丁苯橡胶装置自聚物产生原因分析及处
丁苯橡胶制备实验报告(3篇)

第1篇一、实验目的1. 了解丁苯橡胶的合成原理及制备方法。
2. 掌握乳液聚合反应的基本操作和实验技能。
3. 分析丁苯橡胶的性能及其影响因素。
二、实验原理丁苯橡胶(SBR)是一种合成橡胶,由丁二烯和苯乙烯在引发剂的作用下进行乳液聚合反应而成。
该反应过程为自由基聚合反应,具体原理如下:\[ n\text{C}_4\text{H}_6 + n\text{C}_6\text{H}_5\text{CH}=CH_2\rightarrow (\text{C}_6\text{H}_5\text{CH}-\text{CH}_2\text{C}_4\text{H}_6)_n \]其中,C4H6代表丁二烯,C6H5CH=CH2代表苯乙烯,n为聚合度。
三、实验仪器与试剂1. 仪器:搅拌器、反应釜、温度计、压力计、真空泵、乳液聚合反应装置等。
2. 试剂:丁二烯、苯乙烯、引发剂(过氧化氢、过硫酸铵等)、乳化剂(十二烷基硫酸钠等)、调节剂(十二烷基苯磺酸钠等)、去离子水等。
四、实验步骤1. 准备反应釜,加入适量的去离子水。
2. 加入引发剂,搅拌均匀,待引发剂完全溶解。
3. 加入乳化剂,搅拌均匀。
4. 加入苯乙烯和丁二烯,搅拌均匀。
5. 将反应釜加热至预定温度,维持一段时间。
6. 冷却反应釜,终止聚合反应。
7. 离心分离乳液,得到丁苯橡胶乳液。
8. 将乳液干燥,得到丁苯橡胶粉。
五、实验结果与分析1. 实验结果根据实验条件,我们制备了不同分子量的丁苯橡胶。
实验结果表明,随着聚合温度、聚合时间、单体浓度等条件的改变,丁苯橡胶的分子量、门尼粘度、抗拉强度等性能也会发生变化。
2. 结果分析(1)聚合温度:温度对丁苯橡胶的分子量有显著影响。
温度越高,分子量越小。
这是因为高温有利于自由基的生成和迁移,导致链增长反应加剧,从而降低分子量。
(2)聚合时间:聚合时间对丁苯橡胶的性能也有一定影响。
随着聚合时间的延长,分子量逐渐增大,抗拉强度和硬度也随之提高。
丁苯橡胶聚合机理
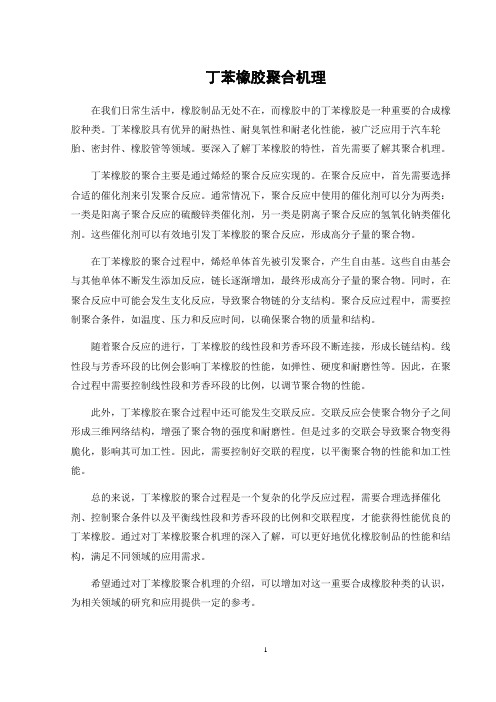
丁苯橡胶聚合机理在我们日常生活中,橡胶制品无处不在,而橡胶中的丁苯橡胶是一种重要的合成橡胶种类。
丁苯橡胶具有优异的耐热性、耐臭氧性和耐老化性能,被广泛应用于汽车轮胎、密封件、橡胶管等领域。
要深入了解丁苯橡胶的特性,首先需要了解其聚合机理。
丁苯橡胶的聚合主要是通过烯烃的聚合反应实现的。
在聚合反应中,首先需要选择合适的催化剂来引发聚合反应。
通常情况下,聚合反应中使用的催化剂可以分为两类:一类是阳离子聚合反应的硫酸锌类催化剂,另一类是阴离子聚合反应的氢氧化钠类催化剂。
这些催化剂可以有效地引发丁苯橡胶的聚合反应,形成高分子量的聚合物。
在丁苯橡胶的聚合过程中,烯烃单体首先被引发聚合,产生自由基。
这些自由基会与其他单体不断发生添加反应,链长逐渐增加,最终形成高分子量的聚合物。
同时,在聚合反应中可能会发生支化反应,导致聚合物链的分支结构。
聚合反应过程中,需要控制聚合条件,如温度、压力和反应时间,以确保聚合物的质量和结构。
随着聚合反应的进行,丁苯橡胶的线性段和芳香环段不断连接,形成长链结构。
线性段与芳香环段的比例会影响丁苯橡胶的性能,如弹性、硬度和耐磨性等。
