脱硫石膏深加工
利用脱硫石膏年产30万吨建筑石膏粉生产线

脱硫石膏是一种重要的工业废弃物,广泛用于建筑和农业领域。
利用脱硫石膏年产30万吨建筑石膏粉生产线可以有效地降低环境污染,实现资源循环利用,并创造经济效益。
在工艺流程上,可以采用石膏湿法脱硫石膏粉磨制工艺。
具体步骤包括:脱硫石膏破碎、脱硫石膏细磨、石膏研磨、石膏干燥和包装。
其中,脱硫石膏破碎可采用颚式破碎机进行粗碎,将脱硫石膏破碎成适当尺寸的颗粒。
脱硫石膏细磨可以采用球磨机进行,使颗粒更加细化。
石膏研磨可以采用研磨机进行,进一步提高石膏的细度。
石膏干燥则可以采用烘干机或旋转干燥机进行,将石膏的水分蒸发掉。
最后,将干燥后的石膏粉装入袋子或桶中进行包装。
为了实现高效、低能耗的生产,需要优化设备的选择和运行参数的调节。
比如,可以采用高效的破碎设备和磨矿设备,提高生产效率。
同时,根据生产工艺的要求,合理控制破碎和磨矿设备的运行参数,有效地节约能源。
此外,还要加强设备维护和运行管理,保证设备的正常运行和寿命。
在产品销售方面,可以将建筑石膏粉用作建材行业的主要原料,如砌筑砂浆、石膏板、石膏轻质板等。
此外,建筑石膏粉也可以用于农业领域,作为土壤改良剂和肥料,提高农作物产量和质量。
通过开发和拓展不同领域的销售渠道,提高产品的市场竞争力,增加企业收入。
总的来说,利用脱硫石膏年产30万吨建筑石膏粉生产线可以实现环境保护、资源循环利用和经济效益的多重目标。
但是,在实际操作中还需考虑设备投资、能耗控制、产品品质等多方面的问题。
因此,需要充分论证和规划,制定详细的操作方案,并严格执行以确保生产线的顺利运行。
国内生产脱硫石膏的工艺
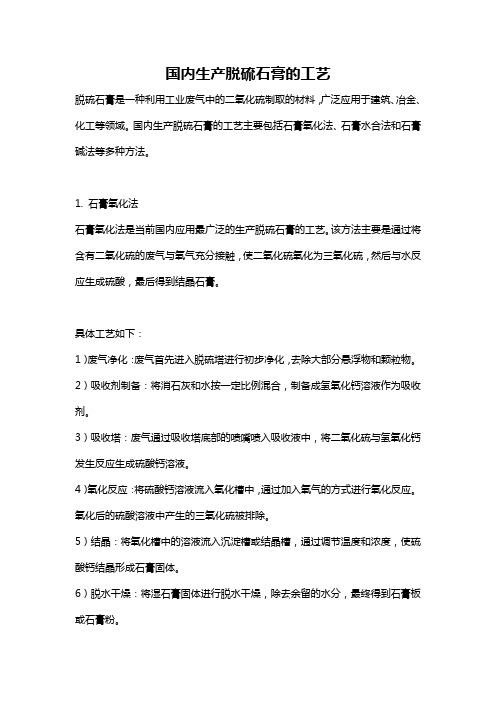
国内生产脱硫石膏的工艺脱硫石膏是一种利用工业废气中的二氧化硫制取的材料,广泛应用于建筑、冶金、化工等领域。
国内生产脱硫石膏的工艺主要包括石膏氧化法、石膏水合法和石膏碱法等多种方法。
1. 石膏氧化法石膏氧化法是当前国内应用最广泛的生产脱硫石膏的工艺。
该方法主要是通过将含有二氧化硫的废气与氧气充分接触,使二氧化硫氧化为三氧化硫,然后与水反应生成硫酸,最后得到结晶石膏。
具体工艺如下:1)废气净化:废气首先进入脱硫塔进行初步净化,去除大部分悬浮物和颗粒物。
2)吸收剂制备:将消石灰和水按一定比例混合,制备成氢氧化钙溶液作为吸收剂。
3)吸收塔:废气通过吸收塔底部的喷嘴喷入吸收液中,将二氧化硫与氢氧化钙发生反应生成硫酸钙溶液。
4)氧化反应:将硫酸钙溶液流入氧化槽中,通过加入氧气的方式进行氧化反应。
氧化后的硫酸溶液中产生的三氧化硫被排除。
5)结晶:将氧化槽中的溶液流入沉淀槽或结晶槽,通过调节温度和浓度,使硫酸钙结晶形成石膏固体。
6)脱水干燥:将湿石膏固体进行脱水干燥,除去余留的水分,最终得到石膏板或石膏粉。
