气缸缸体加工
阀门气缸缸体加工工艺流程

阀门气缸缸体加工工艺流程Valve cylinder processing is a key part of the manufacturing process for valve components. 阀门气缸加工是阀门零部件制造过程中的关键部分。
It involves multiple steps and requires precision and attention to detail to ensure the final product meets quality standards. 它涉及到多个步骤,并需要精确和注重细节,以确保最终产品符合质量标准。
From machining the cylinder body to assembly and testing, each stage plays a critical role in the overall performance and reliability of the valve. 从加工缸体到装配和测试,每个阶段对阀门的整体性能和可靠性都起着至关重要的作用。
The first step in the process is machining the cylinder body. 过程的第一步是加工气缸缸体。
This involves using precision machinery to shape the raw material into the desired dimensions and specifications. 这涉及使用精密机械将原材料塑造成所需的尺寸和规格。
It is essential to follow strict guidelines and measurements to ensure the cylinder body meets the required tolerances and surface finish. 遵循严格的指导和测量是必要的,以确保气缸缸体符合所需的公差和表面光洁度。
发动机缸体生产过程

发动机缸体生产过程嘿,你知道发动机缸体是怎么生产出来的吗?这可真是个超级有趣的过程,就像一场精心编排的大型魔术表演,只不过这魔术的背后是严谨的科学和高超的工艺。
我有个朋友在发动机制造厂里工作,他叫小李。
有一次我有幸去参观了他们的工厂,亲眼目睹了发动机缸体生产的全过程,那场面,真叫一个震撼。
生产发动机缸体啊,首先得从原材料说起。
这些原材料就像是厨师做菜的食材一样重要。
缸体的主要材料通常是高强度的铸铁或者铝合金。
这就好比盖房子,你得先选好结实耐用的砖头。
铝合金材质的缸体就像是轻盈的舞者,重量轻,有助于提高发动机的燃油效率,就像舞者灵活的身姿可以快速移动一样。
而铸铁缸体呢,则像是一位强壮的大力士,具有更高的强度和耐热性,能够承受更大的压力。
接下来就是铸造的过程啦。
这个过程就像是雕塑家在创作一件伟大的作品。
工人们把原材料加热融化,然后倒入事先制作好的模具里。
这模具啊,就像是一个魔法盒,金属液体流进去之后,就会按照模具的形状成型。
我当时看到那红红的、滚烫的金属液体,像岩浆一样流淌进模具,心里想着,这要是不小心洒出来一点儿,那可不得了啊!旁边的老师傅笑着跟我说:“小伙子,这可都是有严格的操作流程的,不会出乱子的。
”我就好奇地问:“师傅,这就像把水倒进一个瓶子里一样,但是要困难多了吧?”老师傅哈哈笑着说:“那可不,这比倒水可复杂太多啦,温度、流速、模具的状况都得严格把控呢。
”铸造出来的缸体雏形可还不行,它就像一块未经雕琢的璞玉。
然后就是机械加工的环节了。
这时候各种大型的加工设备就像一群技艺精湛的工匠,开始对缸体进行精细的加工。
比如说,要在缸体上钻出活塞运动的气缸孔。
