电石炉余热利用方案
电石炉气热能利用及除尘技术

电石炉气热能利用及除尘技术发布时间:2023-03-08T03:34:30.023Z 来源:《福光技术》2023年3期作者:郭海[导读] 介绍了将电石炉气直接引入余热锅炉燃烧及除尘技术,该技术在生产中显示了优越的工艺性能,是一种投资省、见效快、安全、经济、节能的可行性技术新疆圣雄电石有限公司新疆吐鲁番 838100摘要:介绍了将电石炉气直接引入余热锅炉燃烧及除尘技术,该技术在生产中显示了优越的工艺性能,是一种投资省、见效快、安全、经济、节能的可行性技术关键词:密闭电石炉炉气;节能;环保;1 我公司拥有33000KV A密闭电石炉16台,附带净化装置,在年产4.5万吨电石的同时产生约1800万m3炉气,此炉气一直是放空烧掉,既污染了环境(夹带粉尘量约900-1800吨/年),又浪费了宝贵的资源(炉气中含CO:65%-80%、H2:5-10%)。
近年,我们设计并建成了密闭电石炉气热能利用及除尘技改工程。
该技术与现有国内外使用的回收方法相比,具有投资省、热效率高、过程简单、操作方便、运行安全可靠等特点。
取得了良好的经济、社会和环境效益,达到了预期的效果。
1 电石炉气回收技术现状回收密闭电石炉气作为化工原料使用,无论是从净化、提纯的技术难度上考虑,还是从经济合理方面考虑都还存在一定的问题,所以目前国内外一般都把净化后的炉气作为燃料气使用,大多用于锅炉、气烧石灰窑,碳材干燥等方面。
炉气净化有干法和湿法两种工艺。
干法净化技术国内尚未过关,技术及设备需从国外引进,投资较大。
湿法净化工艺虽然成熟,但投资高,污水处理所占场地大,且有二次污染,在技术上不可取。
目前挪威、西德和日本等国家对密闭电石炉气普遍采用干法除尘净化,以代替传统的湿法除尘净化,从而避免了湿法净化带来的二次污染问题。
50年代中期,西德SKW公司率先颁布以素烧陶管为过滤材料的炉气干法净化流程,并对收集的粉尘经过焚烧处理除去氰化物。
70年代,日本BEC公司开发了以玻璃纤维布袋为中心的较经济的全密闭式除尘的炉气净化流程,也包括粉尘焚烧炉,引起了许多国家的关注。
提高电炉余热利用率方案探讨

提高电炉余热利用率方案探讨清晨的阳光透过窗帘,洒在办公室的角落,我泡了杯热咖啡,开始构思这个方案。
电炉余热利用率,这个议题在我脑海中盘旋已久,如何让这些余热发挥出最大的价值,我决定用我十年的方案写作经验,来一场意识流的探讨。
一、问题分析1.余热回收设备不完善,导致余热无法有效回收。
2.生产工艺不合理,导致余热无法充分利用。
3.技术水平限制,无法实现高效回收。
二、解决方案1.完善余热回收设备(1)优化电炉设计,提高热交换效率。
(2)采用高效热交换器,提高余热回收效率。
(3)引入先进的控制系统,实现余热回收设备的自动调节。
2.优化生产工艺(1)调整电炉操作参数,降低能耗。
(2)合理布局生产线,减少热量损失。
(3)加强生产管理,提高生产效率。
3.技术创新(1)研究新型余热回收技术,提高回收效率。
(2)引入大数据分析,优化余热利用方案。
(3)加强与国际先进技术的交流合作,提升自身技术水平。
三、实施步骤1.调查研究(1)了解国内外电炉余热利用的现状。
(2)分析现有技术的优缺点。
(3)收集相关资料,为后续工作提供依据。
2.制定方案(1)根据调查研究结果,制定具体的余热利用方案。
(2)充分考虑生产实际,确保方案的可行性。
(3)明确实施步骤,确保方案顺利实施。
3.实施与监督(1)加强项目管理,确保工程进度。
(2)定期检查,确保工程质量。
(3)建立完善的监督机制,确保方案的实施效果。
