焦炉煤气脱硫及硫回收工艺分析
焦炉煤气制合成气的脱硫及净化工艺技术

焦炉煤气制合成气的脱硫及净化工艺技术摘要:众所周知,中国是一个炼焦大国,在众多焦炉仓促建成之后,由于相应设施不配套,致使一些企业“焦而不化”现象层出不穷,大量的焦炉煤气被直接的燃烧排放,既是对环境的严重污染,也是对资源的极大浪费,因而也被人们称其为“点天灯”。
本文简述了焦炉煤气的一系列净化工艺,并且介绍了采用催化转化与非催化转化制取天然气的工艺流程,希望对于了解焦炉煤气净化技术有借鉴意义。
关键词:焦炉煤气;合成气;脱硫;净化工艺引言焦炉煤气作为焦炭制成过程中煤炭经过高温干馏环节所产生的气态产品,其在炼焦产品总质量中占据着15%-18%的比重,是位于焦炭产品之下的第二大炼焦产品。
据相关统计显示,我国目前焦炉煤气年产量为1331.2亿m3,除去一半用来进行燃料回收,还有665.6亿m3的焦炉煤气可以应用到其他工业领域中,但由于国内焦化产业长期以来将工作重心放于焦炭生产方面,未能对焦炉煤气回收利用充分重视,不少焦化企业处于经济因素的考虑,未能建设起相应的焦炉煤气净化回收装置,大量焦炉煤气未被回收利用,而是直接排放燃烧。
每年未被利用的焦炉煤气高达300多亿m3,经济损失高达数百亿元,在造成极大资源浪费的同时,对周边环境也造成了十分严重的污染。
对此,为了实现焦炉煤气的有效回收利用,满足当前实现绿色工业、循环经济与建设节约型社会的发展要求,本文简要对焦炉煤气净化回收工艺进行介绍,并介绍了相应的应用情况,为日后的焦化工艺提供一定的借鉴参考。
1气体组分焦炉煤气是焦炭生产过程中煤炭经高温干馏出来的气体产物,在干馏温度为550℃,焦炉煤气中有大量的H2S、COS、CS2、NH3、HCN、噻吩、硫磺、硫醚、焦油、萘、苯等化学物质。
焦炉煤气经过净化和提取回收化工产品后成为回炉煤气,回炉煤气的气体组分一般为(%,以体积百分比计):H254-59、CH423-28、CO5.5-7、CO21.5-2.5、N23-5、CnHm2-3、O20.3-0.7。
焦炉煤气工艺流程
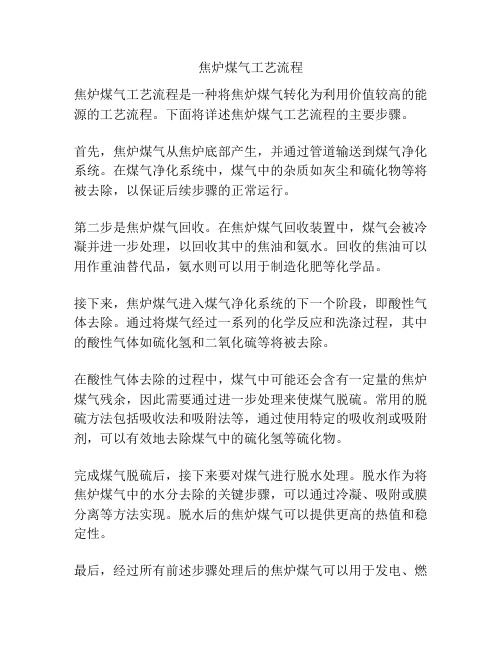
焦炉煤气工艺流程焦炉煤气工艺流程是一种将焦炉煤气转化为利用价值较高的能源的工艺流程。
下面将详述焦炉煤气工艺流程的主要步骤。
首先,焦炉煤气从焦炉底部产生,并通过管道输送到煤气净化系统。
在煤气净化系统中,煤气中的杂质如灰尘和硫化物等将被去除,以保证后续步骤的正常运行。
第二步是焦炉煤气回收。
在焦炉煤气回收装置中,煤气会被冷凝并进一步处理,以回收其中的焦油和氨水。
回收的焦油可以用作重油替代品,氨水则可以用于制造化肥等化学品。