这钻孔的精度要求极高,就像在一根头发丝上雕刻花纹一样精细。
我看到那些机床在高速运转,发出嗡嗡的声音,小李告诉我:“你看,这些设备都是按照设定好的程序进行操作的,误差非常小。
要是这个孔钻歪了或者大小不合适,那这个缸体可就报废了。
”我不禁感叹:“哇,这可真是差之毫厘谬以千里啊!”在加工的过程中,还有一个很重要的步骤就是珩磨。
汽车发动机缸体制造工艺
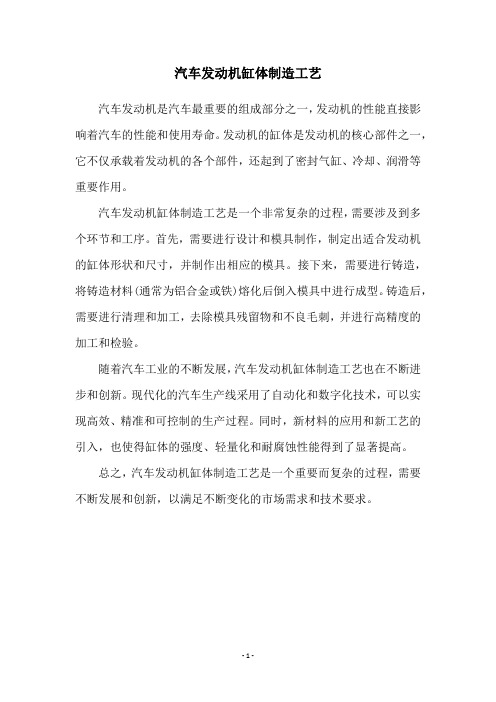
汽车发动机缸体制造工艺
汽车发动机是汽车最重要的组成部分之一,发动机的性能直接影响着汽车的性能和使用寿命。
发动机的缸体是发动机的核心部件之一,它不仅承载着发动机的各个部件,还起到了密封气缸、冷却、润滑等重要作用。
汽车发动机缸体制造工艺是一个非常复杂的过程,需要涉及到多个环节和工序。
首先,需要进行设计和模具制作,制定出适合发动机的缸体形状和尺寸,并制作出相应的模具。
接下来,需要进行铸造,将铸造材料(通常为铝合金或铁)熔化后倒入模具中进行成型。
铸造后,需要进行清理和加工,去除模具残留物和不良毛刺,并进行高精度的加工和检验。
随着汽车工业的不断发展,汽车发动机缸体制造工艺也在不断进步和创新。
现代化的汽车生产线采用了自动化和数字化技术,可以实现高效、精准和可控制的生产过程。
同时,新材料的应用和新工艺的引入,也使得缸体的强度、轻量化和耐腐蚀性能得到了显著提高。
总之,汽车发动机缸体制造工艺是一个重要而复杂的过程,需要不断发展和创新,以满足不断变化的市场需求和技术要求。
- 1 -。
论发动机缸体的加工工艺

环球市场/理论探讨-176-论发动机缸体的加工工艺朱广波 史晓龙上汽通用五菱汽车股份有限公司青岛分公摘要:汽车制造业作为国民经济的支柱产业,多年来为我国经济发展做出了非常突出的贡献。
然而,在经历了突飞猛进的高增长之后,我国汽车工业面临着越来越多的问题和压力。
如何在我国人口红利逐渐消失、企业竞争力日益下降的今天,进一步降低生产成本,同时不断提高产品质量,实现绿色制造,应对市场对产品提出的日新月异的需求尤其重要。
在此背景下本文将着重分析探讨发动机缸体的加工工艺要点,以期能为以后的实际工作起到一定的借鉴作用。
关键词:发动机;缸体;加工1、发动机缸体加工工艺性分析发动机缸体毛坯制作成坯后,上下缸体的6个面都需要采用金属切削加工的工艺方法最终加工成缸体成品,在加工过程中还要穿插气密检测、清洗、珩磨缸孔等工艺方法。
金属切削加工发动机缸体主要包括:铣面、铣孔、钻孔、镗孔、铰孔和攻丝等。
发动机缸体的加工一般情况下可划分为两个阶段,一是分体加工阶段,二是组件加工阶段。
分体加工阶段主要是将上下缸体上的精度要求不太高的一般结构特征、组合后不便加工的结构特征及关系到合缸的结构特征加工到位或去除大部余量,主要包括合缸面、合缸定位销孔、进排气两侧的安装面与孔系、止推面及轴瓦槽等特征。
发动机缸体的重要结构特征,如曲轴孔、气缸孔、缸盖面、前后端的定位销孔等必须安排在发动机缸体合缸后进行精加工。
发动机缸体试制加工的工艺流程安排可视企业设备现状进行合理安排,一般来讲,采用立式加工中心进行加工,装夹较为方便,但工序会相对分散,需要投入的工艺装备较多,会加大试制的加工成本。
采用卧式加工中心进行加工,可以使工序相对集中,投入的工装较少,可降低试制加工成本。
2、发动机缸体加工工艺要点2.1 缸体加工自动线汽车缸体加工自动线是汽车制造行业中的一种高效设备。
自动线又分为刚性自动线和柔性自动线。
在我国,加工缸体最多的当属组合机床自动线,其输送形式有棘爪输送、摆杆式输送和抬起步伐输送等,都属于刚性自动线。
缸体不同角度曲轴瓦面斜油孔加工方式创新
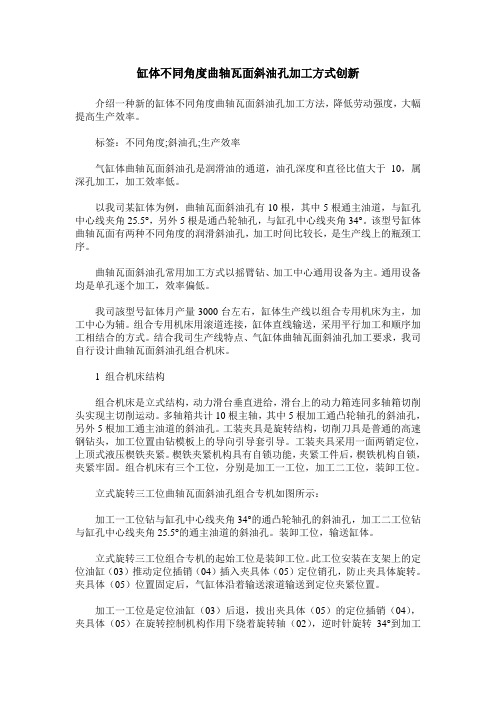
缸体不同角度曲轴瓦面斜油孔加工方式创新介绍一种新的缸体不同角度曲轴瓦面斜油孔加工方法,降低劳动强度,大幅提高生产效率。
