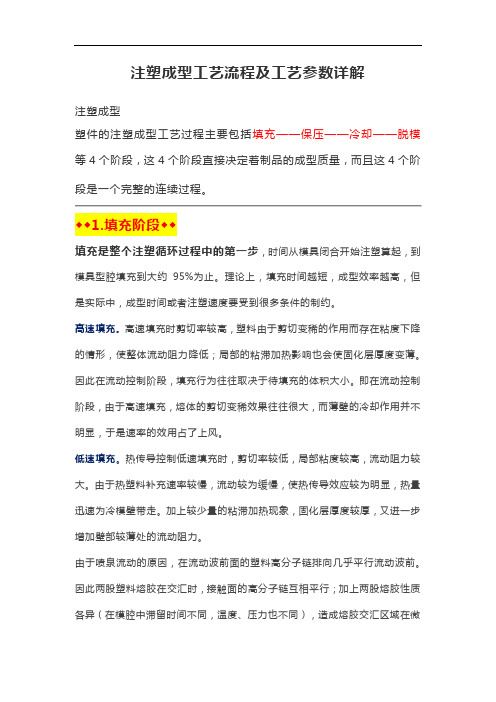
注塑成型工艺流程及工艺参数详解注塑成型塑件的注塑成型工艺过程主要包括填充——保压——冷却——脱模等4个阶段,这4个阶段直接决定着制品的成型质量,而且这4个阶段是一个完整的连续过程。
◆◆1.填充阶段◆◆填充是整个注塑循环过程中的第一步,时间从模具闭合开始注塑算起,到模具型腔填充到大约95%为止。
理论上,填充时间越短,成型效率越高,但是实际中,成型时间或者注塑速度要受到很多条件的制约。
高速填充。
高速填充时剪切率较高,塑料由于剪切变稀的作用而存在粘度下降的情形,使整体流动阻力降低;局部的粘滞加热影响也会使固化层厚度变薄。
因此在流动控制阶段,填充行为往往取决于待填充的体积大小。
即在流动控制阶段,由于高速填充,熔体的剪切变稀效果往往很大,而薄壁的冷却作用并不明显,于是速率的效用占了上风。
低速填充。
热传导控制低速填充时,剪切率较低,局部粘度较高,流动阻力较大。
由于热塑料补充速率较慢,流动较为缓慢,使热传导效应较为明显,热量迅速为冷模壁带走。
加上较少量的粘滞加热现象,固化层厚度较厚,又进一步增加壁部较薄处的流动阻力。
由于喷泉流动的原因,在流动波前面的塑料高分子链排向几乎平行流动波前。
因此两股塑料熔胶在交汇时,接触面的高分子链互相平行;加上两股熔胶性质各异(在模腔中滞留时间不同,温度、压力也不同),造成熔胶交汇区域在微观上结构强度较差。
在光线下将零件摆放适当的角度用肉眼观察,可以发现有明显的接合线产生,这就是熔接痕的形成机理。
熔接痕不仅影响塑件外观,同时由于微观结构的松散,易造成应力集中,从而使得该部分的强度降低而发生断裂。
一般而言,在高温区产生熔接的熔接痕强度较佳,因为高温情形下,高分子链活动性较佳,可以互相穿透缠绕,此外高温度区域两股熔体的温度较为接近,熔体的热性质几乎相同,增加了熔接区域的强度;反之在低温区域,熔接强度较差。
◆◆2.保压阶段◆◆保压阶段的作用是持续施加压力,压实熔体,增加塑料密度(增密),以补偿塑料的收缩行为。
层压成型工艺

夹放在叠合体两面,使板材受压、传 热均匀;并起到传热、冷却的缓冲作 叠合体顺序: 用,防止局部过热或过冷现象。 若厚板料放在叠合体两侧,薄板 料放在中间。因两侧板材较厚,而 铁板(较厚)→衬纸→单面钢板→板料→双面钢板→板 玻璃钢本身的导热系数又低,传热 料→······→双面钢板→板料→单面钢板→衬纸→铁板 冷却的效果不好,内部热量不易散 出,沿板面的垂直方向具有较大的 温差,故最终产品易产生内应力, 造成厚板的翅曲。
1)对多层层压板的每块板料,两表面各放2~3张面层 胶布(面层胶布的含胶量及流动性比里层稍高,能增 加制品的防潮性和美观,并掺有内脱模剂);
2)胶布的挥发分含量不宜过大,控制在1~6%, 否则 应干燥处理; 胶布中可挥发的物质占胶布
总量的百分比 挥发分含量过高,高温成型时容易产生气泡,且挥发分过多易残留在制 品中,对制品的电性能不利。挥发分含量太低,增加干燥时间,使浸胶机生 产效率降低,同时也易使胶布流动量过小,影响压制工艺。
立式上胶机:
进出口段30~60℃,中部 60~80℃,顶部第三段 85~130℃。 玻璃布上下来回一次, 由较低温度区进口,经过 最高温度区,由较低温度 区出口。
b、干燥时间的控制
干燥时间取决于若干因素, t=f(T, w, A, B·· ·) · T—温度; w—风速; A—树脂状况; B—布状况
胶布的干燥有两个阶段
第一阶段
表面气化阶段,表面气化速度决定干燥 速度,随周围介质浓度增加而减小;
第二阶段 内部扩散阶段,内部扩散速度大小决定 了胶布干燥速度的快慢。物料层厚度、结构 对干燥速度有很大影响。
a、烘箱温度的控制 卧式上胶机: 进 口 段 90 ~ 110℃ , 中 部 烘 干 段 120 ~ 150℃,出口段100℃以下。
注塑生产工艺(3篇)

第1篇一、引言注塑成型是一种将热塑性塑料或热固性塑料等材料,通过注塑机在高温、高压条件下注入模具腔内,冷却固化后获得所需形状和尺寸的塑料制品的生产工艺。
注塑成型广泛应用于汽车、家电、电子、医疗、包装等领域,具有生产效率高、产品精度高、成本低等优点。
本文将详细介绍注塑生产工艺的流程、设备、材料及质量控制等方面。
二、注塑生产工艺流程1. 塑料原料准备(1)原料选择:根据产品性能要求,选择合适的塑料原料。
常见的塑料原料有聚乙烯(PE)、聚丙烯(PP)、聚氯乙烯(PVC)、聚苯乙烯(PS)、ABS等。
(2)原料检验:对原料进行外观、粒度、水分、熔融指数等指标的检验,确保原料质量。
(3)原料干燥:将原料进行干燥处理,去除水分,防止注塑过程中产生气泡、变色等问题。
2. 注塑成型(1)预热模具:将模具预热至规定温度,确保模具温度均匀。
(2)加料:将干燥后的原料加入注塑机料斗,通过料斗输送至料筒。
(3)熔融:在注塑机料筒内,通过加热和搅拌使原料熔融。
(4)注塑:将熔融的塑料通过注塑机喷嘴注入模具腔内,填充模具。
(5)保压:在注塑过程中,保持一定的压力,使塑料在模具内充分填充。
(6)冷却:在模具内,通过冷却水或冷却介质使塑料冷却固化。
(7)脱模:待塑料完全固化后,打开模具,取出产品。
3. 后处理(1)产品检验:对注塑产品进行外观、尺寸、性能等方面的检验,确保产品合格。
(2)产品清洗:对产品进行清洗,去除表面油污、杂质等。
(3)产品包装:将合格的产品进行包装,便于储存和运输。
三、注塑设备1. 注塑机:注塑机是注塑成型工艺的核心设备,主要分为立式和卧式两种。
根据产品尺寸、注塑量、塑料类型等因素选择合适的注塑机。
2. 模具:模具是注塑成型工艺的关键,其设计、制造质量直接影响产品质量。
模具应具有足够的强度、刚度和耐磨性。
3. 辅助设备:包括干燥机、冷却水系统、输送带、检验设备等。
四、注塑材料1. 塑料原料:选择合适的塑料原料,确保产品性能满足要求。
塑料浇铸成型方法
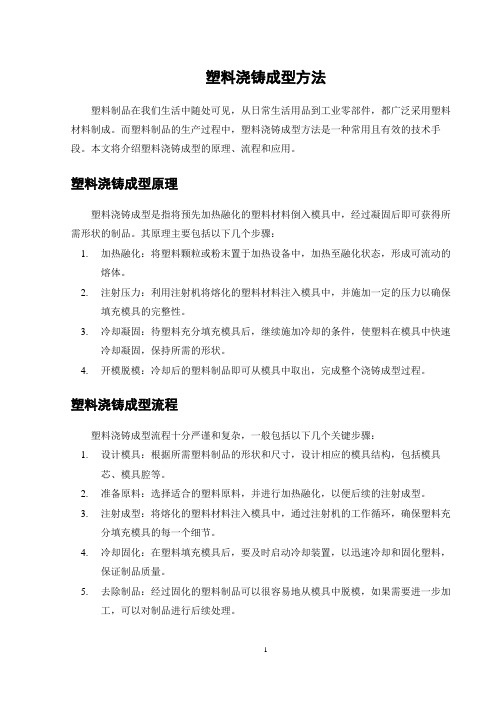
塑料浇铸成型方法塑料制品在我们生活中随处可见,从日常生活用品到工业零部件,都广泛采用塑料材料制成。
而塑料制品的生产过程中,塑料浇铸成型方法是一种常用且有效的技术手段。
本文将介绍塑料浇铸成型的原理、流程和应用。