接下来,焦炉煤气进入煤气净化系统的下一个阶段,即酸性气体去除。
通过将煤气经过一系列的化学反应和洗涤过程,其中的酸性气体如硫化氢和二氧化硫等将被去除。
在酸性气体去除的过程中,煤气中可能还会含有一定量的焦炉煤气残余,因此需要通过进一步处理来使煤气脱硫。
常用的脱硫方法包括吸收法和吸附法等,通过使用特定的吸收剂或吸附剂,可以有效地去除煤气中的硫化氢等硫化物。
完成煤气脱硫后,接下来要对煤气进行脱水处理。
脱水作为将焦炉煤气中的水分去除的关键步骤,可以通过冷凝、吸附或膜分离等方法实现。
脱水后的焦炉煤气可以提供更高的热值和稳定性。
最后,经过所有前述步骤处理后的焦炉煤气可以用于发电、燃烧或者制氢等应用领域。
利用焦炉煤气发电可以有效提高能源利用效率,降低环境污染;利用焦炉煤气燃烧可以代替部分石油和天然气的使用,降低能源依赖性;而将焦炉煤气转化为氢气可以作为清洁燃料应用于氢能源产业。
总之,焦炉煤气工艺流程通过多步骤的处理,将焦炉煤气转化为可再利用的能源,实现了能源的高效利用和减少环境污染的目标。
随着能源问题的日益突出,焦炉煤气工艺流程的发展和应用将发挥越来越重要的作用。
焦炉煤气制合成气的脱硫及净化工艺技术_汪家铭
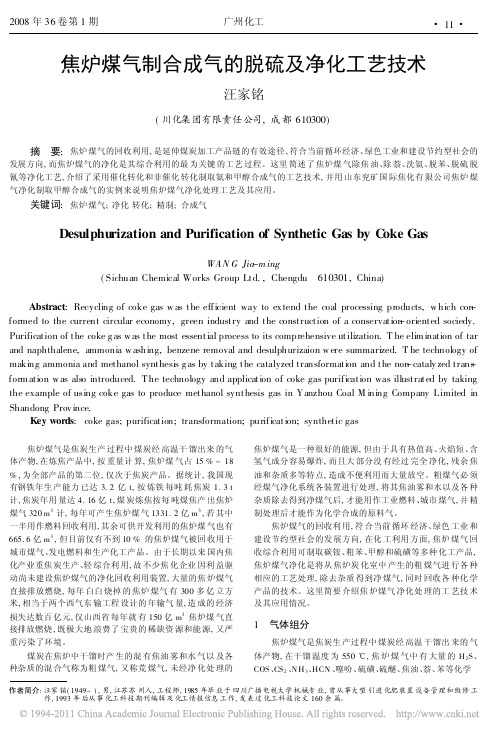
各种组分名称
含量
焦油雾
65~ 125
水气 氮化合物
硫化合物
氧化合物 氯化合物 碳氢化合物
煤中水分的 水气 化合水的水气 氨( NH3 ) 氰化氢( HCN ) 吡啶( C5 H5 N) 氧化氮( N O) 硫 化氢( H2S) 二硫化碳( CS2 ) 硫氧化碳( COS) 噻吩( C4 H4S) 硫醇( CnH2n+ 2 S) 二氧化硫( SO2 ) 酚及同系 物
Key words: coke gas; purificat ion; transformation; purif icat ion; synthet ic gas
焦炉煤气是焦炭生产 过程中 煤炭经 高温干 馏出来 的气 体产物, 在炼焦产品中, 按 重量计 算, 焦炉煤 气占 15 % ~ 18 % , 为全部产品的第二位, 仅次于焦炭产品。据统计, 我国现 有钢铁年生 产能力 已达 3. 2 亿 t, 按 炼铁 每吨 耗 焦炭 1. 3 t 计, 焦炭年用 量达 4. 16 亿 t, 煤 炭炼焦按每 吨煤焦产 出焦炉 煤气 320 m3 计, 每年可产生焦炉煤 气 1331. 2 亿 m3 , 若 其中 一半用作燃料回收利用, 其余可供开发利用的焦炉煤 气也有 665. 6 亿 m3 , 但目前仅有不到 10 % 的焦炉煤气被回 收用于 城市煤气、发电燃料和生产化工产品。由于长期以来 国内焦