标签:不同角度;斜油孔;生产效率气缸体曲轴瓦面斜油孔是润滑油的通道,油孔深度和直径比值大于10,属深孔加工,加工效率低。
以我司某缸体为例,曲轴瓦面斜油孔有10根,其中5根通主油道,与缸孔中心线夹角25.5°,另外5根是通凸轮轴孔,与缸孔中心线夹角34°。
该型号缸体曲轴瓦面有两种不同角度的润滑斜油孔,加工时间比较长,是生产线上的瓶颈工序。
曲轴瓦面斜油孔常用加工方式以摇臂钻、加工中心通用设备为主。
通用设备均是单孔逐个加工,效率偏低。
我司該型号缸体月产量3000台左右,缸体生产线以组合专用机床为主,加工中心为辅。
组合专用机床用滚道连接,缸体直线输送,采用平行加工和顺序加工相结合的方式。
结合我司生产线特点、气缸体曲轴瓦面斜油孔加工要求,我司自行设计曲轴瓦面斜油孔组合机床。
1 组合机床结构组合机床是立式结构,动力滑台垂直进给,滑台上的动力箱连同多轴箱切削头实现主切削运动。
多轴箱共计10根主轴,其中5根加工通凸轮轴孔的斜油孔,另外5根加工通主油道的斜油孔。
工装夹具是旋转结构,切削刀具是普通的高速钢钻头,加工位置由钻模板上的导向引导套引导。
工装夹具采用一面两销定位,上顶式液压楔铁夹紧。
楔铁夹紧机构具有自锁功能,夹紧工件后,楔铁机构自锁,夹紧牢固。
组合机床有三个工位,分别是加工一工位,加工二工位,装卸工位。
立式旋转三工位曲轴瓦面斜油孔组合专机如图所示:加工一工位钻与缸孔中心线夹角34°的通凸轮轴孔的斜油孔,加工二工位钻与缸孔中心线夹角25.5°的通主油道的斜油孔。
装卸工位,输送缸体。
立式旋转三工位组合专机的起始工位是装卸工位。
此工位安装在支架上的定位油缸(03)推动定位插销(04)插入夹具体(05)定位销孔,防止夹具体旋转。
夹具体(05)位置固定后,气缸体沿着输送滚道输送到定位夹紧位置。
气缸缸体加工关键技术分析及研究

气缸缸体加工关键技术分析及研究发布时间:2021-12-08T01:41:43.349Z 来源:《教学与研究》2021年第21期作者:周清卿[导读] 气缸是气压传动系统中的重要组成部分。
缸筒我们国内一般采用的是推镗滚压法和钻床等加工设备。
周清卿江苏省盐城技师学院江苏盐城 224002摘要:气缸是气压传动系统中的重要组成部分。
缸筒我们国内一般采用的是推镗滚压法和钻床等加工设备。
加工效率慢,工序分散,针对这一问题,我们通过改进,采用数控加工中心机床来进行批量试制的方法,因为加工中心机床是汇聚镗、钻、铣和自动换刀为一体的加工设备。
再通过设计专用夹具,可以一次性加工多个缸筒,在保证了加工质量的同时,也提高了工作效率,取得了很好的效果。
本文主要对气缸缸体加工的关键技术进行分析和研究。
关键词:气缸夹具深孔加工盲孔加工本文以某公司制造的一款小型气缸为例。
这一执行元件,借助压缩空气,通过控制电磁阀发出0~40mA的电信号,控制阀门的开关,进而实现远程控制的目的。
因为传动介质中可压缩性和气泄漏等方面对传动比的影响比较大,所以对执行元件气缸制造精度的要求就非常高。
缸筒作为气缸端盖、活塞、活塞杆和密封件等气缸产品的主要支承部件,加工质量的高低会直接影响整套产品的寿命和稳定性。
缸筒加工精度非常高,特别是对同轴度要求更为严格,因为同轴度直接反应缸筒的耐磨性。
本文以该型气缸为例,针对缸筒加工中面临的一系列关键技术问题及其解决方案进行探讨和研究。
一、缸筒加工方法和加工技术要点分析缸筒的大小规格非常多,直径从几十毫米到几百毫米、长度也从几十毫米到十多米不等,社会的需求量也很大。
缸筒的外径一般不要求加工,内部要求非常高。
某公司生产的这款缸筒,材料为铝合金,要求能够承受1MPa的气体压力。
缸筒是整个缸体的关键性精密零件,加工质量的好坏直接影响整个产品的可靠性和稳定性,所以缸筒制造在机械加工中占有非常重要的地位。