塑料浇铸成型原理塑料浇铸成型是指将预先加热融化的塑料材料倒入模具中,经过凝固后即可获得所需形状的制品。
其原理主要包括以下几个步骤:1.加热融化:将塑料颗粒或粉末置于加热设备中,加热至融化状态,形成可流动的熔体。
2.注射压力:利用注射机将熔化的塑料材料注入模具中,并施加一定的压力以确保填充模具的完整性。
3.冷却凝固:待塑料充分填充模具后,继续施加冷却的条件,使塑料在模具中快速冷却凝固,保持所需的形状。
4.开模脱模:冷却后的塑料制品即可从模具中取出,完成整个浇铸成型过程。
塑料浇铸成型流程塑料浇铸成型流程十分严谨和复杂,一般包括以下几个关键步骤:1.设计模具:根据所需塑料制品的形状和尺寸,设计相应的模具结构,包括模具芯、模具腔等。
2.准备原料:选择适合的塑料原料,并进行加热融化,以便后续的注射成型。
3.注射成型:将熔化的塑料材料注入模具中,通过注射机的工作循环,确保塑料充分填充模具的每一个细节。
4.冷却固化:在塑料填充模具后,要及时启动冷却装置,以迅速冷却和固化塑料,保证制品质量。
5.去除制品:经过固化的塑料制品可以很容易地从模具中脱模,如果需要进一步加工,可以对制品进行后续处理。
塑料浇铸成型应用塑料浇铸成型方法在各行各业都有着广泛的应用,主要体现在以下几个方面:1.工业制造:塑料浇铸成型方法可用于制造各种工业零部件、外壳和结构件,广泛应用于汽车、电子产品、家电等行业。
2.日用品制造:许多日常生活用品,如杯子、餐具、玩具等,也多采用塑料浇铸成型方法进行生产。
3.医疗器械:医疗器械中许多塑料制品,如医用注射器、输液瓶等,也是通过浇铸成型技术生产的。
4.建筑材料:一些塑料建筑材料,如塑料管道、阀门等,也可以通过浇铸成型方法来加工制造。
- 1、下载文档前请自行甄别文档内容的完整性,平台不提供额外的编辑、内容补充、找答案等附加服务。
- 2、"仅部分预览"的文档,不可在线预览部分如存在完整性等问题,可反馈申请退款(可完整预览的文档不适用该条件!)。
- 3、如文档侵犯您的权益,请联系客服反馈,我们会尽快为您处理(人工客服工作时间:9:00-18:30)。
成型工艺流程及条件成型常见产品缺陷一.成型工艺流程及条件介绍第一節成型工艺1.成型工艺参数类型(1). 注塑参数a.注射量b.计量行程c.余料量d.防诞量e.螺杆转速f.塑化量g.预塑背压h.注射压力和保压压力i.注射速度(2) 合模参数a.合模力b.合模速度c.合模行程.d.开模力e.开模速度f.开模行程g.顶出压力h.顶出速度i.顶出行程2.温控参数a.烘料温度b.料向与喷嘴温度c.模具温度d.油温3.成型周期a.循环周期b.冷却时间c.注射时间d.保压时间e.塑化时间f.顶出及停留时间g.低压保护时间成型工艺参数的设定须根据产品的不同设置.第二节成型条件设定按成型步骤:可分为开锁模,加热,射出,顶出四个过程.开锁模条件:快速段中速度低压高压速度锁模条件设定:1锁模一般分:快速一中速一低压一高压2.快锁模一般按模具情况分, 如果是平面二板模具,快速锁模段可用较快速度,甚至于用到特快, 当用到一般快速时, 速度设到55-75%,完全平面模可设定到80-90%,如果用到特快就只能设定在45-55%,压力则可设定于50-75%,位置段视产品的深浅(或长短)不同,一般是开模宽度的1/3.3.