自动配料装车系统控制
自动配料控制系统文献综述

自动配料控制系统文献综述1 前言自动配料系统在轻工、纺织、塑料、食品、制药、化工等行业得到了广泛应用,并具有很好的发展前景。
通过许多关于自动配料控制系统的文献,设计出自动配料系统具有通用性强、自动化程度高、工作可靠性高、人机界面友好、可进行远距离控制、成本低廉等特点。
当前针对某一行业, 配料仪器所用传感器种类、量程基本固定,配料的种类数基本固定, 因此, 目前的配料仪器产品使用场合单一, 针对不同行业, 要设计出不同的配料仪器, 使大批量生产难于实现, 这就使得资源的利用率不高, 产品生产成本过高。
因此, 能够开发出可适配多种不同类型的传感器, 具有智能去皮、精确配料、配料种类数由操作人员选择的新型配料仪, 具有广泛的应用价值。
本设计就是以基于单片机为核心, 设计出能适配不同种类传感器和应用于不同行业的通用型自动配料仪。
2 国内外现状近年来我国的配料工业发展迅速,小型配料系统的设备性能有了很大提高。
自动配料装置的核心设备是配料秤,配料秤性能好坏,将直接影响配料质量的优劣。
用微机代替控制仪表进行称量配料,可以对称量误差进行自动补偿,保证配料的准确性,通过微机的键盘和显示器方便进行人机对话,还科研调用管理完成参数设置,检查和修改工艺设定值,并监视称量配料的生产过程,发现故障及时报警,通过打印机及时打印生产报表,自动完成统计工作。
这样,可以降低原料消耗,提高产品质量,实现生产过程的实时动态监视,配料精度低主要原因是电子秤系统的动态范围小,而可靠性主要是中间继电器和过程控制的微机控制系统的可靠性低所致,针对实际问题,采用可编程控制器来代替中间的继电器和过程控制的微型机,为了实现生产过程的动态监视,使用微型机与PLC通信,在屏幕上显示出动态生产数据。
可靠性是重要的质量指标,由于机械工艺,电子元件等基础,工业发展的滞后,国内电脑配料系统可靠性与国外产品相比尚有一定差距。
主要面临的问题是:( 1)不同行业使用的传感器不同, 输出的电信号不同, 这就给信号的初期放大处理和程序设计带来困难。
可编程控制器PLC实验、实训教学大纲

《PLC应用与组态设计实验、实训》课程教学大纲一、课程基本信息二、课程教学目标本实验、实训任务是《PLC应用与组态设计》课程教学中的实验、实训教学环节,使学生进一步丰富感性认识,加深了解PLC的基本结构、工作原理、编程技能等;掌握PLC应用与组态设计的专业技能;牢固树立电气工程及其自动化工程观念,提高分析电气工程及其自动化工程问题的综合能力。
三、教学学时分配四、教学内容和教学要求实验一 PLC认知-电机正反转模拟实验(4学时)(一)实验的目的和要求通过实验了解PLC软硬件结构及系统组成,掌握PLC外围直流控制及负载线路的接法及上位计算机与PLC通信参数的设置,初识PLC语句表、梯形图语言。
(二)实验内容或原理实验基于天煌教仪THPFSL-1/2型可编程控制器技能实训装置(三菱)-电机正反转模拟实验1. 认知三菱FX系列PLC的硬件结构,详细记录其各硬件部件的结构及作用;2. 打开编程软件,用语句表或梯形图语言编写基本的与、或、非程序段,并下载至PLC中;3.正确完成PLC端子与电机正反转模块等的连接操作;4. 验证并监控系统能否正常运行;(三)实验报告1.详细描述FX系列PLC的硬件结构;2,总结出上位计算机与FX系列PLC通信参数的设置方法;3. 用语句表和梯形图语言编写本次实验程序;4. 画出PLC接线图。