二、缸筒加工工装设备设计气缸的形状不规则,造成零件装夹不方便。
气缸缸体材料
气缸缸体材料
气缸缸体是内燃机的重要部件,其材料选择直接关系到内燃机的性能和可靠性。
目前,气缸缸体材料主要包括铸铁、铝合金和镁合金等。
不同的材料具有不同的特性和适用范围,本文将对这些材料进行介绍和比较。
首先,铸铁是传统的气缸缸体材料,具有良好的耐磨性和耐热性,适用于大功率、大排量的发动机。
然而,铸铁的密度较大,重量较重,不利于发动机的节能和减排。
此外,铸铁的加工难度较大,成本较高,不利于发动机的轻量化和成本控制。
其次,铝合金是近年来发展较快的气缸缸体材料,具有良好的导热性和强度重
量比,适用于小功率、小排量的发动机。
铝合金的密度较小,重量较轻,有利于发动机的节能和减排。
此外,铝合金的加工性能较好,成本较低,有利于发动机的轻量化和成本控制。
然而,铝合金的耐磨性和耐热性较差,不适用于大功率、大排量的发动机。
最后,镁合金是一种新型的气缸缸体材料,具有良好的强度重量比和导热性,
适用于超轻量化发动机。
镁合金的密度较小,重量较轻,有利于发动机的超轻量化和高效化。
此外,镁合金的加工性能较好,成本较低,有利于发动机的超轻量化和成本控制。
然而,镁合金的耐磨性和耐热性较差,不适用于大功率、大排量的发动机。
综上所述,不同的气缸缸体材料具有不同的特性和适用范围。
在选择气缸缸体
材料时,需要根据发动机的功率、排量和使用环境等因素综合考虑,以实现最佳的性能和可靠性。
未来,随着材料科学和加工技术的不断进步,新型的气缸缸体材料将不断涌现,为内燃机的发展带来新的机遇和挑战。
发动机缸体、缸盖加工[整理]
发动机缸体、缸盖加工缸体加工工艺流程工艺一:1、毛坯外观检查,上料;2、利用毛坯初级准定位。
粗镗曲轴孔,粗铣前后端面、开档面,钻主油道空,钻铰过度基准孔,半精铣定位面;3、利用上道工序加工的过度基准定位。
粗镗缸孔,钻曲轴斜油孔,钻水套斜冷却孔,钻攻缸盖、框架/主盖(下缸体)螺栓孔,加工工艺基准孔;4、工艺销孔定位。
钻攻进排气侧各螺纹孔系,前后端面部分孔系;5、工艺销孔定位。
镗水泵孔及喇叭孔,铣止推面、锁瓦槽;6、中间清洗、烘干;7、中间试漏。
采用内试法测试主油道、水道、曲轴箱有无压力泄露,前两项10cc/min,后一项30cc/min;8、安装框架/主盖(下缸体);9、合箱后采用上缸体或下缸体的工艺销孔定位。
加工前后端面各螺纹孔系,精铣顶面、前后端面,精镗曲轴孔、缸孔、前后油封孔;10、缸孔、曲轴孔珩磨;11、最终清洗。
浪涌清洗、定点定位、翻转、真空干燥、冷却;12、压装堵盖,密封试漏(外试);13、测量打号;14、外观检查,下线。
工艺二:10 铣定位凸台、发动机支架凸台、机冷器面、工艺导向面20 粗铣底平面、龙门面、对口面、顶平面60 粗铣缸套底孔70 粗铣前后端面80 精铣前后端面90 气缸体打流水号100 铣主轴承座两侧面110 铣油封凹座120 铣主轴承孔瓦片槽130 扩1、2、4、5凹轮轴底孔140 扩第3凸轮轴底孔150 枪钻前后端主油道孔及油泵座内油道孔160 枪钻2个横油道深孔及顶面2个深油孔170 钻5个横油道孔及顶面12个深油孔180钻主轴承内7个斜油孔208人工吹风横油道210 粗镗缸套底孔220 半精镗缸套底孔240 两侧凸轮面及导向以及孔系加工250 前销、后环、出砂孔及凸轮轴凹座底孔及部分螺纹加工; 260 顶面水孔缸盖螺栓孔、导位孔及瓦闰盖定位环孔加工270 底面油底壳螺孔、瓦盖螺栓孔、深油孔、喷油雾孔加工280 精镗缸套底孔290 精拉瓦盖结合面300 水压试验310 第一、七横油孔、增压器回油孔出砂孔加工320 六个7度横油孔及机油标尺孔加工330 中间清洗335 人工清洗窗口面、12个螺孔和主油道340 缸孔分组及压缸套350 