因此,在聚合过程中需要控制线性段和芳香环段的比例,以调节聚合物的性能。
此外,丁苯橡胶在聚合过程中还可能发生交联反应。
交联反应会使聚合物分子之间形成三维网络结构,增强了聚合物的强度和耐磨性。
但是过多的交联会导致聚合物变得脆化,影响其可加工性。
因此,需要控制好交联的程度,以平衡聚合物的性能和加工性能。
总的来说,丁苯橡胶的聚合过程是一个复杂的化学反应过程,需要合理选择催化剂、控制聚合条件以及平衡线性段和芳香环段的比例和交联程度,才能获得性能优良的丁苯橡胶。
通过对丁苯橡胶聚合机理的深入了解,可以更好地优化橡胶制品的性能和结构,满足不同领域的应用需求。
希望通过对丁苯橡胶聚合机理的介绍,可以增加对这一重要合成橡胶种类的认识,为相关领域的研究和应用提供一定的参考。
1。
丁苯橡胶装置聚合反应的影响因素及调整

丁苯橡胶装置聚合反应的影响因素及调整发表时间:2020-12-29T11:04:47.540Z 来源:《科学与技术》2020年26期作者:宋子威[导读] 丁苯橡胶生产由于工艺复杂、使用助剂品种多、流程长等因素宋子威抚顺石化烯烃厂丁苯橡胶车间摘要:丁苯橡胶生产由于工艺复杂、使用助剂品种多、流程长等因素,一旦发生反应波动,需较长的时间进行调整才能使工艺参数恢复正常,此时要综合对各岗位生产工艺进行超前调整,维持生产运行平稳,在保证质量的同时,提高产量,降低消耗。
关键词:工艺操作;反应时间;加料水平;原料质量引言在绿色低碳的大趋势下,人们对橡胶产品质量要求越来越高,特别是汽车行业要求轮胎具有良好的抗湿滑性能和低噪声,这就迫使橡胶生产企业对橡胶产品进行全面品质升级。
环保型溶聚丁苯橡胶(SSBR)是生产高性能轮胎的重要原料,具有耐磨、低生热和低滚动阻力等特点,结构可调节性强,可达到绿色轮胎的使用要求。
我国橡胶产品在牌号、质量和性能等方面仍与先进国家的产品存在一定差距,周边国家如日本、新加坡、印度、韩国等纷纷新建或扩建丁苯橡胶(SBR),尤其是SSBR生产装置,使得市场竞争更加激烈[6-9]。
因此,针对环保型SSBR生产过程中存在的问题进行研究,优化生产工艺,对提升产品竞争力和提产增效具有重要意义。
1聚合反应的影响因素1.1脱气塔塔盘完好水平度影响由于脱气塔在长时间连续运行过程中,塔釜塔盘在受力不匀或非正常操作条件等影响下局部凸起鼓包变形(主要是塔釜1、2层塔板),这样变形后的塔盘在投入生产后,出现塔盘胶乳局部凸起部分无胶乳降液层覆盖,蒸汽在传质传热过程中主要部分从凸起部位上升,而塔盘局部凸起部位由于局部受热过高短期内会出现大量凝胶,堵塞塔板开孔降低塔板开孔率,影响传质传热,塔盘未凸起区域从塔盘孔漏液,在局部高温下,产生大量凝胶,最终由于塔釜塔盘凝胶积聚无法完成传质传热,使整个脱气塔指标不合格,无法长周期运行。
制备丁苯橡胶实验报告
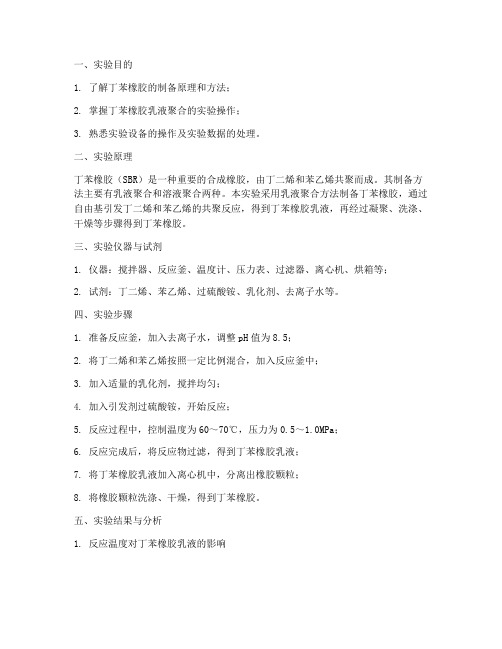
一、实验目的1. 了解丁苯橡胶的制备原理和方法;2. 掌握丁苯橡胶乳液聚合的实验操作;3. 熟悉实验设备的操作及实验数据的处理。
二、实验原理丁苯橡胶(SBR)是一种重要的合成橡胶,由丁二烯和苯乙烯共聚而成。
其制备方法主要有乳液聚合和溶液聚合两种。
本实验采用乳液聚合方法制备丁苯橡胶,通过自由基引发丁二烯和苯乙烯的共聚反应,得到丁苯橡胶乳液,再经过凝聚、洗涤、干燥等步骤得到丁苯橡胶。