四、预期效果1.提高电炉余热利用率,降低能耗。
2.减少环境污染,实现可持续发展。
3.提高企业经济效益,增强市场竞争力。
在这个过程中,我们需要充分发挥技术创新的优势,优化生产工艺,完善余热回收设备,实现高效回收。
同时,加强与国际先进技术的交流合作,不断提升自身技术水平。
让我们携手共进,为实现电炉余热的高效利用而努力!注意事项一:确保设备匹配与兼容性在实际操作中,新引入的高效热交换器与现有电炉系统可能存在匹配问题,这就像给一台老车换上了新引擎,得确保整个动力系统协调运作。
电石炉余热利用方案

40MVA电石炉节能技改方案草拟:孙继江(高级工程师)电话:1乌海市江嘉节能服务有限公司2014年4月电石炉技改方案引言目前,我国每年产生的电石炉尾气超过150亿m3。
处置方式基本为炉气直排或点火炬,不仅浪费了大量能源,也造成环境污染。
国家对此十分重视,在《电石行业准入条件(2007年修订)》中明确规定“新建电石生产装置必须采用密闭式电石炉,电石炉气必须综合利用”,“密闭式电石装置的炉气(指CO气体)必须综合利用,正常生产时不允许炉气直排或点火炬”。
但由于电石炉尾气成分复杂,净化提纯难度大,国内外目前可供选用的真正成熟可行且实现了工业化生产的技术工艺很少,因而电石炉尾气回收利用率一直很低。
截至2008年底,全国电石炉尾气的利用量尚不足15亿m3,利用率不足10%。
每年因此损失约240万吨标准煤,同时排放约1200万吨二氧化碳和90余万吨粉尘。
研究开发经济合理、工艺技术可行的电石炉尾气利用途径,迫在眉睫。
项目建设单位简介:为乌海xxxx化工公司,现有17MVA电石炉两座,技改为40MVA全密闭电石炉一座,配套50万t白灰窑一座,2000kw烟气余热发电机组一套。
一. 电石炉余热回收利用方案1、余热资源情况电石炉炉型全密闭电石炉电石炉容量/MV A 40 MV A烟气发热值/KJ/N m311000-13500出口烟气温度/ ℃600-1000烟气含尘量, /g/Nm3 50-200炉烟气量/Nm3/h 22000-30000烟气焦油含量/mg/Nm3 ≤150热值(kJ/Nm3):2400~2700kcal/ Nm3)2.密闭电石炉、白灰窑烟气余热综合利用工艺流程2.1. 一台40000KVA密闭电石炉,产电石11.5t/h,产生电石废气量4666m3/h, , 废气温度600-1000℃,尾气综合利用一套干法除尘(旋风+布袋)系统组成。
废气入口600℃, 废气出口200℃。
2.2 一台12万t白灰窑,t灰用CO300m3,产白灰15.5t/h(耗用电石废气4650Nm3),产生废气10万m3/h, 废气温度350-450℃,尾气综合利用机组方案由一台10t/h蒸汽锅炉和一套除尘(旋风+布袋)系统组成。
电站锅炉余热利用实施方案样本
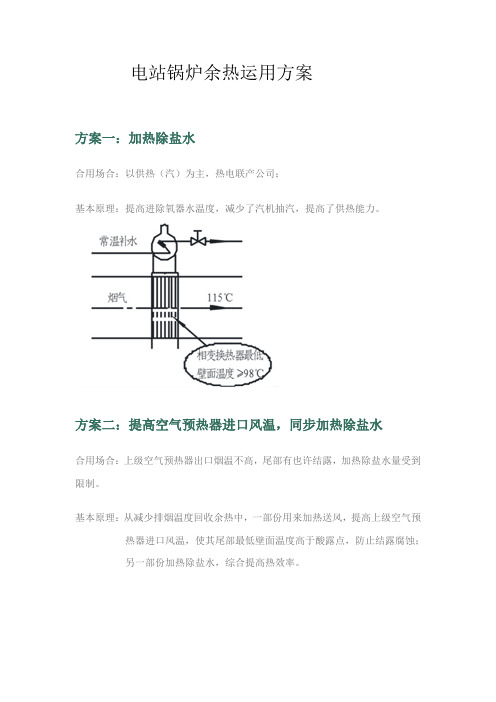
电站锅炉余热运用方案方案一:加热除盐水合用场合:以供热(汽)为主,热电联产公司;基本原理:提高进除氧器水温度,减少了汽机抽汽,提高了供热能力。
方案二:提高空气预热器进口风温,同步加热除盐水合用场合:上级空气预热器出口烟温不高,尾部有也许结露,加热除盐水量受到限制。
基本原理:从减少排烟温度回收余热中,一部份用来加热送风,提高上级空气预热器进口风温,使其尾部最低壁面温度高于酸露点,防止结露腐蚀;另一部份加热除盐水,综合提高热效率。
方案三:内部循环方式合用场合:系统对加热除盐水没有运用价值。
基本原理:一方面,恰当增长锅炉省煤器受热面,可大幅度减少排烟温度提高锅炉热效率。