2. 石膏水合法石膏水合法是利用石膏半水化的特性,将硫酸钙水合成石膏的工艺。
该方法适用于含水量较高的废气处理。
具体工艺如下:1)原料准备:将消石灰与二氧化硫废气以一定比例混合,并添加适量的水蒸气。
2)水合反应:消石灰和二氧化硫在适当的温度和湿度条件下发生水合反应,生成石膏半水合物。
3)结晶:将石膏半水合物放在低温高湿的条件下,进行结晶,形成纯度较高的石膏晶体。
4)脱水干燥:将石膏晶体通过脱水干燥的方式去除余留的水分,最终得到石膏板或石膏粉。
3. 石膏碱法石膏碱法是利用氨水或碱性废液与含二氧化硫废气中的二氧化硫反应生成硫酸铵,并通过浓缩、结晶等工艺得到脱硫石膏。
具体工艺如下:1)原料准备:将氨水或碱性废液与二氧化硫废气进行混合,使其发生反应。
2)硫酸铵制备:将氨水或碱性废液中的氨与二氧化硫反应生成硫酸铵溶液。
3)浓缩:将硫酸铵溶液进行浓缩,使其达到一定浓度。
年产二十万吨脱硫石膏深加工项目可行性研究报告
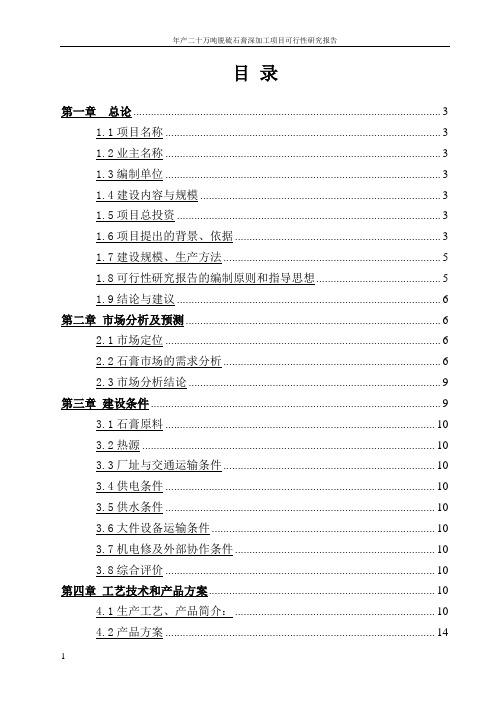
目录第一章总论 (3)1.1项目名称 (3)1.2业主名称 (3)1.3编制单位 (3)1.4建设内容与规模 (3)1.5项目总投资 (3)1.6项目提出的背景、依据 (3)1.7建设规模、生产方法 (5)1.8可行性研究报告的编制原则和指导思想 (5)1.9结论与建议 (6)第二章市场分析及预测 (6)2.1市场定位 (6)2.2石膏市场的需求分析 (6)2.3市场分析结论 (9)第三章建设条件 (9)3.1石膏原料 (10)3.2热源 (10)3.3厂址与交通运输条件 (10)3.4供电条件 (10)3.5供水条件 (10)3.6大件设备运输条件 (10)3.7机电修及外部协作条件 (10)3.8综合评价 (10)第四章工艺技术和产品方案 (10)4.1生产工艺、产品简介: (10)4.2产品方案 (14)4.3生产工艺线特点 (15)第五章投资概算 (15)5.1土建工程投资 (15)5.2设备投资表 (16)第六章环境保护 (32)6.1拟建厂厂址环境概况 (33)6.2主要污染源及污染物 (33)6.3工程设计防治污染的初步方案 (33)6.4环境绿化 (33)6.5本工程环境影响初步分析 (33)第七章劳动保护和定员 (33)7.1劳动安全卫生及保护 (34)7.2生产事故防范 (34)7.3职业危害的防护 (34)第八章项目实施计划和进度 (35)第九章技术经济分析与评价 (35)9.1评价依据、原则和方法 (35)9.2项目投资与资金筹措 (36)9.3成本和费用 (36)9.4产品生产成本合计 (37)9.5损益表 (38)9.6投资回收期 (38)第十章结论 (38)第一章总论1.1项目名称项目名称:脱硫石膏综合利用。