三、实验仪器与试剂1. 仪器:搅拌器、反应釜、温度计、压力表、过滤器、离心机、烘箱等;2. 试剂:丁二烯、苯乙烯、过硫酸铵、乳化剂、去离子水等。
四、实验步骤1. 准备反应釜,加入去离子水,调整pH值为8.5;2. 将丁二烯和苯乙烯按照一定比例混合,加入反应釜中;3. 加入适量的乳化剂,搅拌均匀;4. 加入引发剂过硫酸铵,开始反应;5. 反应过程中,控制温度为60~70℃,压力为0.5~1.0MPa;6. 反应完成后,将反应物过滤,得到丁苯橡胶乳液;7. 将丁苯橡胶乳液加入离心机中,分离出橡胶颗粒;8. 将橡胶颗粒洗涤、干燥,得到丁苯橡胶。
五、实验结果与分析1. 反应温度对丁苯橡胶乳液的影响实验结果表明,反应温度对丁苯橡胶乳液的性能有较大影响。
随着反应温度的升高,丁苯橡胶乳液的分子量逐渐降低,聚合反应速率加快,但乳液稳定性变差。
因此,在实际生产中,应控制反应温度在60~70℃之间。
2. 反应压力对丁苯橡胶乳液的影响实验结果表明,反应压力对丁苯橡胶乳液的性能也有一定影响。
随着反应压力的升高,丁苯橡胶乳液的分子量逐渐降低,聚合反应速率加快。
但过高的压力会导致乳液稳定性变差,甚至出现暴聚现象。
因此,在实际生产中,应控制反应压力在0.5~1.0MPa之间。
3. 乳化剂种类对丁苯橡胶乳液的影响实验结果表明,不同种类的乳化剂对丁苯橡胶乳液的性能有较大影响。
其中,非离子型乳化剂具有较好的乳液稳定性,但乳液粘度较高;阴离子型乳化剂乳液粘度较低,但乳液稳定性较差。
丁苯橡胶装置生产工艺流程解析

03 .
凝聚和分离
Coagulation and separation
凝聚过程
丁苯橡胶装置
Styrene butadiene rubber device
生产工艺流程
Production process flow
凝聚过程
Coagulation process
凝聚过程是物质从混乱到有 序的转化过程,也是自然界
聚合反应条件控制
丁苯橡胶装置生产工艺流程解析 聚合反应条件控制是丁苯橡胶装置生产的关键环节。以下是聚合反应条件控制的几个主要方面: 1. 聚合反应温度控制 聚合反应温度是影响橡胶分子量及分子量分布的重要因素。温度过低会导致反应速率缓慢,影响生产效率;温度 过高则可能导致凝胶化,严重影响产品质量。因此,需要精确控制聚合反应温度,以确保生产效率和产品质量的 稳定。 2. 聚合反应压力控制 聚合反应压力也是影响橡胶分子量及分子量分布的重要因素。 压力过低可能导致凝胶化,影响产品质量;压力过高则可能导致设备损坏,增加能耗。因此,需要精确控制聚合 反应压力,以确保生产效率和产品质量的稳定。 3. 聚合反应时间控制 聚合反应时间也是影响橡胶分子量及分子量分布的重要因素。 时间过短可能导致反应不充分,影响产品质量;时间过长则可能导致凝胶化,影响生产效率。因此,需要精确控 制聚合反应时间,以确保产品质量的稳定和生产效率的提高。 4. 聚合反应物料配比控制 聚合反应物料配比也是影响橡胶分子量及分子量分布的重要因素。 物料配比不合理可能导致凝胶化,影响产品质量;物料配比过高则可能导致生产效率降低,增加能耗。因此,需 要精确控制聚合反应物料配比,以确保产品质量的稳定和生产效率的提高。
04 .