装瓦盖及瓦盖螺栓355 拧紧瓦盖螺栓360 粗镗主轴承孔、凸轮轴衬套底孔370 半精镗主轴沉孔、精镗凸轮轴衬套底孔390 清洗孔395 吹前压端面、机冷器面及底面孔系400 压凸轮轴衬套410 粗车第四轴承止推面420 精镗主凸轮轴孔,惰轮轴孔前销油泵底销孔、后环,精车第四止推孔430 铰主轴承孔440 扩挺杆孔450 第二次扩挺杆孔460 粗镗挺杆孔470 铰挺杆孔480 6个7°横油孔及机油标尺孔加工490 粗镗缸500 缸孔倒角510 精镗缸套孔530 缸套孔返修)540 精铣缸体顶平面548 缸体刷镀550 清洗560 压装前后堵盖、凸轮轴底堵盖、压紧侧面出沙孔、碗形塞590 缸孔分组及打号。
汽车发动机缸体加工工艺分析
汽车发动机缸体加工工艺分析摘要:随着经济的发展和人民生活水平的提高,我国汽车销量大幅增长。
在汽车工业中,汽车零部件的生产效率和加工质量非常重要。
通常情况下,汽车零部件的生产效率和加工质量对汽车工业的发展起着重要的作用。
在汽车零部件中,发动机缸体是最重要的汽车零部件之一。
汽车发动机气缸的加工质量和生产效率在一定程度上决定了汽车的生产效率和性能。
可见,汽车工业要想取得更大的发展,必须大幅度提高汽车发动机缸体的加工质量和生产效率。
本文介绍了汽车发动机气缸体的加工工艺。
关键词:汽车发动机;缸体加工;工艺0 引言发动机是汽车的关键部件,气缸体是发动机的重要组成部分,加工工艺的精度对发动机质量有着决定性的影响。
随着市场竞争的不断加剧,市场对产品种类的需求越来越多样化,极大地刺激了汽车行业的发展。
汽车发动机作为高新技术产品之一,不断优化,产品功能和性能得到提升,原有的缸体生产模式已不能适应现代企业发展的需要,产品品种多样。
只有可调节、生产成本低的柔性生产工艺模式才能满足市场需求,发展空间更大。
1缸体加工的具体工艺流程(1)气缸的表面处理。
圆柱面加工主要分为平面加工和间隙加工。
面加工主要包括面铣削,如顶面、底面和前后端加工。
间隙加工往往需要镗、珩磨、钻孔、铰孔和攻丝,包括水套孔、安装孔、连接孔、活塞缸孔、油孔等。
(2)气缸加工流程。
气缸加工工序主要分为加工主型材、加工主孔和立柱、清洗检查和加工辅助结构四个步骤,不同的工序负责不同的领域和位置基准。
例:有的程序采用两销完全定位方式,有的程序采用近似参考3-2-1完全定位方式。
另外,不同方法的定位面在底面和端面之间也不同。
在气缸的加工中,气缸底面和端面的加工是一个非常重要的工序。
(3)气缸体加工分为阶段。
筒体加工可分为粗加工和精加工两个模块,每个模块又可分为两部分,整个生产线可分为粗加工设备、半精加工设备和精加工设备三部分。
在每个阶段,都需要根据需要的产品来寻找和合理化生产。
关于发动机缸体加工工艺分析
关于发动机缸体加工工艺分析摘要:发动机生产线作为汽车制造企业的重要生产资料从投资规划到正式批量加工生产,其购置成本和运营成本都会对企业的经济效益产生举足轻重的影响,因此,深入了解现代发动机生产线所应当具备的经济技术特征、当前发动机主要零部件加工的先进工艺及其发展趋势,对我国汽车制造企业实现技术转型升级、保持或获得强劲的市场竞争力至关重要。
关键词:发动机;缸体;加工工艺伴随着电子信息技术的快速发展,社会经济水平的不断提高,人们对于汽车的需求量与日俱增,欧美等汽车制造工业比较先进的发达过期,在汽车发动机制造技术方面倾向于创新、高性能和环保。
我国传统的旧材料以及古老汽车发动机的制造技术已经不能够满足汽车行业的发展以及人们对于汽车的需求。
本文对发动机缸体加工工艺进行分析,希望能够促使我国具有更加先进、安全的汽车制造工艺,降低汽车自身的质量问题,避免出现大量交通事故。
1汽车发动机工作原理汽车的构成要素众多,发动机、底盘、车身、电气、等均是其重要的组成部分。