1.2业主名称主办单位:公司法人代表:1.3编制单位编制单位:联系人:1.4建设内容与规模1.4.1三万吨水泥缓凝剂生产线(原有生产线)1.4.2十五万吨β石膏粉生产线(粉刷石膏、石膏砌块的原料)1.4.3十五万吨粉刷石膏生产线1.4.4八万平石膏粉生产线1.5项目总投资项目总投资3120万元。
脱硫石膏深加工
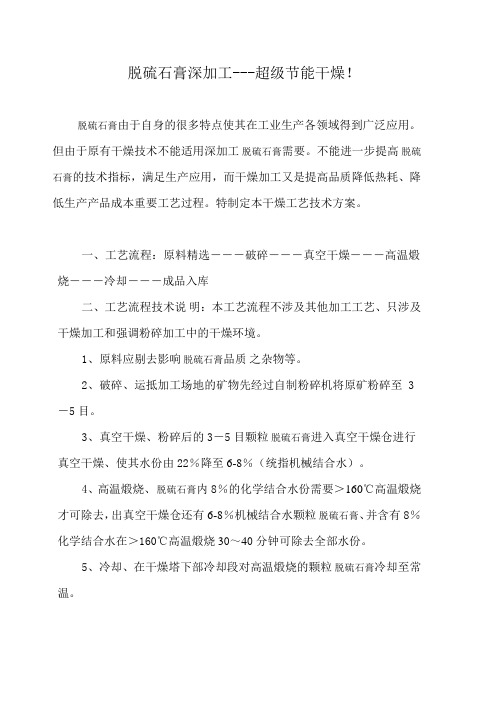
脱硫石膏深加工---超级节能干燥!脱硫石膏由于自身的很多特点使其在工业生产各领域得到广泛应用。
但由于原有干燥技术不能适用深加工脱硫石膏需要。
不能进一步提高脱硫石膏的技术指标,满足生产应用,而干燥加工又是提高品质降低热耗、降低生产产品成本重要工艺过程。
特制定本干燥工艺技术方案。
一、工艺流程:原料精选――-破碎―――真空干燥―――高温煅烧―――冷却―――成品入库二、工艺流程技术说明:本工艺流程不涉及其他加工工艺、只涉及干燥加工和强调粉碎加工中的干燥环境。
1、原料应剔去影响脱硫石膏品质之杂物等。
2、破碎、运抵加工场地的矿物先经过自制粉碎机将原矿粉碎至 3-5目。
3、真空干燥、粉碎后的3-5目颗粒脱硫石膏进入真空干燥仓进行真空干燥、使其水份由22%降至6-8%(统指机械结合水)。
4、高温煅烧、脱硫石膏内8%的化学结合水份需要>160℃高温煅烧才可除去,出真空干燥仓还有6-8%机械结合水颗粒脱硫石膏、并含有8%化学结合水在>160℃高温煅烧30~40分钟可除去全部水份。
5、冷却、在干燥塔下部冷却段对高温煅烧的颗粒脱硫石膏冷却至常温。
6、超细粉碎、出干燥仓的颗粒水份脱硫石膏<0.3%(优于化工部标准8%)、但在超细粉碎过程中、由于微粉脱硫石膏比表面积进一步提高、极易快速吸收水份,因而微粉粉碎过程应在封闭的低温干燥环境中进行、以确保品质。
7、真空包装、粉碎后的微粉应快速真空包装、减少微粉在包装和贮存过程中吸附水份、以免降低品质。
三、真空干燥工艺的技术经济分析。
真空低温连续干燥技术设备是国家科技部“十五”重大科技攻关项目,国家科技部“十一五”科技支撑计划项目,已经通过专家评审,是技术成熟设备成功的项目。
它的优点:确保干燥物料品质、特别节能、环保安全可以进行极限的水分干燥。
1、干燥加工是脱硫石膏加工工艺生产成本的最大支出,根据样品分析、脱硫石膏样品机械结合水22%,化学结合水8%。
脱硫石膏的热容比0.26,当用常规烘干煅烧法生产时、每吨成品需要热能耗>60万大卡。
脱硫石膏晶须

1、重庆市与清华大学的科技对接项目,珞璜电厂每年发电产生的百万吨的废渣找到了新的出路,以前卖给石膏板厂和水泥厂20块/吨的脱硫石膏,经过加工之后出厂价格是以前的两百倍,达到了4000/吨火力发电会产生二氧化硫,这直接污染了空气,需要进行化学处理进行脱硫,成为脱硫石膏,每年有上百万吨脱硫石膏产生。