实验二PLC编程元件-四节传送带控制实验(4学时)(一)实验的目的和要求通过实验了解工程传送带控制要点,掌握FX系列PLC编程元件:输入继电器、输出继电器、辅助继电器、定时器的使用及编程技能;掌握四节传送带控制系统的接线、调试、操作。
(二)实验内容或原理实验基于天煌教仪THPFSL-1/2型可编程控制器技能实训装置(三菱)--四节传送带控制实验1.掌握FX系列PLC编程元件:输入继电器、输出继电器、辅助继电器、定时器的使用及编程;2. 打开编程软件,用FX系列PLC编程元件编写程序段,并下载至PLC中;3. 正确完成PLC端子与四节传送带控制系统模块的接线、调试、操作;4. 验证并监控系统能否正常运行;(三)实验报告1.详细描述四节传送带控制要求;2,画出PLC I\O配置表、PLC接线图3. 用PLC编程元件编写本次实验程序;4. 描述调试过程;5. 总结定时器指令的使用方法及注意事项。
基于顺序功能图的自动配料控制系统设计

基于顺序功能图的自动配料控制系统设计作者:王秀来源:《山东工业技术》2017年第22期摘要:顺序功能图是一种专用于工业顺序控制的图形化编程语言,它能把复杂的梯形图程序简化为每个状态里的简单动作程序。
自动配料控制系统控制要求较高而且电机启停都符合顺序控制,所以本文提出了采用功能图法来实现自动配料控制系统的软件设计。
实践证明其实现过程比较直接简单、容易理解,避免了梯形图法编制自动配料程序中逻辑复杂、不好理解的缺陷。
关键词:顺序功能图;PLC;自动配料;梯形图DOI:10.16640/ki.37-1222/t.2017.22.1140 引言可编程控制器的编程语言主要有梯形图、顺序功能图、语句表等,但是使用较为广泛的是梯形图和顺序功能图两种语言[1]。
梯形图是在继电器控制系统的电气原理图的基础上变化而来的,它的电气逻辑关系表示方法和电气原理图是相同的,所以梯形图语言入门比较容易,一直是最常用的一种编程方法,但是梯形图在处理复杂控制问题时,显得力不从心而且有时感觉无从下手,即使能勉强编制出来复杂顺序梯形图,该程序也逻辑关系复杂且很难理解。
顺序功能图语言是一种真正的图形化编程语言,非常擅长处理复杂顺序问题,是专用于工业顺序控制的一种功能性程序设计语言,不管顺序有多复杂,它都能以图形的方式把问题表达或叙述清楚[2,3]。
1994年5月,IEC公布的PLC标准中,顺序功能图被确定为PLC的位居首位的编程语言。
本文选用德国西门子S7-200PLC为自动配料的控制器来介绍功能图编程语言在自动配料中的应用。
1 顺序功能图顺序功能图用近似流程图来表达控制过程,主要由状态(或步)、有向连线、转移、动作组成。
顺序功能图设计法最基本的设计思想就是将系统的一个工作周期划分为若干个顺序相连的阶段,这些阶段称为状态(或步),并用编程元件(M或S)来代表个状态。
状态是根据输出量的状态来划分的,在任何一个状态之内,各输出量的ON/OFF状态不变[4,5]。
自动配料控制系统的设计
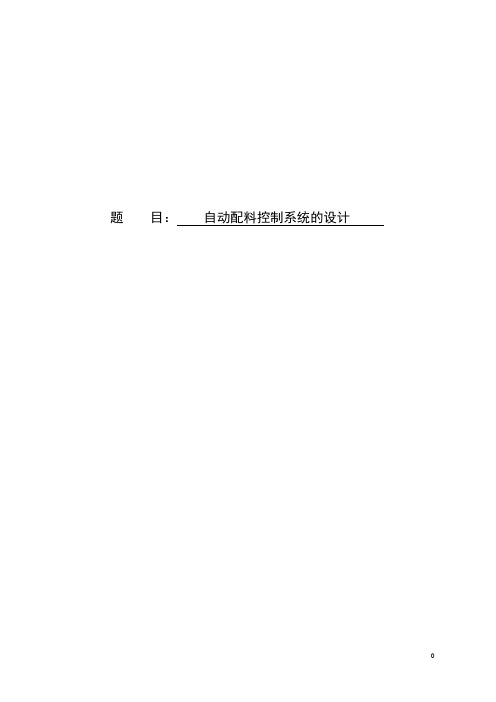
题目:自动配料控制系统的设计内容摘要自动配料系统是一种在线测量动态计量系统,集输送、计量、配料、定量等功能于一体,在冶金、建材、化工、饲料加工等行业中得到广泛应用。
设计开发自动配料优化控制系统,对于改善劳动条件、提高产品质量和生产效率具有十分重要的现实意义。
本文首先对自动配料系统的应用背景、发展趋势进行了综述,针对当前配料生产企业工艺水平相对落后、自动化水平低、生产效率低等不足,设计了一个自动配料优化控制系统,系统能够工作在全自动、远程手动以及本地手动三种模式下。