另一方面,运用相变段整体壁温可调可控、不结露特点,加热锅炉送风、提高空气预热器进口风温,从而避免其遭受结露腐蚀侵害。
方案四:余热锅炉(中、低压)合用场合:系统给水温度和热风温度较高,顾客需要一定量中、低压蒸汽。
基本原理:一、在转向室增设中、低压蒸发段,生产中、低压蒸汽,用以减少排烟温度提高锅炉热效率。
二、运用相变段整体壁温可调可控不结露特点,加热送风,提高空预器最低壁面温度,保证空预器避免低温结露腐蚀。
1—自控装置,2—自控阀,3—低压蒸汽汽包,4—低压蒸汽上升管,5—低压蒸汽下降管,6—低压蒸发段,7—原省煤器,8—低压给水泵,9—空气预热器,,10—烟道,11—相变换热器下段,12—壁温测试仪,13—相变换热器上段,14—风道,15—低压蒸汽汽包安全阀,16—低压蒸汽汽包液位计节能效果•将使锅炉热效率提高1.5%-10%;•大大减少了设备更新费用和锅炉检修停机损失;•在节约燃料同步,相应减少了热污染和燃烧尾气排放量,改进了环境,具备良好社会综合效益节能效益估算表锅炉蒸发量(吨/小时)原排烟温度(℃)设计排烟温度(℃)So2减少排放量(吨/年)Co2减少排放量(吨/年)节煤量(吨/年)35 170 115 42 2952 167865 160 115 60 4215 2392130 155` 115 79 5577 3169 220 150 115 119 8362 4751 410 150 115 205 14443 8206 1000 140 115 320 22519 12795备注:1.假设锅炉原排烟温度为135-170 ℃;2.燃煤热值为5000大卡/公斤;3.受热面最低壁面温度≥ 100 ℃;4.锅炉年运营时间为300天;节能效益计算公式及举例节能效益计算公式符号单位名称Q g Kw 回收热量V g Nm3/h 烟气流量ρg Kg/Nm3烟气密度Cp kj/(kg℃) 烟气比热△t ℃烟气温降φ0.92-0.99 保热系数G c吨/年年节煤量HR h 年运营小时数Q P Kj/kg 煤发热量ηk% 锅炉效率举例某130T/h煤粉炉设计烟气量135000Nm/h,设计出口烟气温度146.7℃,实际运营出口烟气温度190℃,年运营时间8000 小时。
电石炉节能减排以及炉气余热综合利用

电石炉节能减排以及炉气余热综合利用作者:李旭冯召海来源:《经济技术协作信息》 2018年第14期众所周知,电石是高耗能、高污染、高危险的行业。
目前,国内仍然部分企业在电石生产过程产生的高温烟气直接排空,不仅造成了能源的严重浪费,而且污染了环境。
因此研究解决完善炉气利用技术从科学发展观角度对于实现环境保护、劳动保护以及实现能源回收利用、降低生产成本、提高企业和社会经济效益,都有着重要的意义。
节能减排既是促进经济社会可持续发展的需要,也是保护我们的生存环境,提高生活质量,维护民族长远利益的需要。
因此,节能减排,刻不容缓。
为了加强环境保护治理和实现能源回收利用、降低生产成本、提高企业和社会效益,根据国家对电石行业准入要求。
密闭式电石炉炉气(指CO 气体)必须综合利用,正常生产时不允许炉气直排或点火炬。
为了加强环境保护治理和实现能源回收利用、降低生产成本、提高企业和社会效益,由于企业规模小,技术装备落后,难以统筹安排资源综合利用设施,废气中大量一氧化碳和高温余热都不能有效回收,多数废渣和粉料也没有得到合理利用,造成能源和资源的浪费。
一、电石行业的现状概况半密闭电石炉生产规模较小,生产成本较高,预热能源利用较低,而且对环境造成一定污染,根据国家对环保要求,小型半密闭电石炉已经逐步退出电石行业竞争,密闭电石炉是电石行业发展的趋势。