每年处理脱硫石膏我们都要倒贴钱,卖给水泥厂和石膏板厂20元/吨,但是还是处理不完,每年还要留下六七十万吨。
昨天和清华大学签约的硫酸钙晶须的项目就是对脱硫石膏进行深加工成为高附加值的化工产品,一吨脱硫石膏可以加工成0.7吨的晶须,价格达到了4000. 晶须可以应用于造纸橡胶塑料以及刹车片。
2、硫酸钙晶须具有机械强度大,热稳定性好,价格低廉的特点,是塑料橡胶陶瓷水泥的理想增强型材料。
清华大学和国内相关院校合作,经过五年的潜心攻关,于近期开发出水热合成硫酸钙晶须的技术,该技术的原料主要是一些化工副产物(脱硫石膏、磷石膏、电石渣),制备的硫酸钙晶须体貌规则,结晶良好,长径比大(长度200mm~2000mm,直径1-20mm,长径比50~200mm)纯度高(硫酸钙晶须的主含量达到了90%~95%,和原料有关)。
该技术工艺简单成本低廉(2000~4000/吨),所需设备大多也是常规设备。
3、近日,我县连庄镇一耐公司与河北云山化工集团有限公司合作利用清华大学专利生产硫酸钙晶须项目顺利开工建设。
该项目固定资产投资1.116亿元,占地50亩,位于我县经济开发区。
硫酸钙晶须是清华大学十几位专家用5年的时间研究开发出的水热合成硫酸钙晶须技术(专利公开号:101671848A),广泛应用于增强塑料、摩擦材料、建筑材料等方面,主要原料是钢铁厂、电厂废弃的脱硫石膏,是替代同类产品的一次革命性升级。
产品具有科技含量高、成本低、市场前景广阔的特点。
目前,国内已有多家大型企业与该公司进行了联系洽谈。
该项目是我县企业与国内一流大学研发专利的首次对接,也是尖端科研成果在我县实现生产转化的第一次。
脱硫石膏的工艺流程

脱硫石膏的工艺流程脱硫石膏是一种重要的工业原料,广泛应用于建筑材料、农业、环保等领域。
脱硫石膏的生产过程主要是通过燃煤或燃油等燃料进行燃烧产生的废气中的二氧化硫进行脱除,从而得到的一种固体废物。
下面我们将详细介绍脱硫石膏的工艺流程。
1. 石膏熔融工艺。
石膏熔融工艺是一种常用的脱硫石膏生产工艺。
首先,将石膏粉末加入熔融炉中,通过高温加热使石膏熔化成液态。
在熔融炉中,加入适量的矿物质和添加剂,如石灰石、氢氧化钙等,用于调节石膏的成分和性质。
经过一定时间的熔融,石膏液体逐渐冷却凝固成块状,即可得到脱硫石膏。
2. 湿法石膏脱硫工艺。
湿法石膏脱硫工艺是另一种常用的生产工艺。
首先,将石膏粉末与水混合,形成石膏浆料。
然后将石膏浆料加入脱硫反应器中,同时向反应器中通入含有二氧化硫的废气。
在反应器中,二氧化硫与石膏浆料发生化学反应,生成硫酸钙。
经过一定时间的反应,硫酸钙沉淀在反应器中,即可得到脱硫石膏。
3. 干法石膏脱硫工艺。
干法石膏脱硫工艺是一种较为节能的生产工艺。
首先,将石膏粉末加入干法脱硫设备中,通过喷射或气流等方式将含有二氧化硫的废气与石膏粉末充分接触。