在硬件设计上,采用工控机与PLC相结合的总体控制结构,由工控制机实现系统的管理和远程监控,PLC完成设备级的动作控制及相关信号的处理,通过以太网及RS-485总线实现系统的联接与通信;改进了配料车定位系统,利用设计的定位盒实现位置编码方案,提高了定位精度。
在软件设计上,设计开发了画面实时监控和数据库管理(SCADA)等上位机应用软件,能够保存产品配方、料仓数据、实时数据等,并能够实现历史数据查询、报表打印、实时数据及状态显示、远程控制等功能,两台上位机数掘库能够有效地保持同步。
设计了下位机PLC主控程序以及通信、配料精度控制和配料车行走子程序。
针对配料系统普遍存在的配料落差控制问题,采用了一种基于模糊自适应结合PID的复合型预测控制算法,算法将模糊自适应控制宽范围快速调节和PID精确调节的特点有机结合起来,当系统的偏差大于某一设定值时,采用结合了人的经验的模糊自适应规则控制,当系统偏差小于设定值时采用PID控制,模糊控制器的两个输入分别为系统期望值和偏差,通过不同的期望值,预测不同的空中落差,并通过仿真实验证明了该方法的有效性;针对批量生产时的工作效率问题,通过对两台配料车工作时序的认真分析,建立了系统的数学模型,并利用遗传算法进行寻优,精心设计了遗传算子,求解出了最大工作效率所需的两台配料车的最佳行走路径,解决了配料车行走路径的优化问题。
自动配料系统模拟实验之欧阳德创编

摘要PLC,即可编程序控制器,是一种数字式运算操作的电子系统,专为在工业环境下应用而设计。
PLC 具有通信联网功能,它使PLC与PLC之间、PLC与上位计算机以及其他智能设备之间能够交换信息,形成一个统一的整体,实现分散集中控制。
多数PLC具有RS-232接口,还有一些内置有支持各自通信协议的接口。
组态软件由于计算机的普及和其本身价值(实时多任务、开放性、灵活性、通用性和可靠性)被认知,也在快速发展中。
本文基于PLC和组态软件设计自动配料系统。
利用S7-200系列PLC对自动配料系统进行控制,运用与之相配的STEP7编程,通过LAD编程语言编制了上位机的控制程序,从而使该配料系统可以按要求完成自动配料,装料全过程。
重点描述了包括硬件设计、编程环境及软件设计在内的西门子PLC在配料装料系统中的一些细节,以及PLC与上位机之间的通讯。
主要设计了小车装料的全过程,进行PLC外部连接线,模拟实验,通过观察指示灯的亮灭情况,对装料配料系统进一步理解。
关键词:可编程序控制器;配料装料;通信;组态软件目录1 概述11.1 PLC的定义11.2 PLC的分类11.3 PLC的主要功能11.4 PLC的特点21.5 PLC的工作原理22 自动配料系统模拟实验——硬件设计42.1 控制要求42.2 PLC的选择42.3系统设计流程示意图72.4 输入输出列表82.5 自动配料系统实验模板82.6 I/O接线图93 自动配料系统模拟实验——软件设计93.1设计梯形图93.2语句表设计错误!未定义书签。
4 传送系统调试185 结束语19参考文献201 概述1.1 PLC的定义PLC为Programmable Logic Controller的英文缩写,即可编程序控制器。
可编程序控制器是一种数字运算操作的电子系统,专为在工业环境下应用而设计。
它采用了可编程序的存储器,用来在其内部存储执行逻辑运算、顺序控制、定时、计数和算术运算等操作的指令。
煤矿的自动装车系统