半密闭电石炉设备运行率较低,安全性能较低,生产过程产生的大量炉气燃烧后直接排空,或是利用烟气烘干炭材、余热锅炉等,利用效率较低;依据能源利用规律,能源高效高利用,体现出能源的真实价值,我公司将原有的半密闭电石炉技术改造为密闭电石炉,炉气作为烧制石灰燃料,其次在生产过程中产生的粉尘进行集中收集处理,送至附近水泥厂,直接经济效益可大幅度降低生产成本,间接经济效益实现炉气综合利用,排放标准完全符合国家环保要求。
二、项目改造前基本情况我公司拥有两台4 万吨/ 年21MVA半密闭式电石炉,两台5 万吨/ 年30MVA半密闭式电石炉,四台5 万吨/ 年30MVA密闭式电石炉。
电石炉烟气净化及余热利用技术的开发与应用(一)

电石炉烟气净化及余热利用技术的开发与应用(一)1概况中国电石行业约有电石炉四百多座,年产量居世界首位。
国内电石行业在规模、炉型、布局、节能、环保上存在先天不足,再加上原料质量差、管理水平仍然比较低,同时能耗高、污染严重。
一方面电石炉烟气的余热利用效果不佳,另一方面电石炉烟气的除尘净化更是难中之难、重中之重。
在电石生产中,电石炉的烟气是最大污染源,以一座10000KVA的开放式电石炉为例,年排放废气量(以每年生产10个月计算)达6亿标准立方米,年粉尘排放量超过1000吨,污染极其严重。
由于电石炉烟气温度高,粉尘性质特殊,风量变化大,国内电石行业采用了许多除尘技术,进行了大量的烟气净化的实践,但都未能根本解决问题。
为推动国内电石炉行业技术进步,我国八十年代末从德国、挪威、日本等国引进8套25000KVA 全密闭电石炉,引进中空电极、气烧窑、组合式把持器、干法除尘、计算机控制等五项新技术。
从应用上看,组合式把持器、计算机控制二项技术获得了成功,但中空电极、电石炉烟气干法除尘技术却始终无法成功,由于烟气无法净化而不能向气烧窑提供洁净的气源,导致气烧窑技术也最终失败,烟气的污染不能解决,烟气中的大量的热能也白白浪费。
国内电石炉烟气净化的实践告诉我们:无论是早期自行研制的电石炉除尘技术,还是从国外引进的新技术,或者改进后的除尘技术;无论是采用电除尘技术、或者袋除尘技术,还是采用耐高温陶瓷过滤技术,或者水除尘技术,都因为无法适应电石炉烟气变化和焦油糊袋、或形成二次污染而最终全部失败。
新老项目普遍产生的严酷现实使电石炉行业认识到:即使是引进国外技术,也必须是成熟过硬的技术,还要符合中国的国情,否则将无法发挥其先进性。
同时,要求国内电石行业必须下更大的力气和决心开发适合中国国情的电石炉烟气余热利用和烟气净化装制。
1996年8月,由国家建材局合肥水泥研究设计院、中国船舶工业总公司第七研究院、三明化工总厂等单位共同承担设计的电石炉烟气净化及余热利用系统在三明化工总厂4#电石炉投入运行。
电石炉烟气余热利用及净化技术介绍
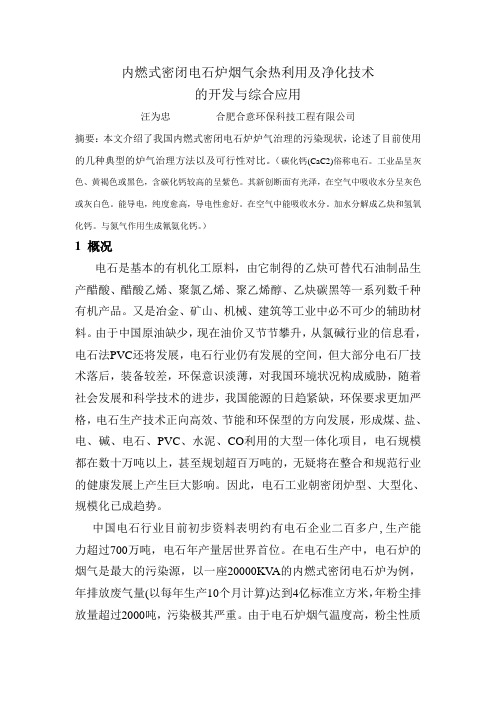
内燃式密闭电石炉烟气余热利用及净化技术的开发与综合应用汪为忠合肥合意环保科技工程有限公司摘要:本文介绍了我国内燃式密闭电石炉炉气治理的污染现状,论述了目前使用的几种典型的炉气治理方法以及可行性对比。
(碳化钙(CaC2)俗称电石。
工业品呈灰色、黄褐色或黑色,含碳化钙较高的呈紫色。
其新创断面有光泽,在空气中吸收水分呈灰色或灰白色。
能导电,纯度愈高,导电性愈好。
在空气中能吸收水分。
加水分解成乙炔和氢氧化钙。
与氮气作用生成氰氨化钙。
