焊装夹具设计毕业设计论文.doc
关于汽车车身焊装夹具设计探讨

关于汽车车身焊装夹具设计探讨摘要:在汽车车身前期设计中,焊装夹具设计是十分关键的内容,设计质量以及加工工艺能够直接影响汽车车身制造质量。
对此,本文首先对汽车车身焊装夹具的作用及组成进行介绍,然后对汽车焊装夹具设计原则以及具体的设计策略进行详细探究。
关键词:焊装;夹具;设计新时期,汽车已成为人们日常出行中的常用交通工具,通过加强汽车焊接质量控制,有利于提高汽车制造质量,促进汽车行业稳定发展。
汽车焊装夹具会直接影响汽车制造周期以及精度,因此,必须重点关注汽车焊装夹具设计。
一、汽车车身焊装夹具的作用及组成现如今,我国汽车使用量在世界范围内占据首位,国内汽车制造行业面临很多发展机遇和挑战,在汽车生产制造方面,车身质量管控至关重要,而不同车型的车身结构形式比较复杂,在具体的设计过程中构图难度大,在各类因素影响下容易发生变形,同时,车身尺寸还会对汽车结构装配质量以及效率产生较大影响,对此,需加强焊接装配工艺控制。
为了促进汽车车身焊接质量提升,应对焊装夹具进行优化设计,进而实现汽车车身流水线生产,尽量缩短焊接装配所需时间,同时通过提高夹具设计精度,还可保证汽车焊接装配质量和效率。
在汽车车身生产制造中,焊装夹具是十分重要的工具,通过快速定位工作元件,能够保证元件焊装的准确性。
在汽车制造中,在金属结构焊接方面,焊装夹具为十分关键的工具类型,在焊接工艺中可发挥夹持和固定的功能,确保汽车焊接工件的形状以及尺寸能够满足企业前期设计方案要求。
在具体的汽车车身焊接过程中,需充分发挥夹具的辅助作用,尽量减少焊接所需时间。
通常情况下,焊装夹具是由三个元件所组成的,即基础元件、符合标准元件以及外购元件[1]。
二、汽车焊装夹具设计原则在汽车焊装夹具设计中,对于整个设计过程,可分为四个环节,包括定位、夹紧、辅助元件以及夹具空间设计。
在具体的设计过程中,必须严格遵循六点定则,具体而言,需对六个方向自由度进行严格控制。
在对汽车车身六个方向自由度进行限定时,可联合应用孔定位法、面定位法等,确保零件定位准确性。
毕业设计论文夹具设计
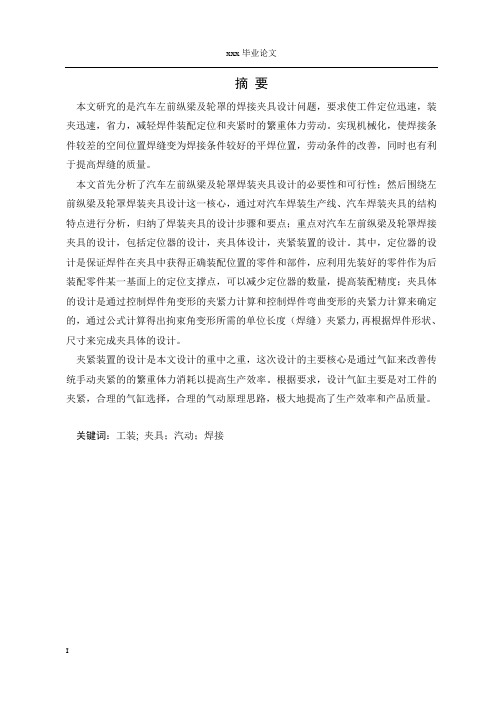
xxx毕业论文摘要本文研究的是汽车左前纵梁及轮罩的焊接夹具设计问题,要求使工件定位迅速,装夹迅速,省力,减轻焊件装配定位和夹紧时的繁重体力劳动。
实现机械化,使焊接条件较差的空间位置焊缝变为焊接条件较好的平焊位置,劳动条件的改善,同时也有利于提高焊缝的质量。
本文首先分析了汽车左前纵梁及轮罩焊装夹具设计的必要性和可行性;然后围绕左前纵梁及轮罩焊装夹具设计这一核心,通过对汽车焊装生产线、汽车焊装夹具的结构特点进行分析,归纳了焊装夹具的设计步骤和要点;重点对汽车左前纵梁及轮罩焊接夹具的设计,包括定位器的设计,夹具体设计,夹紧装置的设计。
其中,定位器的设计是保证焊件在夹具中获得正确装配位置的零件和部件,应利用先装好的零件作为后装配零件某一基面上的定位支撑点,可以减少定位器的数量,提高装配精度;夹具体的设计是通过控制焊件角变形的夹紧力计算和控制焊件弯曲变形的夹紧力计算来确定的,通过公式计算得出拘束角变形所需的单位长度(焊缝)夹紧力,再根据焊件形状、尺寸来完成夹具体的设计。
夹紧装置的设计是本文设计的重中之重,这次设计的主要核心是通过气缸来改善传统手动夹紧的的繁重体力消耗以提高生产效率。
根据要求,设计气缸主要是对工件的夹紧,合理的气缸选择,合理的气动原理思路,极大地提高了生产效率和产品质量。