产品后处理
Product post-processing
丁苯橡胶装置凝聚水COD的影响因素分析
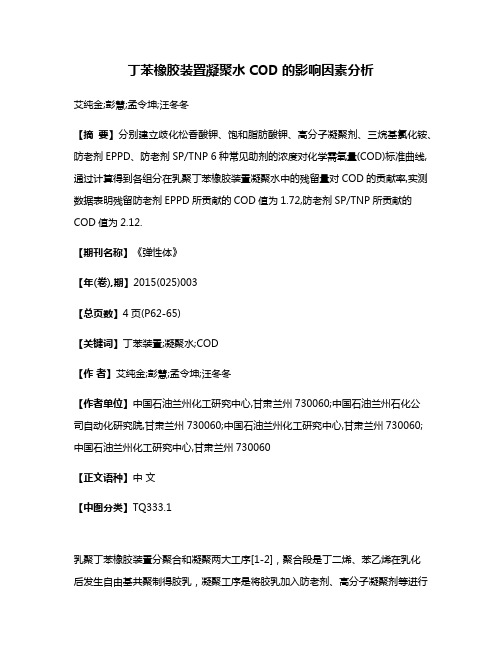
丁苯橡胶装置凝聚水COD的影响因素分析艾纯金;彭慧;孟令坤;汪冬冬【摘要】分别建立歧化松香酸钾、饱和脂肪酸钾、高分子凝聚剂、三烷基氯化铵、防老剂EPPD、防老剂SP/TNP 6种常见助剂的浓度对化学需氧量(COD)标准曲线,通过计算得到各组分在乳聚丁苯橡胶装置凝聚水中的残留量对COD的贡献率,实测数据表明残留防老剂EPPD所贡献的COD值为1.72,防老剂SP/TNP所贡献的COD值为2.12.【期刊名称】《弹性体》【年(卷),期】2015(025)003【总页数】4页(P62-65)【关键词】丁苯装置;凝聚水;COD【作者】艾纯金;彭慧;孟令坤;汪冬冬【作者单位】中国石油兰州化工研究中心,甘肃兰州730060;中国石油兰州石化公司自动化研究院,甘肃兰州730060;中国石油兰州化工研究中心,甘肃兰州730060;中国石油兰州化工研究中心,甘肃兰州730060【正文语种】中文【中图分类】TQ333.1乳聚丁苯橡胶装置分聚合和凝聚两大工序[1-2],聚合段是丁二烯、苯乙烯在乳化后发生自由基共聚制得胶乳,凝聚工序是将胶乳加入防老剂、高分子凝聚剂等进行分离脱水,该工序产生大量凝聚水,凝聚水中含有聚合工序的乳化剂和凝聚工序的凝聚剂、防老剂等组分,未经处理的凝聚水化学需氧量(COD)达3 000以上;防老剂具有强效抗臭氧和抗氧化特性[3-4],被认为是丁苯装置凝聚水COD的主要贡献因素。
系统研究了丁苯装置凝聚水中各组分对COD的贡献率,确定了丁苯橡胶SBR1500E中使用的防老剂EPPD和SBR1502E中使用的防老剂SP/TNP对COD的具体贡献值。
1 实验部分1.1 原料歧化松香酸钾(RS):工业品,质量分数为14.8%的水溶液;饱和脂肪酸钾(FA):工业品,质量分数为17.1%的水溶液;高分子凝聚剂(PC):工业品,质量分数为10.09%的水溶液;三烷基氯化铵(TAC):工业品,质量分数为28.5%的水溶液;EPPD:工业品,质量分数为27.45%的乳液;SP/TNP:工业品,质量分数为33.24%的乳液。
顺丁橡胶装置丁二烯自聚物防控措施分析
顺丁橡胶装置丁二烯自聚物防控措施分析摘要:本文分析丁二烯自聚物的产生、危害,通过总结大庆石化顺丁橡胶装置多年经验,提出了通过降低系统氧含量,酸洗钝化除铁锈及杂质,调整TBC加入等措施,有效缓解自聚物的生成速度,延长装置安全运行周期,从而提高经济效益。
关键词:顺丁橡胶;丁二烯;自聚物;TBC丁二烯属共轭二烯烃,因其化学结构中的碳双键化学性质十分活泼,所以在储存、运输、生产过程中极易产生自聚物,丁二烯的自聚物有危害性,严重时还会引发自发自燃、爆炸、胀裂阀门及管道等事故。
大庆石化顺丁橡胶装置自建成至今饱受丁二烯自聚物的危害,为了减缓自聚物的生成速度,降低其危害性从而保证装置安全稳定运行,大庆石化橡胶装置在实践中从其形成机制、设备设施改进、操作方式变更等多渠道不断摸索总结,形成了一套行之有效的方法,本文从生产实际出发,总结经验以供同行借鉴。
一、丁二烯自聚物的种类与性质1、丁二烯端基聚合物。
是一种高度交联的树脂状聚合物,外观呈玻璃状晶体、带绒毛针状晶体、透明或半透明的颗粒状晶体等形态,其质地坚硬且脆,易于撕裂,不溶于任何有机溶剂。
形成过程是在铁离子的催化作用下,产生自由基,连锁聚合,导致链增长,生成高交联度的块状聚合物使体积增大,产生膨胀应力。
2、丁二烯过氧化物。
是一种粘滞的、浅黄色、糖浆状、可流动的液体,过氧键较长且弱,键能为84~209 J/mol,比较小,极不稳定,受低热、摩擦、震动或与氧化物接触时,极易发生爆炸。
对乳液聚合体系,要求丁二烯过氧化物严格控制在10 mg/L以下。
3、丁二烯二聚物。
是2个丁二烯分子反应生成4-乙烯-1-环己烯(4-VCH)、乙烯基环己烯(VCH)或一般的二聚物。
4-VCH是一种粘滞性的、可流动的、极易爆炸的油状液体,当空气中4-VCH质量达到0.5 mg/L时芳香气味就非常明显。
在ABS装置PBL和高接枝粉(HRG)反应阶段,丁二烯二聚体对聚合反应有抑制作用。
4、橡胶状聚合物。
丁苯橡胶装置单体回收工序自聚物的产生与预防
