自动上料配料系统方案.(DOC)
自动配料系统的解决方案
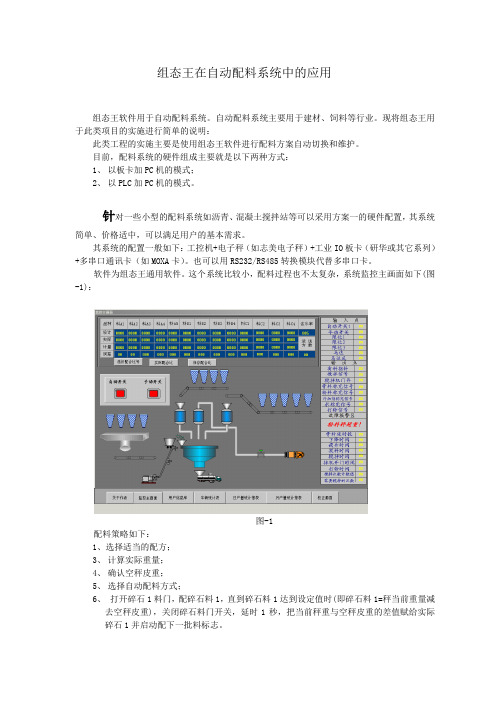
组态王在自动配料系统中的应用组态王软件用于自动配料系统。
自动配料系统主要用于建材、饲料等行业。
现将组态王用于此类项目的实施进行简单的说明:此类工程的实施主要是使用组态王软件进行配料方案自动切换和维护。
目前,配料系统的硬件组成主要就是以下两种方式:1、以板卡加PC机的模式;2、以PLC加PC机的模式。
针对一些小型的配料系统如沥青、混凝土搅拌站等可以采用方案一的硬件配置,其系统简单、价格适中,可以满足用户的基本需求。
其系统的配置一般如下:工控机+电子秤(如志美电子秤)+工业IO板卡(研华或其它系列)+多串口通讯卡(如MOXA卡)。
也可以用RS232/RS485转换模块代替多串口卡。
软件为组态王通用软件。
这个系统比较小,配料过程也不太复杂,系统监控主画面如下(图-1):图-1配料策略如下:1、选择适当的配方;3、计算实际重量;4、确认空秤皮重;5、选择自动配料方式;6、打开碎石1料门,配碎石料1,直到碎石料1达到设定值时(即碎石料1=秤当前重量减去空秤皮重),关闭碎石料门开关,延时1秒,把当前秤重与空秤皮重的差值赋给实际碎石1并启动配下一批料标志。
7、当配下一批料标志成立时,碎石料2料门打开,开始配碎石料2, 直到碎石料2达到设定值时(即碎石料2=秤当前重量减去空秤皮重再减去碎石料1重量),关闭碎石料门开关,延时1秒,把当前秤重时减去空秤皮重重量再减去碎石料1重量之后赋给实际碎石2,启动配下一批料标志。
运用组态王软件强大的组态功能,非常简单地实现了上述配料功能。
当配料系统为大中性的饲料加工厂等大型配料系统,由于系统较复杂,采用板卡加PC的方案显然不能满足控制要求,可以采用方案2。
该系统硬件配置为工控机+电子称(如志美电子秤)+PLC(三菱FX系列或西门子S7-200/300系列或其它系列)+DP通讯卡或其它的通信方式。
软件配置为组态王通用软件。
要配的料种类有:硅砂、方解石、备用料、硝酸钠、硼砂、纯碱、霞石、长石、小料等,计算机根据人工设定的配料量、用否选择和预先设定的时序,来自动完成整个配料过程的各类连锁和控制,工艺画面参见上图(图-1):这两类配料系统均可实现如下功能:1)实现进料、放料、搅拌、出料的自动联锁和控制;2)能实现计量、进料、放料、搅拌、出料的手动操作的功能;3)能显示实时的工作状况和各种物料参数。
自动配料模拟控制系统设计..