)1 概况电石是基本的有机化工原料,由它制得的乙炔可替代石油制品生产醋酸、醋酸乙烯、聚氯乙烯、聚乙烯醇、乙炔碳黑等一系列数千种有机产品。
又是冶金、矿山、机械、建筑等工业中必不可少的辅助材料。
由于中国原油缺少,现在油价又节节攀升,从氯碱行业的信息看,电石法PVC还将发展,电石行业仍有发展的空间,但大部分电石厂技术落后,装备较差,环保意识淡薄,对我国环境状况构成威胁,随着社会发展和科学技术的进步,我国能源的日趋紧缺,环保要求更加严格,电石生产技术正向高效、节能和环保型的方向发展,形成煤、盐、电、碱、电石、PVC、水泥、CO利用的大型一体化项目,电石规模都在数十万吨以上,甚至规划超百万吨的,无疑将在整合和规范行业的健康发展上产生巨大影响。
因此,电石工业朝密闭炉型、大型化、规模化已成趋势。
中国电石行业目前初步资料表明约有电石企业二百多户,生产能力超过700万吨,电石年产量居世界首位。
在电石生产中,电石炉的烟气是最大的污染源,以一座20000KVA的内燃式密闭电石炉为例,年排放废气量(以每年生产10个月计算)达到4亿标准立方米,年粉尘排放量超过2000吨,污染极其严重。
由于电石炉烟气温度高,粉尘性质特殊,风量变化大,国内电石行业采用了许多除尘技术,进行了大量的烟气净化的实践,但都未能根本解决问题。
在全国电石行业,无论是全密闭电石炉、半密闭电石炉还是开放式电石炉,其烟气治理技术多年来都一直是国内电石行业的难题而无法解决。
电石生产过程中石灰窑尾气余热利用工艺
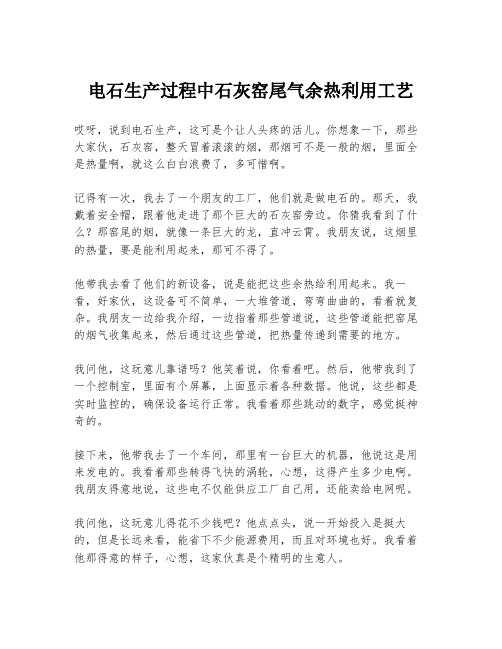
电石生产过程中石灰窑尾气余热利用工艺哎呀,说到电石生产,这可是个让人头疼的活儿。
你想象一下,那些大家伙,石灰窑,整天冒着滚滚的烟,那烟可不是一般的烟,里面全是热量啊,就这么白白浪费了,多可惜啊。
记得有一次,我去了一个朋友的工厂,他们就是做电石的。
那天,我戴着安全帽,跟着他走进了那个巨大的石灰窑旁边。
你猜我看到了什么?那窑尾的烟,就像一条巨大的龙,直冲云霄。
我朋友说,这烟里的热量,要是能利用起来,那可不得了。
他带我去看了他们的新设备,说是能把这些余热给利用起来。
我一看,好家伙,这设备可不简单,一大堆管道,弯弯曲曲的,看着就复杂。
我朋友一边给我介绍,一边指着那些管道说,这些管道能把窑尾的烟气收集起来,然后通过这些管道,把热量传递到需要的地方。
我问他,这玩意儿靠谱吗?他笑着说,你看着吧。
然后,他带我到了一个控制室,里面有个屏幕,上面显示着各种数据。
他说,这些都是实时监控的,确保设备运行正常。
我看着那些跳动的数字,感觉挺神奇的。
接下来,他带我去了一个车间,那里有一台巨大的机器,他说这是用来发电的。
我看着那些转得飞快的涡轮,心想,这得产生多少电啊。
我朋友得意地说,这些电不仅能供应工厂自己用,还能卖给电网呢。
我问他,这玩意儿得花不少钱吧?他点点头,说一开始投入是挺大的,但是长远来看,能省下不少能源费用,而且对环境也好。
我看着他那得意的样子,心想,这家伙真是个精明的生意人。
最后,我问他,这技术能普及吗?他笑了笑,说现在很多人都在关注这个,毕竟节能减排是大势所趋。
他指着那些管道说,你看,这些管道虽然复杂,但是它们能把那些浪费的热量变成实实在在的能源,这可是个大进步。
离开工厂的时候,我回头看了看那些冒着烟的石灰窑,心想,这些大家伙要是都能装上这样的设备,那得省下多少能源啊。
我朋友说,他们还在不断改进技术,希望能让这个过程更简单,成本更低。
我看着他那充满希望的眼神,心里也暖暖的。
总之,这次经历让我大开眼界,原来那些看似无用的烟气,也能变成宝贵的能源。