关键词:工装; 夹具;汽动;焊接AbstractThis study is the car left front rail and wheel cover welding fixture design, requirement for a workpiece positioning rapidly and clamping quickly, effort, reduce welding assembly positioning and the clamping heavy manual labor. Realization of mechanization, make for better conditions for the downhand welding position welding, improve working conditions and to improve the welding quality of poor condition of the space position of welding seam welding.This paper first analyzes the car left front longitudinal beam and the wheel cover the necessity and feasibility of welding fixture design, and then around the left front rail and wheel cover welding fixture design of the core, according to structural characteristics of car body welding production line, automobile welding fixture analysis, summed up the welding fixture design steps and main points; key to car left front longitudinal beam and the wheel cover welding fixture design, including locator design, clip specific design and clamping device design. Among them, design of locator is guarantee welding fixture in China obtain accurate position of the assembly of parts and components, should use first loaded parts as assembly parts a base surface positioning supporting point, can reduce the locator number to enhance the assembly precision; to clamp the specific design is by the angle to control the welding deformation of the clamping force calculation and control of welding a bending deformation of the clamping force calculation to determine the, through the formula calculation show that angle restraint deformation required per unit length (weld) clamping force, then according to the welding shape, size to complete specific design clamp.Clamping device design is the most important in this paper, the main core of this design is through the cylinder to improve the traditional manual clamping of the heavy manual to improve production efficiency. According to the requirements, the design of the cylinder is mainly for the clamping of the workpiece, a reasonable choice of the cylinder, a reasonable aerodynamic principle of thinking, greatly improving the production efficiency and product quality.Key words: Tooling;fixtures;pneumatic;welding目录第1章绪论 (4)1.1 课题的背景及意义 (4)1.2 焊装夹具国内外研究概况 (4)1.3 汽车焊装夹具研究概况 (5)1.3.1 车身焊接原理 (5)1.3.2 汽车车身常用焊接方法 (6)1.3.3 焊装夹具的功用 (8)1.3.4 焊装夹具设计要求 (9)1.3.5 夹具的基本构成 (9)1.3.6 夹具的设计步骤 (10)1.4 本课题研究内容 (10)第2章车身焊装夹具设计 (12)2.1 定位加紧方案确定 (12)2.1.1 夹具的定位方案的确定 (12)2.1.2 夹具的夹紧方案的确定 (14)2.2 单元夹具设计思路 (16)2.2.1 主要控制断面形状(MCS) (16)2.2. 2夹具单元设计思路 (16)2.3 夹具单元设计过程 (17)2.3.1 U09夹具单元设计过程 (17)2.3.2 U14夹具单元设计过程 (23)第3章生成二维图 (29)3.1 装配图的二维图 (29)3.2 零件图的二维图 (32)结论 (35)致谢 (36)参考文献 (37)第1章绪论1.1课题的背景及意义汽车工业是我国国民经济支柱产业之一,在国民经济发展中有特殊地位和作用,汽车工业能极大地带动和促进其它工业和产业的发展,并且成为显示一个国家工业发达水平的重要标志。
焊接夹具论文.doc

目录第一章绪论 (1)1.1课题背景 (1)1.2国外概况和焊装夹具目前发展状况 (1)1.3 本文主要研究内容 (2)第二章汽车焊装夹具整体方案设计 (3)2.1焊装夹具简介 (3)2.1.1焊装夹具基本概念 (3)2.1.2夹具的定位原理 (3)2.2 CD柱内板总成设计分析 (4)2.2.1 CD柱内板总成各部分简介 (4)2.2.2 CD柱内板总成自由度的限定 (6)2.2.3 CD柱内板总成各夹具简介 (6)第三章焊装夹具设计 (7)3.1焊装夹具设计流程 (7)3.2 夹具设计的文件管理 (8)3.2.1 文件目录命名 (8)3.2.2 文件命名 (8)3.3 焊接夹具结构组成和断面形状 (8)3.3.1焊装夹具的结构组成 (8)3.3.2 主要控制断面形状(MCS) (9)3.4 U02焊接夹具设计 (11)3.4.1 P NL截面 (11)3.4.2 压块设计 (12)3.4.3 定位块的设计 (13)3.4.4 压板的设计 (14)3.4.5 连接板 (16)3.4.6 U02夹具运动分析 (18)3.4.7 气缸的选择验证 (19)3.5 U01工位焊接夹具设计 (20)3.6 U11和U12工位焊接夹具设计 (21)3.7 P03工位单独固定销设计 (24)3.7.1 销支架设计 (24)3.7.2 连接块的设计 (25)3.7.3 支架的设计 (26)3.8 绘制工程图 (27)第四章总结 (30)致谢 (30)参考文献 (31)第一章绪论在我国汽车行业不断蓬勃发展,国产汽车品质也越来越高。