煤矿自动装车系统0 引言铁路快速装车系统是一种将散装物料按规定的质量快速连续的称量并装入列车车厢的系统,具有一次称量、一次装载、速度快、精度高等特点。
当前在大型煤矿、非煤矿山等企业使用已经非常广泛,但由于受铁路技术水平及检测技术的影响,我国现有装车系统至今没有一家实现全自动控制。
某些环节仍然停留在手动、半自动装车的水平。
我国煤矿的重车称量是与装车同步进行,一种方式是轨道衡置于跨线煤仓仓口或胶带输送机卸料口下方,边装车边称量,通过称量控制装车;另一种方式是跨线多煤口装车线,轨道衡置于跨线煤仓出口,人工预装车后称量,多退少补,往返儿次才能达到准确装车。
随着电了称重业的发展,日前国外己采用大型定量仓快速装车系统,预先在定量仓中按车皮标重自动预装仓,待列车车厢行进经过定量仓仓口时,自动按车厢标重装车,实现快速、准确装车。
快速定量装车系统主要由输煤系统、定量装车机械设备、三级自动取样系统设备、液压控制系统、电脑监控系统等组成。
1 快速定量装车系统功能设计快速定量装车系统通过计算机采集主上煤带式给料机、主上煤带式输送机及各种现场设备的信号,处理接收操作指令后发出正确的控制指令,实现自动连续调节给料、定量自动装车、二级取样、清单打印、动态图面显示等功能。
1.1 装车操作者选定与机车(或调车绞车)的速度、车型相适应的给料量后,被选择的给料机给料,给料量随时由输送带秤(核了秤)反映出来,在计算机内部与设定的给料量比较,从而调节给料机给料量,两者协调一致,确保了装车的连续和稳定值,保证了连续自动调节给料。
当列车到装车塔下时,由系统控制放下装车溜槽,此时缓冲仓料位己到合适的位置。
操作者按下称重循环按钮后,缓冲仓下的4个配料液压平板闸门自动地向定量仓中卸料,同时称重传感器准确地称重、控制完成定量配料。
其后,由闸门控制向车厢中放料,料量放足后由称重传感器控制排料平板闸门关闭。
而后车辆行驶车厢之间的空档距离,这期间缓冲仓又向定量仓继续配料,为下一车厢装车作准备,从而实现连续定量自动装车。
混凝土搅拌站自动化控制系统的介绍

混凝土搅拌站自动化控制系统的介绍混凝土搅拌站自动化控制系统的介绍1. 什么是混凝土搅拌站自动化控制系统?混凝土搅拌站自动化控制系统是一种通过现代化技术手段来实现混凝土搅拌过程的自动控制与管理的系统。
它利用计算机、传感器、执行器等设备和技术,实现混凝土搅拌站各个环节的智能化控制和监测。
2. 混凝土搅拌站自动化控制系统的组成和工作原理混凝土搅拌站自动化控制系统由硬件和软件两部分组成。
硬件部分包括控制器、传感器、执行器等设备,软件部分包括控制程序和人机界面。
它们通过各个设备之间的信号传递和数据交换,实现对混凝土搅拌站各个环节的精确控制和监测。
混凝土搅拌站自动化控制系统的工作原理如下:- 传感器采集站点内各个环节的数据,例如混凝土配料的参数、搅拌车的位置等。
- 传感器将采集到的数据通过信号传递给控制器。
- 控制器根据预设的参数和算法,对传感器采集到的数据进行处理和分析,并产生相应的控制指令。
- 控制指令通过执行器控制站点内各个设备的运行,实现对混凝土搅拌过程的自动控制。
- 人机界面可以实时显示站点内各个环节的数据和运行状态,以及提供操作和参数设置等功能。
3. 混凝土搅拌站自动化控制系统的优势和应用- 提高生产效率:自动化控制系统可以精确控制混凝土搅拌过程中的各个参数,确保混凝土的质量稳定,并且可以根据需要进行自动化配料和搅拌,提高生产效率。
- 降低人工成本:自动化控制系统能够减少对人工操作的依赖,降低人工成本,并且可以减少人工操作带来的错误和事故风险。