在接触过程中,二氧化硫被吸附到石膏粉末表面,形成硫化钙。
经过一定时间的吸附,硫化钙逐渐沉淀,即可得到脱硫石膏。
4. 石膏干燥工艺。
无论是采用熔融工艺、湿法工艺还是干法工艺,得到的脱硫石膏都需要进行干燥处理。
首先,将脱硫石膏块状物料送入干燥设备中,通过加热和通风等方式将石膏中的水分蒸发。
经过一定时间的干燥,脱硫石膏中的水分得到蒸发,即可得到干燥的脱硫石膏。
5. 石膏粉碎工艺。
最后一步是对干燥的脱硫石膏进行粉碎处理。
首先,将干燥的脱硫石膏送入破碎设备中,通过冲击、挤压等方式将块状石膏粉碎成粉末状。
经过粉碎处理,即可得到成品的脱硫石膏粉末。
通过以上工艺流程,我们可以得到成品的脱硫石膏。
脱硫石膏在建筑材料、农业、环保等领域有着广泛的应用,对于减少二氧化硫等污染物的排放,保护环境具有重要的意义。
年产5万吨脱硫石膏粉生产线工艺方案0
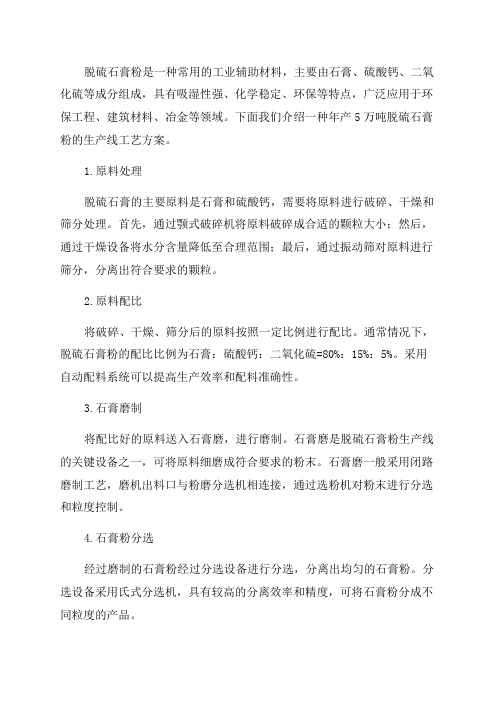
脱硫石膏粉是一种常用的工业辅助材料,主要由石膏、硫酸钙、二氧化硫等成分组成,具有吸湿性强、化学稳定、环保等特点,广泛应用于环保工程、建筑材料、冶金等领域。
下面我们介绍一种年产5万吨脱硫石膏粉的生产线工艺方案。
1.原料处理脱硫石膏的主要原料是石膏和硫酸钙,需要将原料进行破碎、干燥和筛分处理。
首先,通过颚式破碎机将原料破碎成合适的颗粒大小;然后,通过干燥设备将水分含量降低至合理范围;最后,通过振动筛对原料进行筛分,分离出符合要求的颗粒。
2.原料配比将破碎、干燥、筛分后的原料按照一定比例进行配比。
通常情况下,脱硫石膏粉的配比比例为石膏:硫酸钙:二氧化硫=80%:15%:5%。
采用自动配料系统可以提高生产效率和配料准确性。
3.石膏磨制将配比好的原料送入石膏磨,进行磨制。
石膏磨是脱硫石膏粉生产线的关键设备之一,可将原料细磨成符合要求的粉末。
石膏磨一般采用闭路磨制工艺,磨机出料口与粉磨分选机相连接,通过选粉机对粉末进行分选和粒度控制。
4.石膏粉分选经过磨制的石膏粉经过分选设备进行分选,分离出均匀的石膏粉。
分选设备采用氏式分选机,具有较高的分离效率和精度,可将石膏粉分成不同粒度的产品。
5.煅烧工艺分选后的石膏粉可以直接进行包装出售,也可以进行煅烧处理,提高产品质量和降低含水率。
煅烧处理可以采用旋转窑或喷煤窑,通过高温煅烧除去残余的水分和一些有机物质,使产品更适用于建材等领域。
6.环保措施为了达到环保要求,脱硫石膏粉生产线需要设置废气处理系统和废水处理系统。
废气处理系统主要包括除尘器和排放管道,通过过滤和吸附等方式净化废气;废水处理系统采用化学和物理处理方法去除废水中的污染物,达到排放标准。
7.自动化控制为了提高生产效率和产品质量,脱硫石膏粉生产线的每个环节都应采用自动化控制系统。