丁苯橡胶装置单体回收工序自聚物的产生与预防发表时间:2020-12-23T06:05:23.035Z 来源:《防护工程》2020年26期作者:陈麒光[导读] 通过优化工艺操作条件、进行技术改造、规范操作等手段,延长单体回收系统的运行周期,达到连续平稳生产节能降耗的目的。
抚顺石化烯烃厂丁苯橡胶车间摘要:以丁苯橡胶装置为研究对象,分析单体回收单元关键设备易堵聚、运行周期短的原因,通过优化工艺操作条件、进行技术改造、规范操作等手段,延长单体回收系统的运行周期,达到连续平稳生产节能降耗的目的。
关键词:丁苯橡胶;装置;单体回收1单体回收流程说明丁苯橡胶单体回收流程简单介绍:乳液聚合丁苯橡胶生产中,经过反应链聚合反应,一般反应的转化率达到70%左右,未反应的单体要经过单体回收工序进行回收。
首先胶乳流经压力闪蒸罐和真空闪蒸罐,在两级闪蒸罐中,丁二烯单体闪蒸出来经过冷却器冷凝,返送至回收单体储罐中再循环使用,闪蒸后的胶乳进入C-6401汽提塔中,经过多级塔盘,苯乙烯从塔顶汽提出来,经过冷凝后进行回收,已经脱去单体的胶乳再进入下一工序,输送至胶乳储存罐中储存。
如下图:图1工艺流程简图2自聚物的产生机理以及生产条件的制约堵塞单体回收工序管线的物料主要是丁二烯自聚物,包括丁二烯二聚物、丁二烯过氧化物和丁二烯端基聚合物。
丁二烯二聚物:其中:x+y=n,y>x,n=7~30丁二烯过氧化物在丁二烯生产、回收、储存中均会产生,产生的速率与反应温度、反应时间及气相氧的含量有关。
所以,丁二烯的生产、储存时,要求严格控制气相氧含量。
丁二烯端聚物:丁二烯过氧化物断链形成的活性自由基与丁二烯发生连锁式自由基形成,俗称:爆米花状丁二烯端基聚合物,在铁锈和水存在状况下更容易产生端基聚合物。
在丁苯橡胶生产装置中,其中真空系统运行条件是在真空200mmHg的条件下,阀门及法兰连接处无法做到绝对密封,系统中的不凝气体,最终经真空闪蒸槽排往煤油吸收系统和废气处理设备,所以真空状态下的设备及管线由于氧的存在,生产运转周期长容易产生丁二烯的氧化物及端基聚合物的积聚,其中真空闪蒸罐及周边的管线自聚物最普遍。
丁苯橡胶装置自聚物的产生及预防对策
Vol134No111・86・化工新型材料N EW CH EMICAL MA TERIAL S第34卷第11期2006年11月兰州石化科技丁苯橡胶装置自聚物的产生及预防对策李铁柱1 曹建明2 李金山1 仇国贤2(1.中国石油兰州石化公司橡胶厂,兰州730060;2.中国石油兰州石化公司石油化工研究院,兰州730060;摘 要 论述了丁苯橡胶装置中丁二烯自聚物的产生、预防,并提出确保装置安全平稳生产的措施。
关键词 丁二烯,二聚体,过氧化物,端聚物 兰州石化合成橡胶厂乳聚丁苯橡胶(ESBR)装置,投产于上世纪60年代初,历经40余年的发展和技术进步,已由引进时的1135万t/a热聚法丁苯橡胶逐步改造成目前的515万t/a冷聚丁苯橡胶。
在长期生产过程中,对丁二烯自聚物、过氧化物的产生、危害及预防有了系统的认识。
丁二烯自聚物在本套装置上的碳氢相配制、聚合、脱气回收等单元都不同程度的存在。
不仅增大了单体消耗,而且往往堵塞设备、管线、阀门等,使装置被迫停车,影响长周期运行,严重时,会使设备损坏,造成火灾爆炸等恶性事故,对安全生产威胁极大。
1988年,该装置压缩岗位R106丁二烯气液分离罐,因丁二烯过氧化物在设备内分解,瞬间形成强烈的化学反应,导致着火爆炸,设备毁坏。
事故造成了巨大损失,同时也带来深刻教训。
为了确保安全、稳定、长周期、满负荷生产,必须采取积极措施,防止丁二烯自聚物的形成。
本文旨在结合本套装置实际,结合日常生产管理上的一些做法,对丁苯装置长周期开车过程中防止丁二烯自聚物生成的预防做进一步探讨。
1 丁二烯自聚物的产生及其影响因素丁二烯属共轭二烯烃,其化学性质十分活泼,很易自聚,装置上常见的自聚物有丁二烯二聚体、过氧化物和端基聚合物等。
丁二烯二聚体多存在于回收丁二烯中,是由2个丁二烯分子聚合形成的环状化合物。
温度升高对其形成有直接促进作用。
丁二烯二聚体对聚合反应有抑制作用,对聚合反应速率及门尼黏度的下降有明显影响。
丁二烯自聚物的形成、危害及预防措施