同时为了提高汽车产量,增加汽车车身焊接效率,我国汽车行业对汽车车身自动焊接夹具的需求正在不断增长。
汽车车身的加工是通过冲压、焊接、涂装和总装进行生产的,焊接作为四大工艺之一,在汽车设计和生产占据主要部分,同时汽车车身的焊接关系着汽车整体车况的稳定性和安全性,在用户不断追求安全舒适的激烈竞争情况下,汽车焊接在四大工艺中扮演着越来越重要的角色。
浅谈汽车焊装夹具的设计

等要充分考虑其加工工艺性及零部件的通用化和标准化, 便于更换易损件和恢复原设计精度。(5)车身总成的装 焊夹具比较复杂笨重,在制造使用中常需调整样架来进 行调整校正。2.2 装焊定位基准的选
择装夹工件时,使工件在夹具中占有正确位置所采用的 基准,称为定位基准,定位基准的选择正确与否将直接 影响工件的装配精度。2.3 定位方法和定位元件车身装焊 夹具装夹的主要对象是冲压件,由于制
,有手动,气动、液压式等,这些夹紧机构的设计与一 般机床夹具设计大同小异,可参考借鉴。2.5 车身总成装 焊夹具车身总成装焊夹具按其定位方式分为一次性定位 和多次性定位。一次性装配定位的总装
夹具是指车身总成的主要装焊工作在一台总装夹具上完 成。组成车身的零件,合件,分总成等依次装到总装夹 具上,进行定位和夹紧,直至车身总成的主要装焊工作 完毕,才从夹具上取下来。这种夹具的特点是
要求(1)对于冲压零件装焊后应具有互换性的车身合件 及总成,应使用车身的各配合部位,特别是孔洞的形状 尺寸符合技术要求。(2)能快速准确地进行装配定位、 夹紧,被焊部位要便于操作,松开夹紧机
构后,焊件能从夹具上方便地卸下,且安全可靠。(3) 在设计夹具时,要注意夹具上的某些零部件出现导电, 绝缘等问题,提高车身的装焊质量。(4)由于车身结构 复杂,因此,对所设计的定位件、夹紧件
身总成的主要装焊工作是在2台以上的不同装焊夹具上完 成的。车身每通过一台总装夹具就要被定位夹紧1次,主 要用于有骨架驾驶室的装焊,如在第一台夹具上完成内 骨架的装简单,数量少,不存在 水,电,气的连接问题,若增加定位夹紧次数,则容易 产生装配误差。3 设计流程分析以某汽车的前地板预总成 工位的某一焊装夹具为例,阐述其焊装夹
作外形复杂且易变形,因此在夹具设计时应考虑用曲面 外形、曲面上经过整形的平台、工件经拉延和弯曲成形 的台阶、经修边的窗口和外部边缘、装配用孔和工艺孔 等部位定位。由于冲压件外形复杂,装夹过程
分析车身焊接夹具的设计规律论文
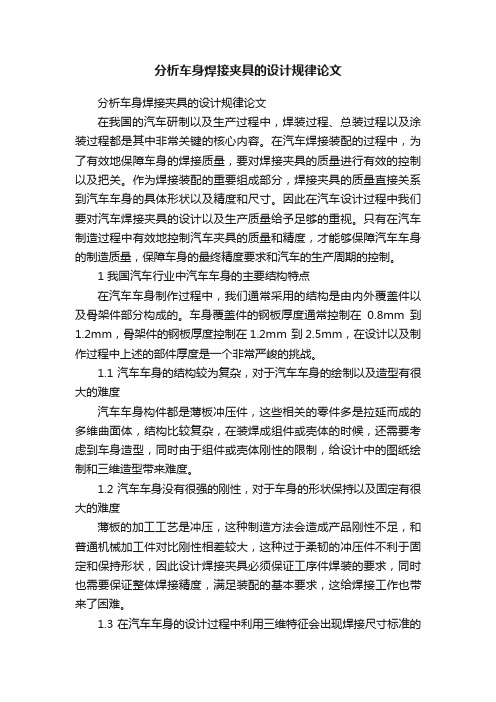
分析车身焊接夹具的设计规律论文分析车身焊接夹具的设计规律论文在我国的汽车研制以及生产过程中,焊装过程、总装过程以及涂装过程都是其中非常关键的核心内容。
在汽车焊接装配的过程中,为了有效地保障车身的焊接质量,要对焊接夹具的质量进行有效的控制以及把关。
作为焊接装配的重要组成部分,焊接夹具的质量直接关系到汽车车身的具体形状以及精度和尺寸。
因此在汽车设计过程中我们要对汽车焊接夹具的设计以及生产质量给予足够的重视。
只有在汽车制造过程中有效地控制汽车夹具的质量和精度,才能够保障汽车车身的制造质量,保障车身的最终精度要求和汽车的生产周期的控制。
1 我国汽车行业中汽车车身的主要结构特点在汽车车身制作过程中,我们通常采用的结构是由内外覆盖件以及骨架件部分构成的。
车身覆盖件的钢板厚度通常控制在0.8mm到1.2mm,骨架件的钢板厚度控制在1.2mm 到2.5mm,在设计以及制作过程中上述的部件厚度是一个非常严峻的挑战。