引言自动配料控制系统是采用PLC控制方式以及新颖的变频调速喂料机构,配合配料控制软件包,实现物料传送、配料控制、配方设计、生产数据管理等功能。
并可以通过网络实现多个配料系统的集合控制。
自动配料控制系统设计步骤:1.主电路设计,并画出接线示意图。
2. 分配I/O地址,列出分配表.3。
设计系统控制的程序框图。
4。
根据程序框图设计该系统的控制梯形图.5. 上机调试通过。
6。
利用PLC系统进行模拟运行1自动配料控制系统结构和工作原理1.1自动配料控制系统方案系统启动后,配料装置能自动识别货车到位情况及对货车进行自动配料,当车装满时,配料系统自动关闭.本设计的突出点是故障检测部分的设计,首先,当某一节传送带发生故障时,该节传送带和其前面的传送带会立即停止,该节之后的传送带会在一定的延时后停止。
其次,当某节传送带上的物体过重时,该节传送带和其前面的传送带会立即停止,并且数码显示电路会显示发生故障的电机的号码,该节之后的传送带会在一定的延时后停止。
1。
2 自动配料控制系统基本结构自动配料的模拟面板如图1.1所示,从图中可以看出四节传送带是本次设计的核心电路,PLC编程也是围绕此面板进行的图1。
1 自动配料系统图自动配料系统的功能是利用四节传送带为小车自动配料,重物通过传送带进行传输,发生故障时系统自动停机。
自动配料实验面板与PLC接线控制对应关系如表1。
1。
1所示。
表1。
1。
1 输入/输出接线列表面板SB1 SB2 S1 SQ1 SQ2 D1PLC I0.0 I0。
1 I0。
2 I0。
4 I0.5 Q0。
0面板D2 D3 D4 L1 L2 M1PLC Q0。
1 Q0。
2 Q0.3 Q0。
4 Q0.5 Q0.6面板M2 M3 M4 A B CPLC Q0。
7 Q1。
0 Q1。
1 I0.6 I0。
7 I1.0面板 D I1.2 I1。
3 I1。
4 I1.51. DOP数码显示电路DOP数码显示电路如图1。
2所示。
自动化配料系统策划书
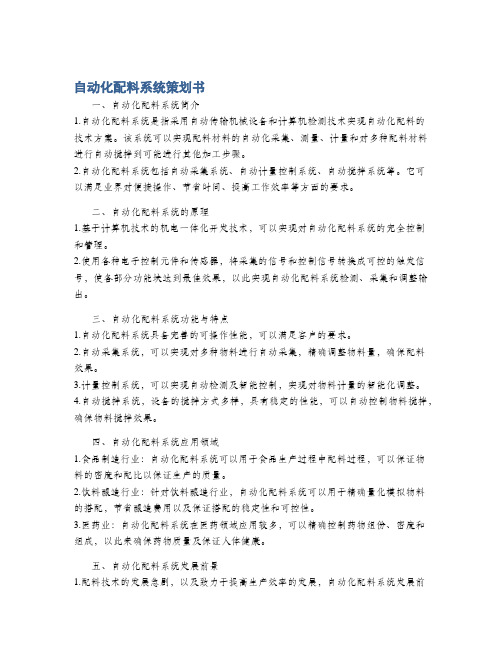
自动化配料系统策划书一、自动化配料系统简介1.自动化配料系统是指采用自动传输机械设备和计算机检测技术实现自动化配料的技术方案。
该系统可以实现配料材料的自动化采集、测量、计量和对多种配料材料进行自动搅拌到可能进行其他加工步骤。
2.自动化配料系统包括自动采集系统、自动计量控制系统、自动搅拌系统等。
它可以满足业界对便捷操作、节省时间、提高工作效率等方面的要求。
二、自动化配料系统的原理1.基于计算机技术的机电一体化开发技术,可以实现对自动化配料系统的完全控制和管理。
2.使用各种电子控制元件和传感器,将采集的信号和控制信号转换成可控的触发信号,使各部分功能块达到最佳效果,以此实现自动化配料系统检测、采集和调整输出。
三、自动化配料系统功能与特点1.自动化配料系统具备完善的可操作性能,可以满足客户的要求。
2.自动采集系统,可以实现对多种物料进行自动采集,精确调整物料量,确保配料效果。
3.计量控制系统,可以实现自动检测及智能控制,实现对物料计量的智能化调整。
4.自动搅拌系统,设备的搅拌方式多样,具有稳定的性能,可以自动控制物料搅拌,确保物料搅拌效果。
四、自动化配料系统应用领域1.食品制造行业:自动化配料系统可以用于食品生产过程中配料过程,可以保证物料的密度和配比以保证生产的质量。
2.饮料酿造行业:针对饮料酿造行业,自动化配料系统可以用于精确量化模拟物料的搭配,节省酿造费用以及保证搭配的稳定性和可控性。
3.医药业:自动化配料系统在医药领域应用较多,可以精确控制药物组份、密度和组成,以此来确保药物质量及保证人体健康。
五、自动化配料系统发展前景1.配料技术的发展急剧,以及致力于提高生产效率的发展,自动化配料系统发展前景广阔。
2.随着生产企业不断完善自动化配料系统,自动化配料系统未来将会得到更多应用,自动化配料系统将会把生产效率提高到前所未有的水平。
3.由于自动化配料系统可以降低人工开销,大大提高了运行效率,未来自动化配料系统将会是市场上重要的产品。
自动上料配料系统方案

物料输送自动上料及配料系统方案一、项目概述锂电池负极材料生产线的前端DCS自动上料及配料系统。
该系统用于以石油炼解后的附产品石焦油为主要原料,通过物理及化学反应生产人工石墨生产线的自动上料、输送,自动配料,自动投放的系统控制,实现系统在线实时监测,信息、故障提醒、生成生产记录、统计报表等。
为业主提供准确可靠的数据报表、产出量报表等。
历史气候情况:该地区属于中亚温湿气候,年平均气温为17.3℃。
其中,一月份最冷,平均气温4.7℃,历史上极端最低气温为零下15.1℃,七月份最热,平均气温29℃,极端最高温曾在8月初出现达40.4℃。