0. 02
0. 06
0. 01~ 0. 05
0. 05
0. 1
0. 1
0. 05
0. 03~ 0. 01
0. 02
0. 01~ 0. 02
( g m3) 萘 0. 3 0. 2
焦炉煤气的净化工艺流程
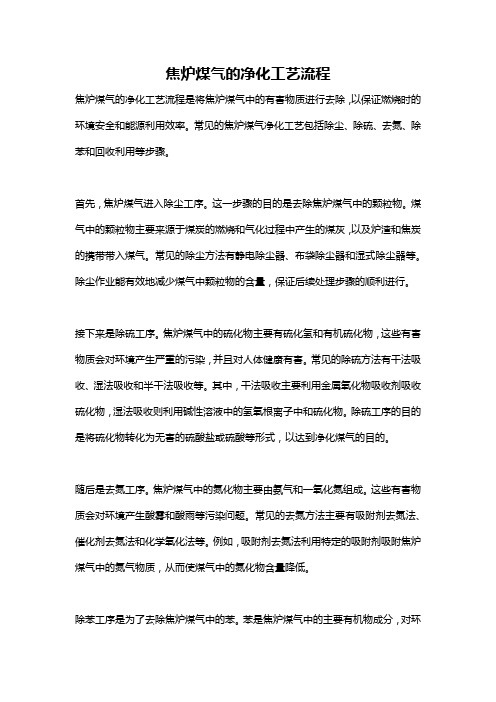
焦炉煤气的净化工艺流程焦炉煤气的净化工艺流程是将焦炉煤气中的有害物质进行去除,以保证燃烧时的环境安全和能源利用效率。
常见的焦炉煤气净化工艺包括除尘、除硫、去氮、除苯和回收利用等步骤。
首先,焦炉煤气进入除尘工序。
这一步骤的目的是去除焦炉煤气中的颗粒物。
煤气中的颗粒物主要来源于煤炭的燃烧和气化过程中产生的煤灰,以及炉渣和焦炭的携带带入煤气。
常见的除尘方法有静电除尘器、布袋除尘器和湿式除尘器等。
除尘作业能有效地减少煤气中颗粒物的含量,保证后续处理步骤的顺利进行。
接下来是除硫工序。
焦炉煤气中的硫化物主要有硫化氢和有机硫化物,这些有害物质会对环境产生严重的污染,并且对人体健康有害。
常见的除硫方法有干法吸收、湿法吸收和半干法吸收等。
其中,干法吸收主要利用金属氧化物吸收剂吸收硫化物,湿法吸收则利用碱性溶液中的氢氧根离子中和硫化物。
除硫工序的目的是将硫化物转化为无害的硫酸盐或硫酸等形式,以达到净化煤气的目的。
随后是去氮工序。
焦炉煤气中的氮化物主要由氨气和一氧化氮组成。
这些有害物质会对环境产生酸雾和酸雨等污染问题。
常见的去氮方法主要有吸附剂去氮法、催化剂去氮法和化学氧化法等。
例如,吸附剂去氮法利用特定的吸附剂吸附焦炉煤气中的氮气物质,从而使煤气中的氮化物含量降低。
除苯工序是为了去除焦炉煤气中的苯。
苯是焦炉煤气中的主要有机物成分,对环境和人体都有一定的危害。
去苯的方法多种多样,包括吸附过程、吸附剂再生过程和热解技术等。
其中,吸附过程主要是利用各种吸附剂吸附苯,吸附剂再生过程则是通过各种手段将吸附的苯从吸附剂中脱附出来。
最后是回收利用工序。
焦炉煤气中除去有害物质后,还含有一些有价值的组分,如甲烷、氢气和一些烃类等。
对于这些有价值的组分,可以通过适当的工艺进行回收利用。
一般来说,回收利用工艺分为低温分馏和高温分馏两种方式。
低温分馏主要是通过降温将焦炉煤气中的一些高沸点成分凝结出来,从而得到所需的有价值气体。
而高温分馏则是通过高温条件下焦炉煤气中的组分按沸点顺序蒸馏分离。
焦炉煤气脱硫工艺