- 1、下载文档前请自行甄别文档内容的完整性,平台不提供额外的编辑、内容补充、找答案等附加服务。
- 2、"仅部分预览"的文档,不可在线预览部分如存在完整性等问题,可反馈申请退款(可完整预览的文档不适用该条件!)。
- 3、如文档侵犯您的权益,请联系客服反馈,我们会尽快为您处理(人工客服工作时间:9:00-18:30)。
40MVA电石炉节能技改方案草拟:孙继江(高级工程师)电话:1乌海市江嘉节能服务有限公司2014年4月电石炉技改方案引言目前,我国每年产生的电石炉尾气超过150亿m3。
处置方式基本为炉气直排或点火炬,不仅浪费了大量能源,也造成环境污染。
国家对此十分重视,在《电石行业准入条件(2007年修订)》中明确规定“新建电石生产装置必须采用密闭式电石炉,电石炉气必须综合利用”,“密闭式电石装置的炉气(指CO气体)必须综合利用,正常生产时不允许炉气直排或点火炬”。
但由于电石炉尾气成分复杂,净化提纯难度大,国内外目前可供选用的真正成熟可行且实现了工业化生产的技术工艺很少,因而电石炉尾气回收利用率一直很低。
截至2008年底,全国电石炉尾气的利用量尚不足15亿m3,利用率不足10%。
每年因此损失约240万吨标准煤,同时排放约1200万吨二氧化碳和90余万吨粉尘。
研究开发经济合理、工艺技术可行的电石炉尾气利用途径,迫在眉睫。
项目建设单位简介:为乌海xxxx化工公司,现有17MVA电石炉两座,技改为40MVA全密闭电石炉一座,配套50万t白灰窑一座,2000kw烟气余热发电机组一套。
一. 电石炉余热回收利用方案1、余热资源情况电石炉炉型全密闭电石炉电石炉容量/MV A 40 MV A烟气发热值/KJ/N m311000-13500出口烟气温度/ ℃600-1000烟气含尘量, /g/Nm3 50-200炉烟气量/Nm3/h 22000-30000烟气焦油含量/mg/Nm3 ≤150热值(kJ/Nm3):2400~2700kcal/ Nm3)2.密闭电石炉、白灰窑烟气余热综合利用工艺流程2.1. 一台40000KVA密闭电石炉,产电石11.5t/h,产生电石废气量4666m3/h, , 废气温度600-1000℃,尾气综合利用一套干法除尘(旋风+布袋)系统组成。
废气入口600℃, 废气出口200℃。
2.2 一台12万t白灰窑,t灰用CO300m3,产白灰15.5t/h(耗用电石废气4650Nm3),产生废气10万m3/h, 废气温度350-450℃,尾气综合利用机组方案由一台10t/h蒸汽锅炉和一套除尘(旋风+布袋)系统组成。
废气入口400℃, 废气出口100℃。
余热回收值: 10000 m3,300-400℃的废气经过锅炉可产生,1000kg过热蒸汽,发电200kw/h,1kw/h等值于0.39kg标煤烟气可回收余热量:100000/1000/1000=10t/h(蒸汽)×200kw/t=2000kw/h可装机2000kwh/400v.2.3. 余热回收产蒸汽10t/h,通过废气贮灌汽源,驱动一套2000kwh/400v汽轮发电机组,运行8000h/年可发电16MW。
减排6240Nt。
3. 余热发电投资估算主要投资内容及投资估算如表4所示。
3.1投资分析(1)年发电量:发电装机容量2000kW,年发电时间8000小时,年发电量16MW·h。
(2)运行成本:包括人工、机油、维修及配件、消耗件、管理、不可预测等费用,折合单位发电成本为0.10元/kW·h。
则年运行成本费用为=16万MW·h×0.10元/kW·h=160万元。