中速段,在快速段结束后即转换成中速,中速的位置一般是到模板(包括三板模, 二板模) 合在一块为止, 具体长度应视模板板间隔, 速度一般设置在30%-50%间, 压力则是20%-45%间.4.低压设定, 低速设定一般是在模板接触的一瞬间,具体位置就设在机台显示屏显示的一瞬间的数字为准, 这个数字一般是以这点为标准,, 即于此点则起不了高压,高于此点则大,轻易起高压.设定的速度一般是15%-25%视, 乎不同机种而定, 压力一般设定于1-2%,有些机则可设于5-15%,也是视乎不同机种不同.5.高压设定, 按一般机台而言,高压位置机台在出厂时都已作了设定, 相对来讲, 是不可以随便更改的,比如震雄机在50P.速度相对低压略高,大约在30-35%左右, 而压力则视乎模具而定, 可在55-85%中取, 比如完全平面之新模, 模具排气良好, 甚至于设在55%即可, 如果是滑块较多, 原来生产时毛边也较多, 甚至于可设在90%还略显不足.加热工艺条件设定1.加热段温度设定必须按照产品所使用的原料的不同而不同, 但却必须遵循一个这样的规则, 即由射口筒到进科段温度是逐步递减的.且递减温度是以10.度为单位.2 特殊情况下. 如料头抽丝, 则射口筒温度应降低, 如果是比较特殊的原料冷凝比较快的. 则射口筒温度则不止比第二节法兰温度高10度.比如PPS.尼龙等.3. 机台马达启动温度视乎机台不同而不同, 一般出于对机台油路中的油封保护需要, 油温最好能控制在40 度-60 度, 以免油封长期高压而变化, 缩短使用寿命, 造成成型不稳定.第三节注射及熔胶(加料) 工艺条件设定一. 注射第四节常见塑料原料的有关温度值.原料Resin 名称Name熔点°CMelt ' s成型温度CMolding Temperature( ' c)分解温度CDecompos ing Temperature( ‘ C)模具温度CMold Temperature( ‘ c)干燥温度°C注射是把塑料原料经加热后射进模腔的过程, 它一般可分为第一级,第二级, 第三级, 第四级及保压几段:1.第一级注射一般是注射料头段.具注射量一般可根据料头的轻重来估计其行程当然也可以依据公式来计算, 如公式:L=Si=Vi/0.785Ds2L:注射行程;Si:注射行程;L: injection stroke Si: injection strokeVi: 理论注射容积; Ds: 螺杆直径;Vi: injection volume of theoretical Ds: diameter of screw0.785:是Q /4 的值.0. 785: value of Q /4.当然, 如果我们在成型时每设定一个参数都要计算一次,要成型出一个产品就要几个小时才能完成了.2.第二级是注塑产品约2/3 的阶段, 当然, 根据产品特殊需要,也允许成型不到2/3 阶段, 比如避免结合线问题,这一阶段的成型速度及压力一般是整个成型段的最大值段,如果排的产品与机台基本是相吻合的.