丁二烯自聚物的形成、危害及预防措施发布时间:2023-03-03T06:45:46.333Z 来源:《中国科技信息》2022年10月19期作者:李涛1 金发荣2 安冰3[导读] 介绍了1,3-丁二烯自聚物形成的原因,通过对顺丁橡胶回收装置自聚物产生的部位以及产生自聚物的原因、危害李涛1 金发荣2 安冰3(13.新疆天利高新石化股份有限公司新疆克拉玛依市 600339; 2. 新疆蓝德精细石油化工股份有限公司新疆克拉玛依市 600339)摘要:介绍了1,3-丁二烯自聚物形成的原因,通过对顺丁橡胶回收装置自聚物产生的部位以及产生自聚物的原因、危害,提出了预防丁二烯自聚物产生的针对性措施,避免丁二烯自聚物的生成,保证装置的安、稳、长运行。
关键词: 1,3-丁二烯;丁二烯自聚物蓝德精细公司顺丁橡胶装置采用国内镍系催化体系溶液聚合生产工艺。
自建成投产以来,回收装置丁二烯系统经常出现自聚物堵塞仪表引线、冷凝器及再沸器管束、机泵过滤器等,造成仪表假显,机泵不上量、换热器换热效果差、塔顶压力高、塔顶采不畅等,严重影响装置长周期运行。
本文结合装置运行过程中的实际问题及解决经验,对回收装置丁二烯自聚物产生的原因进行分析,并制定相应的控制措施。
1 1,3-丁二烯的物化性质常温常压下为无色、有芳香味、有毒的气体,相对密度0.6211(在20℃下的液体),沸点-4.41℃,是一种极易液化的无色气体,可与空气形成爆炸性混合气体,其爆炸极限为2.16%~11.47%;1,3-丁二烯分子结构中有2个双键,碳碳双键具有共轭效应,极不稳定,具有很强的聚合性,产生高分子聚合物。
1,3-丁二烯化学分子式CH2=CH-CH=CH2,缩写为C4H6,分子量54,结构式:2 1,3-丁二烯自聚物的种类1,3-丁二烯自聚物主要有丁二烯二聚物、橡胶状聚合物、丁二烯过氧化自聚物和丁二烯端聚物四种。
2.1 丁二烯二聚物丁二烯二聚物为丁二烯的热聚物,1,3-丁二烯受热发生二聚反应,生成4-乙烯基环己烯,在常温下为液体,具有流动性,沸点116℃,可以与1,3-丁二烯以任何比例互溶。
- 1、下载文档前请自行甄别文档内容的完整性,平台不提供额外的编辑、内容补充、找答案等附加服务。
- 2、"仅部分预览"的文档,不可在线预览部分如存在完整性等问题,可反馈申请退款(可完整预览的文档不适用该条件!)。
- 3、如文档侵犯您的权益,请联系客服反馈,我们会尽快为您处理(人工客服工作时间:9:00-18:30)。
低温乳聚丁苯橡胶装置自聚部位、原因分析及处理措施姓名:李伟才单位:中国石油化工股份有限公司齐鲁分公司橡胶厂时间:2010年5月27日摘要:在丁苯橡胶装置的单体回收系统中,常会生成自聚物,其增长迅速,可引起爆炸,导致设备或管线堵塞或暴裂。
苯乙烯滗析器、丁二烯贮槽、闪蒸槽、压缩机系统及负压系统均发生过严重自聚事故,严重影响装置的正常生产。
本文着重分析自聚原因、自聚发生的部位和应采取的措施,预防自聚事故的发生。
关键词:自聚物氧含量阻聚剂乳聚丁苯橡胶是由丁二烯与苯乙烯共聚生成,丁二烯和苯乙烯都能自聚,在贮槽、回收闪蒸槽、汽提塔、压缩机及循环密封水系统、输送管线中都可能生成自聚物。
自聚物包括苯乙烯自聚物、丁二烯过氧化自聚物及端基聚合物。
自聚物呈白色米花状,遇氧体积迅速增长,生成坚硬的交联聚合物。
自聚物堵塞阀门使其无法开关、堵塞压力检测点和液位监测点造成压力液位指示不准、堵塞管道影响胶乳正常输送,需切换设备进行清理;严重时自聚物能使管线涨裂,造成丁二烯、苯乙烯泄漏,不仅使单体消耗过高还给安全环保的重大隐患。
1 产生自聚物的原因分析1.1系统氧含量较高丁苯橡胶装置产生自聚物一般有以下原因:系统氧含量高,单体贮存温度高,阻聚剂存在问题等。
1.1.1系统存在漏点丁二烯与苯乙烯的回收系统多为负压操作,设备的人孔、管线法兰的石棉垫片长时间运行,由于热胀冷缩振动等会渗漏甚至泄漏,冬季部分管线死角有残液,产生冻情造成垫片呲裂等因素都会造成系统中氧含量升高,使丁二烯容易氧化产生氧化物,过氧化物自由基加速了丁二烯苯乙烯自聚物的生成。
此外,负压系统的气相管线、阀门在运行过程中不可避免的产生少量自聚物,导致设备切出清理时阀门关闭不严,清理期间系统氧含量升高,设备、阀门内漏也是导致系统氧含量升高的主要原因。
1.1.2系统的除氧能力不够通常丁苯装置采取的除氧手段有三种:1、对所有聚合用水经行脱氧处理;2、聚合系统加入除氧剂连二亚硫酸钠溶液;3、回收丁二烯时,将包括氧在内的不凝性气体引入煤油吸收塔,吸收丁二烯后放空,消除系统积累的氧。