底盘能够保证汽车具有良好的稳定性,属于汽车的基本骨架,而发动机则与汽车的安全系数、用户的舒适程度等存在密切关联。
若发动机的质量与性能不达标,则乘车人员会发生歪斜、倾倒等问题,严重时更会增加交通事故的危险,与此同时汽车其他零部件的使用寿命亦会大幅度降低。
在发动机中,其顺畅的运行与诸多零部件有关,一般由进气曲轴活塞进行上下运动,开始进气,在活塞运动加大气缸内的容积后将会形成压强差,此时气体将会从进气门达到气缸,而活塞运动处于最下方时进气结束。
发动机的整个运行过程中所产生气体的问题能够达到400K左右。
在进气结束后发动机会进行压缩,此时的活塞运动方向改为由下至上没进气门与排气门均要关闭,气缸体积减小,气体会发生压缩混合。
而后,发动机的气体开始做功,该过程中会由火花塞将压缩混合形成的气体点燃,在高温与高压的影响下活塞将从下至上进行做功。
最后,发动机需要排气,即排气门需要打开,进气门需要关闭,曲轴通过连杆推动活塞,促使活塞继续由下至上运动,达到最上方时代表完成排气。
- 1、下载文档前请自行甄别文档内容的完整性,平台不提供额外的编辑、内容补充、找答案等附加服务。
- 2、"仅部分预览"的文档,不可在线预览部分如存在完整性等问题,可反馈申请退款(可完整预览的文档不适用该条件!)。
- 3、如文档侵犯您的权益,请联系客服反馈,我们会尽快为您处理(人工客服工作时间:9:00-18:30)。
引言气缸体总成是由气缸体和曲轴箱组成的关键组件,它不仅是内燃机各机构、系统的装配基体,其本身的许多部位又是曲轴连杆机构、配气机构、供给系统、冷却系统和润滑系统的组成部分。
气缸体总成上各孔、各面及相互之间均有较高的尺寸、形状和位置公差要求,其加工难度很大。
气缸体总成的样式加工均使用通用工艺设备,加工工艺过程可分为气缸体和曲轴箱零件的粗加工、半精加工和气缸体总成组件的精加工、关键部位的细加工四个阶段。
整个工艺过程的关键环节是各加工阶段工艺基准的选择、关键部位(主轴孔、缸孔、凸轮轴孔)的加工和重要尺寸(主轴孔、凸轮孔、惰轮孔三孔孔心距坐标尺寸)的计算。
2 各加工阶段工艺基准的选择1.毛坯划线基准的选择毛坯划线基准的选择关系到毛坯各部位加工余量的均匀性和重要部位壁厚的均匀性。
从设计角度考虑,气缸体和曲轴箱的理想划线基准应为:高度方向以通过主轴孔中心线且垂直于缸孔轴线的平面为基准;长度方向以对称线为基准;宽度方向以1~6缸的孔心连线为基准。
从使用角度考虑,理想的划线基准应为:高度方向以底面平面为基准;长度、宽度方向的粗基准应能满足6个气缸孔壁厚均匀的要求,这是因为气缸盖与气缸孔内缸套内壁共同组成燃烧室,缸壁需在高温、高压下工作,如缸壁壁厚不均匀,容易引起缸壁热变形而导致严重事故发生。
在首批气缸体毛坯划线过程中发现,由于制造泥芯下偏,使铸件缸孔中心偏离设计中心1.5~2mm,此时,若以1~6 缸孔孔心连线为基准,则会导致6 个缸孔壁厚不均匀。
为确保缸孔壁厚均匀,根据气缸体铸造特点,选择1~6 缸外壁作为划线的校正基准,较好地解决了壁厚不均匀问题。
图1 确定毛坯划线基准操作示意图确定气缸体毛坯划线基准的操作方法如图1 所示。
将气缸体横卧,用三个千斤顶支在工作平台上(见图1a),前后方向用直角尺以底面基准线校正,调整左右千斤顶,从出砂孔处用高针以1~6 缸外壁校平,以其中某一缸外壁上下平分,划出6个缸的中心连线,此线即为宽度方向的基准线。
将气缸体竖立支在工作台上(见图1b),以上述相同方式划出长度方向的基准线。
2.气缸体与曲轴箱半精加工基准的选择气缸体和曲轴箱是典型的箱体类零件,其加工基准最好采用两销定位。
因此,在半精加工各部位前,首先在气缸体和曲轴箱底面加工2-Ø15H7孔,同时半精铣底面,这样使形成以两零件底面和底面上的2-Ø15H7孔组成的一面两个定位基准。
应当指出,2-Ø15H7孔的粗基准也是1~6缸外壁。