焦炉煤气脱硫工艺(总19页)本页仅作为文档封面,使用时可以删除This document is for reference only-rar21year.March煤化工工艺大作业焦炉煤气脱硫工艺的探讨院系:资源与环境学院班级:化工09—4班姓名:荆智鹏学号: 14指导老师:徐秀梅焦炉煤气脱硫工艺的探讨作者:荆智鹏摘要:煤化工是以煤为原料经化学加工使煤转化为其他化学产品的过程。
从煤气化工段的工艺气中发现,除了含有生产甲醇和其他下游产品所需的CO, H2 和CO2 外,还含有大量多余的CO2 及少量H2S, COS,SO2 等成分,这些碳的氧化物和硫化物是生产甲醇或其他化学品所不需要的,必须将这些杂质除去。
另外,硫化物通过克劳斯工艺生产硫磺,CO2 可以回收送往尿素厂合成尿素,提高经济效益变废为宝。
以天然气或石脑油为原料,采用蒸汽转化法造气,变换气中CO2 的含量约在15-23mol%左右。
以重油或煤原料,采用部分氧化法制气时,变换气中 CO2 的含量高达35mol%以上。
H2S 及有机硫的含量则与原料含硫量有关,约在1000ppm 和10000ppm 之间。
通过净化,使硫化物含量小于0.2-0.5ppm, CO2 小于10ppm。
关键词:煤气脱硫湿法干法催化剂科学的讲,在湿式氧化法脱硫中,副盐的生成是无法回避的,它是化学反应的副产物,是客观存在的。
但是,我们通过多年实际生产状况总结发现,同等规模条件下,不同的工况条件、不同的工艺技术、不同的设备配置以及使用不同的催化剂,副盐生成量的多少却大不一样,而且差别很大。
这一现象引起我们高度的重视,也再次促使我们进一步探讨和研究脱硫中副盐形成的机理,因为只有清楚的了解副盐产生的机理,我们才能有效的找到解决和处理它的措施。
虽然我们不能避免它的形成,但我们可以采取一系列有效措施来减少或抑制它的生成。
从而减少脱硫液中由于副盐的存在而影响企业的正常生产。
特别在大规模的生产中(气量大、H2S含量高),这种现象尤为突出,副盐的生成不仅严重影响了脱硫效率、增加了辅料消耗而且也影响了环保。
焦炉煤气 工艺流程

焦炉煤气工艺流程焦炉煤气是焦炉煤炭在高温下产生的一种气体,在很长一段时间里,焦炉煤气被广泛应用于燃料和化工领域。
下面将为大家介绍焦炉煤气的工艺流程。
焦炉煤气的产生主要是通过焦炉炼焦过程中的不完全燃烧和挥发分解产生的。
在焦炉内炼焦时,煤炭由上部装料口进入焦炉,经过一系列的物理化学变化,最终冷却出来的煤气即为焦炉煤气。
焦炉煤气的工艺流程主要分为三个阶段:炼焦阶段、冷却阶段和净化阶段。
在炼焦阶段,煤炭在高温环境下进行挥发分解,产生焦炭和焦炉煤气。
挥发分解的主要反应包括干馏、结焦与气化等。
煤的挥发分解温度通常在400℃-900℃之间。
焦炉内部的高温炉壁使得煤气中的有机物无法完全燃烧,形成不完全燃烧的焦炉煤气。