全年平均降雨量为1612毫米,最多年份达2264毫米,最少年份只有1237毫米,降雨量集中在4—6月份,占全年的54%,7—9月雨量减少,不到全年的28%。
年相对湿度平均为79%,无霜期年平均为260天左右,年日照时数达1803小时。
石焦油参数:颗粒度(D50)8~10um,常规散装堆积密度为:0.3~0.45,最低为:0.22,挤压后最大密度为:1.1 含水率:小于0.2%,物料安息角:,硬度:1-2.工艺流程要求连贯、可靠、严禁出现跑漏冒等恶性事故的发生,确保系统全年正常生产。
生产线按年度需定期检查,提起排除故障隐患。
1、用户需求分析(1)、产品规模生产要求系统具有更大的产能、更高的稳定性;(2)、降低人工上料劳动强度、改善员工工作环境、提高计量精度;(3)、粉体及液体物料均应自动上料、自动计量;(4)、每次生产的不同配方(原料配比)均可在电脑上进行操作;(5)、生产过程实现自动化控制及远程监控,同时可根据操作级别设置就地操作和急停。
(6)、对储料罐设置上限和下限报警,超限停机。
2、项目设计、制造、安装、检验标准DCS自动上料及配料系统在设计、制造和验收过程中应符合国家相关技术规范和标准,并以最新版为准。
包括但不限于下列标准:GB/T9969—2008 工业产品使用说明书总则GB/T14436—1993 工业产品保证文件GB/T6587 —1986 电子测量仪器GB/T7724—2008 称重显示控制器技术条件JJG555—1996 非自动秤通用检定规程QB 1563—2003 衡器产品型号编制方法GB/T7551—2008 称重传感器GB/T14249.1—93 电子衡器安全要求JJG649-90 数字称重显示器GB/T14249.2-93 电子衡器通用技术要求GB/T5185-1985 气焊、手工电弧焊及气体保护焊,焊缝坡口的基本形式与尺寸GB1184 形状和位置公差、未注公差的规定GB1901 公差与配合尺寸至500mm孔、轴工差带与配合GB/T1804 一般公差线性尺寸的未注公差GB1764 漆膜厚度测定法JB/TQ4000.3 焊接通用技术条件IEC/GB 电动机技术标准GB324-88 钢焊缝符号表示法GB8923 涂装钢材表面锈蚀等级和除锈等级GB9286 色漆和清漆漆膜的划格试验JB8 产品标牌JB/ZQ4000.3 焊接通用技术要求B/ZQ4286-86 包装通用技术条件GB4208 外壳防护等级分类TJ231(四) 机械设备安装工程施工及验收规范GBJ17-88 钢结构设计规范GB191-2000 包装储运图示标志GB3797-89 电控设备第二部分装有电子器件的电控设备GB4064-83 电气设备安全设计导则GB14285-93 继电保护和安全自动装置技术规程GB/T1459898-91 电气装置安装工程电气设备交接试验标准GB1497-85 低压电器基本标准二、本方案自动上料及配料系统组成生产线配料主要完从与混料机下部料仓星型给料机下部开始:通过1号物料输送机→2号物料输送机→1~12号下料器→1~12计量仓→1~12号仓下料排料阀→1~12号水平输送机→1~12号釜口气动球阀止。
原料自动配料系统方案
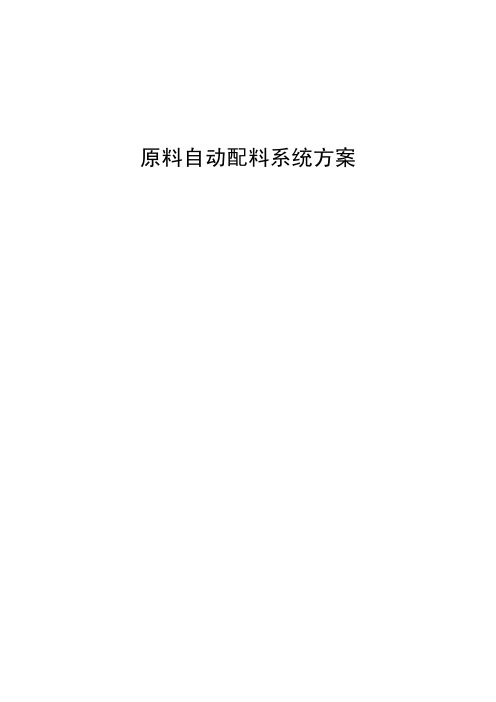
原料自动配料系统方案目录一、概述 (3)二、系统设计要求 (3)1.料仓部分: (3)2.喂料部分 (3)3.秤量部分 (3)4.物料的混合控制 (4)5.砂岩在线测水 (4)6.控制系统 (4)7.控制系统工作条件 (5)三、系统实现原则 (5)四、原料配料系统硬件简介 (5)五、原料配料系统软件功能简介 (9)1、称量管理 (9)2、系统监控 (9)3、报警监控 (10)4、实时打印 (10)5、历史数据管理 (10)6、系统权限管理 (11)7、系统冗余 (11)六、多手段的系统维护方法 (11)1、电话维护 (11)2、远程维护 (11)3、现场维护 (11)附:系统示意图 (13)工艺图 (13)配料控制室 (14)电器布置图 (15)拓扑结构图 (16)一、概述秦皇岛市海北电子技术有限公司原料连续称量配料系统采用先进的SIEMENS (西门子)PLC、工业控制计算机及PANTHER电子称量设备。
其主要组成部分包括动力部分、控制部分、喂排料部分及称量部分等,是为浮法玻璃生产设计的计算机全自动控制配料系统。
二、系统设计要求1.料仓部分:配料车间使用排仓式储料,共设粉料仓8个、碎玻璃料仓1个,粉料仓的出口处有活化漏斗(碎玻璃和石灰石用丝杠闸门),料仓的活化漏斗出口处通过软连接至喂料机的入口处,系统将根据料仓物料流动情况来决定活化漏斗的启动情况,保证物料供给的正常。