(3)年发电收益:发电电价按用电电价0.55元/kW·h计算,年发电收益=年发电总量×发电电价=16MW·h×0.55元/kW·h=880万元。
(4)经济效益:年收益=880万元-160万元=720万元。
(5)技改奖励:300万元(6)投资回收期:(1465-300)÷720万元=1.3年(约18个月)。
二.140m3气烧石灰窑方案一、简述:用电石炉煤气煅烧石灰是行业最可行的技术改造项目。
一来有利环保、二来有非常好经济效益,而且用圆筒的炉型,投资小、见效快。
二、2×280m3竖炉基本参数和指标1. 竖炉为直立圆筒型,有效容积280m3。
炉体高度26.5M,直径9M。
2. 产量 400/日。
3. 燃气消耗电石炉煤气300m3/t.灰。
4. 石灰石粒度40-80mm。
5. 电力总装机容量500kw。
三、双筒竖炉主要结构竖炉主要有炉体、上料斜桥、炉顶装料、出灰机、助燃风机、冷却风机和燃烧器及温度仪表控制及抽烟除尘等几部分组成。
炉体外为金属壳,内砌耐火砖。
四、工艺简述经筛分处理后的合格石灰石原料,由卷杨机拉动料车经斜桥提升至炉顶装入炉内,在炉体中部,园周装有32组燃烧器(高炉煤气使用预混式蜗流燃烧器,焦炉煤气要使用我们研究设计的外混式长火焰烧咀燃烧器和煤气稀释装置。
焦炉煤气热值高,火焰短,不配用这两种专用设备是不能用于烧石灰的)将煤气送入炉内并和助燃风混合燃烧,石灰石在自重作用下的下降过程中,与炽热的煤气火焰进行复杂的热交换,并伴随着石灰石的晶粒发育成长过程完成煅烧。
再三经冷却带被助燃风冷却,然后由卸灰阀卸出炉外。
环保要求严格的要增加抽风机和布袋除尘及平板出灰机等设备。
五、主要设备(单台)1、卷杨机3t;2、上料小车 1.2m3;3、园盘出灰机(或阀式卸灰器) 1台;4、助燃风机9-19 35kw 1台;5、冷却风机9-19 35kw 1台;6、煤气燃烧器 32套;7、电振给料器 1台;8、各种管道阀门 1套;9、电器仪表控制系统设备 1套;六、投资概算包括土建基础,炉体全部设备,带除尘抽风系统的800万左右。
七、效益分析1.气烧石灰没有煤炭能源消耗(用煤烧每吨灰用煤为200公斤-250公斤)所以成本低,而且质量好,无渣又活性好,对电石有非常大的质量作用。
根据现在不少企业核算,每吨灰的利润在60-80元,两座炉一年生产12.5万吨灰,一般一年便可收回投资。
2.效益估算年产白灰12.5万t×64元/t=800万元投资回收期:12个月三.总结建议1.电石尾气煅烧白灰窑;投资800万元,年产白灰12.5万t;效益800-1000万元;所产白灰可满足电石炉所需(9万t/年)。
2.白灰窑余热利用发电;投资1465万元,发电16MW/年,效益720万/年;可用于本厂低压侧接入自用。
3.两项投资回收期;(800+1465)/(800+720)=1.5(年)4.并且可以申报节能奖励资金、财政补贴。
根椐以上设计分析,本项目社会效益与经济效益十分可观,应尽快决策实施。
四.相关参考文献2 密闭电石炉尾气利用途径分析密闭电石炉尾气现有的利用途径可分为两大类:用做燃料或化工原料。
2.1 用做尾气余热锅炉热源发电该技术将密闭电石炉的含尘尾气直接引入特别设计的余热锅炉换热,充分利用电石炉尾气的显热、生产蒸汽。
同时通过锅炉炉膛、烟道落灰斗重力沉降及特别设计的电除尘器对烟气进行除尘处理,达到电石炉尾气热能利用及干法除尘的双重目的。
该技术巧妙地避开了电石炉尾气难以净化的难题,采取先换热后除尘的方案,一台尾气锅炉系统集除尘、供汽、消除有毒有害污染物于一体;电石炉出来的高温炉气经尾气锅炉后。