模具结构合理,排气良好,这一段的压力一般也不会超过80%.速度侧视产品需变, 可能大到95%也可, 自然一般都是在55%-80%间.3.第三段是注射余下的1/3 段, 其速度和压力根据产品的需要, 一般是小于第二段,速度和压力存在于一个往下降的过程. 主要是为了防止产品毛边的产生, 但同时又必须把产品充填饱满.4.第四段:一般有机台还有第五,第六段,这段的成型速度和压力相同前,都存在两段一个递减过程. 其作用都是起到一个再次充满的作用.5.保压段:不论成型什么产品,都存在一个保压过程.任何产品都不同程度的存在一个厚薄不一的问题, 正常情况下, 较厚的部分都可能存在一个收缩凹陷的现象, 为了解决这种现象,就应应用到保压, 保压一般来讲都应用较慢的射速,而压力的设置则应看缩水的情况如何,小到25%,大到80%都有可能.二. 熔胶段工艺1.再复杂的熔胶旋转过程最多不会超过三段, 因为熔胶本身就是存在于把胶熔进料筒的过程, 如果原料粘度大,熔胶压力则大, 但速度则应取决于原料的分解温度熔胶速度越快, 原料中的剪切力则会越大, 料管温度则越高, 局部原料产生分解的可能性则会越大,故一般熔胶会采用中速为宜, 如45%-75%熔, 胶同时会碰到一个比较重要的环节,那就是背压的使用,产品精度要求越大,背压的使用则更大, 背压可使原料分子间结构更紧密,成型出的产品则尺寸更稳定,外观越好.当然,背压太大,则会产生流涎,所以背压的使用又应考虙到其它原因.2.熔胶过程还有一个比较重要的环节,那就是松退,松退分前松退和后松退,其作用一般是为了防止流涎和抽丝, 设定值速度和压力都在20%-50%间, 设定的行程一般在2-5cm间,太长的行程可能会使料筒里面贮存空气,导致下一模出现不期望的气泡.顶出的工艺设定产品经冷却定型后则有一个开模的过程,开模基本上是合模的反过程.开模的未段则有一个慢速设置, 开模完成后, 产品必须顶出的过程.一. 顶前:顶前最好分两个阶级, 第一阶可分为中压慢速, 即是把产品轻轻顶出一部分, 然后是中压中速顶, 中压中速一般指的是35%-55%而, 低速则有可能低到5%,这需视产品不同而言,顶出行程设定是顶出长度稍比产品垂直深度大1-2cm即可.二. 退针Back顶退包括两个过程与顶落的过程基本一致,顶退的终点应预留1-3cm的空间,以保护顶针油管不被顶坏.三. 顶针方式还包括一个多次顶,单次顶及顶针停留的选择,机械手取产品,脱模顺利的情况都采取多项, 为了顶针油缸寿命的延长, 多次顶就以不超过三次为宜, 顶针停留一般用在顶针带着产品退回有可能对增品产生损伤的模具, 同时为配合机械手使用, 有时也需要较短的顶针停留.成型时间的设定在保证产品质量的前提下,周期时间是越短越好,周期时间又包括如下几项:射胶时间,保压时间,熔胶时间,冷却时间,顶出时间,锁模低压时间,甚至乎关系到时间因素的还有还开模与锁模, 及顶出的快慢.1.射胶时间包含保压时间,一般看起来,射胶时间越长,产品越饱和,但我们在讲求质量时,同时也须考虑产能,更何况,射胶时间过长,有可能会造成产品过于饱满而寻致粘模顶的变形呎寸偏大等一系列问题, 故我们在设置射胶时间时应综合考虑, 尽量在合乎质量要求时缩短射胶时间.