2.喂料部分喂料部分包括活化料斗和喂料设备(电磁振动给料机或螺旋输送机,根据物料的实际量程选择不同的规格)芒硝加料团破碎机。
3.秤量部分秤量部分采用三传感器电子斗秤,秤斗上安有除尘口并与集料皮带导料槽相通,以防止粉尘的外泄。
秤量系统采用“减量法”秤量方式。
排料采用电磁振动给料机。
排料应有分时操作的功能,使物料均匀的铺成夹层状态。
芒硝和煤粉先入预混机混合,预混机同其他物料同时排料。
碎玻璃均匀的撒在混合料上。
物料特征及秤台数:物料名称台数每批料用量容重水分%砂岩粉 2 2800kg(2X1400) 1.4 < 5< 2 长石 1 230kg 1.5< 2 白云石 1 700kg 1.51.05~<0.5纯碱 1 900kg1.2<0.5 芒硝 1 50kg 1.1<0.5 碳粉 1 5kg 0.5石灰石 1 230kg 1.5< 2粒度<50mm 碎玻璃 1 1600kg 1.2水秤 1 225kg中间仓复合秤 1 小于 4500kg 1.2 电子秤的静态精度:国家Ⅲ秤标准(经计量部门检定)电子秤的动态精度:95%以上的单料误差≤3个d4.物料的混合控制配合料皮带将物料通过中间复合秤放入混合机内,完成物料的混合操作。
自动上料配料系统方案

照时数达1803 小时。
物料输送自动上料及配料系统方案一、工程概述锂电池负极材料生产线的前端DCS 自动上料及配料系统。
该系统用于以石油炼解后的附产品石焦油为主要原料,通过物理及化学反响生产人工石墨生产线的自动上料、输送,自动配料,自动投放的系统把握,实现系统在线实时监测,信息、故障提示、生成生产记录、统计报表等。
为业主供给准确牢靠的数据报表、产出量报表等。
历史气候状况:该地区属于中亚温湿气候,年平均气温为17.3℃。
其中,一月份最冷,平均气温4.7℃,历史上极端最低气温为零下15.1℃,七月份最热,平均气温29℃,极端最高温曾在8 月初消灭达40.4℃。
全年平均降雨量为1612 毫米,最多年份达2264 毫米,最少年份只有1237 毫米,降雨量集中在4—6 月份,占全年的54%,7—9 月雨量石焦油参数:颗粒度〔D50〕8~10um,常规散装积存密度为:0.3~0.45,最低为:0.22,挤压后最大密度为:1.1 含水率:小于0.2%,物料安眠角:,硬度:1-2.工艺流程要求连贯、牢靠、严禁消灭跑漏冒等恶性事故的发生,确保系统全年正常生产。
生产线按年度需定期检查,提起排解故障隐患。
1、用户需求分析(1)、产品规模生产要求系统具有更大的产能、更高的稳定性;(2)、降低人工上料劳动强度、改善员工工作环境、提高计量精度;(3)、粉体及液体物料均应自动上料、自动计量;(4)、每次生产的不同配方〔原料配比〕均可在电脑上进展操作;(5)、生产过程实现自动化把握及远程监控,同时可依据操作级别设置就地操作和急停。
(6)、对储料罐设置上限和下限报警,超限停机。
2、工程设计、制造、安装、检验标准DCS 自动上料及配料系统在设计、制造和验收过程中应符合国家相关技术标准和标准,并以最版为准。
包括但不限于以下标准:削减,不到全年的28%。
年相对湿度平均为79%,无霜期年平均为260天左右,年日GB/T9969—2022 工业产品使用说明书总则GB/T14436—1993 工业产品保证文件GB/T6587 —1986 电子测量仪器GB/T7724—2022 称重显示把握器技术条件JJG555—1996 非自动秤通用检定规程QB 1563—2022 衡器产品型号编制方法GB/T7551—2022 称重传感器GB/T14249.1—93 JJG649-90GB/T14249.2-93 GB/T5185-1985GB1184GB1901GB/T1804GB1764JB/TQ4000.3 IEC/GBGB324-88GB8923GB9286JB8JB/ZQ4000.3B/ZQ4286-86GB4208TJ231(四)GBJ17-88GB191-2022GB3797-89GB4064-83GB14285-93电子衡器安全要求数字称重显示器电子衡器通用技术要求气焊、手工电弧焊及气体保护焊,焊缝坡口的根本形式与尺寸外形和位置公差、未注公差的规定公差与协作尺寸至500mm 孔、轴工差带与协作一般公差线性尺寸的未注公差漆膜厚度测定法焊接通用技术条件电动机技术标准钢焊缝符号表示法涂装钢材外表锈蚀等级和除锈等级色漆和清漆漆膜的划格试验产品标牌焊接通用技术要求包装通用技术条件外壳防护等级分类机械设备安装工程施工及验收标准钢构造设计标准包装储运图示标志电控设备其次局部装有电子器件的电控设备电气设备安全设计导则继电保护和安全自动装置技术规程GB/T1459898-91 电气装置安装工程电气设备交接试验标准GB1497-85 低压电器根本标准二、本方案自动上料及配料系统组成生产线配料主要完从与混料机下部料仓星型给料机下部开头:通过1 号物料输送机→2 号物料输送机→1~12 号下料器→1~12 计量仓→1~12 号仓下料排料阀→1~12 号水平输送机→1~12 号釜口气动球阀止。