高温电石炉尾气不经冷却直接进入尾气锅炉换热,其炉气显热、得到了最大限度地利用,克服了干、湿法除尘装置需先对炉气进行冷却,易造成物理显热及除尘灰中炭尘燃烧热得不到利用的缺点,是目前较为成功的技术,所产出的过热蒸汽用于发电。
2.2 用做石灰窑生产的热源燃料电石属高能耗产品,其生产过程中的石灰烧制、焦炭干燥等都需要大量的热源。
采用电石炉尾气做热源燃料,可就近利用电石炉尾气,直接降低电石能耗,国内已有多家企业采用该技术。
君正有限公司采用自行开发的尾气干法净化技术,回收的尾气全部用于气烧石灰窑,石灰再用于电石炉生产电石,即节约了资源,又保护了环境,实现了尾气平衡综合利用。
此种利用途径的缺点和局限性是:电石炉尾气需先除尘净化,净化过程易产生二次污染;目前,输送工艺、气烧石灰窑工艺本身还存在一些问题;净化后的尾气属高价值燃料,作为普通燃料使用太可惜。
3 密闭电石炉尾气利用新途径能源生产和供应形式多样化已经成为必然发展趋势,分布式能源是提高能源有效利用率、保护环境的有效途径,已受到世界各国的高度重视并得到广泛应用。
将净化后的电石炉尾气,作为燃气内燃机发电的燃料,具有典型的分布式能源特征,可大可小,附加值高,技术成熟可靠。
3.1 余热发电原理电石炉排出的600~1000℃烟气直接进入余热锅炉换热,使烟气温度冷却至250℃以下排出,进入除尘器除尘,再进入净化装置,净化后的CO气源供给白灰窑使用。
3.2 余热发电工艺流程余热锅炉汔轮机发电系统分为三大部分,电石炉尾气预处理系统、发电系统、外部配套系统。
具体包括电石炉尾气净化、冷却水循环、发电和输配电、余热利用装置、厂房土建等。
其工艺流程如下图:4 结论与建议(1)电石炉尾气作为燃气内燃机燃料,具有显着的分布式能源特征,模块式设计可大可小,投资灵活,技术成熟可靠,能源利用效率高,投资回收期短。
主要产品为电,无市场风险。
特别适合我国电石生产企业多、分布广的国情。
(2)建议有关部门在《电石行业准入条件(2007年修订)》的基础上,制定相应的鼓励政策,促进电石炉尾气的利用,推进电石行业的节能减排工作。
按实际经验生产一公斤石灰约需960kcal热量。
但由于各厂的生产设备和工艺条件各不同也有区别。
一般来说,烧一吨灰用高炉煤气需1600m3左右,烧焦炉煤气需300m3左右。
电石尾气需360m3左右,天然气需120m3左右,发生炉煤气需900m3左右。
在气烧炉内煅烧一吨石灰大约需一百万千卡热量。
一般所需用不同燃料的数量则按它的最低热值换算:高炉煤气热值约850千卡故烧1吨石灰约需1200M3左右。
焦炉煤气热值约4000千卡故烧1吨石灰约需250M3 左右。
发生炉煤气热值约1250千卡故烧1吨石灰约需800M3 左右。
天然气热值约8000千卡故烧1吨石灰约需130M3 左右。
表1不同炉型电石炉的烟气工艺参数承建节能环保型双套筒石灰窑(气烧窑)(2009-04-09 09:45:49)转载▼标签:石灰窑套筒热耗炉况三台杂谈分类:石灰窑双套筒窑采用了窑壳和内套筒的特殊结构,使并流煅烧过程在一个窑体内进行,且占地面积比双膛窑少,生产出来的石灰活性度较高,可达350ml以上,石灰中残余CO2含量小于1.5%,如原料条件好,石灰活性度还可提高,且产品的生烧和过烧现象较少。
双套筒窑使用的燃料范围宽,可使用发热值在1100kCal/Nm3以上的低热值煤气,且煤气压力仅为15kPa左右的常规压力。
整座窑采用循环气体、高温废气换热等方式循环利用热能,所以产品所需的热耗也较低,是一种节能型的石灰窑。
煅烧采用则同时采用了气流的并流和逆流原理,有效地解决了生、过烧问题,提高了石灰的活性。