1.1 汽车车身的结构较为复杂,对于汽车车身的绘制以及造型有很大的难度汽车车身构件都是薄板冲压件,这些相关的零件多是拉延而成的多维曲面体,结构比较复杂,在装焊成组件或壳体的时候,还需要考虑到车身造型,同时由于组件或壳体刚性的限制,给设计中的图纸绘制和三维造型带来难度。
1.2 汽车车身没有很强的刚性,对于车身的形状保持以及固定有很大的难度薄板的加工工艺是冲压,这种制造方法会造成产品刚性不足,和普通机械加工件对比刚性相差较大,这种过于柔韧的冲压件不利于固定和保持形状,因此设计焊接夹具必须保证工序件焊装的要求,同时也需要保证整体焊接精度,满足装配的基本要求,这给焊接工作也带来了困难。
1.3 在汽车车身的设计过程中利用三维特征会出现焊接尺寸标准的问题汽车车身的.焊接具有非常强的三维空间特征,而且三维跨度非常大,这给焊接夹具设计中的尺寸标注带来了一定的困难。
为保证夹具能符合要求,必须对车身进行空间坐标标注,为夹具的空间尺寸特征提供必要的参数。
(汽车行业)汽车车身焊装夹具设计

(汽车行业)汽车车身焊装夹具设计汽车车身焊装夹具设计摘要:通过对汽车车身焊接夹具设计的壹般规律进行探讨,提出了在焊接夹具设计中所应该遵循的基础条件。
在现生产中,焊接夹具的设计充满了丰富的特殊性,因此,具体问题须具体对待。
关键词:焊接夹具设计经验性综合技术汽车车身焊接夹具的设计是壹门经验性很强的综合性技术,在设计时首先要确定生产纲领,熟悉产品结构,了解变形特点,把握制件及装配精度,通晓工艺要求。
只有做到这些,才能对焊接夹具进行全方位的设计。
生产纲领生产纲领决定焊接夹具的自动化水平及焊接工位的配置,是通过生产节拍体现的。
生产节拍由夹具动作时间、装配时间、焊接时间、搬运时间等组成。
夹具动作时间主要取决于夹具的自动化程度;装配时间主要取决于冲压件精度、工序件精度、操作者的熟练程序;焊接时间主要取决于焊接工艺水平、焊接设备的自动化程度、焊钳选型的合理化程度等;搬运时间主要取决于搬运的自动化程度、物流的合理化程度等。
只要把握住之上几点,就能合理地解决焊接夹具的自动化水平及制造成本这对矛盾。
汽车车身的结构特点汽车车身壹般由外覆盖件、内覆盖件和骨架件组成,覆盖件的钢板厚度壹般为0.8-1.2mm,骨架件的钢板厚度多为1.2-2.5mm,也就是说它们大都为薄板件。
对焊接夹具设计来说,有以下特点:1、结构形状复杂,构图困难汽车车身都是由薄板冲压件装焊而成的空间壳体,为了造型美观和壳体具有壹定的刚性,组成本身的零件通常是经过拉延成型的空间曲面体,结构形状较为复杂。
2、刚性差、易变形经过成型的薄板冲压件有壹定的刚性,但和机械加工件相比,刚性要差得多,而且单个的大型冲压件容易变形,只有焊接成车身壳体后,才具有较强的刚性。
3、以空间三维坐标标注尺寸汽车车身产品图以空间三维坐标来标注尺寸。
为了表示覆盖件在汽车上的位置和便于标注尺寸,汽车车身壹般每隔200mm 或400mm 划壹坐标网线。
三个坐标的基准是:前后方向(Y 向)———以汽车前轮中心为0,往前为负值,往后为正值;上下方向(Z 向)———以纵梁上平面为0,往上为正值,往下为负值;左右方向(X 向)———以汽车对称中心为0,左右为正负。
直缝---焊接---夹具设计论文
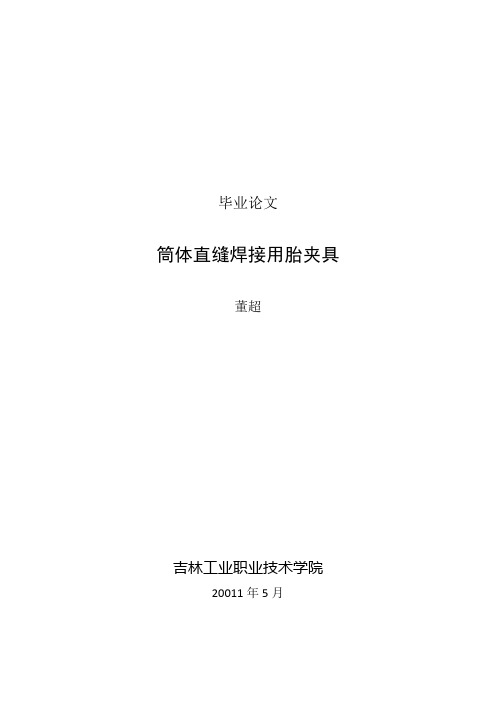
毕业论文筒体直缝焊接用胎夹具董超吉林工业职业技术学院20011年5月毕业论文筒体直缝焊接用胎夹具学生:董超导师:鲁海龙系别:机电工程系专业:焊接技术及自动化班级:3082班答辩日期:20011年5月筒体直缝焊接用胎夹具设计摘要简要从结构,操作及夹紧三方面考虑筒体直缝焊接用胎夹具的特点,对筒体直缝焊接用胎夹具提出了具体的设计方案。