通过PLC控制系统和传感器等设备,对原料处理、石膏磨制、分选和煅烧等过程进行自动控制和监测,确保生产线的稳定运行和产品的一致性。
综上所述,这是一种年产5万吨脱硫石膏粉的生产线工艺方案,包括原料处理、原料配比、石膏磨制、石膏粉分选、煅烧工艺、环保措施和自动化控制等环节,能够满足大规模脱硫石膏粉的生产需求,并且符合环保要求和产品质量要求。
国内外脱硫石膏处理工艺技术现状

国内外脱硫石膏处理工艺技术现状在欧洲、日本或美国,几乎所有的脱硫石膏都应用于建材行业。
我国对脱硫石膏的综合处理技术也已经初步成熟。
目前在国内外大部分的脱硫石膏用于生产纸面石膏板,而另有相当一部分的脱硫石膏用于水泥缓凝剂。
1.国内外脱硫石膏处理工艺技术现状从原材料方面来看,脱硫石膏是与天然石膏等效的原材料,但有一定差异。
主要表现在原始状态、机械性能和化学成分,特别是杂质成分上的差异,从而导致其脱水特征、力学性能、流变性能等特征上与天然石膏有所不同。
脱硫石膏经过干燥、煅烧、冷却、调性后,完全能生产出质量良好的建筑石膏及相关的石膏制品。
从石膏生产工艺技术方面来看,脱硫石膏与天然石膏也是宏观上相似,微观上有一定的区别。
主要体现在原材料的处理上有所不同,即脱硫石膏湿料的处理和煅烧工艺技术装备上有所区别。
在湿料的处理中最主要的设备是湿料仓,湿料仓分为直筒体的储料仓和带曲线形状的出料装置。
出料量的大小可调,且能保证连续稳定。
在德国由WTW公司生产制造的。
杭州中新机电技术有限公司研制的湿料仓和WTW的类似,技术性能也相近。
石膏建材制品的质量取决于建筑石膏粉的质量,而建筑石膏粉的质量是取决于石膏原材料以及煅烧的效率。
因此煅烧是脱硫石膏处理工艺技术中最为关键的。
①气流煅烧工艺气流煅烧即热气体与粉料直接接触,二水石膏迅速脱水而成半水石膏。
这种方式热利用合理,设备紧凑,使用简单,功效高。
德国GRENZEBACH公司及美国BMH公司都有这种设备,前者叫锤式烘干煅烧磨磨,后者称Delta磨。
俗称“气流煅烧磨”,这种“磨”采用高速旋转的锤子将物料抛起并击碎、击细,同时与气流相汇,完成干燥、煅烧的过程。
上述两个设备中锤体的安装方式,锤头的数量,分级器放置的方向等有所不同,但其工作原理是相同的。
锤式烘干煅烧磨集干燥—煅烧为一体,是德国GRENZEBACH公司研制的。
它是一种热烟气的锤式磨机,磨机最侧部为主传动装置,带动直径φ1600mm的转子高速旋转,转子上有多个交叉分布的锤子。
- 1、下载文档前请自行甄别文档内容的完整性,平台不提供额外的编辑、内容补充、找答案等附加服务。
- 2、"仅部分预览"的文档,不可在线预览部分如存在完整性等问题,可反馈申请退款(可完整预览的文档不适用该条件!)。
- 3、如文档侵犯您的权益,请联系客服反馈,我们会尽快为您处理(人工客服工作时间:9:00-18:30)。
脱硫石膏深加工---超级节能干燥!