面粉厂自动配料系统方案
自动配料系统方案一、概述此自动配料系统由先进的西门子PLC,WINCC上位机以及智能仪表组成。
在系统结构上采用集散控制系统,实现了“分散控制,集中管理”,克服了“危险集中”的问题;上位机,智能仪表和下位机相对独立。
具有手动、自动、半自动切换功能,联机时,彼此间按特定的协议互通信息,脱机时,单台秤可独立实现工艺闭环过程控制,上位机远离操作现场,提高了系统的稳定性,改善了操作员的工作环境,下位机选用可编程控制器,具有很强的抗干扰能力,能在恶劣的环境中长期可靠的运行。
二、系统硬件架构1,系统拓扑2,系统结构本系统由一套西门子300系列的PLC系统和一套上位机监控系统组成。
PLC 系统与上位机监控系统用以太网通讯,智能仪表与PLC通过PROFIBUS-DP通讯,上位机监控系统采用 Windows操作系统,安装西门子的WINCC组态软件。
3,硬件功能上位机:对整个系统进行实时监控,画面显示和报表打印;PLC:实现配料系统传送设备的自动控制;配料仪表:用于配料的PID调节及瞬时流量和累计流量等参数的显示;三、系统功能实现1、自动配料系统的主要功能监控功能:对整个配粉系统的传送设备,闸阀门,料位,称重仪表等进行控制管理,对配料过程参数进行检测和监视,通过计算机显示器可显示配料过程中有关控制参数的运行状况,以及显示实时配料曲线和表格;打印管理:可随时打印配料报表,以便保存和查询;通讯功能: PLC和智能仪表之间通过PRFIBUS-DP进行双向数据及信息交换;数据处理:系统可自动对采集的信号进行运算处理,并输出到相应的控制量;报警功能:上位机以画面方式和声光信号方式对各种参数超限或设备状态异常进行报警。
2、自动配料系统的设备连锁控制功能自动配料系统控制系统能实现集中联锁控制、集中单机控制和现场单机设备控制功能,操作方式可以相互切换。
通过计算机鼠标操作工段主令开关,实现以下操作:1)先启动除尘设备,逆物料流向顺序延时启动工艺流程上的设备;2)顺物料流向顺序延时停止工艺流程上的设备,延时停除尘设备;3)发生故障时,来料及故障设备同时停车,其余设备顺序延时停车,显示报警信息,包括故障设备所在楼层位置,电器元件所在MCC柜号及配置,可查询故障报警时间和恢复时间;4)非流程联锁设备的故障暂停及报警操作提示控制,如:设备的手/自动转换开关没切换到位,操作提示报警;短路跳闸报警,联锁停机;过载报警,联锁停机;现场紧急停车报警;料位满或空报警,操作提示;超过时限,联锁停机输送设备测速、跑偏、防堵报警,操作提示,超过时限,联锁停机;5)工艺流程的选择切换及联锁控制,可选择:粉料入配粉仓(由操作员确定具体仓号)粉料出配粉仓(由操作员确定具体仓号)粉料配粉后入打包仓(由操作员确定具体仓号)粉料出打包仓打包(由操作员确定具体仓号)6)气动闸阀门及气动三通的选择切换及联锁控制。
自动配料实施方案
自动配料实施方案一、背景介绍。
随着工业化生产的不断发展,自动化生产已经成为了现代工厂的主要趋势。
在食品加工行业中,自动配料系统的应用也越来越普遍。
自动配料系统能够提高生产效率,减少人工操作,保证产品质量的稳定性,因此受到了广泛的关注和应用。
二、自动配料系统的优势。
1. 提高生产效率,自动配料系统能够精确地控制配料比例,避免了人工操作中可能出现的误差,从而提高了生产效率。
2. 保证产品质量,自动配料系统能够保证每一批产品的配料比例一致,从而保证了产品的质量稳定性。
3. 减少人工成本,自动配料系统能够减少人工操作,降低了人工成本,提高了生产效益。
4. 灵活性强,自动配料系统可以根据不同产品的配方进行调整,适应不同产品的生产需求。
三、自动配料系统的实施方案。
1. 确定配料系统的需求,首先需要明确自动配料系统的具体需求,包括配料的种类、配料的精度要求、生产线的产能等。
2. 选择合适的设备,根据实际需求,选择适合的自动配料设备,包括称重传感器、控制系统、输送设备等。
3. 设计配料系统的布局,根据生产线的实际情况,设计合理的配料系统布局,确保设备的安装位置合理,便于操作和维护。
4. 编写配料系统的控制程序,根据产品的配方要求,编写配料系统的控制程序,包括配料的顺序、时间、速度等参数。
5. 进行系统调试和优化,在安装设备后,进行系统的调试和优化工作,确保配料系统的稳定性和准确性。