在冷却阶段,焦炉煤气经过煤气出口管道进入冷却塔。
冷却塔内部设置了多个冷却层和冷凝层。
焦炉煤气在通过冷却层时,通过与从上方喷洒下来的冷凝剂的交换,将煤气中的水蒸气和部分液化烃冷凝回收。
通过这种方式,焦炉煤气的温度被迅速降低,并且冷凝出来的液体可以进一步提炼。
冷却后,焦炉煤气进入冷凝层,通过与一种冷凝剂接触,使得其中的其他液态有机物冷凝,得到另一批可提炼的液体产品。
在净化阶段,焦炉煤气经过冷却后进入净化系统进行进一步处理。
净化系统主要是通过吸附、干燥和脱硫等工艺,将煤气中的杂质进行去除。
其中,吸附工艺主要是通过将焦炉煤气经过各类吸附剂的床层,实现对焦炉煤气中有机硫化物的吸附。
干燥工艺主要是通过风冷和除湿剂吸附,将煤气中的水分去除。
脱硫工艺主要是通过往煤气中添加一种化学药剂,使其与焦炉煤气中的硫化氢反应生成含硫化合物,然后通过其他工艺将其去除。
最终,经过炼焦、冷却和净化三个阶段的焦炉煤气将得到高纯度、高热值的产品。
这种产品广泛应用于燃料领域,如发电厂、炼铁厂等,也可以在化工领域中用作原料,制造各种化工产品。
总之,焦炉煤气的工艺流程经历了炼焦、冷却和净化三个阶段,通过各种反应和处理,最终得到高纯度、高热值的产品。
煤化工(焦化厂)焦炉煤气6大脱硫技术详解与脱硫工艺选择
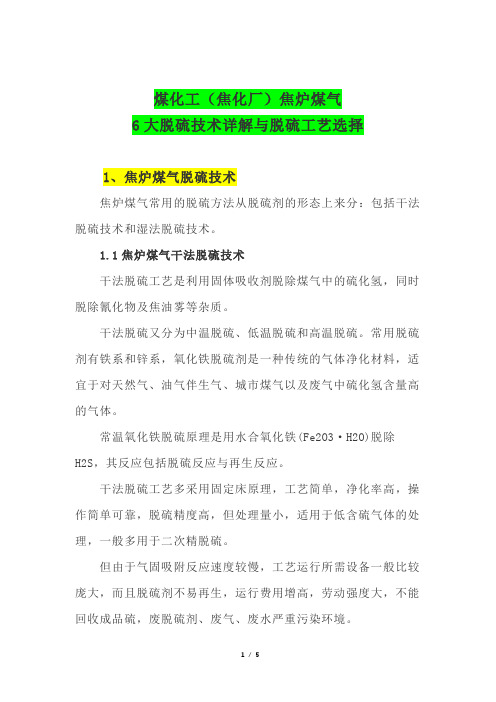
煤化工(焦化厂)焦炉煤气6大脱硫技术详解与脱硫工艺选择1、焦炉煤气脱硫技术焦炉煤气常用的脱硫方法从脱硫剂的形态上来分:包括干法脱硫技术和湿法脱硫技术。
1.1焦炉煤气干法脱硫技术干法脱硫工艺是利用固体吸收剂脱除煤气中的硫化氢,同时脱除氰化物及焦油雾等杂质。
干法脱硫又分为中温脱硫、低温脱硫和高温脱硫。
常用脱硫剂有铁系和锌系,氧化铁脱硫剂是一种传统的气体净化材料,适宜于对天然气、油气伴生气、城市煤气以及废气中硫化氢含量高的气体。
常温氧化铁脱硫原理是用水合氧化铁(Fe2O3·H2O)脱除H2S,其反应包括脱硫反应与再生反应。
干法脱硫工艺多采用固定床原理,工艺简单,净化率高,操作简单可靠,脱硫精度高,但处理量小,适用于低含硫气体的处理,一般多用于二次精脱硫。
但由于气固吸附反应速度较慢,工艺运行所需设备一般比较庞大,而且脱硫剂不易再生,运行费用增高,劳动强度大,不能回收成品硫,废脱硫剂、废气、废水严重污染环境。
1.2焦炉煤气湿法脱硫技术湿法工艺是利用液体脱硫剂脱除煤气中的硫化氢和氰化氢。
常用的方法有氨水法、单乙醇胺法、砷碱法、VASC脱硫法、改良 ADA法、TH 法、苦味酸法、对苯二酚法、HPF 法以及一些新兴的工艺方法等。