关键词筒体夹具设计;英文翻译;Cylinder straight seam welding jigs Briefly from the structure, operating and clamping three aspects cylinder straight with tire fixture seam welding characteristics of the cylinder with tire jig straight seam welded puts forward concrete design scheme目录摘要 (1)第一章绪论 (3)1.1课题背景 (3)1.1.1产生背景 (4)第二章夹具的设计方案 (4)2.1本章小结 (9)第三章夹具的制造工艺 (10)3.1本章小结 (15)结论 (16)参考文献 (17)致谢 (18)第一章绪论焊接工艺装备是在焊接结构生产的装配与焊接过程中起配合及辅助作用的夹具、机械装置或设备的总称,简称焊接工装。
其中夹具主要包括定位器、夹紧器、推接装置等;机械装置或设备主要包括焊件变位机、焊机变位机、焊工变位机等。
在现代焊接结构生产中,积极推广和使用与产品结构相适应的焊接工装,对提高产品质量,减轻焊接工人的劳动强度,加速焊接生产实现机械化、自动化进程等诸方面起着非常重要的作用。
钢制圆形筒体在建材化工等工业中应用十分广泛。
由于应用的行业不同,工作环境不同,故对其使用性能要求和选材随之而异,所用的工装也存在差异。
焊接结构生产全过程中,纯焊接所需作业工时仅占全部加工工时的25%~30%,其余是用于备料、装配及其他辅助工作。
焊接夹具毕业设计

焊接夹具毕业设计焊接夹具毕业设计在工业生产中,焊接是一项常见的工艺,用于将金属部件连接在一起。
而为了确保焊接的质量和效率,使用焊接夹具是必不可少的。
焊接夹具是一种用于夹持工件并保持其正确位置的装置,它可以提供稳定的工作环境,使焊接过程更加精确和高效。
一、焊接夹具的作用焊接夹具在焊接过程中起着至关重要的作用。
首先,它可以固定工件,防止其在焊接过程中发生移动或变形。
这对于要求高精度的焊接任务尤为重要。
其次,焊接夹具可以提供稳定的工作平台,使焊工能够更加专注于焊接操作,减少操作失误的可能性。
此外,焊接夹具还可以提供适当的角度和位置,以确保焊接接头的正确对齐,从而确保焊接质量。
二、设计原则和考虑因素在设计焊接夹具时,有几个原则和考虑因素需要被纳入考虑。
首先是夹具的稳定性和刚度。
夹具必须足够稳定,以确保工件在焊接过程中不会发生移动或变形。
其次是夹具的可调性。
夹具应该具有一定的可调性,以适应不同尺寸和形状的工件。
此外,夹具的结构应该简单、易于操作和维护。
最后,夹具的材料选择也很重要。
夹具应该使用耐热、耐腐蚀和具有足够强度的材料,以确保其在长时间使用中的稳定性和耐久性。
三、常见的焊接夹具类型焊接夹具的类型多种多样,根据不同的焊接任务和工件形状,可以选择不同类型的夹具。
以下是一些常见的焊接夹具类型:1. 弹簧夹具:这种夹具使用弹簧力将工件夹持在一起,适用于小型和中型工件的焊接。
2. 磁性夹具:这种夹具利用磁力将工件固定在焊接平台上,适用于具有磁性的工件。
3. 液压夹具:这种夹具使用液压力将工件夹持在一起,适用于大型和重型工件的焊接。
4. 机械夹具:这种夹具使用机械装置将工件夹持在一起,适用于需要更高精度和稳定性的焊接任务。
四、焊接夹具的设计案例为了更好地理解焊接夹具的设计原理和应用,以下是一个设计案例:假设我们需要设计一个用于焊接汽车车身的夹具。
首先,我们需要考虑到汽车车身的复杂形状和结构。
夹具应该能够固定车身的各个部件,并保持它们的正确位置。
- 1、下载文档前请自行甄别文档内容的完整性,平台不提供额外的编辑、内容补充、找答案等附加服务。
- 2、"仅部分预览"的文档,不可在线预览部分如存在完整性等问题,可反馈申请退款(可完整预览的文档不适用该条件!)。
- 3、如文档侵犯您的权益,请联系客服反馈,我们会尽快为您处理(人工客服工作时间:9:00-18:30)。