- 提高质量稳定性:自动化控制系统可以实时监测混凝土搅拌过程中的各个参数,并能够及时调整控制指令,确保混凝土的质量稳定。
- 减少资源浪费:自动化控制系统可以根据需要进行自动化配料,避免了人工操作带来的浪费和误差。
- 应用范围广泛:混凝土搅拌站自动化控制系统适用于各种混凝土搅拌站,提供了稳定可靠的自动化控制解决方案。
4. 我对混凝土搅拌站自动化控制系统的观点和理解混凝土搅拌站自动化控制系统是现代化建筑施工中不可或缺的重要技术装备。
散装物料定量自动装车系统

SerialNo.620December.2020现 代 矿 业MODERNMINING总第620期2020年12月第12期 赵铁华(1960—),男,董事长,高级工程师,300384天津市高新区海泰发展六道6号。
散装物料定量自动装车系统赵铁华1 肖同武1 李 蔚1 王 宇1 王 燕2(1.天津华通自动化控制有限公司;2.天津华通网络工程有限公司) 摘 要 为了顺利推进散装物料定量自动装车系统的应用,分析了砂石骨料无人智能化定量自动装车系统与传统化手工装车的区别及优势,简述了无人智能化定量自动装车系统的实现与应用。
从投入成本、物流速度、设备成本、人员职业安全及健康等多角度考虑,定量自动装车系统更符合企业可持续的快速发展,可为企业发展助力。
关键词 砂石骨料 定量装车 自动装车 无人装车DOI:10.3969/j.issn.1674 6082.2020.12.050 砂石骨料是建筑、道路、水利水电等工程建设不可或缺的主要材料。
我国是世界上最大的砂石生产国和消费国,市场需求量的不断增长推动了该行业生产规模的大型化、生产方式的智能化,同时也要求货物的发运方式与之相匹配,而现实情况是发运方式并未有太大的变化,不少仍然沿用原始的手工放料方式,这会带来诸多问题,且不符合企业的高质量发展要求。
1 传统手工放料的缺点人工放料主要由人手工操控放散设备,以肉眼判断车辆停放位置和放料质量,进行各种物料的下料。
在人工放料期间,需要工作人员不停地与车辆驾驶人员沟通,通过车辆挪动以观察料面情况,车辆有时需要往复移动多次才能结束装车,这种方式效率很低。
个别放料设备加装有简单的传感设备,以解决罐装车辆装料过程中料高实时回馈问题,但由于砂石骨料的流动特性,下料质量的精度问题依旧存在。
对于物料密度相对比较大的骨料产品,放料所耗时间更长,放料的结果更加依赖于放料人员的经验。
砂石骨料生产集约化、规模化后,为加快物流发运速度,企业在建设时加大了放料设备的投入,增加了放料设备的数量,如果还以传统方式工作,就要求企业配备更多的人力来满足发运的需求。
- 1、下载文档前请自行甄别文档内容的完整性,平台不提供额外的编辑、内容补充、找答案等附加服务。
- 2、"仅部分预览"的文档,不可在线预览部分如存在完整性等问题,可反馈申请退款(可完整预览的文档不适用该条件!)。
- 3、如文档侵犯您的权益,请联系客服反馈,我们会尽快为您处理(人工客服工作时间:9:00-18:30)。
自动配料装车系统控制
一、控制要求
1.总体控制要求:如面板图所示,系统由料斗、传送带、检测系统组成。
配料装置能自动识别货车到位情况及对货车进行自动配料,当车装满时,配料系统自动停止配料。
料斗物料不足时停止配料并自动进料。
2.打开“启动”开关,红灯L2灭,绿灯L1亮,表明允许汽车开进装料。
料斗出料口D2关闭,若物料检测传感器S1置为OFF(料斗中的物料不满),进料阀开启进料(D4亮)。