一面两孔基准建立后,各部位加工尺寸应转换为以主定位销孔为起点的尺寸。
2-Ø15H7孔“工艺基准”的建立原则为:①在对角线上的分布应尽量远;②孔距精度±0.005mm;③确保各被加工面的加工余量均匀;④使2-Ø15H7孔在加工过程中贯穿时间较长。
3.精加工基准的转换当气缸体机和曲轴箱各部位半精加工完成后,将两零件用3个定位销和14个M18螺栓连接起来,组成气缸体总成。
此时,气缸体和曲轴箱的零件加工基准面——底面已被连接,所以需重新建立总成的加工基准。
从气缸体总成的结构形式来分析,总成顶面与气缸盖相连接,对平面度和表面粗糙度要求较高,因此该平面是较理想的加工基准面;而总成底面与油底壳相连接,也有较高的平面度和表面粗糙度要求,且该面上还有2-Ø15H7销孔可与底面和两孔组成一面两孔的加工基准。
从加工和测量角度分析,精加工主轴孔和凸轮轴孔时,若以底面和其上的2-Ø15H7孔定位时,因顶面除有6个缸孔外,其余均为实体结构,这将给对刀和测量带来不便;若以顶面定位,由于底面结构上有6个较大的开放空间,便于对刀、测量和观察。
在实际加工中,选择以总成顶面在工作台上定位,以底面上2-Ø15H7孔精确校正后,在总成侧面铣出一工艺平面,该工艺平面与顶面组成新的精加工基准。
3 关键部位的加工气缸体总成上关键部位(缸孔、主轴孔、凸轮轴孔)的加工至关重要。
三孔的尺寸、形状和位置之差均有较高精度要求,且孔的表面粗糙度要求也校严格,三孔的加工精度直接影响柴油机的整体性能和寿命。
三孔的结构和精度要求如图2 所示。
图2 缸孔、主轴孔、凸轮轴孔的结构及精度要求1.缸孔的加工WD618气缸体总成上有6个Ø130H6(+0.025mm)缸孔,其圆柱度要求为0.01mm,对主轴孔中心线的垂直度要求为0.02mm,对主轴孔中心线和后端面的位移度要求为Ø0.3mm,表面粗糙度要求为R Z6.3µm,a.精细加工设备及加工基准缸孔的精加工在T42100 双立柱坐标镗床上完成;缸孔的细加工则在MB4220×100 半自动立式珩磨机上完成。
加工基准是以总成底面和底面上2-Ø15H7孔组成的一面两孔定位基准。
b.精、细加工工艺处理在德国生产的BFT90/3 卧式镗床上粗镗各缸孔,留余量1.5~2mm;在T42100坐标镗床上半精镗各缸孔,留余量0.4~0.5mm;在T42100坐标镗床上以总成底面和2-Ø15H7孔定位,精镗各缸孔,留研量0.05~0.07mm;在MB4220×100半自动立式珩磨机上以底面及2-Ø15H7孔定位,珩磨各缸孔达到图纸要求。
2.主轴孔的加工主轴孔是由7个Ø110H6(+0.022mm)孔组成,其圆柱度要求为0.01mm ,同轴度要求为Ø0.02mm ,表面粗糙度要求为R Z 10µm 。
a. 精细加工设备及加工基准主轴孔的精加工在个42100坐标镗床上完成;主轴孔的细加工则在德国生产的BFT90/3 卧式镗床上完成。
加工基准采用以顶面在工作台上定位,以侧工艺面校正,再以底面上的2—Ø15H7孔精校正。
b. 精、细加工工艺处理在BFT90/3卧式镗床上粗镗气缸体和曲轴箱上各半圆孔,留余量3mm ;气缸体和曲轴箱各部位粗加工或半精加工后进行把合,形成气缸体总成组件;在T42100 坐标镗床上定位、校正后压紧,校正镗杆平行度<0.005mm(以工作台为基准),半精镗主轴孔至Ø109.5+0.05mm ,松动总成组装螺栓去应力后重新把合;在T42100 坐标镗床上校正工件及镗杆后,用浮动镗刀将主轴孔Ø109.5+0.05mm 尺寸加工至Ø109.85±0.01mm ,表面粗糙度R a 1.6µm ;在BFT90/3卧式镗床上,将总成前面对准镗床主轴,以顶面及侧工艺面校正X 、Y 方向,以主轴孔自身校正轴心后压紧,精镗第一、二孔至Ø110±0.005mm ;将加工主轴孔的枪铰刀(见图3)轴部与机床主轴联接,校正联接套内孔径跳<0.01mm ,铰刀头部放入第一二孔内定位、导向,选用切削速度v=20~30mm/min ,转速n=85r/mm ,进给量s=0.08~0.12mm/r ,精铰主轴孔,使之达到图纸要求。