这些方法都存在缺点:除氧剂溶液配制过程中,部分除氧剂接触氧本身被氧化,造成溶液除氧能力下降;煤油吸收塔系统操作压力较低,不凝气流速小,不能尽快将氧带走,致使回丁系统内的氧含量超标。
1.1.3配制溶液易进入溶解氧聚合反应的配制液,在常压敞口贮罐中配制,虽有氮封但仍可能接触空气,配制液存在少量的溶解氧。
溶解氧在适当的条件下,进行释放,造成系统氧的存在。
1.1.4系统设备氮气置换不合格丁二烯、苯乙烯回收系统在开车投料前、备用设备投用前应进行氮气置换,氧含量在0.5%以下方可投用。
部分班组控制不严格,职工责任心不强,置换不充分,造成系统内氧气积累。
1.2设备、管道存在死角,易自聚通常贮罐上附件如测压点、液位计、阀门等存在流动死角的部位,阻聚剂不能进入其中,易发生自聚,局部自聚后处理不及时,晶种急剧增长,可导致贮罐内丁二烯、苯乙烯自聚,酿成大的生产事故。
1.3苯乙烯中混有一定含量的丁二烯,致使苯乙烯自聚苯乙烯本身不存在“自聚种子”,但有较强的活性,丁二烯在金属(特别是铁)、水和活性氧的共存下可能成为活性“种子”,微量丁二烯作为晶种放入苯乙烯中,容易生成苯乙烯自聚物。
如:苯乙烯泌析器、高、中段压缩机密封水罐、低段压缩机分离器等均易发生自聚。
1.4 贮罐贮存温度也是影响苯乙烯自聚的重要因素自聚物的生长速度随温度的升高而加快,在27℃以上时,反应速度急剧增加。
下表为回收苯乙烯系统物料来源及物料温度关系:表1物料温度表物料来源TK-402 TK-403 TK-406 SE-401 HE-503 SE-50230-40 45-55 <40 5-15 5-15 5-15 物料温度(℃)35 50 35 10 10 10平均温度(℃)前三处与后三处物料流量基本相等,将物料比热也看作相等,将前三处混合后的温度按t1=40℃计,后三处的物料温度按t2=10℃计,则m1c1△t1 = m2c2△t2m1c1(t1-t0)= m1c1(t0-t2)t0 = (40+10)÷2=25℃从计算得出贮槽内温度是25℃,为自聚反应提供了可能条件,在炎热的夏天温度随之升高,如阻聚剂TBC 加入量少,未采取有效的降温措施,可能导致苯乙烯自聚乃至爆聚。
1.5阻聚剂的因素1.5.1丁二烯、苯乙烯中阻聚剂的含量低通常采用的阻聚剂为对叔丁基邻苯二酚(TBC),一般贮槽长期贮存时加入量为300~500ppm,参加聚合反应的丁二烯、苯乙烯阻聚剂的含量控制在30ppm以下。
阻聚剂TBC能阻止端聚物形成,也具有强烈抑制聚合的作用,阻聚剂含量较高,影响聚合反应速率,阻碍聚合反应的正常进行。
1.5.2阻聚剂的质量波动通常采用苯乙烯配制成1%阻聚剂溶液,由于回收丁二烯、苯乙烯中TBC加入量少(10~50ppm),单体中TBC含量波动较大,控制困难。
TBC是回收丁二烯、苯乙烯防止自聚物和端聚物的关键手段,TBC质量对装置长周期运行影响显著。
1.6原料原因1.6.1回收丁二烯、苯乙烯纯度低,外排量较少,循环使用,导致系统积存的杂质增加,系统不能有效置换,易产生自聚物。
1.6.2新鲜苯乙烯内供,新鲜丁二烯主要自产,但09年装置扩能之后,外购丁二烯比例提高至三分之一,外购丁二烯质量参差不齐,部分丁二烯二聚物很高,在贮存和输送过程中,易产生自聚物。
2 回收装置易产生自聚物的设备及管线2.1水环压缩机系统易产生自聚物2.1.1机压缩机循环密封水机泵及排净阀压缩机循环密封水机泵在运行过程中产生自聚物易堵塞排净阀及其管线,机泵内残液排不净,在备用过程中产生自聚物。
2.1.2气相管线中阀门、调节阀等仪表的副线PRCA361、高中低段压力调节等仪表的副线、阀门测压点,以及高中低三段压缩机机体倒淋和三段压缩机循环密封水泵倒淋等也是产生丁二烯自聚物的高发区。
2.1.3压缩机远端的气相液相管线备用压缩机气液相管线,距离主线有一定距离,存在死角,三段压缩机并联使用,因三线扩建时存有缺陷,压缩机的运行在保证定期切换的基础上,要尽可能开启远端压缩机,以保证管线无死角。
2.1.4三段压缩机的循环密封水系统循环密封水系统过滤器、冷却器气相、副线分离器液相管线死角是产生自聚物的场所,主要是苯乙烯的端聚物。
中低段压缩机密封水系统曾多次发生自聚。