(试行)
要求类型规制块1/3 3.规制块的设计要求规范
图1 图2
图3
编制校对审核奇瑞汽车有限公司
要求类型规制块2/3
3.1.规制块尺寸要求
常用规制块有如上(图1、图2和图3)三种结构(两销一钉),根据安装要求的不同,中间孔为M8的螺纹孔或ø9的螺钉过孔,两侧的均为ø8H7的销孔。
其尺寸要求如下(表2)所示:
尺寸类型要求尺寸大小(mm)
第一系列第二系列加工公差要求L 60 45
B1 16 16
H 根据板件型面的形状来确定±0.02
L1 15 15
L2 15 15
B2 8 8 ±0.05
S1 10 10 ±0.05
S2 25 25 ±0.02
S3 12.5 12.5
表2
3.2.技术要求
3.2.1. 材质要求:规制块的材料要求必须为45#钢并要进行热处理,使规制块工作面的表面硬度达到 HRC30~35,工作面的粗糙度为,同时规制块要进行表面发蓝处理。
3.2.2. 在遇到如图4所示的板件结构时(需同时规制板件的两个面),要采用两个单独的规制块分别进行规制,不允许使用如图5所示的结构形式,如特殊情况会签时需经奇瑞公司确认后方可使用。
图4 图5
编制校对审核奇瑞汽车有限公司
要求类型规制块3/3
3.2.3. 规制块设计时原则上要求与板件垂直(图6),若因特殊情况不能保证时,则规制块的压紧方向最大斜角(图7)不大于15°,若大于该角度则需要使用导引挡块(CATCH STOPPER)。
图6 图7
3.2.
4. 第一系列的规制块要优先选用,若设计时的空间不够或选用第一系列无法装配时,可以选用第二系列所规定的规制块,但装配时要便于人员的操作,会签时需经奇瑞公司确认后方可实施。
3.2.5. 规制块压紧时要求每个规制块所能达到的压力F(图8)范围为:25kgf≤F≤30kgf,气缸选用时要依此作为依据。
图8
3.2.6. 供货方若使用其他结构形式的规制块,在图纸会签时可向奇瑞公司提出,得到同意后方可使用。
编制校对审核奇瑞汽车有限公司
CHERY AUTOMOBILE CO., LTD
要求类型调整垫片1/2 4.调整垫片的设计要求规范
图9
图10 图11
编制校对审核奇瑞汽车有限公司
要求类型角座1/2 5.角座的设计要求规范
图12
编制校对审核奇瑞汽车有限公司
要求类型BASE 板1/2
6.BASE板的设计要求规范
图13
6.1.常用尺寸要求如表5所示
尺寸类型常用尺寸大小(mm)
S(面积:单位m²) S≤0.5 0.5<S≤0.8 0.8<S≤2.0 S>2.0 H1 20 20 22 25
H2 15 15 15 15 槽钢型号10 12 16 20及以上
表5
6.2.技术要求
6.2.1. BASE板结构要求用Q235-A和槽钢焊接而成,采用非连续焊缝,焊接完毕后要作热处理(不允许机械消除应力)并作喷砂处理。
6.2.2. 根据BASE板面积的大小应依据表5中的尺寸来选择槽钢型号。
6.2.3. BASE板面上的尖角部分要进行倒角处理。
6.2.4. BASE板面上要求有坐标网格线,网格线深度要求0.2~0.3mm,线距要求:大夹具为200mm,小夹具为100mm,在坐标线的端部要刻上坐标号,并要与车身坐标保持一致。
编制校对审核奇瑞汽车有限公司
要求类型BASE 板2/2
坐标网格线的平行度误差要求:相邻单一间隔距0.10mm/100mm;累积间隔距0.30mm/全长。
6.2.5. 基准孔的空间坐标值应设定为一整数值,基准孔孔径要求为ø10H7,并要加盖板保护,避免夹具工作时对其的损坏及影响,空间分布要合理;基准孔坐标值应明显标注在基准孔附近,便于便携式三座标进行测量。
6.2.6. 基准孔原则上要求至少有4个,对于一些大型夹具,如发舱总成、侧围总成、后底板总成、主下线等,要求基准孔总数为6个。
6.2.