1.2.1 氨水法(AS法):氨水法脱硫是利用焦炉煤气中的氨,在脱硫塔顶喷洒氨水溶液(利用洗氨溶液)吸收煤气中 H2S,富含 H2S 和 NH3的液体经脱酸蒸氨后再循环洗氨脱硫。
在脱硫塔内发生的氨水与硫化氢的反应是:H2S+2NH3·H2O →(NH4)2S+2H2O。
AS 循环脱硫工艺为粗脱硫,操作费用低,脱硫效率在 90 %以上,脱硫后煤气中的 H2S 在200~500 mg·m-3。
1.2.2 VASC法:VASC法脱硫过程是洗苯塔后的煤气进入脱硫塔,塔内填充聚丙烯填料,煤气自下而上流经各填料段与碳酸钾溶液逆流接触,再经塔顶捕雾器出塔。
煤气中的大部分 H2S 和 HCN 和部分 CO2被碱液吸收,碱液一般主要是 Na2CO3或 K2CO3溶液。
焦炉煤气脱硫及硫回收工艺分析
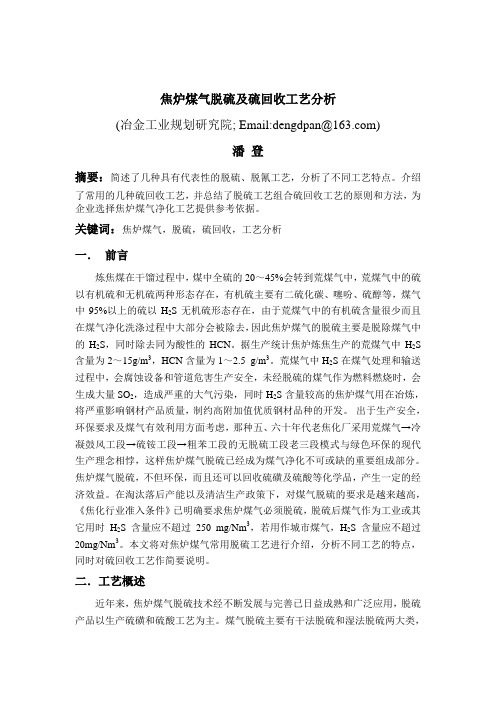
焦炉煤气脱硫及硫回收工艺分析(冶金工业规划研究院; Email:dengdpan@)潘登摘要:简述了几种具有代表性的脱硫、脱氰工艺,分析了不同工艺特点。
介绍了常用的几种硫回收工艺,并总结了脱硫工艺组合硫回收工艺的原则和方法,为企业选择焦炉煤气净化工艺提供参考依据。
关键词:焦炉煤气,脱硫,硫回收,工艺分析一.前言炼焦煤在干馏过程中,煤中全硫的20~45%会转到荒煤气中,荒煤气中的硫以有机硫和无机硫两种形态存在,有机硫主要有二硫化碳、噻吩、硫醇等,煤气中95%以上的硫以H2S无机硫形态存在,由于荒煤气中的有机硫含量很少而且在煤气净化洗涤过程中大部分会被除去,因此焦炉煤气的脱硫主要是脱除煤气中的H2S,同时除去同为酸性的HCN。
据生产统计焦炉炼焦生产的荒煤气中H2S 含量为2~15g/m3,HCN含量为1~2.5 g/m3。
荒煤气中H2S在煤气处理和输送过程中,会腐蚀设备和管道危害生产安全,未经脱硫的煤气作为燃料燃烧时,会生成大量SO2,造成严重的大气污染,同时H2S含量较高的焦炉煤气用在冶炼,将严重影响钢材产品质量,制约高附加值优质钢材品种的开发。
出于生产安全,环保要求及煤气有效利用方面考虑,那种五、六十年代老焦化厂采用荒煤气→冷凝鼓风工段→硫铵工段→粗苯工段的无脱硫工段老三段模式与绿色环保的现代生产理念相悖,这样焦炉煤气脱硫已经成为煤气净化不可或缺的重要组成部分。
焦炉煤气脱硫,不但环保,而且还可以回收硫磺及硫酸等化学品,产生一定的经济效益。
在淘汰落后产能以及清洁生产政策下,对煤气脱硫的要求是越来越高,《焦化行业准入条件》已明确要求焦炉煤气必须脱硫,脱硫后煤气作为工业或其它用时H2S含量应不超过250 mg/Nm3,若用作城市煤气,H2S含量应不超过20mg/Nm3。