脱硫石膏由于自身的很多特点使其在工业生产各领域得到广泛应用。
但由于原有干燥技术不能适用深加工脱硫石膏需要。
不能进一步提高脱硫石膏的技术指标,满足生产应用,而干燥加工又是提高品质降低热耗、降低生产产品成本重要工艺过程。
特制定本干燥工艺技术方案。
一、工艺流程:原料精选――-破碎―――真空干燥―――高温煅烧―――冷却―――成品入库
二、工艺流程技术说明:本工艺流程不涉及其他加工工艺、只涉及干燥加工和强调粉碎加工中的干燥环境。
1、原料应剔去影响脱硫石膏品质之杂物等。
2、破碎、运抵加工场地的矿物先经过自制粉碎机将原矿粉碎至 3-5目。
3、真空干燥、粉碎后的3-5目颗粒脱硫石膏进入真空干燥仓进行真空干燥、使其水份由22%降至6-8%(统指机械结合水)。
4、高温煅烧、脱硫石膏内8%的化学结合水份需要>160℃高温煅烧才可除去,出真空干燥仓还有6-8%机械结合水颗粒脱硫石膏、并含有8%化学结合水在>160℃高温煅烧30~40分钟可除去全部水份。
5、冷却、在干燥塔下部冷却段对高温煅烧的颗粒脱硫石膏冷却至常温。
6、超细粉碎、出干燥仓的颗粒水份脱硫石膏<0.3%(优于化工部标准8%)、但在超细粉碎过程中、由于微粉脱硫石膏比表面积进一步提高、极易快速吸收水份,因而微粉粉碎过程应在封闭的低温干燥环境中进行、以确保品质。
7、真空包装、粉碎后的微粉应快速真空包装、减少微粉在包装和贮存过程中吸附水份、以免降低品质。
三、真空干燥工艺的技术经济分析。
真空低温连续干燥技术设备是国家科技部“十五”重大科技攻关项目,国家科技部“十一五”科技支撑计划项目,已经通过专家评审,是技术成熟设备成功的项目。
它的优点:确保干燥物料品质、特别节能、环保安全可以进行极限的水分干燥。
1、干燥加工是脱硫石膏加工工艺生产成本的最大支出,根据样品分析、脱硫石膏样品机械结合水22%,化学结合水8%。
脱硫石膏的热容比0.26,当用常规烘干煅烧法生产时、每吨成品需要热能耗>60万大卡。
如果每天加工原料150吨、可得到成品105吨。
(原料150吨-成品105吨)×每吨水汽化潜热60万大卡×3干燥热效率=8100万大卡≈需用23吨优质煤。
2、真空干燥工艺特点:⑴将调整合适温度180-200℃高热气体送入煅烧段将8%左右结合水脱去、低于160℃高热气体导入升温段对进入升温段的颗粒原料升温并脱去剩余水分,⑵对颗粒原料升温脱水后的高温高湿气体导入真空干燥仓加热管内、对真空干燥仓内颗粒物料进行升温至100℃降水至<4%,出仓异形管气体降温至<75℃。
冷凝水温<75℃,
<75℃气体引入燃烧室加热到380~420℃循环使用,<75℃冷凝水可供洗浴、取暖使用。
⑶冷却段排出含大量热能空气引入燃烧室燃烧使用。
3、真空干燥工艺技术经济分析:从物料中脱去1吨水需要60万大卡汽化潜热,用常规烘干、煅烧工艺加工膨润土、测算需180~200万大卡热能,需优质煤400~450公斤。
换用真空干燥工艺则热能得到三次充分利用。
⑴180-200℃气体对颗粒脱硫石膏进行煅烧干燥。
⑵<370~140℃高温高湿气体对进入干燥仓颗粒脱硫石膏进行干燥升温。
⑶<130℃高温高湿气体对真空干燥仓内颗粒膨润土进行干燥升温。
⑷出真空干燥的中温冷凝水<75℃、150吨原料加工后有40~50吨中温水,可供洗浴、取暖。
⑸出真空干燥仓的经除湿后的<70℃的大量热气体可返回燃烧室加热至180-200℃循环使用。
⑹进入冷却段的冷空气经冷却干燥成品后、升温的<70℃的空气可供燃烧室使用。
经上述技术措施后,热能源得以在高温、中温、低温下充分利用。
预计每天加工150吨原料脱硫石膏、干燥脱去45吨水需用2000万~2600万大卡热能。
对比常规烘干――煅烧热能耗8100万大卡。
前者只有后者的1/3~1/4。
每天可少用煤15~17吨、减少能耗成本支出9500~13000元,以全年300工作日计算可降低成本285~390万元。
四、真空干燥工艺设备。
1、粉碎机 1.5~2.5万元
2、真空干燥仓 25~30 万元
3、煅烧干燥仓 6~8 万元
4、煤气发生炉及燃烧器 15~20万元
5、真空系统 8~10万元
6、提升机、皮带输送机 2~3万元
7、真空包装计量 2~3万元
8、风机(鼓风、引风) 3.5~4.5万元
9、电控系统 4~6万元
以上合计85~95万元、设备生产运行100天节能费用可收回设备全部投资。
郑州飞航真空干燥技术公司。