6. 培训操作人员,对生产线的操作人员进行培训,使其熟练掌握自动配料系统的操作方法和注意事项。
四、自动配料系统的应用案例。
以某食品加工厂为例,该厂引进了自动配料系统后,生产效率得到了显著提高,配料精度提高了30%,产品质量稳定性得到了保障,人工成本减少了20%,生产线的灵活性也得到了增强。
五、总结。
自动配料系统的实施对食品加工行业具有重要意义,能够提高生产效率,保证产品质量,降低生产成本,提高企业的竞争力。
因此,加强自动配料系统的研发和应用具有重要的现实意义和发展前景。
中频电炉自动加配料系统的设计方案
中频电炉自动加配料系统的设计方案中频电炉自动加配料系统是一种应用于冶金行业的自动化设备,其主要功能是根据生产工艺的要求,自动加入适量的配料到电炉中,以确保生产过程中的稳定性和效率。
下面将为您介绍一个设计中频电炉自动加配料系统的方案。
一、系统结构1.控制系统:负责整个系统的运行和控制。
2.传感器装置:用于监测电炉内的温度、压力等参数的变化。
3.PLC系统:负责控制传感器和执行器的工作,实现配料的自动加入。
4.执行器:根据PLC系统的指令,控制配料的加入。
5.配料单元:包括配料仓、配料传送装置等,用于存放和传送配料。
6.运输设备:用于将配料从配料单元送入电炉。
二、工作原理1.控制系统根据生产工艺设定相应的参数。
2.传感器装置实时监测电炉内的温度、压力等参数的变化,并将数据传输给PLC系统。
3.PLC系统根据传感器数据和设定的参数,判断是否需要加入配料。
4.如果需要加入配料,PLC系统将指令传递给执行器,控制其加入适量的配料。
5.配料单元根据执行器的指令,将相应的配料传送到电炉。
6.运输设备将配料送入电炉,并确保配料的均匀分布。
7.控制系统根据传感器的反馈信号,实时调整加料的速度和时间,以保持电炉内的温度和成分的稳定。
三、系统优势1.提高生产效率:自动化的加料系统可以减少人工操作,提高生产效率和工作效率。
2.降低人工成本:自动化设备减少了人工操作和监控的需求,降低了人力成本。
3.提高产品质量:自动化设备可以精确控制配料的加入,保证了产品成分的一致性和稳定性。
4.减少人员安全风险:自动化设备减少了人工操作的需求,减少了操作人员接触高温环境的风险。
5.减少资源浪费:自动化设备可以根据实时变化的生产需求,精确控制配料的加入,减少了配料的浪费。
四、运行维护综上所述,中频电炉自动加配料系统的设计方案可以提高生产效率和产品质量,减少人工成本和资源浪费,为冶金行业的生产提供了便利和效益。
自动配料系统
自动配料系统
现在有一条产线,自动配料系统,从加料,放料,称重,传送,搅拌,到包装,共20种料需要配,即20个料斗,用比例阀控制放料,称斗会把料量实时反馈回plc,plc输出来控制比例阀的开度,直至最后放料达到要求比例阀关闭。
这样一个系统是用一个300+模拟量模块+数字量模块来做,还是用300+200主从方式,还是全用200组成主从方式来做比较好,各位
最佳答案
300+模拟量模块+数字量模块来做比较省事可靠.
因为用的模拟量输入输出点比较多.200扩展机来比较麻烦.300比较方便.。
- 1、下载文档前请自行甄别文档内容的完整性,平台不提供额外的编辑、内容补充、找答案等附加服务。
- 2、"仅部分预览"的文档,不可在线预览部分如存在完整性等问题,可反馈申请退款(可完整预览的文档不适用该条件!)。
- 3、如文档侵犯您的权益,请联系客服反馈,我们会尽快为您处理(人工客服工作时间:9:00-18:30)。
自动配料灌装生产线计量系统方案一、企业现有生产过程情况概述目前企业的生产过程基本为:粉料采用人工称料用行车或叉车人工运料、手工填料的方式,液料采用称重计量,人工泵送料,反应釜一般采用手动变频启动方式、水计量采用就地显示流量计,需要人工看数手动控制开关,从以上看出企业目前基本没有自动计量及传输控制设备。
1、现存问题(1)、人工上料,劳动强度大,速度慢;(2)、液体原料采用桶装称重计量或流量计显示,桶内残留和流量计显示误差,造成计量精度差。
(3)、整个产品生产过程采用人工手动控制,劳动强度大,差错率高,废品率高,致使产品质量控制困难大、生产效率低。
(4)、为了适应产品规模化、高质量生产的需要,系统的布局、控制模式、管理软件系统均需要有重新设计、实施。
2、用户需求分析(1)、产品规模生产要求系统具有更大的产能、更高的稳定性;(2)、降低人工上料劳动强度、提高计量精度;(3)、固体及液体物料均应自动上料、自动计量;(4)、每次生产的不同配方(原料配比)均可在电脑上进行操作;(5)、生产过程实现自动化控制。
二、本方案自动上料配料系统组成生产线配料主要完成水和4中液料的配料混合。