本文将对焦炉煤气常用脱硫工艺进行介绍,分析不同工艺的特点,同时对硫回收工艺作简要说明。
二.工艺概述近年来,焦炉煤气脱硫技术经不断发展与完善已日益成熟和广泛应用,脱硫产品以生产硫磺和硫酸工艺为主。
- 1、下载文档前请自行甄别文档内容的完整性,平台不提供额外的编辑、内容补充、找答案等附加服务。
- 2、"仅部分预览"的文档,不可在线预览部分如存在完整性等问题,可反馈申请退款(可完整预览的文档不适用该条件!)。
- 3、如文档侵犯您的权益,请联系客服反馈,我们会尽快为您处理(人工客服工作时间:9:00-18:30)。
焦炉煤气脱硫及硫回收工艺分析
焦炉煤气脱硫工艺中常用的方法有吸收法、催化氧化法和膜法等。
其中,吸收法是一种较常用的脱硫技术,其主要原理是通过将煤气经过吸收液(如碱液或氨液)进行接触,使H2S被吸收并转化为硫化物,从而达到脱硫的目的。
催化氧化法则是利用催化剂将H2S氧化为硫,达到脱硫的效果。
膜法则是通过膜的选择性透过性,将H2S从煤气中分离出来,实现脱硫。
吸收法中较为常用的是碱液吸收法。
碱液吸收法的优点是操作简单、脱硫效果较好,但对于含有高浓度的H2S的煤气来说,在吸收液中可能会生成大量的硫化物,导致液氨浴中硫化物过多,降低硫吸收效果。
为解决这一问题,可以通过加入硝酸铁和硝酸铝等添加剂,改善液氨浴的性质,提高脱硫效果。
催化氧化法主要是通过催化剂(如氧化铁、氧化锌等)将H2S氧化为硫,其中反应产物为SO2、在焦炉煤气中,SO2含量较高,通过反应器中催化剂的作用,可以将H2S和SO2相互转化,使SO2被还原为硫,并回收利用。
这种方法适用于H2S含量较高的煤气,可以有效地将H2S转化为有价值的硫。
膜法则是利用特定的膜材料,通过选择性透过性将煤气中的H2S分离出来。
膜法具有操作简单、能耗低、脱硫效果好等优点,但因为膜材料对不同的气体有不同的透过性,所以需要选择合适的膜材料来实现脱硫。
在焦炉煤气脱硫的基础上,硫回收技术可以有效地利用焦炉煤气中的硫资源。
目前常用的硫回收技术有硫磺回收、硫纵向深度利用和硫脱硫液回收等。
硫磺回收是将焦化炉煤气中的SO2和氢气反应生成硫磺,然后收
集硫磺进行回收利用。
硫纵向深度利用是将硫经过高温和高压加工,制成硫酸、硫酸铵和硫化铵等化工产品。
硫脱硫液回收则是利用含氢气的溶液将气中的硫含量吸收,生成硫酸铵和硫化铵等化学品。
综上所述,焦炉煤气脱硫及硫回收工艺分析主要包括吸收法、催化氧化法和膜法等不同的脱硫工艺。
根据不同的情况,可以选择适合的工艺来降低煤气中的硫含量,并对焦炉煤气中的硫进行回收利用,以实现资源的可持续利用。