当S1置为ON(料斗中的物料已满),则停止进料(D4灭)。
电动机M1、M2、M3和M4均为OFF。
3.当汽车开进装车位置时,限位开关SQ1置为ON,红灯信号灯L2亮,绿灯L1灭;同时启动电机M4,经过1S后,再启动M3,再经2S后启动M2,再经过1S最后启动M1,再经过1S后才打开出料阀(D2亮),物料经料斗出料。
4.当车装满时,限位开关SQ2为ON,料斗关闭,1S后M1停止,M2在M1停止1S后停止,M3在M2停止1S后停止,M4在M3停止1S后最后停止。
同时红灯L2灭,绿灯L1亮,表明汽车可以开走。
5.关闭“启动”开关,自动配料装车的整个系统停止运行。
二、面板图
三、功能指令使用及程序流程图
1.增/减计数器指令使用
增/减计数指令(CTUD),在每一个增计数输入(CU)从低到高时增计数;在每一个减计数输入(CD)从低到高时减计数。
当当前值大于或者等于预置值(PV)时,计数器位(C0)接通。
否则,计数器关断。
当复位输入端(R)接通或者执行复位指令时,计数器被复位。
当达到预置值(PV)时,CTUD计数器停止计数。
2.程序流程图
四、端口分配及接线图
2.PLC外部接线图
五、操作步骤
1.检查实训设备中器材及调试程序。
2.按照I/O端口分配表或接线图完成PLC与实训模块之间的接线,认真检查,确保正确无误。
3.打开示例程序或用户自己编写的控制程序,进行编译,有错误时根据提示信息修改,直至无误,用PC/PPI通讯编程电缆连接计算机串口与PLC通讯口,打开PLC主机电源开关,下载程序至PLC中,下载完毕后将PLC的“RUN/STOP”开关拨至“RUN”状态。
4.打开“启动”开关后,将S1开关拨至OFF状态,模拟料斗未满,观察下料口D2、D4工作状态。
5.将SQ1拨至ON,SQ2拨至OFF,模拟货车已到指定位置,观察L1、L2和电动机M1、M2、M3及M4的状态。
6.将SQ1拨至ON,SQ2拨至ON,模拟货车已装满,观察电动机M1、M2、M3及M4的工作状态。
7.将SQ1拨至OFF,SQ2拨至OFF,模拟货车开走。
自动配料装车系统进入下一循环状态。
8.关闭启动开关后,自动配料装车系统停止工作。
六、总结
在我看来,课程设计是最能让人掌握知识的,这是我从多次的课程设计中总结出来的,也就是因为有这个原因,我把每次的课程设计都当成是一份工作或者说是一种挑战,端正态度,秉着认认真真的态度去对待此次课程设计,争取做到比以前更好。
在整个过程中,每一天都是很忙,每天都有忙不完的事情。
本来按照计划是可以正常完成的,但是所有的事情全部挤在一起,真是计划赶不上变化,做课程设计的时间缩短了不少,时间短并不能成为我不能完成的借口,俗话说,时间是挤出来的,起早贪黑的日子并不可怕,习惯成自然才是真理。
在整个设计的过程中,并不是那么顺利,完美总是可望而不可求的,不在同一个地方跌倒两次才是最重要的,抱着这个心理我一步步走了过来,最终完成了我的任务。
十几天的PLC课程设计结束了,不管怎么样还是顺利完成了,真的是万事开头难。
对于这样的课程设计,最主要的还是得掌握其工作过程,然后在从过程中去扩展去升华。
利用两天的时间弄懂其工作过程,利用一天的时间编写顺序功能图和梯形图,用两天时间进行调试,写报告对于我来说,是多么痛苦的事情,苦恼涉及到的种种图比较多,设计是一个比较耗费时间的过程。
其实不然,对自己的设计做一个总结,也能帮助自己发现设计里还存在哪些缺陷。
很多东西只有在自己尝试过后才知道其艰辛,知识在实践后才看到它的价值,真所谓是实践出真知。
附录A。