加工时应注意:①当枪铰刀从第二孔进给至第三孔时,应将进给量S 严格控制在0.08~0.1mm/r 范围内,此时枪铰刀的压光刀可将第一、二孔充分压光。
②铰完第三孔后,可提高进给速度,快速进给至第四孔,以后各孔均按此处理。
③在整个铰孔过程中应对刀刃部分充分冲洗,及充分冷却,以防止铰刀与孔发生粘连。
3. 凸轮轴孔的加工凸轮轴孔由7 个Ø65H7(+0.030mm)孔组成,其同轴度要求为0.02mm ,对总成前面、惰轮孔和Ø17H7孔的位移度要求为0.05mm ,表面粗糙度要求为R z 16µm 。
凸轮轴孔的加工机床、加工基准和工艺 图3 加工主轴孔用枪铰刀处理方法与加工主轴孔相同,只是因孔径较小,切削参数可选为:转速n=125r/mm ,进给量s=0.1mm/r 。
4 重要尺寸的计算气缸体总成上的主轴孔、凸轮轴孔和惰轮孔三孔坐标尺寸的计算较为重要。
设计给出的三孔坐标关系见图4。
1. 坐标尺寸的计算由图4可知:L OA =110+0.05mm ,L AB =151.3+0.05mm ,X 0-A =42.295,Y 0-B =118.5。
在∆ACO 中,有cos α=(X 0-A /L OA )=42.295/110=0.3845,因此α=67°23'14"。
又因为sin α=Y 0-A /L OA ,因此Y 0-A =L OA sin α=101.544。
从图4可得Y A-B =Y 0-B Y 0-A =118.5-101.544=16.956。
在∆ADB 中, X A-B =(L AB 2-Y A-B 2)½=150.347,因此,X 0-B =X A-B -X 0-A =150.347-42.295=108.052。
由此可得各孔坐标尺寸为:A 孔:X 0-A =42.295,Y 0-A =101.544;B 孔:X 0-B =108.052,Y 0-B =118.5。
2. 坐标尺寸之差的计算3. 采用坐标法加工孔系的孔距精度由坐标位移精度间接保证,因此,可用求解尺寸链的方法来确定各坐标尺寸的公差。
4. 在图4中,孔心距尺寸L OA 是由坐标尺寸X 0-A 和Y 0-A 间接保证的,孔心距尺寸L OB 是由坐标尺寸X 0-B 和Y 0-B 间接保证的,而孔心距尺寸L AB 是镗完A 、B 孔后自然获得的,因此,它是由X 0-A 、Y 0-A 、X 0-B 、Y 0-B 四个坐标尺寸间接决定的。
由于L OA 、L AB 的公差值均为0.05mm ,而L OB 的公差大于0.05mm ,因此,只要能满足L AB 的公差要求,各坐标尺寸所确定的公差就能满足L OA 和L OB 的要求。
由此可见,根据这一尺寸链关系即可确定各坐标尺寸的公差。
为计算方便,可分解为图5所示的几个简单尺寸链来计算。
图4 三孔坐标关系图5 三孔尺寸链图5.由图5a可得L AB=(X A-B2-Y A-B2)½(1) 6.对式(1)取全微分分并以微小增量∆L AB、∆X A-B和∆Y A-B代替各偏微分时,便可得到增量关系式为∆L AB ∂L ABX A-B+∂L ABY A-B=X A-B∆X A-B Y A-B∆Y A-B∂X A-B∂Y A-B L AB L AB(2)7.令∆X A-B=∆Y A-B=ε,则ε=L AB∆L ABX A-B+Y A-B(3) 8.将上面计算的各坐标数值代入式(3),可得ε151.3×(±0.025)0.023(mm) 150.347+16.9569.X A-B和Y A-B不是加工中直接得到的坐标尺寸。