7. 槽钢焊接时,开口要向外构成一个封闭的轮廓,方便管路的布置。
6.2.8. BASE板底部滚轮安装板的布置要合理,尺寸要求符合如图13所示:
焊接加强板
图14
6.2.9. 槽钢进行焊接时,不允许直接焊接,应在焊接位置增加加强板,增大焊接面积,增加强度,如图14所示。
6.2.10. 对于要进行CO2焊接的夹具,在BASE板表面要加保护装置,防止焊渣落到BASE板清漆面上,用螺钉固定在BASE板面上,要方便拆卸和更换。
6.2.11. BASE板原则上要求大于板件和及所有的支撑件,若气缸超出底板边缘,应该增加保护装置。
编制校对审核奇瑞汽车有限公司
要求类型导引挡块1/4 7.导引挡块的设计要求规范
7.1.“U”型块
图15 图16
图17 图18 编制校对审核奇瑞汽车有限公司
要求类型导引挡块3/4 7.2.“V”型块
图19
图20
编制校对审核奇瑞汽车有限公司
要求类型定位销1/3 8.定位销的设计要求规范
8.1.定位销的外形尺寸应按以下图示进行设计,其中的尺寸要求如表10所示
(1)圆销:
图21
图22
编制校对审核奇瑞汽车有限公司
要求类型定位销2/3 (2)菱销:
图23
图24
编制校对审核奇瑞汽车有限公司
要求类型定位销3/3
尺寸类型
要求尺寸大小(mm)
第一系列第二系列第三系列第四系列
D D≤10 10<D≤25 25<D≤40 D>40
C 18 D+5
D D
H 14 14 22 32
E 12 12 20 30
F 10 10 16 24
B 5 5 5 5
L 15,20,30
L1 14 14 22 28
L2 12 12 20 30
表10
表10中,第一、二系列如图21、23所示,第三、四系列如图22、24所示。
8.2 定位销技术要求
8.2.1. 定位销直径:D=定位孔理论孔径-0.2 [单位mm];
8.2.2. 定位销材料应采用45#钢,经过热处理后,硬度值达到HRC40-45,表面镀硬铬处理;图21、图22、图23、图24中:Ⅰ、Ⅱ处指示端面应在表面镀硬铬处理后进行精加工,保证装配和定位精度。
图25 图26
编制校对审核奇瑞汽车有限公司
要求类型精度1/1
8.2.3. 定位销工作面的超出板件表面高度为3~5mm,如图26所示,H应为3~5mm。
8.2.4. 定位销定位零件的工作表面粗糙度要求为,其他要求为。
8.2.5. 定位销的装配时应满足方向性要求,如图25所示,便于在调试过程中进行调整。
8.2.6. 菱形销的工作表面处理方法同圆销。
9.精度要求
9.1.各部件要满足如下的精度要求
9.1.1. 定位面的装配精度控制在±0.2mm以内,定位销的装配精度控制在±0.1mm以内。
9.1.2. 定位销的加工精度:直径0~-0.05mm。
9.1.3. BASE板水平面上角座安装销孔与安装销孔之间的公差为±0.02mm,BASE板面粗糙度为,平面度要求达到国标(GB1184-80)7级精度要求。
9.1.4. 所有的安装销孔与加工基准面之间的公差为±0.05mm,销孔内壁粗糙度为。
9.1.5. 基准面与装配面之间要求公差为±0.05mm。
9.1.6. 支架的垂直度允许误差按国标(GB1184-80)7级精度执行。
编制校对审核奇瑞汽车有限公司
内部资料,仅供参考。
精品文档。