计量罐单独设置,液体原料分开计量加料,现场3排搅拌釜分别为1排3个搅拌罐、2 排3个搅拌罐、3排5个搅拌罐。
1、原料罐四个,分别盛放四种不同的液体原料;水料罐1个,用于暂存水,预留用水量。
现场分别在3排搅拌罐的上部设置5T原料计量罐1台,15T水计量罐1台;2、每个原料罐底部都安装有送料管道(管道口径DN65),分别由自动阀门和手动阀门控制开关,每种液料的自动阀门安装在靠近管道出口位置,由送料泵负责将料通过管道打到计量罐,送料泵两端预留回流管及回流阀(回流管口径与主管道相同),在计量罐进料口处的安装自动阀门,实现物料的快投和慢投料控制;3、液料或水通过管道可直接加进计量罐,计量罐的四个支撑底脚与支撑架基础之间各安装一只称重压力传感器模块,负责计量进入计量罐的物料重量,支撑架基础需做水平调试;4、液体原料计量完毕通过计量罐底部的的自动分流装置,分别自动加到相应的搅拌罐中。
自动分流装置结构(见图一):在计量罐的总卸料阀后水平安装到各个搅拌釜的分料自动阀门,把各个分料自动阀门的前端进料管用管道联通,这样可以保证卸料后基本无存料,到各个搅拌釜的卸料管道水和液料管道可以合并一条管道,以减少管道用料成本;5、搅拌好的成品通过反应釜底部的管道泵送至成品罐,由自动阀门和泵控制;6、全部配料数据均存储于控制中心的工控机数据库内;7、全部配料过程均由组态软件实施监控,通过控制界面实施过程操作,生产数据适时存储到系统数据库,以完成对各种生产数据进行存储和分析,同时还能实现原料进存用料管理、成品管理、人员管理、合同管理等各项功能。
三、系统控制方案1、在生产现场设置一个集中控制操作台,动态称重计量仪表安装在操作台上,安装在六个计量罐支撑腿下部的称重传感器数据线与动态计量仪表相连,实时数据由计量仪表经通信线上传给控制中心的工控机,配方及控制命令由控制中心的工控机经通信线下传给仪表及PLC控制器;2、操作台内部安装西门子S系列PLC可编程控制器及继电器等,负责控制各自动阀门和泵的启停;3、计量仪表在PLC的控制下启动,在不同计量阶段输出不同的信号(快投、慢投、卸料等)给PLC,由PLC对外部设备直接控制;4、操作台上安装按钮开关等,可实现上述各部分的手动控制;5、在现场操作处和集中控制操作台上均设有急停按钮,两个急停按钮系串联关系,用于紧急情况的应急断电处理;6、搅拌罐设搅拌电机,由变频器控制。
四、自动配料计量系统组成示意图五、自动配料灌装计量系统控制部分示意图控制系统可实现配料计量过程全部自动控制,包括各阀门、泵、电机、变频器、计量仪表的启动、停止,信号的传输、数据的记录、报表的处理和打印等。
六、系统描述1、控制系统特点(1)、结构简单,控制逻辑清楚;(2)、采用控制领域内的主流产品(如研华工控机、西门子或欧姆龙PLC、施奈德电器件等),可靠性、稳定性好;(3)、采用我公司独有的连续计量技术,效率快、精度高;(4)、操作台集中操作、集中控制,全部仪表一目了然,便于监控和操作,增加了安全性、可靠性,降低了操作员的劳动强度,使操作员不必奔波于各分散的计量仪表之间;(5)、操作台与控制柜的距离近,控制信号传递距离短、可靠性强;(6)、具有强大的软件功能,可实现生产过程实时、直观监控,各种配方管理,物料缺料提醒、异常情况报警等各种功能。
2、控制流程描述(1)、生产启动操作台上设有各工艺环节的手动操控按钮及指示灯,以及启动按钮等。
用户可在操作台面板上按动按钮或直接用鼠标点击电脑屏幕上的启动按钮,即可以手动或自动启动相应的生产线开始生产。
(2)、配方管理每次生产前可以设置输入本次配料的配方,按比例分配所需原料数量(也可采用缺省方式,即仍然使用上一次的配方)。
给自动上料提供数据依据。
(3)、生产过程动态计量在生产启动的同时,PLC就将动态计量启动信号发给称重计量仪表,仪表即开始对各环节的重量进行采集、显示,并在不同的重量阶段采用快投料和慢投料策略,以兼顾提高效率和计量精度。
在到达目标值时,输出停止计量信号,由PLC控制关闭相关阀门、泵等。
同时完成卸料到反应釜的动作,计量仪表自动清零去皮。
(4)、数据存储本次配料结束时,由上位机(电脑)对本次实际数据做存储,并可按要求做一定的精度分析,生成各类报表,用于生产统计、管理。
(5)、报表打印可根据用户需求,在线或离线打印各种所需报表,如当成品日产量、原料消耗,原料库存,成品库存等等。
3、配料计量过程动态计量仪表采用的是动态计量精度控制方式。
在停止或暂停状态下,外部运行输入信号有效时,启动自动配料过程。
按下启动按钮,系统仪表启动,称重仪表清零。