熔胶时间的长短取决于熔胶速度设定的快慢, 背压设定的大小, 但有一点, 熔胶时间控制的长短一定要比冷却时间短.3.冷却时间:冷却时间的长短直接影响到成型的周期,冷却时间越长, 成型时间就越长,造成产能就越低, 故我们在设定高压冷却时间时, 只要能保证到产品成型顺利不会直接影响到变形等问题, 设定的时间也是越短越好4.在大量使用机械手的塑胶公司, 我们的顶出时间一般是与机械手配合为宜,全自动使用机械手时顶出停留时间一般保持1.5-2 秒,半自动生产,如因顶针退回会导致产品掉落或卡紧,而取不下产品,停留时间则应保持5秒左右.5.低压保护时间对保护我们人身安全, 模具安全起很大作用, 配合好模具低压位置和低压压力的调整,低压保护的时间应取1-3 秒,保护时间越短,可能造成的危害则越小.二.成型常见产品缺陷一、白斑:物料没有被完全干燥,有水份对策:需物料排气性好,故成型条件改变,射胶周期放慢。
二、充填不足:(不饱模)1、定义:冲填不足(SHOTSHOR)T 是熔融塑料未完全流遍成型空间(模穴)的各个角落之现象。
2、原因及对策:A、原因:成型品与射出机匹配不当,可塑化能力或射出量不足。
对策:更换机台B原因:喷嘴射出品径太小,冷料阻塞。
对策:加大喷嘴射出口尺寸,以3.5OZ(80-90TONS射出喷嘴口径应为2-2.2m/mC原因:流道设计不良时,塑料流动阻力大。
对策:修改流道尺寸以符合实际需要。
D原因:塑料熔化不均匀,造成射出压力降遇所致。
对策:适当调整背压与螺杆转速,使塑料混合均匀。
E、原因:流道中冷料井预留不足或不当,冷料头进入成型品而阴碍塑料之正常流动充满模穴。
对策:增加冷料井储存空间或打多段射出,移开冷料头使塑料充填顺畅。
F、原因:模具温度太冷,塑料在某一特定压力下流动困难上实际需要,对策:斟酌生产提高模具温度。
G原因:模具排气不良时,空气无法排除。
对策:防火级ABS成型时,挥发性气体残渣,易造成模垢而发生排气口堵塞现象,应定期清除之。
、毛边:(批锋)1、原因与对策A、原因:模具的锁模力不足,塑料高压射入模具内时会在分模面发生间隙,塑料料由此流出。
对策:调整锁模力,提高锁模吨数,如已调至最大则换机台(更大型)B、原因:模具未充分接触喷嘴,模具发生间隙时。
对策:调整足射座顶力。
C、原因:模具导锁磨损,分模面偏移或模具安装板受损,导杆(大柱)强度不足发生弯曲时。
对策:1、更换模具销;2、模具安装板整修;3、模具重量超重应更换较大机台成型。
D原因:异物附着模面时。
对策:清除模面异物E、原因:成型品投影面过大或树脂温度太高。
对策:更换较大机台,降低塑料温度。
四、收缩下陷:1、定义:成型品表面产生凹陷的现象, 这是体绩收缩所致,通常见于肉厚部分, 肋或凸出的背面,直接浇口肉厚不均的部分。
2、凹陷与真空泡同时发生之状况:成型品的中心部位,肉较厚,冷却较慢,外部冷却较快,此时内部(肉厚处)熔融塑料被外侧拉伸,中心部发后空隙,实际为真空泡不易冷却的肉厚部发后于表面者为缺陷。
3、原因及对策A、原因:射出压低的场合对策:射出压低则树脂的压缩不完全而产生收缩下陷,最好是提高射出压。