密封水的丁二烯回收中有与苯乙烯存在,否则很容易使丁二烯成为活性种子,引发苯乙烯的自聚。
丁苯一车间这两部分是分开的,丁苯二车间的苯乙烯和丁二烯回收在同一空间,该系统多次产生大量的自聚物,现已计划改造将苯乙烯和丁二烯的回收分开,以减少自聚物的产生。
丁苯一车间09年大检修苯乙烯泌析器出料室因液位不准确送料不完全,液位监测点堵塞,蒸煮后产生大量的坚硬的苯乙烯自聚物。
2.2单体贮罐易产生自聚物2.2.1回收丁二烯贮罐丁二烯贮罐特别是上部气相空间很容易产生自聚物,测点等经常有自聚物,需要定期氮气置换,夏季用喷淋水降温,加入一定量的阻聚剂。
09年大检修期间胶乳车间暂存的丁二烯产生了自聚,由于发现及时没有发生严重的后果。
2.2.2回收苯乙烯贮罐回收苯乙烯贮罐也很容易产生自聚物,上部呼吸阀、不常流动的管线经常被聚死,检修期间存放一个月的苯乙烯产生了大量的低聚物,无法继续用于生产。
2.2.3苯乙烯泌析器苯乙烯泌析器的水室及苯乙烯室正常运行中也有自聚物产生,例如丁苯一车间。
苯乙烯泌析器曾经发生过苯乙烯暴聚事故,整个苯乙烯泌析器被坚硬透明的苯乙烯自聚物充满,09年大检修冷凝器至泌析器管线的副线也发现及其坚硬的玻璃状透明苯乙烯自聚物。
2.3单体换热系统易产生自聚物2.3.1丁二烯冷凝器丁二烯冷凝器中管程及气相会产生大量的丁二烯自聚物,这部分自聚物坚硬难于清理,导致换热器效率下降。
2.3.2苯乙烯冷凝器苯乙烯冷凝器的管程及气相也会产生大量的苯乙烯自聚物,堵塞列管,坚硬难于清理。
09年大检修发现气相大阀被大量薄片状自聚物覆盖,在设备清理期间,由于自聚物的存在导致阀门关闭不严,系统进氧加剧了自聚物的产生。
2.4其他易产生自聚物的部位2.4.1泄料槽的气相空间设备附件和管线泄料槽的附件,液位上测点、备用泄料槽的进料口阀门前后、安全阀底阀、小集管底阀、视镜需要定期检查,一旦发现有自聚物产生,要及时清理,特别是液位计上测点,产生自聚物后可能造成假液位,特别是负压泄料的气相自聚,进而会造成胶乳发泡冲浆。
2.4.2管线倒淋丁二烯、苯乙烯管线倒淋附近存在流动死角,是自聚物多发的场所。
3 处理措施3.1严格控制系统内氧含量3.1.1系统漏点的查找和消除负压系统切出清理后,拆开的法兰、人孔,要更换垫片,氮气试漏、保压。
对于漏点较大的设备,要逐一从系统中切离,氮气充压、试漏的办法,消除漏点。
3.1.2提高系统的除氧能力生产中试用效果好的除氧剂。
对煤油吸收系统进行改造:增加了一台冷却器及一台加热器。
新增的盐水冷却器,使煤油冷却后的温度达到10-20℃,提高了煤油对丁二烯的吸收效率。
新增的加热器,能将煤油再加热到45-55℃左右,保证溶解的丁二烯脱吸彻底,而氧等不凝气体排出系统。
3.1.3系统连续或间断氮气置换在负压系统新增N2补加管线,控制流量,使设备、管线的氧气进入煤油吸收塔,排出系统。
对部分贮槽间断氮气置换,降低系统内氧含量。
从改造后可以发现,回收氧含量均合格。
分析数据见表2、表3表2:改造前回收系统氧气含量数据统计TK-404 TK-105最大值最小值平均值合格率最大值最小值平均值合格率4.6 0.1 1.03 58.3% 4.2 0.20 0.67 77.5%表3:改造后回收系统氧气含量数据统计TK-404 TK-105最大值最小值平均值合格率最大值最小值平均值合格率0.5 0.1 0.26 100%0.5 0.10 0.19 100%3.2设备管道局部自聚,应及时切出清理1.检修时改造,对管线倒淋尽量减少死角2.机泵压缩机定期切换,尽量开远端压缩机以保证管线无死角,备用时打开倒淋,用氮气吹扫干净,防止单体自聚。
3.发现阀门或测点有自聚的现象,要立即对设备切出清理。
丁二烯过氧化自聚物通常用硫酸亚铁溶液充满设备,用蒸汽加热蒸煮至少40h以上,使过氧化自聚物被充分破坏。
清理时应使用木质工具,严禁使用金属器具。
贮罐的定期清理,消除自聚的活性种,降低系统自聚的可能性。
4.对现场液位计存在死角经常堵塞失灵问题,建议在液位计的连通阀上接入氮气,隔几天吹扫一次,吹扫流程图如下:LGN23.3控制反应,避免苯乙烯中混有一定含量的丁二烯针对苯乙烯中含有丁二烯致使苯乙烯自聚问题,应从稳定聚合、回收系统控制指标入手。
即在日常操作中,控制好转化率、泄料槽闪蒸温度、压力、液位,避免发泡冲浆事故的发生。