然后给原料1(1#料)快投料和慢投料有效信号,系统打开阀门启动料泵,开始1#料的快速加料过程(即同时打开两个进料阀门),同时仪表启动随时跟踪读取称重传感器信号,当重量接近达到预设的大投值时,仪表将关闭快投料信号,使系统进入1#料慢加料过程(关闭一个阀门),同时仪表继续随时跟踪读取称重传感器信号,仪表将判别料斗重量是否大于等于1#料目标值—1#料落差值。
如果大于等于则仪表关闭小投信号,停止加料过程(全部阀门及上料电机关闭),本次计量结束。
如果需要在同一个计量罐内累计加量计量则开始第二种物料的加料,此时仪表首先清零显示输出M2(2#料),快投料和慢投料有效,其过程同上。
否则开始卸料到反应釜。
依次完成2#、3#料的加料过程后,仪表将分别显示料斗中四种物料的重量,仪表输出卸料信号,系统开始卸料过程,当料斗中的重量等于或小于所设定的零区范围时,仪表关闭卸料信号,同时回到停止状态(运行输出无效,暂停输出无效)。
完成一次配料过程。
其中物料的落差初始值是根据经验设定的,随后在计量的过程中落差值根据实际测量值采用自学习的方式,逐次逼近目标值,使误差越来越小。
4、管道阀门工作管理在配料系统启动后,系统PLC自动控制顺序开启各原料气动阀及称重上料阀,同时启动上料电机,加料结束自动关闭上料阀门及电机,开启卸料阀及搅拌电机,原料开始卸料,反应釜开始搅拌,反应釜搅拌结束,系统开启反应釜卸料阀门和卸料电机,把成品料输送到成品罐,本次配料结束。
灌装工人可以启动灌装机,进行装桶工序操作。
配料过程也可以由操作员按照工艺要求手动顺序按动操作台上的阀门、电机按钮,进行手动配料过程操作。
5、原料罐存料管理(备选)原料罐上可以安装静态液位计(如雷达液位计、超声波液位计、浮子液位计、压力液位计等),随时检测液位变化,控制系统适时跟踪采集液位高度数据,并测量计算出原料存量、进料量、出料量等,生成数据报表,便于进行原料库存耗用等管理。
6、控制系统特点(1)、结构简单,控制逻辑清楚;(2)、采用控制领域内的主流产品(如研华工控机、西门子或欧姆龙PLC、施奈德电器件等),可靠性、稳定性好;(3)、采用我公司独有的连续计量技术,效率快、精度高;(4)、操作台集中操作、集中控制,全部仪表一目了然,便于监控和操作,增加了安全性、可靠性,降低了操作员的劳动强度,使操作员不必奔波于各分散的计量仪表之间;(5)、操作台与控制柜的距离近,控制信号传递距离短、可靠性强;(6)、具有强大的软件功能,可实现生产过程实时、直观监控,各种配方管理,物料缺料提醒、异常情况报警等各种功能。
7、控制流程描述(1)、生产启动操作台上设有各工艺环节的手动操控按钮及指示灯,以及启动按钮等。
用户可在操作台面板上按动按钮或直接用鼠标点击电脑屏幕上的启动按钮,即可以手动或自动启动相应的生产线开始生产。
(2)、配方管理每次生产前可以设置输入本次配料的配方,按比例分配所需原料数量(也可采用缺省方式,即仍然使用上一次的配方)。
给自动上料提供数据依据。
(3)、生产过程动态计量在生产启动的同时,PLC就将动态计量启动信号发给称重计量仪表,仪表即开始对各环节的重量进行采集、显示,并在不同的重量阶段采用快投料和慢投料策略,以兼顾提高效率和计量精度。
在到达目标值时,输出停止计量信号,由PLC控制关闭相关阀门、泵等。
同时完成卸料到反应釜的动作,计量仪表自动清零去皮。
(4)、数据存储本次配料结束时,由上位机(电脑)对本次实际数据做存储,并可按要求做一定的精度分析,生成各类报表,用于生产统计、管理。
(5)、报表打印可根据用户需求,在线或离线打印各种所需报表,如当成品日产量、原料消耗,原料库存,成品库存等等。
8、配料计量过程动态计量仪表采用的是动态计量精度控制方式。
在停止或暂停状态下,外部运行输入信号有效时,启动自动配料过程。
按下启动按钮,系统仪表启动,称重仪表清零。
然后给原料1(1#料)快投料和慢投料有效信号,系统打开阀门启动料泵,开始1#料的快速加料过程(即同时打开两个进料阀门),同时仪表启动随时跟踪读取称重传感器信号,当重量接近达到预设的大投值时,仪表将关闭快投料信号,使系统进入1#料慢加料过程(关闭一个阀门),同时仪表继续随时跟踪读取称重传感器信号,仪表将判别料斗重量是否大于等于1#料目标值—1#料落差值。
如果大于等于则仪表关闭小投信号,停止加料过程(全部阀门及上料电机关闭),本次计量结束。
如果需要在同一个计量罐内累计加量计量则开始第二种物料的加料,此时仪表首先清零显示输出M2(2#料),快投料和慢投料有效,其过程同上。
否则开始卸料到反应釜。
依次完成2#、3#料的加料过程后,仪表将分别显示料斗中四种物料的重量,仪表输出卸料信号,系统开始卸料过程,当料斗中的重量等于或小于所设定的零区范围时,仪表关闭卸料信号,同时回到停止状态(运行输出无效,暂停输出无效)。